Методы удаления окалины с поверхности металла. Как убрать сварку с железа
Как удалить холодную сварку: пошаговая инструкция по удалению
В настоящее время на рынке представлено множество различных клеевых составов, продающихся под общим наименованием «Холодная сварка». В действительности ничего общего у таких составов ни с горячей, ни с холодной сваркой нет. Под таким торговым названием продаются полимерные композиционные материалы, которые можно использовать для ремонта изделий из самых разнообразных материалов — от металлов до древесины, керамики, стекла и пластика. Иногда возникает необходимость в том, чтобы убрать такой клей. Причины для этого могут быть самыми разными. При появлении такой нужды вы можете без особых проблем растворить холодную сварку или убрать ее другими методами.
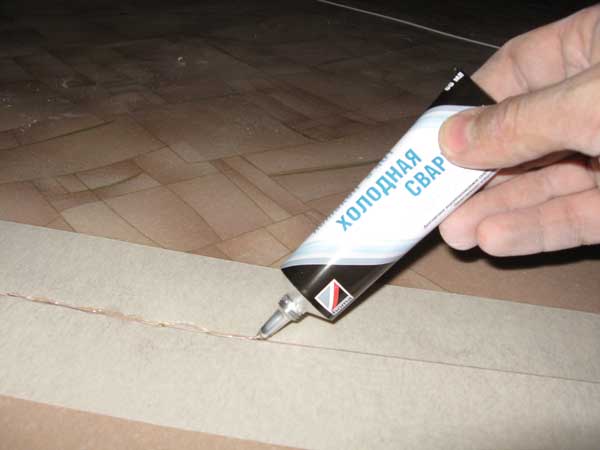
Холодной сваркой можно провести ремонт любых материалов и изделий.
Полезные советы перед началом работы
Перед началом работы нужно подготовить необходимые материалы и инструменты. Их перечень будет меняться в зависимости от того, с каких поверхностей нужно удалить клеевой состав. Вам может понадобиться следующее:
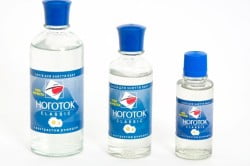
Жидкость для снятия лака с содержанием ацетона поможет убрать холодную сварку.
- Ацетон или жидкость для снятия лака для ногтей с его содержанием.
- Наждачная бумага.
- Мыло.
- Пемза.
- Кусок плотной бумаги или картона.
- Ненужная зубная щетка. Вместо нее можно взять ватный тампон или некоторое количество хлопчатобумажного материала.
- Напильник.
- Растворитель, бензин.
Прежде всего, вы можете приобрести в строительном магазине специальный готовый состав для удаления холодной сварки. В продаже доступно множество различных коммерческих продуктов, которые удаляют клеящие составы без особых проблем. Перед покупкой внимательно изучите инструкцию. Узнайте, с каких поверхностей способен удалять холодную сварку присмотренный растворитель, и выберите наиболее подходящий состав.
В большинстве случаев с холодной сваркой и другими распространенными клеящими составами хорошо справляется ацетон. При отсутствии «чистого» ацетона можете использовать жидкость для снятия лака с его содержанием. То, присутствует ли в составе ацетон, указывается на этикетке в перечне ингредиентов.
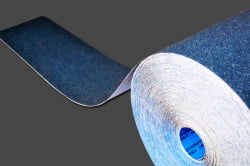
При помощи наждачной бумаги можно легко снять остатки холодной сварки с поверхности изделий.
Основные усилия нужно направлять на края «пятна». Вам нужно попробовать захватить это «пятно» за край и оторвать его от поверхности полностью. Постарайтесь как можно сильнее размочить холодную сварку. Как только состав начнет отставать от поверхности, осторожно попробуйте его снять.
Будьте осторожны с использованием ацетона, бензина, спирта и прочих растворителей. В особенности если холодную сварку нужно убрать с древесины, пластика, керамики и прочих подобных материалов. Под воздействием растворителя они могут утратить свой цвет, а некоторые и вовсе расплавиться. Любые растворители необходимо использовать с осторожностью. Для начала испытайте средство на какой-нибудь незаметной части изделия. Работайте с использованием средств индивидуальной защиты.
Удаление холодной сварки с деревянных поверхностей
Для начала попробуйте размочить холодную сварку теплым мыльным раствором. Используйте ноготь или какой-нибудь другой подходящий предмет, чтобы сковырнуть состав. Если ничего не получится, переходите к более радикальным методам.
Обычно удалить такой клеящий состав помогает ацетон. Он выручит, если деревянная поверхность имеет финишную отделку. Отковыривать холодную сварку от подобной поверхности не стоит, т.к. этим вы рискуете испортить покрытие. Растворители тоже нужно использовать с осторожностью. Делается все в такой последовательности:
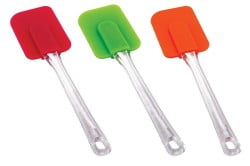
Очень удобно с деревянной поверхности убирать краску при при помощи силиконовой или резиновой лопаточки.
- Вы берете тряпку и смачиваете ее ацетоном.
- Трете поверхность холодной сварки. Небольшие участки обрабатывайте круговыми движениями. Если холодной сваркой заполнено большое пространство, делайте круговые движения в направлении от краев пятна к центру.
- Удобнее всего убирать размягченный состав при помощи силиконовой либо резиновой лопаточки. Под воздействием ацетона края состава поднимутся, а вы сможете подсунуть такую лопаточку под поднятый край и убрать пятно.
- Чтобы удалить ацетон, тщательно вымойте освобожденную от состава поверхность теплой водой. В завершение древесину нужно будет обработать оливковым маслом. Подойдет и пчелиный воск. Если есть специальная полироль для мебели, используйте ее.
Можно попробовать убрать холодную сварку при помощи минерального масла. Данный способ подойдет лишь в том случае, если деревянная поверхность не окрашена. Возьмите кусок ткани, смочите его минеральным маслом и протрите пятно холодной сварки. Трите и смачивайте, пока края не начнут отставать от поверхности. В завершение поверхность тоже нужно будет промыть теплой водой и отполировать.
В некоторых ситуациях единственным возможным вариантом решения проблемы является шлифование. Делается все очень просто. Сначала вам нужно будет заклеить область вокруг пятна клейкой лентой. Это защитит деревянную поверхность. После этого начинайте шлифовать наждачкой, пока пятно не отстанет. Для восстановления отшлифованной поверхности используйте тот же состав, которым она была вскрыта изначально.
Пошаговая инструкция по удалению холодной сварки с пластика
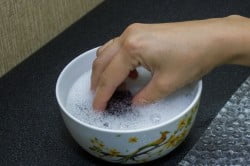
С поверхности пластика холодную сварку можно убрать при помощи мыльного раствора.
Эта задача несколько более сложная, чем удаление состава с древесины. Проблема в том, что пластик плохо переносит агрессивные воздействия вроде шлифовки, обработки ацетоном и прочими растворителями. Поэтому все нужно делать максимально аккуратно, чтобы не повредить материал.
Сначала подумайте, является ли пятно холодной сварки такой уж большой проблемой. Мешает ли она пользоваться предметом по назначению? Не будет ли без нее хуже, ведь зачем-то же она была нанесена ранее?
Попробуйте оттереть пятно без использования агрессивных составов. Можете дополнительно размягчить его теплой водой. Самый простой вариант — края пятна сварки поднимаются, и вы скатываете ее с поверхности. Но так происходит далеко не всегда. Отставшую от поверхности холодную сварку можно соскрести ножом или пластиковым шпателем.
Можно попробовать размягчить состав при помощи мыльной воды. Для этого возьмите тряпку и окуните ее в мыльную воду. Отожмите материал, чтобы он был влажным, но с него не лилась вода. Положите влажный материал на холодную сварку, требующую удаления. Сверху положите полиэтиленовую пленку и заклейте ее края малярным скотчем. Так вы создадите влажный микроклимат. Подождите несколько часов. За это время влажная ткань должна несколько размочить и размягчить клеящий состав. Удалите клей тряпкой, смоченной в теплой мыльной воде. Тереть нужно до тех пор, пока не будет достигнут желаемый результат.
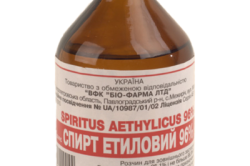
С поверхности пластика сварку можно также убрать с помощью этилового спирта.
Можно воспользоваться спиртом. Подойдет изопропиловый состав. Делайте все в следующем порядке:
- Возьмите кусок мягкой ткани и смочите его в спирте.
- Положите материал на пятно холодной сварки, чтобы она размягчилась.
- После того как состав начнет отставать от пластика, постарайтесь удалить как можно большее его количество.
- Для удаления остатков используйте тряпку, смоченную в мыльном водяном растворе.
- После достижения желаемого результата промойте поверхность теплой чистой водой.
Удаление холодной сварки со стекла и керамики
Со стеклянными и керамическими изделиями нужно быть предельно осторожным. При неправильном обращении их можно легко испортить.
Прежде всего, попробуйте счистить холодную сварку со стекла при помощи острого лезвия. Если слой нетолстый, лезвие бритвы должно с ним справиться, не навредив стеклу. Для удаления остатков используйте теплый мыльный раствор.
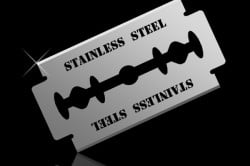
Для снятия холодной сварки со стекла и керамики можно использовать острое лезвие.
Если бритва «не возьмет» холодную сварку, попробуйте размочить состав. Поместите предмет в миску с теплой водой. Если он большой или не может быть помещен в емкость по другим причинам, достаточно будет смочить ткань теплым мыльным раствором, уложить ее на пятно и закрепить сверху слой полиэтиленовой пленки. Оставьте на пару часов, а затем попробуйте соскоблить холодную сварку шпателем или лезвием. Для удаления остатков можно применить ацетон или спирт. При необходимости отполируйте стекло в завершение работы.
Для удаления холодной сварки можете попробовать использовать растворители типа ацетона, уайт-спирита и пр. Для удаления пятна его нужно смочить водой, после чего попробовать удалить загрязнение при помощи тампона, смоченного в растворителе.
Существует и другой метод удаления. При низких температурах большинство клеевых составов теряют свою прочность и без проблем отстают от поверхностей. Поэтому если есть возможность поместить изделие в морозильную камеру или же если за окном температура уже опустилась хотя бы до -15°С, можете попробовать данный метод.
С керамики холодную сварку можно попробовать удалить мокрой тряпкой и резиновым шпателем. Сначала пятно обильно вымачивается, после чего осторожно отчищается при помощи шпателя.
В некоторых ситуациях достаточно использовать обычный растворитель. Все очень сильно зависит от особенностей изделия и толщины слоя холодной сварки.
Советы по удалению холодной сварки с металлических поверхностей
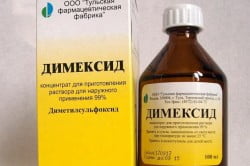
С железа сварку можно удалять диметилсульфоксидом.
С металлом все несколько проще. Он прочнее, и с ним можно больше экспериментировать. Прежде всего, холодную сварку можно попробовать размочить или обработать ацетоном, уайт-спиритом, бензином и пр. Делайте все так, как и в предыдущих методах.
Еще одним средством, которое можно попробовать использовать для удаления холодной сварки, является диметилсульфоксид. Продается в аптеках. Хорошо справляется с самыми разнообразными клеящими составами.
Будьте осторожны с данным средством, работайте в защитных перчатках.
Вещество легко проникает через поврежденную кожу. Могут появиться раздражения и интоксикация.
Если вода и различные растворители не помогают, попробуйте срезать холодную сварку с металла острым ножом. Или же удалите ее при помощи напильника.
Таким образом, способов удаления холодной сварки довольно много. Выбирайте наиболее подходящий. Удачной работы!
moyasvarka.ru
Методы удаления окалины с поверхности металла :: Технология металлов
Неудаленная окалина, всякого рода загрязнения, плохая отделка поверхности деталей резко снижают коррозионную стойкость металла. Поэтому с поверхности деталей следует полностью удалять даже следы окалины, а также мельчайшие частички железа.
В практике применяют химические, электрохимические и механические способы удаления окалины.
К химическим и электрохимическим способам относятся травление, пассивирование и электролитическое полирование, а к механическим — галтовка, крацевание, шлифование и полирование.
Коррозионная стойкость полированной поверхности значительно выше, чем шлифованной или травленой (непассивированной). Поэтому в процессе отделки деталей из нержавеющих сталей следует добиваться высокой чистоты поверхности и полного сглаживания мельчайших неровностей.
Аустенитные хромоникелевые стали хуже шлифуются и полируются, чем хромистые стали. Многие детали, применяемые в машиностроении, подлежат отделке. Поэтому с двухфазных сталей типа 08Х22Н6Т окалину целесообразно удалять механическими способами, так как при химических в результате вытравливания ферритной фазы поверхность металла становится шероховатой и ее дополнительно требуется шлифовать и полировать.
Травление и пассивирование.
Процесс травления состоит из следующих операций: обработки в щелочном расплаве, промывки в холодной проточной воде, травления в растворе кислоты, промывки, пассивирования, промывки, протирки и сушки.
При обработке в щелочном расплаве окись хрома взаимодействует со щелочью:
Сr2O3 + 2NaOH → 2NaCrO2 + Н2O.
Хромит натрия при окислении селитрой переходит в легко растворимый в воде хромат натрия:
2NaCrO2 + 3NaNО3 + 2NaOH → 2Na2CrO4 + 3NaNO3 + h3O.
Входящие в состав окалины окислы железа и хромит железа окисляются селитрой:
2FeO + NaNO3 → Fe2O3 + NaNO3;
2Fe304 + NaNO3 → 3Fe2O3 + NaNO2;
2FeO - Cr2O3 + NaNO3 → Fe2O3 + 2Cr2O3 + NaNO3.
Эти химические реакции вызывают изменение структуры окалины, в результате чего она легко разрушается.
Щелочной расплав состоит из 60—70% едкого натра, 25— 35 % натриевой селитры и 5 % поваренной соли. Металл выдерживают в расплаве 5—25 мин при 450—500 °С.
Детали перед загрузкой в расплав тщательно просушивают. В процессе обработки металла в расплаве окалины частично отслаивается и оседает в виде шлама на дно ванны. Оставшуюся окалину после промывки удаляют травлением в растворе, содержащем 10—18% серной кислоты (плотность 1,84) с добавкой 3—8 % поваренной соли, или в растворе, содержащем 20% серной кислоты, 1,5% азотнокислого натрия и 2,5% поваренной соли. Продолжительность травления 3—5 мин, температура раствора 70—80 °С. При травлении хромистых нержавеющих сталей типа 1X13, Х17, Х25 и Х27 температура раствора должна быть 50—60 °С.
Травильный раствор корректируют, добавляя серную кислоту при уменьшении ее концентрации <11 %. Кислоту вводят в таком количестве, чтобы после тщательного перемешивания ее содержание в растворе составляло 18—22 %. Хлористый натрий и селитру добавляют в тех случаях, когда поверхность протравленного металла приобретает серый цвет.
Двухфазные стали типа ЭИ811 рекомендуют травить в 15— 18%-ном растворе соляной кислоты при 60—70 °С в течение 3—10 мин.
В случае появления рыхлой отслаивающейся пленки на поверхности металла двухфазных сталей (ЭП53, ЭП54) после травления в соляной кислоте в травильный раствор рекомендуют вводить 0,9 % ингибитора ПБ-8/2. Двухфазные стали можно также травить в сернокислотном растворе следующего состава: 18 %-ная h3SO4 + 3 % NaCl + 0,015% ЧМ (травильная присадка) при температуре раствора 80 °С в течение 5— 10 мин.
После травления стали подвергают пассивированию в 3— 5 %-ном растворе азотной кислоты при 40—50 °С в течение 3— 5 мин. Для пассивирования хромистых сталей применяют тот же раствор, но рекомендуют вводить в него дополнительно 1—2 % бихромата натрия. После пассивирования поверхность полуфабрикатов и деталей становится серебристо-матовой, чистой, в результате значительно повышается коррозионная стойкость металла.
Во избежание в процессе пассивирования почернения поверхности металла следует составлять пассивирующий раствор на чистой воде, не содержащей хлоридов. Кроме того, для получения самой пассивной пленки с более высокими коррозионными свойствами промывные воды и щелочные растворы, применяемые при этом процессе, должны содержать минимальное количество хлоридов, а еще лучше не содержать их.
На машиностроительных заводах часто отсутствуют установки с щелочными расплавами. В таких случаях для облегчения кислотного травления перед термической обработкой детали следует погружать в насыщенный раствор поваренной соли.
Во время термической обработки NaCl вступает во взаимодействие с окислами металла и окалина, остывая, при малейшем постукивании легко осыпается.
Окалина может удаляться с поверхности стали и без предварительного разрыхления в щелочном расплаве. Для этого применяют растворы следующего состава: 200—250 г/л азотной кислоты, 15—25 г/л фтористого натрия и 15—25 г/л хлористого натрия. Температура раствора комнатная, продолжительность травления 15—90 мин.
Можно применять раствор с меньшей концентрацией компонентов: 100 г/л азотной кислоты и 4 г/л фтористого натрия при температуре раствора 50—60 °С. Для предварительного разрыхления толстой окалины можно использовать раствор (частей по объему):
Серная кислота (плотность 1,84) . . 6—8
Соляная кислота (плотность 1,19) . . 2—4
Вода ...............100
Для получения блестящей, глянцевой поверхности металла применяют травильную смесь кислот, % (объемн.):
Соляная кислота .....20
Фосфорная кислота . 5
Азотная кислота .....5
Вода ........70
Гидриднонатриевый метод травления применяют для удаления окалины с поверхности деталей из нержавеющих сталей различных марок, сплавов на основе титана, никеля и других металлов, не растворяющихся в щелочах.
Детали обрабатывают в расплавленной щелочи с добавкой 2% гидрида натрия (NaH), который образуется в травильной ванне при взаимодействии металлического натрия с водородом.
Окислы железа полностью восстанавливаются по реакции
4NaH + Fe3O4 = 3Fe + 4NaOH.
Окислы хрома восстанавливаются частично:
NaH + Cr2O3 → 2CrO + NaOH.
Металл, загруженный в расплав, должен быть совершенно сухим, поэтому детали предварительно прогревают в печах при 300 °С. Продолжительность выдержки в расплаве (в зависимости от состояния окалины) составляет 5—20 мин, температура расплава 350—380 °С.
Восстановленная окалина, имеющая вид рыхлой губчатой массы, остается на поверхности деталей; ее удаляют с их поверхности струйной промывкой холодной водой.
Для получения блестящей поверхности стальные детали после гидриднонатриевой обработки дополнительно травят 2—5 мин в 5—10 7о-ном растворе серной кислоты; детали из нержавеющей стали после травления дополнительно пассивируют в течение 1 мин в 5—10%-ном растворе азотной кислоты при 60—70 °С; детали из сплавов титана подвергают травлению в смеси азотной и плавиковой кислот; детали из сплава типа нимоник травят в смеси азотной кислоты и хлорного железа.
В лабораторных условиях без предварительного разрыхления окалины для травления образцов из нержавеющей стали можно применять растворы следующего состава: 5 мл азотной кислоты (плотность 1,4), 45 мл соляной кислоты (плотность 1,19) и 50 мл воды. Температура раствора 60—70 °С, продолжительность травления 5—10 мин. В процессе удаления окалины образцы металла несколько раз вынимают из травильного раствора, промывают водой и зачищают металлическими щетками (сделанными из нержавеющей проволоки).
Удалять окалину с поверхности нержавеющих сталей можно так называемым щелочным раствором перманганата.
В качестве раствора используют 50—100 г/едкого натра, 50—100 г/л перманганата калия. Температура раствора 80— 100 °С. Продолжительность 1—30 мин в зависимости от толщины окалины. При составлении раствора сначала растворяют в воде щелочь, затем вводят необходимое количество перманганата. После обработки металла в указанном растворе следует промывка в воде и дополнительное травление в кислотных растворах. Считают более эффективной такую последовательность операции: травление в кислотах, обработка в щелочном растворе перманганата калия и повторное травление в кислотах.
Удаление окалины с металла объясняется объемными изменениями, происходящими при переходе низших окислов металла в высшие. Так, например, на нержавеющих хромистых сталях окалина состоит из окислов трехвалентного хрома, которые под действием перманганата окисляются до шестивалентного. Окисел шестивалентного хрома легко растворяется в щелочном растворе.
Поскольку перманганат калия является дорогим химикатом, процесс удаления окалины в этом растворе в производственных условиях будет также неэкономичным.
Его можно применять для удаления окалины в лабораторной практике.
Электролитическое травление нержавеющих сталей можно также проводить в 5—10%-ном растворе азотной кислоты при комнатной температуре, продолжительность 10 мин. Катодная плотность тока 3—4 А/дм2. В качестве анодов применяют кремнистый чугун, катодами служит нержавеющая сталь.
Детали с резьбой, а также детали, которые «после термической обработки нельзя механически зачищать и шлифовать, травят на аноде в растворе следующего состава: 100 мл серной кислота (плотность 1,84), 800 мл фосфорной кислоты (плотность 1,54), 100 г хромового ангидрида, 100 мл воды. Температура раствора 70—75 °С, плотность тока на аноде 70—75 А/дм2, продолжительность травления 5—10 мин (катодами служат свинцовые пластины).
Окислы, образующиеся на поверхности стали в процессе сварки, и травильный шлам можно удалять в 15—20%-ном растворе перекиси водорода. Продолжительность процесса 5—10 мин, температура раствора комнатная. Помимо травильных качеств, раствор перекиси водорода обладает хорошими пассивирующими свойствами. Перекись водорода при взаимодействии с окислами металлов быстро разлагается, в связи с чем значительно повышается ее расход, и травление в указанном растворе требует больших затрат.
Для удаления ржавых пятен, образующихся на изделиях в процессе хранения, можно применять 10%-ный раствор лимоннокислого натрия.
Осветление стали Х18Н10Т с целью очистки поверхности от цветов побежалости, окислов и неудаленного травильного шлама можно осуществлять в 30%-ной перекиси водорода при температуре 55—65 °С или в смеси, состоящей из 25 мл/л 30%-ной перекиси водорода и 75 мл/л азотной кислоты (плотность 1,32) при температуре 20—60 °С. Скорость удаления травильного шлама резко возрастает при повышении температуры растворов.
Осветление стали 10Х17Н13М2Т с целью удаления окислов после сварки металла рекомендуют выполнять пастой следующего состава: 200 г/л h3SO4, 20 % NaCl и 400 г/л асбеста, а пассивацию сплава 06ХН28МДТ после шлифования металла — в 19%-ной серной кислоте, содержащей 0,1 % перекиси водорода.
Анодное травление мелких деталей и образцов из аустенитных сталей типа Х18Н10Т проводят в хромовом электролите, содержащем 200—250 г/л хромового ангидрида и 2—2,5 г/л серной кислоты, при температуре 50—55 °С и анодной плотности тока 540—50 А/дм2. Продолжительность травления 3— 10 мин. Катодами при этом служат свинцовые пластины. После травления следует промывка в воде. При наличии на поверхности нержавеющей стали травильного шлама применяют декапировку в 5—15%-ном растворе соляной кислоты с последующей промывкой, нейтрализацией остатков кислоты и сушкой.
Анодное травление можно также осуществлять в 10%-ном водном растворе серной кислоты при плотности тока 10— 20 А/дм2 в течение 2—10 мин. Температура комнатная. В качестве катодов применяют свинцовые пластины или пластины из нержавеющей стали.
Химическое травление.
Удалять окалину после термической обработки с нержавеющих хромоникелевых сталей можно химическим травлением в водном растворе 4%-ной азотной кислоты (плотность 1,35), 36 %-ной соляной кислоты (плотность 1,19). Температура раствора 35—50 °С, продолжительность травления 3—6 мин.
Травление пастами.
Данный вид очистки применяют для листового проката из двухслойной стали, например нержавеющей стали Х18Н10Т и Ст3.
Травильную пасту приготовляют из 200—250 г/л h3SO4, 150—175 г/л NaCl и 15—20 г/л NaNО3. В раствор вводят измельченную огнеупорную глину до получения сметанообразной консистенции.
Пасту наносят кистью на поверхность коррозионностойких листов, затем их укладывают горизонтально и выдерживают в течение суток. После чего пасту смывают водой и биметалл травят по режиму для углеродистой стали в течение 10—15 мин, промывают, пассивируют и сушат.
Для слабого травления (удаления оксидов) рекомендуют насыщенные водные растворы сульфата меди, сильно подкисленные соляной кислотой. Для травления применяют также царскую водку (смесь концентрированных кислот): 3 ч. НС1 + 1 ч. HNО3.
Одновременное травление и окрашивание в темный цвет поверхности нержавеющих сталей достигается в растворе, содержащем 250 см3 концентрированной НС1 и 750 мл воды, в который добавляют 50 г нитрата висмута и 50 г теллуристой кислоты. Для этих же целей (травление и окраска) можно использовать смесь, состоящую из концентрированного раствора 800 мл FeCl3 и концентрированной НС1 (20 мл).
Химическое клеймение деталей из стали типа Х18Н10Т проводят в растворе следующего состава:
Клеймо наносят резиновым штампом, смачивая его о подушечку из листового асбеста или пористой резины. Раствор следует хранить в стеклянной банке с притертой пробкой.
Электролитическое полирование.
Сущность этого способа заключается в анодной обработке поверхности металла в специальных электролитах.
Азотная кислота (плотность 1,4), - 40мл
Соляная кислота (плотность 1,19), - 40мл
Селен (металлический), 4г
Оксид меди, - 4г
Вода, - 100 мл
Поверхность металла сглаживается в результате растворения выступающих участков. При электролитическом полировании удаляются лишь мелкие шероховатости (второго порядка). Поэтому изделия после грубой обработки резцом ми изделия, имеющие глубокие впадины на поверхности (шероховатости первого порядка), перед электрополированием должны предварительно подвергаться механической обработке и иметь поверхность, соответствующую 7—8-му классу чистоты обработки.
Электролитическое полирование может быть осуществлено в растворе, содержащем 45 % фосфорной кислоты, 40 % серной кислоты, 5 % хромового ангидрида и 10 % воды. Температура раствора 50—70 °С, плотность тока 30—60 А/дм2, продолжительность полирования 10—15 мин. В качестве катодного материала применяют свинец, а также в растворе: 20 % серной кислоты, 55 % лимонной кислоты, 25 % воды, температура раствора 80—85 °С, плотность тока 10—25 А/дм2, продолжительность полирования 5—10 мин (катодом служат медные пластинки) .
Химическое полирование.
Для химического полирования аустенитных сталей может быть применен раствор следующего состава: 4 объема соляной кислоты, 1 объем азотной кислоты, 0,5 объема серной кислоты, 5 г/л уксусной кислоты, температура раствора 80—150 °С.
Для химического полирования хромистых и хромоникелевых нержавеющих сталей, а также углеродистых сталей готовят раствор фосфорной кислоты, который медленно нагревают до 250 °С, при этом фосфорная кислота частично переходит в пирофосфорную. Реакция продолжается 1,5 ч (ее окончание определяют по прекращению выделения газа). Затем кислоту быстро охлаждают и добавляют около 10% серной кислоты. Чем больше содержание углерода в стали, тем меньше добавляют кислоты. Полирование проводят при 200 °С в течение 1 —10 мин. После пассивирования, электролитического или химического полирования необходима нейтрализация остатков кислоты на деталях, которую осуществляют в 1—3%-ном растворе кальцинированной соды с последующей промывкой и сушкой.
Дли химического полирования пружин из стали 12Х18Н10Т рекомендуют раствор следующего состава:
Температура раствора 65—70 °С, выдержка 5—30 мин. После электролитического (или химического) полирования получают поверхность с высокой отражательной способностью,
Азотная кислота (плотность 1,4), мл 40
Соляная ( плотность 1,19), мл 70
Серная ( плотность 1,84), мл 230
Клей столярный, г/л 10
Хлористый натрий, г/л 5—6
Краситель кислотный черный, г/л 5—6
которая не загрязняется остатками полировальных веществ. Такому полированию подвергают, предварительно хорошо отшлифованную поверхность. Вместе с тем электролитическое (и химическое) полирование имеет существенный недостаток: детали, подвергнутые сильной деформации, приобретают шероховатую поверхность, а сварные швы, невидимые при механическом полировании, резко выявляются.
Крацевание.
Крацевание применяют для удаления разрыхленного слоя окалины и шлама с поверхности изделий сложной конфигурации.
Операцию крацевания выполняют на крацевальных станках круглыми щетками из тонкой упругой нержавеющей стальной проволоки диаметром 0,1—0,4 мм. Частота вращения щеток 750—1000 мин-1.
Поверхность изделий во время крацевания смачивают 3— 5%-ным раствором кальцинированной соды или полировочной известью.
Галтовка.
Эту операцию осуществляют перед шлифованием для удаления с поверхности металла различных загрязнений, травильного шлама, грубых неровностей и заусенцев.
Детали обкатываются совместно с абразивными полирующими материалами во вращающихся барабанах или колоколах с частотой вращения 30—60 мин-1.
Различают галтовку мокрую и сухую. В первом случае детали обрабатывают с абразивными материалами, к которым добавляют 2—3%-ный раствор соды, во втором —с сухими абразивными материалами.
Не допускается обработка деталей, выполненных из коррозионностойких сталей, шариками из обычной стали.
Гидроочистка.
К гидроочистке относятся гидрошлифование и гидрополирование.
На большинстве установок гидроочистки все операций, за исключением загрузки и выгрузки деталей, механизированы.
Детали шлифуются и полируются в перфорированных барабанах, при этом устраняется ручная отделка на войлочных кругах. Чистота поверхности повышается до 8—9-го класса.
Жидкостному шлифованию и полированию подвергают мелкие детали (массой до 500 г) после штамловки, литья, механической обработки с чистотой поверхности не ниже 4—6-го классов.
Сущность процесса гидроочистки заключается в обработке деталей вместе со шлифующими материалами, помещенными в шестигранный барабан. Последний погружают в ванну с рабочей жидкостью, где он вращается со скоростью 25—30 об/мин. При отделке хромистых сталей частота вращения барабана может быть увеличена до 50 мин-1.
При вращении барабана детали и шлифующий материал перемешиваются и взаимно притираются. Барабан с отверстиями диаметром 3—5 мм выполнен из винипласта, ванна из стали Ст3 внутри облицована винипластом.
Все металлические детали крепления, привод форсунки, баки, мешалки, змеевики и сопла (при струйной подаче жидкости) должны быть выполнены из коррозионностойкой стали, пластмассы или стекла.
Установка должна быть предназначена специально для отделки коррозионностойких сталей. Не допускается одновременная загрузка деталей из обычных сталей.
В качестве рабочей жидкости применяют кипяченую воду, добавляя 0,1—0,2 % нейтрального мыла и 0,1—0,2 % кальцинированной соды. Температура раствора 25—45 °С.
При шлифовании в качестве абразивного материала используют бой электрокорундовых кругов зернистостью 150—180. Барабан загружают из расчета 2 ч. (по массе) абразивного материала и 1 ч. (по массе) деталей.
При полировании применяют фарфоровый бой, иногда добавляют шарики из коррозионностойкой стали (Х17Н2 или Х18). Соотношение полирующих материалов и деталей в барабане примерно то же, что и при шлифовании.
В процессе жидкостного шлифования и полирования не допускается загрязнение раствора металлической пылью, ржавчиной, а также применение в качестве абразивного материала наждака и других веществ, содержащих окислы железа.
Данный процесс обработки широко применяют на машиностроительных заводах легкой и пищевой промышленности при обработке точеных, литых и штампованных деталей различной конфигурации, изготовленных не только из коррозионностойких, но и из углеродистых сталей, а также меди, титана и их сплавов.
Шлифование и полирование.
Шлифование осуществляют для предварительной подготовки поверхности металла перед полированием.
При шлифовании острорежущие грани зерен абразива сглаживают крупные неровности на поверхности деталей, однако при этом остаются риски. Шлифование выполняют на станках с вращающимися кругами (главным образом фетровыми), на поверхность которых наклеивают абразивный материал.
Детали из коррозионностойких сталей перед шлифованием и механическим полированием следует декапировать в 5— 8%-ном растворе азотной кислоты для удаления всех следов, оставленных инструментом.
При шлифовании и полировании необходимо учитывать состав стали, ее структуру и физико-химические свойства.
Аустенитные стали следует шлифовать с давлением образца на круг 3,0—7,5 МН/м2 (30—75 кгс/см2), дальнейшее увеличение давления уменьшает чистоту поверхности металла. При шлифовании хромистых (мартенситных) сталей давление образца на круг не сказывается на чистоте поверхности и практически может повышаться до 25 МН/м2 (250 кгс/см2). Шлифование коррозионностойких сталей следует вести кругами с абразивным порошком, предварительно просаленным жировыми веществами.
Из абразивных материалов при шлифовании и полировании коррозионностойких сталей наиболее широко используют корунд, содержащий 99 % А12О3. Для получении поверхности высокого качества шлифование и полирование следует вести с большим числом переходов и последовательным применением абразивов соответствующих номеров.
Горячекатаный металл шлифуют кругами с тремя переходами абразива № 60—80, 100—120, 150—200. Полируя холоднокатаный лист, обработку ведут с двумя переходами (№ 250 и 300).
При шлифовании камнями нужно чаще править круги (так как они быстро засаливаются) и применять интенсивное охлаждение. При чистовом полировании коррозионностойких сталей для получения зеркальной поверхности применяют войлочные круги, а также круги, сшитые из дисков эластичной кожи и ткани.
Полирование устраняет неровности, которые остаются после шлифования, и поверхность металла приобретает зеркальный блеск.
Его осуществляют на том же оборудовании, что и шлифование. При полировании коррозионностойких сталей применяют известковые, алюминиевые и хромовые пасты. Наилучшими из хромовых паст являются пасты, состоящие из окиси хрома, так называемые пасты ГОИ (различают грубые, средние и тонкие).
При шлифовании и полировании коррозионностойких сталей такие материалы, как наждак, содержащий до 35 % окиси железа, карборунд с небольшим количеством графита, крокус и железный сурик, применять нельзя. Окислы железа в пастах вызывают появление ржавчины, а графит науглероживает поверхность деталей, что может сделать металл склонным к межкристаллитной коррозии. По этим же причинам не следует применять наждачную и особенно крокусную пасту.
Пассивность, а следовательно, и коррозионная стойкость коррозионностойких сталей связаны не только с состоянием поверхности металла, но и со структурой. Поэтому для снятия наклепа и напряжений металл следует подвергать закалке. После термической обработки окалина должна быть полностью удалена. Однако в процессе межоперационного хранения на поверхности коррозионностойких сталей иногда образуются ржавые участки, которые необходимо удалить промывкой в 10%-ном растворе лимоннокислого натрия. Для очистки не следует применять металлические щетки из обычной углеродистой проволоки. Необходимо помнить, что любые частицы железа, остатки окалины, окислы после сварки могут вызвать образование ржавчины.
Обезжиривание и пассивирование.
После окончательной механической обработки с целью повышения коррозионной стойкости деталей следует производить обезжиривание и пассивирование их с тщательной промывкой в горячей воде.
Обезжиривание (удаление жировых загрязнений) осуществляют в одном из следующих растворов, г/л:
1. Na2CО3 или K2CО3 - 30—50
NaOH или КОН - 10—20
Жидкое стекло или мыло - 2—3
2. К2СО3 или Na2CО3 - 15—25
Na3PО4 - 15—25
NaOH - 5—10
Жидкое стекло или мыло - 2—3
Температура растворов 80—90 °С и выше.
Пассивирование — создание тонкой пленки окислов на поверхности металла — происходит в результате его обработки в 5 %-ной азотной кислоте при температуре раствора 50—60 °С в течение 3—5 мин.
Покрытия.
На детали из нержавеющих сталей типа Х18Н10Т можно наносить металлические покрытия.
Омеднение выполняют в электролите следующего состава, г/л: 200 сернокислой меди; 50 серной кислоты; 5—7 фтористого натрия; плотность тока при этом составляет 3—5 А/дм2.
Никелирование осуществляют в обычных электролитах. Однако перед нанесением никеля требуется предварительная электрохимическая обработка поверхности нержавеющей стали в растворе хлористого никеля 250 г/л и соляной кислоты 8 % (объемн.), температура раствора 18—23 °С, плотность тока 3,2 А/дм2, аноды представляют никелевые пластины.
Источник:Туфанов Д.Г. Коррозионная стойкость нержавеющих сталей, сплавов и чистых металлов.М.: Металлургия, 1990.
markmet.ru
Как удалить холодную сварку. Очень нужно.
механически. тоесть отбить.
напильником или грубой наждачкой. Из растворителей ничего не поможет
газовой сваркой
а причем тут холдная сварка
Нагрей до 120 градусов, затем легко удалишь
touch.otvet.mail.ru