Вы узнаете как производятся трубки из пластика: 3 основных момента. Экструдер для пластика
виды машин для пластмассы, принцип работы
Развитие технического прогресса привело к появлению различных технологий, которые позволяют производить изделия, отличающиеся улучшенными эксплуатационными характеристиками. Одной из востребованных в настоящий момент является экструзия. Собой она представляет технологический процесс переработки пластмасс, из которых изготавливают разнообразные детали, а также производят различную профильную продукцию.
Сама технология состоит в приготовлении сплава из полимерных материалов с последующим его продавливанием через специальные насадки, которые придают ему определенную форму. Основным элементом линии по производству изделий из пластика является экструдер.
Принцип действия и конструкция
Следует сказать, что экструзия является далеко не новой технологией. Ее история насчитывает более шести десятилетий. За это время было создано большое количество конструкций машин, с помощью которых обеспечивается ее реализация. Принцип действия этого прибора базируется на сути самого технологического процесса.
Технологический процесс экструзии является сложным физико-химическим процессом, на который оказывают воздействие механические усилия в условиях высокой температуры и влаги. Нагрев продуктов переработки происходит благодаря тому, что возникающая при борьбе с внутренним трением, а также при пластических деформациях механическая энергия превращается в тепло.
В процессе экструзионной обработки существует несколько сменных параметров. К числу наиболее важных следует отнести:
- состав сырья;
- влажность;
- его природа.
При протекании экструзионного технологического процесса может происходить изменение:
- температуры материала;
- давления;
- интенсивности и длительности воздействия на исходное сырье.
Принцип работы экструдера
Само по себе такое оборудование представляет электромеханическое устройство, основным предназначением которого является осуществление процесса формовки профильных деталей из пластика или его полуфабрикатов. В своем составе общее устройство экструдера для пластика содержит следующие компоненты:
- корпус системы нагрева полимерных материалов. В качестве основного источника тепловой энергии при осуществлении этого технологического процесса могут выступать обычные резистивные или индукционные системы. При использовании последних возникновение высоких температур происходит за счёт наведения на корпус высокочастотных индукционных токов Фуко;
- узел нагрузки. Через этот элемент в полость корпуса различными способами поступает исходное сырье;
- рабочий орган. Он создает в оборудовании необходимое давление, благодаря которому обеспечивается перемещение сырья непосредственно от узла загрузки до насадок, которые формуют из полимерных материалов готовые изделия. При использовании экструдера применяются разнообразные физические принципы, поскольку это устройство может иметь разные варианты исполнения — шнековый, дисковый, поршневый. В настоящий момент чаще других применяются шнековые экструдеры;
- экструзионная головка. По-другому специалисты называют ее фильерой. Именно она обеспечивает форму изделий, которая получается по завершении технологического процесса;
- механический привод. В этом оборудовании он представлен двигателем и редукторной системой. Благодаря ему обеспечивается создание и передача необходимого усилия на рабочий орган;
- система контроля и управления. Благодаря ей обеспечивается поддержание необходимого технологического режима.
В качестве исходного материала обычно выступают гранулы и порошок. Они загружаются в оборудование, а далее под действием рабочего органа происходит их перемещение в рабочую зону корпуса. Там под воздействием давления, силы трения и температуры подаваемое извне исходное сырье нагревается, а в процессе его плавления возникает состояние, которое требуется по условиям технологического процесса.
Во время движения исходного сырья в полости корпуса происходит его тщательное перемешивание до состояния однородной гомогенизированной массы.
В условиях высокого давления происходит продавливание расплава при помощи формующих головок и сетчатых фильтров. В результате обеспечивается окончательная гомогенизация и придание материалу заданного профиля.
После этого материал естественным образом охлаждается или же применяется принудительный способ с последующей полимеризацией. В конечном итоге получаются изделия, имеющие необходимую конфигурацию и обладающие заданными механическими и физическими свойствами.
Виды экструдеров
Современные модели экструзионных установок могут различаться между собой как конструкцией рабочего органа, так и назначением.
Одношнековый
Среди всех разновидностей экструзионного оборудования наиболее распространенным является шнековое. Такие машины удовлетворяют всем требованиям экструзионного процесса. В этих агрегатах в качестве основного рабочего органа применяется шнек. Специалисты называют его винтом Архимеда. Многие прекрасно знают этот рабочий элемент по домашним мясорубкам.
При использовании экструдера для производства изделий из пластмассы лопасть шнека захватывает сырье в зоне загрузки, а далее происходит его последовательное перемещение по всей длине цилиндра корпуса, начиная от зоны нагрева через участок гомогенизации и формовки. В зависимости от особенностей технологической карты, которую имеет оборудование, а также вида используемого для производства изделий исходного сырья шнеки могут предусматривать несколько вариантов исполнения — конические, цилиндрические и нормальные быстроходные.
Также могут использоваться шнеки, которые сужаются к выходу. Для этого оборудования в качестве главного параметра специалисты рассматривают соотношение рабочего диаметра шнека и его длины. Также различаются шнеки по шагу витков и их глубине.
Главный недостаток одношнекового экструдера заключается в том, что не всегда имеется возможность для их применения. Например, если в качестве исходного сырья выступают порошковые полуфабрикаты, то наличие одного винта в составе оборудования не позволяет справиться с перемешиванием массы в процессе ее расплавления и последующей гомогенизации. В таких случаях выбор делают в пользу двухшнековых экструдеров.
Двухшнековый
Особенность этого оборудования состоит в том, что в нём винты сцеплены между собой. Поэтому при использовании таких экструдеров имеется возможность совершения шнеками параллельных и встречных вращательных движений. Эти рабочие части оборудования могут быть прямыми или коническими.
Использование подобных машин приводит к тому, что в процессе разогрева исходного сырья его смешивание и гомогенизация осуществляется более тщательно. В конечном итоге на головку для формования изделий поступает однородная и дегазированная масса.
Необходимо отметить следующий момент: в отдельных технологических процессах могут использоваться экструдеры, имеющие большее количество шнеков — до 4. Помимо этого нередко применяется планетарный автомат, когда число шнеков, вращающихся вокруг центрального винта, доходит до 20.
Необходимость в применении такого оборудования возникает при использовании в качестве исходного сырья отдельных видов пластиков, которые в условиях воздействия высоких температур имеют склонность к разрушению. Говоря другими словами, могут лишаться своих основных физических качеств. Таким образом, использование подобных экструдеров обеспечивает нагрев сырья за счет силы трения и высокого давления.
Производство ПВХ-профилей
В настоящий момент востребованным видом изделий являются пластиковые и композитные профили. В большинстве случаев производители изготавливают их, используя метод экструзии. Для изготовления такой продукции в зависимости от применяемого материала, а также сложности и формы изделия задействуются одно- или двухшнековые аппараты, которые имеют соответствующие формовочные головки.
Ассортимент выпускаемых с использованием экструдеров изделий довольно широкий, начиная от тонких нитей и полос и заканчивая листами крупных панелей, которые имеют профиль сложной геометрии. Пластиковые окна и двери, выпускаемые сегодня многими компаниями, собираются с использованием именно ПВХ-профилей, которые изготовлены на экструзионном оборудовании.
При производстве ПВХ-профилей многие производители добавляют в полимерный состав специальные компоненты, что дает возможность изготовления сложных композитов. Например, сегодня многие производители выпускают дерево-пластиковые изделия, которые довольно часто используются для изготовления разных строительных конструкций.
Изготовление труб
В такой сфере, как производство трубных изделий важным условием является отсутствие пузырьков газа в гомогенизированной смеси. По этой причине экструдеры, которые задействуются при производстве такой продукции, производители оснащают системами дегазации. В большинстве случаев применяются шнековые установки. Помимо прочего используют барьерные шнеки, благодаря которым обеспечивается надежное разделение твердого полуфабриката от полностью расплавленного. За счет этого достигается сохранение однородности состава, что положительным образом отражается на качестве выпускаемой трубной продукции и её эксплуатационных характеристиках.
Экструдеры для полиэтилена
Все плёнки, изготовленные из полимерных материалов, производятся компаниями исключительно с использованием способа экструзии. Для производства подобной продукции применяется выдувной экструдер. У оборудования, используемого для производства стрейч-пленки, формовочный узел может иметь вид узкой щели. При применении такого оборудования на выходе получается однослойная пленка, которая имеет необходимые параметры толщины и ширины.
В отдельных моделях могут использоваться круглые щелевые фильеры большого диаметра. При использовании мини-экструдеров можно получить пленку с шириной рукава до 300 мм и с параметром толщины 600 мкм. Такие устройства обладают компактными размерами, что обеспечивает возможность их установки даже в небольшом по площади помещении.
Экструзионные линии
В условиях промышленных предприятий экструзионное оборудование следует рассматривать в качестве главного компонента линии по осуществлению этого процесса. Помимо основного оборудования — экструдера она включает и целый набор других механизмов и устройств:
- намоточные и отрезочные механизмы. Они используются для приведения изделий в необходимый для складского хранения и транспортировки вид;
- маркирующие и ламинирующие системы различного принципа действия;
- механизмы протяжки готовых профилей;
- система охлаждения. Её установка выполняется на выходе экструдера, чтобы повысить скорость процесса полимеризации готовых изделий. Эти системы могут быть различного типа — воздушные или в виде охлаждающей ванны;
- система подготовки и загрузки сырья. В отдельных случаях полуфабрикат необходимо предварительно подвергнуть процедуре просушивания и последующей калибровке перед тем, как подавать его в загрузочный бункер.
В составе оборудования могут использоваться и другие механизмы, а также применяться технологические устройства для автоматизации непрерывного процесса производства.
Подводя итоги
Экструзионная технология является довольно популярной в настоящее время. Ее используют при производстве различных изделий. В основном она применяется для изготовления продукции из пластика. Знакомые каждому в нашей стране пластиковые окна и двери изготавливают с использованием этого процесса. Для производства продукции используется такой прибор, как экструдер. Это оборудование отличается несложным устройством, поэтому изготовить экструдер для пластика своими руками — вполне осуществимая задача.
Особенность этого процесса заключается в предварительном подогреве сырья, которое потом подвергается процедуре плавления в условиях определенного температурного режима и давления. Далее полимерная масса продавливается через формовочные насадки, что и позволяет получить изделия с нужными физическими и качественными характеристиками.
tokar.guru
Устройство для литья пластика (экструдер)
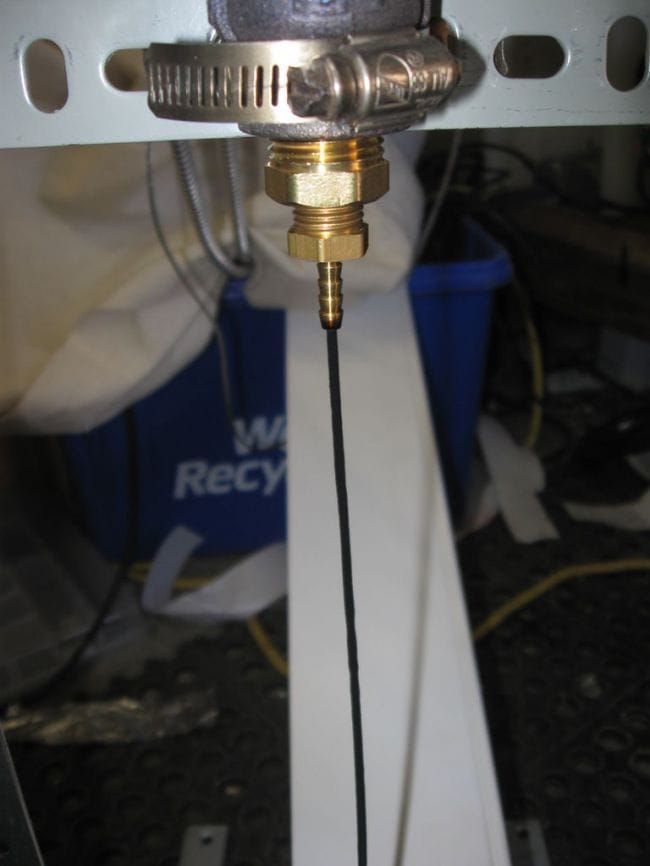
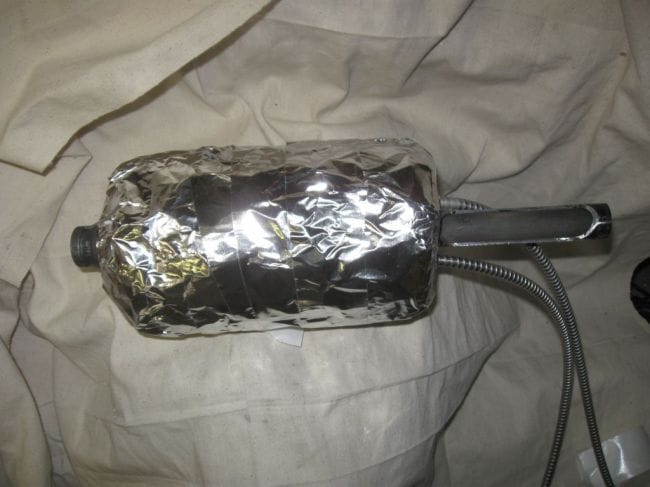
Экструзия (технологический процесс) — метод и процесс получения изделий из полимерных материалов путём продавливания расплава материала через формующее отверстие в экструдере.
Говоря простым языком, в камере устройства пластмасса расплавляется и под давлением выдавливается через сопло головки в пресс-форму.
Инструменты и материалы:-Металлическая труба с резьбой на конце;-Головка торцевая;-Удлинитель для головки;-Сварочный аппарат;-УШМ;-Тиски;-Напильник;-Перфорированный уголок;-Два уголка-кронштейна;-Медная трубка;-Крепеж;-Металлический хомут;-Нагревательный элемент;-Терморегулятор с датчиком;-Стекловолокно;-Алюминиевый скотч;-Фитинги;-Металлическая полоса;-Угольник;-Дрель;
Шаг первый: поршеньКамеру экструдера будет из металлической трубы 20 мм. Внутренняя стенка трубы должна быть ровная без шва. Внутрь камеры будет закладываться пластик, нагреваться и выдавливаться через сопло. Для выдавливания нужен поршень. Поршень мастер изготовил из торцевой головки. Подобрал головку по диаметру трубки. Установил ее на удлинитель. Приварил головку к удлинителю. Заварил торцевое отверстие головки.
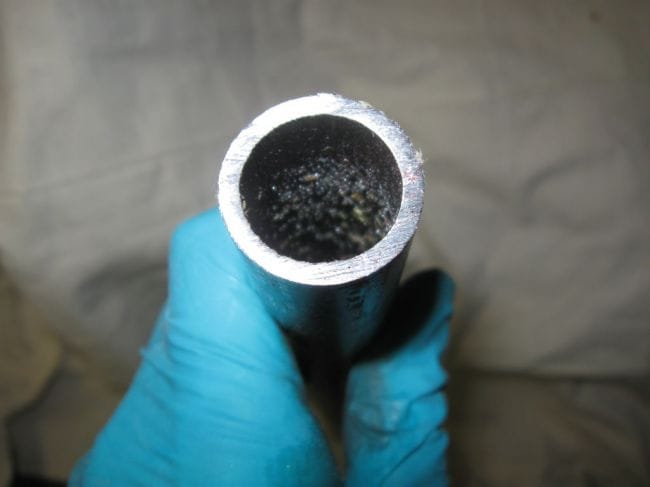
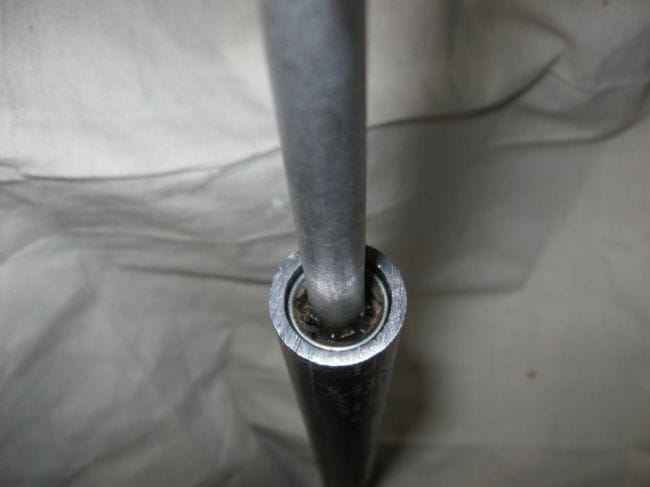
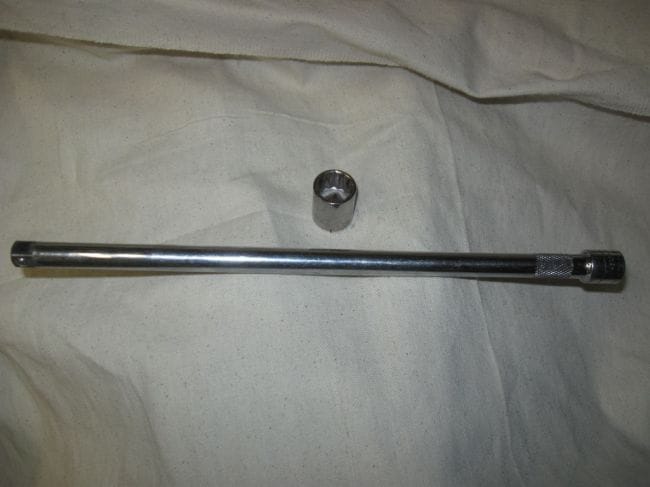
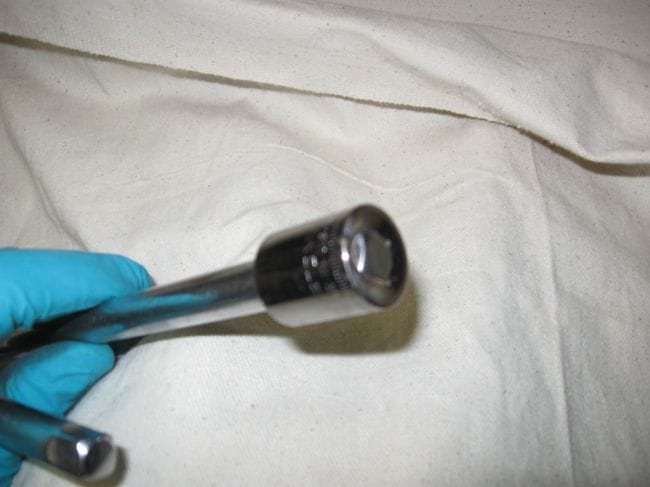
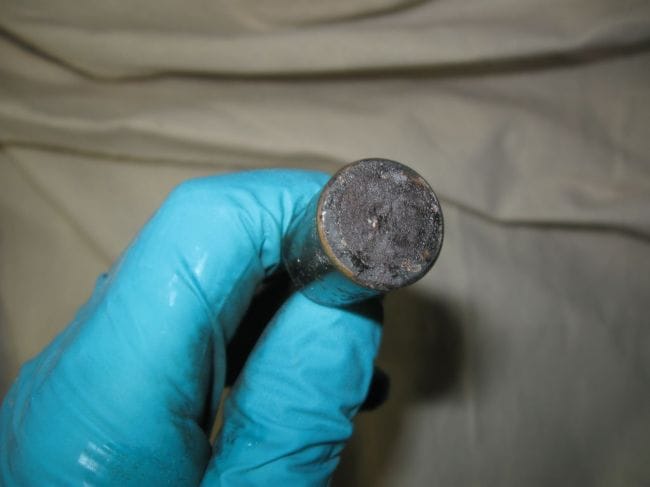
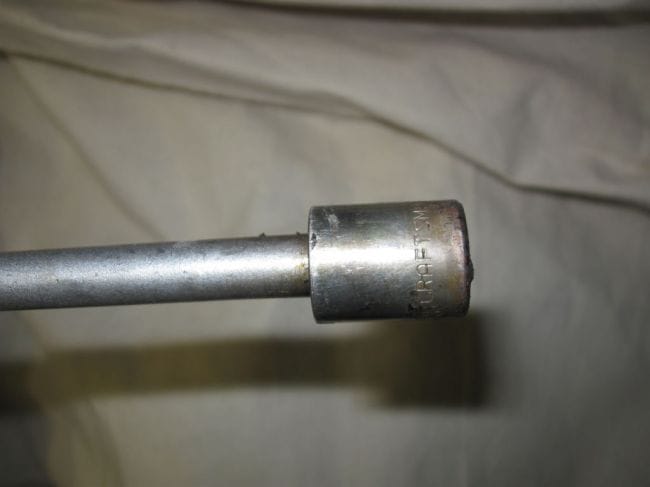
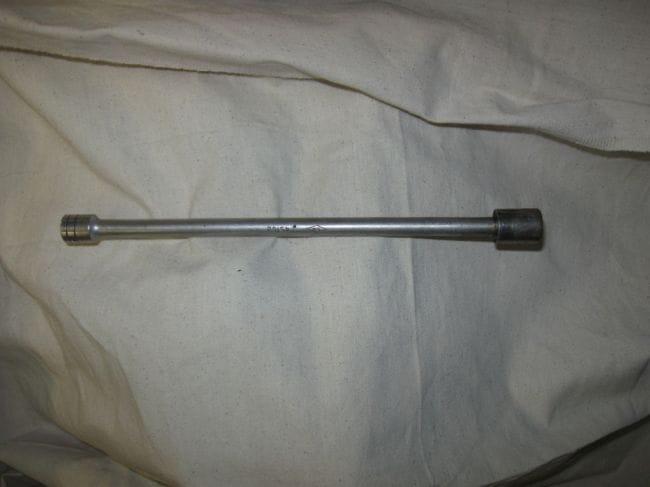
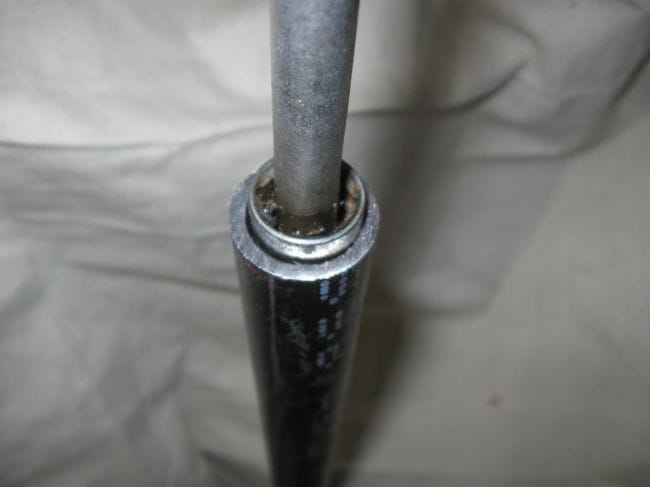
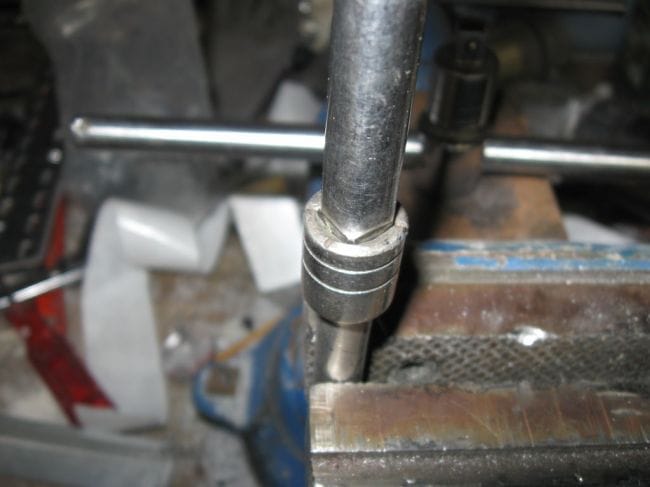
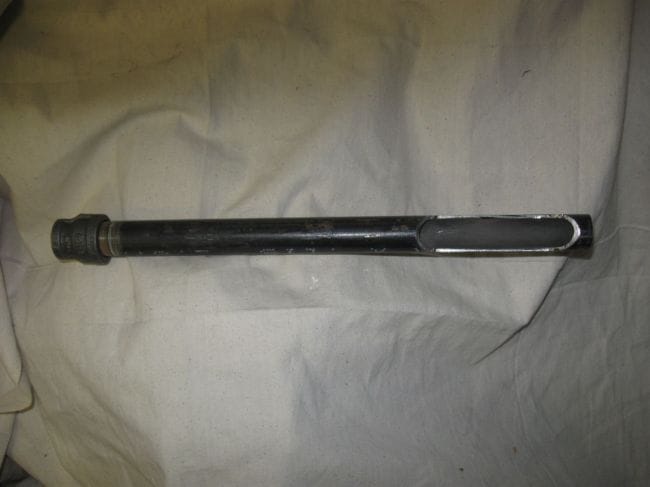
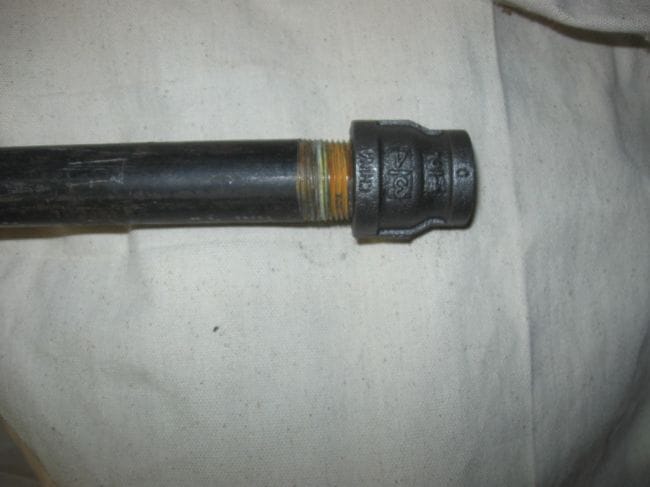
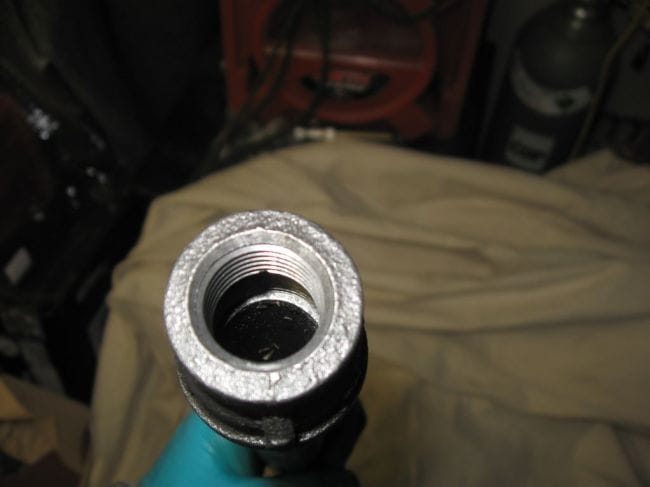
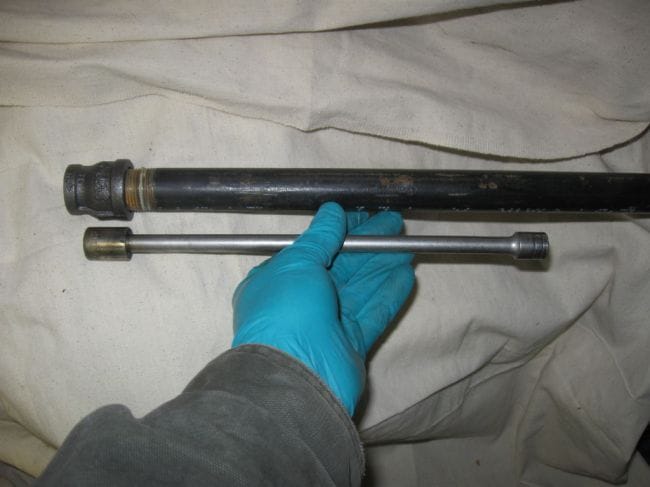
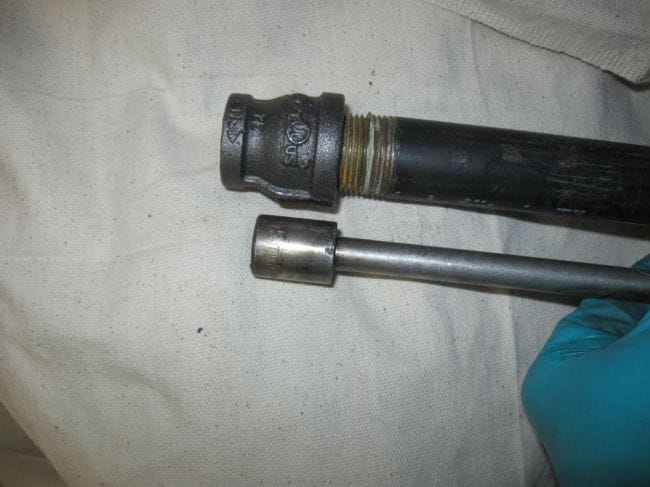
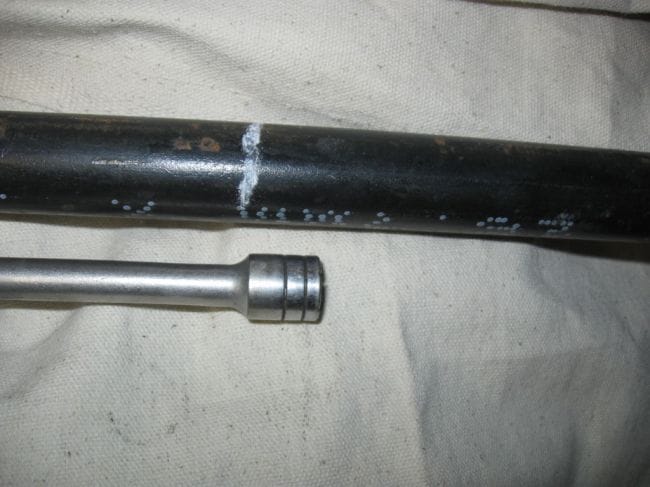
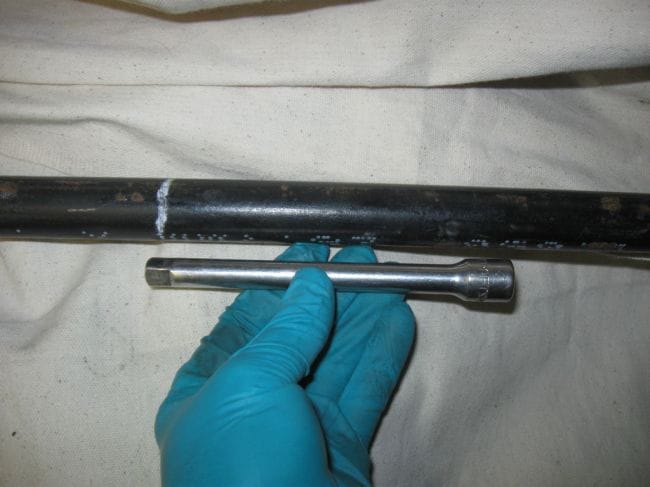
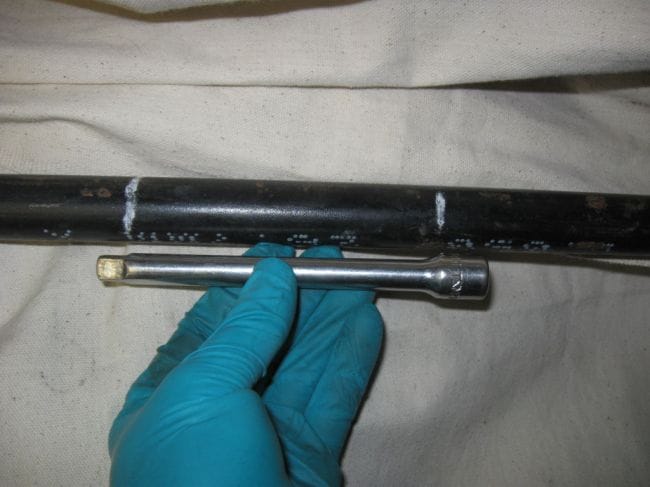
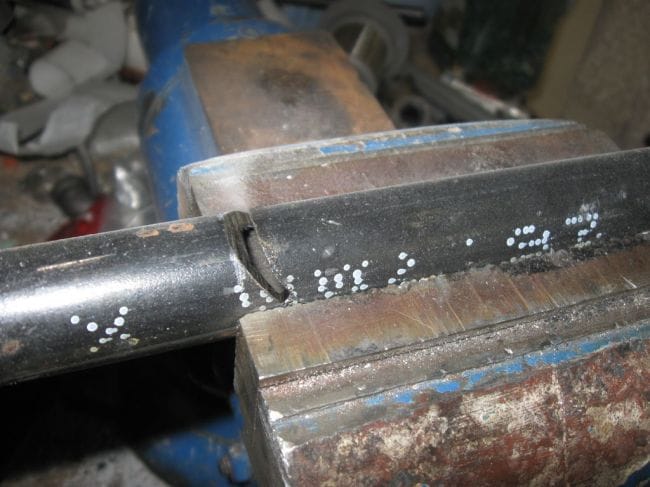
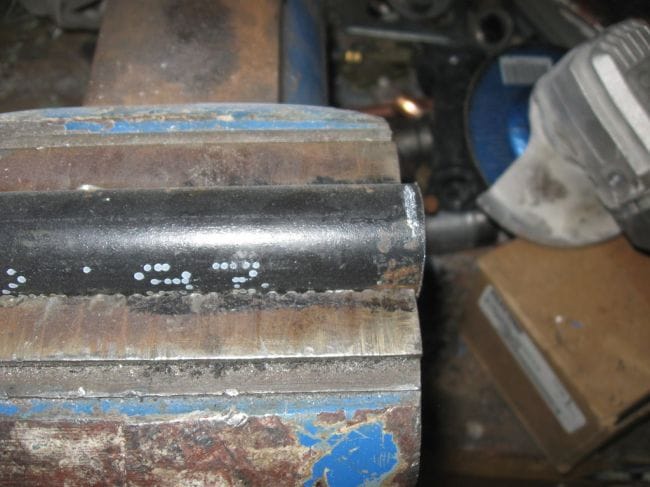
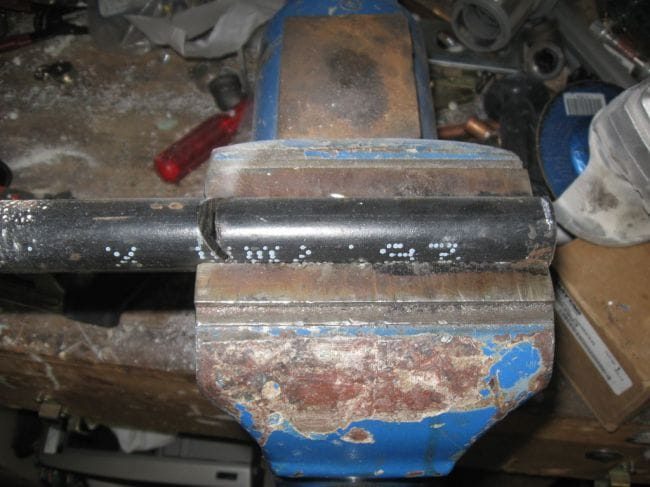
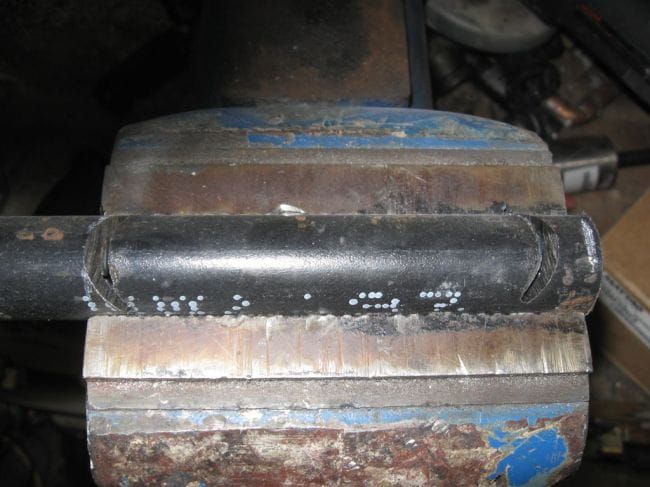
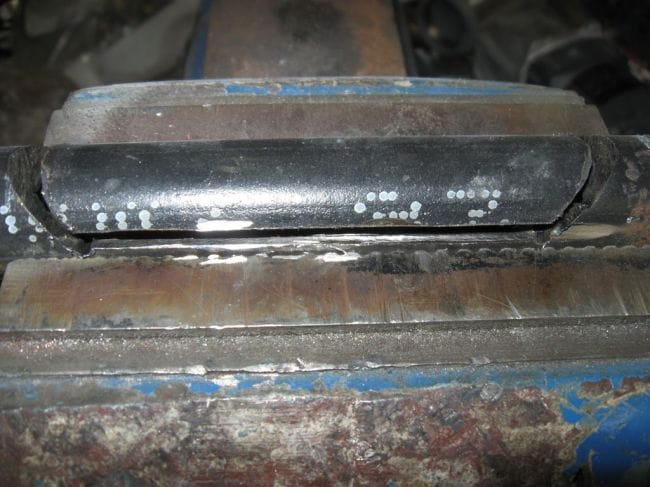
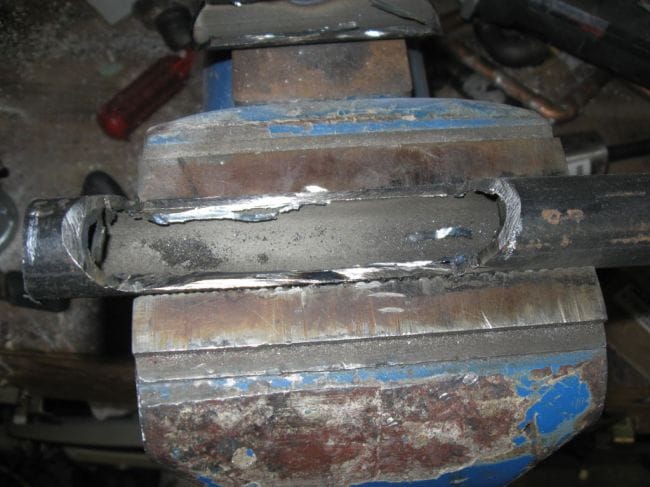
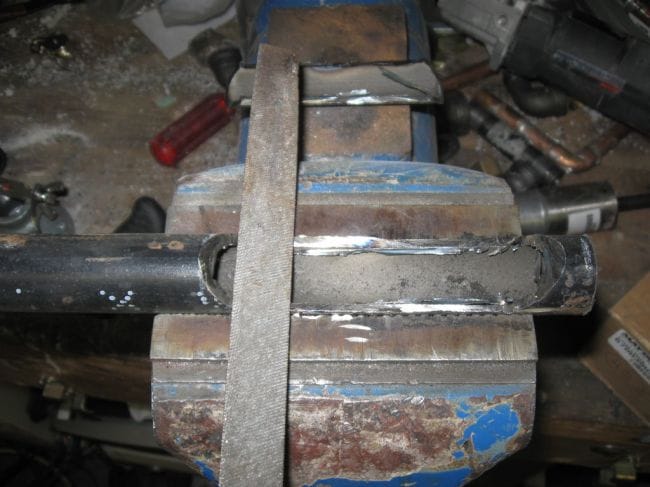
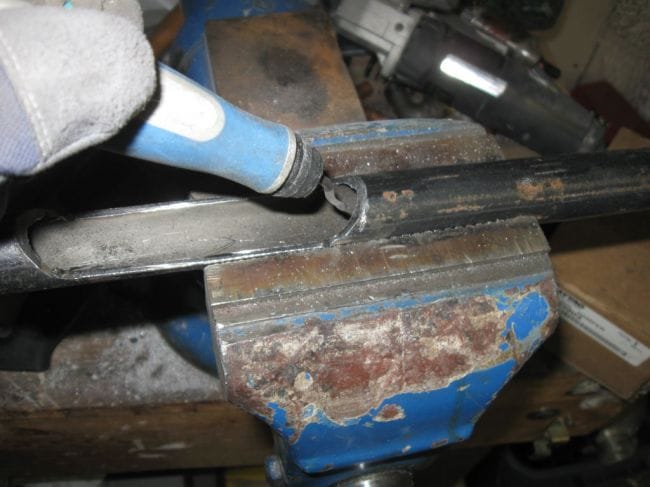
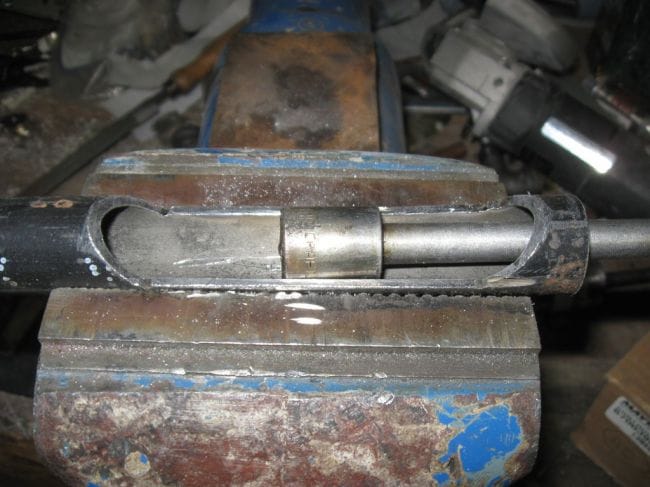
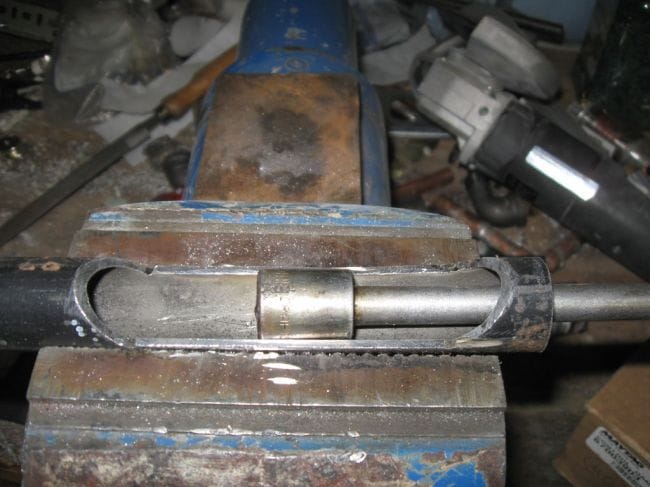
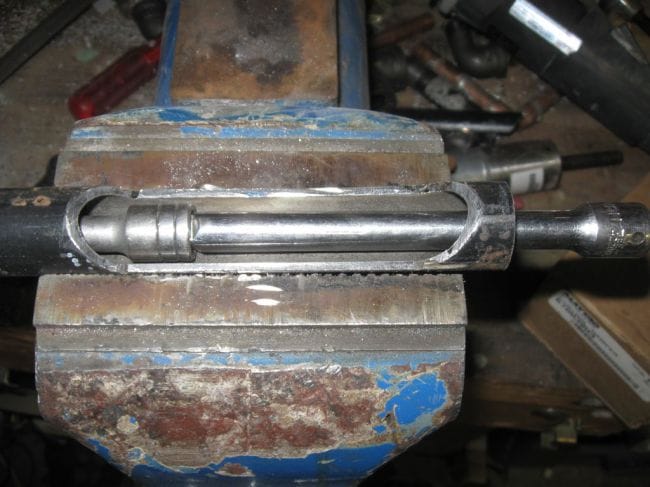

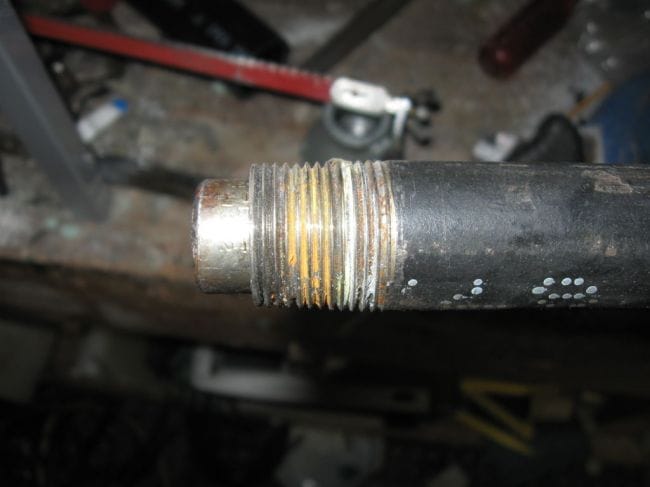

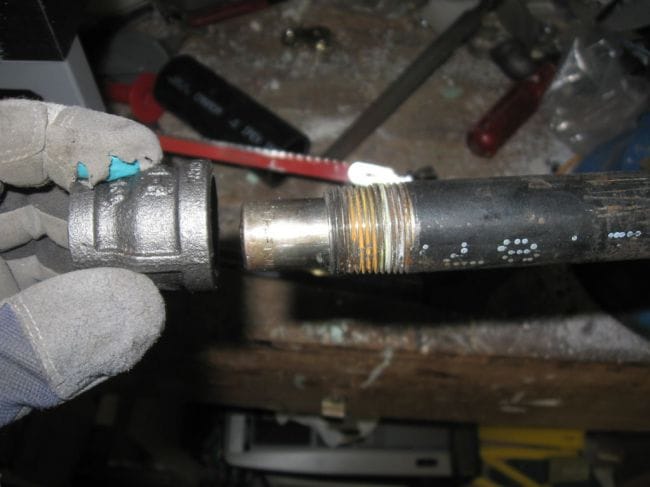
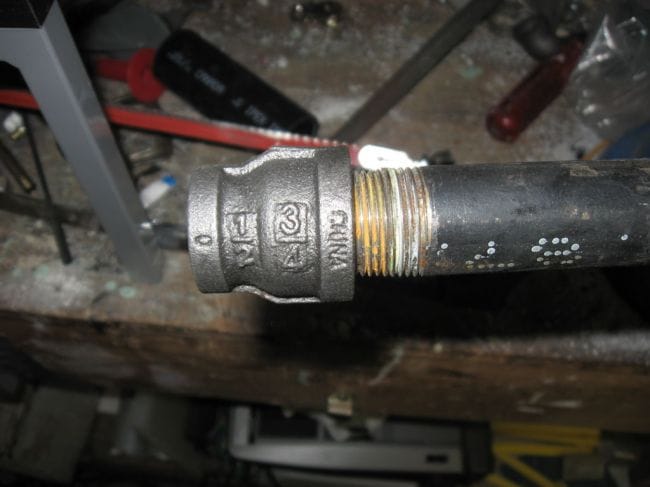
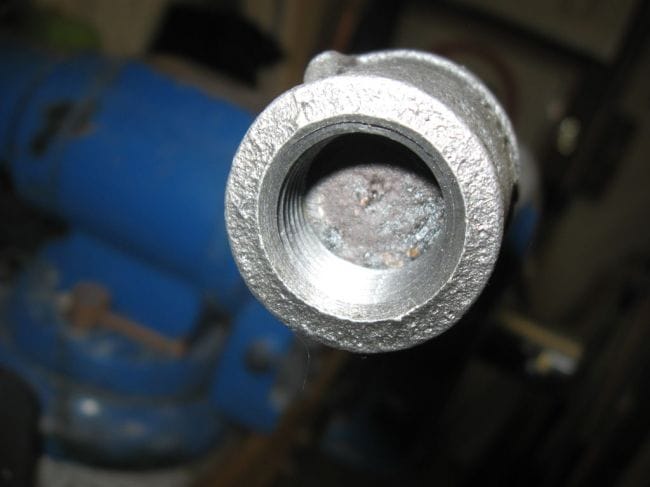
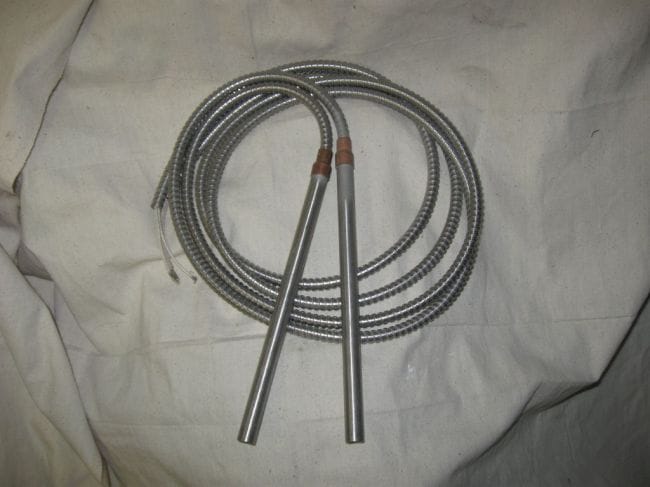
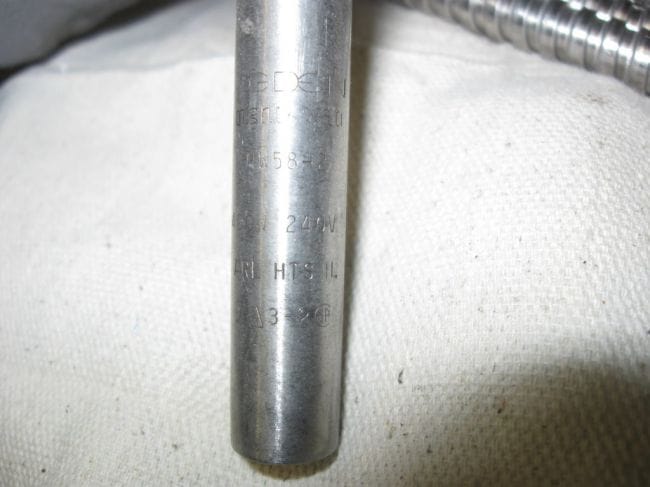
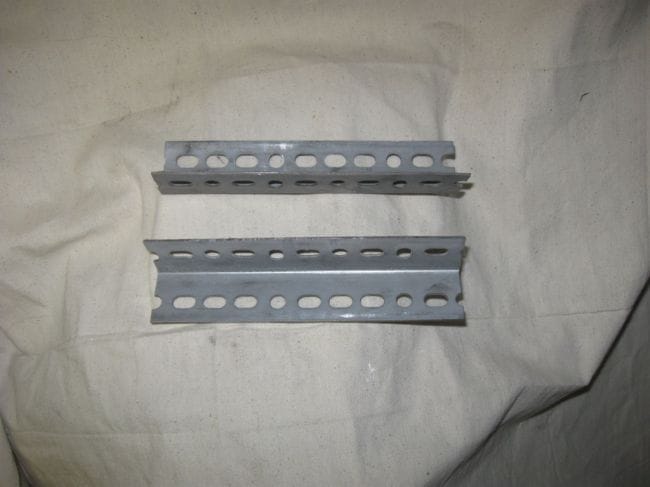
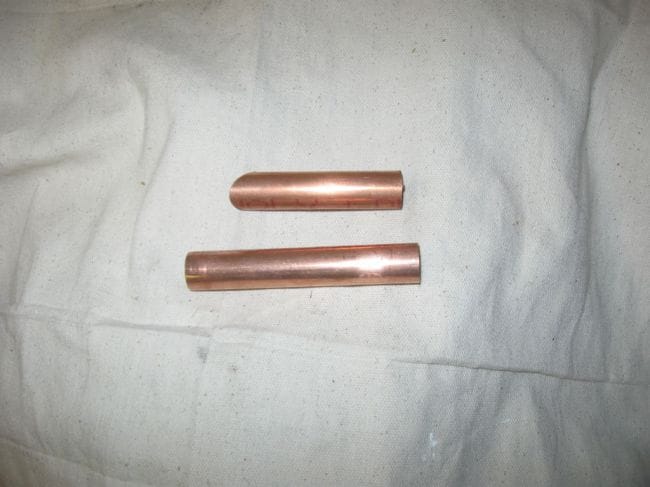
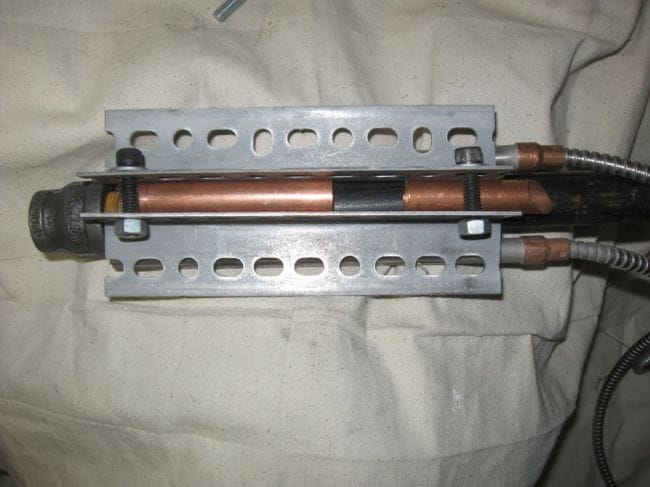
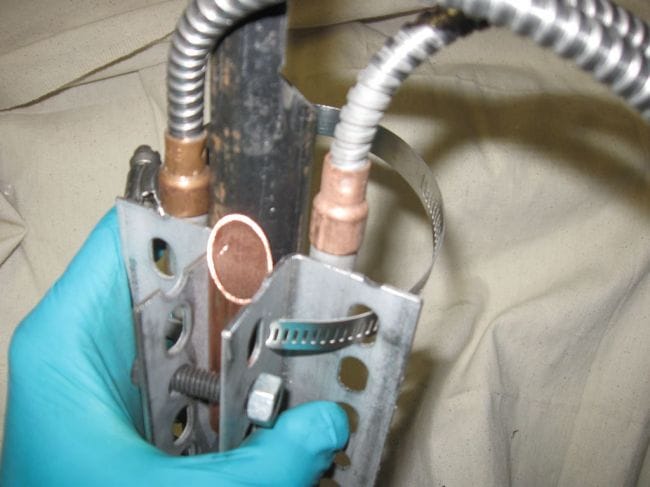
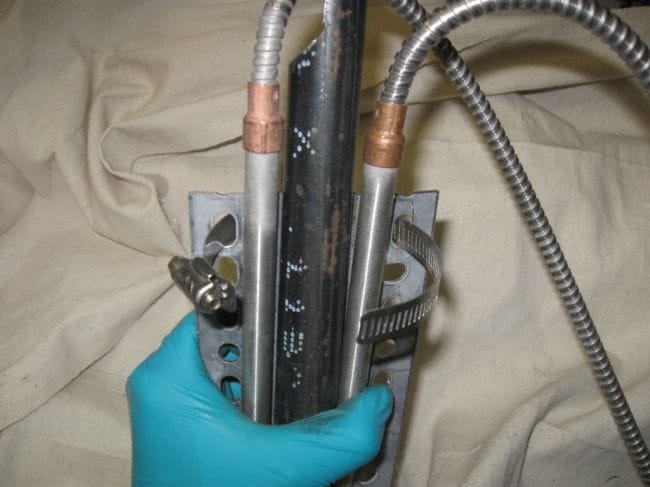
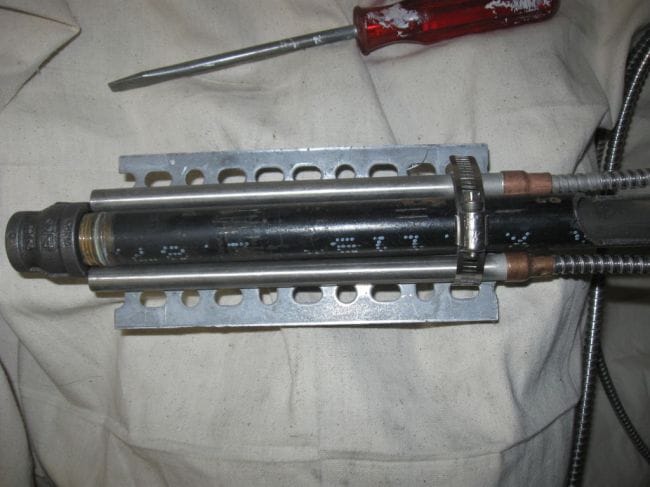
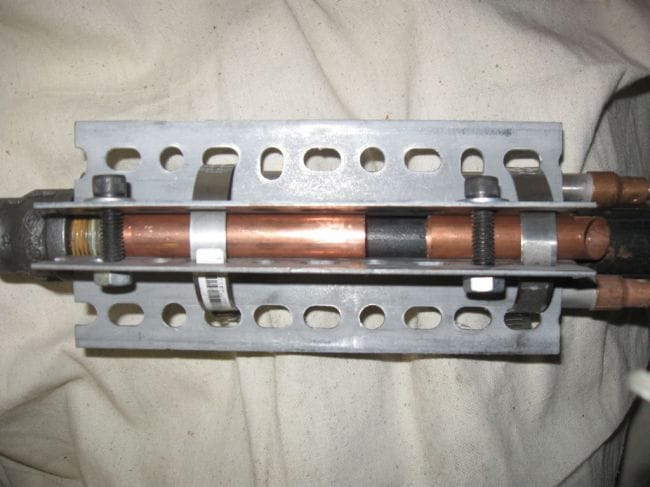
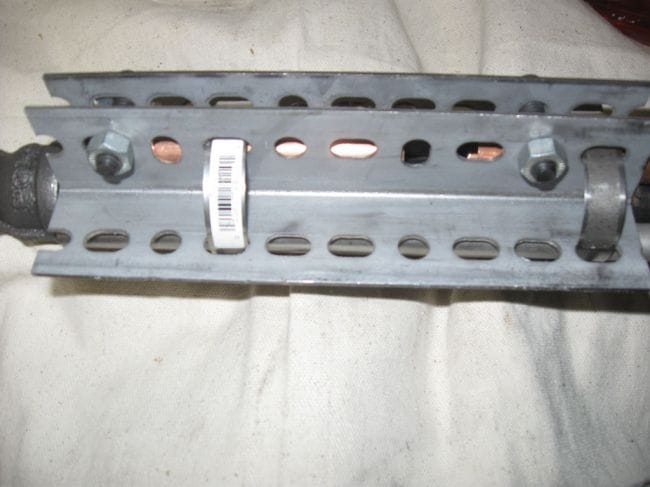
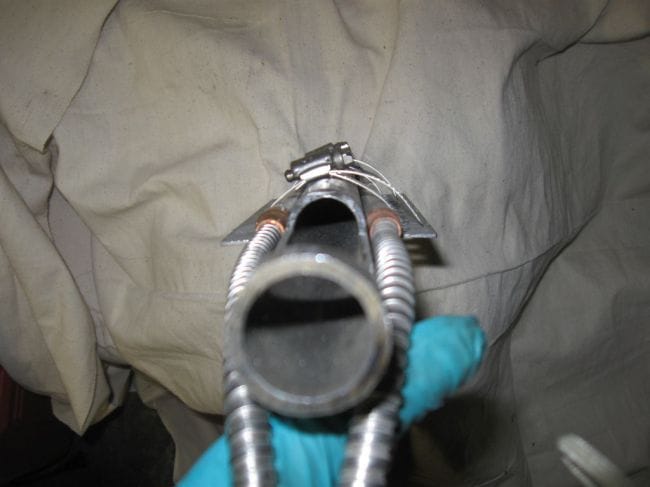
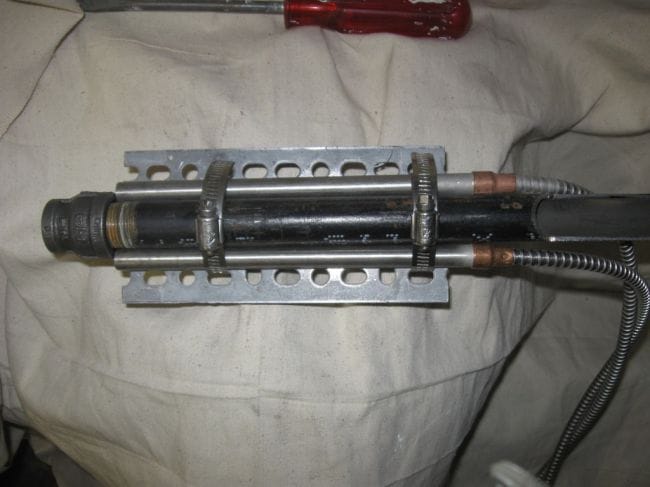
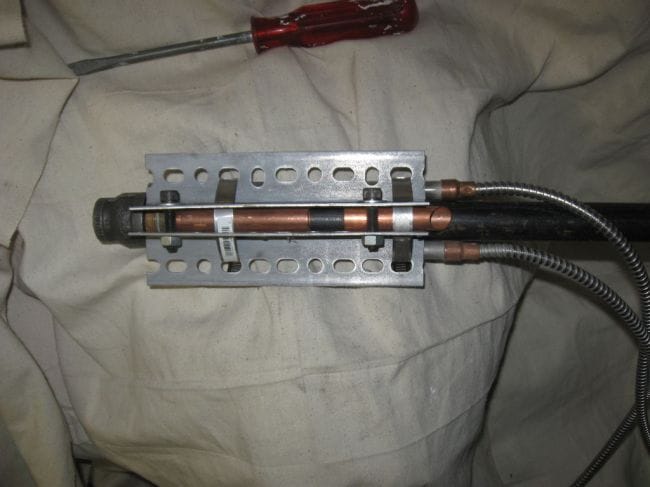
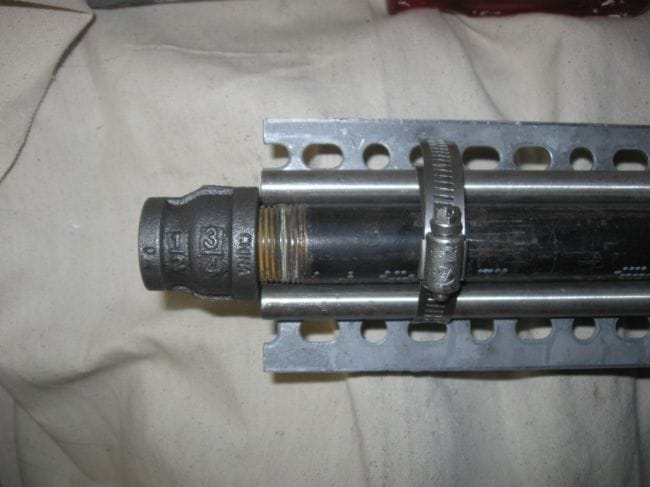
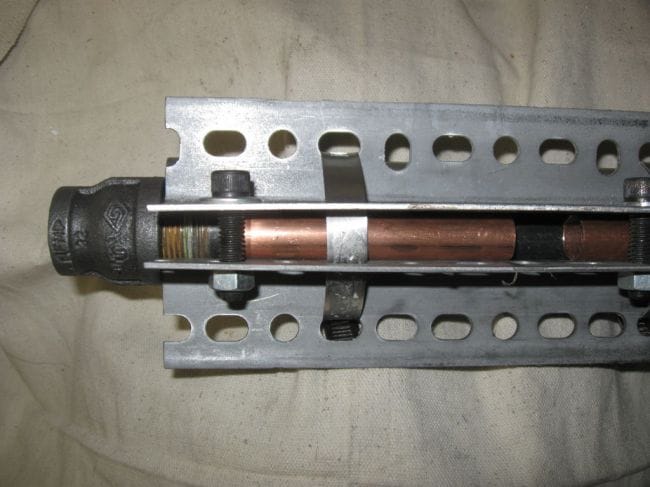
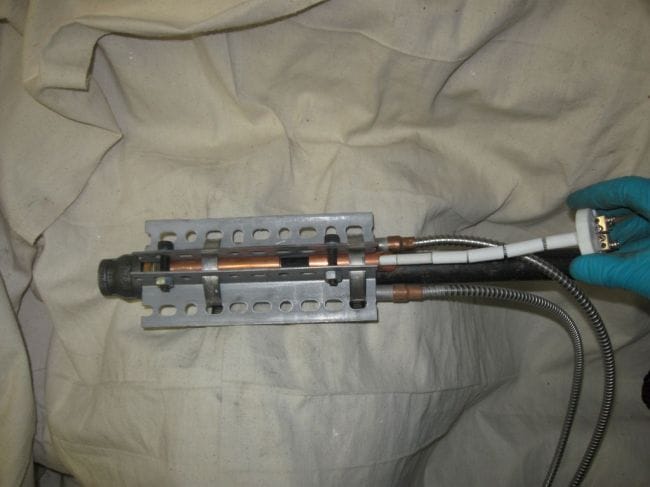
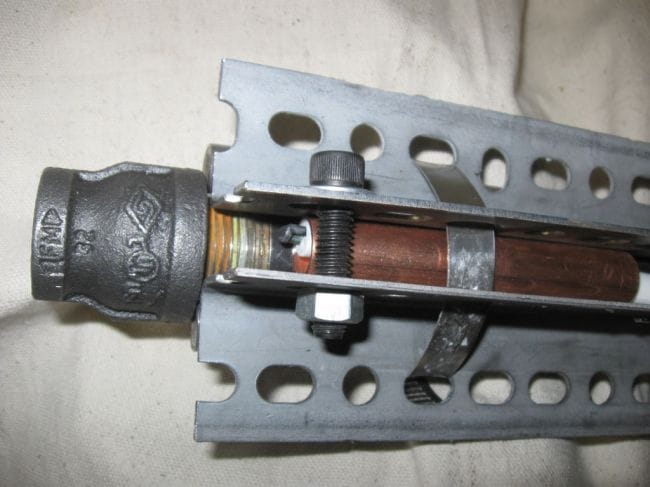
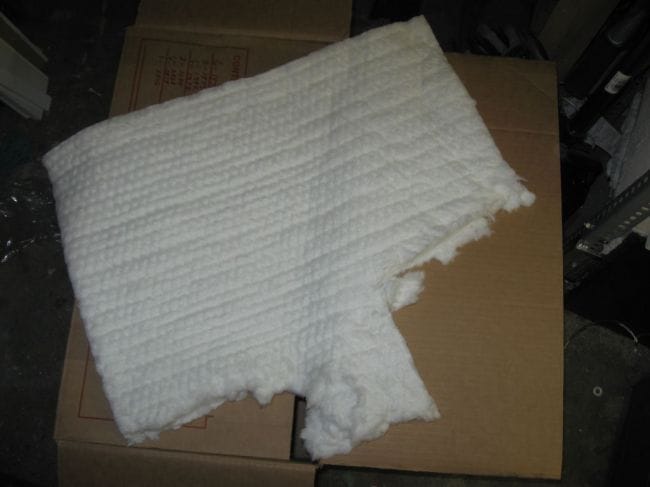
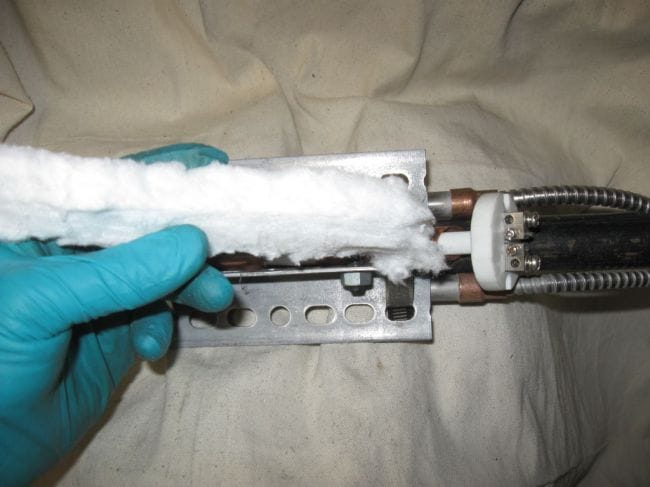
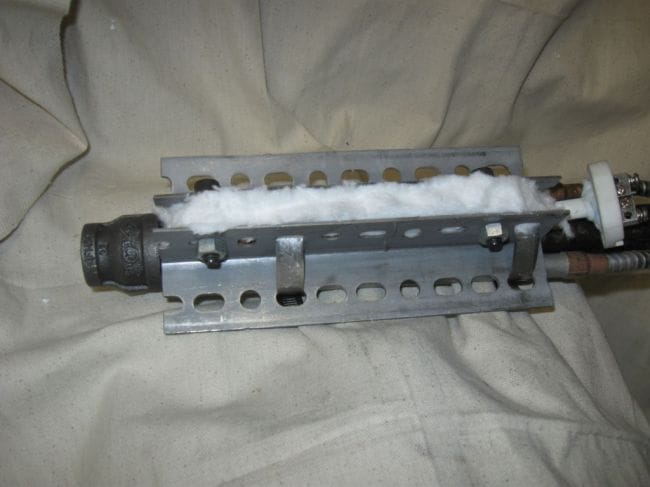
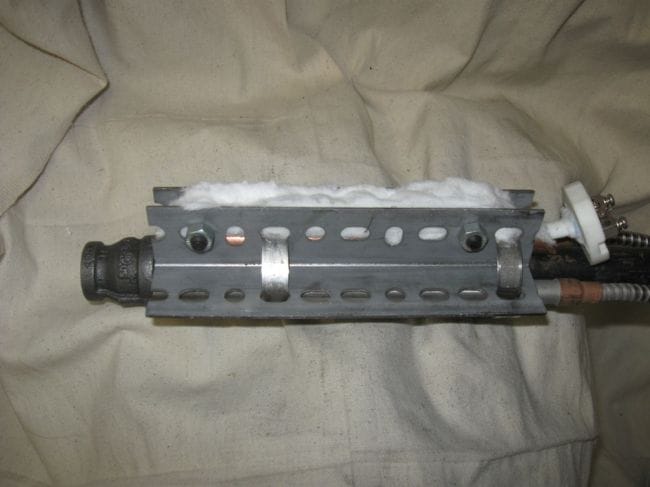
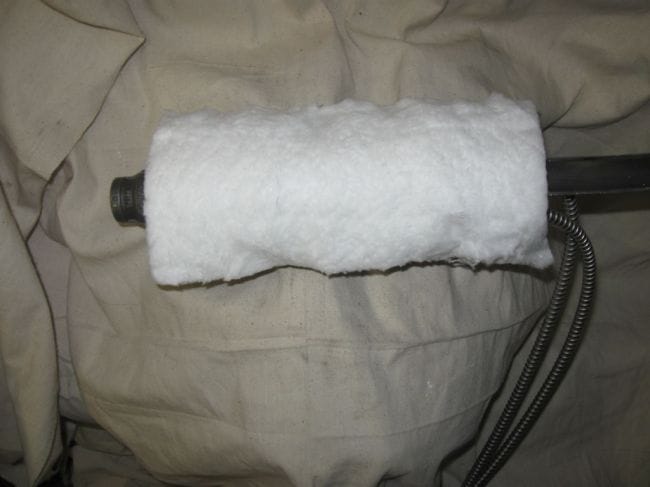
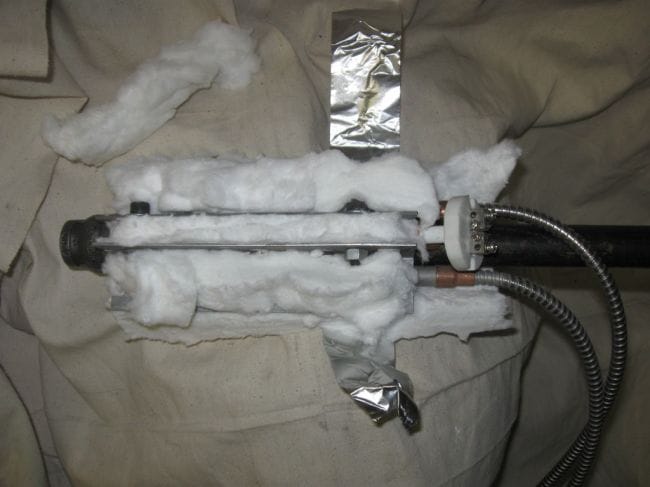
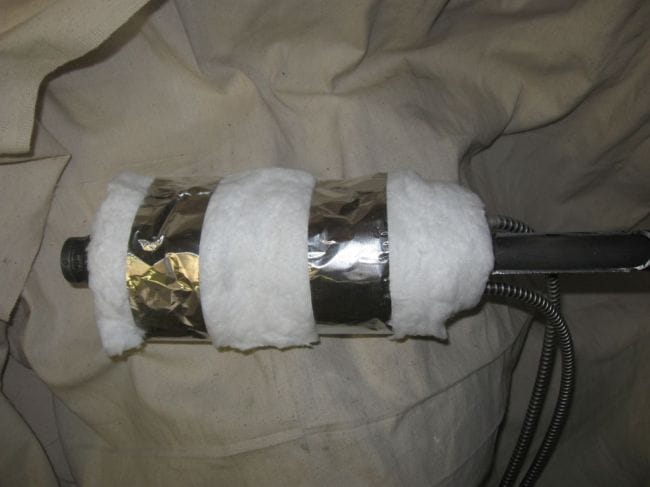

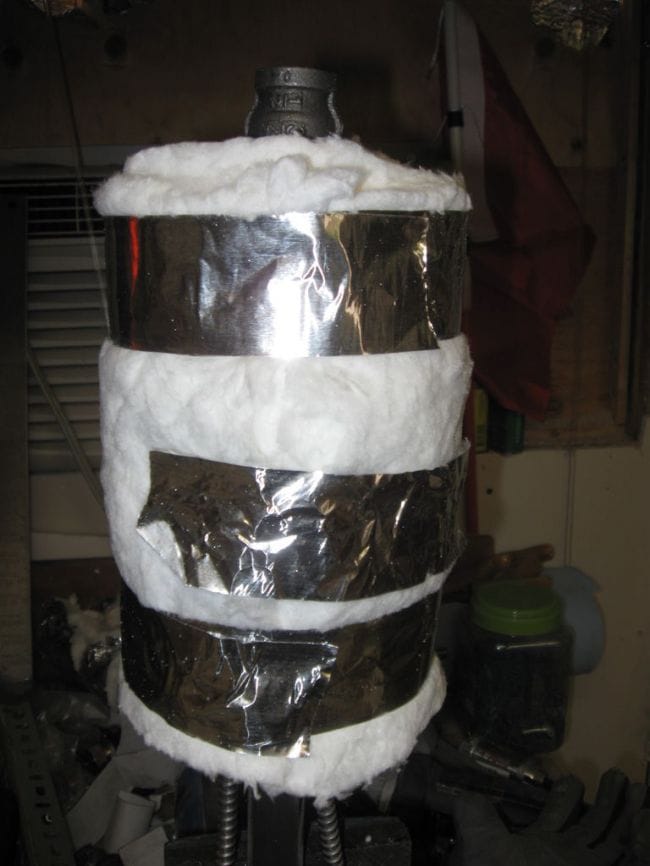
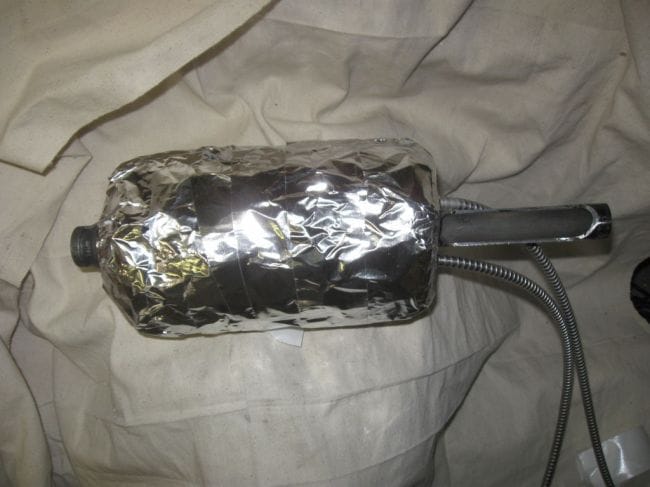
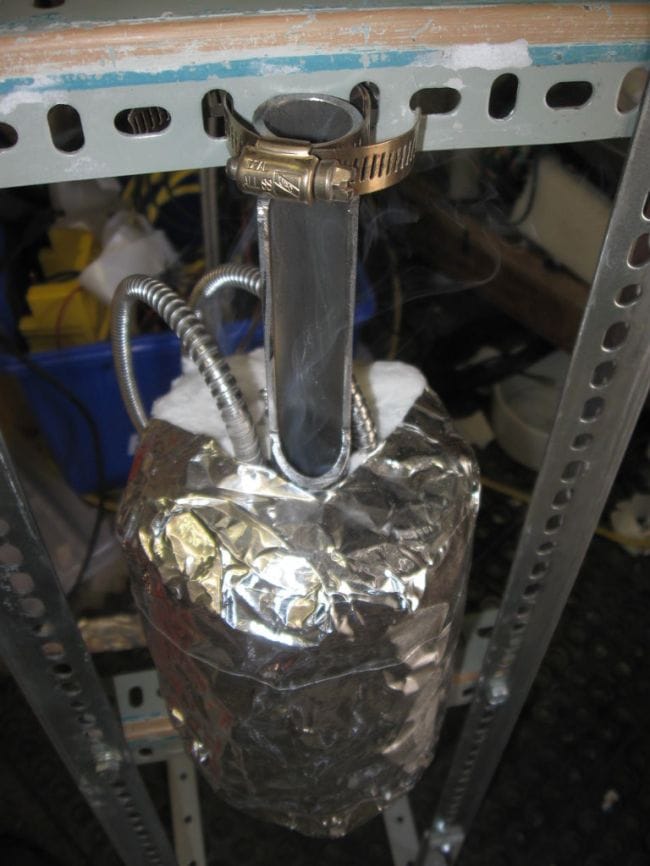
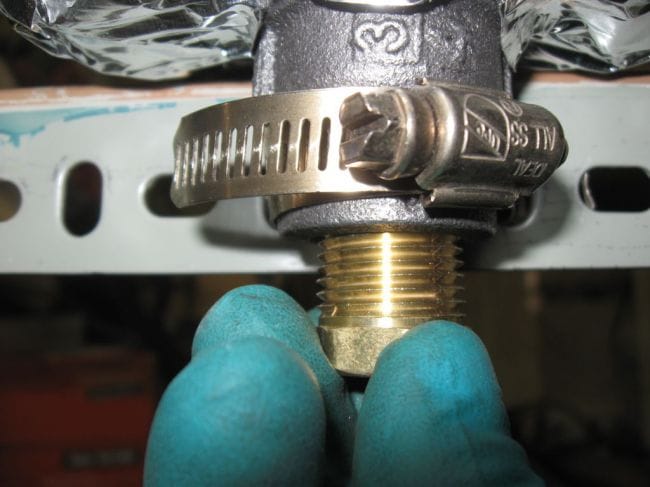
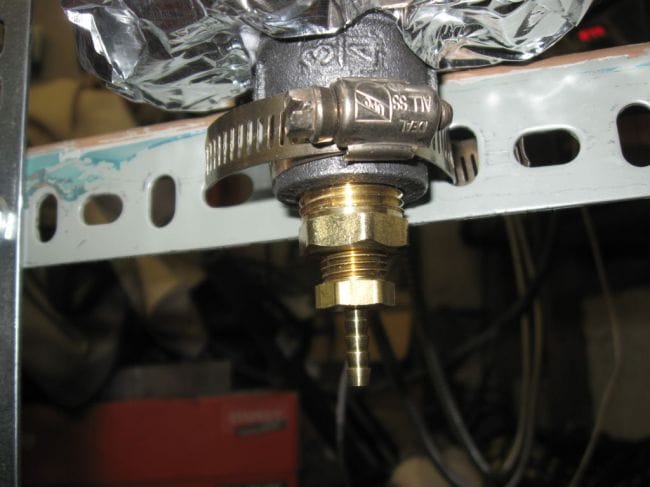
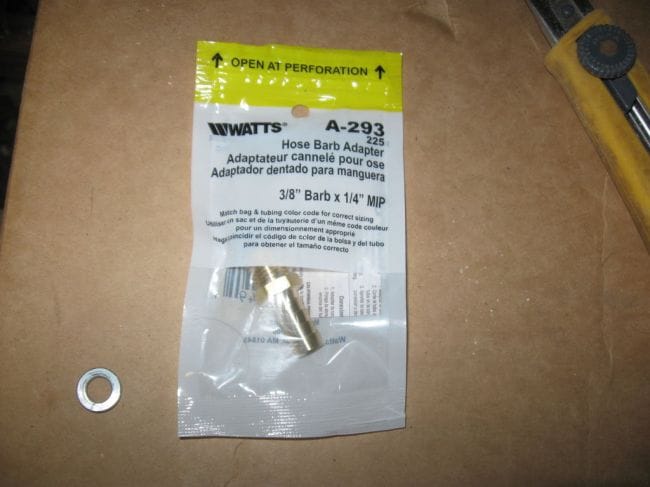
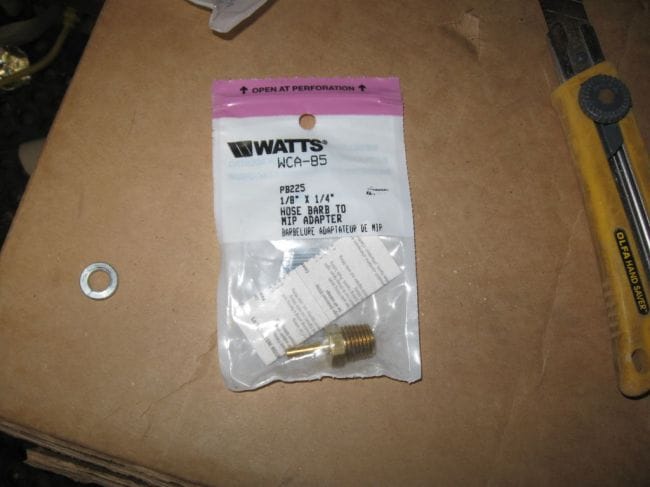
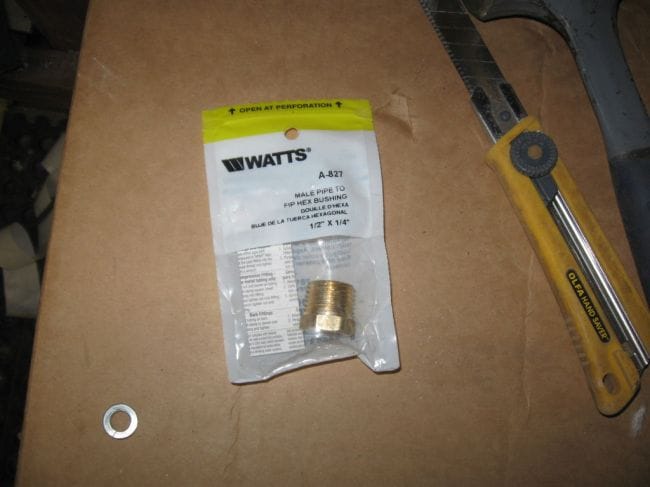
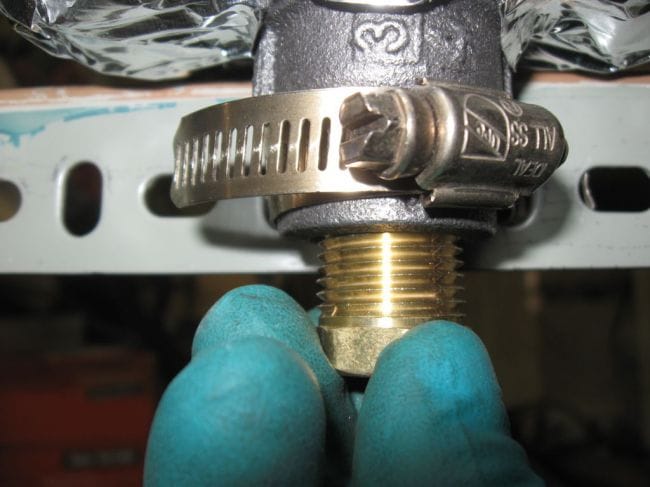
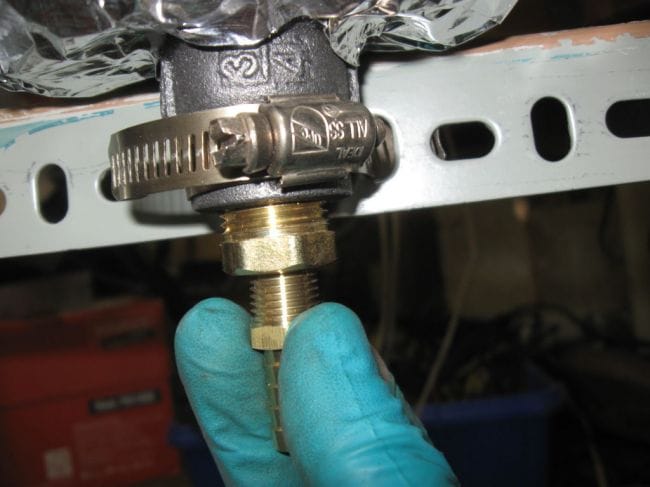
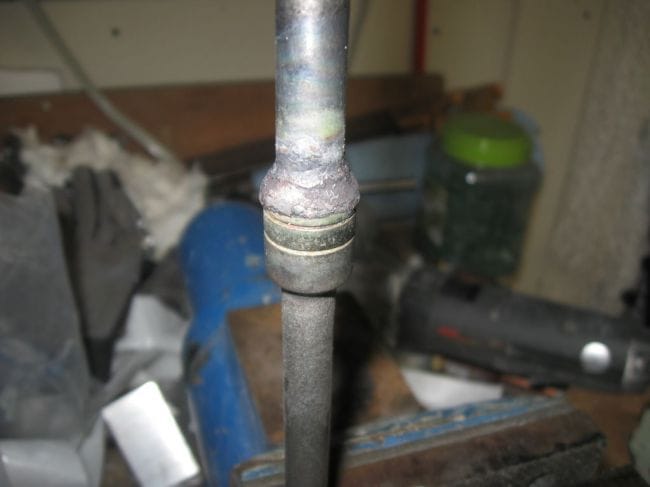
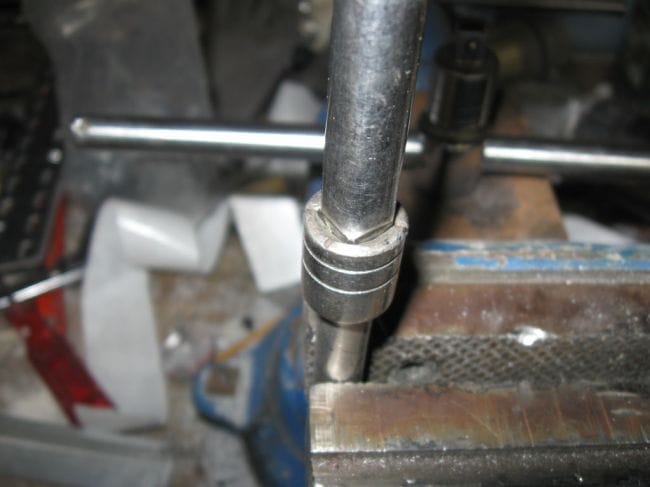
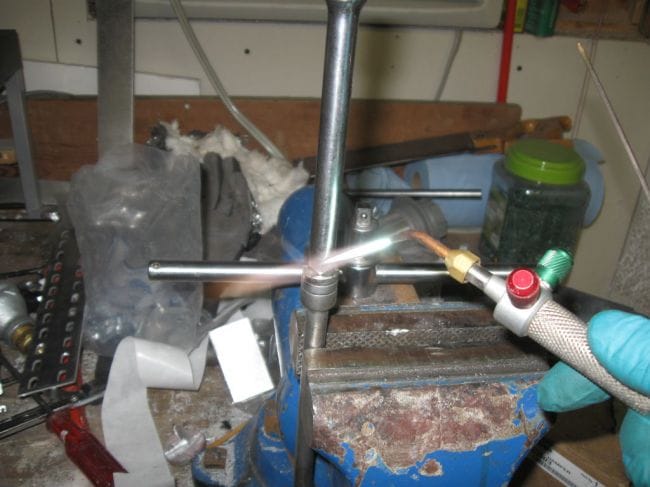
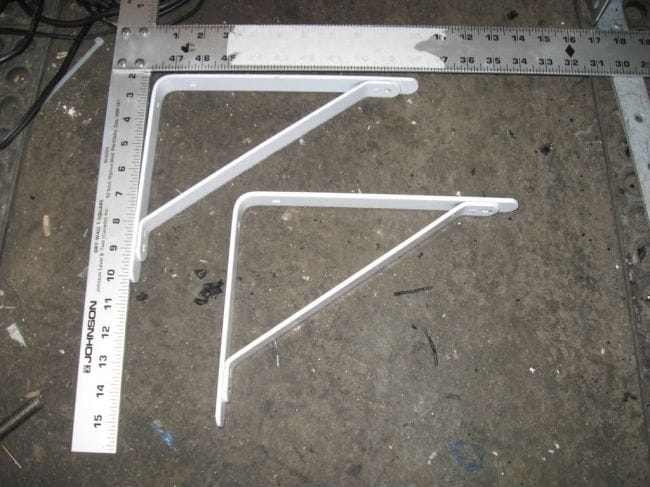
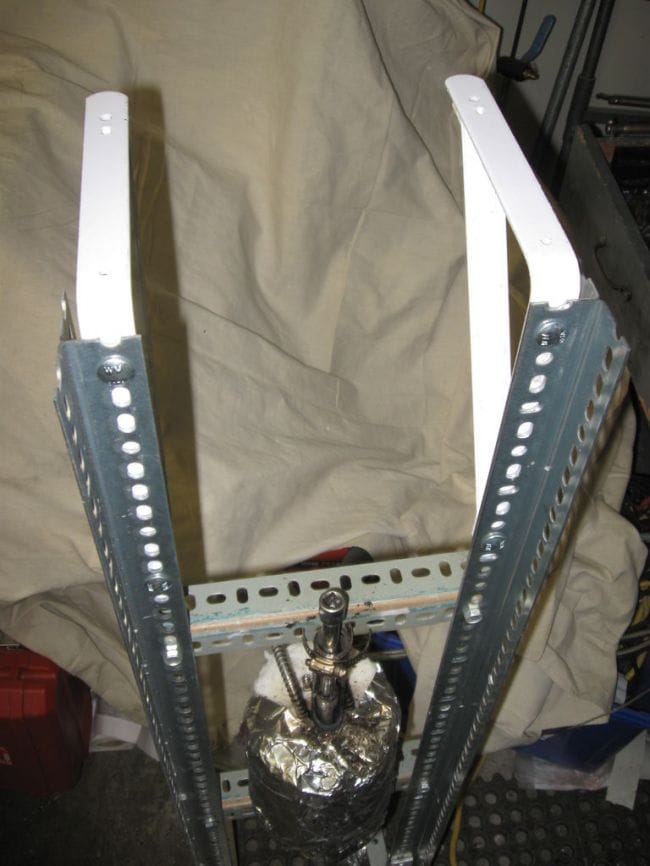
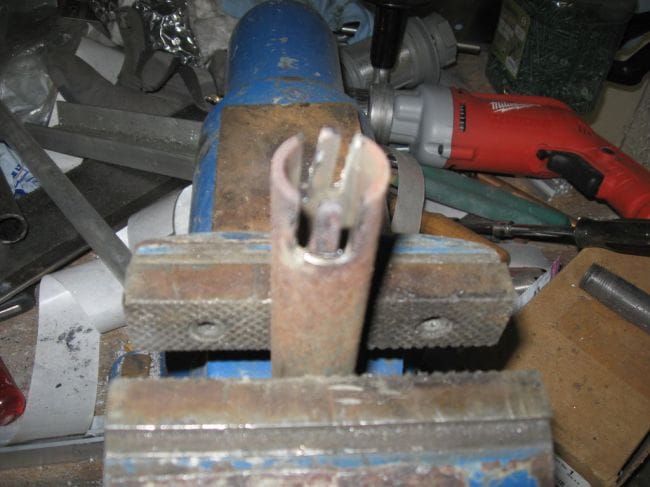
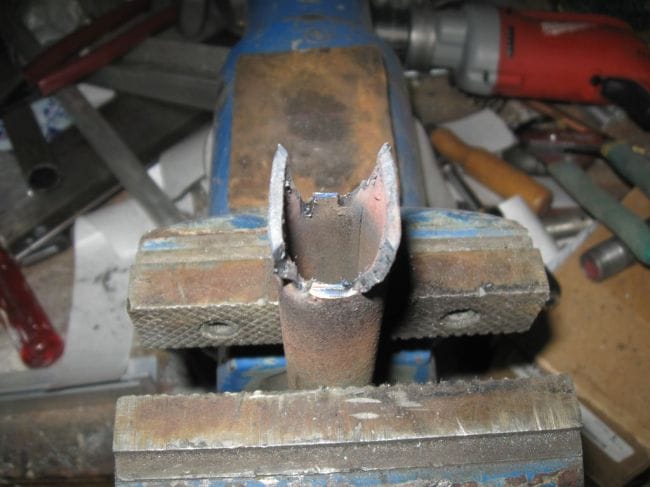
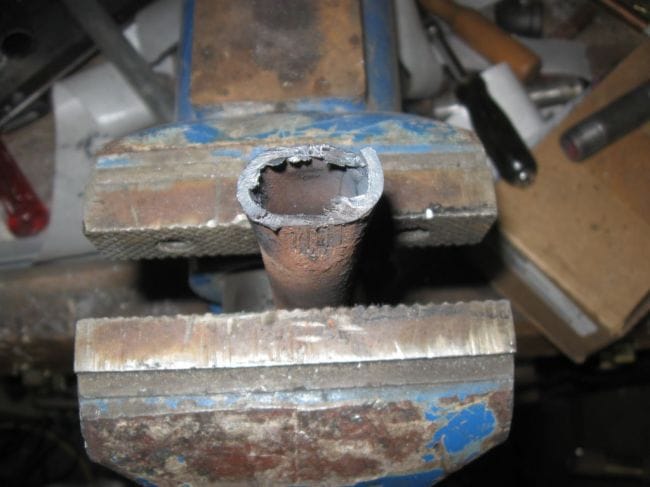
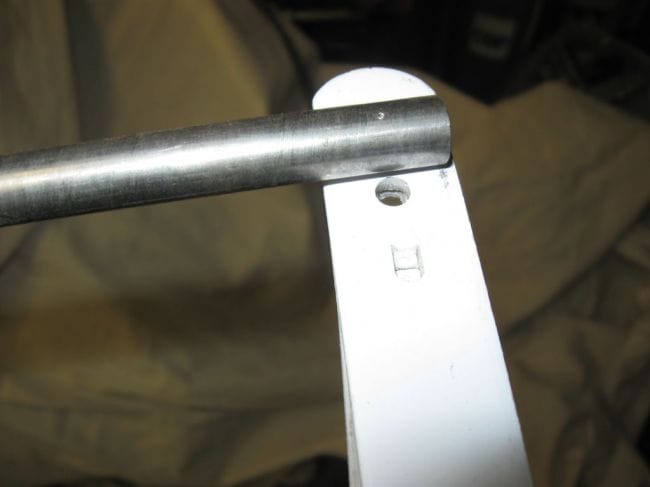
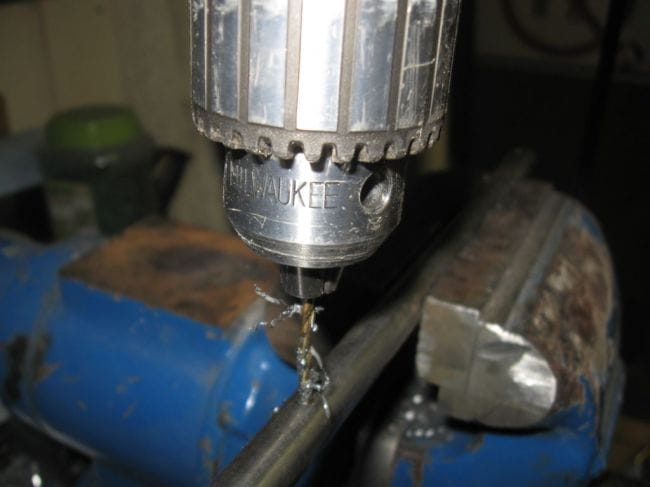
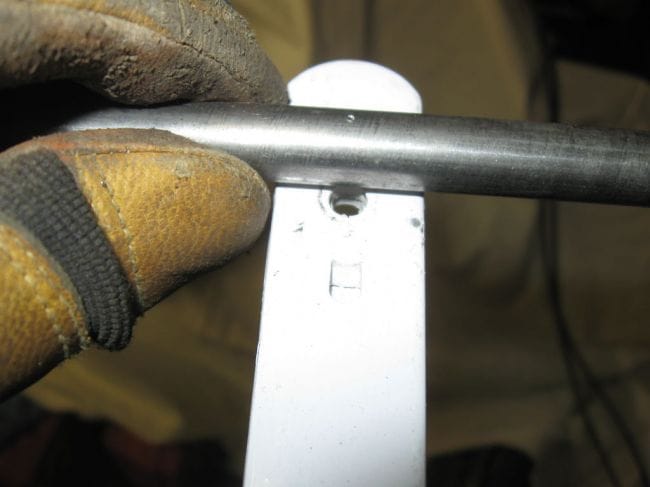
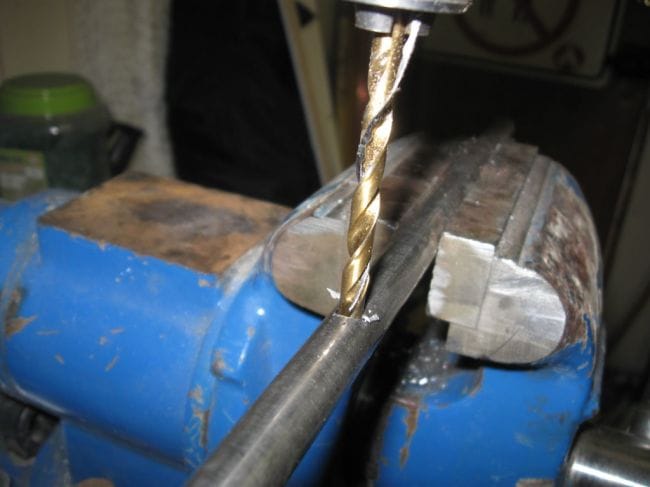
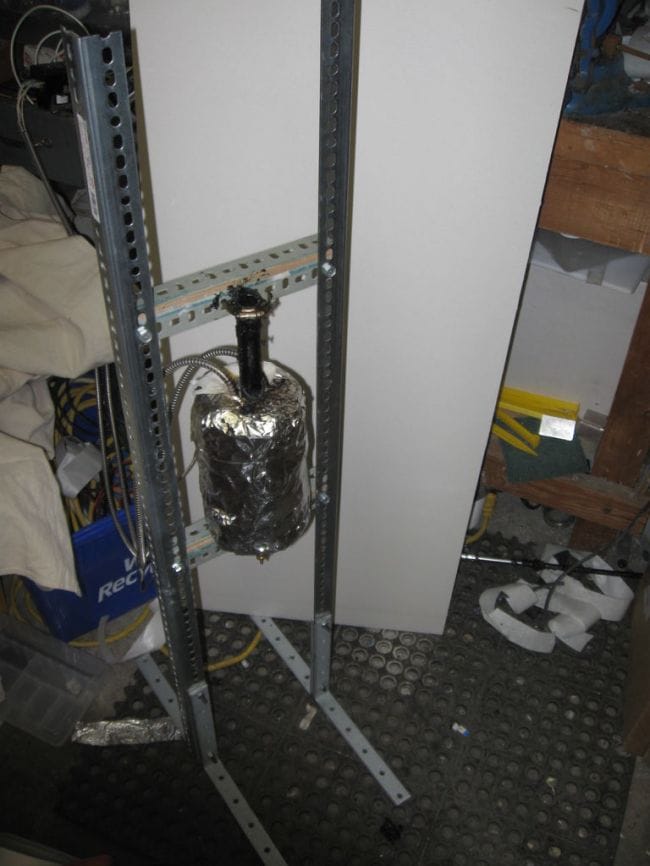
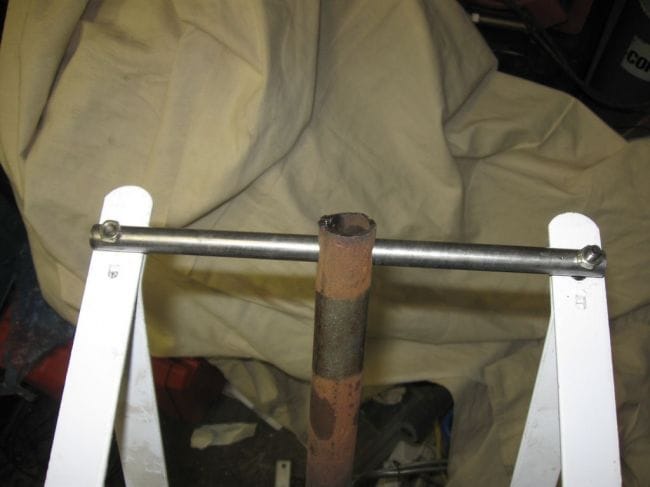
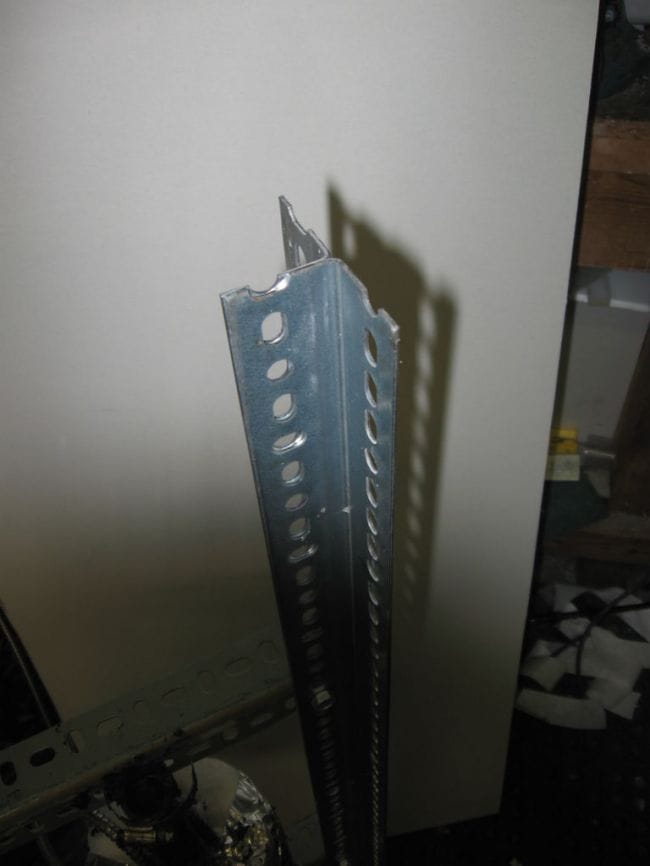
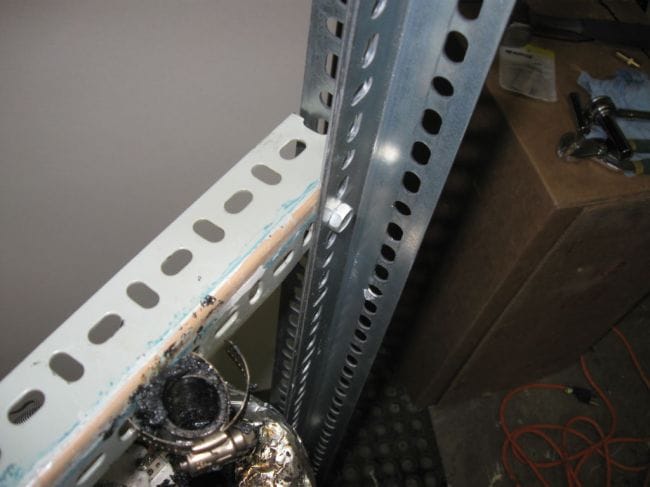
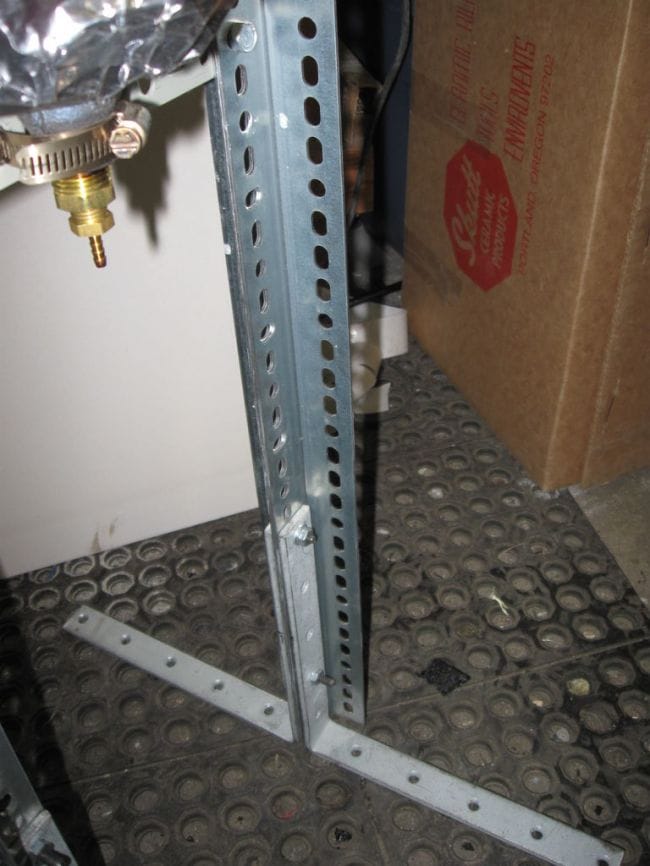
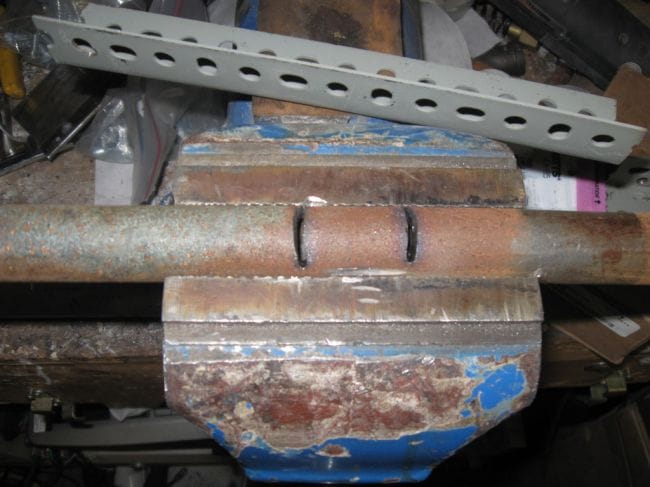
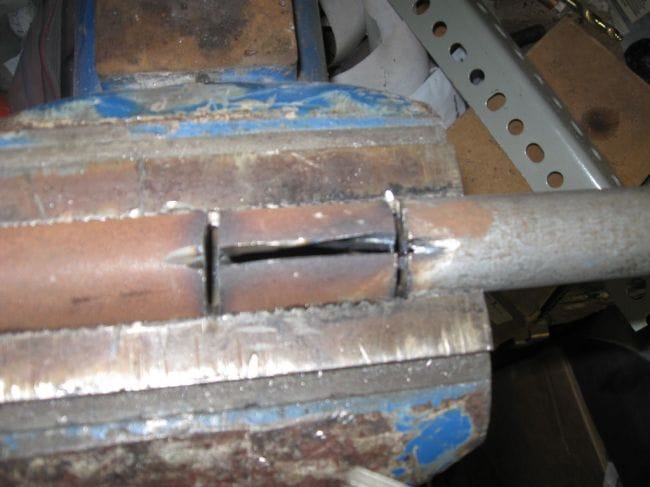
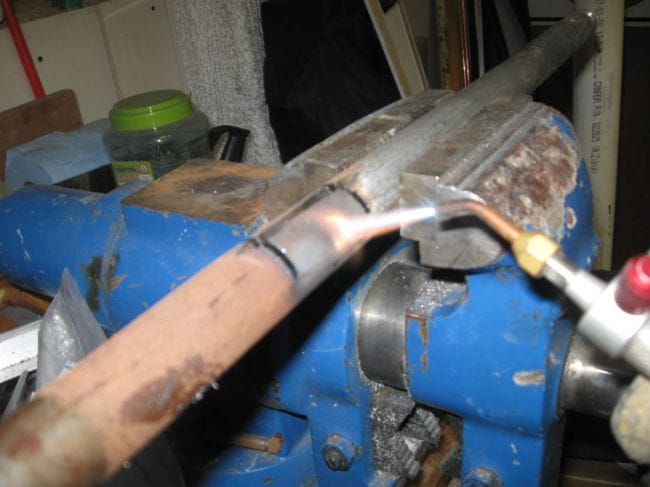
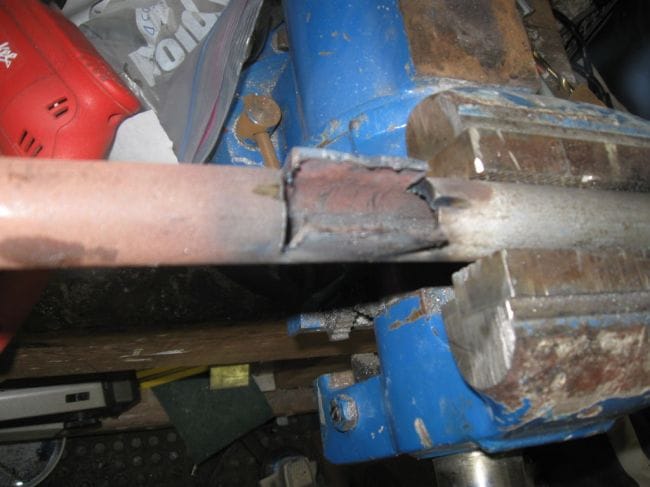

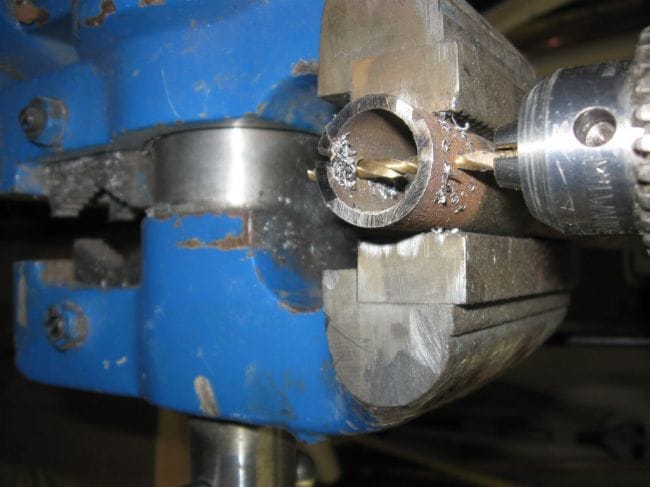
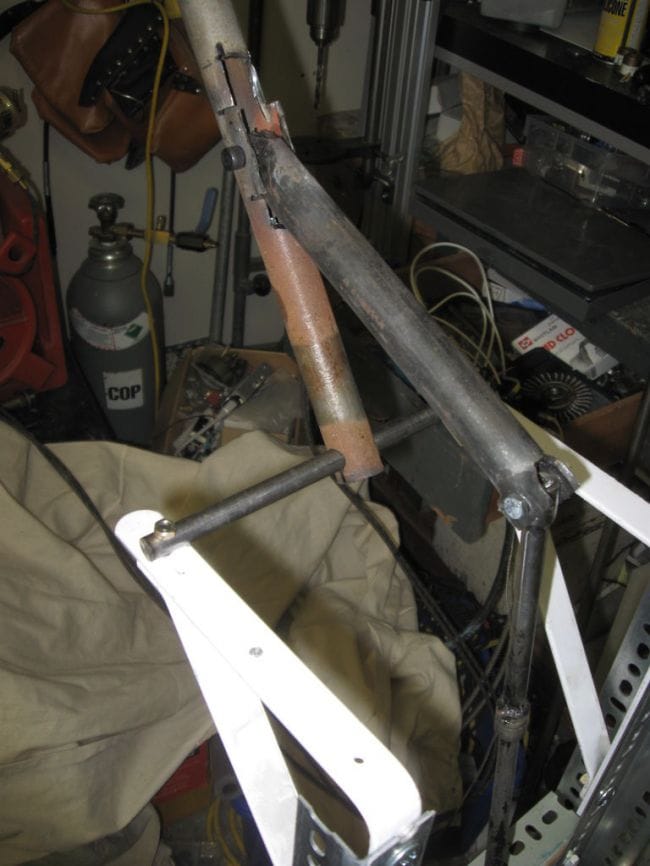
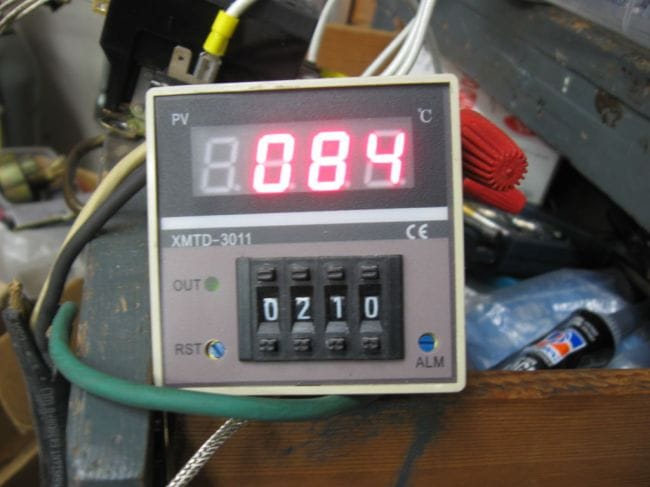
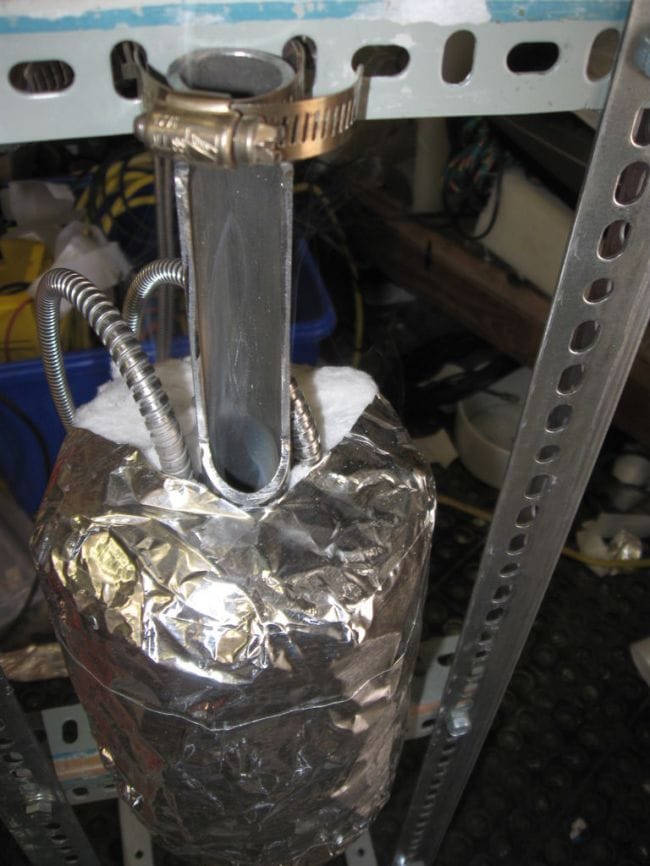
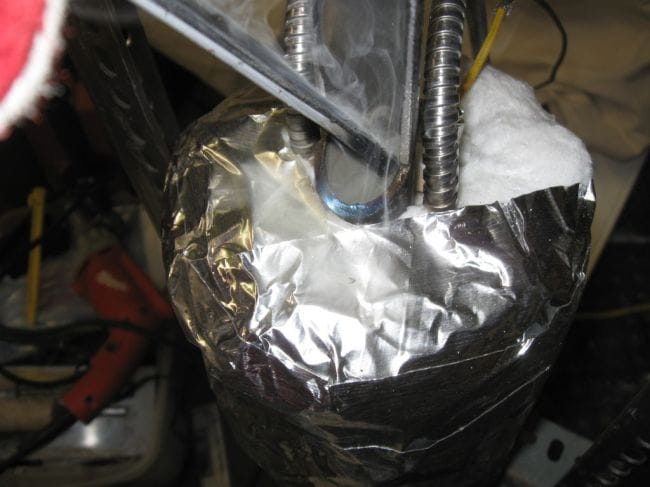
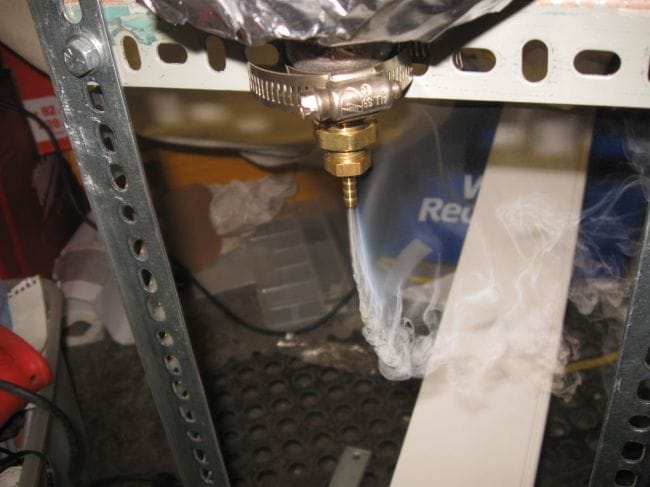
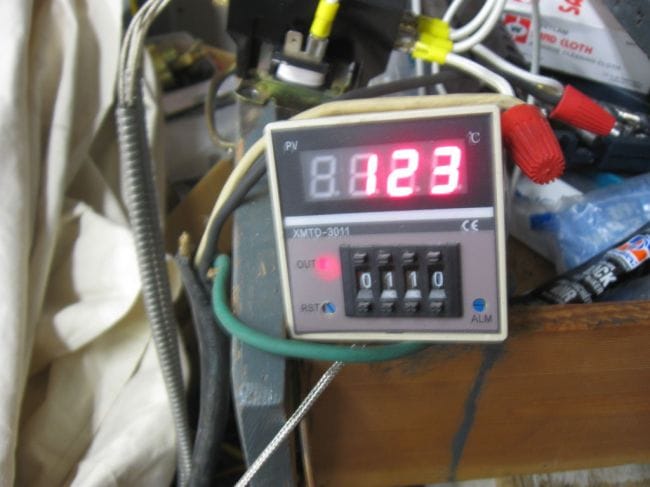
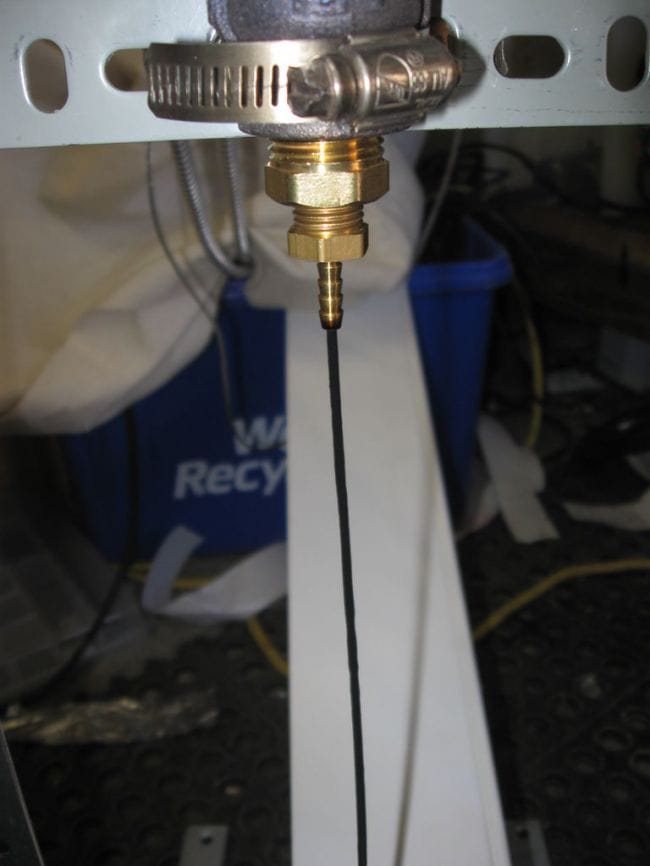
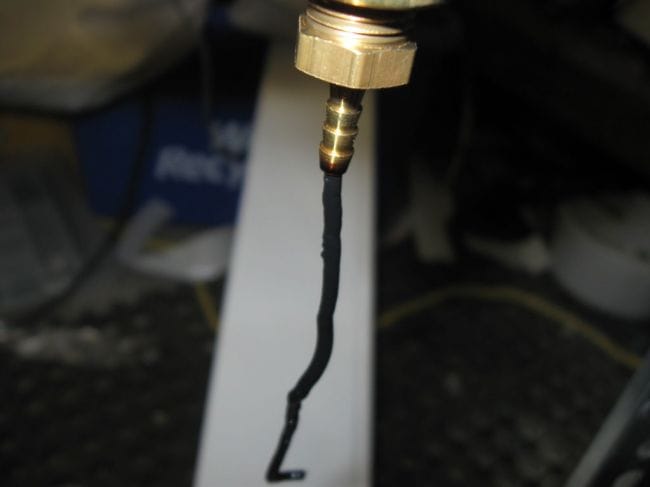
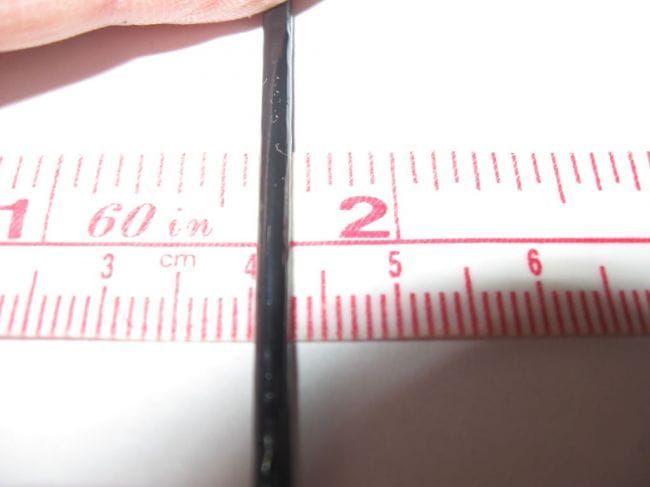
usamodelkina.ru
Портативные экструдеры прутка | Энциклопедия 3D-печати
Описание
Одним из сдерживающих факторов развития FDM-печати является относительно высокая стоимость расходных материалов. Хотя большинство пластиков вполне по карману обыденному пользователю, разница между сырьем и готовой нитью весьма значительна – зачастую стоимость прутка превышает стоимость гранул аналогичного веса в десятки раз. Таким образом, нет ничего удивительного, что на свет появились портативные, настольные устройства для домашнего производства нити из гранул и пластиковых отходов.Устройство экструдера Такие установки позволяют значительно снизить себестоимость печати и, конечно же, улучшить экологию. В этом разделе мы рассмотрим наиболее известные наработки по домашнему производству прутка, включая экструдеры нити и шредеры пластиковых отходов.
Filabot Original
Наиболее известная разработка, отличающаяся высокой производительностью. Устройство предназначено для работы с ABS, PLA и HIPS. В качестве расходного материала используется гранулированный пластик, но возможно и использование пластиковых отходов при том условии, что размер частиц не превышает 5мм.Filabot Original - наиболее известное устройство для домашнего производства прутка Компания предлагает выбор из семи цветов гранулированных красителей для ABS-пластика, позволяющих придавать готовому материалу необходимый оттенок. Красители поставляются в упаковках по 25гр. Для окраски одного килограмма ABS потребуются одна-две упаковки. Для лучших результатов рекомендуется использование красителей с гранулами ABS-пластика белого цвета.
Кроме того, возможно смешивание ABS, PLA и HIPS с углеволокном для получения более прочных и износоустойчивых материалов. Для получения подобного композита требуется лишь смешать пластик с гранулами углеволокна и, если требуется, красителя, а затем загрузить готовую смесь в бункер.
Filabot Original обладает наиболее высокой производительностью среди аналогичных устройств. На экструзию одного килограмма прутка уходит около пяти часов. Температурный диапазон при нагревании составляет 40°С-400°С, что позволяет экспериментировать с широким спектром материалов, включая композиты с древесным наполнителем, электропроводящими добавками и др.
Диаметр прутка может составлять 1,75мм или 3мм в зависимости от насадки. Скорость экструзии составляет 250-750мм в минуту в зависимости от диаметра изготовляемого прутка.
Скорость вращения шнека составляет 35 оборотов в минуту. Потребляемая мощность устройства достигает 300Вт в зависимости от температуры экструзии. Экструдер оснащен фильтром для удаления загрязняющих частиц непосредственно перед экструзией.
Устройство оснащено прочным металлическим корпусом и имеет достаточно компактные габариты, сравнимые с системным блоком компьютера: 431х178x203мм.
Отпускная цена производителя: $899.
Filabot Wee
Filabot Wee - более доступный вариант, мало чем уступающий Filabot Original Версия оригинального экструдера Filabot, оснащенная деревянным корпусом. Данный вариант позиционируется в качестве бюджетной версии и доступен как в собранном виде, так и в качестве комплекта для самостоятельной сборки.Бюджетная версия слегка уступает своему более дорогому собрату в плане производительности: скорость экструзии варьируется от 125мм до 500мм в минуту. Температура экструзии варьируется от 40°С до 350°С.
Устройство предназначено в первую очередь для производства прутка из HIPS, ABS и PLA, хотя возможно и использование других материалов, подходящих в плане температуры экструзии.
Благодаря использованию гранулированных красителей возможно достижение широкой цветовой гаммы – при применении красителей рекомендуется использование белого ABS-пластика, либо материала с легкими цветовыми оттенками.
Добавление гранулированного углеволокна позволяет добиваться более высокой прочности готового прутка. Углеволокно может использоваться в комбинации с любым из расчетных пластиков.
Максимальная потребляемая мощность составляет 300Вт. Устройство поставляется со сменными насадками, позволяющими производить пруток двух наиболее популярных диаметров: 1,75мм и 3мм.
Габариты Filabot Wee аналогичны Filabot Original: 431х178x203мм.
Компания Filabot выложила чертежи Filabot Wee в открытый доступ. Желающие построить экструдер собственными руками могут скачать необходимые файлы здесь и здесь.
Отпускная цена производителя: $749 за экструдер в собранном виде, либо $649 за комплект для самостоятельной сборки.
Filastruder
Относительно недорогой экструдер, разработанный двумя студентами из Университета Флориды: Тимом Элмором и Алленом Хэйнсом.Filastruder - относительно недорогой, но весьма эффективный экструдер Filastruder позволяет производить один килограмм нити за 12 часов работы устройства или от 150мм до 600мм в минуту в зависимости от диаметра сопла, температуры экструзии и используемого материала. Разработчики протестировали экструдер с ABS-пластиком, но допускают возможность использования PLA, HIPS, нейлона, полиэтилена и других пластиков. Максимальная температура экструзии достигает 225°С.
Экструдер достаточно экономичен – максимальная потребляемая мощность составляет 60Вт при среднем показателе в 50Вт.
Filastruder поставляется с соплами диаметром 1,75 или 3мм.
Отпускная цена экструдера Filastruder составляет $300 без бункера или $310 с напечатанным бункером.
Экструдер Лаймана
Экструдер Лаймана – пионер настольных фабрик по производству пластиковой нити Устройство получило название в честь разработчика – Хью Лаймана. Оригинальная разработка является, вероятно, первым домашним экструдером для производства прутка. Именно этот дизайн выиграл главный приз на конкурсе Desktop Factory Competition в 2013 году.Конструкция экструдера максимально упрощена, что стало следствием главного условия конкурса: общая стоимость компонентов, использованных в конструкции, не должна была превышать $250.
Экструдер Лаймана не является коммерческой разработкой и недоступен в розничной торговле. Разработчик выложил инструкции по созданию экструдера в открытый доступ. Необходимые файлы можно скачать здесь.
OmniDynamics Struder
OmniDynamics Struder рассчитан на безопасность и удобство эксплуатации Компактное устройство, анонсированное на площадке Kickstarter в мае 2014 года. Целью разработчиков является создание портативного, удобного и безопасного в использовании устройства.Поставки первых партий экструдера намечены на сентябрь 2014 года. Розничная цена устройства еще не анонсирована, но стоимость предварительного заказа на Kickstarter составляет £149.
Дизайн экструдера рассчитан на работу с любыми термопластиками, используемыми в 3D-печати, включая ABS, PLA, PET, HDPE, HIPS и т.д. Устройство оснащается полноценным контрольным модулем с цветным LCD-дисплеем.
STRUdittle
STRUdittle – перспективный экструдер с компактными габаритами и высокой производительностью Еще одна интересная разработка, получившая необходимое финансирование на Kickstarter.Дизайн устройства нацелен на высокую компактность и хорошую ценовую доступность с сохранением высокой производительности.
По заявлениям разработчиков, устройство способно вырабатывать до 600мм прутка в минуту. Экструдер рассчитан на работу с ABS-пластиком. Отклонения по диаметру нити не превышают 0,03мм при использовании наматывающего устройства или 0,05мм, если пруток просто экструдируется на пол. Заказчики могут указать требуемый диаметр сопла: 1,75мм или 3мм.
Стоимость предварительного заказа на Kickstarter составляет $385 за экструдер в комплекте с наматывающим устройством.
Filabot Reclaimer
Ручная дробилка Filabot Reclaimer позволяет перерабатывать всевозможные пластиковые отходы Перечисленные экструдеры рассчитаны на работу с гранулированными пластиками. В то же время, FDM-принтеры в комбинации с настольными экструдерами обладают прекрасным потенциалом по переработке пластикового мусора в новые изделия. Таким образом, для использования пластиковых отходов в качестве расходных материалов требуется устройство, способное дробить пластик до получения мелких частиц – как правило, не более 5мм. Компания Filabot разработала простой, но эффективный шредер, предназначенный именно для этой цели. Приспособление получило название Filabot Reclaimer.Filabot Reclaimer оснащен прочной сварной металлической рамой и зазубренными валиками из закаленной стали. Устройство не оснащено электроприводом – валики приводятся в движение вручную с помощью рычага.
В качестве сырья может использоваться практический любой термопластик, применяемый в 3D-печати.
Filabot Reclaimer позволяет перерабатывать неудачные модели, отходы 3D-печати и просто ненужные пластиковые изделия. Размеры горловины и, соответственно, перерабатываемых кусков пластика достигают 50х90мм. Ввиду прочной металлической конструкции приспособления, вес Filabot Reclaimer составляет внушительные 11кг. Габариты установки достаточно скромны, достигая 255х255х380мм.
Отпускная цена Filabot Reclaimer составляет $439. Несмотря на относительно высокую стоимость, устройство достаточно быстро окупается, позволяя вкупе с экструдером экономить до 90% от стоимости прутка.
FilaMaker
FilaMaker сочетает функциональность дробилки и экструдера FilaMaker сочетает функции дробилки и экструдера в одном устройстве. Установка была продемонстрирована на ярмарке Maker Faire Rome в 2013 году и завоевала внимание благодаря высокой функциональности, аккуратному дизайну и высокой производительности.FilaMaker способен производить до одного метра нити диаметром 3мм в минуту. Отклонение заданного диаметра не превышает 0,05мм. К сожалению, отпускная цена устройства весьма высока, достигая €1 200.
Перейти на главную страницу Энциклопедии 3D-печати
3dtoday.ru
Экструдеры для пластика - KeyProd
Одной из основных технологий переработки пластмасс и изготовления из них разнообразных деталей и профильной продукции является экструзия. Заключается она в приготовлении расплава полимеров с последующим продавливанием его через формующие сопла – специальные насадки, придающие материалу заданную форму. Главным элементом производственной линии, использующей подобную методику, является экструдер для пластика.
Принцип работы экструдера
Экструдер представляет собой электромеханическое устройство, непосредственное предназначенное для процесса формовки пластмассовых профильных деталей их полуфабрикатов. Общее устройство экструдера для пластика:
- Корпус с системой нагрева до необходимой температуры плавления полимеров. В качестве источника тепловой энергии могут использоваться привычные резистивные системы или индукционные, создающие высокие температуры за счет наведенных на их корпус высокочастотных индукционных токов Фуко.
- Узел загрузки, через который различными способами сырье поступает в полость корпуса.
- Рабочий орган, создающий необходимое давление для перемещения сырья от узла загрузки до формующих насадок. Используются различные физические принципы, так это механизм может быть поршневым, дисковым или шнековым. Наибольшее распространение получили именно шнековые экструдеры.
- Экструзионная головка (иначе – фильера), задающая форму получаемых изделий.
- Механический привод (двигатель и редукторная система), создающий и передающий на рабочий орган необходимое усилие.
- Системы контроля и управления, поддерживающие необходимый технологический режим.
Загруженное в виде гранул, порошка или лома сырье под действием рабочего органа перемещается в рабочую зону корпуса, где под действием давления, трения и подаваемой извне температуры нагревается и плавится до состояния, требуемого по условиям технологического процесса.
В ходе движения в полости корпуса сырье тщательно перемешивается до однородной гомогенизированной массы.
Под действием высокого давления расплав продавливается через сетчатые фильтры и формующие головки, где происходят его окончательная гомогенизация и придание заданного профиля.
Затем, охлаждаясь естественным или принудительным способом, он полимеризуются, и в итоге получаются изделия необходимой конфигурации с заданными физическими и механическими свойствами.
Видео: “Как работает экструдер?”
Виды экструдеров
Современные экструзионные установки различаются как по схеме рабочего органа, так и по своему целевому предназначению.
Экструдеры одношнековые и двухшнековые
Шнековые (червячные) экструдеры – наиболее распространенные, так как практически в полной мере отвечают всем требованиям технологического процесса. Рабочим органом выступает шнек экструдера (винт Архимеда, известный каждому хотя бы по домашним мясорубкам).
Лопасть шнека экструдера захватывает сырье в области загрузки и перемещает последовательно по всей длине цилиндра корпуса, через зону нагрева, гомогенизации и формовки. В зависимости от технологической карты и вида исходного материала шнеки могут быть нормальными или быстроходными, цилиндрической или конической формы, сужающиеся к выходу. Одним из главных параметров является соотношение рабочего диаметра шнека к его длине. Различаются также шнеки шагом витков и их глубиной.
Однако одношнековые экструдеры не всегда применимы. Например, если в качестве сырья используется порошковый полуфабрикат, один винт не справится с тщательным его перемешиванием в ходе расплавления и гомогенизации.
В подобных случаях применяют двухшнековые экструдеры, винты которых могут находиться во взаимном зацеплении, совершать параллельное или встречное вращательное движение, иметь прямую или коническую форму.
В результате процессы разогрева, смешения и гомогенизации проводятся более тщательно, и на головку поступает полностью однородная и дегазированная масса.
Нельзя не отметить, что в некоторых технологических процессах применяются экструдеры и с большим количеством шнеков – до четырех, а кроме того, существуют и планетарные автоматы, когда вокруг центрального винта вращается до 12 сателлитных.
Это бывает необходимым при работе с некоторыми видами пластиков, которые под действием высоких температур имеют свойство к деструкции – потере физических качеств. Таким образом, их нагрев в подобных экструдерах осуществляется за счет силы трения и создаваемого высокого давления.
Экструдер для ПВХ профиля
Производство пластиковых или композитных профилей в большинстве случаев производится именно методом экструзии. Для этого, в зависимости от материала и сложности формы изделия, используют одно- или двухшнековые аппараты с соответствующими формующими головками.
Ассортимент весьма обширен – от тонких нитей или полос до листов, крупных панелей и сложных по геометрии профилей. Ставшие всем привычные пластиковые оконные и дверные системы собираются из ПВХ-профилей, изготовленных именно таким способом.
Добавка в полимер специальных компонентов позволяет выпускать сложные композиты, например, дерево-пластиковые конструкции, которые также часто применяются при изготовлении различных строительных конструкций.
Экструдер для производства труб
При производстве трубной продукции очень важным условием является отсутствие в гомогенизированной смеси пузырьков газа, поэтому экструдеры для труб в обязательном порядке оснащаются системой дегазации. Обычно это – двухшнековые установки, в которых, помимо прочего, применяются так называемые барьерные шнеки, надежно разделяющие еще твердый полуфабрикат от полностью расплавленного. Это обеспечивает полную однородность состава, что очень важно для эксплуатационных качеств выпускаемой трубы.
Экструдеры для полиэтилена
Все полимерные пленки изготавливаются исключительно способом экструзии. Для производства плёнок используется выдувной экструдер. Формующий узел экструдера для стрейч пленки может быть выполнен в виде узкой щели –на выходе получается однослойная пленка необходимой толщины и ширины.
В некоторых моделях используются круглые щелевые фильеры большого диаметра – пленка получается в виде рукава.
Мини экструдеры для пленки производят полиэтилен шириной рукава до 300мм и толщиной до 600 мкм. Небольшой размер устройства позволяет установить его даже в обычном помещении.
Экструзионные линии
В промышленных условиях экструдер – это один из главных компонентов целой экструзионной линии, которая включает, помимо него, ряд других установок и механизмов:
- Система подготовки и загрузки сырья – иногда полуфабрикат нуждается в предварительной просушке и калибровании перед подачей в загрузочный бункер.
- Система охлаждения – устанавливается на выходе экструдера для ускорения процесса полимеризации изделий. Могут быть различного типа – воздушные или в виде охлаждающих ванн.
- Механизмы протяжки готовых профилей.
- Маркирующие и ламинирующие системы различного принципа действия.
- Намоточные и отрезные механизмы для приведения изделий в требуемый для складского хранения и транспортировки вид.
Могут использоваться и другие механизмы и технологические устройства для автоматизации непрерывного процесса производства.
Производители экструзионных линий
Экструзионные линии пользуются огромным спросом, и их производство налажено во многих странах Европы и Азии. Традиционными лидерами в производстве подобного оборудования считаются австрийские производители, практикующие выпуск подобных линий еще с середины прошлого столетия. Европейские системы всегда отличали высочайшее качество, использование самых современных инновационных разработок в области технологии обработки пластмасс.
В последнее время на рынок экструзионных линий активно поставляется
продукция китайских производителей. Вопреки расхожему мнению, это вовсе не говорит о ее низком качестве – и надёжность, и характеристики выпускаемого оборудования в целом отвечают современным требованиям. Кроме того, цены на экструдеры из Китая могут быть значительно ниже европейских.
Стараются не отстать от жизни и отечественные промышленники. Так, пользуются спросом экструзионные линии «Полипром Кузнецк», выпускаемые в Пензенской области, или «Группы компаний СТР» из подмосковных Подольска и Воскресенска.
Цена на экструдеры для пластика варьируются от страны-производителя и индивидуальных характеристик устройства.
www.keyprod.ru
Что такое экструдер и дробилка для пластика: рассмотрим подробно изготовление труб
Трубки ПВХ (пластиковые) считаются первыми трубопроводными изделиями, которые сделаны из полимеров. Впервые такие трубные элементы были изготовлены в Германии в 1935 году, которые использовали при возведении прочной магистрали для транспортировки воды. В тот период при изготовлении трубок рабочие начали пользоваться непластифицированным поливинилхлоридом.
Из такого полимера выполняются трубы малого диаметра, которые работают без избыточного давления потока
Производство ПВХ — трубок является перспективной бизнес-идеей.
Пластиковые трубки считаются долговечными, прочными и лёгкими трубными изделиями из ПВХ — поливинилхлорида. Они хорошо переносят воздействия различных кислот и коррозии.
Кроме того, подобные трубопроводные элементы имеют высокую огнеустойчивость и экологичность.
В настоящее время в РФ производство ПВХ — трубок значительно расширилось, потому что в подобном деле применяется простая технология изготовления, а также растёт спрос на пластиковые трубные изделия.
В этой статье говорится о том, какое оборудование для производства пластиковых труб используется — какие экструдеры использует завод по производству пластиковых труб, а также описана технология изготовления.
Что такое «экструдер»
При изготовлении ПВХ — трубок рабочие используют такое сырье:
- различные полимерные соединения — для трубок высокого или низкого давления;
- полипропилен и др.
Основу изготовления ПВХ — труб составляет станок для производства пластиковых изделий – экструдер для пластика (дробилка для пластика).
Подобное устройство экструдера для пластика перерабатывает полимерное сырье (пластиковые гранулы и др.) — выдавливает трубопроводные элементы из расплавленного полиэтилена.
Трубный завод использует такие виды экструдеров:
- Шнековый экструдер для полиэтилена. Принцип действия такого устройства аналогичен тому, как работает соковыжималка;
- Бесшнековый экструдер, который используют при изготовлении трубопроводных изделий из смеси материалов. Основной рабочий компонент такого оборудования — диск;
- Комбинированная дробилка для пластика, в которой шнек соединён с диском.
Трубные заводы чаще используют шнековые экструдеры для производства изделий из пластмассы.
Оборудование для изготовления
Линия для производства труб из пластика — с использованием экструдера — включает в себя такое оборудование для изготовления пластиковых труб:
- систему подачи сырьевых материалов;
- специальную машину, которую используют при нарезании трубопроводных элементов;
- ванну, которую применяют при калибровке и охлаждении трубных элементов;
- тянущее устройство;
- транспортёрную ленту;
- формовщик — вакуумное устройство;
- накопитель, с помощью которого рабочие укладывают трубопроводные изделия.
В качестве сырьевого трубного материала используют пластиковые гранулы, которые должны обладать соответствующим качеством и сроком годности. Пластик имеет большой срок годности — наиболее подходящий трубный материал.
Станок для производства пластиковых труб
Завод пластиковых труб использует полиэтилен низкого давления (ПНД).
Приемлемый вариант при открытии бизнеса по изготовлению трубок — осуществление поставок с одного завода, потому что при смене сырьевого материала производители пластиковых труб устанавливают новое оборудование для производства труб ПНД.
Технология производства
Линия по производству ПВХ — труб заключается в использовании метода экструзии. Подобная экструзионная линия по изготовлению полипропиленовых трубопроводных элементов — закрытый и бесперебойный цикл.
При изготовлении трубных изделий из пластика рабочие используют полиэтилен марок ПЭ-80 и ПЭ-100. Подобный трубный материал имеет специальные добавки, которые существенно улучшают различные характеристики пластиковых трубопроводных изделий.
Производство из пластика — изготовление ПВХ — трубок — состоит из следующих этапов:
- сначала пластиковые гранулы помещают в загрузочный бункер дробилки, который расположен над специальным материальным цилиндром;
- потом, из бункера полиэтиленовые гранулы перемещаются в матцилиндр, в котором происходит их плавление;
- затем, при применении шнека рабочие перемещают гранулы в головку дробилки, которая придаёт конкретную форму трубной заготовке;
- потом, рабочие нагревают матцилиндр — с помощью применения кольцевого нагревателя, который установлен снаружи цилиндра;
- затем, при перемещении через головку дробилки из расплавленного полиэтилена делают трубопроводную заготовку;
- потом, калибратор обрабатывает трубопроводное изделие по внешнему диаметру и регулирует толщину трубной стенки;
- затем, трубопроводное изделие попадает в ванну, охлаждается в ней и затвердевает;
- потом, на специальном устройстве, отрезают конкретную длину трубопроводного элемента, которую отмеряют на счётчике метража;
- по окончании работ, в зависимости от заказа, трубку обматывают бухтами или поставляют отрезками.
Контроль качества
Изготовление канализационных пластиковых труб
После изготовления конкретного метража ПВХ — трубки её отправляют в отдел техконтроля — ОТК. В этом отделе котором контролёры проверяют следующие геометрические параметры изготовленных трубных изделий:
- внешний трубный диаметр;
- толщину трубных стенок;
- длину трубопроводных отрезков;
- овальность трубопроводного изделия.
Лаборанты делают выборку контрольных образцов — из каждой партии произведённых трубок. Используя контрольные образцы, рабочие проводят контрольные испытания готовых трубных изделий в специальной испытательной лаборатории.
Если произведённая трубная партия успешно прошла контрольные испытания, то контролёры завода выписывают документ, который подтверждает качество трубопроводного изделия — и готовую пластиковую трубку отправляют к потребителю.
При производстве качественных пластиковых трубных изделий должны быть обеспечена бесперебойная работа всех элементов подобной технологической цепи.
В итоге процесс изготовления трубок из пластика считается автоматизированным — в подобном деле отсутствуют большие затраты энергии и трудовых ресурсов.
ПОСМОТРЕТЬ ВИДЕО
Также в процессе производства трубопроводных изделий из пластика не образуются никаких вредных отходов — экологически чистый процесс. Кроме того, изготовление подобных трубок считается достаточно компактным – площадь 1 линии производства равна 100 кв. м. как максимум.
trubexpert.ru
Экструдер своими руками
Экструзия является популярным методом получения полуфабрикатов или товаров, произведенных из полимеров любой длины, поэтому сделанный экструдер своими руками в некоторых случаях позволит сэкономить вам деньги. Данный процесс используют в пищевой промышленности или в производстве комбикорма. Процесс происходит так: расплав полимера выдавливается при помощи головки экструдера в формующую головку с необходимым профилем. Данный способ производства наряду с литьем пластмассовых материалов под давлением сейчас один из наиболее популярных. Практически все полимеры могут подвергаться экструзии: термопласты, эластомеры и другие материалы.

Схема работы сварочного экструдера.
Технология экструдера применяется уже больше шестидесяти лет. За этот длительный период появилось достаточно большое количество машин, которые изготовлены специально для использования данной технологии. Если детально рассмотреть экструдер, то можно понять, что это такое. Процесс экструзии является достаточно сложным, основан он на физических и химических законах. Процесс проходит непосредственно под влиянием механических действий при воздействии высоких температур и наличии влаги. Из-за того, что механическая энергия обращается в тепло, которое выделяется вследствие внутреннего трения, при обработке материал подвергается нагреву.
При обработке экструзионной техникой есть несколько сменных характеристик: состав предоставляемого сырья, процент его влажности и природа. При производстве может меняться давление, температура и т.д.
Применение:
- переработка кормов;
- производство пластика и полиэтилена;
- изготовление труб;
- пищевое производство.
Немного истории

Схема экструдера для пластика.
Экструдер начали применять еще в далеком девятнадцатом столетии. А серийное производство этого оборудования началось в двадцатых годах прошлого века. Сейчас экструдеры значительно отличаются от тех, что были раньше.
В современной промышленности экструдеры пользуются большой популярностью, причем выбрать можно из самых разнообразных видов. Купить новый экструдер — достаточно дорогое удовольствие. Но есть экструдеры, которые можно сделать своими руками.
Наиболее простыми в изготовлении являются экструдеры для глины и кормовые. Чтобы самостоятельно сделать другие виды этого оборудования, необходимо иметь хотя бы какие-нибудь базовые инженерные знания. А для изготовления этих экструдеров требуется не так много времени, и материалы стоят недорого.
Вернуться к оглавлению
Детали экструдеров

Схема экструзии.
- Головка экструдера. Она состоит из корпуса, который обогревается, и инструмента формующего с отверстием. Корпус прикрепляется к экструдеру. Отверстие инструмента может быть сужающимся к центру или в виде круглого канала. Обязательно должен быть раздатчик в виде спирали.
- Корона или активатор улучшает адгезию поверхностей материалов. Активаторы бывают разные, они отличаются по мощности, ширине, бывают с фиксацией односторонней и двусторонней или же с изменяющейся шириной переработки поверхности.
- Горячий нож. Горячий нож достаточно просто устроен, но его нужно правильно направлять относительно рукава, которые движется. Данный элемент увеличивает выход продукции почти в два раза. Горячий нож используется в экономичных целях.
- Шнек может и отсутствовать в оборудовании. Он предназначен для того, чтобы была большая производительность и хорошая гомогенизация расплава обрабатываемого материала полимеров.
- Узел тиснения. Он нужен для придания пленке особой жесткости и товарного красивого вида.
- Узел, обеспечивающий вращение головки. Вращение головки экструдера размещает постоянные неровности пленки, при этом качество рулона делается лучше, но качество пленки не повышается.
- Фальцовочное устройство оборудования.
- Тянущее устройство экструдера.
- Намотчик оборудования.
- Обдувочное кольцо экструдера.
Вернуться к оглавлению
Экструдеры для глины своими руками

Для изготовления простейшего экструдера для глины потребуется обычная пластиковая бутылка любой формы.
Такие экструдеры называют экструдеры для лепки. С их помощью можно работать с разнообразными глинами и пластилином. Данные экструдеры позволяют делать различные детали и фигуры. К примеру, можно изготавливать человеческие волосы или отчетливо рисовать траву.
Основой для этого экструдера выступает простая пластиковая бутылка прозрачного цвета. Ее необходимо хорошо вымыть и высушить, и крышку тоже.
Из крышки с внутренней стороны нужно извлечь пластину. Сделать это можно иголкой или булавочкой. Далее в ней необходимо сделать отверстие, из которого будет выдавливаться глина. Его диаметр должен быть таким, как толщина желаемых линий. Это производится с помощью острого ножа. Края отверстия делаются гладенькими.
Дальше необходимо взять диск из металла, к которому нужно прикрепить ручку в форме буквы «Т». Получившийся экструдер должен быть похож на шприц. Пластина должна быть приготовлена из прочного материала, чтобы во время работы она не изменила свою форму под воздействием давления.
Вернуться к оглавлению
Немного об экструдере для сварки
Благодаря ручному сварочному экструдеру можно делать много видов разнообразных работ с полипропиленом и полиэтиленом.
Сначала может показаться, что данные материалы не являются очень распространенными и редко где применяются.
Но в действительности их применяют во многих сферах. Из подобных материалов с помощью данного типа ручного экструдера делают системы для очищения воды, различных типов емкости и т. д. Преимущественно данные материалы пойдут как вспомогательные, но без них в любом случае нельзя обойтись.
Сварочный ручной экструдер имеет ряд преимуществ. Любая выбранная модель экструдера для экструзионной сварки будет гораздо лучше других.
Главным преимуществом такого оборудования считается простота в эксплуатации.
Подобным экструдером работать можно абсолютно в любом помещении и при различных условиях. Проще говоря, для работы не надо подготавливать специально обустроенное пространство или рабочий цех.

Схема бесконтактной и контактно-экструзионной сварки.
Ручным экструдером для сварки можно делать швы на разнообразные формы и конструкции. Это достаточно удобно, ведь при этом можно самостоятельно контролировать всю работу. Нередко случается, что в одном районе шов нужно сделать тонким, а немного дальше — толще. Ни одно оборудование не может такого сделать автоматически.
Помимо всего вышеперечисленного, стоит учесть, что данное устройство не слишком дорого стоит. Его цена будет приемлема практически для любого человека. Экструдер сварочный необязательно применять во время производства. Довольно часто его применяют дома. Дальнейший уход и обслуживание не заберут много денег. Данный экструдер может производить свою работу в течение многих лет, и он всегда остается актуальным и нужным приспособлением.
Ручные сварочные экструдеры бывают таких видов:
- безшнековые;
- шнековые;
- комбинированные.
Комбинированные экструдеры уместно применять при обработке композитного товара. В данных устройствах применяют и дисковую зону, и шнековую часть. Данное оборудование еще называют червячно-дисковым. К тому же у данного типа экструдеров есть прекрасная смесительная особенность.
Экструдеры, которые не имеют шнеков, используют для производства раствора полимеров, имеющих элементы высоко качества.
Обычно, приобретая данную продукцию, в комплекте покупатель получает несколько специальных насадок и подставок, но производители разные, поэтому и комплектация оборудования также различная. Сварочный ручной экструдер может работать при температурах от 180 до 260°С. Чтобы привести в работу устройство, необходимо подключить его к электрической сети. Желательно подключать его к напряжению в 220 В.
Экструзионная сварка — достаточно сложный процесс, поэтому чтобы сделать своими руками экструдер, необходимо иметь определенные знания и навыки. Разумнее будет приобрести оборудование у надежного производителя.
expertsvarki.ru
Ручной сварочный экструдер
Июль 4, 2017
Ручной сварочный инструмент — экструдер — сегодня уже не является чем-то необычным, сверхъестественным. Благодаря современным технологиям появилась возможность создавать подобный инструмент своими руками.
Экструдер предназначен для выполнения неразъемных соединений различных пластмассовых изделий, которые осуществляются посредством подачи расплавленной массы материала в разогретую ванну, формирующуюся кромками свариваемых образцов.
Применяют данный инструмент для производства емкостей, листовых изделий, устранения повреждений на пластмассовых конструкциях, к примеру, пайка автомобильных бамперов, сделанных из пластмассы.
Слабых мест экструдер не имеет, он отличается продолжительным сроком службы, прост в эксплуатации. Предприимчивые люди приобретают полуфабрикаты из пластмассы и с помощью данного инструмента изготавливают неповторимые конструкции. Одним из подобных проектов можно отметить «баню, организованную на воде». В качестве основания для нее был использован понтон.
Технические характеристики экструдеров РСЭ-1 и РСЭ-3
РСЭ-1 | 580\300\200 | 6 | ПЭ,ПП (гранулы, дроблёнка-вторичка) | до 3 | зависит от диаметра сопла | 0.35 кг | 220 В. | 2 000 Вт |
РСЭ-3 | 520\200\200 | 6.6 | Пруток круглый, сечение — 4 мм | до 2 | Зависит от диаметра сопла, 3—12 мм | — | 220 V, 50 Гц | 2 000 Вт |
Экструдер для сварки своими руками
Подобная идея возникла более чем 60 лет назад, поэтому до сегодняшнего дня она подверглась множествам различных изменений и стала практически идеальной. Появилось огромное количество механизмов, которые отличаются техникой воздействия, но практически однообразных в плане получаемых конструкций.
Как нагревается основа предполагаемой детали? Все достаточно просто: в результате механических процедур вырабатывается тепловая энергия, способствующая дополнительному нагреванию пластика. Не исключены тепловые воздействия извне. В данном случае процесс зависит в большей степени от первоначальной структуры экструдера.
Принцип работы инструмента
Экструдер не является сложным инструментом в управлении, существует три варианта исполнения:
- холодная формовка;
- горячая экструзия;
- обработка тепловая.
Горячая формовка сегодня является самой востребованной технологией. Процедура осуществляется с высокой скоростью и под максимальным давлением. Для ее реализации используется шнековый экструдер, основным элементом конструкции которого является шнек особенной формы. Процедура формовки в данном случае выполняется на выходе. Сырьевой материал вместе с используемыми добавочными элементами помещается в специальную камеру.
Заводские аппараты имеют возможность обустройства специальными устройствами, от которых зависит смешивание, перемещение сырьевых компонентов.

Производство
Как сделать своими руками ручной сварочный экструдер для соединения изделий из полипропилена? Процедура сборки подобного инструмента не представляет особых трудностей, как может показаться на первый взгляд. Собрать его под силу любому желающему.
Изготовление экструдера — это достаточно увлекательный процесс, напрямую зависящий от предназначения, формы аппарата.
Чем может отличаться самодельный экструдер от заводского:
- сборкой элементов конструкции;
- числом рабочих камер;
- присутствием дополнительных систем.
Неизменной остается цилиндрическая форма инструмента. Сегодня она считается наиболее технологичной, поэтому остается без изменений.
Технологические отличия
Необходимо еще осветить несколько достаточно важных моментов, в частности это касается процедуры прохождения сухой экструзии, которая напрямую зависит от тепловой энергии, выделяемой самим аппаратом, образующейся в процессе работы. Также остается возможность привлечения к процессу пара, для которого есть в наличии индивидуальная камера. Пар необходим для увеличения износоустойчивости оборудования.Технология отличается высокой скоростью выполнения работ, процедура осуществляется всего лишь на протяжении 30 секунд. Аппарат для сварки пластика за такой короткий промежуток времени успевает выполнить с сырьем следующие операции:
- измельчение;
- обезвоживание;
- смешение;
- обеззараживание;
- стабилизация;
- увеличение объема.
Для самостоятельного изготовления ручного экструдера в домашних условиях нужно приобрести определенный перечень деталей:
- шнек необходимой формы;
- электродвигатель;
- корпус для устройства;
- емкость подачи;
- емкость выходная;
- камера вакуумная.
Чтобы сделать в бытовых условиях инструмент для сварки пластиковых изделий своими руками, достаточно понять процедуру создания экструдера, его рабочий принцип.
electrod.biz