Подводная сварка: особенности и трудности. Электроды для сварки в воде
Электроды для сварки под водой
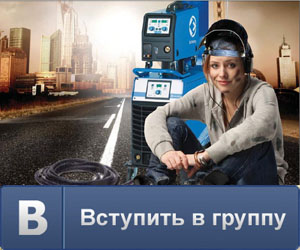
В наше время сварка под водой используется все чаше. Такой вид сварки требуется для ремонт морского и речного транспорта, строительных работах (строительство мостов, дорог и т. д.) и гидротехнических работах. В основном для сварки используются электроды с большим слоем покрытия, иначе сваривание под водой не получится. Вес покрытия у электродов для сваривания под водой составляет 130-170% от массы стержня.
Как вообще происходит сваривание под водой? Вот как: покрытия электродов образуют козырек, под которым дуга может спокойно гореть, при этом вытесняя воду под немалым давлением газов дуги. В основном электроды для сварки под водой имеют покрытие из парафина или лака целлулоида, который растворен в ацетоне. После высыхания первого слоя лака, его наносят еще в два слоя.
Парафинирование электродов таких видов происходит с помощью погружения стержней в расплавленный парафин. Если покрытие электрода создано вышеприведенным способом, то толщина покрытия для 4 миллиметрового стержня составит 0,8 мм, для 5 мм. – 1 мм., и для 6 мм – 1,2 мм.
Второй способ сваривания под водой – это создание наземных условий под водой. Как они создаются? Выбирается необходимый объект сваривания, над которым создается камера, из которой откачана вода. Далее сваривание металлических частей происходит также как и на поверхности Земли. Однако этот способ имеет большой недостаток. На создание камеры и откачку воды уходит много времени, сил, а главное средств. Такой способ сваривания под водой применяется крайне редко из-за своей дороговизны.
Практически всегда для сварки под водой применяются такие виды электродов: ЦМ-7С, АНО-1 и ОЗС-3. Эти виды электродов соответствуют всем требованиям техники безопасности, и Вы можете их легко заказать через страницу «Контакты».
Также для сварки под водой требуется постоянный ток с прямой полярностью, потому что только в этом случае дуга будет прекрасно гореть под водой. Для сварки под водой используются электроды с диаметром от 4 до 6 мм. Для сварки такими электродами применяется напряжение в 220, 300 и 340 соответственно. Еще для сварки под водой есть такие российские электроды как МГМ-50К. Ими можно проводить сварку как в помещениях с повышенной влажностью, так и под водой. Он очень удобен тем, что перед свариванием металл не требует очистки от ржавчины или других загрязнений. Однако если Вы живете в своем доме, то сварка под водой Вам, скорее всего не понадобится. Но если у Вас строительная компания, то электроды для сварки под водой Вам обязательно понадобятся.
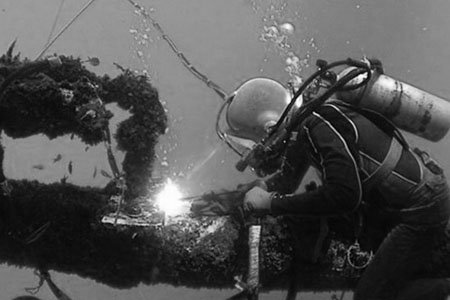
Однако для сварки под водой Вам потребуется на только качественные электроды, но прекрасный сварщик с большим опытом сваривания, как на Земле, так и под водой. Технологии идут вперед, и сваривание под водой становится очень актуальным в наше время. За границей в основном используются сварочные крепежи под водой. Если уже сейчас за границей сварка под водой так популярна, так может быть Вам нужно уже сейчас запасаться электродами для сварки под водой?
elektrod-3g.ru
марки материалов для сварочных работ под водой
Главная страница » Электроды для подводной сварки и резки
На этой странице показана информация по теме "Электроды для подводной сварки и резки" и всему, что с ней связано. Смотрите далее информацию по данному вопросу, а внизу страницы подобраны марки электродов с этой меткой на сайте.
Где купить электроды для сварки под водой
Одним из методов соединения изделий из металлов и сплавов, проводящегося в жидкой среде, является подводная сварка. Данная технология сваривания может иметь четыре формы в зависимости от места проведения:
- сухая камера;
- мокрая сварка, которая также делится на два вида: полуавтоматическая и дуговая ручная;
- сухой бокс, имеющий функцию передвижения под водой;
- специальная рабочая камера.
Наибольшей популярностью пользуются первые два метода.
Применяемые электроды
Состав материалов для проведения подводных сварочных работ во многом схож со структурой аналогичных расходников, использующихся на суше. Основные особенности:
- электроды для сварки в воде имеют более толстое покрытие;
- состав обмазки имеет дополнительные элементы, создающие защитный слой от влаги и не позволяющие покрытию раскисать в воде: целлулоидный лак, смолы и парафин.
Немногие производители смогут предложить клиентам электроды для сварки под водой. Наиболее известной торговой маркой является продукция американской компании Broco (на картинке). Также на рынке присутствуют следующие марки:
- ЦМ-7С.
- АНО-1.
- ОЗС-3.
- МГМ-50К.
- ЭПС-5.
- ЭПС-52.
Какой подводный электрод является лучшим, каждый исполнитель решит самостоятельно.
Где купить электроды для сварки под водой
Где купить электроды различных марок
Выбирайте производителей и продавцов сварочных электродов, перейдя по ссылке ниже на страницу нашего каталога фирм.Выбрать компанию
weldelec.com
технические характеристики, электроды для сварки в воде
Электроды сварочные МГМ-50К выпускаются в соответствии с ГОСТом 9467 Э50А, ГОСТ 9666 и являются аналогом электродов выпускаемых швейцарской фирмой "ОЭРЛИКОН". Электроды имеют рутиловое покрытие и предназначены для сварки особо ответственных конструкций из углеродистых, низколегированных сталей c повышенной прочностью. При сварке разбрызгивание металла незначительно, обеспечивается устойчивое горение дуги, формирование шва во всех пространственных положениях хорошее с легким отделением шлака. При этом металл сварного шва отвечает всем требованиям по плaстичности и ударной вязкости. Сварка может производиться во всех положениях, за исключением вeртикального положения "сверху-вниз".
Сварочные электроды марки МГМ-50К это первые в России электроды обладающие способностью производить сварку в условиях повышенной влажности - электроды для сварки в воде. Свариваемые поверхности не требуют предварительной очистки от ржавчины, масла, загрязнений, что позволяет использовать их для устранения сквозных повреждений трубопровода, нaхoдя щегося под oстаточным давлением воды мощностью до одной атмосферы. Газовый пузырь возникающий вокруг дуги оттесняет воду и создает необходимые условия для сварки. Эти электроды незаменимы при ремонтных работах на водопроводных и теплосетях.
Непосредственно перед работой электроды требуют прокалки в течение 1 часа при температуре 100-110°С. Электроды МГМ-50К выпускаются диаметром 2, 2.5, 3, 3.25, 4 и 5 мм. Картонные пачки по 4 кг и 5 кг герметично заклеиваются полиэтиленовой пленкой. Палеты формируются массой 1000 кг и упаковываются стрейч-пленкой.
Транспортировка разрешается любым видом закрытого транспорта.
Химический состав наплавленного металла, % |
||||
Углерод |
Кремний |
Марганец |
Сера |
Фосфор |
Не более |
||||
не более 0,11 |
0,15-0,45 |
0,5-0,8 |
0,020 |
0,030 |
Механические свойства металла шва, не менее |
||
Временное сопротивление разрыву Н/мм2 (кгс/мм2) |
Относительное удлинение, % |
Ударная вязкость ан, Дж/см2, (кгсм/см2) |
500-610 (50-61) |
22 |
100 (10,2) |
Геометрические размеры электродов и сила тока при сварке в зависимости от положения свариваемого шва |
||||
Диаметр, мм |
Длина, мм |
Рекомендуемый ток, А |
||
нижнее |
вертикальное снизу-вверх |
потолочное |
||
2,0 |
300 |
50-70 |
50-70 |
50-80 |
2,5 |
350 |
70-100 |
60-90 |
80-100 |
3,0 |
350 |
80-120 |
70-100 |
70-100 |
3,25 |
350 |
100-140 |
90-130 |
100-140 |
4,0 |
450 |
140-190 |
130-140 |
140-170 |
5,0 |
450 |
190-240 |
160-200 |
- |
www.metizniki.ru
Подводная сварка: особенности и трудности | сварочные электроды - саморезы - гвозди - сетка рабица
Теоретическое обоснование возможности горения дуги под водой появились ещё в конце позапрошлого века, а в 1932 году советский инженер К.К. Хренов продемонстрировал, как выглядит подводная сварка практически.
Непосвящённым сварка под водой кажется чем-то парадоксальным и противоречащим законам физики, однако именно эти законы и делают такую сварку возможной: интенсивное испарение воды и выделение газов образуют пузырь, внутри которого и горит дуга.
Разумеется, подводная сварка выдвигает особые требования к изоляции: вода, а морская вода в особенности, является прекрасным проводником, и во избежание потерь электричества все подводящие провода должны быть изолированы с особой тщательностью. Того же требуют и правила техники безопасности. Электроды для сварки так же должны быть изолированы от воздействия воды. Остановимся на сварочных электродах подробнее.
Сварка под водой — электроды
Для дуговой сварки под водой применяются сварочные электроды диаметром 4-6 мм. Для подводной сварки хорошо подходят сварочные электроды с ферросплавами, улучшающими качество шва. Электроды для сварки под водой должны быть изолированы, для чего электроды пропитывают парафином, нитролаком, раствором смол и другими веществами. Изготавливают электроды для сварки под водой преимущественно из стали. Замена отработанных сварочных электродов в держателе возможна лишь при отключенном токе.
Стальной стержень сварочного электрода плавится быстрее, чем охлаждаемое водой покрытие. На электроде образуется своеобразный козырёк, внутри которого спрятан стержень. Благодаря этому козырьку электроды способствуют образованию устойчивого пузыря и горению дуги.
Сварка под водой — человек
Подводная сварка возможна практически на любых глубинах. Оборудование и сварочные электроды будут работать под слоем воды любой толщины. Глубина ограничивается лишь особенностями человеческого организма и конструкцией снаряжения.
Громоздкое водолазное снаряжение весьма затрудняет сварочные работы под водой. Неудобство усиливается плохой видимостью и неустойчивостью водолаза. Любое резкое движение или поток течения постоянно меняют положение работающего водолаза. К примеру, при сварке стыковых швов сварочные электроды легко теряют направление и уводят дугу в сторону.
В силу этих причин наиболее удобными при подводной сварке оказываются соединение внахлёст и тавровое соединение, когда кромки шва служат направляющими для сварочного электрода.
Здесь не обойтись без строгого выполнения правил техники безопасности. Запрещена работа с использованием автономных дыхательных аппаратов. Запрещено использование переменного тока. К подводным сварочным работам допускаются только опытные, квалифицированные водолазы.
В морской воде дуга возникает между сварочным электродом и любым металлическим предметом, даже без касания электрода, поэтому нельзя направлять электрод в сторону шлема или водолазного снаряжения.
Подъём водолаза с глубины проводится медленно, с остановками для стабилизации давления. В противном случае высок риск проявлений кессонной болезни. На глубине свыше 50 метров нормальная продолжительность работы не более 15 минут, а время подъёма в несколько раз превышает время работы. Получается, что нормальная работа водолаза-сварщика попросту невозможна при глубинах более 30-40 м.
Очевидно, что для работы на больших глубинах требуется использование автоматических сварочных установок, применение которых освободит человека от работы в тяжёлых условиях.
www.woshod-metiz.ru
Дуговая сварка под водой | Строительный справочник | материалы - конструкции
Впервые в мировой практике подводную дуговую резку угольным электродом в лабораторных условиях осуществили в 1887 г. Н.Н. Бенардос и проф.Д.А. Лачинов. Продолжения эти работы не получили.
Только в начале 30-х гг. ХХ в. были возобновлены работы по применению сварки под водой. В 1932 г. К. К. Хренов разработал электроды для подводной сварки и провел натурные испытания их в Черном море. В середине 30-х гг. ручная дуговая сварка под водой была применена для ряда работ, например ремонта парохода «Уссури» и подъема парохода «Борис». Однако в те годы подводная сварка применялась эпизодически.
Только в годы войны возникла насущная потребность в подводной сварке и резке при ремонте кораблей, мостов, при аварийных и спасательных работах. К.К. Хренов продолжил исследования и разработку техники сварки и резки под водой в специальной лаборатории, организованной в марте 1942 г. при Московском электромеханическом институте инженеров железнодорожного транспорта. В результате были созданы электродные покрытия, обеспечивающие стабильное горение дуги под водой. Результаты всесторонних исследований свойств и состава метала швов, сваренных под водой, показали возможность применения сварки для ремонта подводных частей корпусов кораблей прямо на плаву. По примеру нашей страны сварку и резку под водой начали применять и другие воюющие страны.
В послевоенные годы значительно расширились области применения и объемы подводной сварки. Строительство морских нефтепромысловых гидротехнических сооружений, подводных трубопроводов различного назначения, ремонт судов на плаву, восстановление шлюзовых затворов портовых сооружений и других объектов оказались немыслимыми без применения подводной сварки. Однако обеспечить прочноплотные швы и высокую производительность труда существовавшие тогда способы подводной сварки не могли. Кроме того, для выполнения подводной сварки по «мокрому» методу требовались водолазы-сварщики высокой квалификации. «Мокрый» метод — процесс, осуществляющийся без удаления воды из зоны сварки. В то же время ручная подводная сварка обладала исключительной маневренностью и простотой оборудования, а для ее осуществления не требовались специальные приспособления для удаления воды из зоны сварки, что обуславливало низкую стоимость работ. Попытки улучшить механические свойства сварных соединений и механизировать процесс в конце 50-х гг. ХХ века не увенчались успехом.
В эти годы за рубежом разрабатывается «сухой» способ подводной сварки. Способ основан на применении специальных обитаемых камер различной конструкции. Камеры могут быть различного размера и конструкции:
— большие глубоководные, когда и место сварки и сварщик изолированы от водной среды за счет подачи воздуха в камеру и оттеснения воды за ее пределы;
— водолазные колокола, обеспечивающие выполнение сварки в «сухой» среде, хотя сам сварщик находится по пояс в воде;
— портативный сухой бокс, который обеспечивает «сухую» среду только в зоне сварки.
Применение каждого варианта показало, что сварные швы получаются такого же качества, как и на суше, но имеются и существенные недостатки, которые не привели к широкому распространению «сухой» подводной сварки.
При применении глубоководных камер, как показала практика, необходимы предварительная подготовка и специальное техническое сопровождение. Оказалось, что необходимо разработать и изготовить камеру нужной конструкции, подготовить технические средства (плавучие краны, насосы и другое оборудование), задействовать обслуживающий персонал. Такой вариант выполнения подводной сварки оказался достаточно дорогостоящим.
Два других варианта оказались менее дорогостоящими, но и менее маневренными и универсальными, чем «мокрый» способ подводной сварки. В 1965 г. в нашей стране были начаты исследования, позволившие устранить недостатки «мокрого» способа.
Анализ подводной сварки «мокрым» способом показал, что основными причинами низких механических характеристик сварных швов являются пористость за счет растворения водорода, шлаковые включения за счет окисления компонентов металла кислородом, увеличение скорости охлаждения за счет контакта нагретого металла с водой. Низкая производительность подводной сварки не может быть преодолена при использовании покрытых электродов, так как смена их через каждые 1–2 минуты является в подводных условиях сложной операцией, а козырек обмазки ухудшает наблюдение за формированием шва.
Проведенные работы показали, что наиболее перспективной является полуавтоматическая сварка. Метод достаточно маневренный и универсальный, а механизированная подача проволоки позволяет длительное время вести процесс сварки без перерывов. Поскольку проволока имеет меньший диаметр, чем электрод, и не имеет покрытия, создаются благоприятные условия для наблюдения за формированием сварного шва.
Применение сплошной проволоки без защиты зоны сварки и с подачей защитных газов (аргон, углекислый газ) не обеспечили получение необходимых механических свойств сварных соединений. Дальнейшие исследования показали, что эффективная защита зоны сварки возможна при использовании порошковых самозащитных проволок. Разработанная в Институте электросварки им. Е.О. Патона порошковая проволока марки ППС-АН1 диаметром 1,2—2,0 мм впервые позволила провести подводную сварку «мокрым» способом с получением качественных сварных соединений. При современном уровне техники дуговая сварка порошковой проволокой «мокрым» способом осуществляется на глубине до 30 м. Существуют серьезные ограничения по номенклатуре металлов, пригодных для сварки таким способом. С увеличением глубины резко изменяются свойства дуги, интенсифицируется взаимодействие расплавленного металла с окружающей средой и становится проблематичным получение качественного соединения. Кроме того, следует учитывать, что «мокрый» способ подходит для глубины, доступной для человека в скафандре — не более 120—160 м.
Разработка специального оборудования для подводной полуавтоматической сварки также потребовала решения ряда сложных задач, которые были успешно завершены созданием полуавтомата для подводной сварки А1660.
Механизированная подводная сварка применяется для строительства и ремонта металлоконструкций различного назначения. Проводятся работы по дальнейшей механизации и автоматизации процесса подводной сварки. Разрабатываются автоматы, которые смогут осуществлять сварку под водой с минимальным участием человека. Совершенствуются системы дистанционного наблюдения и управления процессом.
Не исключена возможность применения в указанных условиях контактной стыковой сварки оплавлением. Предварительные эксперименты и опытно-промышленная проверка разработанной в ИЭС им. Е.О. Патона установки для автоматической стыковой сварки оплавлением труб под водой при строительстве и ремонте морских трубопроводов подтвердили перспективность использования этого способа сварки.
Очевидно, что в ближайшем будущем необходимо будет совершенствовать как «мокрый», так и «сухой» способы сварки, а также разрабатывать новые механизированные способы сварки и оборудование, пригодные для использования на километровой глубине.
Использованы иллюстрации http://welding.su/gallery/
Технология дуговой сварки и резки под водой
В жидких средах, в том числе и в воде, можно получить достаточно устойчивый дуговой разряд, который, образуя высокую температуру и имея большую удельную тепловую мощность, испаряет и разлагает окружающую жидкость. Пары и газы, образующиеся при дуговом разряде, создают вокруг сварочной дуги газовую защиту в форме газового пузыря, т. е. в сущности дуга горит не в воде, а в газовой среде. Газ состоит в основном из водорода, образующегося при термической диссоциации водяного пара, а образующийся при диссоциации кислород окисляет материал электродов.
Устойчивая сварочная дуга при использовании обычных источников питания сварочной дуги может быть получена при применении угольных или металлических электродов.
Электроды, применяемые для подводной резки, должны иметь толстое водонепроницаемое покрытие, которое охлаждается снаружи водой и поэтому плавится медленнее стержня электрода, образуя в конце электрода «козырек». Образовавшийся козырек выступает вперед в форме небольшой чашечки и способствует устойчивому существованию газового пузыря и горению дуги.
Водопроницаемость покрытия отрицательно влияет на устойчивость горения дуги, так как вода, испаряющаяся у горячей поверхности электродного стержня, разрушает покрытие и срывает его кусками со стержня. Водонепроницаемость достигается в основном пропиткой покрытия парафином. В качестве покрытия применяют состав из смеси железного сурика (80%) и мела (20%) с добавлением для их связывания жидкого натриевого стекла. Нанесение покрытия производят окунанием. Электродным стержнем служит сварочная проволока Св-08 или Св-08ГС.
Величину тока подбирают из расчета 60 — 70 А на 1 мм диаметра электрода. Напряжение дуги под водой несколько больше, чем на воздухе. Резка под водой применяется при ремонте судов, устройстве различных гидросооружений и др.
build.novosibdom.ru
Электрод для подводной сварки
Изобретение может быть использовано для подводной ручной сварки малоуглеродистых и низколегированных сталей повышенной прочности, в частности при ремонте металлоконструкций ответственного назначения, в том числе трубопроводов, которые эксплуатируются в водной среде. Стальной стержень электрода легирован в основном никелем и хромом. Значение никелевого и хромового эквивалентов ограничены величинами 19...32% и 21...33% соответственно. Покрытие содержит компоненты в следующем соотношении, мас.%: флюорит 22,0-31,0, рутиловый концентрат 22,0-37,0, окись железа 15,0-31,0, полевой шпат 8,0-13,0, магнезит металлургический 4,0-9,0, ферросилиций 0,5-2,0, карбоксиметилцеллюлоза 1,5-2,0. Коэффициент массы покрытия составляет 22-25%. Электрод обеспечивает при сварке во всех пространственных положениях качественное формирование металла шва, стойкость сварных соединений против образования холодных трещин в зоне термического влияния низколегированных сталей повышенной прочности и получение показателей механических свойств металла шва на уровне свойств основного металла. 5 табл., 1 ил.
Изобретение относится к области дуговой сварки плавлением, в частности к разработке сварочных материалов для ручной подводной мокрой сварки малоуглеродистых и низколегированных сталей повышенной прочности. Может быть использовано в газовой и других областях промышленности.
Проблема сварки подводных металлоконструкций ответственного назначения на сегодняшний день не решена. Механические свойства сварных соединений, в первую очередь пластичность, не соответствуют уровню свойств основного металла. Кроме того, при сварке низколегированных сталей повышенной прочности в зоне термического влияния (ЗТВ) возникают холодные трещины, что делает невозможным эксплуатацию металлоконструкций ("Об оценке свариваемости низколегированных сталей с учетом быстрого охлаждения в условиях подводной сварки". Автомат. сварка, 1988, №12, с.48-50). Такой результат вызван двумя основными факторами, обусловленными наличием водной среды, - высокими скоростями охлаждения и высоким содержанием водорода. Для борьбы с холодными трещинами разработаны электроды, обеспечивающие получение металла шва аустенитного типа, обладающего высокими механическими свойствами и позволяющего избежать образования холодных трещин. Но шлаковая система покрытия таких электродов позволяет получать качественное формирование металла шва только в нижнем положении. При сварке на вертикальной плоскости и особенно в потолочном положении сварочно-технологические свойства электродов ухудшаются, так как физические свойства шлака, образующегося при плавлении электродного покрытия, не создают надежной защиты расплавленного металла, не предупреждают его от стекания, а также образования подрезов и наплывов. Как результат, формирование наплавленного металла становится неудовлетворительным, механические свойства таких швов резко снижаются. В то же время большинство работ при ремонте подводных металлоконструкций (подводная часть корпуса судов, трубопроводы, вертикальные опоры платформ и стенки портовых сооружений) нужно выполнять именно в пространственных положениях, отличных от нижнего. Поэтому обеспечение возможности сварки во всех пространственных положениях - один из ключевых вопросов при создании электродных материалов, разработке или совершенствовании технологического процесса подводной сварки.
Известен электрод (Авторское свидетельство СССР №1540992 от 07.02.90, бюл.№5) со стержнем из высоколегированной проволоки Св.-07Х25Н12Г2Т, покрытие которого содержит (мас.%):
Мрамор | 10-14 |
Плавиковый шпат | 18-22 |
Полевой шпат | 2-4 |
Ферромарганец | 7-10 |
Ферротитан | 3-6 |
Ферросилиций | 3-6 |
Поташ | 0,5-1,5 |
Титановый порошок | 4,7-7,7 |
Двуокись титана | остальное |
Недостатком электрода с таким покрытием является слишком большое количество шлака, образующегося при его плавлении. Хотя это и обеспечивает надежную защиту металла сварочной ванны и шва от водной среды, но делает невозможным выполнение сварки в пространственных положениях, отличных от нижнего. Кроме того, вследствие недостаточного запаса аустенитности в металле шва близ линии сплавления возникают хрупкие прослойки, склонные к образованию холодных трещин.
Известен также электрод (Патент РФ №2071895, МПК В23К 35/365) со стержнем из высоколегированной проволоки Св.-10Х16Н25АМ6, покрытие которого содержит (мас.%):
Плавиковый шпат | 36-40 |
Кварцевый песок | 17-21 |
Ферромарганец | 8-12 |
Ферротитан | 4-6 |
Ферросилиций | 4-6 |
Поташ | 1-3 |
Окись хрома | 1-3 |
Двуокись титана | 9-29 |
При таком соотношении CaF2 и TiO2 перенос расплавленного металла имеет ярко выраженный крупнокапельный характер, который значительно ухудшает стабильность горения дуги. Высокое содержание SiO2 приводит к увеличению вязкости шлака, вследствие чего он не полностью укрывает наплавленный металл, формирование шва ухудшается, что делает невозможной сварку в пространственных положениях, отличных от нижнего. Это подтверждается результатами испытаний сварочно-технологических свойств, проведенных разработчиками электрода (Сварочное производство, №11, 2000 г.).
Оба эти электрода позволяют получить сварные соединения с уровнем механических свойств, который отвечает уровню свойств основного металла, и избежать образования холодных трещин в ЗТВ низколегированных сталей повышенной прочности. Но их сварочно-технологические свойства не удовлетворяют поставленным требованиям.
В качестве прототипа нами избран электрод (Авторское свидетельство СССР 1549706 от 15.03.90, бюл. №10), покрытие которого содержит (мас.%):
Мрамор | 14-16 |
Плавиковый шпат | 24-26 |
Полевой шпат | 3-5 |
Ферромарганец | 9-11 |
Ферротитан | 4-6 |
Ферросилиций | 4-6 |
Поташ | 0,5-1,5 |
Двуокись титана | остальное |
Стержнями электродов служит стальная высоколегированная проволока, которая содержит хром и никель в количестве не менее соответственно 13,5 и 22%.
По нашему опыту исследования шлаковых систем диапазон соотношений TiO2/CaF2, использованный в прототипе, не является оптимальным для качественного формирования сварных швов под водой, а введение в эту систему мрамора в количествах, которые превышают 10%, еще и ухудшает сварочно-технологические свойства электродного покрытия. Это не позволяет использовать их для качественной сварки во всех пространственных положениях. Кроме того, введение мрамора не оправданно из-за того, что некоторое (до 5%) уменьшение содержания водорода в наплавленном металле при разбавлении атмосферы дугового промежутка газообразными продуктами разложения мрамора практически не имеет значения из-за аустенитной структуры металла швов.
Задачей изобретения является обеспечение при сварке во всех пространственных положениях качественного формирования металла швов, стойкости сварных соединений против образования холодных трещин в ЗТВ низколегированных сталей повышенной прочности и показателей механических свойств металла швов на уровне свойств основного металла.
Поставленная задача решается тем, что электрод для подводной сварки, включающий стержень из высоколегированной стали и покрытие, содержащее рутиловый концентрат, полевой шпат, флюорит и ферросилиций, отличается от известных тем, что значения никелевого и хромового эквивалентов стержня ограничены следующими величинами: Niэкв. 19...32%, Crэкв. 21...33%, а покрытие содержит окись железа, магнезит металлургический и карбоксиметилцеллюлозу при следующем соотношении компонентов, мас.%:
флюорит | 22,0-31,0 |
рутиловый концентрат | 22,0-37,0 |
окись железа | 15,0- 31,0 |
полевой шпат | 8,0-13,0 |
магнезит металлургический | 4,0-9,0 |
ферросилиций | 0,5-2,0 |
карбоксиметилцеллюлоза | 1,5-2,0, |
при этом коэффициент массы покрытия составляет 22...25%.
Снижение температуры твердения шлака, его удлинение, а также увеличение угла смачивания основного метала расплавленным достигнуты путем введения в покрытие сбалансированного количества флюорита и окиси железа. Введение значительного количества фторидов обеспечивает снижение содержания водорода в металле шва, десульфацию расплавленного металла, высокую степень усвоения легкоокисляющихся элементов и вместе с полевым шпатом оказывает содействие образованию шлаковой корки, которая надежно защищает шов от окружающей среды, и получению хорошего формирования. Это техническое решение - результат тщательного исследования влияния компонентов тройной системы CaF2-TiO2-FeO на сварочно-технологические свойства электродов для подводной мокрой сварки. Использование в качестве стержня высоколегированной проволоки гарантирует получение металла шва аустенитного типа, благодаря которому исключается образование холодных трещин в ЗТВ низколегированных сталей повышенной прочности.
Сущность проведенных опытов иллюстрирует чертеж, где на концентрационном треугольнике качественно воспроизведен характер влияния соотношения ингредиентов системы CaF2-TiO2-FeO на сварочно-технологические свойства электродов. Здесь А - область оптимальных составов покрытия электродов для выполнения мокрой подводной сварки во всех пространственных положениях многопроходных стыковых швов.
Направление 1 - при таком изменении соотношений ингредиентов увеличивается склонность к образованию наплавленных валиков треугольной формы, образованию твердой керамической шлаковой корки со склонностью к заклиниванию при многослойной сварке стыковых соединений, увеличению коэффициента усиления швов, огрублению чешуйчатости, образованию дефектов в виде подрезов, шлаковых включений при сварке многопроходных швов.
Направление 2 - при таком изменении соотношений ингредиентов увеличивается склонность к образованию твердой керамической шлаковой корки, высоких неравномерных грубочешуйчатых, а в конце концов литых валиков округлой формы, ухудшается отделение шлаковой корки, появляются большие капли рядом со швом, возрастает напряжение дуги, режим становится неустойчивым.
Направление 3 - при таком изменении соотношений ингредиентов увеличивается склонность к образованию валиков с малым коэффициентом усиления, мелкочешуйчатой поверхностью и плавным переходом к поверхности основного металла или предварительно наплавленных валиков, перенос расплавленного металла приобретает мелкокапельный характер, наблюдается образование аморфноподобного шлакового покрытия наплавленных валиков, которое легко удаляется щеткой, возможность качественной сварки в пространственных положениях, отличных от нижнего, ограничивается.
Таким образом границы содержания флюорита, рутилового концентрата и окиси железа, а также их соотношение в покрытии электрода, который предлагается в качестве изобретения, определены в ходе исследования шлаковой системы CaF2-TiO2-FeO и отвечают значениям области А оптимальных составов системы.
С целью улучшения стабилизации дугового промежутка и обеспечения стабильного горения дуги как на прямой, так и на обратной полярности, а также определенного увеличения коэффициента формы в покрытие введен магнезит (в виде магнезита металлургического), что также практически предотвращает разбрызгивание. Введение магнезита в количестве, которое превышает принятый предел, приводит к огрублению чешуйчатости валиков и неравномерности их по высоте.
Окись железа при введении в шлаковую систему CaF2-TiO2 снижает температуру ее плавления, а также коэффициент поверхностного натяжения, что приводит к мелкокапельному переносу расплавленного металла и образованию валиков с мелкочешуйчатой поверхностью и плавным переходом к основному металлу или металлу предварительно наплавленных валиков. Введение в покрытие предлагаемого электрода FeO в количестве, меньшем заявленного, приводит к образованию "горбатых" валиков. Превышение количества FeO свыше предлагаемого предела способствует образованию легкоплавких шлаков, которые делают невозможным качественное формирование вертикальных и потолочных швов. Введение FeO в предлагаемом количестве в присутствии фторида кальция вызывает образование фторидов железа, которые также обеспечивают дополнительное снижение диффузного водорода в наплавленном металле.
Введение полевого шпата в указанных границах вызывает образование достаточно плотной шлаковой корки и способствует вместе с магнезитом стабилизации дугового промежутка. Увеличение содержания полевого шпата сверх указанного предела приводит к образованию более жидкотекучих шлаков большой массы, что затрудняет сварку в пространственных положениях.
Ферросилиций способствует переходу необходимого количества марганца из стержня в наплавленный металл. Но повышение его содержания выше предлагаемого предела приводит к росту внутрикристаллитной ликвации в металле аустенитных швов, вследствие чего происходит обогащение кремнием пограничных слоев дендритов. При этом снижается критическая скорость деформирования аустенитного металла швов и их стойкость против образования горячих трещин.
Состав сварочной проволоки был выбран из следующих соображений. Недостаточный уровень легирования (Niэкв.<19% и Crэкв.<21%) приводит к образованию в металле шва близ линии сплавления хрупкой мартенситной прослойки, пораженной холодными трещинами. При использовании проволок с избыточным уровнем легирования возникает риск образования горячих трещин, который можно уменьшить путем введения молибдена. Это позволяет установить верхнюю границу легирования на уровне Niэкв.=32% и Crэкв.=33%.
Для экспериментальной проверки предлагаемого технического решения были изготовлены 5 партий электродов диаметром 4 мм со стрежнями из проволоки Св.-10Х16Н25АМ6 с никелевым эквивалентом 28,81% и хромовым эквивалентом 21,8%, состав покрытия которых приведен в таблице 1.
Таблица 1 | |||||
Состав покрытия электродов, мас.% | |||||
ПокрытиеКомпоненты | 1 | 2 | 3 | 4 | 5 |
флюорит | 20 | 22 | 26 | 31 | 34 |
рутиловый концентрат | 39 | 37 | 29 | 22 | 18 |
окись железа | 11 | 15 | 22 | 31 | 34 |
магнезит | 11 | 9 | 8 | 4 | 3 |
полевой шпат | 15 | 13 | 11 | 8 | 7 |
ферросилиций | 2 | 2 | 2 | 2 | 2 |
карбоксиметилцеллюлоза | 2 | 2 | 2 | 2 | 2 |
Для оценки сварочно-технологических свойств водолазом-сварщиком в лабораторном бассейне на глубине 2 м во всех пространственных положениях сваривались стыковые образцы из стали Ст3 толщиной 14 мм. Формирование наплавленного металла оценивалось по трехбалльной системе с учетом внешнего вида, отделимости шлака, характера шлаковой корки, разбрызгивания, стабильности горения и т.п., таблица 2. Анализ полученных результатов позволяет сделать вывод, что электроды с покрытием предложенного состава обеспечивают удовлетворительное формирование многослойных швов во всех пространственных положениях.
При изготовлении электродов для дальнейших испытаний использовали покрытие №3, таблица 1.
Испытания изготовленных электродов включали сварку и металлографические исследования технологических проб типа Теккен и сварку стыковых соединений в нижнем, вертикальном и потолочном положениях для определения механических свойств. В качестве основного металла использовали сталь 17Г1С, предрасположенную к образованию холодных трещин в ЗТВ.
Для определения трещиностойкости сварных соединений в качестве стержней использовали экспериментальные проволоки с легированием в пределах Niэкв.=19...32% и Crэкв.=21...33%, таблица 3. Результаты испытаний приведены в таблице 4.
Таким образом, использование стержней из проволок с уровнем легирования Niэкв.=19...32% и Crэкв.=21...33% обеспечивает получение сварных соединений без трещин.
Для определения механических свойств металла шва были изготовлены электроды со стержнями из проволоки Св.-10Х16Н25АМ6. Результаты испытаний приведены в таблице 5. Их анализ позволяет сделать следующие выводы. Электроды предложенного состава обеспечивают отсутствие трещин как в металле шва, так и в зоне термического влияния и уровень механических свойств, который превышает уровень механических свойств стали 17Г1С.
Таблица 5 | ||||
Результаты испытаний электродов со стержнями из проволоки Св.-10X16h35AM6 | ||||
Пространственное положение | Механические свойства металла шва | Испытания пробы Теккен | ||
σt, МПа | σb, МПа | δ, % | ||
Нижнее | 420 | 590 | 32 | трещин нет |
Вертикальное | 390 | 570 | 32 | |
Потолочное | 380 | 570 | 30 |
Таким образом, предложенный электрод позволяет получить во всех пространственных положениях качественное сварное соединение с необходимым уровнем механических свойств при сварке под водой низколегированной стали повышенной прочности без холодных трещин в зоне термического влияния и может быть рекомендован для применения при ремонте подводных трубопроводов.
Электрод для подводной сварки, который включает стержень из высоколегированной стали, и покрытие, содержащее рутиловый концентрат, полевой шпат, флюорит и ферросилиций, отличающийся тем, что значения никелевого и хромового эквивалентов стержня ограничены следующими величинами, мас.%:
Niэкв. | 19-32 |
Crэкв. | 21-33 |
а покрытие дополнительно содержит окись железа, магнезит металлургический и карбоксиметилцеллюлозу при следующем соотношении компонентов, мас.%:
флюорит | 22,0-31,0 |
рутиловый концентрат | 22,0-37,0 |
окись железа | 15,0-31,0 |
полевой шпат | 8,0-13,0 |
магнезит металлургический | 4,0-9,0 |
ферросилиций | 0,5-2,0 |
карбоксиметилцеллюлоза | 1,5-2,0 |
при этом коэффициент массы покрытия составляет 22-25%.
www.findpatent.ru
Электросварка под водой - Справочник сварщика
Очень специфичным видом сварки, является электросварка под водой. Впрочем, специфичным является не столько тип сварки, сколько условия, в которых приходиться работать, и с которыми приходиться сталкиваться. Согласитесь, сварка под водой является очень необычной, ведь она проходит в среде, где нет воздуха, где нечем дышать, и где есть определенный уровень давления воды. А ведь без этого вида сварки, сегодня невозможно, так как выполнения сварочных работ необходимы для строительства мостов, создания путепроводов и трубопроводов, при судостроительных работах и так далее. В общем, давайте более подробно рассмотрим сам процесс электросварки.
Итак, как и в обычной сварке, в подводной сварке, используется электросварка. Однако, из-за воздействия водной среды, происходит интенсивное охлаждение дуги, что, в свою очередь, существенно повышает напряжение и тепловую мощность дуги. Как результат, происходит интенсивное плавление металла. Во многом, успеху подводной электросварки, заслуга электродов, а точнее их покрытий. Так, они должны иметь достаточную для работы толщину, а также до 30% веса самого электродного стержня. Покрытие, которое омывается водой, расплавляется гораздо медленнее, чем стержень электрода, поэтому во время горения дуги, это покрытие, образует на поверхности, некий козырек. Он способствует формированию и последующему удержанию газового пузыря, который крайне важен для нормальной работы и горения дуги.
Однако, в процессе сварки, газовый пузырь интенсивно растет, поэтому со временем, газы все же не удерживаются под козырьком, и начинают подыматься наружу. Потому, газовый пучок снова накапливается, и так происходит до бесконечности. Во время сварки, также образуются пары железа и материалов электрода, и при соприкосновении с водой, конденсируются, образовывая мелкие коллоидальные частички, как правило, из окисла железа. Эти частички на протяжении долгого времени не осаждаются в воде, и поэтому, образуют в воде темно-бурое облако, которое мешает сварщику видеть область сварки.
Дуга под водой: 1 — сварочная дуга; 2 — ванна с расплавленным металлом; 3 — электродный козырек; 4 — пузырьки; 5 — электродная обмазка; 6 — рабочий стержень; 7 — муть; 8 — брызги от металла; 9 — газовый пузырь.
Если во время работы используются качественные электроды, то сварочная дуга, в принципе, такая же качественная и устойчивая, как и во время работы на свежем воздухе. Как правило, работа происходит при постоянном токе, причем нормальной полярности. В целом, допускается и проведение подводных сварочных работ при переменном токе, однако на постоянном токе, сварочная дуга будет более качественной и устойчивой, следовательно, и качество сварного шва будет куда лучше.
www.vse-o-svarke.org