Аппарат для резки металла. Аппарат для плазменной резки металла. Аппарат плазменной резки
Устройство аппарата плазменной резки | Строительный портал
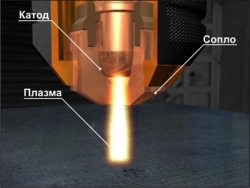
Технология плазменной резки крайне редко применяется в быту, зато в промышленной сфере получила очень широкое распространение. Благодаря тому, что с помощью плазмореза можно легко, быстро и качественно разрезать практически любой токопроводящий металл, а также другие материалы – камень и пластик, его используют в машиностроении, судостроении, коммунальной сфере, изготовлении рекламы, для ремонта техники и многого другого. Срез всегда получается ровным, аккуратным и красивым. Тех, кто только собрался освоить данную технологию, может интересовать резонный вопрос, что собой представляет аппарат плазменной резки, каков принцип его работы, а также какие разновидности плазморезов бывают и для чего используется каждый из них. Все это даст общее понимание технологии плазменной резки, позволит сделать правильный выбор при покупке и освоить работу с аппаратом.
- Принцип работы аппарата плазменной резки металла
- Устройство аппарата плазменной резки
- Разновидности аппаратов плазменной резки
Принцип работы аппарата плазменной резки металла
Как работает плазморез? И что подразумевается под словом «плазма»? Для работы плазмореза необходимо только две вещи – электричество и воздух. Источник энергии подает на резак (плазмотрон) токи высокой частоты, благодаря чему в плазмотроне возникает электрическая дуга, температура которой 6000 – 8000 °С. Затем в плазмотрон направляется сжатый воздух, который на большой скорости вырывается из патрубка, проходит через электрическую дугу, нагревается до температуры 20000 – 30000 °С и ионизируется. Воздух же, который ионизировался, теряет свойства диэлектрика и становится проводником электричества. Плазмой как раз и является этот воздух.
Вырываясь из сопла, плазма локально разогревает заготовку, в которой необходимо выполнить рез, металл плавится. Образованные на лобовой поверхности реза частички расплавленного металла сдуваются потоком воздуха, вырывающимся на огромной скорости. Так происходит резка металла.
Скорость плазменного потока (разогретого ионизированного воздуха) возрастает, если увеличить расход воздуха. Если же увеличить диаметр сопла, через которое плазма вырывается, то скорость уменьшится. Параметры скорости плазмы примерно таковы: на токе 250 А она может быть 800 м/с.
Чтобы рез получился ровным, плазмотрон необходимо держать перпендикулярно плоскости реза, максимальное допустимое отклонение 10 – 50 °. Также большое значение имеет скорость реза. Чем она меньше, тем ширина реза становится больше, а поверхности реза становятся параллельными. То же самое происходит при увеличении силы тока.
Если увеличить расход воздуха, то ширина реза уменьшится, зато кромки реза станут непараллельными.
Устройство аппарата плазменной резки
Аппарат плазменной резки состоит из источника питания, плазмотрона и кабель-шлангового пакета, с помощью которого соединяются источник питания и компрессор с плазмотроном.
Источником питания для аппарата плазменной резки может служить трансформатор или инвертор, которые подают на плазмотрон большую силу тока.
Плазмотрон, собственно, и является главным элементом аппарата – плазменным резаком. Иногда по ошибке весь аппарат называют плазмотроном. Возможно, это связано с тем, что источник питания для плазмореза не отличается никакой уникальностью, а может быть использован вместе со сварочным аппаратом. А единственным элементом, отличающим плазморез от другого аппарата, и является плазмотрон.
Основные составляющие плазмотрона – электрод, сопло и изолятор между ними.
Внутри корпуса плазмотрона находится цилиндрическая камера малого диаметра, выходной канал из которой довольно мал и позволяет формировать сжатую дугу. В тыльной стороне дуговой камеры располагается электрод, служащий для возбуждения электрической дуги.
Электроды для воздушно-плазменной резки могут быть изготовлены из бериллия, гафния, тория или циркония. На поверхности этих металлов образуются тугоплавкие оксиды, предотвращающие разрушение электрода. Но для образования этих оксидов нужны определенные условия. Самыми распространенными являются электроды из гафния. А вот из бериллия и тория их не делают, и виной тому те самые оксиды: оксид бериллия – крайне радиоактивен, а оксид тория – токсичен. Все это может крайне негативно сказаться на работе оператора.
Так как возбуждение электрической дуги между электродом и заготовкой обрабатываемого металла напрямую затруднительно, сначала зажигается так называемая дежурная дуга – между электродом и наконечником плазмотрона. Столб этой дуги заполняет весь канал. После этого в камеру начинает подаваться сжатый воздух, который, проходя сквозь электрическую дугу, нагревается, ионизируется и увеличивается в объеме в 50 – 100 раз. Сопло плазмотрона сужено книзу и формирует из разогретого ионизированного газа/воздуха поток плазмы, вырывающийся из сопла со скоростью 2 – 3 км/с. При этом температура плазмы может достигать 25 – 30 тыс. °С. В таких условиях электропроводимость плазмы становится примерно такой же, как и у обрабатываемого металла.
Когда плазма выдувается из сопла и касается факелом обрабатываемого изделия, образуется режущая плазменная дуга – рабочая, а дежурная дуга гаснет. Если вдруг по какой-то причине рабочая дуга тоже погасла, необходимо прекратить подачу воздуха, снова включить плазмотрон и сформировать дежурную дугу, а затем пустить сжатый воздух.
Сопло плазмотрона может иметь различные размеры и от этого зависят возможности всего плазмотрона и технология работы с ним. Например, от диаметра сопла плазмотрона зависит количество воздуха, которое может проходить сквозь этот диаметр за единицу времени. От количества расхода воздуха зависит ширина реза, скорость работы и скорость охлаждения плазмотрона. В плазморезах используют сопла не больше 3 мм диаметром, зато довольно длинные – 9 – 12 мм. Длина сопла влияет на качество реза, чем длиннее сопло, тем качественнее рез. Но здесь нужно быть осторожным, везде важна мера, так как слишком большое сопло будет быстрее изнашиваться и разрушаться. Оптимальной считается длина, в 1,5 – 1,8 раз больше диаметра сопла.
Крайне важно, чтобы катодное пятно фокусировалось строго по центру катода (электрода). Для этого используют вихревую подачу сжатого воздуха/газа. Если вихревая (тангенциальная) подача воздуха нарушена, то катодное пятно будет смещаться относительно центра катода вместе с дугой. Все это может привести к нестабильному горению плазменной дуги, образованию двойной дуги и даже выходу плазмотрона из строя.
В процессе плазменной резки используются плазмообразующие и защитные газы. В аппаратах плазменной резки с силой тока до 200 А (можно разрезать металл толщиной до 50 мм) используют только воздух. В таком случае воздух является плазмообразующим газом и защитным, а также охлаждающим. В сложных промышленных портальных аппаратах используют другие газы – азот, аргон, водород, гелий, кислород и их смеси.
Сопло и электрод в аппарате плазменной резки являются расходными материалами, которые необходимо своевременно заменять, не дожидаясь их полного износа.
В основном плазморезы принято покупать в готовом виде, главное – правильно подобрать нужный агрегат, тогда не придется ничего «доделывать напильником». Хотя в нашем отечестве есть «Кулибины», которые могут сделать аппарат плазменной резки своими руками, закупив некоторые детали отдельно.
Разновидности аппаратов плазменной резки
Плазморезы различают по нескольким различным параметрам. Аппараты плазменной резки могут представлять собой переносные установки, портальные системы, шарнирно-консольные машины, специализированные конструкции и установки с координатным приводом. Особенно выделяются машины плазменной резки с ЧПУ (числовым программным управлением), которые минимизируют вмешательство человека в процесс резки. Но помимо этих существуют и другие градации.
Аппараты для ручной и машинной резки
Ручной аппарат плазменной резки используется для резки металла вручную, когда плазмотрон держит в руках оператор-человек и ведет его по линии реза. В связи с тем, что плазмотрон все время находится на весу над обрабатываемой заготовкой, рука человека может слегка дрогнуть даже в процессе обычного дыхания, все это отражается на качестве реза. На нем могут быть наплывы, неровный рез, следы рывков и т.д. Чтобы облегчить работу оператору, существуют специальные упоры, которые надеваются на сопло плазмотрона. С помощью него можно поставить плазмотрон непосредственно на заготовку и аккуратно вести его. Зазор между соплом и обрабатываемой заготовкой всегда будет одинаковым и соответствующим требованиям.
Аппараты машинной резки представляют собой плазморезы портального типа и аппараты автоматического раскроя деталей и труб. Такие аппараты используются на производстве. Качество реза таким плазморезом получается идеальным, дополнительная обработка кромок не требуется. А программное управление позволяет делать резы различной фигурной формы в соответствии с чертежом без страха дернуть рукой в неподходящий момент. Рез выполняется точно и гладко. На подобные аппараты плазменной резки металла цена на порядок выше, чем на ручные аппараты.
Трансформаторные и инверторные аппараты плазменной резки
Существуют трансформаторные и инверторные плазморезы.
Трансформаторные плазморезы тяжелее инверторных и больше по размеру, зато они более надежны, так как не выходят из строя в случае скачков напряжения. Продолжительность включения таких аппаратов выше, чем у инверторных, и может достигать 100 %. Такой параметр, как продолжительность включения, напрямую влияет на специфику работы с аппаратом. Например, если ПВ равна 40 %, это означает, что 4 минуты резак может работать без перерыва, а затем ему необходимо 6 минут отдыха, чтобы остыть. ПВ 100 % используется в производстве, там, где работа аппарат продолжается весь рабочий день. Недостатком трансформаторного плазмореза является высокое энергопотребление.
С помощью трансформаторных плазменных резаков можно обрабатывать заготовки большей толщины. На подобный аппарат воздушно-плазменной резки цена выше, чем на инверторный. Да и представляет он собой короб на колесиках.
Инверторные аппараты плазменной резки используются чаще в быту и на маленьких производствах. Они намного экономнее в энергопотреблении, обладают меньшим весом и габаритами и чаще всего представляют собой ручной аппарат. Достоинством инверторного плазмореза является стабильное горение дуги и КПД на 30 % выше, компактность и возможность вести работы в труднодоступных местах.
Аппарат воздушно-плазменной резки и водно-плазменной резки
Стоит отметить, что существуют не только аппараты воздушно-плазменной резки, принцип действия которых и устройство были описаны выше, но и аппараты водно-плазменной резки.
Если в воздушно-плазменных резаках воздух выступает и как плазмообразующий, и как защитный, и как охлаждающий газ, то в водно-плазменных резаках вода выступает в качестве охладителя, а водяной пар плазмообразователя.
Достоинствами воздушно-плазменной резки являются низкая цена и небольшой вес, зато недостаток – ограничена толщина разрезаемой заготовки, зачастую не более 80 мм.
Мощность водно-плазменных резаков позволяет разрезать толстые заготовки, зато их цена несколько выше.
Принцип работы аппарата водно-плазменной резки заключается в том, что вместо сжатого воздуха в нем используется водяной пар. Это дает возможность отказаться от использования компрессора для воздуха или газовых баллонов. Водяной пар более вязкий по сравнению с воздухом, поэтому его необходимо намного меньше, запаса в баллончике хватает примерно на месяц-два. Когда в плазмотроне протекает электрическая дуга, в него подается вода, которая испаряется. Одновременно с этим рабочая жидкость поднимает катод отрицательного полюса от катода положительного полюса сопла. В результате загорается электрическая дуга, пар ионизируется. Еще до того, как плазмотрон приблизится к обрабатываемой заготовке, загорается плазменная дуга, которая выполняет резку. Ярким представителем данной категории плазморезов является аппарат Горыныч, на такой аппарат плазменной резки цена около 800 у.е.
Контактные и бесконтактные аппараты плазменной резки
В зависимости от того, включен разрезаемый материал в электрическую схему плазменной резки или нет, зависит тип резки – контактный и бесконтактный.
Контактная плазменная резка или резка плазменной дугой выглядит так: дуга горит между электродом плазмотрона и обрабатываемой деталью. Это еще называется дугой прямого действия. Столб электрической дуги совмещен с плазменной струей, которая вырывается из сопла на большой скорости. Продуваемый через сопло плазмотрона воздух обжимает дугу и придает ей проникающие свойства. За счет высокой температуры воздуха 30000 °С, повышается скорость его истечения и плазма оказывает сильной механическое воздействие на выдуваемый металл.
Контактный тип резки применяется при работах с металлами, которые могут проводить электричество. Это изготовление деталей с прямолинейными и криволинейными контурами, резка труб, полос и прутков, выполнение отверстий в заготовках и многое другое.
Бесконтактная плазменная резка или резка плазменной струей выглядит так: электрическая дуга горит между электродом и формирующим наконечником плазмотрона, часть плазменного столба выносится за пределы плазмотрона через сопло и представляет собой высокоскоростную плазменную струю. Именно данная струя и является режущим элементом.
Бесконтактная резка используется при работе с нетокопроводящими материалами (неметаллами), например, камнем.
Работа с аппаратом плазменной резки и технология воздушно-плазменной резки – это целое искусство, требующее знаний, терпения и соблюдения всех правил и рекомендаций. Знание и понимание устройства плазмореза помогает выполнять работу качественно и аккуратно, так как оператор понимает, какие процессы происходят в плазмотроне и за его пределами в тот или иной момент, и может ими управлять. Также немаловажно соблюдать все меры предосторожности и технику безопасности, например, работать с плазморезом необходимо в костюме сварщика, в щитке, перчатках, в закрытой обуви и плотных штанах из натуральной ткани. Некоторые окислы, выделяемые в процессе резки металла, могут нанести непоправимый вред легким человека, поэтому необходимо работать в защитной маске или хотя бы обеспечить хорошую вентиляцию в рабочей зоне.
strport.ru
Аппараты для воздушно-плазменной резки металла: обзор моделей
Для резки металла на предприятиях, а также в различных мастерских всё реже используется классический способ с применением ацетиленового резака.
Аппарат воздушно-плазменной резки способен полностью заменить устаревший вариант оборудования по обработке металла. Такое устройство имеет не только более компактные размеры, но и более высокую температуру пламени, что позволяет выполнять резку тугоплавких металлов.
О том, как выбрать такое устройство для организации либо для личного использования, будет подробно изложено в данной статье.
Принцип работы аппарата плазменной резки
В аппарате плазменной резки используется ионизированный газ, который может быть разогрет до температуры 30 000 градусов. Благодаря высокой температуре плазмы, удаётся довольно легко разрезать металлы толщиной до 50 мм. В качестве газа, который может быть ионизирован применяются:
- Воздух.
- Азот.
- Водяной пар.
- Аргон.
- Углекислый газ.
Применение воздуха является «бесплатным» способом обеспечить плазмотрон необходимым газом, но для этого варианта резки потребуется приобрести компрессор.
Принцип работы аппарата плазменной резки металлов, следующий:
- В плазматрон подаётся ток высокой частоты, который образует первичную электронную дугу с температурой около 6 000 градусов.
- В горелку подаётся сжатый газ, который на большой скорости проходит через электрическую дугу.
- Газ ионизируется и достигает температуры 20 000 — 30 000 градусов.
Именно этой струёй ионизированного газа и производится разрезание металла.
Видео:
Виды приборов для плазменной резки
Аппарат для воздушно-плазменной резки металла, может иметь различные габариты и предназначение. Для выполнения точной резки металлов используются станки с программным управлением.
Цена такой установки может составлять сотни тысяч рублей, поэтому приобретение для частного пользования нецелесообразно.
Агрегат бытового назначения можно приобрести по доступной цене, но толщина обрабатываемой заготовки для таких устройств, обычно не превышает 12 мм. Основное преимущество бытовых моделей заключается в их мобильности. Бытовые аппараты плазменной резки могут использоваться ремонтными бригадами для проведения работ непосредственно на месте аварии.
Кроме габаритов и мощности, аппараты плазменной резки могут разделяться по типу трансформации электрической энергии. Инверторные модели обычно используются в быту, по причине сравнительно невысокой мощности таких устройств. Несомненное достоинство этого типа плазморезов заключается в более высоком КПД, который в современных устройствах может достигать значения на 30% больше, чем у трансформаторных моделей.
Трансформаторные плазморезы имеют значительно больший вес и мощность электрической дуги, но из-за высокого энергопотребления применяются, в основном только на производстве. Среди основных положительных качеств трансформаторной модели можно назвать высокую надёжность. Такие устройства хорошо переносят скачки напряжения, в то время как инверторные могут полностью выйти из строя при нестабильном электроснабжении.
Наиболее популярные модели
Среди аппаратов плазменной резки можно выделить несколько моделей, которые хорошо зарекомендовали себя при эксплуатации.
1. Мультиплаз-15000 — работает исключительно от трёхфазной электрической сети.
Агрегат не только предназначен для резки, но и для пайки любых токопроводящих металлов. Мультиплаз-15000 позволяет выполнять высококачественный срез металла благодаря узконаправленной плазменной струе. Благодаря оригинальной конструкции с применением водяного пара в качестве плазмообразующего вещества, работа с аппаратом плазменной резки становится не только высокопроизводительной, но и абсолютно безопасной для экологии.
При использовании этого устройства можно легко обрабатывать металлы толщиной до 50 мм. Стоимость машины — 170 000 руб.
Видео:
2. Кедр CUT 160I — высокопроизводительный прибор (стоимостью 157 000 руб). Работает от трёхфазной сети напряжения 380 В.
Для работы устройства необходим компрессор, который будет подавать сжатый воздух в горелку. Аппарат может быть подключён к порталу с программным управлениям для более точного выполнения работ и повышения скорости резки металла. При высокой скорости реза, Кедр cut 160i позволяет выполнить идеально ровный срез, который не потребуется дополнительно обрабатывать для дальнейшей сварки металлических деталей.
В данном устройстве реализована бесконтактная система запала начальной дуги, что также позволяет упростить и ускорить рабочий процесс. Рекомендуемая производителем толщина обрабатываемого металла составляет 40 мм.
3. РСА-120 IGBT — идеально подходит для резки не только стали, но и цветных металлов. Использование инновационного способа коммутации электрического тока, позволяет повысить КПД устройства, а также значительно снизить вероятность выхода из строя при перепадах сетевого напряжения.
РСА-120 IGBT является профессиональным устройством, которое позволяет работать при значительной нагрузке в течение длительного времени. В конструкции аппарата имеется встроенная защита от перегрева, а также от обрыва фазы и недостаточного давления подаваемого в горелку воздуха. РСА-120 может быть подключён только к трёхфазной сети напряжением 380 вольт. Средняя цена плазменного резака 140 000 руб.
4. СВАРОГ REAL CUT 45 — бытовой плазморез, который можно подключить к обычной электросети напряжением 220 В. Аппарат способен разрезать любой токопроводящий металл толщиной не более 12 мм. Несмотря на небольшую стоимость (19 000 руб) и низкую мощность, отзывы о данном устройстве исключительно положительные.
СВАРОГ REAL CUT 45 относится к классу инверторных устройств, поэтому при работе будет обеспечена максимальная производительность. Мощность тока, которая потребляется устройством составляет всего 6,2 кВт, поэтому каких-либо нарушений в домашней сети при использовании прибора не будет.
Данная модель оснащена плавным регулятором силы тока, что позволяет идеально настроить аппарат для резки различных по толщине металлов.
5. Ресанта ИПР-40К — плазморез бытового назначения отечественного производства, отличается высоким качеством и надёжностью. Цена 20 000 руб.
Аппарат имеет небольшую массу, поэтому идеально подходит для домашнего использования. Для работы плазмореза достаточно подключить устройство к обычной розетке на 220 В, после чего можно будет разрезать любой металл толщиной до 12 мм.
6. MASTER CUT-40 — компактный, лёгкий и удобный в использовании аппарат плазменной резки металлов.
Прибор подключается к домашней электрической сети напряжением 220 В. MASTER CUT-40 отлично подходит для бытового использования как начинающим, так и опытным мастерам.
Вес устройства составляет всего 8 кг, поэтому MASTER CUT-40 может быть применён с максимальной эффективностью в небольших строительных бригадах. Стоимость инвертора — 23 000 руб.
Перечисленные модели устройств существенно отличаются друг от друга только мощностью, остальные характеристики находятся на достаточно высоком уровне, поэтому осуществлять выбор устройства следует прежде всего с учётом возможности подключения к соответствующей электрической сети, а также толщины обрабатываемого металла.
Советы и рекомендации
1. При выборе устройства для плазменной резки следует отдавать предпочтение аппаратам, которые имеют евроразьём для подключения плазмотрона. Наличие такого разъёма гарантирует лёгкое подключение различной длины кабель-шлангового пакета, а также при необходимости удлинения — беспроблемное соединение таких элементов между собой.
2. Для выполнения качественного реза, а также для продления эксплуатационного срока прибора, рекомендуется использовать только качественные расходные материалы. Наиболее часто при выполнении таких работ изнашивается сопло и катод, поэтому следует особенно тщательно следить за состоянием этих деталей.
3. При работе с аппаратом плазменной резки следует неукоснительно соблюдать правила безопасности. Вместе с плазморезом обязательно следует приобрести защитный щиток, очки и специальную одежду. Для защиты от брызг раскалённого металла, необходимо также использовать перчатки и специальную обувь.
4. Если при использовании бытового прибора работать приходится на максимально возможной мощности, то необходимо делать перерывы в работе. Продолжительность безостановочной эксплуатации обязательно указывается в инструкции к оборудованию.
Видео:
P.S. Для покупки «правильного» плазмореза необходимо вначале определиться с мощностью этого устройства. Бытовые устройства не способны выполнить рез толстого металла, но если такой необходимости нет, то инверторные аппараты позволят максимально экономно производить плазморезные работы.
Если прибор приобретается исключительно для домашнего использования, то следует вначале ознакомиться о возможности подключения мощного устройства. Старая аварийная проводка, может стать камнем преткновения на пути подключения аппарата плазменной резки металлов к домашней электрической сети.

plavitmetall.ru
Воздушно-плазменная резка своими руками | Строительный портал
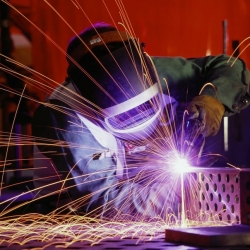
Все чаще в небольших частных мастерских и на маленьких предприятиях используют аппараты плазменной резки металла вместо болгарок и других аппаратов. Воздушно-плазменная резка позволяет выполнять качественные прямые и фигурные резы, выравнивать кромки листового металла, делать проемы и отверстия, в том числе и фигурные, в металлических заготовках и другие более сложные работы. Качество получившегося реза просто великолепно, он получается ровным, чистым, практически без окалины и заусениц, а также аккуратным. С помощью технологии воздушно-плазменной резки можно обрабатывать практически все металлы, а также нетокопроводящие материалы, такие как бетон, керамическая плитка, пластик и дерево. Все работы выполняются быстро, заготовка нагревается локально, только в области реза, поэтому металл заготовки не меняет своей геометрии вследствие перегрева. С аппаратом плазменной резки или как его еще называют – плазморезом сможет справиться даже новичок без опыта сварки. Но чтобы результат не разочаровал, все же не помешает изучить устройство плазмореза, понять его принцип действия, а также изучить технологию, как работать аппаратом воздушно-плазменной резки.
- Устройство аппарата воздушно-плазменной резки
- Принцип работы аппарата воздушно-плазменной резки
- Как выбрать аппарат воздушно-плазменной резки
- Воздушно-плазменная резка своими руками – технология работы
Устройство аппарата воздушно-плазменной резки
Знание устройства плазмореза позволит не только более осознанно производить работы, но и создать самодельный аналог, для чего необходимы не только более глубокие знания, но и желательно инженерский опыт.
Аппарат воздушно-плазменной резки состоит из нескольких элементов, среди которых:
- Источник питания;
- Плазмотрон;
- Кабель-шланговый пакет;
- Воздушный компрессор.
Источник питания для плазмореза служит для того, чтобы преобразовывать напряжение и подавать на резак/плазмотрон определенную силу тока, благодаря чему загорается электрическая дуга. В качестве источника питания могут выступать трансформатор или инвертор.
Плазмотрон – основной элемент аппарата воздушно-плазменной резки, именно в нем происходят процессы, благодаря которым появляется плазма. Плазмотрон состоит из сопла, электрода, корпуса, изолятора между соплом и электродом и каналов для воздуха. Такие элементы как электрод и сопло являются расходными материалами и требуют частой замены.
Электрод в плазмотроне является катодом и служит для возбуждения электрический дуги. Самым распространенным металлом, из которого делают электроды для плазмотронов, является гафний.
Сопло имеет конусообразную форму, обжимает плазму и формирует плазменную струю. Вырываясь из выходного канала сопла, плазменная струя дотрагивается до заготовки и разрезает ее. Размеры сопла влияют на характеристики плазмореза, его возможности и технологию работы с ним. Самый распространенный диаметр сопла – 3 – 5 мм. Чем больше диаметр сопла, тем больший объем воздуха в единицу времени оно можно пропустить через себя. От количества воздуха зависит ширина реза, а также скорость работы плазморезом и скорость охлаждения плазмотрона. Самая распространенная длина сопла 9 – 12 мм. Чем больше длина сопла, тем аккуратнее рез. Но слишком длинное сопло больше подвержено разрушению, поэтому оптимально длину увеличивают на размер, равный 1,3 – 1,5 диаметра сопла. Следует учитывать, что каждому значению силы тока соответствует оптимальный размер сопла, который обеспечивает стабильное горение дуги и максимальные параметры резки. Уменьшать диаметр сопла и делать менее 3 мм нецелесообразно, так как значительно снижается ресурс всего плазмотрона.
Компрессор подает сжатый воздух в плазмотрон для образования плазмы. В аппаратах воздушно-плазменной резки воздух выступает в качестве и плазмообразующего газа, и защитного. Существуют аппараты со встроенным компрессором, как правило, они маломощные, а также аппараты с внешним воздушным компрессором.
Кабель-шланговый пакет состоит из электрокабеля, соединяющего источник питания и плазмотрон, а также шланга для подачи воздуха от компрессора в плазмотрон. Что конкретно происходит внутри плазмотрона, рассмотрим ниже.
Принцип работы аппарата воздушно-плазменной резки
Установка воздушно плазменной резки работает по описанному ниже принципу. После нажатия кнопки розжига, которая находится на ручке плазмотрона, от источника питания на плазмотрон начинает подаваться ток высокой частоты. В результате загорается дежурная электрическая дуга. По причине того, что образование электрической дуги между электродом и заготовкой напрямую затруднительно, то в качестве анода выступает наконечник сопла. Температура дежурной дуги составляет 6000 – 8000 °С, а столб дуги заполняет весь канал сопла.
Спустя пару секунд после розжига дежурной дуги в камеру плазмотрона начинает подаваться сжатый воздух. Он проходит сквозь дежурную электрическую дугу, ионизируется, нагревается и увеличивается в объеме в 50 – 100 раз. Форма сопла плазмотрона заужена книзу, благодаря чему воздух обжимается, из него формируется поток, который вырывается из сопла со скоростью, близкой к звуковой – 2 – 3 м/с. Температура ионизированного разогретого воздуха, вырывающегося из выходного отверстия сопла, может достигать 20000 – 30000 °С. Электропроводность воздуха в этот момент примерно равна электропроводности обрабатываемого металла.
Плазмой как раз и называется разогретый ионизированный воздух, вырывающийся из сопла плазмотрона. Как только плазма достигает поверхности обрабатываемого металла, зажигается рабочая режущая дуга, в этот момент дежурная дуга гаснет. Режущая дуга разогревает заготовку в месте соприкосновения, локально, металл начинает плавиться, появляется рез. Расплавленный металл вытекает на поверхность заготовки и застывает в виде капель и мелких частичек, которые тут же сдуваются потоком плазмы. Данный способ воздушно-плазменной резки называют резкой плазменной дугой (дуга прямого действия), так как обрабатываемый металл входит в электрическую схему и является анодом режущей дуги.
В описанном выше случае для разрезания заготовки используется энергия одного из приэлектродных пятен дуги, а также плазмы столба и вытекающего из него факела. Для резки плазменной дугой используется дуга постоянного тока прямой полярности.
Плазменно-дуговая резка металла используется в таких случаях: если необходимо изготовить детали с фигурными контурами из листового металла, или изготовить детали с прямыми контурами, но так, чтобы не пришлось обрабатывать контуры дополнительно, для резки труб, полос и прутов, для вырезки отверстий и проемов в деталях и другого.
Но также есть еще один способ плазменной резки – резка плазменной струей. В таком случае режущая дуга загорается между электродом (катодом) и наконечником сопла (анодом), а обрабатываемая заготовка не включена в электрическую цепь. Часть плазмы выносится из плазмотрона в виде струи (дуга косвенного действия). Обычно такой способ резки используют для работы с неметаллическими нетокопроводящими материалами – бетоном, керамической плиткой, пластмассой.
Подача воздуха в плазмотрон прямого действия и косвенного действия производится по-разному. Для резки плазменной дугой требуется аксиальная подача воздуха (прямая). А для резки плазменной струей требуется тангенциальная подача воздуха.
Тангенциальная или вихревая (осевая) подача воздуха в плазмотрон необходима для того, чтобы катодное пятно располагалось строго по центру. Если тангенциальная подача воздуха нарушена, неизбежно смещение катодного пятна, а с ним и плазменной дуги. В результате плазменная дуга горит не стабильно, иногда загорается две дуги одновременно, а также весь плазмотрон выходит из строя. Воздушно-плазменная резка самодельная не способна обеспечить тангенциальную подачу воздуха. Так как для устранения турбулентностей внутри плазмотрона используют сопла специальной формы, а также вкладыши.
Сжатый воздух используется для воздушно-плазменной резки таких металлов:
- Меди и сплавов меди – толщиной не более 60 мм;
- Алюминия и сплавов алюминия – толщиной до 70 мм;
- Стали толщиной до 60 мм.
А вот для резки титана воздух использовать категорически нельзя. Более детально тонкости работы аппаратом ручной воздушно-плазменной резки рассмотрим ниже.
Как выбрать аппарат воздушно-плазменной резки
Чтобы сделать правильный выбор плазмореза для частных бытовых нужд или маленькой мастерской, необходимо точно знать для каких целей он будет использоваться. С какими заготовками придется работать, из какого материала, какой толщины, какова интенсивность загрузки аппарата и многое другое.
Для частной мастерской вполне может сгодиться инвертор, так как у таких аппаратов более стабильная дуга и больший на 30 % КПД. Трансформаторы подходят для работы с заготовками большей толщины и не боятся перепадов напряжения, но при этом они больше весят и менее экономичны.
Следующая градация – плазморезы прямого и косвенного действия. Если планируется резать только металлические заготовки, то необходим аппарат прямого действия.
Для частной мастерской или домашних нужд необходимо приобретать ручной плазморез с встроенным или внешним компрессором, рассчитанный на определенную силу тока.
Сила тока плазмореза и толщина металла
Сила тока и максимальная толщина заготовки – основные параметры для выбора аппарата воздушно-плазменной резки. Они взаимосвязаны между собой. Чем большую силу тока может подавать источник питания плазмореза, тем более толстую заготовку можно обрабатывать с помощью данного аппарата.
Выбирая аппарат для личных нужд, необходимо точно знать, какой толщины заготовки будут обрабатываться и из какого металла. В характеристиках плазморезов указывается и максимальная сила тока, и максимальная толщина металла. Но обратите внимание на то, что толщина металла указана из расчета на то, что обрабатываться будет черный металл, а не цветной и не нержавейка. А сила тока указана не номинальная, а максимальная, на данных параметрах аппарат может работать совсем непродолжительное время.
Для резки разных металлов требуется различная сила тока. Точные параметры можно увидеть в таблице ниже.
Таблица 1. Сила тока, необходимая для резки различных металлов.
Например, если планируется резать стальную заготовку толщиной 2,5 мм, то необходима сила тока 10 А. А если заготовка выполнена из цветного металла, например, меди толщиной 2,5 мм, то сила тока должна быть 15 А. Чтобы рез получился высокого качества, необходимо учитывать некий запас мощности, поэтому лучше приобрести плазморез, рассчитанный на силу тока в 20 А.
На аппарат воздушно-плазменной резки цена напрямую зависит от его мощности – выдаваемой силы тока. Чем больше сила тока, тем дороже аппарат.
Режим работы – продолжительность включения (ПВ)
Режим работы аппарата определяется интенсивностью его загрузки. На всех аппаратах указан такой параметр, как продолжительность включения или ПВ. Что она означает? Например, если указана ПВ=35%, то это означает, что плазморезом можно работать 3,5 минуты, а затем ему необходимо дать остыть в течение 6,5 минут. Цикл продолжительности включения рассчитан на 10 минут. Есть аппараты с ПВ 40%, 45%, 50%, 60%, 80%, 100%. Для бытовых нужд, где аппарат не будет использоваться постоянно, достаточно аппаратов с ПВ от 35% до 50%. Для машинной резки с ЧПУ используются плазморезы с ПВ=100%, так как они обеспечивают непрерывную работу в течение всей смены.
Обратите внимание, что в процессе работы с ручной воздушно-плазменной резкой существует необходимость переместить плазмотрон или перейти на другой конец заготовки. Все эти интервалы учитываются в счет времени охлаждения. Также продолжительность включения зависит от загрузки аппарата. Например, с начала смены даже плазморез с ПВ=35% может без перерыва работать 15 – 20 минут, но чем чаще им будут пользоваться, тем короче будет время беспрерывной работы.
Воздушно-плазменная резка своими руками – технология работы
Плазморез выбрали, с принципом работы и устройством ознакомились, пора приступать к работе. Чтобы не наделать ошибок, для начала не помешает ознакомиться с технологией работы с аппаратом воздушно-плазменной резки. Как соблюсти все меры безопасности, как подготовить аппарат к работе и правильно подобрать силу тока, а затем, как разжечь дугу и соблюдать необходимую дистанцию между соплом и поверхностью заготовки.
Позаботьтесь о безопасности
Воздушно-плазменная резка сопряжена с рядом опасностей: электрический ток, высокая температура плазмы, раскаленный металл и ультрафиолетовое излучение.
Меры безопасности при работе с плазморезом:
- Работать необходимо в специальной экипировке: темные очки или щиток сварщика (4 – 5 класс затемнения стекла), плотные перчатки на руках, штаны из плотной ткани на ногах и закрытая обувь. При работе с резаком могут образовываться газы, которые представляют угрозу для нормальной работы легких, поэтому на лицо необходимо надевать маску или респиратор.
- Плазморез подключается в сеть через УЗО.
- Розетки, рабочая подставка или стол, окружающие предметы должны быть хорошо заземлены.
- Силовые кабели должны быть в идеальном состоянии, не допускается повреждение обмотки.
То, что сеть должна быть рассчитана на то напряжение, которое указано на аппарате (220 В или 380 В), это само собой разумеющееся. В остальном же соблюдение техники безопасности поможет избежать травм и профзаболеваний.
Подготовка аппарата воздушно-плазменной резки к работе
Как подключить все элементы аппарата воздушно-плазменной резки, подробно описано в инструкции к аппарату, поэтому сразу перейдем к дальнейшим нюансам:
- Аппарат необходимо установить так, чтобы к нему был доступ воздуха. Охлаждение корпуса плазмореза позволит дольше работать без перерыва и реже отключать аппарат для охлаждения. Место расположения должно быть таким, чтобы на аппарат не попадали капли расплавленного металла.
- Воздушный компрессор подключается к плазморезу через влаго- и маслоотделитель. Это очень важно, так как попавшие в камеру плазмотрона вода или капли масла могут привести к выходу из строя всего плазмотрона или даже его взрыву. Давление подаваемого в плазмотрон воздуха должно соответствовать параметрам аппарата. Если давление будет недостаточным, то плазменная дуга будет нестабильной, часто будет гаснуть. Если давление будет избыточным, то могут придти в негодность некоторые элементы плазмотрона.
- Если на заготовке, которую собираетесь обрабатывать, есть ржавчина, окалина или масляные пятна, их лучше отчистить и удалить. Хоть воздушно-плазменная резка и позволяет резать ржавые детали, все же лучше перестраховаться, так как при нагреве ржавчины выделяются ядовитые пары. Если планируется резать емкости, в которых хранились горючие материалы, то их необходимо тщательно отчистить.
Чтобы рез получился ровным, параллельным, без окалины и наплывов, необходимо правильно подобрать силу тока и скорость резки. В представленных ниже таблицах указаны оптимальные параметры резки различных металлов различной толщины.
Таблица 2. Сила и скорость резки с помощью аппарата воздушно-плазменной резки заготовок из различных металлов.
Первое время подбирать скорость ведения резака будет сложно, необходим опыт. Поэтому поначалу можно ориентироваться на такое правило: вести плазмотрон необходимо так, чтобы с обратной стороны заготовки были видны искры. Если искр не видно, значит, заготовка не разрезана насквозь. Обратите также внимание, что слишком медленное ведение резака негативно сказывается на качестве реза, на нем появляются окалина и наплывы, а также может нестабильно гореть дуга и даже гаснуть.
Теперь можно приступать к самому процессу резки.
Розжиг плазменной дуги
Перед тем как зажечь электрическую дугу, плазмотрон следует продуть воздухом, чтобы удалить случайный конденсат и инородные частицы. Для этого необходимо нажать, а затем отпустить кнопку поджига дуги. Так аппарат переходит в режим продувки. Спустя примерно 30 секунд можно нажимать кнопку поджига и удерживать ее. Как уже описывалось в принципе работы плазмореза, между электродом и наконечником сопла загорится дежурная (вспомогательная, пилотная) дуга. Как правило, она горит не долее 2 секунд. Поэтому за это время необходимо зажечь рабочую (режущую) дугу. Способ зависит от вида плазмотрона.
Если плазмотрон прямого действия, то необходимо сделать короткое замыкание: после образования дежурной дуги необходимо нажать кнопку розжига – прекращается подача воздуха и контакт замыкается. Затем воздушный клапан открывается автоматически, поток воздуха вырывается из клапана, ионизируется, увеличивается в размерах и выводит искру из сопла плазмотрона. В результате загорается рабочая дуга между электродом и металлом заготовки.
Важно! Контактный поджиг дуги не означает, что плазмотрон необходимо прикладывать или прислонять к заготовке.
Как только загорится режущая дуга, дежурная дуга гаснет. Если не получилось зажечь рабочую дугу с первого раза, необходимо отпустить кнопку розжига и нажать ее снова – начнется новый цикл. Причин, по которым может не зажигаться рабочая дуга, несколько: недостаточное давление воздуха, неправильная сборка плазмотрона или другие неполадки.
В процессе работы также бывают случаи, когда режущая дуга гаснет. Причина, скорее всего, в изношенности электрода или несоблюдении расстояния между плазмотроном и поверхностью заготовки.
Расстояние между горелкой плазмотрона и металлом
Ручная воздушно-плазменная резка сопряжена с той трудностью, что необходимо соблюдать расстояние между горелкой/соплом и поверхностью металла. При работе рукой это довольно сложно, так как даже дыхание сбивает руку, и рез получается неровным. Оптимальное расстояние между соплом и заготовкой 1,6 – 3 мм, для его соблюдения используются специальные дистанционные упоры, ведь сам плазмотрон нельзя прижимать к поверхности заготовки. Упоры надеваются сверху на сопло, затем плазмотрон опирается упором на заготовку и выполняется рез.
Обратите внимание, что держать плазмотрон необходимо строго перпендикулярно заготовке. Допустимый угол отклонения 10 – 50 °. Если заготовка слишком тонкая, то резак можно держать под небольшим углом, это позволит избежать сильных деформаций тонкого металла. Расплавленный металл при этом не должен попадать на сопло.
Работы с воздушно-плазменной резкой своими руками вполне можно осилить самостоятельно, только важно помнить о технике безопасности, а также о том, что сопло и электрод – расходные материалы, которые требуют своевременной замены.
strport.ru
Аппарат для резки металла. Аппарат для плазменной резки металла
Операции по обработке металлических материалов требуют применения специального оборудования. В случае с тонкими листовыми изделиями вполне можно обойтись соответствующей ножовкой или даже напильником, однако толстые пласты можно разрезать только при условии интенсивного воздействия на структуру заготовки. Оптимальным решением этой задачи может стать аппарат для сварки-резки металла, действующий по принципам плазменно-воздушной обработки. Внешне такие устройства напоминают классические сварочные приборы, но есть и целый ряд существенных отличий.
Принцип работы плазмореза
Данная методика входит в группу способов обработки, предполагающих термическое воздействие на материал. То есть в процессе работы пользователь направляет рабочую головку прибора с целью нагрева конкретного участка. Устройство резака такого типа предусматривает наличие электродов и содержание плазмообразующих газов – как правило, используется сжатый воздух. После запуска аппарат для плазменной резки металла начинает выработку сварочных токов, которые нагревают электрод. Далее активизируется дуга, под действием которой происходит преобразование газа в расплавленную плазму. В зависимости от модели прибора температурный показатель данного вещества может варьироваться от 5000 до 30 000 °C.
Такой принцип обработки открывает широкие границы для применения устройства. С одной стороны, эффективность плазменного воздействия обуславливает хорошую производительность, что выгодно с точки зрения использования техники на металлургических комбинатах. С другой стороны, резка металла сварочным аппаратом отличается высокой точностью и аккуратностью, что ценят и мастера, выполняющие декоративную обработку изделий.
Разновидности устройств
На рынке можно найти две вариации подобных приборов. Для использования технологии в работе с крупными объемами заготовок рекомендуется применять трансформаторы. Это оборудование, способное резать листы толщиной до 4 см. Вторая разновидность – это инверторы, которые отличаются небольшими размерами и, соответственно, скромными показателями производительности. Так или иначе, наибольшее распространение получили как раз инверторные аппараты плазменно-воздушной резки металла, преимущества которых выражаются не только в компактности. Такие устройства также характеризуются стабильностью горения дуги, что позволяет выполнять качественный рез практически в любых условиях. Кроме этого, последние модели инверторов не так сильно уступают трансформаторам в показателях мощности. Представители высшего звена, к примеру, позволяют выполнять резку листов, толщина которых достигает 3 см.
Основные характеристики плазморезов
С пользовательской точки зрения, главным рабочим показателем является сила тока. От нее зависят возможности прибора в резке различных видов металла. Соотнося потенциал устройства и характеристики заготовки, следует опираться на следующий принцип: повышение силы тока увеличивает мощность дуги и, следовательно, интенсивность нагрева. Например, маломощный аппарат для резки металла с силой тока 40 А позволит справиться с листом толщиной 1-1,2 см. Если же силовой потенциал увеличить до 160 А, то применение оборудования будет возможно и для работы с 4-сантиметровыми листами.
Это вовсе не означает, что надо ориентироваться на максимальные показатели при выборе. Большая мощность не пригодится и даже будет излишней, если требуется выполнение фигурной резки. Если же не предполагается постоянное и целенаправленное использование устройства для работы с конкретными материалами, то есть смысл приобрести аппарат для резки металла универсального назначения. Подобные модели предусматривают возможность регулировки силы тока, что существенно расширяет спектр решаемых задач.
Компрессор для плазмореза
Поскольку методика обработки предусматривает обеспечение подачи сжатого воздуха, то следует изначально подготовить и компрессор. В некоторых моделях он входит и в основную конструкцию, но подобное оборудование имеет серьезные ограничения по мощности. Для регулярной эксплуатации оптимальной будет конфигурация с применением внешнего компрессора. При условии правильно организованной пневматической сети такой аппарат для плазменной резки металла обеспечит и высокую производительность, и стабильность нагрева в течение всего рабочего сеанса.
Производители аппаратов
Начальный сегмент представляют в основном отечественные модели от компаний «Барс», «Сварог» и «Ресанта». Это устройства стоимостью 25-30 тыс. руб., которые неплохо справляются с заготовками толщиной до 1 см. Для более сложных задач обработки стоит обращаться к моделям из линеек Fubag, Telwin, Blue Weld и т. д. В данном случае значительно повышается стоимость (50-70 тыс. руб.), однако пользователь может рассчитывать на возможность формирования реза на большой глубине. Кроме того, аппарат для резки металла высокого класса позволит работать с большим количеством насадок, что обуславливает и многофункциональность инструмента.
Альтернативное оборудование
Строительные технологии позволяют выполнять операции резки твердотельных материалов разными способами. Но далеко не все методы удается оптимизировать с расчетом на применение массовым потребителем. Ближайшую конкуренцию плазменной обработке все еще составляет классический отрезной диск, обеспечивающий механическое воздействие. Однако по сравнению с ним термические рабочие элементы отличаются аккуратностью и точностью обработки. В последнее время распространен и аппарат лазерной резки металла, который представляет собой конструкцию в виде небольшого станка. Подобная техника отличается высокой скоростью реза, точностью и удобством применения, но и цена ее в разы превышает стоимость плазморезов.
Заключение
Метод обработки посредством термического воздействия на сегодняшний день является самым популярным средством для резки металла. Вовсе не потому, что инструмент обеспечивает наилучшие эксплуатационные показатели. Он проигрывает упомянутым лазерным станкам во многих параметрах и стоит дороже традиционных агрегатов с отрезными дисками. Зато с точки зрения универсальности плазменный аппарат для резки металла не имеет конкурентов. Сбалансированность технико-эксплуатационных показателей дает возможность использовать этот инструмент и в быту, и в промышленности. Кроме того, производители дополняют линейки специализированными моделями, которые предназначены для выполнения узкопрофессиональных операций.
fb.ru
Плазменная резка металла – аппараты, технология, видео процесса
В последнее время использование плазменного потока для раскроя материалов набирает все большую популярность. Еще более расширяет сферу использования данной технологии появление на рынке ручных аппаратов, с помощью которых выполняется плазменная резка металла.

Плазменная резка металла значительной толщины
Суть плазменной резки
Плазменная резка предполагает локальный нагрев металла в зоне разделения и его дальнейшее плавление. Такой значительный нагрев обеспечивается за счет использования струи плазмы, формируют которую при помощи специального оборудования. Технология получения высокотемпературной плазменной струи выглядит следующим образом.
- Изначально формируется электрическая дуга, которая зажигается между электродом аппарата и его соплом либо между электродом и разрезаемым металлом. Температура такой дуги составляет 5000 градусов.
- После этого в сопло оборудования подается газ, который повышает температуру дуги уже до 20000 градусов.
- При взаимодействии с электрической дугой газ ионизируется, что и приводит к его преобразованию в струю плазмы, температура которой составляет уже 30000 градусов.
Полученная плазменная струя характеризуется ярким свечением, высокой электропроводностью и скоростью выхода из сопла оборудования (500–1500 м/с). Такая струя локально разогревает и расплавляет металл в зоне обработки, затем осуществляется его резка, что хорошо видно даже на видео такого процесса.
В специальных установках для получения плазменной струи могут использоваться различные газы. В их число входят:
- обычный воздух;
- технический кислород;
- азот;
- водород;
- аргон;
- пар, полученный при кипении воды.
Технология резки металла с использованием плазмы предполагает охлаждение сопла оборудования и удаление частичек расплавленного материала из зоны обработки. Обеспечивается выполнение этих требований за счет потока газа или жидкости, подаваемых в зону, где осуществляется резка. Характеристики плазменной струи, формируемой на специальном оборудовании, позволяют произвести с ее помощью резку деталей из металла, толщина которых доходит до 200 мм.

Устройство и принцип действия плазменной резки
Аппараты плазменной резки успешно используются на предприятиях различных отраслей промышленности. С их помощью успешно выполняется резка не только деталей из металла, но и изделий из пластика и натурального камня. Благодаря таким уникальным возможностям и своей универсальности, данное оборудование находит широкое применение на машиностроительных и судостроительных заводах, в рекламных и ремонтных предприятиях, в коммунальной сфере. Огромным преимуществом использования таких установок является еще и то, что они позволяют получать очень ровный, тонкий и точный рез, что является важным требованием во многих ситуациях.
Оборудование для плазменной резки
На современном рынке предлагаются аппараты, с помощью которых выполняется резка металла с использованием плазмы, двух основных типов:
- аппараты косвенного действия — резка выполняется бесконтактным способом;
- аппараты прямого действия — резка контактным способом.
Оборудование первого типа, в котором дуга зажигается между электродом и соплом резака, используется для обработки неметаллических изделий. Такие установки преимущественно применяются на различных предприятиях, вы не встретите их в мастерской домашнего умельца или в гараже ремонтника.

Аппарат для плазменной резки Ресанта ИПР-25
В аппаратах второго типа электрическая дуга зажигается между электродом и непосредственно деталью, которая, естественно, может быть только из металла. Благодаря тому, что рабочий газ в таких устройствах нагревается и ионизируется на всем промежутке (между электродом и деталью), струя плазмы в них отличается более высокой мощностью. Именно такое оборудование может использоваться для выполнения ручной плазменной резки.
Любой аппарат плазменной резки, работающий по контактному принципу, состоит из стандартного набора комплектующих:
- источника питания;
- плазмотрона;
- кабелей и шлангов, с помощью которых выполняется соединение плазмотрона с источником питания и источником подачи рабочего газа;
- газового баллона или компрессора для получения струи воздуха требуемой скорости и давления.
Главным элементом всех подобных устройств является плазмотрон, именно он отличает такое оборудование от обычного сварочного. Плазмотроны или плазменные резаки состоят из следующих элементов:
- рабочего сопла;
- электрода;
- изолирующего элемента, который отличается высокой термостойкостью.

Резак для ручной плазменной резки
Основное назначение плазмотрона состоит в том, чтобы преобразовать энергию электрической дуги в тепловую энергию плазмы. Газ или воздушно-газовая смесь, выходящие из сопла плазмотрона через отверстие небольшого диаметра, проходят через цилиндрическую камеру, в которой зафиксирован электрод. Именно сопло плазменного резака обеспечивает требуемую скорость движения и форму потока рабочего газа, и, соответственно, самой плазмы. Все манипуляции с таким резаком выполняются вручную: оператором оборудования.
Учитывая тот факт, что держать плазменный резак оператору приходится на весу, бывает очень сложно обеспечить высокое качество раскроя металла. Нередко детали, для получения которых была использована ручная плазменная резка, имеют края с неровностями, следами наплыва и рывков. Для того чтобы избежать подобных недостатков, применяют различные приспособления: подставки и упоры, позволяющие обеспечить ровное движение плазмотрона по линии раскроя, а также постоянство зазора между соплом и поверхностью разрезаемой детали.
В качестве рабочего и охлаждающего газа при использовании ручного оборудования может использоваться воздух или азот. Такая воздушно-газовая струя, кроме того, применяется и для выдува расплавленного металла из зоны реза. При использовании воздуха он подается от компрессора, а азот поступает из газового баллона.Необходимые источники питания
Несмотря на то что все источники питания для плазменных резаков работают от сети переменного тока, часть из них может преобразовывать его в постоянный, а другие — усиливать его. Но более высоким КПД обладают те аппараты, которые работают на постоянном токе. Установки, работающие на переменном токе, применяются для резки металлов с относительно невысокой температурой плавления, к примеру, алюминия и сплавов на его основе.
В тех случаях, когда не требуется слишком высокая мощность плазменной струи, в качестве источников питания могут использоваться обычные инверторы. Именно такие устройства, отличающиеся высоким КПД и обеспечивающие высокую стабильность горения электрической дуги, используются для оснащения небольших производств и домашних мастерских. Конечно, разрезать деталь из металла значительной толщины с помощью плазмотрона, питаемого от инвертора, не получится, но для решения многих задач он подходит оптимально. Большим преимуществом инверторов является и их компактные габариты, благодаря чему их можно легко переносить с собой и использовать для выполнения работ в труднодоступных местах.
Более высокой мощностью обладают источники питания трансформаторного типа, с использованием которых может осуществляться как ручная, так и механизированная резка металла с использованием струи плазмы. Такое оборудование отличается не только высокой мощностью, но и более высокой надежностью. Им не страшны скачки напряжения, от которых другие устройства могут выйти из строя.

Резка по шаблону
У любого источника питания есть такая важная характеристика, как продолжительность включения (ПВ). У трансформаторных источников питания ПВ составляет 100%, это означает, что их можно использовать целый рабочий день, без перерыва на остывание и отдых. Но, конечно, есть у таких источников питания и недостатки, наиболее значимым из которых является их высокое энергопотребление.
Как выполняется ручная плазменная резка?
Первое, что необходимо сделать для того чтобы начать использование аппарата для плазменной резки металла, — это собрать воедино все его составные элементы. После этого инвертор или трансформатор подсоединяют к заготовке из металла и к сети переменного тока.
Далее технология резки предусматривает приближение сопла устройства к заготовке на расстояние порядка 40 мм и зажигание так называемой дежурной дуги, за счет которой будет осуществляться ионизация рабочего газа. После того как дуга загорелась, в сопло подается воздушно-газовый поток, который и должен сформировать плазменную струю.
Когда из рабочего газа сформируется плазменная струя, обладающая высокой электропроводностью, между электродом и деталью создается уже рабочая дуга, а дежурная автоматически отключается. Задача такой дуги состоит в том, чтобы поддерживать требуемый уровень ионизации плазменной струи. Случается, что рабочая дуга гаснет, в таком случае следует перекрыть подачу газа в сопло и повторить все описанные действия заново. Лучше всего, если нет опыта выполнения такого процесса, посмотреть обучающее видео, где подробно показана ручная резка металла.
Оценка статьи:

Поделиться с друзьями:
met-all.org
устройство, принцип действия, выбор, какой лучше
Что такое плазморез, как он работает? Если говорить об этом инструменте, то необходимо отметить, что он является прибором, который использует достаточно узкий круг сварщиков. Для одноразового применения плазменный резак нигде и никогда не применяется. Потому что существуют инструменты, с помощью которых можно провести отрезные операции, не прибегая к дорогому варианту, к примеру, болгаркой.
Но если требования к скорости и объему проводимых процессов достаточно жесткие, то без плазмореза не обойтись. Поэтому его используют в машиностроительной промышленности, в изготовлении больших металлических конструкций, при резке труб и прочего.
Виды плазменных резаков и их назначение
На вопрос, как выбрать плазморез, необходимо ответить так, все будет зависеть от того, в какой области вы его собираетесь использовать. Потому что конструктивные особенности у разных видов сильно отличаются, у всех у них разный тип зажигания дуги и различная мощность системы охлаждения.
- Инструменты, работающие в среде защитных газов: аргон, водород, азот, гелий и так далее. Эти газы обладают восстановительными свойствами.
- Резаки, работающие в среде окислительных газов. Газы обычно насыщаются кислородом.
- Приборы, работающие со смесями.
- Плазменные резаки, работающие в стабилизаторах газожидкостного типа.
- Плазморезы, работающие со стабилизацией водной и магнитной. Специфичный инструмент, который редко используется, поэтому в свободной продаже трудно найти.
Существует еще одна классификация, которая делит плазморезы по виду используемого оборудования.
- Инверторные. Экономичный вариант, который может резать металлические детали толщиною до 30 мм.
- Трансформаторные. Производит резку металлов толщиною до 80 мм, менее экономичный вариант.
По типу контакта плазморезы делятся на контактные и бесконтактные. Из названий можно понять метод использования плазменного резака. В первом случае для него необходим контакт с обрабатываемым металлом, поэтому с его помощью можно отрезать изделия толщиною не более 18 мм. Во втором такого контакта не должно быть, зато толщина отрезаемой металлической заготовки может быть максимально возможной.
И еще один вид разделения – это по типу использования и возможностях потребления электроэнергии. Здесь две позиции: бытовой, работающий от сети переменного тока под напряжением 220 вольт, и промышленные (профессиональные), подключаемые к трехфазной питающей сети напряжением 380 вольт.
Внимание! Даже самый маломощный бытовой резак плазменного типа обладает мощностью 4 кВт. Поэтому при подключении его в бытовую электрическую сеть, необходимо удостовериться, что она сможет выдержать такую нагрузку.
Но данная нагрузка не единственная. В системе плазменной резки используется охлаждение, для чего в комплект к основному оборудованию прилагается компрессор, который также работает от электросети. И его мощность нужно учитывать, подключаясь к бытовой питающей сети.
Устройство плазмореза
Само название уже информирует о том, что резка металлов производится с помощью плазмы. А плазма – это ионизированный газ, который обладает высокой проводимостью электрического тока. И чем выше температура этого газа, тем выше проводимость, а значит, сила резки увеличивается.
Для процессов резки металлов используют воздушно-плазменную дугу. При этом электрический ток имеет непосредственное воздействие на металлические поверхности. То есть, принцип работы плазмореза такой:
- Плавление металла.
- Выдувание его жидкого состояния из зоны среза.
Состоит плазменный резак из:
Важно понять конструктивные особенности самого резака. Внутри него вставлен электрод, изготовленный из редких металлов, таких как бериллий, гафний, цирконий и так далее. Почему именно они? Потому что в процессе нагревания на поверхности такого электрода образуются тугоплавкие оксиды. Они своеобразная защита самого электрода, которая обеспечивает целостность материала, то есть, не разрушается. Но чаще всего в плазменных резаках устанавливаются электроды из гафния, потому что он не токсичен, как торий, и нерадиоактивен, как бериллий.
Немаловажное значение в конструкции резака играет и сопло, через который подается плазма на резку. Именно от него и зависят основные характеристики оборудования. А точнее сказать, от его диаметра и длины. От диаметра зависит мощность плазменного потока, а соответственно и быстрота среза и ширины срезанной канавки. Конечно, от этого зависит и скорость охлаждения заготовки. Чаще всего на резаках плазменной резки устанавливается сопло диаметром 3 мм. Длина сопла влияет на качество среза. Чем оно длиннее, тем качество выше. Хотя очень длинное сопло быстро выходит из строя.
Схема работы плазменной резки
При нажатии на кнопку розжига автоматически включается источник электроэнергии, который подает в резак ток высокой частоты. Появляется так называемая дежурная дуга между наконечником сопла и электродом. Температура дуги – 6000-8000С. Необходимо обратить внимание, что сразу дуга между электродом и разрезаемым металлом не образуется, на это надо время.
После чего в камеру резака начинает поступать воздух из компрессора, он сжатый. При прохождении через камеру, где располагается дежурная дуга, воздух нагревается и увеличивается в сто раз. К тому же он начинает ионизироваться, то есть, превращается в токопроводящую среду, хотя сам по себе воздух – это диэлектрик.
Суженное до 3 мм сопло создает поток плазмы, который с большой скоростью вылетает из резака. Скорость – 2-3 м/с. Температура ионизированного воздуха достигает огромной величины – до 30000С. При такой температуре воздух по проводимости электрического тока приближается к проводимости металла.
Как только плазма касается обрабатываемой металлической поверхности, дежурная дуга выключается, а рабочая включается. Производится плавление металлической заготовки в месте среза, откуда жидкий металл сдувается подающим в зону среза воздухом. Вот такая элементарная схема принципа работы плазменной резки.
Как правильно выбрать инструмент для плазменной резки
Любой работавший с плазменной резкой сварщик отметит, что чем выше сила подающего на электрод тока, тем быстрее проходит процесс. Но есть определенные условия, на которые влияют и другие параметры оборудования.
Тип металла и толщина среза. От этих параметров будет зависеть выбор оборудования, с которым придется работать. А именно такой параметр, как сила тока. Внизу таблица соотношений.
Цветные металлы | 6 |
Черные металлы и нержавейка | 4 |
Чтобы разрезать медный лист толщиною 2 мм, потребуется резак плазменный с силой тока 12 А. И так далее.
Внимание! Рекомендуется приобретать оборудование с запасом силы тока. Потому что указанные параметры в таблице являются максимальными, а с ними работать можно лишь незначительное время.
Достоинства и недостатки
Перед тем как принять решение о приобретение плазменного резака, нужно ознакомиться со всеми положительными и отрицательными сторонами этого оборудования. Ведь, к примеру, в домашних условиях его может заменить обычная болгарка.
Итак, плюсы использования резака для плазменной резки металлов.
- Большая скорость резки, соответственно уменьшение времени на этот процесс. По сравнению с другими режущими инструментами (кислородная горелка, например) скорость выше в шесть раз. Уступает только лазерной резке.
- С помощью плазменного инструмента можно резать толстые заготовки, что иногда не под силу болгарке.
- Режет любые виды металлов. Главное – правильно выставить режим работы.
- Минимальный подготовительный этап. Зачищать поверхности деталей от ржавчины, грязи, масляных пятен нет никакого смысла. Они для резки не помеха.
- Высочайшая точность среза и высокое его качество. Для ручных агрегатов для точности среза используются специальные упоры, которые не дают резаку смещаться в плоскости. Срез получается без наплывов, ровным и тонким.
- Невысокая температура нагрева, кроме зоны среза, поэтому заготовки не деформируются.
- Возможность фигурного среза. И хотя этим могут похвастаться и другие режущие инструменты, но, к примеру, после кислородной горелки придется края среза шлифовать и убирать подтеки металла.
- Стопроцентная безопасность проводимых операций, ведь никаких газовых баллонов в комплекте оборудования нет.
Минусы:
- Высокая цена оборудования.
- Возможность работать только одним резаком.
- Необходимо направление плазмы выдерживать строго перпендикулярно плоскости обрабатываемой детали. Правда, сегодня можно приобрести аппараты, которые режут изделия под разными углами: 15-50°.
- Толщина разрезаемого изделия ограничена, потому что самые мощные плазморезы могут разрезать металл толщиною 100 мм. С помощью кислородной горелки можно резать толщину 500 мм.
И все же плазморезы сегодня достаточно востребованы. Ручные часто используются в небольших цехах, где требуется провести большой объем резки металлов, и где к качеству разреза предъявляются жесткие требования. Обязательно посмотрите видео, которое специально размещено на этой странице сайта.
Поделись с друзьями
2
0
1
0
svarkalegko.com
Ручная плазменная резка металла – аппараты и принцип их работы + Видео
Раскрой материалов потоком плазмы является высокотехнологичным, эффективным способом качественной их обработки. Ручная плазменная резка, проводимая соответствующим оборудованием, расширяет область применения этого вида работ.
1 Особенности аппаратов и технологии плазменной резки
Плазменная резка – термический процесс разделительной обработки материалов, происходящей за счет их плавления. В качестве режущего исполнительного инструмента используется струя низкотемпературной плазмы, которую получают следующим образом. Между электродом плазменного аппарата и его соплом или разрезаемым металлом создается электрическая дуга, температура которой достигает 5000 °С.
Затем в сопло подается под давлением газ, что приводит к повышению температуры электрической дуги до 20 000 °С, в результате чего газ ионизируется и преобразуется в низкотемпературную плазму (высокотемпературный газ). Ионизация при нагреве от дуги возрастает, что ведет к повышению температуры газовой струи до 30 000 °С. При этом поток плазмы ярко светится, обладает высокой электропроводностью, проистекает из сопла со скоростью 500–1500 м/с, попадая на заготовку, локально ее разогревает и плавит в месте реза.
Рекомендуем ознакомиться
Для получения плазмы используют следующие газы:
- воздух;
- кислород;
- азот;
- водород;
- аргон;
- водяной пар.
Охлаждение сопла и удаление с поверхности реза расплавленных частичек материала осуществляется потоком газа или жидкости. Толщина разрезаемого плазменными установками металла может достигать 200 мм.
Эта технология крайне редко используется в быту, зато получила широкое распространение в различных промышленных отраслях. Плазменным аппаратом можно качественно, быстро, легко разрезать любой металл и другие материалы – пластик, камень. Благодаря этому, его используют в судостроении, машиностроении, коммунальной сфере, для ремонта техники, изготовлении рекламы и многого другого. Получаемый срез всегда аккуратный, ровный и красивый.
2 Основная классификация плазменного оборудования для резки
Все устройства для плазменной резки делятся на:
- косвенного действия – для бесконтактной резки;
- прямого действия – для контактной.
Резаки первого типа используются для обработки неметаллических материалов. Такая техника является специфической и не востребована вне производства. При бесконтактном способе электрическая дуга зажигается между электродом и соплом плазмотрона.
Устройствами прямого действия режут различные металлы. При работе с ними разрезаемая деталь включена в электрическую схему плазменного аппарата, и электрическая дуга зажигается между ней и электродом, расположенном в сопле. Поток ионизированного газа подвергается нагреву на всем участке между местом своего выхода и поверхностью заготовки – струя плазмы обладает большей мощностью, чем в устройствах первого типа. Ручная плазменная резка металла выполняется только с помощью оборудования данного типа, контактным способом.
3 Устройства для ручной плазменной резки металлов
Они состоят из плазмотрона, источника питания, набора кабелей и шлангов, с помощью которых производится соединение плазмотрона с источником питания и газовым баллоном или компрессором. Плазмотрон (плазменный резак) – главный элемент такого оборудования. Иногда по ошибке так называют весь аппарат. Возможно, это обусловлено тем, что применяемые для плазмореза источники питания не отличаются от подобных им устройств и могут использоваться вместе со сварочным оборудованием. А единственным элементом, который отличает плазменный аппарат от другого устройства, и является плазмотрон. Его основные составляющие:
- сопло;
- электрод;
- термостойкий изолятор, расположенный между ними.
Плазмотрон – это оборудование, которое энергию электрической дуги преобразует в тепловую энергию плазмы.Внутри его корпуса имеется цилиндрическая камера с выходным каналом (соплом) очень маленького диаметра. В тыльной части камеры установлен электрод, который служит для образования электрической дуги. Сопло отвечает за скорость и форму потока плазмы. Аппарат ручной плазменной резки применяется для раскроя металла вручную – оператор держит плазмотрон в руках и ведет его над линией реза.
Так как рабочий инструмент находится все время на весу, и поэтому может быть подвержен перемещениям из-за непроизвольных движений исполнителя, это неизменно отражается на качестве раскроя. Рез может быть неровным, с наплывами, следами рывков и так далее. Для облегчения и улучшения качества работы существуют специальные подставки, упоры, надеваемые на сопло плазмотрона. Они позволяют поставить оборудование непосредственно на заготовку и вести его вдоль линии реза. Зазор между металлом и соплом в этом случае всегда будет соответствовать предъявляемым требованиям.
При ручной резке плазмообразующим и защитным (для охлаждения сопла и удаления продуктов резки) газом может быть воздух или азот. Они подаются от магистрали, баллона или встроенного в оборудование компрессора.
4 Источники питания ручных плазменных аппаратов для резки
Все источники питания ручных аппаратов работают от электросетей переменного тока. Большинство из них преобразуют получаемую электроэнергию в напряжение постоянного тока, а остальные служат только для усиления переменного тока. Такое распределение обусловлено тем, что у плазмотронов, работающих на постоянном токе, более высокий КПД. Переменный ток применяется в ряде случаев – к примеру, для раскроя алюминия и сплавов из него.
Источником питания может служить инвертор или трансформатор, подающий на плазмотрон ток большой силы. Инверторы обычно используют на маленьких производствах и в быту. Они обладают меньшими габаритами, весом и в энергопотреблении намного экономнее, чем трансформаторы. Инверторы чаще всего входят в состав ручного аппарата для плазменной резки. К достоинствам инверторных устройств относят КПД, который выше, чем у трансформаторных, на 30 %, и стабильное горение электрической дуги, а также компактность и возможность проводить работы в любых труднодоступных местах.
К недостаткам – ограничение по мощности (максимальная сила тока обычно составляет 70–100 А). Как правило, инверторные аппараты используют при разрезании заготовок сравнительно небольшой толщины.
Трансформаторные источники питания получили свое название из-за используемых в их конструкции низкочастотных трансформаторов. Они обладают гораздо большими габаритами и массой, но при этом могут иметь и более высокую, чем инверторные источники, мощность. Трансформаторные аппараты применяют для ручной и механизированной резки металлов различных толщин. Они более надежны, потому что при скачках напряжения не выходят из строя. Продолжительность их включения выше, чем у инверторных аппаратов, и может достигать значений в 100 %.
Продолжительность включения (ПВ) оказывает прямое влияние на специфику работы с оборудованием. Например, если ручная плазменная резка металла, оборудование для которой имеет ПВ 40 %, длилась без перерыва 4 минуты, то затем аппарату необходимо дать 6 минут отдыха для того, чтобы он остыл. Устройства с ПВ 100 % используют в производстве, где аппарат эксплуатируется на протяжении всего рабочего дня. Существенный недостаток трансформаторного оборудования – высокое энергопотребление.
5 Принцип работы аппаратов для ручной плазменной резки
После того, как установка ручной плазменной резки собрана (произведены все подключения и соединения ее элементов), металлическую заготовку подсоединяют к аппарату (инвертору или трансформатору) предусмотренным для этого кабелем. Оборудование подключают к электросети, плазмотрон подносят к обрабатываемому материалу на расстояние до 40 мм и производят зажигание дежурной (инициирующей ионизацию) электрической дуги. Затем открывают подачу газа.
После получения плазменной струи, которая обладает высокой электропроводимостью, в момент ее соприкосновения с металлом образуется рабочая (режущая) электрическая дуга. Одновременно автоматически отключается дежурная. Рабочая дуга поддерживает непрерывность процесса ионизации подаваемого газа, образования плазменного потока. Если она по какой-то причине погаснет, то требуется прекратить подачу газа, заново включить плазменный аппарат и зажечь дежурную дугу, а после этого пустить газ.
tutmet.ru