Ультразвуковая сварка металлов. Ультразвуковая сварка металлов
Ультразвуковая сварка металлов

Рис. 1. Принципиальная схема точечной (я) и шовной (б) сварки ультразвуком: 1 - свариваемые детали, 2 - трансформатор упругих колебаний, Р - сжимающая сила, 3 - сварочный наконечник (ролик), 4 - маятниковая опора (опорный ролик), 5 - сварная точка (шов), у.з.к. - ультразвуковые колебания.
Сварочный наконечник 3 (при шовной сварке - ролик) определяет площадь и объем источника ультразвуковых механических колебаний непосредственно в зоне сварки. Он должен передавать колебания для осуществления трения между поверхностями соединяемых деталей с минимальными потерями между ним и верхней деталью. Величина амплитуды колебаний обычно находится в интервале 10 ... 25 мкм. Таким образом, процесс ультразвуковой сварки металлов происходит в условиях трения, вызванного микроскопическим относительным возвратно-поступательным перемещением участков поверхностей в зоне сжатия, что сопровождается выделением теплоты. Распространение ультразвуковых колебаний при сварке показано на рис. 2.
Рис. 2. Распространение у.з.к. при сваривании. а - начало сваривания; б - процесс сварки; в - окончание процесса.
Исследования показали, что при ультразвуковой сварке действуют два основных источника тепла. Один находится в зоне контакта сварочного наконечника (ролика) с деталью, второй - в зоне соединения деталей. Выделение теплоты у сварочного наконечника обусловлено его трением с деталью и приводит к пластическому деформированию наружной поверхности детали под наконечником. Выделение теплоты между деталями обусловлено действием нормальных сжимающих напряжений и напряжений сдвига, что приводит к внешнему и внутреннему трению в металлах и пластической деформации в зоне сварки. Вибрирующий сварочный наконечник в первый момент сварки развивает интенсивное выделение тепла в зоне его контакта с деталью. В зону сварки ультразвуковые колебания передаются с некоторым опозданием (см. рис. 2). Усилие сжатия обеспечивает передачу ультразвуковых колебаний в зону сварки. Его минимальное значение, при котором начинают образовываться соединения, зависит от свариваемых материалов и их толщины, а оптимальное значение возрастает с увеличением амплитуды колебаний. При увеличении контактного давления начальная скорость нагрева растет за счет улучшения связи между сварочным наконечником и деталями. Скорость нагрева деталей зависит также от формы и состояния поверхности наконечника. Температура в зоне сварки зависит от твердости и теплофизических свойств свариваемых материалов, мощности колебательной системы и параметров режима сварки. Нагрев в зоне сварки обычно не превышает 0,6 температуры плавления. Под действием трения, нагрева и пластического деформирования пленки загрязнений разрушаются и удаляются из зоны сжатия, благодаря чему становится возможным образование узлов схватывания, их расширение и формирование сварного соединения. Установлено, что ультразвуковые колебания способствуют удалению жировых пленок благодаря развитию кавитационных процессов в условиях действия в отдельных микрообъемах попеременных высоких давлений и разрежений. Поэтому УЗ-сварка может выполняться даже при наличии жировых загрязнений поверхностей. Однако принято обезжиривать поверхности перед свариванием, поскольку это увеличивает диаметр точек сварки. Ультразвуковые колебания также снижают поверхностное натяжение металлов, значительно ускоряют образование активных центров и схватывания поверхностей, процессы диффузии и рекристаллизации. Поэтому формирование кристаллической структуры в зоне соединения при сварке происходит достаточно быстро. УЗ-сварка может выполняться с импульсным нагревом места сварки от отдельного источника тепла, что позволяет уменьшить усилие сжатия, амплитуду и время действия уз-колебаний, и деформацию металла. Такой способ разработан для ультразвуковой сварки микродеталей. Свариваемые элементы подлежат действию ультразвуковых колебаний и нагреванию одновременно или в определенной последовательности. Процесс выполняется следующим образом. Сначала сварочный инструмент небольшим усилием прижимается к детали, затем через него пропускается электрический ток для его нагрева и одновременно (или с некоторым опережением или опозданием) включаются ультразвуковые колебания. Способ позволяет сваривать материалы с различными физико-химическими свойствами. Существует мнение, что успешная ультразвуковая сварка разнородных материалов возможна при условии разности атомных радиусов соединяемых деталей не более 15 ... 18%. Это условие соответствует общему представлению о существовании твердых растворов. При разности атомных радиусов в пределах 19 ... 44% сварка металлов усложняется. Исследование А. О. Россошинского позволили получить с помощью ультразвукового сваривания надежные соединения между материалами с существенными различиями атомных радиусов и различиями физико-химических свойств, например, между керамикой и металлами. Образование соединений автор объясняет определенным перемещением металла в зоне сварки. Деформация микровыступов под действием колебаний и их сжатие приводит к взаимному проникновению и перемешиванию материалов, которые соединяются, что и обеспечивает качество сварки. При ультразвуковой сварке можно выделить процессы образования физического контакта, активации поверхностей и объемного взаимодействия, несмотря на кратковременность процесса. Все эти процессы протекают в условиях действия ультразвуковых колебаний. Поэтому иногда отмечается возможность развития процессов усталости в зоне сварного соединения под влиянием длительного действия колебаний и снижение прочности соединений вследствие частичного разрушения узлов схватывания.Что такое ультразвуковая сварка металлов?
На данный момент существует около сотни самых разнообразных способов сварки металлов. У каждого из них есть свои достоинства и недостатки, особенности и сферы применения. Какие-то методы незаменимы на опасных объектах, а какие-то становятся основополагающими в практике домашних мастеров. Но существуют и такие способы сварки, о которых мы мало что слышим в силу узкого применения.
Один из таких способов — сварка ультразвуком. Ультразвуковая сварка нечасто на слуху, но она все же широко применяется при сварке микроэлектроники, проволоки, листового металла и прочих тонких или просто маленьких изделий. В этой статье мы подробно объясним, что такое ультразвуковая сварка и как работает данный метод соединения металлов.
Содержание статьи
Общая информация
Ультразвуковая сварка металлов — метод сварки, в основе которого лежит применение ультразвуковых колебательных волн. Широко применяется не только для сварки металлов, но и для соединения деталей из пластмассы, ткани, натуральной кожи. Также с помощью ультразвука вы сможете сварить стекло с металлом. Вы можете комбинировать ультразвуковую сварку с точечной, контурной или шовной сваркой.
Интересный факт: в конце 60-х годов прошлого века с помощью ультразвуковой сварки был собран автомобиль, изготовленный из пластмассы. Именно благодаря ультразвуковому оборудованию этот проект удалось успешно завершить.
Читайте также: Ультразвуковая сварка пластмасс
Существуют даже специализированные приборы для ультразвуковой сварки. Например, большой популярностью пользуется ультразвуковая швейная машина для сварки полимеров (брезента или подобных изделий). Но про оборудование мы подробнее поговорим позже.
Технология
В работе применяется специальный ультразвуковой сварочный аппарат, который во включенном состоянии непрерывно генерирует ультразвуковые волны частотой от 18 до 180 кГц. При этом может выдавать мощность от 0,01 до 10 кВт. В итоге создаются высокочастотные колебания, которые генерируют тепло и в связке с высоким давлением сваривают детали. Дополнительно заготовка может нагреваться в месте сварки с помощью отдельного прибора, так соединение получается более качественным.Это краткое описание. Подробное описание процесса сварки можно описать следующим образом: высокочастотные колебания сталкиваются с деталями и образуется сухое трение частиц. Если металл покрыт окисной пленкой, то под действием сухого трения она разрушается. После чего образуется чистое трение, во время которого металл плавится и образуется сварочное соединение.
Ультразвуковая сварка металлов может выполняться с использованием самых разнообразных типов сварных соединений. Вы можете сварить две детали внахлест, раздавить кромки и сварить их, можете встык сварить круглую деталь с плоской, и так далее. Словом, возможности практически безграничны.
Достоинства и недостатки
У ультразвуковой сварки (как и у любого другого метода) есть достоинства и недостатки. Давайте рассмотрим их подробнее, чтобы вы могли понять, в каких целях стоит применять ультразвук, а в каких от этой идеи лучше отказаться.
Первое достоинство — отсутствие необходимости в тщательной подготовке металла под сварку. Единственное, что необходимо сделать — обезжирить поверхность. Все. Можно даже не удалять грязь или ржавчину. При других методах сварки подготовительный процесс отнимает много времени и сил, а вот с применением ультразвука эта проблема легко решается.
Второй плюс — местный нагрев. Металл нагревается только в том месте, где планируется сварное соединение. По этой причине исключены какие-либо деформации металла из-за избыточного нагрева. Это достоинство особенно заметно при сварке пластмассовых деталей.
Третий плюс — возможность варить даже в труднодоступных местах, при этом вся сварка производится очень быстро, ведь металл успевает нагреться менее чем за секунду. К тому же, вы без труда сварите очень тонкий металл. И говоря «тонкий» мы подразумеваем даже металлические листы толщиной не более 0,001 миллиметра. Впечатляет!
Но, поскольку наш материал объективен, мы расскажем и о недостатках. Учтите, что все они не так существенны.
Во-первых, в некоторых ситуациях все же приходится приобретать дорогие генераторы ультразвуковых волн, если бюджетные модели не справляются. Но, справедливости ради, случается это крайне редко. В нашей практике еще не было ни одного случая, когда бы недорогой ультразвуковой генератор не справился со своей работой.
Также иногда бывают ситуации, когда ультразвук не может сварить толстый металл. Эту проблему можно решить, если подбирать вогнутые детали. Они будут фокусировать ультразвук в зоне сварки и тем самым даже толстый металл быстро расплавится.
Оборудование
Раз уж мы дважды упомянули оборудование, остановимся подробнее на этой теме. Существует три типа аппаратов для ультразвуковой сварки:
- Аппараты, выполняющие точечно-контурную сварку
- Сварочники, выполняющие шовную или шовно-шаговую сварку
- Мобильные (переносные) аппараты малой мощности, например, сварочные пистолеты.
При этом мощность аппарата может быть от 100 до 1500Вт, в зависимости от его цены, назначения и размеров.
На сварочных аппаратах, произведенных до конца 70-х, использовался магнитострикционный принцип генерации ультразвука. Но на данный момент такие аппараты не выпускаются, им на смену пришли установки, в которых ультразвук генерируется с помощью встроенного пьезоэлектрического преобразователя.
На данный момент такое оборудование производят многие страны Европы и мира, в том числе Россия. Качество отечественной продукции вполне приемлемо, особенно учитывая невысокую стоимость по сравнению с зарубежными конкурентами. Вообще производство ультразвуковых сварочных аппаратов началось еще в Советском союзе. Тогда такие аппараты в основном использовались для сварки микросхем. Сейчас же сфера применения стала куда шире.
Вместо заключения
Сварка ультразвуком незаменима при работе с маленькими и тонкими деталями, которые просто невозможно сварить вручную или с применением других технологий. Благодаря ультразвуку металл не деформируется и не растекается, а образует прочное соединение. Также сварка ультразвуком позволяет беспроблемно варить металлы, покрытые окисной пленкой. Например, алюминий, с которым у сварщиков обычно много проблем.
К тому же, оборудование для ультразвуковой сварки стоит не так уж дорого. Поэтому рекомендуем испробовать в своей практике этот метод соединения металлов. Если вы когда-либо выполняли ультразвуковую сварку своими руками, то расскажите об этом. Ваш опыт будет полезен для многих новичков. Желаем удачи в работе!
svarkaed.ru
УЛЬТРАЗВУКОВАЯ СВАРКА МЕТАЛЛОВ
Количество просмотров публикации УЛЬТРАЗВУКОВАЯ СВАРКА МЕТАЛЛОВ - 675
Ультразвук находит широкое применение в науке для исследования некоторых физических явлений и свойств веществ. В технике ультразвуковые колебания используют для обработки металлов и в дефектоскопии.
В сварочной технике ультразвук должна быть использован в различных целях. Воздействуя им на сварочную ванну в процессе кристаллизации, можно улучшить механические свойства сварного соединения благодаря измельчению структуры металла шва и удалению газов. Ультразвук должна быть источником энергии для создания точечных и шовных соединений. Ультразвуковые колебания активно разрушают естественные и искусственные пленки, что позволяет сваривать металлы с окисленной поверхностью, покрытые слоем лака и т. п. Ультразвук снижает или снимает собственные напряжения и деформации, возникающие при сварке. Им можно стабилизировать структурные составляющие металла сварного соединения, устраняя возможность самопроизвольного деформирования сварных конструкций со временем.
В качестве источника энергии при сварке металлов ультразвук еще не нашел широкого применения, хотя данный способ имеет ряд преимуществ и особенностей по сравнению с контактной и холодной сваркой.
При сварке ультразвуком неразъемное соединение металлов образуется при совместном воздействии на детали механических колебаний высокой частоты и относительно небольших сдавливающих усилий. В принципе данный метод сварки имеет много общего с холодной сваркой сдвигом.
Для получения механических колебаний высокой частоты обычно используется магнитострикционный эффект, состоящий в изменении размеров некоторых металлов и сплавов под действием переменного магнитного поля. Для ультразвуковых преобразователей обычно используют чистый никель или железо-кобальтовые сплавы. Изменения размеров магнитострикционных материалов очень малы: так, для никеля магнитострикционное удлинение составляет 40·10–8. По этой причине для увеличения амплитуды смещения и концентрации энергии колебаний, а также для передачи механических колебаний к месту сварки используют волноводы или концентраторы, которые в большинстве случаев имеют сужающуюся форму.
Эксперименты показывают, что для сварки металлов достаточно иметь волноводы с коэффициентом усиления около 5, при этом амплитуда на конце волновода при холостом ходе должна быть 20–30 мкм. Магнитострикционный преобразователь и волноводы должны быть рассчитаны и изготовлены на заданную частоту ультразвукового генератора [7, с. 20–38].
Основной узел машины для выполнения точечных соединений с помощью ультразвука – магнитострикционный преобразователь (рис. 7.1). Его обмотка питается током высокой частоты от ультразвукового генератора.Охлаждаемый водой магнитострикционный преобразователь 1 изготовлен из пермендюра (К49Ф2), он служит для превращения энергии тока высокой частоты в механические колебания, которые передаются волноводу 6. На конце волновода имеется рабочий выступ 4. При сварке изделие 8 зажимают между рабочим выступом 4и механизмом нажатия 3,
ккоторому прикладывают усилие, крайне важно е для создания давления в процессе сварки.
Сварка происходит при включенном преобразователе. Высокочастотные упругие колебания передаются через волновод на рабочий выступ 4 в виде горизонтальных механических перемещений высокой частоты. Длительность процесса сварки зависит от свариваемого металла и его толщины, для малых толщин она исчисляется долями секунды.
Основные узлы машины для выполнения шовных соединений при помощи ультразвука (рис. 7.2): вращающийся магнитострикционный преобразователь 1 и волновод 2. Конец волновода имеет форму ролика 3. Изделие 5, подлежащее соединению, зажимают между вращающимся роликом 3волновода и холостым роликом 4. Упругие высокочастотные колебания передаются через волновод на ролик, который вращается вместе с волноводом. Изделие, зажатое между роликами, перемещается, и одновременно создается герметичное соединение.
Сварка по контуру, разработанная в МВТУ – МЭИ, обеспечивает получение герметичного шва практически самого сложного контура.
Простейший ее вид – сварка по кольцу. В этом случае конический штифт, вставляемый в волновод, имеет форму трубки. При равномерном поджатии деталей к сваривающему штифту получается герметичное соединение по всему контуру.
Процесс ультразвуковой сварки происходит при воздействии сдвигающих высокочастотных колебаний, давления, приложенного перпендикулярно к поверхности листа͵ и теплового эффекта͵ сопровождающего процесс сварки. В результате в зоне сварной точки наблюдается небольшая пластическая деформация.
Пропускание ультразвука в течение 0,73 с привело к дальнейшему увеличению площади зашлифованного пятна, при этом площадь узла схватывания также возросла. Вокруг основного узла схватывания возникли отдельные небольшие участки схватывания, удлиненные в направлении ультразвуковых колебаний. С увеличением времени пропускания ультразвука более 0,73 с площадь зашлифованного участка почти не изменяется (рис. 7.3, г, д), но площадь узлов схватывания начинает увеличиваться более интенсивно. При пропускании ультразвука свыше 1,06 секунд происходит разрушение сварного соединения с взрывом точки по всему контуру.
Τᴀᴋᴎᴍ ᴏϬᴩᴀᴈᴏᴍ, процесс ультразвуковой сварки происходит под действием трения, вызванного микроскопическим возвратно-поступательным перемещением трущихся поверхностей.
В начальный момент действия ультразвуковых колебаний на свариваемых поверхностях возникает сухое трение, приводящее к разрушению окисных пленок и пленок из адсорбированных газов и жидкостей. После появления ювенальных поверхностей процесс сухого трения переходит в чистое трение, ĸᴏᴛᴏᴩᴏᴇ сопровождается образованием узлов схватывания. Схватыванию в значительной степени способствует малая амплитуда колебаний трущихся поверхностей и возвратно-поступательный характер этих колебаний.
При малых давлениях прочность точки в значительной степени зависит от продолжительности прохождения ультразвука. С повышением давления сварные соединения прочнее при меньшей продолжительности прохождения ультразвука. При очень продолжительном пропускании ультразвука и большом давлении сварное соединение некачественно вследствие значительных деформаций основного металла и приваривания его к электроду. При шовной сварке прочность сварных соединений обычно выше прочности основного металла и разрушение происходит по основному металлу.
Сварка ультразвуком позволяет соединять различные металлы. В частности хорошо свариваются ультразвуком алюминий, медь, никель; удовлетворительно свариваются высоколегированные стали. При этом прочность сварных точечных соединений достаточно высока, разрушение соединений происходит обычно с взрывом точки по контуру как при испытаниях на срез, так и при испытаниях на отрыв.
С помощью ультразвука получены соединения на ряде тугоплавких металлов - ниобии, тантале, молибдене и вольфраме. При этом недостаток сварных соединений вольфрама и молибдена состоит в их хрупкости.
Ультразвуковая сварка нашла наибольшее применение в микроэлектронике, в основном для приварки токоотводов к интегральным схемам. Разработаны и выпускаются значительными сериями ультразвуковые машины для сварки различных элементов микросхем (табл. 7.1).
Таблица 7.1–Технические характеристики машин для сварки изделий микроэлектроники
Показатели | УЗС | УЗС-2 | МС41П2-1 | УЗСКН-1 |
Мощность, В А | ||||
Частота͵ кГц | ||||
Усилие сжатия, кгс | До 0,5 | До 0,5 | 0,02–0,250 | 0,02–1,0 |
Производительность (число точек в минуту) | – | – | ||
Масса, кг |
Машины оснащены автоматическими устройствами, позволяющими в значительной степени увеличивать их производительность: автоматизированы подача проводников, сварка, обрезка проводников и т. п.
Установки типа УЗС (рис.7.4) и УЗС-2 предназначены для присоединения круглых (диаметром 0,03–0,1) и плоских проводников толщиной до 0,1 мм из пластичных металлов (золота͵ алюминия) к тонким золотым, алюминиевым и медным пленкам, напыленным на диэлектрические подложки. Установки комплектуются ламповыми ультразвуковыми генераторами.
Полуавтомат МС41П2-1 предназначен для соединения деталей микросхем в круглом и плоском корпусах ультразвуковой сваркой золотыми и алюминиевыми проводниками диаметром 20—25 мкм. Высокая производительность станка (до 800 сварок в час) обеспечивается автоматической подачей и обрывом проволоки. В полуавтомате для повышения стабильности прочностных показателей использован сопутствующий подогрев. Полуавтомат состоит из следующих узлов: сварочной головки, кассеты с проволокой, ультразвукового генератора, блока регулирования температуры подогрева, манипулятора и микроскопа МБС-2.
Электрическая схема управления машиной выполнена на транзисторных конических элементах с бесконтактной коммутацией цепей. Ультразвуковой генератор на транзисторах имеет автоматическую подстройку частоты, чем достигается стабильность амплитуды колебания сварочного инструмента. Кинематическая схема полуавтомата МС41П2-1 приведена на рис. 7.5.
Корпус сварочной головки 1 может перемещаться вертикально в направляющих. Ее подъем и опускание реализуются кулачком 2. В установленном положении сварочная головка фиксируется стопором. Механическая колебательная система 6 укреплена в корпусе на оси 5. Поворот системы достигается с помощью кронштейна 8 от кулачка 11, который поворачивается от перемещения тяги 13 при нажатии на педаль 14. Обратный ход кулачка происходит под действием пружины 12. Начальное положение сварочного наконечника 7 относительно свариваемой детали регулируют перемещением ползуна 9 с роликом 10 в пазу кронштейна 8. Усилие сжатия регулируют ручкой 3 механизма 4 давления.
Установка для ультразвуковой сварки с импульсным косвенным нагревом УЗСКН-1 (рис. 11) предназначена для изготовления полупроводниковых приборов, тонкопленочных и полупроводниковых интегральных схем.
В установке использован комбинированный цикл – ультразвуковая сварка в сочетании с импульсным .косвенным нагревом. Установка предусматривает возможность сварки как комбинированным циклом с любой последовательностью импульсов ультразвука и нагрева и с разной длительностью смещения моментов их включения, так и сварки только ультразвуком или только косвенным нагревом. Свариваемые элементы нагреваются за счёт теплопередачи от сварочного инструмента (пуансона), нагреваемого импульсом проходящего через него тока промышленной частоты (50 Гц).
Опыт эксплуатации сварочных ультразвуковых установок показал, что данный метод наиболее перспективный в микроэлектронике, так как обеспечивает получение высоконадежных соединений, исключает общий разогрев изделия, позволяет соединять трудно свариваемые обычными методами сочетания материалов и т. п.
ВНИИЭСО разработан ряд ультразвуковых сварочных машин типа КТУ и МТУ к сварной точке. Имеющийся опыт применения сварки ультразвуком выявил следующие преимущества этого способа.
Сварка ультразвуком происходит в твердом состоянии без существенного нагрева места сварки, что позволяет соединять химически активные металлы или пары металлов, склонные образовывать хрупкие интерметаллические соединения в зоне сварки.
Возможны соединения тонких и ультратонких деталей, приварка тонких листов и фольги к деталям неограниченной толщины, сварка пакетов из фольги.
Снижены требования к чистоте свариваемых поверхностей, в связи с чем, возможна сварка плакированных и оксидированных поверхностей и вообще сварка металлических изделий, поверхности которых покрыты различными изоляционными пленками.
Небольшие сдавливающие усилия [10–250 кгс (98–2450 Н)] вызывают незначительную деформацию поверхности деталей в месте их соединения (вмятина, как правило, не превышает 5–10%). Применяется оборудование малой мощности и несложной конструкции (если, к примеру, для контактной точечной сварки алюминия толщиной 1 мм необходима машина мощностью 100–150 кВА, то при сварке ультразвуком аналогичного соединения – всего 5–2,5 кВА).
Ультразвуковая сварка нашла достаточно широкое применение для соединения тонких деталей из однородных и разнородных материалов в приборостроении и радиоэлектронной промышленности.
| |||
Примеры применения. Приварка медных проводников диаметром 0,3 мм, покрытых термостойким лаком, к клеммной колодке (рис. 7.7) без предварительной зачистки изоляции. Приварка контактов размером 1,5x1,5x0,4 мм из платиноиридиевого сплава марки ПИ-10 к контактным пружинам из нейзильбера толщиной 0,12 мм и бериллиевой бронзы Б-2 толщиной 0,15 мм (рис. 7.8). Прессовая сварка по всему контуру медного корпуса прибора типа П6 с медной крышкой толщиной 0,3 мм (рис. 7.9).
В дальнейшем можно ожидать, что данный метод будет использован при сварке металлов, образующих хрупкие интерметаллические соединения, для приварки тонких обшивок к несущей конструкции (в авиационной промышленности, автомобилестроении и ряде других отраслей промышленности).
Значительные успехи бывают получены при воздействии ультразвука на жидкий металл в процессе сварки плавлением. Озвучивание металла приводит к раздроблению зерен, улучшению механических свойств. Обработка ультразвуком сварных соединений после сварки приводит к уменьшению остаточных напряжений, снижению остаточных деформаций и предупреждает развитие деформаций с течением времени.
referatwork.ru
Ультразвуковая сварка металлов
Ультразвуковая сварка металлов
Тарас Никифоров
Технический центр «Виндэк» (Россия, г. Подольск)
Владимир Гуреев
TELSONIC AG (Швейцария)
На мировом рынке только за последнее десятилетие объем продаж оборудования для ультразвуковой сварки увеличился в несколько раз, и эксперты пророчат ему дальнейший рост. Благодаря новым достижениям в разработке технологии данные сварочные системы позволяют решать уникальные задачи в электронной, электротехнической, автомобильной промышленности, а также при производстве аккумуляторов, конденсаторов, солнечных батарей и систем нагрева воды.
В наши дни ультразвуковая сварка металлов находит все более широкое применение и позиционируется чуть ли ни как инновационный продукт. Вместе с тем, мало кто знает, что данный метод был открыт еще в 30-40 годы прошлого столетия, причем, совершенно случайно. При подготовке поверхности алюминия к контактной сварке экспериментаторы, применившие для этой вспомогательной цели ультразвуковые колебания, неожиданно для себя отметили, что соединение металлических пластин происходит еще до пропускания через них сварочного тока. Вот так и было положено начало совершенно новому виду сварки.
Как работает?
Область применения такого метода соединения простирается в диапазоне от пластмасс до цветных металлов. Однако, независимо от свариваемых материалов, оборудование для ультразвуковой сварки традиционно состоит из высокочастотного генератора, блока управления, механической колебательной системы и привода давления (Рис.1).
Ультразвуковой генератор преобразует ток электрической сети в ток высокой частоты, который по получении сигнала с блока управления подается на пьезоэлементы колебательной системы. Преобразование колебаний электрического тока высокой частоты в механические и введение их в зону сварки обеспечивается механической колебательной системой. Последняя, в свою очередь, состоит из конвертера (преобразователь), бустера (усилитель) и волновода (сонотрод) и является главным узлом технологии ультразвуковой сварки.
Для доступности понимания сравним колебательную систему, обеспечивающую практическую реализацию метода, например, с автомобилем (Рис.2). Конвертер выступает в роли мотора, преобразовывая ток высокой частоты в механические колебания с соответствующей частотой. Далее бустер, действуя как коробка передач, изменяет амплитуду колебаний в зависимости от передаточного числа и переадресует их на волновод. Волновод, увеличивая при необходимости амплитуду механических колебаний высокой частоты, передает их непосредственно в зону сварки, приводя в движение верхнюю свариваемую деталь.
В основу работы пьезокерамического конвертера положен хорошо известный многим еще со школьной скамьи пьезоэлектрический эффект. При воздействии на пьезоэлемент переменного давления возникает переменное электрическое напряжение, а под воздействием переменного электрического поля возникают механические напряжения, которые вызывают упругие деформации материала в следствии чего пьезоэлемент начинает сжиматься и увеличиваться на определенную величину с частотой равной частоте тока.
Величина изменения размера пьезоэлемента соответствует амплитуде механических колебаний (Рис.3), которая зависит от мощности и конфигурации конвертера. Так, при частоте 20кГц амплитуда колебаний пьезокерамического конвектора, как правило, не превышает 10мкм. Однако, за счет увеличения амплитуды бустером и волноводом можно получить максимальную амплитуду в зоне сварки - до 70мкм. Для ультразвуковой сварки обычно используется частота от 20кГц и выше. Применение той или иной частоты зависит от материала и габаритов свариваемого изделия.
Применительно к реальным технологиям это явление может иметь очень положительный эффект. Вот и в процессе ультразвуковой сварки металлов колебательные движения волновода совместно с усилием прижатия передаются на верхнюю свариваемую деталь. Она по определению должна быть подвижной относительно нижней детали, прочно закрепленной на наковальне. В результате между деталями возникает трение с определенной частотой и амплитудой, способствующее их сращиванию между собой (Рис.4). Именно поэтому ультразвуковую сварку можно еще классифицировать, как механическую сварку трением с высокой частотой без ввода сварочного тока в зону сварки.
В процессе сварки микроскопические смещения деталей относительно друг друга вызывают стирание шероховатостей, разрушение оксидных пленок и возникновение узлов схватывания. При повышение температуры в зоне сварки, за счет трения и дальнейшей деформации свариваемых деталей, наблюдается повышение пластичности поверхностных слоев металла, вытеснение оксидных пленок и загрязнений из зоны сварки. Все это приводит к интенсивному разрастанию зон схватывания, диффузии одного материала в другой, локальному плавлению верхних атомарных слоев, появлению новых и стойких межатомных связей. Данные структурные изменения можно воочию наблюдать на фотографии микрошлифа покрытых серебром медных проводов, которые были сварены между собой при помощи ультразвука (Рис.5).
Плюсы применения
Ультразвуковая сварка металлов обладает уникальными технологическими свойствами, которые в практическом применении дают ей сто очков вперед на многих направлениях. Перечислим только главные из них.
Прежде всего, это возможность производить сварку без предварительной подготовки поверхности соединяемых деталей и при весьма незначительном температурном воздействии, оказываемом непосредственно на них. Отсюда вытекает такое существенное преимущество ультразвуковой сварки, как умение накрепко и без печальных последствий соединять между собой термочувствительные элементы.
Более того, допустима сварка деталей разной толщины, а также разнородных металлов (медь-алюминий, алюминий-никель и др.). При ультразвуковой сварке достигаются отличные электрические свойства и незначительное переходное сопротивление.
Что очень даже существенно, прочность обеспечиваемых ультразвуком соединений приближается к 70% от прочности основного материала. Дополнительно следует отметить высокую скорость, экологическую чистоту и экономичность процесса.
Проверено практикой
Как уже было сказано, инновационная технология ультразвуковой сварки металлов благодаря своим особым свойствам находит все более широкое применение в самых различных отраслях промышленности. Например, в автомобилестроении метод активно используется при соединении медных многожильных проводов жгутов электропроводки (Рис.6). В России данную технологию весьма успешно применяют, в частности, такие производители автокомпонентов, как Leoni Group, Prettl, ИВК, Завод радиоаппаратуры, ПТОО ОАО «АВТОВАЗ» и другие. Конкурентными преимуществами собственной продукции они во многом обязаны внедрению у себя ультразвуковой технологии. Так ультразвуковые системы TelsoSplice, выпускаемые швейцарской фирмой Telsonic AG, способны сваривать многожильные медные провода суммарным сечением от 0,5 до 45мм2. Также ультразвуковая сварка используется при производстве электромоторов и патронов для подушек безопасности.
Масштабное применение ультразвуковая сварка обрела в электронной и электротехнической промышленности. И ничего удивительного здесь нет. Ведь ультразвук умеет соединять как миниатюрные изделия, так и проводку большого суммарного сечения до 200мм2 (Рис.7). Впрочем, в последнем случае описываемые нами системы оснащаются генераторами мощностью в 10кВт и наделяются способностью оказывать усилие в 8000Н.
С помощью ультразвуковой технологии, например, на «Свердловском заводе трансформаторов тока» к медному контакту присоединяют многожильные провода. Тем же способом специалисты ОАО «Протвинский опытный завод «ПРОГРЕСС» приваривают многожильные медные провода к шинам электрических шкафов. Наглядной демонстрацией преимуществ ультразвуковой сварки можно назвать и ее применение в компании Bosch. В частности, там при изготовлении электродвигателей соединяют провода с контактами без снятия с них защитной эмали, что позволило полностью автоматизировать процесс сборки автомобильных электромоторчиков.Или еще примеры. Растущая потребность в солнечных батареях и системах нагрева воды повлекла за собой использование ультразвуковой шовной сварки металлов в процессе создания и такого рода устройств. Компания «Элеконд» применяет ультразвук в соединении алюминиевой фольги и контактов. Кстати будет сказать, что технология применима также и в изготовлении самой алюминиевой фольги. Но продолжим о применениях, так сказать, по прямому назначению.
При производстве литий-ионных аккумуляторов компания VARTA при помощи ультразвука сваривает между собой алюминиевую, медную и никелевую фольгу. На заводе им. Фрунзе при изготовлении предохранителей тем же способом сваривают медные и биметаллические пластины. ФГУП ВНИИА им. Н.Л. Духова, используя технологию ультразвуковой сварки, соединяет алюминиевую фольгу толщиной всего от 5мкм.
Примером уникальности метода и его нацеленности на решение сложных задач, недоступных другим технологиям, может служить и соединение медных проводников с контактами в керамической подложке (Рис. 8). Впрочем, как в оценке всего нового, не будем спешить с конечным выводом. В самом ближайшем будущем нам еще предстоит узнать, на что еще способна ультразвуковая сварка.
А о том, что это обозримая перспектива свидетельствует опыт уже упомянутой компании TELSONIC AG. Она выпускает прецизионные сварочные системы, способные работать как автономно, так и в составе автоматизированных линий. Причем, неустанно продолжает поиск новых применений. Официальным дилером этой компании в России является ООО «Технический центр «Виндэк» из подмосковного Подольска.
Подводя итог, следует сказать, что использование ультразвуковых технологий существенно облегчает получение требуемых характеристик сварного соединения и повышает эффективность производства.
windeq.ru
Технология и оборудование ультразвуковой сварки металлов (1часть)
Ультразвук находит широкое применение в науке для исследования некоторых физических явлений и свойств веществ. В технике ультразвуковые колебания используют для обработки металлов и в дефектоскопии.
В сварочной технике ультразвук может быть использован в различных целях. Воздействуя им на сварочную ванну в процессе кристаллизации, можно улучшить механические свойства сварного соединения благодаря измельчению структуры металла шва и удалению газов.
Ультразвук может быть источником энергии для создания точечных и шовных соединений. Ультразвуковые колебания активно разрушают естественные и искусственные пленки, что позволяет сваривать металлы с окисленной поверхностью, покрытые слоем лака и т. п. Ультразвук снижает или снимает собственные напряжения и деформации, возникающие при сварке. Им можно стабилизировать структурные составляющие металла сварного соединения, устраняя возможность самопроизвольного деформирования сварных конструкций со временем.
В качестве источника энергии при сварке металлов ультразвук еще не нашел широкого применения, хотя этот способ имеет ряд преимуществ и особенностей по сравнению с контактной и холодной сваркой.
При сварке ультразвуком неразъемное соединение металлов образуется при совместном воздействии на детали механических колебаний высокой частоты и относительно небольших сдавливающих усилий. В принципе этот метод сварки имеет много общего с холодной сваркой сдвигом.
Для получения механических колебаний высокой частоты обычно используется магнитострикционный эффект, состоящий в изменении размеров, некоторых металлов и сплавов под действием переменного магнитного поля. Для ультразвуковых преобразователей обычно используют чистый никель или железо-кобальтовые сплавы. Изменения размеров магнитострикционных материалов очень малы: так, для никеля магнитострикционное удлинение составляет 40-10-6. Поэтому для увеличения амплитуды смещения и концентрации энергии колебаний, а также Для передачи механических колебаний к месту сварки используют волноводы или концентраторы, которые в большинстве случаев имеют сужающуюся форму.
Эксперименты показывают, что для сварки металлов достаточно иметь волноводы с коэффициентом усиления около 5, при этом амплитуда на конце волновода при холостом ходе должна быть 20—30 мкм. Магнитострикционный преобразователь и волноводы должны быть рассчитаны и изготовлены на заданную частоту ультразвукового генератора.
Основной узел машины для выполнения точечных соединений с помощью ультразвука — магнитострикционный преобразователь (рис. 8).
Рис.8. Схема установки для точечной сварки ультразвуком:1—магнитострикционный преобразователь;2— диафрагма;3 — механизм нажатия;4 — выступ;5 — маятниковая опора;6 — волновод;7 — кожух водяного охлаждения;8 — изделие
Его обмотка питается током высокой частоты от ультразвукового генератора. Охлаждаемый водой магнитострикционный преобразователь 1 изготовлен из пермендюра (К49Ф2), он служит для превращения энергии тока высокой частоты в механические колебания, которые передаются волноводу 6. На конце волновода имеется рабочий выступ 4. При сварке изделие 8 зажимают между рабочим выступом 4 и механизмом нажатия 3, к которому прикладывают усилие, необходимое для создания давления в процессе сварки.
Сварка происходит при включенном преобразователе. Высокочастотные упругие колебания передаются через волновод на рабочий выступ 4 в виде горизонтальных механических перемещений высокой частоты. Длительность процесса сварки зависит от свариваемого металла и его толщины, для малых толщин она исчисляется долями секунды.
Основные узлы машины для выполнения шовных соединений при помощи ультразвука (рис. 9): вращающийся магнитострикционный преобразователь 1 н волновод 2. Конец волновода имеет форму ролика 3. Изделие 5, подлежащее соединению, зажимают между вращающимся роликом 3 волновода и холостым роликом 4, Высокочастотные упругие колебания передаются через волновод на ролик, который вращается вместе с волноводом.
Рис.9.Схема установки для роликовой сварки ультразвуком:1—магнитострикционный преобразователь; 2 — волновод; 3 — сваривающий ролик;4 — прижимной ролик; 5 — изделие; 6 — кожух преобразователя; 7 — подвод тока от ультразвукового генератора;8 — привод; 9 — подвод охлаждающей воды
Изделие, зажатое между роликами, перемещается, и одновременно создается герметичное соединение.
Сварка по контуру, разработанная в МВТУ — МЭИ, обеспечивает получение герметичного шва практически самого сложного контура. Простейший ее вид — сварка по кольцу. В этом случае конический штифт, вставляемый в волновод, имеет форму трубки (рис. 10). При равномерном поджатии деталей к сваривающему штифту получается герметичное соединение по всему контуру.
Процесс ультразвуковой сварки происходит при воздействии сдвигающих высокочастотных колебаний, давления, приложенного перпендикулярно к поверхности листа, и теплового эффекта, сопровождающего процесс сварки. В результате в зоне сварной точки наблюдается небольшая пластическая деформация.
Исследование процесса образования сварного соединения при ультразвуковой сварке медных пластин толщиной 0,35 + 0,35 мм показывает, что при малом времени пропускания ультразвука (менее 0,05 с) сварка не происходит.
Рис.10.Схема установки для ультразвуковой сварки по контуру:1— волновод;2 — сменный полый штифт; 3 — сменный прижимной штифт; 4 — прижимная опора; 5 — свариваемое изделие
Рис.11. Макроструктура мест разрушения сварных соединений меди после различной продолжительности пропускания ультразвука. Х16
После разъединения образцов на их поверхности непосредственно под сваривающим выступом наблюдается пятно, имеющее полированную поверхность (рис. 11, а). Диаметр полированного пятна возрастает при увеличении времени сварки (рис. 11, а—д). При пропускании ультразвука в течение 0,1 с в местах контакта обнаруживаются не только зашлифованные поверхности, но и вы- рывы металла, свидетельствующие об образовании прочных соединений, так называемых узлов схватывания. На рис. 11, б виден один узел схватывания на зашлифованной поверхности.
Пропускание ультразвука в течение 0,73 с привело к дальнейшему увеличению площади зашлифованного пятна, при этом площадь узла схватывания также возросла. Вокруг основного узла схватывания возникли отдельные небольшие участки схватывания, удлиненные в направлении ультразвуковых колебаний. С увеличением времени пропускания ультразвука более 0,73 с площадь зашлифованного участка почти не изменяется (рис. 11, г, д), но площадь узлов схватывания начинает увеличиваться более интенсивно. При пропускании ультразвука свыше 1,06 с происходит разрушение сварного соединения с вырывом точки по всему контуру.
Проведенные измерения микротвердости поверхности зашлифованного пятна и основного металла вблизи пятна показали, что микротвердость поверхностного слоя зашлифованного пятна выше (Н50 42—44), чем у основного металла (Н50 28—30). Образование полированного пятна на свариваемых поверхностях указывает на то, что оно возникло вследствие трения под действием высокочастотных колебаний соприкасающихся поверхностей непосредственно под контактным выступом.
Таким образом, процесс ультразвуковой сварки происходит под действием трения, вызванного микроскопическим возвратно-поступательным перемещением трущихся поверхностей.
www.prosvarky.ru
Ультразвуковая сварка металлов и пластмасс
Ультразвуковая сварка металлов и пластмасс – эта еще одна разновидность классической сварки давлением. Данный технологический процесс основан на сжимании двух заготовок, свариваемые кромки (плоскости) которых вибрируют (смещаются в тангенциальном направлении) с ультразвуковыми (до 40 КГц) частотами.
В итоге, при контакте «деталь в деталь», на кромках шва возникает пластическая деформация, перетекающая в объединение кристаллических решеток или полимерных цепочек стыкуемых элементов.
В данной статье мы разберем процесс ультразвуковой сварки с физической и технологической точки зрения. Кроме того, на этой странице вы сможете найти описание типового оборудования, необходимого для сварки заготовок ультразвуковыми колебаниями. А в завершении мы разберем технологические приемы реализации этого процесса.
Ультразвуковая сварка пластмасс и металлов: суть процесса
Процесс ультразвуковой сварки основан на совмещении тангенциальных колебаний и вертикальной нагрузки в зоне контакта двух деталей.
В результате такого воздействия истираются микронеровности, покрывающие контактные поверхности, и разрушается оксидная пленка.
Кроме того, возникает эффект перетекания кинетической энергии возвратно-поступательных колебаний в тепловое излучение, расплавляющее поверхностные слои деталей. И в этих условиях, даже относительно небольшая вертикальная нагрузка приводит к образованию межкристаллических (у металла) или межмолекулярных (у полимера) связей, скрепляющих соединяемые детали.
Таким образом, все установки ультразвуковой сварки функционируют на основе термомеханической технологии получения неразъемного соединения. Причем такие аппараты не нуждаются во внешнем нагреве. Выделяемой при трении деталей энергии вполне достаточно для образования новых межатомных или межмолекулярных связей.
Где используют ультразвуковую сварку?
Ввиду дороговизны оборудования классическое применение ультразвуковой сварки – монтаж элементов металлоконструкций – было бы экономически неоправданным. Однако с помощью этой технологии удается сваривать не только металлы, но и полимеры, и даже органические соединения.
Поэтому ультразвуковая технология используется в приборостроении, электронике и прочих отраслях, где есть спрос на эффективные способы сопряжение металлических и неметаллических элементов.
Кроме того, ультразвуковой способ подходит и для сварки материалов с чрезвычайно прочной оксидной пленкой. Хороший пример такого случая — ультразвуковая сварка алюминия, покрытого тугоплавким оксидом (температура плавления более 2000 градусов Цельсия). В данном случае ультразвуковые аппараты действуют более эффективно, чем классическая аргонодуговая технология.
А еще, существует особая технология ультразвуковой сварки костной ткани, использующая в качестве присадочного материала эфир цианакриловой кислоты. Введенный в разлом кости циакрин твердеет под действием ультразвука и образует высокопрочный шов между обломками органической ткани.
Оборудование для ультразвуковой сварки
Работающая на ультразвуке сварочная установка состоит из следующих блоков:
- Генератора ультразвуковых колебаний, формирующего переменное электромагнитное поле, частота которого выходит за пределы 20 КГц.
- Вибратора, трансформирующего волновые колебания в механическую вибрацию. Вибратор состоит из пакета пластин (толщиной не более десятой части миллиметра), изготовленных их особого материала, который меняет линейные габариты под действием магнитного поля. В итоге, магнитное поле, передаваемое от генератора на пластины, то удлиняет, то укорачивает их размер и электромагнитная волна перетекает в механическую вибрацию.
- Вибратор соединяется волноводом конической или цилиндрической формы, который транслирует механическую вибрацию на поверхность внешней детали. Причем конический волновод работает еще и как резонатор, усиливая амплитуду и повышая эффективность процесса.
Помимо указанных блоков в конструкцию аппарата входит еще и особый сварочный стол, на котором покоятся соединяемые детали. Причем аппарат ультразвуковой сварки транслирует вибрацию на внешнюю деталь в продольном, продольно-поперечном или в продольно-вертикальном направлении. Кроме того, возможно и взаимное кручение стыкуемых элементов.
В завершении описания оборудования следует отметить, что стыкуемые детали попадают на рабочий стол аппарата в следующей последовательности: вниз укладывают толстую деталь, на которую помещают тонкую заготовку. Соотношение толщины верхней и нижней заготовок может достигать значения 1/1000.
Технологические приемы сварки ультразвуком
В процессе сварки ультразвуком используют следующие варианты стыковки деталей:
- Сопряжение внахлест, когда поверх одной плоской заготовки укладывают аналогичную.
- Сопряжение по рельефу, когда нижняя плита соприкасается с рельефной поверхностью верхней детали.
- Сопряжение по кромкам, когда торцы изделий либо накладываются друг на друга, либо стыкуются под углом.
- Сопряжение «крест-накрест» и тавровое сопряжение, когда два прутка накладываются внахлест, при несовпадении осей стыкуемых деталей, или когда торец прутка стыкуют с плоскостью.
- Многослойное сопряжение, когда стыкуют больше двух заготовок.
Кроме того, существует и схема параллельной сварки двух прутков (вдоль оси), прутка и плоскости.
Указанные варианты соединения реализуются за счет трансляции колебаний в продольном (внахлест, рельеф), продольно-поперечном (встык под углом) или крутящем направлении (тавровое или прямое стыковое направление).
steelguide.ru
Технология и оборудование ультразвуковой сварки металлов (4часть)
Установки типа УЗС (рис. 16) и УЗС-2 предназначены для присоединения круглых (диаметром 0,03—0,1) и плоских проводников толщиной до 0,1 мм из пластичных металлов (золота, алюминия) к тонким золотым, алюминиевым и медным пленкам, напыленным на диэлектрические подложки. Установки комплектуются ламповыми ультразвуковыми генераторами.
Полуавтомат МС41П2-1 предназначен для соединения деталей микросхем в круглом и плоском корпусах ультразвуковой сваркой золотыми и алюминиевыми проводниками диаметром 20—25 мкм. Высокая производительность станка (до 800 сварок в час) обеспечивается автоматической подачей и обрывом проволоки. В полуавтомате для повышения стабильности прочностных показателей использован сопутствующий подогрев. Полуавтомат состоит из следующих узлов: сварочной головки, кассеты с проволокой, ультразвукового генератора, блока регулирования температуры подогрева, манипулятора и микроскопа МБС-2.
Электрическая схема управления машиной выполнена на транзисторных конических элементах с бесконтактной коммутацией цепей. Ультразвуковой генератор на транзисторах имеет автоматическую подстройку частоты, чем достигается стабильность амплитуды колебания сварочного инструмента. Кинематическая схема полуавтомата МС41П2-1 приведена на рис. 17.
Корпус сварочной головки 1 может перемещаться вертикально в направляющих. Ее подъем и опускание осуществляются кулачком 2. В установленном положении сварочная головка фиксируется стопором. Механическая колебательная система 6 укреплена в корпусе на оси 5. Поворот системы достигается с помощью кронштейна 8 от кулачка 12, который поворачивается от перемещения тяги 13 при нажатии на педаль 14. Обратный ход кулачка происходит под действием пружины 12. Начальное положение сварочного наконечника 7 относительно свариваемой детали регулируют перемещением ползуна 9 с роликом 10 в пазу кронштейна 8. Усилие сжатия регулируют ручкой 3 механизма 4 давления.
Установка для ультразвуковой сварки с импульсным косвенным нагревом УЗСКН-I (рис. 18) предназначена для изготовления полупроводниковых приборов, тонкопленочных и полупроводниковых интегральных схем.
Рис. 16. Установка УЗС
Рис.17.Кинематическая схема полуавтомата МС41П2-1
В установке использован комбинированный цикл — ультразвуковая сварка в сочетании с импульсным косвенным нагревом. Установка предусматривает возможность сварки как комбинированным циклом с любой последовательностью импульсов ультразвука и нагрева и с разной длительностью смещения моментов их включения, так и сварке только ультразвуком или только косвенным нагревом. Свариваемые элементы нагреваются за счет теплопередачи от сварочного инструмента (пуансона), нагреваемого импульсом проходящего через него тока промышленной частоты (50 Гц).
Для осуществления токоподвода к сварочному инструменту применена конструкция «расщепленного» преобразователя ультразвуковых колебаний, в котором волновод разрезан на две равные части, между которыми расположен тонкий слой изоляции (рис. 19). Сварочный инструмент в виде V-образной иглы вставляется в отверстие на рабочем конце «расщепленного» волновода между его обеими частями и стягивается винтом для обеспечения хорошего акустического и электрического контакта.
На установке УЗСКН-1 можно приваривать круглые (диаметром 0,03—0,1 мм) и плоские (толщиной до 0,05 мм) проводники из алюминия, золота, меди к контактным площадкам из золота, алюминия, меди, тантала, никеля, напыленные на диэлектрические полупроводниковые подложки.
Опыт эксплуатации сварочных ультразвуковых установок показал, что этот метод наиболее перспективный в микроэлектронике, так как обеспечиваем получение высоконадежных соединений, исключает общий разогрев изделия, позволяет соединять трудносвариваемые обычными методами сочетания материалов и т. п.
ВНИИЭСО разработан ряд ультразвуковых сварочных машин типа КТУ и МТУ (табл. 7). Акустический узел (рис. 20) этой серии машин состоит из резонирующего стержня со сварочным наконечником 1, концентратора с магнитострикционным преобразователем 2 с обмоткой. Диаметр контактной площади наконечника определяется технологическими требованиями к сварной точке.
Рис.18.Установка для ультразвуковой сварки с импульсным косвенным нагревом УЗСКН-1
Рис.19.Преобразователь ультразвуковых колебаний к установке УЗСКН-1
Рис.20. Акустический узел машины МТУ-0,4
Технические характеристики машин типа МТУ и КТУ
Показатели | МТУ-0,4 | МТУ-1,5 | КТУ-1,5 | МТУ-4 |
Мощность, кВт | 0,4 | 1,5 | 1,5 | 4,0 |
Частота, кГц | 22,0 | 22,0 | 22,0 | 18,0 |
Усилие сжатия, кгс | 6—60 | 15—150 | 15—120 | 50—550 |
Толщина свариваемых металлов (медь), мм | 0,01—0,2 | 0,1—0,5 | 0,1—0,5 | 0,3—1,2 |
Масса машины, кг | 76 | 82 | 80 | 105 |
Примечание.Производительность машин до 60 точек в минуту. |
Сварочный наконечник изготовлен из высоколегированной стали, применение которой исключает налипание свариваемых металлов (медь, алюминий) на наконечник и не требует зачистки даже после сварки 5—20 тыс. точек. Усилие сжатия свариваемых деталей создается приводом давления. Акустический узел в горизонтальном направлении может перемещаться специальным приводом.
Принцип построения механической колебательной системы сварочной головки ультразвуковых сварочных клещей КТУ-1,5 (рис. 21) аналогичен системе, принятой в сварочных ультразвуковых машинах.
Имеющийся опыт применения сварки ультразвуком выявил следующие преимущества этого способа:
Рис.21. Сварочная головка клещей КТУ-1,5
Рис.22. Медные проводники диаметром 0,3 мм, покрытые лаковой изоляцией, приваренные с помощью ультразвука к клеммной колодке
1. Сварка ультразвуком происходит в твердом состоянии без существенного нагрева места сварки, что позволяет соединять химически активные металлы или пары металлов, склонные образовывать хрупкие интерметаллические соединения в зоне сварки.
2. Возможны соединения тонких и ультратонких деталей, приварка тонких листов и фольги к деталям неограниченной толщины, сварка пакетов из фольги.
3. Снижены требования к чистоте свариваемых поверхностей, в связи с чем возможна сварка плакированных и оксидированных поверхностей и вообще сварка металлических изделий, поверхности которых покрыты различными изоляционными пленками.
4. Небольшие сдавливающие усилия (10—250 кгс 98—2450 Н) вызывают незначительную деформацию поверхности деталей в месте их соединения (вмятина, как правило, не превышает 5—10%).
5. Применяется оборудование малой мощности и несложной конструкции (если, например, для контактной точечной сварки алюминия толщиной 1 мм необходима машина мощностью 100—150 кВА, то при сварке ультразвуком аналогичного соединения — всего 5—2,5 кВА).
Ультразвуковая сварка нашла достаточно широкое применение для соединения тонких деталей из однородных и разнородных материалов в приборостроении и радиоэлектронной промышленности.
Рис.23. Контакты, приваренные к контактным пружинам с помощью ультразвука
Рис.24.Сварные корпусы приборов типа П6
www.prosvarky.ru
www.samsvar.ru
Технология и оборудование ультразвуковой сварки металлов (1часть)
Ультразвук находит широкое применение в науке для исследования некоторых физических явлений и свойств веществ. В технике ультразвуковые колебания используют для обработки металлов и в дефектоскопии.
В сварочной технике ультразвук может быть использован в различных целях. Воздействуя им на сварочную ванну в процессе кристаллизации, можно улучшить механические свойства сварного соединения благодаря измельчению структуры металла шва и удалению газов.
Ультразвук может быть источником энергии для создания точечных и шовных соединений. Ультразвуковые колебания активно разрушают естественные и искусственные пленки, что позволяет сваривать металлы с окисленной поверхностью, покрытые слоем лака и т. п. Ультразвук снижает или снимает собственные напряжения и деформации, возникающие при сварке. Им можно стабилизировать структурные составляющие металла сварного соединения, устраняя возможность самопроизвольного деформирования сварных конструкций со временем.
В качестве источника энергии при сварке металлов ультразвук еще не нашел широкого применения, хотя этот способ имеет ряд преимуществ и особенностей по сравнению с контактной и холодной сваркой.
При сварке ультразвуком неразъемное соединение металлов образуется при совместном воздействии на детали механических колебаний высокой частоты и относительно небольших сдавливающих усилий. В принципе этот метод сварки имеет много общего с холодной сваркой сдвигом.
Для получения механических колебаний высокой частоты обычно используется магнитострикционный эффект, состоящий в изменении размеров, некоторых металлов и сплавов под действием переменного магнитного поля. Для ультразвуковых преобразователей обычно используют чистый никель или железо-кобальтовые сплавы. Изменения размеров магнитострикционных материалов очень малы: так, для никеля магнитострикционное удлинение составляет 40-10-6. Поэтому для увеличения амплитуды смещения и концентрации энергии колебаний, а также Для передачи механических колебаний к месту сварки используют волноводы или концентраторы, которые в большинстве случаев имеют сужающуюся форму.
Эксперименты показывают, что для сварки металлов достаточно иметь волноводы с коэффициентом усиления около 5, при этом амплитуда на конце волновода при холостом ходе должна быть 20—30 мкм. Магнитострикционный преобразователь и волноводы должны быть рассчитаны и изготовлены на заданную частоту ультразвукового генератора.
Основной узел машины для выполнения точечных соединений с помощью ультразвука — магнитострикционный преобразователь (рис. 8).
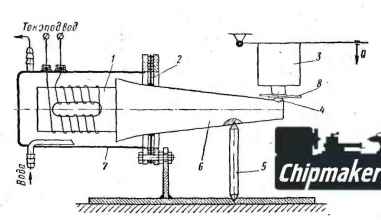
Рис.8. Схема установки для точечной сварки ультразвуком:1—магнитострикционный преобразователь;2— диафрагма;3 — механизм нажатия;4 — выступ;5 — маятниковая опора;6 — волновод;7 — кожух водяного охлаждения;8 — изделие
Его обмотка питается током высокой частоты от ультразвукового генератора. Охлаждаемый водой магнитострикционный преобразователь 1 изготовлен из пермендюра (К49Ф2), он служит для превращения энергии тока высокой частоты в механические колебания, которые передаются волноводу 6. На конце волновода имеется рабочий выступ 4. При сварке изделие 8 зажимают между рабочим выступом 4 и механизмом нажатия 3, к которому прикладывают усилие, необходимое для создания давления в процессе сварки.
Сварка происходит при включенном преобразователе. Высокочастотные упругие колебания передаются через волновод на рабочий выступ 4 в виде горизонтальных механических перемещений высокой частоты. Длительность процесса сварки зависит от свариваемого металла и его толщины, для малых толщин она исчисляется долями секунды.
Основные узлы машины для выполнения шовных соединений при помощи ультразвука (рис. 9): вращающийся магнитострикционный преобразователь 1 н волновод 2. Конец волновода имеет форму ролика 3. Изделие 5, подлежащее соединению, зажимают между вращающимся роликом 3 волновода и холостым роликом 4, Высокочастотные упругие колебания передаются через волновод на ролик, который вращается вместе с волноводом.
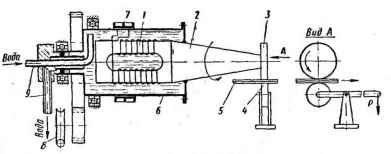
Рис.9.Схема установки для роликовой сварки ультразвуком:1—магнитострикционный преобразователь; 2 — волновод; 3 — сваривающий ролик;4 — прижимной ролик; 5 — изделие; 6 — кожух преобразователя; 7 — подвод тока от ультразвукового генератора;8 — привод; 9 — подвод охлаждающей воды
Изделие, зажатое между роликами, перемещается, и одновременно создается герметичное соединение.
Сварка по контуру, разработанная в МВТУ — МЭИ, обеспечивает получение герметичного шва практически самого сложного контура. Простейший ее вид — сварка по кольцу. В этом случае конический штифт, вставляемый в волновод, имеет форму трубки (рис. 10). При равномерном поджатии деталей к сваривающему штифту получается герметичное соединение по всему контуру.
Процесс ультразвуковой сварки происходит при воздействии сдвигающих высокочастотных колебаний, давления, приложенного перпендикулярно к поверхности листа, и теплового эффекта, сопровождающего процесс сварки. В результате в зоне сварной точки наблюдается небольшая пластическая деформация.
Исследование процесса образования сварного соединения при ультразвуковой сварке медных пластин толщиной 0,35 + 0,35 мм показывает, что при малом времени пропускания ультразвука (менее 0,05 с) сварка не происходит.
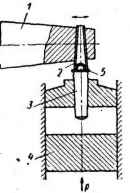
Рис.10.Схема установки для ультразвуковой сварки по контуру:1— волновод;2 — сменный полый штифт; 3 — сменный прижимной штифт; 4 — прижимная опора; 5 — свариваемое изделие
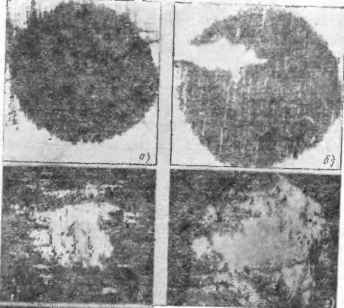
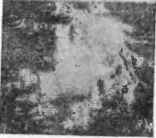
Рис.11. Макроструктура мест разрушения сварных соединений меди после различной продолжительности пропускания ультразвука. Х16
После разъединения образцов на их поверхности непосредственно под сваривающим выступом наблюдается пятно, имеющее полированную поверхность (рис. 11, а). Диаметр полированного пятна возрастает при увеличении времени сварки (рис. 11, а—д). При пропускании ультразвука в течение 0,1 с в местах контакта обнаруживаются не только зашлифованные поверхности, но и вы- рывы металла, свидетельствующие об образовании прочных соединений, так называемых узлов схватывания. На рис. 11, б виден один узел схватывания на зашлифованной поверхности.
Пропускание ультразвука в течение 0,73 с привело к дальнейшему увеличению площади зашлифованного пятна, при этом площадь узла схватывания также возросла. Вокруг основного узла схватывания возникли отдельные небольшие участки схватывания, удлиненные в направлении ультразвуковых колебаний. С увеличением времени пропускания ультразвука более 0,73 с площадь зашлифованного участка почти не изменяется (рис. 11, г, д), но площадь узлов схватывания начинает увеличиваться более интенсивно. При пропускании ультразвука свыше 1,06 с происходит разрушение сварного соединения с вырывом точки по всему контуру.
Проведенные измерения микротвердости поверхности зашлифованного пятна и основного металла вблизи пятна показали, что микротвердость поверхностного слоя зашлифованного пятна выше (Н50 42—44), чем у основного металла (Н50 28—30). Образование полированного пятна на свариваемых поверхностях указывает на то, что оно возникло вследствие трения под действием высокочастотных колебаний соприкасающихся поверхностей непосредственно под контактным выступом.
Таким образом, процесс ультразвуковой сварки происходит под действием трения, вызванного микроскопическим возвратно-поступательным перемещением трущихся поверхностей.
www.prosvarky.ru
Ультразвуковая сварка | Сварка металлов и материалов
Ультразвуковой сваркой выполняют различные виды соединений (рис. 69). Сваркой внахлест можно соединять две (рис. 69,а) или несколько (рис. 69,б) деталей, а также профили (рис. 69,в), фасонные (рис. 69,г) и пустотелые (рис. 69,д) детали. При монтаже радиоэлектронной аппаратуры ультразвуковую сварку применяют, например, для соединения цилиндрических деталей с плоскими (рис. 69,е) и торцового соединения с проволочными выводами (рис. 69,ж), когда проволочная заготовка подается в зону сварки через отверстие в инструменте или опоре и оплавляется в месте сварки. Сварку различных цилиндрических проводов можно выполнять при параллельном (рис. 69,з) или крестообразном взаимном расположении. Пустотелые выводы и контакты соединяют с платами (рис. 69,и) профильными инструментами и опорами. Применяют ультразвуковую сварку и для соединения монтажных лепестков с колпачками (рис. 69,к, л).
Перед ультразвуковой сваркой соединяемые поверхности детали очищают от загрязнений и жировых пленок. Эту операцию целесообразно выполнять в ультразвуковых ваннах. В случае невозможности применить ультразвуковую очистку эти поверхности протирают салфетками, смоченными бензином, ацетоном или слабыми щелочными растворами. Ровные и чистые поверхности свариваются быстрее и качественнее.
К особенностям операций ультразвуковой сварки относится содержание рабочего цикла. Рабочим цикл состоит из сжатия свариваемых заготовок при определенном (рабочем) усилии, собственно сварки при включенных ультразвуковых колебаниях, выдержки под рабочим или измененном усилии и освобождении сваренного материала. Время и последовательность исполнения каждого из указанных элементов рабочего цикла строго увязывается между собой и зависят от вида и свойств свариваемых материалов и акустических параметров процесса (амплитуды колебаний инструмента, частоты и мощности). Правильный выбор рабочего цикла сварки во многом предопределяет качество соединения.
Рис. 69. Соединения, выполненные ультразвуковой сваркой
Обычно при ультразвуковой сварке принимается такой цикл. Рабочее усилие прикладывается к свариваемым деталям до включения ультразвука и остается постоянным в течение всей сварки. После некоторой выдержки деталей под нагрузкой включается ультразвук и выполняется сварка. Затем выключают колебания и выдерживают детали в течение определенного времени под нагрузкой; происходит так называемая «проковка», т. е. окончательное формирование неразъемного соединения. Затем нагрузка снимается.
Практикуется, например, при сварке пластмасс изменение указанной последовательности. Вначале включают ультразвук, а затем прикладывают усилие. При этом в результате постепенного касания колеблющегося инструмента свариваемых деталей с поверхностей их интенсивно удаляют загрязнения, прежде чем наступает сварка. Снимается нагрузка после выключения ультразвука. Такой цикл обеспечивает надежное соединение материалов со значительной степенью загрязнения свариваемых поверхностей, однако при этом необходимо с большой точностью регулировать величину и время рабочего усилия.
Также вредно влияет на качество ультразвуковой сварки цикл, при котором колебания инструмента выключаются после нагрузки. При сварке пластмасс по такому циклу можно наблюдать вспучивание в зоне сварного соединения и другие дефекты.
При ультразвуковой сварке металлических материалов, когда направление колебаний инструмента совпадает с плоскостью сварки, колебания могут передаваться свариваемым деталям. Это вредно сказывается на качестве сварки (появляются трещины и другие дефекты) Для предотвращения сдвига детален при ультразвуковой сварке детали необходимо перед сваркой прочие скрепить между собой. Место крепления должно располагаться как можно ближе к зоне сварки. Для этой цели применяют прихваты и струбцины с эластичными (резиновыми) зажимными элементами. Удобны быстродействующие зажимные устройства (например, пневматические), расположенные вблизи инструмента сварочного станка и являющиеся его элементами. Такие зажимы применены, в частности, при точечной ультразвуковой сварке листовых материалов. После перемещения свариваемых детален на шаг сварки (расстояние между двумя соседними точками сварки) срабатывает зажим и прочно прижимает детали к опоре. Затем автоматически включаются колебания сварочного инструмента и рабочее усилие - происходит сварка. После заданной выдержки снимают нагрузку и ультразвуковые колебания, а затем зажим освобождает свариваемые детали для очередного их перемещения.
Такие зажимы предотвращают одновременно проворот деталей во время сварки, что наблюдается при сварке с ультразвуком. Для этих же целей применяют различные сварочные приспособления - кондукторы, которые фиксируют детали относительно друг друга и по отношению к инструменту, и также обеспечивают их крепление при сварке. Для ультразвуковой сварки миниатюрных деталей применяют «плавающие» и поворотные столы и другие специальные приспособления.
При сварке крупногабаритных листовых деталей для предотвращения их провисания и облегчения работы оператора рядом со сварочным станком располагают столы-рольганги или другие вспомогательные устройства, если таковые не предусмотрены конструкцией самого станка. Такие устройства применяют, в частности, при шовной, а нередко и точечной сварке.
Похожие материалы
www.metalcutting.ru
Ультразвуковая сварка металлов — УЛЬТРАЗВУКОВАЯ ТЕХНИКА — ИНЛАБ
Ультразвуковая сварочная установка И100-7/5
Наше предприятие разрабатывает, изготавливает и поставляет оборудование для ультразвуковой сварки металлов. Ультразвуковая сварочная установка И100-7/5 предназначена для контактного сваривания ультразвуком изделий из различных металлов. Ультразвуковая сварка выгодно отличается от других способов сварки отсутствием протекания электрического тока в зоне сварки; возможностью сваривания высокотеплопроводных материалов, серебро, медь и т.д.; возможностью сваривания разнородных и разнотолщинных материалов; сварка без снятия загрязнений и оксидных пленок.
|
|
Сварочные волноводы и приспособления для закрепления свариваемых деталей разрабатываются и изготавливаются под конкретную конфигурацию сварочного шва и свариваемых металлов, и их стоимость определяется индивидуально.
Сварочная установка может быть изготовлена по согласованному техническому заданию Заказчика.
Гарантийные обязательства - 12 месяцев.
Образцы свариваемых металлов:
![]() |
![]() |
|
Медный многожильный провод сечением 16 мм2 и медные выводы реле электросчетчиков на 100А | Медный многожильный провод и медные клеммы с покрытием и без покрытия |
Сварка медного многожильного провода с медной клеммой (в полном формате в разделе ВИДЕО) |
|
![]() |
![]() |
![]() |
![]() |
![]() |
Медная шина толщина 2 мм - серебро лист толщина 0,15 мм |
Медный провод сечение 1.5 мм2 - лист сталь толщина 0.5 мм |
Медная шина сечением 4.5 Х 2 мм - соединение |
Медный провод сечение 1.5 мм2 - лист латунь толщина 0.25 мм |
Медная шина толщина 2 мм - никель лист толщина 0.3 мм |
С ценами и основными техническими параметрами установки для ультразвуковой сварки металлов можно ознакомиться в разделе Цены (файл Ультразвуковые сварочные установки)
Версия для печатиutinlab.ru