Электроды для наплавки – основной металл будет лучше! Электроды наплавочные
Электроды для наплавки бронзы – какими бывают и как используются + Видео
1 Основные сведения о классификации наплавочных электродов
Имеется два Госстандарта – 9466 и 10051, которые содержат техусловия и рассказывают о типах, на которые подразделяют электроды для наплавки. Интересующие нас изделия принято подразделять на отдельные группы по следующим показателям:
- Вид покрытия. Ручная дуговая наплавка производится электродами с целлюлозным, основным, кислым, смешанным или рутиловым покрытием. Также существуют сварочные (наплавочные) стержни, на которые наносятся особые составы.
- Толщина покрытия. По этой величине наплавочные изделия делят на четыре вида – с очень толстым покрытием (отношение сечения покрытия к сечению сварочного стержня – более 1,8), с толстым (от 1,45 до 1,8), со средним (от 1,2 до 1,45) и с тонким (менее 1,2).
- По полярности и роду тока, используемого при наплавке металлов электродами (переменный и постоянный ток, прямая и обратная полярность).
- По разрешенным положениям наплавочного процесса в пространстве. В этом случае дуговая наплавка металла (ручная) может выполняться четырьмя видами изделий – для вертикального, горизонтального и нижнего положений, для любых положений, для нижнего в лодочку и обыкновенного нижнего, для всех за исключением вертикального сверху вниз.
Рекомендуем ознакомиться
Основными же параметрами, по которым делят сварочные стержни для наплавки изделий из металлов и стали, считается твердость получаемого наплавленного слоя и его химический состав. С этой точки зрения существует более 40 типов электродов, которые подразделяют на шесть больших категорий. О них рассказывается далее.
2 Категории сварочных стержней для наплавки
К первой категории (группе) относятся изделия, применение которых позволяет получать низколегированный низкоуглеродистый наплавленный слой с повышенной стойкостью против ударных нагрузок и трения. Ко второй – стержни, обеспечивающие аналогичный по свойствам слой, но уже для тех изделий из стали, которые работают при температурах от 600 до 6500 °С.
Третья категория электродов включает в себя изделия для получения легированного и углеродистого наплавленного слоя со стойкостью к ударным нагрузкам и повышенному абразивному изнашиванию. Стержни четвертой группы дают возможность получить такой же самый наплавленный металл на поверхности деталей, функционирующих при высоких температурах и давлениях.
Электроды пятой категории используются для получения высокостойкого слоя при трении и изнашивании, вызываемого эрозионно-коррозионными факторами (при температурах от 570 до 6000°), аустенитного высоколегированного металла.
Сварочные стержни шестой группы применяются для наплавки деталей из стали, на поверхности которой требуется высоколегированный дисперсноупрочняемый слой. Такие изделия обычно используются в сложнейших условиях, способствующих их деформированию (до 11000° температуры).
3 Технология наплавочных работ – некоторые важные особенности
Дуговая наплавка изделий из стали и черных металлов в силу своей универсальности применяется очень широко во многих ремонтных и восстановительных цехах промпредприятий.
Технология данного процесса имеет ряд особенностей и сложностей, но они не оказывают негативного влияния на качество наплавочной операции, если работы выполняются опытным сварщиком.
Наплавка производится при помощи стандартного оборудования, на котором выполняются сварочные электродуговые работы. При этом в зависимости от того, какое состояние и химсостав имеет наплавляемый и основной металл, технология может потребовать осуществления дополнительных процедур, в частности следующих:
- с целью обеспечения на поверхности наплавляемой стали каких-либо специальных эксплуатационных характеристик – термообработка;
- для улучшения и ускорения процесса – сопутствующий и предварительный нагрев заготовки.
Сварочные электроды первой категории (марки – ОЗН-300М и 400М, ЦНИИН-4, ОМГ-Н) рекомендованы для наплавки крестовин, осей, валов и иных элементов из низколегированных и углеродистых сплавов для железнодорожного и автотранспорта, второй (ОЗШ-2, 3, 7, 1, ЭН-60М, УОНИ-13/НЖ, ОЗИ-3) – для высадочных и молотовых, вырубных и отрезных штампов, также для компонентов станочного и металлургического оборудования, склонного к быстрому изнашиванию.
Третья категория наплавочных электродов (Т-620 и 590, ЭНУ-2, ВСН-6, ОЗН-7, 6 и 7М) используется для восстановления чугунных и стальных элементов строительной и металлургической техники, высокомарганцовистых и углеродистых сплавов, четвертая (ОЗИ-5 и 6) – для изготовления и ремонта инструментов для металлообработки, горячих и холодных сильнонагруженных штампов.
Электроды пятой группы (ЦН-12М и 6Л) технология наплавки рекомендует применять для восстановления энергетического оборудования и котлов, используемых при давлении не более 78 МПа, шестой (ОЗШ-6 и 8) – для обработки штамповочной и кузнечной оснастки, применяемой при высоких давлениях в термоусталостных условиях.
Для изготовления наплавочных стержней применяется особая проволока. Ее выпускают по Госстандарту 10543. Именно на такую проволоку наносят специальный слой, который и обеспечивает требуемые показатели наплавленного металла.
Кроме того, активно используется технология наплавки ленточными электродами – полосами размерами от 0,6х50 до 1х100 миллиметров. Теоретически можно делать и более крупные ленты, но их применение связано со значительным усложнением наплавочного процесса.
При наплавке ленточным электродом между ним и обрабатываемой деталью формируется электрическая дуга. На основной металл при постепенном расплавлении стержня наносится защитный 3–5-миллиметровый слой. В данном случае ванну и дугу требуется обязательно отделять флюсом от окружающего воздуха.
4 Тонкости процесса наплавки бронзы и цветных металлов
Нанесение на медные, стальные и бронзовые изделия расплавленного слоя бронзы либо меди выполняется:
- в среде защитного флюса графитовыми электродами;
- покрытыми стержнями при электродуговой сварке;
- вольфрамовыми наплавочными изделиями в газовой инертной атмосфере.
Основу электродовнзы либо м для дуговой сварки делают из броеди. Большое распространение получили стержни К-ЮО, покрытие которых состоит из 20 % кремнистой меди, 15 % плавикового и 12,5 % полевого шпата, 47,5 % ферромарганца. Замешивается весь состав на жидком стекле. Данные электроды используют для наплавления на сталь и медь бронзы или меди (получившийся слой затем проковывают). Обратите внимание – в данном случае металлы следует заранее подогреть примерно до 400 °С.
Наплавка бронзы выполняется и стержнями ЗТ, изготовленными из сплава БрКМцЗ-1. По своим параметрам и химическому составу наплавленный такими электродами металл практически идентичен кремнистой бронзе. Наплавочный процесс с применением ЗТ ведется только на обратной полярности и максимально короткой дугой.
При использовании угольных (графитовых) стержней применяют прутки (бронзовые, медные) в качестве присадки. На них наносят флюс (металлический магний 5 % + бура в порошке 95 %). Отметим, что этот вид наплавки характеризуется неудовлетворительным качеством. Используют его редко, выполняя (для улучшения результата) проковку шва с последующим водяным его охлаждением.
Вольфрамовые стержни для наплавки цветмета также применяют лишь в отдельных случаях. Операция проводится в аргоновой либо азотной атмосфере (газы должны иметь максимальную чистоту). Рекомендуется использовать аргон, так как в нем сварочная дуга обладает более высокой устойчивостью.
tutmet.ru
Электроды для наплавки стали
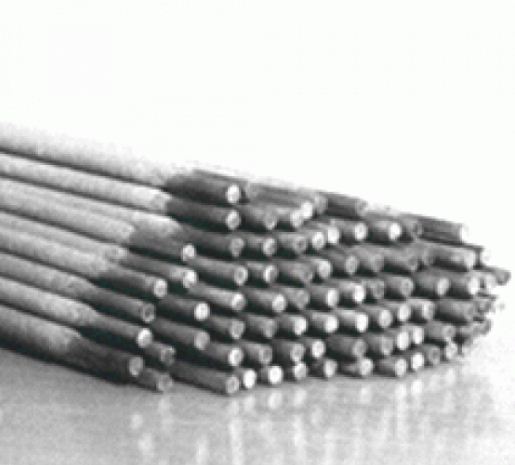
Как правило, сварщикам постоянно приходится иметь дело с различными марками стали. При этом некоей универсальной марки электродов, способных одинаково эффективно сваривать различные сорта стали не существует, и специалистам необходимо учитывать их технические характеристики при работе с тем или иным металлом.
Классификация электродов
Электроды, предназначенные для дуговой сварки сталей, подразделяются на несколько групп, имеющих определенные параметры, соотносящиеся с легирующими составляющими разных марок стали. Перечислим наиболее распространенные типы электродов для наплавки стали и представим их особенности.
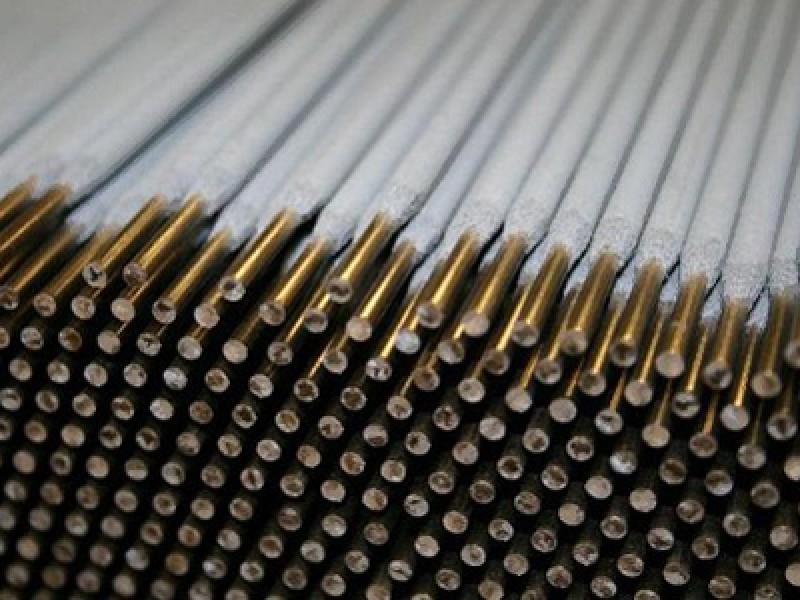
- Электроды для сварки низкоуглеродистых сталей с низким содержанием легирующих элементов. Подобные марки сталей отличаются высокой устойчивостью к абразивному износу и обладают стойкостью к ударным воздействиям.
- Электроды, предназначенные ля сварки среднеуглеродистых низколегированных сталей. Такие марки сталей обладают высокой устойчивостью к трению, а сварной шов способен выдерживать температуру до 650 градусов.
- Электроды для сваривания легированных и высоколегированных углеродистых сталей. Слой наплавленного при сварке металла обладает устойчивостью к абразивному воздействию и ударным нагрузкам.
- Электроды для сварки высокоуглеродистых легированных сталей, стойких к высокому давлению. Электроды этой группы применяются для сварки трубопроводов, работающих под высоким давлением. Наплав стального шва способен выдерживать температуры до 850 градусо
- В этой группе представлены электроды для сварки аустенитных (нержавеющих) высоколегированных марок стали. Характеристики расходных материалов позволяют получать нержавеющий шов при сварке.
- Электроды для работы с термоустойчивыми марками стали, способными выдерживать высокие температуры, превышающие 1000 градусов.
Все вышеперечисленные типы электродов предназначены как для промышленного, так и бытового применения.
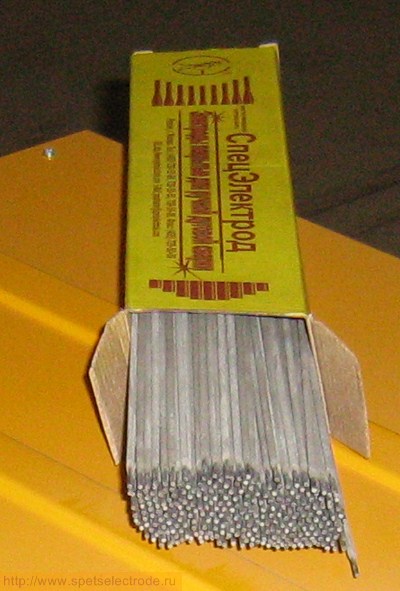
Состав и структура электродов
Для получения качеств, необходимых для эффективной сварки различных сортов сталей, стержни электродов разных типов подбираются в соответствии с марками свариваемых металлов.
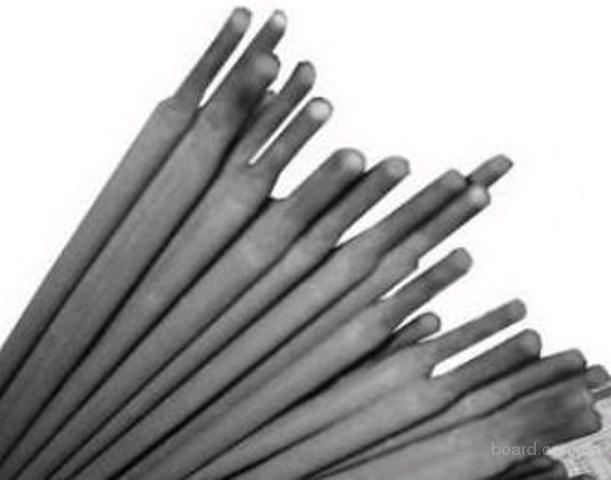
Состав и структура электродов во многом определяют эффективность дуговой наплавки и свойства наплавленного слоя металла.
Помимо элементов, составляющих основу свариваемого металла, состав расходных материалов дополняют присадки, улучшающие и облегчающие процесс сваривания. Так, электроды марки УОНИ 1345 содержат следующие элементы:
- марганец
- углерод
- кремний
- сера
- фосфор
А вот электроды марки ОЗН 6, предназначенные для сварки теплоустойчивых сталей, содержат в своем составе значительную долю титана, обеспечивающего надлежащее качество наплава.
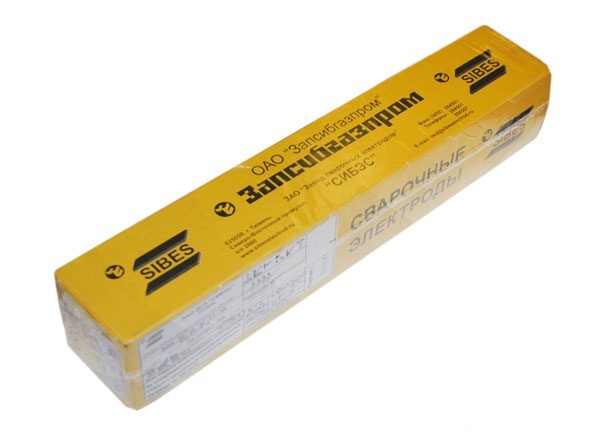
Марки электродов, предназначенных для наплавки сталей
Представим наиболее распространенные марки электродов для наплавки различных сталей.
- ОЗН 300М – используется для сварки узлов и деталей из низколегированных сталей, подверженных быстрому износу.
- УОН и 13НЖ 20Х13 – предназначены для наплавки термостойких сталей, выдерживающих температуру до 400 градусов.
- ОЗН 7 – электроды для сварки высоконагруженных конструкций и элементов.
- Т 590 – для сварки конструкций и деталей из высокоуглеродистых сталей, не подверженных высоким нагрузкам.
- ОЗИ 5 – наплавка изношенного слоя металлорежущих инструментов и пресс-форм горячей штамповки
- ОЗШ 6 – ремонт кузнечнопрессового оборудования, станков и узлов, работающих в условиях высоких нагрузок и экстремальных температур.
Выбор электродов для наплавки различных марок стали
При выборе расходного материала для сварки следует обязательно учитывать марку и структуру стали, которую предстоит сваривать, а также размеры заготовок. Так, для сварки крупных, толстых деталей необходимо выбрать электроды большего сечения, что позволит расплавить сталь на достаточную для надежного соединения глубину. Помимо того, электроды большего диаметра способны выдерживать высокую токовую нагрузку.
В настоящее время, помимо основных марок, представлено множество аналогов производства отечественных и зарубежных компаний. Для выбора оптимального варианта необходимо детально изучить свойств расходных материалов и, по возможности максимально, соотнести их со свойствами свариваемых металлов.
svarkagid.com
Электроды для дуговой наплавки легированных и углеродистых сталей
В большинстве случаев сварщикам приходится работать со сталями различных марок. Это могу быть электроды для сварки стали 40Х или другой марки, но в любом случае именно этот металл является одним из наиболее распространенных. Естественно, что большинство марок электродов для ручной дуговой сварки предназначены для разных сортов стали. Они разделяются на несколько групп, каждая из которых обладает своими особенностями, так как легирующие составляющие могут быть различными и каждая из них придает свою особенность:
- В первую группу можно причислить электроды для наплавки стали с низким уровнем легирования и низким содержанием углерода. Такие металлы хорошо проявляют себя в условиях высокого абразивного износа. Они хорошо переносят ударные нагрузки.
- Вторая группа включает в себя средне углеродистые стали и с низким содержанием легирующих элементов. Они хорошо переносят трение металла о металл и шов может применяться при температурных нагрузках до 650 градусов Цельсия.
- В третью группу входят электроды для высоколегированной стали, легированной и углеродистой. Наплавленный металл проявляет высокую стойкость в условиях абразивного износа. Хорошо переносит ударные нагрузки.
- В четвертую группу включаются электроды для углеродистых сталей, которые имеют высокий уровень легирования. Они могут переносить высокие давления, так что часто применяются для трубопроводов, и могут выдерживать температуры до 850 градусов Цельсия.
- В пятой группе находятся расходные материалы, предназначены для аустенитных металлов с высоким уровнем легирования. При работе с нержавеющими сталями сохраняются антикоррозионные свойства.
- В шестую группу входят электроды для теплоустойчивых сталей, которые могут выдерживать температуру до 1100 градусов Цельсия. Они сваривают высоколегированные разновидности, имеющие дисперсно-упрочняющие свойства.
Все эти разновидности используются как в промышленности, так и в быту, так как сам металл очень распространен, благодаря своим физическим свойствам. Стержень наплавочного материала стараются подбирать под тот сорт, который нужно будет сваривать. Таким образом, электроды для сварки низко углеродистых сталей сами будут иметь низкое содержание углерода.
Физико-химический состав 
Состав является главным параметром, который определяет, как электроды для дуговой наплавки стали будут вести себя во время рабочего процесса, а также какие свойства будет иметь наплавленный металл.
Зачастую это те же элементы, которые входят в основную заготовку, согласно номенклатуре ее сорта, а также несколько элементов, улучшающих свойства сваривания. К примеру, в состав УОНИ 13 45 входят следующие элементы:
Углерод | Марганец | Кремний | Сера | Фосфор |
0,09 | 0,57 | 0,23 | 0,025 | 0,027 |

Электроды для сварки УОНИ 13/45
В то же время в состав электродов ОЗН 6, которые рассчитаны на работу с теплостойкими металлами, входит обильное количество титана, что придает ему требуемые свойства:
Химический элемент | Относительное содержание,% |
Углерод | 1 |
Марганец | 2,6 |
Кремний | 3,7 |
Титан | 4,4 |

Электроды для сварки ОЗН 6
Технические характеристики 
Естественно, что характеристики наплавленной массы также будут сильно отличаться, в зависимости от состава. Здесь даже различные акценты параметров, в зависимости от сферы применения. На примере УОНИ 13 45 можно сравнить разнопрофильные материалы:
Температура испытаний | Сопротивление разрыву временное, Н/мм в квадрате | Удлинение относительное, % | Вязкость ударная, Дж/см в квадрате |
+ 20 °С | 410 | 22 | 147 |
Производительность наплавки, г/мин | Относительный выход наплавленного материала, % | Количество электродов на 1 кг наплавленного шва, кг |
21 | 93 | 1,65 |
Сварочный электрод ОЗЛ 6
Физические свойства | Значение |
Сопротивление временное, МПа | 610 |
Удлинение относительное, % | 33 |
Вязкость ударная, Дж/см2 | 150 |
Предел текучести, МПа | 410 |
Здесь видно, что некоторые параметры могут отличаться в 1,5 раза и выше.

Сварочный электрод ОЗЛ 6
Марки для сварки различных сталей 
Электроды для сварки разнородных сталей могут иметь следующие маркировки:
Марка | Ассортимент диаметров, мм | Положение сварки | Основное назначение |
ОЗН300М | 4, 5 | Нижнее | Для деталей с быстрым износом и сталей низкого легирования. Ими сваривают оси, оси, автосцепки, крестовины и прочие вещи. Твердость 270-360 НВ |
УОНи13/НЖ 20Х13 | 3, 4, 5 | Нижнее, наклонное | Наплавка деталей, которые могут выдерживать до 400 градусов Цельсия. Твердость 41,5-49,5 HRC |
ОЗН-7 | 4, 5 | Нижнее | Сварка сталей 110Г13Л, на которые возлагается высокая нагрузка. Твердость 56 HRC |
Т-590 | 4, 5 | Нижнее, наклонное | Сварка высоко углеродных изделий, которые не подвергаются тяжелым нагрузкам. Твердость 58-64 HRC |
ОЗИ-5 | 4, 5 | Нижнее | Наплавка металлорежущего инструмента и штампов горячей (до 800-8500С) штамповки. Твердость 63-67 HRC |
ОЗШ-6 | 2,5; 3; 4 | Нижнее | Сварка кузнечно-штамповой оснастки, деталей с быстрым износом и станочного оборудования, которое работает в тяжелых условиях. Может выдерживать до 950 градусов Цельсия. Твердость 52-60 HRC |
Обозначение и маркировка 
Электроды для сварки легированных сталей можно рассмотреть пример обозначений в каждом отдельном случае.
Электрод Э46 ЛЭЗ АНО21 УД Е 43 1(3) РЦ13
- Э46 – тип изделия, предназначенный для низколегированных и углеродистых сталей;
- ЛЭЗ АНО21 – марка изделия;
- У – используется для низколегированных и углеродистых сталей;
- Д – толстый слой покрытия;
- Е –электрод плавкий;
- 43 – максимальный предел прочности при растяжении растяжение – 430 Мпа;
- 1 – удлинение относительно — 20%;
- (3) – Ударная вязкость сохраняется при 20 градусах Цельсия;
- РЦ – покрытие смешанное рутилово-целлюлозное;
- 1 – для всех пространственных положений;
- 3 – предназначен для сварки постоянным током обратной полярности, а также переменным при холостом ходу в 50 В.

Внешний вид электродов марки АНО 21
Выбор 
Сварка толстого металла требует более толстых электродов, чтобы они смогли расплавить заготовку на должную глубину и выдержали токовую нагрузку, так что диаметр стоит подбирать не более 1 мм выше от толщины детали. Выбор марки требует детального изучения ее свойств, так как имеется несколько сотен разновидностей, каждая из которых предназначена для своего типа металла. Главное, чтобы стержень максимально совпадал по составу с заготовкой.
«Важно!При дефиците выбор стоит обратить внимание на зарубежные аналоги.»
Основные режимы и нюансы применения
Электроды для конструкционных сталей, одни из самых востребованных в производстве, применяются в следующих режимах:
Величина диаметра, мм | Сила тока, А | ||
В нижнем положении | В вертикальном положении | В потолочном положении | |
2 | 40…80 | 40…60 | 50…70 |
2,5 | 60…110 | 60…90 | 60…110 |
3 | 80…160 | 80…140 | 80…180 |
4 | 110…210 | 110…200 | 90…220 |
5 | 150…300 | 150…280 | 150…270 |
svarkaipayka.ru
Наплавка металла электродом – виды, технология и видео
Этот один из наиболее простых, и в то же время эффективных способов позволяет не только восстанавливать пригодность (работоспособность) деталей. Наплавкой металла электродом можно изменить форму образца, придать поверхностному слою иные (отличные от первоначальных) свойства, повысить его прочность и износостойкость. В чем заключается такая технология, каковы ее особенности и возможна ли реализация в быту – предмет рассмотрения в этой статье.
- Читателя вряд ли интересуют промышленные технологии, да еще и с использованием роботизированной техники, поэтому далее акцент – именно на методике наплавки металлов с помощью электродов на бытовом уровне, то есть своими руками.
- Часто в обиходе металлами называют и сплавы, например, сталь. И технологии, и отдельные детали (например, марка электрода) для каждого конкретного случая могут несколько отличаться. В одной статье невозможно охватить буквально все нюансы, поэтому перед тем, как приступить к наплавке, следует уточнить отдельные моменты, касающиеся используемых металлов. Все, что отмечено ниже – лишь рекомендации общего характера, так же, как и сам запрос, введенный в строку поисковика.
- Так как наплавка в чем-то схожа с известной всем сваркой, полезно будет почитать статьи по технологии последней применительно к различным металлам и сплавам – меди, алюминию, чугуну, нержавейке и ряду других, в зависимости от специфики предстоящей работы.
Терминология
- Наплавка – соединение разнородных металлов способом нанесения одного на поверхность другого.
- Присадочный металл – который наносится; основной – подвергающийся поверхностной обработке по такой методике.
Технология
Взаимное проникновение материалов происходит на молекулярном уровне. Для этого поверхностный слой основы разогревается до расплавления на небольшую глубину, а присадка – до перехода в жидкое состояние. Такое соединение называется гомогенным (от слова смешивание, в переводе с английского) и отличается повышенной надежностью, так как механическим путем разделить его на исходные «части» невозможно.
Преимуществами такой технологии являются возможности по регулированию толщины слоя (причем в значительных пределах) и нанесению присадки на детали (образцы) любой формы.
Основные правила наплава
- Глубина расплава верхнего слоя основы должна быть как можно меньше. Один из способов, позволяющих выполнить это условие – наклон электрода. Он делается в сторону, противоположную направлению его перемещения. Минимальное перемешивание разнородных металлов способствует снижению остаточных напряжений и исключает возможные деформации на отдельных участках.
- Избыток присадки осложняет дальнейшую обработку детали, требует больших трудозатрат и времени.
Технология наплава электродами
В обязательном порядке производится предварительная подготовка металла основы – зачистка + обезжиривание.
Наплавка электродами – наиболее распространенный способ получения гомогенного слоя. Благодаря простоте технологии считается основным для применения как на производстве, так и в домашних условиях. В зависимости от металла основы и преследуемых целей подбирается электрод с соответствующим наплавочным покрытием. В зависимости от его марки получаемый слой приобретает требуемые характеристики. Рисунок все хорошо поясняет.
Подключение схемы – прямое или обратное. Последний вариант используется чаще, как более удобный. Напряжение – постоянное, следовательно, «+» – на покрытом электроде.
Особенности технологии
- Толщина и форма слоя зависят от сечения электрода.
- Для обеспечения качественного наплава напряжение и сила тока дуги должны быть минимальными, а это требует точного согласования. С приобретением практического опыта выполнение данного условия особых сложностей не представляет.
Что нужно знать
- Повышение напряжения приводит к тому, что «валик» растет не в высоту, а в ширину. При этом длина дуги увеличивается.
- Для каждого вида электрода – своя особенность применения. Например, нужен ли предварительный нагрев основы? Для низколегированных сталей это часто не требуется. В каком режиме производится охлаждение? Какой выставить ток? Все технологические нюансы наплавки отражены в документации на конкретные электроды.
- Качество наплавки тем лучше, чем выше температура разогрева. Практически для всех сплавов и металлов ее минимальное значение + 300 ºС. В домашних условиях понадобится хотя бы небольшая термопечь (например, электрическая камерная).
Схемы наплавочных швов
Для поверхностей плоских
Узкими валиками. Они укладываются с перекрытием примерно в ⅓ треть.
Широкими. Электрод перемещается перпендикулярно оси наплава. Движения колебательные, их конфигурация (частота, амплитуда) выбирается исходя из габаритов основы.
Комбинированная методика. Наплав производится валиками узкими, но они располагаются на расстоянии, немного меньшем их ширины. После зачистки основы от шлаков в такие пустоты производится очередной наплав. Как результат – получение сплошного гомогенного слоя.
Рекомендация
Для получения более качественного покрытия основы другим металлом нужно начинать укладку очередного валика с противоположной стороны детали. Причем накладывать слои не последовательно, один за другим, а вразброс – то на одном участке, то на другом. Это предохранит основу от частичной деформации при перегреве.
Для цилиндров
Все три способа показаны на рисунке.
Есть еще одна технология наплавки металлов с помощью электродов – в защитной газовой среде. По своей сути она несложная. Трудность в другом – придется приобретать баллон и заправлять его соответствующим газом (аргоном, гелием или иным) в зависимости от вида присадочного металла. Такой вариант более подходит для небольшой мастерской. Приобретать же газовый баллон для разовой работы в домашних условиях вряд ли целесообразно. Поэтому данная технология в статье не рассматривается.
Давать рекомендации по выбору электродов и специфике их использования автор считает излишним. Во-первых, вся необходимая информация содержится на упаковке. Во-вторых, на все неясные вопросы ответит продавец. В специализированных точках менеджеры неплохо ориентируются в подобной тематике и могут дать дельный совет.
ismith.ru
Электроды |
Тип электрода по ГОСТ 10051-75 или тип наплавленного металла |
Диаметр, мм |
Положение наплавки |
Основное назначение. Твердость наплавленного металла |
группа 1 |
||||
ОЗН-300М |
11Г3С |
4,0;5,0 |
Нижнее |
Наплавка быстроизнашиваемых деталей из углеродистых и низколегированных сталей (например, валы, оси, автосцепки, крестовины, другие детали автомобильного и железнодорожного транспорта). НВ 270-360 |
ОЗН-400М |
15Г4С |
4,0;5,0 |
Нижнее |
Для наплавки быстроизнашиваемых деталей из углеродистых и низколегированных сталей (например, валы, оси, автосцепки, крестовины, другие детали авто-мобильного и железнодорожного транспорта). НВ 360-430 |
ОМГ-Н |
Э-65Х11Н3 |
4,0;5,0 |
Нижнее, наклонное |
Наплавка изношенных участков и заварка дефектов литья железнодорожных крестовин и других деталей из стали марки 110Г13Л. HRCэ 27-35 |
ЦНИИН-4 |
Э-65Х25Г13Н3 |
4,0 |
Нижнее |
Для наплавки изношенных участков и заварка дефектов литья железнодорожных крестовин и других деталей из стали типа 110Г13Л. HRCэ 25-37 |
группа 2 |
||||
ОЗШ-1 |
Э-16Г2ХМ |
3,0;4,0; 5,0 |
Все, кроме вертикального сверху вниз |
Для наплавки молотовых и высадочных штампов. НВ 320-365 |
УОНИ-13/НЖ 20Х13 |
Э-20Х13 |
3,0;4,0; 5,0 |
Нижнее, наклонное |
Наплавка штампов холодной и горячей (до 400оС) обрезки, быстроизнашиваемых деталей машин и оборудования. HRCэ 41,5-49,5 |
ОЗШ-3 |
Э-37Х9С2 |
2,5;3,0; 4,0;5,0 |
Нижнее, вертикальное |
Наплавка обрезных и вырубных штампов холодной и горячей (до 650оС) штамповки, быстроизнашиваемых деталей машин и оборудования. HRCэ 53-59 |
ОЗШ-7 |
5Х10С3М |
2,5;3,0; 4,0;5,0 |
Нижнее, вертикальное |
Для наплавки кузнечно-штамповой оснастки, работающей при температурах до 650оС. HRCэ і56 |
ОЗШ-2 |
10Х5М10В2Ф |
2,5;3,0; 4,0 |
Нижнее, наклонное |
Для наплавки штампов горячей штамповки. HRCэ і57 |
ЭН-60М |
Э-70Х3СМТ |
2,5;3,0; 4,0;5,0 |
Нижнее, полувертикальное |
Наплавка штампов всех типов, работающих при температуре до 400оС, быстроизнашиваемых деталей машин и оборудования. HRCэ 53-61 |
ОЗИ-3 |
Э-90Х4М4ВФ |
3,0;4,0; 5,0 |
Нижнее |
Наплавка штампов холодной и горячей (до 650оС) штамповки, быстроизнашиваемых деталей горно-металлургического и станочного оборудования. HRCэ 59-64 |
группа 3 |
||||
ОЗН-6 |
90Х4Г2С3Р |
4,0;5,0 |
Нижнее, вертикальное, ограниченно потолочное |
Для наплавки быстроизнашиваемых деталей горнодобывающих и строительных машин и металлургического оборудования. HRCэ і58 |
ОЗН-7 |
75Х5Г4С3РФ |
4,0;5,0 |
Нижнее |
Для наплавки быстроизнашивающихся деталей, преимущественно из стали 110Г13Л. HRCэ і56 |
ОЗН-7М |
75Х5Н2СФР |
4,0;5,0 |
Нижнее |
Наплавка быстроизнашиваемых деталей, преимущественно из стали 110Г13Л. HRCэ і56 |
ОЗН/ВСН-9 |
115Х17Н3Г2СРТ |
4,0;5,0 |
Нижнее |
Для наплавки деталей землеройных машин в условиях воздействия мерзлых грунтов. HRCэ і 46 |
ВСН-6 |
Э-110Х14В13Ф2 |
4,0;5,0 |
Нижнее |
Наплавка быстроизнашиваемых деталей из углеродистых и высокомарганцовистых сталей. HRCэ 51-56,5 |
ЭНУ-2 |
360Х15Г3Р |
4,0;5,0 |
Нижнее, наклонное |
Наплавка быстроизнашиваемых стальных и чугунных деталей (ударные нагрузки - умеренные). HRCэ і58 |
Т-590 |
Э-320Х25С2ГР |
4,0;5,0 |
Нижнее, наклонное |
Наплавка быстроизнашиваемых стальных и чугунных деталей машин (ударные нагрузки - минимальные). HRCэ 58-64 |
Т-620 |
Э-320Х23С2ГТР |
4,0;5,0 |
Нижнее, наклонное |
Наплавка быстроизнашиваемых стальных и чугунных деталей машин (ударные нагрузки - умеренные). HRCэ 56-63 |
группа 4 |
||||
ОЗИ-5 |
Э-10К18В11М10Х3СФ |
3,0;4,0; 5,0 |
Нижнее |
Для наплавки металлорежущего инструмента и штампов горячей (до 800-850оС) штамповки. HRCэ 63-67 |
ОЗИ-6 |
100Х4М8В2СФ |
2,5;3,0; 4,0;5,0 |
Нижнее, наклонное |
Наплавка при изготовлении металлорежущего инструмента, ремонте тяжелонагруженных штампов холодной и горячей (до 650оС) штамповки. HRCэ 59-64 |
группа 5 |
||||
ЦН-6Л |
Э-08Х17Н8С6Г |
4,0;5,0 |
Нижнее |
Наплавка уплотнительных поверхностей деталей арматуры котлов, работающих при температурах до 570оС и давлении до 78 МПа. HRCэ 29,5-39 |
ЦН-12М |
Э-13Х16Н8М5С5Г4Б |
4,0;5,0 |
Нижнее |
Наплавка уплотни-тельных поверхностей деталей арматуры энергетических установок, работающих при температуре до 6000С и высоких давлениях. HRCэ 39,5-51,5 |
группа 6 |
||||
ОЗШ-6 |
10Х33Н11М3СГ |
2,5;3,0; 4,0 |
Нижнее |
Наплавка кузнечноштамповой оснастки холодного и горячего деформирования металлов, быстроизнашиваемых деталей металлургического, станочного и другого оборудования, работающего в тяжелых условиях термической усталости (до 950оС) и больших давлений. HRCэ 52-60 |
ОЗШ-8 |
11Х31М3ГСЮФ |
3,0;4,0 |
Нижнее, наклонное |
Для наплавки кузнечноштамповой оснастки горячего деформирования металлов, работающих в сверхтяжелых условиях термической усталости (до 1100оС) и больших давлений. HRCэ 51-57 |
weldzone.info
Наплавочные электроды Т-590:характеристики,обозначение
Электроды наплавочные Т-590 используются для наплавки деталей, которые, в большинстве случаев, используются в условиях ремонта деталей абразивного изнашивания. Это хорошо подходит для материалов, на которые воздействуют умеренные ударные нагрузки. Они могут использоваться как для крупномасштабных работ, к примеру, для ремонта зубьев в ковшах экскаватора, изнашивающихся от контакта с песком, землей и прочими материалами, так и в более мелких масштабах, для ремонта небольшой техники. Также сюда можно отнести восстановление лап культиваторов, дисков, лемехов плугов, ножей в дорожных машинах, щеках дробилок и шнеков смесительных машин. Все это помогает избавиться от необходимости покупки новых деталей к ним, тогда как намного проще и дешевле восстановить их при помощи наплавочных электродов.

Наплавочные электроды Т-590
Преимущества и недостатки 
К преимуществам изделий можно отнести то, что они отлично восстанавливают износившиеся части рабочих машин, которые должны отвечать особым условиям твердости, сохраняя необходимые характеристики. Таким образом, даже после восстановления они будут иметь хорошие рабочие показатели, как это было до ремонта. При отсутствии термической обработки, материал шва получает высокую твердость HRC 58-64. Наличие легирующих элементов позволяет более точно подбирать электроды к материалам, на которые нужна наплавка. Благодаря всему этому увеличивается эксплуатационная эффективность и снижается время простоя при ремонте. Также сокращается необходимость в наличии запасных деталей на складе.
К недостаткам можно отнести отсутствие пластичности наплавленного материала. Также эти электроды являются узконаправленными и не могут применяться универсально для других целей. При наплавлении более двух слоев материала, появляется риск образования трещин, так что для последующей наплавки следует брать другие разновидности. Трещины могут оказать полезный эффект, так как снимают напряжение с определенных участков детали, а после образования трещины можно ее заварить.
Область применения 
Электроды для наплавки Т-590 используются в сфере ремонта. Они подходят для восстановления рабочей поверхности металлических изделий. В основном это такие отрасли промышленности как машиностроение, станкостроение, сельское хозяйство, различные отрасли производства. Они могут пригодиться не только на крупных и мелких предприятиях, но и в частной сфере. Электроды помогут восстановить истершуюся рабочую поверхность деталей, чтобы продлить срок ее службы, а такие вещи могут потребоваться во многих областях использования.
Технические характеристики 
Химический состав металла, входящего в электрод, %
Углерод | Кремний | Марганец | Хром | Бор | Сера | Фосфор |
не более | ||||||
2,9–3,5 | 2,–2,5 | 1,–1,5 | 22,–27, | 0,0–1,5 | 0,035 | 0,04 |
Твердость наплавленного металла
Производительность наплавки (при диаметре в 4 мм), г/мин | Расход на 1 кг наплавленного металла, кг |
30 | 1,4 |
Упаковочные данные
Толщина, мм | Длина, м | Количество электродов в одной пачке, шт. | Вес полной пачки, кг |
4 | 0,45 | 10 | 1 |
5 | 0,45 | 6 | 0,9 |
Особенности выбора режимов наплавки 
Чтобы процесс наплавки прошел правильно, и в итоге все получилось на высоком уровне, необходимо соблюдать правильные режимы проведения процедур. Перед самой сваркой будет полезно провести термообработку электродов, которая проводится в течение одного часа при температуре 300-350 градусов Цельсия.
Электроды наплавочные Т-590 можно использовать как при постоянном, так и при переменном токе. Постоянный ток можно применять любой полярности, а переменный необходимо получать от трансформатора, у которого напряжение холостого хода составляет 70 В.
С четом того, что данные электроды во всех своих разновидностях имеют одинаковый состав и механические свойства, а отличаются лишь диаметром, то и выбор режима будет зависеть преимущественно от силы тока для расплавки электрода. Практически все операции проводятся в нижнем положении, поэтому, данные указываются именно для такого типа работ. Для изделий толщиной 4 мм при наплавке следует подбирать силу тока от 200 до 220 А. Для электродов толщиной 5 мм сила тока должна лежать в пределах 250-270 А. При несоблюдении режима наплавленный материал может ненадежно держаться или проплавить саму основу, на которую он наносится.
Обозначение и расшифровка 
Т – изделие для теплоустойчивых легированных сталей;
590 – марка электрода, соответствует типу Э-320Х25С2ГР.
svarkaipayka.ru
Наплавочные электроды — studvesna73.ru
Электроды для наплавки
Общая краткая характеристика и каталог наплавочных электродов.
В группу электродов для наплавки входят марки, предназначенные для ручной дуговой наплавки поверхностных слоев с особыми свойствами (кроме марок для наплавки слоев из цветных металлов). Их изготавливают и поставляют в соответствии с требованиями ГОСТ 9466-75 и ГОСТ 10051-75. Для наплавочных работ в некоторых случаях также используют сварочные электроды, например, марки, предназначенные для сварки высоколегированных коррозионно -стойких, жаростойких и жаропрочных сталей.
Согласно ГОСТ 10051-75 электроды для наплавки поверхностных слоев по химическому составу наплавленного металла и твердости при нормальной температуре классифицированы на 44 типа (например, марки типа Э-16Г2ХМ, Э-110Х14В13Ф2, Э-13Х16Н8М5С5Г46). Наплавленный металл многих марок регламентируется техническими условиями предприятий-изготовителей.
В зависимости от принятой системы легирования и условий работы получаемого наплавленного металла электроды для наплавки (наплавочные элекироды) могут быть условно разделены на следующие 6 групп:
1-я группа. Марки электродов для наплавки, обеспечивающие получение низкоуглеродистого низколегированного наплавленного металла с высокой стойкостью в условиях трения металла о металл и ударных нагрузок (по назначению к этой группе относятся некоторые марки электродов 3-ей группы).
2-я группа. Марки, обеспечивающие получение среднеуглеродистого низколегированного наплавленного металла с высокой стойкостью в условиях трения металла о металл и ударных нагрузок при нормальной и повышенной температурах (до 600-650 гр С).
3-я группа. Марки наплавочных электродов, обеспечивающие получение углеродистого, легированного (или высоколегированного) наплавленного металла с высокой стойкостью в условиях абразивного изнашивания и ударных нагрузок
4-я группа. Электроды наплавочные, обеспечивающие получение углеродистого высоколегированного наплавленного металла с высокой стойкостью в условиях больших давлений и высоких температур (до 650-850 гр С).
5-я группа. Электроды, обеспечивающие получение высоколегированного аустенитного наплавленного метала с высокой стойкостью в условиях коррозионно-эрозионного изнашивания и трения металла о металл при повышенных температурах (до 570-600 гр С).
6-я группа. Марки электродов для наплавки, обеспечивающие получение дисперсноупрочняемого высоколегированного наплавленного металла с высокой стойкостью в тяжелых температурно-деформационных условиях (до 950-1100 гр С).
Необходимо отметить, что производство наплавочных работ требует применения специальной технологии, которая — в зависимости от химического состава и состояния основного и наплавляемого металлов — может включать обязательное выполнение таких операций, как предварительный и сопутствующий подогрев, термическую обработку для получения заданных эксплуатационных свойств наплавляемой поверхности.
Марки электродов для наплавки
В группу электродов для наплавки входят электроды, предназначенные для ручной дуговой наплавки поверхностных слоев с особыми свойствами (кроме электродов для наплавки слоев из цветных металлов). Электроды изготавливают в соответствии с ГОСТ 9466-75 и ГОСТ 10051-75. Для наплавочных работ в некоторых случаях также используют сварочные электроды, например, электроды, предназначенные для сварки высоколегированных коррозионно-стойких, жаростойких и жаропрочных сталей.
Согласно ГОСТ 10051-75 электроды для наплавки поверхностных слоев по химическому составу наплавленного металла и твердости при нормальной температуре классифицированы на 44 типа (например, электроды типа Э-16Г2ХМ, Э-110Х14В13Ф2, Э-13Х16Н8М5С5Г46). Наплавленный металл многих электродов регламентируется техническими условиями предприятий-изготовителей.
В зависимости от принятой системы легирования и условий работы получаемого наплавленного металла электроды для наплавки условно разделены на 6 групп:
- Электроды, обеспечивающие получение низкоуглеродистого низколегированного наплавленного металла с высокой стойкостью в условиях трения металла о металл и ударных нагрузок (по назначению к этой группе относятся некоторые марки электродов 3-ей группы).
- Электроды, обеспечивающие получение среднеуглеродистого низколегированного наплавленного металла с высокой стойкостью в условиях трения металла о металл и ударных нагрузок при нормальной и повышенной температурах (600-650 о С).
- Электроды, обеспечивающие получение углеродистого, легированного (или высоколегированного) наплавленного металла с высокой стойкостью в условиях абразивного изнашивания и ударных нагрузок.
- Электроды, обеспечивающие получение углеродистого высоколегированного наплавленного металла с высокой стойкостью в условиях больших давлений и высоких температур (650-850 о С).
- Электроды, обеспечивающие получение высоколегированного аустенитного наплавленного метала с высокой стойкостью в условиях коррозионно-эрозионного изнашивания и трения металла о металл при повышенных температурах (570-600 о С).
- Электроды, обеспечивающие получение дисперсноупрочняемого высоколегированного наплавленного металла с высокой стойкостью в тяжелых температурно-деформационных условиях (950-1100 гр С).
Выполнение наплавочных работ требует применения специальной технологии, которая (в зависимости от химического состава и состояния основного и наплавляемого металлов)- может включать обязательное выполнение таких операций, как предварительный и сопутствующий подогрев, термообработку для получения заданных эксплуатационных свойств наплавляемой поверхности.
Тип электрода по ГОСТ 10051-75 или тип наплавленного металла
Твердость наплавленного металла
Наплавка быстроизнашиваемых деталей из углеродистых и низколегированных сталей (например, валы, оси, автосцепки, крестовины, другие детали автомобильного и железнодорожного транспорта).
Для наплавки быстроизнашиваемых деталей из углеродистых и низколегированных сталей (например, валы, оси, автосцепки, крестовины, другие детали авто-мобильного и железнодорожного транспорта).
Наплавка изношенных участков и заварка дефектов литья железнодорожных крестовин и других деталей из стали марки 110Г13Л.
Главная » Информация » Электроды для наплавки: типы, требования ГОСТ
Типы металлических покрытых электродов для ручной дуговой наплавки поверхностных слоев с особыми свойствами устанавливаются ГОСТ 10051-75.
ГОСТ 10051-75 не распространяется на электроды для наплавки поверхностных слоев из цветных металлов и их сплавов
Технические условия на электроды для наплавки — по ГОСТ 9466-75.
Типы электродов для наплавки, твердость наплавленного металлапо ГОСТ 10051-75
ГОСТ 10543-98 устанавливает 44 типа покрытых металлических электродов для ручной дуговой наплавки (таблица 1).
Твердость наплавленного металла после наплавки, в зависимости от типа электродов, устанавливается без термической обработки и после термической обработки.
Таблица 1 — Типы электродов для наплавки по ГОСТ 10051-75
Тип электрода для наплавки
- В скобках — размеры применять ГОСТом не рекомендуется;
- Допускаются электроды номинальными диаметрами 3,15; 3,25; 6,3 и 12,5 мм;
- По соглашению — длина может быть иная, покрытие с конца электрода на длине l допускается не зачищать (торцы должны быть зачищены как контактные).
Классификация электродов для наплавки (по ГОСТ 9466-95)
Условное обозначение электродов для наплавки поверхностных слоев с особыми свойствами — Н (индекс в условном обозначении)
По толщине покрытия электроды для наплавки подразделяются:
- с тонким покрытием — М ( D/d ≤ 1,20)
- со средним покрытием — С (1,20
- с толстым покрытием — Д (1,45
- с особо толстым покрытием — Г ( D/d > 1,80),
где: D — диаметр покрытия, d — диаметр электрода, определяемый диаметром стержня.
По виду электродного покрытия наплавочные электроды подразделяются:
- с кислым покрытием — А ;
- с основным покрытием — Б ;
- с целлюлозным покрытием — Ц ;
- с рутиловым покрытием — Р ;
- с покрытием смешанного вида — соответствующее двойное условное обозначение;
- с прочими видами покрытий — П.
При наличии в составе покрытия железного порошка в количестве более 20 % к обозначению вида покрытия электродов добавляется буква Ж .
По допустимым пространственным положениям наплавки электроды подразделяются:
- для всех положений — 1;
- для всех положений, кроме вертикального сверху вниз — 2;
- для нижнего, горизонтального на вертикальной плоскости и вертикального снизу вверх — 3;
- для нижнего и нижнего в лодочку — 4
По роду и полярности применяемого при наплавке тока. по номинальному напряжению холостого хода используемого источника питания сварочной дуги переменного тока частотой 50 Гц электроды для наплавки подразделяются:
Цифрой 0 — электроды для наплавки только на постоянном токе обратной полярности.
Индексы характеристик наплавленного металла (два индекса):
- первый — средняя твердость наплавленного металла:
- 1 — твердость наплавленного металла обеспечивается без термической обработки после наплавки
- 2 — после термической обработки
Пример условного обозначения электродов для наплавки (на этикетках, в маркировке коробок, пачек и ящиков):
Электроды типа Э-11Г3 по ГОСТ 10051-75, марки ОЗН-300У. диаметром 4,0 мм, для наплавки поверхностных слоев с особыми свойствами Н. с толстым покрытием Д. обеспечивающие среднюю твердость 300 HB ( HRC э 33;
300HV) — 300/33. без термической обработки после наплавки — 1. с основным покрытием Б. для наплавки в нижнем положении 4 на постоянном токе обратной полярности (0 ):
Для формирования на изделиях из металлов и стали особого слоя с заданными механическими значениями используются электроды для наплавки. Они чаще всего необходимы для восстановления элементов разнообразных агрегатов и механизмов.
Содержание
- Основные сведения о классификации наплавочных электродов
- Категории сварочных стержней для наплавки
- Технология наплавочных работ – некоторые важные особенности
- Тонкости процесса наплавки бронзы и цветных металлов
1 Основные сведения о классификации наплавочных электродов
Имеется два Госстандарта – 9466 и 10051, которые содержат техусловия и рассказывают о типах, на которые подразделяют электроды для наплавки. Интересующие нас изделия принято подразделять на отдельные группы по следующим показателям:
- Вид покрытия. Ручная дуговая наплавка производится электродами с целлюлозным, основным, кислым, смешанным или рутиловым покрытием. Также существуют сварочные (наплавочные) стержни, на которые наносятся особые составы.
- Толщина покрытия. По этой величине наплавочные изделия делят на четыре вида – с очень толстым покрытием (отношение сечения покрытия к сечению сварочного стержня – более 1,8), с толстым (от 1,45 до 1,8), со средним (от 1,2 до 1,45) и с тонким (менее 1,2).
- По полярности и роду тока, используемого при наплавке металлов электродами (переменный и постоянный ток, прямая и обратная полярность).
- По разрешенным положениям наплавочного процесса в пространстве. В этом случае дуговая наплавка металла (ручная) может выполняться четырьмя видами изделий – для вертикального, горизонтального и нижнего положений, для любых положений, для нижнего в лодочку и обыкновенного нижнего, для всех за исключением вертикального сверху вниз.
Основными же параметрами, по которым делят сварочные стержни для наплавки изделий из металлов и стали, считается твердость получаемого наплавленного слоя и его химический состав. С этой точки зрения существует более 40 типов электродов, которые подразделяют на шесть больших категорий. О них рассказывается далее.
2 Категории сварочных стержней для наплавки
К первой категории (группе) относятся изделия, применение которых позволяет получать низколегированный низкоуглеродистый наплавленный слой с повышенной стойкостью против ударных нагрузок и трения. Ко второй – стержни, обеспечивающие аналогичный по свойствам слой, но уже для тех изделий из стали, которые работают при температурах от 600 до 6500 °С.
Третья категория электродов включает в себя изделия для получения легированного и углеродистого наплавленного слоя со стойкостью к ударным нагрузкам и повышенному абразивному изнашиванию. Стержни четвертой группы дают возможность получить такой же самый наплавленный металл на поверхности деталей, функционирующих при высоких температурах и давлениях.
Электроды пятой категории используются для получения высокостойкого слоя при трении и изнашивании, вызываемого эрозионно-коррозионными факторами (при температурах от 570 до 6000°), аустенитного высоколегированного металла.
Сварочные стержни шестой группы применяются для наплавки деталей из стали, на поверхности которой требуется высоколегированный дисперсноупрочняемый слой. Такие изделия обычно используются в сложнейших условиях, способствующих их деформированию (до 11000° температуры).
3 Технология наплавочных работ – некоторые важные особенности
Дуговая наплавка изделий из стали и черных металлов в силу своей универсальности применяется очень широко во многих ремонтных и восстановительных цехах промпредприятий.
Технология данного процесса имеет ряд особенностей и сложностей, но они не оказывают негативного влияния на качество наплавочной операции, если работы выполняются опытным сварщиком.
Наплавка производится при помощи стандартного оборудования, на котором выполняются сварочные электродуговые работы. При этом в зависимости от того, какое состояние и химсостав имеет наплавляемый и основной металл, технология может потребовать осуществления дополнительных процедур, в частности следующих:
- с целью обеспечения на поверхности наплавляемой стали каких-либо специальных эксплуатационных характеристик – термообработка;
- для улучшения и ускорения процесса – сопутствующий и предварительный нагрев заготовки.
Сварочные электроды первой категории (марки – ОЗН-300М и 400М, ЦНИИН-4, ОМГ-Н) рекомендованы для наплавки крестовин, осей, валов и иных элементов из низколегированных и углеродистых сплавов для железнодорожного и автотранспорта, второй (ОЗШ-2, 3, 7, 1, ЭН-60М, УОНИ-13/НЖ, ОЗИ-3) – для высадочных и молотовых, вырубных и отрезных штампов, также для компонентов станочного и металлургического оборудования, склонного к быстрому изнашиванию.
Третья категория наплавочных электродов (Т-620 и 590, ЭНУ-2, ВСН-6, ОЗН-7, 6 и 7М) используется для восстановления чугунных и стальных элементов строительной и металлургической техники, высокомарганцовистых и углеродистых сплавов, четвертая (ОЗИ-5 и 6) – для изготовления и ремонта инструментов для металлообработки, горячих и холодных сильнонагруженных штампов.
Электроды пятой группы (ЦН-12М и 6Л) технология наплавки рекомендует применять для восстановления энергетического оборудования и котлов, используемых при давлении не более 78 МПа, шестой (ОЗШ-6 и 8) – для обработки штамповочной и кузнечной оснастки, применяемой при высоких давлениях в термоусталостных условиях.
Для изготовления наплавочных стержней применяется особая проволока. Ее выпускают по Госстандарту 10543. Именно на такую проволоку наносят специальный слой, который и обеспечивает требуемые показатели наплавленного металла.
Кроме того, активно используется технология наплавки ленточными электродами – полосами размерами от 0,6х50 до 1х100 миллиметров. Теоретически можно делать и более крупные ленты, но их применение связано со значительным усложнением наплавочного процесса.
При наплавке ленточным электродом между ним и обрабатываемой деталью формируется электрическая дуга. На основной металл при постепенном расплавлении стержня наносится защитный 3–5-миллиметровый слой. В данном случае ванну и дугу требуется обязательно отделять флюсом от окружающего воздуха.
4 Тонкости процесса наплавки бронзы и цветных металлов
Нанесение на медные, стальные и бронзовые изделия расплавленного слоя бронзы либо меди выполняется:
- в среде защитного флюса графитовыми электродами;
- покрытыми стержнями при электродуговой сварке;
- вольфрамовыми наплавочными изделиями в газовой инертной атмосфере.
Основу электродовнзы либо м для дуговой сварки делают из броеди. Большое распространение получили стержни К-ЮО, покрытие которых состоит из 20 % кремнистой меди, 15 % плавикового и 12,5 % полевого шпата, 47,5 % ферромарганца. Замешивается весь состав на жидком стекле. Данные электроды используют для наплавления на сталь и медь бронзы или меди (получившийся слой затем проковывают). Обратите внимание – в данном случае металлы следует заранее подогреть примерно до 400 °С.
Наплавка бронзы выполняется и стержнями ЗТ, изготовленными из сплава БрКМцЗ-1. По своим параметрам и химическому составу наплавленный такими электродами металл практически идентичен кремнистой бронзе. Наплавочный процесс с применением ЗТ ведется только на обратной полярности и максимально короткой дугой.
При использовании угольных (графитовых) стержней применяют прутки (бронзовые, медные) в качестве присадки. На них наносят флюс (металлический магний 5 % + бура в порошке 95 %). Отметим, что этот вид наплавки характеризуется неудовлетворительным качеством. Используют его редко, выполняя (для улучшения результата) проковку шва с последующим водяным его охлаждением.
Вольфрамовые стержни для наплавки цветмета также применяют лишь в отдельных случаях. Операция проводится в аргоновой либо азотной атмосфере (газы должны иметь максимальную чистоту). Рекомендуется использовать аргон, так как в нем сварочная дуга обладает более высокой устойчивостью.
Трубогиб ручной ТР и другие марки – рассматриваем типы этого приспособления
В этой статье мы рассмотрим различные механические трубогибы, которые можно использовать руками, применяя только мускульную.
Виды сварочных аппаратов – обзор популярных моделей
Статья подскажет вам, какое специальное оборудование имеет смысл приобрести, если вы планируете производить работы по.
Ленточнопильный станок (ленточные пилы)
Цветные металлы и сплавы
Конструкционные стали и сплавы
Технологию наплавки металла часто используют для восстановления изношенных деталей.
На поверхность детали наносится слой металла с помощью сварки.
В результате выходит деталь, которая прослужит ещё несколько времени.
Электрод для наплавки выбирают в зависимости от толщины планируемого слоя.
Для материала до 1,5 мм сварщики используют электроды, диаметром 3 мм, для более толстого материала используют электроды диаметром 4-6 мм.
При этом используется сила тока 11-12 А/мм2, чтобы не повредить поверхность детали.
При выборе электродов для тех или иных металлов сначала должно быть сформировано представление — с каким металлом будет работать сварщик, а именно, необходимо знать какое содержание углерода будет в составе этого металла (менее 0.4% или более)
Электроды для наплавки (наплавочные электроды) могут быть условно разделены на 6 групп:
1) Марки, обеспечивающие получение низкоуглеродистого низколегированного наплавленного металла с высокой стойкостью в условиях трения металла о металл и ударных нагрузок (по назначению к этой группе относятся некоторые марки электродов 3-ей группы).
2) Марки электродов, обеспечивающие получение среднеуглеродистого низколегированного наплавленного металла с высокой стойкостью в условиях трения металла о металл и ударных нагрузок при нормальной и повышенной температурах (до 600-650 гр С).
3) Марки электродов, обеспечивающие получение углеродистого, легированного (или высоколегированного) наплавленного металла с высокой стойкостью в условиях абразивного изнашивания и ударных нагрузок
4) Электроды, обеспечивающие получение углеродистого высоколегированного наплавленного металла с высокой стойкостью в условиях больших давлений и высоких температур (до 650-850 гр С).
5) Марки, обеспечивающие получение высоколегированного аустенитного наплавленного метала с высокой стойкостью в условиях коррозионно-эрозионного изнашивания и трения металла о металл при повышенных температурах (до 570-600 гр С).
6) Электроды, обеспечивающие получение дисперсноупрочняемого высоколегированного наплавленного металла с высокой стойкостью в тяжелых температурно-деформационных условиях (до 950-1100 гр С).
К наплавочным электродам относятся:
ESAB OK NiCrMo-5 (ранее OK 92.35)
ESAB OK 68.82ESAB OK Weartrode 62 (ранее OK 84.84)ESAB OK Weartrode 60 T (ранее OK 84.78)ESAB OK Weartrode 55 HD (ранее OK 84.58)ESAB OK 68.81ESAB OK 67.45ESAB OK Weartrode 55ESAB OK Weartrode 50 TESAB OK Weartrode 45ESAB OK Weartrode 40ESAB OK Weartrode 35ESAB OK 14MnNi (ранее OK 86.28)ESAB OK 13Mn (ранее OK 86.08)ESAB OK Tooltrode 60 (ранее OK 85.65)ESAB OK Tooltrode 50 (ранее OK 85.58)ESAB OK Weartrode 65 T (ранее OK 84.80)ESAB OK Weartrode 60 (ранее OK 83.65)ESAB Булат-1ESAB OK Weartrode 50 (ранее OK 83.50)ESAB OK Weartrode 30 HD (ранее OK 83.29)ESAB OK Weartrode 30 (ранее OK 83.28)ESAB OK 67.43ESAB OK 84.52 (Снят с производства)ESAB OK 84.42 (Снят с производства)
studvesna73.ru