Штамповочные прессы как один из видов обработки листового металла. Штамповка листовая металла
Пресс для штамповки листового металла – виды штамповочного оборудования
Для получения различных изделий из плоской металлической заготовки применяются прессы для штамповки листового металла. Оборудование оказывает механическое воздействие на лист, вызывая пластическую деформацию материала. В результате изменяются размеры и форма детали по заданным параметрам. Методом штамповки можно получить изделия любой геометрической формы, которые отличаются точностью размеров и высокими прочностными характеристиками.
Разновидности штамповочных технологий
Штамповочный процесс обработки заготовок может осуществляться горячим или холодным методом. Эти технологические разновидности предполагают использование специального оборудования и применение определённых условий обработки металла.

Холодная штамповка является одним из разновидностей штампования
Методом горячей штамповки обрабатываются заготовки, предварительно нагретые в специальных устройствах до заданной температуры. Горячая штамповка необходима, когда для обработки холодного сплава не хватает мощности оборудования. Нагревательными устройствами могут служить электрические или плазменные печи. Такой метод требует точного расчёта параметров готовой детали с учётом усадки металла в процессе остывания.
При холодной штамповке детали формируются за счёт механического давления элементов штамповочного пресса. Холодный вариант штамповки считается более распространённым методом обработки металла. Он не требует дополнительного оборудования, сложных расчётов и механической доработки деталей. Благодаря этому методу увеличиваются прочностные показатели материала. Полученные изделия отличаются высоким качеством поверхности и точностью.
Разновидности технологических операций
Технологические операции с металлическим листом бывают разделительные и формоизменяющие.
Разделительные штамповочные операции выполняются на оборудовании, которое оснащено специальным инструментом. В результате от заготовки отделяется определённая часть по прямой линии или заданному контуру. Отделение части листа происходит в следующих процессах:
- Отрезка. Для выполнения этого действия оборудование оснащено дисковыми, вибрационными устройствами или гильотинными ножницами.
- Обрезка. Эта операция отделяет крайние части полученного изделия.
- Пробивка. В металлическом листе с помощью штампа создаются отверстия различной конфигурации.
- Вырубка. Из заготовки получают фигурную деталь с замкнутым контуром.
Формоизменяющие операции предназначены для создания изделия с иными параметрами и размерами без механического разрушения. Различают следующие виды этих операций:
- Отбортовка. Контур заготовки или внутренние отверстия подвергаются воздействию штампа для формирования бортов определённых размеров.
- Вытяжка. Эта операция является разновидностью объёмной штамповки, при которой из плоского материала получают пространственный элемент.
- Обжим. Для сужения торцов полой заготовки применяется штамп с матрицей конического типа, имеющей сужающую рабочую область.
- Гибка. В результате операции изменяется кривизна поверхности путём гибки металла и деформирования заготовки.
- Формовка – это изменение формы отдельных участков за счёт уменьшения толщины детали без нарушения внешнего контура изделия.
- Пуклёвка. Соединение штампом двух пластинок без использования дополнительных элементов.
Типы штамповочного оборудования
Для получения изделий из металлического листа применяются прессы, оснащённые различными штампами. В процессе работы оборудования верхняя составляющая штампа двигается, нижняя часть остаётся неподвижной.
Деформирование заготовки происходит в момент соприкосновения частей оборудования. Существуют разнообразные модели штамповочных прессов, что позволяет выбрать подходящий станок для изготовления требуемых деталей.

Гидравлическая штамповочная машина
Прессы для штамповки металла бывают:
- кривошипно-шатунного типа;
- гидравлические;
- радиально-ковочного типа;
- электромагнитного типа.
Кривошипные прессы являются оборудованием простого типа и могут быть двойного или тройного действия. Своё название прессы получили от кривошипно-шатунного механизма, который представляет собой основной конструктивный элемент станка. Принцип работы механизма основан на преобразовании вращательного движения от привода в возвратно-поступательное периодичное движение элемента пресса – ползуна.
Механизмы для обработки металла
Гидравлический пресс способен развивать значительное усилие до 2 тыс. тонн. Он применяется для операций гибки или объёмной штамповки толстостенных изделий. Действие механизма основано на перемещении поршней двух сообщающихся гидроцилиндров, которые имеют разный диаметр. Именно разница диаметров определяет величину усилия, которое может развивать пресс для штамповки металла.

Чертёж гидравлического пресса
Радиально-ковочный станок предназначен для выполнения формоизменяющих операций в целях получения цилиндрических изделий. В конструкцию механизма входит индукционная печь для предварительного нагрева детали. В процессе обработки обеспечивается вращение заготовки от электродвигателя при прохождении через зону ковки.

Чертёж радиально-ковочного станка
Электромагнитные прессы – новое высокопроизводительное экономичное оборудование для штамповки. Принцип действия основан на движении электромагнитного сердечника, который направляет исполнительный механизм станка к металлической детали.

Чертёж электромагнитного пресса
Особенности открытых и закрытых штампов
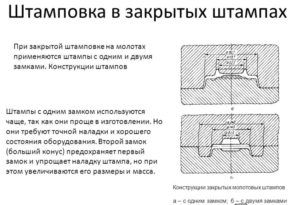
Штамповка закрытым способом
Штамповочное оборудование может быть оснащено открытыми или закрытыми штампами. В открытом штампе избыточный металл вытекает в заусенец или облой, который выполняет определённую функцию. Основными недостатками этой технологии являются: потеря сплава на облой, снижения качества изделия из-за перерезанных волокон при удалении заусенцев.
Закрытые штампы используются для изготовления изделий простой формы. Эта безоблойная технология отличается экономией металла, отсутствием затрат на обрезку заусенцев, высоким качеством продукции из-за всестороннего сжатия. Волокна металла не подвергаются перерезанию. Метод обработки в закрытом штампе применяется для малопластичных сплавов. Основными недостатками считаются: необходимость точной дозировки сплава, сложная конструкция штампа.
В современном производстве штамповка является преимущественно подготовительной операцией, которая позволяет изготавливать детали как для электроники, так и для воздушных или водных судов. Полученная продукция в дальнейшем подвергается сварке, резке, клёпке и другим методам обработки в зависимости от технологического процесса.
Видео по теме: Листовая штамповка
promzn.ru
Художественная листовая штамповка металла в состоянии «сверхпластичности»
Сверхпластичность определяется как способность поликристаллических (ультрамелкозернистых) материалов равномерно пластически деформироваться на очень большие степени (до Ек > 200%) при относительно высоких температурах и малых напряжениях (2...8 МПа) и соответственно малых скоростях деформации, к которым напряжение течения крайне чувствительно.
Состояние сверхпластичности определяется совокупностью ряда признаков: повышенная чувствительность напряжения течения материала к изменению скорости деформации; крайне незначительное деформационное упрочнение; аномально высокий ресурс деформационной способности; напряжение течения металла в состоянии сверхпластичности в несколько раз меньше предела текучести, характеризующего пластическое состояние данного материала.
Наиболее существенный из этих признаков - первый, остальные в определенной мере можно рассматривать как его следствия.
Признаки сверхпластичности проявляются в определенных условиях, среди которых принципиальное значение имеют структурное состояние деформируемого материала, температура и скорость деформации.
По структурному признаку принято различать две разновидности сверхпластичности: сверхпластичность у металлов и сплавов с особо мелким (сверхмелким) зерном (d < 10 мкм) и сверхпластичность полиморфных металлов и сплавов, проявляющуюся при деформировании их в процессе фазовых превращений, при этом исходный размер зерен не имеет значения.
Первую разновидность сверхпластичности называют структурной. Ее отличительными особенностями являются зависимость эффекта от исходного размера зерен (чем меньше зерно, тем больше склонность материала к скоростному упрочнению, соответственно больше его деформационная способность и меньше напряжение течения) и почти неизменное структурное состояние материала в процессе деформации. При этом необходимо, чтобы зерна имели приблизительно равноосную форму, в процессе нагрева до температуры деформации обладали достаточной устойчивостью против роста. Наилучшие условия для предотвращения роста зерна - у двухфазных сплавов. В сверхмелкозернистое состояние сплавы приводят обычно предварительной термической или термомеханической обработкой.
Вторая структурная разновидность сверхпластичности, наблюдающаяся при деформации материала в процессе фазового превращения, характеризуется, в отличие от структурной свёрхпластичности, постоянным изменением фазового состава и структуры материалов в процессе деформации.
Температурный интервал существования структурной сверхпластичности довольно широк; различный для различных металлов и сплавов, он может находиться в пределах от температуры начала рекристаллизации (0,4 Tпл) до температур, близких к температуре плавления. Нижняя граница температурного интервала обусловлена важной ролью диффузионных процессов в механизме деформации сверхмелкозернистых материалов, верхняя граница соответствует температуре начала собирательной рекристаллизации. Однако какой бы ни была температура структурной сверхпластичности, она должна поддерживаться постоянной по объему деформационного объекта в течение всего периода деформации, чтобы обеспечить равномерное течение металла, поэтому структурную сверхпластичность иногда называют изотермической.
Сверхпластичность, связанная с превращениями, реализуется при различных температурных режимах (в процессе монотонно изменяющейся температуры, проходящей через интервал превращения; при термоциклировании в пределах температурной амплитуды, включающей интервал температур превращения).
Скорость деформации для обеспечения состояния структурной сверхпластичности должна быть, с одной стороны, достаточно малой, чтобы успевали в полном объеме протекать диффузионные процессы, участвующие в деформации, с другой стороны, достаточно высокой, чтобы в условиях повышенных температур не допускать роста зерен. Для подавляющего большинства металлов и сплавов оптимальный интервал скоростей деформации, соответствующий структурной сверхпластичности, составляет 10-2 - 10-5 с-1, т.е. находится в промежутке между скоростями высокотемпературной ползучести и скоростями деформации, используемыми в традиционных процессах обработки металлов давлением. Скорость деформации при сверхпластичности превращения должна быть пропорциональна скорости последнего.
Задача определения условий существования сверхпластичности сводится к экспериментальному определению температурно-скоростных режимов деформации и структурного состояния исследуемою материала, при которых последний проявляет максимальную чувствительность напряжения течения к скорости и деформации (способность к скоростному упрочнению).
Для описания структурной сверхпластичности чаще всего используют эмпирическое уравнение s = k × en × vm из которого следуют выражения, определяющие показатели деформационного (n) и скоростного (m) упрочнения. При n=0, что характерно для состояния, структурной сверхпластичности, s = k1 × vm
Таким образом, показатель m определяется как тангенс угла наклона кривой s (v) в двойных логарифмических координатах.
Рис.17. Схема условного разделения кривой сверхпластичности на три участка: I - m £ 0,3; II - 0,3 £ m £ mmax; III - m £ 0,3 (шкалы s и e - логарифмические; шкала m-линейная)
Для материалов в состоянии структурной сверхпластичности эта кривая, которую иногда называют кривой сверхпластичности, имеет характерную S - образную форму, а зависимость показателя т от скорости деформации описывается кривой с максимумом, координата которого по оси V соответствует координате точки перегиба S-образной кривой (рис.17). С увеличением температуры точка перегиба смещается в сторону больших скоростей деформации. Аналогично увеличению температуры действует уменьшение исходного размера зерна сверхпластичного материала.
Таким образом, показатель m не является реологической постоянной материала, т.е. существенно зависит от температурно-скоростных режимов деформаций.
Сверхпластичность фазового превращения характеризуется значительным изменением показателя m в процессе деформации от 0,2 до 1,0, причем в первом приближении он прямо пропорционален скорости фазового превращения. Эта зависимость наглядно иллюстрирует структурную природу нелинейности вязкого течения сверхпластичных материалов (рис.18).
Рис.18. Зависимость напряжения течения сплава MA-1 при растяжении и осадке и коэффициента m от температуры испытания (а) и скорости деформации (б)
Ряд особенностей, характеризующих металлы в состоянии сверхпластичности, - чрезвычайно большая деформационная способность, малое напряжение течения, слабое влияние сверхпластической деформации на микроструктуру, высокая релаксационная способность обеспечивают возможность значительного повышения эффективности процессов обработки металлов давлением и качества готовых изделий. С другой стороны, малые скорости деформации соответствующие состоянию сверхпластичности, необходимость подготовки структуры заготовок и регламентированного температурного режима деформации существенно усложняют и удорожают подготовку производства, снижают производительность технологических процессов и в результате ограничивают использование сверхпластичности в обработке металлов давлением. Сопоставление указанных преимуществ и ограничений, а также обобщение имеющегося опыта использования сверхпластичности, например в процессах штамповки, позволяет выделить ряд технологических задач, при решении которых наибольший эффект обеспечивает деформирование в состоянии сверхпластичности, К таким задачам прежде всего относятся следующие:
1. Штамповка малопластичных и трудно деформируемых металлов и сплавов на основе никеля, титана, магния, алюминия, железа, тугоплавких металлов, которые отличаются, как правило, высокой стоимостью, а их обработка - большой трудоемкостью и многооперационностью, поэтому увеличение деформационной способности материала в состоянии сверхпластичности позволяет существенно увеличить деформацию за один технологический переход и перейти, таким образом, к малооперационной технологии, что в значительной мере компенсирует уменьшение производительности за счет малых скоростей деформации.
Штамповка или другие способы формовки изделий, отличающихся особо сложной формой, получение которой часто недоступно для традиционных методов обработки металлов давлением (например, тонкостенные детали сложной формы с оребрением, замкнутые емкости сферической и более сложной формы и т.д.). Это дает возможность максимально приближать форму и размеры поковки к форме и размерам готовой детали, снижать до минимума или полностью исключить припуск на механическую обработку, добиваясь значительной экономии дорогостоящих металлов и сплавов, снижения трудоемкости механической обработки.
Снижение требуемых усилий штамповки и мощности применяемого оборудования. Прямым следствием этого является увеличение фондоотдачи деформирующего оборудования и уменьшение энергоемкости процессов штамповки: появляется возможность переводить производство ряда крупногабаритных штампованных поковок, получаемых на мощных прессах, на деформирование в состоянии сверхпластичности. Наряду с этим в состоянии сверхпластичности реализуются такие технологические процессы, как, например, бесфильерное волочение, газостатическая формовка, термоупругая штамповка, которые вообще не нуждаются в прессовом оборудовании. Малые удельные усилия при деформировании в состоянии сверхпластичности способствуют существенному увеличению стойкости штампованного инструмента и позволяют заметно уменьшить его стоимость.
Улучшение ряда показателей качества готовой продукции. Повышенная текучесть и малые удельные усилия при штамповке сверхпластичных материалов способствуют более качественному воспроизведению формы ручья штампа, повышению точности размеров и чистоты поверхности поковок, уменьшению разброса размеров в пределах партии поковок. Высокая способность к релаксации напряжений материалов в состоянии сверхпластичности практически исключает внутренние напряжения в изделиях, а это, в свою очередь, обеспечивает стабильность размеров и формы готовых деталей, повышенную стойкость металла детали против коррозии в химически активных средах, исключает коробления в процессе и после термообработки и т.д. И наконец, отсутствие существенных изменений структуры материала заготовки в процессе сверхпластической деформации обеспечивает получение высококачественных штампованных поковок, изотропных в отношении структуры и механических свойств.
6.2. Технологические процессы штамповки металлов в состоянии сверхпластичности
Наиболее часто сверхпластичность используется в технологии объемной штамповки. В этом случае состояние сверхпластичности позволяет осуществить штамповку точных поковок сложной формы и больших размеров из малопластичных материалов при весьма малых условиях деформации. В отличие от кованых поковок, а также от штампованных поковок обычной точности (рис. 19), требующих значительной обработки резанием по всей поверхности, точные штампованные поковки не надо обрабатывать, за исключением мест сопряжения и участков, в которых предусмотрено сверление или вырубка отверстий. При штамповке точечных поковок обеспечиваются жесткие допуски и минимальные радиусы закружений, штамповочные уклоны не превышают 1,75*10-2 рад. В результате при штамповке точечных поковок получают наибольший коэффициент использования металла (КИМ) 0,8 и более (у поковок обычной точности КИМ в среднем равен 0,2-0,5), что очень важно при изготовлении деталей из дорогостоящих металлов и сплавов.
Один из первых вариантов использования состояния сверхпластичности для получения объемных деталей сложной формы возник, как аналогия обработки материалов, относящихся к вязким жидкостям. Схема этого процесса (рис. 20) напоминает литье в металлическую форму под давлением. Процесс заключается в выдавливании цилиндрической заготовки 1 через соответствующие каналы 2 в полости ручьев штампа 3. Этот процесс, позволяющий получать детали неограниченно сложной формы, возможен исключительно для сверхпластичных материалов, таких, как сплавы Zn - 22% Al; Al - 33% Cu; Al - 13% Si. Однако классические сверхпластичные сплавы не нашли пока широкого промышленного применения, поэтому более перспективными выглядят процессы обработки давлением промышленных сплавов в температурно-скоростном режиме сверхпластичности. Наиболее значительные успехи в этой области достигнуты при штамповке поковок сложной формы в изотропных условиях из титановых сплавов.
Рис. 19. Контуры поковки, полученной различными способами: a - ковкой; б - черновой (предварительной) штамповкой; в - штамповкой обычной точности; г - точной штамповкой
Рис. 20. Комбинированный процесс выдавливание - штамповка: а - штампы; б - готовая деталь
cyberpedia.su
Технология штамповки деталей из листового металла. Оборудование |
Изготовление деталей с помощью штамповки занимает ведущее место в технологии обработки металлов давлением и используется в разных отраслях промышленности.
Особое значение имеет штамповка металлических изделий из листового проката. В ее основе лежит пластическое деформирование металла без его нагрева с помощью специальных штампов. Такой способ пластической деформации деталей широко применяется для изготовления деталей разных размеров и сложных форм с большой точностью, что невозможно осуществить с помощью других способов обработки.
Они используются для сборки крупногабаритных изделий машиностроительной отрасли, в автомобилестроении и судостроении, а также в приборостроительной сфере и быту, где часто требуются различные миниатюрные детали.
Технология штамповки деталей из металлических листов и ее виды
Штамповкой называют процесс придания деталям нужной формы и получение определенного документами размера путем механического воздействия на них с помощью давления. Основное направление штамповки – это производство деталей из заготовок, в качестве которых используется листовой прокат. Под действием сдавливающего усилия заготовка подвергается деформации и приобретает нужную конфигурацию.
Различают штамповку, выполненную горячим способом с нагревом заготовки и холодным способом без ее предварительного нагрева. Штамповка деталей из листового металла осуществляется без их предварительного нагрева.
Деформацию давлением с нагревом заготовки используют при изготовлении деталей из металла, не обладающего достаточной пластичностью, и в основном применяют при производстве небольших партий объемных изделий из металлического листа, имеющего толщину в пределах 5 миллиметров.
Технологический процесс горячей штамповки металла во многом совпадает с последовательностью операций холодной обработки заготовок. Отличие состоит в предварительном нагреве исходных заготовок в печах до температуры, обеспечивающей пластичность металла. При этом учитывается степень коробления детали при остывании, а также ее утяжка при деформационной обработке, влияющая на ее размер. Чтобы исключить отклонения от требуемых размеров для деталей, полученных горячей штамповкой, делают большие допуски.
Видео:
При производстве штампованных деталей из листового металла в основном используют метод холодной штамповки.
Холодная штамповка листового металла
Технология холодной деформации листового проката с помощью штампов подразумевает изменение формы и размеров изделия с сохранением их первоначальной толщины.
В качестве материала для получения штампованных изделий холодным способом используют полосы, листы или тонкую ленту в основном из низкоуглеродистых и легированных пластичных сталей, а также медных, латунных (содержащих свыше 60% меди), алюминиевых, магниевых, титановых и других пластичных сплавов. Применение для штамповки сплавов, обладающих хорошей пластичностью, связано с тем, что они легко поддаются деформационному изменению.
Для осуществления холодной штамповки листового металла используют различные операции, которые зависят от поставленной задачи достижения определенной формы заготовки. Их подразделяют на разделительные и формоизменяющие воздействия.
1. При разделительных деформациях материал заготовки частично отделяют по заданному контуру. Отделение осуществляется путем сдвига части металла по отношению к основной заготовке. Такими операциями являются резка, вырубка, пробивка и другие.
Рассмотрим, как осуществляются некоторые операции разделительного характера.
Резка
При проведении резки от детали отделяется определенная часть путем ее разрезания по фигурной или прямой линии. Такая разделительная операция выполняется с помощью пресса, выполненного в виде ножниц разной конструкции.
Такая операция предназначена в основном для подготовки заготовки к другим способам обработки.
Пробивка
Операцию, называемой пробивкой, используют для создания в заготовке отверстия разной формы. Часть металла при пробивке из заготовки удаляется совсем, и ее вес уменьшается.
На рисунке показана схема процесса пробивки.
Вырубка
С помощью процесса вырубки металлической детали придают готовый вид изделия, имеющего замкнутый контур.
На рисунке показана схема изготовления детали с помощью вырубки.
2. Формообразующие деформации включают изменение формы и размеров изделия при перемещении его отдельных областей, не приводящем к его общему разрушению. К ним относят вытяжку, гибку, рельефную формовку, скручивание, обжим и другие операции.
Рассмотрим некоторые виды операций, не приводящие к физическому разрушению формы.
Вытяжка
С помощью вытяжки из листовых плоских заготовок получают полые объемные изделия. Например, таким способом изготавливают детали, имеющие форму полусферы, цилиндра, конуса, куба и других видов. На рисунке показаны разные варианты выполнения вытяжки.
Гибка
С помощью операции гибки листовому изделию придается заданная форма его изгиба. В зависимости от вида гибки такая операция дает возможность получать изогнутые изделия разной конфигурации. Некоторые из них показаны на рисунке.
Рельефная формовка
Этот вид операции подразумевает видоизменение локальных частей изделия, его внешняя конфигурация остается без изменения. На рисунке изображена схемы некоторых операций формовки:
Возможно также применение комбинированных операций, включающих разделение и формообразование одной детали.
Технологический процесс проведения холодной штамповки состоит из этапов, которые связаны с характером деформационной операции и зависят от вида используемого штампового оборудования.
Разработка техпроцесса проводится в следующей последовательности:
- Обозначается структура основных операций, включающая их характер, количество и последовательность выполнения.
- Выполняется расчет первоначальных, промежуточных и готовых размеров детали, а также необходимых деформационных усилий для достижения нужного результата.
- Проводится документальное оформление технологического процесса.
В техпроцесс могут быть внесены дополнительные операции, с помощью которых заготовка приводится к виду, удобному для обработки. К ним относятся очистка, правка листов, нанесение смазки и другие операции.
Видео:
Штамповочный пресс для металла
Все операции холодной штамповки можно осуществлять при наличии специального оборудования, главным из которых является штамповочный пресс. Его устройство может быть на основе механики, либо с использованием гидравлики.
К механическим видам относят:
- эксцентриковые прессы;
- прессы с использованием кривошипно-шатунного механизма.
Для осуществления операций пробивки, вырубки и вытяжка используется штамповочный пресс кривошипного типа.
Устройство и принцип работы пресса кривошипного типа
Любой пресс, предназначенный для штамповки изделий, включает основные узлы, к которым относится: механизм, приводящий его в действие и устройство, осуществляющее непосредственную штамповку.
Действующий механизм – это кривошипный вал, который приводится в движение с помощью электропривода. Для этого электродвигатель при вращении маховика передает вращение кривошипному механизму с помощью зубчатой передачи.
Совершая возвратно-поступательные действия, ползун кривошипа приводит в работу штамповое устройство, которое с усилием давления осуществляет пластическую деформацию.
Основные детали такого пресса выполнены из высокопрочных сталей и дополнительно укреплены с целью придания необходимой жесткости.
Видео:
Устройство гидравлического пресса
Штамповочный пресс для металла гидравлического типа применяется для создания объемных форм с помощью продавливания металла.
Принцип действия такого механизма основан на давлении жидкости, помещенной в двух резервуарах, которые снабжены поршнями. Резервуары соединены трубопроводом. В результате давления в жидкости, возникающего в момент ее нагнетания в цилиндр из другого резервуара, оно передается на ползун и приводит его в движение. При перемещении ползун с большим усилием продавливает заготовку.
Видео:
Изготовление штампов для холодной штамповки металла
Рабочим устройством любого прессового станка является сам штамп. Он включает две рабочие части, называемые матрицей и пуансоном. В процессе работы подвижной является только верхняя деталь штампа – пуансон, закрепленный на ползуне. Матрица расположена снизу и остается неподвижной.
Деформирование листа осуществляется во время прижимания пуансона к матрице с расположенной на ней заготовкой.
Разработке чертежей и изготовлению штампов для пресса предъявляются повышенные требования, т. к. от их точности зависит правильность формирования изделия.
Выполняются такие работы поэтапно в следующей последовательности:
- составляется эскиз штампа;
- с помощью компьютерной схемы штампа, составленной по специальной программе, проводится проверка рационального раскроя материала;
- при необходимости эскиз корректируется, и уточняются размеры штампа;
- обозначаются места расположения отверстий и их размеры, которые затем будут нанесены на поверхность штампа;
- после окончательного согласования чертежей приступают к изготовлению самого штампа.
Видео:
Современные станки для штамповки изделий оснащены штампами, изготовленными с большой точностью при помощи компьютерных технологических программ.
Источник
stroymaster-base.ru
Листовая штамповка металлов на СЗХИ

Листовая штамповка
Листовая штамповка – способ производства самых разных изделий (плоские, объемные, тонкостенные) применяют при этом в виде сырья листовой металл, а производство происходит с помощью штампов на прессах или без их применения. Листовая штамповка подразделяется всего на две категории: горячая штамповка и холодная штамповка.
Горячая штамповка
Наиболее распространена при производстве котельных днищ, полушариев, буев и многих других деталей для судостроения, в основном это детали корпуса судов. Сырьем для таких деталей служит стальной лист толщиной от 3х до 4х миллиметров. Горячая штамповка по многом схожа с штамповкой холодной. Но, следует учитывать, что в случае с горячей штамповкой необходимо учитывать нагрев металла. Также, составляя чертежную документацию необходимо помнить, что металл утягивается при вырубке, пробивке и гибке. К тому же нужно учитывать степень короблении при остывании детали, так как ее размеры уменьшаются. Это делает необходимым увеличение допусков на размеры, в сравнении с холодной штамповкой. Нагрев заготовок осуществляют в пламенных и электрических печах.
Холодная штамповка
Холодная штамповка – более распространенный и продуктивный метод обработки металла по отношению к горячей штамповке. При обработке металла холодной штамповкой возможно получить как крупные, так и мелкие детали (от шестеренок для наручных часов, до кузовных частей автомобиля или даже обшивки и шасси самолетов).
Холодная листовая штамповка позволяет сократить количество отходов от заготовки, сочетая это с весьма высокой производительностью. Но наибольшую эффективность можно извлечь при массовом крупносерийном производстве.
В холодном, листовом штамповании используются: легированная и углеродистая сталь, аллюминий и его сплавы, а также сплавы меди. Также используются неметаллические материалы: картон, кожа, эбонит, резина, фибра, пластмасс.
Технология листовой штамповки.
Наиболее востребованным для осуществления холодной штамповки технологическим оборудованием являются: кривошипные прессы, гидравлические прессы и вибрационные ножницы. Операции холодного штампования делятся на 2 основных вида: разделительные и формоизменяющие. К основным разделительным операциям относятся: резка металла, вырубка металла и пробивка металла.
Резка металла – технологический процесс, при котором происходит отделение металла по заранее немеченой траектории (по прямой, по волнистой или иной траектории обозначенной тех заданием). Резку металла применяют как для получения готовых деталей, так и для раскроя заготовки на полосы или листы. При правильном раскрое листа необходимо максимально продуктивно использовать заготовочный материал, чтобы отходов от производства оставалось меньше, а производимых деталей было больше. Правильность раскроя металла определяется путем подсчета коэффициента использования материала заготовки. Коэффициент – количество вырубленных деталей на м2 материала. Резку металла осуществляют с помощью вибрационных, гильотинных или дисковых ножниц.
Вырубка — операция по получению заготовки замкнутого контура.
К основным формоизменяющим операциям относят гибку, вытяжку, отбортовку, обжим и формовку.
Листовая холодная штамповка |
Формоизменяющие операции |
Растяжка металла |
Рельефная формовка металла |
Отбортовка отверстий металла |
Отбортовка контура металла |
Обжатие металла |
Исправление металла |
Выдавливание металла |
Гибка – воздействие на металл, при котором плоской заготовке придают изогнутую форму.
Вытяжка – операция, при помощи которой плоскую заготовку преобразуют в полуфабрикат. При помощи вытяжки производят не только цилиндрические, но и более сложные детали. Для того, чтобы избежать образования складок на заготовке используют зажимы.
Отбортовка — операция образования бортов по наружному контуру листовой заготовки или вокруг заранее пробитых отверстий. Она применяется главным образом для образования горловин у плоских деталей, необходимых как для нарезания резьбы, так и сварки или сборки. Обычно она выполняется последовательно (I, II, III) за один или несколько проходов в штампах, состоящих из пуансона и матрицы. Операцию отбортовки очень часто выполняют на концах труб при подсоединении к ним фланцев, с помощью которых трубы будут в дальнейшем соединяться.
Обжим — операция сужения (уменьшения) концевой части полых или объемных деталей. Осуществляется она путем обжатия материала штампом снаружи в конической матрице. При этом конфигурация обжимаемой части целиком зависит от формы штампа.
Формовка — операция, связанная с местным изменением формы с сохранением конфигурации наружного контура детали. Примером формовки может служить изготовление ребер жесткости на машиностроительных деталях, а также увеличение размеров по диаметру средней части полой детали.
Технологический процесс обработки различных материалов давлением, как упоминалось выше, производят на прессах. Прессы бывают гидравлические и механические (кривошипные, винтовые, реечные и т. д.). По назначению прессы подразделяют на ковочные, штамповочные, листоштамповочные, чеканочные, обрезные, трубопрофильные, гибочные, правильные, брикетировочные (для изготовления брикетов из кусковатых или порошкообразных материалов), кузнечно-штамповочные автоматы, термопластавтоматы и др.
Кривошипные горячештамповочные прессы ГОСТ 680987Е изготавливаются в России давлением от 61,78 до 617,8 кН (mc — единица силы и веса). Они состоят из станины, ползуна, шатуна, кривошипного вала, стажных колонн, зубчатого колеса 6 и фрикционной муфты. Применение прессов для горячей объемной штамповки очень эффективно в сравнении с другим технологическим оборудованием. Они обеспечивают более высокую точность поковок при значительной экономии металла. Наличие в них индукционного электрического нагрева способствует улучшению условий труда в цехе: уменьшаются шум и сотрясение здания, устраняется задымленность производственных помещений. Управление прессом осуществляется органами регулирования и с помощью сжатого воздуха из цеховой магистрали.
Гидравлические прессы обладают наилучшей характеристикой для глубокой вытяжки и других операций листовой штамповки, так как осуществляют деформирование металла с постоянной скоростью. Подобные прессы широко применяют в авиационной и ракетостроительной промышленности.
Прогрессивные способы холодной листовой штамповки. Новые, виды штамповки благодаря своей простоте и экономичности находят широкое применение в условиях мелкосерийного и единичного производства. К ним относят штамповку резиной, жидкостью, взрывом, электрогидравлическую и др.
Штамповка резиной. С ее помощью осуществляются разделительные и формоизменяющие операции. При этом пуансоном или матрицей является резина. Штамповку резиной чаще всего применяют для изделий из тонколистового металла толщиной до 2 мм (алюминия, медных сплавов, малоуглеродистой стали).
Штамповка жидкостью. В этом случае металл деформируется под давлением жидкости, принимая форму матрицы. Данный способ применяют для вытяжки полых деталей разной формы.
Штамповка взрывом. Для пластического формоизменения заготовки применяют и взрывчатые вещества (взрывчатые газовые смеси из метана, пропана, гиксогена и др.), создающие высокое давление, под действием которого заготовка принимает форму штампа.
Штамповку взрывом применяют для изготовления крупных деталей и деталей сложной формы, когда изготовление их другими способами невозможно (например, сплавы труднодеформируемые) или неэкономично. Такая штамповка не требует сложного и дорогостоящего оборудования.
Электрогидравлическая штамповка. Этот метод характерен тем, что энергоносителем является высоковольтный электрический заряд в жидкости. Разряд вызывает появление ударной волны, которая и деформирует заготовку, придавая ей необходимую форму.
Этот вид штамповки дает возможность выполнять все операции холодной листовой штамповки с большой точностью и с сравнительно малыми затратами.
Магнитноимпульсная формовка. Формирование изделий этим методом происходит при создании импульсного магнитного поля вокруг заготовки и взаимодействия этого поля с импульсными токами, протекающими в заготовке. В результате такого взаимодействия в заготовке возбуждаются вихревые токи, что приводит к образованию вокруг нее также электромагнитного поля. Это создает предпосылки для динамического воздействия на заготовку и ее деформирование.
Этим методом осуществляют обжатие трубных заготовок, рельефную формовку, вырубку и др.
szhi.ru