Ремонт инверторных сварочных аппаратов своими руками. Реостат для сварочного аппарата
Ремонт сварочных аппаратов
Разница между старым сварочным трансформатором и новым инверторным сварочником примерно такая же, как между первыми автомобилями «Даймлер Бенц» и современным «Мерседесом». Инвертор значительно легче своего неподъемного предшественника, имеет встроенные функции, о которых ранее можно было только мечтать, например, возможность контроля величины сварочного тока или функция предотвращения залипания электрода. Но у великолепно задуманной идеи есть существенный недостаток – электронная начинка выходит из строя значительно чаще, чем у «старичков», а ремонт инверторных сварочных аппаратов требует немалых знаний и навыков. Любая попытка отремонтировать оборудование вслепую, без подготовки, чревата пожаром или даже травмой.
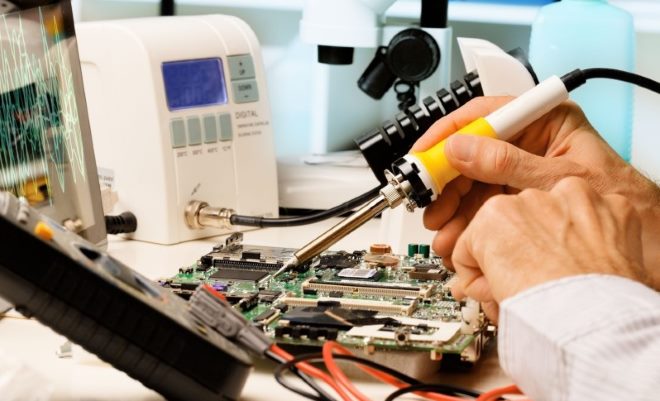
Как правильно организовать ремонт сварочного инвертора
Разумеется, ситуации, когда электронный сварочный аппарат сгорает, как свечка, и не подлежит дальнейшему ремонту, случаются крайне редко. На практике ремонт сварочного аппарата может оказаться намного проще, чем казалось в первый момент. В 90% случаев из строя выходят силовые цепи, в 50% — чувствительные управляющие элементы схемы. Но чтобы выполнять ремонт инверторных сварочных аппаратов своими руками, мало одного желания, как минимум, потребуется следующее оборудование:
- Цифровой тестер или мультиметр, все равно какой, можно с функцией проверки транзисторов;
- Паяльная станция, можно самодельная, но обязательно с регулируемым по температуре феном и исправным низковольтным паяльником;
- Нагрузочный реостат.
Кроме перечисленного, для работы может потребоваться шприц для откачки припоя, кисточка, спирт, лупа, сильный фонарик, лампа накаливания с проводами, ну и, конечно, справочники для заказа запасных частей.
Совет! У большинства профессиональных ремонтников имеется в распоряжении осциллограф. Для ремонта электроники, по сути, незаменимая вещь, если дело касается проверки работы системы управления аппарата.
Не факт, что осциллограф потребуется для ремонта сварочного аппарата своими руками, но в особо сложных случаях без него просто не обойтись.
Восстанавливаем сварочный инвертор, полный курс выживания
Перед тем как раскрывать аппарат и вникать в детали поломки, необходимо выяснить у сварщика две основные подробности. Во-первых, необходимо выяснить, как и в каких условиях произошла поломка сварочного инвертора, и во-вторых, были ли попытки выполнить ремонт другими специалистами.
Проблема заключается в том, что «любители» нередко заменяют заводские детали первыми попавшимися под руку компонентами. Без схемы восстановить номинал и марку детали, что крайне важно для качественного ремонта сварочного аппарата, очень сложно.
Процесс восстановления сварочного аппарата выполняется в три этапа:
- Разборка устройства и осмотр внутренних повреждений;
- Последовательная диагностика и устранение выявленных проблем;
- Испытание и проверка работоспособности сварочного аппарата не на искру, как делает большинство любителей, а на балластный реостат большой мощности.
Нередко любительский ремонт сварочных аппаратов заканчивается проверкой, зажигается дуга или нет. Использование реостата позволяет проверить один из основных параметров работоспособности сварочного инвертора – способность к регулировке и подстройке сварочного тока под нагрузкой.
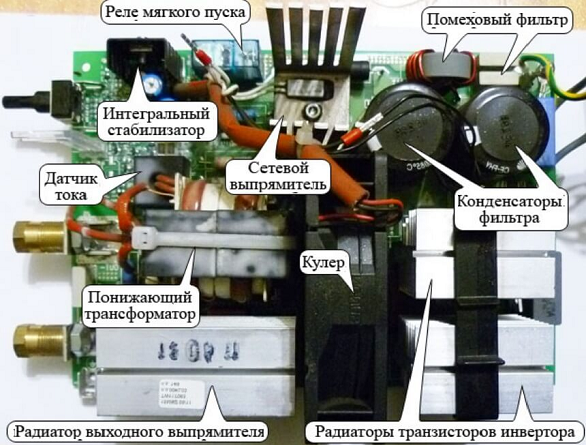
Перед тем как приступать к ремонту, нужно разобраться и выяснить для себя, как устроен аппарат, и в чем особенности его работы. Например, посмотреть типовую схему или блок схему, тогда станет понятно, что и где находится на плате.
Этап первый, определяем проблемы внешним осмотром платы
Чтобы получить доступ к внутренней начинке сварочного агрегата, необходимо освободить электронную плату от корпуса и сетевого шнура.
Совет! Если перед ремонтом аппарат включался в сеть для проверки, перед разборкой сварочного инвертора осторожно замкните выходные муфты под сварочные шланги с помощью пары проводов и обычной лампы накаливания 100-150 Вт. Это поможет избежать ударов током.
Для разборки нужно снять два-четыре винтовых или саморезных крепления корпуса и вытащить из и соединительных фишек провода. Для ремонта остается голая плата, утыканная электронными деталями. Первым делом осматриваем ее, стараемся выявлять критические для ремонта сгоревшие или поврежденные элементы, подгоревшие дорожки платы, черные резисторы и раздувшиеся конденсаторы.

В подавляющем большинстве случаев выходят из строя и подлежат ремонту следующие элементы платы сварочного аппарата:
- Балластное мощное сопротивление, разряжающее конденсаторы в силовом блоке схемы. Если питающий блок исправен, то при попытке включить сварочный аппарат конденсаторы моментально наберут немаленькую емкость и напряжение под 300В. Если в ходе ремонта, при отсутствии резистора, включить аппарат сварочный и случайно коснуться руками клемм, получите крайне болезненный удар током, почти как электрошоком;
- Полевые транзисторы-ключи. Их легко найти, они всегда установлены на массивных алюминиевых радиаторах. Если сгорело сопротивление, почти всегда требуется ремонт и замена как минимум одного из транзисторов;
- Если не регулируется сварочный ток, то, скорее всего, потребуется ремонт драйвера, одного из его каналов или операционного усилителя, входящего в схему управления.
Разумеется, приведенный перечень для ремонта является наиболее распространенным, но не исчерпывающим. Например, может сгореть термодатчик, следящий за перегревом сварочного аппарата, токовый трансформатор, работающий в паре с операционником, элементы входного диодного моста и многое другое. Поэтому ремонт сварочного аппарата необходимо начинать с прозвонки элементов по цепи.

Второй этап ремонта, проверяем цепи прозвонкой
В ходе ремонта нужно проверить самые нагруженные элементы платы. Переворачиваем ее тыльной стороной кверху и острыми щупами тестера, продираясь сквозь слой защитного лака, проверяем наличие короткого замыкания. Первоначально проверим, не пробит ли выпрямительный диодный мост на выходе. Ремонт диодов — довольно редкая вещь, если внутрь сварочного аппарата не попала вода или не произошло КЗ на шнуре. Аналогично меряем мост на входе.

После блока питания переходим к самым ответственным местам силовой части схемы. Это пара мощных конденсаторов и ключи на полевых транзисторах. Для ремонта необходимо установить наличие сопротивления между коллектором и эмиттером, или правильнее – переходы сток-сток, сток-затвор. В 99% случаев полевые транзисторы выходят из строя первыми, как результат — короткое замыкание между коллектором и стоком.
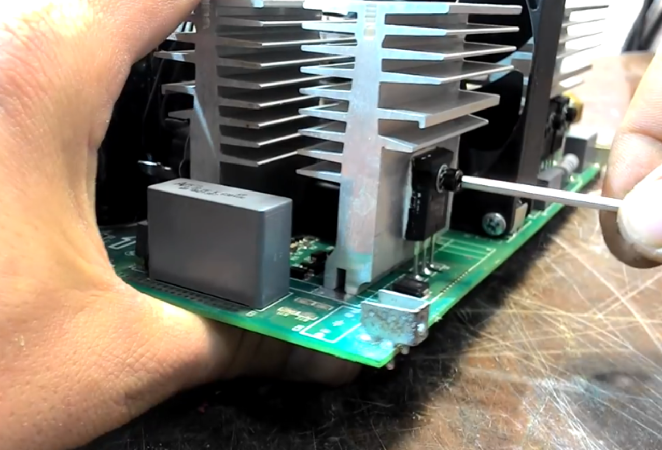
Кроме них, вторым кандидатом на ремонт и замену является драйвер платы сварочного аппарата. Но для его ремонта потребуются очень серьезные навыки и знания. Поэтому, если после замены транзисторов будут определены неисправности в каналах драйвера, лучше поручить его ремонт более квалифицированному специалисту.
Как проверить целостность драйвера
Забегая вперед, можно сказать, что после демонтажа ключей или полевых транзисторов потребность в ремонте драйвера первоначально определяют по состоянию опорных резисторов, соединяющих канал драйвера с затвором полевого транзистора — ключа. Для этого просто пальцем по плате проследим дорожку от места затвора до первого резистора. Проверяем его на обрыв, если сопротивления резисторов в каждом канале примерно совпадают, то на 99% можно считать, что устройство управления в рабочем состоянии.

В противном случае для ремонта сварочного аппарата придется обращаться к специалисту.
Простейший ремонт сварочного аппарата
Для ремонта агрегата потребуется снять старые транзисторы и заменить их новыми деталями. Каждый ключ крепится к массивному алюминиевому радиатору болтиком. После снятия болтов выворачивают саморезы крепления радиаторов. Для ремонта потребуется аккуратно выпаять полевой транзистор с помощью фена паяльной станции, делается это с максимальной осторожностью, чтобы не повредить дорожки и навесной монтаж. При выпаивании транзистор должен выйти без усилия, в противном случае поднимутся дорожки, и стоимость ремонта сварочного аппарата может подскочить в несколько раз. Место выпайки нужно освободить от припоя с помощью груши или шприца и очистить от пригорелого лака.
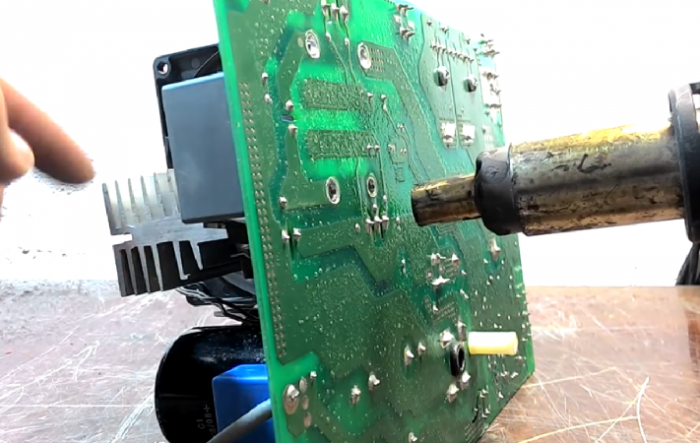
Перед установкой новых полевых транзисторов – ключей нужно выполнить ремонт балластного сопротивления. Вместо старого резистора, впаиваем новую деталь на 47 Ом, 10 Вт. Кроме того, прозваниваем конденсаторы и супрессоры, установленные по схеме на дорожках полевиков.
Чтобы продолжить ремонт, необходимо проверить форму и размер сигнала, приходящего по каждому каналу драйвера на затворы своего ключа — полевого транзистора. Перед тем как подключить осциллограф, между стоком и затвором рекомендуется выполнить навеску в виде конденсатора в несколько сот пикофарад, тем самым имитируется емкость затвора транзистора. Такой способ позволяет в ходе восстановления платы сварочного аппарата оптимальным образом нагрузить каждый канал драйвера, поэтому сигнал приходит в том виде, в котором он существует в реальных условиях при проведении сварочных работ.
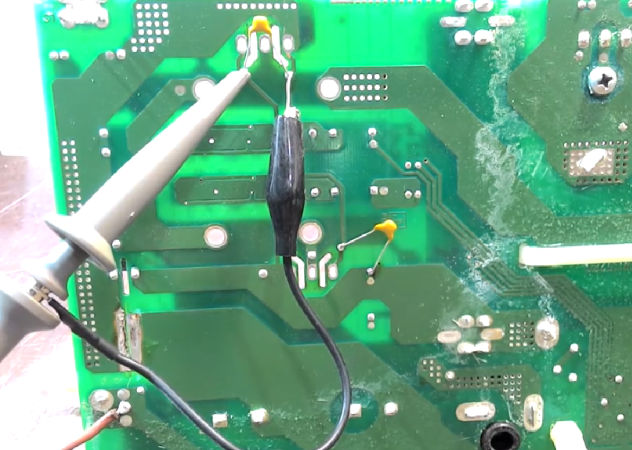
После напайки конденсаторов подключаются щупы осциллографа, и включается питание платы сварочного аппарата.

Форма сигнала подтверждает, что ремонт выполнен правильно, на затворы транзисторов приходит сигнал от драйвера нужной формы и величины.
Осталось только закрепить новые полевые транзисторы с нанесенной теплоотводящей пастой на алюминиевых радиаторах. Радиаторы устанавливаются на плату, а ножки транзисторов поочередно запаиваются. Восстановление сварочного аппарата практически закончено, осталось только испытать устройство.

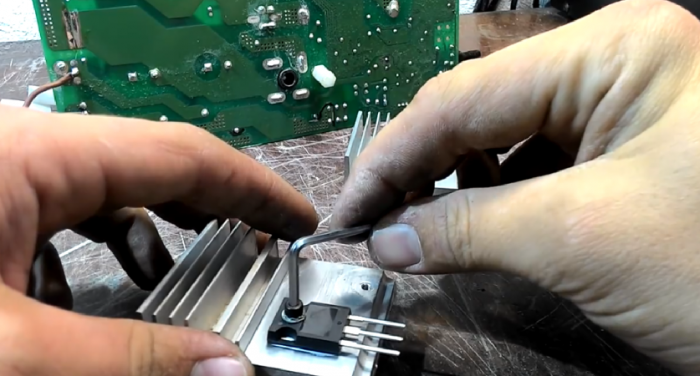
Заключение
Для этого подключаем к выводным контактам платы сварочного аппарата лампу на 40 Вт и включаем ее, если лампа загорелась вполнакала, значит, восстановление выходных цепей выполнено успешно. Чтобы удостовериться в полной работоспособности аппарата, к муфтам сварочных шлангов подключают реостат и тестером измеряют напряжение на выходных клеммах. Если поворотом ручки напряжение на клеммах муфты плавно меняется от 60 В до 10 В, значит, аппарат полностью исправен, в противном случае нужно менять операционный усилитель в цепи регулировки.
bouw.ru
Устройство для регулирования сварочного тока
Использование: устройство предназначено для регулирования сварочного тока и может быть использовано в сварочном производстве различных предприятий. Сущность изобретения: устройство содержит источник питания, блок подачи команд и исполнительный блок, содержащий балластный реостат с коммутирующими элементами. Управление величиной тока обеспечивается пропускной способностью электролита в резервуаре, куда опущены электроды, подсоединенные у упомянутым коммутирующим элементам, а один электрод к сварочному кабелю. Величина тока регулируется площадью электродов, концентрацией раствора. Балластный реостат может составляться и набором автономных резервуаров с электродами. 2 з. п. ф-лы, 1 ил.
Изобретение относится к электродуговой сварке, в частности для регулирования постоянного сварочного тока.
Известно устройство для регулирования сварочного тока, выполненное регулируемым балластным реостатом РБ-301. Регулированием тока обеспечивается поглощением части на сопротивление и превращением электрической энергии в тепловую. Прежде всего здесь нерационально используется электроэнергия, значительные затраты на изготовление, недолговечность, т.п. обуславливают нецелесообразность использования этого традиционного устройства в современных условиях. Известно устройство для регулирования сварочного тока, содержащее тиристор-прерыватель, дроссель, коммутирующие ячейки и блоки управления. Регулирование тока обеспечивается прерывностью, паузами. Но наличие пауз приводит к снижению качества сварного соединения, в связи с чем использование описанного устройства ограничено. Известно устройство для дистанционного регулирования величины сварочного тока, содержащее источник сварочного тока, переносной блок подачи команд и исполнительный блок, содержащий балластный реостат с коммутирующими элементами. Регулирование тока обеспечивается путем включения-отключения ступеней балластного реостата, что, как и в первом случае, нерационально в условиях жесткой экономии электроэнергии и ее высокой стоимости. Цель изобретения исключить нерациональный расход электроэнергии, одновременно снизив стоимость и обеспечив необходимое качество питания, надежность устройства. Достигается это тем, что в устройстве для регулирования сварочного тока, содержащем источник сварочного тока, блок подачи команд и исполнительный блок, содержащий балластный реостат с коммутирующими элементами, балластный реостат представляет собой резервуар с электропроводной жидкостью (в дальнейшем электролит) с помещенными в нее электродами, соединенными с коммутирующими элементами, другой выход которых подключен к источнику питания, при этом к одному электроду подключен сварочный кабель. В предпочтительном варианте электроды, подсоединенные к коммутирующим элементам, выполнены с регулируемой площадью поверхности, погруженной в электролит, например, с увеличивающейся площадью каждого электрода, с регулированием величины погруженной поверхности, перемещением электрода и т.п. Таким образом, известное решение усовершенствовано путем замены блока балластных реостатов, потребляющих электроэнергию, на проводник, меняющий свою электропроводность. Между отличительными признаками и достигаемым техническим результатом имеется следующая причинно-следственная связь. Особенностью предложения является то, что регулирование сварочного тока осуществляется путем изменения электропроводности электролита и площади погруженных в нее электродов. Для проявления этого нового качества необходима следующая совокупность существенных отличительных признаков: наличие резервуара с электролитом и электродами; соединение каждого электрода с коммутирующими элементами, другой выход которых подключен к источнику питания, при этом к одному электроду подключен сварочный кабель. Исключение из приведенной совокупности отличительных признаков хотя бы одного (любого) признака не обеспечивает получение нового качества регулирования сварочного тока при помощи электролита. В предпочтительном варианте предложения площади поверхностей электродов, погружаемых в электролит, выполнены регулируемыми, что расширяет диапазон регулирования, повышает его оперативность и плавность. Описанное новое качество проявляется в техническом эффекте устраняются потери электроэнергии, одновременно обеспечивается требуемое качество питания, удешевление изготовления, надежность работы. Заявляемое решение неизвестно из уровня техники и поэтому оно является новым. Выполнение балластика в виде резервуара с электролитом и погруженными в нее электродами неочевидно для специалистов отрасли, не следует явным образом из уровня техники, в связи с чем можно сделать вывод о соответствии рассматриваемого решения уровню изобретения. Заявляемое решение промышленно применимо, т.к. оно предназначено для использования в промышленности, содержит элементы, изготавливаемые промышленностью. Таким образом, заявляемое решение ново, имеет изобретательский уровень; промышленно применимо, т.е. соответствует критериям изобретения и на этом основании ему может быть представлена правовая охрана. На чертеже изображена схема предлагаемого устройства. Устройство содержит блок подачи команд из выключателей 1.5, который при необходимости может быть выполнен дистанционным, и исполнительный блок из электронной схемы, представляющей собой набор автономных коммутационных элементов из тиристоров 6.10, в цепь управления которыми включены упомянутые выключатели 1.5, и последовательно герконы 11.15. Аноды тиристоров 6.10 подключены к источнику питания, а катоды к электродам 16.20, погруженным в электролит 21, заключенный в резервуаре 22, представляющим собой проводник заданной проводимости между упомянутыми электродами 16.20 и электродам 23, подсоединенным к сварочному кабелю 24. Рассмотренный резервуар 22 с электродами 16.20 может быть выполнен в виде автономных емкостей с автономными, описанными выше коммутационными элементами (на чертеже не показано). Для повышения надежности работы герконы 11.15 размещаются возле токоведущей шины, при этом, для усиления магнитного поля шины на участке между тиристорами 6.10 и электродами выполнен петлей. Для повышения оперативности и плавности регулирования тока электроды 16.20 выполнены с возможностью регулирования площадей поверхностей, контактирующих с электролитом, например, конусообразными, с регулируемой величиной погружения, например, винтовым приводом, т.п. Устройство работает следующим образом. На вход устройства подключается кабель от источника питания, а на его выход сварочный кабель 24. Сварщик набирает необходимый ему ток, включая тот или иной из выключателей 1.5 или их группу, тем самым подготавливая количество коммутирующих элементов-тиристоров 6.10 к работе. Замыкая сварочный электрод на массу свариваемого изделия, к закрытым тиристорам 6.10 подается напряжение по цепи: источник питания, аноды тиристоров 6. 10, катоды тиристоров 6.10, электроды 16.20, электрод 23, сварочный кабель 24, сварочный электрод, масса, источник питания. Тиристоры 6.10, у которых будут включены выключатели 1.5 откроются, пропуская через себя ток, определяемый площадь электродов 16.20 и проводимостью электролита. При прохождении тока через тиристоры 6.10, магнитное поле петли шины мгновенно включит герконы 11.15, т.е. их н.з. контакты разомкнутся и отключат цепь управления тиристоров 6.10, которые останутся в открытом состоянии. При необходимости изменить величину тока сварщик дополнительно включает (выключает) бездействующие выключатели. Если они все включены, то дополнительное увеличение тока достигается увеличением поверхности электродов 16. 20, опускаемых в электролит 21. И, наконец, еще одной возможностью изменить силу тока является изменение проводимости электролита, с увеличением которой увеличивается пропускная способность балластика, сила тока. Таким образом, в основу предложенного решения положено использование свойства диэлектрической жидкости превращаться в проводник. Жидкость, насыщенная электронами, становится проводником и пропускает определенный ток, величина которого обусловлена ее электропроводностью. Благодаря предложенному устройству регулирования сварочного тока: от источника питания потребляется ток величиной, необходимой для сварочного процесса, иными словами, величина потребляемого тока и сварочного почти одинакова, т.к. потери при прохождении через электролит незначительны (аналогично работе транзистора). Именно этот эффект создает экономию электроэнергии; достигается исключение дорогостоящих материалов, используемых при изготовлении существующих балластных реостатов. Использование в качестве проводника электропроводной жидкости, например воды с добавлением соды, делает это устройство простым в изготовлении, удобным в эксплуатации, дешевым, общедоступным.РИСУНКИ
Рисунок 1www.findpatent.ru
Расчет универсальной нагрузки для диагностики сварочных аппаратов
Техника измерений
Главная Статьи, аналитика
Техника измерений
Появление малогабаритных сварочных аппаратов(СА)инверторного типа значительно расширило парк СА. Увеличилось и количество обращений в ремонтные мастерские, связанные с ремонтом сварочных аппаратов. После ремонта любой сварочный аппарат требует испытания на соответствие своим техническим параметрам, заявленным в паспорте. К таким параметрам, прежде всего, относятся:
- напряжение холостого хода;
- минимальный сварочный ток;
- максимальный сварочный ток;
- продолжительность нагрузки ПН%;
Для определения последних трех параметров требуется мощная универсальная нагрузка, позволяющая имитировать работу СА на электрическую дугу. В качестве такой нагрузки зачастую используется балластный реостат типа РБ-315 (1) или генератор статической нагрузки фирмы TEL-WIN (2). Как известно из теории и практики электродуговой сварки (3), напряжение дуги при ручной сварке покрытыми электродами определяется формулой:
Ud = 20+0,04xld
где Ud - напряжение на дуге в Вольтах, Id - ток дуги в Амперах;
В соответствии с этой формулой составляется таблица зависимости напряжений Ud от тока ld. Ручкой регулировки тока на СА выставляют требуемую минимальную или максимальную величину тока. Диагностируемый СА нагружают на балластный реостат, который с помощью имеющихся у него переключателей позволяет задавать различные сопротивления нагрузки. С помощью переключателей балластного реостата подбирают такое сопротивление нагрузки, при котором измеряемое напряжение на выходе СА и измеряемый ток нагрузки соответствовали бы имеющимся табличным значениям сварочной дуги. Таким способом можно определить реальный ток на выходе испытуемого СА. Этот процесс измерения сварочного тока требует определенных трудозатрат, так как подобрать сразу необходимое сопротивление балластного реостата, как правило, не удается.
Для упрощения процесса измерения параметров СА автор предлагает следующий универсальный имитатор нагрузки для сварочных аппаратов (далее - ИНСА).
ИНСА представляет активную нагрузку, состоящую из проволочной спирали R сопротивлением 0,04 Ом, включенной последовательно со стабилизатором напряжения (J1 20 В.
Рис. 1 Эквивалентная схема ИНСА
Как видно из эквивалентной схемы (рис.1), напряжение Ud, приложенное к зажимам этой схемы, будет соответствовать вышеприведенной формуле при произвольных значениях тока ld. Таким образом имитатор нагрузки СА будет являться эквивалентом сварочной дуги и с его помощью можно имитировать сварочный процесс без получения электродугового разряда с температурой 5000...7000 °С и без необходимости использовать все сварочные аксессуары (защитная маска, электрод, электрододержатель).
Максимально допустимый ток стабилизатора напряжения U1 должен быть не менее максимального тока диагностируемых СА .
Рис.2. Функциональная схема ИНСА
На рис. 2 показана функциональная схема предлагаемогоимитатора нагрузки, рассчитанного на максимальный ток 300 А.
Выходные кабели испытуемого СА подключаются к зажимам IN1, IN2 имитатора нагрузки. Напряжение с выхода СА подается на диодный мост VD1 и на схему выделения напряжения А1. Диодный мост VD1, рассчитанный на максимальный ток диагностируемых сварочных аппаратов, необходим для того, чтобы имитатор нагрузки можно было использовать для испытаний СА постоянного и переменного токов. На выходе схемы выделения напряжения А1 вырабатывается напряжение 2Uvd, равное напряжению падения на двух диодах выпрямительного моста VD1. Это напряжение поступает на вход сумматора АЗ и вычитается из опорного напряжения 20 В, поступающего на второй вход сумматора. С выхода сумматора АЗ напряжение, равное (20-2Uvd), поступает на инверсный вход стабилизатора напряжения U1 (обведен пунктиром). Стабилизатор работает с последовательно включенным резистором R2. Принцип работы стабилизатора напряжения U1 аналогичен работе микросхемы TL431 - трехвыводного регулируемого параллельного стабилизатора [4]. На прямой вход стабилизатора поступает напряжение с преобразователя А2, который преобразует действующее (среднеквадратичное)значение напряжения, снимаемого с точки соединения проволочных резисторов R1 (0,04 Ом) и R2, в постоянное напряжение [5]. Посредством операционного усилителя DA1, силового транзистора VT1 и проволочного резистора R2 в точке соединения резисторов R1 и R2 поддерживается стабилизированное напряжение, равное величине (20-2Uvd) В. Номинал резистора R2 определяется максимальным значением тока ld_max из выражения: ld_max=(20-2Uvd)/(R2+Rsd), где Rsd - сопротивление открытого состояния силового MOSFET-транзистора VT1. Для ld_max=300 А значение R2=0,05 Ом.
Резистор R0 используется в качестве шунта для измерения величины тока ld. При токе величиной 300 А падение напряжения на нем равно 75 мВ. Напряжение с этого шунта подается на схему выделения действующего значения тока А4 и, далее, на регистратор тока А. Входное напряжение Ud на входе ИНСА определяется по формуле:
Ud=2Uvd+ldx0,04+(20-2Uvd)+ldxR0 = 20+ldx0,04+ldxR0
Поскольку величина падения напряжения на резисторе R0 не превышает 75 мВ, то последним слагаемым ldxR0 можно пренебречь. Таким образом, получаем:
Ud= 20+Idх0,04
То есть, напряжение Ud на входе имитатора нагрузки будет соответствовать необходимому напряжению дуги при ручной сварке.
Кроме этих узлов функциональная схема имеет блок питания А5 (DC/DC-преобразователь), формирующий напряжение питания и опорное напряжение вышеперечисленных узлов, и вентилятор FEN для охлаждения диодного моста VD1 и транзистора VT1. Таким образом, вышеописанный ИНСА будет представлять из себя конструкцию, на передней панели которой размещаются амперметр (регистратор тока) и две клеммы для подключения кабелей от диагностируемого СА. Подключение к внешнему источнику питания ИНСА не требуется - все электронные узлы, включая вентилятор охлаждения, питаются от диагностируемого сварочного аппарата. Измерение выходного тока СА будет предельно просто - нужно подключить сварочные кабели к клеммам имитатора и снять показания регистратора тока.
Основной вопрос при разработке данного имитатора - это правильное определение теплового режима элементов конструкции. Для этого в первую очередь необходимо определить максимальную мощность, выделяемую на диодном мосте VD1 и силовом транзисторе VT1.
Мощность, выделяемая на диодном мосте VD1, вычисляется по формуле:
Pvd=2xIdxUvd
Максимальная мощность будет выделяться при максимальном токе Id_max.
Для ld_mах=300 А И Uvd= 1,5 В (падение напряжения на одном диоде) получим Pvd_max=900 Вт.
При условии, что ток, потребляемый блоком питания А5, много меньше тока ld, мощность, выделяемая на силовом транзисторе VT1, равна
Pvt=ldXUvt=ldX(20-2Uvd-ldxR2)
Максимальная мощность Рvt_max будет выделяться при токе ld=(20-2Uvd)/2R2=17/0,1 = 170 А и составит Рvt_mах=170х(20-2х1,5 -170x0,05)= 1445 Вт. Исходя из этих значений мощностей: Pvd_max=900BT И Pvt_max=1445 Вт Необходимо рассчитывать эффективную площадь радиатора охлаждения, на котором будут устанавливаться диоды моста VD1 и силовой транзистор VT1.
Можно отказаться от диодного моста VD1 и заменить его вторым стабилизатором напряжения U2 противоположной полярности, включенным последовательно со стабилизатором U1, как показано на рис. 3.
Рис. 3. Функциональная схема ИНСА без диодного моста
Когда напряжение, поступающее из сварочного аппарата, имеет полярность "плюс" на клемме IN1 и "минус" на клемме IN2, то работает стабилизатор U1. Второй стабилизатор блокируется диодом VD2, являющимся составной частью силового транзисторного модуля VT2. При противоположной полярности приложенного напряжения ("плюс" на клемме IN2, а "минус" на клемме IN 1) работает второй (верхний на рис. 3) стабилизатор напряжения U2, а стабилизатор U1 блокируется диодом VD1. При такой функциональной схеме количество тепла, выделяемое на активных элементах схемы при ld_mах=300 А, уменьшается, поскольку в каждый полу-период тепло выделяется только на одном диоде транзисторного модуля, а не на двух диодах моста, как имело место в первой функциональной схеме с диодным мостом. Однако, максимальная мощность Pvt_max, выделяемая на силовом MOSFET-транзисторе, будет больше, чем в схеме с диодным мостом.
Если же заменить линейный стабилизатор напряжения импульсным, то можно существенно снизить рассеиваемую мощность на силовом MOSFET-транзисторе, поскольку он будет работать в ключевом режиме.
В настоящее время автором отрабатывается схема конструкции вышеописанного универсального имитатора нагрузки сварочного аппарата.
Литература
1. В.Я. Володин. Как отремонтировать сварочные аппараты своими руками. Наука и Техника,Санкт-Петербург, 2011, стр. 33, 291-293.
2. http://valvolodin.narod.ru/schems/Tecnica_141-161.pdf. Инструкция по ремонту инверторного сварочного аппарата Tecnica 141-161, стр. 10 Static load generator
3. ГОСТ Р МЭК 60974-1-2004, п. 11.2.1.
4. Микросхемы для линейных источников питания и их применение. ДОДЭКА, изд. второе, 1998 г., стр. 219.
5. Пейтон, Волш. Аналоговая электроника на операционных усилителях. БИНОМ, Москва,
1994, стр. 326.
Автор: Александр Бегиев ( г. Волжский, Волгоградская обл.)
Дата публикации: 04.02.2014
Мнения читателей- Kabayan / 28.06.2015 - 14:10Super inoramftive writing; keep it up.
- Avo / 10.08.2014 - 07:33Всё уже давно умными людьми написано. Многократно печаталось и "сдиралось"перепечатав. Но как у многих руки росли из мест на чём сидят , так всё и продолжается... К сожалению. Может даже и хуже ! Настоящие специалисты как всегда "на вес золота " !
- боря / 25.07.2014 - 22:00хорошими руками и головой сварщику не до того, ему работы всегда сильно много. на игрушки в рабочее время его не хватает. причём люди они технически продвинутые , это я без трёпа постоянно общаюсь с ними в обычной жизни и по работе.
- Сергей / 09.05.2014 - 06:35Человек даже с небольшим опытом, сразу определит качество сварочного аппарата . Проблема в том, что все больше человеков у которых руки из места на котором сидят ростут .
Вы можете оставить свой комментарий, мнение или вопрос по приведенному вышематериалу:
www.radioradar.net