Пайка железа с помощью оловянного припоя. Пайка металла
выбор флюса и особенности работы с жестью и оцинковкой
Процесс пайки – это химическое соединение двух металлов с помощью припоя. Причем кристаллическая структура металла не изменяется. То есть, соединяемые части остаются при своих технических характеристиках.
Само соединение получается достаточно надежным, но многое будет зависеть от вида припоя и технологии пайки. К тому же необходимо отметить, что не все металлы могут быть соединены этим процессом. Основные же металлы, особенно стальные (железо), между собой могут быть спаяны.
Три технологии
Существует три технологии пайки железа оловом:
- паяльником. Для этого придется использовать мягкие припои с большим содержанием свинца;
- паяльной лампой. Здесь потребуются твердые припои с большим содержанием олова;
- электрическая пайка железа.
Первый способ применяют в том случае, если железо не будет в процессе эксплуатации подвергаться большим нагрузкам. Второй – это лужение железа оловом, когда оловянный припой наносится на поверхность металлического изделия и растирается по всей его плоскости тонким слоем.
В этой технологии обязательно применяется флюс для пайки. Третий вариант используется в производственных масштабах, для чего применяется специальное оборудование.
Пайка листов жести
Пайка жести (тонкого листового железа) является часто встречаемым процессом в изготовлении металлической тары. Но нередко и в домашних условиях приходится скреплять листы железа между собой, собирая герметичные конструкции. Поэтому перед тем как припаять один лист к другому, необходимо подготовить все нужное.
Для процесса пайки железа с помощью олова понадобится припой с небольшой концентрацией олова, к примеру, ПОС-40, флюс, паяльник и шило.
Флюс в процессе пайки железа выполняет функции растворителя и окислителя одновременно. То есть, сразу происходит смачивание металла и защита от окислительных процессов. В качестве флюсов используют канифоль и соляную кислоту или хлористый цинк и борную кислоту.
Что касается паяльника, то для проведения качественной пайки оловом лучше выбрать электрический инструмент мощностью более 40 Вт. Старый паяльный инструмент, который нагревается от пламени огня, сегодня практически не используют даже в домашних условиях.
Последовательность действий
Вот основные этапы данного процесса:
- зачистка соединяемых листов;
- нанесение флюса;
- разогрев паяльника и лужение;
- пайка оловом;
- очистка стыка бензином.
Очистку проводят механическим способом наждачной бумагой. Если загрязнения большие, то придется провести обработку растворителем. Если не удается очистить и таким методом, тогда проводят травление серной кислотой.
Два куска листового железа подносят друг к другу на расстояние 0,3 мм. Их края обрабатывают пастообразным флюсом при помощи кисточки. Жало паяльника очищается наждачкой, и сам инструмент включается в электрическую сеть через розетку. Чтобы проверить, хорошо ли он нагрелся, надо помести его жало в нашатырную смесь, которая должна закипеть.
Теперь проводится этап лужения железа. То есть, с помощью припоя из олова или его сплава обрабатываются края двух листов жести, чтобы покрыть их оловянным слоем, который будет выполнять защитные функции от коррозии металла.
Все готово, остается только запаять два конца листов. Жало паяльника подносится к месту стыка вместе с припоем из олова, и они оба продвигаются плавно по границе соединения.
При этом жало необходимо прижимать не острым концом, а плоской гранью, за счет чего будет прогреваться одновременно и соединяемые детали, что скажется на высоком качестве проведенной пайки железа.
Особенности работы с оцинкованными изделиями
Пайка оцинковки оловом по чисто технологическому процессу от предыдущей ничем не отличается. Но есть в технологии свои тонкие нюансы, которые сказываются на качестве конечного результата.
Нельзя паять оцинковку припоями, в состав которых входит большое количество сурьмы. Это вещество при контакте с цинковым покрытием создает непрочный шов.
В качестве флюса лучше использовать борную кислоту и хлористый цинк. Если сами изделия уже были залужены оловом в процессе производства, тогда в качестве флюса можно применять канифоль.
Когда производится соединение оцинкованного железа (листового) и проволоки, то последнюю надо согнуть под прямым углом, чтобы увеличить площадь контакта двух изделий.
В остальном процесс проводится точно также. Кстати, неважно, проволока была изготовлена из оцинковки или обычной стали.
Есть еще несколько важных позиций, которые надо учитывать в процессе пайки оцинкованных изделий. Если для пайки железа используются припойные стержни на основе олова и свинца, то для них лучше добавлять флюс на основе хлористого цинка и хлористого аммония. Соотношение 5:1 соответственно.
Припой на основе олова и кадмия требует едкого натра в качестве флюсовой добавки.
Если между собой соединяются оцинкованные изделия из железа, в состав защитного слоя которых входит более 2% алюминия, то применяется припой на основе олова и цинка. А в качестве флюса используют соляную кислоту и вазелин (стеарин).
В независимости от того, какие детали или узлы соединяются пайкой, необходимо после окончания процесса и остывания шва промыть место стыка водой, чтобы удалить остатки флюса.
Техника безопасности
Пайка железа оловом – процесс небезопасный. Поэтому надо строго соблюдать меры предосторожности. На руки надеваются защитные перчатки, под паяльник обязательно устанавливается подставка, чтобы разогретое жало не касалось стола и подручных материалов. И сама процедура должна проводиться аккуратно.
При кажущейся простоте паячной операции, на самом деле это серьезная процедура. И относиться к ней надо с большим вниманием. Что-то упустили, неправильно даже приложили, и можно считать, что качество стыка резко упало. Поэтому важно к каждому этапу подходить ответственно, особенно это касается очистки двух стыкуемых изделий из железа.
svaring.com
Как паять стальные детали
Как паять стальные детали
Нередко возникает надобность скрепить стальные детали без сверлений, и без сварки. Выручит пайка стали. Но как это сделать правильно, ведь здесь имеются особенные нюансы. Несколько рекомендаций от специалистов.
Какая сталь паяется хорошо
Отдельные марки стали хорошо поддаются пайке, другие паяются с большим трудом, ни с каким припоем соединяться не желают, ни под каким флюсом. Как правило, мягкие стали «для гвоздей» легко паяются. На бытовом уровне это можно объяснить и тем, что материал усеян микроскопическими кратерами и неровностями. Но также имеются электротехнические марки, особо твердые и упругие, и применяемые для валов, точной механики. Здесь уже как повезет…Вопрос в том, что определить марку на глазок домашнему мастеру невозможно. Узнать насколько хорошо паяется данная деталь из стали, или близкого к ней сплава, можно только экспериментальным путем.
Как выполняется соединение оловом – порядок действий
Все зависит от того, насколько удачно можно залудить данную деталь, насколько прочным окажется контакт оловянного припоя со сталью. Чтобы контакт оказался удовлетворительными, если это возможно вообще, нужно выполнить следующее:- зачистку стали, химическую зачистка под припоем;
- разогрев детали до температуры плавления припоя, нахождение припоя на детали под флюсом некоторое время в текучем состоянии.
Наиболее безобидной в применении, но эффективной в данном случае, оказывается ортофосфорная кислота, которую легко приобрести в автомагазине, как «очистку ржавчины».
Требуемая мощность разогревающих устройств полностью зависит от массы деталей.
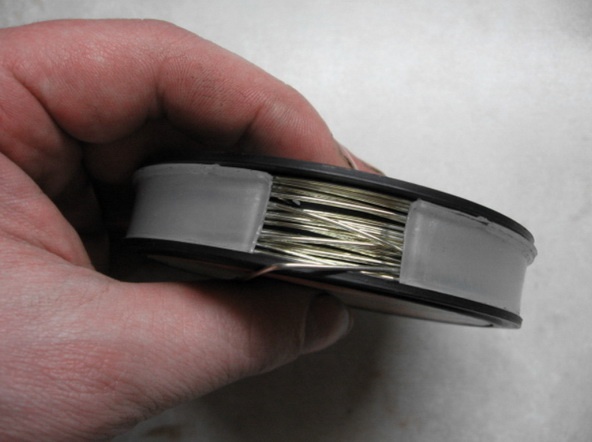
Процесс пайки двух стальных деталей
Если нужно спаять два больших гвоздя, то мощности одного паяльника 100 Вт будет маловато. Для разогрева зажатого в тисках большого гвоздя, или подобной по массе детали из стали, нужно воспользоваться строительным феном. Или газовой горелкой.Также понадобится вата на палочке, для подачи флюса в зону разогрева, и паяльник от 50 Вт.
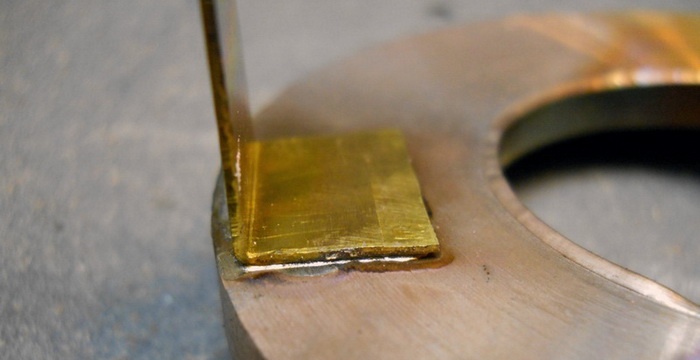
- Зачищенная наждачкой сталь разогревается горелкой.
- На горячую деталь наносится ортофосфорная кислота и тут же подается паяльником расплавленный оловянный припой.
Это же повторяется с другой деталью. Затем разогреваются две детали, находящиеся вместе, и в зону контакта подается дополнительный припой паяльником.
Насколько прочна пайка стали, можно ли сделать прочнее
Прочность такого соединение будет обуславливаться многими факторами:- прочностью связи припоя с металлом,
- площадью соединения,
- направлением нагрузки по отношению к спаянным плоскостям.
Другое направление увеличения прочности – покрытие припоем не только плоскости, но и боковин детали, - охват детали припоем. Тогда сопротивление на отрыв при разнонаправленных нагрузках будет больше.
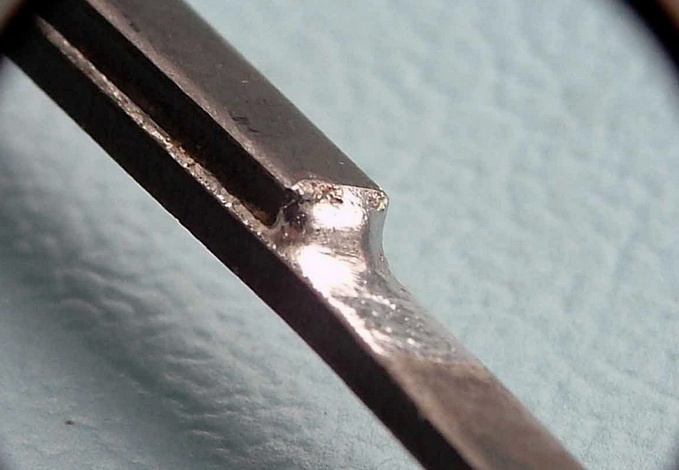
Особопрочная пайка, особые припои
Чтобы применить составы дающие прочное соединение со сталью, с собственной температурой плавления порядка 800 - 900 град, нужно использовать графитовый тигель.Работу должны вести только специалисты по плавке металлов. Необходимо знать основы плавления металлов, порядок обращение с расплавами и технику безопасности. В общем, пайка стали сверхпрочными припоями выполняется на специализированных предприятиях.
Возможный состав припоя:
- 55% цинка, 45% меди, немного кремния для увеличения текучести.
Состав расплавляется под слоем угля в графитовом тигеле.Стальные детали, подлежащие пайке, разогреваются газовой горелкой. В качестве флюса используется ортофосфорная кислота.Расплав подается на детали. Как правило, залуживание и пайка производятся за один разогрев и деталей и припоя.Но подобная пайка стали по сложности превосходит простую сварку….
Но в быту, где нужно «залатать», «прикрепить», «состыковать» две стальные детали, нужно пользоваться припоями с низкой температурой плавления, типа свинцово-оловянных.
stroy-block.com.ua
Пайка - черный металл - Большая Энциклопедия Нефти и Газа, статья, страница 1
Пайка - черный металл
Cтраница 1
Пайка черных металлов медно-фосфорными припоями не допускается, так как из-за образования хрупких фосфидов железа паяный шов не выдерживает ударных, вибрационных и изгибающих нагрузок. Для уменьшения образования фосфидов железа стальные изделия перед пайкой иногда меднят. [1]
Пайка черных металлов медно-фосфористыми припоями не рекомендуется, так как при этом образуются хрупкие паяные швы. [2]
Пайка черных металлов медно-фосфорными припоями не допускается, так как из-за образования хрупких фосфидов железа паяный шов не выдерживает ударных, вибрационных и изгибающих нагрузок. Для уменьшения образования фосфидов железа стальные изделия перед пайкой иногда меднят. [3]
То же и дополнительно при пайке черных металлов. [4]
Как и меднофосфористые припои без серебра, меднофосфорис-тые припои с серебром рекомендуются для пайки меди и ее сплавов и не рекомендуются для пайки черных металлов, так как шов получается хрупким. [6]
Для пайки меди обычно пользуются фосфорно-мед-ными припоями, для пайки стали - серебряными припоями. Фосфорно-медные припои для пайки черных металлов непригодны. [7]
При пайке медью или серебряными припоями черных металлов зазоры должны быть 0 03 - 0 15 мм, а серебряными припоями цветных металлов 0 05 - 0 25 мм. Для мед-ноцинковых припоев, употребляемых при пайке черных металлов, зазоры должны быть 0 05 - 0 25 мм. При пайке цветных металлов медноцинковыми и фосфористомедными припоями зазоры следует брать 0 1 - 0 3 мм, а при пайке алюминия и алюминиевых сплавов кремнеалюминиевыми припоями 0 1 - 0 2 мм. [9]
Медно-фосфористые припои, представляющие собой сплав меди и фосфора, служат для пайки меди и латуни. Недостатком этих припоев является то, что они непригодны для пайки черных металлов, так как не смачивают спаиваемые поверхности, поэтому швы получаются хрупкими. [10]
Меднение применяется главным образом для создания подслоя при никелировании и хромировании стальных изделий, а также при серебрении и золочении. Медные покрытия создают прочное сцепление с другими металлами, поэтому их применяют под пайку черных металлов, для сообщения деталям притирочных свойств, для восстановления размеров некоторых деталей, для защиты от цементации углеродом, для увеличения электропроводности стальной ленты и проволоки. [11]
Медно-фосфористые припои являются заменителями серебряных припоев марок ПСр 25, ПСр 45 и мягкого припоя. Они широко применяются в электропромышленности для пайки меди и латуни. Для пайки черных металлов медно-фосфористые припои непригодны, так как плохо смачивают поверхности металла, вследствие чего паяные соединения получаются хрупкими. Соединения, выполненные этими припоями, имеют низкие пластические и ударные свойства, а потому эти соединения не следует применять для деталей, работающих в условиях вибрационных или ударных нагрузок. [12]
Медно-фосфорные припои могут быть использованы только для пайки меди и ее сплавов. Чистую медь ими можно паять без флюса, что важно для обеспечения чистоты фреоновых систем. При пайке черных металлов шов, образуемый медно-фосфорными припоями, очень хрупок из-за образования в нем фосфидов железа. [13]
Существенное значение для прогрева металла имеет частота тока. Чем она меньше, тем на большую глубину в нагреваемом изделии индуктируется ток, и наоборот. Известно, что для нагрева с целью пайки черных металлов оптимальная частота тока берется от 70 000 до 200 000 гц. [14]
Страницы: 1
www.ngpedia.ru
Пайка деталей из разных видов жести: особенности и технология.
Как в производстве, так и в домашних условиях люди сталкиваются с необходимостью пайки деталей из жести, которая имеет свои особенности и подготовку. По сути, жесть — это холоднокатаная листовая сталь, подвергающаяся впоследствии термической обработке и нанесению гальванического покрытия в виде олова, цинка, хрома и прочих материалов. Своё применение жесть (белая и луженая) находит в производстве банок для холодных напитков или металлической тары любых размеров. Таким образом достигается облегчение корпуса упаковки. Поэтому корректная пайка данного металла важна.
Материалы для спаивания металла
Классический вариант спаивания жести требует наличия припоя, содержащего олово и другие химические элементы, флюс, а также паяльника с шилом.
Согласно рекомендациям, применять следует припой марок ПОС 40, ПОС 30 и ПОСС 4-6. Это обусловлено химическими свойствами материалов в процессе пайки оловом. Каждый из припоев может содержать несколько элементов, среди которых олово, сурьма, мышьяк, медь и висмут. Данные припои отличаются от других сопротивлением срезу за счёт содержания примесей. К примеру, ПОС 40 содержит 40 % олова, 2% сурьмы, по 0,05 – 0,1% оставшихся элементов. Также это повышает сопротивление разрыву шва после пайки. При понижении олова в составе повышают сурьму. Но бывает и так, что пайка предусматривает наличие такого компонента как свинец (ПОС 90). В случае оцинкованного материала ситуация другая.
Спаивание железа предусматривает наличие флюса. По сути, он является растворителем и химическим окислителем. Во время пайки благодаря этому элементу не происходит окисление. Также обеспечивается смачивание металла железом для лучшего качества шва. Популярными флюсами для металла выступают соляная кислота и канифоль. Последняя активно применяется в радиотехнической промышленности. Иногда используется хлористый цинк и борная кислота.
Выделить наиболее подходящий флюс для спаивания деталей из жести не выйдет, так как каждый из них даёт положительный результат. Если необходимо растворить густые жировые вещества, применяют хлористый аммоний. Зачастую для данной процедуры делают смеси из вышеперечисленных компонентов.
Важную роль в процессе пайки с оловом играет применяемый инструмент, которым обычно выступает паяльник. Согласно рекомендациям его мощность должна быть более 40 Вт. Желательно применять электрический паяльник. В этом случае пайка будет удобна, а швы в результате получатся прочными и надёжными. Сразу следует заметить, что без надобности оставляться инструмент в нагретом виде не стоит во избежание пожара, а также ухудшения свойств ручки. В промышленности применяются паяльные станции, стоимость которых превышает в несколько раз классическое оборудование, но изделия имеют различные насадки, а также дополнительные элементы (подставка, датчик температуры и т.д).
Процесс пайки металлических деталей
Пайка предусматривает несколько этапов, в процессе которых обеспечивается качественный шов. Для спаивания металла необходимы:
- зачистка поверхности;
- обезжиривание;
- нанесение флюса;
- подготовка паяльника;
- лужение места будущего шва;
- пайка элементов из жести;
- очистка поверхности бензиновой смесью;
- контроль получившегося шва.
Очистка поверхностей обеспечивается следующим инструментом:
- напильник;
- шабер;
Промежуток между деталями должен составлять 0,3 мм для возникновения капиллярных сил. Данная ситуация позволяет металлу заполнить кромки зазора и обеспечить качественный шов. Иногда механически детали очистить не получается и используют травление, но в случае жести это редкий вариант. При наличии жировых пятен на поверхности необходимо применять раствор соды (10%). В домашних условиях обезжиривание делают при помощи ацетона, бензиновой или спирто-бензиновой смеси. Благодаря их свойствам обеспечивается отличная очистка.
Следующим этапом спаивания металла жести выступает нанесение флюса. Как правило, это производится кисточкой или ветошью. Флюс хранят в обычных ёмкостях при комнатной температуре. Пайка предусматривает обильное смачивание данным компонентом места шва.
В процессе подготовки паяльника необходимо обеспечить чистоту поверхности, чтобы в будущем припой свободно распространялся по рабочей плоскости. Для этого крупнозернистой шкуркой, либо обычным напильником заостряется кончик инструмента. Далее он включается в сеть и разогревается. Периодически наконечник смачивается нашатырной настойкой, чтобы избежать лишних загрязнений. Кстати, именно этой смесью проверяют уровень нагрева инструмента. При хорошо разогретом паяльнике, нашатырь на поверхности начинает шипеть и покрывается зеленовато-голубым оттенком.
Далее производят лужение. Следует заметить, что при спаивании таких деталей из жести, как консервные банки, этот этап пропускается, так как он включен в технологию изготовления. Оно обеспечивает повышенную плотность и прочность шва. Важным аспектом является то, что процесс выполняют тем же материалом, который используют во время пайки. Таким образом, если спаивание металла осуществляется ПОС 30, то и лужение производится данным припоем.
Процесс самой пайки металлических изделий предусматривает закрепление элементов для удобства создания шва. Один кусок жести накладывается на другой, либо между ними образовывают небольшой зазор. Придерживать края можно при помощи шила или другого подобного инструмента. Разогретым наконечником паяльника берётся немного припоя ПОС 30 (ПОС 40) и поворотами в сторону данный материал распространяется по всей поверхности (если не заполняется полностью поверхность, значит инструмент зачищен не качественно).
Кончик с припоем подносят к изделиям из железа и проводят по предполагаемому шву плавными движениями. Закрепление при этом играет важную роль, так как при потенциальном сдвиге процесс придётся повторить заново. Таким образом, необходимое количество припоя наносится на поверхность, образовывая качественный шов. Прижимать паяльник следует всей гранью, а не отдельным его концом. В процессе этого происходит также нагрев элементов жести, за счёт чего шов хорошо присоединяется к поверхности.
После окончания пайки следует обработать получившийся слой металла бензиновой смесью или спиртом для снижения концентрации тепла и очистки от остатков припоя и кислоты. Это позволяет избежать появления ржавчины в дальнейшем.
Контроль поверхности выполняют зрительно. В промышленных масштабах применяют микроскопы и лупы. Шов должен быть глянцевым, без пор и трещин, покрывать только необходимую плоскость. Лишь в этом случае пайка считается качественной.
Особенности оцинкованных деталей
Для пайки оцинковки следует применять припои ПОС 30 и ПОС 40. Это связано с тем, что в составе ПОСС 4-6 имеется большое количество сурьмы, которая лишает впоследствии образованный шов прочности и эластичности. Во время спаивания деталей из оцинковки согласно рекомендациям используют раствор хлористого цинка. В случае, когда поверхность была лужена заранее, можно применять канифольный флюс и не производить промывку изделия после спаивания. Пайка в остальном обеспечивается тем же технологическим процессом, что описывался выше.
Действия с проволокой
Если вы планируете спаять проволоку с жестью, как оцинковки, так и обычной, следует один из углов первой согнуть под углом в 90 градусов. Это обеспечит прочность и надёжность конструкции. Процесс полностью схож с предыдущим описанием.
Меры предосторожности
Обязательно следует пользоваться предметами собственной защиты. Для паяльника применяйте специальные подставки, чтобы жало не касалось подручных предметов. Это может привести к их повреждению или чрезвычайной ситуации. Ни в коем случае нельзя прикасаться ко шву до полного его остывания, так как возможны ожоги кожи. Желательно работать в специальных перчатках, чтобы на руки не попали элементы в процессе пайки оцинковки. Важным аспектом здесь станет внимательное и осторожное обращение.
Как видите, пайка деталей из оцинковки или без покрытия предусматривает достаточно простые операции, которые с лёгкостью выполняются в домашних условиях. Следует придерживаться рекомендаций для получения качественных швов.
Похожие статьиgoodsvarka.ru
Паяние металла — Слесарные работы
Паяние является одним из видов неразъемных соединений двух деталей между собой посредством особого металла, или чаще сплава — припоя (рис. 222).
Рис. 222.
Температура плавления припоя немного ниже температуры плавления спаиваемых металлов.
Кроме того, припой и спаиваемые металлы должны легко сплавляться между собой.
Припои бывают мягкие с температурой плавления ниже 325° и твердые с температурой плавления не ниже 500°. Металлы с высокой температурой плавления (медь, латунь, серебро, золото) могут быть использованы в качестве твердых припоев.
Мягкие припои применяются для припаивания арматуры к бензиновым и масляным бакам, а также при паянии фильтров, отстойников и т. п. Главной составной частью мягких припоев являются олово и свинец. Твердые припои применяют в тех
случаях, когда изделия испытывают большие усилия или подвержены в работе высокому нагреву, вследствие чего соединение должно быть прочным.
Припои бывают в виде порошков, зернышек, пластинок, проволочек.
Выбор припоя (марка и химический его состав) зависит от назначения спаиваемого шва и от спаиваемых материалов. Трубопроводы и ниппели паяют исключительно твердыми припоями — серебряными и латунными. Для латунных припоев берут обыкновенную латунную проволоку диаметром 1-1,5 мм. Температура плавления такой латуни около 950°.
Пайку твердыми припоями производят в кузнечном горне или на паяльной лампе.
Если на поверхности трубы имеются трещины, то запаивать такой трубопровод запрещается. Все трубопроводы испытывают гидравлическим давлением; после испытания надо продуть трубы сжатым воздухом.
Для очистки изделий от окалины и для предохранения их от окисления перед паянием покрывают места спая протравами и флюсами. К протравам относятся: соляная кислота для паяния цинка, нашатырь для спаивания латуни и жести и хлористый цинк для спаивания меди, латуни, бронзы. В качестве флюса чаще всего используют буру, канифоль, стеарин, криолит.
Паять можно обычным или электрическим паяльником, паяльной лампой, горелкой, паяльной трубкой, а также погружением в ванну с расплавленным оловянным припоем. Кроме того, спаиваемые изделия можно нагревать в специальных печах. Если опаиваемые изделия велики и трудно поддаются прогреву паяльником, нужно сначала нагреть их до 150° в горне или на паяльной лампе. При паянии больших и толстых изделий .применяют ацетиленовые горелки. При паянии тонких изделий прогревают не само место спайки, а немного отступя ог него, чтобы тепло притекало и этому месту постепенно.
Инструмент, приспособления и материал
Паяльник, газовая горелка, паяльная лампа, напильники, шаберы, паяльные клещи, щипцы, волосяные щетки; приспособления для соединения спаиваемых изделий; протравы, флюсы, припои.
arxipedia.ru
Пайка различных металлов и сплавов
Изделия, очищенные и подготовленные для пайки, не должны храниться продолжительное время во избежание окисления. Их следует возможно скорее загружать в печь или контейнер с обеспечением защитной среды. Особенное внимание должно быть уделено удалению воздуха при пайке высоколегированных сталей и сплавов, содержащих легкоокисляемые элементы. Удаление воздуха может достигаться, вакуумированием или продуванием защитного газа — аргона. При продувании температура должна повышаться постепенно, начиная от комнатной до 800—900° С (1073— 1173 К). Этот процесс требует значительного расхода аргона. Вакуумирование более рационально, так как при этом значительно снижается расход аргона. Большое значение при пайке имеет контроль температуры нагрева изделия; перегрев может оказать вредное влияние.
Общее время пребывания припоя в расплавленном состоянии состоит из времени:

где t1 — время нагрева от температуры плавления припоя до температуры пайки; t2 — время выдержки при пайке; t3 — время охлаждения от температуры пайки до температуры кристаллизации припоя.
В случае взаимодействия припоя с основным металлом и t2 следует возможно сокращать. После окончания процесса пайки необходимо удалить флюс, очистить окисленные поверхности, устранить наплывы и участки растекания припоя, в особенности в тех местах, которые подлежат последующей обработке. Требование удаления флюса вызвано возможным отрицательным влияние его, например появлением коррозии (в алюминиевых сплавах).
Флюсы (для пайки алюминиевого сплава) удаляют промывкой горячей и холодной водой при условии последующей обработки в растворе хромового ангидрида. Флюсы на основе буры образуют на поверхности твердую корку. Их удаляют механическим путем или погружением деталей в горячую воду.
Паяные швы на алюминиевых сплавах обрабатывают металлической щеткой и вторично промывают от флюсов, могущих остаться в порах швов. Растекающийся припой удаляют механическим, химическим или электромеханическим способами.
Для контроля качества паяных соединений применяют разные методы. Существенное значение имеет внешний осмотр швов. Швы проверяются на прочность, плотность, электропроводимость. Паяные швы можно контролировать физическими методами: рентгеновским просвечиванием, применением радиоактивных изотопов, прозвучиванием.
Кроме испытания паяных образцов без их разрушения, нередко применяют испытания с доведением их до разрушения. Результаты, полученные при испытаниях до разрушения нескольких образцов, позволяют установить механические свойства серии аналогичных изделий.
К углеродистым и низколегированным сталям относятся стали, имеющие температуру плавления 1450—1520° С (1723—1793 К). При низкотемпературной пайке сталей применяются главным образом оловянно-свинцовые припои с активными флюсами. Перед пайкой рекомендуется детали облуживать. Это ускоряет процесс пайки и позволяет обеспечивать высокие механические свойства соединений.
Более часто для пайки сталей применяют высокотемпературные медно-цинковые припои с добавкой серебра (температура плавления 940—700° С (1213—973 К). Однако вследствие легкого испарения цинка эти припои не применяют для вакуумной пайки. Их целесообразно использовать при пайке в среде с низкими окислительными свойствами, например продуктов неполного сгорания азотно-водородной смеси с флюсом в виде буры, борного ангидрида и т. д. Для пайки углеродистых сталей в качестве припоя применяют также чистую медь, в особенности при пайке в печах в среде водорода. Медь хорошо растекается, заполняет малые зазоры. При этом прочность соединений превосходит прочность самой меди.
К высоколегированным сплавам относятся коррозионно-стойкие аустенитные стали 0Х18Н9, 12Х18Н9 со стабилизирующими добавками — титаном, ванадием, ниобием и т. д., кислотоупорные хромистые стали Х17, Х25 и другие ферритного класса, жароустойчивые никелевые сплавы, например, имеющие около 80% Ni и др.
Указанные сплавы могут паяться легкоплавкими припоями с применением активных флюсов.
Состав припоев, %
Система | Марка припоя | Температура, °С | Ag | Си | Zn | Мп | Ni | |
плавления | работы | |||||||
Ag-Cu | ПСр 72 | 779 | До 400 | 42 | 28 | - | - | - |
Ag—Си—Zn | ПСр 45 | 660—725 | 400 | 45 | 30 | 25 | — | — |
Ag—Mn | П 85-15 | 970 | 600 | 85 | — | — | 15 | — |
Си—Zn | Л 62 | 905 | — | — | 62 | 38 | — | — |
Си | — | 1083 | 500 | — | 100 | — | — | — |
Ni—Mn | 1270 | - | - | - | - | - | 20 | 80 |
Однако пайка легкоплавкими припоями указанной группы сплавов технически нецелесообразна. Рациональнее применять для их соединений высокотемпературные припои (табл. 21).
В соответствии с маркой припоя применяются флюсы с различными составляющими. Некоторые припои при быстром нагреве т. в. ч. теряют свои составляющие.
Высоколегированные сплавы и стали можно паять в среде аргона, водорода, в вакуумных печах. Недостаток пайки в аргоне — не вполне удовлетворительная растекаемость припоя. Для улучшения растекаемости во флюсы вводят добавки, например литий. Пайка в атмосфере водорода требует высокой его чистоты; использование водорода всегда сопряжено с некоторой опасностью взрыва.
Пайка в вакууме дает хорошие результаты при применении припоев, не содержащих легко испаряющихся элементов (цинка и др.). При пайке указанных выше материалов мoгyт возникать поры вследствие испарения некоторых составляющих припоя, например, цинка: непровары в результате неудовлетворительного смачивания расплавленным припоем соединяемых частей или недостаточной очистки поверхностей; трещины при проникновении жидкого припоя между границами зерен основного металла. Особенно часто образуются трещины при пайке медно-цинковыми и медно-серебряными припоями. Применением более высокотемпературных припоев можно избежать растрескивания паяных соединений.
Применение никелевых припоев иногда сопровождается образованием подрезов основного металла в местах перехода к швам.
Это происходит вследствие того, что припой этого рода имеет способность растворять основной металл. Чтобы избежать этого явления, следует вести технологический процесс пайки при возможно более низкой температуре.
При помощи пайки хорошо соединяются изделия из чистой меди и медных сплавов. Чистая медь хорошо паяется при нагреве в вакуумных печах, а также в атмосфере хорошо очищенного водорода без каких-либо примесей кислорода. Медно-цинковые сплавы, содержащие 4— 38% Zn, при длительном нагреве теряют его (цинк испаряется), поэтому латунные детали перед пайкой целесообразно покрывать медью.
Пайка широко применяется для соединений различных бронз; алюминиевых, содержащих 5—10% А1; бериллиевых, применяемых в приборостроении и имеющих в своем составе 2—2,5% Be; хромовых, содержащих около 0,5% Сг; оловянных, применяемых при обработке давлением, содержащих олово, а также фосфор и др.
Медь и ее сплавы легко паяются при применении низкотемпературных припоев с использованием канифольных флюсов, не вызывающих коррозии. Нередко перед пайкой поверхности деталей облуживают чистым оловом слоем толщиной 0,005 мм на стали и 0,0075 мм на меди. Низкотемпературные припои не обеспечивают высокой прочности паяных соединений, поэтому рекомендуется пайка в печах высокотемпературными твердыми припоями. Целесообразно применение медно-фосфорных и серебряных припоев и флюсов на основе буры с добавлением фтористых соединений. Алюминиевые бронзы хорошо паяются серебряными припоями с никелем, который препятствует проникновению в припой алюминия и повышает производительность технологического процесса.
Титан и его сплавы паяют в электрических печах, т. в. ч., газопламенными горелками. Наилучшие механические свойства спая достигаются при пайке т. в. ч. Это объясняется тем, что в результате сокращения термического цикла при этом способе пайки отсутствует рост зерна, приводящий к охрупчиванию соединений. При пайке титановых сплавов целесообразно применять серебряные припои, имеющие температуру плавления ниже температуры рекристаллизации титана и выше температуры, требуемой для удовлетворения условий смачивания припоем паяных деталей.
Очень важная задача производства — соединение пайкой различного рода керамических материалов и окислов друг с другом и с металлами. Возможны разные случаи: металлы более тугоплавки, нежели керамика, при этом соединение обеих деталей происходит в твердом состоянии, контакт обеспечивается необходимым давлением, применением покрытий. В последнем случае соединение достигается при температурах ниже температуры плавления каждой из соединяемых деталей.
Особенно благоприятные условия для соединения, когда металлы имеют температуру плавления ниже температуры плавления керамики и в результате своих специфических химических свойств склонны к образованию связи с последней. Так, например, титан и цирконий имеют большое сродство к кислороду и образуют твердые растворы со многими, металлами и окислами. Окислы титана и циркония весьма тугоплавки. При некоторых условиях эти металлы восстанавливают окислы металлов, образующих керамику, и присоединяют к себе освобожденный кислород. Такое восстановление, необходимое для прессовой пайки, следует проводить в условиях вакуума или в среде аргона.
Серьезные затруднение пайки керамик с металлами — существенная разница в их температурных коэффициентах расширения, в результате чего в соединениях образуются остаточные напряжения значительной величины. В неблагоприятных случаях, при недостаточной пластичности материалов в них возникают трещины. Для устранения этого явления иногда между соединяемым металлом и керамикой прокладывают пластины из пластичного металла, например молибдена. При пластических деформациях последнего опасность возникновения трещин в керамике значительно уменьшается.
С помощью специальных присадочных металлов можно получать качественные соединения не только однородных элементов, например А1а03 + А1203, но и разнородных. Сплавы, содержащие сильные карбидообразующие элементы — молибден, тантал, титан, цирконий и др.,— хорошо смачивают графит.
www.prosvarky.ru
ПАЙКА ТУГОПЛАВКИХ МЕТАЛЛОВ | Инструмент, проверенный временем
Тугоплавкие металлы и сплавы на их основе обладают высокими температурами плавления и термоэмиссионными свойствами, способностью активно окисляться и поглощать газы при повышенных температурах. Материалы этой группы обладают высокой коррозионной стойкостью в определенных агрессивных средах.
Молибден и вольфрам образуют летучие окислы, интенсивно испаряющиеся при нагреве выше 600ь С. В связи с этим на детали, изготовленные из этих материалов, предназначенные для работы на воздухе при высоких температурах, требуется наносить защитные покрытия.
Молибден и вольфрам отличаются малой плотностью при 20° С и охрупчи — ваются после нагрева выше температур рекристаллизации вследствие роста зерна.
Ниобий и тантал при нагреве на воздухе выше 200′ G активно окисляются и взаимодействуют с азотом. Окисление этих металлов и взаимодействие с азотом приводит к образованию на поверхности окисных и нитридных пленок.
В связи с высокой активностью тугоплавких металлов к взаимодействию
Рис. 5. Схема пайки в кварцевой трубке с нагревом ТВЧ:
1 — резиновый шланг для подачи аргона; 2 — трубка для подачи аргона; 3 — резиновая пробка; 4 — кварцевая трубка; 5 — индуктор; 6 — паяемый образец; 7 — керамические трубки; 8 — подставка: 9 — трубка для выхода аргона
с газами и способностью окисляться при нагреве для пайки требуется высокая чистота среды по кислороду и азоту.
Молибден и вольфрам рекомендуется нагревать в вакууме, аргоне, гелие, а также в среде водорода и диссоциированного аммиака с точкой росы —40-і—50° С.
Для пайки ниобия и тантала следует использовать вакуум С остаточным давлением не выше 1-І0~4 мм рт. ст. и очищенные нейтральные газы (аргон, гелий).
Для сохранения свойств исходного материала максимальная температура пайки материалов этой группы не должна превышать температуру их рекристаллизации.
Однако для деталей, предназначенных для работы при более высоких температурах (2000° С и выше), температура пайки может превышать температуру рекристаллизации и в этом случае снижение свойств паяемого металла неизбежно.
Пайку легкоплавкими и среднеплавкими припоями (ГОСТ 19248—73) проводят при температурах до 1200—
1300° С, а пайку высокоплавкими и тугоплавкими припоями — при более высоких температурах в зависимости от требований, предъявляемых к условиям работы изделий при эксплуатации. Нагрев под пайку до температур 1200—1300° С можно осуществлять в обычных электрических печах с применением герметичных контейнеров, заполненных необходимой для пайки средой, в вакуумных печах различных типов и в водородных печах. Нагрев под пайку при температурах выше 1250—3300° С можно производить токами высокой частоты (ТВЧ), световым лучом, электросопротивлением в герметичных контейнерах, камерах, кварцевых трубках, в вакууме или газовой среде, а также расфокусированным или сканирующим электронным лучом в электронно-лучевых установках. На рис. 5 приведена схема пайки в кварцевой трубке с нагревом ТВЧ. При нагреве ТВЧ и электросопротивлением необходимо учитывать форму и сечение стенок нагреваемых деталей. Нагрев ТВЧ целесообразно применять для деталей, имеющих форму тел вращения, а электросопротивлением — для деталей с постоянной толщиной стенок в зоне нагрева.
Пр и пайке припоями указанных групп возникают различные трудности. При пайке легкоплавкими и среднеплавкими припоями наиболее сложным вопросом является обеспечение смачивания, а при пайке тугоплавкими припоями — по возможности сохранение исходных свойств паяемого металла.
Пайку тугоплавких металлов оловянно-свинцовыми припоями можно осуществлять при температурах до 350—400° С по медным или никелевым покрытиям, наносимым на паяемые поверхности термовакуумным напылением, гальваническим и другими способами.
Для лучшего сцепления никелевого покрытия с поверхностью тугоплавких металлов рекомендуется применять термическую обработку деталей в вакууме при 850—900° С после нанесения покрытий.
Для пайки молибдена и вольфрама без покрытий оловянно-свинцовыми припоями, а также припоями на основе серебра и меди можно рекомендовать способ предварительного лужения поверхности деталей, включающий следующие операции: нанесение на поверхности, подлежащие пайке или лужению, водного раствора окислов молибдена (Мо02, Мо03), доведенного до сметанообразного состояния;
12 Под ред. Ю, Н. Зорина
11. Сопротивление срезу образцов из сплавов ВМ1 (числитель) и ВН2 (знаменатель) паяных припоями ВПр2 и ВПр4
|
сушку при температурах до 100° С и нагрев деталей в среде водорода с точкой росы — 40-—50° С для восстановления окислов молибдена. Последующее лужение молибдена и вольфрама по восстановленному слою окислов ведут в среде водорода, аргона и в вакууме при температуре выше 800° С. При нагреве в среде водорода процессы восстановления окислов и лужения можно совместить в одну операцию нагрева.
Слой окислов представляет сеть разветвленных капилляров, течение припоя в которых возможно при углах смачивания поверхности припоем 8 < 90°. По такой технологии можно нанести припой на поверхность практически любой величины и заданной конфигурации [8]. Процесс лужения по слою окислов может рассматриваться как способ управления течением припоя по поверхности и в около галтельных участках шва.
Для высокотемпературной пайки в интервале температур 1200—1300е С могут быть использованы припои на основе серебра, меди, никеля и палладия. Пайка тугоплавких металлов в этом интервале температур для каждого металла имеет свои особенности.
Молибден и вольфрам плохо смачиваются припоями на основе серебра и меди, поэтому пайку их этими припоями лучше вести при температурах, превышающих температуру пайки для обычных металлов на 50—150е С, т. е. при 950— 1200е С. Для пайки лучше использовать самофлюсующие припои на основе меди и серебра или применять пайку по покрытиям из меди и никеля.
При выборе припоев для высокотемпературной пайки ниобия в шлервале 1200—1300е С необходимо учитывать способность его к образованию интерметаллического соединения с никелем, входящим в состав многих стандартных припоев. Для пайки ниобия в качестве припоя можно рекомендовать чистую медь, припои на основе меди и палладия. Средние прочностные свойства паяных соединений из сплавов молибдена и ниобия приведены в табл. 11.
Тантал и его сплавы особенно чувствительны к примесям газов, имеющихся в нейтральной среде. Поэтому пайку тантала и его сплавов осуществляют в вакууме при остаточном давлении ниже ЫО’ЧЫО*5 мм рт. ст. Тантал плохо смачивается припоями; пайку среднеплавкими припоями рекомендуется вести по покрытиям из серебра, меди, никеля.
При пайке тугоплавкими припоями для всех указанных меіаллов в качестве припоев можно применять чистый титан, цирконий и сплавы на их основе; для пайки вольфрама — чистый ниобий и тантал.
Указанные металлы-припои образуют с молибденом, ниобием, танталом и вольфрамом сплавы в виде непрерывного ряда твердых растворов.
Учитывая, что пайку тугоплавкими припоями проводят при температурах, значительно превышающих температуры рекристаллизации указанных матерна*
лов, механические свойства паяных соединений при температурах испытаний ■~2000° С не превышают 2—6 кгс/мм2.
Исследование большого числа тугоплавких припоев показало, что для пайки в качестве припоев могут быть использованы системы сплавов: Ті—Nb, Ті—Nb— Сг, Ті—Mo, Ті—Мо—Сг, Ті—Mo—Zr, Nb—Zr, Nb—Zr—Cr, Mo—Cr, Nb—V, Nb—V—Zr, Ті—Та, Та—Zr, Nb—Cr и др. В этих системах большая часть припоев — твердые растворы, оказывающие небольшое влияние на охрупчивание паяемых металлов, но имеющие более высокие температуры плавления и довольно широкий интервал кристаллизации. Припои эвтектического состава (сплавы Та—Zr, Nb—Сг) часто позволяют снизить температуру пайки при той же рабочей температуре соединений.
Припои титан—ниобий, содержащие от 20 до 40% Ті — пластичные и могут быть получены в виде фольги; при содержании титана более 40% пластичность их снижается. Введение в их состав до 10—15% Сг позволяет снизить температуру плавления припоев и повысить пластичность. Припои титан—молибден, содержащие 15—45% Ті, имеют температуру плавления 1850—2000° С; введение хрома и циркония в эти припои снижает температуру их плавления.
Припои, содержащие ванадий и цирконий в твердых растворах Nb—V и Nb—Zr, обладают лучшим смачиванием и затеканием в зазоры.
Из стандартных припоев-сплавов для пайки тугоплавких металлов нашел применение сплав ЦН-25 (цирконий—ниобий) с температурой пайки 1850° С.
При пайке вольфрама припоем платина — бор с добавками порошка вольфрама в результате диффузии образуется сплав, работающий при температуре 2000° С.
Для пайки узлов и изделий из молибдена, вольфрама и ниобия, работающих на воздухе при температурах до 1600° С и имеющих защитные покрытия при выборе припоя, необходимо учитывать особенности взаимодействия припоя с элементами, входящими в состав защитного покрытия.
hssco.ru