Энциклопедия по машиностроению XXL. Штамповка деталей
Штамповка деталей - Справочник химика 21
Пресс для штамповки деталей из размягченной массы стекла. Пресс (рис. 87) для штамповки стекла имеет сменные пуансоны и матрицы, изготовленные из стали. Нижняя часть — матрица — [c.174]
Технологические процессы производства аппаратуры охватывают почти все виды обработки металлов горячую и холодную обработку давлением (гибочные операции, штамповка деталей аппаратов), сварку металлов и сплавов, термическую и холодную резку (разделительную и поверхностную), термическую обработку (во многих ее разновидностях), механическую обработку, сборку и др. [c.3]В последнее время термическую обработку и нагревание при ковке и штамповке проводят в атмосфере инертных газов (аргон, гелий), смеси азота с водородом и вакууме. При нагревании в перечисленных средах резко уменьшается глубина разрушения, что позволяет значительно снизить глубину механической обработки, существенно сократить расход ценного металла и обеспечить точную штамповку деталей. [c.88]
Кроме описанных способов получения точных деталей в комбинированных и простых штампах, в последние годы освоен новый способ штамповки деталей в универсальных штампах из отдельной заготовки, который приведен в книге В. М. Богданова и А. Г. Яковлева. [c.209]
Более толстые хроматные пленки на алюминии применяют в качестве защитно-декоративных и более дешевых, чем при анодировании. Хроматные пленки на алюминии (как и анодные) позволяют производить штамповку деталей из покрытой ленты без разрушения покрытия. Это значительно снижает трудоемкость. [c.111]
Пресс для штамповки деталей из размягченной массы стекла. [c.174]
Для штамповки деталей из алюминия, а также черных металлов и медных сплавов. [c.335]
Разработка специальных составов делает возможной горячую штамповку деталей из тонколистных материалов, таких, как титан, молибден, вольфрам. При этом тонкая (1 мм) листовая заготовка обмазывается слоем высококалорийного пиротехнического состава при его поджигании лист сразу по всей поверхности нагревается до нужной температуры. Из-за кратковременности нагрева металлы (молибден, вольфрам) не успевают окисляться на воздухе [60]. [c.287]
Имеются сведения о применении покрытия, состоящего из 85% РЬ и 15% 5п, с целью улучшения обрабатываемости листовой стали давлением [16]. Свинцовооловянное покрытие при операциях штамповки деталей выполняет роль смазки. [c.121]
Штампы для штамповки деталей из полосового материала. [c.110]
Горячая штамповка деталей средней сложности из легированных сталей 11 [c.121]
Эпоксидные литьевые смолы применяются в США для производства форм глубокой вакуумной вытяжки из термопластичных пленок. Для снижения усадки и повышения теплопроводности формы покрывают алюминиевым порошком. При изготовлении штампов для штамповки деталей из тонкого листа в эпоксидную смолу в качестве наполнителя добавляют окислы алюминия. При изготовлении шаблонов, гибочных штампов, калибров и другого штампового инструмента применяют эпоксидные смолы, усиленные стекловолокном. Поверхности перечисленных деталей покрывают эпоксидным лаком с окислами алюминия. Это усиливает сцепление стекловолокна с поверхностью формы. Поверхности больших моделей покрывают слоем замазки на основе эпоксидных смол. Эта замазка затвердевает в обычных условиях, повышает качество поверхности и увеличивает срок службы моделей [30]. [c.87]
При необходимости использования для штамповки деталей предварительно лакированного материала применяют матрицы, изготовленные из нейлона. Так, по зарубежным данным, для матриц, на которых производилась гибка закругленных уголков орнаментной рамки для крепления стекла в телевизорах, использовали нейлон. Матрица изготовлялась из листового нейлона толщиной 6—4 мм и прикреплялась винтами к стальной плите, что придавало ей необходимую жесткость и прочность. [c.87]
ТОЧНАЯ ШТАМПОВКА ДЕТАЛЕЙ ОПТИКО-МЕХАНИЧЕСКИХ ПРИБОРОВ [c.1]
Книга посвящена практике холодной штамповки деталей оптико-механических приборов. В ней описываются современные методы точной штамповки — комбинированная штамповка в совмещенных и последовательных штампах, штамповка в перфорированной полосе и объемная штамповка прессованием и выдавливанием. [c.2]
Отделение небольших излишков материала (припусков) после вырубки или объемной штамповки деталей с целью получения геометрически правильных и точных по размеру и чистых поверхностей среза [c.8]
При штамповке деталей сложной конфигурации следует при- менять наклонный, встречный (заход ряда в ряд), многорядный раскрой и раскрой с поворотом полосы. [c.64]
Из примеров видно, что наибольшую экономию материала дает раскрой без перемычек, который применяется лишь для штамповки деталей, имеющих малую точность размеров. [c.64]
На фиг. 6. 5 приведена более сложная и совершенная конструкция штампа совмещенного действия для штамповки деталей типа зубчатого колеса. В штампе совмещаются вырубка по контуру и пробивка центрального и фасонных отверстий. В качестве материа- [c.92]
При штамповке деталей оптико-механических приборов часто встречается обратная (реверсивная) вытяжка. Штамп, совмещающий вырубку, вытяжку и обратную вытяжку, приведен на фиг. 6. 34. Его действие понятно из чертежа. [c.120]
Сущность способа заключается в проведении множества шта.мпо-вочных операций и операций резания — фрезерование, сверление и др. — непосредственно в полосе, не отделяя от нее деталей, с постоянной базировкой на специальные пробиваемые в полосе технологические (перфорационные) отверстия, являющиеся базовыми (фиг. 8. 1). При изготовлении деталей по этому способу в зависимости от количества операций требуется соответствующее количество штампов, на которых производится выполнение каждой отдельной штамповочной операции, и станков для выполнения операций резания. Полоса по следовательно передается со штампа на штамп или на станок для выполнения очередной операции. Как и при штамповке деталей из штучных заготовок, при этом способе можно также соз- [c.169]
В целом гехнологический процесс производства аппаратуры охватывает почти все виды обработки металлов горячую и холодную обработку давлением (правка, гибка, калибровка, штамповка деталей [c.3]
Точная штамповка деталей в полосе с базировкой на перфорационные отверстия рациональна также и при формовочно-вытяжных операциях при изготовлении малогабаритных деталей (до 50 мм), особенно в тех случаях, когда форма штампуемой детали не обеспечивает надежного закрепления детали в штампе. Ниже рассматриваются два таких примера. [c.190]
В. м. Богданов, А. Г. Яковлев. Штамповка деталей по а мелкосерийном производстве, Машгиз, 1952 [c.209]
Следует заметить, что условия контроля при штамповке деталеи меняются в зависимости от того, изготовляются ли детали поточным методом (непрерывно) или партиями с перерывами между отдельными операциями. [c.271]
В то же время "ШС-2" изготавливается из натуральных продуктов - кориандрового масла и шерстного жира, а "Росойл-222" - сложная композиция из минеральных и растительных масел, загущенная полимерными загустителями и наполнителями, что влечет за собой высокую стоимость этих продуктов. Учитывая эти обстоятельства, представляет интерес использование-дешевых парафиновых отложений в качестве технологической смазки на операциях листовой штамповки деталей средней сложности. [c.168]
Технологические результаты. Прокатка штучных заготовок (рис. 3) деталей типа гаечный ключ из стали ЗОХГСА и их последующая штамповка показали экономию металла до 15%, а прокатка и штамповка деталей типа рукоятка из сплава АК-6 показали возможность получения облоя, равного только мостику заусенечной канавки, что обеспечивает экономию металла до 30% по сравнению со штамповкой из круглого прутка. Наилучшей формой сечения заготовки под прокатку следует считать круг и квадрат. [c.41]
Т.е. с псевдо-а-структурой легируют А1, Мп, V, 2г, N6, 8п, Ре, Сг, 81 содержат до 5% р-фазы. Отличаются высокой технологичностью (при содержании А1 6%), высокой термич. стабильностью, хорошей свариваемостью термически не упрочняются, осн. вид термич. обработки-отжиг при 590-740 °С. Низкоалюминиевые псевдо-а-сплавы предназначены в осн. для изготовления листов, лент, полос, труб, профилей. Листовую штамповку деталей простой формы производят в холодном состоянии, при штамповке деталей сложной формы необходим подогрев до 500 С. Недостатки этих сплавов-сравнительно невысокая прочность и жаропрочность, большая склонность к водородной хрупкости. Пр> меняются для изготовления сложных в технол. отношении деталей, рабо-таюпщх при т-ре до 350 °С. [c.594]
Различают желтое и зеленое хроматирование алюминиевой ленты, применяемой при штамповке деталей. Для получения на алюминии желтых хроматных пленок используют кислые растворы на основе хромовой кислоты, фтор (свободный или комплексный) и активаторы (феррицианиды, молибденаты, соединения [c.111]
Технический титан марки ВТ1-0 содержит 99,2% Т1. Основные примеси, % Ре 0,5 мм, трубы, прутки, проволоку, поковки и штамповки. Он хорошо обра батывается давлением в горячем состоянии. Допускает штамповку деталей не сложной формы из листа в холодном состоянии. Удовлетворительно обрабаты Бается резанием (приблизительно так же, как аустенитные нержевающие стали) и хорошо сваривается. Технический титан применяют для конструкций с рабочей температурой стенки от —269 до +250 °С без ограничения давления. [c.116]
Коррозионная стойкость металла полированной поверхности значительно выше, чем шлифованной или травленной (неспасси-рованной). Поэтому в процессе обработки поверхности деталей рабочего колеса из коррозионно-стойкой стали следует получать поверхность более высокого класса шероховатости. При штамповке деталей не рекомендуется применять свинцовые штампы. Если свинец и другае легкоплавкие металлы остались на поверхности, то во время термической обработки или работы дымососов на горячих газах сталь будет подвержена межкристаллитной коррозии. [c.70]
ГО.050.223—83 Нормативы трудоемкости изготовления технологической оснастки. Основные положения 4 ГО.052.032—83 ОСТПП. Организация специализированного участка холодноштамповочного производства для поэлементной штамповки деталей. — Взамен ОСТ 4 ГО.052.032—72 4 ГО.052.034 Аппаратура радиосвязи. Методика технологической [c.133]
Типовой технологический процесс 16 0.686.859—80 ОЕСТПП. Источники света электрические. Штамповка деталей цоколей. Типовые технологические процессы. — Взамен ОСТ 16 0.686.035—73, ОСТ 16 0.686.114—74 16 0.686.874—80 ОЕСТПП. Источники света электрические. Варка и выработка стекла. Типовой технологический процесс. — Взамен РТМ ОАА.686.046—70, РТМ ОАА.686.071—71 [c.151]
Укринол-5/5 (ТУ 38-101389—79) — средневязкое минеральное масло с активными серохлорсодержащими присадками, в том числе с хлорпарафином ХП-470 (40 %). Содержит 5 % консервационного масла К-17, что улучшает противокоррозионные свойства. Рекомендуется для использования на холодновысадочных автоматах, а также при штамповке деталей из меди и медных сплавов. Изготовляется на ДОЗ. [c.107]
При штамповке деталей из листового проката аустенитных ие ржавеющих сталей, в силу прочности обрабатывае.мого материала, потребный расход мощности прессового оборудования превышает почти в два раза мощность, необходимую для выполнения той жг операииш из листового проката малоуглеродистых сталей. [c.52]
В последнее время все более широкое распространение находит метод штамповки деталей на гидропрессе при повышенных давлениях путем обжатия листовой заготовки резиной в формблоках. [c.79]
На рис. 99 приведена схема пресса фирмы Вепкап (Япония) для штамповки деталей из трубных заготовок гидравлическим выпучиванием. Основные узлы пресса гидравлический насос 7 с мульти- [c.110]
Необходимо отметить, что штамповка деталей (пружин) из пружинных сталей первой прочности (1П) и второй прочности (2П) должна производиться с учетом величины угла пружинения в гибочном штампе. Стали с более высокой прочностью — выше 2П —гибке не подвергаются, из них можно штамповать только плоские детали вырубкой, пробивкой. При гибке сталей с прочностью более 2П упругое пружинение настолько велико, что по существу формоизменения материала (заготовки) не происходит. При вырубных операциях этих же сталей происходит интенсивный износ рабочих частей штампов. Стойкость их понижается в несколько раз по сравнению со стойкостью штампов, работающих на материале с обычной прочностью. Это делает штамповку неэкономичной. Поэтому штампоз-ку-вырубку, пробивку из сталей, имеющих прочность более 2П, можно допускать только в исключительных случаях. [c.34]
Т акого типа конструкции успешно могут применяться для штамповки деталей из упругих ( пружннны х) материалов, у которых участки отгибаются под небольшими углами. Необходимо отметить, что растяжение при гибке ограничено, по-это1му и углы гибки обычно не превосходят 25—30°- [c.75]
Деталь рычаг призмы к фотоаппарату Зоркий (фиг. 9.5). Материал штампуемой детали — листовая латунь Л62 голшиной 8 мм. Назначение детали — обеспечить в соединении с фугими деталями точность юстировки фотоаппаратов по дистанци-)нной шкале. До разработки нового процесса штамповки деталь изготовлялась из кусковой заготовки на 10 деталей на металлоре-куших станках за 42 операции. Трудоемкий и длительный процесс бработки детали сильно сдерживал производство фотоаппаратов. 3 основу нового технологического процесса изготовления детали )ыли положены два главных условия [c.231]
Контроль при запуске партии деталей (или наладке технологического процесса, штампов). Этот вид контроля чрезвычайно важен при массовом производстве сложных и точных, деталей, когда ошибка или недосмотр в наладке могут повлечь за собой массовый брак дорогостоящих деталей, потерю ритма в работе-и удорожание продукции. Во избежание этого наладка штампа для изготовления сложных и точных деталей обязательно контролируется цеховым контрольным аппаратом путем проверки нескольких пробных деталей, отштампованных на вновь установленных штампах а предъявленных в ОТК мастером или бригадиром-наладчиком. Штамповка деталей разрешается, если детали оказались вполне годными.. В особых случаях при штамповке сложных и точных деталей (трудно контролируемых) производится клеймение первой детали запускаемой партии. Это ускоряет и облегчает процесс контроля в ходг-производства, так как можно быстро убедиться в качестве отштампованной детали путем сравнения ее с первой клейменой деталью. КрО Ме того, клеймение первой детали налагает большую ответственность на лиц, ведущих процесс-наладчика, мастера и т. п. [c.271]
При штамповке деталей фотоаппаратов, к декоративным качествам которых предъявляются высокие требшания, чистота исходногс [c.282]
Для подобных случаев штамповки деталей сложной конфигурации из твердых тонких материалов оказывается выгоднее ивготов-лять (хотя и неудобно и дорого) цельные матрицы (фиг. И. 20), а не составные. [c.304]
chem21.info
Способ штамповки полых деталей
Использование: в способах штамповки деталей из листа, имеющих полую чашу и плоский широкий фланец. Сущность изобретения: способ штамповки полых деталей, состоящих из чаши и плоского широкого фланца, включает прижим периферийной части заготовки и вытяжку-формовку ее центральной части. В процессе вытяжки увеличивают давление прижима, осуществляя торможение фланца до его полной остановки при величине площади поверхности заготовки, втянутой в рабочее окно матрицы Fвт, равной Fвт = Fч(Sr/So), где: Fч - площадь поверхности чаши готовой детали; So - толщина исходной заготовки из листа; Sч - средняя толщина чаши готовой детали, определяемая из соотношения: Sч = Soexp(-3n/2)
0,1Soexp(-3n/2), где n - показатель интенсивности упрочнения штампуемого материала. Затем, при неподвижном фланце заготовки осуществляют равномерное растяжение и утонение предварительно вытянутой части заготовки по величине средней толщины чаши готовой детали. Технический результат - снижение расхода штампуемого металла за счет уменьшения размеров заготовки и увеличение глубины штампуемой детали. 2 ил.
Изобретение относится к области обработки металлов давлением, а именно к способам штамповки деталей из листа, и может быть использовано при изготовлении деталей, имеющих полую чашу и плоский широкий фланец.
Известен способ штамповки деталей с плоским широким фланцем путем инструментальной вытяжки (Романовский В.П. Справочник по холодной штамповке. Л. Машиностроение, 1971, с. 189). Формообразование детали осуществляется в результате многопереходного втягивания металла в рабочее окно матрицы. Недостаток этого способа заключается в том, что при вытяжке в результате втягивания металла размеры фланца существенно сокращаются. Для изготовления детали с заданными размерами фланца необходимо использовать заготовку из листа с увеличенными исходными размерами. Кроме этого, при инструментальной вытяжки дно заготовки практически не деформируется. Металл деформируется неравномерно, уточняется, в основном, в зоне радиусного перехода (в этом сечении и происходит разрушение заготовки). Пластические свойства металла по очагу деформации используются не полностью, что снижает глубину вытяжки и требует увеличения размеров исходной заготовки. Наиболее близким по технической сущности к заявляемому способу является штамповка по схеме: эластичный пуансон жесткая матрица (Исаченков Е.И. Штамповка резиной и жидкостью. М. Машиностроение, 1967, с. 339). Формообразование детали осуществляется, в основном, в результате формовки (растяжения) части заготовки, расположенной над рабочим окном матрицы. Недостаток способа заключается в том, что использование эластичного пуансона создает на промежуточных стадиях деформирования плавные радиусы скругления заготовки. Это приводит к нерегулируемому утонению центральной части донного участка заготовки. Именно здесь происходит наиболее интенсивное утонение и растяжение металла, а также разрушение заготовки. В результате высокой неравномерности деформации утонения, пластические свойства металла по очагу деформации используются не полностью, что приводит к увеличению размеров исходной заготовки из листа и снижает глубину вытяжки за переход. Поставлена задача разработать способ штамповки полых деталей с широким фланцем, который позволит снизить расход штампуемого металла за счет уменьшения размеров исходной заготовки из листа, а также увеличить глубину штампуемой детали. Отмеченные эффекты могут быть достигнуты путем выравнивания деформации утонения по образующей чаши штампуемой детали. Ликвидируя сосредоточенное утонение заготовки и равномерно утоняя металл в зоне чаши до максимально возможной величины, которая пропорциональна пластичности штампуемого металла, становится возможным максимально увеличить площадь поверхности заготовки в процессе формообразования. Это позволяет уменьшить исходные размеры заготовки из листа и увеличить глубину штампуемой детали. Поставленная задача решается тем, что в способе штамповки полых деталей с широким фланцем, включающим прижим периферийной части заготовки и вытяжку-формовку ее центральной части, согласно изобретению, в процессе вытяжки увеличивают давление прижима, осуществляя торможение фланца до его полной остановки при величине площади поверхности заготовки, втянутой в рабочее окно матрицы Fвт, равной






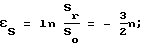
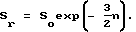

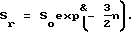

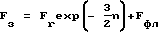

Формула изобретения
Способ штамповки полых деталей, состоящих из чаши и плоского широкого фланца, включающий прижим периферийной части заготовки и вытяжку-формовку ее центральной части, отличающийся тем, что в процессе вытяжки увеличивают давление прижима, осуществляя торможение фланца до его полной остановки при величине площади поверхности заготовки, втянутой в рабочее окно матрицы Fвт, равной Fвт Fч



РИСУНКИ
Рисунок 1, Рисунок 2www.findpatent.ru
Детали сложные - Штамповка объемна
На первом этапе (1950 - 1965 гг.) развития реактивной авиационной техники основные детали (лопатки), имеющие сложные геометрические формы и точные размеры, изготовляли объемной штамповкой, механической обработкой, шлифованием, сваркой или пайкой. Получение пустотелых лопаток методом штамповки практически стало невозможным. [c.12]
Холодной объемной штамповкой получают детали из большой номенклатуры сталей и сплавов цветных металлов, детали симметричные и асимметричные, со шлицами, канавками, ступенчатыми полостями и других сложных форм. Масса деталей, штампуемых на автоматах, достигает 3,5 кг, а на прессах — 40 кг, диаметр поковок — до 200 мм. [c.434]
Ковку и горячую объемную штамповку применяют для изменения формы заготовки, чтобы максимально приблизить ее к форме готовой детали. Это формоизменение обусловлено пластичностью. Чем выше пластичность, тем более сложную форму можно получить в конечной поковке из простой начальной заготовки. Пластичность или пласти- [c.474]
Технологический процесс холодной объемной штамповки состоит из следующих операций 1) подготовки исходного металла (очистка от окалины и загрязнений, смазка), 2) изготовления заготовок (рубка, а иногда и предварительное деформирование при получении сложной формы деталей), 3) штамповки (высадка, гибка, прессование, калибровка и т. д.), 4) отделки (термическая обработка, травление, нанесение покрытий, сверление отверстий, фрезерование пазов, зачистка и т. д.) Сочетание этих операций определяется сложностью изготовления детали. [c.414]
Операции горячей штамповки. Основные операции горячей штамповки напоминают рассмотренные в 4 операции объемной холодной штамповки, но отличаются от них гораздо большими степенями деформации и позволяют получить более сложные детали, что обусловлено высокой пластичностью нагретого металла. [c.97]
Недостатком объемной штамповки является необходимость применения специального и часто весьма сложного инструмента (штампов) для каждого наименования детали, что значительно удорожает процесс изготовления изделия. [c.10]
Объемная холодная штамповка применяется для изготовления деталей сложной формы, но малых размеров из металлов, обладающих высокой пластичностью. Процесс объемной штамповки — пластическая деформация деталей — подобен горячей штамповке. Однако отсутствие нагрева позволяет получить более точные детали и с более чистой поверхностью. Применение объемной штамповки в сочетании с другими штамповочными операциями позволяет получить детали, не требующие или почти не требующие дальнейшей механической обработки. [c.67]
Штамповка точных поковок сложной формы. Известно, что чем сложнее конфигурация поковки, тем большее число переходов требуется для ее штамповки и больший объем металла идет в отход. Изготовление поковок в штампах с разъемной матрицей позволяет не только получать поковки с размерами и формой, близкими к размерам и форме детали, но и значительно сократить последующую механическую обработку поверхностей сложной конфигурации. Эта разновидность точной объемной штамповки осуществляется либо на универсальном оборудовании (кривошипных горячештамповочных прессах), либо на специальном (прессах двойного действия). [c.50]
Детали больших габаритных размеров сложной формы переменного сечения, с ребрами и проушинами Подмоторные рамы, панели, лонжероны, шасси, рамы, кронштейны Мерная заготовка из слитка без предварительного или с предварительным прессованием слитка Объемная штамповка из легких сплавов типа АК на мощных прессах [c.292]
Наибольшей эффективности этого способа достигают при изготовлении деталей сложной формы, обработка которых на металлорежущих станках связана с большой трудоемкостью и значительным отходом металла в стружку. Типовые детали, изготовленные холодной объемной штамповкой, показаны на рис. 26. [c.314]
При помощи объемной штамповки могут быть получены детали весьма сложной формы. [c.229]
Явление сверхпластичности в промышленности используют при объемной изотермической штамповке и при пневмоформовке. Сверхпластичность позволяет в процессе штамповки за одну операцию получить детали сложной формы, повысить коэффициент использования металла, уменьшить трудоемкость и стоимость изготовления изделий. Недостатком является необходимость нагрева штампов до температуры обработки и малая скорость деформаций. [c.77]
В последнее время в практику холодной объемной штамповки стало внедряться прессование жидкостью высокого давления, которое позволяет получать профили и детали сложной конфигурации из малопластичных материалов. При прессовании жйдкостью, вследствие уменьшения сил трения и более равномерного распределения напряжений, удельные усилия гораздо ниже, чем при обычном выдавливании, а потому инструмент более стоек. При изготовлении отдельных деталей могут также применяться радиальное (ротационное) обжатие, раскатка и обкатка роликами и шарами. В литературе приводятся различные способы холодной объемной штамповки, позволяющие снижать удельное усилие. [c.304]
Для объемной штамповки применяют паровоздушные штамповочные молоты двойного действия с массой падающих частой до 1800 кг (имеют наибольшее распространение), гидравлические и фрикционные прессы, кривошипные ковочно-штамповочные прессы, горизонтально-ковочные машины, винтовые фрикционные прессы и др. Паровоздушные штамповочные молоты по своему устройству сходны с паровоздушными молотами для ковкн. Для горячей штамповки используют также бес-шаботные, высокоскоростные паровоздушные молоты, у которых происходит соударение нижнего и верхнего бойков, движущихся навстречу друг другу со скоростью 20 м/с (на других штамповочных молотах — 6—8 м/с). При работе на этих молотах сотрясения почвы не происходит. На этих молотах можно штамповать малопластичные высоколегированные стали и детали сложной конфигурации. [c.156]
В последние годы получило развитие производство химически загущенных композиционных формовочных систем. Листовые и объемные формовочные материалы становятся стандартными для многих автомобильных деталей, таких как обрамление облицовки (решетки) радиатора, панель передних фар и удлинители крыльев, используемых на большинстве легковых автомобилей. С применением в изделиях низкоусадочных и требующих малой фасонной обработки полиэфирных смол при относительно высоком давлении прессования (- 6,9 МПа) сложные детали могут быть изготовлены методом прямого прессования с производительностью 30 шт. в 1 ч на одну пресс-форму. Так как ребра жесткости, бобышки и элементы утолщения стенок могут быть заформованы в деталь, операции механической обработки, изготовления и объединения деталей существенно упрощаются по сравнению с обработкой аналогичных деталей, изготовленных из стального листа штамповкой или литьем в постоянные формы. [c.496]
Формообразующие детали штампов для объемной штамповки, матрицы пресс-форм для прессования деталей из пластмассы, резины, для литья под давлением имеют в большинстве случаев сложную конфигурацию полостей. Вопрос их бесстружкового изготовления успешно решается за счет применения холодного выдавливания на гидравлических прессах. Сущность метода заключается в том, что закаленный мастер-пуансон вдавливается в заготовку, заключенную в специальное приспособление — пакет-штамп. Получается оттиск, который по форме и размерам точно соответствует рабочей части пуансона. [c.83]
Шта-аповка — это способ изготовления изделий давлением с помощью специального инструмента (штампов), рабочая полость которых определяет конфигурацию конечной штамповки (изделия). Штамповки по своим размерам, точности, допускалз и припускам значительно лучше аналогичных деталей, изготавливаемых свободной ковкой. Штампованные заготовки значительно приближены по форме и размерам к готовой детали. Специальные методы точной штамповки (высокоскоростная, штамповка в изотермических условиях и др.) позволяют изготавливать заготовки, подлежащие механической обработке только по сопрягаемым поверхностям. Процессы штамповки подразделяются на два вида объемная и листовая штамповка. При объелшой штамповке ггс-пользуют сортовую или профильную заготовку, при ЛР.СТОВОЙ штамповке заготовкой является металл в виде листа. Методами объемной шта ч1Повки изготавливают заготовки сложной конфигурации (шестерни, коленчатые валы, кронштейны, рычаги и другие детали для машиностроения). Для листовой штамповки характерно получение различных корпусных изделий (деталей обшивки и корпуса легковых и грузовых автомобилей, гнутых [c.345]
На рис. 4.16 и 4.17 приведены два примера эффективного применения САПР/АПП в процессе производства механических деталей и целостных изделий. На первом из рисунков показана в двух видах одна и та же деталь из листового металла слева изображена деталь в готовом виде, прюшедшая операции штамповки и формовки. Одна из трудностей изготовления подобных деталей связана с обеспечением необходимой точности раскроя листа металла на плоские детали требуемых размеров и формы, с тем чтобы заданные размерные характеристики готовой детали не нарушались в результате сворачивания выкройки в объемное тело. И дело здеа> не только в сложных геометрических очертаниях, но и в том, что исходная заготовка должна иметь некоторый припуск на обработку в операциях сгибания. В составе САПР/АПП имеются специальные программные средства, предназначенные для выполнения необходимых вычислений при определении размеров выкройки детали. В нашем примере такая выкройка показана на рис. 4.16 справа. [c.91]
mash-xxl.info
Штамповка - это... Что такое Штамповка?
Объёмная Ш. (или Ш. сортового металла) по сравнению с ковкой позволяет получать поковки более сложной конфигурации, требующие значительно меньшей обработки резанием для окончат. оформления детали. При объёмной Ш. течение металла ограничивается стенками полости штампа, что вызывает увеличение сопротивления деформированию тем в большей степени, чем сложнее конфигурация поковки. Нагрев заготовки позволяет примерно в 10—15 раз снизить сопротивление деформированию, а также повысить пластичность металла. Холодная Ш. сортового металла применяется для изготовления небольших деталей — массой менее 1 кг, горячая — для деталей массой 1,5―2 т; более тяжелые поковки изготовляются ковкой. Границы между этими процессами изменяются по мере совершенствования кузнечно-прессового оборудования и увеличения развиваемого ими усилия деформирования. Поскольку стоимость штампов наряду со стоимостью металла заготовки является основной составляющей себестоимости поковки, применение объёмной Ш. экономически выгодно при серийном производстве.
Объёмная Ш. сопровождается потерями металла с удаляемым заусенцем (облоем). Меньшие отходы даёт Ш. в закрытых штампах, однако удельные нагрузки в них больше, чем в открытых, что приводит к уменьшению стойкости штампов. Снижение отходов при Ш. в открытых штампах достигается предварительной обработкой заготовки в заготовит. ручьях, ковочных вальцах, использованием заготовок, приближающихся по форме к поковке, а также выбором рациональной формы канавки для заусенца. При горячей Ш. поверхность заготовки окисляется, образуя слой окалины, что также ведёт к потерям металла; потери металла с окалиной сокращаются при безокислительной нагреве в пламенных печах (с защитной атмосферой) или скоростном нагреве в индукционных нагревательных установках. Применение высокоскоростной Ш. (скорость подвижных частей молота 10—25 м/сек) позволяет уменьшить охлаждение заготовки в процессе деформирования и получать детали с тонкими ребрами. Для уменьшения охлаждения заготовки применяют также изотермическую Ш. (главным образом цветных металлов), при которой штамп нагревают до температур, близких к ковочным. Начинает применяться совмещение литья с горячей Ш., при котором отливается заготовка, близкая по форме к поковке; после застывания металла и охлаждения до ковочных температур заготовку штампуют в открытых или закрытых штампах. Ш. улучшает механические свойства литой заготовки; образующиеся отходы сразу поступают на переплавку.
При листовой Ш. заготовкой служит лист, полоса или лента. Применяется листовая Ш. для изготовления плоских и пространственных (в т. ч. сложных) деталей, у которых толщина значительно меньше др. размеров — обычно менее 10 мм. Заготовки большей толщины обычно штампуют с нагревом до ковочной температуры (горячая листовая Ш.). При листовой Ш. (особенно холодной) отделочная обработка деталей резанием, как правило, не требуется. Листовая Ш. рациональна в производствах с различной серийностью.
В мелкосерийном производстве применяются особые способы Ш.: Ш. эластичными средами (жидкостью, резиной, полиуретаном и т.п.), импульсная Ш., использующая энергию ударной волны в жидкости (взрывная и электрогидравлическая Ш.) или действие мощных быстроменяющихся магнитных полей (электромагнитная Ш.). С целью увеличения допустимого формоизменения заготовки иногда применяется Ш. с дифференцированным нагревом. В этом случае деформируемая часть заготовки нагревается за счёт контакта с нагретым инструментом или при прохождении через неё электрического тока. Рациональное распределение температур в заготовке и соответственно механических свойств металла значительно повышает допустимое формоизменение заготовки.
Для Ш. используются разнообразные машины: Молоты, кривошипные прессы (См. Кривошипный пресс), горизонтально-ковочные машины (См. Горизонтально-ковочная машина), гидравлические прессы (См. Гидравлический пресс), кузнечно-штамповочные автоматы (См. Кузнечно-штамповочный автомат) и др. В крупносерийном производстве для Ш. применяют автоматы и автоматизированные линии, а также всевозможные загрузочные и манипулирующие устройства (включая промышленных роботов), позволяющие существенно повысить производительность труда.Лит.: Малов А. Н., Технология холодной штамповки, 4 изд., М., 1969; Брюханов А. Н., Ковка и объёмная штамповка, 2 изд., М., 1975.
Е. А. Попов.
dic.academic.ru
Способ изготовления деталей точной объемной штамповкой
Изобретение относится к машиностроению, а именно к объемной штамповке лопаток для турбомашин. Способ изготовления деталей способом точной объемной штамповки включает изготовление и наладку первого средства инструментальной оснастки для объемной штамповки, объемную штамповку деталей посредством вышеупомянутого средства инструментальной оснастки, при этом вышеупомянутые детали имеют заданную избыточную толщину, и чистовую обработку деталей. Способ дополнительно содержит реализацию цифровой модели поверхности вышеупомянутого первого средства инструментальной оснастки, восстановление вышеупомянутого средства инструментальной оснастки или изготовление нового средства инструментальной оснастки по вышеупомянутой цифровой модели после выполнения объемной штамповки определенного количества деталей. Детали подвергают чистовой обработке непосредственно после операции объемной штамповки, при этом вышеупомянутая операция обработки включает операцию механической полировки. Обеспечивается снижение затрат на чистовую обработку и получение строго идентичных деталей. 9 з.п. ф-лы, 3 ил.
Настоящее изобретение относится к способу точной объемной штамповки металлических деталей и, в частности, сложных деталей, например крупногабаритных лопаток для турбин.
При изготовлении металлических деталей способы объемной штамповки предпочтительным образом применяют в том случае, когда необходимо обеспечивать поглощение деталями значительных нагрузок при работе. Одним из примеров таких деталей являются лопатки компрессора или нагнетателей турбореактивного двигателя, в которых внутренние нагрузки создаются, в основном, за счет воздействия на них вибраций и центробежных сил.
Операция объемной штамповки заключается в том, что осуществляют пластическую деформацию металлической болванки путем ударного воздействия или путем наложения давления. Процесс обычно состоит из нескольких операций, при которых осуществляют последовательную формовку заготовок, постепенно становящихся все более близкими к готовой детали. При необходимости операцию объемной штамповки детали завершают операцией калибровки, приводящей к получению более точных форм.
Для лопаток компрессора, например, изготовленных из титана, способ обработки содержит следующие операции: высадки, экструдирования и штамповки из прутков.
Перед операцией высадки выполняют подготовку металлических прутков, включающую нанесение на них эмалевого покрытия. Это покрытие представляет собой покрытие на основе стекла, которое предназначено для облегчения прохождения материала в средства инструментальной оснастки. Оно также служит в качестве теплоизоляции, обеспечивая поддержание надлежащей температуры во время перемещения из печи в пресс и предотвращение любых тепловых ударов при соприкосновении детали со средствами инструментальной оснастки. Его функция также состоит в том, что оно обеспечивает защиту детали от окисления. Согласно предпочтительному варианту осуществления настоящего изобретения покрытие наносят на детали способом электростатического напыления перед их загрузкой в печь.
Параллельно с этим производят смазку внутренней поверхности обеих оболочковых форм или инструментальной оснастки для высадки. Операция высадки заключается в том, что посредством пуансона осуществляют надавливание на конец прутка, нагретого до температуры, обеспечивающей хорошую пластичность, в направлении к внутренней части полости, образованной двумя оболочковыми формами. В том случае, когда для получения надлежащей формы детали необходимо несколько операций, операцию высадки выполняют путем выполнения нескольких последовательных операций с использованием необходимых средств инструментальной оснастки. Например, этот технологический процесс может быть целесообразен для формовки замков лопаток компрессора, а также, при необходимости, их лопастей.
Между каждыми операциями высадки необходимо обеспечивать удаление покоробленного эмалевого покрытия, а также образовавшейся окалины, с использованием соответствующих ванн перед нанесением нового слоя эмали.
В соответствии с типом детали, например для лопаток компрессора, но не для лопаток нагнетателя, перед операцией высадки выполняют операцию экструдирования. Эта операция заключается в том, что производят протягивание металлической заготовки через экструзионную головку, профиль которой соответствует профилю создаваемого изделия.
После выполнения предварительной объемной штамповки деталей подобным способом осуществляют их объемную штамповку, придавая им заданные формы, посредством штампов для объемной штамповки.
Эта операция механической объемной штамповки заключается в том, что создают деталь путем принудительного воздействия на ее заготовку таким образом, чтобы она заполнила собой за счет ударного воздействия или приложения давления оттиск, выгравированный в штампе для объемной штамповки, соответствующем форме получаемой детали. При использовании титана, предел текучести которого сильно зависит от температуры, объемную штамповку выполняют при нагреве вплоть до определенного предела, определяемого изменением структуры материала, которое приводит к изменению его механических свойств.
Для лопатки компрессора или лопатки нагнетателя известная операция формовки содержит две операции штамповки:
операцию штамповки с приданием заранее заданной формы, посредством которой осуществляют предварительную формовку замка лопатки и, при необходимости, лопасти лопатки и начинают сплющивание лопатки, превращая форму прутка из округлой в сплющенную;
операцию чистовой штамповки, завершающую цикл объемной штамповки, при которой осуществляют деформацию материала и доводку детали, делая ее настолько близкой по форме к окончательной геометрической форме, насколько это возможно, перед механической обработкой.
Операции штамповки выполняют на гидравлических или на винтовых прессах с предварительным нагревом их штампов для объемной штамповки. При таких условиях время проковки является относительно коротким во избежание слишком быстрого остывания детали и перегрева штампа для объемной штамповки за счет теплообмена между деталью и вышеупомянутым штампом, поскольку температура средств инструментальной оснастки должна отличаться от температуры детали. Кроме того, вследствие высокого уровня механических нагрузок, которым они подвергаются за счет соприкосновения с деталью, на выгравированное клише штампа для объемной штамповки наносят смазочный материал для замедления процесса охлаждения детали, для более легкого прохождения материала и для снижения нагрузок, возникающих при объемной штамповке.
После выполнения объемной штамповки детали осуществляют ее механическую обработку и полировку до достижения окончательных размеров. Такая операция является необходимой вследствие избыточной толщины, остающейся после объемной штамповки. На самом деле, выгравированное клише штампа для объемной штамповки задают таким образом, чтобы оно обеспечивало избыточную толщину детали. Операции объемной штамповки, механической обработки и полировки позволяют получить после их выполнения готовую деталь, имеющую точную форму и требуемую чистоту поверхности.
Для деталей, в особенности выполненных из титана, полировка является важной операцией. Она предназначена для устранения дефектов, возникающих в результате операции объемной штамповки и способных вызывать развитие трещин.
Настоящее изобретение относится, прежде всего, к усовершенствованию таких средств инструментальной оснастки, как вышеописанные штампы для объемной штамповки и оболочковые формы. Существует потребность в усовершенствовании этих технологических операций с целью повышения экономической эффективности этого способа.
Известен способ изготовления деталей точной объемной штамповкой, содержащий изготовление и доводку первого средства инструментальной оснастки для объемной штамповки, объемную штамповку деталей посредством вышеупомянутого средства инструментальной оснастки, при этом вышеупомянутые детали имеют заданную избыточную толщину, чистовую обработку деталей и восстановление вышеупомянутого средства инструментальной оснастки или изготовление нового средства по модели поверхности вышеупомянутого первого средства после выполнения определенного количества деталей объемной штамповкой (см. SU 1006148 А, В23Р 6/00, 23.03.1983).
Согласно обычному способу время, требуемое для подготовки средств инструментальной оснастки, является достаточно продолжительным, поскольку последовательные операции повторной корректировки являются обязательными.
В действительности, оттиск штампа для объемной штамповки не точно совпадает по форме и размерам с необработанной деталью, получаемой способом объемной штамповки. Он отличается от нее "поправочными членами", которые обеспечивают компенсацию упругопластической деформации средств инструментальной оснастки во время цикла объемной штамповки. Авторам настоящего изобретения неизвестно то, каким образом можно осуществить точное прогнозирование этих поправочных членов, и, следовательно, необходимо выполнять повторную корректировку штампа для объемной штамповки в дополнение к проведению измерений полученных испытательных образцов. При так называемой "точной" объемной штамповке значения избыточной толщины являются малыми, равными, например, 0,8 мм, поэтому готовая деталь может быть получена путем полировки необработанной детали с использованием шлифовальной ленты или, при необходимости, в особенности в том случае, если деталь выполнена из титана, - посредством совокупности операций химической обработки и полировки с использованием шлифовальной ленты. Этот способ применяют для аэродинамической поверхности лопаток.
Следовательно, создание штампа для точной объемной штамповки является длительным и дорогостоящим процессом, поскольку для этого требуется выполнение многочисленных операций повторной корректировки, чередующихся с операциями проверки деталей, полученных способом объемной штамповки.
Операция повторной корректировки не может быть выполнена быстро, поскольку для этого необходимо осуществлять контроль процесса объемной штамповки при каждой операции нагрева и при каждой операции монтажа средств инструментальной оснастки на прессе, изготовление нескольких деталей, калибровку и контроль этих деталей. Кроме того, пробные детали обычно не используют; в большинстве случаев они попадают в отходы. Следует отметить, что во время выполнения операций проверки и повторной корректировки такие средства, как пресс, конвейер для штампов для объемной штамповки, контрольно-измерительная аппаратура, являются недоступными для выпуска продукции.
Также следует отметить, что согласно этому обычному способу практически невозможно получить два идентичных образца средств инструментальной оснастки, например штампов для объемной штамповки или оболочковых форм.
Эта недостаточная точность выполнения средств инструментальной оснастки приводит к недостаточной точности изготовления изделий с использованием вышеупомянутых средств инструментальной оснастки.
После того, как выполнена наладка оборудования для штамповки, то есть после того, как необработанные пробные детали, полученные способом объемной штамповки, приобрели требуемую форму и размеры, такой штамп для объемной штамповки может быть введен в эксплуатацию для изготовления серийных деталей. При работе происходит постепенное ухудшение качества штампа, и, например, после изготовления 1000-5000 деталей, что зависит от обстоятельств, возникает необходимость в восстановлении штампа или в использовании другого штампа.
Согласно первому способу, восстановление штампа для объемной штамповки заключается в том, что осуществляют перезаполнение тех зон, из которых был сорван материал, а также механическую обработку и полировку нового оттиска. Согласно второму способу, восстановление оттиска осуществляют полностью путем механической обработки после удаления азотированного слоя и удаления материала на толщину в несколько миллиметров. Этот способ именуют повторной смывкой. При восстановлении штампа или изготовлении нового штампа требуется выполнение тех же самых наладочных операций, что и при наладке исходного штампа. Следовательно, они также являются длительными и дорогостоящими.
Чистовая обработка путем полировки абразивной лентой на пятикоординатном или на шестикоординатном станке хорошо подходит для деталей сложной формы, например для аэродинамических поверхностей лопатки. В отличие от операции механической обработки, например, способом вальцевания чистовая обработка с использованием абразивной ленты обеспечивает при каждом проходе удаление материала заранее заданной толщины, причем вышеупомянутая толщина возрастает при увеличении скорости абразивной ленты и давления, оказываемого лентой на деталь, и вышеупомянутая толщина уменьшается при увеличении поступательной скорости ленты относительно детали. Следовательно, форма и размеры детали после прохода абразивной ленты непосредственно зависят от формы и размеров детали перед вышеупомянутым проходом.
Это не вызывает никаких проблем с первыми деталями, созданными посредством штампа для объемной штамповки, поскольку все они являются идентичными. Однако по мере продолжения объемной штамповки может быть замечено ухудшение качества штампа (износ, пластическая деформация и т.д.).
Производят выборочный контроль деталей для их систематической проверки. В том случае, когда размеры детали достигают заданного порогового значения ухудшения качества, осуществляют восстановление средств инструментальной оснастки или изготовление новых средств инструментальной оснастки. Для деталей, полученных посредством новых штампов или восстановленных штампов, может потребоваться несколько проходов чистовой обработки, между которыми выполняют измерения, поэтому они являются строго идентичными тем деталям, которые были получены посредством первого штампа. Эта схожесть результатов является особенно важной при изготовлении наборов лопаток на этапе производства ротора турбореактивного двигателя.
Проблема, которую следует решить, состоит в обеспечении снижения затрат на чистовую обработку и в получении строго идентичных деталей при изготовлении их способом объемной штамповки с использованием различных штампов для объемной штамповки. Эта проблема также состоит в том, чтобы избежать изготовления деталей, поступающих в отходы вследствие того, что они не удовлетворяют техническим требованиям, а это в случае точной объемной штамповки является важным критерием оценки качества технологического процесса.
Согласно настоящему изобретению, эта проблема может быть решена посредством процесса изготовления деталей способом точной объемной штамповки, содержащего следующие операции:
изготовление и доводка первого средства инструментальной оснастки для объемной штамповки,
объемная штамповка деталей посредством вышеупомянутого средства инструментальной оснастки, при этом вышеупомянутые детали имеют заданную избыточную толщину, и
чистовая обработка, а этот способ отличается тем, что это также содержит следующие операции:
реализация цифровой модели поверхности вышеупомянутого первого средства инструментальной оснастки,
выполнение объемной штамповки деталей,
после выполнения объемной штамповки определенного количества деталей осуществляют восстановление вышеупомянутого средства инструментальной оснастки или изготовление нового средства инструментальной оснастки по вышеупомянутой цифровой модели.
В преимущественном варианте детали подвергают чистовой обработке непосредственно после выполнения объемной штамповки, при этом вышеупомянутая операция обработки содержит операцию механической полировки.
В частности, в том случае, когда детали выполнены из титана, операция чистовой обработки содержит совокупность операций механической полировки и химической обработки.
Операция химической обработки заключается в химическом растворении сплавов титана. Степень удаления материала определяется временем выдержки деталей.
Способ согласно настоящему изобретению отличается тем, что:
а) Первый штамп для объемной штамповки налаживают таким образом, чтобы необработанная деталь, получаемая способом объемной штамповки, имела избыточную толщину, подлежащую удалению за счет операции механической полировки и/или химической обработки за один проход или, по меньшей мере, без значительного числа проходов, требующих большого количества операций повторной корректировки, выполняемых вручную.
б) После наладки первого штампа для объемной штамповки осуществляют сбор данных о местоположении заданного количества точек на поверхности оттиска в цифровом виде и производят оцифровку модели вышеупомянутой поверхности.
с) Операция изготовления нового сменного штампа для объемной штамповки содержит операцию чистовой механической обработки, выполняемой таким образом, чтобы цифровая модель его оттиска была идентичной цифровой модели оттиска первого штампа для объемной штамповки.
В предпочтительном варианте операция полировки является автоматизированной за счет применения абразивных лент. В преимущественном варианте используют станок, снабженный системой с контактным шкивом, приводящим в движение абразивную ленту. Этот тип механизма имеет преимущество, заключающееся в том, что он позволяет контролировать количество удаляемого материала и обеспечивать требуемую чистоту поверхности на основании простых параметров станка, таких как, например, нагрузка на деталь, прикладываемая контактным шкивом, рабочая скорость ленты на контактном шкиве, а также относительная скорость смещения шкива относительно обрабатываемой детали.
Этот технологический процесс позволяет осуществлять управление удалением избыточного материала и значительно уменьшить количество последовательных операций чистовой обработки после объемной штамповки. Обеспечено гарантированное получение геометрической конфигурации детали, а также чистоты ее поверхности после чистовой обработки при минимальном количестве операций повторной корректировки, выполняемых вручную, причем такая операция повторной корректировки может вообще отсутствовать.
Другие отличительные признаки и преимущества станут очевидными из приведенного ниже описания способа, предложенного в настоящем изобретении, со ссылкой на чертежи, на которых изображены:
фиг.1 - штамп для объемной штамповки,
фиг.2 - оболочковая форма для высадки,
фиг.3 - ленточный полировальный станок.
Из фиг.1 и 2 видно, что средство инструментальной оснастки, используемое в способе объемной штамповки согласно настоящему изобретению, вне зависимости от того, содержит ли оно штамп 20 для объемной штамповки лопаток или оболочковую форму 30 для высадки, является сложным по форме и дополнительно:
содержит зоны искривления и закручивания, имеющие
большое искривление,
очень малое искривление,
являющиеся глубокими и узкими, например, глубиной 100 мм и шириной 20 мм в нижней части;
состоит из плоскостей, цилиндров, конусов и сопряжений между частями поверхностей и имеет существенные изменения по высоте между обеими сторонами средства инструментальной оснастки.
Происходит постепенное ухудшение качества штампа для объемной штамповки, в особенности из-за износа оттиска и из-за пластической деформации. Когда степень ухудшения качества достигает установленного заранее порогового значения и полагают, что необходимо произвести обновление средства инструментальной оснастки, выполняют восстановление вышеупомянутого средства или изготавливают новое средство инструментальной оснастки на основании сохраненной информации о том средстве инструментальной оснастки, наладка которого была произведена ранее. Тем самым обеспечивают непрерывность способа.
После наладки первого средства инструментальной оснастки в соответствии с окончательными размерами осуществляют реализацию цифровой модели таких средств инструментальной оснастки. Сами средства реализации этой цифровой модели поверхности инструментальной оснастки являются известными и доступными для приобретения на рынке.
Наиболее часто используемыми в промышленности изделиями являются контактные датчики, которые могут входить в состав трехкоординатных измерительных машин (ММТ). Вследствие того, что их торцы имеют сферическую форму, результаты, полученные посредством подобных датчиков, должны быть подвергнуты пересчету с введением поправок на радиус.
Среди бесконтактных датчиков наиболее современными являются датчики на основе оптических способов с одним или с несколькими источниками лазерного излучения или на основе оптических способов без использования лазеров. В обоих из них используют принцип измерения на основе тригонометрии и, в частности, на основе триангуляции.
В варианте способа с использованием источников лазерного излучения деталь освещают источником когерентного света, обычно лучом лазера, а посредством одной или нескольких ПЗС-камер (камер на основе приборов с зарядовой связью) наблюдают изображение под углом, который обычно отличается от угла испускания излучения. После этапа калибровки камер производят вычисление координат точек объекта, исходя из координат его изображения на ПЗС-матрице камеры.
В варианте способа без использования лазера его принцип основан на проецировании на деталь регулярной сетки, сетки интерференционных полос с последующим вычислением координат точек на поверхности объекта способом триангуляции.
После выбора датчика нужно определить стратегию оцифровки трехмерных данных, которая состоит в следующем:
находят одно или несколько положений датчика (датчиков), которые позволяют реализовать цифровую модель всех поверхностей детали, к которым должен быть осуществлен доступ,
исходя из вышеупомянутого результата производят выбор плотности множества точек в соответствии с выполняемой впоследствии задачей, которой является, например, быстрый поиск прототипа, восстановление поверхности или визуализация.
Для всех средств инструментальной оснастки, используемых для объемной штамповки, требуется точность сбора данных, например, порядка 0,02 мм.
При необходимости, в соответствии со сложностью геометрической конфигурации некоторых частей поверхности, вслед за этим выполняют операцию восстановления геометрической конфигурации поверхности. Такая операция может быть выполнена с использованием средства обработки данных, которое является известным для специалиста в данной области техники.
Прежде всего, осуществляют сбор данных о множестве точек, полученных путем оцифровки. В соответствии с качеством этого множества точек может возникнуть необходимость в применении к ним фильтра, назначение которого состоит в ослаблении множества малых локальных отклонений с одновременным удалением точек, имеющих большие отклонения, ошибок измерений и т.д.
Осуществляют восстановление, исходя из этого обработанного множества:
Для опорных зон (плоскостей, цилиндров, сфер) восстановление формы осуществляют автоматически.
В случае неудачного исхода этой операции осуществляют восстановление поверхности, "наилучшим образом" покрывающей совокупность выбранных точек, очерченных ее границами. Последними могут являться границы уже восстановленных элементов, кривые в виде графиков, построенных по множеству точек, теоретических элементов. Программное обеспечение позволяет после завершения восстановления каждой площади производить анализ всей восстановленной поверхности (максимальное отклонение, максимальное расстояние между границами двух соседних площадей…). Этот анализ предоставляет оператору возможность видоизменять параметры восстановления (математически заданные параметры, натяжение поверхности, кривизну границ…).
После создания цифровой модели ее сохраняют в виде файла формата CAD (автоматизированного проектирования, АП) для импорта в среду автоматизированного производства, АП (САМ), для создания производственной стратегии, а затем - в цифровую программу на станке, например на высокоскоростном станке типа UHS.
Эту программу затем используют для изготовления новых средств инструментальной оснастки, штампов для объемной штамповки, поэтому они являются строго идентичными идеальному исходному средству инструментальной оснастки.
В том случае, когда средство инструментальной оснастки получено путем "повторной смывки", или в случае новых средств инструментальной оснастки проверку производят путем сравнения CAD-модели и идеального средства инструментальной оснастки с множеством точек, полученных путем оцифровки изготовленных средств инструментальной оснастки.
Ниже приведено описание способа чистовой обработки после абразивной обработки детали посредством шестикоординатного полировального станка.
Осуществляют контроль геометрической конфигурации детали способом многомерного контроля и производят повторную компенсацию толщины и геометрических форм по всей лопатке посредством совокупности операций маскирования "слабых мест" с использованием клейкой ленты и химической обработки.
Затем удаляют избыточную толщину материала и создают требуемую конечную чистоту поверхности лопатки на заданной плоскости путем автоматизированной полировки на шестикоординатных полировальных станках. Ниже приведено описание способа согласно фиг.3, на которой показан шестикоординатный станок промышленного типа.
Станок содержит станину 1 с держателем 2 деталей, например лопатки компрессора, которую удерживают горизонталью вдоль ее главной оси посредством механического или гидравлического фланцевого устройства. Первый двигатель 4 обеспечивает положение детали по углу поворота (ось U вращения) вокруг ее главной оси. Второй двигатель 6 обеспечивает смещение держателя детали вдоль оси (х) поступательного перемещения. Третий двигатель 8 приводит в движение абразивную ленту, установленную на контактном шкиве 10, натяжение которой обеспечивают посредством системы роликов.
Кроме того, ось вращения шкива 10 расположена таким образом, что может совершать поступательное перемещение вдоль двух осей (y и z), перпендикулярных к первой оси х, и может поворачиваться вокруг обеих соответствующих им осей V и W вращения.
Контактную поверхность шкива постоянно удерживают в таком положении, чтобы она была расположена по касательной к поверхности детали.
Согласно одному из вариантов осуществления настоящего изобретения используют шкив, имеющий ширину 25 мм и наружный диаметр 120 мм. Поверхность достаточно твердого покрытия снабжена канавками, поскольку его твердость по Шору равна 65.
Операция полировки заключается в том, что деталь перемещают вдоль оси х и поворачивают вышеупомянутую деталь вокруг ее оси. Шкив постоянно удерживают таким образом, чтобы он соприкасался с поверхностью детали по касательной. К шкиву прикладывают давление, задаваемое давлением, приложенным посредством цилиндра, задают скорость ленты для удаления контролируемого количества материала с учетом скорости врезной подачи детали относительно шкива.
После вывода детали из полировального станка она готова для механической обработки замка лопатки и, при необходимости, лопасти лопатки, которая удовлетворяет требованиям по геометрической конфигурации, а также по чистоте поверхности.
1. Способ изготовления деталей точной объемной штамповкой, включающий изготовление и доводку первого средства (20,30) инструментальной оснастки для объемной штамповки, объемную штамповку деталей посредством вышеупомянутого средства инструментальной оснастки, при этом вышеупомянутые детали имеют заданную избыточную толщину, чистовую обработку деталей и восстановление вышеупомянутого средства инструментальной оснастки или изготовление нового средства по модели поверхности вышеупомянутого первого средства после выполнения определенного количества деталей, отличающийся тем, что способ дополнительно включает реализацию цифровой модели поверхности вышеупомянутого первого средства (20, 30) инструментальной оснастки и восстановление вышеупомянутого средства инструментальной оснастки или изготовление нового средства (20, 30) инструментальной оснастки по вышеупомянутой цифровой модели.
2. Способ по п.1, отличающийся тем, что детали подвергают чистовой обработке непосредственно после операции объемной штамповки, при этом вышеупомянутая операция обработки включает операцию механической полировки.
3. Способ по п.1, отличающийся тем, что вышеупомянутая операция чистовой обработки включает операцию химической обработки.
4. Способ по п.1, отличающийся тем, что для определения момента времени, в который следует выполнить восстановление или изготовление нового средства (20, 30) инструментальной оснастки, осуществляют контроль деталей, полученных способом объемной штамповки.
5. Способ по п.1, отличающийся тем, что проводят наладку средства (20, 30) инструментальной оснастки, включающую сбор цифровых данных о местоположении заданного количества точек на поверхности средства инструментальной оснастки, сравнение местоположения вышеупомянутых точек с цифровой моделью и исправление поверхности вышеупомянутого средства инструментальной оснастки.
6. Способ по п.5, отличающийся тем, что сбор данных о точках на поверхности средства инструментальной оснастки осуществляют посредством бесконтактного оптического измерения.
7. Способ по п.5, отличающийся тем, что сбор данных о точках на поверхности средства инструментальной оснастки осуществляют в цифровом виде с использованием механического средства.
8. Способ по п.1, отличающийся тем, что дополнительно производят удаление вышеупомянутой избыточной толщины деталей посредством абразивной обработки.
9. Способ по п.8, отличающийся тем, что абразивную обработку осуществляют с использованием ленты, установленной на шкиве, который прижимают к поверхности детали, имеющей избыточную толщину.
10. Способ по п.9, отличающийся тем, что количество удаляемого материала с детали задают путем выбора давления шкива на поверхность, поступательной скорости ленты и скорости перемещения шкива.
www.findpatent.ru
Детали штамповкой - Энциклопедия по машиностроению XXL
За отдельными исключениями, связанными с конфигурацией или весом детали, штамповку ведут от прутка . [c.461]
Таким образом, очевидна целесообразность при заданной программе принять в качестве заготовки детали штамповку, изготовленную на горизонтально-ковочной машине. [c.19]
Для получения заготовок повышенной точности используют многократную штамповку в закрепленных штампах. В этом случае заготовку последовательно штампуют в двух-трех чистовых ручьях с обрезкой облоя. Каждый последующий ручей дает все большее приближение к формам и размерам готовой детали. Штамповка в открытых штампах неизбежно сопровождается потерей металла на образование облоя (до 20% от веса заготовки). [c.13]
В последнее время все более широкое распространение начинают получать толкающие конвейеры с программным управлением. Они мо гут транспортировать заготовки, полуфабрикаты, детали по заданной программе с автоматическим адресованием, по команде перфокарты, находящейся на нижней стороне тележки, к которой прикреплена серьга для подвешивания груза (например, листовой детали или поковки) или подвешена люлька, в которую загружаются мелкие детали (штамповки, поковки). Толкающий конвейер имеет два подвесных пути (рис. Vn.2), расположенных один под другим (или рядом). По верхнему пути движутся, как у обычного конвейера, тележки, к которым подвешена тяговая цепь, по нижнему — тележки с подвесками транспортируемых грузов, передвигаемых кулаками, соединенными с цепью шарнирно. Нижняя грузовая трасса представляет собой систему путей с переводными стрелками, разветвленную в зависимости от количества адресов для доставки грузов. [c.129]Масса детали, штамповки или поковки [c.393]
Затем проводят подготовительные операции, от которых во многом зависят качество покрытия и его эксплуатационные свойства. Порядок проведения подготовительных операций зависит от природы основного материала, способа изготовления детали (штамповка, резание, литье и т. д.), срока межоперационного хранения и характера загрязнения. [c.153]
Более высокие классы точности имеют самые большие допуски на изготовление. С такими классами точности изготовляются детали штамповкой, вытяжкой, литьем под давлением и в кокилях и т. П- [c.100]
На рис. 8 показано крепление тонкого щитка и угловой детали. Штамповка гнезд под винты усложняет изготовление. [c.48]
Выпуск свыше 250 шт. в сутки, заготовка детали — штамповка [c.19]
Любая машина, прибор состоят из д е т а л е й, соеди ненных между собой. Детали могут отличаться друг от друга по форме, размерам и технологическому процессу их изготовления. Одни детали изготовляют из листового материала, другие — из сортового и фасон кого проката или изделий-заготовок путем механической обработки третьи получают литьем, горячей штамповкой и т. д. [c.6]
Детали, имеющие форму тела вращения (валики, оси, штуцеры, втулки, пробки), обычно изображают горизонтально, т. е. параллельно основной надписи чертежа (рис. 12, а). Такое изображение обусловлено положением детали при ее обработке на станке. Независимо от способа получения заготовок (прокаткой, высадкой, горячей штамповкой, литьем, ковкой) эту группу деталей чаще всего обрабатывают точением на станках токарного типа. [c.19]
Для обозначения поверхностей, которые образуются без удаления слоя (литье, поковки, штамповки), поверхностей в состоянии поставки, без дополнительной обработки (детали из сортового материала, листов, труб, профилей, прутков). [c.124]
При чтении чертежей на изделия-заготовки необходимо иметь в виду, что для их изготовления обычно применяют только один технологический метод (литье или штамповку, ковку или прокат) в зависимости от формы деталей и других особенностей. При таких условиях шероховатость поверхностей и класс точности размеров обычно бывают постоянными для всех элементов детали. [c.150]
Детали, ограниченные поверхностями вращения, можно изготовлять из прутков, круглых заготовок литьем или горячей штамповкой, при этом облегчается изготовление металлической формы для литья, изготовление матриц и пуансонов, так как их формообразующие поверхности можно легко обработать. [c.159]
Симметричные детали, включающие призматические, пирамидальные и другие подобные элементы, могут быть получены литьем или горячей штамповкой. Плоскость разъема штампов или форм обычно совпадает с плоскостью симметрии самой детали. [c.159]
В серийном и массовом производствах детали, имеющие относительно толстые элементы, переводят на литье или горячую штамповку. [c.162]
При чтении чертежей аналогичных деталей, если в чертеже указана марка материала в общей форме, надо подумать о возможности изготовления этой детали из сортового материала. Для массового производства полный технико-экономический расчет может показать целесообразность перевода ее на горячую штамповку или литье. [c.179]Рассматривая типовые детали, полученные горячей штамповкой (рис. 135), и примерную схему их получения, можно отметить важные особенности их формы, а именно наличие плоскости, по которой пройдет разъем штампа, и возможность извлечения детали из штампа в направлении, перпендикулярном к этой плоскости. Оси всех выступающих цилиндрических, конических и других элементов (бобышек) располагаются перпендикулярно к этой же плоскости. [c.190]
На рис. 171 приведен чертеж детали, у которой имеются два ребра, полученные простым гибом, и одно сложное, полученное штамповкой с вытяжкой, ограниченное линейчатой поверхностью. Линейчатую поверхность здесь можно представить как след движущейся прямой линии, концы которой касаются двух направляющих — плоских кривых линий. [c.229]
Согласно ГОСТ 2.109—73 детали, которые изготовляют из полуфабрикатов, например из листового материала путем простой отрезки, вырубки, штамповки и т. п., могут выполняться без отдельных черте- [c.285]
На детали сложной формы, полученные из листового материала путем штамповки с вытяжкой, а также литые, точеные, фрезерованные и др., составляют отдельные чертежи. [c.290]
Форма изображенной на чертеже детали обусловливает и особенности выполнения работы по ее чертежу. Так, для деталей, изготовляемых из изделий-заготовок, сортаментного материала, а также для ремонтных изделий, приходится выяснять по чертежу элементы, подлежащие дополнительной обработке, их форму, размеры. Для деталей литых, пластмассовых, горячей штамповки надо предварительно спроектировать и изготовить модель, форму и т. п. с учетом усадки материала. Для деталей, изготовляемых из листового материала, предварительно изготовляют плоские развертки или заготовки, приспособления, штампы. С целью экономии материала необходимо по чертежу решать вопрос о минимальных габаритных размерах заготовок деталей. [c.31]
На рис. 116, а показан чертеж детали из листового материала, представляющей тело вращения. Схема получения детали из листовой заготовки ротационной вытяжкой показана на рис. 116, б. Для таких деталей при их изготовлении на давильном станке заготовкой служат круглые доски, диаметр которых определяется по формулам, полученным опытным путем. В массовом производстве такие типовые детали целесообразно изготовлять штамповкой в один или несколько проходов. [c.152]
Заготовка детали штамповка из хромоиикелевой ста марки 18ХНВА с пределом прочности -80- -90 и твердостью 232 — 25i Нд [c.496]
Способ комбинированной ковки и горячей штамповки заключается в разделении процесса на предварительную свободную ковку и последующую штамповку, выполняемую на кривошипном прессе. Этот способ позволяет уменьшить расход металла на 40—50% по сравнению со свободной ковкой и применяется для изготовления поковок массой не более 70 кг в условиях мелкосерийного производства. При изготовлешш средних и мелких поковок простой формы используют подкладные штампы. Более сложные поковки обрабатывают в закрепленных штампах. Это наиболее распространенный способ получения штампованных заготовок в серийном и массовом производстве. Для получения заготовок повышенной точности используют многократную штамповку в закрепленных штампах. В этом случае заготовку последовательно штампуют в двух-трех ручьях с обрезкой облоя. Каждый последующий ручей обеспечивает все большее приближение форм и размеров заготовки к формам и размерам детали. Штамповка в открытых штампах сопровождается потерей металла на образование облоя (до 20% массы заготовки). [c.33]
При проектировании детали, намеченной к изготовлению горячей штамповкой, и составлении ее рабочего чертежа конструктор должен наряду с эксплуатационными требованиями к детали учитывать и технологические требования к ее конструкции, обе-спечиваюш,ие возможность изготовления детали штамповкой. [c.209]
Из листовой меди толш,иной 0,1...0,3 мм хорошо получаются детали штамповкой в свинец. В основном это обтекатели неуби-рающегося шасси. Медные и латунные трубочки различных диаметров понадобятся при изготовлении различных выхлопных патрубков, колодцев оружия и т. п. [c.8]
Материал, выбранный для изготовления детали, должен обосновываться подетальным расчетом на прочность. В основу расчета берут действующие нагрузки и механические свойства материала. В зависимости от формы детали может быть назначен один или несколько технологических процессов ее изготовления, поэтому при выборе материала важное значение приобретают и технологические свойства материала обрабатываемость резанием, свариваемость, уп-рочняемость при термообработке, линейные свойства, способность к ковке, штамповке (пластические свойства и зависимость их от температуры нагрева), способность к гибке, паянию и т. д. [c.117]
На рис. 111 показана деталь, ограниченная плоскостями, изготовленная литьем, например, из стали 45Л. Эту деталь можно также изготовить из листа путем фрезерования. В массовом производстве ее легко перевести на штамповку или точное литье. Деталь имеет более сложную призматическую форму, поэтому необходимы два изображения. Понять форму детали и ее размеры нетрудно. В тех случаях, когда на чертеже детали призматической формы отсутствует третье изображение, углы между гранями следует считать прямыми радиусы скруг-лення их кромок обычно указывают в технических требованиях. [c.164]
На рис. 114, а показан чертеж детали, требующей отштамповки углубления конической формы, пробивки отверстий и вырубки по контуру. Эти операции можно выполнять на штампе. На рис. 114, б показана схема штамповки детали из полосовой заготовки на механических прессах. Сначала пробивают отверстия и отштамповывают углубление, затем производят вырубку по контуру. За каждый ход пресса получают одну деталь, развертки для таких деталей не требуются. [c.170]
На рис. 138 показан чертеж другой детали, сконструированной с учетом изготовления ее горячей штамповкой. В отличие от предыдущей I главное изображение детали, представляет фигуру несимметричную. При проектировании штампа важно определить наивыгоднейшие габаритные размеры этой фигуры с целью экономии металла (см. гл. VIII). [c.195]
mash-xxl.info
Suspend page
This Account Has Been Suspended
Your hosting account has been suspended. There are several reasons that might lead to this:
- Suspension due to non-payment of fees, account will be unsuspended automatically after payment for hosting.
- Your trial term of web hosting has expired.
- Suspension due to a violation of a rule or policy.
You can resolve all issues in yours billing account, and if you didn't find the response yor can also open ticket in Suport service.
If you have no opportunity to pay now you can take postponing on payment of a hosting for up to 14 days. To order postponing use the section in yours billing account "Postponing on a hosting".

Ваш хостинг-аккаунт заблокирован, причины могут быть следующие:
Все вопросы Вы можете решить в Вашем биллинг-аккаунте, а также открыть тикет в разделе Тех.поддержка, если не нашли ответа.
Если на данный момент у Вас нет возможности оплатить, Вы можете взять отсрочку на оплату хостинга сроком до 14 дней. Для оформления отсрочки воспользуйтесь разделом в Вашем биллинг-аккаунте "Отсрочка на хостинг".
dlja-mashinostroitelja.info