Способ термитной сварки рельсов. Термитная сварка рельс
Термитная сварка рельс на ЖД и проводов по ГОСТу: технология
Термитная сварка – это один из многочисленных способов варки. В этом процессе металлические изделия нагреваются с помощью термита. Он включает в себя смесь, состоящую из магния или же опилок алюминия (23%) с добавлением железной окалины (окись железа 77%). Соединение заготовок с использованием взрывоопасной смеси делится на способ плавления и литья. Виды термитной сварки могут использоваться отдельно и в комплексе.

Процесс термитной сварки
Возможность применения данного способа 
Этот способ соединения различных металлических частей наибольшее распространение получил на железной дороге. Термитная сварка, которую ещё называют алюминетермитной, применяется для стыковки рельсов.

Процесс термитной сварки рельс на ЖД
Обычно, для производства работ задействуют бригады, состоящие из двух или трёх человек. Термитная сварка рельс на железной дороге предполагает использование специального оборудования, вес которого варьируется в пределах 350-400 килограмм. Для проведения работ, о которых идёт речь, необходимы автономные источники электрической энергии.
Кроме того, её активно используют при сварке чугуна. Она востребована для обработки телефонных и электрических коммуникаций. С помощью данного метода можно работать с трубами и отдельными частями силовых агрегатов.
Термитная сварка проводов используется для оконцевания, соединения жил сечений различного диаметра. Речь идёт о проводах изготовленных из алюминия. Этот метод соединения подходит для работы с медными жилами до 10 мм2.
Использование карандаша 
Карандаш – это кусочек обыкновенной проволоки из углеродистой стали. В диаметре 2-3 мм и размерами частиц в пределах 0,5 мм. В состав входит: 24% опилок алюминия, 76% окалины железа. Сварка термитным карандашом возможна в домашних условиях: на даче или загородном доме при выполнении несложных, в техническом плане, мероприятий.
Помните, что тушение пожара при воспламенении от шашек, либо патронов возможно с использованием песка. Тушение водой недопустимо!
Термитные шашки для сварки выпускаются двух видов:
- для соединения кабеля и изолированных проводов с медными жилами: ПА;
- для производства работ с алюминиевыми и сталь/алюминиевыми проводами.
Шашка состоит: из кокиля и термитной массы.
«Важно!
Не допускается хранение патронов и спичек в одном месте и единой упаковке.»

Термитные шашки для сварки
Для сварки проводов термитными патронами подходят соединения диаметром 5-32 миллиметра. Патрон включает в себя: кокиль, вкладыш и термитную массу.
Преимущества и недостатки 
Термитная сварка обладает рядом преимуществ. К примеру, термитная сварка рельсов не предполагает использование дорогого или специального оборудования по сравнению с контактным способом. Нет необходимости задействовать большое количество рабочей силы. Следовательно, этот способ обработки рельсовых стыков и стрелочных переводов предполагает экономию бюджетных средств.
«На заметку!
Для обработки только 1 рельсового стыка бригаде из 2-3 человек понадобится менее часа, всего 50 минут рабочего времени.»
Три бригады за 120 минут способны изготовить от 10 до 12 рельсовых стыков. Кроме этого:
- Термитная сварка создаёт крепкое соединение отдельных частей. Обладает высокой стойкостью к разрушению.
- Технология термитной сварки проста и доступна. Она одинаково эффективна на промышленном производстве и бытовых целях.
- Специалисты утверждают, а практики подтверждают, что использование этого метода — наиболее приемлемый вариант при ликвидации аварий и нестандартных ситуаций.
- Качественное, получаемое при термитной сварки, соединение.

Шов после термитной сварки
Термитная сварка имеет свои недостатки. К ним можно отнести:
- Высокое поглощение влаги.
- Взрывоопасный способ ведения работ. Так, попадание воды на шашку, вызовет взрыв.
- Неконтролируемый процесс горения.
Но, несмотря на свои недостатки – это один из действенных способов надёжного соединения рабочих деталей.
Схема процесса термитной сварки

Схема термитной сварки рельс
Видео с процессом термитной сварки рельс на железной дороге 
Оборудование, которое используется для термитного метода соединения рельс 
Для проведения работ необходимо подготовить соответствующее оборудование такое как:
- Тигель, изготовленный из вольфрама или керамики. Условие использования: должна быть плавящаяся заглушка. А также тигель, обустроенный для слива жидко металла в форму.
- Для работы понадобится пресс для сжигания форм, оставшихся после заливки металла.
- Отливочные формы, с помощью которых расплавленный металл приобретает законченный продукт: форму рельс.
- Для процесса потребуется подставка для тигля. А также горелка и термометр.
Также, необходимо подготовить дополнительный инструмент: кувалду, зубило, шлиф/машинку с кругами. И использовать спец/одежду о необходимости, которой говорится далее.
Техника безопасности при выполнении работ 
Из-за способности воспламеняться термитная сварка относится к категории пожароопасного производства. Следовательно, к ТБ предъявляются жёсткие меры. Рабочий объект должен быть оборудован рабочим инвентарём и находиться в исправном состоянии.
Термитная сварка подразумевает получение допуска к работе лиц, достигших 18 лет, прошедших специальное обучение.
Перед началом производственного процесса обязательным условие считается подготовка рабочего места, организация труда. А также проведение устного инструктажа с рабочими бригадами.
Результат инструктажа о ТБ заносится в рабочий журнал под подпись каждого участника.
Важным аспектом безопасности считается применение специальных средств индивидуальной защиты: термостойкой одежды, рукавиц, защитных очков для глаз.
«Важно!
Термит складируется в отдельном помещении. Накопительный склад должен находиться на расстоянии не менее 30 метров от жилых зданий и производственных помещений.»
ГОСТ термитной сварки Р 57181-2016 определяет порядок проведения работ и технологический процесс использования взрывоопасного продукта.
Не рекомендуется использование данного метода обработки при низких t0, а также при дождливой погоде. Доставка взрывоопасного материала и огнеупоров осуществляется транспортом с крытым кузовом, который должен быть заранее подготовлен: чистый и сухой.
Заключение 
Термитная сварка процесс неновый. Он используется уже на протяжении последних 50 лет. Несмотря на это процесс актуален для широкого применения в металлургической отрасли и других направлениях хозяйствования.
Из вышесказанного можно сделать вывод, что термитная сварка процесс узко/профильный и специфичный. Основным условием работ является безопасность.
Это использование противопожарных средств защиты и соблюдение рекомендаций с учётом ГОСТ и отдельных положений, утверждённых на уровне министерств и ведомств.
Существует множество материала и технической литературы на тему, как осуществляется термитная сварка. В интернете всегда есть обучающие и ознакомительные ролики.
алюминотермитная сварка рельсовых стыков
Сварка рельсовых стыков — очень ответственная и непростая задача. Материал полотна содержит большое количество углерода, что относит его к разряду трудносвариваемых металлов. Это проявляется в образовании трещин на шве, которые способствуют разрушению соединения. Дополнительно, концентрация напряжения на материале специфичной формы усложняет процесс создания прочного стыка. Вместо электродугового ручного метода была разработана альтернатива — алюминотермитная сварка рельсов. В чем ее суть и как это работает?
Основное предназначение метода
Рельсы — это сложная конструкция, обеспечивающая движение многотонных поездов на большой скорости. Для бесперебойного прохождения тяжелых составов требуется целостность дорожного полотна. Поэтому все рельсы нужно соединять между собой. Шпалы обеспечивают определенную амортизацию и устойчивость линии без просадок. Но плохо сваренные стыки могут причинить серьезный вред всей конструкции и проходящим поездам.
Сам процесс наложения шва на рельсовое полотно довольно проблематичен. Дуговая сварка не способна проплавить такую толщину без большого скоса кромок. Если производить глубокую разделку на торцах, то сваривание сторон займет много времени. Газовая сварка вообще не рассчитана на такую толщину металла. Еще одна сложность заключается в том, что если материал шва окажется недостаточно твердым, то произойдет смещение центрации и просадка одной из сторон стыка. Колесо движущегося состава, каждый раз проходя по этому месту, будет биться о выступающий борт. Постоянные удары в торец рельса приводят к быстрому разрушению полотна, остановке движения, и частым ремонтным работам.
Для самих поездов плохие стыки чреваты вредом для подвижной части. При регулярных ударах колесной пары о выступы начинают образовываться сколы на поверхности головок и их последующее сминание. Повышается вибрация при движении, а потеря баланса приводит к дальнейшему разрушению рельсов и ходовой части.
Если материал шва будет чрезмерно твердым, то постоянные нагрузки при многотонных поездах и внутреннее напряжение посодействуют самопроизвольному распаду металла соединения. Чтобы решить задачу по сварке рельсов, было проведено множество опытов. Бекетов Н.Н. выявил процесс, названный алюминотермия. Он позволяет качественно соединять рельсовые пути, с должной прочностью и необходимой вязкостью шва, обеспечивая движения тяжелых составов без просадок и трещин.
Описание алюминотермитной сварки
Чтобы соединения рельсов между собой было качественным, используется алюминотермитная сварка. Суть метода заключается в плавлении специального порошка, который засыпается между свариваемыми сторонами полотна. Он прочно связывает основной материал и делает структуру шва повышенной вязкости и сопротивлению на разрыв. Такие стыки рельсов не проседают со временем и выполняются за короткий срок.
В состав порошка входит два компонента: 23% алюминиевой крошки (откуда и взято название метода), и 77% оксида железа. Порошок имеет мелкодисперсную структуру, и максимальная величина гранул составляет 0,5 мм. Метод основан на способности металла к восстановлению в окислах алюминия. Но это возможно при очень высокой температуре. Поэтому используется запал, который поджигает смесь. Гранулы воспламеняются и температура доходит до 3000 градусов. Благодаря этому оксид железа способен преобразоваться в чистый металл.
На месте применяется заливочная форма, обеспечивающая попадание сплава в зону стыка. Важно создать герметичную конструкцию, поэтому были разработаны формы под разные конфигурации рельс. Остаточные щели заделываются термостойкой обмазкой. Жидкий состав затекает в место соединения, полностью заполняя свободное пространство. В процессе образовывается шлак, который являясь самым легким, всплывает на поверхности.
Рельсовый стык, будучи еще в горячем состоянии, нуждается в уплотнении, для усадки материала. Поэтому на месте работ используются прессы. После создания соединения убираются все приспособления и отбивается шлак молотком. Шов имеет грубые наплывы, поэтому нуждается в обработке шлифовальной машиной и болгаркой в труднодоступных местах.
Преимущества и недостатки
У алюминотермитной сварки рельсов существует несколько основных преимуществ:
- Создание шва на рельсовом полотне занимает около 30 минут (со всеми подготовительными работами). Причем бригада может за 50 минут наложить около 12 швов. Это достигается за счет конвейеризации процесса: один рабочий выставляет рельсы и переходит на следующее место, второй устанавливает форму и создает стык, третий обрабатывает поверхность.
- Основные комплектующие для алюминотермитной сварки можно купить в магазинах. Смесь продается в специальных бочках.
- Процесс сварки относительно не сложен, и достаточно нескольких тренировок на практике, чтобы рабочий научился самостоятельно выполнять сварку.
- Экономия электроэнергии, которая необходима только для запитки шлифовального оборудования.
- Высокое качество шва, способное выдерживать большие нагрузки.
- Возможность проводить сварочные работы вдали от населенных пунктов в полевых условиях.
Но у алюминотермитной сварки существуют и недостатки. Порошок относится к разряду легковоспламеняющихся средств, и требует осторожного обращения. Если в него случайно попал огонь, то потушить состав уже не возможно и расплавленный металл протечет в неподходящем месте, что приведет к ненужному расходу материала, и возможно, к пожару. Если в горящую емкость попадет вода, то это спровоцирует взрыв и разбрызгивание расплавленного материала. Для качественного соединения требуется предварительный подогрев сторон рельс пламенем горелки. Поэтому, несмотря на простоту самой сварки, подготовка и последующая обработка стыка требуют наличия баллонов и электричества.
Оборудование для сварки
Чтобы реализовать на месте сварку алюминотермитным методом потребуется следующее оборудование и материалы:
- бочка с порошком и специальной заглушкой;
- отливочная форма, соответствующая конструкции рельса;
- в случае использования не бочки, а развесного порошка — тигель для засыпки состава и подставка под него;
- обмазочная паста для герметизации стыка;
- пресс для последующего уплотнения;
- шлифовальная машинка;
- молоток и зубило;
- металлическая лопатка для забора горящего шлака из карманов приспособления;
- горелка для предварительного подогрева (операцию можно провести и без нее, но с худшим результатом качества).
Поэтапное выполнение
Технология создания сварного шва на рельсовом полотне реализовывается в определенной последовательности. Сперва, снимаются ближайшие крепления на шпалах, и ослабляются дальние зажимы. Это позволит свободно установить стороны и убрать возможное напряжение в металле. Выставляются торцы рельс так, чтобы они находились на одинаковом уровне относительно друг друга со всех сторон. Перепады приведут к перегрузке на этом участке и быстрому разрушению. Между сторонами оставляется зазор в 25 мм для полноценного затекания расплавленного материала. Чтобы сохранить размер зазора при регулировочных движениях торцов, закладываются пластины соответствующей толщины.
Происходит фиксация полотна захватами или струбцинами, чтобы сохранить уровень и ровность линии. Накладывается форма, точно соответствующая изгибам по боковому рельефу рельс. Оставшиеся щели замазываются огнеупорной пастой. На стык устанавливается подставка с воронкой, сверху которой помещается емкость с порошком. Если он в развесном виде, то необходим тигель.
Алюминотермитная смесь поджигается специальным запалом, после чего расплавляется нижняя заглушка, и состав вытекает в форму. Заполняется соединение, после чего разбирается форма и отбивается шлак. Стык обрабатывается прессом для усадки и начинается шлифовальный процесс. Его обязательно провести на поверхности рельсового полотна соприкасаемого с ходовой частью поезда.
Сварка с применением алюминотермитного порошка позволяет прочно соединять рельсы. Это сохраняет целостность путей и колес подвижного состава. Она используется и на других видах стали, даже на соединении проводов. Простота применения и доступность материалов делают его удобным сварочным методом.
Поделись с друзьями
0
0
2
0
svarkalegko.com
Термитная сварка рельсов » Demidovo52.Ru
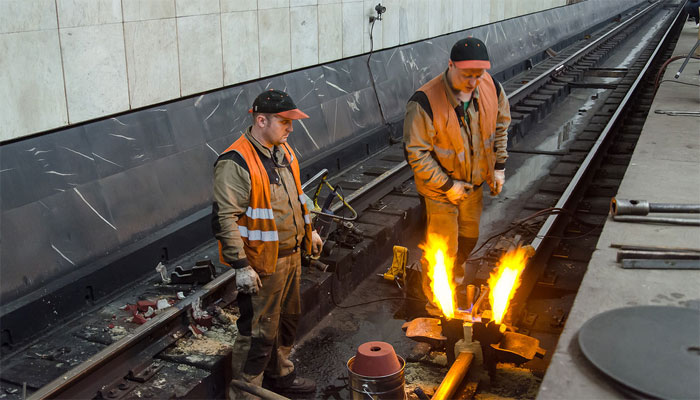
Многим известен такой вид сварки, как электродуговая и газовая. Они широко применяются как на производстве, так и в строительстве. Но термитная сварка мало кому известна. Поэтому речь пойдет о ней. Благодаря использованию термитной сварки, получаются, ничем не хуже по качеству соединения, как при электро или газосварке, притом не требуется источник электропитания или газовые баллоны.
Сферы применения
Термитную сварку на сегодняшний день используют для сваривания чугуна, электрических и телефонных коммуникаций, труб, частей двигателя и так далее. Особо часто термит используют для сваривания железнодорожных рельсов. Соединения получаются достаточно надёжные. Место ремонта может быть на любом участке дороги, даже в несколько сот километров от населенного пункта.
Термитная сварка
Появление термитной сварки было обусловлено необходимостью стыкового соединения металлов без использования громоздкого оборудования и наличия электросети. Поэтому в 1859 г. Бекетов Н. Н. обнаружил способ, в основе которого лежит алюминотермия ― процесс получения металла восстановлением их окислов алюминия. Он определил, что смесь порошка алюминия и оксида железа, горя при 3000° C, превращаются в сталь и шлак.
В 1898 г. исследователь из Германии Гольдшмидт, впервые применил термитную сварку на практике, соединив два железных бруска. Сделал он это, образовав форму вокруг места стыка и засыпав его термитным порошком. Сгорев, термитный порошок превратился в расплавленное железо, соединив таким образом два металлических бруска. При этом шлак всплывал на поверхность и мог свободно отделиться.
С того времени состав термита практически не изменился. Чаще всего термит имеет в своём составе опилки алюминия ― 23%, и окись железа― 77%. Фракция порошка составляет ― 0,5 мм. В момент поджига порошка, возникает химическая реакция, благодаря которой выделяется много тепла. Плавясь, окись железа переходит в чистое железо, а расплавленный алюминий окисляется.
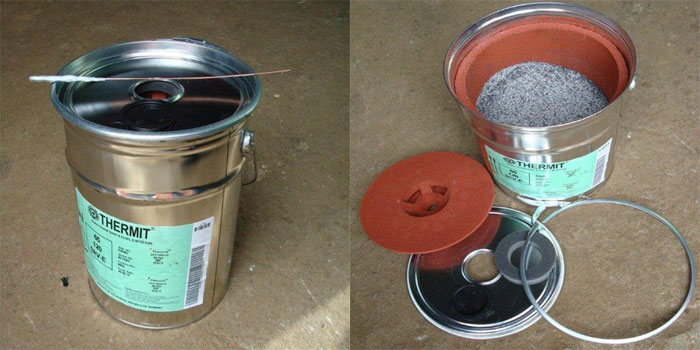
Термитная сварка рельсов
Процесс сваривания рельсов термитом заключается в следующем:
- обрезка рельс с двух сторон, чтобы промежуток между ними был 23 ― 25 мм. Притом они должны быть выставлены горизонтально и вертикально;
- в зазор между рельсами вставляется пластина из углеродистой стали, для образования зазора;
- стык рельсов зажимается прессом;
- на место соединения монтируется огнеупорная форма, а стыки формы с рельсами, засыпаются песком, или замазываются специальной пастой;
- поверх форм прикрепляется тигель (конус в виде лейки из огнеупорного материала) в котором первоначально сжигается термит. Расплавленный жидкий металл полученный в тигле, в последствии выливают в форму на стыке рельс;
- термит в тигле поджигается термитным карандашом, после чего происходит горение основной смеси 20 ― 30 секунд;
- снизу в воронке тигля установлена заглушка, которая расправляется и освобождает проход жидкому металлу в форму. Сталь и шлак заполняя форму, образуют соединительный шов, притом шлак частично вытесняется наружу в специальные чаши, прикрепленные сбоку тигля;
- горячая сталь заливаемая в форму, проплавляет торцы рельс. После, убирается тигель, и форма сжимается прессом;
- форму снимают, и пока металл ещё горячий, удаляют его избыток;
- получившийся шов, тщательно шлифуют до образования однородной плоскости с рельсой.
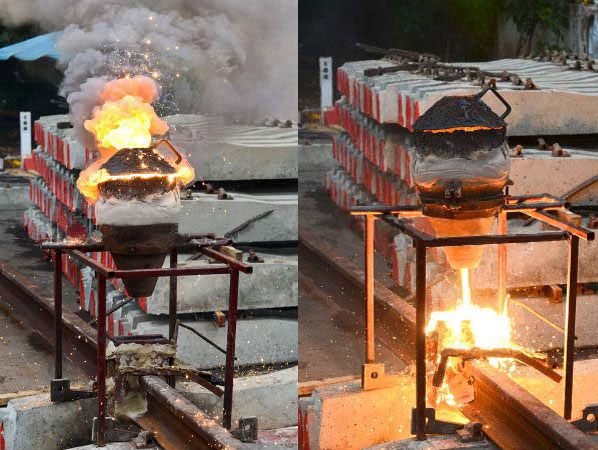
Термитные карандаши
В продаже можно найти термитные карандаши. Это кусок проволоки состоящей из углеродистой стали, диаметром до 5 мм. На неё наносят термитную смесь перемешанную с клеем. С одной стороны карандаша имеется место для запала. Что-то вроде бертолетового шнура, но нанесенного в виде дорожки на сам карандаш. Карандаш вставляют в держатель ― как для электросварки, ― и поджигают верхнюю часть. Когда огонь доходит до основного состава на другом конце карандаша, происходит запал термита. Сварку необходимо производить с защитным щитком и рукавицами. Этот же карандаш применяется для поджига основной смеси в тигле. Его поджигают и бросают в тигель с термитной смесью.
Кроме карандашей, существуют ещё термитные шашки и патроны. По принципу работы они схожи с термитным карандашом.
Достоинства термитной сварки
- крепкое и надежное сварочное соединение с высокой стойкостью к разрушению;
- технология сварки отличается простотой и доступностью, что предполагает ее использование как в промышленности, так и в быту;
- самый оптимальный вариант сварки при аварийных ситуациях.
Недостатки
- высокое поглощение влаги;
- смесь из-за способности воспламенятся, считается пожароопасной, что требует бережного отношения и хранения;
- попадание влаги на термитную шашку приводит к образованию взрыва;
- неспособность контролировать процесс горения термита.
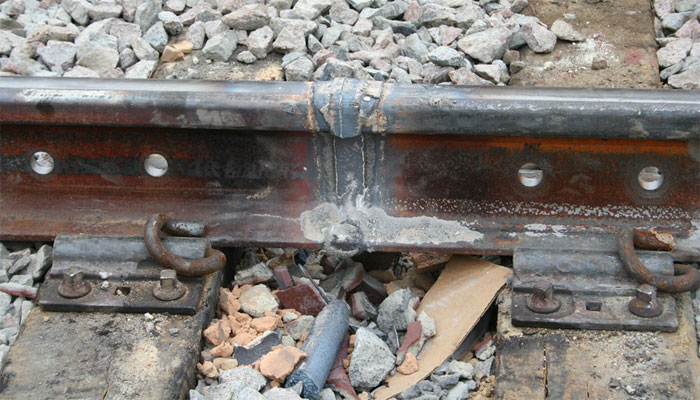
Оборудование для термитной сварки рельс
- вольфрамовый или керамический тигель с плавящейся заглушкой, и приспособленный для слива жидкого металла в форму;
- отливочные формы для придания расплавленному металлу формы рельсов;
- пресс для сжатия форм после заливки металла;
- дополнительное оборудование: подставка для тигля, термометр, горелка;
- дополнительные материалы и инструменты: болгарка, шлифовальные круги, кувалда, зубило, металлическая щётка, термостойкая одежда, рукавицы, защитные очки для глаз и другое.
Все это обеспечит качественную работу и защитит персонал от разрушительного воздействия тепла и грязи получаемых при сгорании термосмеси.
Условия для сварки рельс термитом
Чтобы соединение при процессе сварки получилось качественным и крепким, необходимо соблюдать следующие условия:
- количество порошка термита необходимо просчитать столько, сколько нужно для заполнения металлом формы вокруг рельса;
- важно, чтобы смесь шихты была тщательно измельчена и перемешана;
- температура горения зажигательного элемента (шашка, карандаш), как катализатора поджига основной смеси, должна быть не менее 1400° C.
demidovo52.ru
Термитная сварка крупногабаритных деталей | Сварка и сварщик
При эксплуатации в металлургической промышленности прокатного, кузнечнопрессового и другого оборудования, испытывающего большие динамические нагрузки и выдерживающего высокие температуры, происходят разрушение крупных деталей и выход из строя станин прокатных станов, прессов и ковочно-высадочных машин. Термитная сварка позволяет восстанавливать разрушенные детали. При этом необходимо обеспечить минимальную деформацию восстанавливаемого узла. Если, например, прямоугольная замкнутая рама разрушена с одного конца, то необходимо производить предварительный подогрев не только места сварки, но и противоположной стороны, чтобы компенсировать температурные деформации при сварке.
Нагрев противоположной стороны необходимо продолжить и после сварки до тех пор, пока сваренная часть несколько охладиться, а температура противоположных сторон рамы выровняется.
В технической литературе освещено применение термитной сварки при:
а) производстве крупногабаритных деталей, состоящих из нескольких элементов: коленчатых валов, рулевых рам судов, приварке лопастей к гребным валам судов и пр.;
б) восстановлении цилиндров прессов, поршневых штоков, колонн кузнечных прессов, роторных валов, валков, а также ведущих реверсивных шестерен прокатных станов, всевозможных станин-клетей прокатных станов, станин прессов и главных станин ковочно-высадочных машин и пр.;
в) ремонте чугунного технологического оборудования сталелитейных цехов: изложниц, шлаковых ковшей, поддонов и т. д.
Термитную сварку крупногабаритных деталей лучше всего производить в литейном цехе, где имеется необходимое технологическое оборудование, а также грузоподъемные механизмы.
Летом в сухую погоду термитную сварку можно производить и под открытым небом - на монтажной площадке, удаленной от огнеопасных объектов.
Перед сваркой крупногабаритной детали следует сделать химический анализ на содержание в металле основных примесей. На основании полученных данных определяют, какими элементами нужно легировать термитную сталь, и производят расчет количества легирующих элементов и стального наполнителя для введения в термитную шихту. Необходимо также рассчитать количество термитной шихты для сварки данной детали. Для этого подсчитывают объемы всей сварочной зоны, литниковой и выпорной систем, а также прибыльной части.
Перед сваркой обрезают газом поверхности, которые будут свариваться, а затем зачищают их. После этого фиксируют взаимное положение частей, подлежащих сварке. Свариваемые элементы прихватываются электросваркой по зазору при помощи технологических перемычек. После прихватки одна из свариваемых частей должна быть раскреплена для свободного перемещения от температурного воздействия.
Термитная сварка деталей из серого чугуна
Термитная сварка крупных чугунных деталей дает большой экономический эффект, особенно для восстановления технологического оборудования металлургического производства: различных ковшей, изложении, поддонов, а также всевозможных станин.
Приступая к термитной сварке чугунных деталей, нужно учитывать повышенную чувствительность чугуна к температурным изменениям. При нагревании чугуна выше критической точки и охлаждении со скоростью, превышающей 149^ в мин., он становится хрупким.
В процессе сварки в зоне, прилегающей к термитному металлу, чугун разогревается выше критической точки. Чтобы ликвидировать отрицательное влияние температуры на эту зону, необходимо уменьшать скорость ее охлаждения за счет предварительного нагрева смежных участков.
Одним из важнейших условий успешного проведения термитной сварки чугунных деталей является предварительный подогрев. При сварке чугунных деталей, помимо местного подогрева в зоне сварки до 900 , необходимо произвести и общий подогрев всей детали до 450-500°.
Сваривая жесткие конструкции типа чугунных замкнутых рам, нужно предотвращать появление в них напряжений, которые могут привести к разрушению детали. Для этого с успехом применяют общий компенсационный подогрев.
Усадка термитного металла почти в два раза превышает усадку чугуна; при слишком большом отношении длины свариваемого сечения к толщине могут образоваться поперечные трещины - поэтому термитную сварку чугунных деталей целесообразно применять лишь тогда, когда ширина деталей превосходит ее толщину не более чем в восемь раз.
Если в относительно тонкой детали имеются длинные трещины, ее целесообразно разделить по оси трещины на две части и произвести сварку всего сечения. Узкие трещины нужно расширить и несколько удлинить. Это необходимо для качественного провара.
При сварке удлиненных стыков их по возможности следует располагать в вертикальном положении, чтобы создать наиболее благоприятные условия для удаления в прибыльную часть песка и шлака. Если сварку производят в горизонтальном положении, шов нужно "промыть" термитным металлом, чтобы освободить его от вредных включений.
Приварка стыковых соединений к рельсам
На железнодорожном транспорте широко применяется термитная приварка электросоединений к рельсам. Для этого используется специальный термит, состоящий из окислов меди, сплава меди с алюминием и ферромарганца. Сжигается этот термит в тигельформе из жаропрочного графита, способного выдержать несколько сот плавок.
При сгорании термитной шихты получается марганцовистая бронза, которая приваривает стыковой соединитель к рельсу. Таким же термитом, но с применением специальной сварочной оснастки производится приварка заземляющих устройств к мечтам линий высоковольтных электропередач и контактной сети.
Термитная наплавка рельсов
Трещины в головке, участки пробуксовки и другие дефекты рельсов устраняют термитной наплавкой, которая состоит из следующих операций:
- поврежденное место рельса вырезается газом до здорового металла;
- устанавливается форма;
- производится предварительный подогрев горелкой наплавляемого участка до 900-950°. При этом желательно применять горелку с прямолинейным соплом, рабочая ширина которого равна ширине головки рельса;
- заливка термитной сталью. Чтобы получился качественный провар, термитную сталь из тигля льют непосредственно на ремонтируемый участок рельса. Между запорным устройством тигля и наплавляемой поверхностью рельса необходимо выдерживать расстояние не более 150 мм, чтобы уменьшить разбрызгивание заливаемой стали;
- после этого удаляют формы, обрубают шлак, обрезают газом излишки наплавленного металла и шлифуют рабочие поверхности.
Для повышения износоустойчивости наплавляемой термитной стали в термитную шихту вводят несколько повышенное количество легирующих элементов-ферромарганца и углерода.
Термитная сварка стыков узкоколейных рельсов
Термитная сварка стыков узкоколейных рельсов без предварительного подогрева может применяться в горной и лесной промышленности. Для этого используют такие же сухие формы, как и при термитной сварке арматурных стержней.
Количество термита для сварки стыка без предварительного подогрева удваивается. Это компенсируется высокой производительностью (7-10 мин.) на один стык и компактностью применяемой оснастки.
Приварка элементов заземления к металлоконструкциям
На действующих газопроводах для предохранения их от разрушения почвенной коррозией осуществляется электродренажная защита - привариваются стальные стержни, которые подключаются к источникам постоянного тока. Стальные стержни приваривают только термитом. Использование других видов сварки - электрической или газовой - недопустимо, так как в ходе сварки может произойти прожог труб, по которым подается горючий газ под давлением. Термит для приварки стержней дренажной защиты состоит из железоалюминиевой шихты с введением в нее дополнительно магния и ферромарганца.
Для сварки стальных проводов широко применяют спрессованный в цилиндрические шашки термит, который состоит из 25% металлического магния и 75% железной окалины.
Магниевый термит применяется потому, что при сгорании он не образует жидких шлаков.
Термитно-муфельная шашка, сгорая в течение нескольких секунд, выделяет большое количество тепла, причем размеры шашки после окончания термитной реакции остаются неизменными. Это и позволяет с большим успехом использовать магниевый термит в качестве концентрированного источника местного подогрева стыков проводов, которые после необходимой выдержки осаживаются специальными клещами.
Термитная сварка многопроволочных проводов
При строительстве электрических установок высокого напряжения часто приходится сваривать стыки многопроволочных проводов. Перед сваркой производят механическую подготовку и обезжиривание стыков, закладывают подготовленные концы проводов в цилиндрический термитный патрон и закрепляют их в сварочных клещах.
Стык проводов при поджигании термитного патрона и в процессе сварки должен быть в горизонтальном положении.
После осадки проводов клещами процесс сварки заканчивается. Остывший шлак необходимо сбить.
При сварке сталеалюминевых и алюминиевых проводов со сваренного стыка необходимо удалять металлический кокиль - оболочку термитного патрона.
weldering.com
Способ термитной сварки рельсов
Ров.- . >:оэнаи № 48427
)3й-,31Класс 19а, 26
АВТОРСКОЕ СВИДЕТЕЛЬСТВО НА ИЗОБРЕТЕНИЕ
ОПИСЯНИЕ способа термитной сварки рельсов.
К авторскому свидетельству М. А. Карасева, заявленному 13 мая
1935 года (спр. о перв. ¹ 169252).
0 выдаче авторского свидетельства опубликовано 31 августа 1936 года.
Обычный способ термитной сварки рельсов промежуточным литьем состоит в том, что в полый канал, образуемый огнеупорными сварочными формами, заливается жидкий термитный металл.
Металл, проникая в щель стыка рельсов и расплавляя концы подошв, шеек и головок рельсов, по остывании сваривает их. С целью получения в самой щели и около щелевой зоны плотной без усадочных раковин отливки металл наплавлялся поверх головки рельса, образуя большие и высокие наросты.
При сварке рельсов типа Феникс (желобчатых) металл кроме того оплавлял и совершенно заливал весь жолоб.
Удаление прилива с катающей (рабочей) плоскости головки рельса и боковой его части (места прохода реборды колеса вагона в рельсах типа Виньоль), а также удаление металла из жолоба рельса типа Феникс представляли большие трудности и стоили очень дорого.
Термитный металл, которым сваривались рельсы, часто выходил слишком твердым, не поддающимся обработке зубилом и простой пилой, и требовал шлифовальных камней — кругов.
Головка рельса под влиянием черезмерно высокой температуры (3000 — 3300 ) термитного металла получала пережог своего металла, вследствие чего теряла свои качества в отношении сопротивления износу и смятию. Через незначительное время на месте сварки образовывались выбоины, и стык, хотя и хорошо сваренный, выходил из-за черезмерного по нему удара вагона из строя.
Предлагаемый способ термитной. сварки промежуточным литьем устраняет вышеупомянутые недостатки. Сваренный стык не только не уступает по стойкости целому рельсу, но делается даже более прочным благодаря увеличению катающей поверхностй.
На чертеже фиг. 1, 2 изображаюг поперечный и продольный вертикальные разрезы литейной формы с вкладышем, устанавливаемой на стыке рельса, типа Феникс; фиг. 3 представляет горизонтальный разрез литейной формы и вид сверху сквозь шлаковую камеру на вкладыш, место первоначального удара струи жидкого металла и желобкя-сливы L, по которым металл стекает вниз по обеим сторонам вкладыша в каналы отлива стыка; фиг. 4, 5, б — вид сбоку, снизу и поперечный разрез вкладыша„ фиг. 7 †аксонометрическ проекция половинки литейной формы; фиг. 8 — горизонтальное сечение облива из термита.
Главным и характерным фактором в предлагаемом способе сварки промежуточным литьем являются вкладыши К (фиг. 1 — 6), устанавливаемые перед насадкой литейных форм на головку рельса в месте щели.
Вкладыш для рельсов типа Виньоль имеет почти прямоугольную форму с соответствующей в соприкасающейся с головкой части конфигурацией. Для рельсов типа Феникс (желобчатых) вкладыш в нижней своей части имеет конфигурацию, показанную на фиг. 1 — 6.
Как видно из фиг. 1, 2, 4 — 6, вкладыш имеет на нижней плоскости, соприкасающейся с головкой рельса 1, дном жолоба z и малым жолобом рельса у, полый канал lzy с сечением d (фиг. 2 и 4) в виде сектора с хордой, равной тройной ширине щели и и (фиг. 2) при стреле (высоте), равной ширине щели.
Канал lzy определяет размеры (сечение) облива около щелевой зоны головки, жолоба и малого яблока. Термит попадает в канал в таком количестве, которого достаточно только для расплавления и сварки концов рельсов.
Вкладыш, устанавливаемый над стыком рельса, предохраняет таким образом головку его от разъедания металлом и
:оплавления вне границы облива.
Головка рельса вдоль всей щели
3h оплавляется лишь на ширину — и имеет
2 гребень, возвышающийся над щелью на высоту, равную Ь.
В верхней части половинок литейной формы Е, F (фиг. 1) делаются соответ
Обе половинки формы, плотно смыкаясь по плоскости их разъема Н8 (фиг. 1), обхватывают плотно и тело вкладыша.
При заливке в сварочную форму
;металл по боковым каналам тт поднимается более, чем на двойную высоту головки рельса, образуя сверх вкладыша слой жидкого металла толщиною 20—
25 мм. В боковых каналах металл, оставаясь под слоем горячего (вначале также, жидкого) шлака значительное время жидким, образует как бы напорные приливы, принимающие в себя усадочные раковины и газовые пузырьки всей зоны межстыковой щели ниже плоскости катания рельса. Таким образом получается плотная отливка и хорошая сварка.
При снятии формы со стыка весь металл от плоскости, проходящей через специально сцеланные для этой цели пережимы а и b до уровня rt, легко обламываются легкими ударами молотка.
Перед запиловкой образующегося над щелью головки гребня его осаживают (проковывают) легкими ударами кувалды, уменьшая тем самым почти наполовину его высоту. Затем снимают незначительные остатки этого гребня по уровню рабочей головки рельса.
Чтобы предупредить черезмерный перегрев металла рельса жидким весьма высокой температуры (3000 — 3300") металлом термита, но в то же время гарантировать расплавление поверхностеФ концов рельсов в стыке, сечение облива делается не по полуокружности или полуэллипсису, как в обычном способе промежуточного литья, а по форме, показанной на фиг. 8.
При данной конфигурации облива оплавление шейки и подошвы рельса происходит постепенно, границы ad u
bd возрастают внутрь, к оси OS стыка.
В этом случае сопротивление излому стыка оказывает помимо металла облива и основной металл рельса, имеющий большее временное сопротивление разрыву.
В случае разрыва стыка по шейке и подошве рельса разрушение при. данной конфигурации облива идет не по границе облива и поверхности рельса, а по линии К1. шейка получает разрыв внутри облива. Это безразличное на первый взгляд явление обусловливает при разрыве стыка безопасность движения по нему вагона в течение 1 /2 — 2 месяцев.
Оба конца лопнувшего стыка оказываются как бы заключенными в стальную прочную муфту, которая, плотно охватывая концы рельсов со всех сторон, будет значительное время сохранять стык от расстройства и смятия его при ударе.
Предлагаемый способ промежуточного литья снижает на 15 — 20% против обычного способа расход термита, а следовательно и главного компонента термита. фиг1 фигР
Я фйГ3 фйг4
Д фиг5 фигб
Предмет изобретения.
l. Способ термитной сварки рельсов с применением промежуточного литья и вкладышей для предохранения головки рельса от разъедания термитом при его наливании,. отличающийся тем, что во избежание всплывания вкладыша его снабжают по концам знаками, которые вформовываются в гнезда обеих половинок сварочной формы.
2. Прием выполнения способа термитной сварки рельсов по и. (, отличающийся тем, что для избежания нарушения в стыке профиля рельса типа Феникс, между нижней поверхностью вкладыша и плоскостью катания рельса образуют канал, конфигурация которого соответствует очертанию верхней поверхностм головки рельса.
Тип. „Печатный Труд .Зак. 6939-499



www.findpatent.ru
- Сварка монтажный шов
- Сварка шов монтажный
- Технология ванная сварка
- Технология ванная сварка
- Расчет стыковых сварных швов
- Расчет стыковых сварных швов
- Что такое дуги
- Что такое дуги
- Что такое дуги
- Стыковка оцинкованного листа сваркой
- Стыковка оцинкованного листа сваркой