Электроды для сварки железнодорожных рельс. Сварка рельсовых стыков электродами
Методы сварки железнодорожных, крановых и подкрановых рельс ПРСМ
В железнодорожной отрасли и в строительстве применяется техника, которая перемещается по рельсам. Как правило, она имеет достаточно большой вес, а соответственно металл сталкивается с большими нагрузками. Чтобы изделия смогли выдержать все сложности эксплуатации, сварка рельс должна происходить в точности с предписанными технологиями, так как это сложный процесс. С одной стороны, проблем добавляет большой диаметр изделий, которые не позволяет проварить их на всю глубину, что обеспечило бы более высокое качество. С другой стороны, сварное соединение всегда будет самым слабым местом конструкции и его необходимо усиливать.

Сварка рельс
Сварка рельсовых стыков может проходить как в ручную, так и в автоматическом режиме. После нее всегда требуется проводить обработку материала, чтобы достичь гладкой поверхности. Таким образом, для качественного проведения процесса требуется:
- Использовать профессиональную технику;
- Необходимо выбрать подходящие расходные материалы;
- Обеспечить лучшие условия свариваемости благодаря флюсам и прочим средствам;
- Соблюдать точные режимы сварки;
- Тщательно обработать полученное соединение, чтобы рельсы были пригодны к эксплуатации.
Свойства свариваемости 
Над проблемой, которую представляет собой сварка крановых рельсов, а также прочих их разновидностей, люди работают достаточно давно. Ведь сами изделия производятся из упрочненной стали, которая зачастую обрабатывается механическим путем. Любая обработка на упрочнение добавляет сложности к свариваемости и к любым другим термическим обработкам. Тем не менее, современные технологии позволяют добиться приемлемых результатов. Одним из самых доступных вариантов среди электродов, которые можно свободно найти в продаже, являются УОНИ 13/45 и УОНИ 13/55. Это изделия для работы с ответственными сооружениями, мощными каркасами из металлоконструкций, а также они подходят и для рельс. Но это далеко не единственный метод, хотя и самый простой из всех возможных.

Сварка крановых рельсов
Сварка рельсов пути производится по ГОСТ 103-76. Сюда входит несколько методов, которые отличаются принципом действия, сложностью, используемой техникой и прочими нюансами. Каждый из них по-своему помогает бороться с плохой свариваемостью изделий. Также их выбор зависит от вида самих рельс, которые должны будут поддаться будущему ремонту.
Виды 
- Железнодорожные промышленные – применяются для относительно коротких участков путей на различных предприятиях. Это ширококолейные варианты, для которых используются марки РП75, РП65 и РП50.
- Железнодорожные для узкой колеи – используются в подземных шахтах и узкоколейной железной дороге. Здесь применяют такие марки как Р24, Р18, Р11 и Р8.
- Рудничные для проводников в шахтах – применяются при создании бесстыкового и звеньевого пути широкой колеи. Также применяются и для стрелочных переводов. Здесь используются марки Р43, Р38 и Р33.
- Рамные – используются для строительства пересечений и соединений на пути. Здесь нужна марка РР65.
- Крановые – служат для создания путей прохождения строительного крана на площадках. Тут могут быть такие марки как, КР140, КР120, КР100, КР80 и КР70.
- Остряковые – служат для верхнего строения в ж/д пути. Из них делают стрелочные переводы, круговые опорные устройства и прочее. Здесь пригодны марки ОР75, ОР65, ОР50 и ОР43.
- Железнодорожные – стандартные изделия для создания бесстыкового и звеньевого основного пути для ж/д транспорта. Тут применяются марки Р75, Р65 и Р50.
- Трамвайные с желобом – используются для создания путей прохождения трамваев. Здесь применяются марки Т62 и Т58.
- Контррельсовые – используются в верхних конструкциях ж/д пути. Это могут быть марки РК75, РК65 и РК50.
- Усиковые – из них изготавливаются крестовины, у которых непрерывная поверхность качения. Марка УР65.
Способы сварки рельсов 
Существуют различные методы сварки рельсов, которые используются в наше время. Среди них стоит выделить основные:
Электродуговая сварка рельсов вручную – самый простой и доступный метод. Она подходит для соединения стыков и плетей. Изделия располагаются с небольшим зазором, который постепенно заполняется расплавленным металлом. Здесь используется переменный или постоянной род тока.

Электродуговая сварка рельсов вручную
Одной из разновидностей предыдущего варианта является ванный метод. Для этого используется специальная ванночка, которая задерживает стекание расплавленного материала. Торцы предварительно перпендикулярно своей оси обрезаются. Монтаж осуществляется без перелома. Зазор между изделиями должен быть около 1,5 см. В этот зазор помещается электрод, который расплавляется под силой тока и сваривается с основным материалом.

Ванная сварка рельс
Термитная сварка железнодорожных рельс основана на химической реакции окиси железа и алюминия. При их контакте и под воздействием температуры более двух тысяч градусов, сталь приобретает огнеустойчивую форму. Она идентична форме самого рельса. Это давний метод, который применяется уже более сотни лет.
Газопрессовая сварка подкрановых рельсов предполагает не полное расплавление, так как температура рабочего процесса не достигает точки плавления металла. сварка рельсовых плетей здесь достигается за счет высокого давления. Качество соединения оказывается достаточно высоким, а структура его получается очень однородной. Здесь необходимо плотная стыковка концов изделия. На рельсорезном станке ножовка прорезает торцы двух изделий, что помогает максимально очистить стыковочную поверхность. Перед соединением торцы обрабатываются четыреххлористым углеродом. Далее идет нагрев и зажатие заготовок при помощи гидравлического пресса.

Газопрессовая сварка рельс
Режимы 
Для получения качественного соединения нужно придерживаться соответствующих режимов. Для каждой марки изделий нужны свои параметры, так как они обладают различными свойствами. Здесь приведены наиболее часто используемые варианты:
Параметр режимов | Значения параметров для рельсов | ||
Р75 | Р65 | Р50 | |
Длительность сварки, с | 330 | 280 | 235 |
Сила осадки, кН | 350 | 330 | 250 |
Минимальная сила зажатия, кН | 530 | 500 | 380 |
Контактное сила, кН | 75 | 62 | 48 |
Первоначальная дистанция между электродами, мм | 153 | 135 | 125 |
Величина оплавления линейная, мм | 25 | 24 | 22 |
Проверка качества 
Вне зависимости от того, проводила процедуру машина для сварки рельсов или человек, требуется проконтролировать качество. Первоначальным методом контроля являются измерительные приборы. Затем проверяется состояние поверхности шва, так как она должна быть максимально ровной и гладкой. Затем проводится ряд неразрушающих контролей качества, но это делается уже после остывания металл и обработки поверхности.
Меры безопасности
Когда проводится сварка рельсов электродами, то следует использовать средства индивидуальной защиты, проверить заземление и исправность техники. Не следует находиться близко к расплавленному металлу, если в том нет необходимости. При использовании различных машин следует проверить их перед использованием на работоспособность. Если у какой-либо техники имеются поломки или в расходных материалах замечен брак, то такие вещи не должны использоваться в процессе.
svarkaipayka.ru
Сварка рельсовых стыков электродами
Электроды для сварки железнодорожных рельс
Даже отбракованные или отслужившие свой срок рельсы являются желаемым приобретением для любого рачительного домовладельца. Ведь прочный и стойкий к коррозии рельс может заменить любую металлическую балку.
Однако монтирование конструкций из этого сорта металлопроката весьма затруднительно. Тяжелые рельсы требуют прочных сварочных швов. Железнодорожники используют для этих целей особый термитный состав. Ну а в быту необходимы специальные электроды для сварки железнодорожных рельс. И в этой статье мы опишем именно такую продукцию, с помощью которой вы сможете состыковать рельсы любым, удобным для вас способом.
«Рельсовые» электроды
Решая, какими электродами варить рельсы, стоит принять во внимание толщину данного сорта металлопроката. Поэтому источником присадочного материала в процессе сварки рельс могут быть только особые электроды серии УОНИ, предназначенные для стыковки толстотелых конструкций. Причем для сварки рельсов достаточно «младших» представителей этой серии – электродов УОНИ 13/45 и 13/55, которыми можно стыковать заготовки из высокоуглеродистых или низколегированных сталей.
От прочих источников присадочного материала электроды УОНИ 13/45 и 13/55 отличаются особым флюсом (покрытием), в состав которого входят ферромарганцевые руды, графит, кремний и прочие материалы.
Благодаря такому многокомпонентному миксу обеспечивается устойчивое горение дуги, передающей высокую температуру в зону сварки, и подавляется процесс образования пор в сварочном шве. Интересен и состав электродной проволоки. Ее изготавливают из железоуглеродистого сплава, легированного никелем и молибденом. Диаметр проволоки – 2-5 миллиметров.
В итоге, опираясь на особый состав флюса и присадочного материала, серия УОНИ обеспечивает не только высокую скорость работы, но и не менее высокую прочность сварочного шва.
Подготовка электрода к сварке
Электроды для сварки рельсов – работают в очень сложных условиях. Ведь толщина стыкуемых кромок в данном случае может равняться нескольким десяткам сантиметров.
Поэтому к качеству таких электродов предъявляют особые требования, а именно:
- На покрытии таких электродов не должно быть крупных трещин.
- Влажность покрытия должна соответствовать определенному значению.
И если соответствие электрода первому требованию можно проверить визуально, то с влажностью все намного сложнее. Поэтому перед сваркой все электроды из серии УОНИ подвергают обязательному прокаливанию (подсушиванию) в особой установке.
Эта процедура выглядит как прогрев изделия до температуры в 350-400 градусов Цельсия. Причем электроды загружаются в уже разогретый «жарочный шкаф» и «томятся» в нем около 1-2 часов.
После такой подготовки электроды можно использовать в любом положении, формируя с их помощью и нижние, и потолочные, и вертикальные швы на постоянном токе, и обратной полярности подключения.
Единственное «противопоказание к применению» для серии УОНИ – это сварка по направлению сверху вниз.
steelguide.ru
Способ сварки рельсовых стыков
Изобретение относится к области сварки, а именно к сварке рельсов железнодорожного пути. На кромках рельсов (1) и (2) или кромке одного из рельсов выполняют поперечный разрез по вертикальной плоскости от головки до начала подошвы рельса. Выполняют горизонтальный разрез по торцевой поверхности рельсов или рельса перпендикулярно по отношению к ранее произведенному разрезу и снимают на торцевой поверхности подошвы фаску под углом 45° с образованием у основания подошвы притупления (3). Устанавливают рельсы с необходимым технологическим зазором (4). Вводят внутрь зазора сварочную проволоку вместе с изолированным концевым наконечником электрододержателя сварочного полуавтомата. Осуществляют электродуговую сварку непрерывно по всей высоте рельса с использованием боковых формирующих накладок-кристаллизаторов в зоне сварки на сварочном токе, обеспечивающем образование жидкой ванны во всем объеме технологического зазора. Жидкую ванну в корне шва получают за счет расплавления кромок основного металла рельсов. Повышаются механические свойства сварного шва и производительность процесса, а также облегчается труд сварщика. 2 ил.
Изобретение относится к электродуговым методам сварки железнодорожного рельсового пути и может быть использовано преимущественно для полуавтоматической электродуговой сварки рельсов.
Известен способ автоматической сварки стыков железнодорожного рельсового пути, в котором сварку рельсов ведут с использованием сварочного автомата электродуговым методом (см. Япония №08-00328 А, кл. В23К 31/00, опубл. 09.01.1996).
Однако такой способ сварки не может применяться в условиях различного износа рабочих поверхностей головки рельсового пути и требует высокой квалификации сварщиков.
Наиболее близким из известных по своей технической сущности и достигаемому результату является выбранный в качестве прототипа способ сварки рельсов железнодорожного пути, включающий обрезку кромок рельсов или кромки одного из рельсов, установку рельсов с необходимым технологическим зазором, введение внутрь зазора сварочной проволоки и электродуговую сварку с использованием боковых формирующих накладок-кристаллизаторов в зоне сварки на сварочном токе, обеспечивающем образование жидкой ванны во всем объеме технологического зазора (см. авторское свидетельство СССР №78136, кл. В23К 9/02, 1942).
В известном способе рельсы устанавливают с зазором между свариваемыми кромками от 9-14 мм. При таком зазоре сварной шов получается, в основном, за счет расплавления электродного материала. Свариваемые кромки настолько сильно разогреваются, что образуется общая ванна расплавленного металла, которая поддерживается в жидком состоянии в течение всего периода сварки. В качестве форм, которые формируют внешнюю сторону сварного соединения, могут служить графитовые пластины, внутренняя поверхность которых изготавливается по форме рельса. Размеры и формы усиления сварного шва зависят от размера и формы соответствующего углубления, которое делается в форме.
Концы рельсов обрезают рельсообрезным станком по плоскости, перпендикулярной к оси рельса. Скос кромок перед сваркой не производят. Зазор между торцами рельсов порядка 9-14 мм не позволяет сварить кромки подошвы рельсов, поэтому для формирования обратной стороны корня шва применяют формирующую подкладку. Сварной шов получается, в основном, за счет расплавления электродного материала, расплавленная масса которого заполняет зазор между торцами подошвы рельсов и формирующей подкладкой.
Наиболее существенным недостатком этого способа является частая смена электрода (длина электрода, применяемого для ручной сварки рельсов - 450 мм). После сгорания электрода процесс сварки прерывается. На поверхности шва образуется твердая защитная шлаковая корка. Для продолжения сварочного процесса необходимо снова зажечь дугу, расплавить шлак и продолжить процесс. Периодическое обрывание дуги приводит к тому, что в сварном шве образуются дефекты типа непровар, шлаковые включения, газовые поры. Эти дефекты являются причиной низких механических свойств сварного соединения.
Технической результат от использования настоящего изобретения - повышение механических свойств сварного шва; сокращение времени сварки рельсов; экономия дорогостоящих сварочных материалов, а также облегчение труда сварщика.
Указанный технический результат достигается тем, что в способе сварки рельсов железнодорожного пути, включающем обрезку кромок рельсов или кромки одного из рельсов, установку рельсов с необходимым технологическим зазором, введение внутрь зазора сварочной проволоки и электродуговую сварку с использованием боковых формирующих накладок-кристаллизаторов в зоне сварки на сварочном токе, обеспечивающем образование жидкой ванны во всем объеме технологического зазора, при обрезке кромок рельсов или кромки одного из рельсов выполняют поперечный разрез по вертикальной плоскости от головки до начала подошвы рельса, горизонтальный разрез по торцевой поверхности рельса перпендикулярно по отношению к ранее произведенному разрезу и снимают на торцевой поверхности подошвы фаску под углом 45° с образованием у основания подошвы притупления, а электродуговую сварку производят непрерывно по всей высоте рельса с использованием сварочного полуавтомата с электрододержателем, снабженным изолированным концевым наконечником, который вводят со сварочной проволокой в технологический зазор, при этом образование жидкой ванны в корне шва осуществляют за счет расплавления кромок основного металла рельсов.
Предложенный способ сварки может быть осуществлен в двух вариантах.
На фиг.1 представлен сварной стык с подготовкой кромки одного из рельсов, на фиг.2 - сварной стык с подготовкой 2-х кромок рельсов.
На фиг.1 обозначены: 1 - рельс (без обработки кромки), 2 - рельс с подготовленной кромкой, 3 - притупление, 4 - зазор между кромками, α - угол между кромками.
На фиг.2 обозначены: 1, 2 - рельсы с подготовленной кромкой, 3 - притупление, 4 - зазор между кромками, α - угол между кромками. Угол α между кромками находится в пределах 30-60°.
В первом варианте способа сварки с подготовкой кромки одного из рельсов предварительно осуществляют механическую обработку кромок рельсов или кромки одного из рельсов, выдерживая зазор между торцами рельсов 22-25 мм. На сварочный держатель, вместо обычного мундштука, устанавливается специальный наконечник (изолированная концевая насадка), который позволяет производить сварку в узкий зазор по всей высоте рельса. Наконечник с проволокой вводят внутрь зазора и осуществляют сварку с применением формирующих накладок-кристаллизаторов в зоне сварки при силе тока, обеспечивающего образование жидкой ванны во всем объеме зазора. Для повышения прочности сварного стыка осуществляют подготовку торцов рельсов обрезкой их по вертикальной плоскости, составляющей с продольной осью рельса угол в 45°, для того чтобы сварной шов испытывал минимальную нагрузку при перекатывании колеса по поверхности головки рельса. Сварку ведут непрерывным, полуавтоматическим электродуговым способом.
Сваривают железнодорожные рельсы тапа Р65. Подготавливают кромки рельса с двух концов или с одного, выдерживая зазор между торцами рельсов 22-25 мм. Поверхности концов рельсов перед сваркой зачищают до металлического блеска. Под подошву свариваемых рельсов устанавливают медную подкладку, формирующую обратную сторону шва, и закрепляют ее струбциной. Подошву рельса сваривают самозащитной порошковой проволокой диаметром 1,6 мм, при силе тока 190-200 А. Устанавливают на шейку и головку рельсов боковые медные формы - кристаллизаторы и закрепляют их струбциной. Сваривают шейку и головку рельса.
Предложенный способ позволяет получить сварной шов с механическими свойствами, которые равнозначны свойствам основного металла, при этом полученные механические свойства сварного шва увеличивают срок службы рельсов до срока службы, установленных в путь рельсов без сварки.
Во втором варианте способа сварки с подготовкой 2-х кромок рельсов предварительно осуществляют механическую обработку кромок рельсов или кромки одного из рельсов, при этом производят поперечный разрез по вертикальной плоскости от головки до начала подошвы рельса, а затем производят горизонтальный разрез по торцевой поверхности рельса перпендикулярно по отношению к ранее произведенному разрезу и на торце подошвы снимают фаску с притуплением у основания подошвы рельса, устанавливают рельсы с необходимым технологическим зазором, вводят внутрь зазора электрод и осуществляют сварку с использованием сварочного полуавтомата и применением форм у места сварки при силе тока, обеспечивающей образование жидкой ванны во всем объеме зазора, причем жидкую ванну в корне шва получают за счет расплавления кромок основного металла.
Предварительно осуществляют механическую обработку кромок рельсов или кромки одного из рельсов, производят поперечный разрез по вертикальной плоскости от головки до начала подошвы рельса и горизонтальный разрез по торцевой поверхности рельса перпендикулярно по отношению к ранее произведенному разрезу и на торце подошвы снимают фаску с притуплением у основания подошвы рельса, а жидкую ванну в корне шва получают за счет расплавления кромок основного металла.
Сваривают железнодорожные рельсы тапа Р65. В механических мастерских дистанции отмеряют кусок рельса длиной 3 м или более в соответствии с ТУ 32 ЦП-670-88 и подготавливают кромки рельса с двух концов для установки на место дефектного рельса. При этом производят поперечный разрез по вертикальной плоскости от головки до начала подошвы рельса. Затем осуществляют горизонтальный разрез по торцевой поверхности рельса перпендикулярно по отношению к ранее произведенному разрезу и на торце подошвы снимают фаску под углом 45° с притуплением 2 мм у основания подошвы рельса. На рельсе, из которого удаляется дефектный участок, делают разметку. Отрезают дефектный кусок рельса, равный по размеру подготовленному, и устанавливают на это место кусок рельса с подготовленными под сварку кромками. Зазор между рельсами составляет 2 мм. Концы рельсов перед сваркой зачищают до металлического блеска.
Под подошву свариваемых рельсов устанавливают формирующую обратную сторону шва медную подкладку и закрепляют ее струбциной. Корень шва сваривают электродом марки УОНИ - 13/65 диаметром 3 мм, ток 140-160 А, с последующим заполнением зазора между торцами подошвы рельсов электродом марки УОНИ - 13/65, диаметром 5 мм, ток 250-280 А.
Устанавливают на шейку и головку рельсов боковые медные формы и закрепляют их струбциной. Сваривают шейку и головку рельса электродами марки УОНИ - 13/65, диаметром 5 мм, ток 250-280 А.
Предложенный способ позволяет получить сварной шов с механическими свойствами, которые равнозначны свойствам основного металла, при этом полученные механические свойства сварного шва увеличивают срок службы рельсов до срока службы установленных в путь рельсов без сварки.
Способ сварки рельсов железнодорожного пути, включающий обрезку кромок рельсов или кромки одного из рельсов, установку рельсов с необходимым технологическим зазором, введение внутрь зазора сварочной проволоки и электродуговую сварку с использованием боковых формирующих накладок-кристаллизаторов в зоне сварки на сварочном токе, обеспечивающем образование жидкой ванны во всем объеме технологического зазора, отличающийся тем, что при обрезке кромок рельсов или кромки одного из рельсов выполняют поперечный разрез по вертикальной плоскости от головки до начала подошвы рельса, горизонтальный разрез по торцевой поверхности рельса перпендикулярно по отношению к ранее произведенному разрезу и снимают на торцевой поверхности подошвы фаску под углом 45° с образованием у основания подошвы притупления, а электродуговую сварку производят непрерывно по всей высоте рельса с использованием сварочного полуавтомата с электрододержателем, снабженным изолированным концевым наконечником, который вводят со сварочной проволокой в технологический зазор, при этом образование жидкой ванны в корне шва осуществляют за счет расплавления кромок основного металла рельсов.
www.findpatent.ru
Способы сварки рельсов (Электроконтактная, электродуговая, газопрессовая и алюмотермитная сварка), страница 2
Сварка рельсов вторым способом - оплавлением с предварительным прерывистым подогревом состоит из стадии прерывистого подогрева, стадии непрерывного оплавления; стадии осадки и сварки, стадии остывания сварных стыков. В этом способе в отличие от первого разогрев металла рельсов производится путем многократного циклического смыкания и размыкания рельсовых концов. Электроконтактная сварка обеспечивает наиболее высокое качество сварных стыков. Качество сварных стыков определяется степенью пластических деформаций и нагрева металла рельсов. В связи с этим первостепенной является обязательность строгого обеспечения режимов сварки, утверждаемых Главным управлением пути МПС.
7.3. Электродуговая сварка
При электродуговой сварке рельсы соединяют металлом электрода, который расплавляется от тепла дугового разряда.
Электродуговая сварка стыков не требует приложения осадочного давления. Для этой сварки используют переменный ток от трансформатора или постоянный ток от передвижного сварочного агрегата.
Лучшим способом электродуговой сварки является ванный способ, при котором концы рельсов, обрезанные перпендикулярно продольной оси, устанавливают без перелома в плане, а в профиле с возвышением 3-5 мм, и в таком положении закрепляют с зазором 14-16 мм.
Между торцами вводят электрод, через который пропускают ток в 300-350 ампер. Расплавленный металл электрода заполняет зазор между торцами по всему сечению рельса.
Чтобы расплавленный металл электрода не растекался, применяют инвентарные медные формы, которыми закрывается зазор снизу и с боков. Сваренные стыки шлифуют по всему периметру рельса. Качество сваренного стыка зависит от электродов и их обмазки, постоянства жидкого состояния металла до окончания процесса сварки, тщательности обработки шва.
Электродуговую сварку применяют только для рельсов, укладываемых на станционных путях, кроме главных и приемо-отправочных.
7.4. Газопрессовая сварка
Газопрессовая сварка обеспечивает соединение металла при температуре
ниже точки плавления с приложением давления.
Основным достоинством газопрессовой сварки рельсов является высокое качество соединения и получение однородной структуры металла в зоне стыка, поэтому данный вид сварки особенно выгоден в применении к более тяжелым типам рельсов.
Перед сваркой торцы двух рельсов приставляют плотно один к другому и вместе стыка одновременно прорезают торцы обоих рельсов дисковой пилой на рельсорезном станке или при помощи механической ножовки, что обеспечивает плотность прилегания торцов и чистоту металла. Непосредственно перед сваркой торцы рельсов должны быть тщательно промыты четыреххлористым углеродом или дихлорэтаном. Подготовка перед сваркой заключается в предварительном нагреве концов рельс.
Для нагрева рельса применяются многопламенные горелки типа МГ – 50Р,
МГ – 65Р, МГ – 75Р. Многопламенная горелка типа МГ – Р65 представлена на рисунке 1.3.
Рис.7.3: Многопламенная горелка МГ-Р65 (а) и ее ствол (б):
1 – верхняя часть горелки; 2 – колодки с отверстиями для газа; 3 – нижняя часть горелки; 4 – газопровод; 5 и 9 – трубопроводы для проточной воды; 6 – газовая скоба соединяющая 1 и 3; 7 – газовая распределительная камера; 8 – шнур с ниппелем; 10 – надставка, соединяющая ствол со смесительной камерой; 11 – смесительная камера; 12 – ствол горелки; 13 и 14 – штуцера для подачи газа к стволу.
Концы рельсов зажимают гидравлическим прессом и нагревают до температуры 12000С системой многопламенных горелок, совершающих колебательные движения вдоль стыка (50 колебаний в минуту). Одновременно рельсы сжимаются с установленной расчетом силой (10 – 13 тонн) до получения осадки заданной величины (около 20 мм).
Для сварки применяются универсальные газопрессовые станки СГП – 8У или МГП – 9.
После сваривания производится обработка стыка, а затем его нормализация.
7.5. Алюмотермитная сварка
Создание высокоскоростных магистралей и бесстыкового пути устанавливает высокие стандарты качества к рельсам, особенно в местах их соединения. В полной мере этим стандартам отвечает алюмотермитная сварка рельсов.
Алюмотермитная сварка рельсов предназначена для соединения между собой в любом сочетании объемно-закаленных, поверхностно-закаленных и термически не упрочненных рельсов.
Сварка стыков рельсовых плетей и стыков (кроме изолирующих) стрелочных переводов, уложенных на деревянных или железобетонных шпалах и брусьях, может производиться на главных, приемо-отправочных, станционных и горочных путях железных дорог Российской Федерации, на подъездных путях промышленных предприятий, а также в метрополитене.
В основе этого процесса лежит термитная реакция, открытая в 1896 году профессором Гансом Гольдшмидтом, и представляющая собой химическую реакцию восстановления чистого железа из его окиси при помощи алюминия с выделением большого количества тепла:
Fe2O3 + 2Al => 2Fe + Al2O3 + 849 кДж
Термитная реакция происходит в тигле в течение нескольких секунд после поджига термитной порции, состоящей из смеси порошкового алюминия, оксида железа, частиц стали, демпфирующих реакцию, и легирующих добавок, необходимых для получения стали нужного качества. Реакция проходит при температуре свыше 2000oС с конечным послойным разделением продуктов реакции: жидкой стали (снизу) и легкого шлака (сверху).
В России ВНИИЖТ совместно с иностранными фирмами Снага (Словакия), Электро-Термит (Германия), Рельтех (Чехия и Франция) выполняют работы, связанные с термитной сваркой рельсовых элементов в зоне соединительных путей. При укладке бесстыкового пути термитный способ сварки рельсов (рис.1.4.) играет ведущую роль. В настоящее время в зоне стрелочных переводов он является основным методом соединения рельсов. Это экономически выгодная технология, отличающаяся большой гибкостью применения. В большинстве случаев сварку можно проводить без закрытия перегона. Технология фирмы «Электро-Термит», получив наибольшее распространение по сравнению с другими фирмами, представляет на рынке России два основных метода электро-термитной сварки, а именно так называемый, метод СоВоС (SoWoS) и метод СкФау (SkV) (рис.1.5).
vunivere.ru
Электроды для сварки железнодорожных рельс
Люди, которые ведут масштабное строительство или просто привыкли все делать мощно, то они, наверняка, сталкиваются с проблемой сваривания рельс. Сваривание рельс является проблемой, потому что они имеют большой диаметр и, как следствие, создают препятствия для комфортного сваривания. Поэтому для сваривания рельс Вам нужно использовать качественные электроды, которые позволяют Вам быть полностью уверенными в качестве сваренного изделия.
Одними из тех электродов, которые можно использовать для сваривания рельс, являются УОНИ 13/45 или УОНИ 13/55. Да, действительно, сварочные электроды УОНИ являются прекрасным выбором для сваривания таких толстотелых конструкций как рельсы.
Электроды УОНИ используются для сваривания ответственных конструкций из металла, когда к металлическому шву предъявляются высокие требования по ударной вязкости. Многие профессиональные сварщики рекомендуют электроды УОНИ для сваривания конструкций, работающих под нагрузками, давлением и другими воздействиями факторов окружающей среды.
Сваривание электродами УОНИ позволяет обеспечить получение металла высокого качества, который имеет высокую устойчивость к образованию трещин и содержанием водорода. Сваривание электродами УОНИ можно производить во всех пространственных положениях. Для сваривания нужно использовать постоянный ток обратной полярности.
Материалом для изготовления сварочных электродов УОНИ является сварочная проволока Св-08А, которая полностью соответствует государственным стандартам, принятым в нашей стране. На поверхности покрытия сварочных электродов УОНИ допускаются небольшие трещины, которые могут быть на покрытии сварочного электрода. Однако если покрытие сварочного электрода сильно повреждено, то Вам нужно проверить, в каком месте Вы их храните, потому что из-за попадания влаги Вы можете испортить сварочный электрод.
В покрытия сварочных электродов УОНИ есть некоторые особенности, которые требуют обязательной прокалки перед использованием. Прокаливание электродов УОНИ производится при температуре от 350 до 400 градусов по Цельсию.
Прокалка электродов перед свариванием облегчает работу с ними и позволяет сделать сварочный шов, нанесенный ними, более прочным. Также прокалка или просушка электродов при указанной температуре позволяет сделать их менее восприимчивыми к влаге.
Как видите, использование сварочных электродов УОНИ позволяет производить сваривание высокого качества. Благодаря их высокому качеству и особенностям сваривания, Вы можете в краткие сроки начинать производить сваривание рельс.
Сварка рельс – это сложная работа, поэтому для того чтобы Вы могли ее как можно быстрее и качественнее сделать, Вам нужно использовать электроды УОНИ. Также для того чтобы Вы могли производить прокалку электродов УОНИ и хранить их в подходящем месте Вам лучше всего приобрести специальную печь для прокалки электродов.
elektrod-3g.ru
www.samsvar.ru
Способ сварки рельсовых стыков
Изобретение относится к дуговым способам сварки и используется преимущественно для ручной электродуговой сварки железнодорожных рельсов. Способ сварки рельсовых стыков включает установку рельсов с зазором между свариваемыми кромками, введение внутрь зазора плавящегося электрода и сварку с применением форм, установленных у места сварки, при силе тока, обеспечивающей образование жидкой ванны во всем объеме зазора. Предварительно осуществляют механическую обработку кромок рельсов или кромки одного из рельсов, включающую выполнение поперечного разреза по вертикальной плоскости от головки до начала подошвы рельса, выполнение горизонтального разреза по торцевой поверхности рельса перпендикулярно по отношению к ранее произведенному разрезу и снятие на торцевой поверхности подошвы фаски с притуплением у основания подошвы рельса. При образовании жидкой ванны в корне шва дополнительно осуществляют расплавление кромок основного металла рельсов. Это позволит получить сварной шов с механическими свойствами, равнозначными свойствам основного металла, что увеличит срок службы рельсов. 2 ил.
Изобретение относится к дуговым методам сварки, преимущественно используется для ручной электродуговой сварки железнодорожных рельсов.
Известен способ сварки рельсовых стыков, в котором сварку рельсов ведут ручным электродуговым способом (SU 78136, В 23 К 9/02, 1942).
В известном способе рельсы устанавливают с зазором между свариваемыми кромками от 9-14 мм в зависимости от выбранного диаметра электрода, поэтому сварной шов получается, в основном, за счет расплавления электродного материала. Свариваемые кромки настолько сильно разогреваются, что образуется общая ванна расплавленного металла, которая поддерживается в жидком состоянии в течение всего периода сварки. В качестве форм могут служить графитовые пластины, внутренняя поверхность которых изготавливается по форме рельса. Размеры и формы усиления сварного шва зависят от размера и формы соответствующего углубления, которое делается в форме.
Концы рельсов обрезают рельсообрезным станком по плоскости, перпендикулярной к оси рельса. Скос кромок перед сваркой не производят.
Большой зазор между торцами рельсов порядка 9-14 мм не позволяет сварить кромки подошвы рельсов, поэтому для формирования обратной стороны корня шва применяют формирующую подкладку. Сварной шов получается, в основном, за счет расплавления электродного материала, расплавленная масса которого заполняет зазор между торцами подошвы рельсов и формирующей подкладкой.
Наиболее существенным недостатком этого способа является наличие большого зазора между торцами рельсов. Расплавленный электродный металл является естественной перемычкой между свариваемыми рельсами, по которой дуга перемещается от кромки одного рельса к кромке другого. Сварное соединение, полученное таким способом, имеет крупнозернистое строение из-за перегрева электродного металла и, как следствие, более низкие механические свойства, чем у основного металла. В зоне сплавления кромки рельса с расплавленной массой электродного металла возникает большая вероятность возникновения дефектов типа непровара, шлаковые включения, поры.
Технической задачей настоящего изобретения является повышение механических свойств сварного шва путем уменьшения зазора между торцами рельсов до размера, позволяющего сварить металл подошвы рельсов и получить сварной шов с механическими свойствами, которые равнозначны свойствам основного металла.
Способ согласно изобретению, заключается в том, что предварительно осуществляют механическую обработку кромок рельсов или кромки одного из рельсов, при этом производят поперечный разрез по вертикальной плоскости от головки до начала подошвы рельса, а затем горизонтальный разрез по торцевой поверхности рельса перпендикулярно по отношению к ранее произведенному разрезу, и на торце подошвы снимают фаску с притуплением у основания подошвы рельса, устанавливают рельсы с зазором, вводят внутрь зазора электрод и осуществляют сварку с применением форм у места сварки при силе тока, обеспечивающей образование жидкой ванны во всем объеме зазора, причем жидкую ванну в корне шва получают за счет расплавления кромок основного металла.
Отличия предложенного способа сварки рельсовых стыков состоят в том, что предварительно осуществляют механическую обработку кромок рельсов или кромки одного из рельсов, при этом производят поперечный разрез по вертикальной плоскости от головки до начала подошвы рельса, а затем горизонтальный разрез по торцевой поверхности рельса перпендикулярно по отношению к ранее произведенному разрезу, и на торце подошвы снимают фаску с притуплением у основания подошвы рельса, а жидкую ванну в корне шва получают за счет расплавления кромок основного металла.
Сущность предлагаемого способа поясняется чертежами.
На фиг.1 представлен чертеж при механической обработке кромки одного из рельсов, на фиг.2 - кромок рельсов.
На фиг.1 обозначены: 1 - рельс (без обработки кромки), 2 - рельс с подготовленной кромкой, 3 - притупление, 4 - зазор между кромками, α - угол между кромками.
На фиг.2 обозначены: 2 - рельс с подготовленной кромкой, 3 - притупление, 4 - зазор между кромками, α - угол между кромками.
Угол α между кромками лежит в пределах 30-60°.
Далее представлен один из примеров осуществления способа.
Сваривают железнодорожные рельсы типа Р65. В механических мастерских дистанции отмеряют кусок рельса длиной 3 м или более в соответствии с ТУ 32 ЦП-670-88 и подготавливают кромки рельса с двух концов для установки на место дефектного рельса. При этом производят поперечный разрез по вертикальной плоскости от головки до начала подошвы рельса. Затем осуществляют горизонтальный разрез по торцевой поверхности рельса перпендикулярно по отношению к ранее произведенному разрезу и на торце подошвы снимают фаску под углом 45° с притуплением 2 мм у основания подошвы рельса. На рельсе, из которого удаляется дефектный участок, делают разметку. Отрезают дефектный кусок рельса, равный по размеру подготовленному, и устанавливают на это место кусок рельса с подготовленными под сварку кромками. Зазор между рельсами составлял 2 мм (см. фиг 1). Концы рельсов перед сваркой зачищают до металлического блеска.
Под подошву свариваемых рельсов устанавливают формирующую обратную сторону шва медную подкладку и закрепляют ее струбциной. Корень шва сваривают электродом марки УОНИ - 13/65, диаметром 3 мм, ток 140-160 А, с последующим заполнением зазора между торцами подошвы рельсов электродом марки УОНИ - 13/65, диаметром 5мм, ток 250-280 А.
Устанавливают на шейку и головку рельсов боковые медные формы и закрепляют их струбциной. Сваривают шейку и головку рельса электродами марки УОНИ - 13/65, диаметром 5 мм, ток 250-280 А.
Предложенный способ позволяет получить сварной шов с механическими свойствами, которые равнозначны свойствам основного металла, при этом полученные механические свойства сварного шва увеличивают срок службы рельсов до срока службы установленных в путь рельсов без сварки.
Способ сварки рельсовых стыков, включающий установку рельсов с зазором между свариваемыми кромками, введение внутрь зазора плавящегося электрода и сварку с применением форм, установленных у места сварки, при силе тока, обеспечивающей образование жидкой ванны во всем объеме зазора, отличающийся тем, что предварительно осуществляют механическую обработку кромок рельсов или кромки одного из рельсов, включающую выполнение поперечного разреза по вертикальной плоскости от головки до начала подошвы рельса, выполнение горизонтального разреза по торцевой поверхности рельса перпендикулярно ранее произведенному разрезу и снятие на торцевой поверхности подошвы фаски с притуплением у основания подошвы рельса, а образование жидкой ванны в корне шва осуществляют расплавлением кромок основного металла рельсов.
www.findpatent.ru
Сварка рельсовых стыков: технология (видео)
Сварка рельсовых стыков весьма востребована на сегодняшний день. Как известно, когда подвижной состав проходит сборные стыки, они начинают с высокой скоростью расстраиваться. При этом исчезает плавный ход, из-за чего разрушается верхнее покрытие железнодорожного пути. А данный вариант поможет исправить ситуацию.

Схема стыковой сварки.
Основные характеристики
Требуется прокладывать рельсовые пути, которые имеют сваренные стыки, на любых видах путей, в результате получается бесстыковой рельс.
Рельсовая нить разрывается именно в местах, где образован стык. Такой разрыв, даже при установке стыковых накладок, оказывает большое влияние на жесткость конструкции, начинают увеличиваться просадки.
В результате при прохождении подвижного состава рельсового стыка колесо ударяется о головку торца принимающего рельса. Из-за многочисленных ударов в стыковые соединения начинает быстро изнашиваться ходовая часть вагонов, а также уложенных рельсов. За счет сильных ударов колесной пары по набегающему рельсу появляется сколы рельсовых головок и их сминание. Обычно такие дефекты обнаруживаются в 60 см от места стыка. Рельсы начинают ломаться в болтовых отверстиях, изгибаются накладки, деформируются стыковые болты. Все перечисленные недостатки не касаются бесстыкового пути, причем он обладает несколькими положительными качествами:

Схема конструкции контактной сварки.
- почти на 30% снижаются затраты на обслуживание рельсового пути;
- значительно экономится электроэнергия, снижается расход топлива примерно на 10%;
- увеличивается срок эксплуатации верхних путей,
- подвижной состав может работать намного дольше;
- пассажиры испытывают больший комфорт при движении поезда;
- становится надежнее работа автоблокировки и электроцепей.
За счет таких положительных качеств бесстыковой вариант был принят на вооружение всеми главными железнодорожными линиями в мире.
Иногда выбор определенного вида сварки стыков зависит от стоимости работ и производительности. Такой выбор влечет за собой появление в особо ответственных конструкциях сварочных соединений, качество которых находится на очень низком уровне.
Вернуться к оглавлению
Практические рекомендации
Чтобы получить отличное сварное соединение, требуется иметь материал с хорошей свариваемостью. В основном свариваемость характеризует свойства металла, существующую реакцию на сварочный процесс, а также способность получать такое сварочное соединение, которое будет отвечать всем заданным технологическим требованиям.
Когда детали выполнены из материала, свободно поддающегося сварочному процессу, с получением высококачественного шва особых условий не требуется. Но для деталей из плохо свариваемого материала требуются дополнительные технологические условия. Иногда применяется специальный вид сварки, который намного дороже и сложнее. Причем выполнение работ требует строгого соблюдения технологического процесса.

Сварка рельсов востребована на сегодняшний день так как рельсовая нить разрывается и быстро изнашиваться ходовая часть вагонов.
В состав стали для рельсов входит очень много углерода, почти 82%. Этот материал относится к группе материалов, имеющих плохую свариваемость. При сварке возможно появление трещин, что совершенно недопустимо на рельсах. В них концентрируется напряжение, которое может привести к разрушению стыкового соединения и крушению состава.
Сегодня известно два вида сварки рельсовых стыков:
- контактная;
- алюмотермитная.
Большое распространение получила контактная сварка, однако у нее есть несколько серьезных недостатков, ограничений, когда проводятся ремонтные работы железнодорожных путей:
- для сварки требуются специальные рельсосварочные машины, стоящие очень дорого;
- длительности доставки оборудования и его последующая эвакуация;
- для проведения работ необходимо задействовать многочисленные бригады;
- за неимением большого количества времени, приходится постоянно выполнять работу без соблюдения технологического процесса, в результате чего стык получается очень низкого качества;
- невозможно выполнить сварку стыка прямо в том месте, где переводятся стрелки.
Контактная сварка стыков проигрывает алюминотермитной сварке рельсов. Для нее необходимо иметь:
- сложное и очень дорогое оборудование;
- многочисленную бригаду;
- перерывы при движении поездов.
Алюминотермитная сварка рельсов делается очень быстро. На операцию уходит примерно полминуты. Если считать подготовительные работы и завершающую обработку сварочного шва, требуется около 45 минут.
Надо сказать, что такая сварка позволяет одновременно сваривать несколько стыков, в результате сокращается время, затраченное на работу.

Рельсовые стыки с различной формой стыкуемых торцев.
Для сварки стыка необходимо три человека. Их обучение проходит в самые короткие сроки. Масса применяемого оборудования достигает 350 кг. Для проведения сварочных работ, когда используется алюмотермитная сварка и проводятся другие специальные операции, применяются автономные источники подачи топлива.
Чтобы проводить алюминотермитную сварку рельсов, инженерами было создано переносное миниатюрное оборудование, которое может функционировать в автономном режиме прямо в полу.
Технологи смогли подобрать определенный состав термитного раствора и его зернистость. Это помогло добиться термитной реакции, при которой не возникает взрывов, не наблюдается затухания и поддерживается самая оптимальная скорость и нужная температура всех материалов, участвующих в реакции.
Алюминотермитная сварка состоит из нескольких основных технологических шагов:
- начального высокотемпературного подогрева;
- окончательной сварки рельсов.
Вернуться к оглавлению
Дополнительные моменты
В качестве подогрева применяется специальная многопламенная горелка.
Операция длится примерно 7 минут. Контроль над подогревом и его окончанием выполняется визуально. Здесь очень важно, чтобы подогрев выполнял высококвалифицированный сварщик.

Схема электроконтактной сварки.
Такой предварительный подогрев является важной составляющей технологического процесса при алюминотермитной сварки рельсов. В результате не происходит несплавлений, сводится к минимуму возникновение закалочных структур. Когда выполняется сварочная операция, заметно снижаются параметры остаточных напряжений сварочного шва и околошовной зоны, не возникает появление трещин.
После того как рельс прошел этап подогрева, выполняются сварочные работы, происходит возгорание термитной смеси. Начинается процесс реакции воспламенения термита. Он в автоматическом режиме выпускается в межстыковой рельсовый зазор.
После долгих экспериментов было доказано, что главными технологическими параметрами, которые влияют на качество будущего сварочного шва, можно считать;
- время предварительного подогрева;
- мощность используемого газового пламени.
Чтобы получить бесстыковой рельсовый путь с применением алюминотермитного способа, разрешается использовать рельсы, бывшие в употреблении, а также их новую модификацию. Для такой сварочной операции применяют:
- упрочненные рельсы;
- неупрочненные рельсы;
- рельсы мартеновского производства;
- рельсы бессемеровского изготовления.
Можно сваривать таким образом рельсы самых разных железнодорожных путей: станционные, подъездные и даже стрелочные переводы.
Но помните: рельсы, которые будут свариваться, должны быть однотипными и обладать одинаковой группой годности.
expertsvarki.ru
способы и их основные особенности
При осуществлении монтажа, а также ремонтных работах на железнодорожном полотне, крановых установках, и других условиях, где применяются рельсы, используется особая технология сваривания. Так как в описываемых условиях необходима особая прочность, а также стойкость к различного рода нагрузкам, то сварка железнодорожных рельсов относится к отдельной категории сварки.
Электродуговая сварка
Стоит отметить, что одним из самых распространенных методов, который применяется при сварке рельсовых плетей и стыков рельс, является электродуговая сварка. В данном случае рельсы укладываются в необходимом положении, а пространство между их стыками послойно постепенно заполняется необходимым сварочным материалом. Последний расплавляется от температуры дугового разряда. Для сварки торцов железнодорожных рельсов данным способом может применяться переменный ток, поступающий от трансформатора или же постоянный ток, получаемый от мобильного сварочного агрегата.
Самым оптимальным вариантом является ванный метод. При этом концы рельсов, предварительно обрезанные перпендикулярно их продольной оси, монтируются без перелома. При этом в профиле должно быть возвышение от 3 до 5 миллиметров. В такой позиции рельсы должны быть закреплены с зазором от 14 до 16 мм.
Между торцов железнодорожных рельсов вводится электрод, через который пропускается ток 300-350 ампер. В итоге, расплавленный метал электрода заполняет зазор между торцами, равномерно по всему сечению.
Для исключения растекания металла используются различные методы закрывания зазора между рельсами. После сваривания место работы шлифуется по всему периметру.
Термитная сварка
Технология данного типа сварки заключается в реакции, которая возникает при контакте окиси железа и алюминия. Сталь, которая возникает в описываемых условиях при температурах более 2000 градусов, должна заливаться в огнеустойчивую форму, которая полностью идентична геометрии самого рельса.
Термитная технология была открыта еще в 1896 году известным профессором Гансом Гольдшмидтом. По сути термитная технология представляет собой восстановление железа из окиси с использованием алюминия. При этом термитная реакция характеризуется выделением большого количества тепла.
Термитная технология еще именуется алюминотермитная сварка рельсов, так как в ней применяется алюминий. Интересно, что термитная реакция происходит на протяжении всего нескольких секунд после поджигания термитной порции. Кроме окиси железа и алюминия ,в состав данной смеси включаются частицы стали ,демпфирующие реакцию ,а также легирующие добавки. Последние служат для того, чтобы была получена сталь необходимого качества и параметров. Интересно, что в конце реакции осуществляется послойное разделение на жидкую сталь и легкий шлак, который оказывается сверху.
Термитная технология позволяет соединять между собой поверхностно-закаленные, объемно-закаленные, а также термически не упрочненные рельсы в любых комбинациях. Термитная сварка позволяет соответствовать высоким требованиям, которые сегодня выдвигаются к высокоскоростным магистралям и бесстыковым путям.
Газопрессовая сварка
Данная технологи основывается на соединении металлов при температуре, которая находится в пределах, ниже точки плавления, но при высоком давлении. Главные «плюсы» данной технологии:
- Однородная структура металла в области стыка железнодорожных рельсов;
- Высокое качество получаемого соединения.
Ввиду вышеописанных преимуществ, данный тип сварки очень эффективен при сварке тяжелых железнодорожных рельсов. Перед осуществлением собственно сварки, концы железнодорожных рельсов плотно приставляются друг к другу. При этом при помощи дисковой пилы рельсорезного станка или механической ножовкой осуществляется одновременное прорезывание торцов обеих рельсов. В итоге обеспечивается максимальная чистота металла, а также высокая плотность прилегания. Перед самим процессов сваривания торцы промываются четыреххлористым углеродом. Также дл я этих целей может применяться дихлорэтан. Подготовительный же этап перед непосредственно сваркой заключается в нагревании концов рельс, для которого применяются многопламенные горелки.
После этого концы рельсов должны быть зажаты при помощи гидравлического пресса с последующим нагревом до 1200 градусов при помощи все тех же многопламенных горелок. Последние осуществляют колебательные движения вдоль образованного стыка. Частота этих колебаний составляет 50 колебаний в минуту. Вместе с этим рельсы сжимаются с силой от 10 до 13 тонн, которая устанавливается специальными расчетами. В результате получается осадка около 20 мм. Для осуществления описываемых действий используются универсальные газопрессовые станки.
После завершения сваривания полученный стык обрабатывается. После этого производится также его нормализация.
Итоги
Итак, существует три ключевые технологии сваривания рельсов. Каждая из них обладает собственными «плюсами» и «минусами». Однако стоит отметить, что алюмотермитная сварка максимально соответствует всем современным жесточайшим требованиям к бесстыковым железнодорожным путям. Потому ее применение полностью обоснованно при построении и ремонте современных магистралей.
Похожие статьиgoodsvarka.ru
Сварка рельсов
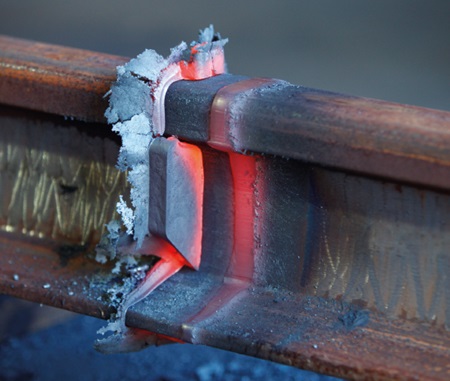
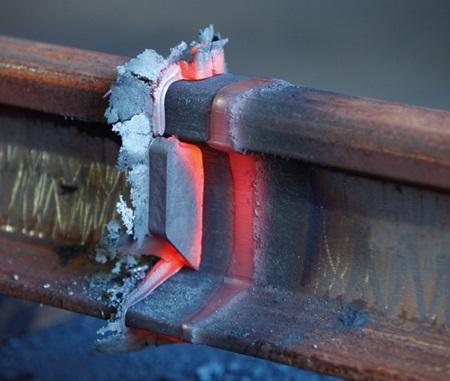
При работах с крановыми установками и выполнении монтажа железнодорожного полотна возникает необходимость соединения и сварки рельсов. В данном случае используется специальная технология, которая обеспечивает особую прочность соединения и устойчивость к повышенным нагрузкам. Необходимо сказать, что такие работы относятся к отдельной категории сварочных работ, об особенности которых мы и расскажем в этой статье.
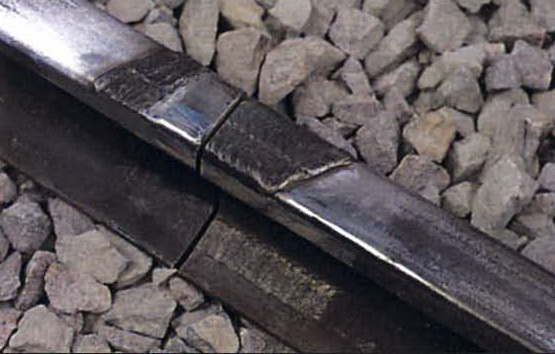
Сварка может выполняться следующими технологиями:
- Термитная.
- Электродуговая.
- Газопрессовая сварка.
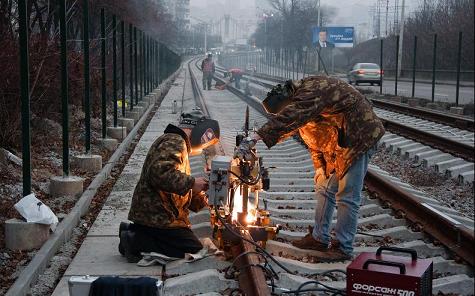
Каждая из этих технологий имеет свои определенные недостатки и преимущества. Поговорим поподробнее о таких способах сварки.
Электродуговая сварка стыков рельсов
На сегодняшний день данная технология получила наибольшее распространение, что объясняется простотой оборудования, легкостью самой работой и качеством выполненного соединения. При выполнении сварочных работ рельсы укладываются в нужном положении, после чего имеющееся между стыками послойно пространство заполняется сварочным материалом. Расплавление сварочного материала обеспечивается за счет высоких температур дугового разряда. При необходимости сварки торцов рельсов используется переменный ток от трансформатора. Также возможно использование мобильных сварочных аппаратов, работающих от постоянного тока.
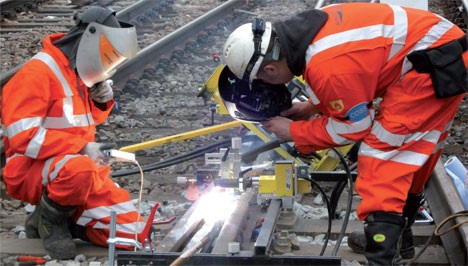
При использовании электродуговой технологии возможно выполнение сварка рельсовых стыков ванным методом, при котором рельсы, обрезанные перпендикулярно своей оси, монтируются внутри ванны. В ванне проводится их качественное сваривание друг с другом. При данном методе сварки рельсы закрепляются с зазором не более 16 миллиметров. Возвышение профиля может колебаться в диапазоне 3-5 миллиметров.
При использовании ванного метода между торцов располагают электрод, по которому подается электрический ток мощностью порядка 350 Ампер. Электрод быстро заполняет зазор между соединяемыми рельсами, равномерно распределяя расплавленный материал по всему сечению. Данный метод исключает растекание металла, при этом обеспечивается максимально качественное закрытие зазора между соединенными металлическими элементами. После завершения сварки необходимо будет зашлифовать соединительный шов по периметру.
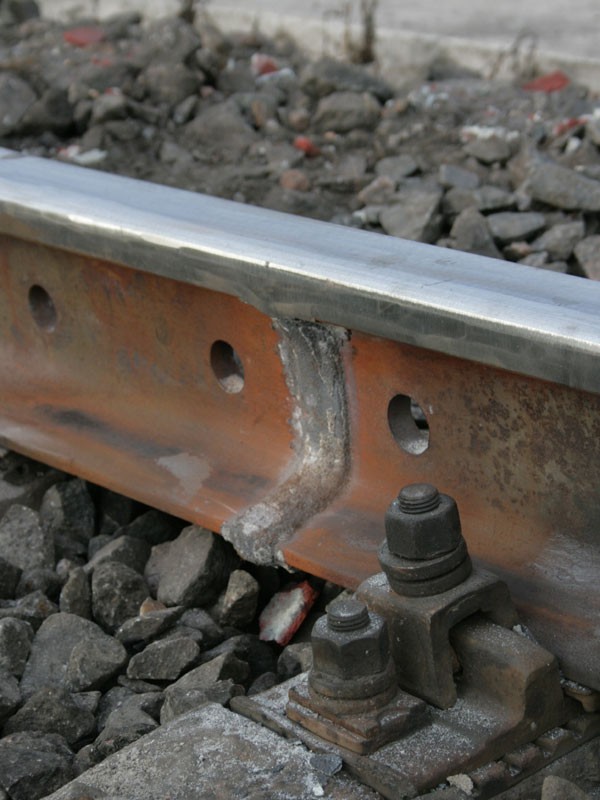
Алюминотермитная сварка рельсов
Метод термитной сварки основывается на свойстве окиси алюминия и железа вступать друг с другом в реакцию при высоких температурах. Такую термитную сварку также называют алюминотермитной технологией. Для выполнения такой сварки используется устойчивая к высоким температурам форма, которая по своему внешнему виду идентична геометрии рельсов. Такая форма должна выдерживать температуру больше 2000 градусов, при которой возникает контакт алюминия и железа.
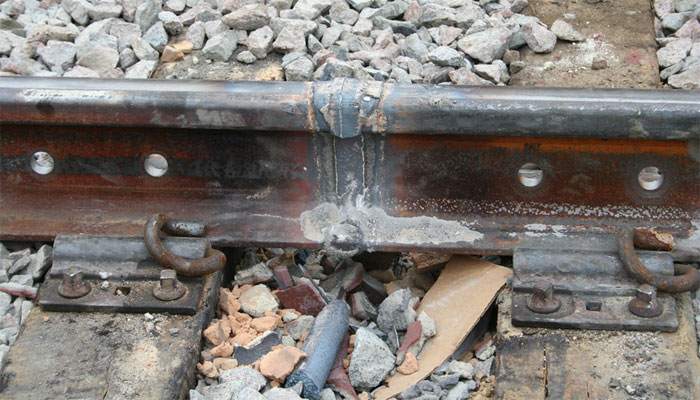
Открыта данная технология сварки еще в конце 19 века. Однако по причине ее технологической сложности распространение она получила лишь относительно недавно. Основные трудности при выполнении такой термитной сварки заключаются в том, что реакция окиси алюминия и железа возникает лишь при температурах в несколько тысяч градусов. Соответственно требовалось нагреть до таких экстремальных температур, как сами рельсы, так и использовать соответствующую форму, способную не расплавляться и сохранять свою геометрию.
Для соединения металлов необходимо поджечь термитную смесь, которая быстро выгорает с образованием высокой температуры. Такая термитная порция содержит не только окиси алюминия и железа, но и разнообразные легирующие добавки. Такие добавки необходимы для получения максимально прочного соединения с нужными параметрами устойчивости к механическим воздействиям. Во время такой температурной реакции происходит послойное разделение легкого шлака и жидкой стали. Шлак при этом оказывается сверху и в последующем с легкостью удаляется из соединения.
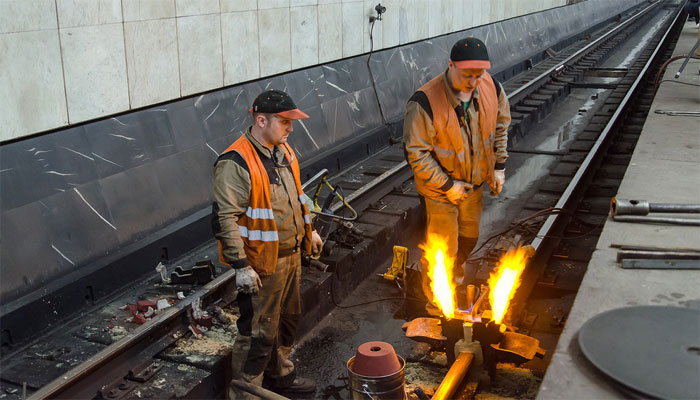
Термитный способ сварки рельсов позволяет соединять объемно-закаленные и поверхностно-закаленные материалы. Необходимо сказать, что при помощи подобной технологии обеспечивается прочное и долговечное соединение, поэтому термитный способ сварки нашел применение при изготовлении безстыковых высокоскоростных железнодорожных магистралей.
Газопрессовая технология
Эта оригинальная технология соединения рельсов подразумевает использование температуры ниже точки плавления, однако за счет воздействия высокого давления обеспечивается качественное соединение рельсов. Из преимуществ данной технологии сварки можно отметить следующее:
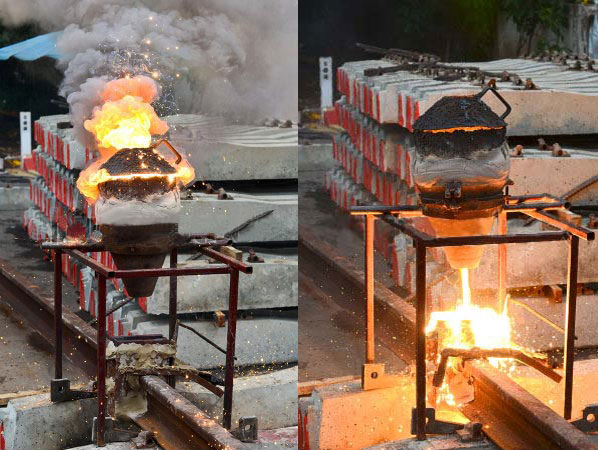
- Отличные показатели качества выполненного соединения.
- Однородная структура стыка железнодорожного покрытия.
- Высокая производительность.
- Минимальный расход наплавляемых материалов.
Такая газопрессовая сварка широко применяется при соединении тяжелых железнодорожных рельсов. При выполнении используется специальное оборудование, которое позволяет обеспечить максимально высокое давление соединяемых рельсов. Металлические изделия плотно прижимаются друг к другу, после чего при помощи специальной струбцины концы нагреваются, а за счет высокого давления рельсы соединяются друг с другом. В процессе такой работы необходимо обеспечить промывку свариваемых элементов треххлористым углеродом. Это позволяет обеспечить соединение металлических элементов на молекулярном уровне.
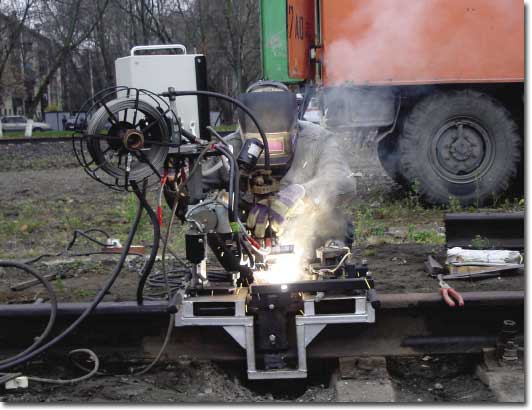
Показатели рабочей температуры при газопрессовой технологии составляют порядка 1200 градусов. Для такой работы используются многопламенные горелки и мощные гидравлические прессы. Для качественного разогрева места соединения используют многопламенные горелки, осуществляющие в области сварного стыка многочисленные колебания, что и позволяет качественно разогреть металл. Гидравлический пресс, используемый для соединения рельсов, обеспечивает давление в 13 тонн и более. Усадка рельсов при их соединении данной технологией составляет около 20 миллиметров.
Заключение
Существующие в настоящее время технологии позволяют получить долговечное, надежное и устойчивое к механическим нагрузкам соединение. Выбор той или иной технологии выполняется в зависимости от доступного оборудования и конкретных разновидностей соединяемых рельсов. Необходимо сказать, что качественный выбор такого используемого оборудования и следование всей технологии работ позволит вам гарантировать качественно выполненную сварку рельсов.
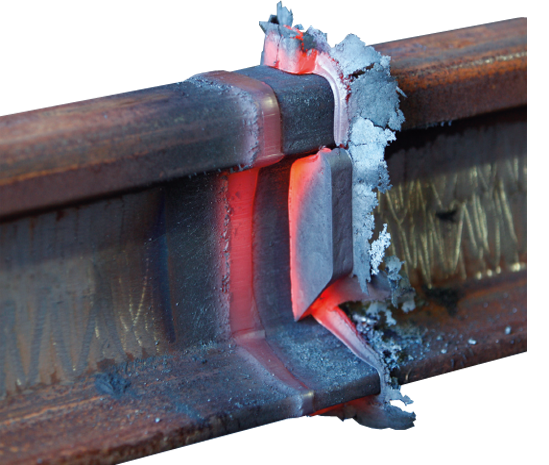
svarkagid.com
Электроды для сварки рельсов: какие использовать?
Даже отбракованные или отслужившие свой срок рельсы являются желаемым приобретением для любого рачительного домовладельца. Ведь прочный и стойкий к коррозии рельс может заменить любую металлическую балку.
Однако монтирование конструкций из этого сорта металлопроката весьма затруднительно. Тяжелые рельсы требуют прочных сварочных швов. Железнодорожники используют для этих целей особый термитный состав. Ну а в быту необходимы специальные электроды для сварки железнодорожных рельс. И в этой статье мы опишем именно такую продукцию, с помощью которой вы сможете состыковать рельсы любым, удобным для вас способом.
«Рельсовые» электроды
Решая, какими электродами варить рельсы, стоит принять во внимание толщину данного сорта металлопроката. Поэтому источником присадочного материала в процессе сварки рельс могут быть только особые электроды серии УОНИ, предназначенные для стыковки толстотелых конструкций. Причем для сварки рельсов достаточно «младших» представителей этой серии – электродов УОНИ 13/45 и 13/55, которыми можно стыковать заготовки из высокоуглеродистых или низколегированных сталей.
От прочих источников присадочного материала электроды УОНИ 13/45 и 13/55 отличаются особым флюсом (покрытием), в состав которого входят ферромарганцевые руды, графит, кремний и прочие материалы.
Благодаря такому многокомпонентному миксу обеспечивается устойчивое горение дуги, передающей высокую температуру в зону сварки, и подавляется процесс образования пор в сварочном шве. Интересен и состав электродной проволоки. Ее изготавливают из железоуглеродистого сплава, легированного никелем и молибденом. Диаметр проволоки – 2-5 миллиметров.
В итоге, опираясь на особый состав флюса и присадочного материала, серия УОНИ обеспечивает не только высокую скорость работы, но и не менее высокую прочность сварочного шва.
Подготовка электрода к сварке
Электроды для сварки рельсов – работают в очень сложных условиях. Ведь толщина стыкуемых кромок в данном случае может равняться нескольким десяткам сантиметров.
Поэтому к качеству таких электродов предъявляют особые требования, а именно:
- На покрытии таких электродов не должно быть крупных трещин.
- Влажность покрытия должна соответствовать определенному значению.
И если соответствие электрода первому требованию можно проверить визуально, то с влажностью все намного сложнее. Поэтому перед сваркой все электроды из серии УОНИ подвергают обязательному прокаливанию (подсушиванию) в особой установке.
Эта процедура выглядит как прогрев изделия до температуры в 350-400 градусов Цельсия. Причем электроды загружаются в уже разогретый «жарочный шкаф» и «томятся» в нем около 1-2 часов.
После такой подготовки электроды можно использовать в любом положении, формируя с их помощью и нижние, и потолочные, и вертикальные швы на постоянном токе, и обратной полярности подключения.
Единственное «противопоказание к применению» для серии УОНИ – это сварка по направлению сверху вниз.
steelguide.ru