Термическая сварка. Сущность термитной сварки. Термическая сварка
Термическая сварка
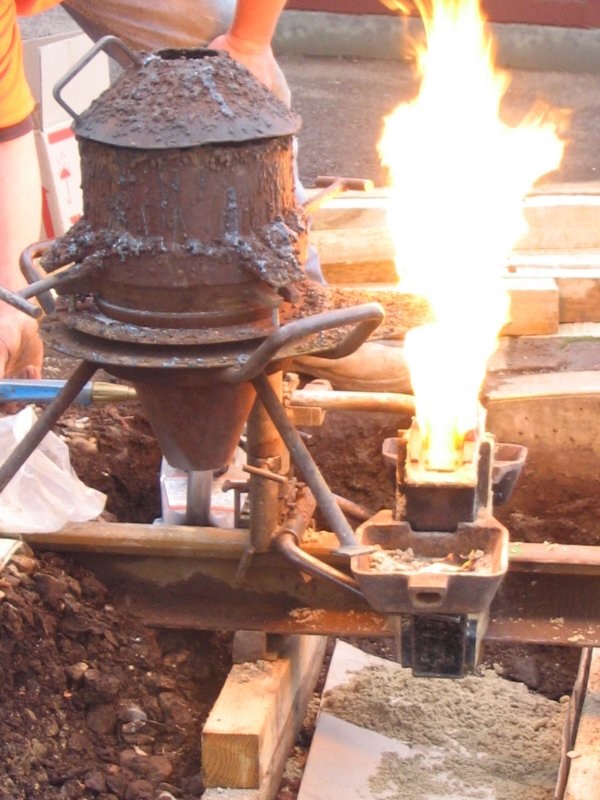
Под термической сваркой принято понимать соединение металлов, основывающееся на расплавлении кромок металла, в результате чего образуется соответствующая ванна, в которой металл соединяется на молекулярном уровне и позволяет выполнить прочный монолитный шов. Подобные технологии благодаря своей простоте и качеству соединения металлических элементов получили широкое распространение. К такому термическому классу принято относить лазерную, плазменную, газовую, дуговую технологию. Поговорим поподробнее о преимуществах и недостатках термической сварки, а также опишем ее распространённые классы.
Из преимуществ такой термической технологии можем выделить следующее:
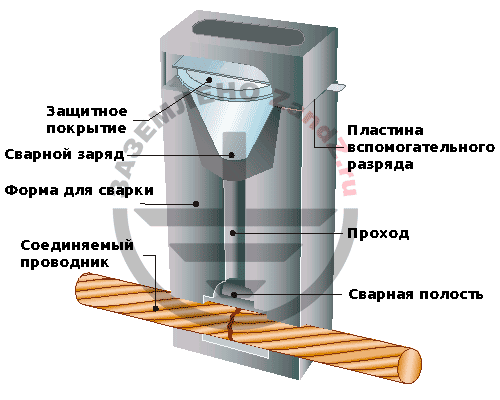
- Отличные показатели прочности соединения.
- Низкая трудоемкость работ.
- Невысокая себестоимость.
- Минимальный расход металла.
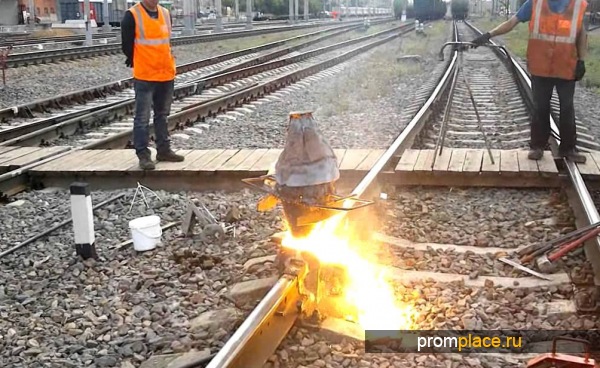
Если же говорить о недостатках, то можно отметить следующее:
- Неровности на поверхности заготовки и наличие оксидной пленки существенно ухудшает качество соединения.
- Термическая сварка возможна только с металлами, близкими по показателям тугоплавкости.
Термическое влияние сварки
Газовая термическая сварка подразумевает нагрев металла в зоне соединения при помощи газового пламени. Такая газовая горелка может использовать различный газ, который эффективно нагревает металл до его жидкого состояния, а после кристаллизации и затвердевания обеспечивается максимально прочное соединение. Газовые горелки позволяют оптимальным образом регулировать температуру пламени, что в свою очередь дает возможность работать с различными по тугоплавкости материалами. Газовая сварка может выполняться как по классической технологии термической обработки металлов, так и с использованием дополнительного присадочного материала. Такие электроды расправляются одновременно с соединяемыми металлами, кристаллизуются и на молекулярном уровне соединяют материалы. Следует учитывать свойства конкретных металлов, сплавы которых входят во взаимодействие друг с другом.
Из преимуществ данной технологии можем отметить простоту данной работы и отличное качество соединения. В то же время необходимо отметить, что данная технология подразумевает использование специального оборудования, в том числе баллонов со сжатым газом, поэтому к проведению такой работы с газом допускаются только сертифицированные специалисты, имеющие большой опыт работы с такими горелками на газу. Также должное внимание необходимо уделить качеству используемого оборудования.
Полуавтоматическая термическая сварка: технология
Использование данной технологии подразумевает использование специальной проволоки, которая с помощью автоматической системы аппарата подается в рабочую зону, где быстро расплавляется и позволяет обеспечить прочность соединения. В качестве защитного газа может использоваться аргон и СО2. Основное назначение такого газа — это защита сварочной ванны от воздействия воздуха, который может существенно ухудшить качество соединения металлов.
При полуавтоматической технологии используется специальное оборудование, которое позволяет быстро расплавлять кромки. При этом данная технология отличается простотой и может выполняться как профессиональными специалистами, так и обычными домовладельцами при необходимости им выполнить прочное соединение элементов. Даже обычные домовладельцы смогут с использованием таких полуавтоматических аппаратов провести сварку, обеспечив максимальное качество выполненного соединения.
Аргонодуговая сварка
Такой вид термической сварки подразумевает использование вольфрамовых электродов, которые заправляются в горелку. При выполнении соединения такой электрод с помощью автоматической системы подается в пламя горелки, расплавляется и стекает в шов, гарантируя соединение на молекулярном уровне. Для защиты сварочной ванны от негативного воздействия кислорода используется аргон, который предотвращает появление окислительной пленки. Аргон поступает из подключенного к горелке баллона со сжатым газом. Регулируют подачу аргона при помощи редуктора, выставляя его на определённое положение, в зависимости от конкретной разновидности металлических элементов.
svarkagid.com
Термическая сварка. Сущность термитной сварки.
Сварка является одним из основных способов получения соединения неразъемного. В большинстве случаев, она выступает единственным способом, с помощью влияния которого можно получить такое прочное соединение. Создать максимально приближенные заготовки и по размерам и по формам можно с помощью сварки. Вы можете создать даже такие конструкции, которые не будут отличаться от новых конструкций машин. Отлично подойдет термическая сварка.
С помощью термического соединения конец и первой, и второй детали нагревают при помощи специального прибора, в течение некоторого времени, до тех пор, пока не дойдет до максимально нужной температуры. Затем детали прижимают друг к другу с небольшим усилием. Таким образом, шов, возникший в результате стыка, делает конструкцию очень прочной.
Сварке подвергаются абсолютно любые неметаллы и металлы, имеющие любую толщину, да и в любом положении пространства будь то в космосе, на земле или в воде.
С помощью термического соединения, которые получаются с использованием термического соединения, характерны тем, что имеют высокие механические свойства, низкую трудоемкость, небольшой расход металла, невысокую себестоимость.
Препятствия, которые могут не позволить состыковаться деталям следующие:
- — адгезионные пленки;
- — оксидные пленки;
- — неровности на поверхности заготовок.
Для того, чтобы получить сварное соединение необходимо использовать энергию извне. В связи с этим все виды сварки можно разделить на три группы:
Околошовная зона отличается тем, что влияния нагрева высоких температур охлаждения и плавления происходят неравномерно и кратковременно.
Когда металл переходит в состояние из жидкого в твердое, то могут образоваться кристаллы. Такой процесс носит название кристаллизации.
Чем быстрее охлаждается сварочная ванна, тем тонким будет кристаллический слой и меньше будут размеры зерен. Зона сплавления имеет мелкие кристаллы.
Зона, где происходит термические влияния, характеризуется тем, что происходит увеличение кристаллов и их слияние с зернами основного металла.
Околошовная зона и ее размеры зависят от того, какой вид термического соединения, скорость проведения, режим, химический состав, физические свойства.
Процесс термического соединения, в результате которого свариваются металлические детали жидким металлом определенного химического состава. Сущность реакции термической заключается в том, что алюминий имеет способность восстановления окислов металлов с весьма значительным выделением тепла.
Тепло, выделившееся в результате этой реакции, сравнительно долгое время может сохранить металл в состоянии жидком, что дает возможность использовать его для целей технологических.
Какие условия необходимы для того, чтобы началась термическая реакция?
- — Термическую шихту необходимо рассчитать так, чтобы в ходе реакции смогло выделиться количество тепла, которое необходимо для перегрева и расплавления конечных продуктов в реакции.
- — Компоненты термитной шихты: окислы железа, алюминиевый порошок должно быть достаточно мелкими и хорошо перемешанными.
- — Для начала термитной реакции в любой точке термитной шихты необходимо создать температурный толчок не ниже 1350°. после чего термитная реакция быстро распространится на всю шихту.
Применение термического соединения в зоне трамвайного хозяйства
Зона стыков рельсов и их сварка помогут радикально решить проблему с токами блуждающими, которые наносят немалый ущерб подземной металлической коммуникации.
Бесстыковой путь позволит вам уменьшить затраты по текущему содержанию пути, увеличит скорость движения транспорта рельсового, уменьшит шум и удлинит срок службы состава.
Из всех способов термического соединения — промежуточного литья, кузнечного, комбинированного, «дуплекс» стал таким, который смог получить наиболее широкое распространение.
В связи с тем, что произошло массовое применение термического соединения на транспорте, появилась потребность в улучшение стыка сварного. Таким образом, можно получить плотный стык, который будет иметь хороший провар и постоянный химический состав термической стали. В связи с этим увеличится производительность, уменьшатся расходы материалов.
Условия, для проведения термической реакции
Для того, чтобы осуществлена реакция между окислителем и восстановителем, нужно наличие некоторых условий, таких как химическая чистота компонентов термической шихты. Восстановителем в данном случае будет алюминий в состоянии порошкообразном, а окислителем будет порошок окалины железной.
Оказание огромного влияния на реакцию измельченными составляющими термической шихты, как раз и приведет к правильному завершению.
Если же будут отклонения от пределов, которые были указаны, то это приведет к нарушениям нормального соотношения окислителя и восстановителя. А это в свою очередь приведет к тому, что снизится ее калорийность. Все это окажет негативные влияния на качество сварки.
Для того, чтобы реакция между зонами — окалиной железной и алюминием осуществилась, необходима, чтобы термическая шихта была нагрета до той температуры, когда может воспламениться. Обычно такая температура для подобного сплава равна 1360°. Это является критической точкой, которая оказывает влияния на начало термической реакции.
Термохимические процессы, которые протекают медленно, являются безопасными, но они могут стать причиной такого влияния, что снизит теплотворную способность термита. В связи с этим, хранить его долго не рекомендуется.
Применение термита
Термит широко используют в совершенно разных отраслях хозяйства. Его используют для того, чтобы сваривать стальные и чугунные конструкции, а также арматуру, также есть возможность сваривать провода и трубы контактной сети, а также провода высоковольтных линий электропередач.
В технической литературе есть немало способов применения сварки:
- — производство крупных деталей, которые состоят из нескольких деталей, таких как коленчатые валы, рулевые рамы судов, приварка лопастей к гребным валам;
- — восстановление цилиндров прессов, колон кузнечных прессов, поршневых штоков, роторных валов, а также те ведущие реверсивные шестерни прокатных станов, всевозможные станины — клети прокатных станов, станины пресса и главные станины;
- — ремонт чугунного оборудования: шлаковые ковши, поддоны, изложницы.
Термическую сварку деталей крупногабаритных лучше всего производить в цехе литейном, где вы найдете достаточно необходимого технологического оборудования, а также немало грузоподъемных механизмов.
Сварка термическая больших размеров чугунных деталей может дать немалый экономический эффект, особенно оказывает влияния не восстановление технологического оборудования производства металлургического: различных поддонов, ковшей, изложниц, а также станин.
Когда вы приступите к термической сварке изделий из чугуна, не забудьте учесть влияния чувствительности к температурным изменениям.
Когда чугун нагревается выше критической точки и охлаждается очень быстро, он становится хрупким.
Важнейшее условием термического соединения является не что иное, как предварительный подогрев.
Похожие статьиgoodsvarka.ru
Термическая сварка - Большая Энциклопедия Нефти и Газа, статья, страница 1
Термическая сварка
Cтраница 1
Термическая сварка основанатна использовании перегретого жидкого металла для расплава обрабатываемого изделия и присадочного металла. Жидкий металл получается в результате химической реакции между расплавленным оксидом и алюминием. [2]
Термическая сварка способом промежуточного литья состоит в том, что соединяемые концы деталей, установленные с некоторым зазором, заформовываются огнеупорной массой и подогреваются. После окончания происходящей в тигле термитной реакции и некоторой выдержки термитный металл выпускается из тигля и заливается в межстыковое пространство. Через несколько часов форма снимается и срубаются литники и прибыли. [3]
Методы термической сварки классифицируются обычно по способу нагревания свариваемого материала: горячим газом, электротермическим, ультразвуковым методами, трением, нагревом в электрическом поле высокой частоты. Ни один из указанных методов сварки не является универсальным. [4]
Рассмотреть термическую сварку, в процессе которой верхняя плита лресса нагревается, а нижняя - охлаждается. [6]
При термической сварке два куска материала сжимаются вместе и нагреваются в течение короткого промежутка времени. По мере размягчения материал сжимается под действием внешней нагрузки, образуя на поверхности контакта сварной шов. Прочность шва определяется следующими факторами: продолжительностью контакта свариваемых поверхностей, их температурой, величиной сжимающего усилия, а также природой самого материала. [7]
При термической сварке два куска пленки сжимаются вместе в течение короткого промежутка времени и нагреваются под давлением. По мере размягчения материала свариваемые пленки слипаются, образуя на поверхности контакта сварной шов. Прочность шва определяется продолжительностью контакта, температурой свариваемых поверхностей, величиной сжимающего усилия, а также природой самой пленки. [8]
Классификация методов термической сварки производится обычно по способу нагревания свариваемой пленки. В одном случае тепло к материалу подводится через слой пленки непосредственно от обогреваемых плит. В другом случае под воздействием токов высокой частоты тепло для сварки образуется внутри самого свариваемого материала. Наиболее важные характеристики, относящиеся к сварке первого типа, следующие: продолжительность процесса, сжимающее усилие и температура плит. При высокочастотной сварке основными управляемыми параметрами процесса ( в дополнении к продолжительности контакта и сжимающему усилию) являются применяемые напряжения и частота тока. [9]
Что касается термической сварки, то она может быть эффективно применена для раструбных соединений труб из полихлорвинила, полиэтилена, хлорированного полиэфира и полипропилена. При этом методе соединения требуется более высококвалифицированный персонал, чем при остальных методах. Сварка выполняется путем нагревания трубы и сварочного прутка из того же материала при помощи воздуха или горячего газа, подаваемого из особого пистолета. В качестве газа для полихлорвинила может применяться воздух, но для других термопластов используется инертный газ ( С02, N2 и др.) во избежание окисления и ухудшения качества сварного шва. При сварке полиэтилена и полипропилена продукты окисления, образующиеся непосредственно в процессе экструзии, должны быть счищены. [10]
Если при термической сварке температура в зоне сварки остается постоянной, то при импульсном методе она изменяется и в зависимости от толщины полиэти-ленцеллофана соответственно изменяется продолжительность нагрева и температура. К недостаткам этого метода следует отнести продолжительность цикла, вызванную необходимостью охлаждать сварной шов. Цикл сварки может быть сокращен за счет подвода охлаждающей воды к нихромовой пластине или к опорному столу, на котором находится свариваемая пленка. [11]
Большое преимущество имеет термическая сварка при переработке кожеподобных материалов из пластифицированных полиамидов и полиуретанов, применяемых вместо ткани для изготовления приводных ремней. [12]
Свойство термопластичности позволяет применять термическую сварку при изготовлении изделий из термопластов. Нагрев свариваемых участков от внешнего источника тепла - горячим воздухом или контактом с разогретой металлической пластиной - приводит к перегреву поверхности вследствие низкой теплопроводности термопласта. [14]
На рис. 46 приведены схемы различных способов термической сварки. [15]
Страницы: 1 2 3 4
www.ngpedia.ru
Термические виды сварки
Наиболее широкое распространение получила сварка плавлением, которая состоит в том, что жидкий металл одной оплавленной кромки детали соединяется и перемешивается с жидким металлом второй оплавленной кромки, образуя общий объем жидкого металла, который называется сварочной ванной. В зависимости от вида используемой энергии различают электрическую и газовую сварку. В свою очередь, электрическая сварка плавлением подразделяется на дуговую, плазменно-дуговую, электрошлаковую, электроконтактную, электронно-лучевую и др. Ведущее место во всех отраслях промышленности и строительства занимает электродуговая сварка[15].
Дуговая сварка.Сущность дуговой сваркисостоит в том, что свариваемый металл плавится теплом электрической дуги. Для образования сварочной дугииспользуют электрическую цепь со специальным источником питания. Дуга горит между электродом и изделием. Для питания дуги используется переменный или постоянный ток от трансформаторов, выпрямителей, мотор-генераторов и т.п.
При дуговой сваркеплавящимся электродом шов образуется за счет расплавления электрода и свариваемого металла. При сварке неплавящимся электродом шов заполняется металлом свариваемых частей, а иногда также присадочным металлом, подаваемым в зону дуги со стороны. В качестве плавящихся электродов используют стальные, медные, алюминиевые, неплавящихся – угольные, графитовые, вольфрамовые.
Для выполнения качественной сварки требуется защищать сварочный электрод, зону дуги и сварочную ванну от взаимодействия с кислородом и азотом воздуха. Для этого выполняют сварку покрытыми электродами, в защитной атмосфере (защитных газах), под флюсом, порошковой самозащитной проволокой.
По степени механизации сварочного процесса дуговая сварка подразделяется на ручную, полуавтоматическую (механизированную) и автоматическую.
Газовая сварка.Технологические процессы, выполняемые с применением газового пламени, называются газопламенной обработкой металлов (ГОМ). В настоящее время в качестве горючих газов для ГОМ используют ацетилен (С2Н2), сжиженные газы на основе пропан-бутановых смесей, природный газ; при этом окислителем служит кислород или воздух.
Газовая сварка отличается низкой производительностью, сопровождается нагревом широкой зоны, большими деформациями металла и существенными изменениями его структуры. В последнее время газовую сварку применяют преимущественно при ремонте, а также на тех работах, где ее использование незаменимо или более рационально.
Плазменная сварка. Плазменнойназывают сварку сжатой в узкий канал электрической дугой. Устройства для получения сжатой дуги называют плазматронами. Простейший плазматрон состоит из изолятора, неплавящегося электрода и медного, охлаждаемого водой сопла. В сопло подают плазмообразующий инертный, нейтральный или содержащий кислород газ, который в столбе дуги нагревается до высокой температуры и плавит металл. Плазматроны могут работать на постоянном и переменном токе.
Различают плазматроны прямого и косвенного действия.Для сварки и резки чаще применяют плазматроны прямого действия – рис. 4.12. В них дуга горит между электродом и обрабатываемым изделием. В плазматронах косвенного действия дуга горит между электродом и соплом. Их применяют при обработке неэлектропроводных материалов и в качестве нагревателей газов.
Рис. 4.12. Схема плазматрона прямого действия: 1 – сварочный источник питания; 2 – высокочастотный генератор; 3 – вольфрамовый электрод; 4 – плазмообразующий газ; 5 – охлаждающая вода; 6 – защитный газ; 7 – сопло защитного газа; 8 – сопло, формирующее дугу; 9 – дуга; 10 – изделие
Электронно-лучевая сварка.Для расплавления стыка примыкающих друг к другу кромок деталей и образования качественного сварного шва в этом методе используется кинетическая энергия пучка разогнанных в сильном электрическом поле электронов. Электронный луч обеспечивает высокую удельную мощность на поверхности пятна нагрева. Сварка производится в вакууме.
Лазерная сварка. При облучении поверхности тела энергия квантов света поглощается этой поверхностью. Если световую энергию сконцентрировать на малом участке поверхности, то можно получить высококонцентрированный нагрев с интенсивностью до 1011 Вт/м2. На этом принципе основана сварка лучом оптического квантового генератора – лазера. Лазерную сварку производят на воздухе или в среде защитных газов (Ar, СО2). Полученные таким образом соединения отличаются высокой прочностью и благодаря высокой локализации нагрева минимальной деформацией сварных конструкций.
Широкое применение новых конструкционных материалов на основе тугоплавких и высокоактивных материалов (титана, циркония, молибдена, вольфрама и др.) потребовало создание способов их обработки источниками тепла с высочайшей плотностью энергии. Наиболее полно этим условиям отвечают рассмотренные электронно-лучевая и лазерная технологии.
Похожие статьи:
poznayka.org
Виды сварки | Строительный справочник | материалы - конструкции
Термический класс сварки
К термическому классу сварки относятся соединения, получаемые местным плавлением поверхностей при помощи тепловой энергии. Тепло для сварки можно получить при помощи электрической дуги (дуговая сварка), от сгорания газовой смеси (газовая сварка), электронным или фотонным лучом (электронно-лучевая или лазерная сварка), сжиганием термитной смеси (термитная сварка), при прохождении электрического тока через расплавленный металл (электрошлаковая сварка) и т.д.
Дуговая сварка
При этом способе тепло для плавления получают от электрической дуги, возникающей в узком разрыве электрической цепи между сварочным электродом и изделием. Электрическое сопротивление этого зазора поднимает температуру до 4500 - 6000°С, в результате чего расплавляется конец электрода и участок детали, подлежащий соединению посредством сварки. После остывания металла получается сварочный шов, по прочности не уступающий основному металлу изделия. Яркий голубой свет и эффектный фонтан искр являются отличительной чертой дуговой сварки. Особым видом дуговой сварки является плазменная сварка, при которой нагрев осуществляется сжатой дугой.
Газовая сварка
При газовой сварке разогрев свариваемой кромки происходит при помощи газопламенной ее обработки. Пламя, полученное при выходе из газовой горелки, создает температуру до 3000°С и позволяет не только проводить сварку металлических кромок отдельных деталей, но и резать металл, нагревать его для гибки и т.д.
Лучевая сварка
Тепло в зоне сварки при лучевой сварке получают, бомбардируя сварочную кромку направленным электронным или фотонным потоком. Электронный поток получают при помощи специального прибора - электронной пушки, а фотонный поток создают в лазерных установках.
Термитная сварка
При термитной сварке используют тепло, полученное в результате сжигания термитной смеси, состоящей из алюминия и оксидов железа.
Электрошлаковая сварка
При электрошлаковой сварке плавление кромок свариваемых деталей получают теплом, возникающим при прохождении электрического тока через расплавленный электропроводный шлак.
Термическая разделительная резка
Под термической разделительной резкой понимают процесс обратный сварке, то есть, когда атомы металла сгорают в струе технически чистого кислорода, а полученные при этом продукты сгорания удаляются из зоны резания.
Термомеханический класс сварки
К термомеханическому классу относят кузнечную, контактную, диффузионную и прессовую сварку, использующую одновременно энергию механического и термического воздействия.
Кузнечная сварка
Кромки свариваемых деталей нагревают в специальных печах-горнах до требуемой температуры, а затем при помощи ударного механического воздействия соединяют между собой. Если для соединения деталей используют механические прессы, а для нагрева - все ранее перечисленные способы термического воздействия, то такой вид сварки называют прессовым.
Контактная сварка
Соединяемые детали сдавливают между собой, а тепло для сварки получают при прохождении электрического тока через контактную часть деталей. В зависимости от размеров контактной части свариваемых деталей различают точечную, стыковую, шовную и рельефную контактную сварку. Этот вид получил одно из ведущих мест в машиностроении, так как является наиболее экономичным и производительным. Контактная сварка легче всего поддается механизации и автоматизации, где механические роботы заменяют человека со сварочным электрододержателем.
Диффузионная сварка
Сварку деталей получают за счет диффузии атомов из одной детали в другую, возникающей при относительно небольшом длительном нагреве и пластической деформации, получающейся от механического давления.
Механический класс сварки
В механическом классе сварки соединение поверхностей осуществляется механическим воздействием (давление, трение, взрыв и т.д.) без использования внешнего источника тепла.
Сварка трением
При сварке трением нагрев свариваемых деталей получают за счет сил трения, возникающих при вращении деталей относительно друг друга при одновременном сдавливании их между собой.
Холодная сварка
При сильном сдавливании деталей между собой получается пластическая деформация металла, при которой атомы двух деталей настолько близко сближаются, что между ними возникают силы взаимодействия. В результате этого получается достаточно прочное соединение деталей, называемое холодной сваркой.
Сварка взрывом
Сближение атомов между собой может происходить в результате направленного взрыва, при котором частицы быстро движутся навстречу друг другу и, соударяясь, сближаются между собой настолько, что между ними возникают силы взаимодействия.
Ультразвуковая сварка
Силы взаимодействия между атомами при ультразвуковой сварке возникают в результате колебаний кристаллической решетки металла под действием ультразвуковых колебаний.
build.novosibdom.ru
Термическая обработка сварных конструкций | Техническая литература онлайн
В настоящее время в машиностроении значительно более высокими темпами, чем ранее, осуществляется переход на стали с низким, средним и высоким содержанием легирующих добавок. Легированные стали обеспечивают дальнейший рост допускаемых напряжений, а также возможность работы конструкций при динамических и при резко выраженных ударных нагрузках. Вместе с тем теперь предъявляются очень высокие требования к металлообработке и, в частности, к сварке.
Сварка вообще, и в особенности сварка легированных сталей, в большинстве случаев производится в строго ограниченных термических режимах. Термическое воздействие на сварные конструкции имеет место на следующих этапах их изготовления: до производства сварочных работ, в процессе их производства и после завершения сварки.
До производства сварочных работ термическое воздействие па основной материал производится:
- отжигом или отпуском для приведения металла в состояние, обеспечивающее свариваемость в соответствии с требованиями технических условий;
- предварительным подогревом с целью уменьшения перепада температур между источником тепла и основным металлом.
В машиностроении при сварке литья и штампованных частей с прокатом, при сварке предварительно гнутых в холодном состоянии деталей, в особенности из легированной стали, для измельчения зерна, устранения наклепа и внутренних напряжений применяются отжиг или отпуск.
Предварительная термическая обработка проводится на большинстве машиностроительных заводов не в сварочных цехах, а в термических отделениях литейных и кузнечных цехов или в термическом цехе. Предварительный же нагрев деталей с целью уменьшения перепада температур между источником тепла и основным металлом производится в сварочных цехах. Этот нагрев может быть общим для всей детали или только местным.
Предварительный нагрев воздействует на процесс нагрева при сварке и на охлаждений после сварки металла шва и зоны термического влияния основного металла, а также и всей детали. В результате такого воздействия устраняются местное появление структур в металле, приводящих к снижению его механических свойств и возникновение пик резко выраженных внутренних напряжений. Зона термического влияния становится выраженной не резко, она как бы делается размытой, пики внутренних напряжений сглаживаются.
В тяжелом машиностроении многолетним опытом установлена необходимость термической обработки для снятия напряжений у ряда конструкций, работающих при динамической нагрузке. К таким конструкциям относятся шаровые мельницы, рамы экскаваторов, части дробилок, прессов, молотов и т. д. Сборка некоторых из этих деталей ранее производилась без термической обработки. Однако после эксплуатации их в течение 1—½ г. в основном металле вблизи швов вторично появлялись трещины и разрывы, которые заваривались с соблюдением всех требований для заварки трещин. По истечении некоторого времени, после вторичной эксплуатации деталей снова появлялись трещины в смежных местах, а иногда и в новых. Многие из конструкций после неоднократных исправлений и появления новых трещин были демонтированы и заменены новыми. Изготовление таких деталей с последующей термической обработкой (снятием внутренних напряжений) полностью исключило появление трещин и указало на возможность повышения допускаемых напряжений.
Устранение термической обработкой внутренних напряжений в деталях машин необходимо еще и потому, что деталь, при наличии внутренних напряжений, после механической обработки, т. е. после снятия напряженных слоев металла, изменяет форму (коробится). Изменение формы бывает иногда настолько велико, что деталь после коробления может оказаться неисправимым браком. В некоторых случаях при малой механической обработке коробление проявляется и с течением времени, уже в эксплуатации, теряет соосность, а это приводит к расстройству машин, например, зубчатых передач.
Экономия на исключении термической обработки из общего производственного цикла в машиностроении не оправдывается последующим многократным перерасходом, связанным с браком деталей в производстве и расстройством машин, а также убытками от их остановки в процессе эксплуатации. Исключение термической обработки сварных конструкций не оправдывается и опытом изготовления стального литья, которое всегда проходит эту обработку.
Так называемые структурные напряжения, возникающие от изменения параметров кристаллической решетки при структурных превращениях стали, также могут быть снижены предварительным подогревом, который изменяет скорость охлаждения деталей после сварки. У низкоуглеродистой стали при нагреве происходит увеличение длины по кривой а‘а‘‘а‘‘‘ δ‘ (фиг. 139), при этом на участке а‘‘а‘‘‘ объем стали уменьшается в связи с переходом перлита в аустенит, который имеет большую плотность по сравнению с перлитом. При охлаждении низкоуглеродистой стали обратные превращения происходят приблизительно при тех же температурах. При резком охлаждении легированной стали по кривой δ‘δ‘‘δ‘‘‘ превращение происходит при более низких температурах, и аустенит превращается в мартенсит, обладающий по сравнению с аустенитом и перлитом наименьшей плотностью и наибольшим объемом, в связи с чем в стали часто наблюдаются закалочные трещины. При замедлении охлаждения превращение можно осуществить по кривой δ‘b‘b‘‘b‘‘‘b‘‘‘‘b‘‘‘‘‘. Такой режим охлаждения предотвращает образование трещин, так как частичный расход аустенита совершается при более высоких температурах.

Кривые изменения длины при нагреве и охлаждении стали
Сварка с предварительным нагревом применяется для массивных деталей, когда для нее требуется сравнительно небольшое время, при котором не успевает произойти охлаждение детали. С целью уменьшения скорости охлаждения свариваемую деталь закрывают листами асбеста, иногда засыпают шлаком. Изменение термического состояния детали при сварке с предварительным нагревом в зависимости от времени представлено на фиг. 140, а.

Кривые термических режимов при сварке
В процессе сварки термическое воздействие на деталь производится или от постороннего источника тепла, или сварщиком, изменяющим режим сварки: силу тока, напряжение на дуге, скорость перемещения электрической дуги или газовой горелки. Термическое воздействие, производимое самим сварщиком, является наиболее простым технологическим мероприятием, но во многих случаях недостаточным. Метод определения режима, наиболее благоприятно действующего на структуру металла сварных соединений из низкоуглеродистой и легированной стали, приводится в работах Н. Н. Рыкалина и Л. А. Фридлянда. Сварка с подогревом применяется для деталей сложной формы или тонкостенных, а поэтому быстро охлаждающихся на воздухе при большой продолжительности сварки. Процесс сварки начинается предварительным нагревом, а затем сварка проводится при непрерывном подогреве. После окончания сварки деталь, чтобы выравнять температуру до требуемого уровня, дополнительно подогревается. Затем наступает медленное охлаждение детали, помещаемой в печь или особую камеру с нетеплопроводной поверхностью, обеспечивающей медленное и регулируемое понижение температуры. Изменения температуры детали в зависимости от времени при указанном режиме даны на фиг. 140, б.
В отношении деталей, требующих для сварки непродолжительного времени, в течение которого не успевает произойти охлаждение шва, изготовленных из сталей, не имеющих резко выраженной склонности к образованию трещин, применяется режим с выравнивающим нагревом (фиг. 140, в).
Детали сложной формы с большим объемом и временем сварочных работ значительно охлаждаются в процессе сварки. Для таких деталей в конце сварки необходим выравнивающий подогрев, а иногда и промежуточные подогревы. Режимы такого рода представлены на фиг. 140, г и д.
Предварительный нагрев производится до температур 120— 220° в зависимости от свойств стали и времени сварки, в течение которого температура не должна быть ниже 120—150°. Для сталей с повышенной склонностью к воздушной закалке в конструкциях сложной конфигурации температура предварительного нагрева доводится до 300—350°.
Рекомендуем производить выбор термического режима сварки в соответствии с данными табл. 50.
Таблица 50
Термические режимы сварки
Род стали и состояние поставки | Детали простой формы из нежестких частей (стержни, рамы и пр.) | Сосуды, плоские детали, решетчатые конструкции | Сложные сосуды, профильные элементы, плоские детали с ребрами | Сложные узлы с пространственным расположением свариваемых частей |
1. Хорошо сваривающаяся сталь: углеродистая сталь с С | Сварка без ограничений | |||
Сварка без ограничения | Ограждение от ветра | Сварка в цехе при t≥ + 5° | ||
2. Удовлетворительно сваривающаяся сталь: углеродистая сталь с 0,25— 0,35% С и легированная сталь с 0,18—0,25% С в отожженном состоянии или после термообработки на низкую и среднюю твердость. | Сварка при t≥ +5° без ограничений | В трудных случаях сварка по режимам а или в или местный подогрев | ||
В состоянии закалки и низкого отпуска или не улучшенный металл после литья, ковки и т. п. | Сварка при t≥ + 5° без особых ограничений | В трудных случаях сварка по режимам а или в | Как правило, сварк 1 по режимам а или в | |
3. Ограниченно сваривающаяся сталь: углеродистая сталь с 0,35— 0.45% С и легированная сталь с 0,28—0,38% С в отожженном состоянии пли после термообработки на низкую или среднюю твердость. | Сварка при t≥ 5° без ограничений | Сварка при t≥ + 5° без ограничений, иногда с местным подогревом | В трудных случаях сварка по режимам а или в | Как правило, сварка по режимам а или в |
В состоянии закалки на высокую твердость или не улучшенный металл после литья, ковки и т. п. | Сварка при ( + 5° без ограничений | Сварка но режимам а или п | Сварка по режимам а, б, а, г и д | |
4. Плохо сваривающаяся сталь: углеродистая сталь с 0,45% С и выше и легированная сталь с 0,38% С и выше, в отожженном состоянии | Свирка без ограничений | Сварка по режимам а и в | Сварка по режимам а, б, в, г и д | |
После термообработки на низкую и среднюю твердость. | Сварка в некоторых случаях по режимам а и в, иногда только местный подогрев | Сварка по режимам а и в, иногда по режимам б и г | Сварка по режимам а, б, в, г и д | |
После обработки на высокую твердость и в не улучшенном состоянии после литья, ковки и т. п. | Сварка по режимам а и в, иногда с местным подогревом | Сварка по режимам а, б, в, г и д |
/* Here you can add custom CSS for the current table */ /* Lean more about CSS: https://en.wikipedia.org/wiki/Cascading_Style_Sheets */ /* To prevent the use of styles to other tables use "#supsystic-table-76" as a base selector for example: #supsystic-table-76 { … } #supsystic-table-76 tbody { … } #supsystic-table-76 tbody tr { … } */
Термическая обработка сварных конструкций после сварки производится с целью:
- снятия внутренних напряжений в сварном соединении и всей конструкции;
- повышения механических свойств металла шва и основного металла в зоне термического влияния;
- получения структур, обеспечивающих требующуюся твердость.
Снижение внутренних напряжений достигается высоким отпуском, т. е. нагревом всей детали до температуры в 600—650°. Снижение внутренних напряжений обусловлено тем, что при температуре 600—700° происходит уменьшение значения предела текучести для низкоуглеродистой стали до 3,5—5 кг)мм2 и для легированной стали различных марок до 8—10 кг/мм2 (фиг. 141).

Зависимость предела прочности и предела текучести
Механические свойства металла шва и основного металла повышаются отпуском при низких, средних и высоких температурах. В машиностроении ряд конструкций изготовляется при помощи сварки из деталей, во многих случаях предварительно обработанных на высокую твердость, потому что после сварки конструкции не могут быть подвергнуты такой обработке (закалке). Так как в таких конструкциях в результате сварки получаются внутренние напряжения, то чтобы их устранять, применяют отпуск.
Но сталь, обработанная предварительно по условиям эксплуатации машин на высокую твердость, должна ее сохранить и после отпуска. В этом случае может быть проведен только отпуск с нагревом в пределах от 180 до 280°. При отпуске до 400° углеродистая сталь с 1,02% С приобретает структуру троостита; при отпуске до 400—550° структура стали состоит из троостита и сорбита; выше 550° структура переходит в зернистый перлит.
Естественно, что у легированных сталей при различных температурах отпуска получается другое распределение структур. В соответствии с изменением структуры изменяются и механические свойства стали.
На фиг. 142 представлены кривые, показывающие изменения механических свойств закаленной стали в зависимости от температуры отпуска. По этим кривым можно заключить, что только отпуск при температурах 500—550° обеспечивает высокие значения ударной вязкости, а снижение твердости создает некоторую возможность механической обработки.

Кривые изменения механических свойств закаленной стали в зависимости от температуры отпуска
Низкотемпературный отпуск устраняет образование трещин, но не уничтожает хрупкой закаленной зоны. Своеобразная термическая обработка наложением многослойных валиков сваркой рассмотрена в следующем разделе.
Если стали, которые при эксплуатации машин должны иметь высокую твердость, свариваются в отожженном состоянии, то после сварки они подвергаются закалке иногда с последующим отпуском. Высокомарганцевые аустенитные стали (13—18% Mn) свариваются в закаленном состоянии, а после сварки проходят вторичную закалку для получения во всех частях аустенитной структуры.
Таким образом, в машиностроении термическая обработка сварных деталей весьма разнообразна.
Во многих случаях сварка ведется на подогретых деталях, иногда подогрев повторяется в процессе сварки или после нее, поэтому нагревательные средства устанавливаются в потоке производства машиностроительных конструкций.
Для термической обработки сварных конструкций применяется: стационарное оборудование в виде печей или горновых устройств с нагревом их твердым, жидким, газообразным топливом и электронагревом. Применяется также и переносное оборудование в виде печей и аппаратуры как для общего, так и для местного нагрева жидким и газообразным топливом, либо способом электронагрева сопротивлением или индукционным электронагревом.
Печи с выдвижным подом (фиг. 143) применяются для предварительной и последующей (после сварки) термической обработки. Предварительный подогрев вести в таких печах нецелесообразно, так как передача нагретой детали с платформы на рабочее место отнимает много времени. В особенности она бывает затруднительной, когда необходим для детали промежуточный подогрев. Проведение сварочных работ на самой тележке приводит к простоям печи.

Печь с выдвижным подом
Кроме того, в этом случае требуется отодвигать тележку на значительное расстояние, чтобы тепло, излучаемое печью, не осложняло работу сварщика, работающего и так в крайне трудных температурных условиях от тепла, излучаемого деталью. Такие печи можно применять только при условии, если тележки могут отводиться на значительное расстояние по обе стороны печи. Длина печей с выдвижным подом колеблется в пределах от 5 до 30 м.
Печи со съемными сводами (фиг. 144) при длине камеры в 15—40 м применяются для предварительной и последующей термической обработки. Подогрев в них еще более неудобен, так как операции погрузки и выгрузки очень затруднены. Эти печи могут применяться для компактных массивных деталей, не деформирующихся при нагреве до температур термической обработки и не требующих особо тщательной укладки.

Печь со съемным сводом
На некоторых заводах термическую обработку сварных изделий производят в вертикальных шахтных печах (фиг. 145). Подача детали в печь вместе с подвеской производится краном, после чего подвеска крепится на специальной балке, опирающейся на колонны, а кран освобождается для дальнейших операций. Эти печи не дают возможности рационально использовать объем при коротких, компактных сварных деталях. Они предназначены для однотипных длинных изделий (трубы, барабаны) и имеют то преимущество, что в этом случае устраняется влияние собственного веса на изменение формы изделия, которое для подобных изделий усложняет технологию их термической обработки в горизонтальных печах.

Вертикальная печь
Предварительный и последующий промежуточный подогревы следует проводить подогревающими устройствами, которые включаются в работу на рабочем месте сварки, открывая свободный доступ к месту сварки. К таким подогревающим устройствам относятся колпаковые печи (фиг. 146) с газовым или электрическим нагревом. Съемный колпак, который несет на себе нагревающее устройство, может полностью или частично (не на всю высоту) открывать нагреваемую деталь.

Колпаковая печь
К устройствам такого же типа относятся горны с колпаком, изолирующим деталь от охлаждения (фиг. 147). Детали в горне нагреваются снизу электрическим током, газом, жидкими горючими или углем. Подогрев углем создает большой запас тепла и способствует медленному охлаждению при отсутствии дутья, которое может быть включено только на время, необходимое для повышения температуры. В это время деталь необходимо закрыть колпаком и на время подогрева сделать перерыв в сварке. При электрическом подогреве благодаря отсутствию продуктов горения работу по сварке можно вести и во время подогрева. При сварке изделий, требующих сравнительно невысокого подогрева (100—200°), подогревающие горны следует делать со съемным сводом из несколь- ном топливе. Применяется также индукционный нагрев или электронагрев элементами сопротивления. Подогрев такими устройствами производится с набором их из нескольких секций по форме изделия.

Горно с изолирующим колпаком
Термическая обработка для снятия напряжений и изменения структуры зоны термического влияния производится при местном нагреве детали, для которого используются переносные устройства в виде секционных газовых печей, а также печей с электрическим нагревом сопротивлением или индукционным. Например, цилиндрические изделия значительной длины подаются в печи частями, а стыковые швы проходят последующую термическую обработку с местным нагревом.
В тяжелом машиностроении изготовляется большое количество всевозможных сварных барабанов для прессовой и химической аппаратуры, которая находится под контролем Государственной инспекции Котлонадзора.
Термическая обработка таких сосудов и трубопроводов к ним проводится при следующих режимах.
Обязательной термической обработке подвергаются:
- Корпуса сосудов, изготовленные из углеродистых сталей, при толщине стенки свыше 25 мм или если толщина стенки более вычисленной по формуле: (Dвн+127)/120 см
- Корпуса сосудов, изготовленные из легированных сталей, при толщине стенки свыше 12 мм или при наличии большого количества приваренных деталей (штуцеры, фасонные части и т. п.).
- Штампованные днища из целого листа или сварные (из лепестков) независимо от марки стали при толщине листа свыше 16 мм.
Днища, полученные холодной штамповкой, подвергаются термической обработке при любой толщине стенки.
Режимы термической обработки для изделий из углеродистой стали: отжиг при 600—650° с выдержкой 2,5 мин. на каждый миллиметр толщины стенки, но не менее 30 мин. с последующим медленным охлаждением на воздухе.
Режимы термической обработки для изделий из молибденовой стали: отжиг при 680—700°, выдержка 5 мин. на каждый миллиметр толщины стенки, но не менее 60 мин.; последующее охлаждение со скоростью 50—75° в час до 300° и полное охлаждение на спокойном воздухе.
Изделия из хромомолибденовой стали подвергаются:
- двойной термической обработке: нормализация при 900— 930° с выдержкой 1 мин. на 1 мм толщины стенки, с последующим замедленным охлаждением до 500° на спокойном воздухе (скорость 40—50° в мин.) и отпуск при 650—680° с выдержкой 3 мин. на 1 мм толщины стенки, с медленным охлаждением (50—75° в мин.) до 300° и с окончательным охлаждением на спокойном воздухе;
- полному отжигу с нагревом выше верхней критической точки и медленным охлаждением с печью.
Сварные аппараты и днища из стали марки Ст. 3 подвергаются высокому отпуску при 650—670° (скорость нагрева 100—120° в час) с выдержкой 4 мин. на 1 мм толщины стенки и охлаждением до 300° с печью, затем на воздухе.
По правилам на трубопроводы от 3 октября 1949 г. термическая обработка сварных соединений трубопроводов обязательна при применении легированных сталей (15М, 20М, 15ХМ). Для трубопроводов из углеродистой стали термическая обработка обязательна в тех случаях, где это требуется проектом.
Трубы из стали марок 20, 15М и 15ХМ диаметром 273 мм и более с толщиной стенки более 10 мм после горячей гибки подвергаются термической обработке.
После горячей гибки труб диаметром 213 мм и более из стали марок 15М и 15ХМ производится отжиг по режиму: нагрев до 890—910° (со скоростью нагрева 100—150° в час), выдержка 3—4 мин. на 1 мм толщины; охлаждение до 300° с печью, а затем на воздухе.
Трубы тех же размеров из стали марки 20 подвергаются отжигу при 870—880° (скорость нагрева 100—150° в час) с выдержкой 3—4 мин. на 1 мм толщины и охлаждением до 300° с печью, затем на воздухе.
В тяжелом машиностроении термическую обработку для снятия напряжений в сварных конструкциях из углеродистых сталей проводят по следующему режиму:
- посадка в печь при температуре печи в зависимости от конфигурации деталей не выше 250—350°;
- нагрев до температуры 450—570° со скоростью не более 60°/час;
- выдержка при температуре 450—600° в течение 6—12 час.;
- охлаждение в печи с выключенными горелками и закрытыми шиберами до температуры не выше 350°;
- дальнейшее охлаждение на спокойном воздухе.
Существенным технологическим вопросом при термической обработке сварных конструкций машин и сооружений является закрепление детали, чтобы предотвратить ее чрезмерное коробление. При температурах 600—750°, в результате значительного снижения предела текучести стали, изделие, находясь под действием собственного веса, может получить полное, неустранимое в дальнейшем никакими мероприятиями изменение формы. Наиболее сильно это проявляется при термической обработке цилиндрических изделий большого диаметра, когда сосуд теряет форму и принимает эллиптическое сечение. Для предотвращения этого внутрь сосуда устанавливают временные металлические распорки.
При укладке изделия на под печи оно должно иметь опоры во многих точках, причем для опор нужна значительная площадь, устраняющая возможность прогиба, а также и местные деформации на опорах. Все опоры должны быть плотно подбиты и, кроме того, установлены так, чтобы их положение при повышении температуры не изменялось.
При термической обработке изделия балочной формы двутаврового, швеллерного или двустенчатого сечения могут потерять форму под действием собственного- веса и получить коробление, если сварные швы будут наложены несимметрично по отношению к центру тяжести сечения. Чтобы это устранить, детали крепят к плотовине (фиг. 148) пода или к тележке, или же конструкции скрепляют друг с другом таким образом, чтобы коробление устранялось их взаимным действием (фиг. 149). Это наиболее, эффективно тогда, когда длинные детали проходят термическую обработку в вертикальных печах (фиг. 150).

Крепление деталей при термообработке
imetal.in.ua
Термический класс сварки
Виды сварки
К термическому классу сварки относятся соединения, получаемые местным плавлением поверхностей при помощи тепловой энергии. Тепло для сварки можно получить при помощи электрической дуги (дуговая сварка), от сгорания газовой смеси (газовая сварка), электронным или фотонным лучом (электронно-лучевая или лазерная сварка), сжиганием термитной смеси (термитная сварка), при прохождении электрического тока через расплавленный металл (электрошлаковая сварка) и т.д.
Дуговая сварка
При этом способе тепло для плавления получают от электрической дуги, возникающей в узком разрыве электрической цепи между сварочным электродом и изделием. Электрическое сопротивление этого зазора поднимает температуру до 4500 - 6000°С, в результате чего расплавляется конец электрода и участок детали, подлежащий соединению посредством сварки. После остывания металла получается сварочный шов, по прочности не уступающий основному металлу изделия. Яркий голубой свет и эффектный фонтан искр являются отличительной чертой дуговой сварки. Особым видом дуговой сварки является плазменная сварка, при которой нагрев осуществляется сжатой дугой.
Газовая сварка
При газовой сварке разогрев свариваемой кромки происходит при помощи газопламенной ее обработки. Пламя, полученное при выходе из газовой горелки, создает температуру до 3000°С и позволяет не только проводить сварку металлических кромок отдельных деталей, но и резать металл, нагревать его для гибки и т.д.
Лучевая сварка
Тепло в зоне сварки при лучевой сварке получают, бомбардируя сварочную кромку направленным электронным или фотонным потоком. Электронный поток получают при помощи специального прибора - электронной пушки, а фотонный поток создают в лазерных установках.
Термитная сварка
При термитной сварке используют тепло, полученное в результате сжигания термитной смеси, состоящей из алюминия и оксидов железа.
Электрошлаковая сварка
При электрошлаковой сварке плавление кромок свариваемых деталей получают теплом, возникающим при прохождении электрического тока через расплавленный электропроводный шлак.
Термическая разделительная резка
Под термической разделительной резкой понимают процесс обратный сварке, то есть, когда атомы металла сгорают в струе технически чистого кислорода, а полученные при этом продукты сгорания удаляются из зоны резания.
Термомеханический класс сварки
К термомеханическому классу относят кузнечную, контактную, диффузионную и прессовую сварку, использующую одновременно энергию механического и термического воздействия.
Кузнечная сварка
Кромки свариваемых деталей нагревают в специальных печах-горнах до требуемой температуры, а затем при помощи ударного механического воздействия соединяют между собой. Если для соединения деталей используют механические прессы, а для нагрева - все ранее перечисленные способы термического воздействия, то такой вид сварки называют прессовым.
Контактная сварка
Соединяемые детали сдавливают между собой, а тепло для сварки получают при прохождении электрического тока через контактную часть деталей. В зависимости от размеров контактной части свариваемых деталей различают точечную, стыковую, шовную и рельефную контактную сварку. Этот вид получил одно из ведущих мест в машиностроении, так как является наиболее экономичным и производительным. Контактная сварка легче всего поддается механизации и автоматизации, где механические роботы заменяют человека со сварочным электрододержателем.
Диффузионная сварка
Сварку деталей получают за счет диффузии атомов из одной детали в другую, возникающей при относительно небольшом длительном нагреве и пластической деформации, получающейся от механического давления.
Механический класс сварки
В механическом классе сварки соединение поверхностей осуществляется механическим воздействием (давление, трение, взрыв и т.д.) без использования внешнего источника тепла.
Сварка трением
При сварке трением нагрев свариваемых деталей получают за счет сил трения, возникающих при вращении деталей относительно друг друга при одновременном сдавливании их между собой.
Холодная сварка
При сильном сдавливании деталей между собой получается пластическая деформация металла, при которой атомы двух деталей настолько близко сближаются, что между ними возникают силы взаимодействия. В результате этого получается достаточно прочное соединение деталей, называемое холодной сваркой.
Сварка взрывом
Сближение атомов между собой может происходить в результате направленного взрыва, при котором частицы быстро движутся навстречу друг другу и, соударяясь, сближаются между собой настолько, что между ними возникают силы взаимодействия.
Ультразвуковая сварка
Силы взаимодействия между атомами при ультразвуковой сварке возникают в результате колебаний кристаллической решетки металла под действием ультразвуковых колебаний.
build.novosibdom.ru
Глава 1 Термический класс сварки
Классификация видов сварки плавлением
Термический класс сварки включает все виды сварки с использованием тепловой энергии.
Сварку плавлением в зависимости от различных способов, характера источников нагрева и расплавления свариваемых кромок деталей можно разделить на следующие основные виды:
• газовая сварка;
• электрическая дуговая сварка;
• электрошлаковая сварка;
• электронно-лучевая сварка;
• плазменная сварка;
• лазерная сварка;
• термитная сварка.
Этот класс характеризуется тем, что сварка осуществляется плавлением кромок соединяемых частей. При этом образуется ванна расплавленного металла. После отвода источника нагрева металл сварочной ванны кристаллизуется и образуется сварной шов, соединяющий свариваемые части. Сварка – сложный и быстропротекающий физико-химический процесс образования соединения материалов. Подготовка заготовок и продуманная технология делают сварку легкой, быстрой.
Из курса физики нам известно, что состояние любого вещества характеризуется взаимосвязью молекул и атомов. Различают четыре основные состояния материи:
• твердое;
• жидкое;
• газообразное;
• плазму.
Твердое тело представляет собой «агрегат» атомов, находящихся во взаимодействии, а его физические характеристики определяются их взаимным расположением (кристаллической решеткой) и химическими связями, действующими между ними.
Соединение сваркой твердых тел можно представить как образование прочных и устойчивых химических связей между атомами соединяемых элементов. Для получения прочного соединения твердых тел необходимо их сблизить до возникновения межатомных связей.
В твердом и жидком состоянии расстояние между молекулами и атомами очень мало. Этим объясняется малая сжимаемость этих веществ и их общее название – «конденсированное состояние».
В газах расстояние между молекулами значительно больше, поэтому газы сравнительно легко сжимать под воздействием внешнего давления.
Различие в электропроводности твердых, жидких и газообразных веществ также объясняется различием расстояний между атомами и молекулами. В твердых и жидких веществах крайние электроны, далеко отстоящие от ядер своих атомов, легко теряют связь с ядром. Благодаря этому появляются свободные электроны, легко перемещающиеся по объему вещества. Такие свободные электроны называются электронами проводимости и являются носителями тока в проводниках. В газах электроны притягиваются только к своим ядрам, поэтому при нормальных условиях газы электрический ток не проводят.
Вся история человечества связана с освоением энергии, в частности тепловой энергии. От древнего пламени костра до управления потоками света в лазерном луче – вот история технологии. В таблице 1 приведены данные о плотности потоков тепловой энергии и минимально достижимых площадях нагрева материалов, т. е. фокусировке потоков энергии в пятно нагрева.
Таблица 1
Энергетические свойства источников тепла
Классификацию сварки можно провести по степени механизации процессов. Тогда выделяют сварку: ручную, механизированную (полуавтоматическую), автоматическую.
Ручная сварка производится оператором (сварщиком) с помощью инструмента вручную, без применения механизмов.
Механизированная сварка выполняется оператором при помощи устройства (машины или механизма), подающего электродную проволоку в зону сварки.
Автоматическая сварка осуществляется без участия человека. При этом механизируются операции по получению сварного шва по заданной программе.
По способу защиты металла различают: сварку в воздухе, в вакууме, в среде защитных газов, под слоем флюса, в пене и т. п.
Общая схема методов сварки плавления (рис. 1) может быть представлена рядом последовательных стадий состояния металла в зоне сварки:
1 – элементы собраны под сварку и закреплены в необходимом положении относительно друг друга. Между элементами остается зазор. В зоне стыка полностью отсутствуют химические связи;
2 – на поверхность металла в зоне стыка воздействуют мощным концентрированным потоком тепловой энергии Q. Подведенный тепловой поток нагревает кромки материала выше температуры плавления. Расплавленный металл обеих кромок сливается, образуется общая ванночка из жидкого металла (сварочная ванна). Ванночка удерживается на частично оплавленных кромках. Зазор между заготовками исчезает. Химические связи в жидком металле близки к химическим связям твердого тела, поэтому эту стадию принято называть образованием физического контакта;
3 – при прекращении теплового воздействия на кромки свариваемых элементов (выключение источника тепла или перемещение его вдоль кромок) зона сварки охлаждается за счет передачи теплоты вглубь свариваемых элементов и в окружающую среду. Происходит кристаллизация сварочной ванны с образованием литой структуры шва, т. е. создание химических связей по сечению свариваемого соединения. Частично оплавленные зерна основного металла на границе сварочной ванны являются основанием для «пристройки» атомов из жидкости для кристаллизации шва.
Рис. 1. Схема стадий образования соединения сваркой плавлением:
1 – сборка под сварку;
2 – образование сварочной ванны под воздействием теплоты;
3 – кристаллизация ванны с образованием сварного соединения;
4 – макроструктура зерен на границе шва.
Рассмотрим основные виды сварки плавлением.
Следующая глава
info.wikireading.ru
Каталог статей
Виды термического класса сварки
Термический класс объединяет виды сварки,которые производятся местным плавлением металла. Сущность сварки плавлением заключается в расплавлении кромок соединяемых деталей под действием источника нагрева, в результате чего создается общий объем жидкого металла (сварочная ванна), а после остывания - сварной шов. |
Рис.11 - сварочная дуга; 2 - электрод; 3 - электрододержатель; 4- сварочные провода; 5 - источник питания; 6 - основной металл; 7 - сварной шов. | 1. Ручная дуговая сварка (рис. 1) производится металлическими электродами, покрытыми специальной обмазкой. К электроду и свариваемому металлу подводится электрический ток, в результате чего возникает дуга, постоянную длину которой необходимо поддерживать на протяжении всего процесса сварки. Дуга расплавляет металлический стержень электрода, его покрытие и основной металл. Капли металла металлического стержня, покрытые шлаком, переходят в сварочную ванну, где смешиваются с расплавленным основным металлом. По мере плавления электрода покрытие образует газашлаковую защиту, изолирующую зону дуги и сварочную ванну от атмосферного воздуха. По мере удаления дуги происходит остывание ванны, и образуется сварной шов. |
Рис.21 - горелка; 2 - шланг для подвода ацетилена;3 - шланг для подвода кислорода; 4 - ацетиленовый баллон; 5 - ацетиленовый редуктор;6 - кислородный редуктор; 7 - кислородный вентиль; 8- кислородный баллон. | Рис.З1- присадочная проволока; 2- горелка; 3-основной металл; 4- сварочное пламя. | 2. Газовая сварка (рис. 2) - это сварка плавлением, при которой металл в зоне соединения нагревают газовым пламенем до расплавления. Пламя образуется при сгорании горючего газа в кислороде. При нагреве газовым пламенем (рис. 3) кромки свариваемых заготовок расплавляются вместе с присадочным металлом, который может дополнительно вводится в пламя горелки. После затвердевания жидкого металла образуется сварной шов. |
Рис.41 - сварочная проволока; 2 - сопло горелки; 3 - защитный газ; 4 - токоподводящий мундштук;5 - подающие ролики ; 6 - сварной шов. | Рис.51 - горелка; 2 - подающий механизм; 3 - катушка с проволокой; 4- шланг для подачи углекислого газа. | 3. Полуавтоматическая сварка в среде защитного газа производится сварочной проволокой , которая подается автоматически в зону сварки. Дуга горит между непрерывно подающейся проволокой и свариваемым металлом (рис. 4). Одновременно с проволокой подается газ (углекислый, аргон или др.), который защищает сварочную ванну от вредного воздействия воздуха. Сварщик перемещает горелку вдоль свариваемых кромок. Внешний вид полуавтомата для сварки в углекислом газе показан на рис. 5. |
Рис. 61 - автомат (нижняя часть) ; 2 - проволока; 3 - флюс; 4- основной металл; 5 - сварной шов; 6 - шлаковая корка; 7 - сварочная дуга. | 4. Автоматическая сварка под флюсом (рис. 6). При дуговой сварке под флюсом дуга горит под порошкообразным флюсом, слой которого полностью закрывает дугу и зону сварки. Электродом служит голая проволока. Флюс защищает расплавленный металл от газов воздуха и улучшает качество металла шва. Дуговая сварка под флюсом выполняется автоматами и полуавтоматами. Сварочный автомат - это аппарат, в котором подача сварочной проволоки в дугу и перемещение дуги по изделию механизированы. | |
Рис. 71 - горелка; 2 - баллон с аргоном; 3 - редуктор; 4 - ротаметр; 5 - сварочный преобразователь; 6 - присадочная проволока. | Рис. 81- горелка; 2 - присадочная проволока; 3 -основной металл; 4- сварной шов; 5 - газ; 6 - сварочная дуга; 7- вольфрамовый электрод. | 5. Аргонодуговая сварка вольфрамовым электродом осуществляется с использованием вольфрамового электрода, который закрепляется в горелке, и одновременной подачей защитного газа аргона, поступающего из баллона под давлением в зону сварки (рис. 7). С помощью редуктора устанавливается нужное давление, а ротаметр измеряет расход газа.Аргонодуговая сварка вольфрамовым электродом может быть как ручной, так и автоматической. Дуга горит между вольфрамовым электродом и основным металлом (рис. 8). Вольфрамовый электрод не плавится. Расплавляются основной металл и присадочная проволока, в результатечего образуется сварочная ванна, а после остывания - сварной шов. Аргон защищает сварочную ванну от вредного воздействия газов воздуха. |
газовая сварка, сварка, дуговая сварка
www.sibelektrod.ru
КЛАССЫ СВАРКИ.
Сварка является процессом, в результате которого получают неразъемное соединение. Оно создается при помощи установки межатомной связи между свариваемыми частями при общем или местном нагреве. Сегодня существует достаточно большое количество видов сварки. Все они подразделяются по физическим, технологическим и техническим признакам. Относительно физических признаков и формы используемой энергии выделяют классы сварки:
1) термический
2) термомеханический
3) механический.
Термический класс сварки включает в себя типы сварки, осуществляемые при помощи плавления. Здесь используется тепловая энергия. В этом классе различают такие типы сварки, как плазменная сварка, сварка дуговая, газовая сварка, электрошлаковая сварка. Самым распространенным видом считается электродуговая сварка. Здесь плавление происходит благодаря теплоте от электрической дуги. Также применяется ручная дуговая сварка, которая является универсальным. Она производится в труднодоступных местах, для небольших швов, при монтажных работах. Кромка деталей, которые соединяются, а также присадочная проволока сплавляются в результате электрошлаковой сварки. При плазменной сварке используется сжатая плазменная струя, оказывающая газодинамическое и тепловое воздействие. Такой вид сварки является достаточно многофункциональным. В ходе газопламенной сварки применяется присадочный материал, чтобы усилить швы.
Также классы сварки подразделяются на термомеханический класс, подразумевающий виды сварки, при которых используется давление и тепловая энергия. Данный класс подразделяется на следующие виды: диффузионная сварка и сварка контактная. Кратковременным нагревом без оплавления места соединения характеризуется контактная сварка. В таком случае создается пластическая деформация, в результате которой происходит непосредственно сварное соединение. При применении контактной сварки непосредственно место соединения разогревается при помощи электрического тока, проходящего в месте сварки по металлу.
Механический класс представлен видами сварки, производящиеся с применением механической энергии и давления. Этот класс выделяет ультразвуковую сварку, сварку взрывом, холодную сварку и сварку трением. В этом случае в месте сварочного контакта получается выделение наибольшего количество теплоты.
Классификация контактной сварки.
Контактная сварка включает в себя несколько видов. Классификация сварки зависит от нескольких признаков:
1.В зависимости от формы сварного соединения: рельефная, шовная, точечная, стыковая.
2.Конструкция соединения может быть либо стыковой, либо нахлесточной.
3. По отношению к состоянию металла в месте сварки: без расплавления и с расплавлением металла.
4. В зависимости от способа подвода тока: односторонняя и двусторонняя.
5. По степени перемещения роликов в процессе шовной сварки: шаговая или непрерывная.
Классы дефектности сварного соединения.
Оценка единичных дефектов по ширине в том случае, если толщина свариваемых элементом в пределах 45 миллиметров, может производиться по нормам третьего класса вместо четвертого. Оценка единичных пор и включений при кольцевом сварном соединении толщиной не больше 10 миллиметров, возможно производить по пятому классу. Имеется возможность допускать внутренний непровар, который располагается в месте смыкания корневого шва. Глубина его должна быть не больше, чем 10 процентов от толщины стенки корпуса, но также и не больше 2 миллиметров.
Непровар допускается в корневом шве, глубина не больше 10 процентов от номинальной толщины свариваемого элемента, но и не больше двух миллиметров:
- в угловом сварном соединении сосудов четвертой и пятой групп, которые предназначены для работы при температурных условиях не выше 0 градусов.
- в кольцевом стыковом соединении, которое доступно для сварки лишь с одной стороны и выполняется без подкладного кольца.
Классификация покрытых электродов.
На сегодняшний день в промышленности используются сварочные электроды для сварки углеродистой конструкционной стали. Такие электроды соответствуют ГОСТу 9467-60. Их основа состоит из разных механических признаков сварных соединений, выполняемых электродами. Кроме того, в наплавленном металле довольно сильно сокращается количество серы и фосфора.
Маркировка сварочных электродов обозначается буквой «Э». Дальше следуют цифры, которые обозначают самое нижнее значение, являющееся прочностью данного электрода. Согласно ГОСТу электроды выделяются от Э34 до Э145. Если после буквы «Э» идет буква «А», то это обозначает, что электрод может обеспечивать большое значение пластических характеристик. Электрод, имеющий характеристику Э34, дает достаточно низкую прочность и относится к таким электродам, которые называются тонким стабилизирующим покрытием.
elektrosvarshchik.ru
www.samsvar.ru