Сварочные шлаки. Как отличить шлак от металла при сварке
как отличить шлак от металла видео Видео
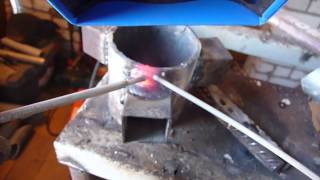
...
2 лет назад
Сварочные инверторы для постоянных работ https://www.urzp.ru/ В этом видео я покажу как начинающим сварщикам видеть...
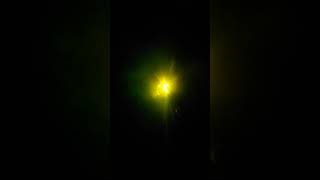
...
9 меc назад
Как отличить метал от шлака.

...
3 лет назад
Ручная дуговая сварка имеет ряд отличий от сварки полуавтоматической, сварочная ванна при дуговой сварке...
...
3 лет назад
Как варить, что бы не было шлаковых включений.
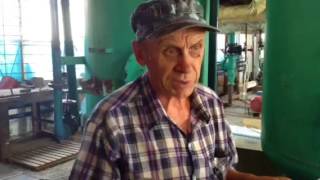
...
1 лет назад
Непровар и как его избежать- это видео для начинающих сварщиков. И чтобы его избежать достаточно соблюдать...

...
5 лет назад
Вот так выглядит процесс переноса металла сварочного электрода и формирование сварочной ванны при 7000 кадр...
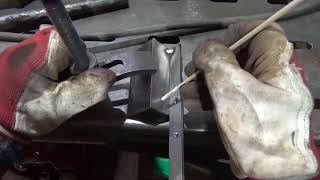
...
4 меc назад
Полезный совет №21.
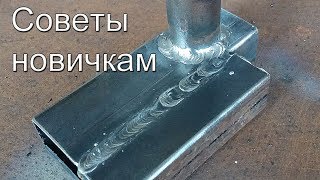
...
8 меc назад
Советы начинающим сварщикам. Как научиться варить металл, на что обращать внимание. Мой ВК: https://vk.com/alim_rizaev...
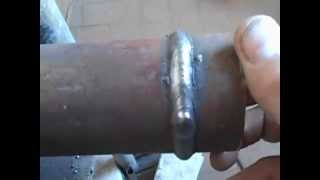
...
3 лет назад
Выносливые сварочные аппараты https://www.urzp.ru/ Трубогибы, профилегибы http://www.kovka-stanki.ru/ Фото выполненных в данном...
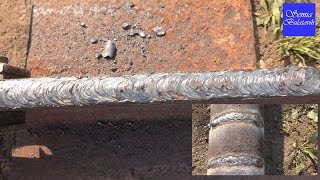
...
2 лет назад
Учимся варить. Как варить красивые швы начинающим сварщикам. Если Ваш канал еще не подключен к партнерке,...
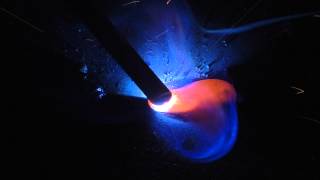
...
5 лет назад
Сварочная ванна.
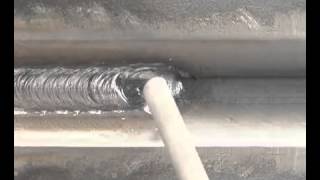
...
5 лет назад
Профессиональное обучающее видео по электро дуговой сварке.
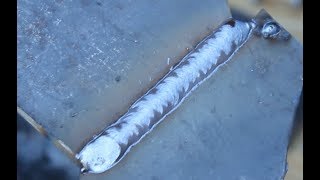
...
11 меc назад
Практическое пособие по обучению сварке. В этой части варим вертикальный шов и будет интересный эксперимент.
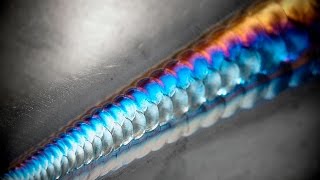
...
3 лет назад
Сварка и сварочные швы которые смело можно отнести к образцовым швам. Сварка, сварочные электроды и всё...
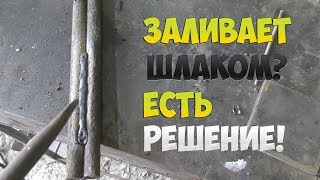
...
2 меc назад
Привет! Меня зовут Роман, и я работаю сварщиком порядка 15 лет! За время работы набрался достаточного опыта...
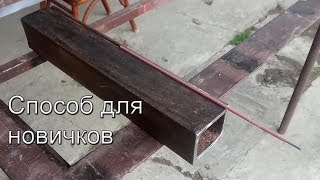
...
8 меc назад
Проверяем интересный способ сварки. Красивый сварочный шов без навыков. Помощь каналу: Карта Visa Сбербанк...
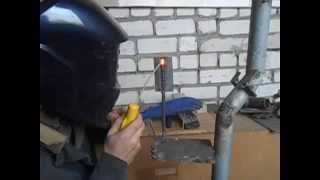
...
3 лет назад
Как варить тонкую нержавейку.
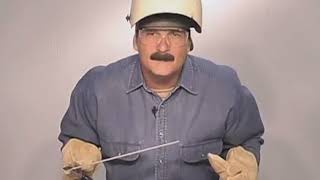
...
6 меc назад
В этом видео Вы узнаете все подробности и тонкости дуговой сварки. Профессиональный сварщик расскажет...
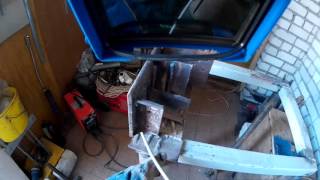
...
2 лет назад
В этом видео я расскажу и покажу для чего и как правильно делать удлинение дуги, вдавливать электрод и как,...
videoprime.ru
Сварочные шлаки :: Книги по металлургии
РОЛЬ ШЛАКА (ФЛЮСА) ПРИ СВАРКЕ
Содержащий шлакообразующие вещества сварочный материал называется флюсом. Флюс применяется при нескольких способах сварки и наплавки. Он является обязательным материалом, обеспечивающим технологию электродуговой сварки и наплавки под флюсом, сварки по флюсу, сварки с магнитным флюсом, а также электрошлаковой сварки и наплавки. Шлак образуется также при плавлении электродного покрытия, сердечника порошковой и активированной проволок, окислении электродного металла сварочной ванны, при сварке в окислительной атмосфере и т. п.
Роль шлака при сварке и наплавке очень велика. Его составом определяется атмосфера дуги, от которой зависят стабильность ее горения, стойкость против порообразования швов, объем и соотношение выделяющихся при сварке вредных газов. От шлака зависит и стабильность электрошлакового процесса. Взаимодействие расплавленного шлака с металлом сварочной ванны существенно влияет на химический состав металла шва, от которого в свою очередь зависят структура, стойкость против образования кристаллизационных (горячих) трещин и пор металла.
К важнейшим функциям шлака, имеющим значение при всех видах сварки плавлением, относятся :
1) обеспечение устойчивости процесса сварки;
2) хорошее формирование шва;
3) защита зоны сварки от доступа воздуха;
4) предупреждение образования в швах дефектов;
5) управление химическим составом металла шва;
6) обеспечение требуемых механических свойств металла шва и сварного соединения в целом;
7) обеспечение легкой отделимости шлаковой корки с поверхности металла.
Шлак должен также обладать хорошими санитарно-гигиеническими свойствами, в процессе сварки выделение вредных веществ должно быть минимальным. Кроме этих общих функций имеются и функции, специфические для каждого вида сварки.
Устойчивость процесса электродуговой сварки в первую очередь зависит от устойчивости (стабильности) горения дуги, т. е. постоянства во времени основных электрических параметров дуги — напряжения и силы тока. Сварочная дуга один из видов электрического разряда в газах, а поэтому устойчивость ее горения, при прочих равных условиях, определяется составом атмосферы дуги. При нагреве теплом дуги шлак выделяет газы и пары, изменяя этим состав атмосферы дуги. Наличие в шлаке оксидов щелочных и щелочноземельных металлов (в отличие от фторидов и хлоридов) повышает устойчивость горения дуги и процесса сварки.
Формирование шва зависит, прежде всего, от режима сварки, т. е. от длины дуги, ее подвижности и т. п. Так, при сварке под флюсом длина дуги и ее подвижность зависят от размеров зерен флюса. При крупном флюсе дуга более подвижна и ширина шва больше, чем при сварке под мелким флюсом. Соответственно этому глубина провара больше при сварке под мелким флюсом, чем под крупным.
Внешний вид шва в значительной мере определяется равномерностью отложения металла, зависящей от состояния сварочной ванны. «Кипение» металла сварочной ванны вследствие выгорания углерода и выделения растворенных в металле газов может значительно ухудшить внешний вид шва. Введение в сварочную ванну раскислителей «успокаивает» ее и способствует образованию швов с более мелкими чешуйками на поверхности. Если шлак имеет чрезмерно высокую вязкость при температуре твердения металла, шов формируется хаотично, воспроизводя форму затвердевшей шлаковой корки .
При сварке под флюсом обеспечивается надежная защита зоны сварки от доступа воздуха. Однако при других способах дуговой сварки для такой защиты от внешней атмосферы требуется, чтобы шлак полностью покрывал поверхность металла сварочной ванны. Для этого нужно, чтобы межфазное натяжение на границе шлак— металл было минимальным, а изменение вязкости шлака с ростом температуры было плавным. Как правило, более надежную защиту металла сварочной ванны от доступа воздуха, а также лучшее качество формирования поверхности шва дают «длинные» шлаки с постепенным снижением их вязкости при затвердевании. Худшие результаты получаются при «коротких» шлаках, характеризующихся резким изменением вязкости при затвердевании. Необходимо также, чтобы температура затвердевания шлака была ниже температуры затвердевания металла.
К числу наиболее опасных дефектов сварных швов относятся поры и кристаллизационные трещины. Основными причинами возникновения пор в швах могут являться загрязнение основного металла и сварочной проволоки ржавчиной и маслом, влажный флюс и др. Роль шлака в предупреждении появления пор заключается:
1) в защите металла сварочной ванны от доступа воздуха;
2) выделении в атмосферу дуги газов и паров, снижающих Концентрацию в ней водорода и азота путем разбавления газовой фазы;
3) выделении в атмосферу дуги газообразных соединений фтора, образующих с водородом нерастворимый в жидкой стали фторид водорода;
4) окислении металла сварочной ванны.
О роли шлака в защите сварочной ванны от доступа воздуха сказано выше.
Интенсивность испарения шлака в процессе сварки сравнительно невелика, поэтому она не может дать существенного снижения парциального давления азота и водорода в зоне сварки. Более эффективно действует введение газообразующих веществ в состав электродного покрытия, керамического флюса или сердечника порошковой проволоки.
Для уменьшения пористости швов, вызванной водородом, в зону сварки вводятся фториды. Лучше всего связывается водород в виде фторида водорода HF фторидом кремния SiF4 — газом, образующимся при сварке в результате взаимодействия фторида кальция CaF2 и диоксида кремния SiO2.
Окисление металла сварочной ванны шлаком или газовой фазой снижает растворение в нем водорода, уменьшая этим возможность появления пор в швах.
Для получения беспористых (плотных) швов на кипящей и, «полууспокоенной» стали важное значение имеют кремнийвосстановительный процесс и поступление кремния в металл сварочной ванны из других источников.
Стойкость швов против образования кристаллизационных трещин зависит от химического состава металла шва. Влияя на содержание в металле шва углерода, серы, марганца, кремния и других элементов, шлак тем самым изменяет стойкость швов против образования кристаллизационных трещин: уменьшение концентрации углерода, серы и кремния в шве, а также увеличение марганца повышают эту стойкость. Изменения химического состава могут обусловливаться как окисляющим или легирующим действием шлака на металл сварочной ванны, так и его влиянием на отношение в металле шва долей переплавленных основного и электродного металлов.
Требуемые механические свойства металла шва и сварного соединения в целом обеспечиваются путем получения швов нужного химического состава и без дефектов. На механические свойства металла шва существенно влияет наличие фосфора, который при сварке восстанавливается из шлака и переходит в металл. Поскольку фосфор — вредная примесь, для уменьшения его перехода в металл необходимо максимально снижать содержание фосфора в шлаке.
Отделимость шлаковой корки от поверхности шва зависит от окисляющего действия на нее жидкого шлака. Длительность этого действия очень невелика и составляет для обычных режимов автоматической дуговой сварки 20—30 с. Жидкий шлак, если он содержит значительные количества оксидов FeO, MnO, SiO2 или ТiO2, окисляет поверхность затвердевшего металла. Образующаяся при этом весьма тонкая оксидная пленка прочно удерживается на поверхности шва. Если поверхность металла окислена, а в составе шлака находятся соединения, прочно сцепляющиеся с оксидной пленкой (А12O3, Сr2O3 и др.), следует ожидать сильного удерживания шлака на поверхности металла. Выполнение требований как в отношении легкой отделимости шлака, так и минимального окисления легирующих элементов обеспечивается применением шлаков с низким содержанием оксидов FeO, MnO, SiO2 и TiO2, т. е. с пониженными окислительными свойствами. Отделимость шлаковой корки от поверхности шва улучшается также при увеличении разности коэффициентов термического расширения металла и шлака.
Наиболее простой и надежный способ уменьшения выделения вредных газов при дуговой сварке — применение шлаков, не содержащих в своем составе фторидов. Однако стойкость швов против образования пор при этом не всегда может быть обеспечена.
В связи с принципиальными отличиями процесса электрошлаковой сварки от электродуговой, к флюсам для электрошлаковой сварки предъявляются особые требования. Они обусловлены, с одной стороны, необходимостью обеспечить устойчивый электрошлаковый процесс, а с другой — наличием устройств для удержания шлаковой и металлической ванн. От флюса требуется :
1) обеспечение быстрого начала электрошлакового процесса и поддержание его устойчивого прохождения, в особенности при малой глубине шлаковой ванны и большой скорости подачи сварочной проволоки;
2) удовлетворительное формирование поверхности шва;
3) отсутствие отжимания ползунов от свариваемых кромок шлаком, вытекания последнего в зазоры между ползунами и кромками при достигаемой на практике точности сборки свариваемых изделий.
Флюс также должен обеспечивать выполнение других функций — защищать зону сварки от доступа воздуха, давать хорошо отделяющийся от поверхности шва шлак и др.
Ввиду того что электрошлаковый процесс основан на электрической проводимости шлака, последняя существенно влияет на прохождение процесса. Устойчивость электрошлакового процесса возрастает с повышением электрической проводимости шлака в жидком состоянии. Чем она меньше, тем при более высоком напряжении должна проводиться электрошлаковая сварка. Следует, однако, иметь в виду, что шлаки с высокой электрической проводимостью при прохождении через них электрического тока выделяют мало тепла и поэтому для успешного осуществления процесса сварки требуются значительные электрические мощности. При небольших силах тока сварка с применением таких шлаков не дает надежного сплавления кромок.
Для обеспечения устойчивого прохождения электрошлакового процесса важно, чтобы шлак имел высокую температуру кипения и не выделял много газов при высоких температурах. Некоторые шлаки кипят спокойно, без бурного выделения газов. Такое кипение, если оно не слишком интенсивно, не мешает процессу сварки, а наоборот, служит хорошим регулятором температуры ванны, поглощая излишек энергии при повышении температуры.
Шлак для электрошлаковой сварки не должен быть слишком тугоплавким или «коротким», в противном случае будут отжиматься ползуны, что приведет при сварке швов большой протяженности к вытеканию шлака и металла сварочной ванны и прекращению процесса сварки. Вместе с тем, чтобы шлак не вытекал в зазоры между ползунами, он не должен быть чрезмерно жидкотекучим. Поэтому при электрошлаковой сварке требуется оптимальная вязкость шлака, при которой не будет происходить ни отжимания ползунов от свариваемых кромок, ни вытекания шлака в зазоры. Если шов формируется без применения ползунов (сварка с неподвижной подкладкой), вязкость шлака играет второстепенную роль и основным требованием, предъявляемым к физическим свойствам шлака, остается оптимальная электрическая проводимость.
При электрошлаковой сварке шлаковая ванна надежно защищает расплавленный металл от доступа воздуха. Однако остается возможность поступления газов к металлу через шлак.
Металл шва, сваренный электрошлаковым способом, более стоек против образования пор, чем таковой, сваренный электродуговым способом, ввиду специфических условий кристаллизации металлической ванны. Причиной появления пор является наличие на кромках изделий значительного слоя окалины, а также большая влажность и загрязненность флюса. Поры могут также возникнуть в результате отклонения химического состава шва от заданного, в частности из-за низкого содержания в нем кремния или других раскислителей.
Образование кристаллизационных трещин в швах, выполненных электрошлаковой сваркой, например на стали, зависит главным образом от химического состава основного металла и формы сварочной ванны. Последняя, в свою очередь, определяется режимом сварки. Состав и свойства флюса практически не влияют на образование дефектов этого типа.
При электрошлаковой сварке подача шлака в ванну очень небольшая, она ограничивается отлагающейся на поверхности шва шлаковой коркой (толщиной 1—1,5 мм). С учетом потерь на рассыпание это составляет около 5 % массы наплавленного металла, т. е. в 20 раз меньше, чем при электродуговой сварке под флюсом. В связи с небольшим расходом при электрошлаковой сварке углеродистых и низколегированных сталей шлак мало влияет на химический состав металла шва. При наличии в основном металле и сварочной проволоке таких химически активных элементов, как титан, алюминий и др., для предупреждения их окисления должны применяться бескремнистые или бескислородные флюсы.
Отличие электрошлаковой сварки от электродуговой под флюсом состоит в наличии зеркала шлаковой ванны, с которого в окружающую атмосферу свободно выделяются пары и газы. Это ухудшает гигиенические условия труда и требует устройства местных вытяжных отсосов, независимо от состава применяющегося флюса.
markmet.ru
Сварочный шлак как предпосылка возникновения шлаковых включений
Главный побочный эффект от дуговой сварки – это сварочный шлак. Он представляет собой побочный материал неметаллического происхождения, который состоит либо из расплавленного электронного покрытия плавящегося электрода (при ручной дуговой сварке, в том числе при сварке инвертором) либо из расплавленного сварочного флюса (автоматическая сварка под флюсом).
Этот материал является побочным, потому что после непосредственного соединения он подлежит удалению. В случае, когда по каким-то причинам он начинает контактировать с затвердевающей деталью и становится уже частью полученного шва – это является серьезным дефектом. Такой результат называется шлаковыми включениями. Они визуально видны на поверхности изделия. Удалить шлаковые включения, когда они уже полностью находятся в затвердевшей детали можно только путем сверления, чтобы потом сварить его заново.
Главная причина возникновения шлаковых включений – это ситуация, когда небольшой объем металла слишком быстро застывает, в результате чего весь шлак не успевает «выйти» за пределы области сварочной ванны. При наличии этого дефекта эксплуатация соединения по назначению будет невозможна.
Шлаковые включения могут быть макроскопические и микроскопические. Первые появляются в случае плохой зачистки кромок либо вообще её отсутствия. Они представляют собой сферический материал, с удлиненными хвостами. Избежать их появление можно путем тщательного очищения кромок соединяемых деталей. Микроскопические включения могут возникнуть в процессе возникновения химических реакций в процессе сварки, когда металл кристаллизуется.
Полное устранение такого производственного брака невозможно, при незначительных шлаковых включениях соединение может быть признано качественным. Существуют определенные условия и признаки, при которых устанавливается допустимое значение наличия такого вида брака на изделии. Такие допустимости устанавливаются в зависимости от количества, расположения и размера дефектного шва; от процентного соотношения площади всего брака к площади наплавленного металла на изделии; от удельного веса наплавленного металла.
Причины, по которым дефект необходимо удалять после работы
- При удалении шлака изделие визуальным выглядит лучше.
- Когда производится много слоёв.
- Часто изделие необходимо покрывать сверху, например, краской.
- Чтобы проверить насколько качественно выполнен шов.
Основные причины появления шлаковых включений.
- Быстрое застывание металла небольших объемов, в результате чего шлак не успевает выйти за границы сварочной ванны.
- Применение электродов и флюса большого удельного веса и/или из тугоплавких материалов.
- Малые показатели раскисления металла. Раскисление подразумевает процесс исключения из уже мягкого металла молекул кислорода. Кислород для него является вредной составляющей, которая ухудшает качество.
- Высокие показатели силы поверхностного натяжения шлака. При этом, он не всплывает на поверхность.
- Плохо зачищены кромки деталей или валики шва.
- Низкое качество электрода, а точнее его покрытия, плавление которого осуществляется неравномерно, его частицы попадают в сварочную ванну.
- Не соблюдение правил и техники и режимов соединения деталей (выбор неподходящей скорости, угла наклона электрода), изменение длины дуги без причины.
- Непрофессионализм сварщика. Если вам нужно качественное изделие, лучше привлечь к этому нелегкому делу специалиста в этой области. Если вы хотите сделать все сами, то прежде чем браться за ответственную сложную работу, нужно наработать практику с несложными соединениями.
Так выглядит сварочный шлак после удаления со шва
Профессиональные сварщики умеют сразу же отличить шлак от металла при сварке и «выгонять» его в процессе работы, однако, у каждого свои советы, как это сделать. Некоторые утверждают, что лучше использовать новые электроды, в которых покрытие более темное, а металл красного оттенка (это не касается рутиловых электродов), другие говорят, что металл более жидкий, а шлак вязкий. На его вязкость влияет температура.
Чтобы шлак не закрывал сварочную ванну, необходимо регулировать положение электрода. Положение должно быть таким, чтобы направление газа от испарения покрытия электрода выдувало данный дефект на поверхность шва. Сварщику ни в коем случае нельзя оставлять его в сварочной ванне. Сварочный шлак должен оперативно поддаться процессу кристаллизации и без особых усилий удаляться.
Попадание шлака в готовое соединение бывает неизбежно, такой дефект если не невозможно устранить, то зачастую очень сложно. Именно поэтому существуют допустимые нормы наличия «лишних» включений в уже сваренном изделии. Например, в межгосударственном стандарте касательно строительных стальных конструкций (введен в действие в 2001 году). В приложении к этому документу предусмотрены требования к качеству сварных соединений, допустимые дефекты. Требования в части шлаковых включений указаны в таблице ниже.
Длинные дефектыHe допускаются
Короткие дефекты:
стыковой шов
h ≤ 0,2 Sh ≤ 0,25 Sh ≤ 0,3 S
угловой шов
h ≤ 0,2 Kh ≤ 0,25 Kh ≤ 0,3 K
Максимальный размер включения2 мм3 мм4 мм
Таким образом, чтобы обеспечить правильное появление шлака на поверхности сварочного шва, необходимо знать, как его отличить от металла. В случае, если заметно, что шлак остается в сварочной ванне и не выходит наверх, нужно изменить угол наклона электрода. Перед процессом соединения необходимо позаботиться о надлежащем состоянии кромок, а также о правильном выборе режимов и параметров. Электроды нужно выбирать высокого качества, тогда и сварной шов будет качественный. Если соблюсти все условия, тогда шлак будет не вязкий, низкого удельного веса, с малым поверхностным натяжением. Только в этом случае, шлаковые соединения будут взаимодействовать с деталью, увеличивая его показатели раскисления, удаляя кислород. И только тогда сварочный шлак будет легко выходить на поверхность шва. Здесь не обойтись без профессионализма сварщика, выполняющего работу. Он должен уметь отличить шлак от металла при сварке, знать, почему вообще он появляется. Только опытный специалист сумеет сделать качественное и прочное соединение.
home.nov.ru