Использование плазмы для резки металлолома. Аппарат для резки металла плазмой
Как выбрать плазморез | Строительный портал
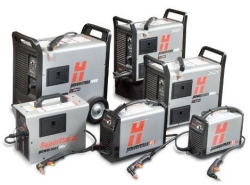
Плазморез нельзя назвать инструментом на каждый день в домашнем хозяйстве. В хозяйственных нуждах он пригождается редко, в основном в период интенсивного строительства. А вот в производственной и строительной сфере аппарат плазменной резки – незаменимая вещь. Вместо того чтобы мучиться и отрезать листовой металл ручной болгаркой, можно использовать плазморез, тогда работы будут выполняться быстро и качественно, срез будет ровным, аккуратным, без заусениц и окалины. Плазменная резка используется в машиностроении, для изготовления и ремонта металлоконструкций и техники, для резки труб и листового металла в коммунальной, хозяйственной сфере и рекламе. У новичка, никогда не работавшего с данной технологией, может возникнуть вполне резонный вопрос, как выбрать плазморез для тех или иных нужд. В данной статье мы расскажем о принципе работы плазмореза и о том, на какие характеристики необходимо обратить внимание при выборе.
- Преимущества и недостатки использования плазмореза
- Принцип работы плазмореза и расходные материалы
- Как выбрать плазморез
Преимущества и недостатки использования плазмореза
Всегда найдется индивидуум, который скажет, что ему удобнее работать болгаркой для легких работ и газорезкой в сложных ситуациях. И, честно говоря, это личное дело каждого, но эти личные предпочтения никоим образом не умаляют тех достоинств, которые может предложить плазменная резка.
Преимущества использования плазмореза:
- Скорость резки. При осуществлении резки металла толщиной до 50 – 60 мм производительность увеличивается в 5 – 10 раз. Более выгодной можно считать только лазерную установку для резки.
- Возможность обрабатывать любой металл: сталь, нержавеющую сталь, титан, чугун, медь, алюминий и сплавы. Нужно только правильно подобрать силу тока.
- Не нужно предварительно подготавливать деталь/заготовку – снимать ржавчину, краску или грязь. Они абсолютно не мешают процессу.
- Срез высокого качества. Он получается точным, ровным, без наплывов и окалины, дальнейшая обработка практически не требуется.
- Место среза нагревается лишь в узком диапазоне, поэтому тепловые деформации металла заготовок минимальны, даже если толщина металла очень маленькая.
- Безопасность в том плане, что не используются баллоны с газом. Для работы плазмореза необходим только воздух.
- Возможность делать срезы фигурной формы, ограничений по геометрии среза нет.
- Минимальное загрязнение окружающей среды за счет не использования газов.
Недостатки использования плазмореза:
- Относительно небольшая допустимая толщина металла для резки. В самых продвинутых промышленных моделях она не превышает 80 – 100 мм. Для сравнения для кислородной резки ограничение – 500 мм.
- Довольно жесткое требование перпендикулярного расположения относительно заготовки. Так максимальным отклонением считается 10 – 50 °, если превысить его, ширина реза увеличивается, а с ним и износ расходных деталей.
- Невозможность использования двух резаков, подключенных к одному аппарату.
Как видите, преимуществ у плазменной резки довольно много. С помощью нее можно резать и обрабатывать металл для дверей, ворот, фигурных оградок и заборов, изготавливать детали с отверстиями, кронштейны, лестницы, фасонные детали, систему отопления и вентиляции, разрезать и демонтировать большие конструкции и многое другое.
Принцип работы плазмореза и расходные материалы
Для начала давайте определимся, что такое плазма в данном конкретном случае. Плазма – это воздух, нагретый электрической дугой до очень высоких температур 25000 – 30000 °С и находящийся в ионизированном состоянии. Как известно, ионизированный воздух перестает быть диэлектриком и начинает проводить электрический ток, который расплавляет металл и выдувает его из зоны среза.
Плазмотрон – это главный рабочий орган плазмореза, а не сам плазморез, как иногда его называют. Плазмотрон – это плазменный резак, который подключен к основному аппарату с помощью пакета, состоящего из кабеля и шланга для подачи воздуха.
Плазмотроны бывают разными: прямого и косвенного действия. В случае использования плазмотронов прямого действия разрезаемая заготовка включена в электрическую цепь, другими словами дуговой разряд возникает между металлом и электродом в плазмотроне. Именно такая разновидность данных деталей устанавливается в аппаратах плазменной резки, используемых для обработки металлических заготовок. А вот для неметаллических деталей используются плазмотроны косвенного действия, тогда дуга возникает непосредственно в самом резаке.
Сопло – определяет возможности всего плазмотрона, оно может быть различных размеров. От диаметра сопла зависит, сколько воздуха может через себя оно пропустить, от этого зависит и размер реза и скорость и интенсивность охлаждения плазмотрона. Для плазменной резки обычно используют сопла маленького диаметра – до 3 мм и большой длины – 9 – 12 мм. Чем больше длина сопла, тем выше качество реза, но слишком большая длина приводит к быстрому износу и разрушению сопла и снижает надежность работ. Оптимальной считается длина сопла в 1,5 – 1,8 раз больше диаметра.
Электродом или катодом внутри плазмотрона выступает металлический стержень, преимущественно из гафния. В более дорогих аппаратах могут использоваться другие конструкции.
В процессе плазменной резки также используются газы: плазмообразующие и защитные. Так вот в аппаратах с максимальной силой тока до 200 А и рассчитанных на разрезание металла толщиной до 50 мм используется только воздух, который выступает и в качестве плазмообразующего, и в качестве защитного газа. В таком случае срез имеет удовлетворительное качество, хоть все же может быть некоторое окисление обрабатываемой поверхности. В более сложных промышленных системах используются другие газы – кислород, водород, аргон, гелий, азот и их смеси.
В конструкции плазмореза сопло и электрод являются расходными материалами, которые требуют своевременной замены. Ниже мы поговорим о том, на сколько их хватает.
Как выбрать плазморез
Итак, на что обратить внимание при выборе аппарата плазменной резки? Первое – универсальность. Например, аппараты под названием «плазморез CUT» предназначены сугубо для резки металлов. Но ведь помимо них есть и другие – аппараты, которые совмещают несколько функций одновременно: CUT – разрезание, TIG – аргонодуговую сварку и MMA – дуговую сварку штучным электродом. В зависимости от потребностей аппарат можно использовать для любой из этих целей. Но учтите, что такая универсальность плохо сказывается на качестве работ и итоговом КПД. В любом случае выбирать вам.
Плазморез FoxWeld Plasma 43 Multi как раз относится к универсальным аппаратам, предназначен для работы в сети с напряжением 220 В. Номинальная сила тока – 60 А, но ее можно регулировать: для MMA в диапазоне 10 – 150 А, для TIG – 10 – 160 А, а для плазменной резки CUT в диапазоне от 20 А до 40 А. Максимальная толщина металла, который можно разрезать с помощью такого аппарата, равна 11 мм (черные металлы и нержавейка). Стоимость данного плазмореза равна 530 – 550 у.е.
Виды плазморезов
Машины плазменной резки делятся на два вида:
Трансформаторный плазморез позволяет резать листовой металл до 40 мм толщиной.
Плазморез инверторный предназначен для разрезания металла до 30 мм толщиной. При этом потребляет меньше электроэнергии и обладает большим на 30 % КПД, чем трансформаторный. Еще один немаловажный момент – более стабильное горение дуги в инверторном аппарате, а также его компактность, позволяющая производить работы в труднодоступных местах.
Также плазморезы делятся на контактные и бесконтактные. Первым для начала работы необходимо прикосновение к металлу обрабатываемой заготовки, а вторым – нет. Как правило, контактный поджиг предусмотрен только у моделей, рассчитанных на разрезание 10 – 15 мм металла. Более сложные аппараты для разрезания металла 20 – 80 мм толщиной уже обладают бесконтактным поджигом.
И еще плазморезы бывают бытовыми и промышленными и различаются требованиями к энергосети. Например, бытовые модели могут работать от 220 В, а профессиональные только от 380 В. Учтите, плазморезы обладают колоссальной мощностью – более 4,5 кВт, не каждая сеть в частном секторе сможет выдержать такие нагрузки. Перед покупкой обязательно необходимо удостовериться в том, что ваша сеть справится с большими нагрузками, так как помимо плазмореза придется еще подключать и компрессор. Но об этом чуть позже.
Сила тока и толщина заготовки
Самыми главными зависящими друг от друга критериями выбора плазмореза являются сила тока и максимальная толщина металла, который может обрабатывать конкретный плазморез. Чем выше сила тока в плазморезе, тем дуга сильнее нагревает металл и соответственно быстрее его расплавляет.
Чтобы правильно подобрать плазморез по силе тока, необходимо точно знать, для обработки каких металлов будет использоваться аппарат, и какую толщину будут иметь заготовки. Для резки разных металлов нужны разная сила тока. Ее можно посмотреть в таблице ниже.
Таблица 1. С какой силой тока необходимо резать различные металлы.
Например, вам необходим аппарат, с помощью которого вы собираетесь разрезать листовую сталь толщиной 3 мм, тогда считаем: 3х4=12 А. Не стоит брать плазморез с минимальным показателем, т.е. 12 А, так как это значение является идеальным вариантом. Лучше взять аппарат с запасом не менее 25 – 30 %, т.е. рассчитанный на силу тока в 20 А.
Если необходимо разрезать медную заготовку толщиной 40 мм, то понадобится аппарат 40х6= 240 А, т.е. профессиональный – промышленный.
Важно! Всегда берите плазморез с запасом по силе тока, чтобы не перегружать его. Рассчитывайте максимальную толщину металла самостоятельно, так как чаще всего в технических характеристиках указывается толщина из расчета, что резаться будет черный металл.
Яркий тому пример плазморез TelWin Superior Plasma 60 HF 400V с силой тока 60 А, но в характеристиках указана толщина 20 мм. Если же подсчитать, то для разрезания 20 мм меди необходимо 120 А. Кстати, данный аппарат рассчитан на сеть с напряжением 380 В и обладает мощностью 7,5 кВт, так что для домашнего использования явно не подойдет. Стоимость такого плазмореза равна 1770 – 1780 у.е. Преимуществами данной модели являются: микропроцессор, облегчающий работу, потенциометр для регулирования силы тока с шагом в 15 А, встроенный манометр для определения давления воздуха, штекерные входы для быстрого соединения кабелей. Ну и, конечно же, в комплект входит плазмотрон.
Вообще же итальянский бренд TelWin выпускает различные модели с силой тока на 25 А, 40 А, 50 А, 60 А, 80 А, 90 А, 120 А, 160 А. Но производятся они не только в Италии, но и в Китае, поэтому обратите пристальное внимание на страну производителя, указанную на упаковке. Хотя сам производитель утверждает, что в любом случае стандарты Евросоюза соблюдены.
Продолжительность включения
Интенсивность использования плазмореза имеет очень большое значение при выборе аппарата.
В характеристиках плазморезов есть такая графа как ПВ (продолжительность включения), которая исчисляется в процентах. Какое время аппарат может работать, а какое ему необходимо для отдыха и охлаждения. За основу берется рабочий цикл в 10 минут. Например, если ПВ = 40 %, то это означает, что плазморез может работать 4 минуты и далее требуется 6 минут отдыха. Если ПВ=80 %, то время работы – 8 минут и время отдыха – 2 минуты.
Важно! Продолжительность включения плазмореза зависит от силы тока. Чем выше сила тока, используемая в процессе работы, тем меньше продолжительность включения.
Если планируется нечастое проведение резки металлоконструкций на стройке, то достаточно будет плазмореза попроще, с ПВ менее 50 % или равным 50 %. В таком случае он будет использоваться для вспомогательных работ. Если же планируется резка металла в течение всего рабочего дня, тогда необходимо подбирать аппарат с ПВ максимально приближенным к 100 %, кстати, есть модели с ПВ=100%, их можно использовать в течение всей рабочей смены без перерывов, но в них чаще всего используется водяное охлаждение.
Среди доступных бытовых моделей, представленных на рынке, плазморез Сварог обладает самой большой ПВ, равной 60 % на максимальном токе. Особенно это касается моделей с силой тока выше 60 А, рассчитанных на сеть 380 В. Кстати, если Вы думаете, что чисто славянское слово «сварог» означает, будто эти плазморезы российского производства, то вынуждены вас огорчить, - нет, это лишь выгодное маркетинговое название сугубо китайского продукта, импортируемого в Россию.
Все остальные плазморезы известных марок TelWin, FoxWeld и BlueWeld обладают продолжительностью включения не больше 35 %.
А вот плазморез Ресанта ИПР-25 китайского производства (бренд из Латвии) имеют такую ПВ на 25 А= 35%, ПВ на 20 А= 60 А, а ПВ на 15 А=100%. Диапазон силы тока в данной модели от 5 до 25 А.
Встроенный компрессор или внешний
Для образования плазмы необходима подача сжатого воздуха, и от того, откуда берется этот воздух, зависит, есть ли у плазмореза встроенный компрессор или необходим внешний. Модели плазморезов с встроенным компрессором обладают не слишком большой мощностью, поэтому используются только в бытовых условиях и на частных предприятиях. Такие аппараты удобны для перемещения и использования в трудных местах, так как не требуется подключение к пневмосети.
Для постоянного использования плазмореза в течение целого рабочего дня необходим внешний компрессор. Обязательно необходимо обратить внимание, что расход воздуха в плазморезе не должен быть больше, чем количество производимого компрессором сжатого воздуха. Ну и, конечно, давление воздуха в плазморезе не должно превышать давление, которое обеспечивает компрессор. Только правильное соотношение этих параметров обеспечивает стабильную дугу и высокую производительность работы плазмореза в течение всего рабочего дня.
Важно! Воздух должен быть абсолютно сухим, не содержать масла и других посторонних примесей. Для осушения необходим специальный влагоотделитель. Поступать воздух должен с равномерной скоростью, без пульсаций.
Крайне важно соблюдать указанное условие и обязательно следовать инструкции к плазморезу. Неправильная эксплуатация приведет к быстрому выходу из строя, а вы даже не поймете, что же произошло. Например, в поисках самого надежного самого лучшего аппарата вы остановили свой выбор на плазморезе Hypertherm американского производства на 45 А, который стоит почти 3000 у.е., но в первый же день работы у вас сгорит ручка плазмотрона. И никто вам не заменит ее по гарантии. Почему?
Представьте себе, между соплом плазмореза и электродом вырывается плазма с температурой 20000 °С, вырывается она за счет движущегося воздуха со скоростью 60 – 100 л/мин. И теперь представьте, что будет происходить, если подаваемый воздух будет не сухим, а с примесью влаги. Эта влага будет взрываться прямиком в плазмотроне, при этом пострадают циркониевое вкрапление на электроде, сам электрод, диффузор и сопло. Придется все это покупать, благо все вышеперечисленное является расходниками и доступно в продаже отдельно от аппарата.
Частота замены расходников
Самыми частозаменяемыми деталями плазмореза являются электрод и сопло. Обычно они выходят из строя не одновременно, например, на одно сопло хватает два электрода. Но все индивидуально, бывает, что приходится менять одновременно.
Частота замены расходников слишком прикладной вопрос, на него нельзя ответить заочно. Все зависит от интенсивности использования аппарата, толщины разрезаемого металла и силы тока. Например, некоторые говорят, что одного сопла хватает на одну рабочую смену (один рабочий день), если толщина металла не превышала 10 мм. Другие, что расходников хватает на 500 – 600 резов, а третьи, что на 150 м реза. Какой способ исчисления вам ближе, на тот и ориентируйтесь.
Износ сопла выглядит как нарушение его геометрической формы, а это может негативно влиять на качество реза. Износ электрода – выработка стержня, максимально допустимая 1,5 мм. Если не проследить за этим, то при большей выработке катода он может пригореть к головке плазмотрона, что приведет к выходу его из строя.
Именно поэтому модель плазмореза необходимо подбирать в зависимости от наличия к ней расходных материалов в свободном доступе. Неплохим вариантом является плазморез BlueWeld китайского производства и TelWin, ко всем ходовым моделям имеются сопла и электроды по вполне доступным ценам до 25 у.е.
Удобство использования плазмореза
Немаловажный фактор выбора плазмореза – удобство. Первое, что может повлиять, это длина пакета кабель-шланга. Чем он длиннее, тем дальше можно отойти от аппарата, и тем более удобно разрезать широкие листовые материалы. Тем не менее, один пакет длиной 20 – 30 м тоже не слишком удобен, так как его каждый раз необходимо раскручивать, даже если работы будут проводиться в 2-х метрах от аппарата. Именно поэтому желательно выбирать модели с евроразъемами для подключения пакетов. Так можно купить модель с пакетом 6 – 12 м, которые можно менять и наращивать по мере необходимости длину. К тому же, учтите, что при длине кабель-шлангового пакета более 20 м теряется мощность. Поэтому использовать пакеты большой длины лучше в условиях необходимости, например, для работ на открытом воздухе, чтобы не выносить аппарат.
Отдельно хотелось бы сказать про плазморез Горыныч, разработанный российскими учеными. Это многофункциональной устройство работает на воде, имеет силу тока 3 – 10 А, объем требуемой для работы жидкости 80 мл. Данный аппарат хорошо зарекомендовал себя в разных сферах – при монтаже подземных и наземных коммуникаций, в том числе водопровода и отопления, в работе по камню и стеклу, при ремонте холодильников, вентиляционных систем и кондиционеров, а также для резки и выполнения отверстий в любых металлах. Стоимость такого плазмореза 800 у.е.
В заключение несколько слов о технике безопасности. Не стоит работать плазморезом при отрицательных температурах, нельзя дожидаться полного износа расходных материалов – сопла и электрода. И самое главное – если у вас нет опыта работы с плазморезом, не начинайте работу самостоятельно, попросите помощи у опытного специалиста или понаблюдайте за его работой и только затем пробуйте сами.
strport.ru
строение и принцип работы, плюсы
Среди множества способов раскроя, плазменную резку металлов называют в числе наиболее популярных. Технологию поддерживает специальное оборудование – плазморезы с числовым программным управлением.
Их широко используют во многих отраслях. При помощи этой машины точно, эффективно производятся элементы строительных металлоконструкций, детали для различного оборудования, компоненты сельхозмашин, металлические двери, стеллажи учреждений торговли; вентиляционные устройства в промышленности, множество другой продукции.
Строение и принципы работы
Плазменный станок с ЧПУ представлен различными моделями, которые отличаются по типу устройства, схемой управления и методом подачи материала. Но у них обязательно наличие таких составляющих:
- плазмотрон с системой подачи газового вещества;
- поворотная поверхность рабочего стола для облегчения установки металлолистов;
- механизм передвижения резака и система магнитных креплений;
- датчик контроля для управления высотой горелки над поверхностью заготовки;
- профильная рельса и по обе стороны от нее две зубчатые рейки;
- системы ЧПУ.
Плазморез отличается простым принципом работы. Поступивший на резак поток воздуха с определенным давлением, соприкоснувшись с электродом, приобретает температуру, максимум, до 30 000˚ С. У ионизированного воздуха возрастает электропроводность.
Как итог, металл расплавляется от контакта с направленным потоком раскалившегося воздуха или газовой смеси (это и есть плазма), и отрезанная часть отбрасывается, благодаря давлению. Так проходят процессы плазменной резки металла с ЧПУ. Обработав программу, заданную оператором агрегата, аппарат, используя плазму, режет листы металла самостоятельно, а участие людей в процессе – минимальное.
Эксплуатационные преимущества аппарата
Станок плазменной резки металла с ЧПУ владеет некоторыми преимуществами:
- рабочие операции по раскрою металлических листов сложной конфигурации выполняются с уникальной точностью;
- плазморез отличается низким потреблением электроэнергии, не нуждается в дополнительных устройствах и финансовых затратах. Производственные издержки снижаются, а рентабельность возрастает;
- аппарат имеет высокую производительность плазменной резки ЧПУ. Ни одно устройство, занимающееся раскроем металлов (кроме лазера) неспособно достичь аналогичной скорости, какая есть у плазмореза. Этим обусловлено его промышленное применение для выпуска массовой продукции;
- аппарат удобен в эксплуатации и прост в обслуживании;
- устройство способно разрезать плазмой листы всех металлов, низколегированных и углеродистых сталей, чугуна толщиной от 0,5 до 150 мм, обеспечивая чистоту среза. Дополнительная обработка торцов раскроенных заготовок не нужна;
- плазморезы, работающие без выделения газа и открытого огня, — безопасны;
- есть функция автоматического определения толщины листа металла.
Недостатков у данного оборудования практически нет. Но их не используют для раскроя листов высоколегированной стали с толщиной, превышающей 10 см, а также титана.
При грамотном регулярном обслуживании, можно гарантировать плазморезу большой срок службы. О специфике, периодичности его выполнения можно узнать из видео материалов.
Особенности процесса резки
Пользуясь плазморезами, надо учитывать их технические характеристики, химсостав применяемых смесей, параметры изделий, особенность их обработки.
Если у листов небольшая толщина (до 1см), достаточно будет иметь температуру маломощной плазменной дуги. Заготовки с большей толщиной можно кроить, добавочно стабилизировав дугу. Когда же толщина превышает 10 см, нужны плазменные установки, которые в состоянии сформировать дугу с более мощным воздействием.
Много значат виды источника. Для тонколистовой стали до 6 мм достаточно иметь небольшой ток. Чтобы обрабатывать листы, вдвое толще, понадобится источник с высоким уровнем тока. Когда же источник тока окажется более слабым, участки срезов будут иметь отложения шлака.
Ответственного подхода требует выбор составов, которыми обрабатывают заготовки, готовят их к раскрою. Обычно это смеси, содержащие аргон, азот и водород, в случае с медными сплавами, предпочтение отдают водороду. А вот при разрезании изделий из латуни, алюминия наиболее приемлемо сочетание таких элементов, как азот и водород.
Экономичными считают станки плазменной резки, технологический процесс на них по раскрою стали, алюминия или меди производится с применением воздуха.
Существуют модели плазморезов, которые способные разрезать несколько листов за один прогон. Когда же настрой на особое качественное резание, применяются плазмотроны на кислороде.
Что касается стола машины, под ним расположена система удаления частиц дыма, отходов металла. За резкой металлических листов осуществляется контроль со стороны ЧПУ блока. ПО (в корректном русском переводе) отслеживает процесс укладки их на стол в оптимальном режиме, производит расчет затрат времени, количества деталей, составляет отчеты.
А что в обзоре плазморезов
На предприятиях различных отраслей используют:
- стационарные модели, среди них есть машины портального; шарнирного; консольного типа для резки металла при помощи плазмы;
- мобильные или переносные такого же предназначения (вертикальная плазменная резка), оборудованные системами ЧПУ.
Сегодня несложно сделать выбор плазменного станка, — есть много производителей, специализирующихся на изготовлении устройств подобного рода. Ассортимент представлен отечественными и зарубежными моделями. Назовем и кратко охарактеризуем хотя бы некоторые из них:
- Установка PlasmaCut от российской компании Юнимаш ориентирована на то, чтобы ее применяли на предприятиях среднего и малого бизнеса. Источник плазмы Hypertherm – из числа наиболее технологичных, в наличии механизм FOCUT, осуществляющий контроль за высотой резака, мощные ШД. Управлять ним можно дистанционно, посредством USB и Ethernet, со стойки, на которой смонтирован пульт управления.
- Станок IGNIS для плазменной резки с ЧПУ (Россия) представляет несколько модификаций – IGNIS 2500, 3000 и 6000 с разными габаритами, мощностью плазмообразующего источника и грузоподъемностью. Все они рассчитаны на применение при толщине металла 28 мм, имеют стабильный спрос и применимы в техническом оснащении небольших по масштабу работы мастерских, предприятий.
- Powermax считается машиной уникальных свойств, способной выполнять плазменный раскрой изделий, различных по виду и форме.
- PlasmaBox – отличный станок из серии многокоординатных, имеет четыре ШД, работающих с разными мощностями.
- РВ 6000, РМ 3000, PS 2500 – агрегаты, выполняющие нарезку заготовок с разной длиной и толщиной.
Все эти высокопроизводительные станки пользуются системой ЧПУ фирмы AMN. В некоторых моделях для применения в промышленности, плазмотрон охлаждается принудительно под воздействием жидкости, у остальных охлаждение – естественное воздушное.
Замолвим слово и о труборезах
Очень популярны и труборезные станки, которые можно отнести к группе портальных. Например, для резки труб применяют Автом-3 с плазменным резаком. Его скорость в несколько раз превышает аналогичный показатель газового резака. Наиболее востребованы станки плазменной резки, рассчитанные на раскрой стальных труб, с толщиной стенок 38-40 мм. Они способны резать трубу достаточно быстро, и ее отрезки будут с ровными краями.
Если нужно разрезать трубы диаметром от 100 до 315 мм из нержавейки или малоуглеродных сортов стали (при толщине до 2 мм), которые будут применяться в монтаже систем промвентиляции, наиболее эффективен труборез ТВ-30. Он способен работать в режиме ручного управления или автоматического, имея систему ЧПУ. Плазменным оборудованием этого типа можно пользоваться от сети с напряжением 380 В, с давлением подаваемого сжатого воздуха выше 0.6 МПа.
Достижения высокой точности послужит труборез с ЧПУ Vanad Miron. Технологические операции по резке труб выполняются автоматически, обязательно наличие температуры +5 – + 40˚С и вытяжной вентиляции.
Труборезный станок способен выполнять некоторые подготовительные действия при подготовке поверхности: зачищать сварочные швы, снимать фаску и разделывать кромки. У него есть возможность резать, помимо круглых, трубы квадратного или прямоугольного сечения.
Труборезную установку переносного типа использую при выполнении работы в труднодоступном месте в случае малосерийных заказов. Например, у плазменных станков Титан ПИПР 15-5 есть однофазный инвертор, выполняющий воздушно-плазменную резку, здесь применяется контактный способ дугового зажигания.
А если сделать плазменный станок самому
На станке с ЧПУ для плазменной резки металла можно сделать много полезных вещей. В нем заинтересованы небольшие мастерские по изготовлению металлических дверей. Но стоит это оборудование (особенно импортные варианты) — недёшево, поэтому некоторые домашние мастера стремятся его собрать самому из частей труб квадратных сечений.
Важно знать, что агрегат, несложный по конструкции, сделать без знаний и умений невозможно. Особенно сложно собрать сам плазмотрон. Но составляющие части аппарата и ЧПУ для управления станком реально приобрести отдельно в специализированных онлайн-магазинах.
Хотя возможны варианты электромагнитной и фотоэлектронной систем управления, но именно плазменные станки с ЧПУ способны обеспечить наиболее точную и быструю работу. Домашнему умельцу, заинтересованному в оборудовании, предстоит также собрать систему подачи газа, добиться высокой точности позиционирования, чтобы в полной мере пользоваться возможностями этого аппарата, предусмотренными его техническими характеристиками.
Заключение
Плазомрез с программным управлением для раскроя металла в листах и труб, работающий в бесперебойном цикле, — с очень большими возможностями. К станку у многих особое трепетное отношение. Но все модели, которые поставляются российским потребителям, — весьма просты в эксплуатации и обслуживании. И научиться работать на них смогут люди, имеющие спецподготовку по профилю металлообработка.
vseochpu.ru
Резка металлолома плазмой
Плазма является высококонцентрированным источником тепловой энергии, которая с успехом применяется для разделительных операций с различными металлами. Во многих случаях резка плазмой считается более эффективной технологией разделки металлолома, поскольку не нуждается в кислороде и горючих газах, а также позволяет эффективно разделять металл в различных условиях своего применения.
Мобильная установка для резки нержавейки
Сразу хочется сказать о плюсах такого оборудования, как мобильная ручная плазморезка, применительно к теме — лома и ломозаготовки цветных металлов, а конкретнее лома нержавейки.
Часто в металлолом идут емкости из нержавейки — это могут быть обычные пивные кеги (которые необходимо утилизировать — порезать и превратить изделие в лом), другие емкости — ж/д цистерны из нержавейки, пищевые емкости, огромные цистерны на химических заводах и другое. Все эти емкости необходимо демонтировать на месте, «покрошить» для перевозки. Для резки таких изделий обычное оборудование, которым режется черный лом — кислород и пропан, не подойдет, т.к. нержавеющая сталь относится к жаропрочным сталям и температуры кислорода с пропаном будет недостаточно. В этом случае на помощь придет мобильная установка плазменной резки.

Мобильная установка плазменной резки
С ее помощью легко можно резать нержавейку толщиной до 5мм, если требуется работа с более толстыми листами, то нужно подбирать под каждую задачу свою установку. Т.к. как оборудования подобного рода имеет высокую цену, то для начала (для демонтажа единичного объекта, где требуется порезать емкости) лучше поискать плазморезку в аренду.
Конечно, резка емкостей из нержавейки это не единственное преимущество плазменной установки, скорость резания, работа с более толстыми листами металла — вот основные преимущества «плазмы».
Но есть и недостатки — это массивность дополнительного оборудования, а также обязательное наличие компрессора, в некоторых случая резка плазмой будет обходиться дороже, поэтому, если есть возможность, то дешевле будет резать обычным резаком — кислородом.
Видео — как работает установка для ручной воздушно-плазменной резки металла:
Принцип резки металлов высококонцентрированной плазмой
Для локального повышения температуры в зоне плазменного столба необходим мощный источник энергии (им в большинстве типов промышленных установок является обычный сварочный генератор и концентрированный поток окисляющего газа), а также герметичный объём, где возбуждается разряд.
Последовательность резки металла при газовой и плазменной резке разная. В первом случае резак имеет в своём составе две коаксиально размещённых трубы. Через одну из них – внешнюю – под большим давлением прокачивается инертный газ (это может быть аргон или двуокись углерода), задача которого – сжать поток пламеобразующего газа – кислорода, который в это же время подаётся по внутренней трубе плазмотрона. Такая конструкция ограничивает неконтролируемое распространение пламени по разделяемой поверхности, повышает энергетические характеристики источника тепла, и исключает оплавление кромок разрезаемого фрагмента лома. В стационарных аппаратах современного типа перемещение инструментальной головки может программироваться, в зависимости от конфигурации исходного изделия. Резка на плазме при помощи плазменных резаков переносного типа производится перемещением инструментальной головки самим оператором.

Принцип плазменной резки металла
В электрических плазмотронах сжатие столба дуги производится поперечным потоком среды-диэлектрика (чаще всего ею является индустриальное масло, хотя может быть и вода). Для создания больших давлений, которые достигают 5…10 ат, в комплектацию электрического плазмотрона входит также соответствующая насосная установка. Это снижает компактность оборудования, поэтому плазменные резаки с применением электрического дугового разряда применяются на специальных участках, для разделки особо крупногабаритных фрагментов лома (размерами более 200 мм). Их преимущество – высокая производительность процесса, которая достигает по стали 20000 мм3/мин, а при пониженных требованиях к точности – и 40000 мм3/мин.

Технология плазменной резки
Для резки лома чугуна, алюминия и других цветных металлов постепенно приобретает распространение технология мультиплазмирования, для которой характерно возбуждение электрического разряда в водной или спиртсодержащей среде. Соответствующие аппараты отличаются компактностью, однако требуют высококвалифицированного обслуживания и настройки.
Независимо от конструкции, аппарат для резки металла плазмой создаёт в рабочей зоне локальные температуры от 6000 до 200000С, чего достаточно не только для размерного плавления наиболее тугоплавких металлов, но и для размерного испарения частиц, которые выносятся потоком среды из зоны разделения. Скорость потока при этом достигает 500…1000 мс.
Конструкции и работа плазменных резаков
Основным узлом газовых плазменных резаков является инструментальная головка. Она включает в себя:
- Защитный внешний кожух их жаропрочной стали.
- Сопло (в комплект к аппаратам входит несколько конфигураций, которые используются для плазменной резки различных профилей).
- Охлаждающий узел, которым предотвращается перегрев катода.
- Охладитель рабочего сопла, исключающий его тепловую деформацию, особенно при длительной резке.
- Трубопроводы для подачи инертного и плазмообразующего газов.
Для стационарных установок плазменной резки в конструкции предусматривается подвижный стол, на котором закрепляется разрезаемый фрагмент металлолома. Такой стол имеет программируемое перемещение с задаваемой точностью и производительностью резки.

Стационарная плазменная установка
Все электрические дугоплазмовые резаки являются устройствами прямого действия, в которых возбуждаемая дуга включается в общую электрическую цепь. Безопасность их применения обеспечивается надёжной термоизоляцией токоведущих элементов установки от прочих деталей оборудования. В качестве материала электрода используется графит марок МПГ иди ЭЭГ, хотя при малых требованиях к точности может применяться и медь. При постепенном повышении тока дуги происходит ионизация межэлектродного промежутка, и образующаяся плазма производит размерное разделение металла. Сам процесс протекает в переносной герметизированной камере, которая перекрывает всю зону разделения, и препятствует снижению рабочего давления прокачиваемой рабочей среды. При понижении давления точность такой резки заметно снижается, а сам процесс превращается в размерное плавление металла. Поэтому рабочее давление прокачки не может быть менее 3…4 ат.
Электродуговая резка плазмой – единственный способ резки лома твёрдых сплавов

Электродуговой ручной плазменный металлизатор
Качество ручной плазменной резки зависит только от квалификации и выносливости оператора. Поэтому для облегчения условий его труда такие аппараты снабжаются комплектом переносных упоров. Упоры устанавливаются на сопло, вследствие чего отпадает необходимость в том, чтобы держать резак навесу.
Для работы плазменных резаков, использующих газовый способ инициирования плазмы, необходимо непрерывное поступление инертного газа (чаще – азота), при помощи которого из зоны реза удаляют грат и застывшие частицы металла. В качестве источника подачи таких газов используются либо баллоны, либо стационарная магистраль.
Все плазмотроны работают от электрического источника постоянного тока. Исключение составляет резка лома алюминия, которая ведётся на переменном токе.
Видео — как режет аппарат плазменной резки Aurora PRO Airhold 40:
Технические характеристики аппаратов плазменной резки
Ниже приведены сравнительные характеристики газовых плазменных резаков, способных разделять фрагменты лома чёрных и цветных металлов:
Модель | Способ возбуждения разряда | Наибольшая толщина резки, мм | Напряжение питания, В | Наличие компрессора | Мощность, кВт | Длинга шлинга, м | Рабочий ток, А |
Сварог CUT70 | Инвертор | До 20 | 380 | — | 9,5 | 1,5 | 20…60 |
FUBAG 65T | Выпрямитель | До 30 | 380 | — | 6,8 | 6 | 20…65 |
BRIMA CUT120 | Выпрямитель | До 40 | 400 | + | 18,0 | 3 | 20…120 |
Для выбора подходящей модели плазмотронов, реализующих электрический способ возбуждения дуги, можно воспользоваться данными следующей таблицы:
Тип | Наибольшая толщина резки, мм | Напряжение питания, В | Рабочий ток, А | Потребляемая мощность, кВт |
Telwin Plasma 34 | До 6 | 220 | 5…25 | 6,5 |
DecA PAC1235 | До 12 | 220/380 | 5…35 | 4,0 |
HyperthermHPR800 | До 160 | 380 | До 40 | 24,0 |

Установка плазменной резки HyPerformance HPR400XD и брусок толщиной 140 мм
xlom.ru
Плазменная резка металла: станки с ЧПУ
Что такое плазменная резка и ее особенности
Плазменная резка – один из способов обработки металла. Между электродом и соплом зажигается электрическая дуга, температура которой может достигать 30 тыс. градусов, а скорость 1500 м/с. Плазма без особых усилий режет металл в 200 мм толщиной.

Образование луча плазмы происходит посредством достижения короткого замыкания между форсункой и заготовкой или поджиганием высоковольтного импульса. Для образования плазмы используют два типа газов: активные (кислород или воздух) и малоактивные (азот, аргон или водород). Первая группа газов применяется для обработки черных металлов, а вторая – цветных.
Кислород применяется для работы с низколегированными и мягкими типами металла. Резка с использованием кислорода позволяет избежать улетучивания железа и образования заусениц. Однако дешевизна воздуха и высокая эффективность не компенсируют его недостаток – им нельзя обрабатывать заготовки, толщина которых превышает 20 мм.
Достоинства и недостатки плазменной резки
К достоинствам относятся такие пункты:
- Технология позволяет обрабатывать все типы металлов;
- Высокая скорость обработки средних и тонких листов;
- Небольшая площадь нагревания поверхности материала, что позволяет обрабатывать заготовку без тепловой деформации;
- Высокая скорость и качество среза;
- Абсолютная безопасность, поскольку на производстве отпадает необходимость устанавливать баллоны со сжатым воздухом;
- Гравировка и фигурная резка. Технология позволяет выполнять даже самые сложные схемы резки.

Наряду с достоинствами, плазменная резка металла имеет несколько недостатков:
- Дороговизна оборудования;
- Максимальная толщина, с которой может работать плазмотрон, составляет 10 см;
- Высокий уровень шума создается газом, вылетающим на скорости звука. Оператор должен находиться в шумоподавляющих наушниках;
- Плазмотрон требует только профессионального обслуживания и установки подлинного программного обеспечения.
Плазменная резка эффективно справляется с обработкой металлических заготовок, толщиной до 80 мм. В отличие от кислородно-газовой резки, которая нуждается в контроле интенсивности и скорости, плазменная резка не нуждается в мониторинге этих параметров. По этой причине она применяется в узкоспециализированных сферах обработки металла, например, в резке растянутых металлических пластин. Кроме этого, плазма быстрее и эффективнее справляется с нелинейной резкой.
Плазменная резка требует свободного доступа к баллонам со сжатым воздухом и сети питания, что вызывает некоторые трудности у операторов станка.
Виды и типы станков для плазменной резки
Самым простым оборудованием для обработки металла считается обычный ручной аппарат. Это оборудование применяется в индивидуальных хозяйствах. На промышленных объектах предпочитают использовать мощную аппаратуру ЧПУ (числовое программное управление). Такие станки отличаются высокой производительностью, точностью, и качеством резьбы. Оборудование с ЧПУ применяется преимущественно для автоматического раскроя материалов.
Установка для ручной воздушно-плазменной резки металла
Таким образом, все оборудование условно можно поделить на две группы – переносные и стационарные установки. Ручной аппарат относится к мобильным станкам, стационарное оборудование принято делить на несколько видов:

- Портальные станки справляются с раскроем металла, толщина которого достигает 80 мм. Отличаются высокой скоростью и качеством обработки;
- Портально-шарнирные станки производят резку только в вертикальном направлении;
- Шарнирные станки имеют специальную раму для крепления заготовки. Шарнирное оборудование может резать, гравировать или вырезать декоративные элементы на материале. В большинстве случаев такие станки поддерживают ЧПУ.
Рассмотренные виды станков позволяют сделать вывод, что самым совершенным оборудованием считается станок плазменной резки металла с ЧПУ. Аппарат способен не только быстро обрабатывать заготовки, но и работать в автоматическом режиме. Роль оператора в этом случае сводится к минимуму – он запускает компьютерную программу и контролирует работу станка, корректируя при необходимости его действия.

Сложное оборудование нуждается в дополнительных системах электропитания, баллонов с воздухом и газами. Высокотехнологическое оборудование работает с заготовками быстро и эффективно, сводя финансовые и временные затраты к минимуму.
Обзор станков с ЧПУ
Сфера применения высокотехнологического оборудования достаточно обширна. Станки с ЧПУ применяются в:

- Плазменной резке металла на заказ;
- Изготовление деталей для любых видов техники и электроники;
- Формирование заготовок для фрезерной или токарной обработки;
- Изготовление металлических конструкций – заборов, дверей, решеток и т. д.;
- Производство элементов вентиляции и металлоконструкций.
Кроме этого, технология плазменной резки используется в машиностроении, авиационной промышленности, изготовлении рекламы, производстве техники и других отраслях.
Станок Vanad Mira 15/30 (Чехия) поддерживает несколько скоростных режимов, развивая скорость вплоть до 10 м/мин. Аппарат предназначается для нарезки металлических листов на производстве. Рабочая поверхность состоит из стола и мобильной конструкции. Система ЧПУ обеспечивает комплексное управление двигателями, что позволяет контролировать степень деформации материала.

Система ЧПУ вмещает больше 20 Гб памяти на жестком диске. Программное обеспечение позволяет редактировать системные файлы без привлечения специалистов. Стоит отметить, что система ЧПУ защищается ключом безопасности, это означает, что доступ к системным файлам есть только у строго фиксированного круга лиц.
PCM1530S – это станок с ЧПУ для лазерной резки листового металла. Особенности модели:
- Оператор может чистить рабочую поверхность во время обработки детали;
- Для удобства загрузки или выгрузки производитель предусмотрел направляющие ролики;
- Жизненно важные элементы прикрываются кожухами, которые защищают оборудование от попадания абразивных частиц;
- Высоковольтные кабели защищаются прочными оболочками, что минимизирует вероятность повреждения.

Hypertherm (США) – станок для плазменной резки размерами 1550 на 3100 мм. Аппарат обрабатывает листы из оцинкованной и тонколистовой стали, толщина которых не превышает 0,5–8 мм. Сфера применения: средние и крупные предприятия, занимающиеся производством деталей для автомобилей и техники. ЧПУ позволяет проводить высокоточное гравирование и фигурную резку.
SPS-3400 – станок с ЧПУ от корейской компании «Space ONE». Аппарат способен поддерживать высокую скорость обработки деталей (до 4 метров/минуту). Максимальная скорость работы составляет 6 метров/минуту.
Особенности системы:
- Длина, ширина и высота рабочей поверхности: 1280*2600*150 мм;
- Производитель гарантирует качественное обслуживание ЧПУ и онлайн поддержу установленного программного обеспечения;
- Аппарат способен выполнять не только резку, но и раскрой, гравировку и фигурную резьбу по металлу.
Реклама партнеров
Видео: Станок плазменной резки и раскроя металла
Похожие статьи
promtu.ru
Станки плазменной резки металла | Техника и человек
При малых объёмах производства заготовок из листового металла, имеющих сложную конфигурацию, использование листовой штамповки экономически невыгодно. Предпочтение отдают технологии плазменной резки, для реализации которой не нужна специализированная штамповая оснастка, а производительность и качество поверхности раздела (при правильно подобранных параметрах технологического режима) оказываются вполне приемлемыми.
Сущность технологии
При плазменной резке разделение металла происходит вследствие целенаправленного теплового воздействия концентрированной газовоздушной струи на разрезаемую поверхность. Обеспечив сжатие такой струи до сечений порядка 0,2…2 мм2, можно создать такую объёмную плотность тепловой мощности, которая позволяет успешно резать даже тугоплавкие и жаропрочные стали.
Процесс может быть реализован в двух разновидностях – контактной и бесконтактной. В первом случае источником тепла является столб кислорода или ацетилена, сжимаемый извне инертным газом, например, аргоном. Внешне это напоминает обычную газопламенную резку, но, в отличие от неё, характеризуется значительно более высокими скоростями перемещения газов, и давлениями, под которыми горячая смесь поступают в зону реза. Во втором случае источником тепла является электрическая дуга, сжимаемая поперечным потоком диэлектрической рабочей среды. Ею может быть масло, керосин (по отдельности, либо в виде эмульсии) и даже вода.
Бесконтактная плазменная резка происходит так. В рабочей головке станка размещены две трубы, коаксиально расположенные одна относительно другой. Торец рабочей головки представляет собой суживающееся сопло. По внутренней трубе прокачивается газовоздушная горючая смесь, а по наружной – инертный газ.
Сопло подводят на расстояние 5…15 мм от поверхности раздела, после чего последовательно включают подачу кислорода/воздуха и ацетилена, а затем – инертного газа. Отрегулировав сечение газовоздушной струи соответственно необходимым показателям качества и производительности резки, горючую смесь поджигают, а затем по специальной программе или вручную перемещают рабочую головку вдоль поверхности разделения. Более современным является способ, когда газовоздушную смесь поджигают не пламенем, а переменным электрическим разрядом.
При контактной плазменной резке все составляющие процесса – электрод и заготовку включают в общую электрическую цепь станка. Чаще всего используется обратная полярность электрического тока, когда анодом служит разрезаемый металл, а катодом – электрод рабочей головки станка.
При подаче тока большой мощности (350…500 А и более) и с первоначальным касанием анода и катода происходит пробой межэлектродного промежутка с формированием дугового разряда. В дальнейшем, чтобы не допустить короткого замыкания, анод и катод разводят на величину межэлектродного промежутка в 0,5…0,8 мм. В отличие от дуговой сварки, столб дуги при плазменной резке сжимается в своём поперечном сечении до размеров 0,2…0,5 мм2, при этом внутри столба создаются температуры до 100000С. Поддерживая напряжение на дуге в пределах 28…35 В, и перемещая электрод по необходимой траектории, производят разделение металла заготовки.
Стационарные и переносные станки для газоплазменной резки
Переносные установки газоплазменной резки состоят из:
1. Плазмотрона, где формируются необходимые параметры поджигающего разряда: ток, скважность, напряжение.
2. Компрессора, создающего необходимое для образования плазмы давление воздуха.
3. Баллона с инертным газом.
4. Шлангов для подачи сжатого воздуха и аргона, а также присоединительных электрических кабелей.
5. Собственно рабочей головки, которую иногда называют плазмотроном.
6. Аппаратуры управления: регуляторов расхода аргона, манометров, контролирующих работу компрессора и т.д.
Непосредственно в плазмотрон входят:
- Корпус с рукояткой, при помощи которой плазмотрон перемещается по разрезаемой поверхности;
- Трубчатого наконечника, внутри которого подаётся охлаждающий его сжатый воздух;
- Ниппельного узла для подачи инертного газа;
- Сопла нужного сечения: с увеличением толщины разрезаемого металла диаметр сопла уменьшается, что связано с необходимостью увеличить кинетическую энергию газовоздушной струи;
- Изолятора (предусматривается для установок с принудительным электроподогревом наконечника, что повышает температуру смеси на выходе из сопла).
В условиях высоких температур и давлений происходит ионизация рабочей смеси, в результате чего температура в центре струи достигает 5000…60000С.
Плазмотрон подводят в разрезаемой заготовке и начинают перемещать его вдоль лини и разделения. Скорость перемещения зависит от толщины разрезаемого металла. Заготовку укладывают на раму или решётчатый настил: так удобнее контролировать качество резки по виду газовоздушной струи с противоположной стороны. Частицы расплава металла заготовки выдуваются из зоны реза тем же потоком воздуха, который служит для охлаждения наконечника плазмотрона.
Тот же принцип положен и в основу функционирования стационарных установок газоплазменной резки. Рабочая головка устанавливается на раму портального типа, которая оснащается автономным приводом её перемещения по всем координатам. Подлежащий разрезанию лист размещается на столе станка, и может перемещаться по специально предусматриваемым направляющим. Обычно такие станки оснащаются программируемым приводом, из-за чего производительность резки возрастает. Из одного листа металла можно изготавливать несколько плоских заготовок различной конфигурации, управляя в процессе резки как передвижением портальной рамы с рабочей головкой, так и движениями стола с заготовкой.
Существующие модели стационарных аппаратов газоплазменной резки позволяют разрезать стальные заготовки толщиной до 20…30 мм, а неметаллические материалы (например, камень) – до 200…250 мм. Возможности переносных исполнений скромнее: до 12…15 мм.
Стационарные и переносные станки для электродуговой резки
Сжатие горючей газовоздушной или газокислородной смеси недостаточно эффективно при разделении тугоплавких сталей и твёрдых сплавов. Для достижения необходимой температуры плазмы требуется рабочая среда с более высокой вязкостью. Кроме того, электрическая дуга гораздо лучше управляется путём соответствующего изменения значений тока и напряжения. Поэтому стационарные станки электродуговой резки используются при необходимости разделения толстолистовой стали и других токопроводящих материалов повышенной теплопроводности.
Станок рассматриваемого типа включает в себя:
1. Источник питания электрическим током (сварочный преобразователь, трансформатор или выпрямитель; последние используются чаще, поскольку обладают повышенным КПД).
2. Станцию рабочей жидкости, которая, в свою очередь, состоит из бака, насосной установки и системы гидрораспределительных автоматических золотников.
3. Инструментальную головку, в которую входят полый электрод и герметизированная камера, перекрывающая зону реза, и создающая внутри неё необходимое давление рабочей среды.
4. Блок автоматики и управления, который должен обеспечивать синхронное перемещение электрода и герметизированной камеры. Это перемещение начинается только после того, как в рабочей зоне установились необходимые электрические параметры разряда – ток и напряжения, а также скорость поперечного потока рабочей жидкости.
5. Шланги, электрические кабеля.
6. Раму с рабочим столом, на которой монтируется инструментальная головка. Рама оснащается автономным приводом движения, который предусматривает прямое её перемещение вниз, при разрезании металла, и холостое вверх – при удалении разрезанной заготовки со стола.
Станок для электродуговой резки плазмой работает так. Подлежащая разрезанию заготовка устанавливается на рабочий стол и позиционируется на нём по контрольным упорам. В посадочное место инструментальной головки помещают полый графитизированный электрод, конфигурация которого соответствует линии разрезания материала заготовки. Выбор материала электрода обуславливается требованием его минимального износа во время горения электрической дуги, хотя можно использовать также и медные электроды. Электрод соединяют с клеммными зажимами электрической сильноточной цепи и позиционируют относительно каналов отвода частиц разрезаемого металла.
Раму с инструментальной головкой опускают вниз до тех пор, пока уплотнительные кольца герметизированной камеры полностью не перекроют зону обработки, после чего включают привод подачи рабочей жидкости, и устанавливают в зоне реза необходимое её давление. Убедившись в стационарности потока и отсутствии гидравлических потерь, включают привод подачи инструментальной головки вниз, до контакта с заготовкой. При пробое межэлектродного промежутка автоматика корректирует значения тока обработки и напряжения на дуге в соответствии с необходимой плотностью тока, начинается процесс электродуговой плазменной резки. При этом электрическая дуга, как саморегулируемая система поддерживает текущие значения тока и напряжения в нужном диапазоне значений, при которых плазма будет стабильной, а качество резки – наилучшим.
Положительные особенности станков для плазменной резки
Современные конструкции рассмотренного оборудования позволяют:
1. Обеспечивать высокое качество реза, поскольку высококонцентрированной плазмой можно разделять металл с минимальными отходами и незначительной шероховатостью рабочих кромок.
2. Разрезаемый металл не деформируется, поскольку тепловое воздействие дуги или газовоздушной плазмообразующей смеси носит локальный характер.
3. Станки легко автоматизируются, а стационарное оборудование, оснащённое системами ЧПУ, может выполнять сложные резы по программе, без участия человека.
Устройство станка плазменной резки с ЧПУ
4. Станки высокоэкологичны, поскольку надёжная герметизация зоны обработки не позволяет избыточному теплу и газам выделяться наружу.
5. Расходный инструмент прост в изготовлении, и отличается высокой стойкостью.
6. Оборудование пожаробезопасно, поскольку инертный газ (в случае газовоздушной плазмы) или диэлектрическая рабочая среда (при электродуговой плазме) исключают воспламенение отдельных узлов.
7. Рабочие нагрузки, как на ручные, так и на стационарные аппараты незначительны, поэтому при плазменной резке нет необходимости прилагать физические усилия.
Также Вам может быть интересно видео, в котором рассказывается устройство плазмотрона:
zewerok.ru
теория, использование станков, выбор оборудования
Плазменная резка - способ обработки материалов (чаще всего - металла, но подойдут и неметаллические проводниковые материалы), при котором в качестве режущего инструмента выступает не резец, а дуга или струя плазмы.
Требования к резке металла, особенно на крупном производстве, затрагивают скорость работы без потери качества. Под эти критерии как раз подходит плазменная резка, которая обеспечивает высокую скорость работы при изначально низких эксплуатационных расходах. Под плазменной резкой подразумевается подача неионизированного газа в столб дуги, где этот газ становится нагретой плазменной струей. Сама дуга дополнительно сжимается скоростным потоком газа, из-за чего резка металла выполняется без проблем.
Принципы плазменной резки металла
Плазменная резка имеет два направления - поверхностная и разделительная. Наиболее популярной является разделительная резка. Что касается методов, то их тоже всего два:
- Резка дугой плазмы, при которой металл, подлежащий резке, попадает в электрическую цепочку. Дуга возникает между электродом и самим материалом, что выдвигает особенные требования к материалу, так как он должен проводить ток.
- Резка струей плазмы, при которой материал не участвует в электрической цепочке, так как дуга появляется между электродами, в резаке. С помощью резака косвенного воздействия можно разрезать практически любой металл, в том числе и диэлектрики.

Принцип работы плазменного резака заключаются в следующем. Сформированный в газовом канале сжатый воздух поступает в зону с зажженной электрической дугой, которая отвечает за преобразование газа в плазму. Материал разрезается путем его плавления, лишние частички металла сразу удаляются потоком воздуха, поэтому зачистка рабочей зоны происходит моментально. Материал греется только в локальных зонах.
Преимущества плазменной резки металла:
- Скорость работы. Предварительно нагревать материал не требуется, ширина разреза получается минимальной. Кроме того, так как зона термического влияния относительно небольшая, то слой краски или другое покрытие не будет разрушено.
- Универсальность заготовок. Если газовая резка не подходит для работы с алюминием или с нержавеющей сталью, то плазменная резка совместима с практически всеми типами металлов.
- Безопасность работы. В оборудовании для газовой резки, в отличие от оборудования для плазменной резки, существует вероятность обратного удара пламени или даже взрыва газовых баллонов при неправильном подключении устройства.
- Позволяет обрабатывать листы большего размера чем при лазерной резке. На выходе получаются детали с меньшим количеством дефектов.
- Слабое загрязнение воздуха.
Газы для плазменной резки
В установках для получения плазменной струи могут использоваться следующие газы:
- обычный воздух;
- технический кислород;
- азот;
- водород;
- аргон.
Газы имеют решающее значение для качества резки материалов. В зависимости от типа разрезаемого металла применяются различные газы или сочетания газов. Каждый газ имеет свои физические свойства. При выборе газа необходимо учитывать энергию ионизации и диссоциации, теплопроводность, атомную массу и химическую реакционную способность. Для резки нержавеющих сталей не рекомендуется использовать сжатый воздух, в зависимости от толщины материала может применяться азот в чистом виде, либо смешанный с аргоном.
Плазменная резка алюминия толщиной до 70 мм может осуществляться сжатым воздухом. Более качественный рез листа алюминия до 20 мм достигается при использовании чистого азота, а с 70 мм до 100 мм включительно с помощью азота с водородом. Резка алюминия плазмой при толщине от 100 мм осуществляется смесью аргона с водородом. Этот же состав рекомендовано использовать для меди и высоколегированной толстостенной стали.
Виды плазменной резки
В технологии плазменной резки металла выделяют:
- воздушно-плазменную резку металла;
- газоплазменную;
- лазерно-плазменную резку.
Первые два способа похожи по принципу действия: электродуга и ионизированный поток раскалённого газа. Основное отличие в рабочем теле, в первом случае — это воздух, во втором — газ или водяной пар. Переносные (ручные) аппараты режут металл с помощью воздушной ионизированной струи.
Лазерно-плазменный раскрой металла используется в промышленности и представляет собой комбинацию способов лазерной и плазменной резки на одном станке с ЧПУ, что повышает производительность оборудования.
Оборудование для плазменной резки металла
Станки бывают ручными, портальными и переносными.
Ручной станок представляет собой относительно небольшой короб, к которому подводится плазморежущая горелка. Специальный компрессор может спускать воздух, азот вместе с воздухом и другие газы. Такие аппараты могут работать, как с переменным, так и с постоянным током, но первое допускается, только если материалом заготовки является нетвердый сплав. Устройства компактные, их легко транспортировать на рабочее место, а для работы требуется только подключить устройство в розетку. Ручные станки хороши там, где подобные работы выполняются редко, а точность проведения операций не критична.
Портальные установки намного крупнее ручных, а их конструкция специально разработана для выкладки металлических листов. Процесс максимально автоматизирован, темп работы портального оборудования высокий, высока и точность резки. Портальные станки могут использоваться для резки заготовок, с толщиной не более 80 мм. С учетом того, что оборудование потребляет много энергии, важно грамотно просчитать объем выполняемых операций.

Наиболее функциональные - переносные аппараты, которые имеют секцию для укладки металлических листов. Листы укладываются автоматически, а управление станком происходит посредством ЖК-монитора с клавиатурой. Подобное оборудование обеспечивает еще большую точность работы по металлу, полную автоматизацию всех процессов и экономию энергии. Оправдает себя только в цеховом помещении или на объектах строительства.
Отдельно нужно выделить следующие два важных элемента, которые встречаются во всех перечисленных станках: сопло и компрессор.
В первую очередь сказать нужно о сопле. Основные характеристики сопла - сечение и длина. Первый параметр влияет на точность резки, второй параметр определяет скорость работы, поэтому тут нужно искать золотую середину. У резаков косвенного действия отдельно подбираются электроды, которые могут изготовляться из разных материалов. Считается, что лучшим материалом является гафний.

Теперь поговорим о втором важно элементе – компрессоре. От качества работы компрессора зависит многое, например, скорость реза заготовки. Воздух, подаваемый в рабочую зону, должен быть не только нагретым до определенной температуры, но и чистым. Соответственно, никаких примесей там быть не должно. Для домашнего пользования подойдут резаки, в которых компрессор встроенный, с функцией очистки и осушки воздуха.
Рекомендации по работе резака
Подготовка оборудования подразумевает подачу в аппарат сжатого воздуха, что может быть выполнено за счет небольшого компрессора, системы сжатого воздуха или баллона. Практически все аппараты способы регулировать поток воздуха. Чтобы выбрать оптимальную температуру, стоит сначала попробовать разрезать на самом большом напряжении, после чего постепенно уменьшать ее. Нужно добиться максимально чистого разреза, так как при слишком большом напряжении или при маленькой скорости резки на заготовке может появиться окалина.
Горелку нужно располагать как можно ближе к краю заготовки. Как только режущая дуга будет зажжена, то нужно начинать движение, причем, сама дуга должна быть направлена под прямым углом к листу. Признаком качественного разреза являются искры с обратной стороны металла – это будет означать, что материал прорезан насквозь. Если требуется выполнить строжку плазменной дугой, то это будет возможно, только если средний угол наклона горелки будет составлять 40 градусов. Длина горящей плазменной дуги в начале строжки должна быть минимальной, но ее можно увеличить в процессе работы.
Для выполнения отверстия также потребуется перевести начальное положение аппарата таким образом, чтобы угол наклона составлял 40 градусов. После запуска режущей дуги останется повернуть горелку так, чтобы угол составил 90 градусов. Дуга без проблем расплавит металл, но только при условии, что толщина заготовки не превышает предельно допустимой толщины, которая прописывается в аппарате устройства.
Как выбрать аппарат плазменной резки металла
При выборе аппарата плазменной резки металла обратите внимание на следующие показатели: выходная и входная мощности, размер наконечника и скорость работы.
Выходная мощность оборудования подбирается в соответствии с тем, какой толщины будет заготовка и из какого материала она будет изготовлена. Выбор размера наконечника тоже зависит от материала. Например, устройство, которое работает на мощности 27 А при 90 разрежет заготовку с толщиной около 12 мм. Для более толстых заготовок потребуется использовать уже более мощные устройства.
На скорость резки станка нужно обращать внимание только тогда, когда предстоит массовое производство. Некоторые устройства могут обрабатывать заготовку с одними и теми же параметрами с разницей в 4 минуты. Показатель скорости измеряется сантиметрами в минуту.
Чтобы определить входную мощностью, которой будет достаточно для работы устройства, потребуется проверить первичное напряжения и допустимую для аппарата силу тока. Существуют универсальные аппараты, которые способны работать при любом напряжении и при любой силе тока, но и цена их будет выше.
Особенность таких устройств в том, что они через некоторое время начинают перегреваться, из-за чего в работе нужно делать перерыв. Например, при показателе в 70%, только три из десяти минут устройство должно будет находиться в режиме простоя.
У аппарата плазменной резки могут быть дополнительные элементы, позволяющие держать его на расстоянии от заготовки. Плазменные горелки могут изготовляться из разных материалов, рекомендуется остановиться на горелках с эпоксидным соплом, которые прочнее керамических. Также обращать внимание нужно на режим температур – предпочтительным считается порог в 40 градусов и выше.
К оглавлению
ajan.ru
виды и принцип действия, устройство плазмотрона, видео технологии резки плазмой
Еще совсем в недалеком прошлом для того, чтобы разрезать металл, приходилось прибегать к совершенно неудобным громоздким аппаратам, работающим на газе. При этом такие резаки не всегда могли справиться с поставленной задачей. На сегодняшний день как на небольших предприятиях, так и на промышленных объектах широко используется плазменная резка, с помощью которой можно максимально точно обработать металл любой конфигурации и толщины.
Принцип действия плазменной резки
Плазменная резка – это разделительная обработка металла с помощью термического процесса. Роль режущего инструмента здесь играет струя низкотемпературной плазмы.
Принцип действия плазменного аппарата:
- Между разрезаемым металлом и электродом или соплом плазмотрона создается электрическая дуга с температурой в 5000С.
- В сопло под давлением поступает газ, за счет чего температура электрической дуги повышается до 20 000С.
- Газ ионизируется и преобразуется в высокотемпературный газ или низкотемпературную плазму.
- От нагретой дуги возрастает ионизация, и температура газовой струи повышается до 30 000С. Во время этого процесса поток плазмы обладает высокой теплопроводностью и ярко светится.
- Плазма со скоростью в 500–1500 м/с проистекает из сопла, попадает на подготовленный металл, разогревает его и плавит в месте разреза.
Более наглядно процесс резки металла с помощью плазмотрона можно посмотреть по видео.
Виды плазменной резки
Плазменная резка металла бывает нескольких видов:
-
Простая. При таком способе используется электрический ток и воздух. Длина электрической дуги во время такого процесса ограничена, поэтому при толщине листа в несколько миллиметров обработка поверхностей сравнивается с резкой лазером. Простой способом применяется для обработки только мягкой или низколегированной стали. При разрезе материала заусенцы не образовываются, кромка остается ровной. Иногда вместо воздуха может применяться азот.
-
С применением воды. Во время резки вода используется для охлаждения плазмотрона и защиты среза от негативного влияния окружающей среды. Кроме этого, водой поглощаются все вредные испарения.
-
С использованием защитного плазмообразующего газа. Срез во время такой резки защищен от окружающей среды, поэтому качество разрезания металла увеличивается.
Также резать металл можно с помощью дуги или струи. В первом случае обрабатываемый материал является частью цепи, во втором – дуга образовывается между электродами.
Устройство для плазменной резки металлов
Главным элементом оборудования является плазменный резак, который называется плазмотроном. Его основные составляющие:
-
Электрод, который расположен в тыльной части камеры. Он образовывает электрическую дугу.
-
Сопло отвечает за форму потока плазмы и ее скорость.
-
Термостойкий изолятор расположен между соплом и электродом.
Кроме плазматрона, устройство для резки металла оборудовано:
- компрессором или газовым баллоном;
- источником питания;
- набором шлангов или кабелей, предназначающихся для соединения плазматрона с компрессором и источником питания.
Так как с помощью аппарата работать приходится на весу, рез может получиться неровным. Поэтому для улучшения качества резки рекомендуется использовать подставки или специальные упоры, которые надеваются на сопло.
На видео можно посмотреть, как режется материал с помощью плазмотрона.
Преимущества и недостатки плазменной резки
По сравнению с лазерной резкой, работы по резке металлов с помощью плазмы имеют много достоинств:
- Материал можно точно и быстро разрезать независимо от того, какой он толщины.
- С помощью плазмы разрезается любой металл: тугоплавкий, черный, цветной.
- Аппаратом для плазменной резки можно обрабатывать не только металл, но и другие материалы.
- Плазмотроном легко режутся материалы различной ширины и под углом.
- Во время работ в воздух практически не выбрасываются загрязняющие вещества.
- Изделия получаются практически без загрязнений и с наименьшим количеством дефектов.
- Плазмотроном можно выполнять художественные работы. С его помощью доступна художественная резка деталей, сложная фигурная резка.
- Так как металл перед работой прогревать не нужно, сокращается время прожига.
Все достоинства плазменной резки можно увидеть на видео ниже.
Как и любой аппарат, наряду с преимуществами, плазмотрон имеет свои недостатки:
- необходимость соблюдения правила обслуживания;
- большой шум, создаваемый аппаратом во время его работы;
- толщина разрезаемого металла не должна быть более 10 сантиметров;
- высокая стоимость плазмотрона.
Технология плазменной резки
Перед первым использованием плазмотрона рекомендуется посмотреть видео и изучить, как проходит весь процесс.
- Горелка плазмы размещается близко к краю заготовки.
- Включается кнопка «Пуск». После этого сначала зажжется дежурная дуга, а затем режущая.
- Горелку по обрабатываемому материалу следует вести медленно, с наклоном в 90 градусов.
- С помощью контроля за появлением брызг регулируется скорость разрезания. Если с другой стороны металла брызг нет, то материал полностью разрезать не удалось. Причинами могут быть: неправильный угол наклона горелки, низкий ток, высокая скорость аппарата.
- После завершения процесса горелку необходимо наклонить, так как еще какое-то время будет идти воздух.
Если во время работы по какой-то причине погаснет плазменная дуга, то подачу газа нужно прекратить, затем аппарат заново включить и начать обработку.
Несколько полезных советов
Перед началом работ на аппарате для плазменной резки металла следует тщательно изучить схему подключения и проверить исправность шлангов и кабелей.
Качество резки напрямую зависит от типа и конфигурации сопла. Его диаметр влияет на формирование дуги и скорость ее образования, а также на ширину реза и объем пропускаемого газа или воздуха. Поэтому после применения сопла с правильно подобранным диаметром, можно получить качественный и чистый срез с ровными краями.
Для улучшения режущих характеристик длину сопла можно увеличить, а также его в любой момент можно поменять.
Чтобы в результате работы материал не деформировался, не было заусениц и окалин, необходимо правильно рассчитать ток. Для этого сначала подается высокий ток и делается пара надрезов. По полученному результату будет видно — оставить ток высоким или нужно его снизить.
Конечно, цена на оборудование для плазменной резки достаточно высокая. Однако приобретенный аппарат довольно быстро окупится, поэтому при покупке его стоимость не должна быть определяющим фактором.
Оцените статью: Поделитесь с друзьями!stanok.guru