Основы теории технологических процессов листовой, объемной штамповки, ковки. Формовка металла
вытяжка металла
Вытяжка металла является довольно распространённой операцией при производстве деталей автомобилей, или мотоциклов (да и вообще большинства транспортных средств) из стального листа и применяется повсеместно — от промышленного производства до обычной гаражной мастерской. В этой статье, рассчитанной больше на новичков, будут описаны операции, связанные с вытяжкой листового металла и придания плоской заготовке объёма, а так же способы, с помощью чего можно придать листовой заготовке объём.
Оговорюсь сразу, что в этой статье о промышленной вытяжке (формовке) листового металла с помощью специальных прессов (штампов) будет сказано не много, так как это промышленное оборудование недоступно для гаражной мастерской и главный упор будет дан на более простой ручной труд, который можно использовать даже новичкам, в обычной даже домашней мастерской.
Вытяжка металла — что это такое.
Вытяжка заготовок из листового металла— это формовочная операция, которая осуществляется на производстве в специальных вытяжных штампах (или вручную, но об этом ниже). С помощью этой операции происходит процесс превращения плоской листовой заготовки в объёмную (выпуклую) и полую деталь, имеющую замкнутый контур кромок. А получение полых объёмных деталей разной формы из полых и уже предварительно отштампованных заготовок, является повторной вытяжкой листового металла.
Процесс вытяжки осуществляют как без преднамеренного утоньшения стенок листовой заготовки, так и с утоньшением её стенок. При первом варианте вытяжка стального листа осуществляется без заранее рассчитанного изменения толщины стенок заготовки. А во втором варианте вытяжка осуществляется за счет заранее рассчитанного изменения поперечного сечения детали и утоньшения её стенок. Вообще утоньшение стенок при вытяжке происходит в любом случае, но как было описано выше — с расчётом и без.
Вытяжка листового металла бывает обычной и глубокой. При глубокой вытяжке стального листа избыточный объём листового материала как правило является причиной образования морщин (складок) на заготовке. И чтобы получить полую выпуклую заготовку вытяжкой без получения складок, следует нагревать заготовки, получать объём в несколько приёмов и иметь сравнительно небольшую разницу между диаметром заготовки и диаметром цилиндра.
А за одну операцию вытяжки можно получить отштампованные детали относительно небольшой высоты. Ну а для того, чтобы предотвратить образование складок, следует применять штампы, в которых листовая заготовка перед началом процесса вытяжки прижимается к поверхности матрицы специальным прижимом, так называемым «складко-держателем».
И как было сказано выше, при глубокой вытяжке эту операцию осуществляют в несколько приёмов (в несколько переходов), в зависимости от соотношения высоты и диаметра формуемой листовой заготовки, а также в зависимости от относительной толщины стенок детали. И в несколько приёмов осуществляют вытяжку с постепенным уменьшением диаметра заготовки, а так же с увеличением высоты полости вытягиваемой заготовки.
При глубокой вытяжке степень деформации металлического листа, который образует стенки заготовки, возрастает по мере удаления от дна заготовки к её кромкам. И следует отметить, что в донышке детали металлический лист почти не испытывает пластической деформации, а у кромок заготовки металл испытывает наибольшие структурные изменения, а в районе стенок металлический лист испытывает наибольшее растяжение.
При вытяжке металла следует учитывать коэффициент вытяжки m . Коэффициент вытяжки — это отношение диаметра d готовой детали к диаметру D изначальной заготовки.
При вытяжке и формовке какой то детали из листового металла, каак знают многие, применяют специальные прессы (штампы), развивающие давление в несколько тонн и которые вдавливают паунсон в матрицу, размеры и форму которых принимает заготовка при её формовке (соответственно заготовка укладывается между паунсоном и матрицей). Наглядно применение простейшего пресса, паунсона и матрицы я описал вот здесь, при выдавливании выпуклостей на листовом металле обода колеса, который имеет толщину 2,5 мм.
Однако при формовке (вытяжке) следует учесть, что чем больше радиус закругления листового материала, тем меньше напряжение в этом материале и соответственно меньше утоньшение стенок заготовки. Но если сделать слишком большой радиус закругления кромок матрицы, то это приведёт к образованию складок на формуемой детали.
И радиусы закруглений кромок на матрице делают в зависимостиот толщины материала заготовки и глубины её вытяжки и вычисляют опытным путём, в зависимости от пластичности разного листового материала (металла или сплава).
Ну а радиус закругления пуансона по возможности делается равным радиусу закругления матрицы, если лист не слишком толстый. Однако при более глубокой вытяжке и использовании более толстого материала, радиус и другие размеры паунсона (его высота и диаметр) может быть взят и значительно меньшим, соответственно требуемой форме формуемой заготовки и толщины материала.
Следует помнить, что минимально допустимый радиус закругления пуансона должен быть равен толщине вытягиваемого материала умноженной на два (удвоенной толщине). И если радиус закругления кромок пуансона будет слишком мал, то это приведёт к значительному утоньшению материала заготовки, или заклиниванию детали между паунсоном и матрицей.
Как правило зазор между пуансоном и матрицей в промышленных вытяжных штампах делают по наибольшей допустимой толщинелистового материала, который будет использоваться при вытяжке, причём делают ещё и с добавкой на утолщение краёв детали при её вытяжке.
Ну а для окончательного перехода при вытяжке заготовки с заданным наружным размером детали, зазор в так называемом»бутерброде» (паунсон-заготовка-матрица) устанавливают за счет пуансона. А если при вытяжке имеется заданный внутренний размер готовой детали, то нужный зазор делают за счет наружной поверхности матрицы. Ну а в процессе вытяжки, при всех переходах формовки детали, (кроме последнего окончательного), направление зазора не учитывают, так как это не имеет значения.
Вытяжка металла с использованием ручной выколотки.
Ну а теперь мы переходим к более интересной обработке листового материала, с точки зрения гаражных мастеров и вообще более простого гаражного оборудования. Вид ручной обработки листового материала, который будет описан ниже, не смотря на простейший инструмент и простейшее оборудование, (по сравнению с заводским оборудованием), позволяет сделать многое и придать листовому металлу практически любую форму.
Формовка, вытяжка, выколотка или дифовка — это очень древний вид холодной обработки листового металла (сплава), который применялся ещё всредневековые времена для изготовления щитов, шлемов рыцарских доспехов. Сам процесс обработки осуществляется с помощью ударов молотка (киянки) от который материал за счёт своей элластичности изгибается, вытягивается, садится и в результате этого принимает нужную форму.
Следует отметить, что от кузнечной ковки этот вид деятельности отличается тем, что он осуществляется в холодном состоянии (как известно многим — при кузнечной ковке маталл нагревается докрасна). И в большинстве случаев ручная выколотка или дифовка (что в принципе одно и то же) применяется для листового материала не толще 2 мм., а кузнечные работы производят из массивных заготовок.
И ещё следует написать, что выколотка (дифовка) так же отличается и от чеканки, так как здесь не используют чеканы (специальные деревянные инструменты для выдавливания при чеканке), а используется только лишь молоток, или киянка, или механический молоток (о механическом молотке я как нибудь напишу отдельную статью, когда закончу его изготовление).
Кстати, хочу заметить, что примером крупных работ, выполненных с помощью выколотки, была сделана статуя Свободы в Америке (на острове Либерти на входе в гавань города Нью-Йорк), которая была выколочена из медных листов, имеющих толщину 2мм. Также по этой технологии была изготовлена и наша отечественная крупная скульптура «Рабочий и колхозница».
Многие видели эту скульптуру в начальных кадрах фильмов, которые были сняты на киностудии «Мос-фильм». Но мало кто знает, что этот выдающийся монумент (высота фигуры мужчины и женщины достигает 24 метра!) выколочен вручную из листовой хромо-никелевой нержавеющей стали, имеющей толщину около 1 мм.
Также ручная выколотка применялась в прошлом веке на многих автомобильных заводах для формовки деталей автомобиля (до появления штампов) а в большинстве кастом мастерских детали машин и мотоциклов изготавливают этим способом и по сей день. Кстати примеры работ, по изготовлению деталей мотоциклов можно найти и у меня на сайте в рубрике тюнинг мотоцикла (одну из работ можно почитать и посмотреть вот здесь, а так же в видеоролике чуть ниже).
Выколотку (дифовку) можно условно разделить на три вида: механизированная выколотка, ручная свободная выколотка и выколотка по болванке (модели). Однако всё это условно и при изготовлении множества деталей из листового материала можно использовать любой вид, а так же чередовать разные виды обработки даже для одной детали.
Конечно же всё зависит от поставленных задач, творческих планов, от фантазии и от форм деталей которые требуется получить в итоге. Все виды ручной обработки листового металла каждый мастер выбирает сам и в процессе накопления опыта и оборудования, уже может понять что использовать в каком то конкретном случае и для какой детали.
Технология ручной выколотки.
Как было упомянуто мной выше, свободная ручная выколотка листового металла является древнейшим видом обработки, но она применяется и сейчас во многих кузовных и кастом-мастерских. Основная задача при выколотке (дифовке) — это создание объёмного полого изделия из листового металла (сплава). Эта техника состоит из нескольких последовательных процессов (в основном 3 основных процесса).
Один из процессов заключается в расплющивании листовой заготовки на плоской наковальне с помощью стального молотка, где получается увеличение площади листа за счёт уменьшения его толщины. Расплющивание происходит если равномерно ударять молотком по всей поверхности листовой заготовки.
Следует учесть, что если наносить удары молотком по небольшому участку заготовки (например по её середине) не затрагивая краёв заготовки, то она будет не только расплющиваться и уменьшаться по толщине в местах ударов, но будет одновременно девормироваться образовывая сферическую поверхность, которая будет вогнутая со стороны ударов и выпуклая с противоположной стороны. Сферическая поверхность будет образовываться потому, что нетронутые ударами края заготовки (которые остались толще в поперечном сечении) не дадут листовому металлу раздаваться в стороны.
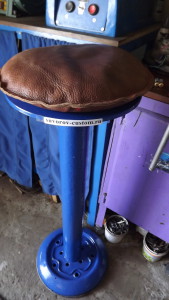
Изготовленная мной стойка и кожаная подушка для отбивки выпуклостей.
Кстати сферическую (или выпуклую) поверхность листовой заготовке гораздо быстрее и эффективнее сделать не на плоской и твёрдой наковальне, а на мягкой кожаной подушке (как на фото слева), набитой песком или дробью (или на деревянном пеньке с углублением) и этот процесс я как раз показываю в своих видеороликах у меня на канале Ютуба (канал suvorov-custom) и один из видеороликов показан чуть выше.
Второй процесс обработки — это сгибание листового металла, при котором вогнутая сторона заготовки испытывает сжатие, а выпуклая сторона перетерпевает растяжение. Сгибание стальной заготовки осуществляют с помощью молотка или киянки на гладком ребре наковальни (кстати боёк инструмента может быть стальным отполированным, или из мягкого материала, или сплава — об инструменте я напишу подробнее ниже).
Сгибание заготовки можно выполнить по радиусу и под углом, по дуге, по кривой, или просто по прямой линии и всё зависит от творческих задач, а так же от выбора формы ребра фасонной наковальни. При сгибании происходит ещё и вытяжка металла.
Третий процесс — это осадка металла, при которой увеличивается толщина листового металла (в поперечном сечении). Вообще осадка в большинстве случаев применяется для сжатия кромок листового металла. Чтобы сжать листовой металл у кромок можно использовать также и Шринкер, о котором я подробно написал вот здесь.
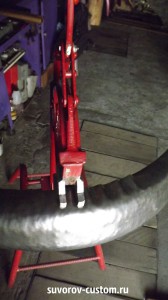
выдавливание гофров на самодельном крыле
Но у кого нет шринкера, то для сжатия используют осадку металла, перед которой производится гофрирование кромок заготовки. А после гофрирования они осаживаются молотком или плоской лопаткой (см. фото справа) и этот процесс я наглядно показал в видеоролике ниже.
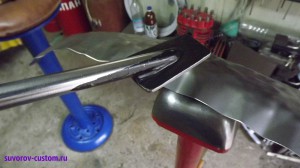
выравнивание волн и гофров на крыле с помощью лопатки
Там показана более совершенная гофрилка (как на фото слева), но можно использовать и более простую, представляющую два конических штыря (я их показал в видео).Гофрирование и осадка листового металла является более сложным процессом чем обычная формовка и требует некоторых навыков, которые приходят с опытом.
Однако в большинстве мастерских уже не используют сжатие металла с помощью осадки (и гофрилок) и как правило применяют Шринкер и Стретчер. Но всё же для новичков следует написать несколько строк об осадке с помощью гофрирования.
Гофры на листовом металле (сплаве) по возможности должны быть низкими и широкими — так их легче выводить (осаживать). А узкие и слишком высокие гофры при осадке нагоняются друг на друга и при этом могут образовываться трудноустранимые складки и даже трещины в листовом металле. Так же важно чтобы гофры не были подсечены или завалены на одну сторону.
Ну и ещё важно чтобы рабочие поверхности губок гофрилки были отполированы до зеркального блеска и закалены. Это позволит не оставлять на поверхности листового металла (сплава) царапины и другие повреждения, а твёрдость полученная закалкой позволит не изнашиваться губкам гофрилки довольно длительное время.
Инструменты и приспособления.
При выколотке (дифовке) вручную применяются различные опорные и ударные инструменты. Из ударных инструментов следует иметь различные по форме бойков молотки и киянки, которые изготавливают из различных материалов.
Молотки могут быть из прочных сталей и их бойки должны быть обязательно отполированы и закалены. Так же молотки могут использоваться с бойками из материалов имеющих меньшую твёрдость, чем обрабатываемая заготовка. Например молотки изготавливают из меди, датуни, бронзы, алюминия и даже свинца. А киянки могут быть из прочных пластиков, твёрдой резины, текстолита, капролона, бука, граба, самшита, дуба и других подобных материалов.
Только деревянные молотки должны быть снабжены латунными кольцами вокруг бойков, чтобы предотвратить растрескивание древесины. При ударах молотками (или киянками) с мягкими бойками, обрабатываемый материал (особенно из мягких сплавов, типа алюминия) меньше гартуется и на обрабатываемой поверхности не остаётся царапин и засечек.
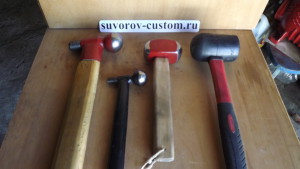
Изготовленные мной молотки для придания выпуклости.
Однако если глубина вытяжки небольшая, то вполне можно использовать и стальные отполированные бойки, которые за счёт своей гладкой зеркальной поверхности так же не оставляют на поверхности заготовки никаких повреждений.
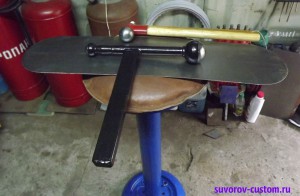
Изготовленные мной молотки для выколотки крыла (для разной глубины выпуклости)
И я почти всегда пользуюсь молотками с сферическими стальными бойками (например таким как в видео выше и на фотографиях справа и слева), которые очень эффективны и работа по выколотке осуществляется гораздо быстрее.
Ручную выколотку для вытяжки металла производят на наковальнях изготовленных из стали, меди или свинца, а так же на деревянном пеньке (колоде) с углублением или на кожанной падушке. Также выколотку в некоторых случаях производят на специальных опорных приспособлениях, которые представляют из себя опорные стойки с закреплёнными на них наковаленками разной выпуклости, или имеющие различный изгиб. И разумеется форма опорной поверхности зависит от формы детали, которую в итоге необходимо получить.
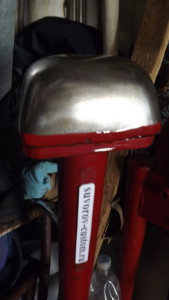
Изготовленная мной наковаленка полукруглая, но с более острыми углами.
Все опорные приспособления (например как на фото слева и справа — показаны мои самодельные наковальни разной выпуклости) можно изготовить самостоятельно из металлических болванок, что я и сделал. После обточки поверхности наковаленок их необходимо ошлифовать, отполировать и закалить. А некоторые опорные приспособления (в том числе и для механического молотка) вполне возможно выточить из болтов большого размера.
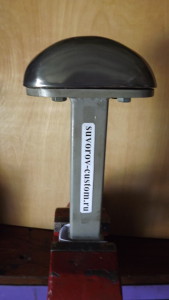
Изготовленная мной наковаленка полукруглая.
Но сейчас уже вполне возможно приобрести в интернет магазинах (или в автомагазинах в крупных городах) наборы различных поддержек (небольших наковаленок) предназначенные для кузовного ремонта.
Кроме ударных и опорных инструментов для вытяжки металла (ручной выколотки) потребуются и другие инструменты, с помощью которых необходимо вырезать листовой металл, подрезать его кромки и обрабатывать их.
Для этих целей подойдут распространённые слесарные инструменты: круглогубцы, плоскогубцы, ножницы по металлу (ручные или электрические), угло-шлифовальная машинка (болгарка), электро-лобзик, различные напильники, шлифовальные диски и прочие инструменты, которые я уже описывал, например в статьях про кузовной ремонт.
Практика вытяжки металла (ручной выколотки).
Конечно же формовку металла (его вытяжку с помощью выколотки) лучше наглядно посмотреть в одном из моих видеороликов на моём канале. Но всё же ниже следует написать основные моменты, так сказать азы ручной выколотки, например при изготовлении полусферы из листового металла. Ведь во многих изделиях изготовленных из листового металла имеются поверхности, близкие к сферическим.
Для наглядности вырежем из алюминиевого или медного листа два одинаковых круга, диаметром примерно 15 — 20 сантиметров (для новичков лучше начинать с более мягких сплавов, так как они более мягкие и эластичные, а по мере накопления опыта можно пробовать работать со сталью).
Уложив один из кругов на плоскую наковальню, далее можно равномерно проковать его молотком со стальным полированным бойком. После проковки заметим, что кружок остался плоским, но стал немного больше в диаметре, чем второй круг, который не подвергался обработке (проковке). Это значит, что в местах ударов листовой металл стал тоньше, но пропорционально увеличился по своей площади.
Теперь возьмём второй круг и начнём выколачивать его с середины, и постепенно, нанося удары по спирали, уходим к краям круга. Причём, приближаясь к краям кружка, постепенно уменьшаем силу ударов. При этом становится видно, что края круга начинают постепенно выгибаться, а в середине кружок приобретает вогнутость.
Причём там где вогнутость ( где наносились более сильные и частые удары) метал стал тоньше, а на краях, где ударов было меньше (и сила удара тоже) метал остался толще. А сам круг получил вогнутую с одной стороны поверхность, а с другой стороны выпуклую поверхность.
Теперь можно повторить проковку как первого (плоского) круга — чтобы увеличить его диаметр, так и второго выпуклого круга (чтобы увеличить его выпуклость). Проковав оба кружка несколько раз, в определённый момент можно будет почувствовать, что геометрическая форма и размеры заготовок из листового металла остаются неизменными, сколько бы усилий (ударов) мы не прилагали к ним.
А всё дело в том, что с листовым металлом произошло явление называемое наклёпом (или нагартовкой). То есть прокованный металлический лист сильно нагартован и в нём возникли большие напряжения, которые не дают заготовке изменять форму дальше.
Чтобы продолжить работу по вытяжке металла и увеличению его выпуклости (или по увеличению площади) необходимо снять напряжения с помощью отжига заготовки. Отжиг можно произвести с помощью газовой горелки, паяльной лампы, или просто на газовой плите. При этом сталь, медь, латунь или бронзу следует нагреть докрасна и дать заготовке медленно остыть.
А вот для отжига алюминиевых сплавов разумеется требуется более низкая температура (ведь температура плавления алюминия составляет 680º) и алюминий нельзя нагреть до красна — он попросту расплавится. Для того чтобы понять насколько греть, есть несколько способов: например начертить через всю поверхность алюминиевой заготовки линию хозяйственным мылом и как только линия начнёт чернеть, нагрев заготовки прекращаем.
Ещё один вариант — это нанести копоть на поверхность заготовки, если на газовой горелке перекрыть кислород и добиться горения одного лишь газа, который и закоптит поверхность детали. После того,, как заготовка станет чёрной от копоти, открыв кислород добиваемся нормального пламени и начинаем греть деталь, пока копоть не исчезнет. Обязательно греем поверхность постоянно перемещая горелку, не задерживаясь на одном месте.
После отжига листовой металл (или сплав) снова становится ковким, пластичным и мягким и можно снова продолжать работу по вытяжке металла выколоткой, до тех пор, пока заготовка вновь не нагартуется.
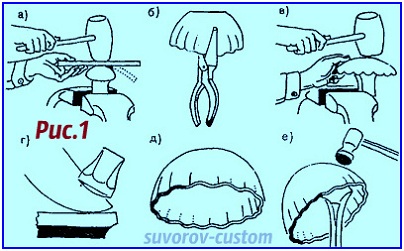
Этапы изготовления полусферы
Последовательность операций по выколачиванию полусферы не сложна даже для новичков и показана на рисунке 1 и 2 слева и справа. Выколачивать полусферу можно на плоской наковальне, но лучше чтобы она имела кое какую выпуклость.
А ещё лучше и быстрее выколотить объём, как я уже говорил, с помощью кожаной подушки (фото выше), набитой песком или дробью, или уложив заготовку на углубление в деревянном пеньке (как показано на видео ниже, где я изготавливаю фару из плоского стального листа).
При первоначальной проковке заготовки глубина полусферы должна составлять где то одну шестую часть радиуса круглой заготовки. После проковки необходимо нанести на кромки заготовки гофры (как показано на рисунке или в видео). При нанесении гофров с помощью гофрилки следует стараться чтобы гофры (желобки) были направлены на центр круга и имели плавные поверхности. А высота каждого желобка должна быть примерно равна его ширине.
После нанесения гофров необходима следующая операция, которая уже была описана выше — осадка. Она осуществляется с помощью молотка с немного сферическим (полукруглым) бойком, или плоской лопаткой, которую я использую в видео по изготовлению модели крыла мотоцикла (для алюминия лучше использовать пластиковые киянки). После простукивания гофров молотком, киянкой или лопаткой, там где были гофры листовой металл станет толще, чем был.
За счёт этого диаметр заготовки (или радиус крыла мотоцикла — о изготовлении крыла и нанесении гофров на крыле читаем тут) станет меньше. После осадки гофров необходимо опять немного выколотить середину, при этом добиваясь плавного перехода от середины к краям.
Но как правило, на этом этапе работы, полусфера пока ещё не имеет достаточной глубины (выпуклости), ведь готовая полусфера должна быть равна половине её диаметра. Значит заготовку снова нужно отжечь, заново нанести гофры, выполнить осадку и опять выколотить середину с плавным переходом к краям.
Изготовление полусферы это основа для новичков, которые впоследствии желают сделать какие то более сложные объёмные детали из листового металла. И впоследствии опыт в формовке и вытяжке металла придёт и каждый поймёт, что при изготовлении различных изделий, имеющих более сложную форму (например баки, крылья, фрагменты кузовов ретро-автомобилей, скульптур и т.п.) сначала формуют фрагменты деталей, представляющие простые геометрические формы (полусфера, конус, цилиндр и т.п.) и затем эти фрагменты подгоняют и стыкуют между собой, ну и соединяют с помощью сварки.
Надеюсь эта статья о вытяжке металла (его формовке, дифовке — ручной выколотке) будет интересна и полезна начинающим мастерам, а если полезна, то не забудьте поделиться с друзьями, нажав на кнопки ниже, успехов всем.
suvorov-castom.ru
Основы теории технологических процессов листовой, объемной штамповки, ковки
Вытяжка - это технологическая операция ЛШ, заключающаяся в превращении плоской или полой заготовки в открытое сверху полое изделие замкнутого контура. По геометрической форме получаемых деталей выделяют вытяжку изделий осесимметричной, коробчатой и сложной несимметричной формы. Кроме того, различают вытяжку с прижимом и без прижима, а также с утонением и без утонения стенок.
Схема вытяжки без прижима приведена на рис. 1.15. Пуансон, воздействуя на центральную часть заготовки (рис. 1.15а), вызывает ее прогиб за счет создания изгибающего момента со стороны матрицы и пуансона. Дальнейшее опускание пуансона приводит к появлению радиальных растягивающих напряжений, достаточных для перевода фланцевой части заготовки в пластическое состояние. С этого момента начинается втягивание заготовки в матрицу с образованием боковых поверхностей вытягиваемого изделия при одновременном уменьшении диаметра заготовки. Действие радиальных растягивающих напряжений σρ приводит к тому, что во фланце в тангенциальном (широтном) направлении возникают сжимающие напряжения σθ. Совместное действие этих напряжений обеспечивает втягивание фланца в отверстие матрицы и получение изделия (рис. 1.15б).
За одну операцию вытяжки можно получить одну неглубокую деталь, т.к. при больших степенях вытяжки в опасных зонах (переход от фланца к стенке и от стенки к дну) величина радиальных растягивающих напряжений от может превышать максимальную σρmax , что приведет к отрыву фланца или дна от стенки детали.
Напряженно-деформированное состояние в исследуемых сечениях в случае вытяжки с прижимом представлено на рис. 1.16.
Сечение 1. Фланцевая часть находится под воздействием тангенциальных и осевых сжимающих напряжений и радиального растягивающего, то есть реализуется объемная схема напряженного и деформированного состояния. Без прижима осевые напряжения σz равны нулю.
Под воздействием такой схемы напряженно-деформированного состояния с наличием максимальной величины тангенциальных напряжений сжатия (σθmax) возможна потеря устойчивости фланцевой части заготовки и образование гофр (складок). Для предотвращения этого явления используется прижим или складкодержатель, при применении которого осевая деформация εz значительно уменьшается и стремится к нулю, что обеспечивает снижение складкообразования вследствие уменьшения толщины фланцевой части.
Сечение 2. В данном сечении перехода от фланца к цилиндрической части изделия реализуется сложная деформация, вызванная пространственным изгибом, наибольшим радиальным растяжением и незначительным тангенциальным сжатием. Действующие в этом сечении радиальные растягивающие напряжения являются максимальными и могут привести к отрыву фланцевой части заготовки, особенно при большой величине силы прижима Q.
Сечение 3. В стенке (цилиндрической части) полого изделия реализуется линейно-напряженное и плоско-деформированное состояние.
Сечение 4. Часть данного закругления изделия является наиболее опасным с точки зрения возникновения трещин сечением. Это вызвано действием объемной схемы напряжений двухосного растяжения и одноосного сжатия, под действием которых происходит значительное утонение стенок в этой части заготовки. Для предотвращения отрыва дна от стенок, что является следствием действия такой схемы н.д.с., необходимо, чтобы величина радиальных растягивающих напряжений не превышала σθmax.
Сечение 5. Дно изделия находится в плоско-напряженном и объемно- деформированном состоянии. На первом переходе вытяжки толщина металла практически не изменяется, а на последующих операциях дно значительно утоняется.
Таким образом, при вытяжке возникает разноименная схема напряженного и деформированного состояния. Следствием этого является различная толщина стенок изделия, что может привести к трем основным причинам брака при вытяжке: складкообразованию на фланцевой части заготовки, для предотвращения чего необходимо применять прижим; отрыву фланца от стенки заготовки; отрыву дна от стенки заготовки.
Для устранения последних двух видов брака необходимо назначать величину вытяжки по переходам с учетом минимально допустимых коэффициентов вытяжки. В противном случае величина растягивающих напряжений σρ. превысит максимальную σρmax и произойдет отрыв, причем чем выше сила прижима Q, тем более вероятен отрыв фланцевой части изделия.
Сила вытяжки
Для расчета силы вытяжки рекомендуется пользоваться обобщенной формулой:
Р=L·S·σρmax·k
где L - периметр детали; S - толщина; к - коэффициент, учитывающий форму детали; σρmax - максимальное радиальное напряжение.
Так как для всех случаев трудно учесть особенности процесса вытяжки изделий различной геометрической формы, предлагается на основе производственных и экспериментальных данных для определения силы использовать различные эмпирические коэффициенты. Например, для цилиндрических деталей с широким фланцем обобщенная формула запишется в виде
Р= π d·S·σ·k
где σ - предел прочности металла.
При расчете силы вытяжки высоких квадратных коробок на начальных операциях рекомендуется пользоваться последней формулой, а на последней операции следующей зависимостью:
P=(4B-1,72rK)·S·σ·kb
где В и rK - соответственно, ширина и радиус углового закругления коробки; кв - коэффициент.
rolling-mills.ru
Формовка металла | Сталь и всё о стали
Формовочная земля должна хорошо принимать форму — запечатлевать все детали модели, сохранять приданную форму и быть при этом достаточно пористой, чтобы образующиеся газы легко проходили через нее.
Для нашей мастерской пригоден будет мелкий просеянный песок (90%) с небольшой (10%) примесью глины. Глину надо хорошо разболтать с водой и полить этим раствором сухой песок. Получается достаточно хорошая формовочная земля. Эти смеси — тощая формовочная земля — употребляют для изготовления сырых, непросушенных форм. Однако юным мастерам надо самим производить опыты с различными местными сортами песка и глины, выбирать наиболее подходящие. Иногда очень хорошую формовочную землю представляет собой мелкий песчанистый ил по берегам ручьев и рек.
Формовочная земля должна быть слегка влажной на ощупь, не слишком сухой и не мокрой. Качество формовочной земли узнают простой пробой. Комок земли, полученный сжатием кулака, сдавливают двумя пальцами или кидают с небольшой высоты. Если шарик развалится только на две-три части, — земля хорошая. Если же проба рассыплется на мелкие куски, — связность земли мала. Связующими веществами являются глина, патока, сахарный сироп, клейстер.
При изготовлении форм с тонкими деталями надо брать более жирную формовочную землю. Но при этом надо помнить, что земля всегда должна оставаться пористой. Для пористости в жирную землю можно добавить толченый древесный уголь или древесные опилки, истертый мох и другое.
Для изготовления шишек надо брать более жирную землю. Иногда для прочности в шишку приходится вставлять металлический стержень, в нее вкладывают восковой фитиль или соломинку, с целью образовать вентиляционный канал, что увеличивает ее пористость. Шишки надо тщательно сушить до полного высыхания. При сушке соломинки выгорают, а воск расплавляется.
Формовочная земля должна быть очень тщательно отсеяна и перемешана так, чтобы она стала совершенно однородной. Ею набивают опоки с моделью, затем их разнимают, вынимают модель, подчищают форму и прорезывают канал от литника к заполняемой металлом полости.
Модель и форму надо при формовке припыливать, чтобы получить чистые отпечатки. припыливания лучше всего брать модельной доске. ликоподий, детскую присыпку.Для более грубых отливок употребляют в качестве припыла графит, древесный уголь в порошке, пемзу. Припыл насыпают в холщевый мешочек.
Готовую припыленную форму из тощей земли можно прямо заливать металлом. Это будет сырая форма. Однако при более жирной земле, металле с высокой температурой плавления и форме с тонкими деталями опоку с формой лучше сушить и даже нагревать перед отливкой при помощи паяльной лампы, горячих углей или ставя в печь. Форму можно подсушить или высушить совершенно.
Кроме таких временных форм (так как они служат для изготовления отливки лишь один раз), можно изготовлять формы постоянные. На заводах их делают из металла; мы же будем изготовлять их из глины, гипса. При изготовлении таких постоянных форм надо предусмотреть выход из нее воздуха и газов при заливке, а также возможность вынимания отливки без какого бы то ни было повреждения формы.
Постоянные формы делают только тогда, когда надо сделать много одинаковых деталей. Например, юному мастеру может понадобиться десятка два колес. Для таких отливок лучше всего сделать постоянные формы. Опишем несколько способов формовки на очень простых типичных моделях. Для начала возьмем в качестве модели небольшой конус. Его форма позволяет отформовать модель в одной опоке. Вот как это делается.
На подмодельную доску укладывают нижнюю опоку, перевернув ее вниз той стороной, которой она соединяется с верхней половиной. Внутрь опоки на доску ставят модель плоскостью вниз и слегка ее припыливают. При укладке модели сбоку можно положить деревянный полуцилиндрик, или баклу-шу, для отформования литникового канала.
Модель засыпают слоем самой мелкой свежей сеяной земли толщиной сантиметра в два и плотно уминают его пальцами, стараясь не сдвинуть модели. Постепенно наполняют опоку землей, утрамбовывая колотушкой.
Набив половины линейкой и в том месте, где наниковой баклушей. ходится модель, делают шпилькой несколько проколов, почти доводя их до модели, чтобы сделать отдушины для выхода газов сквозь землю. Закрывают опоку второй под-модельной доской, осторожно переворачивают опоку и снимают первую доску, оказавшуюся наверху. Под доской будет плотно набитая землей.
Шпилькой делают отдушины в верхней опоке, вынимают литниковую баклушу и осторожно снимают верхнюю опоку. Сняв, ее ставят набок. В этой верхней опоке получится только отверстие для литникового стояка; вся же форма будет в нижней опоке, откуда теперь можно вынуть баклушу литникового канала и самую модель.
Если при формовке не вкладывалась баклуша для литникового канала, то, не вынимая модели, надо прорезать карасиком от литника к модели литниковый канал. По модели надо слегка постучать, раскачать ее, чтобы она отделилась от земли, а затем, воткнув в нее шило, осторожно вытащит.
Маленькие модели можно вытаскивать при помощи куска мягкой смолы. Так как при вколачивании заостренного шиладеревянная модель Несколько разрушается.
Вынимание модели, то можно в ней предварительно сделать отверстия для винтов, которые ввинчиваются при вынимании модели. При вынимании может случиться, что в форму попадут песчинки или даже обломятся края формы Песок удаляют при помощи карасиков, ложечек и скребоч-ков и выдувают ртом или резиновой грушей. Обвалившиеся края подравнивают. Чтобы они были крепче, перед удалением модели их можно осторожно смочить водой при помощи мягкой кисточки.
На воронке верхней половины можно положить перекладину из глины, чтобы в форму не попали вместе с металлом шлаки и зола. После этого припыливают поверхности обеих опок и осторожно их складывают, следя за знаками на боках опок. После припыливания можно опять вдавить осторожно модель в форму, чтобы стенки формы были 1лаже. При отливке из легкоплавких металлов можно сразу же и заливать форму.
Заливку надо производить возможно быстрее, чтобы вся литниковая воронка была постоянно заполнена металлом. Перерыв струи металла в процессе заливки может повлечь за собою попадание внутрь формы — в тело будущей отливки — всяких загрязнений, обычно всплывающих на поверхность металла в литниковой воронке.Дав металлу застыть, разнимают опоку. Часть земли около формы пристанет к металлу (рис. 25), образуя корку около металла. При недостаточном при-пыливании и высокой температуре металла земля пристает довольно крепко. Ее удаляют стальными щетками. На рисунке 26 изображена готовая отливка вместе с литниковым каналом, литником и литниковой воронкой.
Это самый простой пример формовки и отливки. Если верхняя часть модели не плоская, а имеет другой вид и сама модель неразъемная, дело будет сложнее. Положим, что надо отлить колесо с ребордой для железнодорожных моделей или шкив. У них сделана литейная конусность, чтобы модели легко можно было вытащить из формы. Несмотря на сложность формовки, она уже не представляет особых затруднений после первой работы. Укладывают модельную доску, накрывают перевернутой нижнел опокой и набивают ее уже известным образом. Перевернув опоку, карасиком удаляют слой земли над моделью так, чтобы вокруг ее поверхности образовалась ямка с пологими краями (рис. 28). Края эти как следует уминают и заглаживают, припыливают поверхность, ставят верхнюю опоку и заканчивают набивку.
Вынимают модель, чистят форму, складывают ее и заливают. Надо больше осторожности при разъеме таких опок, особенно если форма в верхней опоке выпуклая.Такой способ формовки вполне допустим, когда верхний край АВ ступицы колеса или шкива не выходит за пределы линии АВ, проведенной через край обода.
Если же ступица выходит за пределы плоскости обода то необходимо подкладывать под обод кусочки дерева такой толщины, чтобы в процессе формовки сохранить горизонтальное положение модели. Можно формовать также и при помощи фальшивой опоки (см. ниже), помещая в фальшивую опоку всю выступающую за плоскость обода часть ступицы.
Формовку неразъемной модели можно делать иногда не с подрезкой, а при помощи фальшивой опоки.Этот способ состоит в том, что сначала набивают верхнюю опоку и затем вдавливают в поверхность земли модель верхней половиной на такую глубину, чтобы модель можно было впоследствии вытащить без повреждения формы.
Припыливают поверхность, ставят нижнюю опоку и набивают ее. Перевертывают обе опоки и верхнюю снимают, выколачивают из нее землю, подчищают модель и поверхность в нижней опоке. Наставляют снова верхнюю пустую опоку и набивают ее вторично обычным порядком, с литниковой баклушей и отдушинами. Для большого числа неразъемных моделей эти два способа очень хороши. Набитая первоначально фальшивая опока не годится в качестве части формы, ее обычно разрушают.
www.inmetal.ru
2 Формовка
ФОРМОВКА
ИЗГОТОВЛЕНИЕ ЛИТЕЙНЫХ ФОРМ
Формовка — наиболее сложная и трудоемкая операция производства отливок в разовых песчаных формах. Трудоемкость изготовления литейных форм составляет 40...60 % от общей трудоемкости получения отливок.
Основными операциями изготовления литейных форм являются: уплотнение формовочной смеси для получения точного отпечатка модели в форме и придание форме достаточной прочности; устройство вентиляционных каналов для вывода газов из полости формы; извлечение модели из формы; отделка и сборка формы. Формы изготавливаются вручную, на формовочных машинах и на автоматических линиях.
1.Ручная формовкаприменяется в условиях единичного производства, в ремонтном производстве, для крупных отливок массой 200…300тоннРис. 37Л Ручная формовка для отливки детали типа втулки
На модельную плиту 3 (рис. 37Л, а) укладывается половина модели 2 и устанавливается нижняя опока, затем сквозь сито 4 на поверхность модели наносится противопригарный припыл — древесно-угольная пыль, графитовый порошок (рис. 37Л, б). Лопатой 5 засыпают опоку наполнительной формовочной смесью (рис. 37Л, в). Ручной или пневматической трамбовкой 6 уплотняют смесь (рис. 37Л, г), сгребают ее остатки и накалывают душником (шилом) 7 отверстия для лучшего выхода газов (рис. 37Л, д). Затем нижнюю опоку с заформованной моделью переворачивают на 180° устанавливают вторую половину модели 8 и верхнюю опоку 9 (рис. 37Л, е). После установки моделей литниковой системы 10 в той же последовательности заформовывают верхнюю опоку (рис. 37Л, ж). По окончании формовки опоки разнимают, осторожно удаляют модели, поправляют обрушившиеся места формы и, уложив в нижнюю полуформу на место знаков 11 стержень 12 (рис. 37Л, з), вновь устанавливают верхнюю полуформу на нижнюю и скрепляют их при помощи болтов, струбцин или просто придавливают грузом, чтобы предотвратить прорыв металла по плоскости разъема формы. В таком виде литейная форма готова для заливки металла.
Для получения крупных отливок полуформы перед сборкой сушат при температуре 350 °С в течение 6...20 ч в зависимости от габаритов формы.
2.Машинная формовка
Машинная формовка экономически целесообразна в условиях серийного и массового производства, когда формовочные машины загружены в течение не менее 40...60 % рабочего времени.
Сущность машинной формовки заключается в механизации основных операций: установки модельных плит и опок, наполнения опок формовочной смесью, уплотнения смеси и удаления моделей из форм. Отдельные конструкции формовочных машин позволяют также механизировать некоторые вспомогательные операции: поворот опок, снятие готовых полуформ со стола машины, передачу их на сборку и т. п.
По способу уплотнения смеси формовочные машины делятся на прессовые, встряхивающие, пескометные (рис. 38Л) и комбинированные (встряхивающие с подпрессовкой или прессовые с вибратором).
2.1.Машинная формовка прессованием.
Рис. 38Л Схема машинной формовки прессованием
Сжатый воздух подается в нижнюю часть цилиндра 1. При этом прессовый поршень 2 и стол 3 с прикрепленной к нему модельной плитой 4 поднимаются (рис. 38Л, а). Колодка 7, закрепленная на траверсе 8, входит внутрь наполнительной рамки 6 (рис. 38Л, б) и уплотняет формовочную смесь в опоке 5. При стравливании сжатого воздуха прессовый стержень и стол с модельной плитой опускаются (рис. 38Л, в) и опока с уплотненной формовочной смесью извлекается из машины.
Плотность формовочной смеси уменьшается по мере удаления от прессовой колодки из-за трения смеси о стенки опоки. Поэтому прессование используют для уплотнения смеси в опоках высотой не более 200-250 мм.
2.2.Машинная формовка встряхиванием
Рис. 39Л Схема машинной формовки встряхиванием
Сжатый воздух подается в нижнюю часть цилиндра 1 (рис. 39Л, а). При этом встряхивающий поршень 2 поднимается и перекрывает впускное отверстие 10, а нижняя его кромка открывает выхлопные окна 7 (рис. 39Л, б). Воздух выходит в атмосферу, давление под поршнем снижается, и стол 3 с укрепленной на нем модельной плитой 4 падает, ударяясь о торец цилиндра 8 (рис. 39Л, в). Скорость стола и модельной плиты падает до нуля, а формовочная смесь в опоке 5 и наполнительной рамке 6 продолжает двигаться вниз по инерции и поэтому уплотняется. Когда канал 9 встряхивающего поршня окажется против отверстия 10, сжатый воздух снова войдет в полость цилиндра. Это повлечет новый подъем стола и новый удар его о торец цилиндра при падении и т. д.
Встряхивающий стол совершает 120-200 ударов в минуту. При этом способе слои формовочной смеси будут иметь наибольшую плотность у модельной плиты. Встряхиванием уплотняют формы высотой до 800 мм. Для уплотнения верхних слоев формы встряхивание совмещают с прессованием.
2.3.Уплотнение форм пескометом
Рис.40Л Схема уплотнения форм пескометом
Для уплотнения смеси при получении крупных отливок применяются пескометы (рис. 40Л). Рабочий орган пескомета - метательная головка - выбрасывает порции формовочной смеси на рабочую поверхность модельной плиты. В стальном кожухе 1 метательной головки вращается закрепленный на валу электродвигателя ротор 4 с ковшом 5. Формовочная смесь подается в головку непрерывно ленточным конвейером 3 через окно в задней стенке кожуха. При вращении ковша со скоростью 1000-1200 об/мин. формовочная смесь собирается в пакеты 5 и центробежной силой выбрасывается через выходное отверстие в опоку 6. Попадая на модель 7 и модельную плиту 8, смесь за счет кинетической энергии равномерно уплотняется по высоте опоки. Метательная головка может перемещаться над опокой, управление работой пескомета автоматизировано. Пескомет - высокопроизводительная машина, его применяют для уплотнения крупных литейных форм.
Формовочные машины, объединенные транспортными устройствами с другими машинами и механизмами, позволяют создавать поточные (механизированные, полуавтоматические и автоматические) участки формовки.
3.Безопочная автоматическая формовка
Используется при изготовлении форм для мелких отливок из чугуна и стали в серийном и массовом производстве. Изготовление литейных форм осуществляется на высокопроизводительных пескодувно-прессовых автоматических линиях (рис. 41Л)
Рис. 41Л Изготовление безопочных литейных форм
Формовочная камера заполняется смесью с помощью сжатого воздуха из головки 2 с открытой задвижкой 8. Уплотнение осуществляется при перемещении модельной плиты 1 плунжером 4 с усилием Р (рис. 41Л, а). После уплотнения поворотная модельная плита 3 отходит влево и поворачивается в горизонтальное положение (рис. 41Л, б). Подача сжатого воздуха прекращается, а горловина головки 2 перекрывается задвижкой 8 Уплотненная полуформа под действием усилия Р1 перемещается плунжером 4 до соприкосновения с полуформой, полученной ранее, образуя полость 5. Затем производится заливка полости расплавленным металлом из ковша 6. После затвердевания и охлаждения отливок, формы подаются на выбивную решетку, где отливки 7 освобождаются от формовочной смеси.
4. Формовка по газифицируемым моделям.
Рис. 42Л Применение формы с газифицируемой моделью | 1 – опока; 2 – постель из формовочной смеси; 3 – газифицируемая модель отливки; 4 – центрирующий выступ модели; 5 – керамический стояк; 6 – верхняя часть формовочной смеси; 7 – керамическая литниковая чаша; 8 – разливочный ковш; 9 – расплавленный металл; 10 – газовая прослойка между расплавленным металлом и газифицируемой моделью |
Для изготовления достаточно крупных (массой до 20 т) единичных отливок из чугуна, стали и цветных металлов вместо обычной формовки оказывается весьма эффективным применение формовки по газифицируемым моделям, изготовленным из пенополистирола. Формовка по газифицируемым моделям осуществляется следующим образом (рис. 42Л, а). Сначала в опоке1делается постель2из формовочной смеси, на которую устанавливают газифицируемую модель3, которая покрыта противопригарным покрытием и точно повторяет конфигурацию отливки, что позволяет не изготавливать стержни для получения полостей, отверстий и выступающих частей отливки. На центрирующий выступ модели4надевается керамический стояк5, после чего опока заполняется доверху формовочной смесью6, и на стояк устанавливается керамическая литниковая чаша7.
Особенность данного вида формовки заключается в том, что газифицируемую модель из формы перед заливкой не извлекают (рис. 42Л, б), а расплавленный металл из ковша8через литниковую систему заливают непосредственно на модель. Под действием теплоты расплава9модель3газифицируется, и между ней и заливаемым металлом образуется газовая прослойка10, которая непрерывно уходит в материал формы, освобождая очередные участки полости для заполнения жидким металлом. Для последовательной газификации модели расплавленный металл подводят снизу, не делая при этом открытых прибылей и выпоров во избежание выделения газов и сажи в атмосферу цеха. Для уменьшения количества сажи одновременно с заливкой металла в форму подают углекислый газ СО2, который способствует окислению продуктов разложения модели и значительно снижает количество образующейся сажи.
По сравнению с обычной формовка по газифицируемым моделям имеет следующие преимущества: 1) становится возможным получение отливок сложной конфигурации без применения стержней; 2) значительно упрощается процесс изготовления литейной формы, а при использовании сухих формовочных смесей (сухого песка без глины) значительно снижается трудоёмкость не только формовки, но и выбивки формы после заливки; 3) благодаря неразъёмной форме и отсутствию операции извлечения модели отпадает необходимость выполнения формовочных уклонов, повышается точность отливки, исключаются заливы по плоскости разъёма, усложняющие очистку отливки.
7
studfiles.net
Формообразующие операции листовой штамповки. Гибка. Вытяжка. Отбортовка. Обжим. Раздача. Рельефная формовка.
Формообразующие операции — в которых стремятся получить заданную величину деформации, чтобы заготовка приобрела требуемую форму. Основные формообразующие операции: гибка, вытяжка, отбортовка, обжим, раздача, рельефная формовка.
Листовая штамповка. Холодная листовая штамповка. Штамповка листовая металла.Разделительные операции листовой штамповки. Отрезка. Вырубка. Пробивка. Высечка.
Схемы формообразующих операций
а — гибка; б,в — вытяжка; г — отбортовка; д — обжим; е — рельефная формовка
Гибка – образование угла между частями заготовки или придание заготовке криволинейной формы. При гибке пластически деформируется (см. Пластическая деформация) только участок заготовки в зоне контакта с пуансоном 1 (рис., позиция а): наружные слои заготовки растягиваются, а внутренние – сжимаются. Деформация растяжения наружных слоев и сжатия внутренних увеличивается с уменьшением радиуса скругления рабочего торца пуансона, при этом возрастает вероятность образования трещин. Поэтому минимальный радиус пуансона ограничивается величиной в пределах 0.1…2,0 от толщины заготовки, в зависимости от механических свойств материала.
При снятии нагрузки растянутые слои заготовки упруго сжимаются, а сжатые – растягиваются, что приводит к изменению угла гибки α, т.е. к пружинению детали. Это следует учитывать или уменьшением угла инструмента на величину пружинения, или применением в конце рабочего хода дополнительного усилия.
Гибку производят в штампах, а также вращающимися фигурными роликами, играющими роль матрицы, на профилегибочных станах.
Холодная обработка металлов давлением
Вытяжка – образование полого изделия из плоской или полой заготовки (рис., позиция б). Вырубленную заготовку диаметром Dз и толщиной S укладывают на плоскость матрицы 3. Пуансон 1 надавливает на заготовку и она, смещаясь в отверстие матрицы, образует стенки вытянутой детали диаметром d.
Формоизменение при вытяжке оценивают коэффициентом вытяжки kв = Dз / d, который в зависимости от механических характеристик металла и условий вытяжки не должен превышать 2,1.
При Dз — d > (18..20)S, возможны потеря устойчивости фланца и образование складок при вытяжке. Их предотвращают прижимом 2 фланца заготовки к матрице с определенным усилием Pпр.
Высокие детали малого диаметра получают за несколько операций вытяжки с постепенным уменьшением диаметра D полуфабриката и увеличением его высоты (рис., позиция в). При последующих переходах для предотвращения разрушения металла принимают:
Промежуточный рекристаллизационный отжиг для устранения наклепа позволяет увеличить kв до 1,4…1,6.
Опасность разрушения заготовок устраняют применением смазочных материалов для уменьшения сил трения между поверхностями заготовок и инструмента.
При вытяжке зазор между матрицей и пуансоном составляет (1..1.3)S.
Отбортовка – получение борта диаметром dб путем вдавливания центральной части заготовки с предварительно пробитым отверстием dо в матрицу (рис., позиция г). Формоизменение оценивают коэффициентом отбортовки:
который зависит от механических характеристик металла заготовки и ее относительной толщины S / do. Большее увеличение диаметра можно получить, если заготовку отжечь перед отбортовкой или изготовить отверстие резанием, создающим меньшее упрочнение (см. Наклеп. Наклеп металла. Сущность явления наклепа.) у края отверстия.
Отбортовку применяют для изготовления кольцевых деталей с фланцами и для образования уступов в деталях для нарезания резьбы, сварки, а также для увеличения жесткости конструкции при малой массе.
Листовая штамповка. Холодная листовая штамповка. Штамповка листовая металла.Разделительные операции листовой штамповки. Отрезка. Вырубка. Пробивка. Высечка.
Обжим – уменьшение периметра поперечного сечения концевой части полой заготовки. Производится заталкиванием заготовки в сужающуюся полость матрицы (рис., позиция д). За один переход можно получить d = (0.7..0.8)Dз. Для большего формоизменения выполняют несколько последовательных операций обжима.
Раздача – увеличение периметра поперечного сечения концевой части полой заготовки коническим пуансоном; это операция противоположная обжиму.
Рельефная формовка – местное деформирование заготовки с целью образования рельефа в результате уменьшения толщины заготовки (рис., позиция е). Формовкой получают конструкционные выступы и впадины, ребра жесткости, лабиринтные уплотнения.
www.mtomd.info
Штамповка и формовка металла
Компания Проминдуктор предлагает индукционные нагреватели для штамповки и формовки металлоизделий.
Ковка и штамповка деталей машин, инструмента других металлоизделий являются древнейшими процессами металлообработки, но и в наше время эти процессы наиболее распространены из – за высокой производительности, экономичности и качества продукции.
Экономное расходование металла при изготовлении поковок заложено в самой идее пластического формоизменения при обработке давлением, которая состоит в преобразовании заготовки простой формы в заготовку сложной формы того же объема. Отходы производства поковок не присущи технологии ковки и объемной штамповки и большее или меньшее их количество характеризует лишь степень достигнутого технического совершенства данного способа производства поковок.
Возможность использования высоких скоростей деформации, быстроходность современных кузнечных машин и небольшое число необходимых относительно несложных технологических операций обуславливает кратковременность рабочего цикла и высокую производительность кузнечно – штамповочного производства. Кованные и штампованные изделия отличаются высокими механическими свойствами. Общеизвестно, что лучший металл – это металл деформированный, а затем термически обработанный.
В современной металлообрабатывающей промышленности кузнечно – штамповочное производство является одним из основных способов изготовления заготовок и деталей. Свободной ковкой и объемной штамповкой изготавливают заготовки и детали массой от десятков граммов, до сотен тонн, размерами от сантиметров до нескольких десятков метров.
К преимуществам индукционного нагрева относятся:
1. Экономия и большая скорость нагрева металла, отсутствие необходимости подачи воздуха в камеру нагрева (как в случае применения печей для поддержания горения топлива), что значительно уменьшает окалинообразование. Потери металла в виде окалины при индукционном нагреве составляют всего 0,2…0,4 % масса нагреваемого металла, что почти в 10 раз меньше чем при пламенном нагреве.
2. Повышение стойкости штампов. При уменьшении окалины на металле стойкость штампов повышается, так как окалина оказывает абразивное воздействие.
3. Повышение производительности труда. Большая скорость нагрева позволяет увеличить температуру начала штамповки, так как перегрев металла при малых выдержках в нагретом состоянии происходит при более высоких температурах. Штамповка при более высоких температурах целесообразна из – за меньших затрат работы на деформацию, что приводит к повышению производительности.
4. Улучшение условий труда. Отсутствие грязи и копоти на рабочем месте улучшает условия труда в горячих цехах, что приближает условия работы в них к условиям работы в холоднопрессовых цехах.
5. Повышение качества продукции. Равномерность нагрева и точный контроль температурного режима при индукционном позволяют обеспечить однородные структуру и свойства металла, сократить тепловые виды брака и увеличить точность размеров поковок за счет уменьшения колебания величины усадки при их остывании.
6. Отсутствие необходимости в тщательной очистке поковок; экономия времени на очистку заготовок от окалины перед штамповкой; простота обслуживания нагревателей; удобство применения защитных атмосфер в нагревательных индукторах и т. д.
Нагрев металла является одним из важнейших звеньев производственного процесса в металлургии и машиностроении, влияющий на производительность, энерго и материалоемкость производства, себестоимость и качество продукции. Выбор же метода нагрева существенным образом отражается на технико-экономических показателях продукции. Здесь необходимо учитывать технологичность и мобильность производства, его объемы, стоимость сырья и энергоносителей, качественные показатели продукции и другие факторы. В кузнечно-штамповочном производстве для нагрева заготовок из различных сталей, цветных металлов и сплавов в интервале 800-1300ОС применяют устройства индукционного нагрева.
Индукционный нагрев по расходу энергии на тонну заготовок менее экономичен, чем нагрев в пламенных печах. Однако его широко применяют, т.к. он повышает производительность труда, позволяет полностью автоматизировать процесс нагрева заготовки и обеспечить высокую стабильность процесса, улучшить условия труда и сократить потери металла на окалинообразование. Потери металла в виде окалины при индукционном нагреве почти в 10 раз меньше, чем при нагреве в пламенных печах. Уменьшение окалины повышает качество поковок и увеличивает стойкость штампов кузнечно-штамповочного оборудования.
Вместо использования газовых, пламенных печей и других нагревательных устройств в большинстве случаев вполне целесообразно и оправданно применение индукционных нагревательных установок. Такая замена позволяет, в конечном итоге, снизить себестоимость продукции.
Основное и главное преимущество индукционного нагрева заключается в следующем. В любой не индукционной нагревательной установке металл, помещенный в область воздействия температур, нагревается за счет теплопередачи. Таким образом, осуществляется, по сути, "косвенный" нагрев. В индукционных нагревательных установках, магнитный поток, созданный током генератора, пронизывает металл, находящийся в индукторе. Под действием магнитного потока, в металле (заготовке) протекают индуцированные токи, непосредственно воздействуя на структуру металла, и как следствие, нагревая его. Интенсивность нагрева пропорциональна мощности источника тока, рабочей частоте (частоте изменения магнитного поля) и зависит от физических свойств металла.
Оперативно изменяя мощность преобразователя частоты, изготавливая индукторы специальной конструкции, оказывается возможным регулирование температуры нагрева заготовок. Выбор рабочей частоты генератора позволяет управлять глубиной прогрева, что широко используется в индукционных закалочных установках.
calculator.prominductor.ru
Способ формовки листового металла
Изобретение относится к области обработки металлов давлением, в частности к формовке листового металла для облицовки стен и потолков. В металлическом листе по всей его площади выдавливают рельефные рисунки. Каждый рельефный рисунок образуют несколькими канавками, ориентированными под углом друг к другу, и их пересечением. Выдавливание рельефного рисунка в виде пересечения канавок и всех канавок, отходящих от него на некоторое расстояние, осуществляют за одну операцию, главным образом в результате растягивания в области рельефного рисунка металлического листа при его зажиме с противоположных сторон снаружи от рельефного рисунка и удержании. При этом выдавленные по отдельности рельефные рисунки соединяют друг с другом в областях канавок. Повышается качество изделий и расширяются технологические возможности. 9 з.п. ф-лы, 2 ил.
Настоящее изобретение относится к способу формовки листового металла, описанному в ограничительной части пункта 1 формулы изобретения.
Тонкий листовой металл (например, листовая сталь толщиной 0,5-1,5 мм и листовой алюминий толщиной 1-4 мм) широко используется для облицовки зданий, как снаружи, так и внутри. В традиционной практике используется кассетная конструкция, когда металлические листы режут и гнут в виде кассеты или коробки, а затем прочно привинчивают к фахверку из стали или дерева. Кассеты устанавливают рядом друг с другом так, что их края частично перекрываются с образованием как можно более непроницаемой облицовки, защищающей здание от дождя и ветра.
Однако используемым в настоящее время наружным облицовкам из листового металла или кассетам присущи существенные недостатки. Чтобы при установке кассет обеспечить водонепроницаемость и хороший внешний вид облицовки, фахверк, на котором устанавливают кассету, должен быть строго прямым. Каждую кассету нужно подогнать, установить и прочно привинтить по отдельности, что замедляет процесс монтажа и повышает его трудоемкость.
В каждом углу кассеты ее фланцы, установленные один поверх другого, не закрывают полностью всю площадь, так как их закрепляют по точкам и поэтому всегда остаются угловые области, через которые в конструкцию может проникнуть вода. Эту проблему можно частично решить установкой в местах соединений отдельных стыковочных полос, что составляет отдельную операцию.
Производственные затраты на изготовление кассет из листового металла относительно высоки, поскольку требуются операции резки и гибки, а из-за резки значительную долю материала составляют отходы. В конструкции, изготовленной путем резки и гибки, в углах всегда остаются зазоры, позволяющие воде протекать внутрь конструкции. Кроме того, края листа в углах кассеты остаются без покрытия и, таким образом, в значительной мере подвержены коррозии. Далее поверхность стены, облицованная кассетами, имеет довольно монотонный и примитивный внешний вид и лишена какого бы то ни было изящества в архитектурном смысле.
Следует также отметить, что из-за разрезов и углов по меньшей мере некоторые края кассеты должны быть перпендикулярны к ее поверхности, при этом между соседними кассетами образуются щели прямоугольного сечения. С учетом долговременного использования конструкции эти щели очень нежелательны, так как в них накапливается грязь, которая вскоре выходит на поверхность кассеты и оставляет следы, пачкая облицованную кассетами стену и ухудшая ее внешний вид. Поэтому для поддержания хорошего внешнего вида традиционные стенные кассетные конструкции из листового металла нуждаются в относительно частой мойке, однако поскольку через них может просачиваться вода, их не рекомендуется мыть. В то же время чистка кассетных конструкций не практикуется.
Другим традиционным решением является изготовление профилированных металлических листов с закругленными или прямоугольными канавками, которые выдавливают в тонком металлическом листе, помещая его между вращающимися роликами соответствующей формы. Получаются длинные рифленые листы, которые для последующего использования разрезают на отрезки требуемой длины. Профилированные листы такого типа широко используются для наружной облицовки стен различных складских зданий в сельских и промышленных районах, но из-за малопривлекательного внешнего вида они не годятся для наружной облицовки, например, общественных зданий и учреждений, где обычно используют кассеты.
Технической задачей изобретения является устранение недостатков, присущих известным техническим решениям. Особой целью изобретения является создание нового способа листовой штамповки, который позволит заменить традиционные кассетные конструкции из листового металла более разнообразными и допускающими изменения облицовками из листового металла, индивидуально подобранными и приспособленными к каждому конкретному применению. Еще одной целью изобретения является обеспечение возможности многонаправленной и одновременной формовки металлических листов.
Признаки изобретения изложены в пунктах его формулы. В предлагаемом способе формования листового металла для изготовления листов для облицовки стен и потолков, в котором в металлическом листе выдавливают рельефные рисунки так, что они расположены по всей площади поверхности листа по существу равномерно, согласно изобретению рельефный рисунок образуют из нескольких канавок, ориентированных под углом друг к другу, и их пересечения, причем это пересечение и все отходящие от него на некоторое расстояние канавки создают за одну операцию выдавливания. При этом металлический лист зажимают с противоположных сторон за пределами рельефного рисунка и в основном удерживают, так что рельефный рисунок создается главным образом в результате растягивания листа в области рельефного рисунка. Глубина полученного рельефного рисунка может достигать величины, в 50 раз превышающей толщину заготовки.
Затем эти рельефные рисунки, расположенные в радиальной конфигурации и выдавленные по отдельности, соединяют между собой в областях канавок, другими словами, рельефные рисунки выдавливают в металлическом листе так, что канавки соседних рельефных рисунков перекрывают друг друга в достаточной мере для того, чтобы сформировать непрерывные канавки между пересечениями соседних рельефных рисунков. Таким образом, рельефные рисунки, состоящие каждый из пересечения и отходящих от этого пересечения канавок, образуют в металлическом листе сетку из канавок, т.е. непрерывный повторяющийся рисунок, состоящий из пересечений канавок и канавок, соединяющих эти пересечения.
В одной из вариантов осуществления изобретения металлический лист зажимают на участке непосредственно вокруг вытисненного рисунка, так что рельефный рисунок формируется практически только путем растягивания листа в области рельефного рисунка. В зависимости от вида рельефного рисунка можно также удерживать лист зажатым на участке внутри рисунка.
В другом варианте осуществления изобретения зажимают только краевые участки формуемого металлического листа. Таким образом, можно зажать целый лист по краям и затем создавать на нем рельефные рисунки согласно изобретению так, что будет получен целый лист с требуемым рисунком.
Выдавливание металлического листа и его удерживание предпочтительно означает, что в выдавливающем устройстве имеется, например, нижний инструмент и верхний инструмент, форма которых соответствует требуемой форме металлического листа и между которыми помещают и растягивают металлический лист с формированием на нем рельефных рисунков. При этом участки или области металлического листа, расположенные вблизи рельефного рисунка, или только участки по краям листа зажимают между верхней и нижней частями удерживающего устройства в процессе выдавливания, так что металлический лист растягивается практически только в области рельефного рисунка, а главное, остается ровным и не подвергается смятию в процессе формования.
В способе согласно изобретению используется непрерывная, практически бесконечная заготовка, поступающая с барабана или рулона, причем заготовку подвергают выдавливанию и формованию поэтапно. Такой процесс является очень гибким и позволяет успешно организовать как мелкосерийное, так и крупносерийное производство.
Предпочтительно, чтобы лист имел два или более рельефных рисунков, соединенных канавками с образованием большего рельефного рисунка, который содержит несколько пересечений и создается за одну операцию выдавливания, что значительно ускоряет формование металлического листа. Рельефный рисунок, выполненный за одну операцию выдавливания, может иметь ширину, предпочтительно равную ширине всего металлического листа, например 1250 мм.
Длина канавок в рельефных рисунках может быть различной и предпочтительно ее можно изменять, чтобы можно было сделать расстояние между рельефными рисунками или их пересечениями таким, какое требуется для конкретного применения. Так, в металлическом листе можно сформировать, например, полностью бесступенчатым путем, рисунок в клетку нужного размера. В предпочтительном варианте осуществления изобретения канавки расположены под прямым углом друг к другу и в каждом рельефном рисунке канавки отходят от пересечения в четырех направлениях, поэтому когда эти рисунки выдавливаются и канавки соседних рельефных рисунков образуют продолжение одна другой, канавки на металлическом листе создают прямоугольные или, возможно, квадратные фигуры.
В предпочтительном варианте осуществления изобретения пересечение в рельефном рисунке представляет собой не только место соединения канавок, но также выдавленную область, которая шире или больше, чем канавки, например круглую или квадратную область, в которую, на ее краях, входят канавки. При этом получаются более живые и разнообразные рельефные рисунки.
Таким образом, существенная особенность способа формовки листового металла согласно изобретению состоит в том, что заданный, повторяющийся рельефный рисунок создают поэтапным выдавливанием, т.е. за один раз формируют один рельефный рисунок, и рельефные рисунки в готовой листовой облицовке по существу занимают всю площадь листа либо в виде непрерывной сетки, либо в виде отдельных, расположенных рядом друг с другом рисунков. Другой существенной особенностью является то, что в процессе выдавливания лист зажимают и удерживают на участках, расположенных вблизи рельефного рисунка или на расстоянии от него, поэтому рельефные рисунки образуются в основном или по существу в результате растягивания листа только в области рельефных рисунков. Благодаря этому лист остается ровным, а рисунки в точности выравнены несмотря на поэтапное выдавливание.
По сравнению с известными техническими решениями способ формовки листового металла согласно изобретению имеет значительные преимущества. Он позволяет изготавливать большие и непрерывные поверхности листового металла с рисунком, благодаря чему уменьшается количество швов и соединительных участков, причем листы можно установить значительно быстрее и легче. При использовании штамповки, окраски или других методов выдавливания можно получить комплекс рисунков, таким образом создавая декоративное оформление, например, имитируя различные поверхности, например каменную или бревенчатую облицовку. Кроме того, в отличие от предыдущих технических решений, лист можно установить к наблюдателю выпуклой или вогнутой поверхностью.
Конструкция обладает хорошей водонепроницаемостью, так как отсутствуют разрезы, а все края листов остаются прямыми, в результате не образуется мест протечек или открытых мест, подверженных коррозии, даже в углах соединений. По сравнению с традиционными кассетами края различных частей уплотнены за счет их формы, а листы устанавливаются с частичным наложением их краев друг на друга, образуя плотные соединения.
Значительные преимущества достигаются в отношении производственных затрат, так как практически не требуется резка, а используется только поэтапное выдавливание для придания листу нужной формы, и в результате получается готовый лист требуемого размера. Ширина листа может достигать ширины исходного листа, а длина может быть почти любой.
Используемые канавки могут быть выполнены как симметричными, так и несимметричными, скошенными или скругленными, чтобы они не собирали грязь и не загрязняли конструкцию в целом, как это происходит в случае с современными кассетами. Благодаря большим размерам листов и их жесткости для их установки не требуется такого точного соблюдения размеров, как в известных технических решениях. Можно свободно выбирать размеры сформированных в металлическом листе панелей, например, образующих рисунок в клетку, что намного облегчает задачу установки листов, поскольку листам можно придать нужный размер заранее в соответствии с размерами места крепления, без необходимости резки или рубки листов на месте установки.
Изобретение позволяет создавать облицовочные конструкции, обладающие непроницаемостью и имеющие очень точные размеры не только для плоских, но и для криволинейных поверхностей, например для различных контейнеров, водонапорных башен и лестничных клеток. Благодаря возможным большим размерам и высокой жесткости изделия, изготовленные способом согласно изобретению, могут также использоваться в качестве облицовки, например, потолков и шумовых барьеров. Благодаря жесткости облицовка не производит лязга или шума при сильном ветре в отличие от известных кассетных конструкций.
Ниже изобретение будет описано подробно со ссылками на сопровождающие чертежи, где на фиг.1 изображена известная кассетная конструкция и на фиг.2 - металлический лист, изготовленный способом согласно изобретению.
На фиг.1 представлена известная стандартная кассета, широко используемая в настоящее время. Кассета выполнена путем резки и гибки металлического листа. Помимо того, что процесс изготовления кассеты является медленным и трудоемким, она имеет подверженные коррозии углы 1, образованные разрезами, и отверстия 3. Кроме того, открытые углы 1 и открытые угловые области 4 создают в конструкции нежелательные места протечек. Размеры кассеты в общем случае варьируются в пределах от 300×400 до 1000×2000 мм, поэтому при использовании маленьких кассет стоимость установочных работ составляет существенную долю от полной стоимости.
На фиг.2 показан металлический лист, изготовленный способом согласно изобретению. Исходным материалом является, например, полоса листового металла, которая может иметь ширину 200...1500 мм в направлении, которое на чертеже является поперечным, и почти бесконечную длину в вертикальном направлении на чертеже. Согласно изобретению каждый рельефный рисунок 5 состоит из пересечения 6 и четырех канавок 7, отходящих от него под углом 90° друг к другу.
Размер рельефного рисунка 5 таков, что два соседних рельефных рисунка, выдавленных в разное время, явно перекрывают друг друга. Благодаря этому канавки двух соседних рельефных рисунков в точности входят одна в другую, образуя единую непрерывную канавку, соединяющую два пересечения. В этом варианте изобретения канавки имеют в сечении форму равносторонней трапеции, но они могут иметь другую форму, например приблизительно прямоугольную, круглую, скругленную на углах, или форму, представляющую собой подходящую комбинацию из указанных форм.
В нижней части фиг.2 изображен отдельный прямоугольный рельефный рисунок 5, у которого заштрихованные участки 8 представляют собой участки, где металлический лист крепко удерживается и зажимается посредством соответствующего удерживающего устройства, а между этими участками 8 выдавливаются и формуются канавки и пересечение. Возможен также вариант, когда лист зажимают и удерживают, прикладывая зажимное усилие только к его краевым участкам 9.
При использовании этого варианта осуществления изобретения получается единое и непрерывное изделие из листового металла нужной длины, которое соответствует множеству традиционных отдельных кассет. Его можно закрепить лишь несколькими винтами. В нем отсутствуют подверженные коррозии разрезы, за исключением наружных краев. Конструкция имеет очень мало стыков, что уменьшает потенциальные места протечек.
Описанный выше со ссылками на сопровождающие чертежи пример не ограничивает изобретения, и возможны другие варианты его осуществления в объеме, определяемом формулой изобретения.
1. Способ формовки листового металла для изготовления листов для облицовки стен и потолков, включающий выдавливание в металлическом листе рельефных рисунков, расположенных равномерно по всей его площади поверхности, отличающийся тем, что каждый рельефный рисунок образуют несколькими канавками, ориентированными под углом друг к другу, и их пересечением, выдавливание рельефного рисунка в виде пересечения канавок и всех канавок, отходящих от него на некоторое расстояние, осуществляют за одну операцию, главным образом в результате растягивания в области рельефного рисунка металлического листа при его зажиме с противоположных сторон снаружи от рельефного рисунка и удержании, а выдавленные по отдельности рельефные рисунки соединяют друг с другом в областях канавок.
2. Способ формовки по п.1, отличающийся тем, что из рельефных рисунков, состоящих из пересечений и отходящих от них канавок, в металлическом листе образуют сетку, состоящую из пересечений канавок и канавок, соединяющих эти пересечения.
3. Способ формовки по п.1, отличающийся тем, что одновременно выдавливают два рельефных рисунка, соединенных общей канавкой.
4. Способ формовки по п.1, отличающийся тем, что одновременно выдавливают несколько рельефных рисунков, соединенных канавками.
5. Способ формовки по п.1, отличающийся тем, что при выдавливании рельефного рисунка в нем регулируют длину канавки для регулировки расстояния между пересечениями в отформованном металлическом листе.
6. Способ формовки по любому из пп.1-5, отличающийся тем, что канавки в рельефном рисунке располагают под прямым углом друг к другу для образования в металлическом листе канавками прямоугольных, предпочтительно квадратных фигур.
7. Способ формовки по любому из пп.1-5, отличающийся тем, что образуют только прямые канавки.
8. Способ формовки по любому из пп.1-5, отличающийся тем, что в пересечении образуют область шире, чем канавки, например круглую или прямоугольную область.
9. Способ формовки по п.1, отличающийся тем, что металлический лист удерживают зажатым на участках, расположенных непосредственно вокруг рельефного рисунка для формирования рельефного рисунка растягиванием листа только в области рельефного рисунка.
10. Способ формовки по п.1, отличающийся тем, что металлический лист удерживают зажатым на краевых участках всего металлического листа, подлежащего формовке.
www.findpatent.ru