Формовочные смеси для литья. Формовочная смесь для литья алюминия
Формовочные смеси для литья, стержневые смеси. Свойства, изготовление
Литейное производство достаточно простой и широко распространенный технологический процесс для получения отливок различного размера и разнообразной формы. Получение деталей методом литья практикуется в автомобилестроении, станкостроении, вагоностроении и многих прочих отраслях машиностроения. Для получения полых или с множеством отверстий отливок используются стержневые и формовочные смеси различных составов. Экономически обосновано использование песчано-глинистых форм при массовом производстве.

Формовочные смеси для литья
Состав смесей зависит от:
- способа формовки:
- ручная;
- машинная;
- типа металла:
- сталь;
- чугун;
- цветной металл и его сплавы;
- типа производства:
- единичное;
- серийное;
- массовое;
- типа литья;
- технологического оснащения.
Материалы, которые используются для получения формовочных смесей, подразделяются на следующие группы:
- песчаник;
- различные сорта глины;
- вспомогательные:
- связующие материалы;
- противопригарные смазки и покрытия;
- огнеупорные;
- специальные.
Глинистые пески могут содержать глины в своем составе до 50%. Делят их по количеству содержания глины на:
- тощие – до 10%;
- полужирные – до 20%;
- жирные – до 30%;
- очень жирные – до 50%.
Также используются кварцевые пески. Силикатная основа позволяет принимать в форму расплав, температура которого достигает 1700С.
Получение отливок высокого качества требует использования противопригарных покрытий и материалов мелкой фракции, чтобы предупредить образование в форме пор.
Виды и состав смесей
К формовочным смесям для литья предъявляются следующие требования:
- механическая прочность;
- теплопроводность;
- газовая проницаемость;
- огнестойкость;
- теплоемкость.
Формовочные и стержневые смеси обладают одинаковыми свойствами. Но к стержням предъявляются более высокие требования, потому что на него расплавленный металл оказывает более сильное давление.

Состав различных смесей
Формовочные смеси делятся на три типа:
- единые;
- облицовочные;
- наполнительные.
Единая смесь предназначается для наполнения всего объема литейной формы. В полном объеме используется при машинной формовке при выпуске отливок в большом количестве. Для ее приготовления используется большой объем еще неиспользовавшихся материалов.
Облицовочная смесь предназначена для получения слоя формы, контактирующего непосредственно с расплавом. Его толщина зависит от типа смеси и тяжести отливки и составляет 20-100 мм. Для того чтобы дополнить оставшийся объем используется наполнительная смесь.
Состав формовочной смеси напрямую зависит от формы и метода ее изготовления. Формирование песчано-глинистых форм происходит двумя способами, в результате которых получаются сухие и сырые формы. Для их податливости при формировании в смесь вводятся сгорающие наполнители – торф или древесные опилки. В состав подсушиваемых форм кроме глины и песка закладываются крепитель, измельченный асбест и барда.
Кроме них используются:
- быстро отверждающиеся;
- самостоятельно отверждающиеся;
- твердеющие при химическом преобразовании;
- жидкостекольные составы.
В быстро отверждающихся смесях связкой выступает жидкое стекло. Если для сушки жидкого стекла необходима теплая продувка, то в данном случае отвердение происходит за счет феррохромового шлака.

Классификация формовочных смесей
Самостоятельно отверждающиеся составы в первоначальном состоянии жидкие. Затем в них вводятся ПАВ и песочный наполнитель. Такой состав сохраняет текучесть не более 10 минут. Поэтому они приготавливаются на формовочных участках.
Химически отверждающиеся смеси имеют малый срок жизни. В следствие чего в смесь добавляется едкий натр.
Жидкостекольные разновидности после формирования подвергаются сушке продуванием углекислым газом. В процессе сушки протекают химические реакции: образование кремниевой кислоты и углекислого натрия.
Для изготовления стержня, например, первого класса, смесь целиком состоит кварца и крепителей. Для формовки крупных стержней используется 1/3 часть использованного и восстановленного состава.
Температура плавления цветных металлов значительно ниже, чем у сталей и чугунов. Из-за чего формовочные смеси имеют меньшую огнеупорность. Для литья бронзы и медных сплавов формовочные составы готовят при использовании глинистого песка П класса. Такие наполнители как борная кислота, серный цвет или фтористая присадка используются для литья алюминия. Они препятствуют активному окислению расплава.
Требуемые свойства
Для получения качественной отливки необходима литейная форма, изготовленная из ингредиентов, подобранных под разлив определенного металла. Формовочная смесь для литья должна обладать определенной влажностью. При малой влажности форма склонна к осыпаемости, что затрудняет формовку.
Плохая газовая проницаемость провоцирует образование в отливке дефектов — газовых пор и раковин. Из-за чего необходим песок крупной фракции (более 50%).
Свойства формовочных смесей характеризует твердость. Она зависит от равномерности и степени уплотнения. Уплотнение формы сверх нормы провоцирует появление таких дефектов как:
- пригар;
- распор;
- вскип.

Литье в песчано-глинистую форму
Высокая прочность формы и стержня не позволяет изменять геометрию отливки. Чтобы ее получить применяются специальные связующие материалы.
Приготовление смесей
Процесс приготовления формовочных и стержневых смесей проводится в три этапа. Первый этап — подготовительный. Здесь происходит подготовка еще неиспользованных материалов. Проводится сушка, дробление и последующее просеивание.
На втором этапе происходит подготовка отработанного состава. Это позволяет экономить на материалах. Процесс начинается на охладительных барабанах. Происходит выбивка, размельчение, охлаждение.
Формовочные смеси для литья готовятся на третьем этапе в смесителях. Широкое применение нашли катковые модели. Они используются для приготовления таких составов как:
- единые;
- стержневые смеси;
- облицовочные;
- с добавками:
- вязкие;
- жидкие;
- пылевидные.
При больших объемах выпуска производство автоматизировано. Механизация процессов отражается на снижении себестоимости продукции.
Если вы нашли ошибку, пожалуйста, выделите фрагмент текста и нажмите Ctrl+Enter.
stankiexpert.ru
Получение точных отливок из алюминиевых, магниевых и медных сплавов по постоянной модели

Производство точных отливок

В гипсовых формах изготовляют отливки только определенной массы. Особо сложные отливки получают в оболочковых керамических формах. Согласно сообщениям некоторых специализированных фирм (Canadion—Marconi, Sterling Metals Limited, Munetto) керамические формы более выгодны для отливок, имеющих очень большую разностенность.
Преимущества гипсовых форм для литья алюминиевых сплавов приводятся в работах.
Гипсовые формовочные смеси. Связующим в этих смесях является гипс, качеству которого придается большое значение. Для гипсовых форм пригоден только такой гипс, который при затвердевании не дает усадку. Гипсовые формовочные смеси имеют следующий ориентировочный состав, %: 30—100 гипса, 5—40 асбеста, 19—30 талька, 5—80 кварцевой муки, 0—10 гончарной глины, 33 молотого кирпича, 0—50 кварцевого песка, 70 кристобалита, 0—1,5 извести, 0—5 портландцемента, 0,25— 3,0 бромистого аммония.
Гипсовые формовочные смеси замешивают на воде до сметано-образного состояния в следующих соотношениях компонентов: 0,35 ч. воды на 1 ч. смеси. Отдельные присадки в гипсовые смеси влияют на их свойства следующим образом: молотый асбест повышает пористость; если асбест используют в волокнистой форме, то улучшаются механические свойства формы. Молотый асбест должен иметь соответствующую зернистость. Кварцевая мука снижает объемные изменения гипсовой смеси во время затвердевания, прокаливания и охлаждения формы. Тальк и кварцевый песок, как инертные наполнители, компенсируют объемные изменения. Известь и цемент стабилизируют объемные изменения формы. Бромистый аммоний при обжиге форм разлагается на газообразные вещества и способствует повышению газопроницаемости форм.
Помимо указанных присадок вводят также много других, применяемых значительно реже: борную кислоту в количестве от 1 до 2% и буру 0,35—0,5%, способствующих быстрому отверждению смеси. Жидкое стекло повышает прочность и сопротивление форм против истирания. Альгинат натрия в количестве 0,1—0,5%, карбонат натрия (0,1—0,5%), формалин регулируют скорость отверждения. Алюминат кальция в количестве 2,5—12% и окись цинка замедляют отверждение и придают формам большую прочность. В качестве присадки для повышения прочности форм используют также добавки окислов алюминия, железа и т. п.
Гипсовые формы должны иметь следующие основные свойства: достаточную прочность и сопротивление истиранию; достаточную газопроницаемость; возможно наименьшие объемные изменения.
Перечисленные свойства обеспечиваются составом смеси и способом ее приготовления. Наибольшее влияние на свойства смеси (помимо ее состава) оказывает вязкость гипсовой массы, определяемой соотношением сухих компонентов и воды. В результате исследований авторов оказалось, что количество воды на 1 кг формовочной смеси не должно превышать 0,8 л, иначе формы будут иметь низкую прочность, высокую газопроницаемость и при сушке большую усадку; наилучшим является соотношение 0,45— 0,55 л воды на 1 кг смеси. При меньших количествах воды гипсовая смесь очень густая и заливать ею сложные модели трудно; в такую смесь замешивается много воздушных пузырьков. Если соотношение приближается к 0,8 л воды на 1 кг смеси, то отверждение смеси резко замедляется и она даже через 48 ч остается мягкой. Это относится к гипсовой смеси, состоящей из 50% гипса «Rocasso», 30% асбестовой крошки и 20% кварцевой муки.
На свойства гипсовых форм еще влияют температура и время перемешивания формовочной смеси. Для указанной гипсовой смеси лучше всего применять воду с температурой 50—52 °С; при этой температуре формы имеют максимальную прочность, сопротивление истиранию, газопроницаемость и постоянство объема. Время перемешивания гипсовой смеси не должно превышать 3 мин. Более быстрое или более длительное перемешивание приводит к усадке гипсовых форм.
Несмотря на то, что гипсовые формы имеют в составе смеси вещества для повышения газопроницаемости, все же ее величина недостаточна, и поэтому получаются отливки с дефектами, например неслитинами.
Газопроницаемость можно повысить тремя способами:
1) присадкой в формовочную смесь таких веществ, которые после отверждения и нагрева формы газифицируются и удаляются из нее и за счет этого повышают газопроницаемость. Чаще всего для этих целей используют хлорид или бромид аммония;
2) нагревом в автоклаве (способ Antioch). При нагреве во влажной атмосфере при температуре 90° С гипс (дигидрат кальция) переходит в полугидрат [39], так как при этой температуре дигидрат является неустойчивой формой сульфата кальция. Вода, выделившаяся при разложении дигидрата кальция, растворяет полугидраты до насыщения. Так как растворимость полугидратов с увеличением температуры снижается, то в автоклаве поддерживается низкое давление (от 0,07 до 0,2 МПа). После выдержки (6 ч) формы в автоклаве ее охлаждают во влажной атмосфере. Поверхность формы охлаждается быстрее, чем внутренняя ее часть, поэтому в наружных слоях формы выделяются мелкие кристаллы дигидрата, а во внутренних частях формы — крупные. В такой форме с мелкозернистым поверхностным слоем и пористой внутренней частью газопроницаемость существенно выше;
3) вспениванием смеси (способ Gypsum Hydroperm). Сущность способа в том, что в гипсовые смеси добавляют вспениватель. В смесь вводят вещества, например, карбонат и разбавленную кислоту или перекись водорода и аммиачную воду. Между ними при перемешивании смеси идут реакции с выделением большого объема газа. Можно вводить в гипсовую смесь органические пенообразователи, которые при перемешивании захватывают воздух и хорошо его стабилизируют во всем объеме. Отвердевшая гипсовая форма насыщена мелкими газовоздушными пузырьками, что увеличивает газопроницаемость формы; условно назовем этот способ механическим вспениванием. Для каждого из этих способов существует своя технология.
В первом случае газопроницаемость повышается только после нагрева до температуры, при которой из формы практически удалена вся вода (и свободная, и связанная). При нагреве в автоклаве и при механическом вспенивании формовочной массы пористость образуется в тот момент, когда в форме имеется вся вода, как химически связанная, так и свободная.
Формы, у которых газопроницаемость повышают по первому способу, содержат в исходной гипсовой смеси вещества, которые образуют пористость тотчас после затвердевания массы. Это необходимо для того, чтобы облегчить отвод водяных паров при последующей термообработке. Механически удаляется вода при температуре 85—96 °С. Сушить форму следует осторожно, так как пористость весьма невелика и при образовании больших объемов водяного пара может произойти ее повреждение. Минимальное время нагрева до указанной температуры составляет 8 ч. Затем следует нагрев до 200—220 °С, при котором удаляется большая часть связанной воды. Скорость нагрева 50 °С/ч. При этой температуре формы выдерживают до 12 ч. Затем следует нагрев до 380 °С с той же скоростью, чтобы разложить аммониевые соли. Выдержка при этой температуре 5 ч. Далее формы охлаждают при 100 °С их извлекают из печи и подготовляют к заливке.
При изготовлении гипсовых форм, подлежащих нагреву в автоклаве или вспениванием, ‘в смесь не вводят присадки, повышающие газопроницаемость, такие, как асбест, стеклянная вата. Они в данном случае излишни. Более того, при их использовании увеличивается шероховатость поверхности форм. В период тепловой обработки гипсовой формы она становится достаточно газопроницаемой для удаления влаги. Именно в этот период удаляется свободная и дигидратная вода. Полугидратная вода удаляется во время заливки металла в форму. Образующиеся пары благодаря высокой газопроницаемости формы удаляются через стенки без какого-либо повреждения формы.
Таким образом, тепловая обработка форм при нагреве в автоклаве или при вспенивании очень проста, и сами формы не так чувствительны к скорости нагрева. Тепловую обработку форм проводят при низких температурах, находящихся между эндотермическими пиками, обусловленными потерей дигидратной и полу-гидратной воды. При нормальных условиях эта температура находится в пределах 180—225 °С. В диапазоне этих температур формы (в зависимости от их величины) выдерживают 10— 18 ч. После охлаждения формы подготовляют к заливке.
Сравнительные испытания всех трех описанных способов, проведенные предприятием ZPS г. Готвальдов (ЧССР), показали, что
газопроницаемость форм была в пределах 48—52 J. N. Р. Одинаковыми были также качество поверхности отливок и плотность металла непосредственно под литейной коркой.
Вспенивание форм требует точного выдерживания технологических параметров: давления, температуры и времени пребывания в автоклаве.
Для повышения газопроницаемости за счет разложения аммониевых солей необходима медленная и осторожная тепловая обработка форм. Объемную стабильность таких форм можно повысить присадкой 1% сульфата алюминия A123. Обработку гипсовых форм в автоклаве применяют в серийном производстве, а механическое вспенивание—в единичном.
Если необходимо иметь только определенную часть отливки с особо качественной поверхностью и жесткими допусками на размер, используют комбинированную форму. В песчаную форму вставляют или гипсовый стержень, или часть гипсовой формы.
Максимальная масса отливок из алюминиевых сплавов, которые можно получать в гипсовых формах, составляет 10—160 кг. Минимальная толщина стенки 1,5 мм, в особых случаях 0,55 — 1,0 мм.
Шероховатость поверхности в пределах от 60 до 80 RMS. Теплопроводность гипсовых форм относится к теплопроводности обычных песчаных форм как 0,65 : 1,0, что необходимо учитывать, в частности, при литье свинцовистых бронз. Содержание свинца в таких бронзах должно быть не более 2,5%, а содержание углерода максимум 7%; при более высоком содержании свинца при охлаждении происходит его ликвация.
Читать далее:
Сплавы для отливок, получаемых литьем по выплавляемым моделям
Статьи по теме:
pereosnastka.ru
состав формовочной смеси для литья алюминия видео Видео

...
2 лет назад
Самая простая смесь для формования под литьё.
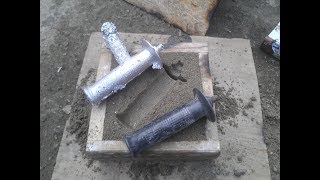
...
9 меc назад
Эксперименты с формовочной смесью для литья алюминия.
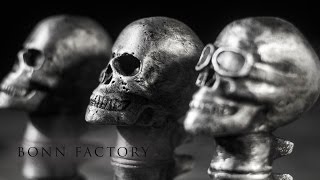
...
1 лет назад
Литье алюминия в песок. Подробный состав смеси для литья с объяснениями на примере. Создание уникальной...
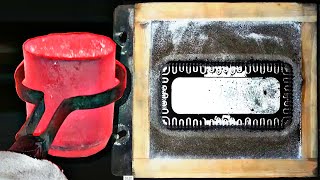
...
9 меc назад
Бентовая глина в литейном производстве применяется как связующий компонент для формовочной смеси или...
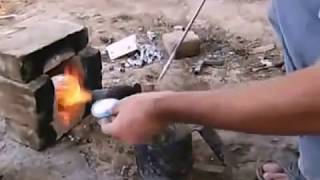
...
5 лет назад
литье алюминия в формовочную смесь состоящую из цемнента и тормозной жидкости.
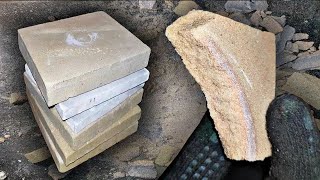
...
2 лет назад
Литье в земляные формы — один из древних способов, не утративший своего значения и теперь. Процесс получен...
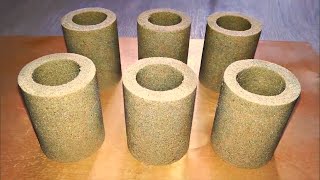
...
12 меc назад
Как неорганическое связующее в формовочных смесях жидкое стекло имеет ряд несомненных преимуществ – огро...
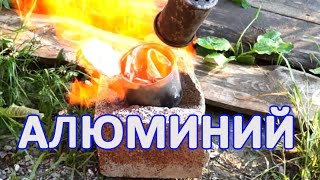
...
2 лет назад
ВСЁ для рыбалки: https://goo.gl/ysv6j1 Изготовил форму для отливки алюминия из гипса своими руками. Литье алюмин...
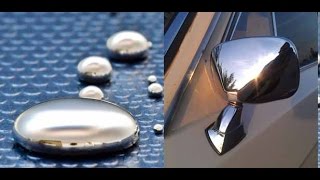
...
2 лет назад
Заработать на YouTube подключив партнерку http://join.air.io/leshaone Канал https://www.youtube.com/c/leshanavolvo Группа ВК http://vk.com/kulibincom...
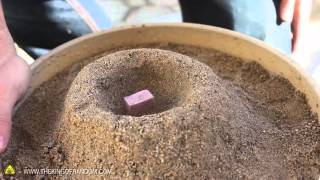
...
3 лет назад
Литьё по газифицируемым моделям — технология, позволяющая получить отливки по точности равные литью по...
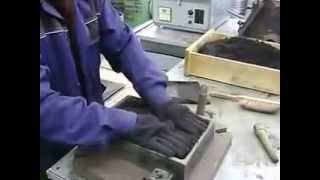
...
3 лет назад
Литьё в песчаные формы — дешёвый, самый грубый, но самый массовый (до 75-80 % по массе получаемых в мире отливок...
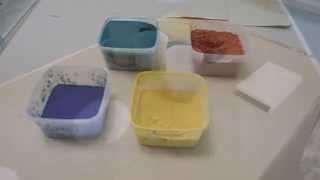
...
3 лет назад
На видео показано производство литьевого мрамора, состав материала и конечный результат. Для изготовления...
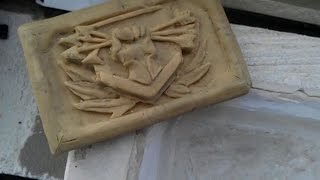
...
2 лет назад
Форма пряги знак из игры World of Tanks.
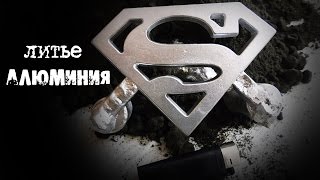
...
2 лет назад
Прошу прощение за монтаж музыки это мое первое видео... Видео показывает литье алюминия в домашних условиях....
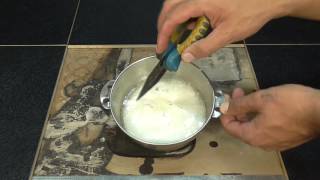
...
2 лет назад
Все о Шифере: http://шифер.рф всем привет.сегодня интересный эксперимент в котором заливаем расплавленный...
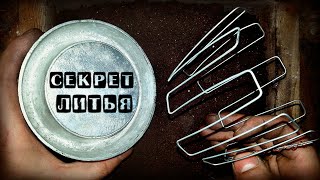
...
7 меc назад
Я не думаю, что проволочный каркас для ФОРМ является для кого-то загадкой, и все же предлагаю вашему внимани...
videoprime.ru
Литье алюминия в гипсовую оболочку
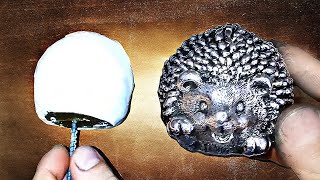
Кому это пригодится? Алюминий – материал проверенный. Из него изготавливали и посуду, и детали для авиацион...
(Формовочная смесь) Как разводить жидкое стекло с песком подробно в пропорциях!
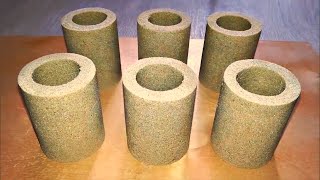
Как неорганическое связующее в формовочных смесях жидкое стекло имеет ряд несомненных преимуществ – огро...
Как сделать формовочная смесь обратимая многократного использавания крысеев В.И

Формовочная смесь песок + бентонитовая глина
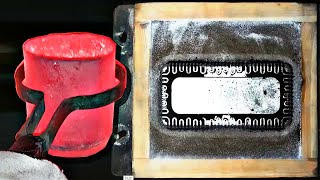
Бентовая глина в литейном производстве применяется как связующий компонент для формовочной смеси или...
Формовочная смесь песок +жидкое стекло
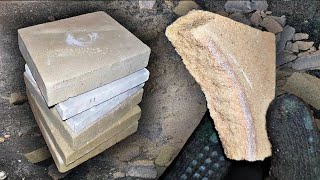
Литье в земляные формы — один из древних способов, не утративший своего значения и теперь. Процесс получен...
Литье алюминия в песчаную форму ( песок + бентонит ) - РУЧКА КПП АВТОМОБИЛЯ
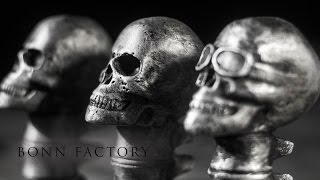
Литье алюминия в песок. Подробный состав смеси для литья с объяснениями на примере. Создание уникальной...
литье алюминия в цемент
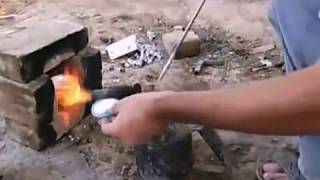
литье алюминия в формовочную смесь состоящую из цемнента и тормозной жидкости.
формовочная смесь для литья алюминия

Самая простая смесь для формования под литьё.
формовочная смесь для литья алюминия 2
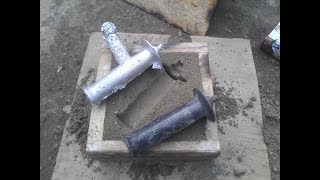
Эксперименты с формовочной смесью для литья алюминия.
food-health-vika.com