Электроды, применяемые для роликовой сварки. Роликовая сварка
Точечная сварка. Роликовая сварка. Рельефная сварка. История развития
Рекомендуем приобрести:
Установки для автоматической сварки продольных швов обечаек - в наличии на складе! Высокая производительность, удобство, простота в управлении и надежность в эксплуатации.
Сварочные экраны и защитные шторки - в наличии на складе! Защита от излучения при сварке и резке. Большой выбор. Доставка по всей России!
Нагрев места стыка двух деталей проходящим через них электрическим током характерен для всех способов контактной сварки. Вторым существенным признаком этого вида сварки является обязательное приложение усилия сжатия контактируемых деталей. По характеру приложения такого усилия и типа соединения различают стыковую, точечную, шовную (роликовую) сварку и другие способы. Э. Томсон и его коллеги в США разрабатывали технологию стыковой контактной сварки и не пытались изменить характер приложения силы и форму соединения, несмотря на то, что прототипом нового способа контактной сварки мог послужить самый распространенный в XIX в. вид неразъемного соединения — клепка.
Неизвестно, когда и при каких обстоятельствах пришел Н. Н. Бенардос к принципу точечной контактной сварки. Первый в мире патент на этот способ (и «прибор» для его реализации) был выдан на его имя в Германии: № 46776—49 от 21.01.1888 г. В качестве электродов служили графитовые бруски, вставляемые в клещи, которые сжимали вручную (рис. 33).
В заявке на изобретение, поданной в России, Бенардос подробно описывает технологию и предлагает несколько устройств для точечной сварки. Так, один из «приборов» выполняли в виде стойки, на которой укрепляли изолированно друг от друга кронштейны: нижний жестко, а верхний — на шарнире (рис. 34).
На концах кронштейнов, к которым подавали напряжение, крепили электроды из угля или другого электропроводного «огнеупорного тела, соответственно для этого подготовленного» [20]. Свариваемые заготовки собирали встык или со скосом кромок и заводили между электродами. При этом верхний кронштейн поднимался. Перед началом сварки этот кронштейн с электродом прижимали грузом. По мере разогревания кромок до пластического состояния или до подплавления изделие передвигали, и вслед за нагревом производилось обжатие роликами.
Точечная сварка продолжала развиваться. Спустя 10 лет О. Кляйншмидт заменил угольные электроды в «приборах» Бенардоса медными электродами и усовершенствовал устройство для сварки, встроив трансформатор в клещи (рис. 35).
На разработку был выдан патент США № 616463 от 20.12.1898 г. С этого времени точечная сварка вышла из стадии лабораторных экспериментов, и началась работа над повышением производительности процесса. Бушайе разработал конструкции «дуплекс-электродов» для выполнения сразу двух сварных точек (пат. Франции № 330200 от 13.03.1903 г.). Верхний и нижний электродные узлы имели собственные трансформаторы. При параллельном подключении обмоток трансформаторов получается только одна точка, при последовательном включении — сразу две.
Оптимальную конструкцию электродов разработал Харматта (патент США № 1046066 от 3.12.1912 г.). Тейлор предложил перекрестный процесс нагрева места сварки таким образом (рис. 36), чтобы ток проходил по диагонали между двумя разделенными на части электродами (пат. США № 1243004 от 16.10.1917 г.).
Одновременно отрабатывали оптимальную конструкцию узлов, механические и электрические схемы машин для точечной сварки (рис. 37). Были разработаны машины с качающимся плечом-хоботом, мощные стационарные и легкие переносные машины, клещи разных конструкций.
В конце XIX в. точечную сварку использовали для приварки ручек к кастрюлям и сковородкам, для изготовления других неответственных изделий, заменяя клепку, а иногда — пайку. Однако это малозаметное применение убедительно доказало, что точечная сварка намного производительнее клепки и что пригодна она для соединения многих металлов. Точечную сварку начали широко использовать в США в 1914 г., когда в автомобильной промышленности клепка была заменена приваркой листовых элементов автомобилей (крыльев, обшивки кузова, деталей шасси). Мощность установок колебалась в пределах 5—35 кВ А. Установки имели ручное или ножное управление. К 1923 г. стационарные точечные машины позволяли сваривать до 200 точек в минуту. Использование новой технологии в массовом производстве создало возможность дальнейшего развития процесса сварки, совершенствования сварочного оборудования и даже создания новых способов сварки, таких как рельефная и роликовая. Идея рельефной сварки возникла благодаря многократному появлению «ошибочных» соединений, которые выполняли в спешке неквалифицированные рабочие. В 1918 г. Гамильтон и Оберег обратили внимание на преимущества приварки деталей сразу в нескольких местах на заранее отштампованных выступах и разработали промышленную технологию рельефной сварки.
В процессе изготовления изделий цилиндрической формы часто нижний опорный электрод выполняли в виде ролика, вращающегося вместе с изделием при установке в требуемое положение, а верхний — в виде короткого цилиндрического стержня. На таких машинах осуществляли точечные соединения, они же послужили прототипом машин для шовной сварки, когда свариваемые детали проходят между двумя роликами, нагреваются мощными импульсами тока, в результате чего образуется шов из отдельных перекрывающихся точек.
В 1905 г. Снурек и Гислер предложили схему многоэлектродной точечной сварки [110]. Однако только в 1924 г. была разработана конструкция соответствующих машин, которые были применены при сборке корпусов автомобилей на заводе Форда.
В 1910 г. Джевонсом был изобретен способ контактной сварки, заключающийся в том, что между свариваемыми кромками помещали небольшие пластинки (закладки), в которых и концентрировалась теплота. Эта технология была достаточно сложной. С целью ее упрощения как при точечной, так и при шовной сварке вместо закладок были предложены тонкие полоски (ленты), которые сматывали с катушек и подавали сверху и снизу изделия (рис. 38).
В 1930 г. на верфях Германии были внедрены машины с двумя электродами и двумя трансформаторами фирмы «Оттенземер Айзенверке». Затем в короткое время различными фирмами в США и Европе были разработаны схемы многоточечной сварки — с несколькими постепенно включаемыми электродами; с одновременным включением в симметричном и несимметричном исполнении; с трансформаторами, имеющими двойную вторичную обмотку; с трансформаторами, расположенными с противоположных сторон и др. Многоэлектродными машинами можно было одновременно или почти одновременно выполнять несколько сварных точек, полностью сваривать изделие (например, узел автомобиля), не перемещая элементы и электроды до окончания процесса [111, 112].
Для многоточечной сварки были разработаны два типа машин — многоцелевые машины и сварочные прессы [113, 114]. Первые были снабжены перемещающимся столом, их использовали для сварки различных изделий; вторые применяли для сварки строго определенных изделий, когда положение электродов и опорных поверхностей было фиксированным. В 30-е годы были решены многие технические проблемы; обоснованы расстояние между электродами и расположение трансформаторов, разработаны системы подвода тока, выбрано оптимальное количество одновременно свариваемых точек, установлена последовательность постановки точек и т. д. Особое внимание было уделено конструкции электродов и системам регулирования процесса сварки.
Кляйншмидт, заменив угольные электроды Бенардоса медными, обеспечил точечной сварке практическое применение. Электролитическая медь обладает большой тепло- и электропроводностью, а при механической обработке (протяжке) — удовлетворительной твердостью. Однако в результате нагрева в процессе эксплуатации прочность меди падает. Начиная с 1915 г., поиск материала для электродов велся в двух направлениях: электролитическую медь легировали с целью придания ей твердости, добиваясь при этом незначительного снижения электропроводности; повышали электро- и теплопроводность сплавов на другой основе, добавляя медь. В 1925 г. были разработаны «псевдосплавы», названные «элколит», «элмет», «моллори» и т. п., получаемые путем спекания при высоких давлениях и температурах порошков вольфрама, покрытых медью [115]. Поскольку проводимость этого материала была ниже, чем чистой меди, из него выполняли только наконечники, которые припаивали к охлаждаемому полому стержню. В машинах для шовной сварки вольфрам медную ленту припаивали в виде обода к торцу роликов, Однако паяная конструкция стоила дорого, и, кроме того, всегда существовала опасность плохого контакта в месте соединения из-за неточной сборки и дефектов пайки.
В результате поиска достаточно прочных материалов с хорошей электро- и теплопроводностью были подобраны элементы, способные образовывать твердый раствор с медью (кобальт, хром, кадмий, бериллий и молибден) при их содержании не более 1%. Из этих сплавов начали изготавливать цельнометаллические электроды и ролики.
Серьезным недостатком первых машин для контактной сварки, особенно шовных, являлся большой расход энергии — «лишний» нагрев зоны сварки происходил из-за длительного воздействия сравнительно небольшой силы тока. В 1920 г. было предложено осуществлять подачу токов большой силы, и в машинах установили реле времени. Роликам придавалось прерывистое вращательное движение через фрикционную муфту и стопорный механизм. Для уменьшения силы тока в период перемещения изделия во вторичный контур сварочного трансформатора включался элемент индуктивности. Сердечник индуктивной катушки был связан с роликами и перемещался при их движении, возвращаясь в исходное положение с помощью пружины. Однако вскоре обнаружили, что чем больше сила сварочного тока, тем меньше точность регулирования длительности импульса. Поэтому пришлось заниматься совершенствованием системы управления.
Регулирование параметров тока и длительности сварки являются важными составляющими технологии, а аппаратура управления — существенной частью сварочных машин. В аппаратах Томсона в первичной обмотке трансформаторов находились отводы, переключением которых регулировалось напряжение во вторичной обмотке, как правило, состоявшей из одного витка. Продолжительность прохождения сварочного тока контролировалась электромагнитной системой, содержащей конденсатор, питаемый от резистора и включенный параллельно обмотке соленоида. В 1924 г. в схему была включена неоновая лампа, благодаря чему ток мог проходить через систему только при напряжении строго определенного уровня.
В 1932 г. в США в контактных машинах появилась система управления, основанная на тиратронах. Эта система нашла применение на машинах средней мощности (до нескольких кВ А), однако при их эксплуатации обнаружились серьезные недостатки, в частности, плохо работали прерыватели.
В 1934 г., практически с момента появления в США игнитронно-ртутных вентилей со вспомогательным (поджигающим) электродом, управляющим зажиганием основного дугового разряда, их стали использовать в сварочных машинах. В последующие годы система управления контактными машинами, основанная на игнитронах, совершенствовалась. Были разработаны схемы управления игнитронами, в которых использовали достижения электронной техники и применяли вспомогательные элементы (стабилизаторы, усилители и т. д.), а также элементы защиты.
В 1930-х гг. продолжали работать над проблемой перегрузки сетей однофазными машинами, что вызывало колебания напряжения. Одно из решений этой проблемы было найдено в 1941 г. братьями Марио и Давидом Сиаки: оно основывалось на применении трехфазных источников с выпрямителями [116].
К концу 1930-х гг. конструкция (узлы, компоновка, архитектоника) контактных машин претерпела серьезные изменения по сравнению с исходными образцами. Первые машины часто выполняли, кроме прочих действий, проковку или обкатку, и в некоторых из них были предусмотрены механические командоаппараты в виде валов с кулачками. Производительность машин во многом зависела от быстродействия систем захвата и сжатия свариваемых деталей. В поисках оптимальных конструкций были опробованы гидравлические, пневматические и электромагнитные системы.
В конце XIX в. машины для стыковой сварки представляли собой сравнительно простое устройство с электрическим и механическим узлами, управление работой которых осуществляли педалью (рис. 39, а, б).
Первые устройства для точечной сварки имели вид клещей. Через два-три десятилетия были созданы несколько десятков различных по назначению универсальных и специализированных машин, а по размерам — от огромных формовочных станов для производства труб и изготовления автомобилей до подвесных и переносных клещей.
Серьезной проблемой в развитии контактной точечной сварки явилось создание клещей, отличающихся высокой маневренностью, легкостью и быстродействием. В первое десятилетие XX в. в таких подвижных сварочных постах генераторы тока конструктивно отделялись от механических, пневматических или гидравлических устройств для позиционирования и сжатия. Длина кабеляи шланга водяного охлаждения составляла 2—3 м, и, учитывая потери, приходилось повышать напряжение вторичной обмотки сварочного трансформатора, а следовательно, его мощность и габаритные размеры.
Следующим этапом было создание клещей с трансформатором, вмонтированным в подвижную конструкцию. Возникли новые проблемы — необходимость уменьшения габаритных размеров трансформатора, увеличения удельной мощности, минимизации потерь, С этой целью были применены трансформаторы с броневой магнитной системой, в которых первичная и вторичная обмотки были навиты и защищены магнитной цепью, выполненной из листов кремнистой стали с ориентированными кристаллами. Первичную обмотку выполняли из медной проволоки, а вторичную — из литой меди с припаянными трубками-каналами для охлаждающей воды. В подвесных трансформаторах первичные обмотки чередовались с витками вторичной обмотки, что увеличило удельную мощность до 0,7—1 кВА/кг [117].
Первая технология стыковой сварки труб, разработанная в 1902 г. Э. Томсоном и получившая название «прямошовный» метод, по способу приложения давления была сходна с кузнечно-прессовой сваркой. В цельносварных трубах были заинтересованы многие отрасли промышленности и строительства. Технология их изготовления и соответствующее оборудование продолжали совершенствоваться. За два десятка лет были предприняты попытки использовать для производства труб все известные способы контактной сварки. В 30-х гг. фирма «А. О. Смит» разработала технологию сварки оплавлением и внедрила ее в производство труб с толщиной стенки 5 мм и диаметром 500 мм, которые сваривались по всей длине (12 м) на машинах мощностью 5000 кВА.
В контактной сварке использовали ток промышленной частоты до тех пор, пока в 1939 г. фирма «Бабкок энд Вилько Ко» не применила ток частотой 200—350 Гц, Трубы из полосового проката сваривали машинами с вращающимся трансформатором. Однако это еще не был процесс, основанный на индукционном нагреве токами, открытыми Фуко, и теоретически исследованный в 1884 г, Хевисотдом. Впервые на практике это явление использовал в 1891 г. Э. Томсон, осуществивший индукционный нагрев листового железа. В 1900 г. была пущена в эксплуатацию индукционная плавильная печь Челлина. Началом развития процессов высокочастотной сварки считается разработка фирмой «Лоррен-Эско» в 1928 г. процесса (пат. Франции № 922431), в котором индуцированный ток концентрировался в зоне сварки ферритным сердечником. Однако основное развитие сварка токами высокой частоты получила после 1940-х гг.
Много общих существенных признаков с контактной сваркой имеет и конденсаторная сварка, идея которой возникла благодаря случаю. В 1905 г. сотрудник фирмы «Вестингауз Электрик» Л. В, Чабб, экспериментируя с электрическими конденсаторами, обнаружил, что проволока приваривается к алюминиевой пластине при прохождении через них разряда накопленного электричества [118]. Это наблюдение позволило сделать определенные выводы: разряд разрушил прочную оксидную пленку, затрудняющую пайку, и поэтому появилась возможность получить прочное соединение алюминиевых проводов. Конденсаторную сварку сразу же стали применять в электротехнике (приварка серебряных, вольфрамовых и других контактов, соединение алюминиевых и медных проводов), в ювелирном деле (приварка золотых и платиновых булавок и проволочек).
Как уже отмечалось, стыковая сварка нашла применение почти сразу после создания Томсоном первых образцов машин, Сначала это было изготовление проводов для электротехнических целей, затем — производство труб и различных стержней и, наконец, наиболее эффективное применение — производство вооружения в США, в частности, снарядов в годы Первой мировой войны. В Европе в это время наиболее активно развивала и внедряла контактную сварку немецкая фирма «Альгемайне Электрише Гаэельшафт» (АЭГ). Кроме «чисто» контактных машин, эта фирма в 1930-х гг. разрабатывала и выпускала машины для приварки шпилек.
Контактная сварка нашла применение в самолетостроении уже в 1908 г., вскоре после того, как в ряде стран было решено использовать для основных узлов самолетов металл. При изготовлении стальных ланжеронов, стоек, раскосов, элеронов и т. д, применяли точечную и роликовую сварку. В 1928 г. фирма «Форд Мотор» внедрила контактную сварку для ответственных узлов самолетов из дюралюминия. В начале 1930 г. были проведены статические и усталостные испытания на натурных образцах и моделях, подтвердившие возможность применения контактной сварки алюминиевых конструкций. В США с 1935 г. ее начали использовать фирмы «Боинг», «Дуглас» и «Сикорски», почти одновременно в Европе — фирмы «Фиат» вместе с «КантьериАэронавтика д'Италия», выпустившие первый металлический итальянский самолет [119, 120].
Особенно широкое применение все способы контактной сварки находят в автомобилестроении.
Г. Форду принадлежит особая роль в развитии контактной сварки. Его заказы были стимулом для усовершенствования технологии и оборудования. В свою очередь сварка обеспечила высокие темпы производства автомобилей. В первые годы на заводах Форда выпускали до 3000 автомобилей в год, а в 1909 г. их количество достигло 10 тыс. в основном благодаря применению стыковой и точечной сварки вместо клепки.
К началу 1928 г. на заводах компании «Форд Мотор» было 320 машин для сварки оплавлением, 540 машин для точечной сварки и 25 машин для роликовой сварки. В 1928 г. на автомобиле модели «Форд-А» насчитывалось около 1300 сварных точек, на модели 1932 г. их количество составило 2000 шт. Соединение всех штампованных деталей корпуса, крепящихся к шасси, осуществлялось точечной и роликовой сваркой. В следующем году технология была усовершенствована — днище и две боковые стенки сваривали за одну операцию на машинах с двумя трансформаторами (мощностью по 250 кВ А) менее чем за 60 с, причем чистое сварочное время составляло менее 10 с. В конечном итоге развитие оборудования для точечной сварки пошло по двум направлениям — создание клещей (подвижных сварочных постов) и создание многоточечных машин (контактных машин-прессов). Также были усовершенствованы и машины для роликовой сварки.
Развитие контактной сварки в СССР также стимулировалось интенсивным ростом автомобилестроения. Нижегородский (Горьковский) автомобильный завод был спроектирован и оснащен в основном оборудованием фирмы «Форд» и, в меньшей степени, установками нескольких германских фирм. Разнообразные машины для контактной сварки, поставленные Советскому Союзу из США, а также обученный американскими специалистами инженерно-технический персонал определили направления развития Контактной сварки в СССР [121].
Развитию и внедрению высоких технологий придавалось большое значение. С середины 1930-х гг. оборудование контактной сварки, разработанное и выпускаемое заводом «Электрик» им. А. К. Скороходова, применялось на уже работающих и строящихся заводах страны. Так, на стыковых машинах АСН —25 на строительстве Уралвагонзавода в месяц сваривалось до 500 т арматурной стали.
В 1934 г. на заводе «Электрик» были также разработаны машины АС—75 и АС—100 для стыковой сварки непрерывным оплавлением, специальные роликовые машины АШ—25 для сварки продольных швов, АШ—16 для сварки поперечных швов и фланцев, аппараты для точечной сварки AT-50—1, прессы для рельефной сварки.
Кроме производства автомобилей, с применением точечной контактной сварки для прикрепления обшивки к каркасу начали выпускать цельнометаллические пассажирские вагоны. Опыт, полученный при пуске первых автомобильных и тракторных заводов, послужил толчком к организации выпуска мощных отечественных контактных машин улучшенной конструкции и одновременно способствовал освоению ряда относительно новых технологических процессов — рельефной сварки при изготовлении тормозных колодок и колес, шовностыковой сварки труб из непрерывно сворачиваемой стальной ленты, точечной и шовной сварки стальных деталей с гальваническим покрытием и т. д.
С применением контактной сварки из коррозионно-стойкой стали были изготовлены самолеты, дирижабли, скульптурная группа В. И. Мухиной «Рабочий и колхозница». Основные работы были выполнены в лаборатории акционерного общества «Оргаметалл» (впоследствии ЦНИИТМАШ) Я. М. Глуховым, П. Н. Львовым, В. И. Коровиным, в Институте гражданского воздушного флота С. М. Поповым и др. В конце 30-х гг. в СССР было начато освоение стыковой сварки железнодорожных рельсов (ЦНИИТМАШ совместно с научно-исследовательскими организациями Наркомата путей сообщения и др.).
www.autowelding.ru
Электроды, применяемые для роликовой сварки » Портал инженера
![]() |
Рис. 1. Различная форма рабочей поверхности роликов
Охлаждение роликов может быть естественным (воздушным), от охлаждаемой оси и искусственным (водяным), а также комбинированным. Охлаждение массивных роликов большого диаметра при сварке стали с небольшой скоростью и частых перерывах между операциями может быть естественным. При большой величине тока и значительной толщине свариваемых деталей применяют водяное охлаждение роликов. Наиболее простым является наружное водяное охлаждение роликов и зоны сварки. При таком способе используются ролики простой конструкции. Наружное охлаждение применяют в том случае, если назначение узла допускает попадание в него влаги, а металл является достаточно стойким в коррозионном отношении.
В большинстве сварочных машин применяют внутреннее водяное охлаждение оси, через которую отводится тепло от ролика. Более эффективным является внутреннее охлаждение роликов, но оно требует установки уплотняющей прокладки между осью и торцом ролика. Конструкция ролика с внутренним охлаждением показана на рис. 2, а. Вода поступает из оси по каналам в теле ролика 1 в кольцевую проточку. Существенной трудностью при изготовлении такого ролика является герметизация проточки кольцом 2. Кольцо может быть соединено с роликом 1 с помощью пайки; при этом следует применять припои, температура плавления которых меньше, чем температура начала разупрочнения металла ролика. Крепление кольца может быть выполнено на винтах с герметизирующей прокладкой. На рис. 2, б приведена конструкция ролика с внутренним охлаждением для машин типа МШП. Ролик 1 закреплен на валу 2 с помощью резьбовых шпилек 4 с гайками, которые прижимают к наружному торцу ролика диск 5. Вода поступает по трубке.3 во внутреннюю полость диска 5 и затем по радиальным каналам 6 подходит к торцу ролика и, омывая его, по каналам 7 подается в полость вала 2, Резиновые кольцевые уплотнения исключают попадание воды на свариваемые детали.
В настоящее время посадочные части роликов наиболее распространенных конструкций выполняются по нормали МН 113—60. Установлено три исполнения роликов:
1) с посадочным отверстием диаметром 25 мм и четырьмя отверстиями под шпильки крепления;
2) с посадочным отверстием диаметром 40 или 45 мм и шестью отверстиями;
3) с посадочным отверстием диаметром 60 мм и восемью отверстиями.
![]() |
Рис. 2. Конструкции роликов с внутренним охлаждением
При необходимости интенсифицировать выделение тепла в одной из деталей применяют ролики со специальной конструкцией рабочей части. Для сварки деталей с большой разницей в толщине или очень теплопроводных металлов используют ролики (рис. 3, а), у которых основание 1 выполнено из медного сплава, а рабочая часть 2 — из вольфрама или молибдена, припаянного к основанию. Повышения интенсивности нагрева также достигают за счет «сужения» тока на ограниченной площади рабочей поверхности ролика 1 с помощью двух стальных колец 3 (рис. 3, б) или выполнения на боковых поверхностях ролика Кольцевых выточек (рис. 3, в), уменьшающих сечение токоподвода вблизи рабочей поверхности.
![]() |
Рис. 3. Ролики со специальной рабочей частью:
а — из вольфрама; б — со стальными кольцами; в — с выточками
При швах большой протяженности на деталях малой толщины (0,1…0,3 мм) или имеющих какое-либо покрытие рабочая поверхность роликов быстро изнашивается, в связи с чем ухудшается качество сварки. В таких случаях роль рабочей поверхности роликов выполняет проволока из холоднотянутой меди (НВ 100) — рис. 4. Ролики имеют канавку, в которой помещена проволока, перематываемая при вращении роликов с одной катушки на другую. Такой способ обеспечивает стабильную форму рабочей поверхности и многократное использование проволоки в качестве электродов при роликовой сварке.
![]() |
Рис. 4. Использование проволоки в качестве электродов при роликовой сварке:
1 — ролики; 2 — проволока; 3 — детали
Для роликовой приварки фланцев к листу могут использоваться электроды в виде чашек (рис. 5). Нижний электрод 5 неподвижен, а верхний 3 обкатывается по нахлестке фланца 4. Обкатка производится при вращении вокруг вертикальной оси электрододержателя 1, причем наклонная ось 6 описывает конус, а рабочая часть электрода 5 с фланцем 4 постоянно перемещается по окружности в соответствии с вращением электрододержателя 1. При использовании электродов «чашка—чашка» свариваемые детали неподвижны. Существенным преимуществом этого способа является отсутствие в цепи подвода сварочного тока скользящего контакта, так как верхний электрод не вращается относительно гибкой шины 2.
![]() |
Рис. 5. Роликовая сварка электродами «чашка—чашка»
При роликовой сварке сильфонов с. арматурой используют электроды-цанги для зажима арматуры по наружной (рис. 6, а) или внутренней поверхности (рис. 6, б). Их обычно изготавливают из латуни под размер каждой из конкретных деталей и крепят при помощи резьбы на токоведущей оси машины. Вместо цанг могут использоваться гладкие оправки с плотной посадкой по отверстию в арматуре. Часто роликовую сварку выполняют с использованием промежуточных электродов-проставок. Такой способ применяется при сварке телескопических соединений трубок 1 в патроне 4 с помощью оправки 2 (рис. 7). Привод вращения осуществляется от патрона 4, ролики 3, 5 вращаются свободно. Возможно применение внутренней токопроводящей оправки для сварки продольного шва труб малого диаметра на поперечной машине.
![]() |
Рис. 6. Электроды-цанги, используемые при сварке сильфонов с арматурой:
а — наружная цанга;
б — внутренняя цанга;
1 — свариваемые детали; 2 — цанги; 3 — ролик
![]() |
Источник: http://k-svarka.com
Обсудить на форумеingeneryi.info
Точечная и роликовая сварка
Категория: Сварочные работы
Точечная и роликовая сварка
Точечная сварка. Сущность точечной сварки заключается в следующем. Если через два листа стали (рис. 1, а), уложенные внахлестку, и через сжимающие их два конусообразных медных электрода пропустить электрический ток большой силы, то стальные листы в точке прохождения электрического тока разогреются.
Рис. 1. Схема контактной сварки: а — точечной, б — роликовой; 1 — электроды, 2 — свариваемый материал
При достаточной силе тока температура нагрева будет настолько высока, что сталь в этом месте размягчится и начнет переходить в пластичное состояние. Если в этот момент выключить ток, не прекращая сжатия листов электродами, в этой точке стальные листы сварятся. Сваренное место имеет форму точки или кружка диаметром от 1 до 20 мм в зависимости от продолжительности нагрева и диаметра концов электродов.
Продолжительность сварки стали в одной точке очень незначительна, в час можно выполнить сварку в 3600 точках.
Передвигая листы стали, можно изготовить сварной точечный шов.
Преимущество точечной сварки перед ручной электродуговой заключается в том, что она пригодна для сварки тонких листов стали. Недостатком ее является то, что шов получается не сплошным и, следовательно, не вполне герметичным.
Для точечной сварки используют точечную сварочную машину ДТП-50.
Роликовая сварка. Для получения сплошного сварного шва применяют роликовую сварку, которая является разновидностью точечной. Листы стали зажимают между электродами (рис. 1, б), которые имеют вид дисков. Верхнему диску сообщается прерывистое движение, нижний поворачивается свободно. Сварка происходит с небольшими интервалами, так как ток пропускается только в момент движения электродов. Под действием электрического тока стальные листы между электродами нагреваются, размягчаются и свариваются. В следующий момент ток автоматически выключается для охлаждения шва и одновременно останавливается электрод. Затем цикл повторяется и таким образом получается непрерывный сварной шов.
Для роликовой сварки тонких листов применяется электросварочная шовная машина АШП-25. Машина имеет переключатель с шестью ступенями скорости подачи электрода и регулятор времени.
Сварочные работы - Точечная и роликовая сваркаgardenweb.ru
Особенности процесса роликовой сварки - Технологии - Cтатьи - Dalex
- каждый последующий участок шва подогревается теплом, выделяющимся при формировании предыдущего участка. Поэтому на единицу длины шва вводится большее количество тепла, чем при точечной сварки, и основной металл разогревается сильнее;
- значительная часть тока шунтируется через ранее сваренные участки шва, вызывая дополнительный подогрев деталей в области контакта деталь – ролик. Это часто вызывает наволакивание металла на рабочую поверхность роликов.
Роликовая сварка с непрерывной подачей тока (рисунок 1, а) требует строго согласования скорости перемещения детали и режима нагрева, так как в противном случае может образоваться прожог или непровар. Этот способ применяется при сварке стальных деталей толщиной не более 0,5 мм. При большей толщине свариваемого материала в области шва образуются внутренние дефекты вследствие того, что кристаллизация заканчивается без давления (за сварочными роликами).
При сварке деталей большей толщины применяют прерывистую подачу импульсов тока и непрерывное перемещение деталей (рисунок 1, б). В этом случае за счет лучшего теплоотвода удается устранить наволакивание металла и обеспечить гладкую поверхность шва.
При сварке деталей из легких сплавов для улучшения их охлаждения, обеспечения кристаллизации под давлением и стабилизации условий формирования каждой точки применяет прерывистое (шаговое) перемещение свариваемых заготовок. При этом импульс сварочного тока подается в тот момент, когда детали неподвижны, а перемещение их происходит во время паузы (рисунок 1, в).
При использовании роликовых машин для прерывистой точечной сварки также применяют шаговое перемещение деталей (рисунок 1, г). При необходимости во время остановки роликов, давление роликов увеличивается; во время перемещения деталей для уменьшения деформации, давление имеет меньшее значение.
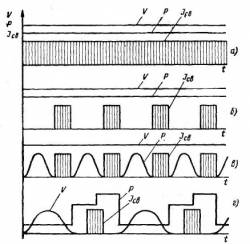
При непрерывном вращении роликов ток на участке контакта деталей может включаться импульсами через длительные паузы (рисунок 2, а) с образованием круглых или вытянутых по направлению движения точек. При уменьшении пауз возможно совпадение границ расплава (рисунок 2, б) некруглых точек и образование шва, а при уменьшении скорости сварки их перекрытие (рисунок 2, в). Шов также образуется при определенных режимах сварки переменным током без пауз (рисунок 2, г). Изменение тока в полупериодах (рисунок 2, д) еще более расширяет возможности непрерывной сварки. При малых скоростях сварки непрерывная сварка связана с большими потерями тепла, а при больших скоростях сварки появляются выпучивание и трещины в литой зоне.
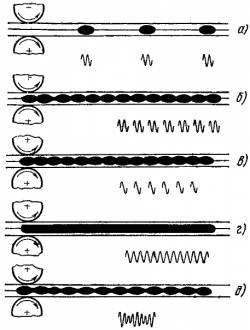
При роликовой сварке плотным швом ток только на 15 процентов выше, чем при обычной точечной сварке (в обоих случаях длительность протекания тока и давление роликов одинаковы). Это обусловлено теплоотдачей от соседних точек и снижением радиуса электрода из-за интенсивной деформации металла в зоне контакта впереди электрода.
В современной производственной практике наибольшее распространение получил цикл роликовой сварки прерывистой подачей импульсов тока и непрерывное перемещение деталей. На рисунке 3 показана схема перемещения роликов.
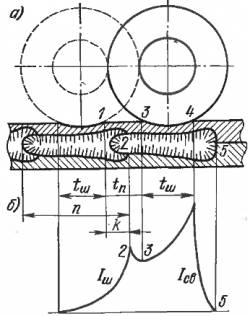
Рассмотрим момент, когда ролики после сварки точки длиной n передвинулись из положения ролика, изображенного штриховой линией в позицию, указанную сплошной линией. Он достаточно плотно контактирует с металлом по длине от линии 3 до линии 4. В этот момент и включается импульс тока длительностью tсв. Как видно (рисунок 3, а) за время tп (время вращения ролика без тока от линии 1 до линии 2) успел образоваться непроваренный участок от линии 2 до линии 3. Вот этот участок и сваривается за счет шунтирования, который по своей плотности распределяется в момент включения сваривающего тока по эпюре, показанной на рисунке 3, б.
Компания ООО "Партек" поставляет машины роликовой Dalex (Германия). Оборудование контактной роликовой и точечной сварки, Вы можете посмотреть в нашем каталоге.
© Без согласования с автором, частичная или полная перепечатка статьи запрещена. Все права защищены.
www.dalexweld.ru
Роликовая контактная сварка - Большая Энциклопедия Нефти и Газа, статья, страница 1
Роликовая контактная сварка
Cтраница 1
Роликовая контактная сварка применяется в тех случаях, когда необходимо получить не только прочное, но и плотное соединение деталей между собой. При этом способе свариваемые детали накладываются внахлестку друг на друга и зажимаются роликовыми электродами ( фиг. [1]
Роликовую контактную сварку выполняют на электросварочной шовной машине АШП-25. На этой машине можно сваривать детали при шести различных режимах работы, так как роликовый электрод имеет шесть скоростей вращения. Это позволяет сваривать стальные листы различной толщины, не заменяя элементов оборудования. [2]
Точечную и роликовую контактную сварку, при которой зоны максимального нагрева малодоступны для атмосферных газов, обычно производят без защитной среды. Стыковую сварку оплавлением некоторых тугоплавких металлов также иногда выполняют на воздухе; в этом случае роль защитных газов выполняют пары свариваемого металла, выделяющиеся в стыке. [3]
Машины роликовой контактной сварки с наружным водяным охлаждением роликов должны иметь корыто-поддон для сбора стекающей воды. [4]
Машины роликовой контактной сварки с наружным водяным охлаждением ролпков должны иметь корыто-поддон для сбора стекающей воды. [5]
В области роликовой контактной сварки улучшены серийные машины и аппаратура управления сварочным процессом. Созданы импульсные машины с шаговым перемещением деталей, облегчающие качественную сварку легких сплавов. Ряд предприятий разработал и внедрил специальные приспособления, позволяющие выполнять роликовую сварку любых криволинейных швов, практически неограниченной длины. Наличие таких приспособлений позволяет значительно расширить область применения этого вида сварки. [6]
Для соединения мембран применяют роликовую контактную сварку герметичным швом. Предварительно мембраны скрепляют точечной сваркой в 4 - 8 точках, расположенных симметрично по борту мембраны. [7]
Соединения листов, сваренных роликовой контактной сваркой, испытываются растяжением образцов, представленных на фиг. [8]
Герметизация мембранной оболочки грузового танка выполняется обычно роликовой контактной сваркой или сваркой трением. Стрелками показаны усилия, возникающие при их взаимодействии. [9]
Соединение внахлестку является основным видом соединений при точечной и роликовой контактной сварке. [10]
Одним из универсальных и надежных видов оборудования являются установки роликовой контактной сварки, применяемые для герметизации мегаллостеклянных и металлокерамических корпусов прямоугольной формы размером до 75 мм. [11]
В предлагаемом теплообменнике для снижения его стоимости путем применения роликовой контактной сварки для крепления ребер последние выполнены в виде спирали и имеют U-образную форму в сечении, перпендикулярном оси трубчатой поверхности. [12]
Одними из универсальных и надежных видов оборудования являются установки для роликовой контактной сварки, позволяющие герметизировать металлостеклянные и металлокерамиче-ские корпуса размерами до 75 мм. [13]
Виды контакта и сварки разнообразны и различаются формой получаемого сварного соединения; основными являются стыковая, точечная и роликовая контактная сварка. Сварочный ток может быть постоянным или переменным, нормальной, пониженной или повышенной частоты. [14]
Виды контактной сварки разнообразны и различаются формой получаемого сварного соединения; основными являются стыковая, точечная и - роликовая контактная сварка. Сварочный ток может быть постоянным или переменным, нормальной, пониженной или повышенной частоты. [15]
Страницы: 1 2
www.ngpedia.ru
Роликовая сварка - Большая Энциклопедия Нефти и Газа, статья, страница 4
Роликовая сварка
Cтраница 4
Роликовая сварка применяется вместо па ки при изготовлении баков для горючего. [46]
Роликовая сварка широко используется в производстве комнатных электрохолодильников ( изготовление шкафов, испарителей), газогенераторов, огнетушителей, реактивных двигателей и многих других изделий. [47]
Роликовая сварка может быть непрерывной или прерывистой. [48]
Роликовая сварка является видоизменением точечной сварки сопротивлением и отличается тем, что сварка протекает в контакте листов на кратчайшем пути следования тока от одного вращающегося ролика к другому. В результате между двумя листами получается непрерывный шов. При роликовой сварке ток может протекать непрерывно или прерывисто. Во избежание коробления, связанного с большим выделением тепла, при роликовой сварке шов усиленно охлаждают водой или ведут сварку под водой. [49]
Роликовая сварка точечным швом плоских крупногабаритных панелей может осуществляться с использованием подвижной каретки, двигающейся в направляющих. [50]
Роликовая сварка применяется для сварки листовых конструкций, требующих плотно-прочных швов, например различных резервуаров, баков, тары и других изделий массового производства. [51]
Роликовая сварка производится внахлестку, величина которой составляет 4 - 5 мм. [52]
Роликовая сварка дает прочный и плотный шов и применяется при массовом производстве изделий из тонколистовой стали, а также при сварке масляных, бензиновых и водяных баков, труб и других изделий. [53]
Роликовая сварка имеет много общего с точечной и отличается от нее тем, что электроды имеют форму дисков. При этом способе сварки точки образуются с частичным перекрытием, благодаря чему образуется сплошной плотный шов. [55]
Роликовая сварка ( рис. 2 - 2, в) заключается в том, что заготовки соединяют непрерывным прочноплотным сварным швом, который состоит из ряда последовательных точек, частично перекрывающих друг друга. Заготовки устанавливают в сварочной машине между роликами, один из которых ведущий, или между одним ведущим роликом и оправкой. На ролики действует усилие F механизма давления, и к ним подведен ток. [56]
Роликовая сварка чаще всего применяется для соединения деталей суммарной толщиной до 5 мм. [58]
Роликовая сварка осуществляется на стационарных и передвижных машинах, оборудованных специальным приспособлением для сжатия роликов. В табл. 28 даны ориентировочно режимы для роликовой сварки малоуглеродистой стали. [59]
Роликовая сварка может быть непрерывной и прерывистой, при последней применяют прерыватели тока. Прерывистая сварка обеспечивает высокое качество сварного соединения, однако шов получается менее чистый, чем при непрерывной сварке. Роликовая сварка дает прочный шов и может быть использована при изготовлении силовых конструкций. [60]
Страницы: 1 2 3 4 5
www.ngpedia.ru
Роликовая сварка
Количество просмотров публикации Роликовая сварка - 76
Точечная сварка
Стыковая сварка
При стыковой сварке торцы соединяемых деталей приводятся в соприкосновение, после чего вдоль деталей пропускается значительный ток, разогревающий место стыка до крайне важно й для сварки температуры. Далее продольным сжимающим усилием достигается непосредственная сплошность соединения.
Различают две разновидности стыковой сварки: сварку без оплавления и сварку с оплавлением.
Регулирование количества подводимой энергии при заданном сопротивлении контакта͵ определяемом условиями сварочного процесса, может осуществляться либо изменением сварочного тока, либо изменением продолжительности протекания тока.
Машины для стыковой сварки классифицируются следующим образом.
1. По способу сварки - для сварки сопротивлением и оплавлением (непрерывным оплавлением или оплавлением с подогревом).
2. По назначению - универсальные и специализированные.
3. По устройству механизма подачи - с пружинным, рычажным, винтовым (от штурвала), пневматическим, гидравлическим или электромеханическим приводом.
4. По способу монтажа и установки - стационарные и переносные.
При точечной сварке соединяемые детали обычно располагаются между двумя электродами, закрепленными в специальных электрододержателях. Под действием нажимного механизма электроды плотно сжимают свариваемые детали, после чего включается ток.
При этом виде сварки соединение деталей непрерывным или прерывистым швом осуществляется за счёт пропускания через свариваемые детали тока, подводимого посредством вращающихся роликов.
Машины для роликовой сварки обычно снабжены двумя токоподводящими роликами, из которых один выполняется приводным, а другой вращается за счёт трения при передвижении свариваемых деталей.
Роликовую сварку чаще всего применяют для соединения тонкостенных деталей, к примеру при изготовлении топливных баков и бочек для транспортировки различных материалов.
Различают три режима роликовой сварки.
1. Непрерывное движение свариваемых деталей относительно роликов с непрерывной подачей тока. 2. Непрерывное движение свариваемых деталей относительно роликов с прерывистой подачей тока. 3. Прерывистое движение свариваемых деталей относительно роликов с прерывистой подачей тока (шаговая сварка).
Роликовая сварка весьма эффективна при изготовлении тонкостенных сосудов, при производстве сварных металлических труб и ряда других изделий.
Основными элементами роликовых машин являются станина, верхняя и нижняя консоли с роликовыми электродами, механизм сжатия, привод вращения ролика и сварочный трансформатор с гибким токоподводом
Аналогично точечной роликовая сварка тонких деталей может выполняться импульсами тока разрядки конденсаторов, для чего выпускаются различные типы роликовых машин.
Для обеспечения заданной производительности контактных сварочных установок и качества сварки крайне важно строго выдерживать время протекания сварочного тока в цикле сварки.
Это достигается соответствующими элементами схем управления, которые разрывают цепь сварки и управляются регуляторами времени.
Для разрыва цепи применяют механические выключатели тока, электромагнитные контакторы и электронные контакторы.
referatwork.ru