Преимущества сварки в среде защитных газов. Сварка меди полуавтоматом в среде аргона
Сварка меди аргоном - особенности и видео-уроки
Несмотря на то, что сварку меди можно произвести привычной ручной сваркой, с помощью металлических или угольных электродов, в последнее время, чаще всего используется — высокоэффективная сварка меди аргоном.
Универсальная аргоновая сварка позволяет без проблем варить крупногабаритные и мелкие детали из меди.
Как известно, из-за высокой тепло- и электропроводимости, а также высокой стойкости к агрессивным средам и коррозии медь применяют в энергетическом и химическом машиностроении.
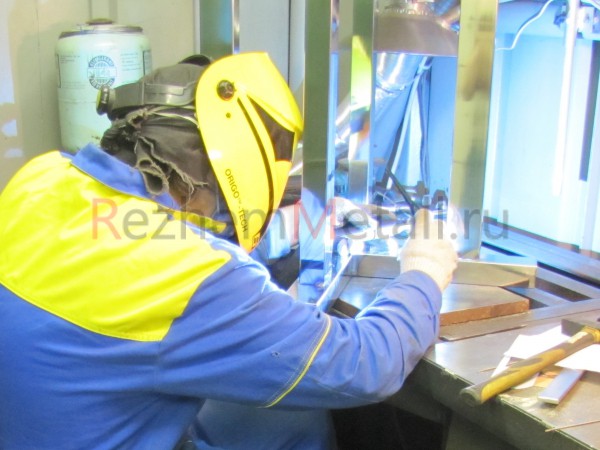
Фото процесса
А так как медь – очень хороший проводник, то и работа с ней требует довольно специфичного оборудования.
Сварка аргоном производится при прямой полярности и постоянном токе с помощью вольфрамового неплавящегося электрода. Температура аргонно-дуговой сварки должна достигать 300-400 градусов.
Прежде чем начать варить, дугу следует нагреть на графитовой или угольной пластинке. Не рекомендуется зажигать дугу сразу же на изделии, которое вы будете варить – это загрязнит электрод.
Необходимо помнить, что сварка меди аргоном осуществляется в вертикальном, потолочном или нижнем положениях.
Особенности работы с медью
Хотя сварку медных деталей можно производить с помощью специальных электродов, все-таки для этих целей лучше всего использовать неплавящиеся электроды из вольфрама.
Такие электроды хорошо «проваривают» швы, в отличие от сварки обычными электродами, они получаются прочными, ровными и чистыми.
Так как во время сварочных работ используется смесь газов: аргона и азота, то для безопасности сварка должна производиться только специально подготовленным сварщиком.
Вольфрамовые неплавящиеся электроды бывают нескольких видов: ЭВЛ и ЭВИ. ЭВЛ – это лаптанированные электроды, а ЭВИ – итерированные электроды.
Для сварки деталей из меди с помощью аргона используют именно итерированные электроды из вольфрама. Если толщина медных деталей свариваемых аргоном превышает 5 мм, то применяют обязательную разделку кромок.
Видео:
Без разделки кромок всю толщину металла невозможно будет прогреть, так как медь обладает высокой теплопроводностью.Следует знать, что для металла толщиной 5 – 12 мм используют одностороннюю разделку, а если толщина металла больше указанной, то разделывают обе кромки обрабатываемой детали.
Качество сварного шва также зависит от примесей, содержащихся в меди – чем чище медь, тем качественней шов. Кроме вольфрамовых электродов, также используется еще и присадочная проволока.
Присадочная проволока изолирует свариваемые детали от кислорода, который все же попадает в область сварки.

Таблица режимов сварки меди
Материал присадочной проволоки непременно должен соответствовать составу того металла, который предполагается варить..
В качестве присадки можно взять медную проволоку, которая содержит большое количество марганца. С одной стороны марганец надежно связывает поступающий в область сварки кислород, но с другой – примеси марганца снижают прочность сварного шва.
Поэтому в качестве присадки лучше всего использовать проволоку с содержанием каких-либо редкоземельных материалов.
Такие материалы полностью удаляют из швов кислород, но при этом не остаются в составе шва, как примеси марганца.
К сожалению, присадочная проволока из редкоземельных материалов весьма дорога, из-за чего немногие решаются ее использовать, отдавая предпочтение недорогой медной проволоке.
Преимущества использования аргона при работе с медью
Как уже говорилось выше, сварка меди аргоном считается самой чистой. При такой ее разновидности — почти не выделяются пары оксидов.
Во время аргоновой сварки на пол не падают раскаленные искры, которые могли бы повредить полы и настенные покрытия.
Таким образом, сварку аргоном можно проводить даже в жилых помещениях, не боясь при этом что-либо испортить или испачкать.
Еще одно неоспоримое преимущество аргоновой сварки – это качество. При сварке меди аргоном шов получается чистым и аккуратным, без шлаков и подрезов.
С помощью аргона можно на малых токах варить даже тонколистовые 0,5 мм изделия из меди.
К тому же, аргоновая сварка позволяет работать со сложными металлами, которые не поддаются обычной сварке, а также восстанавливать прежний объем детали, наплавляя металл поверх нее.
Видео:
Если у вас есть определенные знания в этой области, то можете произвести все работы самостоятельно, но перед этим — рекомендуется посмотреть видео сварки меди аргоном и приобрести соответствующее оборудование.Для домашнего использования идеально подойдет специальное многофункциональное оборудование.
Если же планируется больший объем сварочных работ, например, на производстве, то в данном случае потребуется приобрести несколько аппаратов, которые обладают разными функциональными возможностями.
rezhemmetall.ru
Преимущества сварки в среде защитных газов
Среди самых эффективных способов сваривания металлов выделяется сварка в защитных газах. Специальные газы, поступающие в область сваривания, предотвращают поступление воздуха, который оказывает негативное влияние на свойства соединения материалов.
Благодаря этому сварные швы получаются чистыми (без шлака), герметичными (без пор) и соответствуют заданным характеристикам при соблюдении рекомендаций ГОСТ 14771-76.
Ручной способ и сваривание в камере
Проводимая на аппаратах полуавтоматического типа, ручная дуговая сварка в защитном газе бывает двух видов: локальная и общая в камере. Самая распространенной является локальная защита в струе инертного газа, который истекает из сопла сварочной горелки.
Местная защитная среда позволяет варить изделия любой сложности и любых габаритов, но не дает стопроцентной гарантии. Надежная защита обеспечивается только в зоне ламинарного потока газа, где возникает турбулентность, происходит захват воздуха и в этой области качество шва резко падает. Поэтому задача сварщика заключается еще и в расположении сварочной ванны в зоне ядра потока.
Организация нейтральной среды в камере обеспечивает стопроцентную защиту и позволяет получить сварной шов требуемого качества.
В камере создается избыточное давление, где размещаются свариваемые детали и аппарат для сварки с проволокой. В камерах обычно производят сварку металлов высокой химической активности, типа молибдена или титана.
Сварку в защитном газе можно проводить плавящимся электродом и с таким же успехом – неплавящимся.
Достоинства и слабые места процесса
К преимуществам работы в защитной газовой среде можно отнести следующее:
- качество шва значительно лучше, чем при использовании обычной электродуговой сварки;
- часть защитных газов имеют невысокую стоимость, но все же обеспечивают высочайшее качество шва;
- освоение данной технологии сварки не представляет никаких трудностей для сварщиков имеющих опыт работы с другим технологическим оборудованием;
- в защитных газах может производиться сварка как тонкостенных, так и толстостенных заготовок;
- процесс сварки идет с высокой производительностью;
- значительно упрощается работа с алюминием, цветными металлами и их сплавами, коррозионностойкой сталью;
Недостатки у данной технологии имеются, но не так существенны. Для работы на открытом воздухе требуются защитные экраны для предотвращения сдувания потока газа с области сваривания.
При сварке в закрытых помещениях должна быть вентиляция или обеспечено проветривание. Аргон, применяемый в сварочных работах, имеет высокую стоимость.
Какие газы применяют
Для защиты от воздействия воздуха применяют газ, которые условно разделяют на две группы инертные и химически активные.
Инертные газы всем хорошо известны – аргон, гелий и их сочетание. Вытесняя воздух из зоны окружения свариваемых заготовок, они не реагируют с металлом и не растворяются в нем.
Их применяют при сваривании алюминия, магния, титана и сплавов. В специальной литературе такой вид сварки с защитной средой из инертных газов обозначается как MIG (металл, инертный газ).
Если применять неплавящийся электрод для сварки в среде защитных газов, то такой процесс будет отлично подходить для соединения тугоплавких сталей, химически активных металлов или особо ответственных соединениях.
Сварка с активными газами получила название MAG сварки (металл, активный газ). К активным реактивам относят углекислоту, азот, водород, кислород.
Наибольшее распространение получила углекислота благодаря своей низкой стоимости. Для сравнения, азот стоит в 1,5 раза дороже, кислород в 3, водород в 4 раза, аргон и гелий в 45 и 156 раз соответственно.
В углекислоте
Сварка полуавтоматом в углекислоте получила широкое применение из-за ее дешевизны. Углекислота, попадая в область расплава, защищает его от разрушающего воздействия воздуха.
Но из-за высокой температуры в районе сварочной ванны она разлагается на окись углерода и кислород, поэтому в области сваривания оказываются три газа: углекислота, окись углерода и кислород.
Чтобы не допустить окисления, в сварочную проволоку добавляют кремний и марганец, который реагирует с кислородом раньше железа. За счет этого гасятся реакции образования вредных окисей.
При этом углекислый газ сохраняет свои изолирующие свойства, а соединения кремния и марганца вступают в реакцию друг с другом, в результате чего получается легкое по плотности вещество, которое всплывает в расплаве. Образовавшийся шлак впоследствии легко удаляется.
Перед использованием углекислоты нужно обязательно удалить воду из баллона. Для этого его переворачивают и сливают воду, через 20 минут процедуру повторяют, в противном случае пары воды вызовут пористость шва.
В азотной среде
Азот используют при сваривании деталей из меди и нескольких видов нержавеющей стали. Это обусловлено тем, что азот не реагирует с медью. В качестве электродов используются графитовые или угольные прутки, применение вольфрамовых прутков приводит к их перерасходу из-за образования легкоплавких соединений.
Работают на токах 150-500 А и напряжении дуги 22-30 В. Расход азота находится в пределах 3-10 л/мин. Газ хранится в баллонах при давлении 150 атмосфер.
Сварочное оборудование ничем не отличается от других видов сварки использующих газы, только в горелке предусмотрено специальное крепление для угольного электрода.
Оборудование
В аппаратуре для производства сварочных работ в защитной среде в качестве источника питания чаще всего используют инверторы с широкой регулировкой величины сварочного тока.
Они снабжены устройством подачи сварочной проволоки и газовую систему с баллонами, шлангами, понижающими редукторами. Сварку плавящимся электродом в защитных газах ведут постоянным или импульсным высокочастотным током.
Главными параметрами, характеризующими оборудование, является ток, который можно изменять; напряжение для зажигания и стабильного горения дуги; скорость подачи проволоки, ее толщина. Режимы сварки полуавтоматом многообразны. В зависимости от свариваемых материалов сила тока и другие параметры могут значительно меняться.
Перед началом сварочных работ в защитном газе свариваемые поверхности требуется очистить от всевозможных загрязнений. В первую очередь необходимо очистить кромки от оксидной пленки, ржавчины, жира, масла. Для этого применяются стальные скребки, растворители, нетканые материалы.
Применение защитных газов требует соблюдения определенной последовательности операций. Сначала подается защитный газ, затем включается источник питания, начинает подаваться присадочная проволока и зажигается дуга, потом только начинается процесс сварки.
После гашения электродуги, еще 10-15 секунд в зону сварки подают инертный газ. Это делается для того, чтобы избежать пагубного влияния атмосферы на шов.
В зависимости от видов свариваемых металлов, их толщины используют различные защитные газы. Например, аргон обеспечивает стабильность электрической дуги, а гелий позволяет получать более глубокую проварку шва.
При сварке меди используется водород. Наиболее универсальным газом, который может использоваться практически при сварке любых металлов является аргон. Только его высокая стоимость вынуждает применять более дешевые газы типа углекислого или азота.
Как и электродуговую, в автоматическом режиме применяют технологию сварочного процесса в газовой среде. Она легко поддается автоматизации и используется в роботизированных комплексах в больших производствах. Полуавтоматы широко применяются в мелких мастерских и автосервисах.
svaring.com
Аргонодуговая сварка меди | Мир сварки
Назначение
Настоящая инструкция распространяется на ручную аргонодуговую сварку меди.
Инструкцией надлежит руководствоваться при проектировании, разработке технологических процессов, изготовление, контроле и приемке сварных узлов.
Отступления (ужесточение или снижение требований) от настоящей инструкции могут быть внесены в технологическую документацию на изделие по согласованию с главным технологом и представителем заказчика.
Материалы, оборудование, приспособления, инструмент даны в приложениях №1 и №2.
Выполнение аргонодуговой сварки меди должно производиться дипломированными сварщиками при соблюдении правил техники безопасности, изложенных в инструкции по ТБ.
Подготовка деталей и сварочной проволоки к сварке
Обезжирить поверхность деталей, а также сварочную проволоку, методом протирки хлопчатобумажной тканью, смоченной в бензине. Разрешается выполнять обезжиривание деталей в соответствии с соответствующей технологической инструкцией.
Удалить напильником заусеницы с кромок свариваемых деталей.
Зачистить стальной щеткой до металлического блеска, с обеих сторон на ширину 15-20 мм, кромки деталей, изготовленных из листа или штамповкой.
Разрешается вместо зачистки выполнять травление по соответствующей технологической инструкции.
Присадочную проволоку травить по соответствующей технологической инструкции.
Обезжирить методом протирки хлопчатобумажной тканью, смоченной в бензине поверхность деталей после механической обработки.
Хранить детали и проволоку после обработки в чистом и сухом помещении не более трех суток до сварки. Если до сварки прошло более трех суток операции обезжиривания повторить.
Сборка, прихватка и сварка
Подготовить пост аргонодуговой сварки к работе, выполняя требования инструкции ТБ.
Подключить сварочную горелку к источнику постоянного тока для выполнения работ на прямой полярности.
Установить на оборудовании ориентировочной режим сварки согласно таблице 1.
Закрепить вольфрамовый электрод в горелке таким образом, чтобы вылет его из сопла горелки не превышал 5-12 мм.
Выключить подачу аргона за 6-10 с до начала сварки и приступить к работе.
Выполнить сварку технологических образцов.
Выключить подачу аргона на ранее чем через 10-15 с после окончания сварки.
Проверить качество сварки технологических образцов в соответствии с требованиями раздела «Контроль качества сварки» и произвести корректировку режима сварки, если в этом будет необходимость.
Установить свариваемый узел на рабочем столе сварщика в положении удобном для сварки.
Подать охлаждение на свариваемый узел, если это предусмотрено маршрутной картой.
Протереть кромки деталей бязевым тампоном, смоченным в растворителе.
Произвести прихватку кромок свариваемых деталей, если сборка узла выполнена с зазором более 0,5 мм, или если сборочно-сварочное приспособление не обеспечивает жесткой фиксации свариваемых деталей друг относительно друга.
Выполнить прихватку в виде отдельных точек начиная с участков наилучшего сопряжения кромок свариваемых деталей. Присадочный материал применять по мере надобности.
Произвести прихватку по всей длине свариваемого шва. Шаг между прихватами установить опытным путем.
Зачистить механическим путем до металлического блеска зону прихваток и сами прихватки.
Протереть зачищенные участки бязевым тампоном, смоченным в растворителе.
Приступить к сварке узла соблюдая следующие требования:
Производить сварку необходимо путем непрерывного перемещения вольфрамового электрода вдоль оси шва без остановок.
Наклонять горелку при сварке в сторону противоположную направления сварки таким образом, чтобы ось вольфрамового электрода составляла с осью сварного шва 60-80°.
Применять сварочную проволоку необходимо по мере надобности для выполнения расчетного размера шва.
Вносить, в зону сварки присадочную проволоку таким образом, чтобы угол между вольфрамовым электродом и присадкой составлял 90°.
Производить перекрытие начала шва при окончании сварки 10-20 мм, при возобновлении сварки, после случайного и вынужденного обрыва дуги, окончание шва перекрыть на 15-20 мм.
Произвести контроль ОТК сварных узлов и деталей после окончания работ согласно разделу «Контроль качества сварки».
Ориентировочные режимы сварки даны в таблице 1.
1,0 | 60-70 | 50-75 | 2,0 | 1,6-2,0 | 6-8 |
1,5 | 75-90 | 60-90 | 2,0 | 1,6-2,0 | 8-10 |
2,0 | 90-105 | 75-105 | 2,0 | 2,0-2,5 | 9-11 |
2,5 | 90-115 | 90-115 | 3,0 | 2,0-2,5 | 11-12 |
3,0 | 115-130 | 115-130 | 3,0 | 2,0-3,0 | 11-12 |
4,0 | 115-145 | 115-145 | 3,0 | 2,0-3,0 | 11-12 |
5,0 | 130-145 | 130-145 | 3,0 | 2,0-3,0 | 12-14 |
6,0 | 145-160 | 130-160 | 3,0 | 2,5-3,0 | 12-14 |
Контроль качества сварки
Выполнять сплошной контроль качества сварки внешним осмотром.
Производить осмотр сварных швов по всей длине с обеих сторон.
Произвести разбраковку дефектов сварных швов согласно требованиям таблицы 2.
Подваривать дефектные участки сварных швов допускается не более двух раз.
Непровары | Не допускаются. Устраняются повторной сваркой |
Поры, раковины диаметром 0,3-1 мм, но не более 5 шт на длине 100 мм шва | Не допускаются. Устраняются повторной сваркой |
Прожоги суммарной длиной не более 10% длины шва и шириной или диаметром не более ширины шва | Не допускаются. Устраняются повторной сваркой |
Трещины | Не допускаются. Устраняются повторной сваркой |
Скопление мелких пор диаметром не более 0,3 мм, но не более одного скопления на длине шва, при этом превышать 10 % швов длиной до 100 мм и 20 % для швов длиной более 100 мм | Допускаются |
Проплав в стыковых, угловых швах, не мешающий элементам дальнейшей сборки и не представляющий пористого провисания металла | Допускаются |
Вспомогательные материалы
- Вольфрам лантанированный в виде прутков ТУ-48-19-27-72.
- Аргон газообразный высший сорт или первый сорт ГОСТ 10157-73.
- Проволока сварочная марки М1 или М2 ГОСТ 16130-72.
- Бензин авиационный Б70 ГОСТ 1012-72.
- Ткань хлопчатобумажная бязевой группы ГОСТ 11680-76.
- Перчатки трикотажные ГОСТ 1108-74.
- Шкурка шлифовальная бумажная водостойкая ГОСТ 10054-75
- Бензин А-76 ГОСТ 2084-77 и «Галоша» ТУ 38-401-67-108-92.
Оборудование, приспособления, инструмент
- Источник питания для сварки в среде защитных газов типа ПС-300, ПСО-300, ПСО-500, ВКСМ-1000 или УДГ-101 с комплектом сварочных горелок, цанг, сопел.
- Реостат балластный типа РБ-200 или РБ-300.
- Ротаметр марки РМ-II или РМ-IV ГОСТ 13045-67.
- Редуктор кислородный типа РК-30, РК-50 или РК-14 ГОСТ 6268-78.
- Набор трубок резиновых технических тип 4 для подачи защитных газов и воды в горелку ГОСТ 5496-78.
- Шлем маска защитная сварочная с набором защитных сварочных стекол ЭС-100, ЭС-300, ЭС-500 ГОСТ 1361-69.
- Очки герметичные защитные ГОСТ 9496-60.
- Сборочно-сварочные приспособления.
- Напильник ГОСТ 1465-69.
- Щетки стальные из нержавеющей проволоки ∅0,2-0,3 мм для зачистки металла шва и деталей.
- Штангенциркуль ГОСТ 166-73.
weldworld.ru
Сварка меди аргоном

Видео сварки меди:
В чистом виде медь редко где применяется, это очень осложняет сварочный процесс. Наличие примесей характеризует физико-химические свойства сплава. К данным свойствам относят: высокий коэффициент термического расширения, высокую теплопроводность, высокую линейную укладку, высокую текучесть, высокую чувствительность к водороду, легкую окисляемость, интенсивное испарение цинка.Все вышеперечисленные свойства очень усложняют сварку меди. На подготовительном этапе проходит тщательная разделка и очистка поверхностей именно перед сваркой. Зазор при сварке между поверхностями должен быть очень мал не более 2 мм, из-за этого детали сжимают между собой. Сварку меди производят в среде защитных газов, ими могут являться гелий, азот или аргон. Металл толщиной до 5 мм, перед началом сварки должен быть предварительно подогрет 250-300 С.При сварке начальный шов накладывается без колебаний электрода. Сварку нельзя прерывать, корень шва должен быть проварен тщательнейшим образом. Шов проковывают после окончания сварки, а после отжигают при температуре 600 С.Сварку меди можно проводить разнообразными способами: газовой, ручной, автоматической под флюсом, электрошлаковой, дуговой и другими. И каждый из вышеперечисленных способов имеет свои недостатки и достоинства.Кроме статьи "Сварка меди аргоном" смотрите также:
nanolife.info
Сварка в среде защитных газов меди и ее сплавов
Сварка в среде защитных газов меди и ее сплавов производится неплавящимся и плавящимся электродами. Неплавящимся вольфрамовым электродом сваривают в аргоне без предварительного подогрева медь толщиной до 4-6 мм, в гелии и азоте толщиной до 6-8 мм. Плавящимся электродом можно сваривать без подогрева металл большей толщины: в аргоне до 6-8 мм, в гелии и азоте до 10-12 мм. Необходимость применения предварительного, а при больших толщинах и сопутствующего подогрева серьезное затруднение при сварке меди в среде защитных газов. Гелий и азот обеспечивают более высокий по сравнению с аргоном КПД процесса сварки, поэтому они заслуживают предпочтения. Однако аргон, являясь наиболее универсальным защитным газом, широко применяется и для меди (первый и второй сорта по ГОСТ 10157—73). Целесообразно использовать газовые смеси (например, следующего объемного содержания: 70-80 % Аr, 20-30% N2) для экономии аргона и увеличения производительности сварочных работ.
Сварку вольфрамовым электродом ведут на постоянном токе прямой полярности. Медь толщиной до 5-6 мм можно сваривать без разделки кромок. Для металла больших толщин применяется V или X образная разделка с углом раскрытия 60-70°.
Техника сварки в разных защитных средах различается в основном необходимостью поддержания разных по длине дуг. Для аргона и гелия длина дуги должна быть как можно меньше (обычно около 3 мм). Значительно длиннее дуга в азоте (около 12 мм). Поэтому в зависимости от среды, в которой выполняется сварка меди, резко различаются и статические характеристики дуг зависимость напряжения дуги от величины сварочного тока. При данном сварочном токе напряжение дуги, а следовательно, ее мощность и тепловложение самые высокие в азоте (в 3-4 раза больше, чем в аргоне). В гелии эти показатели примерно в 2 раза выше, чем в аргоне.
При сварке в азоте швы более склонны к порообразованию, особенно при малых размерах сварочной ванны и повышенной скорости ее охлаждения Это объясняется тем, что в азоте металл сварочной ванны проявляет тенденцию к уменьшению жидкотекучести. Расход защитного газа, зависящий во многом от его теплофизичееких свойств и плотности, в среднем следующий: аргона 8-10 л/мин, гелия 10-20 л/мин и более, азота 15-20 л/мин. Смеси газов для сварки меди применяются редко. Для повышения скорости сварки рекомендуется смесь аргона с азотом или гелием, где объемное содержание азота или гелия составляет 30%. При сварке используют графитовые подкладки или медные пластины, охлаждаемые водой.
Сварка в среде аргона обычно ведется справа налево при наклоне электрода по отношению к изделию углом вперед на 80-90°; угол наклона присадочной проволоки 10-15°, вылет неплавящегося электрода 5-7 мм. При сварке в среде азота применяются пониженные по сравнению с аргоном сварочные токи. Сварка меди неплавящимся электродом выполняется с использованием присадочного металла из раскисленной меди, медно-никелевого сплава МНЖКТ5-1-0,2-0,2, бронзы Бр.КМц3-1, Бр.ОЦ4-3, а также специальных сплавов, содержащих эффективные раскислители РЗМ. Оптимальные параметры режимов предварительного подогрева и сварки меди неплавящимся электродом выбирают исходя из номограммы.
Распространенная технология аргонодуговой сварки меди с применением присадочных проволок МНЖКТ5-1-0,2-0,2 и Бр.КМц3-1, которые позволяют получать швы удовлетворительного качества, в ряде случаев не обеспечивают теплофизических свойств металла шва и эксплуатационной надежности сварных соединений. Для сварки изделий электротехнической промышленности создана присадочная проволока марки Св.МЛ0,2. Электрическая проводимость швов составляет 80-95% электрической проводимости основного металла. Наилучшие свойства при сварке кислородсодержащей меди обеспечиваются при использовании в качестве защитной среды гелия. Угол загиба сварных соединений составляет 180°; σв =190÷210 МПа.
Таблица 1. Ориентировочные режимы сварки меди в среде аргона неплавящимся электродом.
b, мм | dЭ, мм | dпр, мм | Число проходов (кроме подвароч-ного) | Iсв, А | Расход аргона, л/мин |
1,2* | 2,5-3,0 | 1,6 | 1 | 120-130 | 7,0-8,5 |
1,5* | 2,5-3,0 | 2,0 | 1 | 140-150 | 7,0-8,5 |
2,5* | 3,5-4,0 | 2,5-3,0 | 1 | 220-230 | 7,5-9,5 |
3* | 3,5-4,0 | 2,5-3,0 | 1 | 230-240 | 7,5-9,5 |
10** | 4-4,5 | 3,0 | 3 | 1-й проход 200-350 | 7-8 |
4-4,5 | 5,0 | 2-й проход 200-350 | 7,0 | ||
4-4,5 | 6,0 | 3-й проход 200-400 | 7,0 | ||
4-4,5 | 3,0 | Подварочный шов 250-350 | 7,0 | ||
12** | 4-4,5 | 3,0 | 4 | 1-й проход 250-350 | 8-10 |
4-4,5 | 5,0 | 2-й проход 250-400 | 8-10 | ||
4-4,5 | 6,0 | 3-й проход 300-450 | 8-10 | ||
4-4,5 | 6,0 | 4-й проход 300—450 | 8-10 | ||
4-4,5 | 3,0 | Подварочный шов 250-350 | 8-10 | ||
19** | 5-5,5 | 3,0 | 6 | 1-й и 2-й проходы 250-400 | 10-12 |
5-5,5 | 5,0 | 3-й и 4-й проходы 250-450 | 10-12 | ||
5-5,5 | 6,0 | 5-й и 6-й проходы 300-550 | 10-12 | ||
25*** | 5-5,5 | 3,0 | 8 | 1-й и 2-й проходы 250-400 | 12-14 |
5-5,5 | 5,0 | 3-й и 4-й проходы 300-450 | 12-14 | ||
5-5,5 | 6,0 | 5-й и 6-й проходы 300-550 | 12-14 | ||
5-5,5 | 6,0 | 7-й и 8-й проходы 350-600 | 12-14 |
* Без разделки кромок,
** V-образная разделка кромок, α = 70-90°,
*** Х-образная разделка кромок, α = 70-90°.
Таблица 2. Ориентировочные режимы сварки тонколистовой меди в среде азота неплавящимся электродом.
b, мм | dЭ, мм | dпр, мм | Iсв, А | Диаметр выходного сопла горелки, мм |
1,2-1,5 | 2,5-3,0 | 1,6-2,0 | 120-130 | 6-8 |
2,5-3,0 | 3,0-4,0 | 2,5-3,0 | 200-230 | 8-10 |
Наиболее часто встречающиеся дефекты сварных швов на меди пористость и горячие трещины. Образование трещин в процессе кристаллизации сварных швов связано с наличием остаточных примесей в основном металле, таких, как висмут, кислород, свинец, сера, селен, теллур, фосфор.
По характеру влияния на образование трещин примеси могут быть разделены на три группы.
1. Примеси, повышающие склонность к образованию и распространению трещин при сварке висмут, теллур, селен, фосфор, свинец. Указанные примеси, кроме фосфора, оказывают вредное влияние на свариваемость меди при их концентрациях в тысячных и десятитысячных долях процента. Влияние фосфора проявляется при его содержании в меди более 0,01%. Наибольшее влияние оказывают висмут и теллур. Свинец начинает существенно влиять только при больших скоростях сварки (более 14 м/ч), а пои введении его в медь, раскисленную фосфором, даже уменьшает склонность к образованию и распространению трещин.
2. Примеси, оказывающие в зависимости от концентрации переменное влияние на образование и распространение трещин. При малых концентрациях (до 0,01 %) они увеличивают склонность к образованию и распространению трещин, а при больших уменьшают ее. Такими примесями являются кислород, сера, кадмий.
3. Примесь, практически не влияющая на образование трещин, мышьяк. По характеру влияния на образование кристаллизационных трещин легирующие добавки (при содержании их до 0,6%) можно разделить на следующие группы: элементы, уменьшающие склонность швов к образованию и распространению трещин, хром, ниобий, иттрий, в меньшей степени титан, марганец, ванадий, кремний; элементы, практически не влияющие на образование трещин, но уменьшающие склонность к их распространению, железо, никель, кобальт, алюминии, цинк; элементы, оказывающие переменное влияние на образование трещин в зависимости от их концентрации и скорости сварки, бор, цирконий, магний.
Рис. 1. Рекомендуемые режимы подогрева и сварки, формы разделок меди для ручной сварки неплавящимся электродом.
Такое действие легирующих добавок связано с влиянием их на характер кристаллизации и различной раскисляющей способностью по отношению к меди.
Повышенной склонностью к образованию горячих трещин характеризуются также комплексно-легированные медно-никелевые и марганцево-медные сплавы, алюминиевые и оловянные бронзы. При сварке сплавов на медной основе возможно образование горячих трещин как в металле шва, так и в зоне термического влияния. Горячие трещины в металле шва, как правило, обусловлены широким эффективным интервалом кристаллизации сплавов. Основной причиной образования таких трещин можно считать низкие пластические свойства этих сплавов при повышенных температурах, обусловленные наличием провала пластичности, который наблюдается в большинстве сплавов на медной основе. Температурные границы и минимальная пластичность в этом интервале для разных сплавов различны. Чем больше интервал потери пластичности, чем больше он смещен в область низких температур и чем меньше пластичность в этом интервале, тем выше склонность сплава к образованию трещин. Наибольшей склонностью к горячим трещинам в металле шва обладают марганцево-медные сплавы, наименьшей алюминиевые бронзы. Образованию трещин в ЗТВ подвержены медно-никелевые сплавы, а наиболее стойкими против образования таких трещин являются алюминиево-никелевые и марганцево-алюминиевые бронзы.
Для обеспечения отсутствия трещин в ЗТВ сплавов системы Сu-Ni-Аl и Мn-Сu сварку производят узкими валиками с охлаждением после каждого прохода до температуры ниже 100° С.
Для повышения стойкости металла шва против горячих трещин разработаны сварочные проволоки Бр.АЖНМц8,5-4-5-1,5; Бр.МцАЖН12-8-3-3; ММц40. С применением указанных материалов производится ручная аргонодуговая сварка неплавящимся электродом на постоянном и переменном токах и полуавтоматическая аргонодуговая сварка плавящимся электродом. Механические свойства сварных соединений обеспечиваются практически на уровне свойств основного металла.
Таблица 3. Механические свойства медных сплавов и их сварных соединений.
Материал | σв, МПа | σ0,2, МПа | δ, % | ψ, % |
Алюминиево-никелевая бронза | ||||
Основной металл | 642 | 238 | 22,9 | - |
Сварное соединение | 691 | 390 | 18,4 | - |
Наплавленный металл | 703 | 294 | 27,5 | 26,4 |
Марганцево-алюминиевая бронза | ||||
Основной металл | 663 | 280 | 32,0 | - |
Сварное соединение | 701 | 404 | 17,4 | - |
Наплавленный металл | 766 | 464 | 28,1 | 34,2 |
Медно-никелевый сплавы с 5-6% Ni | ||||
Основной металл | 366 | - | 68,5 | - |
Сварное соединение | 376 | - | 38,9 | - |
Наплавленный металл | 378 | 239 | 32,0 | 45,8 |
Медно-никелевые сплавы с 40% Ni | ||||
Основной металл | - | - | - | - |
Сварное соединение | - | - | - | - |
Наплавленный металл | 596 | 279 | 40,6 | 45,3 |
Марганцево-медный сплав | ||||
Основной металл | 525 | 310 | 35,3 | 44,8 |
Сварное соединение | 526 | 320 | 30,0 | 44,6 |
Наплавленный металл | 532 | 240 | 36,7 | 48,0 |
Высокую производительность сварочных работ обеспечивают новые эффективные способы и приемы сварки. К ним относится ручная гелиеводуговая сварка меди на форсированных режимах (Iсв =700÷900 А; Uд =25÷30 В), которая позволяет успешно решать вопрос изготовления и ремонта медных конструкций. Резко повышает производительность работ двухдуговая сварка неплавящимся электродом.
Таблица 4. Ориентировочные режимы сварки меди плавящимся электродом.
Параметр | Защитный газ | |
Гелий | Азот | |
Диаметр электродной проволоки из Бр.КМц3-1, мм | 2,5 | 1,5 |
Сварочный ток, А | 260-270 | 280-290 |
Скорость сварки, м/ч | 4,5-5,0 | 4,5-5,0 |
Скорость подачи электродной проволоки, м/ч | 5,8 | 6,0 |
Расход газа, л/мин | 20,0 | 16,7 |
Температура предварительного подогрева, °С | 175-210 | 150-175 |
Примечание. b =1 мм.
Рис. 2. Рекомендуемые режимы сварки меди плавящимся электродом.
Сварку меди плавящимся электродом в среде защитных газов ведут на постоянном токе обратной полярности. Она применяется для меди толщиной не менее 6-8 мм. Рекомендуются V и Х-образные разделки. Производительность сварки меди плавящимся электродом примерно в 2-3 раза выше, чем при сварке неплавящимся электродом. Однако при плавящемся электроде сложно обеспечить стабильность процесса и получить беспористые швы. Так, при плотности сварочного тока выше 300 А/мм2 в аргоне и 110 А/мм2 в азоте образуется пористый шов. Для каждых защитной среды и режима сварки выбирают оптимальный диаметр проволоки. Лучшие свойства металла шва при сварке меди плавящимся электродом в среде инертных газов обеспечивает применение проволоки, легированной 0,22% Mg, 0,22% Li, 0,2% Cr. Она обладает лучшими сварочно-технологическими свойствами по сравнению с зарубежными и отечественными проволоками, предназначенными для сварки меди в среде инертных газов, в частности имеет более высокую стойкость к образованию пор и трещин, обеспечивает стабильное горение дуги и струйный перенос электродного металла, более высокую электрическую проводимость швов. При сварке меди плавящимся электродом в среде азота на пористость швов влияют легирующие элементы в металле проволоки. Положительное влияние при этом оказывают такие элементы, которые активно образуют нитриды и в которых азот малорастворим. Как показывает опыт, при сварке меди в среде азота наблюдается повышенное разбрызгивание электродного металла. Существенно улучшает перенос и уменьшает разбрызгивание легирование проволоки литием и магнием. Длина дуги при сварке меди плавящимся электродом является одной из важнейших характеристик процесса, так как от нее зависят не только потери электродного металла, насыщение его водородом и окисление, но и эффективный КПД дуги. При сварке меди током прямой полярности длина дуги зависит как от состава защитного газа, так и от состава электродной проволоки. Удовлетворительное формирование швов при сварке проволоками различного химического состава можно получить при длине дуги 4-5 мм.
При сварке меди плавящимся электродом наилучшие результаты достигаются в условиях струйного переноса электродного металла на токе обратной полярности в аргоне, а также на токе прямой полярности как в инертных, так и в активных газах при использовании электродов.
Наилучшие результаты при сварке плавящимся электродом получают при струйном переносе электродного металла, наблюдающемся при сварке на токе обратной полярности в аргоне, а также на токе прямой полярности как в инертных, так и в активных газах при использовании электродов с поверхностно-активирующими покрытиями. Сварку неплавящимся электродом применяют для листовой латуни малых толщин (до 3-4 мм). При сварке латуни плавящимся электродом используют бронзу, легированную алюминием с добавкой фосфора, а также Бр.КМц3-1. Режимы сварки латуни практически те же, что и при сварке меди. Предварительный подогрев необходим лишь при сварке листов толщиной более 12 мм.
Высокие механические свойства соединений из бронзы получают при сварке в среде инертных газов. Так, на алюминиевой бронзе этот способ позволяет получать наиболее прочные и пластичные соединения по сравнению с другими способами сварки. В качестве защитного газа используют аргон и гелий. Применение гелия обеспечивает сварку бронз без предварительного подогрева длинной дугой при напряжении, на 25% большем, чем при сварке в среде аргона. При ручной сварке тонколистовых бронз (b =1÷2 мм) неплавящимся электродом в среде аргона Iсв=100÷140 А; при автоматической сварке Iсв=190÷220A; υCB=30÷35 м/ч. Сварку алюминиевой бронзы плавящимся электродом выполняют проволокой из бронзы диаметром 1,6 мм при Iса = 325 A; υЭ = 390 м/ч; Uд=27÷29В и расходе аргона 17-23 л/мин.
Наиболее высокие механические свойства соединений достигаются при сварке раскисленной меди с применением такого же присадочного металла (σВ =211,9МПа; α=180°). При сварке нераскисленной меди пластичность швов снижается.
Механические свойства сварных соединений из латуней практически такие же, как и основного металла.
Таблица 5. Механические свойства сварных соединений из латуней, выполненных в среде аргона
Латунь | σв, МПа | а, град |
Л62 | 314—343 | 180 |
ЛМц58-2 | 338—363 | 180 |
ЛС59-1 | 299—314 | 180 |
Примечания. 1. Толщина основного металла 4 мм. 2. Образцы для испытания на разрыв плоские, со снятым усилением.
oitsp.ru
Медь используется в химическом и энергетическом машиностроении благодаря тому, что она имеет высокую коррозионную устойчивость, а также устойчива в агрессивных средах. Эти свойства будут повышаться при повышении чистоты металла, что заставляет предъявлять к сварочному шву особые требования. Сваривание бронзы и латуни имеет много своих особенностей, но свойства чистой меди, присутствующей в этих сплавах, значительно утрачиваются. В зависимости от количества содержания примесей в сплаве, медь различается на пять основных марок:
Аргоновая сварка меди очень похожа на газовую, однако она имеет некоторые отличия и особенности, отличающие ее от других видов сварки. Главным элементом, с помощью которого производится сваривание, является инертный газ аргон. Сваривание производится с помощью неплавящегося вольфрамового электрода. Вольфрамовый электрод является главной составляющей сварочного аппарата. Этот электрод изготавливают из вольфрама по причине его тугоплавкости. Данный металл не боится высокой температуры, поэтому электроды, сделанные из него, считаются неплавящимися. Возле вольфрамового электрода расположено сопло, из которого выходит газ аргон. Аргон не пропускает воздух к сварочной ванне, что позволяет защитить сварочный процесс от факторов окружающей среды. Если воздух попадает на сварочный электрод, то он будет окисляться, а если воздух попадет на свариваемый металл, то он начнет гореть. В сравнении с газовой и электрической сваркой, у аргонодуговой сварки преимуществ намного больше. При сваривании меди аргоном в металле сварочного шва не скапливаются различные шлаки. С помощью аргона можно производить сваривание даже тонкого металла. Например, аргонодуговым сварочным аппаратом можно сваривать даже пластинки фольги. В случаях, когда требуется сваривание чугуна или алюминия, аргонодуговой аппарат приходится как раз кстати. На данный момент аргонодуговые сварочные аппараты широко применяются в автомастерских для ремонта автомобилей. Стоит обратить внимание, что аргонодуговое сваривание является самым надежным из всех остальных видов сварки. Сварочный шов после работы практически не заметен и сливается с металлом свариваемого изделия. Если потребуется, то в сварочный шов можно добавить другие металлы. Для выполнения такой задачи потребуется присадочная проволока. Обычно присадочную проволоку используют для укрепления сварочного шва. Аргонодуговым сварочным аппаратом можно сваривать не только медь, алюминий и чугун. В некоторых случаях данный тип сваривания используют для сварки серебра, золота и других драгоценных металлов. Сваривание получается наивысшего качества в случае, когда для работы используется чистый газ аргон.
|
3g-svarka.ru
Сварка меди аргоном
Медь обладает высокой электро- и теплопроводностью, а также высокой коррозийной стойкостью к воздействию агрессивных химических сред. Благодаря этим характеристикам ее широко используют в энергетическом машиностроении и химическом производстве.
От чистоты меди зависят вышеперечисленные свойства и поэтому к сварочным работам, выполняемым по данному металлу, предъявляются требования особого характера.Техническая медь делиться на пять категорий, они в свою очередь обуславливаются количеством содержащихся примесей. Аргоновая сварка меди в среде защитных газах выполняется при использовании плавящегося и не плавящегося вольфрамового электрода. Для сварки меди толщиной до 1 сантиметра применяют сварку с использованием присадочной проволоки и вольфрамового электрода.
Специалисту отмечают, что при сварке с использованием аргона высшего сорта по ГОСТ 10157-73, дуговой разряд несколько ниже, чем при использовании азота высокой чистоты по МРТУ 6-02-375-66. Но при выполнении сварных работ на листах меди малой толщины и в этом случае образуется дуговой разряд высокой устойчивости.
Не стоит забывать, что при сварке меди из-за процесса окисления существует большая вероятность образования пористости швов, для избегания подобных фактов рекомендуется использовать легированные присадочные и электродные проволоки.
Сварочные работы на меди следует выполнять, используя ток прямой полярности и электроды лантанированного вольфрама.Такие электроды обладают хорошей устойчивостью в защитных газах. В момент выполнения сварки электрод должен располагаться в плоскости стыка и меть наклон от 60 до 80 градусов (угол наклона должен располагаться в положении «углом назад»). Для выполнения сварных работ на меди имеющей толщину 4-5 миллиметров необходимо использовать подогрев до 300-400 С.
Для получения в процессе сварки сварного шва практически идентичного по свойствам в отношении к основному материалу, рекомендуется использовать присадки из чистой меди М0 и М1. Если, ввести в сварной шов присадочные проволоки, содержащие легирующие компоненты и раскислители, можно значительно увеличить механические свойства сварного соединения. Но при этом снизить электро- и теплопроводность металла. Следует отметить, что снижение электро- и теплопроводности меди на ответственных участках конструкции является не допустимым фактором.
3g-svarka.ru