Защитное действие цинкового покрытия. Цинковое покрытие
Свойства цинкового покрытия и область применения
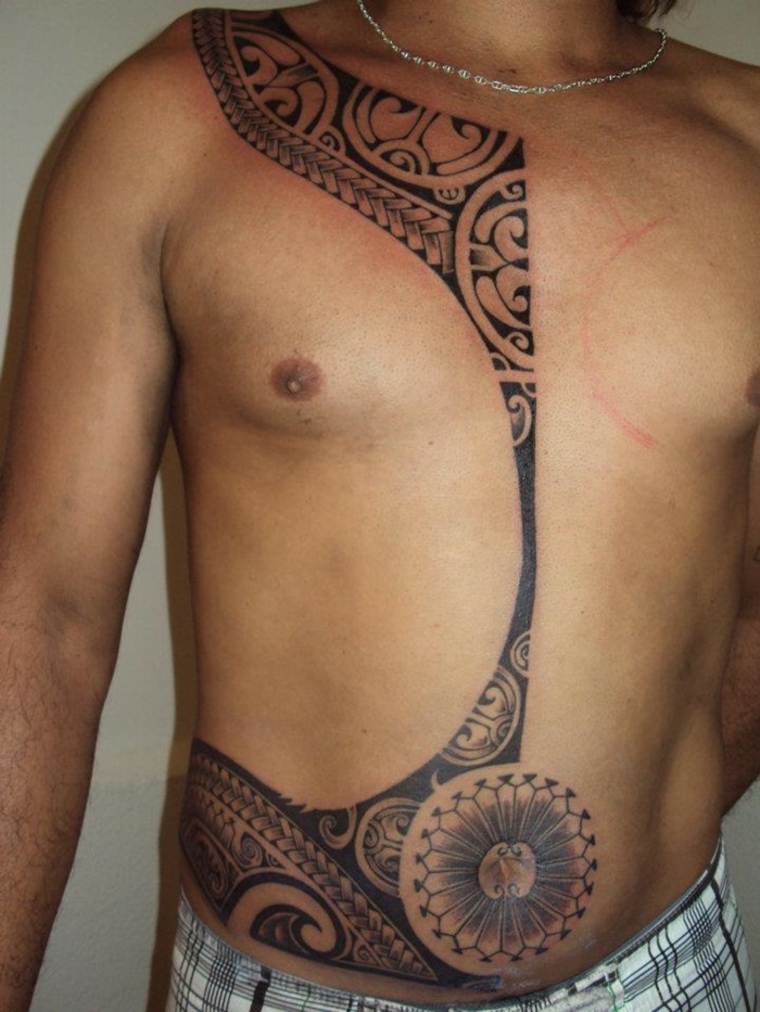
Цинковые покрытия являются достаточно эластичными и хорошо выдерживают развальцовку, изгибы, вытяжку. Свежеосажденный цинк хорошо паяется с применением бескислотных флюсов; для пайки цинковых покрытий, находившихся на воздухе длительное время, необходимы активные флюсы.
Цинк относится к весьма активным металлам, легко реагирующим с кислыми и щелочными растворами. В паре с железом, имеющим более положительный потенциал, цинк является анодом, поэтому в результате коррозионных процессов, происходящих на поверхности оцинкованных деталей под действием влажного воздуха, растворяется цинк, а не основной металл. Коррозионный процесс, происходящий по такой схеме, является более благоприятным, чем в случае катодных покрытий, например никель по стали, так как разрушение основного металла практически не происходит до тех пор, пока сохраняется цинковое покрытие. На поверхности цинка в атмосферных условиях влажный воздух, содержащий углекислый газ, сернистые соединения и тому подобные вещества, обусловливает образование светло-серых продуктов коррозии в виде тонкого слоя гидроокиси цинка Zn(OH)2, карбонатов цинка ZnCO3 · Zn(ОН)2.
В промышленной и приморской атмосферах в состав продуктов коррозии входят также хлориды и сульфаты цинка. Скорость коррозии цинкового покрытия по мере накопления на поверхности продуктов коррозии уменьшается в результате частичного заполнения пор в покрытии. Таким образом, пленка из продуктов коррозии толщиной до 20 мкм служит своего рода дополнительной защитой.
Анодный характер цинка по отношению к стали обусловливает возможность защиты оголенных участков поверхности, отстоящих па расстоянии нескольких миллиметров от кромки покрытия. Забоины и царапины в покрытии не влияют существенно на коррозию изделий. Протекторное действие цинка обусловливает также защиту от коррозии непокрытой резьбы гаек, если они навинчены на оцинкованные болты, срезы листовых оцинкованных материалов, проволоки и т. п.
В некоторых случаях цинковое покрытие принимает катодный характер защиты по отношению к стали, например при воздействии горячей воды (температура выше 70° С), в результате происходит весьма интенсивная коррозия стали, а цинковое покрытие не разрушается.
Защитное действие цинкового покрытия резко ослабляется в атмосфере, содержащей продукты органического происхождения: синтетические смолы, олифу, хлорированные углеводороды и т. п. вещества. Цинковые покрытия разрушаются, если они находятся в контакте или в одном и том же закрытом объеме со свежеокрашенными и промасленными деталями. Для повышения химической устойчивости цинка при воздействии агрессивной атмосферы его поверхность подвергают специальной химической обработке в растворах, содержащих хромовую кислоту или ее соли, при этом в результате реакции образуются пленки хроматов цинка, значительно улучшающие коррозионную устойчивость покрытия. Устойчивость достигается также обработкой оцинкованных деталей в растворах, содержащих соли фосфорной кислоты. Эта операция называется фосфатированием.
Высокие защитные свойства цинковых покрытий, обусловленные анодным характером этого покрытия и низкой стоимостью цинка но сравнению с другими цветными металлами, обусловливают широкое распространение процесса цинкования в различных отраслях промышленности. Цинковые покрытия составляют более 60% всех видов металлических покрытий, применяемых в народном хозяйстве. Цинкованию подвергаются листы кровельного железа, трубы, каркасы, шасси радиоприемников, детали автомобилей приборов, станков, сельскохозяйственных машин, крепежные детали, проволока и другие изделия массового производства.
Толщина цинкового покрытия на деталях устанавливается в зависимости от условий эксплуатации изделий, а также условий сопряжения деталей при сборке. Выбор толщины покрытия производится в соответствии с ведомственными нормами, отраслевыми стандартами и другой нормативно-технической документацией.
Таблица 1. Толщина цинкового покрытия.
Характеристика ycлoвий экслуатации |
Толщина, мкм |
Обозначение по ГОСТ 9791-68 |
Легкие условия (ЛС). Отапливаемые и вентилируемые помещения. Относительная влажвость 65 ± 15 % при температуре 25° С. |
6 - 9 |
Ц 6 |
Средние условия (СС). Отсутствие атмосферных осадков, неотапливаемые помещения, атмосфера загрязнена небольшим количеством промышленных газов. Температура воздуха от -60 до + 60° С, относительная влажность 95 ± 3 % при температуре +30° С. |
15 - 18 |
Ц 15 хр |
Жесткие условии (ЖС). Эксплуатации на открытом воздухе. Воздействие атмосферных осадков, загрязненных промышленными газами. Относительная влажность 95 ± 3 % при температуре +35° С (тропические условия). |
24 - 30 |
Ц 24 хр |
Эксплуатация в особых условиях. Длительное пребывание в воде. Атмосфера насыщена промышленными газами. |
36 - 42 |
Ц 36 хр |
В табл. 1 даны рекомендации по выбору толщины цинкового покрытия в зависимости от условий эксплуатации и приведено обозначение цинкового покрытия на чертежах деталей. При выборе толщин покрытия для мелких резьбовых крепежных деталей необходимо учитывать условия свинчиваемой, поэтому толщина слоя цинка на резьбовых деталях с шагом до 0,8 мм устанавливается 3 - 6 мкм для деталей с шагом более 0,8 мм - 9 -18 мкм.
Необходимо также принимать во внимание, что если деталь находится внутри прибора и защищена кожухом от попадания влаги, а при работе прибора выделяется теплота, то условия эксплуатации детали являются менее жесткими, чем условия эксплуатации изделия.
Цинковые покрытия бывают от серого до светло - серого цвета. При длительном хранении оцинкованных деталей допускается потускнение поверхности. Образование осыпающегося белого налета на цинковом покрытии ухудшает его внешний вид, но не снижает защитных свойств.
Для цинковых покрытий, подвергнутых хроматированию, цвет - от золотисто - желтого до желтовато - зеленого с радужным оттенком. Коричневый цвет пленки не допускается. Отсутствие хроматной пленки в порах и раковинах литья, в швах сварки и около них, вблизи щелевых зазоров и малых отверстий допускается. Нарушение хроматной пленки в виде отдельных рисок и точек тоже допускается. Цинковое фосфатированное покрытие имеет цвет от светло-серого до темно-серого с явно выраженной кристаллической структурой фосфатной пленки. Основные физические свойства цинка представлены ниже:
Плотность, г/см3 - 7,1Температура плавления, °C - 420Твердость электролитического цинка, кгс/мм2 - 50 - 60Электрическое сопротивление, Ом*см - 5,75*10-8
Возможно Вас так же заинтересуют следующие статьи: comments powered by HyperCommentsecm-zink.ru
Цинковое покрытие - Большая Энциклопедия Нефти и Газа, статья, страница 1
Цинковое покрытие
Cтраница 1
Цинковые покрытия обладают высокой коррозионной стойкостью в большинстве нейтральных сред, в особенности в пассивированном виде. Цинковые покрытия без нанесения герметизирующего состава не следует применять в коррозионно-агрессивных условиях ( морская и промышленная среда), в невентилируемых помещениях и вблизи электронного оборудования, при работе которого выделяются фенольные пары, испускаемые изоляционными материалами, лаками и капсулирующими составами. [1]
Цинковое покрытие, обработанное этим раствором, приобретает зеленовато-желтую окраску с радужным оттенком. [2]
Цинковое покрытие хорошо защищает стальные изделия от коррозионного воздействия бензина и серосодержащих жидкостей. При этом цинковое покрытие эффективнее, чем кадмиевое или свинцовое. [3]
Цинковое покрытие может быть выполнено путем очистки металла кислотой ( травлением) с последующим погружением его в расплавленный цинк; цинк может быть также нанесен на металл гальваническим способом или способом шерардизации, при котором нагретый металл помещается в барабан, содержащий цинковую пыль. Преимущество этого способа перед другими заключается в том, что после шерардизации резьба на трубе остается пригодной для использования, чего обычно не бывает после оцинковки другими способами. [4]
Цинковое покрытие, полученное методом электрометаллизации, было всесторонне исследовано в лабораторных условиях и проверено на большом числе технических средств в процессе эксплуатации с различными нефтепродуктами ( автомобильными и авиационными бензинами, топливом для реактивных двигателей, дизельным топливом, маслом и смазкой) в течение более 20 лет. [5]
Цинковое покрытие теряет свои защитные свойства, если оно становится катодом по отношению к железу в резервуарах горячей воды. При определенных условиях цинк может подвергнуться быстрому агрессивному воздействию, что приводит к оголению поверхности железа. Основной причиной быстрой коррозии цинка является присутствие в воде небольших количеств ( 0 1 мг / л) меди. Последняя осаждается на поверхности цинка и образуются локальные гальванические пары, которые ускоряют питтинговую коррозию и перфорацию поверхности. Ньюеллом [119] проведены испытания на коррозию шести оцинкованных резервуаров в продолжение приблизительно двух лет. [6]
Цинковые покрытия, полученные электролитическим путем, отличаются также достаточно высокой стойкостью против коррозии в условиях тропического климата. [7]
Цинковые покрытия часто подвергаются фосфатированию в растворе следующего состава ( в г. л): 20 - 35 окиси цинка; 20 - 30 фосфорной кислоты; 1 5 - 2 натрия азотистокислого; температура раствора 28 - 30 С; продолжительность обработки 25 - 30 мин. Изделия после фосфатирования пассивируются в растворе бихромата натрия ( 50 - 80 г / л) при температуре 50 - 80 С в течение 2 - 3 сек. [8]
Цинковое покрытие применяют для защиты деталей от коррозии, оно обладает высокими защитными свойствами в атмосферных условиях. Покрытие обладает средней твердостью, выдерживает изгибы и развальцовку, хорошо сохраняется при свинчивании. Оно непригодно для деталей, работающих на трение, плохо выдерживает запрессовку, плохо подвергается пайке и сварке и не применяется для деталей, подвергающихся термообработке. Цинковые покрытия на воздухе покрываются характерным белым налетом окиси цинка, не ухудшающим, однако, свойств покрытия. [9]
Цинковое покрытие при температуре выше 250 С становится хрупким. Его не следует применять для стальных деталей толщиной менее 0 5 мм, так как они становятся хрупкими. [10]
Цинковое покрытие способно растворяться в кислых и щелочных средах. Поверхность оцинкованных деталей может быть матовой или блестящей. [11]
Цинковые покрытия относятся к анодному типу: растворяясь, защищают сталь электрохимически, поэтому оценка защитных свойств производилась по изменению потенциала стали под покрытием в зависимости от времени выдержки в модельной среде. [12]
Цинковое покрытие на изделиях из алюминия и его сплавов наносится в целях защиты их от коррозии, причем цинк обеспечивает электрохимическую защиту алюминиевым сплавам, а в известных условиях и алюминию. Цинковые покрытия наносятся в специальных целях, например для предохранения резьбы от заедания и иногда для последующей пайки. При последующей пайке толщина цинкового слоя должна быть не менее 9 - 10 мк. [13]
Цинковое покрытие может применяться в качестве подслоя при нанесении других покрытий. В этом случае производится предварительное меднение цинкового подслоя в медном цианистом электролите обычного состава при плотности тока 0 3 а / дм2 и температуре 18 - 20 С. Для качественного отложения меди при последующем покрытии в кислом электролите решающую роль играет толщина цинкового подслоя, полученного в электролитах для блестящего цианистого цинкования, плотность тока при цинковании и температура электролита. При несоблюдении определенных условий на медном осадке через некоторое время электролиза обнаруживаются вздутия и пузыри. Оптимальной толщиной слоя цинка является толщина около 2 мк. Цинкование следует производить при плотности тока 1 5 а / дм2, так как при больших плотностях тока наступает вздутие покрытия. [14]
Цинковые покрытия защищают стальные изделия от коррозии электрохимически. [15]
Страницы: 1 2 3 4
www.ngpedia.ru
Цинковые покрытия - сравнение методов цинкования и их характеристики

Глубокий анализ-сравнение различных методов нанесения цинковых покрытий!
Как уже говорилось, горячее цинковое покрытие представляет из себя систему железо-цинковых сплавов с различным отношением содержания железа и цинка с постепенно уменьшающимся содержанием железа по мере приближения к внешней стороне покрытия.
Все железо-цинковые сплавы прочнее, чем сталь основы, что придает покрытию высокую устойчивость к истиранию. Наоборот, внешний ή-слой мягче, чем сталь, что создает хорошие условия для устойчивости к удару.
Таким образом, совокупность этих слоев создает устойчивость к разрушению при перевозках, монтаже и при обслуживании.
Цинковое покрытие, нанесенное электрохимическим способом, по механическим свойствам подобно обычному цинку, то есть является относительно мягким. Кроме того, электрохимическое цинкование осуществляется при обычной температуре, поэтому, кроме очень узкой переходной области, в системе не наблюдается железо-цинковых сплавов, и адгезия цинкового слоя к металлу основы относительно невелика. Сам процесс нанесения покрытия представляет определенные сложности с точки зрения равномерности нанесения покрытия, поскольку ток стремится избегать полостей. Приходится изощряться при пространственном расположении анодов. Метод является достаточно дорогостоящим, и поэтому ограничиваются нанесением покрытия на мелкие, в том числе резьбовые детали. Он не может конкурировать с методом горячего цинкования при защите цинком крупных, средних и даже большинства относительно мелких деталей.
Рис. 2. 11. Часть ассортимента деталей, которые могут быть механически оцинкованы.
Наоборот, метод шерардизации в модификации “Дистек” постепенно начинает отвоевывать пространство как у электрохимического, так и горячего цинкования. Достаточная толщина покрытия (до 60-120 мкм), его равномерность и плотность с последующей защитой методом фосфатирования позволяет изделиям выдерживать в солевом тумане (одним из основных методов определения коррозионной устойчивости изделий) до 1500 часов, что является очень хорошим показателем. Поскольку нанесение покрытия производится при 380-400°С на поверхности изделия, образующиеся железо- цинковые слои на данных изделиях получаются более твердыми, чем в случае электрохимического нанесения покрытий. Поступают сообщения о создании новых установок, позволяющих обрабатывать все более крупные изделия.
Сравнение свойств различных видов цинковых покрытий очень наглядно видно из таблицы № 2.12.
Поскольку, как видно из таблицы, все виды цинковых покрытий имеют как свои преимущества, так и недостатки, очевидно, что каждый тип покрытия имеет свою нишу применения. Встает вопрос, насколько долговечны покрытия различного типа, и имеется ли в этом вопросе преимущество одного типа покрытия перед другим. Ответ на этот вопрос дает рис. № 2.12, где приведены времена жизни покрытий, нанесенных различными способами и различной толщины. Из рисунка видно, что практически все точки для покрытий, полученных самыми разнообразными способами (горячее цинкование, электрохимическое, шерардизация, окрашивание в координатах “длительность службы” - “толщина покрытия” с очень малым разбросом укладываются на единую кривую, что говорит об отсутствии связи времени службы изделия с типом нанесения покрытия, основной фактор - это толщина покрытия. Однако надо иметь в виду, что красочное покрытие ограничено в сроке службы из-за подверженности его истиранию.
Рис. 2.12. Зависимость времени жизни покрытия от его толщины при разных способах нанесения.
Таблица № 12.2. Сравнение различных методов нанесения цинковых покрытий на функциональные свойства изделий (механическое цинкование в таблице не рассматривается, но по характеристикам оно ближе всего к методу шерардизации).
Характеристика покрытия |
Горячее цинкование |
Электрохимическое нанесение |
Шерардизация (механич. цинкование) |
Напыление цинка |
Окраска цинк-содержащими красками |
Адгезия |
Покрытие, сросшееся со сталью, из-за наличия различных железосодержащих слоев |
Хорошая, сравнимая с таковой для покрытий из других металлов |
Хорошая, сравнимая с таковой для электрохимического покрытия |
Хорошая механическая подготовка под окраску при условии, что дробеструйная подготовка проведена нормально |
При хорошей дробеструйной обработке дает наилучшие результаты |
Непрерывность и однородность |
Хорошие - любая непроцинковка хорошо видна в виде “черных пятен”. Некоторый избыток цинка на точках слива |
Однородная в пределах возможности ванны. Поры не представляют проблемы, поскольку сталь защищается прилегающим цинком |
Покрытие тонкое на углах - в противоположность горячему цинкованию |
Зависит от опытности оператора. Покрытие пористое, но поры вскоре заполняются продуктами коррозии цинка |
Хорошая - любые поры заполняются продуктами реакции |
Толщина |
Обычно 50-125 мкм на трубах и другой продукции; более толстые покрытия до 250 мкм получаются на сталях, раскисленных кремнием или после дробеструйной очистки перед цинкованием. Покрытия толщиной 10-30 мкм применяются на проволоке и листе. |
Толщина в пределах 3-15 мкм. Более толстые слои возможны, но невыгодны экономически |
Изменяются по желанию, обычно в пределах 10-80 мкм |
Толщина изменяется в интервале 100-150 мкм, но покрытия до 500 мкм могут использоваться |
До 40 мкм краски (или более в специальных случаях) при окраске в один слой |
Формуемость и механические свойства |
Обычные покрытия, на конечных изделиях не пригодны к изменению формы; слой сплава устойчив к абразивному воздействию, но хрупкий при гибке. Специальные покрытия с тонким слоем сплава или при его отсутствии хорошо формуются (на листах) и устойчивы к сварке |
Сталь с электрохимическим покрытием обладает превосходной формуемостью и может быть сварена точечной сваркой. Небольшие детали обычно подвергаются такой обработке перед окраской |
Хорошие. Не наблюдается охрупчивания высокопрочных сталей |
При применении конечной продукции формовка не нужна. Можно осуществлять сварку через тонкое покрытие, если это необходимо, но обычно экранируют края, которые необходимо сварить, и после сварки эти места покрывают слоем цинка |
Сопротивление к истиранию лучше, чем у обычных красок. Окрашенные листы могут быть подвергнуты формовке и сварке с небольшими нарушениями покрытия |
Последующая обработка |
Конверсионные покрытия - хроматы предотвращают белую ржавчину; фосфатирование на новых листах является хорошей основой для последующей окраски |
Конверсионные покрытия (например, хроматы) для предотвращения белой ржавчины. Часто используются как основа для последующего окрашивания |
Могут быть применены конверсионные покрытия |
Возможно нанесение защитных покрытий, которые становятся основой для окрашивания, давая более долгую жизнь изделиям |
Может быть использова на отдельно или в качестве грунтовки под обычные красочные покрытия |
Другие свойства |
Доступны ванны различных размеров. Части изделий до 25 метров могут быть оцинкованы в некоторых случаях. Требуется внимательное отношение к дизайну изделия.Имеются непрерывные процессы цинкования листов и проволоки |
Любые размеры ванн доступны. Процесс обычно используется для простых, в основном, малых изделий, пригодных для цинкованиях в барабанах или при непрерывном цинковании листов и проволоки. Никакого нагревания, за исключением случая уменьшения водородной хрупкости для высокопрочных сталей |
Идеально для малых изделий, включая шайбы и пружины (примерно до 15 см или 250 г). Трудности при нанесении, например, внутри полых изделий |
Нет ограничений на размер или форму, очень экономичен для изделий с высоким отношением массы к поверхности. Неэкономичен при окрашивании сетчатых изделий. Наличие дополнительных трудностей (например, внутри труб) могут ограничить применение. Наилучший метод для нанесения очень толстых покрытий. Малое нагревание стали |
Пригоден для всего, что может быть окрашено, хотя могут быть трудности при окрашивании трубчатых структур. Не требуется никакого нагревания |
ecm-zink.ru
Применение - цинковое покрытие - Большая Энциклопедия Нефти и Газа, статья, страница 1
Применение - цинковое покрытие
Cтраница 1
Применение цинковых покрытий нерационально, если рН среды заметно меньше 7 или более 12 из-за усиления коррозии цинка. [2]
Области применения цинковых покрытий обширны. Ими пользуются для защиты резервуаров от действия бензина керосина, воды и других агрессивных жидкостей, для защиты труб, арматуры, крепежных деталей. С помощью цинковых покрытий предотвращают контакты между сталью, медью и другими металлами, способными образовывать гальванические пары, приводящие к разрушению металла. Цинк применяют в качестве покрытия не только для стали, но и для меди, латуни, алюминия. При повышенных температурах защитные свойства цинка в воде резко ухудшаются. [3]
Для ниобия удовлетворительные результаты были получены при применении цинкового покрытия, которое успешно защищает ниобий до температур порядка 950 С. [4]
В условиях высокой влажности воздуха при значительных колебаниях температуры с обильным выпадением росы ( в тропических широтах) скорость коррозии сильно возрастает, и применение цинковых покрытий нецелесообразно. Морская вода также быстро разрушает цинковое покрытие. [5]
С целью уменьшения коррозии стальные пластины меднятся. Применение цинкового покрытия недопустимо, так как под действием дуги цинк быстро сгорает, давая большое количество паров, резко ухудшающих условия гашения дуги. Деленное гашение с решеткой из стальных пластин может осуществляться без магнитного ДУТЬЯ: в этом случае нижний край пластин опускается до уровня контактов. [6]
Было показано, что покрытие другими металлами, например цинком или никелем, служит в качестве удовлетворительного метода устранения высокотемпературного солевого коррозионного растрескивания. Применение цинковых покрытий может вызывать сомнения, поскольку цинк в твердом и жидком состояниях способствует охрупчиванию основного металла. [7]
Защитные свойства цинковых покрытий в морской воде достаточно высоки, и оцинкованную сталь широко используют для защиты от коррозии стальных сооружений, морских нефтепроводов. Эффективно применение цинковых покрытий для защиты от коррозии стальных опор нефтепромысловых сооружений. По данным литературных источников, диффузионное цинкование позволяет повысить коррозионную стойкость стальных опор в зоне переменного смачивания ( 0 5 м над водой), где стойкость незащищенной стали наименьшая; при этом скорость коррозии составляет для оцинкованной стали 5 - 10 мкм / год, для незащищенной 300 мкм / год. [8]
Цинк является активным металлом и почти всегда обладает протекторным действием, поэтому эффективность цинковых покрытий прямо пропорциональна их толщине. Область применения цинковых покрытий определяется химическими свойствами цинка, который как амфотерный металл легко растворяется в кислых и щелочных средах. Цинковые покрытия на стали широко применяются при защите конструкций, подвергаемых воздействию атмосферной коррозии. [9]
Из металлов подгруппы цинка ( Zn, Cd, Hg) наиболее широко в гальванотехнике используют цинк, в меньшей степени - кадмий. Область применения кадмиевых и цинковых покрытий в значительной степени определяется защитными и физико-механическими свойствами цинка и кадмия. Основной областью использования цинковых и кадмиевых покрытий является защита стальных деталей от коррозии. Несмотря на относительно высокий нормальный потенциал - 0 76 В, металлический цинк является довольно коррозионностойким в атмосферных условиях. Так как потенциал цинка имеет более отрицательное значение, чем потенциал железа, то при контакте цинка с железом и наличии влаги образуется гальванический элемент, в котором железо служит катодом. Таким образом, покрытие цинком защищает сталь не только механически, но и электрохимически. [11]
Весьма перспективно применение цинкового покрытия по стали, ввиду более отрицательного потенциала цинка. Но для продолжительной защиты ( исходя из скорости коррозии цинка) необходимы достаточно толстые покрытия. [13]
Более сложно осуществлять сварку плавлением алюминия и его сплавов со сталью без биметалла. Непосредственная сварка алюминия со сталью, как правило, не дает положительных результатов. Шов получается хрупким вследствие образования интерметаллидов и большого различия физико-химических свойств соединяемых металлов. Удовлетворительное соединение алюминия со сталью возможно с применением цинкового покрытия. Наличие цинка на поверхности стали улучшает растекание алюминиевой присадки. Слой цинка толщиной до 30 мм предварительно наносят на сталь гальванически или горячим погружением. [14]
В водных средах Cd в отличие от Zn хорошо противостоит воздействию сильных щелочей. Подобно цинку он корродирует в разбавленных кислотах и водных растворах аммиака. Соли кадмия токсичны, и поэтому его покрытия нельзя использовать при хранении пищевых продуктов. В этом отношении цинковые соли - менее токсичны, вследствие чего допускается применение цинковых покрытий для сосудов с холодной питьевой водой, однако контактирование этих покрытий с продуктами питания также не рекомендуется. [15]
Страницы: 1 2
www.ngpedia.ru
Термодиффузионное цинковое покрытие - это... Что такое Термодиффузионное цинковое покрытие?
Покрытия термодиффузионные цинковые (ТДЦ)
Определения
Впервые этот метод был применен в Англии в начале ХХ века и получил название «шерардизация» (по фамилии изобретателя — Шерард (Sherard Cowper-Coles)). Термодиффузионное цинковое покрытие является анодным по отношению к черным металлам и электрохимически защищает сталь. Оно обладает прочным сцеплением (адгезией) с основным металлом за счет взаимной диффузии железа и цинка в поверхностных интерметаллидных фазах Zn-Fe, поэтому покрытие мало подвержено отслаиванию или скалыванию при ударах, механических нагрузках и деформациях обработанных изделий. Преимущество термодиффузионной технологии покрытий по сравнению с гальваническими состоит не только в ее превосходстве по коррозионной стойкости, но и в том, что она не вызывает водородного охрупчивания металла. Термодиффузионное цинковое покрытие в точности повторяет контуры изделий, оно однородно по толщине на всей поверхности, включая изделия сложной формы и резьбовые соединения. Суть технологии термодиффузионного цинкового покрытия состоит в том, что антикоррозионное покрытие формируется в результате насыщения цинком поверхности металлических изделий в порошковой среде при температуре 290-450 °C, причем выбор температурного режима зависит от типа стальных изделий, марки стали и требований производителей деталей. Такая технология позволяет получить любую толщину покрытия в диапазоне от 6 до 100 микрон по требования заказчика без изменения технологического процесса. Процесс происходит в закрытом контейнере с добавлением к обрабатываемым деталям специальной насыщающей смеси. Пассивация (финишная обработка деталей) является обязательной частью процесса термодиффузионного цинкования. Пассивация предназначена для предотвращения образования белых продуктов коррозии на поверхностях, подвергаемым воздействию атмосфер с высокой влажностью, соленой воды, морских атмосфер или циклам конденсации и высыхания.
Защита металлов от коррозии
Защита металлов от коррозии обеспечивает долговременное функционирование различных деталей, конструкций и сооружений. Около 10% выпускаемых годового выпуска стали и стальных изделий ежегодно теряют свои технические характеристики из-за коррозии, что оценивается десятками миллиардов долларов. Один из наиболее распространенных способов защиты металлов от коррозии — покрытие цинком. Выбор цинка не случаен и объясняется высоким отрицательным значением окислительно-восстановительного потенциала пары Zn2+/Zn. Этот металл защищает основной металл (железо) анодно, то есть в гальванической паре «Fe-Zn» растворяется цинк. Электрохимической альтернативой цинку является кадмий, но его применение во многих странах запрещено из-за высокой токсичности. В РФ кадмирование имеет ограниченное использование и возможно, как правило, только по специальному разрешению. Толщина защитного цинкового покрытия выбирается в зависимости от назначения изделия и условий его эксплуатации. Анализ условий применения различных металлоизделий показывает, что защитное (антикоррозионное) покрытие для этих условий должно обладать не только повышенной коррозионной стойкостью, но быть также устойчивым к абразивному износу и иметь высокую степень сцепления с поверхностью защищаемого изделия.
Методы антикоррозионной защиты
Гальванические (электролитические) покрытия. Покрытия на поверхность изделий наносят в растворах электролитов под действием электрического тока. Основными компонентами этих электролитов являются соли цинка. Гальванический способ защиты металлоизделий имеет низкую коррозионную стойкость (около 140 часов в камере нейтрального соляного тумана), не позволяет нанести покрытие на изделия сложной конфигурации, при подготовке поверхности к оцинкованию на высокопрочных изделиях вызывает водородное охрупчивание, не позволяет производить демонтаж металлоизделий, имеет низкую степень сцепления с поверхностью. Данный вид защиты несет, скорее, декоративную функцию.
Металлизационные покрытия. Покрытия наносят путем распыления струей воздуха или горячего газа расплавленного цинка. В зависимости от способа напыления используют цинковую проволоку (пруток) или порошок цинка. В промышленности используют газопламенное напыление и электродуговую металлизацию.
Цинконаполненные покрытия. Эти покрытия представляют собой композиции, состоящие из связующего и цинкового порошка. В качестве связующих используют различные синтетические смолы (эпоксидные, фенольные, полиуретановые и др.), лаки, краски, полимеры. Проявляют скорее свойства лакокрасочных, чем металлических покрытий.
Горячее цинкование. Как правило, горячее цинковние применяют для защиты от коррозии крупных металлоконструкций. Оцинкование мелких деталей и деталей с резьбой не дает необходимого качества оцинкованной поверхности. После обезжиривания, промывки, травления и повторной промывки, детали в барабане окунают в ванну (обычно керамическую) с расплавленным цинком. Вращением барабана обеспечивают поток цинковой массы относительно деталей для заполнения всех пор и микротрещин. Затем барабан вынимают из ванны и раскручивают для удаления излишков цинка центрифугированием. На деталях образуются наплывы, на внутренних резьбах остаются излишки цинка, резьбу приходится протачивать, снимая таким образом защитный цинковый слой, что в дальнейшем вызывает коррозию. Данный способ неприменим для мелких деталей, например для метрических крепежных изделий. Не применим для деталей из высокопрочной и легированной стали.
Термодиффузионные цинковые покрытия позволяют защищать от коррозии детали из любых марок стали, в том числе высокопрочных, и чугуна без изменения свойств основного металла, детали сложной конфигурации с отверстиями, детали в сборе, сварные и резьбовые. Ограничение размера деталей размером контейнера.
Комбинированные покрытия представляют собой комбинацию цинкового покрытия, лакокрасочного или полимерного. В мировой практике такие покрытия известны как «дуплекс-системы». В таких покрытиях сочетается электрохимический защитный эффект цинкового покрытия с гидроизолирующим защитным эффектом лакокрасочного или полимерного. Следует отметить, что гальванические и металлизационные цинковые покрытия не содержат интерметаллидных соединений (фаз) и состоят из цинка соответствующего химического состава. Горячецинковые покрытия, получаемые методом горячего цинкования (из расплава цинка) и диффузионные покрытия, наносимые из порошковых смесей на основе цинка, имеют аналогичный механизм образования — диффузионный. Однако диффузия цинка в металл различна: с применением горячецинкового покрытия диффузия составляет 0,1÷3%, термодиффузионного цинкования — 50÷70%. В соответствии с диаграммой состояния системы Fe—Zn в структуре этих покрытий присутствует ряд аналогичных фаз (интерметаллических соединений). Однако общее строение этих покрытий все-таки различно, также как их свойства.
Процесс нанесения термодиффузионного цинкового покрытия (ТДЦ)
Процесс нанесения покрытия представляет собой замкнутый технологический цикл, разбитый на несколько операций:
1-й этап: предварительная механическая очистка с помощью дробеметной установки; 2-ой этап: загрузка очищенных деталей в контейнер; добавление насыщающей смеси; 3-й этап: проведение термодиффузионного процесса, обеспечивающего нанесение на покрываемую поверхность деталей цинкового слоя; 4-й этап: разгрузка деталей из контейнера с одновременной очисткой их от остатков насыщающей смеси и пассивирование. 5-й этап: остывание готовой продукции. Детали, предназначенные для нанесения следующих видов покрытий (краски, склейки, пластифицирование и др.), как правило, пассивируются 1 раз. Во всех других случаях проводятся две пассивационные операции, с промежуточной промывкой деталей. Для получения качественного антикоррозионного покрытия все технологические этапы имеют одинаково важное значение и являются равными составляющими технологического процесса. Следует отметить, что технология нанесения покрытия не делает исключения ни для одного вида деталей, которые по своим размерам, весу и конфигурации входят в технологический контейнер оборудования, принятого на вооружение в данный момент. Оборудование, предназначенное для обработки деталей другого размера, выполняется на заказ. Соответственно на этапе выработки технического задания определяется габаритный размер контейнера и печей, а также мощность остальных агрегатов в линии, пропускная способность дробемета, пассивационных установок и сушки. Этап подготовки поверхности включает в себя ультразвуковую, дробемётную или пескоструйную очистку деталей, которая особенно важна для металлоизделий, имеющих на себе окалину после термической обработки во время производства.
Технические преимущества
Первое — это способность технологического процесса получить любую толщину покрытия по требованию заказчика. Второе — отсутствие склеивания деталей. Это один из самых негативных моментов, имеющих место в горячем цинке и в гальванике. Третье преимущество касается внешней и внутренней формы деталей. Российский рынок показал, что большинство крепежных и любых других вспомогательных деталей раньше красилось, пластифицировалось или просто оставалось без покрытия, так как они имели резьбовые соединения, полые и глухие отверстия, сложные соединения, сварные швы. Плюсом также является отсутствие каких-либо наплывов цинка в местах углублений или соединений. Четвертое преимущество относится к возможности последующей обработки деталей разными видами красок, пластификаторов и т. п. Практически все виды промышленных красок хорошо прилегают к термодиффузионному покрытию. Высокая адгезия увеличивает коррозионную стойкость, практически исключается вздутие и отслоение красок с поверхности. Срок службы деталей с двойным покрытием увеличивается, что приводит к значительной экономии при их эксплуатации. Пятое преимущество состоит в экологической чистоте процесса (если нет необходимости в обезжиривании изделия).
Нормы и стандарты
В декабре 2003 года Департаментом электрификации и электроснабжения ОАО «Российские железные дороги» была выпущена инструкция по применению термодиффузионного цинкования деталей и конструкций контактной сети. Данная инструкция распространяется на защитные цинковые покрытия, наносимые методом термодиффузионного цинкования на резьбовые детали, арматуру, конструкции контактной сети и другие изделия из углеродистой и низкоуглеродистой стали, в том числе повышенной прочности, на чугунные и детали из цветных металлов контактной сети, включая чугунные оконцеватели фарфоровых изоляторов. C января 2008 года вышли ГОСТы на высокопрочный крепеж для металлических конструкций, в которых есть указание на применение термодиффузионного покрытия для защиты от коррозии высокопрочных болтов, гаек и шайб.
См. также
Ссылки
1. ГОСТ 9.316-2006 Единая система защиты от коррозии и старения. Покрытия термодиффузионные цинковые. Общие требования и методы контроля. 2. ГОСТ 52643-2006 Болты и гайки высокопрочные и шайбы для металлических конструкций. Общие технические условия. 3. ЗАЩИТНЫЕ ЦИНКОВЫЕ ПОКРЫТИЯ: СОПОСТАВИТЕЛЬНЫЙ АНАЛИЗ СВОЙСТВ, РАЦИОНАЛЬНЫЕ ОБЛАСТИ ПРИМЕНЕНИЯ. Е. Проскуркин ГП «НИТИ», Украина журнал «Национальная металлургия» сентябрь, октябрь 2005 г. http://www.nmet.ru/a/2005/10/03/153.html
dic.academic.ru
Защитное действие цинкового покрытия — Цинковый портал
Защитное действие цинкового покрытия ярко проявляется в результате механического или химического негативного влияния. В нейтральной среде и при отсутствии нарушений поверхностной целостности защитное действие цинкового покрытия подобно другим антикоррозионным защитам.
Защитное действие цинкового покрытия. Специфика механизма защиты
Защитное действие цинкового покрытия по отношению к матричной основе в результате негативного влияния происходит электрохимическим путем. В гальванической паре железо-цинк стальная основа является катодом, а цинковое покрытие – анодом, поэтому поверхностный слой, разрушаясь, защищает матричную основу. Способ функциональной защиты объясняется значением электрохимического потенциала металла по отношению к железу. Чем выше отрицательные показатели потенциала металла, тем эффективнее защита. При положительном потенциале защитного металла по отношению к матричной основе происходит разрушение поверхностного слоя изделия.
Самозащита цинкового покрытия
Преимуществом цинкового покрытия при негативном воздействии является возможность сохранить защитные функции за счет образования поверхностной пленки из продуктов коррозии. При кислородной деполяризации ионы цинка от анодных участков и ионы гидроокисла (〖ОН〗^-) от катодных участков, диффундируя в растворе, могут продвигаться навстречу друг другу. Ионы цинка, попадая в катодную область с повышенным значением рН (за счет более высокой концентрации ионов (〖ОН〗^-)), образуют нерастворимые соединения 〖Zn(OH)〗_2, которые в конечном итоге выпадают в осадок. При рН ˃ 5,2 происходит реакция:
На металлической поверхности цинка действуют адсорбционные силы, которые в состоянии прочно удерживать образующиеся молекулы 〖Zn(OH)〗_2. В результате получается плотный, хорошо удерживаемый на поверхности металла осадок, обладающий защитными свойствами.
Защитные пленки, затрудняя доступ электролита к металлу и диффузию ионов металла в раствор, сильно изменяют течение коррозионного процесса. Изменение состава продуктов коррозионного разрушения связано и с изменением их защитных свойств.

В атмосферных условиях, при отсутствии загрязнений воздуха, на цинке могут образоваться продукты коррозии, состоящие из окиси цинка ZnO, гидрата окиси цинка 〖Zn(OH)〗_2 и карбоната ZnCO_3. В сухом воздухе на цинке образуется окись цинка ZnO. Удельный объем окиси цинка в 1,44 раза больше удельного объема металла, из которого она образовалась, что способствует формированию очень плотной поверхностной пленки.

Из таблицы видно, что в углекислых растворах цинк перестает растворяться вследствие образования на нем защитной пленки из углекислого цинка.
Наибольшее защитное действие в условиях атмосферной коррозии будут оказывать пленки, наименее растворимые под воздействием атмосферных осадков.
Из таблицы следует, что окись цинка и гидрат окиси обладают малой растворимостью.
Факторы, определяющие скорость коррозии цинкового покрытия
Цинк и цинковые соединения обладают амфотерными характеристиками (в зависимости от внешних условий воздействия у него проявляются как кислые, так и основные свойства), поэтому коррозия цинка зависит от показателя кислотности. В кислых средах, где показатель кислотности ниже 6, коррозия цинка протекает беспрепятственно (отрезок l на графике), такой же процесс разрушения наблюдется в щелочной среде, где рН больше 12,5 (отрезок lll).
Коррозионная стойкость цинка в сухой атмосфере обеспечивается за счет образования на поверхности защитной пленки (оксида цинка). В случае увеличения негативного атмосферного влияния (воздействия влаги, диоксида углерода, примесей) на цинковую поверхность происходят реакции с образованием гидроксида цинка Zn(ОН)2, затем формируется защитное покрытие, состоящее из карбонатных соединений (ZnCO3·3Zn(ОН)2·Н2O). Пленки имеют плотную структуру, труднорастворимы, обладают хорошим сцеплением с цинковой основой. Образование защитных пленок происходит в диапазоне кислотности от 6 до 12,5 (отрезок ll на рисунке).
Скорость коррозии цинка зависит от
• природы внешних факторов воздействия, • чистоты цинкового образца (наличие примесей), • технологических параметров изначальной обработки цинка.
Удовлетворительная стойкость коррозионному разрушению цинковых покрытий получается только в растворах, близких к нейтральным. В кислых (рН ˂ 7) и щелочных (рН ˃ 12,5) средах цинковое покрытие быстро разрушается.
Зависимость обратимого электродного потенциала цинка от рН раствора приведена ниже.
На скорость коррозионного разрушения цинка различные химические элементы оказывают специфическое влияние. Ускоряют растворение цинка в 0,5-н. растворе соляной кислоты:
• медь, • железо, • сурьма.
Влияние кадмия, мышьяка и олова на коррозионное разрушение поверхности цинка носит более слабый характер. Алюминий вначале воздействия слабо повышает скорость коррозии, затем — замедляет. Свинец, ртуть – препятствуют процессу коррозионного разрушения.
В 0,5-н. растворе серной кислоты:
• медь, железо ускоряют скорость коррозии цинка; • кадмий и свинец – замедляют.В 18%-ном растворе серной кислоты наиболее ускоряющее действие оказывает
• железо, • никель, • сурьма;
более слабое:
• мышьяк, • висмут, • алюминий, • серебро, • медь,
замедляющий эффект:
• магний, • кадмий, • ртуть, • свинец.
Наибольшее повышение скорости коррозии происходит при введении в цинк различных примесей (для железа до 0,1%).
Защитное действие цинкового покрытия определяется двумя факторами:
1) возможностью защищать стальную основу от коррозионного разрушения электрохимическим путем (гальваническим), 2) возможностью самозащиты собственной поверхности при негативном воздействии путем образования труднорастворимых цинковых соединений.
www.zinkportal.ru
Что дает металлам цинковое покрытие? Как цинк защищает от коррозии?
Мы часто слышим и видим в рекламе, что если уж защищать металлы от коррозии, то только с помощью цинка. Но, не все знают - почему именно цинк? Что же дает металлам цинковое покрытие – расскажем в этой статье.
Цинкование – самый эффективный метод защиты
Цинкование – это покрытие различных металлических поверхностей слоем цинка с целью защиты от коррозии. То, что именно цинкование является наиболее эффективным методом в борьбе с ржавчиной, выяснили давно, более 200 лет назад. При проведении исследований различных методов именно цинкование показывало самые долгосрочные результаты – более 50 лет металлы, покрытые слоем цинка, не ржавеют.
С тех пор специалисты в области антикоррозии применяют цинкование различными способами. Изначально это было горячее цинкование, затем гальваническое, диффузионное, газодинамическое. Но, в 80-х годах XX века произошел определенный прорыв в этой области, появился новый метод – холодное цинкование.
Холодное цинкование – наиболее удобный, экономичный и долговечный способ нанесения цинкового покрытия. Он заключается в покрытии подготовленной поверхности металла составом с очень высоким (96-98%) содержанием цинка, а так же различных добавок. Наносить состав для холодного цинкования можно с помощью обычной кисти или валика, прямо на месте эксплуатации конструкции, то есть ее не нужно никуда отвозить. Результатом такой защиты является отсутствие коррозии на протяжении 25-50 лет, причем металлы под защитой холодного цинкования коррозируют в 3 раза медленнее, чем защищенные другими способами, несмотря на тот же цинк в составе (по проведенным исследованиям Фулмеровского центра). В чем же секрет?
Как работает покрытие цинком?
Железо при взаимодействии с влагой и кислородом окисляется и образует на поверхности непрочную, рыхлую пленку, она постепенно и прекращается в ржавчину. Такая ненадежная защита продолжает пропускать влагу и кислород вглубь железа и разрушать его. Но, цинк, олово и алюминий при взаимодействии с влагой и кислородом образуют прочную пленку, не пропускающую разрушения дальше. Именно поэтому с помощью тонкого слоя этих металлов защищают другие металлы, более подверженные коррозии.
Цинк выделяется среди этой группы "прочных" металлов тем, что обеспечивает дальнейшую защиту от влаги и кислорода даже при повреждении покрытия, в то время как защита олова или алюминия при нарушении целостности слоя слабеет или даже начинает способствовать коррозии.
Цинк защищает металлы сразу двумя способами - барьерным (пассивным) и катодным (также называемым активным, протекторным или электрохимическим).
Катодная защита подразумевает, что цинк при нанесении на железо образует с ним гальваническую пару, в которой железо - менее активный металл, а цинк - более активный. При контакте с влагой и кислородом цинк-анод вступает в реакцию первым, жертвует свои электроны на борьбу с коррозией, а железо - катод принимает электроны, защищается и остается практически не тронутым ржавчиной. Защитный процесс продолжается до полного истощения слоя цинка.1 слоя в 40-60 мкм хватает на 10-25 лет.
Сразу 2 способа защиты, которые сменяют друг друга, очень пригождаются металлам с первого дня эксплуатации. Дело в том, что любое покрытие составом не герметично на 100%, а имеет дефекты и поры. Цинковое покрытие также может пропускать некоторое количество кислорода на начальном этапе использования. Именно тогда оно защищает металлы от ржавчины протекторным или электрохимическим способом. В процессе эксплуатации происходит уплотнение структуры покрытия, полное растворение цинковых соединений и вступает в силу барьерная защита, как при горячем цинковании. Если целостность покрытия будет нарушена (царапины, механические повреждения, разъедание химикатами), то за работу снова возьмется катодная защита.
Не просто цинк – или почему холодное цинкование защищает дольше?
На практике, цинковое покрытие – самое надежное и долговечное. Однако, одно цинковое покрытие, другому рознь. Вы можете приобрести краску с цинком, правильно ее нанести, но защита не прослужит десятки лет. Потому, что цинк, добавленный в краску, не будет работать таким способом. Такую длительную защиту (25-50 лет) дают только составы для холодного цинкования. Почему же холодное цинкование долговечнее других цинковых способов обработки?
Холодное цинкование обеспечивает те же защитные характеристики, как и другие методы, например, горячее цинкование. Но, в отличие от них гораздо проще наносится на месте эксплуатации конструкций, меньше стоит и дольше служит.
В составах для холодного цинкования содержится 96 и более % цинка, чистотой 99,995%. То есть почти на 100% без примесей! А чем выше концентрация цинка и его чистота – тем дольше прослужит покрытие. Именно это позволяет «холодному» покрытию коррозировать максимально медленно, по сравнению с другими методами оцинковки. Частицы цинка в составе защищены смолами – это еще повышает защитные характеристики покрытия. Кроме того, минимальный размер частиц (от 12-15 мкм, до 3-5 мкм в разных составах) и их овальная форма образуют прочное электрохимическое соединение с металлом. Благодаря этому, даже царапины и повреждения на поверхности покрытия не приводят к его отслаиванию, сохраняя отличную адгезию. Так могут только активные покрытия с катодной защитой. А просто покрытия, в которых добавлен цинк – так не могут.
Даже такой проверенный метод цинкования, как горячий, немного уступает холодному цинкованию. Потому, что при горячем цинковании используются составы с содержанием цинка 80-85% с чистотой до 98%. Смолы, защищающие цинк там отсутствуют, так как не выдержат нагрева до 400°С и все равно потеряют защитные свойства. К тому же, не каждую конструкцию можно разобрать, перевезти и поместить в горячую ванну с цинком.
Сколько прослужит цинковая защита, нанесенная холодным способом?
Сроки действия покрытий, нанесенных методом холодного цинкования, отличаются в зависимости от условий эксплуатации и толщины слоя, а так же от степени очистки поверхности металла. Загрязненная атмосфера, влияние различных химикатов, бензина, солей, щелочей и нефтепродуктов могут незначительно, но ускорить истощение покрытия. Срок действия покрытия, эксплуатируемого на открытом воздухе, всегда меньше, чем более бережное использование внутри помещений.
Сроки, гарантированные производителем для состава холодного цинкования Барьер-цинк:
Зависимость толщины слоя и срока службы покрытия Барьер-цинком:
- 40 мкм: 7-10 лет;
- 60 мкм: 10-20 лет;
- 80 мкм: 14-25 лет;
- 100 мкм: 18-25 лет;
- 120 мкм: более 20 лет.
Стоит отметить, что это сроки, которые гарантирует производитель. Реальные сроки службы покрытия в 1,5-2,5 раза превышают гарантийные. К тому же срок службы такого покрытия всегда можно продлить, в любой момент, добавив еще слой и сделав его толще.
ЕСЛИ У ВАС ЕСТЬ ВОПРОСЫ ПО ВЫБОРУ АНТИКОРРОЗИЙНОГО СОСТАВА ИЛИ КРАСКИ ВЫ МОЖЕТЕ ОБРАТИТЬСЯ ЗА ОТВЕТАМИ К НАШИМ МЕНЕДЖЕРАМ ПО ТЕЛЕФОНАМ:
в Санкт-Петербурге: +7(921)927-58-47, +7 (812) 603-41-53
в других городах: 8 (800) 707-53-17
или почте: [email protected]
terazinc.ru