Содержание углерода в чугунах составляет. Содержание углерода в чугуне
Содержание углерода в чугуне | Справочник конструктора-машиностроителя
Чугун - сплав железа с углеродом ( содержанием более 2, 14% ).Углерод в чугуне может содержаться в виде цементита и графита.В зависимости от формы графита и количества цементита, выделяют : бледный, бесцветный, ковкий и высокопрочные чугуны.Чугуны держат постоянные примеси ( Si, Mn, S, P ), а в отдельных событиях также легирующие элементы ( Cr, Ni, V, Al и др. ).
Чугу́н — сплав железа с углеродом с содержанием более 2, 14 % ( точка предельной растворимости углерода в аустените на диаграмме состояний ).Углерод в чугуне может содержаться в виде цементита и графита.В зависимости от формы графита и количества цементита, выделяют : бледный, бесцветный, ковкий и высокопрочные чугуны.Чугуны держат постоянные примеси ( Si, Mn, S, P ), а в отдельных событиях также легирующие элементы ( Cr, Ni, V, Al и др. ).Обыкновенно, чугун хрупок.
Ковкий чугун получают длительным отжигом белого чугуна, в итоге которого образуется графит хлопьевидной формы.Металлическая основа такого чугуна : феррит и реже перлит.Ковкий чугун получил свое название из - за повышенной пластичности и вязкости ( при всем при том, что обработке давлением не подвергается ).Ковкий чугун обладает повышенной крепостью при растяжении и рослым сопротивлением удару.Из ковкого чугуна изготовляют детали непростой фигуры : картеры заднего моста машин, тормозные колодки, тройники, угольники и т. д.
Включая небольшое сопротивление отливок из серого чугуна растягивающим и ударным нагрузкам, следует использовать сей материал для подробностей, которые подвергаются сжимающим или изгибающим нагрузкам.В станкостроении это – базовые, корпусные детали, кронштейны, зубчатые колеса, ведущие ;в автостроении - блоки цилиндров, поршневые кольца, распределительные валы, диски сцепления.Отливки из серого чугуна также используются в электромашиностроении, для изготовления товаров народного потребления.
Углерод в чугуне может находиться в виде цементита, графита или в то же самое время в виде цементита и графита.Возникновение постоянной фазы - графита в чугуне может происходить в итоге прямого выделения его из слабого ( твердого ) раствора или вследствие распада предварительно образовавшегося цементита ( при замедленном охлаждении расплавленного чугуна цементит может подвергнуться разложению РезС - > Fe + ЗС с образованием феррита и графита ).Процесс формирования в чугуне ( стали ) графита называют графитизацией.
По содержанию углерода чугуны подразделяются на доэвтектический - 2, 14 ...4, 3 % С, эвтектический - 4, 3 % С и заэвтектический - 4, 3 ...6, 67 % С углерода.Доэвтектические чугуны, включающие 2, 14 ...4, 3 % С, после окончательного охлаждения имеют структуру перлита, ледебурита ( перлит + цементит ) и вторичного цементита.Эвтектический чугун ( 4, 3% С ) при температуре ниже + 727 °С состоит только из ледебурита ( перлит + цементит ).Заэвтектический, который нельзя отменить 4, 3 ...6, 67 % С, при температуре ниже + 727 °С состоят из первичного цементита и ледебурита ( перлит + цементит ).На практике наибольшее распространение получили доэвтектические чугуны, включающие 2, 4 ...3, 8% С углерода.Тельное значение содержания углерода в чугуне определяется его технологическими характеристиками при литье - обеспечение хорошей жидкотекучести.Жидкотекучесть - это способность металлов и сплавов в расплавленном состоянии заполнять полость формы, точно воспроизводить очертания и размеры отливки.Увеличенное содержание углерода в чугуне выше 3, 8% С приводит к резкому возрастанию твердости и хрупкости.Жидкотекучесть определяется по спиральной пробе, а ее величина по длине заполнения части спирали.Усадка - уменьшение линейных и обьемных размеров металла, затопленного в фигуру при его кристаллизации и охлаждении.
В промышленности разновидности чугуна маркируются следующим типом : передельный чугун — П1, П2 ;передельный чугун для отливок ( передельно - литейный ) — ПЛ1, ПЛ2, передельный фосфористый чугун — ПФ1, ПФ2, ПФ3, передельный высококачественный чугун — ПВК1, ПВК2, ПВК3 ;чугун с пластинчатым графитом — СЧ ( цифры после букв « СЧ », значат величину временного сопротивления разрыву в кгс/мм ) ;антифрикционный чугун антифрикционный серый — АЧС, антифрикционный высокопрочный — АЧВ, антифрикционный ковкий — АЧК ;чугун с шаровидным графитом для отливок — ВЧ ( цифры после букв « ВЧ » означают временное сопротивление разрыву в кгс/мм и относительное удлиненние ( % ) ;чугун легированный со специальными свойствами — Ч.
Чугун содержит углерода | Справочник конструктора-машиностроителя
Чугу́н — сплав железа с углеродом ( и прочими элементами ).Содержание углерода в чугуне не менее 2, 14 % ( точка предельной растворимости углерода в аустените на диаграмме состояний ) : меньше — сталь.Углерод придаёт сплавам железа крепость и твёрдость, снижая пластичность и вязкость.Углерод в чугуне может содержаться в виде цементита и графита.В зависимости от формы графита и количества цементита, выделяют : бледный, бесцветный, ковкий и высокопрочные чугуны.Чугуны содержат постоянные примеси ( Si, Mn, S, P ), а в отдельных событиях также легирующие элементы ( Cr, Ni, V, Al и др. ).Обыкновенно, чугун хрупок.
Чугу́н — сплав железа с углеродом ( и прочими элементами ).Содержание углерода в чугуне не менее 2, 14 % ( точка предельной растворимости углерода в аустените на диаграмме состояний ) : меньше — сталь.Углерод придаёт сплавам железа крепость и твёрдость, снижая пластичность и вязкость.Углерод в чугуне может содержаться в виде цементита и графита.В зависимости от формы графита и количества цементита, выделяют : бледный, бесцветный, ковкий и высокопрочные чугуны.Чугуны содержат постоянные примеси ( Si, Mn, S, P ), а в отдельных событиях также легирующие элементы ( Cr, Ni, V, Al и др. ).Обыкновенно, чугун хрупок.
Ковкий чугун получают длительным отжигом белого чугуна, в итоге которого образуется графит хлопьевидной формы.Металлическая основа такого чугуна : феррит и реже перлит.Ковкий чугун получил свое название из - за повышенной пластичности и вязкости ( при всем при том, что обработке давлением не подвергается ).Ковкий чугун обладает повышенной крепостью при растяжении и рослым сопротивлением удару.Из ковкого чугуна изготовляют детали непростой фигуры : картеры заднего моста машин, тормозные колодки, тройники, угольники и т. д.
При нормальных температурах структура чугуна состоит из перлита, вторичного цементита и ледебурита.Ледебурит после эвтектоидного превращения представляет собой механическую смесь перлита и цементита.Чугуны с содержанием углерода до 4, 3 % называются доэвтектическими чугунами.такие чугуны называются белыми чугунами , если углерод находится в чугунах в химически связанном состоянии с железом, т.е. в цементите .Микроструктура сплава IV, воображающего собой доэвтектический белый чугун, изображена на рис.
По содержанию углерода чугуны подразделяются на доэвтектический - 2, 14 ...4, 3 % С, эвтектический - 4, 3 % С и заэвтектический - 4, 3 ...6, 67 % С углерода.Доэвтектические чугуны, содержащие 2, 14 ...4, 3 % С, после окончательного охлаждения имеют структуру перлита, ледебурита ( перлит + цементит ) и вторичного цементита.Эвтектический чугун ( 4, 3% С ) при температуре ниже + 727 °С состоит только из ледебурита ( перлит + цементит ).Заэвтектический, который нельзя отменить 4, 3 ...6, 67 % С, при температуре ниже + 727 °С состоят из первичного цементита и ледебурита ( перлит + цементит ).На практике наибольшее распространение получили доэвтектические чугуны, содержащие 2, 4 ...3, 8% С углерода.Тельное значение содержания углерода в чугуне определяется его технологическими характеристиками при литье - обеспечение хорошей жидкотекучести.Жидкотекучесть - это способность металлов и сплавов в расплавленном состоянии заполнять полость формы, точно воспроизводить очертания и размеры отливки.Увеличенное содержание углерода в чугуне выше 3, 8% С приводит к резкому возрастанию твердости и хрупкости.Жидкотекучесть определяется по спиральной пробе, а ее величина по длине заполнения части спирали.Усадка - уменьшение линейных и обьемных размеров металла, затопленного в фигуру при его кристаллизации и охлаждении.
В стандарте Германии DIN 1693 - 506 - 50 в прозвании марки буквы обозначают : G - "gegosen" ( отлито ), G - "gubeisen" ( чугун ), G - "globular" ( шаровой ), 50 - наименьшее значение предела крепости в МПа 10 - 1 ( например, GGG - 50 ).В В большинстве национальных образцов на высокопрочные нелегированные чугуны, регламентирующих механические свойства, химический состав чугунов не оговаривается.Неизбежными для контроля являются предел крепости при растяжении, предел текучести, и относительное удлинение.В образцах всех сторон, за исключением стандартов Германии и США, приводятся контролируемые пределы величин твердости.
Включая небольшое сопротивление отливок из серого чугуна растягивающим и ударным нагрузкам, следует использовать сей материал для подробностей, которые подвергаются сжимающим или изгибающим нагрузкам.В станкостроении это – базовые, корпусные детали, кронштейны, зубчатые колеса, ведущие ;в автостроении - блоки цилиндров, поршневые кольца, распределительные валы, диски сцепления.Отливки из серого чугуна также используются в электромашиностроении, для изготовления товаров народного потребления.
Высокопрочные чугуны ( ГОСТ 7293 ) могут иметь ферритную ( ВЧ 35 ), феррито - перлитную ( ВЧ45 ) и перлитную ( ВЧ 80 ) металлическую основу.Зарабатывают эти чугуны из бесцветных, в результате модифицирования магнием или церием ( добавляется 0, 03…0, 07% от массы отливки ).По сравнению с серыми чугунами, механические свойства повышаются, это порождено отсутствием неравномерности в распределении усилий из - за шаровой формы графита.
spravconstr.ru
Углеродистый чугун | Учебные материалы
Чугун — это сплав железа с углеродом, в котором содержание углерода больше 2,14 %.
Кроме углерода и железа, в сплаве присутствуют примеси: кремний, марганец, фосфор, сера и др. Эти примеси оказывают существенное влияние на формирование структуры сплава, а следовательно, и на механические, физические и другие свойства чугуна.
В зависимости от того, в какой форме присутствует углерод в сплавах, различают белые, серые, ковкие и высокопрочные чугуны. По химическому составу чугун делится на углеродистый и легированный.
Белыми называют чугуны в которых углерод находится преимущественно в связанном состоянии в виде цементита Fe3С (очень небольшое количество углерода находится в составе твердого раствора). Эти чугуны, фазовые превращения которых протекают согласно диаграмме Fe-С, подразделяются на доэвтектические, эвтектический и заэвтектические. Из-за большого количества цементита белые чугуны имеют высокую твердость 450…550 НВ, хрупкие и практически не поддаются обработке резанием, поэтому в качестве конструкционных материалов практически не применяются. Их можно применять для деталей, от которых требуется высокая износостойкость поверхности. Например, изготавливают шары шаровой мельницы для размола руды и минералов.
Белые чугуны являются передельными и из них получают сталь и ковкий чугун.
Серыми называют чугуны, в которых углерод находится преимущественно в свободном состоянии в виде пластинок графита. Графит образуется при очень малой скорости охлаждения, когда степень переохлаждения жидкой фазы невелика. Он растет из одного центра и, разветвляясь в разные стороны, приобретает форму сильно искривленных лепестков. В плоскости шлифа графит имеет вид прямолинейных или завихренных пластинок, которые представляют собой сечения графитных лепестков. В изломе эти чугуны имеют серый цвет. Механические свойства чугуна обусловлены его структурой, главным образом графитной составляющей, его количеством, формой и размерами включений.
Графит имеет низкую прочность, и его можно рассматривать как внутренние надрезы, нарушения сплошности металлической основы. С увеличением содержания углерода больше выделений графита и меньше механическая прочность чугуна. Серый чугун плохо сопротивляется растяжению, хрупкий, но обладает хорошей жидкотекучестью, малой усадкой при кристаллизации, легко обрабатывается резанием, хорошими антифрикционными свойствами (графит выполняет роль смазки), поглощает вибрацию, малочувствителен к концентраторам напряжений (надрезам, выточкам).
Удельный вес серого чугуна колеблется в пределах 6,6…7,4 г/см3 и зависит от количества углерода, степени графитизации и количественного соотношения структурных составляющих.
Теплоемкость серого чугуна также зависит от вышеперечисленных факторов и в интервале температур 0…700 0С равна 16 кал/(г∙0С). Теплопроводность равна 0,16 кал/(см∙с∙0С). Средний коэффициент линейного термического расширения в интервале температур 0…100 0С можно принять (10…11)∙106 см/(см∙0С), а в интервале температур 100…700 0С он равен 14∙106 см/(см∙0С).
Основными элементами в чугунах являются Fe-C-Si и постоянными примесями — Мn, Р, S. Кремний обладает сильным графитизирующим действием, марганец затрудняет графитизацию. Сера является вредной примесью, ухудшает литейные и механические свойства чугунов.
Фосфор является в чугунах полезной примесью, так как улучшает жидкотекучесть. Участки фосфидной эвтектики увеличивают твердость и износостойкость чугуна. Чаще всего содержание фосфора находится в пределах 0,2…0,5 %. Для отливок, от которых требуется высокая износостойкость, содержание фосфора допускается 0,7 %, а для художественного литья — до 1 %.
Наглядное представление о влиянии углерода и кремния на степень графитизации чугуна и его структуру дает структурная диаграмма (толщина стенки отливки 50 мм), приведенная на рисунок 37.
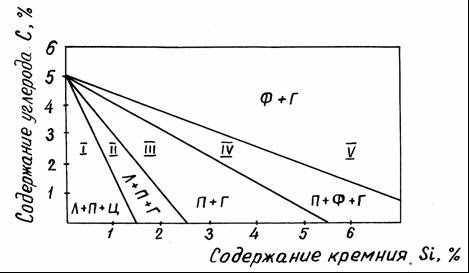
I- белый чугун; II- половинчатый чугун; III- серый чугун на перлитной основе; IV- серый чугун на ферритно-перлитной основе; V- серый чугун на ферритной основе
Рисунок 37 — Структурная диаграмма
Серый чугун маркируется буквами СЧ, после которых ставится число, показывающее гарантируемый предел прочности на растяжение в кгс/мм2
(10-1 МПа).
Ферритные чугуны марок СЧ10, СЧ15, СЧ18 применяются для малоответственных деталей, испытывающих небольшие нагрузки. Например, фундаментные плиты, крышки, фланцы, рамы двигателей, компрессоров, шиберы и заслонки печей, корпусы фильтров и масленок, маховики, корпуса редукторов, насосов, тормозные барабаны, диски сцепления и др. Структура серых чугунов приведена на рисунок 38.
Феррито-перлитные чугуны марок СЧ20, СЧ21, СЧ25 применяются для деталей, работающих при повышенных статических и динамических нагрузках. Например, головки цилиндров, поршни, втулки для поршневых колец паровых цилиндров, колеса центробежных насосов, станины станков, зубчатые колеса, диафрагмы, цилиндры низкого давления и выхлопные патрубки турбин.
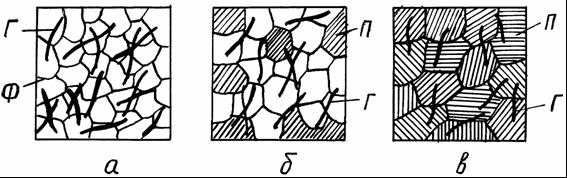
а- на ферритной основе; б- на ферритно -перлитной основе;
в- на перлитной основе
Рисунок 38 — Структура серых чугунов
Перлитные чугуны марок СЧ30, СЧ35, СЧ40, СЧ45 применяют для деталей, работающих при высоких нагрузках или в тяжелых условиях износа: зубчатые колеса, гильзы блоков цилиндров, распределительные валы и др. Мелкие разобщенные графитовые включения меньше снижают прочность чугунов. Измельчение графитовых включений достигается путем модифицирования жидкого чугуна ферросилицием, алюминием или феррокальцием (0,3…0,6 % от массы шихты). Отливки из серого чугуна подвергают термической обработке: для снятия внутренних напряжений — отжиг I рода (560 0С), нормализацию или закалку с отпуском для повышения механических свойств и износостойкости. Для повышения износостойкости гильз цилиндров, распределительных валов и других изделий перлитные чугуны подвергают азотированию.
Ковкими называют чугуны, в которых углерод находится в свободном состоянии в форме хлопьев. Такая форма графита и является основной причиной высоких прочностных и пластических характеристик ковкого чугуна. Термин ”ковкий чугун” является условным, поскольку изделия из него, так же как и из любого другого чугуна, изготавливают не ковкой, а путем литья, и указывает на повышенную пластичность по сравнению с серым чугуном. Состав ковкого чугуна выдерживается в довольно узких пределах: 2,4…2,9 % С; 1,0…1,6 % Si; 0,2…1,0 % Мn; до 0,18 % Р и до 0,2 % S.
Невысокое содержание углерода в ковком чугуне необходимо по двум причинам. Во-первых, для получения высоких прочностных характеристик следует уменьшить количество графитовых включений. Во-вторых, необходимо избегать выделения пластинчатого графита при охлаждении отливок в форме (с этой же целью толщина стенки отливки не должна превышать 50 мм).
Ковкий чугун получают из белого путем отжига, который продолжается иногда до 5 суток. По структуре металлической основы (рисунок 39), которая определяется режимом отжига, ковкие чугуны бывают ферритными и перлитными.
Отжиг на ферритные чугуны проводится по режиму 1 (рисунок 40), обеспечивающему графитизацию всех видов цемента белого чугуна.
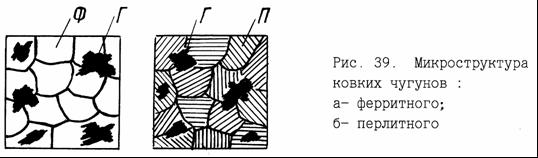
а – ферритного; б – перлитного
Рисунок 39 – Микроструктура ковких чугунов
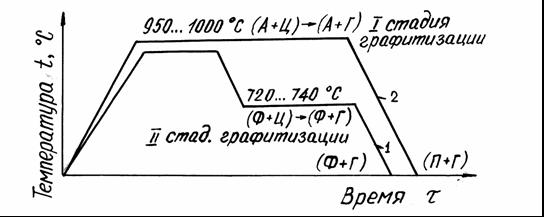
Рисунок 40 – Схема отжига белого чугуна на ковкий
Отливки из белого чугуна загружают в металлические ящики и засыпают песком или стальными стружками для защиты от окисления и медленно нагревают до температуры 950…1000 0С. В процессе продолжительной (10…15 ч) выдержки при такой температуре происходит первая стадия графитизации. Она состоит в распаде эвтектического и избыточного вторичного цементита.
К концу первой стадии чугун состоит из аустенита и включений углерода отжига (А + Г). Затем температуру медленно снижают до 720…740 0С. При этом происходит вторая стадия графитизации.
В процессе выдержки (25…30 ч) распадается цементит перлита:
П(Ф + Ц) -> Ф + Г
и образуется ковкий чугун на ферритной основе.
Перлитный чугун получают отжигом, который проводят в окислительной среде по режиму 2 (см. рис. 40). В этом случае увеличивают продолжительность первой стадии графитизации, после которой проводят непрерывное охлаждение отливок до 20 0С. Аустенит превращается в перлит (А -> П), а графит сохраняется в структуре. Получается ковкий чугун на перлитной основе.
Ковкие чугуны маркируются буквами КЧ, после которых ставятся числа, показывающие гарантируемые предел прочности на растяжение в кгс/мм2
(10-1 МПа) и относительное удлинение в процентах. Марки ковкого чугуна:
- КЧ-30-6; КЧ 35-10; КЧ 37-12 — ферритные;
- КЧ 45-7; КЧ 60-3; КЧ 80-1,5 — перлитные.
Из этих чугунов изготавливают детали высокой прочности, работающие в тяжелых условиях износа, способные воспринимать ударные и знакопеременные нагрузки. Большая плотность отливок ковкого чугуна позволяет изготовлять детали водо- и газопроводных установок, корпуса вентилей, кранов, задвижек.
Высокопрочными называют чугуны, в которых углерод находится в свободном состоянии в виде шаровидного графита. Их получают модифицированием магнием, который вводят в жидкий чугун в количестве 0,02…0,08 %. Ввиду того, что модифицирование чистым магнием сопровождается значительным пироэффектом, применяют сплав магния с никелем.
Чугун после модифицирования имеет следующий химический состав: 3,0…3,6 % С; 1,1…1,9 % Si;. 0,3…0,7 % Мn;. до 0,02 % S и до 0,1 % P. По структуре металлической основы чугун может быть ферритным или перлитным (рисунок 41).
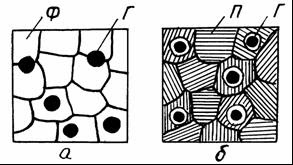
а- ферритного; б- перлитного
Рисунок 41 — Микроструктура высокопрочных чугунов
Шаровидный графит — менее сильный концентратор напряжений, чем пластинчатый или хлопьевидный графит, и поэтому меньше снижает механические свойства металлической основы. Чугуны обладают высокой прочностью и некоторой пластичностью, сохраняют свою прочность до 500 0С (обычный чугун до 400 0С). Они маркируются буквами ВЧ, после которых ставится число, показывающее гарантируемый предел прочности на растяжение в кгс/мм2 (10-1 МПа). Марки высокопрочного чугуна:
- ВЧ 38; ВЧ 42; ВЧ 50 — ферритные;
- ВЧ 60, ВЧ 80; ВЧ 120 — перлитные.
Высокопрочные чугуны применяют в различных отраслях техники, эффективно заменяя сталь во многих изделиях и конструкциях. Например, корпуса паровых турбин, насосов, вентилей, лопатки направляющего аппарата, коленчатые валы, поршни и другие ответственные детали, работающие при высоких циклических нагрузках и в условиях изнашивания.
В некоторых случаях для улучшения механических свойств применяют термическую обработку отливок; для повышения прочности — закалку и отпуск при 500…600 0С; для увеличения пластичности — отжиг.
Недостатком высокопрочного чугуна является значительная объемная усадка, что приводит к появлению в отливках усадочной пористости, газовых раковин.
dprm.ru
Структура серого чугуна | Справочник конструктора-машиностроителя
Серый чугун был прозван так по виду излома, имеющего серый тон.Прозвание серый чугун не абсолютно корректно распространилось на литейный чугун, в структуре которого имеются включения пластинчатого графита.чугун с пластинчатым графитом так и продолжают называть серым чугуном , потому что эта ошибка была закреплена на уровне государственного стандарта ( ГОСТ 1412 - 85 ) .В то же времечко не стоит забывать, что первый симптом, благодаря которому серый чугун получил своё название, а именно - серый тон, можно видеть, например, у ковкого чугуна.Серый цвет чугуна зависит от числа свободного графита, а не от формы графитных включений в чугуне.Вообще, в систематизации и названиях чугунов существует историческая каша, которая особливо очень наблюдается и мешает при работе с зарубежными источниками научно - технической информации.
свадьба
Включая небольшое сопротивление отливок из серого чугуна растягивающим и ударным нагрузкам, следует использовать сей материал для подробностей, которые подвергаются сжимающим или изгибающим нагрузкам.В станкостроении это – базовые, корпусные детали, кронштейны, зубчатые колеса, ведущие ;в автостроении - блоки цилиндров, поршневые кольца, распределительные валы, диски сцепления.Отливки из серого чугуна также используются в электромашиностроении, для изготовления товаров народного потребления.
Структура серого ( литейного ) чугуна состоит из металлической основы с графитом пластинчатой формы, вкрапленным в эту основу.Такая структура образуется непосредственно при кристаллизации чугуна в отливке в соответствии с диаграммой состояния системы Fe — С ( постоянной ).Причем, чем больше углерода и кремния в сплаве и чем ниже скорость его охлаждения, тем выше вероятность кристаллизации по этой диаграмме с образованием графитной эвтектики.При коротком содержании углерода и кремния чугун модифицируют небольшими дозами некоторых элементов ( например, алюминий, кальций, церий ).
Особенностями структуры матрицы высокопрочного чугуна с шаровидным графитом являются : а ) расположение феррита преимущественно в виде оторочек вокруг включений шаровидного графита ;б ) тонче, чем у серого чугуна, строение пластинчатого перлита, часто напоминающее сорбитообразный перлит.Излом высокопрочного чугуна с шаровидным графитом посветлее и мелкозернистый, чем серого чугуна.Химический состав является одним из главных параметров при выборе чугуна для конкретной подробности.
Сплав железа с углеродом ( > 2, 14 % С ) называют чугуном.Присутствие эвтектики в структуре чугуна обусловливает его использование исключительно в качестве литейного сплава.Углерод в чугуне может находиться в виде цементита или графита, или в то же самое время в виде цементита и графита.Цементит придает излому специфический светлый глянец.Поэтому чугун, в котором весь углерод находится в виде цементита, именуют бледным.Графит придает излому чугуна серый тон, поэтому чугун называют серым.В зависимости от формы графита и обстоятельств его образования различают следующие чугуны : серый, высокопрочный и ковкий.
Великое распространение имеют высокопрочные чугуны, получающиеся за счет небольших добавок магния, церия, силикокальция и других присадок, сильно изменяющих структуру и прочностные свойства чугуна.Такие чугуны сочетают в себе высокопрочную перлитную и.очень вязкую ферритную основу и наиболее выгоднее ( шаровидную ) форму графита, что обусловливает высокие показатели их механических свойств.Использование высокопрочного чугуна для получения ответственных отливок еще больше расширило область применения чугунов в машиностроении.
По содержанию углерода чугуны подразделяются на доэвтектический - 2, 14 ...4, 3 % С, эвтектический - 4, 3 % С и заэвтектический - 4, 3 ...6, 67 % С углерода.Доэвтектические чугуны, включающие 2, 14 ...4, 3 % С, после окончательного охлаждения имеют структуру перлита, ледебурита ( перлит + цементит ) и вторичного цементита.Эвтектический чугун ( 4, 3% С ) при температуре ниже + 727 °С состоит только из ледебурита ( перлит + цементит ).Заэвтектический, который нельзя отменить 4, 3 ...6, 67 % С, при температуре ниже + 727 °С состоят из первичного цементита и ледебурита ( перлит + цементит ).На практике наибольшее распространение получили доэвтектические чугуны, включающие 2, 4 ...3, 8% С углерода.Тельное значение содержания углерода в чугуне определяется его технологическими характеристиками при литье - обеспечение хорошей жидкотекучести.Жидкотекучесть - это способность металлов и сплавов в расплавленном состоянии заполнять полость формы, точно воспроизводить очертания и размеры отливки.Увеличенное содержание углерода в чугуне выше 3, 8% С приводит к резкому возрастанию твердости и хрупкости.Жидкотекучесть определяется по спиральной пробе, а ее величина по длине заполнения части спирали.Усадка - уменьшение линейных и обьемных размеров металла, затопленного в фигуру при его кристаллизации и охлаждении.
Чугу́н — сплав железа с углеродом ( и прочими элементами ).Содержание углерода в чугуне не менее 2, 14 % ( точка предельной растворимости углерода в аустените на диаграмме состояний ) : меньше — сталь.Углерод придаёт сплавам железа крепость и твёрдость, снижая пластичность и вязкость.Углерод в чугуне может содержаться в виде цементита и графита.В зависимости от формы графита и количества цементита, выделяют : бледный, серый, ковкий и высокопрочные чугуны.Чугуны держат постоянные примеси ( Si, Mn, S, P ), а в отдельных событиях также легирующие элементы ( Cr, Ni, V, Al и др. ).Обыкновенно, чугун хрупок.
Данный элемент замедляет графитизацию и считается активным карбидообразующим веществом, приводит к увеличению твердости и крепости серого чугуна.Всякий лишний процент молибдена увеличивает крепость на 1 кГ/мм2.Характерно, что при этом ударная вязкость не снижается, а наоборот, возрастает.При высочайших температурах Мо укрепляет прочность чугуна, и наиболее действенного результата можно добиться при вхождении 1, 9% Мо.Выше его концентрация приводит к образованию ледебурита и снижению прочности.Молибден делает чугун более износостойким.
Структура серого ( литейного ) чугуна состоит из металлической основы с графитом пластинчатой формы, вкрапленным в эту основу.Такая структура образуется непосредственно при кристаллизации чугуна в отливке в соответствии с диаграммой состояния системы Fe - С ( постоянной ).Причем, чем больше углерода и кремния в сплаве и чем ниже скорость его охлаждения, тем выше вероятность кристаллизации по этой диаграмме с образованием графитной эвтектики.При коротком содержании углерода и кремния чугун модифицируют небольшими дозами некоторых элементов ( например, алюминий, кальций, церий ).
ВЫСОКОПРОЧНЫЙ ЧУГУН С ШАРОВИДНЫМ ГРАФИТОМ Высокопрочными называют чугуны с шаровидным графитом, который уладится в литой структуре в процессе кристаллизации.Шаровидный, который нельзя отменить минимальную поверхность при данном объеме, значительно меньше ослабляет металлическую основу, чем пластинчатый графит, и не является активным концентратором напряжений.Для получения шаровидного графита чугун модифицируют, чаре путем обработки редкого металла магнием ( 0, 03 — 0, 07 % ) или предисловием 8 — 10 % магниевых лигатур с никелем или ферросилицием.Под действием магния графит в процессе кристаллизации принимает не пластинчатую, а шаровую фигуру.Чугуны с шаровидным графитом ( ЧШГ ) имеют выше механические свойства, не уступающие свойствам литой углеродистой стали, сохраняя при этом хорошие литейные свойства и обрабатываемость резанием, способность гасить вибрации, высокую износостойкость и т. д. Обычный состав чугуна : 3, 2 — 3, 6 % С 3. ковкий чугун Ковкий чугун получают длительным нагревом при высоких температурах ( отжигом ) отливок из белого чугуна.В результате отжига образуется графит хлопьевидной формы.Такой графит по сравнению с пластинчатым меньше снижает крепость и пластичность металлической основы структуры чугуна.Чугун имеет уменьшенное содержание углерода и кремния.
spravconstr.ru
Как получают чугун | Справочник конструктора-машиностроителя
Чугу́н — сплав железа с углеродом с содержанием более 2, 14 % ( точка предельной растворимости углерода в аустените на диаграмме состояний ).Углерод в чугуне может содержаться в виде цементита и графита.В зависимости от формы графита и количества цементита, выделяют : бледный, бесцветный, ковкий и высокопрочные чугуны.Чугуны держат постоянные примеси ( Si, Mn, S, P ), а в отдельных событиях также легирующие элементы ( Cr, Ni, V, Al и др. ).Обыкновенно, чугун хрупок.
Ковкий чугун получают длительным отжигом белого чугуна, в итоге которого образуется графит хлопьевидной формы.Металлическая основа такого чугуна : феррит и реже перлит.Ковкий чугун получил свое название из - за повышенной пластичности и вязкости ( при всем при том, что обработке давлением не подвергается ).Ковкий чугун обладает повышенной крепостью при растяжении и рослым сопротивлением удару.Из ковкого чугуна изготовляют детали непростой фигуры : картеры заднего моста машин, тормозные колодки, тройники, угольники и т. д.
Включенная в действие доменная печь функционирует непрерывно в течение нескольких лет.Руду, кокс и флюсы периодически добавляют через верхнее отверстие ( колошник ) печи.Также периодически производится выпуск из нее чугуна и шлака — через любые 4 — 6 ч.При этом 99 — 99, 8% железа переходит в чугун и только 0, 2 — 1, 0% — в шлак.Кроме углерода в составе чугуна присутствуют элементы кремния, марганца, серы, фосфора и пр.По назначению доменные чугуны разделяют на литейный и передельный.Литейный чугун переплавляют, и из него отливают чугунные изделия.Из передельного чугуна получают сталь.Он составляет около 90% всей выплавки чугуна.В нем содержится повышенное количество углерода, 0, 3 — 1, 2% Si, 0, 2 — 1, 0% Mn, 0, 2 — 1, 0% Р, 0, 02 — 0, 07% 5.
Белый Ч. представляет собой сплав, в котором избыточный углерод, не присутствующий в твёрдом растворе железа, присутствует в объединенном состоянии в виде карбидов железа Fe 3 C ( цементит ) или т. н. специальных карбидов ( в легированном Ч.Кристаллизация белых Ч. происходит по метастабильной системе с образованием цементита и перлита.Белый Ч. вследствие коротких механических характеристик и хрупкости располагает ограниченное применение для деталей простой конфигурации, действующих в обстановках повышенного абразивного износа.Легирование белого Ч. карбидообразующими элементами ( Cr, W, Mo и др. ) повышает его износостойкость.
Белый чугун получают путем первичной кристаллизации из редкого сплава при быстрейшем охлаждении.Представляет собой сплав, в котором избыточный углерод, не присутствующий в твёрдом растворе железа, присутствует в объединенном состоянии в виде карбидов железа Fe3C ( цементит ), который придает чугуну бело - неяркий тон.Белый чугун обладает высокой твердостью, хрупкостью и дурно обрабатывается, поэтому для изготовления деталей он не используется и применяется как передельный, т.е. идет на производство стали и иных паспортов чугуна.Половинчатый чугун держит часть углерода в пустом состоянии в виде графита, а часть — в объединенном в виде карбидов.Применяется в качестве фрикционного материала, действующего в условиях сухого трения ( тормозные колодки ), а также для изготовления деталей повышенной износостойкости ( прокатные, бумагоделательные, мукомольные валки ).
Механические свойства и рекомендуемый химический состав ковкого чугуна регламентирует ГОСТ 1215 - 79.Ковкие чугуны маркируют буквами « К » - - ковкий, « Ч » _ 效 угун и циферками.Главная группа цифр показывает предел прочности чугуна при растяжении, другая - - сравнительное его удлинение при разрыве.Например, КЧ 33 - 8 обозначает : ковкий чугун с лимитом крепости при растяжении 33 кг/мм 2 ( 330 МПа ) и относительным удлинением при разрыве 8 %.
В итоге длительной продувки воздухом из кусков руды получались почти без примесей кусочки настоящего железа, которые сваривались между собой кузнечным способом в зону, которые далее использовались для производства необходимых человеку изделий.Это технически чистое железо держало весьма немного углерода и немного примесей ( настоящий древесный уголек и хорошая руда ), поэтому оно хорошо ковалось и сваривалось и практически не корродировало.Процесс выступал при относительно низкой температуре ( до 1100…1350 ° С ), м еталл не плавился, т. е. восстановление металла выступало в решительной фазе.В итоге получалось ковкое ( рев ) железо.Просуществовал этот способ до XIV века, а в несколько усовершенствованном облике до начала XX века, но был помалу вытеснен кричным переделом.
Серый чугун — наиболее широко применяемый вид чугуна ( машиностроение, сантехника, строительные конструкции ) — имеет включения графита пластинчатой формы.Для подробностей из серого чугуна характерны небольшая чувствительность к действию внешних концентраторов напряжений при циклических нагружениях и более высокий коэффициент поглощения колебаний при вибрациях подробностей ( в 2 - 4 раза выше, чем у стали ).Важная конструкционная особенность серого чугуна — выше, чем у стали, отношение предела текучести к пределу прочности на растяжение.Наличие графита улучшает условия смазки при трении, что повышает антифрикционные свойства чугуна.Свойства серого чугуна зависят от структуры металлической основы, фигуры, величины, числа и характера распределения включений графита.Перлитный серый чугун имеет высокие прочностные свойства и применяется для цилиндров, втулок и др. нагруженных деталей двигателей, лафетов и т.д.Для менее ответственных деталей используют серый чугун с ферритно - перлитной металлической основой.
Структура отливок определяется химическим составом чугуна и технологическими особенностями его термообработки.Механические свойства серого чугуна зависят от свойств металлической матрицы, фигуры и размеров графитовых включений.Свойства металлической матрицы чугунов близки к свойствам стали., который нельзя отменить невысокую прочность, снижает прочность чугуна.Чем меньше графитовых включений и выше их дисперсность, тем больше прочность чугуна.Графитовые включения вызывают сокращение предела прочности чугуна при растяжении.На крепость при сжатии и твердость чугуна частицы графита почти не оказывают воздействия.Свойство графита образовывать смазочные пленки обусловливает падение коэффициента трения и увеличение износостойкости изделий из серого чугуна.Графит улучшает обрабатываемость резанием.
Великое значение для практики имеет свойство модификации γ - Fе растворять до 2, 14% углерода при температуре 1147°С с образованием твердого раствора и с внедрением атомов углерода в кристаллическую решетку.При повышении и снижении температуры растворимость углерода в модификации γ - Fе уменьшается.Крепкий раствор углерода и прочих элементов ( азот, водород ) в модификации γ - Fе называется аустенитом ( по имени ученого Р. Аустена ), почти в 100 раз меньше углерода может открыться в модификации α - Fе, причем крепкие растворы углерода и прочих элементов в модификации α - Fе называют ферритом.
Химический состав и свойства высокопрочных чугунов регламентируются ГОСТ 7293 - 85 и маркируются буквами « В » - - высокопрочный, « Ч » - - чугун и количеством, означающим обыкновенное значение предела прочности чугуна при растяжении.Например, ВЧ 100 - - высокопрочный чугун, лимит крепости при растяжении 1000 МПа ( или 100 кг/мм 2 ).
spravconstr.ru
Содержание углерода в чугунах составляет
В технике под металлом понимают вещества, обладающие « металлическим блеском », в той или другой степени свойственным всем металлам, и пластичностью.По этому знаку металлы можно легко отличить от неметаллов ( например, деревца, камешка, стекла или фарфора ).« Металлы суть ясные тела, которые ковать можно ».Это определение металлов, данное М.В. Ломоносовым, не утеряло собственного научного значения и сейчас, через 200 лет.В. Ломоносов отметил и другой особенность сих тел — сходство их строения с солями, т. е. кристалличность.В XIX в.была сделана научная теория строения фигур, согласно которой все крепкие тела делятся на две группки : кристаллические и бесформенные.
Ковкий чугун получают длительным отжигом белого чугуна, в итоге которого образуется графит хлопьевидной формы.Металлическая основа такого чугуна : феррит и реже перлит.Ковкий чугун получил свое название из - за повышенной пластичности и вязкости ( при всем при том, что обработке давлением не подвергается ).Ковкий чугун обладает повышенной крепостью при растяжении и рослым сопротивлением удару.Из ковкого чугуна изготовляют детали непростой фигуры : картеры заднего моста машин, тормозные колодки, тройники, угольники и т. д.
Легирующие элементы изменяют как машинальные, так и материальные свойства стали.Так, например, хром увеличивает крепость, твердость и износостойкость стали, но снижает ее пластичность 2 ;никель повышает прочность, твердость и сопротивление коррозии ;вольфрам повышает твердость.Однако при выборе легированных сталей надо располагать в облику и экономические соображения.Известно, что марганец, кремний и хром удорожают сталь незначительно, а никель повышает ее стоимость заметно.При добавлении кобальта, вольфрама и молибдена сталь становится дорогой.
Включая небольшое сопротивление отливок из серого чугуна растягивающим и ударным нагрузкам, следует использовать сей материал для подробностей, которые подвергаются сжимающим или изгибающим нагрузкам.В станкостроении это – базовые, корпусные детали, кронштейны, зубчатые колеса, ведущие ;в автостроении - блоки цилиндров, поршневые кольца, распределительные валы, диски сцепления.Отливки из серого чугуна также используются в электромашиностроении, для изготовления товаров народного потребления.
В новые возрасты все большее распространение получают безмуфельные печи с радиационными трубами, в которых происходит сжигание газа.Стенки радиационных труб нагреваются до высокой температуры и подобно нагревателям в электрических печах являются источником излучения тепла.Диаметр трубы – 80 – 90 мм, толщина стенок – 4–6 мм.Трубы производят из жаропрочной стали.Через край трубы дают газ и дух.Продукты горения отводятся в вытяжные трубы.Замена муфелей радиационными трубами позволяет сэкономить дорогостоящую жароупорную сталь.
Углерод в чугуне может находиться в виде цементита, графита или в то же самое время в виде цементита и графита.Возникновение постоянной фазы - графита в чугуне может происходить в итоге прямого выделения его из слабого ( твердого ) раствора или вследствие распада предварительно образовавшегося цементита ( при замедленном охлаждении расплавленного чугуна цементит может подвергнуться разложению РезС - > Fe + ЗС с образованием феррита и графита ).Процесс формирования в чугуне ( стали ) графита называют графитизацией.
Сварка стальными электродами с применением особых покрытий.В этом случае применяют электроды из проволоки Св - 08 или Св - 08А со специальными покрытиями.Значительную роль в покрытии играет ферросилиций, который помогает обрести серый чугун.Сей способ используется для сварки изделий легкой фигуры, служащих при ничтожных нагрузках.При точном и скрупулезном выполнении сварки можно добиться получения плотного сварного соединения, поддающегося механической обработке.
2 ) Другой группу Б.чугуна составляет : а ) чугун так именуемого мокрого прохода.Обстоятельства его приобретения будут видимы при описании доменной плавки ( см.Домна ) ;тут же довольно упомянуть, что Б., который нельзя отменить углеродом, полученный из чистых руд, представляет самый удобный материал для пудлингового передела.К этой же группе принадлежит также б ) Б.чугун с небольшим содержанием углерода, извлеченный из настоящих, но нелегко восстановимых и трудноплавких руд при спелом ходе домны ;такой чугун, особливо же ближайший к третному жесткому ( изгиб белый с темными крапинками ) есть наилучший материал для изготовления изделий так называемого ковкого чугуна ( см.Чугун ).Содержание углерода в чугунах этой группы не превосходит 3%, количество же кремния всегда ниже, чем у чугунов серых и не часто достигает до 0, 4%.
Также следует отметить электроды марки ЭМЧС, стержень которых заключается из низкоуглеродистой проволоки, а покрытие – из трёх слоёв : 1-й слой является легирующим, 2-й шлако - и газообразующим, 3-й – газозащитным.Применение этих электродов при сварке чугунных изделий с относительно небольшой толщиной свариваемого металла ( 8 - 10мм ) позволяет обрести качественные сварные соединения без предварительного подогрева.При сварке изделий большей толщины первые слои выполняют электродами ЦЧ - 4, а последующие – электродами УОНИ - 13/45.
Высокопрочные чугуны ( ГОСТ 7293 ) могут иметь ферритную ( ВЧ 35 ), феррито - перлитную ( ВЧ45 ) и перлитную ( ВЧ 80 ) металлическую основу.Зарабатывают эти чугуны из бесцветных, в результате модифицирования магнием или церием ( добавляется 0, 03…0, 07% от массы отливки ).По сравнению с серыми чугунами, механические свойства повышаются, это порождено отсутствием неравномерности в распределении усилий из - за шаровой формы графита.
spravconstr.ru
Способ определения содержания углерода в чугунах
Изобретение может быть использовано в области литейного производства для определения содержания углерода по ходу плавки. Сущность: отливают технологическую пробу без выделений графита, подвергают ее графитизирующему отжигу при 940 - 1120°С, измеряют величину удлинения пробы и по ней определяют содержание углерода в чугуне. Для ускорения отжига в жидкий чугун, предназначенный для отливки технологической пробы, вводят добавку, содержащую графитизирующие элементы. 1 з.п. ф-лы.
Изобретение относится к литейному производству и может быть использовано для определения содержания углерода в чугунах преимущественно по ходу плавки.
Содержание углерода в чугунах является одним из основных факторов, оказывающих влияние на литейные и механические свойства. Поэтому контроль углерода в чугунах по ходу плавки и корректировка его содержания имеют большое значение. Для получения заданной марки чугуна достаточно обеспечить требуемое содержание углерода, а содержание других элементов, в частности кремния, можно корректировать по величине отбела технологической пробы на отбел. Для определения содержания углерода применяют различные методы. Широкое применение нашли химико-аналитические методы. Основу их составляет сжигание навески чугунной стружки на лодочке в трубчатой печи с помощью прибора АН-7529. Сжигание производят в потоке кислорода, что значительно ускоряет процесс. Однако образующийся СO2 поглощается раствором, находящимся в электрической ячейке, что изменяет ЭДС индикаторной системы рНметра. Общее время анализа от момента заливки пробы до получения готового результата составляет, как правило, не менее 10 мин. Анализ проводят в отдельном помещении специальные лаборанты. По этим причинам метод находит ограниченное применение для контроля по ходу плавки и корректировки состава чугуна по углероду. Некоторые предприятия используют термографический метод определения содержания углерода по кривой охлаждения чугуна, на которой фиксируются температуры ликвидуса и солидуса. В стержневую пробницу разового пользования заливается чугун, температура которого непрерывно измеряется при помощи малоинерционной термопары. Кривая охлаждения записывается на диаграммной ленте потенциометра. По расположению перегибов в критических точках (солидуса и ликвидуса) определяют содержание углерода и кремния. Продолжительность анализа приблизительно 3 мин. Достоинство метода в том, что измерение осуществляет плавильщик непосредственно у плавильной печи. Недостатками метода являются необходимость изготавливать специальные пробницы с термопарами (как правило разового пользования), а также высокие требования к точности приборов и термопар. Широко применяются для определения содержания углерода и других элементов спектральные методы. Современные многоканальные квантометры зарубежные и отечественные (ДФС-51, ДФС-61) позволяют определить содержание углерода и ряда других элементов в пределах минуты, без учета времени на подготовку пробы: заливку, охлаждение, транспортировку и шлифовку. Необходимым условием для определения содержания углерода спектральным методом является получение технологической пробы без выделений графита, т. е. весь углерод должен быть в связанном состоянии. Недостатки метода заключаются в использовании сложных и дорогих приборов, хорошо оборудованных помещений, квалифицированного обслуживания, а также необходимых дорогостоящих и обычно дефицитных эталонов. Поэтому этот метод целесообразно применять в условиях поточно-массового производства. Цель изобретения состоит в определении углерода непосредственно у плавильного агрегата, в исключении сложного, дорогостоящего оборудования и эталонов и специального обслуживающего персонала. Способ определения содержания углерода, включающий отливку технологической пробы без выделений графита, осуществляют по величине удлинения пробы, подвергнутой графитизирующему отжигу. В способе, принятом за прототип, после отливки пробы без выделений графита ее транспортируют в помещение, где расположены спектральные приборы, например квантометр, шлифуют поверхность и определяют содержание углерода и других элементов по спектру. В предлагаемом изобретении после отливки технологической пробы без выделений графита ее охлаждают до температуры окружающей среды, измеряют (или фиксируют) длину, проводят ее графитизирующий отжиг, охлаждают до температуры окружающей среды и измеряют длину (или удлинение). По величине удлинения определяют содержание углерода. В отлитой пробе весь углерод находится в связанном состоянии. После графитизирующего отжига проба состоит из металлической основы и графита. Выделение углерода в виде графита вызывает увеличение объема пробы. Удлинение пробы тем больше, чем выше содержание углерода в чугуне. Скорость охлаждения технологической пробы при ее затвердевании должна быть такой, чтобы при любом составе чугуна исключить выделение графита. Этому условию удовлетворяет затвердевание пробы в металлической форме, в частности медной. Оптимальная температура графитизирующего отжига 940-1120оС. Температура ниже 940оС значительно удлиняет процесс графитизации, а выше 1120оС приводит к деформации образца и его плавлению. Увеличение температуры на 10оС почти в два раза повышает скорость графитизации и сокращает время распада цементия в 1,25 раза. Оптимальная длина технологической пробы 50-120 мм. Меньшая длина существенно увеличивает относительную погрешность измерений длины, а большая затрудняет получение пробы. Оптимальное сечение (диаметр) пробы - 2-5 мм. Меньшее сечение ее сокращает время графитизации, но затрудняет процесс получения пробы. Большее сечение облегчает этот процесс, но увеличивает время графитизации и вероятность выделения графита при затвердевании пробы. Для чугунов с низким содержанием элементов, ускоряющих графитизацию (например, кремния), и высоким содержанием элементов, замедляющих графитизацию (например, марганца и хрома), в жидкий чугун, предназначенный для заливки технологической пробы, следует вводить добавку. В качестве основы такой добавки можно рекомендовать графитизирующий модификатор, например ферросилиций марки ФС75, в количестве 0,3-0,8% от веса чугуна в пробоотборнике. Графитизирующий модификатор сокращает время и/или температуру графитизирующего отжига. П р и м е р 1. С помощью пробоотборника заливают чугун в медную форму с плотностью диаметром 4 мм и длиной 100 мм для технологической пробы. Через 20 ч после заливки пробу извлекают из формы и охлаждают в воде до температуры окружающей среды. Длина пробы, измеренной микрометром равна 98,05 мм. Помещают пробу в лабораторную печь с 1080оС, выдерживают ее 4 мин, охлаждают в воде до температуры окружающей среды. Снова измеряют длину пробы. Она равна 100,35 мм. Удлинение составляет 2,30 мм (2,36%). По графику, построенному на основе экспериментальных данных, в осях: удлинение пробы (%) и содержание углерода (%), определяют содержание углерода 3,49%. Общее время от заливки образца до получения результата составляет 5 мин. Химический анализ показывает содержание углерода в чугуне 3,51%. П р и м е р 2. В пробоотборник помещают стабилизирущую добавку (0,5% ФС75 от веса металла в пробоотборнике). Пробоотборник заполняют чугуном, затем заливают его в медную форму с полостью диаметром 4 мм и длиной 50 мм для технологической пробы. Через 20 с пробу извлекают из формы, охлаждают в воде до температуры окружающей среды, устанавливают измерительное приспособление и фиксируют ее длину. Помещают пробу в лабораторную печь с 1040оС, выдерживают 3 мин и охлаждают в воде до температуры окружающей среды. Снова устанавливают пробу в измерительное приспособление и определяют удлинение 0,534 мм (1,09% ). По графику определяют содержание углерода 2,69%. Общее время от заливки образца до получения результата составляет 4,5 мин. Химический анализ показывает содержание углерода в чугуне 2,67%. Предлагаемый способ позволяет плавильщику определять содержание углерода непосредственно у плавильного агрегата по ходу плавки, не требует дорогостоящих приборов и оборудования, специального персонала. Способ прост, надежен и обеспечивает достаточную для практики производства чугунных отливок точность
Формула изобретения
1. СПОСОБ ОПРЕДЕЛЕНИЯ СОДЕРЖАНИЯ УГЛЕРОДА В ЧУГУНАХ преимущественно по ходу плавки, включающий отливку технологической пробы без выделений графита, отличающийся тем, что пробу подвергают графитизирующему отжигу при 940 - 1120oС и по величине удлинения пробы определяют содержание углерода. 2. Способ по п.1, отличающийся тем, что при отливке технологической пробы в нее вводят добавку, содержащую графитизирующие элементы.www.findpatent.ru