Электроды разного диаметра: специфика применения. Толщина электрода в зависимости от толщины металла
Выбор электродов для сварки: рекомендации
Выбор электродов для сварки — это неотъемлемый момент при подобных процессах. Современное строительство редко когда обходится без применения этого вида работ. Причем это относится к малоэтажным строениям (частные и дачные дома) и к постройкам больших коммерческих зданий.

Качество сварки, прежде всего, зависит от качества электрода, которым была произведена работа, поэтому к его выбору необходимо подойти особо внимательно и ответственно.
Каркасы, емкости, основания для гаражей и навесов, элементы кровли — все металлические детали этих конструкций соединены между собой средствами сварки. Для того чтобы шов получился качественным, надежным и прочным, необходимо иметь хорошее оборудование и расходные материалы. Поэтому выбор самих электродов для сварки является одним из основных при подготовке работ. От того, насколько правильно подобраны электроды, зависит качество выполненного сварного соединения.
Оборудование для сварочных работ
Существует несколько способов, которым выполняется сварка:

Классификация видов сварки.
- газопрессовая;
- контактная;
- роликовая;
- электрошаговая.
Но выделяют газопрессовую и контактную. При газопрессовой сварке используется пламя ацетилкислорода. Этот способ выбирают, если надо добиться высокой производительности выполненных работ. Поэтому отраслями, где применяют газопрессовую сварку, являются нефтяная и газовая при прокладке магистральных трубопроводов на большие расстояния.
При контактной сварке процесс выполняется при помощи электрического тока, обладающего низким напряжением и высокой силой тока. Этот способ выполняется вручную или механически. При этом контактную сварку можно выполнять встык, внахлест, детали могут прикладываться друг к другу под любым углом. От того, каким принят способ выполнения шва, зависит выбор необходимого оборудования. В итоге от выбора электрода, сварочных агрегатов зависит качество выполненных работ.
К выбору сварочного оборудования следует подходить из конкретных условий выполнения работ. А именно:

Напряжение питающей сети сварочного аппарата для бытового использования является 220 В.
- Напряжение питающей сети. При производственных условиях оно составляет 380 В, в бытовых — 220В. При частых скачках напряжения рациональнее использовать инвертор, который может защитить аппарат от подобных влияний и обеспечит надежную работу.
- Типы и марки металлов, которые необходимо соединить. Постоянный ток, который требуется для сварки деталей из чугуна или цветного металла могут обеспечить сварочный генератор или выпрямитель. Трансформатор применяют для сварки элементов из черного металла.
- Вес сварочного аппарата. Не всегда большой вес говорит о длительности полноценного использования. Современные сварочные агрегаты, обладая достаточно небольшим весом, могут служить долго, выполняя все поставленные задачи, в отличие от увесистых устаревших моделей. Особенно это актуально, когда требуется частое перемещение как между объектами, так и внутри объекта строительства.
- Время работы без возможного перегрева. Эта паспортная характеристика, которая указывается в документации к оборудованию, обозначает, сколько времени может работать аппарат без перерыва, чтобы не допустить угрозы перегрева. Например, если указаны цифры 5х20%, то это означает возможность беспрерывной работы 1 минуту, а затем необходим перерыв в 4 минуты.
- Выходные характеристики сварочного аппарата. При меньших показателях выходных характеристик тока и напряжения дают возможность выполнять работы с толстым металлом. Однако в таких аппаратах обмотка быстрее нагревается, следовательно, термостат быстрее может вызвать отключение сварочного агрегата.
Кроме сварочного оборудования в процессе сваривания 2-х и более металлических деталей принимает участие электрод. К выбору, которого надо подходить ответственно. От него зависит не только качество и долговечность шва, но и количество наплавляемого металла, его состав.
Вернуться к оглавлению
Практические рекомендации

Схема сварочного электрода.
Производитель сварочного оборудования чаще всего дает рекомендации, какие именно марки и типы электродов можно использовать в сочетании с ним. Проволока, которая лежит в основе электрода, должна быть качественной изначально. Далее, определяющим параметром использования конкретного типа электродов, является его покрытие.
Выбор электродов необходимо делать исходя из параметров и характеристик свариваемых поверхностей. При этом надо учитывать, что каждая из марок электродов обладает своими особенностями применения. Если использовать не тот тип электрода, то сварной шов может не получиться.
Электроды, согласно нормативным документам, можно разделить по нескольким параметрам:
- назначения использования;
- вид покрытия и его толщина;
- механические свойства и состав покрытия.
Вернуться к оглавлению
Покрытие электрода
Покрытие проволоки может быть:

Виды покрытия электрода для сварки.
- Рутиловым. Оно выполнено из диоксида титана, который для напыления на проволоку используется в виде порошка. Применение этого покрытия позволяет получить качественный сварной шов. Такие электроды способствуют стабилизации при горении. Эта марка используется для соединения ржавых или влажных деталей. Малое количество образовывающихся при сварке брызг, способствует малому расходу металла при выполнении работ, шов при этом получается аккуратным. Они способны работать как при использовании оборудования, работающего на постоянном, так и на переменном токе. Стоимость их довольно высокая, но широта применения данного вида вполне это оправдывает.
- Ильменитовым. При покрытии проволоки к диоксиду титана добавляют железо. При работе образуется прочный эластичный шов.
- Основным.
В качестве материалов для покрытия используют карбонатовые и фтористые соединения.
Они устойчивы к воздействию изменяющимся температурам окружающей среды. Но существенным недостатком этого вида электродов является то, что их применение ограничивается только деталями, которые не имеют ржавой кромки. Однако их можно использовать при выполнении работы в любом положении и направлении (сверху вниз, снизу вверх). Их применяют для сваривания конструкций, которые в дальнейшем будут эксплуатироваться при низкой температуре с переменными или ударными нагрузками. Особенностью использования данных электродов является то, что они могут быть применены только в сварочных работах, которые ведутся постоянным током обратной полярности.
Кроме того, различают еще рутилово-основное и рутилово-целлюлозное покрытие. Электроды, которые покрыты первым из них, используются при прокладке трубопроводов любого назначения среднего или малого диаметра. Второе покрытие наносят на проволоку, которую будут применять при сварке толстого покрытия.
Вернуться к оглавлению
Дополнительные моменты
При выполнении сварки постоянным током существует 2 возможности, как подключить электрод к оборудованию:

Схема подключения электрода при сварке током прямой полярности.
- Если полярность прямая, электрод соединяют с зажимом «-», а деталь к «+».
- Если полярность обратная, то электрод соединяют с «+», а деталь с «-». Эта полярность используется при работе с металлами из тонкого листа, прожог при этом невозможен.
Взаимодействие 3-х характеристик сварки (диаметр электродов, толщина металла сварки, сила тока и вид тока) обуславливает способ выбора. Для этого используют соотношение, которое определяет, что для 30-40А силы тока принимается 1 мм диаметра проволоки. Если процесс сварки выполняется вертикально, то силу тока можно уменьшить на 15%.
Данное соотношение выглядит таким образом:

Таблица выбора электрода от толщины металла и силы тока.
- Диаметр 8-12 мм применим при силе тока 450 А при толщине металла более 8 мм. Длина швов составляет 35-45 см. Свариваемый металл может быть из любого вида стали.
- Диаметр 6 мм используют при силе тока 230-370 А, толщина металла 4-15 мм. Сварной шов имеет длину 35-45 см.
- Диаметр 5 мм используется при силе тока 150-280 А, металлические детали имеют толщину 4-15 мм. Образуется шов длиной 35-45 см.
- Диаметр 4 мм применяют, если сварка проходит при 100-220 А, толщина металла 2-10 мм. Тип выбора стали при выполнении сварки, не имеет значения.
- Диаметр 3 мм используется, когда сварка производится при силе тока в 70-100 А, а толщина металла является 2-5 мм.
- 2,5 мм применим, если соответствует сила тока 70-100 А при толщине 1-3 мм с длиной шва в 25-35 см.
- Диаметра 2 мм используется, когда сила тока составляет 50-70 А, металл имеет толщину 1-2 мм. Шов должен быть не более 25-30 см.
Электроды, диаметр которых 3 мм и менее, используются при сварке деталей, при производстве которых использована легированная сталь.
Кроме того, по цвету покрытия можно определить, какие именно добавки участвовали при его напылении. Для зеленого покрытия использован только вольфрам. Если покрытие синее, то к вольфраму добавили оксид лантана. Для получения белого покрытия электрода к вольфраму добавлен оксид циркония.
moiinstrumenty.ru
Электроды разного диаметра: специфика применения
Качественное соединение свариваемого металла кроме особенностей подключения сварочного аппарата во многом зависит от спецификации электрода. Диаметр металлического стержня электрода также важен для правильного соединения материалов, как и знание специфики самих материалов.
Для электродуговой сварки толщина электрода выступает важной характеристикой требующей не только корректировки соответствующего показателя силы тока, но и возможности расплавить ввариваемые поверхности заготовок. Маркировка диаметра электродов всегда указывается на упаковке. Такое маркирование позволяет подобрать оптимальную силу тока и рассчитать толщину деталей для сваривания, то есть рассчитать мощность сварочного аппарата и выставить необходимые показатели для работы.
Для сваривания тонкотелых деталей, например, листового металла используются аппараты ручной дуговой сварки, в которых применяется технология сваривания металла в защитной среде инертных газов, это в основном ручная аргонодуговая сварка, или как ее называют по-другому сварка полуавтоматом. Такая особенность связана с тем, что самые тонкие по диаметру электроды 1,2-1,6 мм обычно в домашних мастерских не используются, потому, что требуют высокой квалификации сварщика.
Самыми популярным выступают размеры диаметром 3 или 3,2 мм. Это основной рабочий диапазон, используемый повсеместно. Стоит отметить, что и большинство сварочных аппаратов бытового назначения отлично справляются с большинством задач, именно используя такие электроды.
Электроды толще 6 мм в основном используются для восстановления поврежденных поверхностей или наплавки металла, это специальный вид продуктов, требующих значительный по силе ток, который большинство бытовых инверторов просто не в состоянии выдать из-за своих характеристик.
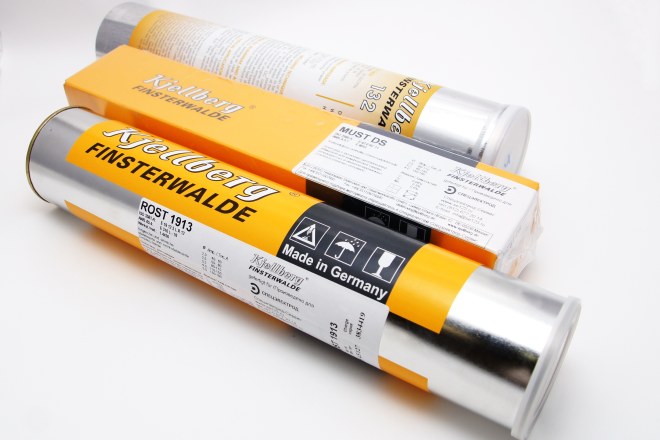
В целом толщина электродов может быть использована для сваривания деталей, в зависимости от их толщины:
- 1-2 мм металла соединяется электродами 1,5-2 мм;
- для металла 3-5 мм подходят 3-4 мм марки;
- конструкции из металла 6-12 мм свариваются 4-5 мм электродами;
- для металла 12-15 мм подходят 5 мм;
- 16-20 мм требуют диаметр в 6-8 мм;
- более мощные конструкции свариваются 8-10 мм стержнями.
Вторым важным показателем диаметра электрода выступает необходимость выдерживания сварочным аппаратом установленной величины сварочного тока:
- 1,5-2 мм требуют 30-45 А;
- 3-4 мм соответствует показатель тока в 65-200, а в зависимости от толщины свариваемого металла;
- 5-6 мм 200-250 А;
- 8 и выше от 250А.
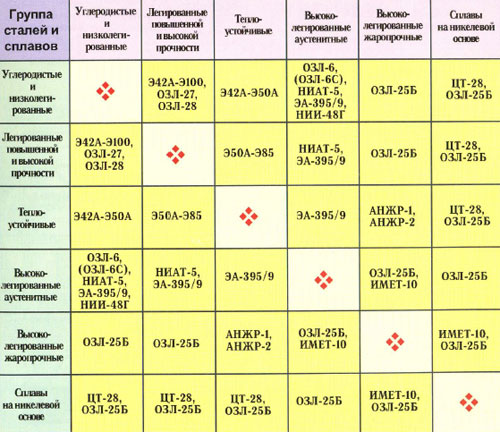
Кроме того, что на упаковке указывается маркировка диаметра электрода и соответствие необходимой силе тока, в расшифровке указывается и целевое назначение для применения соединения специфического материала. Такая спецификация позволяет использовать необходимые по размеру электроды и в месте наложения шва не допускать излишнего нагрева металла, то есть не давать металлу изменять свои свойства.
Так, сегодня в большинстве случаев используется в качестве элементов конструкций металл, маркируемый как:
- стали углеродистые и низколегированные;
- конструкционные легированные стали и конструкции;
- теплоустойчивые легированные стали;
- высоколегированные стали со специальными свойствами;
Соответствующее обозначение в обязательном порядке указывается на упаковке, имеющей соответствующий буквенно-цифровой код:
- «У» – применение для соединения углеродистых и низколегированных сталей и конструкций;
- «Л» – предназначенные для легированных конструкционных сталей;
- «Т» – специальные легированные теплоустойчивые стали;
- «В» – высоколегированные стали;
- «Н» – материалы, используемые для наплавки слоев на поверхности металла.
Обозначение в соответствии с положением шва в пространственным
Для надежного соединения деталей большую роль играет такой фактор, как пространственное положение шва. Для разных видов работ производители разработали специальные по своим свойствам электроды, способные обеспечивать надежную дугу в положениях, для которых они предназначены.
Самым легким считается горизонтальное положение свариваемых деталей, в таком положении детали находятся внизу, а сварочный электрод вверху, это так называемое базовое положение, для сварки деталей в таком положении особых навыков не требуется, да и специальные свойства электродов здесь не нужны.
В буквенно-цифровом коде такое обозначение выступает под цифрой 1.
Для работ во всех положениях свариваемых деталей и поверхностей, кроме наложения шва сверху вниз маркировка соответствует цифре 2.
Для большинства поверхностей, нижнего, горизонтального и в вертикальной плоскости по направлению сварного шва «снизу вверх» соответствует номенклатура 3.
Для нижнего положения и нижнего в «лодочку» положения, так называемых потолочных работ используются электроды с маркировкой 4.
Универсальные по назначению электроды, в том числе и для специальных сварных швов маркируются цифрой 5.
Тем, кто только начинает приобщаться к сварочным работам рекомендуется использовать обычные сварочные электроды самого первого уровня. Это наиболее оптимальный вариант, при условии, что большинство деталей будет расположено в горизонтальном положении и сваривание, будет производиться сверху вниз. Образуемая при возникновении электрической дуги сварная ванны металла в таком положении никуда не утекает, остается на месте и позволяет сформировать надежный шов.
Использование свойств электродов в зависимости от качества удобства в работе
Одним из важных свойств процесса электросварки выступает стабильность электрической дуги, возникающей в момент прикосновения электрода и свариваемой детали. В этом процессе для формирования правильной свариваемой ванны металла играет качество и состав обмазки электрода или его покрытия. Сегодня в зависимости от технологии производства применяются четыре основные типа покрытия стержней, которые имеют различия:
- по толщине слоя покрытия;
- качеству изготовления;
- составу основных компонентов.
Толщина слоя маркируется на упаковке обозначением кода буквенными кодировками:
- М – самое тонкое покрытие;
- С – покрытие средней толщины;
- Д – толстый слой покрытия;
- Г – специальный увеличенный толстый слой покрытия.
Качество изготовления, указывается цифровым обозначением в нижней части маркировки, высшее качество соответствует 1, среднее 2, низкое качество 3.
Для создания нормальных условий сваривания металла большую роль играет не только качество, но и состав покрытия, формирующий шлаковую поверхность и образующий пространство вокруг сварной ванны металла со специальной средой необходимой для плавления металла.
Производители сегодня создают покрытие из основных четырех видов покрытия стержня:
- «А» – покрытие кислотное;
- «Б» – основной вид покрытия;
- «Ц» – целлюлозное или органическое покрытие;
- «Р» – рутиловое.
Для каждого типа покрытия имеются специфические, свойственные только этим видам особенности работы и качественные показатели, как сварочных ванн, так и степени формирования капель металла и их разбрызгивания.
Маркированные буквой «А» – электроды с кислотным типом покрытия, во время работы характеризуются образованием особо жидкой сварочной ванной, это связано с тем, что металл стержня электрода переходит в нее уже в жидком состоянии.
Такое поведение характерно для нестабильной, неустойчивой дуги, во время формирования ванны металл разбрызгивается и появляется высокая вероятность резкого повышения температуры свариваемых заготовок. Кислотное покрытие требует осторожности и умения в работе, поскольку нередки случаи прожига поверхности, особенно тонкого листового металла. Создать прочный шов удается не всегда, при сваривании таким электродом, образуется насыщенный кислородом шов, что не добавляет в крепости соединению.
Основное покрытие, маркирующиеся литерой «Б» среди своих особенностей формирует короткую дугу, это особенность проявляется в формировании ванны с малой подвижностью. При расплавлении металла электрода формирует капли в основном среднего и крупного размера, такая размерность капли не дает растекаться металлу и шов ложиться более жесткий. При использовании сварочных аппаратов переменного тока следует быть особо внимательным, поскольку плавиковый шпат покрытия CaF2, дает дополнительную корку, что существенно усложняет процесс сварки.
С другой стороны, это тот тип покрытия, который среди всех типов отличается наилучшими характеристиками вязкости и плотности. Сварочный шов с использованием электродов с основным покрытием практически не образуют трещин и разрывов, металл отлично заполняет пустоты и надежно соединяет заготовки. Электроды с основным покрытием для ручной дуговой сварки применяются не только для сваривания простых конструкций, они повсеместно используются для конструкций с высокой нагрузкой и такими, к которым предъявляются особые требования, например, емкости подавлением.
Вместе с тем, такой отличный результат требует к применению электродов с основным покрытием и дополнительной подготовки поверхностей:
- устройство фасок заготовок;
- разделка кромок;
- зачистка от ржавчины и обработка от органических примесей;
- надежное и плотное сочленение частей.
В качестве дополнительной подготовки рекомендуется прокалить поверхности для улучшения свойств сварного шва.
Органические вещества, применяемые в формировании покрытия электродов маркируются на упаковке литерой «Ц», это обозначение свидетельствует, что в числе основных веществ, участвующих в формировании покрытия имеется целлюлоза. Для таких материалов характерной особенностью выступает универсальность применения в плане пространственного наложения шва, они пригодны для любых типов швов. Однако, следует быть особо внимательными при проваривании вертикальных швов и швов с нижним расположением – целлюлозное покрытие дает большое разбрызгивание металла, что приводит в получению грубого, широкого шва. Получить красивый шов новичку с помощью электрода с органическим покрытием будет чрезвычайно сложно, да и опытные сварщики как показывает практика практически не применяют этот тип покрытия при формировании однопроходных лицевых швов. Большое содержание в целлюлозе газообразующих веществ и компонентов, выделяющих при горении огромное количество газа, с другой стороны, отлично формируют газозащитный слой ванны, и не дают угаснуть дуге.
Насыщенность газозащитного слоя вокруг сварочной ванны делает возможным формирование надежного сварного шва, поскольку крупные капли металла не растекаются, и хорошо остывает. Электроды с целлюлозным покрытием незаменимы для вертикальных швов, ответственных соединений в качестве первопроходного конструктивного шва, наложения швов сверху вниз.
Рутиловое покрытие сегодня наиболее оптимальный вариант для тех, кто только собирается начать использовать соединение деталей с помощью электродуговой сварки. Электроды, маркируемые на упаковке литерой «Р» характеризуются легким возбуждением дуги, стабильностью ее поддержания, отличной формой и аккуратностью шва. В дополнении ко всем перечисленным характеристиками следует добавить еще и отличное качество сварного шва, замечательно соединяющее поверхности.
Для рутиловых поверхностей характерным выступает и такая особенность, как возможность прохождения повторным швом поверх первого без удаления шлака. TiO2, входящий в качестве одного из основных компонентов покрытия обеспечивает такую возможность, что существенно экономит силы и возможности. Практически при использовании рутиловых электродов не происходит выделения токсических веществ и позволяет контролировать процесс сварки буквально в любом положении. Формируемый шов соединения имеет низкую пористость внутренней структуры и отличную отделимость шлака. Эти электроды отлично подходят для соединения прихваточных швов, угловых соединений и формирования лицевых швов.
svarkagid.com
Режимы ручной дуговой сварки | Строительный справочник | материалы - конструкции
Режимы дуговой сварки представляют собой совокупность контролируемых параметров, определяющих условия сварочного процесса. Правильно выбранные и поддерживаемые на протяжении всего процесса сварки параметры являются залогом качественного сварного соединения. Условно параметры можно разделить на основные и дополнительные.
Основные параметры режима дуговой сварки: диаметр электрода, величина, род и полярность тока, напряжение на дуге, скорость сварки, число проходов.
Дополнительные параметры: величина вылета электрода, состав и толщина покрытия электрода, положение электрода, положение изделия при сварке, форма подготовленных кромок и качество их зачистки.Выбор диаметра электрода
Диаметр электрода выбирают в зависимости от толщины свариваемого металла, положения, в котором выполняется сварка, катета шва, а также вида соединения и формы кромок, подготовленных под сварку. Для того чтобы правильно выбрать диаметр электрода, можно воспользоваться таблицей 1.
Таблица 1. Примерное соотношение диаметра электрода и толщины свариваемых деталей
Толщина свариваемых деталей, мм | 1-2 | 3-5 | 4-1С | 12-24 | 30-60 |
Диаметр этектрода, мм | 2-3 | 3-4 | 4-5 | 5-6 | 6-8 |
Однако такое соотношение является примерным, так как на этот фактор накладывает отпечаток размещение шва в пространстве и количество сварочных проходов. К примеру, при потолочном положении шва не рекомендуют применять электроды с диаметром более 4 м. Не пользуются электродами больших диаметров и при многопроходной сварке, так как это может привести к непровару корня шва.
Сила тока выбирается в зависимости от диаметра шва длины его рабочей части, состава покрытия, положения сварки и т.д. Чем больше сила тока, тем интенсивнее расплавляется его рабочая часть и тем выше производительность сварки. Но это правило может приниматься с некоторыми оговорками. При чрезмерном токе для выбранного диаметра электрода происходит перегрев рабочей части, что чревато ухудшением качества шва, разбрызгиванием капель жидкого металла и даже может привести к сквозным прогораниям деталей. При недостаточной силе тока дуга будет неустойчива, часто будет обрываться, что может привести к непроварам, не говоря уже о качестве шва. Чем больше диаметр электрода, тем меньше допустимая плотность тока, так как ухудшаются условия охлаждения сварочного шва.
Опытные сварщики силу тока определяют экспериментальным путем, ориентируясь на устойчивость горения дуги. Для тех, кто еще не имеет достаточного опыта, разработаны следующие расчетные формулы: Для наиболее распространенных диметров электрода (3 -6 мм)
I = (20 + 6dэ )dэ
где Iсв — сила тока.
Для электродов диаметром менее 3 мм ток подбирают по формуле:
Icв = 30dэ
Для сварки потолочных швов сила тока должна быть на 10 - 20% меньше, чем при нижнем положении шва.
Кроме того, на силу тока оказывает полярность и вид тока. К примеру, при сварке постоянным током с обратной полярностью катод и анод меняются местами и глубина провара увеличивается до 40%. Глубина провара при сварке переменным током на 15 - 20% меньше, чем при сварке постоянным током. Эти обстоятельства следует учитывать при выборе режимов сварки.
Выбор режима дуговой сварки
При выборе режимов сварки следует учитывать и наличие скоса свариваемых кромок. Все эти обстоятельства учтены и сведены в таблицах 2 и 3. Особенности горения сварочной дуги на постоянном и переменном токе различны. Дуга, представляющая собой газовый проводник, может отклоняться под воздействием магнитных полей, создаваемых в зоне сварки. Процесс отклонения сварочной дуги под действием магнитных полей называют магнитным дутьем, которое затрудняет сварку и стабилизацию горения дуги.
Таблица 2. Режим сварки стыковых соединений без скоса кромок
Характер шва | Диаметр электрода, мм | Ток, А | Толшина металла, мм | Зазор, мм |
Односторонний | 3 | 180 | 3 | 1,0 |
Двухсторонний | 4 | 220 | 5 | 1,5 |
Двухсторонний | 5 | 260 | 7-8 | 1,5-2,0 |
Двухсторонний | б | 330 | 10 | 2,0 |
Примечание: максимальное значение тока должно уточняться по паспорту электродов.
Таблица 3. Режимы сварки стыковых соединений со скосом кромок
Диаметр электрода, мм | Ток, А | Толщина металла, мм | Зазор, мм | Число слоев креме подваренного и декоративного | |
Первого | Последующего | ||||
4 | 5 | 180-260 | 10 . | 1,5 | 2 |
4 | 5 | 180-260 | 12 | 2,0 | 3 |
4 | 5 | 180-260 | 14 | 2,5 | 4 |
4 | 5 | 180-260 | 16 | 3,0 | 5 |
5 | 6 | 220-320 | 18 | 3,5 | 6 |
Примечание: значение величины тока уточняется по паспортным данным электрода.
Особенно ярко выражено магнитное дутье при сварке на источнике постоянного тока. Магнитное дутье ухудшает стабилизацию горения дуги и затрудняет процесс сварки. Для уменьшения влияния магнитного дутья применяют меры защиты, к которым относят: сварку на короткой дуге, наклон электрода в сторону действия магнитного дутья, подвод сварочного тока к точке, максимально близкой к дуге и т.д. Если полностью избавиться от действия магнитного дутья не удается, то меняют источник питания на переменный, при котором влияние магнитного дутья заметно снижается. Малоуглеродистые и низколегированные стали обычно варят на переменном токе.
build.novosibdom.ru
Какими электродами варить тонкий металл
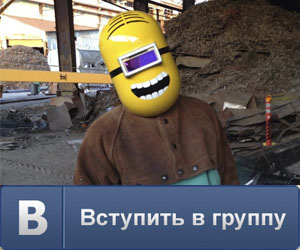
Прежде всего, стоит отметить, что тонким металлом считается металл толщиной 2 или менее миллиметров. В наше время такой металл находит все более широкое применение, потому что для изготовления деталей для сваривания такой толщины не нужно использовать большое количество металла, и, как следствие, Вы можете приобрести такие детали по более выгодным ценам.
Чаще всего со свариванием тонкого металла можно столкнуться при работе с профильными трубами. В большинстве своем толщина металла профильных труб не превышает 2 миллиметров, поэтому производить сваривание таких конструкций можете показаться весьма сложным.
Чаще всего многие производят сваривание тонкого металла ручной дуговой сваркой. К примеру, если Вы производите сваривание, метала толщиной 1,5 миллиметра, то Вам лучше всего воспользоваться электродами толщиной 2 миллиметра. Подбирать сварочный электрод для сваривания тонкого металла Вам нужно исходя из Ваших ожиданий от конструкции и типа металла.
Для сваривания тонкого металла многие используют непрерывную сварку по длине всего шва. Значение сварочного тока равняется 40 – 60 Амперам, а, может быть, больше или меньше, потому что такие параметры зависят от типа сварочного аппарата.
Главное, что Вам нужно достичь при сваривании тонкого металла это проваривание, но не прожиг металла. При проведении сваривания тонкого металла непрерывистой дугой Вам нужно вести электрод со средней скоростью, потому, что превысив ее, Вы проварите только верх шва, понизив – прожжете металл.
Вторым способом сваривания тонкого металла является сваривание с прекращением дуги. В основном при сваривании тонкого металла используется данный способ сваривания. Если же металл при сваривании слишком тонкий или Вы используете слишком большой сварочный ток, то Вам можно использовать точечное сваривание, позволяющее производить сваривание точками, при этом, не прожигая металл.
Происходить сварочный процесс должен достаточно быстро, чтобы металл не успевал остывать. Даже при сваривании точечным способом Вам нужно быть предельно внимательными, что не прожечь металл или сделать поверхностный шов, который не будет способен выполнять свою работу.
А теперь переходим к свариванию тонкого металла полуавтоматом. Да, действительно, производить сваривание полуавтоматической сваркой намного проще, нежели другими способами сваривания. Примечательно, что данный сварочный аппарат может производить сваривание на маленьком токе. При сваривании полуавтоматической сваркой можно производить сваривание непрерывно и точками.
Производить сваривание разным способами с использованием полуавтоматического сварочного аппарата не имеет значения, потому что для успешного сварочного процесса Вам нужно просто в определенные моменты вовремя нажимать на кнопку. Все дело не в сварочных аппаратах, а в опыте сварщика и его желании учиться и использовать современные качественные электроды и технологии сваривания.
elektrod-3g.ru
Сварочные электроды | Электроды от Электродгруп | Производство электродов МР, УОНИ, ОЗС, АНО,
Осуществление любых ответственных работ, в том числе ручной дуговой сварки, одним из обязательных условий имеет компетентный подход к подбору материалов. Неотъемлемой составляющей этой процедуры является соответствующее внимание ко всем параметрам сварочных электродов, одним из которых является их диаметр.
Диаметр сварочных электродов
Диаметр сварочных электродов для работы с различными по химическому составу сталями прописан в различных нормативных документах. К примеру, согласно ГОСТ- 9466-75, определен номинальный диаметр электрода, который соответствует диаметру стержня. Следует отметить, что номинальный диаметр электрода для сварки не включает в себя толщину обмазки.
Толщина покрытия электродов для сварки
Согласно п. 1.5. ГОСТ-9466-75, для каждого диаметра и марки электрода существует своя индивидуальная толщина обмазки. Определяется зависимости от отношения D/d, где D - диаметр с покрытием, а d - диаметр стержня, при этом соотношение у электродов с тонким покрытием (буквенное обозначение М) должно быть менее или равно 1,2; для электродов со средним покрытием (буквенное обозначение С) должно быть менее или равно 1,45; для электродов с толстым покрытием (буквенное обозначение Д) должно быть менее или равно 1,80; а для электродов с особо толстым покрытием (буквенное обозначение Г) должно быть больше 1,80.
К примеру, сварочные электроды УОНИ-13/45, марка Э-42А УОНИИ-13/45-d4-УД Е 412(4)-Б 20. В соответствии с маркой номинальный диаметр электрода равен d4, показатель – Д означает, что покрытие толстое. Полный диаметр D электрода с покрытием равен 6 мм, отношение D/d или 6/4 равно 1,5, что соответствует параметру электродов с толстым покрытием так как попадает в диапазон от 1,45 до 1,8.
Примечательно, что иностранные производители придерживаются таких же правил, только диаметры импортных электродов не соответствуют российским стандартам. Так к примеру японские сварочные электроды LB-52U имеют номинальные диаметры d. 2,6, d. 3,2, d. 4, а диаметры вместе с покрытием D 3,9, D 4,8, D 6, отношение диаметров равны 1,5, что соответствует толстому покрытию. Также сварочные электроды ОК 53.70 фирмы The ESAB Group произведенные в Швеции соответствуют международным стандартам d. 2,6, d. 3,2, d. 4 мм, а принадлежащий ESAB российский Завод ЭСАБ-СВЭЛ выпускает продукцию с торговой маркой ОК с диаметрами российских стандартов.Выбор диаметра электрода
Выбор диаметра электрода для сварки осуществляется в зависимости от толщины свариваемого металла, его марки и химического состава, формы кромок, положения сварки, разновидности соединения. К основным особенностям различных диаметров электродов относятся:
1. Сварочные электроды 1 мм – предназначены для работы с металлом, толщина которого 1-1,5 мм, при силе тока 20-25А;
2. Электроды сварочные 1,6 мм – в соответствии с ГОСТ9466-75 для низкоуглеродистой и легированной стали выпускаются двух размеров 200 или 250 мм, используемые для работы с металлами толщина которых от 1 до 2 мм с силой тока 25-50А;
3. Электроды сварочные 2 мм – согласно ГОСТ9466-75 для низкоуглеродистой и легированной стали изготавливаются длинной 250 мм, допускается также длинна 300 мм, толщина свариваемых металлов от 1 до 2 мм, сила тока 50-70А;
4. Электроды сварочные 2,5 мм – по ГОСТ9466-75 для низкоуглеродистой и легированной стали выпускаются длинной 250-300мм, допускается также длинна 350 мм, толщина свариваемых металлов от 1 до 3 мм, сила тока 70-100А;
5. Электроды сварочные 3 мм – наиболее широко применяемый диаметр электрода, в соответствии с ГОСТ9466-75 для низкоуглеродистой и легированной стали выпускаются трех размеров 300, 350 и 450 мм, предназначены для работы с металлами, толщина которых от 2 до 5 мм с силой тока 70-140А;
6. Электроды сварочные 4 мм – широко используемый диаметр пригодный для работы как на профессиональном так и на бытовом оборудовании. Выпускается согласно ГОСТ9466-75 двух размеров 350 и 450 мм для любых видов стали, для металлов, толщина которых от 2 до 10 мм с силой тока 100-220А;
7. Электроды сварочные 5 мм – электроды этого диаметра требуют достаточно мощного сварочного оборудования. В соответствии с ГОСТ9466-75, изготавливаются длинной – 450 мм для низкоуглеродистой и легированной, а для высоколегированной стали допускается также длинна – 350 мм. Предназначены для работы с металлами, толщина которых от 4 до 15 мм с силой тока 150-280А;
8. Электроды сварочные 6 мм – предназначены для работы на профессиональном оборудование. Согласно ГОСТ9466-75, выпускается длинной – 450 мм для низкоуглеродистой и легированной, а для высоколегированной стали допускается также длинна – 350 мм. Предназначены для работы с металлами, толщина которых от 4 до 15 мм с силой тока 230-370А;
9. Электроды сварочные 8-12 мм – для работы на высокопроизводительном промышленном оборудовании. В соответствии с ГОСТ9466-75, выпускается длинной – 450 мм для низкоуглеродистой и легированной, а для высоколегированной стали допускается также длинна – 350 мм. Предназначены для работы с металлами, толщина которых свыше 8 мм с силой тока от 450А;
При этом необходимо отметить, что при определенном диаметре электрода диапазон силы тока для каждой марки электродов свои. К примеру, при диаметре электрода 3 мм для УОНИ 13/55 сила тока 70-100А, а для МР-3 сила тока 80-140А.
electrodgroup.ru
Выбор диаметра электрода для РДС (ММА)
25.03.2013
Диаметр сварочных электродов для работы с различными по химическому составу сталями прописан в различных нормативных документах. К примеру, согласно ГОСТ- 9466-75, определен номинальный диаметр электрода, который соответствует диаметру стержня. Следует отметить, что номинальный диаметр электрода для сварки не включает в себя толщину обмазки.
Толщина покрытия электродов для сварки
Согласно п. 1.5. ГОСТ-9466-75, для каждого диаметра и марки электрода существует своя индивидуальная толщина обмазки. Определяется зависимости от отношения D/d, где D - диаметр с покрытием, а d - диаметр стержня, при этом соотношение у электродов с тонким покрытием (буквенное обозначение М) должно быть менее или равно 1,2; для электродов со средним покрытием (буквенное обозначение С) должно быть менее или равно 1,45; для электродов с толстым покрытием (буквенное обозначение Д) должно быть менее или равно 1,80; а для электродов с особо толстым покрытием (буквенное обозначение Г) должно быть больше 1,80.
К примеру, сварочные электроды УОНИ-13/45, марка Э-42А УОНИИ-13/45-d4-УД Е 412(4)-Б 20. В соответствии с маркой номинальный диаметр электрода равен d4, показатель – Д означает, что покрытие толстое. Полный диаметр D электрода с покрытием равен 6 мм, отношение D/d или 6/4 равно 1,5, что соответствует параметру электродов с толстым покрытием так как попадает в диапазон от 1,45 до 1,8.
Примечательно, что иностранные производители придерживаются таких же правил, только диаметры импортных электродов не соответствуют российским стандартам. Так к примеру японские сварочные электроды LB-52U имеют номинальные диаметры d. 2,6, d. 3,2, d. 4, а диаметры вместе с покрытием D 3,9, D 4,8, D 6, отношение диаметров равны 1,5, что соответствует толстому покрытию. Также сварочные электроды ОК 53.70 фирмы The ESAB Group произведенные в Швеции соответствуют международным стандартам d. 2,6, d. 3,2, d. 4 мм, а принадлежащий ESAB российский Завод ЭСАБ-СВЭЛ выпускает продукцию с торговой маркой ОК с диаметрами российских стандартов.
Выбор диаметра электрода
Выбор диаметра электрода для сварки осуществляется в зависимости от толщины свариваемого металла, его марки и химического состава, формы кромок, положения сварки, разновидности соединения. К основным особенностям различных диаметров электродов относятся:
1. Сварочные электроды 1 мм – предназначены для работы с металлом, толщина которого 1-1,5 мм, при силе тока 20-25А;
2. Электроды сварочные 1,6 мм – в соответствии с ГОСТ9466-75 для низкоуглеродистой и легированной стали выпускаются двух размеров 200 или 250 мм, используемые для работы с металлами толщина которых от 1 до 2 мм с силой тока 25-50А;
3. Электроды сварочные 2 мм – согласно ГОСТ9466-75 для низкоуглеродистой и легированной стали изготавливаются длинной 250 мм, допускается также длинна 300 мм, толщина свариваемых металлов от 1 до 2 мм, сила тока 50-70А;
4. Электроды сварочные 2,5 мм – по ГОСТ9466-75 для низкоуглеродистой и легированной стали выпускаются длинной 250-300мм, допускается также длинна 350 мм, толщина свариваемых металлов от 1 до 3 мм, сила тока 70-100А;
5. Электроды сварочные 3 мм – наиболее широко применяемый диаметр электрода, в соответствии с ГОСТ9466-75 для низкоуглеродистой и легированной стали выпускаются трех размеров 300, 350 и 450 мм, предназначены для работы с металлами, толщина которых от 2 до 5 мм с силой тока 70-140А;
6. Электроды сварочные 4 мм – широко используемый диаметр пригодный для работы как на профессиональном так и на бытовом оборудовании. Выпускается согласно ГОСТ9466-75 двух размеров 350 и 450 мм для любых видов стали, для металлов, толщина которых от 2 до 10 мм с силой тока 100-220А;
7. Электроды сварочные 5 мм – электроды этого диаметра требуют достаточно мощного сварочного оборудования. В соответствии с ГОСТ9466-75, изготавливаются длинной – 450 мм для низкоуглеродистой и легированной, а для высоколегированной стали допускается также длинна – 350 мм. Предназначены для работы с металлами, толщина которых от 4 до 15 мм с силой тока 150-280А;
8. Электроды сварочные 6 мм – предназначены для работы на профессиональном оборудование. Согласно ГОСТ9466-75, выпускается длинной – 450 мм для низкоуглеродистой и легированной, а для высоколегированной стали допускается также длинна – 350 мм. Предназначены для работы с металлами, толщина которых от 4 до 15 мм с силой тока 230-370А;
9. Электроды сварочные 8-12 мм – для работы на высокопроизводительном промышленном оборудовании. В соответствии с ГОСТ9466-75, выпускается длинной – 450 мм для низкоуглеродистой и легированной, а для высоколегированной стали допускается также длинна – 350 мм. Предназначены для работы с металлами, толщина которых свыше 8 мм с силой тока от 450А;
При этом необходимо отметить, что при определенном диаметре электрода диапазон силы тока для каждой марки электродов свои. К примеру, при диаметре электрода 3 мм для УОНИ 13/55 сила тока 70-100А, а для МР-3 сила тока 80-140А.
svarka-udm.ru
Ручная сварка металлическим электродом. Технология ручной сварки
При сварке металлическим электродом по методу Славянова электрическая дуга горит между свариваемым изделием и электродом. До ведения процесса сварки электросварщик включает ток, берет в правую руку электрододержатель с электродом и закрывает лицо маской или щитком для защиты от лучей и яркого света дуги. После этого, коснувшись металла в месте шва концом электрода и быстро отведя его от изделия на 2—3 мм, возбуждает дугу. Затем, перемещая электрод вдоль шва, производит сварку изделия.Под влиянием высокой температуры сварочной дуги, равной приблизительно 6000°, металл электрода и изделия расплавляется. Под дугой образуется ванна жидкого металла с вдавленной поверхностью. Углубление в жидком металле называется кратером. Расплавленный металл ванны, остывая, образует сварной шов соединения.При обрыве дуги в процессе сварки металл быстро остывает и на конце шва остается конечный кратер. В кратере сконцентрированы большие напряжения, возникшие при остывании шва и нередко от него берут начало трещины в электросварных швах. Поэтому кратер необходимо заплавлять или конец шва выводить на специальные планки.Расстояние между концом электрода и поверхностью расплавленного металла называется длиной дуги.Глубина, на которую расплавляется при сварке основной металл, называется глубиной проплавления, или проваром.Для обеспечения прочного соединения изделий сварочным швом глубина провара должна быть не менее 1 мм.Электросварщик должен обладать большим навыком, чтобы поддерживать постоянную длину дуги. Следует стремиться держать дугу покороче. Это увеличивает глубину провара, уменьшает разбрызгивание жидкого металла, улучшает качество шва. И, наоборот, при очень длинной дуге глубина провара уменьшается, плавящийся электрод дает сильное разбрызгивание, качество наплавленного металла ухудшается. При сварке толсто-обмазанными электродами длина дуги должна быть не более 3—4 мм.
Во время сварки нагреву подвергается основной металл, прилегающий к шву. Переходная зона, лежащая между расплавленным металлом и основным, нерасплавленным, металлом, называется зоной влияния или зоной термического воздействия. В этой зоне металл имеет измененную структуру и ухудшенные механические свойства, в ней часто возникают трещины. При сварке малоуглеродистых сталей свойства металла в зоне влияния не существенно отличаются от свойств основного металла.Если сварщик перемещает дугу прямолинейно по поверхности изделия, то получается полоска наплавленного металла, так называемый валик.Поперечное сечение валика определяется его высотой, шириной и глубиной проплавления.Сечение валика шва зависит от скорости перемещения электрода вдоль шва. Чем медленнее сварщик перемещает электрод, тем шире будет валик.Для получения широких валиков сварщик придает электроду колебательные движения поперек шва.В последние годы в отечественной промышленности получил распространение высокопроизводительный способ сварки опертым электродом или погруженной дугой, разработанный Центральной научно-исследовательской лабораторией строительных сооружений института «Проектстальконструкция».Для сварки этим способом требуются электроды с более толстой обмазкой. Электросварщик после возбуждения дуги опирает конец электрода на свариваемое изделие. При горении дуги на конце электрода образуется чехольчик из нерасплавленной обмазки, которым электрод опирается на изделие. Чехольчик поддерживает длину дуги в 2—3 мм, препятствуя короткому замыканию электрода.При сварке погруженной дугой повышается производительность ручной сварки, увеличивается глубина проплавления металла и достигается экономия электродов и электроэнергии до 30% по сравнению с обычным способом ручной сварки.При выполнении сварочных работ весьма важно соблюдать правильный сварочный режим.В определение сварочного режима при ручной сварке входят понятия о факторах, влияющих на качество и производительность сварки. К ним относятся: диаметр электрода, род тока (постоянный или переменный), при сварке на постоянном токе полярность, сила сварочного тока и скорость перемещения дуги.Диаметр электрода подбирается в зависимости от толщины свариваемого металла, положения шва в пространстве, типа сварного соединения. Недопустимо производить, сварку тонкого металла электродами большого диаметра, так как при этом будут сквозные прожоги металла. Нецелесообразно также производить сварку металла большой толщины электродами малого диаметра, так как в этом случае значительно увеличивается время для заварки шва.При сварке многослойных швов первый слой выполняется электродами диаметром 3—4 мм, чем обеспечивается провар корня шва. Последующие слои выполняются электродами диаметром 5—8 мм. При многослойной сварке необходимо стремиться к наименьшему числу слоев, наплавляя каждый последующий слой возможно большим диаметром электродов, что ускоряет выполнение сварочных работ.Вертикальные и горизонтальные швы не рекомендуется сваривать электродами диаметром, превышающим 5 мм, так как при сварке электродами большего диаметра образуется ванна больших размеров, жидкий металл которой стремится стекать вниз.Примерное соотношение между диаметром электрода и толщиной свариваемого металла приведено в таблице 1.
Соотношение между диаметром электрода и толщиной свариваемого металла
На производительность сварки и качество шва весьма важное влияние оказывает сила сварочного тока, которая устанавливается в зависимости от толщины свариваемого металла и диаметра электрода.Сила тока должна быть такой, чтобы после сварки отсутствовали прожоги основного металла, непровар, подрезы основного металла вдоль шва, поры в шве.Силу сварочного тока в зависимости от принятого диаметра электрода при ручной сварке можно ориентировочно подбирать по таблице 2.
Сила сварочного тока в зависимости от диаметра электрода
При сварке горизонтальных швов сила тока уменьшается по сравнению с силой тока для сварки в нижнем положении примерно на 10—15%, а для потолочной — на 15—20%.
загрузка...
iron-lab.ru