Технологический процесс хромирования. Как металл хромировать
Технологический процесс хромирования
Технологические операции при ремонте (восстановлении) деталей хромированием выполняют в следующей последовательности.
Механическая обработка. Поверхности деталей, подлежащие хромированию, шлифуют до выведения следов износа и получения необходимой геометрической формы.
Промывка деталей в органических растворителях и протирка ветошью. В качестве растворителей применяют бензин, керосин, трихлорэтан, бензол и др.
Монтаж деталей на подвеску. Необходимо следить, чтобы детали одинаково отстояли от поверхности анода. Ванну следует загружать однородными деталями, укрепленными на одинаковых подвесках. Подвески и контакты должны быть изготовлены из одинаковых материалов. Контактные крючки рекомендуется изготавливать из бронзы и меди. В качестве материала для подвесок, применяют сталь, сечения подвесок рассчитывают, исходя из плотности тока 0,7… 1,0 А/мм2. Ежедневно аноды очищают от окислов и налета электролита.
Обезжиривание. Рекомендуется применять электролитическое обезжиривание в растворе следующего состава: едкий натр (NaOH)—30… 50 г/л; кальцинированная сода (iNa2C03)—25…30 г/л и жидкое стекло (Na2Si03) — 10 … 20 г/л.
Температура электролита — 60… 70°, плотность тока — 5….15 А/дм2. Время выдержки на катоде — 2… 3 мин, а на аноде — 1…2 мин. После обезжиривания детали сначала промывают горячей водой (60… 80°), а затем холодной. Обезжиривание считается законченным, если после промывки вода равномерно смачивает поверхность. После обезжиривания производится изоляция1 поверхностей, не подлежащих хромированию. Для изоляции можно применять перхлорвиниловый лак, лак АК-20, целлулоид,, винипласт, плексиглас, хлорвиниловые трубки или хлорвиниловую» изоляционную ленту.
Декапирование — это процесс обработки деталей в хромовом* электролите, состоящем из 100 г хромового ангидрида (СгОз) и 2…3 г серной кислоты (H&SO4) на 1 л воды.
Декапирование (травление) стальных деталей проводят в течение 30… 90 с при плотности тока 25… 40 А/дм2. А для деталей из серого чугуна лучшие результаты, в смысле прочности сцепления, достигаются при плотности тока 20… 25 А/дм2 и продолжителыюсти декапирования 25… 30 сек. Температура электролита во всех случаях должна быть 55… 60 °С.
Процесс хромирования. После анодного декапирования детали загружают в ванну хромирования и прогревают их при выключенном токе в течение 5… 6 мин, а затем дают полный ток согласно режиму хромирования. При хромировании чугунных деталей вначале в течение 3… 5 мин дают «толчок тока» при плотности, в 2…2,5 раза превышающей выбранную по режиму. Колебания температуры электролита могут быть в пределах ±1 °С. Не допускаются перерывы тока в процессе электролиза, так как они вызывают отслаивание хромового покрытия. Продолжить процесс после перерыва тока можно, если хромируемую поверхность подвергнуть анодному травлению при плотности тока 25… 30 А/дм2 в течение 30… 40 с, а затем изменить направление тока. В этом случае осаждение хрома следует начинать при катодной плотности тока 20… 25 А/дм2 и постепенно увеличивать до нормальной.
Аноды для хромирования изготавливают из чистого свинца или сплава, состоящего из 92…93% свинца и 7… 8% сурьмы. Аноды из чистого свинца в большей степени покрываются нерастворимой и непроводящей пленкой хромовокислого свинца, чем аноды из сплава свинца и сурьмы. В большинстве случаев аноды изготавливают плоскими и цилиндрическими. При хромировании деталей сложной конфигурации очертания анода определяются формой катода. Расстояние между анодами и деталями рекомендуется делать 30… 35 мм, но не более 50 мм. Расстояние деталей от днища ванны должно составлять не менее 100… 150 мм, а от верхнего уровня электролита — не менее 50… 80 мм. Уровень электролита должен быть ниже верхних кромок ванны на 100…150 мм. При завешивании деталей в ванну необходимо, чтобы все участки анодов были одинаково удалены от противоположных участков катода. При этом толщина слоя хрома откладывается равномерно по всей поверхности детали.
Глубина погружения анодов и деталей (катодов) в ванну должна быть одинаковой, так как при различной глубине на краях хромируемых деталей образуются утолщения, искажающие форму. Скорость осаждения слоя хрома при плотности тока 40… 100 А/дм2 составляет 0,03… 0,06 мм/ч.
По окончании процесса хромирования детали выгружают из ванны и вместе с подвесками промывают в холодной воде (в сборнике электролита) 15… 20 с. Окончательно детали моют в холодной проточной воде.
Обработка после покрытия. Промытые и очищенные от изоляции детали иногда подвергают термической обработке при температуре 150—200°С в течение 2…3 ч, а затем механической.
Для шлифования применяют круги мягкие или средней твердости с размером зерна от 60 до 120. Шлифование ведут при интенсивном охлаждении жидкостью и при скорости круга 20…30.м/с и выше. Скорость вращения детали—12…20 м/мин.
Режимы электролиза. Процесс осаждения хрома и свойства хромовых покрытий зависят от режима, при котором осаждается хром на поверхности металла, т. е. от катодной плотности тока и температуры электролита. Наиболее ясное представление о примерных границах режимов электролиза, обеспечивающих получение серого, блестящего и молочного осадков хрома, дает диаграмма плотности тока и температуры (DK—t), изображенная на рисунке 19.
Серый осадок хрома появляется на катоде при низких температурах электролиза (35…50 °С) и широком диапазоне плотностей тока. Осадки блестящего* хрома обладают высокой твердостью (6000… 9000 Н/мм2), высокой износостойкостью и меньшей хрупкостью.
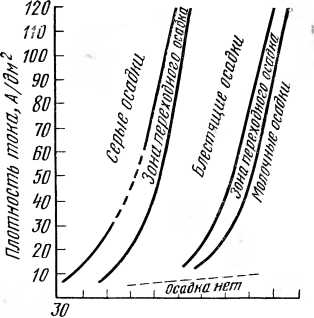
Молочный хром получается при более высоких температурах, электролита (выше 70 °С) и широком интервале плотностей тока. Молочные осадки отличаются пониженной твердостью (4400..-6000 Н/мм2), пластичностью и повышенной коррозионной стойкостью.
Пористое хромирование. Пористое хромирование применяется при ремонте деталей, работающих на трение в паре с различными металлами и сплавами при высоких удельных давлениях и окружных скоростях или при повышенных температурах. К таким деталям относятся гильзы цилиндров двигателей внутреннего сгорания, коленчатые валы и др.
Пористые хромовые покрытия можно получать механическим,, химическим и электрохимическим способами.
При механическом способе на поверхность детали до хромирования наносят углубления в виде пор или каналов. Такую подготовку обеспечивают накаткой специальным роликом, дробеструйной обработкой и другими способами. После хромирования воспроизводятся неровности, полученные при подготовке.
Химическим способом получают пористость путем травления поверхности в соляной кислоте.
Наибольшее распространение получил электрохимический способ получения пористого хрома. Этот способ заключается в анодной обработке хромированных деталей в электролите того же состава. В зависимости от режимов хромирования пористость хромовых покрытий бывает двух типов — канальчатая и точечная.. При ремонте гильз цилиндров, втулок, коленчатых валов и подобных им деталей применяется канальчатый тип пористости. Такук> пористость и наименьший износ в условиях трения можно получить при хромировании в электролите, состоящем из 250 г Сг03 и 2,5 г h3S04 на 1 л воды, при температуре электролита ¦60+1 °С и катодной плотности тока 55… 60 А/дм2. Травление ведут при плотности анодного тока 35 …45 А/дм2 в течение 8 мин в том же электролите.
Точечная пористость образуется при хромировании в универсальном электролите при плотности тока 45… 55 А/дм2 и температуре 50… 55 °С. Анодную обработку проводят так же, как и при канальчатой пористости, т. е. при плотности тока 35… 45 А/дм2 в течение 8 мин.
Хромирование в саморегулирующемся электролите. В последнее время разработан новый хромовый электролит, называемый скоростным саморегулирующимся, его состав: хромовый’ ангидрид — 225… 300 г/л, кремнефтористый калий — 20 г/л и сернокислый стронций — 6 г/л.
В таком электролите выход по току при хромировании составляет 17… 22%. Саморегулирующимся он назван потому, что при электролизе в нем автоматически поддерживается необходимая концентрация анионов, вводимых в хромовый электролит. Это происходит в результате избыточного количества труднорастворимых солей кремнефтористого калия и сернокислого стронция, растворимость которых изменяется в зависимости от концентрации хромового ангидрида и температуры электролита.
Чтобы получить износостойкое покрытие в саморегулирующемся электролите, рекомендуют соблюдать следующие режимы хромирования: плотность тока 50… 100 А/дм2, температура электролита 45… 55°С. Молочные осадки можно получить при температуре электролита 55… 70 °С и плотности тока 20… 35 А/дм2. Микротвердость покрытий из саморегулирующегося электролита составляет 3000… 13 000 Н/мм2.
Недостаток такого электролита — сильное взаимодействие его со сталью и другими металлами, в результате чего происходит растравливание обрабатываемых поверхностей. Поэтому загружать детали в ванну необходимо только при включенном токе. Аноды для хромирования в саморегулирующемся электролите рекомендуется применять из сплава: 90% свинца и 10% гост олово. Чтобы приготовить саморегулирующийся электролит, в ванне хромирования растворяют нужное количество хромового ангидрида и доливают воду до рабочего уровня. Предварительно хромовый ангидрид подвергают анализу на содержание серной кислоты, которую удаляют из электролита путем добавления в него углекислого бария или стронция. На 1 г серной кислоты вводят 2,2… 2,3 г углекислого бария или 1,53 г углекислого стронция. После осаждения серной кислоты в электролит вводят нужное количество сернокислого стронция и кремнефтористого калия и нагревают до температуры 50…60°С. Нагревание длится 15… 16ч при периодическом перемешивании через каждые 2… 3 ч. После этого электролит готов к эксплуатации.
Корректируют электролит путем систематического добавления хромового ангидрида. Вместе с хромовым ангидридом вводят углекислый стронций. Кремнефторид калия и сернокислый стронций в количестве 1 г/л добавляют, когда поверхность отхромированных деталей приближается к 1 м2.
Контроль хромовых покрытий. В производственных условиях качество покрытий следует проверять внешним осмотром и замером размеров хромированных поверхностей. При внешнем осмотре необходимо обращать внимание на блеск, отслоение и плотность осадка, равномерность и отсутствие шелушения и другие видимые дефекты. Дефекты покрытий получаются в результате неисправностей в работе ванн хромирования, например отслаивание покрытия возникает в результате недостаточного обезжиривания и декапирования, а также при наличии перерывов тока в процессе хромирования. Шелушение осадков появляется при недостаточном контакте детали с подвеской или при повышенной плотности тока. Неравномерное покрытие может быть при образовании пленки хроматов свинца на анодах, недостатке серной кислоты, избытке трехвалентного хрома. Во избежание перечисленных выше дефектов, необходимо откорректировать электролит и устранить другие неполадки в работе ванн хромирования.
Оборудование. Схема расположения оборудования участка восстановления деталей хромированием приведена на рисунке 20.
Источники тока — выпрямители с напряжением 12 В ВАКГ-12/6-3000, ВАГГ-12/600М, ВАС-600/300 и другие, а также низковольтные генераторы АНД 500/250, 750/375, 1000/500, 1500/750. Ванны для гальванического участка изготавливают из листовой стали толщиной 4… 5 мм. Облицовка для ванн промывки и обезжиривания не требуется. Внутреннюю поверхность ванны хромирования облицовывают свинцом.
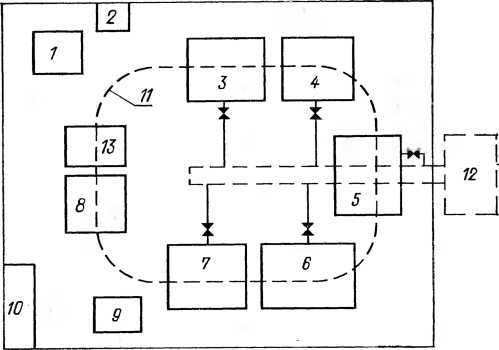
Себестоимость восстановления 1 дм2 поверхности хромированием в универсальном электролите при толщине покрытия 0,1 мм ориентировочно составляет 44,8 коп., 0,2 мм — 52,0 коп., 0,3 мм—-58,6 коп.
Электролитическое железо имеет светло-серый цвет, обладает достаточно высокой твердостью и износостойкостью. Химический состав электролитического железа зависит от состава исходных материалов, используемых при электролизе.
При обычном осаждении с применением стальных растворимых анодов содержание примесей в покрытиях находится в пределах: 0,035 …0,06% С; 0,03 …0,05% S; 0,05 …0,01% Р, 0,0009… 0,023% Si; до 0,01% Мп.
В электролитических осадках железа имеются также примеси таких металлов, как Mg, Со, Ni и другие, обусловленные содержанием этих металлов в анодах и электролитах. Кроме этого, электролитическое железо содержит значительное количество водорода, выделяющегося на катоде вместе с железом. Атомный вес железа 55,85 г. Электрохимический эквивалент 1,042 г/А-ч.
Составы электролитов. На ремонтных предприятиях наибольшее распространение для железнения получили горячие хлористые электролиты, состоящие из двух компонентов: хлористого железа и соляной кислоты. В ремонтной практике чаще всего применяют четыре вида хлористых электролитов, отличающихся концентрацией железа.
Малоконцентрированный электролит содержит 200 …250 г/л хлористого железа (FeCl2-4h30). При температуре 60… 80 °С и плотности тока 30… 50 А/дм2 электролит обеспечивает получение плотных, гладких мелкозернистых осадков железа с твердостью 4500… 6500 Н/мм2, толщиной 1,0… 1,5 мм. Выход железа по току составляет 85… 95%. Скорость осаждения железа равна 0,4… 0,5 мм/ч на сторону. Электролит допускает колебание кислотности при электролизе от 0,8 до 1,5 г/л, которое незначительно отражается на механических свойствах покрытий. Недостатком этого электролита является постепенное увеличение концентрации железа в процессе электролиза в результате несоответствия между скоростью растворения анодов и скоростью осаждения железа на катоде, что вызывает затруднения при обслуживании ванны железнения.
Среднеконцентрированный электролит оптимальной концентрации содержит 300…350 г/л хлористого железа (FeCl2-4h30). Катодный выход железа из этого электролита при температуре 75 °С и плотности тока 40 А/дм2 составляет 96%. В этом электролите анодные и катодные выходы железа по току становятся примерно одинаковыми, концентрация железа остается почти неизменной и электролит длительное время по концентрации железа не требует корректировки. В настоящее время этот электролит нашел широкое применение на ремонтных предприятиях.
Среднеконцентрированный электролит содержит 400 …450 г/л хлористого железа. Электролит используется для восстановления деталей, имеющих достаточно высокие износы и сравнительно невысокую твердость. Электролит дает возможность получать гладкие плотные покрытия толщиной до 2 мм и твердостью 2500… 4500 Н/мм2. Электролит также находит применение для восстановления посадочных отверстий в корпусных, деталях.
Высококонцентрированный электролит содержит 600… 680 г/л хлористого железа. Электролит при температуре 95… 105°С и плотности тока 5…20 А/дм2 позволяет получать мягкие (120… 200 кг/мм2), вязкие покрытия толщиной 3… 5 мм..
Электролиты более высокой концентрации рекомендуется применять в случаях, когда к восстанавливаемым деталям не предъявляются повышенные требования по твердости рабочих поверхностей.
За последнее время разработаны холодные электролиты, позволяющие применять более высокие плотности тока и обеспечивающие высокую производительность процесса.
Хлористый марганец МпС12-4Н20 Аскорбиновая кислота Двухлористое железо FeCl2-4h30 Хлористый марганец МпС12-4Н20 Хлористый калий КС1 (или) NaCl Аскорбиновая кислота Двухлористое железо FeCl2*4h30 Сернокислое железо FeS04*7h30 Двухлористое железо FeCl2-4h30 Метилсульфатное железо Fe (Ch4OSO3) 2*4Н20
Хлористые электролиты без добавок, приведенные в таблице* позволяют получать качественные износостойкие покрытия толщиной 0,6… 1,0 мм и обеспечивать восстановление широкой номенклатуры изношенных деталей до нормальной работоспособности и номинальных размеров. Электролит, в состав которого» входят двухлористое железо и йодистый калий, обеспечивает по-пучение качественных осадков, железа’ при условии применения асимметричного переменного тока.
Присутствие аскорбиновой кислоты в электролитах позволяет вести электролиз в широких пределах значений pH от 1,8 до 6,0, что значительно упрощает регулирование кислотности электролита. Электролит, состоящий из двухлористого железа и метил-сульфатного железа, по сравнению с хлористым менее агрессивен и более устойчив к окислению. Покрытия, полученные из этого электролита, имеют меньшее количество трещин, обладают более равномерной структурой.
Приготовление и корректирование электролита. Для приготовления хлористого электролита используют двухлористое железо (Fe€l2-4h30).
Соляная кислота (НС1) применяется в виде водного раствора разной концентрации с плотностью от 1,14 до 1,20. Приготовление электролита производится в следующем порядке. В ванну заливают проточную или дистиллированную воду комнатной температуры и добавляют соляную кислоту из расчета 0,5 г/л воды. В подкисленную воду засыпают двухлористое железо, выдерживая требуемую концентрацию, и перемешивают до полного растворения. После растворения двухлористого железа электролит должен отстояться в течение 1 … 2 ч, пока не примет светло-зеленый цвет. Затем электролит проверяют на кислотность. Нормальная кислотность должна быть pH 0,8… 1,2. При необходимости добавляют недостающее количество кислоты в соответствии с ее плотностью, приведенной ниже.
Плотность кислоты, г/см3 1,14 1,15 1,16 1,17 1,18 1,19 1,20 Количество кислоты, г/л 20 19 18 17 16 15 14 Количество кислоты, см*/л……. 18 16,6 15,5 14,6 13,6 12,6 11,6
Приготовленный таким образом электролит следует проработать током при плотности 30 А/дм2 и соотношение поверхностей анодов и катодов Sa : SK = 2 : 1 в течение двух часов.
Удельный вес электролита (плотность) г/см8 1,12 1,15 1,17 1,20 1,23 1,26 1,29 1,32 1,35 Концентрация железа, г/л … 200 260 300 350 400 450 500 550 600. Контроль кислотности электролита можно осуществлять с помощью индикаторной бумаги «Рифан» с pH 0,3 …2,2 или потенциометров ЛПУ-01, ЛПМ-60.
sxteh.ru
как хромировать металл в домашних условиях
Хромирование — одно из наиболее используемых и красивых видов покрытий. Нанесение хрома является физико-химическим действием, в период которого тонкий пласт металлического хрома оседает на плоскости обрабатываемой детали. Он придаёт изделиям замечательный серебристый вид, а кроме того, оберегает железо от ржавчины. Можно произвести высококачественное хромирование в домашних условиях.
Содержание материала
Особенности независимой процедуры
Чтобы правильно и надёжно осуществлять процесс нанесения хрома своими руками, следует принимать во внимание все характерные черты химических и физиологических преображений, которые совершаются. Большая часть химических элементов, участвующих в хромировании, представлена особенно опасными элементами, следовательно, прежде чем приступать к проведению эксперименты с хромированными покрытиями, тщательно изучить необходимо теоретическую сторону процесса.
Хром придаёт плоскости замечательный наружный вид, благодаря которому продукция приобретает весьма изящный вид. Гальваника открывает большие возможности для усовершенствования декоративных, физиологических и химических качеств материалов. Хром чрезвычайно устойчив к воздействию агрессивных сред, он не темнеет под воздействием окружающей среды, благодаря этому он отыскал обширное применение при конструировании частей кузовов автомобилей и частей элементов, работающих в сложных условиях. Толщина блестящего напыления весьма мала: от 0,075 до 0,25 миллиметров.
Также рекомендуем прочитать:
В отличие от никеля, в основной массе случаев хром не используют к металлу. Для этого применяют лёгкий слой оцинковки. Такого рода слой состоит из меди и требует применения технологических воздействий, усложняя и без того трудный процесс.
Ещё одна проблема, которая может остановить на пути к осуществлению задачи — получение реактивов. Главным компонентом является соединение хрома (CrO3), иное наименование — ангидрид хрома. Неприятной чертой его применения является то, что оксид хрома является самым мощным ядом, смертельная доза которого — 6 г. Это соединение имеет небольшой оборот, который строго контролируется государством.
Остатки, возникающие в результате завершения хромирования, должны быть утилизированы в соответствии со специальным порядком, а не поступать в канализацию или в почву. Элемент является сильным канцерогеном: если он появляется на коже, будет очень сильное раздражение, в том числе экзема и дерматит, может сформироваться опухоль.
Реактивы для применяемого электролита
Важно рассмотреть все нюансы процесса перед тем, как хромировать металл в домашних условиях. Процесс хромирования своими руками в домашних условиях осуществляется электрическими средствами. Для его выполнения следует иметь катод, анод (заготовку) и электролит, в котором станут осуществляться химические взаимодействия.
В качестве катода применяется лист свинца либо его соединение с оловом. Правильнее всего, чтобы полновесная пластинка была несколько больше, чем заготовка. Катод подключён к позитивному электроду. Анод соединён с материалом, накрытым хромом. Он должен быть подвешенным в среде электролита таким способом, чтобы он не затрагивал стен, низа и не затрагивал катода.
Для формирования электролита необходимы следующие элементы:
- хромовый ангидрид, 250 г / л электролита;
- серная кислота — 2−2,5 г / л;
- чистейшая, без включений, вода.
Перед изготовлением электролита воду нагревают до температуры 60−80 °С, затем растворяют в ангидриде хрома. Затем нужно слегка охладить раствор и добавить небольшое количество серной кислоты тонким потоком. Кислота должна быть не промышленной, а чистой. Электрическая компенсация очень чувствительна к формуле электролита, поэтому на предприятиях есть лаборатории, которые проводят непрерывный мониторинг устойчивости состояния реагентов. Если проводится гальваника в домашних условиях или хромирование собственными руками, придется обойтись без помощи технологов.
Оборудование для хромированных деталей
Воздействие хромирования может быть не только на изделия из металла, но и пластмассы. Хромирование пластика в домашних условиях, например, фары, проводится немного иначе. Следует знать, что для выполнения процедуры используются реагенты, которые могут представлять опасность для здоровья.
Для покрытия хромом в домашних условиях деталей необходимо следующее оборудование:
- ванна пластиковая;
- выпрямитель, способный обеспечить напряжение до 12 вольт и до 50А;
- кислотостойкий нагреватель для нагрева электролита;
- термометр с границей замера 0−100 градусов.
Параметры и объемы единичных видов оборудования, используемых для хромирования, формируются в зависимости от размера и количества возделываемых продуктов. Нужно подобрать наименьшие объемы ванны, в которую детали будут погружены. Ванная может быть сделана из пластмассового ведра либо иного прямоугольного контейнера. Для того чтобы раствор не улетучился при долгом хранении, следует гарантировать воздухонепроницаемую крышку. В качестве выпрямителя можно использовать зарядное устройство для автоаккумулятора (подходит для мелких деталей).
Хромовые элементы будут делаться в электролите, который состоит из:
- очищенной воды;
- триоксида хрома (CrO3) 220−250 г/л;
- серной кислоты (h3SO4) 2,2−2,5 г / л.
Кроме этих деталей, понадобится следующий набор: соляная кислота (HCl), ацетон и листовой металл.
Подготовка плоскости и металлизирование
Независимая хромировка не может быть выполнена без соответствующей подготовки плоскости продукта. Вначале необходимо сформировать медную или никелированную подложку, потому как элемент не находится в плоскости стали, алюминия либо любого иного сплава.
Медный слой либо никелирование исполняется в гальванической ванне. Катод — металлическая медь или никель, электролит предполагает собой раствор серной кислоты, сульфата меди либо никеля. После окончания изготовления продукт тщательнейшим образом полируется, следя затем, чтобы не испортить тонкий пласт основы, необходимо ее обезжирить и высушить.
Независимое хромирование должно осуществляться при устойчивых параметрах всех частей. Каждое отклонение может послужить причиной к повреждениям напыления. К примеру, преобладание концентрации тока на единицу участка приводит к формированию выростов и дендритов металлического хрома в заостренных углах продуктов.
Несоблюдение температурного порядка и колебания сосредоточения реагентов провоцируют потускнение, пятнистость напыления. После хромирования элементов блестящая плоскость покрывается необходимым пластом сплава, напряжение отключается, продукция отсоединяется и располагается в ванну с очищенной водой. Процесс правильнее воспроизводить несколько раз, меняя воду.
Этапы хромирования элементов
Захромировать напрямую можно только такие металлы, как медь, латунь и никель. Чтобы самому хромировать металлические детали, надо предварительно нанести медный, латунный или никелевый слой. Для этого необходимы подходящий электролит и технология. После сушки плоскость активизируют в растворе соляной кислоты (100 г / л).
Период обрабатывания зависит от состояния плоскости (5−20 мин). Части промывают водой и погружают в хромированную ванну. Для этого подвеску изготавливают из проволоки либо стержня. К подвеске подаётся «отрицательный» провод. Рядом с медным стержнем прикреплён увесистый анод, к которому прилагается «плюс». Через 20−40 минут части вытаскивают из ванны и промывают в воде.
После просыхания допускается полирование слоя хрома, чтобы плоскость была отражающей. Подготовить электролит нетрудно: вначале в воде раскрывается ангидрид хрома, а затем добавляется тонкая струйка серной кислоты. Перед тем как загружать детали, нужно повесить любую пластину и включить электролит на полчаса-час.
Если композиция с ярко-красным цветом превращается в светло-бордовый оттенок, то в этом случае можно включить хромированные элементы. Состав хрома должен нагреваться до 45 градусов. Ток вводится в зависимости от площади плоскости покрываемых элементов. Для обработки 1 кв. дм необходим ток в 15−25 ампер.
Основные недостатки покрытия не должны пугать новичков. Некачественный слой можно замачивать в соляной кислоте. После этого детали промывают в воде, а процессы металлизации повторяются.
Чаще всего есть ряд ключевых недостатков:
- Отшелушивание блестящей плёнки. Главная причина — нехорошая адгезия из-за недостаточного обезжиривания. После вытаскивания напыления поверхность вновь вычищается и активизируется.
- Установка хрома в заостренных краях. Этот недостаток показывает на высочайшую уплотненность тока в заостренных концах. По возможности кромки лучше скруглить либо настроить экраны в проблематичных зонах.
- Матовое покрытие. Для достижения блеска следует повысить температуру раствора, уменьшить электричество либо прибавить ангидрид хрома.
Прежде чем хромировать собственными руками, необходимо тщательнейшим образом оценить предстоящую цену работы и произвести вывод о необходимости ее проведения. Прежде чем сформировать приспособление для хромирования, необходимо распланировать будущее устранение отходов. При попадании в грунт, а далее в колодцы соединение хрома порождает отравление и формирование болезни, следовательно, настойчиво рекомендовано не начинать работу, не определяясь ранее со всеми особенностями процесса. Видеоурок поможет узнать тонкости покрытия поверхности металла хромом.
pochini.guru
Как хромировать металл - Как? Так!
Содержимое:
4 метода:
Процесс хромирования заключается в получении электролитическим методом тонкого поверхностного слоя хрома на детали, изготовленной обычно из металла с низкой коррозионной стойкостью. Хром - довольно распространенный металл, который, однако, почти не используется в чистом виде. Вы не найдете предметы, изготовленные из хрома, однако хромирование широко распространено. Этот процесс позволяет получить очень яркие, глянцевые, зеркальные металлические поверхности деталей автомобилей и мотоциклов, сантехники, многих других бытовых и промышленных объектов. Обладая высоким сопротивлением к окислению, хром защищает металлы и уменьшает поверхностное трение. Хромирование - высокоспециализированный процесс с использованием высокотоксичных, летучих и канцерогенных веществ (таких как хромовая и серная кислоты), с очень вредными отходами производства. Если вы заинтересовались этим процессом, обязательно соблюдайте все меры безопасности.
Шаги
Метод 1 Использование хрома для декоративных целей
- 1 Хром можно наносить в декоративных целях на такие подверженные коррозии металлы, как сталь, латунь, медь, алюминий, нержавеющая сталь.
- Хром хорошо отражает свет, имеет более эстетичный и гладкий вид по сравнению с другими покрытиями, например краской.
- При декоративном электролитическом хромировании никель и хром наносятся на металлический объект, например на обод колеса или капот автомобиля.
- Никель обеспечивает гладкость, блеск поверхности и повышает сопротивление коррозии.
- Очень тонкий слой хрома поверх никеля предохраняет его от потускнения, царапин и ржавчины.
Метод 2 Используйте покрытие "твердый хром" для крупных деталей
- 1 Покрытие "твердый хром", также известное как "промышленный" или "инженерный" хром, используется для нагруженных деталей (например стальных) крупных механизмов с целью уменьшить их трение и износ.
- Покрытие "твердый хром" не тверже других хромовых покрытий, оно просто достаточно толстое для того, чтобы можно было измерить его твердость.
- Покрытия типа "твердый хром" толще декоративных покрытий на три порядка.
Метод 3 Раствор шестивалентного хрома
- 1 Для получения 3,79 литра (1 галлона) раствора смешайте 936 грамма (33 унции) хромовой кислоты и 9,36 грамма (0,33 унции) дистиллированной воды.
- Пропорции могут быть несколько другими, в зависимости от площади хромируемой поверхности.
- 2 Размешайте раствор в иммерсионной ванне, используемой для опытов или химической обработки.
- Обезжирьте и тщательно очистите детали перед нанесением на них покрытия.
- При приготовлении раствора осторожно доливайте ингредиенты, избегая их разбрызгивания.
- Помните, что раствор канцерогенно опасен.
- Соблюдайте предельную осторожность, поскольку раствор склонен к возгоранию, а также может взаимодействовать со множеством других веществ, что небезопасно.
Метод 4 Система электролиза
- 1 Растворите никелевые пластины в хромовой/серной кислоте.
- 2 Подсоедините положительный полюс источника питания к раствору.
- 3 Подсоедините отрицательный полюс к детали и погрузите ее в раствор.
- Отрицательно заряженная деталь будет притягивать к себе положительно заряженные ионы металла.
- Толщина покрытия определяется продолжительностью процесса электролиза.
- Поддерживайте температуру раствора в интервале 35-46 градусов Цельсия (95-115 градусов Фаренгейта) для получения декоративного покрытия.
- Для получения покрытия типа "твердый хром" поддерживайте температуру раствора в пределах 49-66 градусов Цельсия (120-150 градусов Фаренгейта).
- При работе с реактивами обязательно используйте респиратор и другие средства защиты.
- 4 После нанесения покрытия промойте деталь в проточной воде несколько раз.
Советы
- Для получения однородного покрытия подогрейте деталь до температуры раствора, прежде чем погрузить ее в ванну.
- Хромовая кислота очень едкая, тем не менее ее можно хранить в плотно закрытой стеклянной посуде, фильтруя перед очередным использованием.
Предупреждения
- Правила утилизации растворов кислот жестко регулируются законодательством; следуйте правилам, установленным в вашей местности.
- При работе с кислотами обязательно используйте средства защиты, такие как защитные очки, фартук, респираторная маска, плотные резиновые перчатки.
- Хромовая и серная кислота вступают в опасные реакции с ацетоном, спиртами, натрием, калием, аммиаком, мышьяком, сероводородами, фосфором, пиридином, селеном, серой и многими другими веществами.
- Избегайте любого контакта кислот с кожей.
- Перед началом работы запаситесь аптечкой, легко доступной для всех учасников эксперимента.
- Раствор хромовой кислоты вступает в быструю реакцию со многими материалами, включая распространенные виды топлива, что может привести к возгоранию и пожару.
- Избегайте вдыхания любых паров.
- Помните, что раствор хромовой кислоты является канцерогеном.
Что вам понадобится
- Кристаллы хромовой кислоты
- Жидкая серная кислота
- Дистиллированная вода
- Никелевые пластинки
- Источник питания
- Средства безопасности: защитные очки, фартук, маска, резиновые перчатки
- Устройство электролиза
- Химическая посуда (ванна)
Прислал: Шестакова Мария . 2017-11-12 13:57:06
kak-otvet.imysite.ru
Как хромировать металл | Кизиярский завод металлоконструкций
Чтобы подготовить поверхность к хромированию, тщательно удалите с нее все следы ржавчины и окисления, которые образовались из-за влияния окружающей среды. Необходимо затереть металл наждачной бумагой.
Чтобы обезжирить поверхность, вы можете воспользоваться специальной смесью. Готовиться она на основе гашеной извести следующим образом: добавьте в литр воды 35 грамм гашеной извести, 10 грамм едкого калия и 3 грамма расплавленного стекла. После приготовления температура смеси будет достигать 90 градусов. Обезжиривание нужно проводить в течение часа, после чего аккуратно промыть поверхность водой комнатной температуры.
Вам понадобится приготовить электролитическую ванну: для этого в литр воды добавьте 300 грамм хромовой кислоты и 3 грамма концентрата серной кислоты. Подогрейте смесь до 50 градусов и добавьте 500 миллилитров дистиллированной воды. В получившийся раствор насыпьте хромовый ангидрит и тщательно перемешайте. После этого добавьте воды до необходимого объема. Расположите по обеим сторонам, или вокруг всей поверхности, которую вы хотите хромировать, две свинцовые пластины, содержания олова или сурьмы в которых составляет семь процентов. Размер пластин должен превышать металлическую деталь в два раза. Температура приготовленной вами ванной должна быть 60 градусов. Время выбирайте в соответствии с тем, какой результат вы хотите получить. Используйте автомобильный аккумулятор для подачи напряжения. Сила тока не должна превышать 3.10 кА / кв. м. DC.
Затем вы опускаете вашу деталь в ванну на то время, которое установили сами. После того как вытащите, протрите ее влажной, мягкой тряпкой и отполируйте, если есть необходимость.
Если после ванны вы увидели, что деталь не прохромировалась, то вам следует проверить контакт анода и катода. В данном случае анодом служит свинец, а катодом – хромированная поверхность. Проверьте температуру, она должна строго соответствовать приведенным значениям, если она выше уменьшите ее, если ниже, то увеличьте. Проверьте также и поверхность анода – на ней могла остаться пленка окислов. Внимательно посмотрите, все ли вы добавляли в нужных пропорциях. Если что-то не так – исправьте и начните процедуру хромирования сначала.
kamzmk.ru
4 методика:Использование хрома для декоративных целейИспользуйте покрытие "твердый хром" для крупных деталейРаствор шестивалентного хромаСистема электролиза Процесс хромирования заключается в получении электролитическим методом тонкого поверхностного слоя хрома на детали, изготовленной обычно из металла с низкой коррозионной стойкостью. Хром - довольно распространенный металл, который, однако, почти не используется в чистом виде. Вы не найдете предметы, изготовленные из хрома, однако хромирование широко распространено. Этот процесс позволяет получить очень яркие, глянцевые, зеркальные металлические поверхности деталей автомобилей и мотоциклов, сантехники, многих других бытовых и промышленных объектов. Обладая высоким сопротивлением к окислению, хром защищает металлы и уменьшает поверхностное трение. Хромирование - высокоспециализированный процесс с использованием высокотоксичных, летучих и канцерогенных веществ (таких как хромовая и серная кислоты), с очень вредными отходами производства. Если вы заинтересовались этим процессом, обязательно соблюдайте все меры безопасности. ШагиМетод 1 из 4: Использование хрома для декоративных целей
Метод 2 из 4: Используйте покрытие "твердый хром" для крупных деталей
Метод 3 из 4: Раствор шестивалентного хрома
Метод 4 из 4: Система электролиза
Советы
Предупреждения
Что вам понадобится
|
ves-mir.3dn.ru