Лаборатория неразрушающего контроля. Неразрушающий контроль металла
Методы контроля качества металлопродукции статья www.Equipnet.ru
Автор: Юлия Рощина, специально для www.EquipNet.ru Фотографии с сайтов nw-technology.ru, avek.ru, syntezndt.ru, mirndt.ru
Основная задача любой системы контроля – выявление дефектов и определение пределов прочности и надежности. Дефекты могут возникнуть в результате ошибки при конструировании, производстве или эксплуатации: дефекты литья, усталостное разрушение, атмосферная коррозия, изнашивание сопряженных деталей, дефекты при нанесении покрытий, дефекты неразъемных соединений металла и так далее. В каждом конкретном случае применяются специальные методики, позволяющие определить степень влияния дефекта на качество изделия: насколько уменьшится надежность, рабочие характеристики, как изменятся сроки и условия эксплуатации, или дефект является критичным и предмет не может быть допущен к использованию. Различают две основные группы испытаний: разрушающего и неразрушающего контроля.
Методы разрушающего контроля
Разрушающий контроль служит для количественного определения максимальной нагрузки на предмет, после которой наступает разрушение. Испытания могут носить разный характер: статические нагрузки позволяют точно измерить силу воздействия на образец и подробно описать процесс деформации. Динамические испытания служат для определения вязкости или хрупкости материала: это разного рода удары, при которых возникают инерционные силы в частях образца и испытательной машины. Испытания на усталость – это многократные нагрузки небольшой силы, вплоть до разрушения. Испытания на твердость служат для измерения силы, с которой более твердое тело (например, алмазный наконечник ударника) внедряется в поверхность образца. Испытания на изнашивание и истирание позволяют определить изменения свойств поверхности материала при длительном воздействии трения. Комплексные испытания позволяют описывать основные конструкционные и технологические свойства материала, регламентировать максимально допустимые нагрузки для изделия.
Для определения характеристик механической прочности используют разрывные машины. Например, WEB 600, производства TIME Group Inc.: она способна развивать усилие 600 кН. Машины для технологических испытаний, такие как ИА 5073-100, ИХ 5133, ИХ 5092 отечественного производства, поставляемые компанией ООО «Северо-Западные Технологии», служат для испытаний на скручивание проволоки, выдавливание листового металла, перегибов проволоки и так далее.
Есть несколько методов определения твердости металла: по Виккерсу, когда в поверхность вдавливается четырехгранная алмазная пирамидка под действием нагрузки в 5, 10, 20, 30, 50 и 100 кгс. Затем отпечаток измеряют по диагоналям квадрата, и по таблице определяют число твердости. Машины для определения твердости – твердомеры. Например ИТ 5010 – машина для определения твердости по Виккерсу.
При исследовании твердости по методу Роквелла, образец плавно нагружают до 98 Н (10 кгс). Затем дается дополнительная нагрузка до максимального значения 490 Н (50 кгс) – 1373 Н (140 кгс). После его достижения на шкале индикатора прибора отображается количество единиц твердости образца. Один из распространенных твердомеров по Роквеллу – ТР 5006 М. Среди машин, предназначенных для испытания на усталость можно назвать МУИ-6000 (поставщик – «Северо-Западные Технологии»).
Методы неразрушающего контроля
Если методы разрушающего контроля применяются только к контрольным образцам, для выяснения общих механических свойств, то неразрушающий контроль служит для массового контроля качества продукции. Работа приборов неразрушающего контроля основывается на принципах изменения свойств предмета при наличии дефектов. Это ультразвуковая дефектоскопия и толщинометрия , радиография , магнитопорошковый и капиллярный контроль, вихретоковый контроль, оптико-визуальный контроль и другие. Например, оборудование ультразвуковой дефектоскопии измеряет разницу в прохождении ультразвука, в зависимости от толщины и плотности металла. Толщиномеры 26МG, 26MG-XT, 26XTDL, 36DLPLUS, производства компании Panametrics служат для определения остаточной толщины стенок труб, котлов и других конструкций, подверженных износу. 36 DL PLUS – современный цифровой эхо-импульсный переносной контактный толщиномер, который позволяет измерять толщину даже тех объектов, к которым можно подойти только с одной стороны. Применяется в энергетике и машиностроении для измерения толщины стенок трубопроводов, сосудов давления, котлов и других объектов.
Один из распространенных методов неразрушающего контроля – вихретоковый. Он основан на измерении возмущений вихревых токов при наведении электрического тока на образец. Даже малейшая трещина или каверна в металле, точечная коррозия или истончение сразу фиксируется в изменении вихревых токов. Современные вихретоковые дефектоскопы служат для контроля посадочных полок дисков колес, ряда крепежных деталей авиационных конструкций, детектирования трещин вблизи крепежных отверстий, а также для отображения С-скана крепежных отверстий, контроля многослойной коррозии в автомобильной, авиационной и аэрокосмической отраслях. Среди оборудования вихретокового контроля можно назвать приборы компании Zetec, которые позволяют выполнять широкий спектр обследований различных конструкций самолетов, узлов двигателей и колес. Например, MIZ®-21SR – многорежимный вихретоковый дефектоскоп и бонд-тестер. Это легкий портативный прибор, использующий два метода вихретоковой дефектоскопии для обнаружения непроклея, расслоения и аномалий плотности. Кроме того, MIZ®-21SR имеет функции измерения проводимости и толщины покрытий. Вся информация отображается на дисплее с высоким разрешением и четкостью изображения.
Рентгеновский контроль
Этот метод обыкновенно используется для дефектоскопии крупных сварных металлических конструкций, подверженных коррозионному воздействию атмосферы: трубопроводов, опор и несущих и любых других металлических конструкций. Рентгеновские аппараты могут быть стационарные (кабельного и моноблочного типа), переносные или монтироваться на кроулеры. Кроулер – самоходный, дистанционно управляемый робот, несущий автономный рентгеновский комплекс. Он предназначен для контроля качества сварных соединений трубопроводов. Такой аппарат по команде извне перемещается в трубопроводе, останавливается и снимает рентгенограмму. Экспонирующее устройство кроулера работает полностью независимо. Одни рентгеновские аппараты требуют экспонирования и проявки специальной пленки, другие отражают информацию сразу в цифровом виде.
Среди аппаратуры рентгеновского контроля нужно назвать продукцию ЗАО «Синтез НДТ», входящую в группу предприятий «ЮНИТЕСТ». Стационарные аппараты серии «Витязь» изготовлены моноблоком, со стеклянной рентгеновской трубкой. Их стоимость относительно невысока. Серия «Бастион» – аппараты кабельного типа, в них используется металлокерамическая трубка, что обеспечивает надежность и длительный срок службы, но они более дороги. Как правило, стационарные аппараты используются для контроля материалов или готовой продукции, они отличаются от переносных высокой стабильностью параметров тока, напряжения и минимумом пульсаций. Переносные рентгеновские аппараты серии «РПД», того же производителя, предусматривают и варианты для работы в тяжелых климатических условиях, на Крайнем севере. В этом случае, блок питания и управления монтируется в металлическом корпусе, категория защиты — IP65. На кроулеры устанавливаются панорамные рентгеновские трубки серии СХТ. Они обеспечивают максимально возможную жесткость спектра излучения с высоким КПД, аппараты питаются от аккумуляторной батареи кроулера. Оборудование СХТ снабжено системой принудительного воздушного охлаждения анодов вентиляторами.
Сегодня не существует одного универсального метода, который позволял бы измерить все свойства металлического изделия разом. Поэтому методы контроля качества применяются в комплексе: на стадиях разработки и изготовления – разрушающие, в процессе эксплуатации – различные неразрушающие. Выбор конкретного способа контроля зависит не только от специфики и назначения металлической конструкции, но и от многочисленных внешних факторов, которые непременно учитываются специалистами.
www.equipnet.ru
Неразрушающий контроль металла
Довольно распространённой ситуацией является необходимость выполнить проверку надёжности, а также рабочих параметров у различных типов объектов или их составных узлов. Классические методы подразумевают необходимость выполнить демонтаж или другое нарушение целостности конструкции.
Такой вариант не всегда считается приемлемым и его удачной альтернативой является использование неразрушающего контроля металла. Отличительной особенностью является возможность выполнения процедур без каких-либо механических повреждений или деформаций.
Особенности неразрушающего контроля металла
Неразрушающий контроль способен эффективно выявить дефекты структуры в металлических конструкциях. Подобные мероприятия необходимо рассмотреть с различных сторон.
Для каких объектов необходимо выполнять НК
Проведение мероприятий по контролю характеристик конструкции без необходимости физического вмешательства может быть использовано в самых разных сферах. Наша компания предлагает подобные работы для следующих типов оборудования и объектов:
- Газовые устройства, а также их детали и составные узлы.
- Внутренние или наружные газопроводы. Части систем газоснабжения объектов и распределения газа.
- Трубопроводы, осуществляющие передачу пара или горячей воды под давлением от 0,07 МПа и выше. Другим условием является температура среды от 115 градусов Цельсия.
- Технические устройства, эксплуатация которых осуществляется на опасных типах объектов.
- Котлы для нагрева воды.
- Сосуды и ёмкости, работа которых выполняется при высокой температуре или давлении от 0,07 МПа.
Выше указаны далеко не все варианты, в которых может быть использован неразрушающий контроль металла. Сферы применения подобной технологии постоянно расширяются, за счёт разработки новых методик осуществления работ. Наша компания оказывает услуги на данном рынке не первый год и способна предложить квалифицированный подход к решению поставленных задач.
Неразрушающий контроль трубопроводов
Обнаружение дефектов трубопроводов без нарушения их целостности, а в некоторых случаях и прекращения работы, является задачей НК. Данный тип конструкций применяется в энергетике, нефтегазовой, а также некоторых других сферах.
Проблемы и дефекты трубопроводов
Неразрушающий контроль труб подразумевает, что изделия будут исследоваться на предмет дефектов. Как правило, они имеют производственно-технологический тип своего происхождения. Под дефектами подразумеваются волосовины, плены внутренние или наружные, бугры, вмятины, неровности внутренней поверхности, раковины, а также ужимы и рванины. Большую проблему может представлять коррозия, поскольку она приводит к резкому снижению характеристик. Неразрушающий контроль трубопроводов имеет дополнительную сферу использования: определение очной толщины стенок.
Типы неразрушающего контроля объектов и оборудования
Процедуры НК, как уже говорилось ранее, способны с высокой точностью выявить различные дефекты в структуре металлов. Для решения поставленных задач могут быть использованы различные методы, основанные на определённых физических процессах. На данный момент, применяются следующие методы:
- Магнитные. Используется в тех случаях, когда материал изготовления ферромагнитен. Учитываются и замеряются параметры коэрцитивной силы, напряжённости, магнитной проницаемости, а также ряд других.
- Электрические. Подобный неразрушающий контроль трубопроводов и других объектов использует электроемкостные, а также электропотенциальные информативные параметры.
- Акустические. Применяются упругие колебания и волны. Замеряется спектр, частота, время и амплитуда колебаний.
- Вихретоковые. Неразрушающий контроль бурильных труб этого типа выполняется при исследовании электропроводящих типов материалов. Информативные параметры: частотные, фазовые, а также амплитудные и спектральные.
- Оптические. На поверхность направляется излучение, а специальный элемент отвечает за сбор его после индуцирования или отражения.
- Тепловые. В подобном случае принято использовать теплометрические и термические параметры. На их основании и выполняется неразрушающий контроль бурильных труб.
- Радиационные. Применяется излучение, испускаемое специальным оборудованием. Анализируется плотность и спектр энергетического потока.
- С использованием проникающих веществ. Диффузия позволяет найти течь за счёт проникновения жидкостей сквозь неё. Для улучшения эффективности можно повысить давление.
Преимущества взаимодействия с нашей компанией
Обеспечение надёжности объектов – это важная задача и доверять её необходимо только квалифицированным специалистам. Наша компания реализует различные неразрушающие методы контроля металлических конструкций с использованием современного оборудования и эффективных методик обработки полученной информации.
Экспертиза промышленной безопасности
www.gorex.ru
Ультразвуковой контроль металла. | | Блог о контроле качества металла
Неразрушающий контроль. Основные методы УЗК.
Ультразвуковой метод исследования качества металлов является одним из основных методов неразрушающего контроля. Принцип контроля заключается в сканировании объекта ультразвуковыми волнами (излучение в объект и прием отраженных волн) с помощью дефектоскопа и пьезоэлектрического преобразователя. Ультразвуковая дефектоскопия помогает определить местонахождение, форму, глубину и объем несплошности внутри изделия. Например, по времени распространения УЗ можно определить расстояние до дефекта, а амплитуда отраженного импульса указывает на ориентировочный размер дефекта.Ультразвуковой контроль проводится разными средствами, в зависимости от конкретных условий. К основным методам неразрушающего контроля с использованием ультразвуковых волн относится – теневой, зеркальный, зеркально – теневой, эхо, дельта — метод.Диапазон волн для металлопромышленного комплекса колеблется от 0,5 МГц до 10 МГц. При необходимости оценить качество сварного шва можно при частоте 20 МГц, это позволяет определять мельчайшие дефекты.Низкие частоты УЗК используют для:• деталей с незначительной толщиной;• отливок и сварочных соединений;• металла с крупнозернистой структурой.Дефектоскопия с использованием ультразвука обладает следующими преимуществами:1. не приносит вреда организму человека;2. быстрота и точность;3. минимальные финансовые расходы;4. мобильность;5. исследование можно поводить на работающем объекте;6. метод не предполагает разрушение испытуемого материала.Основные недостатки УЗК:1. низкая способность определения истинных размеров дефекта;2. исследуя металл с крупнозернистой структурой, наблюдается сильное рассеивание и затухание звука;3. требует предварительной зачистки поверхности;4. необходимость нанесения контактных жидкостей на поверхность для обеспечения стабильного контакта.В сравнении с другими методами, ультразвуковая дефектоскопия является надежным и эффективным методом неразрушающего контроля.
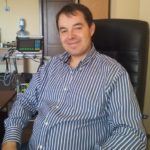
ndt-welding.com
Контроль при помощи лаборатории неразрушающего контроля
Завод металлоконструкций Аполло уже длительное время работает с компанией ООО «Технология», которая имеет "ЛАБОРАТОРИЯ НЕРАЗРУШАЮЩЕГО КОНТРОЛЯ". Работы по контролю осуществляется как на территории ЗМК Аполло, так и за её пределами.
Лаборатория проводит контроль в области промышленной безопасности на производстве, строительстве и является независимой.
Какие используются методы?
Какие виды деятельности?
- проведение неразрушающего контроля при изготовлении, эксплуатации, строительстве, ремонте, монтаже, реконструкции и техническом диагностировании вышеперечисленных объектов.
Какие объекты аттестации?
- Металлические конструкции (в том числе: Стальные конструкции мостов)
Кто осуществляет контроль?
- Контроль осуществляют аттестованные сотрудники, имеющие «Квалификационные удостоверения» и допущенные в качестве специалистов неразрушающего контроля.
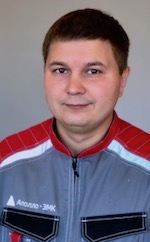
Подмарёв Сергей
Руководитель Лаборатории неразрушающего контроля
Подмарёв Сергей Александрович
+7 (987) 989-42-72 [email protected]
Какой используется инструмент?
- Набор ВИК
- Дефектоскоп ультразвуковой А1212 «MASTER»
- Рентгенографический дефектоскоп
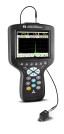
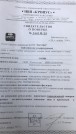
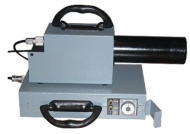
Какой будет результат?
По результатам работы лаборатории выдаётся ЗАКЛЮЧЕНИЕ, которое подтверждает качество сварных соединений.
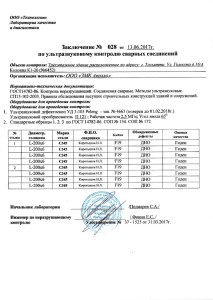
Заключение по УЗК
- Согласно ГОСТ 14782-86. Контроль неразрушающий. Соединения сварные. Методы ультразвуковые.
- СП13-102-2003. Правила обследованиянесущих строительных конструкций зданий и сооружений.
Данное ЗАКЛЮЧЕНИЕ прикладывается к исполнительной документации проекта и подтвержает качество продукции.
〉Визуально-измерительный контроль
Этот метод самый дешевый, быстрый и наиболее информативный. Он базовый и предшествует всем остальным методам неразрушающего контроля.
При внешнем осмотре можно проверить качество подготовки к сборке заготовок перед сваркой, качество сварных швов.
Дефекты.
- выявление вмятин
- подрезов
- заусенцев
- ржавчины
- прожоги
- наплывы и другие видимые дефекты
Нормативы.
Визуальный и измерительный контроль можно провести при помощи простых инструментов, но несмотря на простоту, необходим основательный подход. Предусматривается разработка технологической карты, в которой изложены наиболее рациональные способы и последовательность работ.
Контроль ВИК регламентируется инструкцией по визуальному и измерительному контролю РД 03-606-03. В которой содержатся требования к квалификации персонала, регистрации результатов, средствам контроля, процессу контроля и способам оценки.
Инструменты.
в стандартный набор ВИК входит
- шаблоны сварщика
- угольник
- штангенциркуль
- фонарик
- маркер по металлу
- лупа измерительная
- термостойкий мел
- набор щупов
- рулетка
- линейка
- зеркало с ручкой
- набору радиусов и др.
Процесс.
- Сначала проверяем заготовки перед сборкой. Не должно быть заусенцев, вмятин, окалины, ржавчины и т.д.
- Проверяем качество кромок под сварку — притупление кромок и угол их разделки, для соединений с разделкой кромок и тавровых соединений.
- Замеряем зазор между кромками для стыковых и угловых соединений, ширину нахлёстки и зазор между листами — для нахлёсточных соединений
- Собранные под сварку детали узлы с отклонениями от технических условий подвергаются исправлению
- Далее наблюдаем за процессом сварки. Следим за режимами сварки (напряжение, ток, скорость подачи), стабильностью горения дуги, за правильностью выполнения валиков в многослойных швах. Особенно тщательно смотрим на первый слой, при помощи лупы.
- Далее осматриваем готовые изделия. Невооружённым глазом или с лупой выявляем дефекты швов — трещины, подрезы, свищи, прожоги, непровары. Также смотрим на форму шва — распределение чешуек и общее распределение металла в усилении шва.
- Сварные швы сравниваем с эталонами или используем специальные шаблоны.
- Результаты измерений заносим в журнал и при необходимости отправляем изделие на доработку
Внешний вид поверхности шва характерен для каждого способа сварки, а также для пространственного положения, в котором выполнялась сварка. Равномерность чешуек характеризует работу сварщика, его умение поддерживать постоянную длину дуги и равномерную скорость сварки. Неравномерность чешуек, разная ширина и высота шва указывают на колебание мощности дуги, частые обрывы и неустойчивость горения дуги в процессе сварки. В таком шве возможны непровары, поры, шлаки и другие дефекты. При сварке в вертикальном и потолочном положениях сварные швы имеют резко выраженную Неравномерность чешуек, бугры, седловины и наплывы. При сварке в защитных газах в вакууме внешняя поверхность швов гладкая, блестящая, без чешуек и имеет вид полоски расплавленного металла.
〉Ультразвуковая дефектоскопияДиагностика сварных швов при помощи ультразвука (УЗК) — это неразрушающий целостности сварных соединений метод контроля и поиска скрытых дефектов. УЗК эффективен при поиске воздушных пустот, неоднородности химического состава (шлаковые включения) и обнаружение неметаллических элементов.
Впервые УЗК проведен в 1930 году — метод не новый. Но очень популярный и используется повсеместно.
Теория.
Волну ультразвука — нельзя услышать ухом человека, но это и является основой для многих диагностических методов. Многие диагностические отрасли используют проникновение и отражение звука. Особенно где не допустимо нанесение вреда человеку.
Многие факторы влияют на качество проведения УЗК:
- чуствительность приборов
- настройка и калибровка дефектоскопа
- выбор более подходящего метода, в зависимости от опыта оператора
Контроль швов (ГОСТ 14782-86) и допуск в эксплуатацию не возможен без устранения дефектов.
Дефекты.
- поры
- трещины в околошовной зоне
- расслоение наплавленного металла
- непровары шва
- провисание металла в нижней зоне сварного шва
- дефекты свищеобразного характера
- несплошности и несплавления шва
- зоны поражённые короззией
- участки с искажением геометрического размера
- участки с несоответствием химического состава
Принцип работы.
Технология основана на способности высокочостытных колебаний проникать в металл и отражаться от поверхности пустот, неровностей, коррозии и других включений в основном металле. Созданная звуковая волна проникает в соединение и в случае дефекта отклоняется от своего нормального распространения. Это видно на приборе и оператор делает заключение по выявленному дефекту. так можно определить, например:
- относительный размер дефекта — по амплитуде отражённого импульса
- расстояние до дефекта — по времени распространения ультразвуковой волны в металле
Процесс проведения УЗК.
- Сначала удаляется краска и ржавчина в околошовной зоне, не менне 100 мм, с каждой стороны
- Затем поверхность металла и сам шов обрабатывается солидолом или глицерином, для более точного результата
- Настраиваем прибор по стандарту, в зависимости от задачи УЗК
- Проверяем: толщины до 20 мм — стандартные настройки (зарубки), свыше 20 мм — настраиваются АРД-диаграммы.
- Продольно-поперечными движениями перемещаем пьезоэлектрический преобразователь (ПЭП) относительно сварного шва и стараемся повернуть вокруг оси на 10-150.
- После появления устойчивого сигнала, ПЭП поворачиваем в зону максимальной амплитуды
- Но смотрим не является ли это колебание следствием отражения от самого шва (такое часто бывает)
- Если нет, то фиксируем дефект и записываем результат
- Контролируем параметры по ГОСТу
- Все результаты заносим в таблицу для удобства поиска и устранения дефектов
Предназначена для выявления скрытых дефектов в сварных соединениях.
Принцип.
Основан на поглощении рентгеновских лучей, зависящих от плотности среды и атомного набора элементов, образующих материал среды. Наличие дефектов приводит к тому что лучи, проходящие через металл, ослабляются в разной степени. И наблюдая за распределением интенсивности проходящих лучей, можно определить расположение и наличие неоднородностей металла.
Преимущества.
- Наряду с возможностью определять основные дефекты сварных швов, можно увидеть, что не покажет ни один другой метод — например, непропаи, раковины, и другие.
- Есть возможность определить точное место обнаруженного дефекта, что дает возможность быстрого ремонта
- Результаты проверки можно наглядно представить на рентгеновской плёнке
Инструмент.
Прибор состоит из рентгеновской трубки в защитном кожухе, высоковольтного генератора, пульта и кабели. Пульт управления состоит из трансформатора, регулятора напряжения и тока, измерительных приборов и сигнальной системы управления.
Высоковольтный генератор состоит из трансформатора накала трубки, выпрямителя и высоковольтного трансформатора.
Источник излучения (ренгеновский аппарат) подбирается в зависимости от толщины контролируемого металла и необходимой чувствительности. И для получения четкой проекции источник должен иметь малый размер фокусного пятна и находиться на достаточном расстоянии от изделия.
Дефекты.
Минимальный размер дефекта зависит от формы и местонахождения.
Лучше всего выявляются дефекты, имеющие протяженность вдоль пучка проникающего излучения. Такие изображения дефектов получаются более резкими чем криволинейные дефекты. Ну а если дефект находится под углом к направлению просвечивания, то чувствительность ухудшается и зависит от величины раскрытия дефекта и угла между направлением просвечивания и направлением дефекта. В следствии экспериментов установлено, что дефекты с малым раскрытием (трещины) не выявляются, если угол пучка излучения по отношению к оси трещины больше 7 градусов.
Допустимые размеры указываются в чертежах и технических условиях. Если нет, то следует руководствоваться ГОСТ 23055-78 «Контроль неразрушающий. Сварка металлов наплавлением. Классификация сварных соединений по результатам радиографического контроля».
apollo-zmk.ru
Неразрушающие методы контроля | Дефектоскопия
Неразрушающие методы контроля позволяют проверять качество поковок и деталей (на отсутствие наружных и внутренних дефектов) без нарушения их целостности и могут быть использованы в сплошном контроле. К таким методам контроля относятся рентгено- и гамма-дефектоскопия, а также ультразвуковая, магнитная, капиллярная и другие виды дефектоскопии.
Рентгенодефектоскопия
Рентгенодефектоскопия основана на способности рентгеновского излучения проходить через толщу материала и поглощаться последним в различной степени в зависимости от его плотности. Излучение, источником которого является рентгеновская трубка, направляют через контролируемую поковку на чувствительную фотопластинку или светящийся экран. Если в поковке имеется дефектное место (например, трещина), излучение, проходящее через него, поглощается слабее, а фотопленка засвечивается сильнее. Регулируя интенсивность рентгеновского излучения, получают изображение в виде ровного светлого фона в бездефектных местах поковки и отличительного темного участка - в месте нахождения дефекта.
Выпускаемые промышленностью рентгеновские установки позволяют просвечивать стальные поковки толщиной до 120 мм, а поковки из легких сплавов - до 250 мм.
Гамма-дефектоскопия
Контроль поковок гамма-дефектоскопией аналогичен контролю рент- генодефектоскопией. На определенном расстоянии от исследуемого объекта устанавливают источник гамма-излучения, например капсулу с радиоактивным кобальтом-60, а с противоположной стороны объекта - устройство для регистрации интенсивности излучения. На индикаторе интенсивности (фотопленке) проявляются дефектные участки, имеющиеся внутри заготовки или поковки. Толщина контролируемых заготовок (поковок, деталей) достигает 300 .. .500 мм.
Во избежание облучения при использовании в качестве методов контроля рентгено- и гамма- дефектоскопии необходимо строго соблюдать требования безопасности и быть предельно осторожным.
Рис. 9.7. Установка для ультразукового контроля металла: 1 - осциллограф, 2, 3, 4 - световые импульсы, 5 - блок, 6 -головка, 7 - поковка, 8 - дефект
Ультразвуковая дефектоскопия
Ультразвуковая дефектоскопия является наиболее распространенным методом контроля, позволяющим проверять поковки толщиной до 1 м. Установка для ультразвукового контроля эхо-методом (рис. 9.7) состоит из искательной головки 6 и блока 5, в котором размещены генератор ультразвуковых электрических колебаний (частота свыше 20 кГц) и осциллограф 1. Головка 6 представляет собой пьезоэлектрический преобразователь электрических колебаний в механические.
С помощью искательной головки на исследуемый участок поковки 7 направляют импульс ультразвуковых колебаний, который отразится сначала от поверхности поковки, затем ( с некоторым опозданием) - от дефекта 8 и еще позже - от донной поверхности объекта. Отраженный импульс (эхо) вызывает колебание пьезокристалла искательной головки, который преобразует механические колебания в электрические.
Электрический сигнал усиливается в приемнике и регистрируется на экране осциллографа 1: расстояние между импульсами 2,3 и 4 определяет глубину нахождения дефекта, а форма кривых - величину и характер последнего.
Магнитная дефектоскопия
Наиболее распространенным видом магнитной дефектоскопии является магнитно-порошковый метод, применяемый для контроля магнитных сплавов железа, никеля и кобальта. Стальную деталь намагничивают электромагнитом, а затем покрывают суспензией из керосина и магнитного порошка. В местах наличия дефекта частицы магнитного порошка скапливаются, копируя форму и размеры не только поверхностных трещин, но и дефектов, расположенных на глубине до 6мм.
Магнитно-порошковый метод позволяет выявить крупные и очень мелкие дефекты шириной 0,001 ...0,03 и глубиной до 0,01 ... 0,04 мм.
Капиллярная дефектоскопия основана на свойстве жидкостей под действием капиллярных сил заполнять полости поверхностных дефектов (трещин). Используемые для контроля жидкости либо обладают способностью люминесцировать под действием ультрафиолетового излучения (люминесцентная дефектоскопия), либо имеют окраску, четко выделяющуюся на общем фоне поверхности. Например, при люминесцентной дефектоскопии поковки погружают в раствор минерального масла в керосине, промывают, просушивают, а затем опыляют порошком оксида магния. Если осматривать невооруженным глазом такую поверхность при свете ртутной лампы, на фоне темно-фиолетовой поверхности поковки ясно видны ярко-белые трещины. Метод позволяет определять наличие трещин шириной от 1 до 400 мкм.
Похожие материалы
www.metalcutting.ru