Штамповка изделий из металла – о разновидностях и технологиях процесса. Изготовление штампов для холодной штамповки металла
Холодная штамповка – щадящий и эффективный метод производста
1 Что дает материалу холодная деформация?
Металловеды и люди, связанные с производством, знают, что такое штампование, но мы все-таки уделим немного внимания и расшифруем этот термин. Это процесс пластической деформации материала, в результате чего последний приобретает заданные размеры и формы. Если есть воздействие больших температур, то речь идет о горячем деформировании, но мы более подробно остановимся на холодной штамповке металла, которая проходит без термического влияния.

Фото холодной штамповки металла
Рекомендуем ознакомиться
Все операции в этом случае выполняются в специальных технологических оснастках (штампах) и обязательно сопровождаются упрочнением. Благодаря чему готовое изделие отличается повышенным значением этой характеристики. А вот его пластические свойства, напротив, ухудшаются. Однако повышение прочности имеет и некоторые побочные эффекты, например, материал становится более хрупким и т. д. Поэтому между операциями осуществляют рекристаллизационный отжиг. Детали отличаются повышенной точностью и прекрасным качеством.
2 Листовая и объемная штамповка – в чем разница?
Особенностью холодной объемной штамповки является температура заготовок, которая не должна превышать ковочную. Это способствует увеличению сопротивления металла, а, следовательно, его текучесть снижается. Этим методом изготавливают элементы повышенной точности. К достоинствам относится отсутствие различных дефектов, таких как царапины, горячие трещины, риски, усадка. Однако из-за повышенного сопротивления внутри материала изготовить деталь сложной формы не удастся, для этого нужно прибегнуть к горячей штамповке.

На фото - горячая штамповка
Следующий вид – листовая штамповка. Ее особенностью является форма заготовки – лист, лента, полоса. Этим методом можно получить самые разнообразные изделия массой от нескольких грамм до десятков килограмм. В основном толщина стенок получаемых деталей такая, как у исходного материла. Получить пространственные элементы можно только из достаточно пластических металлов.
3 Какой путь проделывает деталь?
Сегодня существует множество специальных программ проектирования штампов для холодной штамповки, однако они неавтономные и в основном неразрывно связаны со всей системой. Чертежи могут быть как двумерными, так и современными, выполненными в формате 3D. А сам процесс требует некоторых навыков, знания компьютера и выполняется в такой последовательности:
- нанесение эскиза;
- изучение схемы раскроя и ее проверка специальной программой;
- редактирование;
- повторная проверка размеров;
- нанесение рабочих отверстий.

Фото штампов для холодной штамповки
Далее следует довольно тяжелый и ответственный процесс изготовления штампов холодной штамповки. После окончательной подготовки чертежа изделие разделяют на отдельные части, внимательно изучают их. Обязательно необходимо уделить особое внимание техническим требованиям, предъявляемым к готовой детали. Затем составляют для каждого элемента маршрутно-технологическую карту с учетом всех нюансов, начиная от времени, потраченного на изготовление, и заканчивая характеристиками. Следует заметить, что в этом процессе не может быть мелочей, так как любой, даже самый незначительный недочет приведет к дефектам. Имеет значение последовательность операций, правильное распределение материала, подбор оборудования и режимов.
К качеству штампов для холодной штамповки тоже предъявляются весьма серьезные требования. Ведь именно от них зависит размер, форма и чистота поверхности готового изделия.

На фото - формирование элементов листовым способом
Формирование элементов листовым способом подразумевает ряд операций. Сначала материал поступает на стан, где вырезаются либо выдавливаются части детали. Затем следуют формоизменяющие операции. К ним относятся гибка, обжим, формовка и вытяжка. При этом не стоит недооценивать и роль вспомогательных процессов. Это отжиг и травление, благодаря которым задаются желаемые механические свойства. Еще можно повысить износостойкость с помощью дополнительных защитных покрытий. Кроме того, детали подвергают правке, очистке и смазке.
Технологический процесс объемной холодной штамповки делится на две основные схемы. Первая состоит из трех операций. Предварительно проводят термическую обработку металла с целью его разупрочнения. Затем подготавливают поверхность проката и осуществляют непосредственно штамповку. Но можно придерживаться и иной схемы, включающей в себя 4 этапа. В этом случае сначала подготавливают мерные заготовки, а потом уже проводят все операции аналогично первой схеме.
tutmet.ru
Штамповка изделий из металла – технологии изготовления + Видео
Штамповка изделий из металла признается специалистами по-настоящему передовым методом выпуска разных по назначению деталей. Она придает готовым изделиям требующиеся размеры и формы посредством пластической деформации.
Разновидности штампования – каждой детали своя технология
Штамповочные мероприятия делятся на формоизменяющие и разъединительные. Под формоизменяющими процессами понимают такие операции, как холодное выдавливание, вытяжка, формовка. Разъединительное штампование – это процедуры, при которых металл (обычно листовой) делится на заданные геометрические части (рубка, резка, пробивка).
Рассматриваемый нами процесс получения штампованных деталей может быть объемным либо листовым.

Процесс получения штампованных деталей
Если изготовление деталей производится из металлических листов толщиной не более 6 миллиметров, речь идет о листовой штамповке. Во всех остальных случаях говорят об объемной операции. Штампование выполняется при помощи специальных механизмов, которые называют прессами. Они способны посредством механического воздействия деформировать исходную заготовку.
Штамповка листов металла выполняется по разным схемам в зависимости от оснастки, используемой для изменения размеров и формы материала. С этой точки зрения штампование бывает:
- валковым;
- гидро- или магнитно-импульсным;
- эластичными средами;
- взрывом;
- в инструментальных штампах.

Штамповка листов металла
Изготовление штампованных изделий выполняется по двум технологиям – холодной и горячей. Далее мы рассмотрим наиболее часто используемые способы производства разнообразных деталей штампованием.
Горячая объемная штамповка для массового изготовления изделий
Под таким процессом понимают методику обработки металлических заготовок давлением. Сырьем для операции выступает прокат – периодический, прямоугольного, квадратного или круглого профилей. Его перед обработкой режут на заготовки определенных размеров. В некоторых случаях поковка отделяется от проката непосредственно на агрегате для штампования.

Обработка металлических заготовок давлением
Обязательным атрибутом горячей объемной операции является штамп – специальный инструмент с выступами и полостями. При заливке металл заполняет эти «неровности». На финальном этапе штамповки по конфигурации поковки образуется замкнутая единая полость. Штампы могут быть закрытыми и открытыми.
Объемное горячее штампование рекомендуется производить при массовом и крупносерийном производстве деталей. Данная технология позволяет получать сложные изделия (по форме). Также она характеризуется следующими достоинствами:
- отличное качество поверхности получаемых деталей;
- высокая производительность рабочего процесса;
- безупречная точность формы штампованных деталей;
- малый объем отходов металла.

Объемное горячее штампование
Горячая листовая штамповка применяется тогда, когда металлические изделия производятся из листов 3–4 миллиметра по толщине. Начальная заготовка при этом нагревается в специальных электрических либо пламенных устройствах-печах.
Холодная листовая штамповка – гарантия получения высокоточных деталей
Данная операция имеет ряд достоинств:
- экономическая целесообразность использования ХЛШ (холодной листовой штамповки) и при производстве изделий мелкими партиями, и тогда, когда осуществляется массовое изготовление деталей;
- возможность выпуска продукции с высокой жесткостью и показателем прочности при минимальном ее весе;
- простота автоматизации и качественной механизации штамповочных операций – один агрегат за 8–12 часов способен «выдать» до 35–40 тысяч готовых изделий;
- достойное качество получаемых поверхностей и отличная точность параметров деталей – отделочные процедуры за счет этого сокращаются до минимума;
- экономия расхода металла;
- возможность изготовления мелких и крупных по размерам деталей.

Массовое изготовление деталей
При ХЛШ используют заготовки из латуни, легированных пластичных металлических сплавов, титановых, магниевых и алюминиевых композиций, низкоуглеродистых сталей. Исходный материал подается в штамповочный агрегат в виде лент и полос в рулонах, листов, полученных методом прокатки. Холодная штамповка востребована при выпуске изделий для приборо- и тракторостроительной промышленности, ракето-, самолето- и автопредприятий.
Объемная штамповка по «холодной» технологии незаменима при производстве:
- элементов вертолетов – втулок винтов и других деталей;
- коленвалов двигателей внутреннего сгорания;
- опор (шаровых) автомобильных подвесок;
- различных метизов – зубчатых шайб, косых шайб и так далее;
- любых высоконагруженных и высокоточных изделий.

Производство различных метизов
Объемная холодная штамповка позволяет получать указанные детали без царапин и рисок, а также иных поверхностных дефектов.
Оцените статью: Поделитесь с друзьями!это процесс обработки металлов. Виды штамповки и оборудование
Технологический процесс, при котором происходит обработка заготовок, позволяющий получить плоские или объёмные готовые изделия различных форм и размеров, - это штамповка. Рабочим инструментом для такой цели является штамп, который закреплён на прессе или другом оборудовании. Штамповка - это два вида технологии, которые в зависимости от условий выполняются горячим или холодным способом, а потому и оборудование, и технологические нормы отличаются друг от друга.
Категории
Помимо разделения технологии на холодный и горячий способы, штамповка - это целый ряд категорий, на которые подразделяются методы обработки материала. Зависит выбранный способ чаще всего от назначения изделия, но и технологические условия тоже на него влияют. Например, есть способ, при котором отделяется часть заготовки, и это штамповка разделительная. Сюда же входят пробивка, рубка, резка деталей. Есть категория операций, когда применяется горячая штамповка, посредством которой лист металла меняет форму. Их ещё называют формовкой. В результате детали подвергаются гибке, вытяжке и другим процедурам.
Холодная и горячая штамповка реализуются с использованием одного и того же принципа, который предполагает деформирование материала, но в остальном изготовление продукции этими методами имеет много отличий. Предварительный нагрев деталей до определённых (и достаточно высоких) температур предполагается в основном на крупных промышленных предприятиях, каким является, например, металлообрабатывающий завод. Это связано со сложностью такого технологического процесса, большим количеством операций, качественно выполнить которые можно только с точным предварительным расчётом и соблюдением высокой точности степени нагрева заготовки.
Горячий способ
Штампованные детали, обработанные по горячей технологии, должны обладать отменным качеством, поскольку, например, из листового металла разной толщины изготавливают такие ответственные вещи, как днища котлов и другие полусферические изделия, в том числе и ответственные элементы в судостроении. Для нагрева металлической детали используют оборудование, обеспечивающее правильный температурный режим.
Эти устройства и печи могут быть плазменными, электрическими или другими, их достаточно много видов. Перед подачей горячей детали на штамповочный пресс нужно не только норму нагрева рассчитать, но и разработать подробный чертёж уже готового изделия, где обязательно учесть усадку металла после остывания.
Холодная штамповка
Выполнение штамповки холодным способом подразумевает формирование изделия посредством давления, которое оказывают на заготовку рабочие элементы пресса. Усадке такие изделия не подвержены, потому что предварительно их не нагревают. Дальнейшая механическая доработка таким изделиям тоже не нужна после того, как окончена штамповка. Способы штамповки могут быть разными, холодный же является и более удобным, и экономически выгодным.
Материалы, хорошо поддающиеся холодной штамповке, относятся не только к углеродистым или легированным сталям. Штамповочное производство успешно работает и на алюминиевых, и на медных сплавах. Холодный способ выполняется преимущественно с помощью гидравлических прессов, и производство их регулируется ГОСТом. Серийные модели весьма разнообразны, а потому появляется возможность подобрать подходящий станок для производства любых конфигураций и размеров изделий. Штампы для штамповки металлов по своему оснащению очень сильно отличаются от тех, которые работают с такими материалами, как кожа, резина, картон, полимерные сплавы и тому подобное.
Разделительное штампование
Одной из самых распространённых технологическх операций является разделительное штампование, которое отделяет от заготовки часть металла. Этот способ используется почти на всех производственных предприятиях. На штамповочный пресс устанавливают специальные инструменты, которые производят резку, вырубку и пробивку материала. Благодаря этому процессу можно разделять металлические детали хоть по кривой, хоть по прямой линии реза. Резку выполняют самые разные устройства: гильотинные ножницы, вибрационные и дисковые станки и тому подобное. Используется резка для того, чтобы для дальнейшей обработки раскроить заготовки.
Вырубка - другая технологическая операция. Например, нержавеющий лист из металла нужно превратить в детали с замкнутыми контурами. Листовой металл при помощи пробивки снабжают отверстиями любой конфигурации. Нужно сказать, что и этот технологический процесс требует тщательной предварительной подготовки и подробного плана, с расчётом геометрических параметров инструмента, который используется. Иначе качественное изделие может и не получиться. Технологических операций, касающихся штамповки, очень много, потому что требуется изменить начальную конфигурацию деталей. Это гибка, формовка, отбортовка, вытяжка и обжим.
Технологические операции
Наиболее распространённая операция, изменяющая форму детали, это гибка, которая формирует на поверхности заготовки из металла запланированные участки с изгибом. Вытяжкой называется объёмная штамповка. Это операция, с помощью которой получается объёмное изделие из такой плоской металлической поверхности, как, например, металлический нержавеющий лист. Именно с помощью вытяжки он превращается в цилиндр, конус, полусферу или принимает коробчатую конфигурацию. Изделия из листового металла должны иметь бортик по краю и вокруг отверстий, если они внутри заготовки выполнены. Например, отбортовка должна завершать конец трубы, чтобы установить на неё фланец. Такая операция требует наличия специального инструмента.
При помощи обжима происходит обратное действие. Отбортовка расширяет концы заготовок из листового металла, а обжим сужает. Те же концы труб или край полости требуют такой операции, которая осуществляется посредством конической матрицы наружно. Формовка тоже относится к основным операциям, относящимся к штамповке. Она помогает изменить форму отдельным элементам штампованной детали, а наружный контур оставляет неизменным. Объёмная штамповка требует работы специального оборудования и сложных предварительных чертежей, а потому в домашних условиях практически никогда не реализуется.
Выбор пресса
Для обработки металлов, даже самых мягких (например, для штамповки алюминия), требуется специальное оборудование: гидравлический или кривошипный пресс или гильотинные ножницы. И конечно же, необходимы многие знания. Например, как произвести расчёты по расходу материала и выполнить технические чертежи. Требования ГОСТа при этом обязательно учитываются.
Чтобы выбрать нужный пресс для штамповки, сначала нужно чётко представить себе задачу, которую ему предстоит решать. Выполнение таких операций, как пробивка или вырубка, требует использования штамповочного оборудования простого действия, с небольшим ходом ползуна и шайб в процессе обработки. Но уже для вытяжки необходимо совсем другое, более мощное оборудование, где ползун и шайбы совершают значительно более широкий ход. Такая способность есть у оборудования двойного действия.
Оборудование по ГОСТу
Выполнение штамповки в зависимости от условий задачи может быть совершено на оборудовании следующих типов: одно-, двух- и четырёхкривошипном. Последнее - с установкой ползунов крупных размеров. Однако оснащение штамповочного пресса матрицей не зависит от конструктивного исполнения. Основную работу посредством движения выполняет ползун, соединённый нижней своей частью с подвижным штампом. А чтобы ползун пресса двигался, приводной электродвигатель снабжён элементами кинематической цепи: клиноременной передачей, пусковой муфтой, шайбами, кривошипным валом, шатуном, регулирующим величину хода ползуна.
Запускается ползун с помощью ножной пресс-педали, которая связана с пусковой муфтой, после чего начинаются его возвратно-поступательные движения, направленные на рабочий стол пресса. Четырёхшатунный пресс имеет другой принцип действия. Его рабочие органы направляют всё усилие в середину четырёхугольника, который образуют четыре шатуна. Такое устройство успешно используют для изготовления изделий самой сложной конфигурации: асимметричных или габаритных.
Для сложных изделий
Чтобы получить качественные изделия сложной конфигурации, очень широко используется пресс пневматического типа с двумя или тремя ползунами. Пресс двойного действия работает двумя ползунами одновременно: внешний фиксирует заготовку, а внутренний производит вытяжку поверхности металлического листа. Тонкие листы металла штампуют специальными фрикционными прессами, а толстые - гидравлическими, которые имеют более надёжные шайбы.
Отдельная категория штамповочного оборудования - штамповка, управляемым взрывом. Такие устройства направляют мощность взрыва на отдельные участки металлической заготовки (обычно значительной толщины). Это инновационное оборудование, работа которого даже на видео выглядит весьма эффектно. Сгибы и общую конфигурацию сложного изделия обрабатывают с помощью встроенных вибрационных ножниц.
Листовая штамповка
Листовая штамповка (например, изготовление перфолиста) подразумевает процесс пробивания листового металла. Вся остальная штамповка - объёмная. Применяемая оснастка для штамповочного оборудования разделяется на виды. Она может быть инструментальной, импульсной (взрыв, магнитный или гидроимпульс), валковой или штамповкой эластичными средами. Листовой штамповкой можно изготовить пространственные и плоские детали различной массы - от долей грамма, и различных размеров - от долей миллиметра (здесь можно посмотреть на секундную стрелку наручных часов). Также листовой штамповкой изготавливаются детали во многие десятки килограммов по массе и в несколько метров величиной (автомобильная облицовка, ракеты и самолёты).
Используют для этого преимущественно низкоуглеродную сталь, а также и легированную - с особой пластичностью, латунь, медь, алюминий и магний со сплавами, титан и многое другое. Листовая штамповка - это почти все отрасли промышленности: ракето-, самолёто-, тракторо-, авто-, приборостроение, электротехническая промышленность и так далее, можно перечислять всё. Преимущества её велики.
Объёмная штамповка
Объёмная штамповка может быть выполнена и холодным, и горячим способами. Горячая - обработка давлением, где формообразование поковки осуществляется с помощью штампа. Заготовками служат прокат прямоугольного, круглого, квадратного профиля, который разрезается на мерные заготовки (иногда не разрезают, а штампуют прямо из прутка, отделяя затем поковку прямо штамповочной машиной).
Объёмная штамповка применяется при массовом производстве и серийном, что повышает производительность труда и снижает отходы металла. Качество изделий тоже соответствует высоким стандартам. Такой штамповкой получают изделия, исключительно сложные по форме, которые нельзя получить даже свободной ковкой.
Штампы открытые и закрытые
Открытые штампы позволяют наблюдать зазор между неподвижной и подвижной частями станка. При горячей штамповке в зазор вытекает облой - металл, закрывающий выход из полости и заставляющий остальную массу заполнить полость полностью. В процессе деформирования в облой попадают излишки металла. Но удалять облой трудно.
Закрытые штампы не позволяют заглядывать внутрь и наблюдать процесс - полость закрыта. Облой тоже не предусмотрен. Устройство такого штампа зависит от типа станка. Здесь нужно очень строго соблюдать точность объёмов и равенство их в заготовках и поковках: недостаток металла оставит пустыми углы полости, а избыток его сделает поковку больше требуемой по высоте.
fb.ru
Материалы для изготовления штампов - Слесарно-инструментальные работы

Категория:
Слесарно-инструментальные работы

В штампах для холодной штамповки (рис. 1, а) только формообразующие детали, т. е. пуансон и матрицу, изготовляют из инструментальной стали; в штампах для горячей штамповки из инструментальной стали изготовляют или все детали (рис. 1, б), или только вставки (рис. 1, в). В качестве материала для формообразующих деталей штампов применяют инструментальные стали, твердые сплавы, пластмассы и другие материалы.
Рис. 1. Виды штампов: а — для холодной штамповки: 1 — нижняя плита, 2 — матрица, 3 — направляющая колонка, 4 пуансон, 5 — верхняя плита, 6 — направляющая втулка; б — две половины цельного штампа для горячей штамповки: А —- нижняя, Б — верхняя; 1 — протяжной ручей, 2 — чистовой ручей, 3 — черновой ручей, 4 — гибочный ручей, 5 — хвостовая часть, 6 — подъемное отверстие, 7 — клещевина, 8 — контрольная сторона, 9 — шпоночный паз; в — сборный штамп для горячей штамповки: 1 •— блок с подготовительными ручьями, 2 — вставка чистового ручья, 3 — вставка чернового ручья, 4 — углубления для вставок
Углеродистые инструментальные стали У7, У8, У9 и У10 пониженной прокаливаемости используют для изготовления матриц и пуансонов штампов для холодной штамповки, имеющих простую форму их рабочего контура (в таких штампах нет резких переходов между элементами; отсутствуют узкие прорези, тонкие перемычки металла между отверстиями и т. п.). Это связано с тем, что стали пониженной прокаливаемости деформируются при закалке, в результате чего образуются трещины.
Пуансоны и матрицы штампов для холодной штамповки более сложной формы делают из сталей марок X, 9ХС, ХВГ, ХГС и других повышенной прокаливаемости.
Пуансоны и матрицы штампов для холодной штамповки весьма сложной формы изготовляют из сталей марок Х12Ф, Х12Т, Х12М высокой прокаливаемости. Эти стали, близкие по своим свойствам к быстрорежущим сталям, содержат около 1% углерода, 12% хрома и около 1% ванадия (титана или молибдена), характеризуются высокими прочностью, износостойкостью, теплостойкостью (около 500°С). Важным достоинством сталей высокой прокаливаемости являются малая деформация и, следовательно, сохранение размеров их рабочего контура при закалке. К недостаткам относятся склонность к карбидной неоднородности и плохая обрабатываемость резанием. Сталь марки Х12Ф почти в 2,5 раза дороже, чем углеродистая сталь марки У10.
Тонкие и длинные пуансоны дыропробивных штампов для холодной штамповки и другие нежесткие детали изготовляют из сталей марок 4ХС, 5ХС, 4ХВ2С, 5ХВ2С и т. п. повышенной вязкости. Снижение хрупкости у этих сталей достигается уменьшением содержания углерода (не более 0,5%), а высокая износостойкость определяется наличием хрома и вольфрама. Теплостойкость сталей этой группы около 300 °С; закаливают их в масле, сквозную закалку получают у образцов диаметром до 50 мм.
Штампы и вставки для горячей штамповки (молотовые штампы) изготовляют из сталей марок 5ХНВ, 5ХНТ, 5ХНС, 5ХНСВ, 5ХНМ и других повышенной вязкости при нагреве. Молотовые штампы обычно имеют большую массу, работают в условиях ударной нагрузки и деформируют металл, нагретый до температуры 900—1200 °С. Поэтому главными требованиями к сталям этой группы являются высокие вязкость, теплостойкость и сопротивление образованию окалины. Рабочий контур этих штампов обычно имеет сложную форму и значительные размеры, что требует возможно большей прокаливаемости и минимальной деформации при закалке. Эти требования обеспечиваются химическим составом сталей, в котором содержится 0,5% углерода, хром, никель и другие легирующиие элементы. Теплостойкость сталей этой группы достигает 500 °С.
Наиболее высокие свойства имеет сталь марки 5ХНМ, из которой изготовляют крупные штампы (наименьшая сторона куба более 400 мм), имеющие сложную форму рабочего контура; твердость таких штампов 36—39 HRC3.
Штампы средних размеров изготовляют из сталей марок 5ХНВ, 5ХНС и 5ХНСВ. Эти стали, легированные вольфрамом или кремнием, по свойствам близким к стали 5ХНМ, но уступают ей по прокаливаемости. Твердость таких штампов 37—42 HRC,.
Несколько ниже теплостойкость и прокаливаемость у стали марки 5ХНТ, которую применяют для изготовления молотовых штампов малых размеров (наименьшая сторона куба до 300 мм). Твердость таких штампов 41—45 HRQ.
Рабочие детали штампов для горячей штамповки, обладающие малой массой и подвергающиеся при работе нагреву до высоких температур (матрицы для обрезки облоя, тонкие прошивные пуансоны, ножи для горячей резки т. п.), изготовляют из сталей марок ЗХ2В8, 4Х2В8, 4Х8В8 и других повышенной прочности при нагреве. Эти стали имеют высокие прочность, износостойкость, теплостойкость (до 650 °С).
Все более широкое применение для изготовления формообразующих деталей штампов получают твердые сплавы ВКЮ, ВК15, ВК20, ВК25 и ВКЗО. Эти сплавы, отличающиеся от сплавов той же группы, применяемых для режущих инструментов, большим содержанием кобальта (10—30%), характеризуются повышенной прочностью и вязкостью, но пониженной твердостью и износостойкостью.
Твердый сплав применяют для оснащения пуансонов и матриц дыропробивных и вырубных штампов. В электротехнической промышленности такие штампы применяют для листовой штамповки пластин, из которых собирают трансформаторные сердечники, статоры и роторы электродвигателей и другие подобные детали. Выбор марки твердого сплава зависит от прочности листа и его толщины. Чем прочнее материал и толщина листа, тем больше кобальта должен содержать твердый сплав.
Читать далее:
Формообразующие детали штампов для холодной штамповки
Статьи по теме:
pereosnastka.ru
Изготовление штампов для холодной листовой штамповки
19.09.14
Первые ручные штампы для изготовления мечей, всевозможных инструментов и посуды из металла применялись кузнецами Киева, Новгорода, Чернигова применялись больше десяти веков назад. А вот серийное изготовление штампов для холодной листовой штамповки началось вместе с бурным ростом автомобилестроения, судостроения, крупного промышленного и сельскохозяйственного машиностроения.
Что такое штамп, и какие они бывают
Сложное приспособление для массового изготовления металлических деталей строго заданных техпроцессом и техническими чертежами называется штампом.
По технологическим и механическим свойствам они делятся на:
- штампы для холодной штамповки металла
- штампы для горячей штамповки металла
Первые предназначены для работы с металлом толщиной до 10мм, вторые с раскаленным металлом толщиной от 12 до 20мм.
По виду оборудования штампы делят на прессовые, молотовые и специальные.
Молотовые штампы по своей конструкции являются сравнительно простыми устройствами. У них, в отличие от вырубных, нет направляющих колонок, втулок, клинов, съемников или толкателей. Две части молотового штампа холодной штамповки с ручьями заданной формы соединяются по поверхности раздела штампа.
По профилю ручья штампы получают название:
- высадочный, подкатной или протяжной
- окончательный или чистовой
- гибочной
- отрубной
- осадочный для сплющивания заготовок
Прессовые штампы для холодной штамповки гораздо сложнее по своим конструкционным параметрам и требованием, поэтому проектирование штампов для холодной штамповки доверяют самым опытным сотрудникам конструкторско-технологических бюро, хорошо разбирающимся в штамповом хозяйстве.
В нижней плите штампа расположена матрица, в нее запрессованы направляющие для соединения с верхней плитой и выбраны пазы для жесткого крепления к столу пресса.
Межцентровое расстояние запрессованных колонок должно буквально на микроны совпадать с запрессованные в верхнюю часть плиты втулок.
Иначе при опускании верхней плиты с пуансоном по направлению к матрице, расположенной в нижней плите, втулки не смогут точно попасть на колонки или будут сильно перегреваться при работе из-за малейшей неточности. А ведь счет деталей в смену идет на тысячи! Вот сколько закрытий и открытий и закрытий выполняет обыкновенный штамп. А в неделю, а в месяц.
Обрабатывать такое количество деталей, зачастую довольно сложной конфигурации, механической обработкой на токарных, фрезерных и шлифовальных станках намного сложнее, затратнее по времени в разы, да и брака в работе допускаться будет много на каждой последовательной операции.
По этой причине в инструментальных цехах большинства современных крупных предприятий налажено собственное изготовление штампов для холодной штамповки.
Сложные по профилю пуансон и матрице лучше вырезать из закаленных плит высококачественной легированной стали на специальных электроэрозионных станках медной или латунной проволокой толщиной 0.01-0.02мм. Особенно при вырубке деталей из тонкого материала на беззазорных штампах.
С увеличением толщины полосы для вырубки увеличивается зазор между пуансоном и матрицей. А при вырубке деталей толщиной от 6 до 10мм на рабочей части матрицы, а порой и пуансоне делается волнистая разгрузка, чтобы пуансон заходил в матрицу не одновременно. Все эти нюансы рассчитываются в СКБ и приходят в инструментальных цех на участок изготовления штампов вместе с чертежами и техническим процессом.
Кроме вырубных прессовых штампов есть много разновидностей гибочный штампов для изготовления изогнутых по заданному чертежами размеру и углу из полосы нужной толщины или прутка. При гибке деталей в зависимости от толщины, плотности и упругости полосы порой приходится следить за параметрами изделия и делать поправки на отпружинение. Особенно это проявляется при получении полосы той же толщины, но от другого поставщика, замечено на практике.
Если вырубные штампы на прессах в основном работают в вертикальной плоскости, то гибочные нередко можно встретить с горизонтальным расположением пуансона и матрицы. В народе их иногда называют «бульдозерами» и гнут они толстые детали.
Вырубные штампы с одновременным выполнением на детали круглых, квадратных или овальных отверстий (а иногда и всех одновременно) называют компаундами.
pres-forms.ru
технология, штампы, станок, пресс и другое оборудование для штамповки листового металла
С помощью листовой штамповки различными отраслями промышленности сейчас производятся изделия в достаточно широкой номенклатуре. Это один из многих способов обработки металла, который используются человеком очень давно.
Общие принципы штамповки
Процесс производства изделий из металлического листа штамповкой — это основа изготовления многих видов продукции в виде готовых деталей и различных полуфабрикатов. Изделие получается путём деформации листовой заготовки под действием внешнего давления.
Технология листовой штамповки металла известна ещё из древности, когда таким путём человек научился обзаводиться оружием, когда у него появилась потребность в различных украшениях и предметах бытового назначения. Ещё с середины 18-го века этот способ обработки металла начал совершенствоваться, благодаря чему появились первые технологии серийного производства различных предметов, пользующихся большим спросом у населения. Важно, что штампованные детали в большинстве своём являются высококачественными и обладают отличными свойствами при эксплуатации.
Лишь в 20-м столетии приёмы штамповки листовой стали достигли более высокого производственного уровня. Большим двигателем в развитии этого производства стала автомобильная отрасль, ведь именно путём штамповки получают детали автомобильных кузовов и другие детали любых транспортных средств. Теперь штамповка глубоко внедрена в такие отрасли, как ракетостроение, строительство судов и самолётов. Штамповочная технология стала просто незаменимой в современном машиностроении.
Популярность технологий штамповки объясняется их следующими качествами:
- возможностью наладить механизированные и автоматизированные производственные процессы, роторно-конвейерные линии производства;
- доступностью простых приёмов изготовления металлических полуфабрикатов любых геометрических форм и размеров;
- снижением себестоимости производства высокоточных взаимозаменяемых деталей без последующих обработок абразивными и режущими инструментами.
Следует отметить, что горячая и холодная штамповка листового металла служит надёжной гарантией того, что полученные детали не будут иметь излишней металлоёмкости, их форма будет рациональной, а прочность не уступит исходному материалу. Штамповка листового металла позволяют получать массивные изделия для машиностроительной и судостроительной отраслей, одновременно и филигранные изделия с тонкими стенками для различных бытовых приборов.
Часто предприниматель организует оказание услуг листовой штамповки на заказ. Для этого клиент обязан предоставить ему чертёж требуемой детали и материал, из которого её следует изготовить. Если у заказчика отсутствует нужный листовой материал, он может купить его у производителя. Стоимость таких услуг напрямую связана со сложностью заказываемых деталей. Если для выполнения работы требуется изготовление специального пресса, то стоимость услуги значительно возрастает.
Технологические особенности штамповки
Сырьём для получения изделий методом штамповки являются полосы и листы из стали и других металлов, различные ленты, профилированные заготовки.
Штамповка разделяется на горячую и холодную, но предпочтение производственники всё же отдают холодной, так как в этом случае не требуется энергозатратных операций нагрева исходного материала. Горячая листовая штамповка металла применяется в тех случаях, когда штамповочное оборудование не обладает достаточной мощностью, чтобы деформировать листы большой толщины. Второй причиной применения горячей штамповки является низкая пластичность исходного материала, когда в холодном состоянии его деформации начинают носить не пластичный, а разрушающий характер.
Методы листовой штамповки делят на операции разделительного и формоизменяющего типов. Разделительные операции применяются для получения деформации сдвига по контуру производимой детали из металла.
К разделительным операциям штамповки нужно отнести:
- резку металлических листов гильотинными, дисковыми или вибрационными ножницами по прямой или кривой линии;
- пробивку или прошивку листа для получения в заготовке отверстий требуемой формы и нужного размера;
- вырубку деталей, имеющих замкнутый контур.
Изменение же формы деталей при штамповке не требует разрушения целостности листа, таким путём лишь получают требуемые конфигурации деталей и их заданные размеры.
К формоизменяющим операциям можно причислить:
- отбортовку или создание бортиков на изделии по заданным контурам и размерам;
- вытяжку, благодаря которой на деталях получают различные полости и геометрические формы;
- обжимку, когда конической матрицей получают сужение торцевых участков металлических полых заготовок;
- гибку и формовку, благодаря которым плоские детали получают изогнутую конфигурацию.
При холодной штамповке чаще используют листовой материал из медных или алюминиевых сплавов. Широко используются и листы углеродистой и легированной стали. Нередко штамповке подвергаются материалы неметаллической природы, это заготовки из картона, кожи, пластмассы.
Станки и пресса для штамповки
Работы по штамповке листового металла выполняются с помощью специальных штампов, которые изготавливают из стали инструментального класса. Обычно штамп состоит из двух частей – подвижной и неподвижной. В подвижную часть станка устанавливается пуансон, а в неподвижную – матрица. Это рабочие элементы большинства штампов, именно при сближении их и происходит деформация листового металла и получение штампованных деталей.
Пуансон и матрицу крепят к рабочим элементам пресса для штамповки листового металла. К исполнительному элементу пресса закрепляется пуансон, а матрицу закрепляют на рабочем столе станка.
Рабочие элементы штампов изготавливают из дорогих стальных сплавов инструментального класса. В случаях же штамповки мягких металлов, например, меди, алюминия, для изготовления штампов можно использовать и более дешёвые материалы, включая пластмассы и даже прессованную древесину.
Чтобы понизить себестоимость штамповки больших по размерам и по весу деталей, изготавливаемых малыми партиями, матрицы штампов иногда изготавливают даже из бетона или чугуна. А в качестве пуансона применяют специальный контейнер, заполненный водой. Контейнер размещается над матрицей, опускается вниз до упора. Затем внутри контейнера инициируется пороховой заряд, благодаря которому достигается требуемое давление на обрабатываемый металл. Происходит его деформация и при этом формируется нужная заготовка или готовая деталь.
Основными видами штамповочного оборудования являются станок для листовой штамповки и гильотинные или вибрационные ножницы. Ножницы используют для раскроя металлического листового материала, обычно они легки в эксплуатации и обладают высокой функциональностью. А вот подборку пресса следует производить, исходя из вида операций, которые будут с его помощью выполняться. Часто на производстве устанавливают пресс кривошипного типа, так как его работа очень проста и не требует интенсивного обслуживания.
Разберёмся с этим принципом работы:
- с помощью клиноремённой передачи от двигателя через муфту на кривошип передаётся требуемое вращательное движение;
- шатун, который можно регулировать по длине хода, передаёт своё движение на ползун устройства;
- запуск рабочего хода ползуна с пуансоном осуществляется с помощью педальной муфты.
Чтобы выполнять прессовку простых по конфигурации деталей, достаточно иметь обычный прессовый станок и штампы для листовой штамповки. Для того же, чтобы штамповать изделия средней и высокой сложности, потребуется особый тип прессового устройства, которое снабжено двумя и более ползунами и более сложные комплекты штампов.
При обработке металла совершает движение лишь пуансон, который закреплён на ползуне прессового станка. Неподвижная матрица снизу представляет опору, на которой и происходит требуемая деформация листовой заготовки.
Чтобы изготавливать изделия высокой точности и без дефектов, потребуется специальное оборудование, не образующее при воздействии на металл трещин, заусенец, рисок и царапин. При холодной штамповке пуансон должен преодолеть большое сопротивление холодного металла. Таким путём получать изделия сложной формы без дефектов проблематично. Выходом из этой ситуации является горячая штамповка.
Промежуточным этапом между холодной и горячей штамповкой является обработка листового материала давлением или объемная листовая штамповка металла. Заготовка при этом не нагревается предварительно, она также остаётся холодной. Просто движение ползуна с пуансоном происходит в замедленном темпе, а в качестве заготовок используются тонколистовой металл, полоса, лента. При этом способе обработки практически не происходит изменение толщины металлической заготовки, получить же изделия пространственной конфигурации без дефектов вполне возможно. Но для этого требуется применять лишь материалы высокой пластичности, не склонные к деформациям сдвига.
Популярные публикации:
Какой выбрать кузнечный молот?
Технология формовочного литья алюминия своими руками.
Какой купить станок гидроабразивной резки металла?
Покупка оборудования для штамповки
Компании, производящие оборудование для холодной и горячей штамповки металлов, проводят постоянные модификации своих станков с той целью, чтобы оно позволяло получать высококачественные детали и функционировать длительный срок.
К такому оборудованию относятся:
- электрические пресса;
- пневматические пресса;
- гидравлические прессовые устройства.
Продажи производятся непосредственно с сайтов компаний-производителей, где с клиентом предварительно проводятся различные беседы консультационного типа. Большинство этих компаний занимаются изготовлением не только стандартной прессовой техники, но и производят оборудование с учётом требований заказчиков.
Современные гидравлические прессовые станки изготовлены из такого металла, что практически могут создавать деформации любого материала. На сайте производителя клиенту предлагают прессовое оборудование в широкой номенклатуре. Чтобы купить оборудование для листовой штамповки, достаточно оформить свой заказ и произвести предварительную оплату.
Условия доставки заказа в любой регион РФ также нужно обговорить заранее. Компании охотно оказывают транспортные услуги, но уже за дополнительную плату. По дополнительному же договору специалисты поставщика берутся за установку и пуско-наладку поставляемых прессовых устройств. Очень важно при этом не забыть оформить договорённость на гарантийное обслуживание станков, которая предусматривает их бесплатный ремонт в случае выхода из строя в период действия гарантии поставщика.
namillion.com
Штамповочный пресс для металла: устройство и принцип работы
Содержание статьи:
Штамповка — это один из наиболее частых видов обработки металла, который представляет собой деформацию, придающую детали необходимую форму методом выдавливания на поверхности определенного рельефа, узора, отверстий. Процесс этот осуществляется на специальных прессах различной конструкции.
Виды штамповки и оборудования
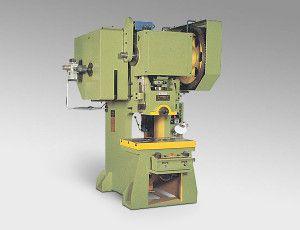
однокривошипный штамповочный пресс
На производстве используются два вида штамповки:
- горячая;
- холодная.
При горячем способе обрабатывается нагретый металл. При этом улучшаются качества материала: он становится плотнее, однороднее. Плюс холодного метода в том, что на поверхности не появляется слой окалины, размеры детали получаются точнее, поверхность глаже.
Штамповка может быть листовой или объемной. Листовым методом производят: посуду, ювелирные изделия, детали часов, климатической техники и микросхем, оружие, медицинское оборудование, детали для автомобиле-, машино- и станкостроения. Полученные детали не требуют дальнейшей обработки. В ходе объемного прессования холодный или раскаленный металл продавливается в формах.
В металлообработке прессы используются для:
- производства поковок;
- запрессовки шестеренок, подшипников;
- объемной и листовой штамповки.
Станки для прессования могут основываться на принципах механики или гидравлики, обрабатывать материалы статическим или ударным способом.
Механические бывают:
- эксцентриковые;
- кривошипными.
Кривошипные станки выполняют холодную и горячую штамповку металла давлением: вытяжку, вырубку и прорубку. Гидравлические прессы используются для объемной кузнечной обработки металла. Согласно технологическим возможностям прессы делятся на: универсальные, специальные и специализированные. Универсальные можно использовать практически для любых видов ковки (пример — гидравлический ковочный станок). Специализированные станки выполняют только один технологический процесс (пример — кривошипные вытяжные). Специальные прессы производят конкретный вид изделий, используя одну технологию.
Принцип работы и устройство прессов различных типов
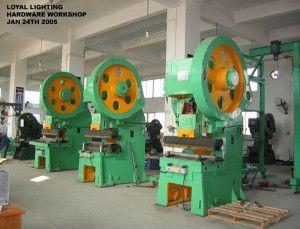
цех по штамповке металла
Любой стандартный штамповочный станок состоит из следующих основных узлов: мотора, передачи, исполнительного механизма. Передача и двигатель вместе составляют «привод». Главная характеристика привода — это вид связи двигателя и исполнительного механизма: механическая или не жесткая (жидкость, газ, пар). Рабочие органы прессов: валки, ползун, траверсы, ролики, бабы.
Кривошипно-шатунный пресс
Привод станка вращается, движение на ползуне преобразуется в возвратно-поступательное. Под действием этого движения при помощи штампа обрабатывается металл. Все детали станка производят из прочной стали и оснащаются ребрами жесткости. Движение ползуна происходит по жесткому графику. Усилие по ползуну достигает 8 тысяч тонн. Кривошипные ковочные установки позволяют ускорить, упростить и удешевить производство деталей, сэкономить до 30% проката. Все кривошипные станки делятся на простые, с двойным и тройным действием.
Кривошипно-шатунный пресс способен выполнять следующие виды работ:
- штамповку в открытых и закрытых матрицах;
- формирование заусенца;
- выдавливание;
- прошивку;
- комбинированную обработку.
Механический пресс воздействует на материал ударом, тогда как гидравлический, прилагая меньшую силу, получает больший эффект. Поэтому вторые используют для изготовления крупных изделий с толстыми стенками.
Гидравлические прессы
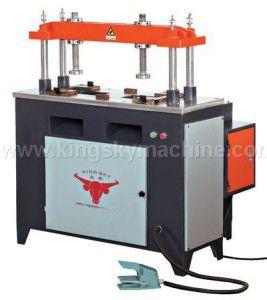
гидравлический пресс
Способны проштамповывать поверхность, продавливать и ковать изделия из металла. Они также применяются для переработки металлических отходов. Действие станка основано на увеличении силы давления на металл во множество раз. Пресс представляет собой два сообщающихся цилиндра с водой, между которыми проходит труба. В цилиндрах установлены поршни. Принцип работы пресса основан на законе Паскаля.
Радиально-ковочный аппарат
Обрабатывает металл горячим способом. Болванка поступает в нагревательный модуль, функционирующий по принципу индукции. Здесь она нагревается, когда металл становится достаточно податливым, подается через конвейер на механизм захвата, подающий заготовку прямо в зону обработки. Ковка или штамповка осуществляется бойками, в процессе заготовка все время крутится, благодаря чему она обрабатывается равномерно со всех сторон. Пресс работает от электромотора, соединенного клиноременной передачей с валами. Они размещены вертикально и направляют движение на шатун и боек, между которыми установлен ползун. Чтобы все движения механизма были синхронными, существуют копирные барабаны. Держатель болванки вращается электромотором посредством червячных передач. Пружинная муфта в нужные моменты притормаживает движение.
Электромагнитный пресс
Это новейшая разработка, которая только начинает использоваться в промышленности. Рабочий орган станка — сердечник электромагнита, который совершает движения под действием электромагнитного поля. Сердечник двигает ползун или штамп, пружины возвращают ползун в исходное положение. Такие станки отличаются высокой производительностью и экономичностью. На сегодняшний день существуют модели с небольшой амплитудой движения рабочего органа — 10 мм и усилием не более 2,5 тонны.
Работа штамповочного станка черновой обработки в видеоролике:
Обзор прессов IPONMAC и их характеристик
Серия модели | KD 23D | HL41 | ПГ41 |
Номинальное усилие, т | 10-80 | 40-315 | 40-315 |
Высота открытия/просвет, мм | 130-280 | 800-1600 | 800-1600 |
Размер стола/нижней плиты, мм | до 520*860 | до 1400*1200 | до 1400*1200 |
Мощность привода, кВт | 1,1-7,5 | 5,5-30 | 5,5-30 |
Масса, кг | 600-5280 | 3000-36000 | 3-36000 |
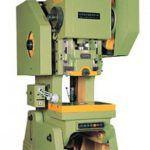
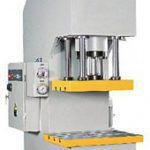
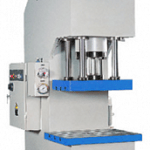
stanokgid.ru