Ультразвуковой дефектоскоп для контроля сварных соединений. Ультразвуковой контроль сварных соединений
Ультразвуковой контроль сварных соединений
Сварные соединения являются новообразованиями на любых конструкциях и их дальнейшая безопасная эксплуатация во многом зависит от качества их наложения, а это, в свою очередь, можно выявить только специальной проверкой. Качество сварных швов металлических соединений проверяют, используя для этого различные методики дефектоскопии. Из всего существующего на сегодняшний день разнообразия видов дефектоскопии можно выделить ультразвуковой контроль сварных соединений, который является наиболее доступным и недорогим методом диагностики. Причем УЗК практически не уступает по точности измерений таким видам неразрушающего контроля, как рентгеноскопия, гамма-скопия, радиоскопия и другим.
Теоретическое определение УЗК
Методика ультразвукового неразрушающего контроля является далеко не новым видом дефектоскопии и впервые была применена на практике в 1928 году, а с развитием технического прогресса и промышленных технологий стала использоваться во многих сферах деятельности человека.

Весь эффект УЗК основан на том, что акустические ультразвуковые волны при прохождении однородной среды не меняют свою прямолинейную траекторию движения, а вот при разделе сред, имеющих различную структуру и обладающих разными величинами удельного акустического сопротивления, происходит их частичное отражение. При этом чем существеннее разница в физических и химических свойствах материалов, тем больше будет звуковое сопротивление в месте раздела сред, тем ощутимее и заметнее эффект при отражении звуковых волн.
К примеру, при образовании сварного шва в структуре металла обычно остается смесь газов, которая не успела выйти во время затвердевания наружу. При этом газообразная среда обладает фактически в пять раз меньшим волновым сопротивлением прохождению ультразвуковых колебаний, чем металлическая кристаллическая решетка, что и позволяет практически полностью отражаться ультразвуковым колебаниям.
Ультразвуковой контроль, либо дефектоскопия сварных соединений являются неразрушающим их целостность методом по поиску внутренних структур, имеющих химические или физические отклонения от заданных норм, которые при недопустимой величине и определяются как механические дефекты сварных швов.
Достоинства УЗК
С помощью методики ультразвукового контроля осуществляется диагностика всех видов сварки, пайки и склейки, что позволяет выявлять такие дефекты соединений, как:
- воздушные пустоты и поры,
- расслоения в наплавленном металле шва,
- околошовные трещины,
- химически неоднородные вкрапления,
- шлаковые отложения,
- неоднородность структуры,
- искривление геометрических размеров.
Главными преимуществами ультразвуковой дефектоскопии можно назвать возможность проведения контроля:
- соединений как из однородных, так и из разнородных материалов;
- структур, состоящих как из металлов, так и неметаллов;
- без разрушения и без повреждения исследуемых образцов;
- с высокой мобильностью;
- с высокой скоростью исследований;
- при низкой себестоимости;
- без опасных факторов для персонала в сравнении с рентгено- или радио-дефектоскопией.
Недостатки УЗК
Использование ультразвукового контроля имеет ряд особенностей, а именно — требуется существенная подготовка исследуемых поверхностей для прохождения от пьезоэлектрических преобразователей ультразвуковых волн по структуре металла. Необходимо:
- создание шероховатостей 5 класса на поверхности сварного соединения с направлением полос перпендикулярно шву;
- нанесение на исследуемый участок контактной массы (в виде воды, масел) для полного исключения воздушного зазора, а в случае с вертикальной или при сильнонаклоненной поверхности использовать густые клейстеры, неспособные к быстрому стеканию;
Непосредственно к недостаткам этой методики дефектоскопии можно отнести:
- необходимость в использовании специальных пьезоэлектрических преобразователей, имеющие радиус кривизны подошвы в диапазоне величины +-10% от радиуса исследуемого объекта для диагностики округлых форм конструкцией с диаметром менее 200 мм;
- существенные сложности при исследовании крупнозернистых структур металлов, к примеру, чугуна или аустенита при толщине более 60 мм, связанного со значительным затуханием и с существенным рассеванием ультразвуковых колебаний;
- невозможность проведения контроля деталей с малыми и сложными формами;
- затруднительность в оценке соединений разных видов сталей, что связано с неоднородностью основных металлов и сварного шва;
- невозможность установления реальных размеров различных типов дефектов из-за их формы, физических свойств и расположения в структуре сварного шва.
Виды ультразвукового контроля швов
Технология проведения ультразвуковой дефектоскопии основывается на способности акустических колебаний высокой частоты, порядка 20 кГц, проходить однородную структуру и частично отражаться от различных препятствий в виде пор, трещин и других неоднородностей. Существует несколько методов получения отражения ультразвукового сигнала, а именно:
- теневой, который определяет разницу амплитуды между прошедшими и отраженными колебаниями;
- зеркально-теневой, основанный на определении коэффициента затухания отраженных волн;
- эхо-зеркальный или тандемный, использующий для своей работы два аппарата;
- дельта метод, заключающейся в определении энергии отраженных от дефекта колебаний;
- эхо-импульсный, который основывается на регистрации отраженных ультразвуковых волн.
Наиболее распространенными являются два вида дефектоскопии сварных швов при помощи ультразвука — это теневая и эхо-импульсная методика проведения контроля.
Методика проведения УЗК
Несмотря на существование нескольких методик ультразвуковой дефектоскопии их проведение практически схоже и различается лишь в наборе диагностического оборудования. Так, проведение процедуры дефектоскопии можно описать следующей последовательностью:
- Производиться тщательная подготовка исследуемой поверхности путем механического удаления остатков шлака, краски и ржавчины со сварочного шва. Вдобавок очищают полосы по 50 мм с обеих сторон от него.
- Место проведения дефектоскопии обильно покрывают жидкой массой в виде воды, минеральных масел или густых специальных клейстеров — это необходимо для возможности беспрепятственного прохождения ультразвуковых волн.
- Производиться предварительная настройка прибора на определенную методику, рассчитанную на решение конкретных задач.
- Пьезоэлектрический преобразователь УЗК последовательно начинают перемещать по зигзагообразной траектории по сварочному шву.
- После получения устойчивого сигнала необходимо периодически поворачивать пьезоэлектрический преобразователь в разные стороны вокруг своей оси так, чтобы получить на экране прибора сигнал с максимальной четкостью изображения.
- При обнаружении дефектов их фиксируют и записывают соответствующие координаты.
- При необходимости, ультразвуковой контроль сварных швов проводят в один или несколько проходов.
- Полученные результаты дефектоскопии заносятся в журнал проверки.
wikimetall.ru
Ультразвуковая дефектоскопия УЗК сварных швов и соединений
Во время сваривания металлических деталей подбирается правильный режим, специальные расходные материалы, добавочные предметы, улучшающие свойства сваривания, а также сама технология. Но это все равно полностью не защищает от возможного появления брака. Если появился заметный дефект, то это еще не так страшно, потому как часто встречаются скрытые поры, трещины, раковины и прочее. Чтобы их обнаружить, требуются особые методы, одним из которых является ультразвуковая дефектоскопия сварных швов. Как понятно из названия, здесь используются ультразвуковые волны, а точнее, их принцип отражения от границ поверхностей с различным уровнем плотности.

Ультразвуковая дефектоскопия сварных швов
Такой метод является очень распространенным и набрал большие обороты популярности. Сейчас встречаются такие приборы, которые могут проводить анализ не только в качестве стационарной установки, но и как мобильные устройства. Это позволяет проводить контроль практически в любом удобном месте. Но для проведения анализа необходимо иметь определенные знания, так далеко не каждый человек сможет правильно расшифровать полученные сигналы. Ультразвуковой контроль сварных швов проходит по ГОСТ 14782-86.

Контроль сварных швов
Преимущества 
- Это очень распространенный и недорогой способ неразрушающего контроля сварных швов;
- Скорость проведения является достаточно высокой и результатов не придется долго ждать;
- Безопасность для здоровья человека;
- Исследуемую деталь не нужно отделять от всей конструкции;
- Есть много вариантов приборов для проведения процедуры;
- Можно подвергать анализу достаточно широкие области изделия;
- Помогает точно определить место, где находится тот или иной дефект, а также его характер.
Недостатки 
- Для использования прибора необходим специалист, который сможет правильно расшифровать полученные данные;
- Затруднительно проводить анализ при большой толщине детали;
- Нет высокого уровня точности, которые дают некоторые другие разновидности контроля.
Теория акустической технологии
Проверка сварных швов ультразвуком основана на свойствах ультразвука. Стоит сразу отметить, что человеческое ухо не ловит такие волны. Для его распространения, а также последующего считывания требуется специальный ультразвуковой дефектоскоп для контроля сварных соединений. Благодаря тому, что звук не слышно, он стал использоваться в самых различных методах, а не только в сфере сварки. Практически ни в какой из областей ультразвуковые волны не наносят вреда исследуемому объекту во время контроля. Он помогает локализовать дефекты, даже если речь идет об относительно небольших участках, но все это зависит от размеров и особенностей самого прибора.

Ультразвуковой дефектоскоп
Чтобы определить, насколько качественно пройдет УЗК сварных швов, требуется учитывать такие факторы как чувствительность приборов, калибровка и правильность настройки, опыта оператора и прочего. В данной области УЗК помогает определиться, подходит ли то или иное изделие по допускам, которые выдвигаются к швам в конкретном случае, так как иногда небольшие дефекты все же допускаются.
Особенности проведения данной процедуры 
Проверка сварных швов ультразвуком хоть и обладает универсальностью применения, в ней все же есть определенные ограничения. При правильном применении и качественной настройке техника даст полное представление об имеющемся дефекте. Но здесь встречаются следующие рамки:
Выявляемые дефекты:
- Поры;
- Области, где имеется искаженный геометрический размер;
- Непроваренные участки шва;
- Участки с инородным химическим составом;
- Трещины в зоне около шва;
- Расслоение наплавленного металла;
- Зоны, в которых имеется ржавчина;
- Наслоение шва и несплошности;
- Провисание частей металла снизу шва;
- Свищи.
Подробные данные ультразвуковое исследование сварных швов может обеспечить в следующих разновидностях металлов:
- Медь и ее сплавы;
- Легированная сталь;
- Чугун;
- Аустенитная сталь;
- Металл с плохими свойствами проведения ультразвука.
Геометрические рамки проведения процесса:
- Максимальная толщина металла, с которой ведется работа – 500-800 мм;
- Минимальная толщина металла, с которой ведется работа 8-10мм;
- Максимальная глубина, на которой может находиться шов для распознания его нюансов – 10 метров;
- Минимальная глубина, на которой может находиться шов для распознания его нюансов – 3 мм.
Стоит отметить, что все данные зависят от марки прибора и могут иметь некоторые отличия.
К проверке пригодны следующие виды сварных соединений и швов:
- Сваренные трубы;
- Тавровые соединения;
- Стыковые соединения;
- Кольцевые швы;
- Продольные;
- Плоские швы.
Устройство дефектоскопа 
В качестве одного из компонентов здесь имеется генератор электроимпульсов. Он создает сигналы, которые потом подаются на преобразователь. Во время анализ обращен к образцу, чтобы звуковой испульс попал именно на него. Когда волна будет возвращаться от столкновения с поверхностью, то она попадает на преобразователь, который передает сигнал на усилитель. Затем его принимает электронно-лучевая трубка, соединенная с генератором развертки.

Дефектоскоп для ультразвуковой проверки сварных швов
Принцип работы 
Проверка сварочных швов ультразвуком основана на том, что звуковые волны отражаются от плотных поверхностей при столкновении с ними. Когда волна проходит сквозь шов в котором есть трещины, то на переходе между границей металла и воздуха будет еще одно отражение волны звука. Оно придет раньше, чем отражение от перехода на нижней грани. Преобразователь сможет уловить не только разницу во времени, но и локализовать место нахождения дефекта. Усилитель, который передает сигнал на трубку, помогает построить график, по которому специалист сможет определить все особенности проверяемого шва.
Методика
УЗК контроль сварных соединений проводится по следующему методу:
- Сначала подготавливается металл, с которого убирается шлак, ржавчина и краска в области около 10 см диаметром;
- Чистая поверхность металла обрабатывается машинным или трансформаторным малом, чтобы улучшить прохождение сигнала;
- Устройство настраивают согласно заданному стандарту, относительно параметров металла и способа обнаружения (при толщине до 2 см используются стандартные настройки, а если выше, то нудна настройка АРД-диаграмм).;
- Искатель перемещается зигзагообразно вдоль исследуемой поверхности шва, с поворотом около 15 градусов;
- Если проявляется устойчивый сигнал на экране устройства, то искатель нужно максимально развернуть;
- Поиск проводится до тех пор, пока на дисплее не появится сигнал, у которого имеется максимальная амплитуда
- По ГОСТ ультразвуковой контроль сварных швов проводится два раза;
- Если работа ведется с тавровыми швами, то они проверяются эхо-методом;
- После результатов проверки создается таблица данных, по которой можно будет легко найти обнаруженные дефекты.
«Важно!
При выявлении колебаний дефекта нужно проверить все несколько раз, чтобы убедиться в точности предположения, после чего можно фиксировать дефект.»
Меры по технике безопасности
Дефектоскопия сварных швов ультразвуком является достаточно безопасной процедурой, при которой нужно соблюдать правила электробезопасности и инструкции того места, где проводится сам процесс.
svarkaipayka.ru
Ультразвуковой метод контроля качества сварных соединений
Рекомендуем приобрести:
Установки для автоматической сварки продольных швов обечаек - в наличии на складе! Высокая производительность, удобство, простота в управлении и надежность в эксплуатации.
Сварочные экраны и защитные шторки - в наличии на складе! Защита от излучения при сварке и резке. Большой выбор. Доставка по всей России!
Свойства ультразвуковых волн
Метод ультразвуковой дефектоскопии металлов и других материалов впервые был разработан и практически осуществлен в Советском Союзе в 1928—1930 гг. проф. С. Я. Соколовым.
Ультразвуковые волны представляют собой упругие колебания материальной среды, частота которых лежит за пределами слышимости в диапазоне от 20 кгц (волны низкой частоты) до 500 Мгц (волны высокой частоты).
Ультразвуковые колебания бывают продольные и поперечные. Если частицы среды перемещаются параллельно направлению распространения волны, то такая волна является продольной, если перпендикулярно-поперечной. Для отыскания дефектов в сварных швах используют в основном поперечные волны, направленные под углом к поверхности свариваемых деталей.
Ультразвуковые волны способны проникать в материальные среды на большую глубину, преломляясь и отражаясь при попадании на границу двух материалов с различной звуковой проницаемостью. Именно эта способность ультразвуковых волн используется в ультразвуковой дефектоскопии сварных соединений.
Ультразвуковые колебания могут распространяться в самых различных средах — воздухе, газах, дереве, металле, жидкостях.
Скорость распространения ультразвуковых волн C определяют по формуле:
C = fλ
где f — частота колебаний, гц;λ — длина волны, см.
Для выявления мелких дефектов в сварных швах следует пользоваться коротковолновыми ультразвуковыми колебаниями, так как волна, длина которой больше размера дефекта, может не выявить его.
Получение ультразвуковых волн
Ультразвуковые волны получают механическим, термическим, магнитострикционным (Магнитострикция — изменение размеров тела при намагничивании) и пьезоэлектрическим (Приставка «пьезо» означает «давить») способами.
Наиболее распространенным является последний способ, основанный на пьезоэлектрическом эффекте некоторых кристаллов (кварца, сегнетовой соли, титаната бария): если противоположные грани пластинки, вырезанной из кристалла, заряжать разноименным электричеством с частотой выше 20 000 гц, то в такт изменениям знаков зарядов пластинка будет вибрировать, передавая механические колебания в окружающую среду в виде ультразвуковой волны. Таким образом электрические колебания преобразовываются в механические.
В различных системах ультразвуковых дефектоскопов применяют генераторы высокой частоты, задающие на пьезоэлектрические пластинки электрические колебания от сотен тысяч до нескольких миллионов герц.
Пьезоэлектрические пластинки могут служить не только излучателями, но и приемниками ультразвука. В этом случае под действием ультразвуковых волн на гранях кристаллов-приемников возникают электрические заряды малой величины, которые регистрируются специальными усилительными устройствами.
Методы выявления дефектов ультразвуком
Существуют в основном два метода ультразвуковой дефектоскопии: теневой и эхо-импульсный (метод отраженных колебаний.)
Рис. 41. Схемы проведения ультразвуковой дефектоскопииа — теневым; б — эхо импульсным методом; 1 — щуп-излучатель; 2 — исследуемая деталь; 3 — щуп приемник; 4 — дефект
При теневом методе (рис. 41, а) ультразвуковые волны, идущие через сварной шов от источника ультразвуковых колебаний (щупа-излучателя), при встрече с дефектом не проникают через него, так как граница дефекта является границей двух разнородных сред (металл — шлак или металл — газ). За дефектом образуется область так называемой «звуковой тени». Интенсивность ультразвуковых колебаний, принятых щупом-приемником, резко падает, а изменение величины импульсов на экране электронно-лучевой трубки дефектоскопа указывает на наличие дефектов. Этот метод имеет ограниченное применение, так как необходим двусторонний доступ к шву, а в ряде случаев требуется снимать усиление шва.
При эхо-импульсном методе (рис. 41,6) щуп-излучатель посылает через сварной шов импульсы ультразвуковых волн, которые при встрече с дефектом отражаются от него и улавливаются щупом-приемником. Эти импульсы фиксируются на экране электроннолучевой трубки дефектоскопа в виде пиков, свидетельствующих о наличии дефекта. Измеряя время от момента посылки импульса до приема обратного сигнала, можно определить и глубину залегания дефектов. Основное достоинство этого метода состоит в том, что контроль можно проводить при одностороннем доступе к сварному шву без снятия усиления или предварительной обработки шва. Этот метод получил наибольшее применение при ультразвуковой дефектоскопии сварных швов.
Импульсные ультразвуковые дефектоскопы
Контроль сварных соединений осуществляется при помощи ультразвуковых дефектоскопов, которыми можно выявлять трещины» непровары, газовые и шлаковые включения в стыковых, угловых, тавровых и нахлесточных соединениях, выполненных дуговой, электрошлаковой, газовой и контактной сваркой. Контролировать можно как сварку сталей, так и сварку цветных металлов и их сплавов.
Электрическая схема дефектоскопов, состоящая из отдельных электронных блоков, смонтирована в металлическом кожухе, на передней панели которого находится экран электроннолучевой трубки и расположены рукоятки управления. Дефектоскопы укомплектованы призматическими щупами-искателями (рис. 42) с углами ввода ультразвукового луча 30, 40 и 50° (0,53; 0,7 и 0,88 рад). Придаются также и прямые щупы, при помощи которых ультразвуковые колебания вводятся перпендикулярно поверхности контролируемого изделия. Комплект щупов позволяет выбирать для каждого конкретного случая необходимую схему прозвучивания. Во всех щупах в качестве пьезоэлектрического преобразователя используются пластинки титаната бария.
Рис. 42. Конструктивная схема призматического щупа1 — кольцо изоляционное; 2 — асбестовая прокладка; 3 — накладка контактная; 4 — втулка изоляционная; 5 — втулка; 6 — пластинка из титаната бария; 7 — корпус;8 — призма из плексигласа
В зависимости от количества щупов и схемы их включения ультразвуковые дефектоскопы могут быть двухщуповыми, в которых один щуп является излучателем, а другой приемником, или однощуповыми, где функция ввода и приема ультразвуковых колебаний выполняются одним щупом. Это возможно потому, что прием отраженного сигнала происходит во время пауз между импульсами, когда никаких других сигналов, кроме отраженных, на пьезоэлектрическую пластинку не поступает.
В качестве индикаторов дефектов применяются электроннолучевые трубки. Ряд дефектоскопов оснащен также световым (электрической лампочкой на искательной головке щупа) и звуковым (динамиком и телефонными наушниками) индикаторами.
Типовая блок-схема импульсного ультразвукового дефектоскопа, работающего по однощуповой схеме, приведена на рис. 43.
Рис. 43. Блок-схема импульсного ультразвукового дефектоскопа УЗД-7Н1 — задающий генератор; 2 — генератор импульсов; 3 — пьезоэлектрический щуп; 4 — генератор развертки; 5 — приемный усилитель; 6 — электроннолучевая трубка; 7 — контролируемое изделие
Задающий генератор, питаемый переменным током, вырабатывает электрические колебания, передаваемые на генератор импульсов и пьезоэлектрический щуп. В последнем высокочастотные электрические колебания преобразуются в механические колебания ультразвуковой частоты и посылаются в контролируемое изделие. В интервалах между отдельными посылами высокочастотных импульсов пьезоэлектрический щуп при помощи электронного коммутатора подключается к приемному усилителю, который усиливает полученные от щупа отраженные колебания и направляет их на экран электроннолучевой трубки. Таким образом, пьезоэлектрический щуп попеременно работает как излучатель и приемник ультразвуковых волн.Генератор развертки обеспечивает развертку электронного луча трубки, который прочерчивает на экране электроннолучевой трубки светящуюся линию с пиком начального импульса.
При отсутствии дефекта в контролируемом изделии импульс дойдет до нижней поверхности изделия, отразится от нее и возвратится в пьезоэлектрический щуп. В нем механические колебания ультразвуковой частоты снова преобразуются в высокочастотные электрические колебания, усиливаются в приемном усилителе и подаются на отклоняющие пластины электроннолучевой трубки. При этом на экране возникает второй пик донного импульса (как бы отраженного от дна изделия).
Если на пути прохождения ультразвука встретится дефект, то часть волн отразится от него раньше, чем донный сигнал достигнет пьезоэлектрического щупа. Эта часть волн усиливается приемным усилителем, подается на электроннолучевую трубку и на ее экране между начальным и донным импульсами возникнет пик импульса от дефекта.
Благодаря синхронной работе генератора развертки луча, генератора импульсов и других устройств дефектоскопа взаимное расположение импульсов на экране электроннолучевой трубки характеризует глубину расположения дефекта. Расположив на экране трубки масштабные метки времени, можно сравнительно точно определить глубину залегания дефекта.
Методика ультразвукового контроля
Перед началом ультразвукового контроля зачищают поверхность сварного соединения на расстоянии 50—80 мм с каждой стороны шва, удаляя брызги металла, остатки шлака и окалину. Зачистку выполняют ручной шлифовальной машинкой, а при необходимости еще и напильником или наждачной шкуркой.
Чтобы обеспечить акустический контакт между щупом-искателем и изделием, зачищенную поверхность металла непосредственно перед контролем тщательно протирают и наносят на нее слой контактной смазки. В качестве смазки применяют автол марок 6, 10, 18, компрессорное, трансформаторное или машинное масло.
Затем проверяют правильность показаний дефектоскопа на эталонах сварных швов с заранее определенными дефектами.
Контроль стыковых соединений проводят путем поочередной установки щупа по обеим сторонам проверяемого шва.
Рис. 44. Схема проведения ультразвукового контроляа — перемещение призматического щупа по поверхности изделия; б — контроль прямым лучом; в — контроль отраженным лучом
В процессе контроля щуп-искатель плавно перемещают вдоль обеих сторон шва по зигзагообразной линии (рис. 44, а), систематически поворачивая его на 5—10° в обе стороны для выявления различно расположенных дефектов.
Прозвучивание производят как прямым (рис. 44, б), так и отраженным (рис. 44, в) лучом. Стыковые соединения при толщине металла более 20 мм обычно проверяют прямым лучом. При толщине металла менее 20 мм усиление шва не дает возможности установить щуп так, чтобы ультразвуковой луч проходил через корень шва. В этих случаях контроль осуществляют однократно или двукратно отраженными лучами. При толщине металла менее 8 мм его прозвучивают многократно отраженным лучом.
Пределы перемещения щупа поперек шва зависят от угла ввода луча и способа прозвучивания и определяются по номограммам, прилагаемым к инструкции на эксплуатацию дефектоскопа. Чтобы обеспечить перемещение щупов в заданных пределах, их устанавливают в специальный держатель (рис. 45).
Рис. 45. Держатели призматических щупова — для контроля стыковых швов отраженным лучом; б — для контроля стыковых швов прямым лучом; в — для контроля угловых швов
Рис. 46. Схема определения размеров дефекта в стыковом швеа — протяженности l; б — высоты h
Рис. 47. Конструктивная схема жидкостного глубиномера1 — генератор дефектоскопа; 2 — цилиндр; 3 — компенсирующий объем; 4 — глубиномер; 5 — механизм перемещения поршня; 6 — жидкость; 7 — поршень; 8 — пьезоэлектрическая пластинка
При обнаружении дефекта в сварном шве на экране дефектоскопа появляется импульс. Условную протяженность его измеряют длиной зоны перемещения щупаискателя вдоль шва, в пределах которой наблюдается появление и исчезнование импульса (рис. 46, а). Условную высоту дефекта определяют как разность глубин, измеренных в крайних положениях щупаискателя, в которых появляется и исчезает импульс при перемещении щупа перпендикулярно оси шва (рис. 46, б). Условную высоту дефектов, имеющих большую протяженность, измеряют в месте, где импульс от дефекта имеет наибольшую амплитуду.
Глубину залегания дефекта определяют при помощи глубиномеров. Жидкостной глубиномер (рис. 47) состоит из пьезоэлектрической пластинки, которая возбуждается от генератора дефектоскопа одновременно с основной излучающей пьезоэлектрической пластинкой щупаискателя. Эта пластинка помещена в цилиндр с компенсирующим объемом. Цилиндр наполнен жидкостью и имеет поршень, связанный со шкалой глубиномера. При прозвучивании сварного шва на экране электроннолучевой трубки вместе с начальным и донным сигналом появляется так называемый служебный импульс, отраженный от поршня цилиндра глубиномера. Положение его на экране трубки дефектоскопа определяется положением поршня в цилиндре. Передвигая поршень, совмещают служебный импульс с импульсом, отраженным от дефекта, и по шкале глубиномера определяют глубину залегания дефекта. При совмещении поршня с донным импульсом можно определить толщину металла. Подобные глубиномеры могут быть присоединены к любому ультразвуковому импульсному дефектоскопу.
Повышения скорости контроля можно достичь применением несложных устройств (рис. 48), позволяющих осуществлять перемещение дефектоскопа вдоль шва и возвратно-поступательное движение щупа. Щуп-искатель устанавливается на тележке устройства и соединяется с ультразвуковым дефектоскопом. На этой же тележке находится механизм передвижения, состоящий из электродвигателя мощностью 12 вт, червячных пар и кривошипного механизма.
Рис. 48. Схема автоматизированного контроля стыков трубопроводов с помощью специального приспособления1 — контрольный механизм; 2 - труба; 3 — роликовая цепь; 4 — коробка со щупом; 5 — ультразвуковой дефектоскоп
Значительно увеличивается надежность и скорость контроля при использовании автоматического ультразвукового дефектоскопа ДАУЗ-169, позволяющего контролировать сварные соединения при толщине листов от 6 до 16 мм. Он представляет собой датчик, установленный на автоматически передвигающейся каретке, соединенной гибким кабелем со шкафом с электронными блоками.
Дефекты регистрируются записью на диаграммной ленте и краскоотметчиком на контролируемом шве, работа которого дублируется световой сигнализацией. Скорость контроля составляет 1 м/мин. Применение его значительно увеличивает надежность и производительность процесса контроля сварных швов.
Оформление результатов контроля
Результаты ультразвуковой дефектоскопии согласно ГОСТ 14782—69 фиксируют в журнале или в заключении, обязательно указывая:
а) тип сварного соединения; индексы, присвоенные данному изделию и сварному соединению; длину проконтролированного участка шва;
б) технические условия, по которым выполнялась дефектоскопия;
в) тип дефектоскопа;
г) частоту ультразвуковых колебаний;
д) угол ввода луча в контролируемый металл или тип искателя, условную или предельную чувствительность;
е) участки шва, которые не подвергались дефектоскопии;
ж) результаты дефектоскопии;
з) дату дефектоскопии;
и) фамилию оператора.
При сокращенном описании результатов дефектоскопии каждую группу дефектов указывают отдельно.
Характеристика протяженности дефекта обозначается одной из букв А, Б, В. Цифрами обозначают: количество дефектов в шт.; условную протяженность дефекта в мм; наибольшую глубину залегания дефекта в мм; наибольшую условную высоту дефекта в мм.
Буква А указывает, что протяженность дефекта не превышает допускаемую техническими условиями. Буква Б используется для характеристики дефекта большей протяженности, чем типа А. Буквой В обозначают группу дефектов, отстоящих друг от друга на расстоянии не более величины условной протяженности для дефектов типа А.
Ниже приводится пример сокращенной записи результатов дефектоскопии в журнале или в заключении.
На участке шва сварного соединения С15 (ГОСТ 5264—69), обозначенном индексом МН-2, длиной 800 мм обнаружены: два дефекта типа А на глубине 12 мм, один дефект типа Б условной протяженностью 16 мм на глубине 14—22 мм, условной высотой 6 мм и один дефект типа В условной протяженностью 25 мм на глубине 5—8 мм.
Сокращенная запись результатов испытания выглядит так:
С15, МН-2, 800; А-2-12; Б-1-16-22-6; В-1-25-8.
Техника безопасности при ультразвуковом контроле
К работе с ультразвуковыми дефектоскопами допускают лиц, прошедших инструктаж по правилам техники безопасности и имеющих соответствующее удостоверение. Перед проведением контроля на большой высоте, в труднодоступных местах или внутри металлоконструкций оператор проходит дополнительный инструктаж, а его работу контролирует служба техники безопасности.
Ультразвуковой дефектоскоп при работе заземляют медным проводом сечением не менее 2,5 мм2. Работать с незаземленным дефектоскопом категорически запрещается. При отсутствии на рабочем месте розетки подключать и отключать дефектоскоп может только дежурный электрик.
Запрещается проводить контроль вблизи сварочных работ при отсутствии защиты от лучей электрической дуги.
Л.П. Шебеко, А.П. Яковлев. "Контроль качества сварных соединений"
www.autowelding.ru
Ультразвуковой дефектоскоп для контроля сварных соединений
Неразрушающий контроль соединений – современный метод диагностики наличия и глубины дефектов в узлах и деталях. В отношении оценки последующей работоспособности сварных соединений особенно эффективной признана ультразвуковая дефектоскопия. Дело в том, что в подавляющем большинстве производственных ситуаций имеющиеся неоднородности сварного шва располагаются так, что хорошо отражают именно акустические волны сверхвысокой частоты. Этот метод проверки и заключает в себе ультразвуковой дефектоскоп.
В чём заключается эффективность неразрушающего контроля сварных соединений?
Идеально однородные среды в процессе взаимодействии с источником ультразвуковых колебаний не ослабляют амплитуду звуковых волн. Совсем иное происходит, если сканируются реальные объекты. При наличии в них участка с искажениями первоначальной структуры всегда наблюдается существенное искажение и уменьшение амплитуды звукового давления, которое количественно проявляется в виде ослабления или даже полного поглощения ультразвуковых волн.
Интенсивность таких искажений устанавливается законом ослабления
P=Р0 exp(-αd),
где: Р0 – исходное значение амплитуды звукового давления; Р – значение на выходе из диагностируемого сварного шва; d – толщина шва; α – коэффициент ослабления.
Поскольку параметр d чаще представляют как расстояние до источника ультразвукового излучения, то считается, что звуковая волна имеет вид полусферы, а потому ослабление будет равномерным по всем направлениям. В практике измерений оно обычно устанавливается в децибелах (дБ), поэтому может быть вычислено по формуле
α = 20/d∙lg(P0/Р)
Промышленный ультразвуковой дефектоскоп, применяемый для определения сплошности и качества сварных швов, оценивает интенсивность эхо-сигнала, которая пропорциональна амплитуде звукового давления:
p0/P = H0/H
где: Н0 и Н соответственно — амплитуды звукового сигнала на входе и выходе из прибора.
Для практически применяемого диапазона частот 1…15 МГц (что и случается для подавляющего большинства металлических изделий) интенсивность эхо-сигналов соотносится с относительным ослаблением ультразвукового сигнала следующими соотношениями:
Н/Н0 | 1,26 | 1,78 | 2,82 | 5,01 | 10,0 | 21,62 |
Мощность сигнала, дБ | 2 | 5 | 9 | 14 | 20 | 30 |
Из представленной таблицы следует, что применение оценочного критерия логарифмической интенсивности ультразвукового сигнала может эффективно фиксировать изменения в его амплитуде.
Причинами ослабления ультразвуковых волн происходит вследствие поглощения и рассеивания сигналов. Энергия поглощения превращает колебательную энергию в тепловую. Она пропорциональна частоте ультразвуковых колебаний, поэтому ультразвуковые дефектоскопы для контроля сварных соединений изготавливаются с максимально возможными генерируемыми частотами.
С повышением частоты облегчается фокусировка прибора, благодаря чему распознавание неоднородностей или дефектов улучшается. При этом должны соблюдаться следующие условия:
- Размер оцениваемой неоднородности должен быть больше половины длины волны.
- Направление сканирования должно быть перпендикулярным направлению хода звукового луча.
- Прибор не должен использовать так называемые критические частоты (для металлических конструкций это, например, частоты близкие к 6 МГц), при которых из-за явления дифракции ультразвуковых волн чувствительность метода резко снижается.
Энергия рассеивания более существенна для поликристаллических тел. Поэтому для крупнозернистых структур (например, чугуна) ультразвуковая дефектоскопия малочувствительна. Также неэффективно ультразвуковое сканирование при пониженных температурах окружающей среды.
Для получения ультразвуковых колебаний применяются два вида источников: магнитострикционные генераторы и пьезоэлектрические преобразователи. Каждое из устройств имеет свои рациональные области применения.
Конструкции ультразвуковых пьезоэлектрических дефектоскопов
Пьезоэффект заключается в том, что при силовом воздействии на определённые кристаллические вещества (изоляторы с полярно расположенными осями) в них возникают напряжения определённого знака, которые, в свою очередь, инициируют электрические поверхностные заряды. При этом величина напряжений прямо пропорциональна механической нагрузке, что очень важно именно в конструктивном смысле, поскольку упрощает конструкцию прибора. Таким образом цена ультразвукового дефектоскопа для контроля сварных соединений будет невысокой.
Пьезоэлектрический эффект обратим, а потому использующие его ультразвуковые дефектоскопы быстро переналаживаются, и не нуждаются в сложной регулировке. При этом при помощи прямого пьезоэффекта ультразвуковые волны обнаруживаются, а при помощи обратного – генерируются.
Принцип работы пьезогенератора дефектоскопа следующий. На конденсаторные пластины, которые наложены на кристалл, подаётся переменное электрическое напряжение. Это вызывает колебание кристалла с той же частотой. В качестве преобразователей используют такие материалы, как кварц, титанат бария, сульфат лития и др. При наличии внешнего давления атомы в структурной ячейке пьезоэлемента сдвигаются, что и является моментом начала разряда конденсаторных пластин. При изготовлении ультразвукового дефектоскопа для контроля сварных соединений, использующего подобный принцип, излучатель вырезается таким образом, чтобы плоскость колебания по отношению к толщине рассматриваемого сварного шва излучала продольные волны. Если требуется оценить неравномерность структуры соединения на значительной площади, то используют пластину, вырезанную в перпендикулярном направлении. Тогда с приложением напряжения она будет излучать поперечные волны, которые будут равномерно распространяться в толще исследуемого соединения.
Корпуса пьезоизлучателей изготавливают из керамики, что повышает уровень требований к условиям работы ультразвуковых дефектоскопов для контроля сварных соединений. В частности, им противопоказаны удары и сотрясения корпуса.
Магнитострикционные преобразователи ультразвуковых дефектоскопов
Магнитоскрикция заключается в деформации ферромагнитной детали, которая размещена в силовом магнитном поле. Длина этой детали изменяется в зависимости от вида силовых линий магнитного поля, её материала, температуры и степени намагниченности. В ультразвуковых дефектоскопах используются ферромагнетики, относительное изменение длины которых – не менее 10-5.
Работают такие преобразователи следующим образом. В приборе создаётся переменное электромагнитное поле, при этом ферромагнитный стержень начинает совершать колебания удвоенной амплитуды. Поскольку линейная деформация магнитостриктора не зависит от направления силовых линий магнитного поля, то подмагничивания такого элемента не требуется.
Как и пьезоэффект, магнитострикция обратима. В качестве излучателей применяются химически чистый никель, а также его сплавы с медью или железом. Минимальная частота, при которой обнаружение дефектов сварных конструкций окажется эффективным, составляет 60 Гц, хотя в приборах обычно реализуются частоты от 300 Гц.
Магнитострикционные преобразователи конструктивно проще, однако уступают пьезогенераторам по параметрам минимальной площади диагностируемой зоны: она должна быть достаточно большой. Кроме того, такие ультразвуковые дефектоскопы теряют свою чувствительность при обследовании только что полученных сварных швов. Ещё одним ограничением магнитострикционных источников получения ультразвуковых волн считается их повышенная энергоёмкость. Зато они более компактны, а потому применимы в стеснённых для диагностики условиях.
Промышленные конструкции ультразвуковых дефектоскопов для контроля сварных соединений
Для измерения необходимы:
- Сам регистрирующий прибор.
- Искательная головка (передатчик).
- Контрольная головка (приёмник).
- Устройство отображения (монитор или цифровой дисплей).
Напряжение от источника переменного тока (аккумулятор или генератор — для стационарных дефектоскопов) подаётся на излучатель, а от него ультразвуковые волны передаются в исследуемый сварной шов. Интенсивность ослабления исходного сигнала определяет степень неоднородности шва. Возникающая амплитуда сигнала далее усиливается и регистрируется, при этом возможна как визуальная оценка качества, так и запись результатов на цифровой носитель информации.
Перед использованием ультразвуковой дефектоскоп для контроля сварных соединений подлежит юстировке. Как образец, используется сварной стык с идеальными параметрами качества, при этом отклонение шкалы/стрелки должно быть максимально возможным.
В качестве приёмника дефектоскопы некоторых фирм используют преобразователь изображения. При этом фиксируется фактическое значение плотности энергии звукового поля за швом. Этот способ получения конечной информации более нагляден, но требует определённого пространства за исследуемым соединением.
Излучение звуковой энергии в ультразвуковых дефектоскопах может быть выполнено двумя способами – резонансным или импульсным. В первом случае излучение ультразвука происходит непрерывно, а применяемые частоты находятся в диапазоне 1…12,5 кГц. При импульсном методе используется сигнал (эхо) звуковой волны, который отражается от дефектной зоны или задней поверхности сварного стыка. Подача звукового импульса происходит через 1…2 мкс, чем обеспечивается высокая точность сканирования объекта. Конечный импульс отражается на мониторе, и может регистрироваться цифровым устройством записи. Энергопотребление дефектоскопов такого типа значительно меньше.
Признанным мировым лидером в производстве переносных дефектоскопов для контроля сварных соединений, цена которых вполне соответствует их качеству, считаются аппараты от компании SONATEST (Франция). Данные приборы отличаются компактностью и точностью получаемых данных. Например, применяемые для тестирования качества сварки труб, листовых материалов и т.п. ультразвуковые дефектоскопы линейки Harfang Veo характеризуются следующими эксплуатационными достоинствами:
- большим диапазоном регулировки направления и силы излучения, а также скорости диагностики;
- точностью измерения;
- воспроизводимостью результатов, включая и 3D-моделирование структуры сварного шва;
- удобствами настройки;
- возможностью подключения для целей сканирования нескольких источников;
- ёмкими батареями, допускающими замену непосредственно в ходе измерений.
proinstrumentinfo.ru
Ультразвуковой контроль тонкостенных сварных соединений
Одной из важных областей применения ультразвукового контроля является контроль качества сварных соединений. Основные дефекты сварных швов (шлаковые включения, несплавления по кромкам и между валиками, непровар корня шва, подрез, продольные и поперечные трещины, поры и пр.), за исключением отдельно лежащих мелких пор, хорошо обнаруживаются ультразвуком.
При всём разнообразии сварных соединений существуют общие принципы методики контроля, выбора основных параметров. Но в тоже время, у каждой группы сварных соединений, в зависимости от типоразмеров, разделки кромок, вида сварки, стыкуемых материалов и пр., есть свои особенности, которые необходимо обязательно учитывать при подготовке к контролю. Например, такие нелюбимые дефектоскопистами, так называемые "тонкостенки", т.е. сварные швы толщиной от 2 до 6 мм. До сих пор действует укоренившееся в сознании ультразвуковиков утверждение: "Меньше 6 мм УЗК не контролируем, это только рентген". А напрасно. На самом деле существует целый арсенал средств и приёмов контроля сварных соединений данных типоразмеров: хордовые ПЭП + СОП, малогабаритные совмещённые наклонные ПЭП с малой стрелой (5 ÷7 мм) и большим углом ввода (700, 750), наклонные раздельно-совмещённые ПЭП. И здесь необходим конкретный подход. Если сварка трубных элементов диаметром до 100 мм со стенкой 2÷6 мм, то вероятнее всего, без хордовых ПЭП не обойтись.
Хордовый преобразователь предназначен для контроля определённого типоразмера трубы (диаметр X толщина ± 20%) и приобретается в комплекте с СОП, в котором выполнено торцевое плоскодонное отверстие с Sпдо согласно НТД (рис. 1). Но стоит обязательно учесть то, что конструкция "правильного" хордового преобразователя должна быть такой, чтобы основная энергия излучаемого ультразвукового пучка концентрировалась в рабочем сечении сварного шва для того, чтобы минимизировать появление ложных сигналов от геометрических отражателей, например, валиковусиления сварного шва. А вот при смещении кромок, что нередко встречается при стыковке трубных элементов, даже удачная конструкция хордового ПЭП может не решить задачу контроля.
Но есть ещё традиционная схема контроля притёртыми наклонными совмещёнными ПЭП и наклонными раздельно-совмещёнными ПЭП. Мощные шумы, ложные сигналы от валика усиления, по времени почти совпадающие с сигналом от дефекта, низкая чувствительность к вертикальным дефектам (например, свищам) ограничивают применение совмещённой схемы (рис 2.). ООО "ИЦ Физприбор " разработало линейку раздельно-совмещенных наклонных ПЭП с частотами 5Мгц, 8Мгц и углами ввода 650, 700, 750, предназначенных для контроля тонкостенных сварных швов из малоуглеродистых, нержавеющих сталей и сплавов алюминия.
Характерная особенность данных ПЭП – отсутствие мёртвой зоны и фокусировка УЗ поля в определённом диапазоне толщин. В отличии от преобразователей остальных производителей, ПЭП «ИЦ Физприбор» имеют чёткие характеристики и рекомендации применения для выбора оптимального варианта контроля конкретного сварного соединения. Для настройки чувствительности используются обычные стандартные образцы предприятия (СОП) с зарубкой.
Также возможно заказать преобразователи, притертые под диаметр трубы от 32 до 300 мм. А для решения задачи ультразвукового контроля тонкостенных (2 – 4 мм) сварных конструкций больших диаметров (> 500мм), баков, резервуаров, применение наклонных РС ПЭП вообще незаменимо. Однако, следует учитывать, что в связи с тем, что эффективная ширина пучка сопоставима с толщиной рассматриваемых тонкостенных сварных соединений, концепция контроля такова:
- выявляются дефекты без определения глубины залегания, что для малых толщин не имеет большого значения;
- уверенно обнаруживаются наиболее значительные дефекты сварных швов, влияющие на эксплуатационные свойства конструкций - непровары корня шва.
В заключение хотелось бы ещё раз отметить, что задача УЗК «тонкостенок» выполнима и имеет ряд решений, эффективность которых зависит от оптимального выбора параметров контроля, с учётом всех особенностей контролируемого сварного соединения.
Экспериментируйте, пробуйте!
Специалист 2 уровня УЗК Клявина С.Ю., г.Челябинск
oilloot.ru
РДИ 38.18.016-94 Инструкция по ультразвуковому контролю сварных соединений технологического оборудования, РД от 23 июня 1994 года №38.18.016-94
РДИ 38.18.016-94
УТВЕРЖДАЮ
Зам. руководителя Департамента нефтепереработки Минтопэнерго РФ В.П.Белов 23.06.1994 г.Директор института, канд. техн. наук, ст. науч. сотр. А.Е.Фолиянц
Зам. директора института по научной работе, канд. техн. наук, ст. науч. сотр. Н.В.Мартынов
Зав. лабораторией неразрушающих методов контроля, канд. техн. наук, ст. науч. сотр. Б.П.ПилинОтветственные исполнители:Старший научный сотрудник З.И.РолдугинаСтарший научный сотрудник И.А.Митрофанова
1. ОБЩИЕ ПОЛОЖЕНИЯ
1.1. Настоящая инструкция распространяется на ультразвуковой контроль стыковых, угловых и тавровых сварных соединений из сталей перлитного и мартенситно-ферритного классов, выполняемый в условиях монтажа, ремонта и эксплуатации сосудов, аппаратов, трубопроводов на предприятиях химической и нефтехимической промышленности.
1.2. Настоящая инструкция устанавливает порядок, методику проведения ручного ультразвукового контроля следующих видов сварных соединений, выполненных электрошлаковой и дуговой сваркой:- стыковых кольцевых сварных соединений трубопроводов, сосудов и аппаратов с толщиной свариваемых элементов не менее 8 мм и с номинальным наружным диаметром не менее 200 мм;- стыковых продольных сварных соединений трубопроводов, сосудов и аппаратов с толщиной свариваемых элементов не менее 8 мм и с номинальным наружным диаметром не менее 400 мм;- угловых и тавровых сварных соединений, выполненных из плоских и цилиндрических (трубных) элементов с толщиной элементов не менее 8 мм и номинальным наружным диаметром корпуса (при вварке штуцеров в корпус) не менее 800 мм, диаметром штуцера не менее 100 мм при отношении диаметра ввариваемого штуцера к диаметру корпуса не более 0,5;- тавровых сварных соединений с толщиной стенки свариваемых элементов не менее 8 мм;- нахлесточных сварных соединений с толщиной свариваемых элементов не менее 8 мм.
1.3. В соответствии с настоящей инструкцией разрешается проводить ультразвуковой контроль сварных швов в любом пространственном положении. Допустимая температура окружающего воздуха в зоне контроля определяется типом используемого дефектоскопа и указывается в инструкции по его эксплуатации.
1.4. Инструкция учитывает требования ГОСТ 14782-86, ГОСТ 20415-75*, ГОСТ 23829-79**, ОСТ 2044-83, ОСТ 26.291-87, СНиП 3.05.05-84.________________* На территории Российской Федерации действует ГОСТ 20415-82;** На территории Российской Федерации действует ГОСТ 23829-85. - Примечание изготовителя базы данных.
1.5. Контроль по настоящей инструкции обеспечивает выявление дефектов типа трещин, непроваров, пор, неметаллических и металлических включений без расшифровки характера этих дефектов и без определения их действительных размеров, но с регистрацией координат, расположения и количества дефектов.
1.6. Положения настоящей инструкции распространяются на ультразвуковой контроль сварных соединений при температуре поверхности до 70 °С.
1.7. Настоящая инструкция не распространяется на ультразвуковой контроль антикоррозионной наплавки и контроль сварных соединений с неполным проплавлением свариваемых элементов (т.е. при наличии конструктивного зазора).
1.8. Контроль по настоящей инструкции не гарантирует выявление:- вольфрамовых включений;- дефектов, расположенных в мертвой зоне преобразователя;- дефектов, размеры которых меньше длины поперечной ультразвуковой волны;- плоских дефектов, ориентированных относительно акустической оси искателя под углом менее 70°.
1.9. С введением в действие настоящей инструкции отменяется действующая в отрасли "Инструкция по ультразвуковому контролю сварных соединений технологического оборудования, РДИ 38.18.002-83".
1.10. Для проведения работ по ультразвуковому контролю на предприятии должна быть организована лаборатория неразрушающих методов контроля.
1.11. Лаборатория должна быть укомплектована аппаратурой из рекомендуемого перечня приборов, приведенного в приложении 2. Качественный состав и необходимое количество приборов определяются на основании характера и объема выполняемых работ по ультразвуковому контролю на каждом конкретном предприятии.
1.12. Для организации работ по ультразвуковому контролю лаборатория должна иметь нормативно-техническую документацию, приведенную в конце основного текста настоящей инструкции.
1.13. Ультразвуковой контроль осуществляется по заявке, форма которой устанавливается предприятием. В заявке следует указывать название установки, объект контроля, тип сварного соединения, его расположение на объекте контроля, марку стали, толщину и диаметр сварных элементов и другие необходимые сведения.
1.14. Ответственность за результаты ультразвукового контроля несет специалист, подписавший заключение о результатах контроля.
2. ТРЕБОВАНИЯ К СПЕЦИАЛИСТАМ
2.1. К проведению работ по ультразвуковому контролю допускаются лица, прошедшие обучение и аттестацию в соответствии с "Правилами аттестации специалистов неразрушающего контроля"* и имеющие I, II или III уровень квалификации.________________* На территории Российской Федерации действуют ПБ 03-440-02, здесь и далее по тексту. - Примечание изготовителя базы данных.Обучение специалистов проводится по типовым программам (приложение 4 "Правил аттестации специалистов неразрушающего контроля").К аттестации по акустическому (ультразвуковому) методу контроля допускаются специалисты, имеющие после специальной подготовки стаж работы по указанному методу не менее:для I уровня квалификации - 6 месяцевдля II уровня квалификации - 12 месяцев.Минимальный стаж работы после специальной подготовки, необходимый для аттестации кандидата на III уровень, указан в приведенной ниже таблице.
Общее образование и специальная подготовка | Стаж работы | |
II уровень | неаттестованного | |
ВУЗ или ИПК по неразрушающему контролю | 12 | 24 |
Техникум по неразрушающему контролю | 24 | 48 |
Технический ВУЗ или техникум | 48 | 72 |
Аттестацию проводят специализированные организации, имеющие лицензию Госгортехнадзора России. В приложении 3 приведен перечень организаций, которые могут проводить аттестацию специалистов на I, II и III уровни квалификации.
2.2. Специалисты I уровня квалификации ведут работу по контролю конкретной продукции без выдачи заключения о качестве объекта. Специалист I уровня не несет ответственности за выбор метода контроля, аппаратуры и режимов ее работы.
2.3. Специалисты II уровня квалификации:- выполняют контроль и оценку качества продукции;- руководят работой специалиста I уровня квалификации;- дают заключение о качестве объекта по результатам контроля, выполненного специалистом I уровня квалификации;- ведут подготовку специалистов I уровня квалификации;- разрабатывают технологические карты контроля в соответствии с действующими нормативно-техническими документами по контролю конкретной продукции в рамках своей квалификации;- проводят инспекционный контроль продукции, проконтролированной специалистами I и II уровней квалификации.
2.4. Специалисты III уровня квалификации:- выполняют контроль и оценку качества продукции;- руководят работой специалистов I и II уровней квалификации;- дают заключение о качестве продукции по результатам контроля, выполненного специалистом I уровня квалификации;- ведут подготовку специалистов I, II и III уровней квалификации;- разрабатывают методики и технологические карты контроля в соответствии с действующими нормативно-техническими документами по контролю конкретной продукции в рамках своей квалификации;- согласовывают технологические карты, разработанные специалистами II уровня;- проводят инспекционный контроль продукции, проконтролированной специалистами I и II уровней квалификации.
2.5. Согласно "Правилам аттестации специалистов неразрушающего контроля" срок действия квалификационного удостоверения специалистов I и II уровней - 3 года, III уровня - 5 лет.
2.6. В случае изменения места работы специалиста I и II уровней квалификации, перерыва в работе по ультразвуковому контролю более одного года и истечения срока действия квалификационного удостоверения, оно теряет силу.
2.7. По истечении первого срока действия квалификационное удостоверение может быть продлено соответствующим аттестационным органом при условиях:- ходатайства с места работы;- отсутствия перерыва в работе по УЗ контролю более одного года.При отсутствии этих документов специалист должен пройти повторную аттестацию в одной из организаций, приведенных в приложении 3.
2.8. По истечении двух сроков действия квалификационного удостоверения проводится повторная аттестация в одной из организаций, приведенных в приложении 3.
3. СРЕДСТВА КОНТРОЛЯ
3.1. При контроле сварных соединений следует применять ультразвуковые эхо-импульсные отечественные дефектоскопы УД2-12, УД11ПУ и импортные USK-6, USK-7 и др.Допускается применение других дефектоскопов, обеспечивающих проведение контроля в соответствии с требованиями настоящей инструкции.
3.2. Каждый дефектоскоп должен иметь паспорт, техническое описание и инструкцию по эксплуатации.
3.3. Дефектоскопы подлежат обязательной поверке 1 раз в год, а также после каждого ремонта, в организациях, имеющих право на поверку.
3.4. Приказом по предприятию назначаются ответственные за состояние аппаратуры лица из числа ИТР или высококвалифицированных дефектоскопистов, имеющих уровень квалификации не ниже II-го, которые должны 1 раз в квартал и непосредственно после ремонта проверять исправность дефектоскопической аппаратуры, находящейся в распоряжении службы контроля.
3.5. Для контроля сварных соединений следует применять прямые, раздельно-совмещенные и наклонные преобразователи с рабочей частотой в диапазоне 1,8-10 МГц и углами ввода 40°, 45°; 50°; 60°, 65°; 70°. Преобразователи должны удовлетворять требованиям ГОСТа 23702-79.
3.6. Для обеспечения достоверности результатов контроля следует регулярно проверять следующие параметры:- условную чувствительность;- стрелу преобразователя;- точку ввода;- угол ввода;- величину мертвой зоны;- разрешающую способность.
3.7. Проверка основных параметров контроля при работе с отечественными дефектоскопами проводится в соответствии с ГОСТ 14782-86 по стандартным образцам, входящим в "Комплект контрольных образцов и вспомогательных устройств КОУ-2" (ПО "Волна, г.Кишинев).
3.8. При работе с импортными дефектоскопами проверка основных параметров контроля проводится по образцам Международного института сварки V1 и V2 в соответствии с методическими рекомендациями по использованию дефектоскопа или инструкцией по его эксплуатации.
3.9. Для настройки дефектоскопа и оценки измеряемых характеристик, обнаруженных дефектов необходимо иметь испытательные образцы с искусственными отражателями заданных размеров и местоположения.
3.10. Испытательные образцы и искусственные отражатели в них должны быть изготовлены в соответствии с требованиями ГОСТа 14782-86.
3.11. Рекомендуемые размеры испытательных образцов в зависимости от толщины контролируемого изделия приведены в табл.1.
Таблица 1
Рекомендуемые размеры испытательных образцов
Толщина контролируемого изделия, , мм | Ширина, мм | Длина, мм |
До 10 вкл. | 20 | 80 |
Св. 10 до 20 вкл. | 30 | 100 |
Св. 20 до 30 вкл. | 40 | 5+30 |
Св. 30 до 60 вкл. | 60 | 4+30 |
Отклонение толщины образца от номинальной толщины контролируемого изделия не должно превышать ±3 мм.
3.12. Искусственные отражатели в испытательных образцах могут быть изготовлены в виде плоскодонных, боковых цилиндрических или плоских угловых отражателей (зарубок). Размеры отражающей поверхности искусственных отражателей определяются предельно-допустимыми размерами для конкретной толщины изделия (рис.1).
Рис.1. - Испытательные образцы
Испытательные образцы
Рис.1
3.13. При изготовлении в испытательных образцах искусственных отражателей в виде плоских угловых отражателей (зарубок) следует использовать инструмент, входящий в КЭУ-I (ТУ-25-08-468-69).
3.14. Соотношение между площадью вертикальной грани плоского углового отражателя (зарубки) и площадью плоскодонного отражателя , дающими сигнал одинаковой амплитуды, определяется выражением:
;
значение коэффициента зависит от угла ввода ультразвукового луча в металл и определяется по табл.2.
Таблица 2
Значения коэффициента
Угол ввода, град. | 40 | 45 | 50 | 60 | 65 | 70 |
2,4 | 1,75 | 1,3 | 0,6 | 0,5 | 0,75 |
4. ПОДГОТОВКА К КОНТРОЛЮ
4.1. Перед проведением контроля дефектоскопист должен:- изучить объект контроля;- произвести его внешний осмотр;- определить способ контроля;- определить угол ввода и выбрать преобразователь;- определить пределы перемещения преобразователя и зону зачистки;- настроить дефектоскоп.
4.2. Изучение объекта контроля предусматривает изучение технической документации на контролируемый объект, особенностей конструкции и технологии изготовления сварного соединения, анализ результатов предыдущего контроля, а также определение необходимого объема контроля и норм отбраковки.
4.3. По результатам внешнего осмотра устанавливается пригодность изделия к контролю, при этом определяется:- соответствие ширины валика усиления требованиям нормативно-технической документации на контролируемое изделие;- наличие недоступных для контроля участков изделия;- отсутствие недопустимых внешних дефектов.
4.4. Контроль ультразвуковым методом следует проводить только после устранения всех обнаруженных при внешнем осмотре дефектов.
4.5. Выбор способа контроля и угла ввода преобразователя определяется возможностью прозвучивания всего сечения сварного шва.При контроле сварных швов применяют следующие способы контроля:- прямым или раздельно-совмещенным преобразователем;- наклонным преобразователем;- прямым лучом;- однократно отраженным лучом;- двукратно или многократно отраженным лучом.
4.6. Контроль прямым или раздельно-совмещенным преобразователем проводят на стыковых сварных швах со снятым валиком усиления (как правило, на сварных соединениях большой толщины, выполненных автоматической сваркой), а также на угловых и тавровых сварных соединениях с плоскими стенками, при двустороннем доступе к изделию.Способ контроля прямым лучом наклонными преобразователями применяют для выявления дефектов в корне шва (в стыковых швах с V-образной разделкой) или в нижней части шва (в стыковых швах с Х-образной разделкой).Способ контроля однократно-отраженным лучом наклонными преобразователями применяют для контроля середины и верхней части шва.Способ контроля двукратно и многократно отраженным лучом используют в тех случаях, когда сварное соединение имеет малую толщину и/или большую ширину валика усиления или размера катета углового шва, что препятствует вводу прямого ультразвукового луча в наплавленный металл шва.Все применяемые схемы контроля приведены в методиках контроля каждого типа сварного соединения в настоящей инструкции.Значения углов ввода и способы контроля сварных соединений различных толщин и типов приведены в табл.3.
Таблица 3
Параметры контроля сварных соединений
Тип сварного соединения | Толщина сваренных элементов | Ширина валика усиления или катет сварного шва | Рабочая частота | Угол ввода, не менее град. | Ширина зоны зачистки с одной стороны шва |
1 | 2 | 3 | 4 | 5 | 6 |
Стыковые сварные соединения | |||||
- с односторонним швом (V-образная разделка кромок) | 8 | 21 | 4,0-5,0 | 70 | 85 |
10 | 23 | 4,0-5,0 | 70 | 95 | |
12 | 26 | 4,0-5,0 | 65 | 90 | |
14 | 26 | 2,0-2,5 | 65 | 100 | |
16 | 28 | 2,0-2,5 | 65 | 110 | |
18 | 28 | 2,0-2,5 | 65 | 115 | |
20 | 28 | 2,0-2,5 | 65 | 125 | |
22 | 31 | 2,0-2,5 | 65 | 135 | |
24 | 31 | 2,0-2,5 | 65 | 145 | |
- с двухсторонним швом (Х-образная разделка кромок) | 26 | 28 | 2,0-2,5 | 65 | 150 |
28 | 28 | 2,0-2,5 | 65 | 160 | |
30 | 34 | 2,0-2,5 | 65 | 170 | |
32 | 34 | 2,0-2,5 | 65 | 175 | |
34 | 34 | 2,0-2,5 | 65 | 185 | |
36 | 34 | 2,0-2,5 | 65 | 195 | |
38 | 34 | 2,0-2,5 | 65 | 205 | |
40 | 37 | 2,0-2,5 | 65 | 210 | |
42 | 37 | 2,0-2,5 | 65 | 220 | |
44 | 37 | 2,0-2,5 | 65 | 230 | |
46 | 37 | 2,0-2,5 | 65 | 240 | |
48 | 37 | 2,0-2,5 | 50 | 155 | |
50 | 41 | 2,0-2,5 | 50 | 160 | |
52 | 41 | 2,0-2,5 | 50 | 165 | |
54 | 41 | 2,0-2,5 | 50 | 170 | |
56 | 44 | 2,0-2,5 | 50 | 175 | |
58 | 44 | 2,0-2,5 | 50 | 180 | |
60 | 44 | 2,0-2,5 | 50 | 185 | |
65 | 47 | 2,0-2,5 | 40 | 150 | |
70 | 47 | 2,0-2,5 | 40 | 160 | |
75 | 50 | 2,0-2,5 | 40 | 165 | |
80 | 50 | 2,0-2,5 | 40 | 175 | |
85 | 53 | 2,0-2,5 | 40 | 180 | |
90 | 53 | 2,0-2,5 | 40 | 190 | |
Угловые сварные соединения | |||||
- с V-образной разделкой кромок | 8 | 13 | 4,0-5,0 | 70 | 85 |
10 | 18 | 4,0-5,0 | 70 | 95 | |
12 | 18 | 4,0-5,0 | 70 | 105 | |
14 | 23 | 2,0-2,5 | 70 | 115 | |
16 | 29 | 2,0-2,5 | 70 | 130 | |
18 | 29 | 2,0-2,5 | 70 | 140 | |
- с K-образной разделкой кромок | 20 | 17 | 2,0-2,5 | 65 | 150 |
22 | 20 | 2,0-2,5 | 65 | 135 | |
24 | 23 | 2,0-2,5 | 65 | 140 | |
26 | 25 | 2,0-2,5 |
docs.cntd.ru
Ультразвуковой контроль - «МЦК» - контроль сварных швов
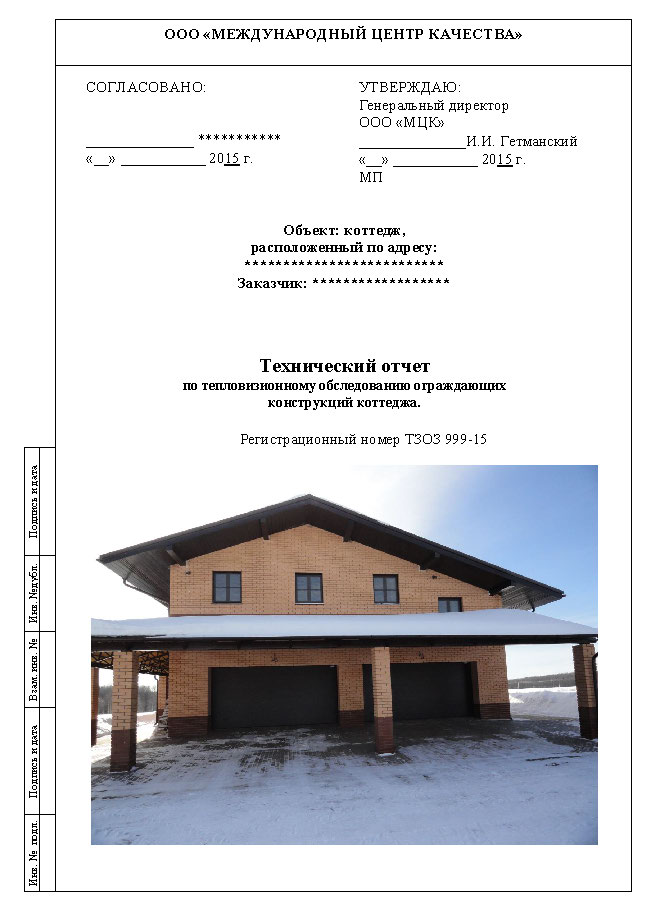
Пример технического отчета тепловизионного обследования.
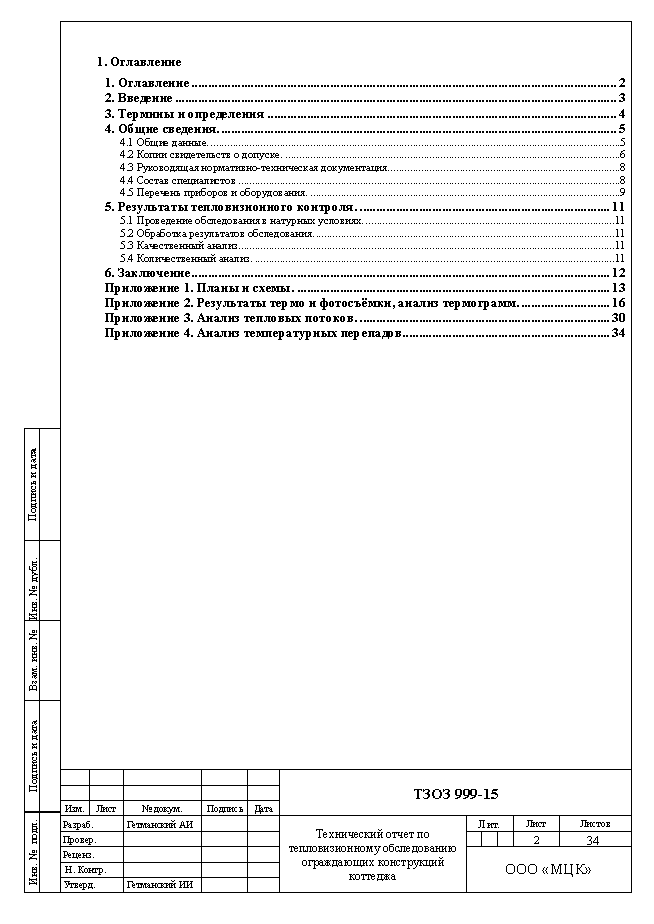
Структура технического отчета.
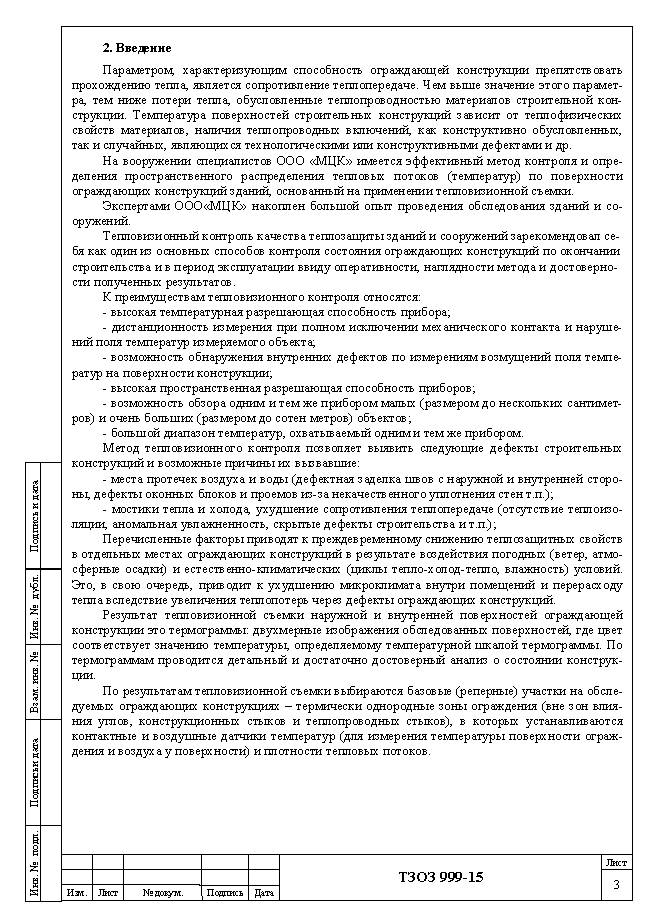
Общие положения технического отчета.
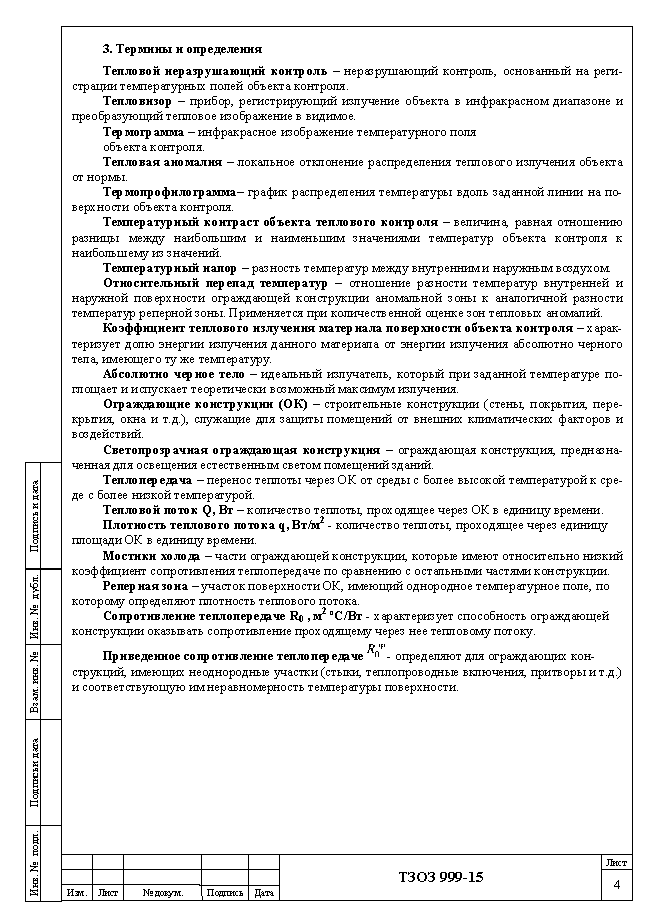
Термины и определения.
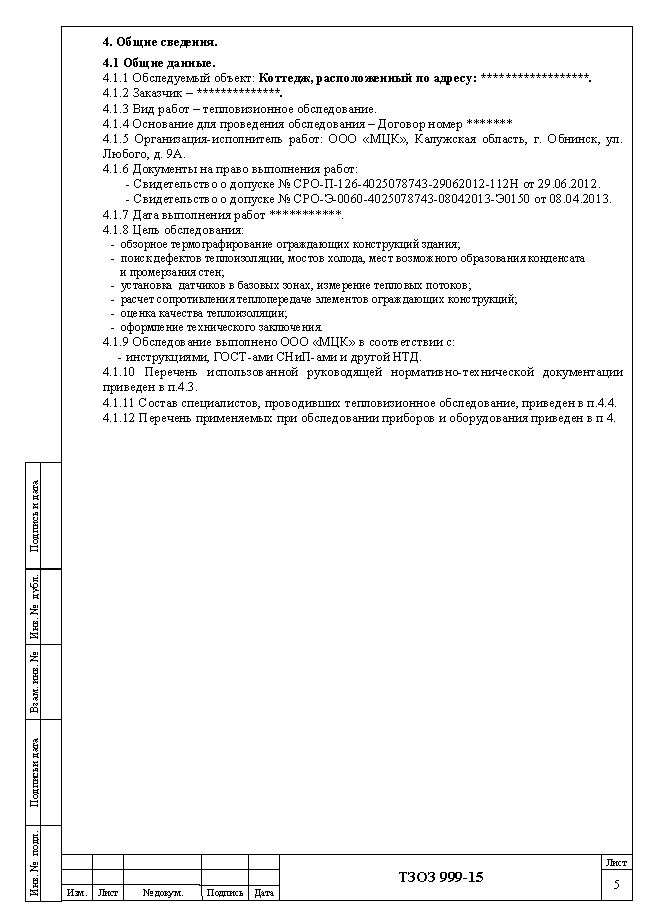
Общие сведения.
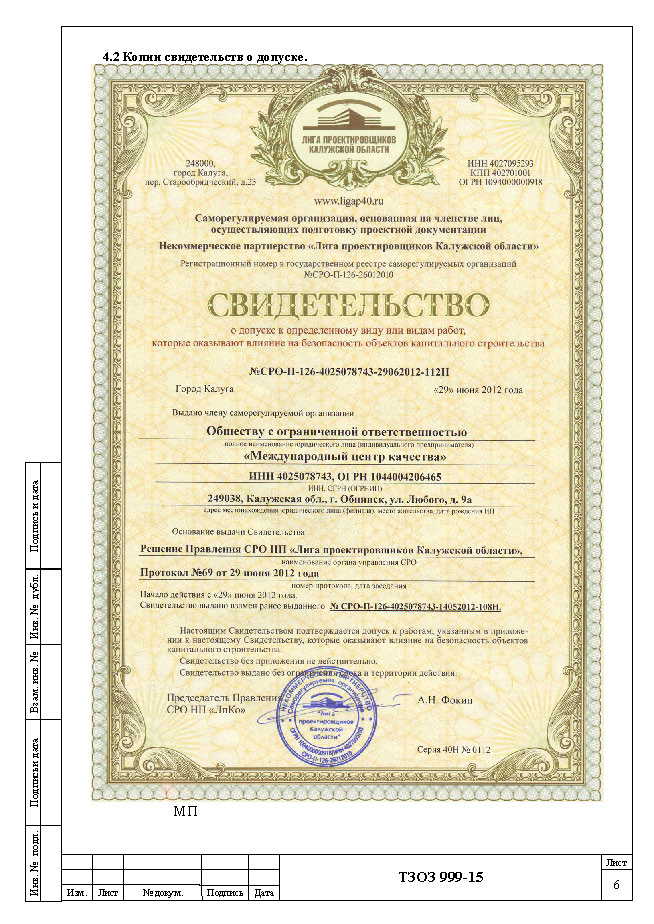
Допуск СРО на обследование зданий.
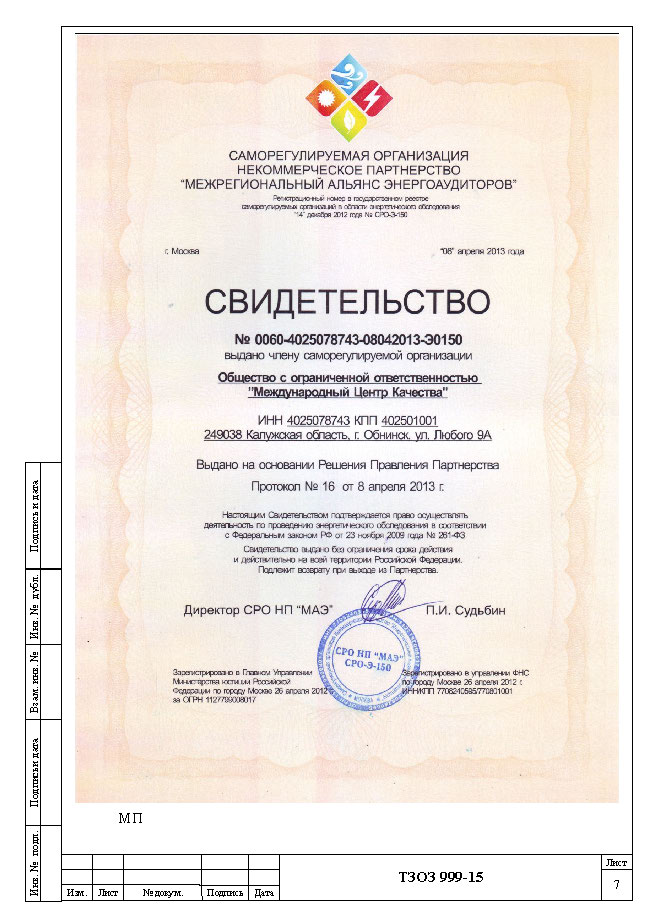
Допуск СРО энергоаудит.
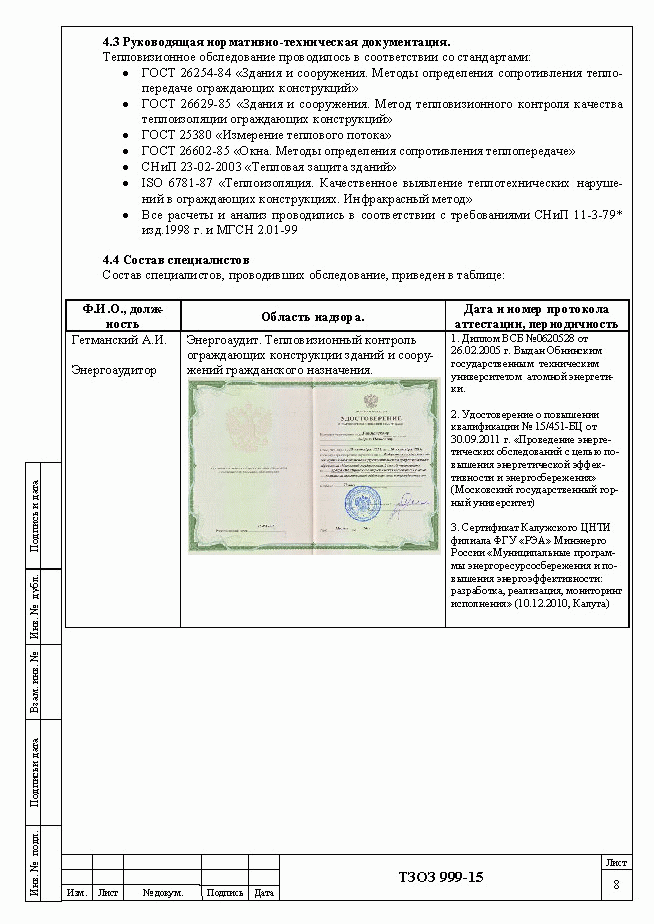
Нормативно-техническая документация.
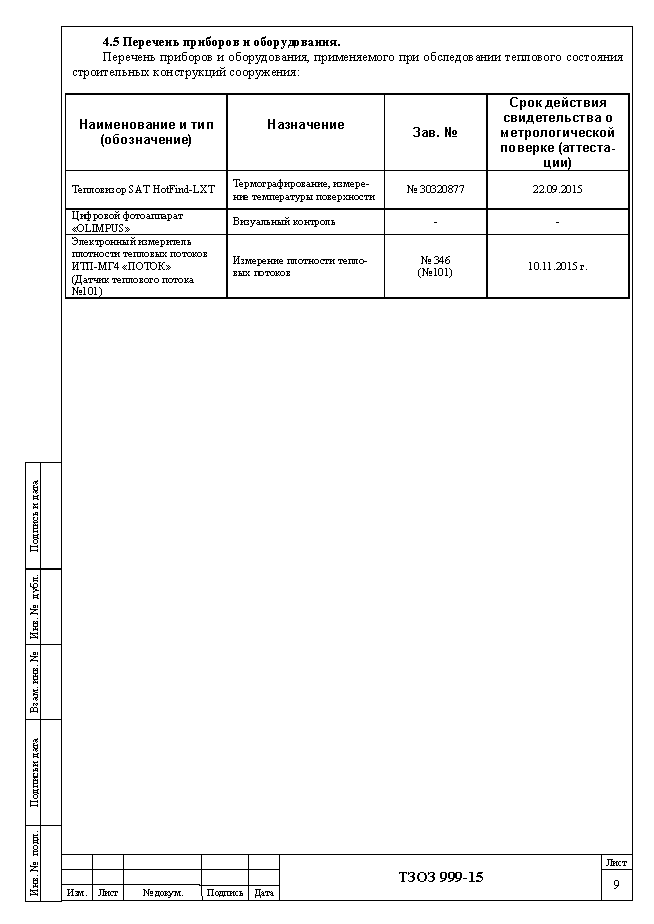
Используемое оборудование тепловизионного контроля.
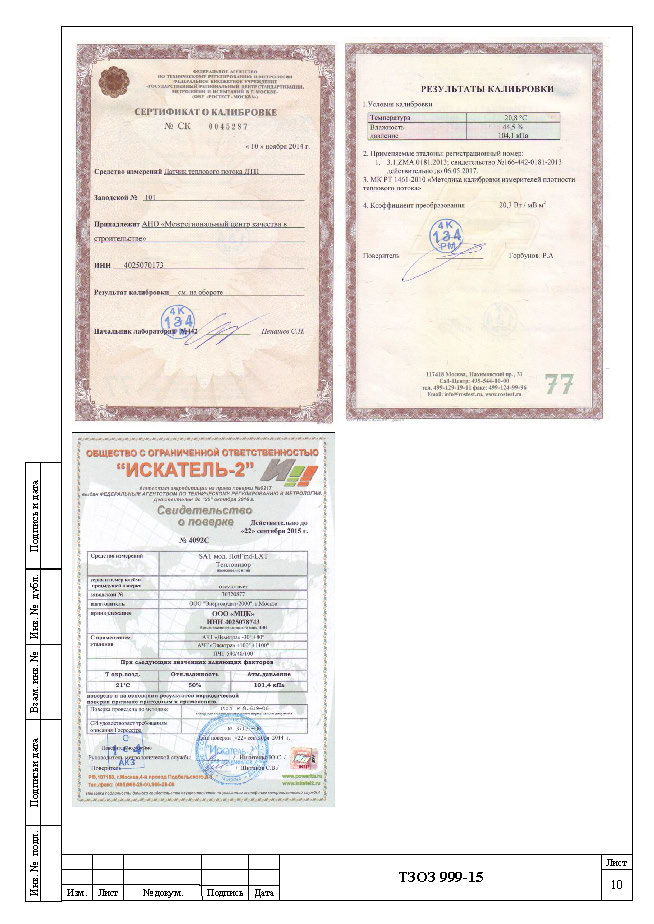
Данные о поверке средств измерения.
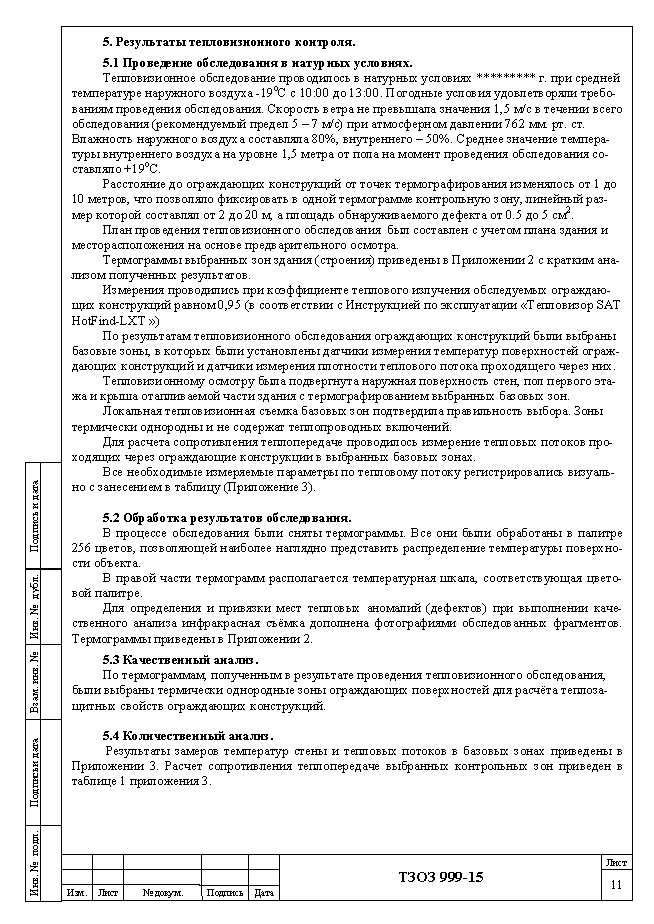
Результаты тепловизионного контроля.
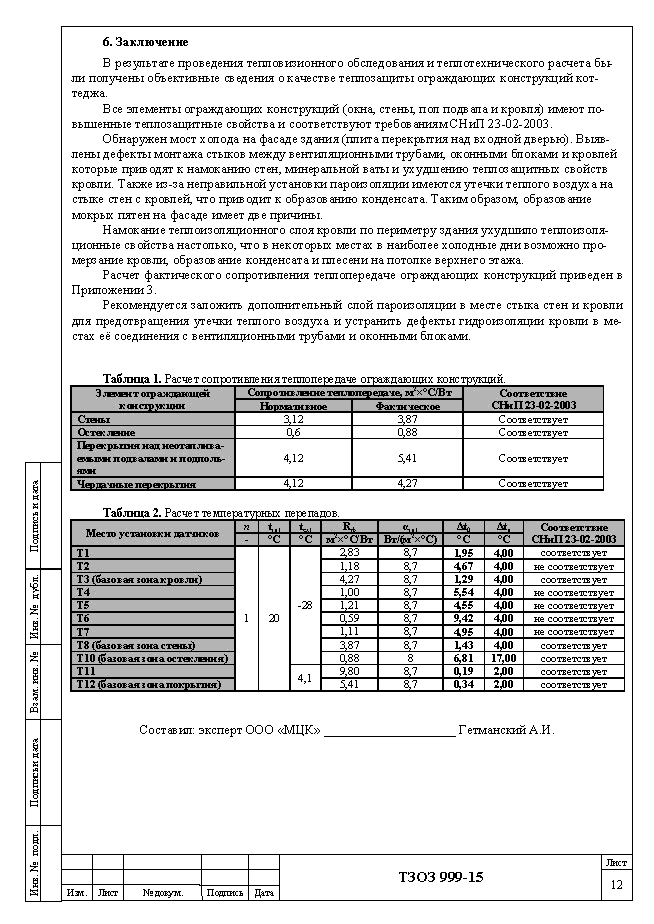
Экспертное заключение.
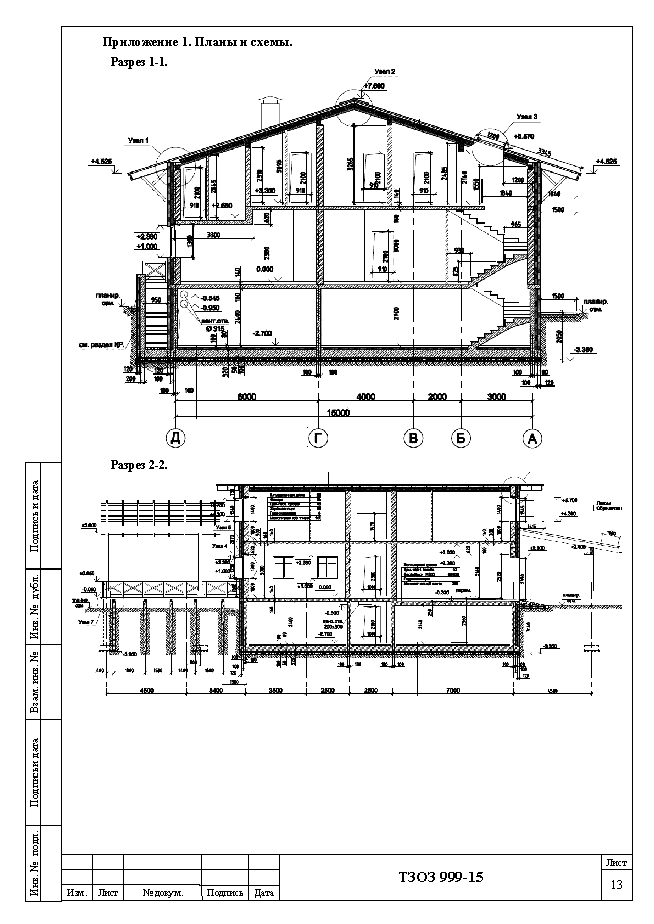
Приложение 1. Планы и схемы.
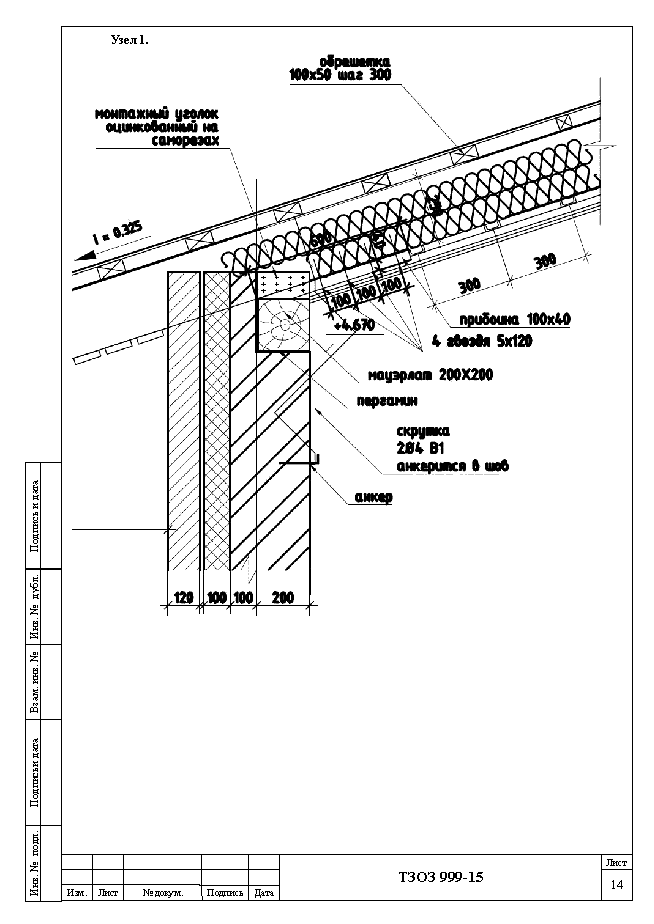
Схема узла примыкания крыши к стене.
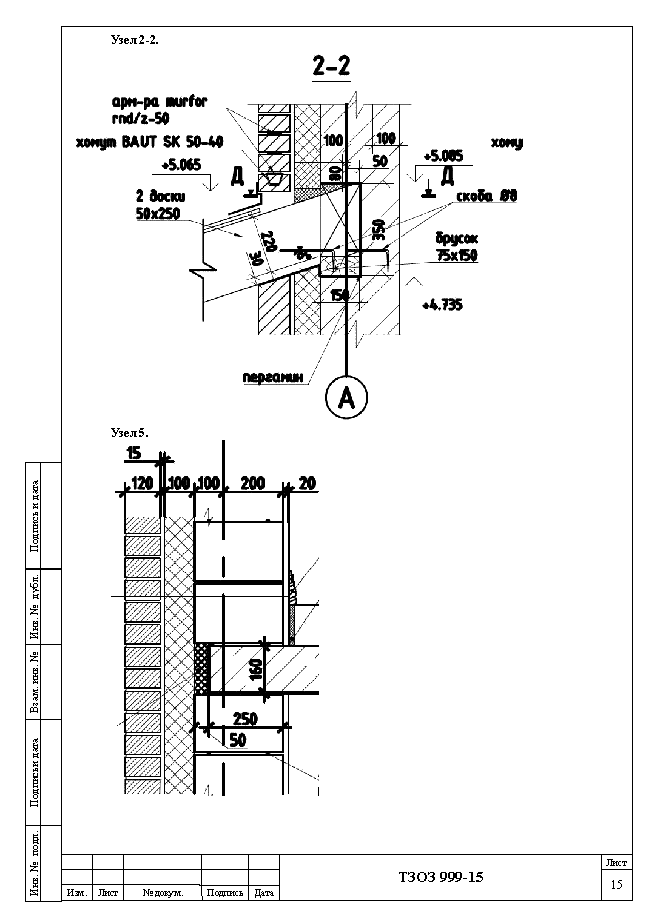
Схемы обследованных узлов и соединений.
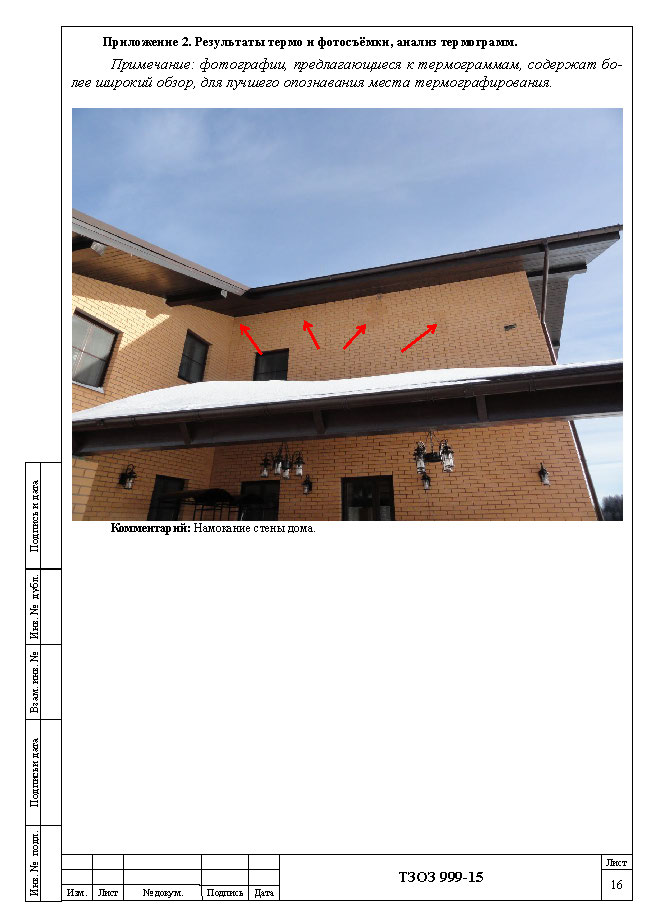
Образование конденсата на стенах дома.
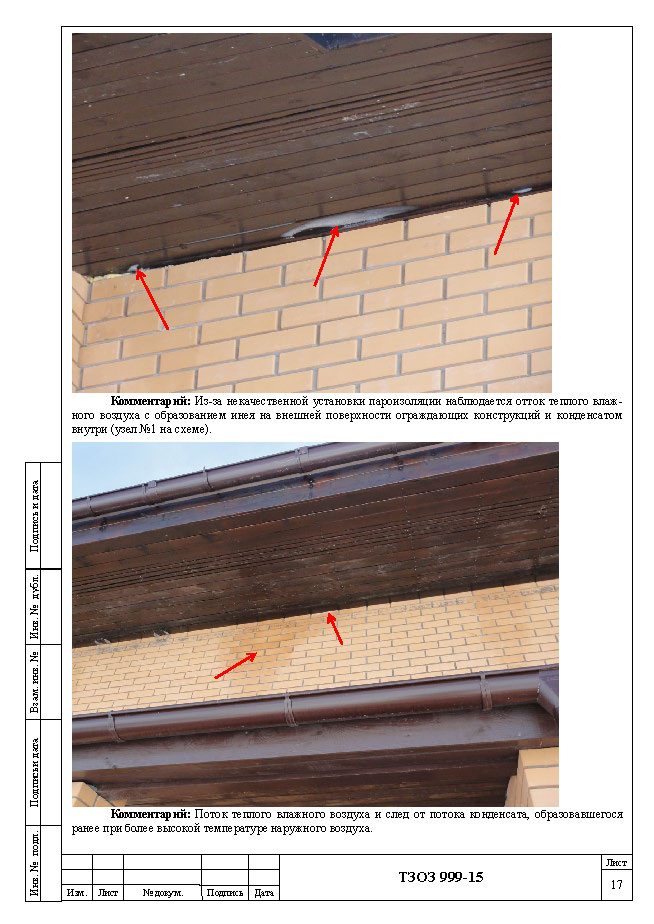
Конденсат на крыше и стенах дома.
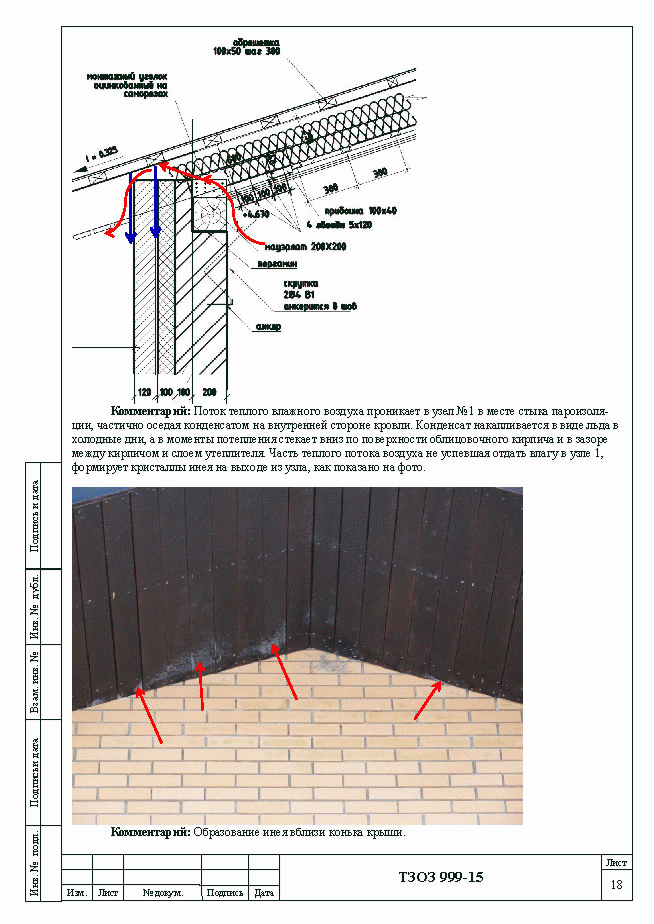
Причина конденсата. Вот почему образуется конденсат на окнах, крыше и стенах.
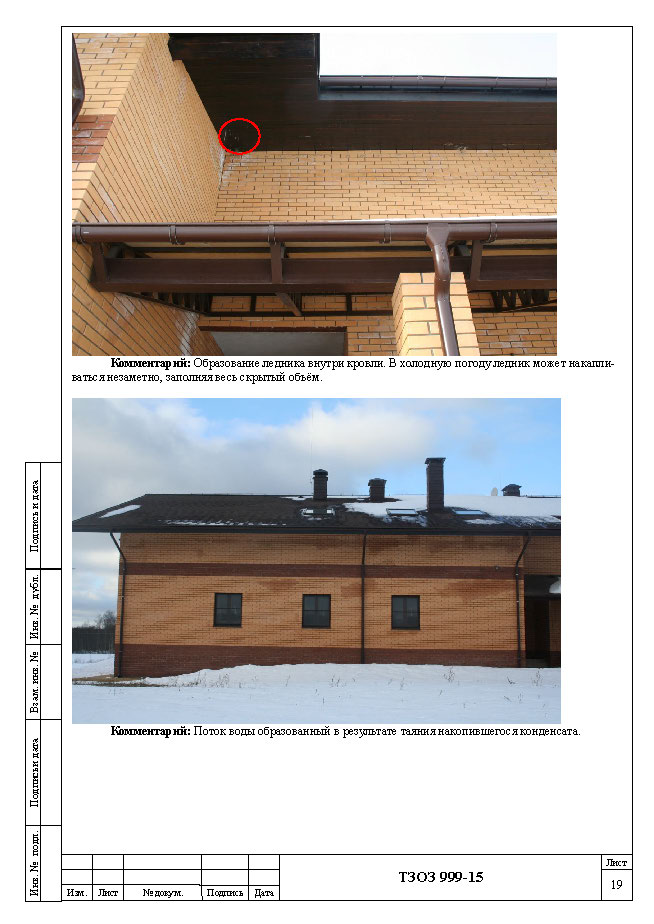
Промерзание стен дома.
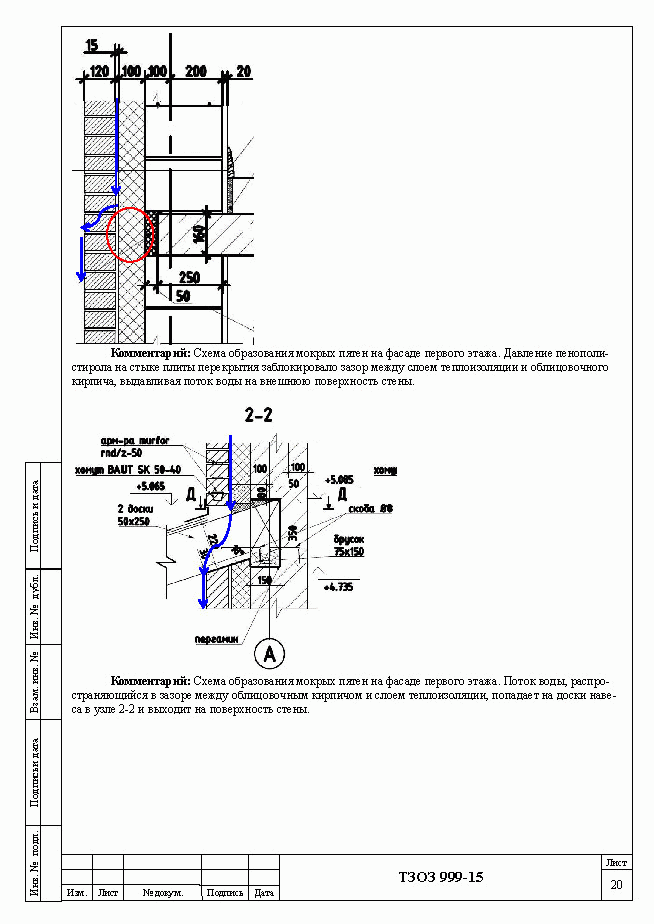
Причина конденсата. Вот почему собирается конденсат на стенах.
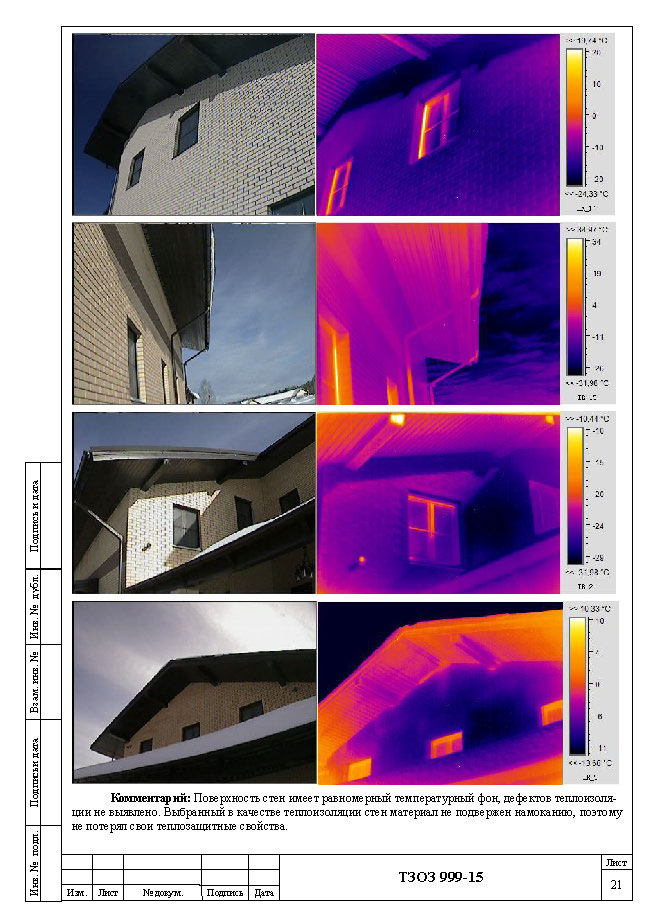
Тепловизионное обследование дома.
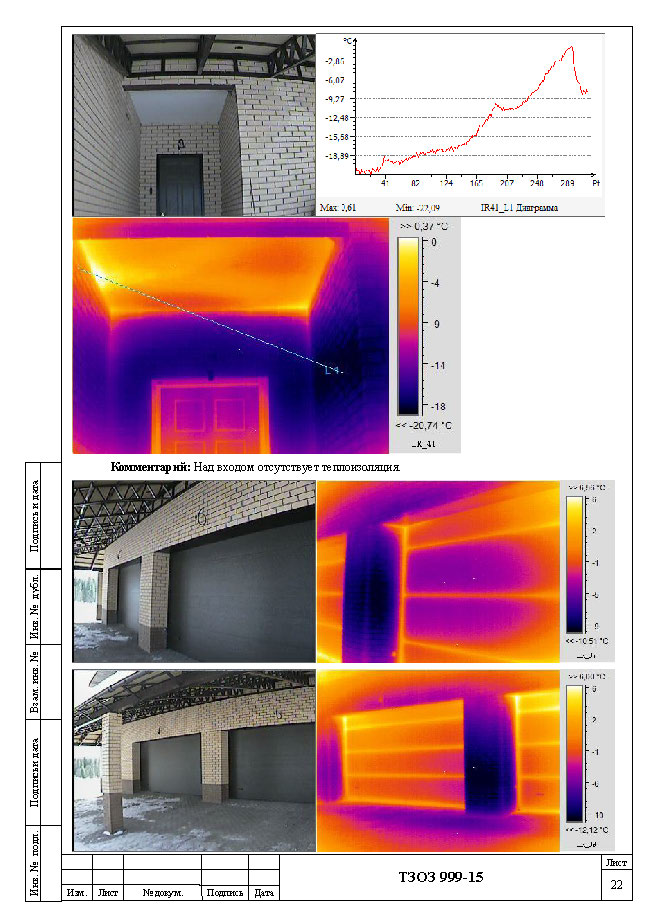
Обследование тепловизором ворот и дверей.
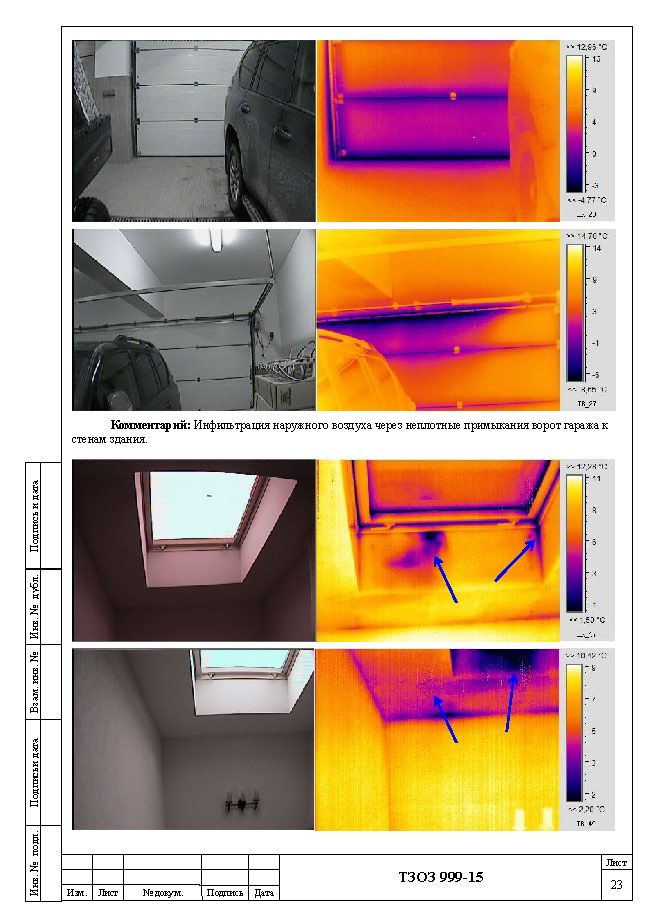
Съемка тепловизором частного дома.
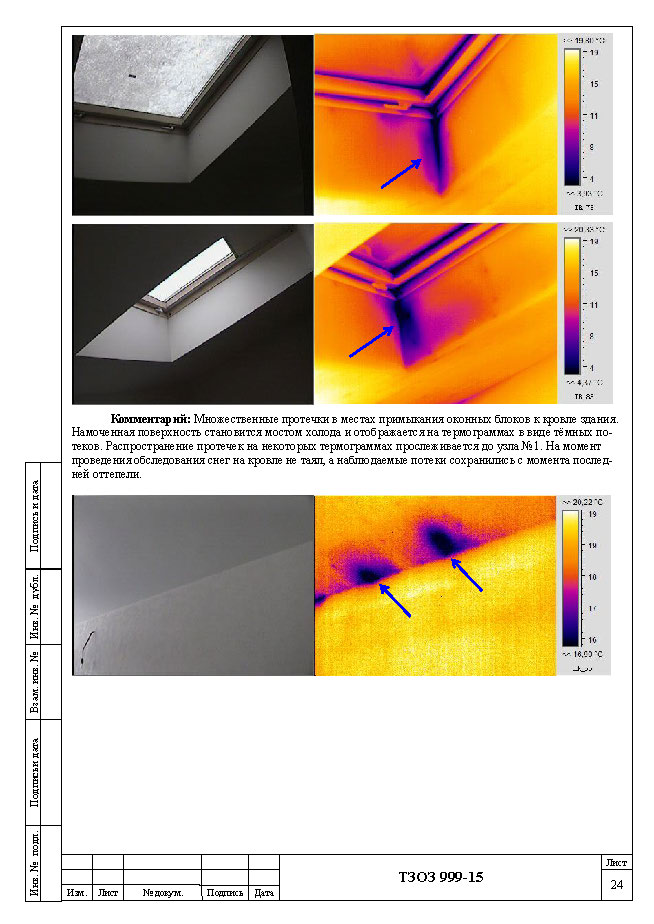
Обследование тепловизором жилого дома.
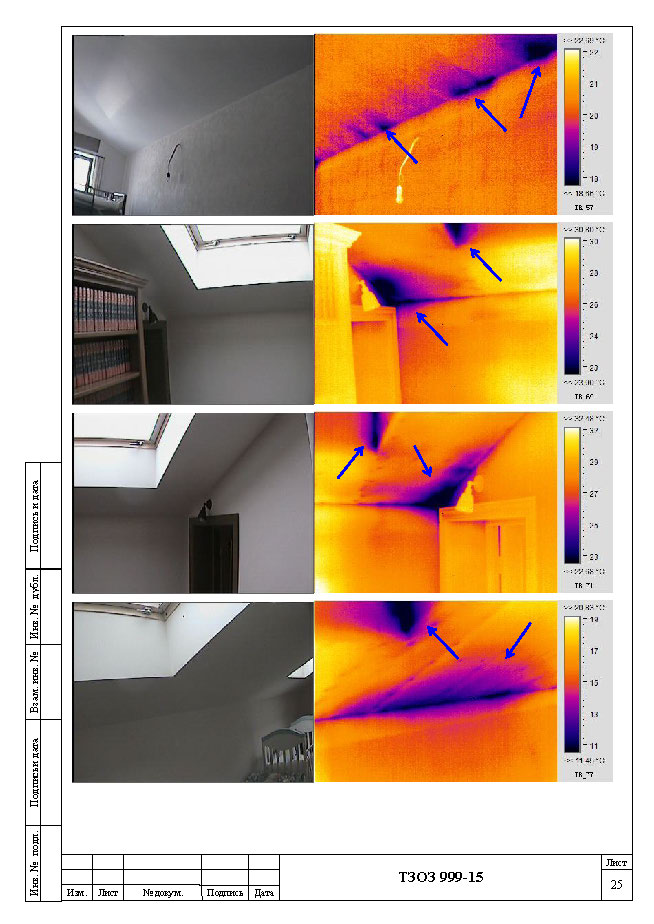
Обследование тепловизором коттеджа.
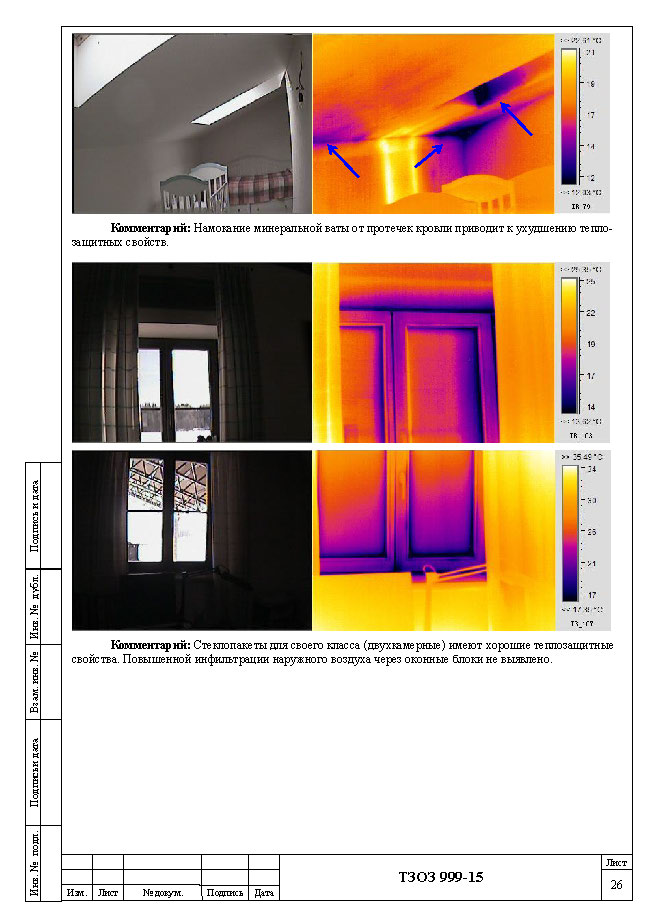
Обследование дома тепловизором.
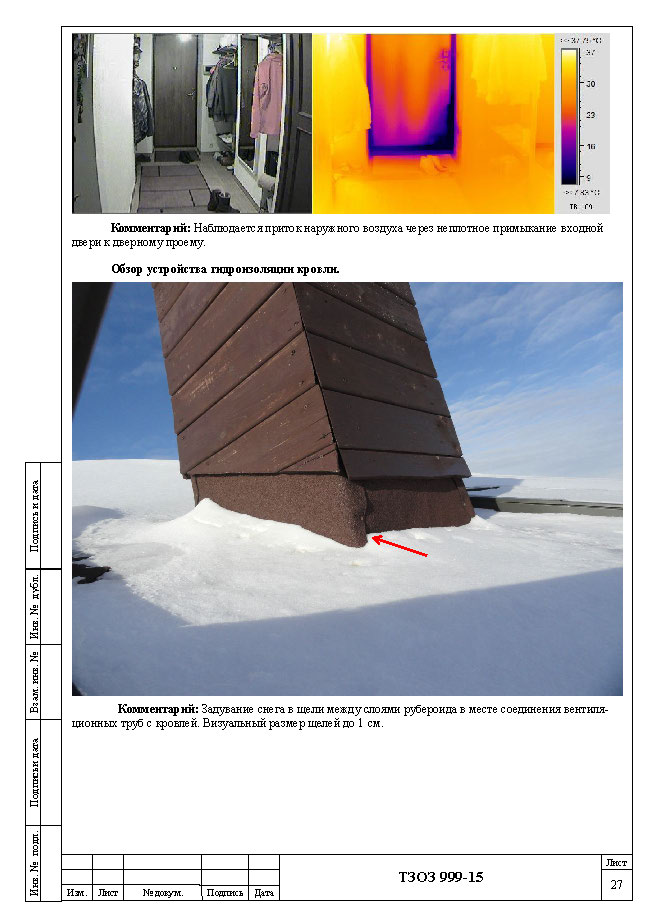
Тепловизионное обследование коттеджа.
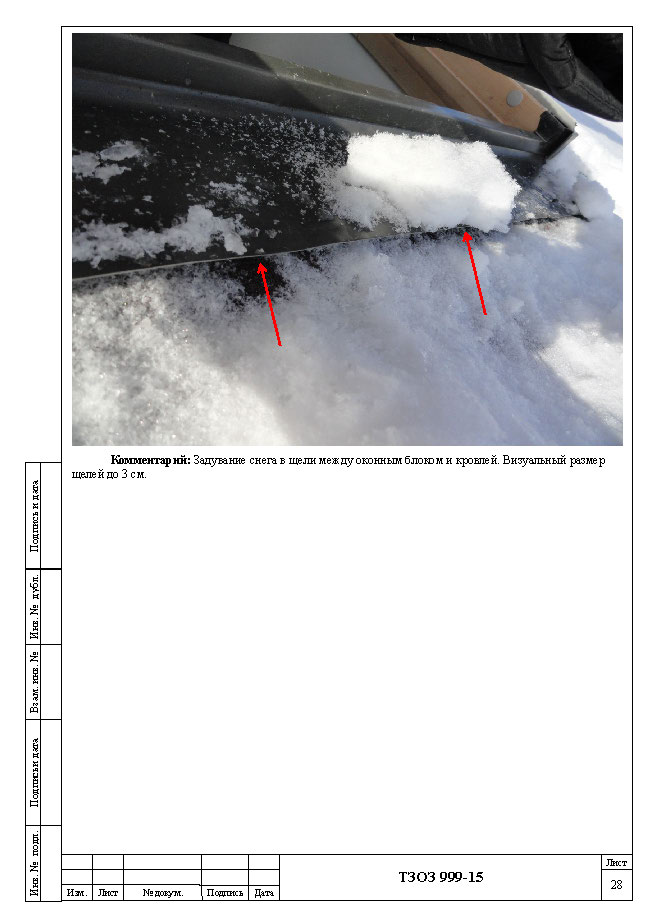
Тепловизионное обследование дома.
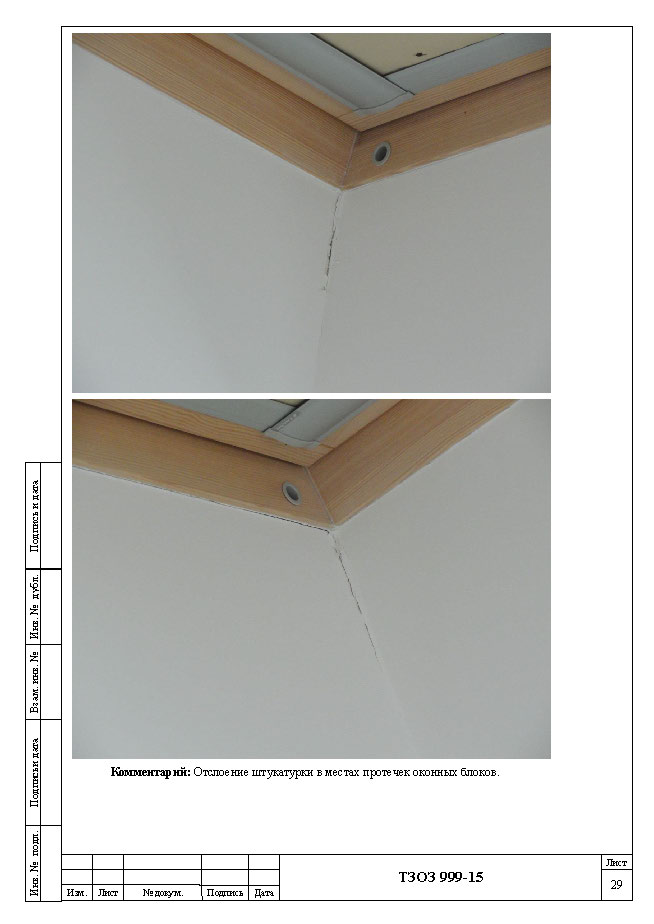
Обследование дома тепловизором.
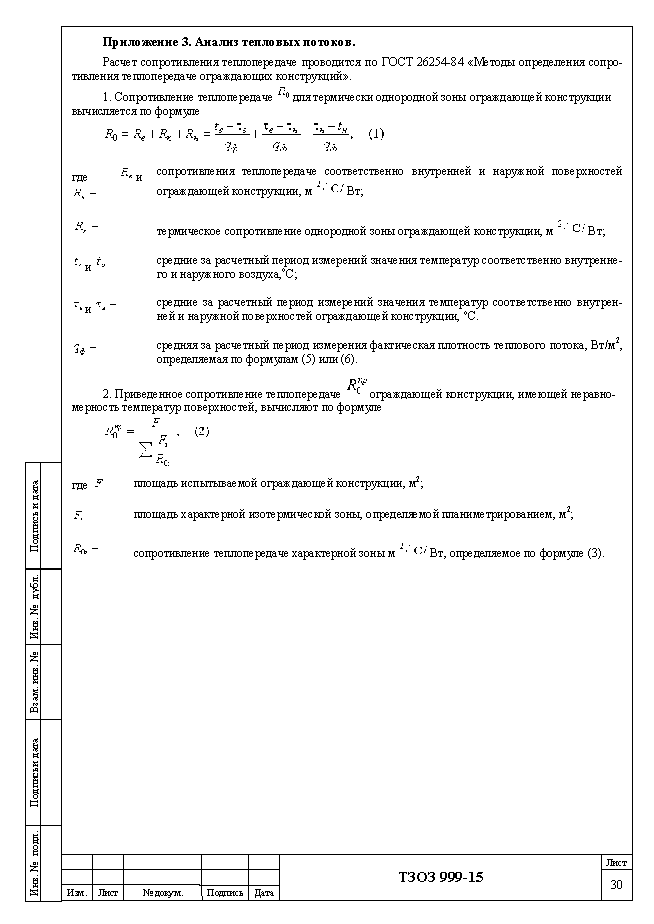
Анализ тепловых потоков.
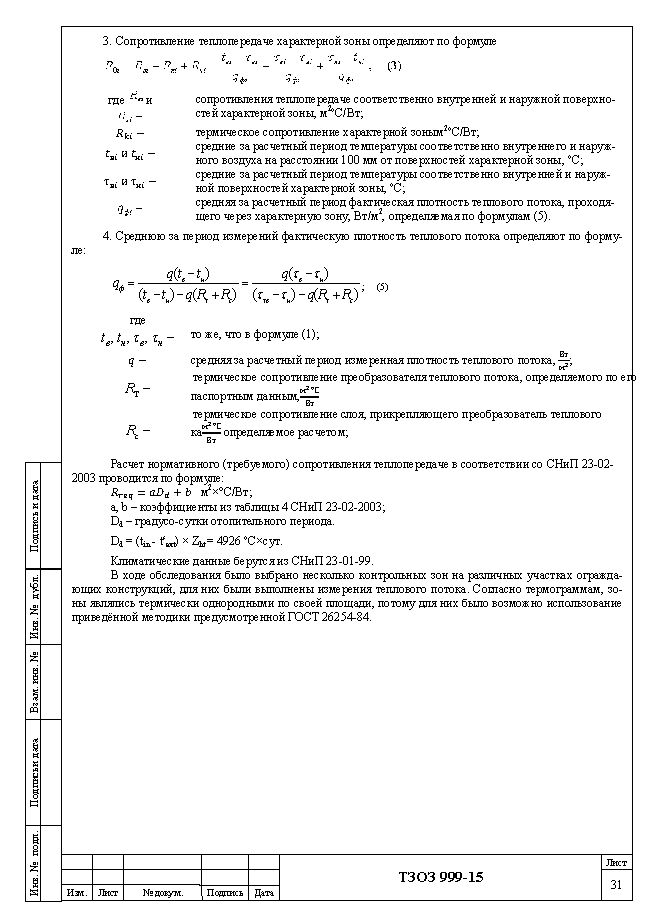
Расчет сопротивления теплопередаче.
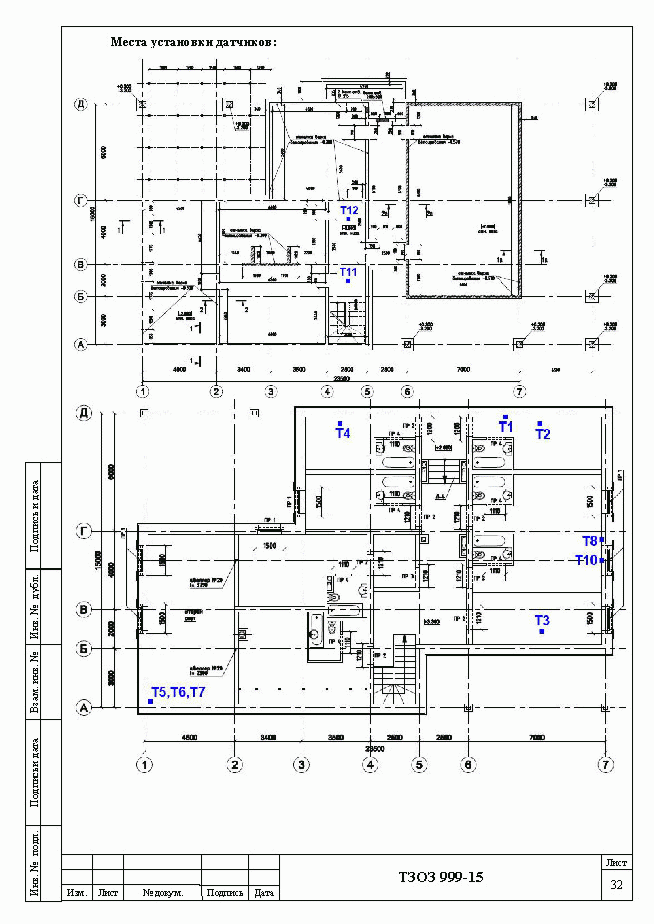
Места измерения тепловых потоков.
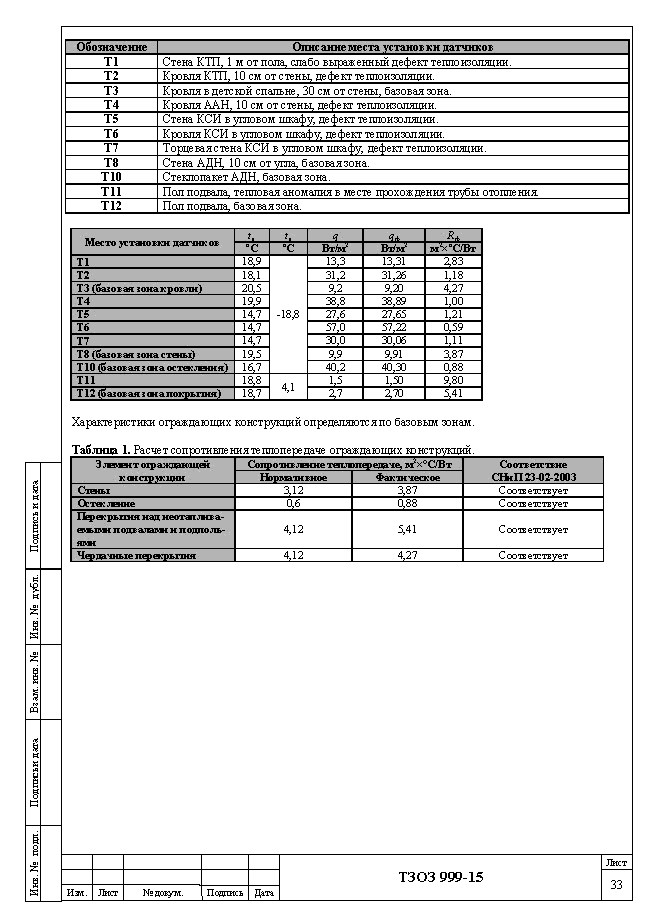
Результаты тепловизионного обследования.
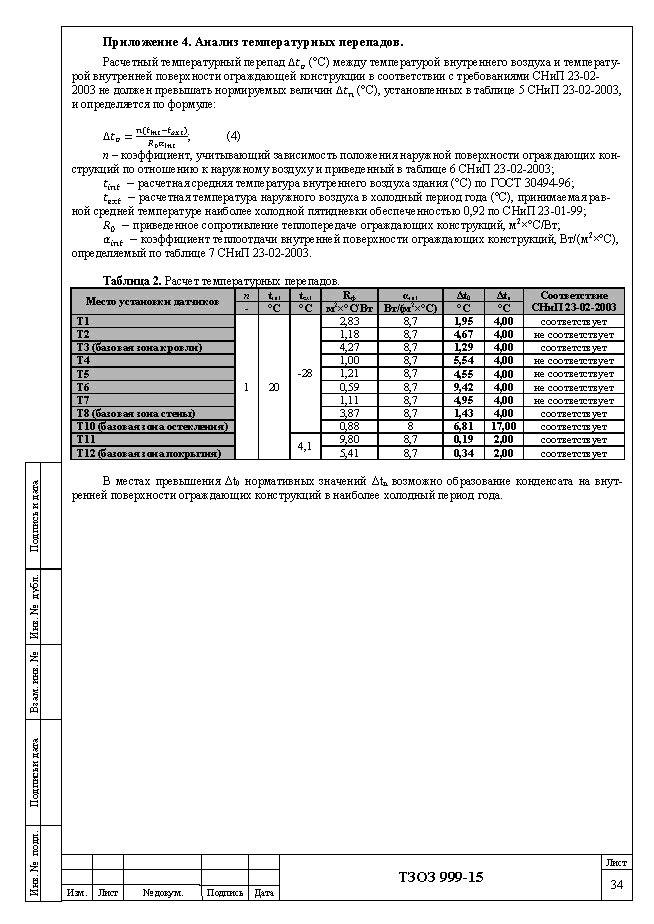
Анализ температурных перепадов.
www.mosexp.ru