Преимущества использования зернового экструдера. Экструдер что это такое
что это такое? Описание экструдера. Как изготовить своими руками?
Экструзия представляет собой способ получения полуфабрикатов или изделий из полимерных материалов неограниченной длины. Применяется этот процесс также в пищевой и комбикормовой промышленности. Головкой экструдера расплав полимера выдавливается в формующую головку с нужным профилем. Этот способ изготовления, наряду с литьем пластмасс под давлением, на данный момент один из самых популярных. Экструзии подвержены почти все основные типы полимерных материалов: эластомеры, термопласты, реактопласты и прочие. Итак, сам процесс понятен, поэтому стоит рассмотреть экструдер: что это такое, как он работает, а также другие моменты, связанные с ним.
Принцип действия и конструкция
Экструзионная технология существует уже более шестидесяти лет, и за это время появилось много конструкций машин, предназначенных для ее реализации. Принцип действия прибора определяется сутью самого технологического процесса. Итак, если рассматривать экструдер, что это такое, становится понятно после определения того, что данный сложный физико-химический процесс протекает под влиянием механических усилий при условии высокотемпературного воздействия и присутствия влаги. Продукт при переработке нагревается за счет того, что механическая энергия превращается в тепло, выделяемое в процессе борьбы с внутренним трением, а также пластической деформации продукта либо благодаря внешнему нагреву.
В процессе экструзионной обработки имеется несколько сменных параметров, а именно: состав сырья, его влажность и природа. Во время производства может изменяться температура, давление, а также интенсивность и продолжительность воздействия на сырье.
Методы работы
Рассматривая экструдер, что это такое, будем разбираться по порядку. Существует три основных метода работы: холодная формовка, горячая экструзия и теплая обработка. Наиболее распространен в последнее время метод горячей формовки, осуществляемый при высоком давлении и скорости, когда имеется значительный переход механической энергии в тепловую. Чтобы реализовать процесс, можно использовать шнековый экструдер, у которого основным рабочим органом служит шнек специальной конструкции, осуществляющий вращение в цилиндрическом корпусе. Формообразующая матрица находится на выходе.
Схема экструдера предполагает, что в конструкции его рабочей части шнеки и камеры смонтированы для точного выполнения поставленных задач. Имеется загрузочная камера, куда осуществляется ввод сырья и разнородных добавок, закрытые камеры, в которых есть отверстия для измерения давления и температуры, а также добавление жидких веществ и отбор проб. Шнеки можно оснастить дополнительными элементами, благодаря чему перемещение продукта будет осуществляться под дополнительным сопротивлением, а также все будет перемешиваться в процессе.
Экструдер: что это такое и как он устроен?
Рабочую часть механизма с учетом стадий процесса обработки можно разделить условно на три зоны: первая, отвечающая за прием сырья; вторая, отвечающая за пластификацию и сжатие; третья - зона выпрессовывания продукта. Рабочая часть шнековых экструдеров может иметь одну из нескольких разных конструкций:
- одинарные шнеки: цилиндрические с постоянным или переменным шагом, конический, винтовой, конический с шагом, уменьшающимся к выходу;
- сдвоенные шнеки: вращающиеся в одном или разных направлениях;
- сдвоенные шнеки, входящие в зацепление: вращающиеся в одном направлении и самоочищающиеся, вращающиеся в разных направлениях и частично очищающиеся.
Использование
Экструдер зерновых работает за счет того, что в частицах зерна, находящихся в камере закрытого типа, при нагревании происходит нарастание внутреннего давления за счет испарений влаги. Из-за мгновенной разгерметизации камеры происходит расширение паровоздушной смеси, что приводит к увеличению объема зерновых частиц.
В комбикормовой промышленности чаще всего используются одношнековые механизмы с постоянным шагом и цилиндрической формой шнека. Производство экструдеров такой конструкции использует набор шнеков, а между ними в четко определенной последовательности находится несколько подпорных шайб, а шнеки и шайбы на шпильке закрепляются при помощи болта с конусной головкой. Кожух рабочей части изнутри оснащается несколькими продольными каналами, которые гарантируют, что продукт не будет перекручиваться во время перемещения. На выходе кожуха имеется обычная конусная гайка, снабженная отверстием. Регулирование зазора между конусами болта крепления шнеков с выходной гайкой позволяет регулировать температуру продукта. Так устроен экструдер. Что это такое, вам уже понятно, теперь осталось разобраться с иными моментами.
Производство механизмов
Разные модели экструдеров характеризуются различным конструктивным исполнением элементов, включенных в рабочую часть, числом рабочих камер, присутствием дополнительных систем, с помощью которых расширяются технологические возможности приборов, особенностью приводов, питателей и прочих частей. Форма цилиндра признана самой технологичной в плане изготовления, что делает ее себестоимость самой низкой.
Технология сегодня
Итак, можно рассмотреть, как работает экструдер. Что это такое, было описано ранее, а теперь стоит определиться с некоторыми важными моментами. Современные конструкции механизмов реализуют технологию сухой экструзии. Она так названа из-за того, что весь процесс осуществляется при помощи тепла, выделяемого в процессе прохождения продукта сквозь рабочую часть механизма. Имеется возможность использования пара при экструдировании. Для этого у прибора имеется камера предварительной паровой обработки сырья. Использование пара позволяет увеличить производительность и уменьшить износ основных частей и узлов механизма.
Сухая экструзия
Весь процесс занимает не более 30 секунд. Этого времени хватает для измельчения, тепловой обработки, обезвоживания, смешивания, обеззараживания, стабилизации и увеличения объема. Можно сделать экструдер своими руками, работающий по данной технологии. Для этого потребуется приобрести все элементы для будущего механизма, которые в дальнейшем будут соединены в соответствии со схемой прибора. Вам понадобится шнек подходящей конфигурации, электродвигатель, который станет основой механизма, корпус будущего прибора, подающая емкость и емкость на выходе, камера, в которой будет создаваться вакуум.
Альтернативные примеры
Процесс экструзии может использоваться не только при производстве. Существует такой прибор, как ручной сварочный экструдер, который предназначен для соединения полимерных материалов, а именно пленок, между собой посредством нагрева их краев с одновременной стыковкой. Чаще всего такой прибор используется для соединения элементов из термопластов. Эти вещества встречаются сейчас повсеместно. Это тазики, шланги, ведра, бочки, люки, емкости, канализационные решетки, элементы наружной и внутренней отделки помещений. Перечень можно составить достаточно длинный. Такое обилие термопластов привело к тому, что промышленные производители разработали весьма компактные приборы, которые предназначены для работы с этими материалами на местах их использования. Именно для этого был разработан сварочный экструдер. Его использование заметно упростило работы по сварке изделий из синтетических термопластов: поливинилхлорида, полиэтилена и полипропилена.
Экструдер - это... Что такое Экструдер?
Современные Э. — автоматизированные установки, производительность которых достигает 3—3,5 т/ч. Доля термопластичных полимерных материалов, перерабатываемых в Э., колеблется в разных странах в пределах 30—50%.
Лит.: Бернхардт Э. (сост.), Переработка термопластичных материалов, пер. с англ., М., 1962; Завгородний В. К., Калинчев Э. Л., Махаринский Е. Г., Оборудование предприятий по переработке пластмасс, Л., 1972; Оборудование для переработки пластмасс, М., 1976; Торнер Р. В., Теоретические основы переработки полимеров, М., 1977.
М. Л. Фридман.
Схема одношнекового горизонтального экструдера: 1 — двигатель; 2 — экструзионная головка; 3 — нагреватель корпуса; 4 — корпус; 5 — шнек; 6 — загрузочное устройство; 7 — упорный подшипник; 8 — редуктор.
dic.academic.ru
Что такое экструдер и экструзия, принципы работы
Экструзия исключает из производственного цикла трудоемкую механическую обработку. Это быстрый и недорогой способ получения пленок, труб, профиля и других изделий, выпускаемых погонажом из полимерного сырья. В статье расскажем, что такое экструдер, как происходит процесс экструзии полиэтилена, разберем тонкости экструзионной технологии.
Что такое экструзия полимеров?
Процесс экструзии происходит при нагреве полимеров максимум до 250 0С. Производство идет на скорости до 120 метров/минуту. Около 30 % всего объема полимеров перерабатывается по экструзионной технологии с помощью экструдеров. Попробуем разобраться в тонкостях этого процесса.
Щель имеет определенную форму, которая определяет геометрию изделия — сайдинг, пленка, оконный ПВХ профиль. В качестве сырья используются гранулы полиэтилена ПВД и ПНД, полипропилена, ПВХ, полистирола и других полимеров.
Экструзия включает в себя следующие этапы:
- получение однородного расплава в экструдере;
- формование;
- охлаждение продукции;
- натяжение и намотка (пленки), нарезка (профиль, труба).
Устройство и принцип работы экструдера, что это такое
Уже по тому, что слова «экструдер» и «экструзия» являются однокоренными, становится понятным, что экструдер — это основной рабочий орган экструзионной линии.
По длине экструдер для полимеров условно делится на три зоны: загрузки, сжатия расплава и дозирования.

Экструдер для пленки

Схема экструдера для полиэтилена
- Зона загрузки. Гранулы (порошок, вторичное сырье) подаются в бункер самотеком или под напором сжатого компрессором воздуха. Шнек, который приводится в движение работой привода, вращается, и уплотняя полимер до состояния пробки, продвигает его к горячим секциям экструдера.
- Зона плавления. Здесь шаг между витками начинает уменьшаться. Как следствие один и тот же объем полимера пытается поместиться в уменьшившемся пространстве. Пробка прижимается к обогреваемым стенкам трубы экструдера, плавится, расплав перемешивается. Хотим уточнить, что плавление происходит, в основном, не за счет нагревателей (они лишь интенсифицируют процесс), а из-за огромных сдвиговых деформаций в уплотняющемся полимере.
- Зона дозирования. На выходе из экструдера полимер продавливается через систему фильтрующих сеток и проходит через формующее отверстие, профиль которого зависит от формы выпускаемой продукции.
Важно! Экструдер может различаться по типу и количеству шнеков. Выпускаются: одношнековые, двухшнековые и многошнековые, дисковые и многодисковые экструдеры.
О конструкции одношнекового экструдера.
Внутри толстостенного корпуса (трубы) вращается шнек — металлический стержень с винтовой навивкой. Шнек перемещает гранулы по направлению к экструзионной головке. Корпус опоясывают секции хомутовых нагревателей, которые греют металл и плавят полимер, прижимаемый винтом к внутренней поверхности трубы. «Горячую» часть оборудования помещают в водоохлаждаемый кожух, и сверху утепляют термочехлом.

Одношнековый экструдер, схема
Экструзия пленки
Наиболее популярными формовочными изделиями, которые получают с применением экструзии, являются пленки. Их изготавливают из полистирола, полипропилена, полиамида, лавсана, поликарбоната, ПВХ, но самыми востребованными из них являются, конечно же, пленки из экструдированного полиэтилена высокого и низкого давления. Именно на их примере мы рассмотрим, какие этапы этот материал проходит на выходе из экструдера.
Существует два метода экструдирования пленок:
- Метод раздува рукава.
- Метод плоскощелевой экструзии.
Читайте также какие дефекты могут возникнуть при экструзии пленки и как их устранить.
Метод раздува рукава.
Полимер выдувается из экструдера для пленки через кольцевую щель в формующей головке. Визуально это выглядит, как из фильеры поднимается сплошной пленочный цилиндр, раздуваемый изнутри воздухом. Воздух подается под давлением через дорн — отверстие в центре головки.
Охлаждение при экструзии полиэтилена, в зависимости от ориентации рукава, может производиться по двум схемам:
- Если рукав направлен вертикально вверх или горизонтально, то пленка обдувается воздухом, поступающим через охлаждающие кольца по периметру рукава;
Раздувной экструдер
- При отводе рукава вниз используется водяное охлаждение — такая схема сокращает время кристаллизации.
После остывания пленка складывается с помощью специальных «щек» в полотно и протягивается через отжимающие воздух валки. Готовый материал отправляется на намотку.
Чем быстрее охладить расплав полиэтилена на выходе из экструдера, тем выше будет прозрачность и блеск пленки. Почему так происходит? Дело в том, что при остывании в пленке образуется два вида молекулярных структур — кристаллическая и амфорная. Когда материал охлаждают медленно, то макромолекулы полимера успеют сформироваться в кристаллы, и экструдированная пленка будет мутной и неэластичной, но прочной. При быстром охлаждении кристаллы не успевают соединиться и пространство между ними заполняют амфорные связи, придающие пленке прозрачность, хорошую эластичность и гибкость.
Метод плоскощелевой экструзии.
Отверстие в фильере плоскощелевого экструдера протачивают в виде тончайшей щели. Пленка из формовочной головки выходит в виде непрерывного полотна определенной толщины и ширины.

Плоскощелевой экструдер для производства стрейч-пленки
Существует два варианта охлаждения пленки полученной плоскощелевым методом:
- Первый, это когда экструзионный полиэтилен сразу же после формования подается на охлаждающий барабан, температура поверхности которого поддерживается на уровне 30…50 0С.
- Второй вариант — пленку пропускают через ванну с проточной водой. Такое шоковое охлаждение позволяет получать блестящий и прозрачный материал, но есть свои нюансы. Когда пленка заходит в воду, она вызывает рябь на ее поверхности, из-за которой на полиэтилене появляются пятна.
После охлаждения и сушки полиэтилен протягивается через натягивающие валы и идет на намотку.
Соэкструзия и коэкструзия.
Соэкструзия — это технология, использующаяся для получения многослойных пленок.
В качестве сырья может использоваться: полиэтилен низкой и высокой плотности, полипропилен, полиамидная пленка и др. полимеры. Гранулят этих пластических масс плавится в разных экструдерах, после чего соединяется и проходит через одну формовочную фильеру (головку). Для прочного склеивания нужно, чтобы молекулярная сетка полимеров была похожа по структуре. Но если нужно связать барьерный слой, например, EVOH и линейный полиэтилен, то потребуется специальные вяжущие сополимеры.
Соэкструзионные многослойные пленки используются для вакуумирования продуктов, как транспортная упаковка, с/х пленка (для мульчирования, пленка с эффектом антифог), упаковка фармацевтических препаратов.
По похожей технологии, которая получила название коэкструзия, изготавливают панели сайдинга и профиль ПВХ. Поливинилхлорид — основа профиля, занимает около 80% толщины панели, оставшиеся 20% — акрил. Как и в случае соэкструзии, используется работа двух коэкструдеров, где отдельно плавят ПВХ и акрил. Соединяются эти расплавы в щелевой филере, откуда выходят уже готовым спаянным изделием.
Коронарная обработка пленки после экструзии
Химическая инертность и малая поверхностная энергия пленки делают ее невосприимчивой к типографской или любой другой краске. Нанесение покрытия на поверхность полиэтилена станет возможным, если его поверхностная энергия будет хотя бы на 10 дин/см выше энергии наносимой краски. В ином случае краска будет просто собираться в капли. «Подзарядить» пленку можно коронированием. Каждая экструзивная линия оборудована активатором обработки коронным разрядом, который состоит из: генератора, трансформатора и электродов. При пропадании пленки в область электромагнитного поля растет ее поверхностная энергия и повреждается верхний слой макромолекул (микротравление).
Применение технологии экструзии
- Химическая промышленность. Почти все термопласты и их композиции могут перерабатываться экструзией в готовые изделия (пленки, трубы, оболочки изоляции, сайдинг, листы).
- Производство комбикорма. Измельченное сырье для производства комбикорма поступает в экструдер, где подвергается уплотнению, сжатию и температурной обработке при температуре до 200 0С. Этот способ переработки повышает питательность и усвояемость корма, сохраняет в нем витамины и препятствует размножению микроорганизмов.
- Брикетирование твердого биотоплива. Переработка биомассы (торфа, угольной пыли, шелухи подсолнечника, отходов сахарного производства, соломы сои, щепы) и прессование ее в гранулы или брикеты производится на экструдерах;
- Пищевая промышленность. Макароны, кукурузные палочки и хлопья, жевательная резинка и чипсы, соевые продукты— все эти продукты изготавливают с помощью пищевой экструзии.

Экструзия теста, экструдер для теста
Развитие экструзионного производства сейчас идет сейчас по трем направлениям. Это: усовершенствование существующего оборудования, применение новых композиций полимеров, совершенствование автоматизированных систем управления. Последнее направление представляется наиболее актуальным — уже сейчас в России появились установки оборудованные АСУ на основе микропроцессора. Они позволяют автоматически контролировать не только работу экструдера, но и системы подготовки сырья, калибровки и обрезки готовых изделий.
oplenke.ru
Экструзия. Экструдеры. Экструзионные линии
Экструзионная линия для производства гранул композиционного материала для кабельной промышленности
Исходные данные:
Полимерное сырье и его структура:
Требования к техническим характеристикам линии:
Предлагаемое оборудование: Экструзионная линия производства гранул композиционного материала для кабельной промышленности на основе двухвинтового экструдера в комплекте с гравиметрической системой дозирования и водокольцевой системой грануляции.
Полимерное сырье и его структура:
Технические характеристики:
Установленная мощность:
Сжатый воздух:
Электродвигатель:
Материальное исполнение:
Стандартные параметры энергоносителей:
Воздух:
Комплектация экструзионной линии:
- Опорная рама;
- Приемный бункер для гранул Полиэтилена;
- Гравиметрический дозатор для гранул Полиэтилена;
- Приемный бункер для гранул Сажевого концентрата;
- Гравиметрический дозатор для гранул Сажевого концентрата;
- Приемный бункер;
- Гравиметрический дозатор для гранул;
- Гравиметрический насос дозатор для Дибутилоловодилаурата;
- Электрический блок управления;
- Двухвинтовой экструдер;
- Вакуумный блок для закрытого контура вентиляции;
- Энергосберегающий электродвигатель экструдера;
- Электрическая панель для цифрового преобразователя;
- 15" сенсорный экран электрического шкафа управления;
- Электрическое соединение внутри линии;
- Датчики давления и температуры;
- Водокольцевой гранулятор;
- Системы охлаждения замкнутого контура;
- Вибрационная сортировочная установка для гранул.
Линия по производству изделий из резинокомпозита
Вес: 3,55 кг/м лин Теоретическая плотность: 1,1 – 1,20 кг/дм3 Макс линейная скорость 1 м/мин ± 10%
Производительность: ожидаемая мощность с типом профиля материала 60х60: 180 кг/ч ±10% В зависимости от формулы процесса и свойств сырого материала. Точные данные определяются после лабораторных проб.
Вес: 3,125 кг/м лин Теоретическая плотность: 1,1 – 1,20 кг/дм3 Макс линейная скорость 1 м/мин ±10%
Производительность: ожидаемая мощность с типом профиля материала в виде полупирамиды 60х70х45: 160 кг/ч ±10% В зависимости от формулы процесса и свойств сырого материала. Точные данные определяются после лабораторных проб.
Принципы работы:
1.Гравиметрическое устройство подачи для HDPE (полиэтилен повышенной плотности) 2.Гравиметрическое устройство подачи для вторичного сырья 3.Гравиметрическое устройство подачи для пигментного концентрата 4.Гравиметрическое устройство подачи для добавок в порошок 5.Гравиметрическое устройство подачи для наполнителя 6.Установка боковой подачи для наполнителя 7.Дегазация
Преимущества прямой экструзии
Нет необходимости предварительно смешивать / гранулировать материал. Применима более высокая влажность содержания. Компактный. Простое управление логистикой. Экономия энергии. Более низкая стоимость обслуживания / управления благодаря меньшему размеру экструдера. Более низкая стоимость обслуживания благодаря модульной конструкции винтов и бочки (емкости). Значительное снижение стоимости (на энергию, рабочую силу, логистику, управление…). Более высокие механические характеристики благодаря улучшенному смешиванию наполнителя / пластика. Меньше ухудшения свойств материала благодаря только одной истории нагрева/разделения. Непрерывная линия регулирования (настройки) состава. Поддержка собственного ноу-хау в процессе производства по внутренним заказам.
Линейные компоненты
СЕКЦИЯ А погрузочно-разгрузочные устройства для сырья СЕКЦИЯ B Гравиметрическое устройство подачи сырья СЕКЦИЯ С одновременно поворачивающийся двухшнековый экструдер СЕКЦИЯ D пресс-формы и калибраторы СЕКЦИЯ E главный шкаф управления СЕКЦИЯ F оборудование, расположенное ниже по технологической цепочке
Опции и вспомогательные системы
Для секции С: система замкнутого контура для вентилирующего вакуумного насосаОпция 1 оборудование для соэкструдированного отделочного слояВспомогательная система 1 метод помола отходовВспомогательная система 2 установка для охлаждения водой
1. Обработка сырья (сырьевого материала). 2. Гравиметрические устройства подачи непрерывного действия. 3. Опорные рамы. 4. Одновременно поворачивающийся двухшнековый экструдер. 5. Устройство боковой подачи для наполнителя. 6. Зубчатый насос дозировки полимеров. 7. Пресс-форма для профиля. 8. Калибраторы и охлаждающая ванна. 9. Опорный стол калибратора. 10. Отвод изделия из экструдера. 11. Чистка щеткой или система тиснения. 12. Система поперечного разреза. 13. Стол комплектации (сбора).
СЕКЦИЯ А погрузочно-разгрузочные устройства для сырья
Поз. А. 1 Полимер в форме гранул в мешках по 25 кг. Пневматический питатель с заборным щупом. Гранулы будут вытягиваться из короба (корзины) (не включен в объем поставки), который расположен на стороне экструдера. Макс горизонтальное расстояние 5 м. Макс вертикальное расстояние 6 м.
Поз.А.2 Измельченные отходы Для хлопьев в коробке (не включено), расположенной на стороне экструдера. Пневматический питатель (устройство погрузки (с заборным щупом. Макс горизонтальное расстояние 5 м. Макс вертикальное расстояние 6 м.
Поз.А.3 Добавки в форме гранул Ручная погрузка из стеллажа накопителя.
Поз.А.4. Добавки в форме порошка Ручная погрузка из стеллажа накопителя.
Поз.А.5 Наполнитель в форме порошка Для наполнителей в больших мешках. Конструкция держателя для больших мешков (макс габариты 1,1х1,1х2 м) Подвеска для больших мешков: вручную с помощью вильчатого погрузчика Пневматическая система выгрузки для трудно передвигаемого порошка. Корзина (короб) для хранения с системой вибрации. Порошковый фильтр для воздушной вентиляции. Система погрузки с помощью архимедова винта.
СЕКЦИЯ B Гравиметрическое устройство подачи для сырья
Поз. B.1 Гравиметрическое устройство подачи для полимера в форме гранул Дозирующая система весового питателя непрерывного действия с максимальной мощностью до 50% от производительности всей линии. Питатель винтового действия с высоким разрешением цифровой ячейки погрузки. Бункер повторной погрузки 50 л. Датчик уровня. Пневматический клапан нагнетания.
Поз. B.2 Гравиметрическое устройство подачи для измельченных отходов Дозирующая система весового питателя непрерывного действия с максимальной мощностью до 15% от производительности всей линии Питатель винтового действия с высоким разрешением цифровой ячейки погрузки. Бункер повторной погрузки 23 л. Датчик уровня. Пневматический клапан нагнетания.
Поз. В.3 Гравиметрическое устройство подачи для добавки в форме гранул Дозирующая система весового питателя непрерывного действия с максимальной мощностью до 10% от производительности всей линии Питатель винтового действия с высоким разрешением цифровой ячейки погрузки. Бункер повторной погрузки 23 л. Датчик уровня. Пневматический клапан нагнетания.
Поз. В.4 Гравиметрическое устройство подачи для добавки в форме порошка Дозирующая система весового питателя непрерывного действия с максимальной мощностью до 10% от производительности всей линии Питатель винтового действия с высоким разрешением цифровой ячейки погрузки. Бункер повторной погрузки 23 л. Датчик уровня. Пневматический клапан нагнетания.
Поз. В.5 Гравиметрическое устройство подачи для наполнителей в форме порошка Дозирующая система весового питателя непрерывного действия с максимальной мощностью до 65% от производительности всей линии Питатель винтового действия с высоким разрешением цифровой ячейки погрузки. Бункер повторной погрузки 200 л. специального исполнения для порошка, который тяжело пересыпать Датчик уровня вибрации. Пневматический клапан нагнетания.
Поз. В.6 Панель управления Для управления до 8 весовыми установками Удобный в пользовании графический дисплей с сенсорным экраном. ПО для управления дозированием.
Поз.В.7 Стальная опорная рама Для опоры весового дозатора и погрузочных устройств. Надежная и устойчивая конструкция для работы персонала на промежуточном этаже без взаимодействия с гравиметрическим взвешиванием / системой контроля. Лестницы для доступа к стеллажу накопителя.
В.7.1. Сеть распределения электропитания Комплект кабелей для соединения каждого устройства повторного наполнения с кабиной управления. Комплект кабелей для соединения каждого гравиметрического устройства с кабиной управления, включая специальный кабель для коммуникации. Комплект кабельных желобов для соответствующей опоры при прокладке кабелей.
В.7.2 Сеть распределения сжатого воздуха Комплект труб для соединения каждого устройства, установленного на платформе от отдельной питающей точки. В комплекте с регулятором давления и воздушным фильтром.
СЕКЦИЯ С одновременно поворачивающийся двухшнековый экструдер
Поз.С.1 Одновременно поворачивающийся двухшнековый экструдер С высокими эксплуатационными характеристиками, винтовой тип, находящийся в зацеплении для характеристик по самоочистке.
С.1.1. Опорная стальная сварная рама Изготовлено из прочных сварных стальных пластин и профилей. Предоставляется с уравнивающими болтами.
С.1.2 Бачок (емкость) Модульное исполнение, изготовлено из 10 квадратных секторов емкости, каждый сектор длиной 4 D. Корпус из секторов изготовлен из стали С-50 с внутренней сменной футеровкой, износостойкого сплава. Встроенный водный контур охлаждения, простая конструкция и легкое обслуживание. Система нагрева высокой эффективности – патронный нагреватель.
С.1.3 Комплект винтов Прошивной вал из специального сплава – стойкий к повреждению/деформации/скручиванию. Модульное исполнение. Винтовые элементы
С.1.4. Редуктор
С.1.5. Главный двигатель переменного тока
С.1.6. Установка водного охлаждения для экструзионного бачка (емкости) Для подачи охлаждающей воды к каждому сектору бачка. Включая циркулирующий насос. Теплообменник вода/вода с расширительной камерой. Соединяющий трубопровод.
С.1.7. Датчики температуры плавления и давления Встроены в передний конец бачка.
Поз.С.2. Система вентиляции, включая: вакуумный насос с водяным кольцом (система замкнутого контура, предложено в качестве опции) вентилирующий свод конденсатор дыма промежуточный коллектор порошка
С.2.1. Дополнительная система вентиляции Для отработанной излишней влажности от фильтров. Естественная вентиляция (не вакуумный насос).
С.2.2. Специальная препятствующая закупориванию система для древесной муки Двухвинтовое устройство для заталкивания обратно материала, который вылезает из бачка (емкости) из-за увеличения в объеме и давления пара. Необходим для высокого процента фильтрации наполнителя или содержания высокой влажности. Вакуумное отверстие установлено наверху на противоположном к винтам конце. Винты сделаны из закаленной и шлифованной стали. Стальной бачок с термообработкой. Приводится от редукторного двигателя переменного тока.
Поз.С.3 Двухвинтовой боковой питатель Винты, диаметр: 70 мм Для подачи наполнителей в расплавленную пластмассу. Двойные винты сцепленного типа. Винты, изготовленные из закаленной и шлифованной стали. Бачок (емкость) из закаленной стали с цепью водяного охлаждения. Приводится от редукторного двигателя переменного тока, регулируемого цифровым частотным контроллером.
Поз. С.4 Редуктор 70 Для стабилизации линейного выхода и образования достаточного давления для питания головки пресс-формы без влияния на качества экструдера. Специальное исполнение, подходящее для экструзии заполненных материалов. Специальное износостойкое покрытие корпуса насоса и редукторов. Редукторный двигатель 7, 5 кВт и универсальное соединение. Зонд (щуп) давления плавления на входе/выходе. Зонд (щуп) температуры плавления на выходе. Зоны нагрева, вкл. основной кабинет (управления), специализированная система управления, соединенный с устройством контроля экструдера.
Опции для секции С
Поз.С.5 Замкнутый контур для вакуумного насоса Желательно не тратить воду, и цеха для обработки воды нет. Сепараторная емкость воздуха/воды встроена в опору насоса. Встроенный теплообменник вода/вода. Необходимо часто сменять воду (через 305 дней в зависимости от уровня загрязнения воды).
СЕКЦИЯ D пресс-формы и калибраторы
Поз. D.1. Пресс-форма профилей для насыпного материала профиля 60х60
D.1.1. Экструзионные пресс-формы для профилей Соединение с редукторным насосом. Встроенный, нержавеющая сталь. Обогрев при помощи электрических нагревателей. #5 терморегулируемых зон, вкл. главный кабинет.
D.1.2. Калибровочная группа профилей Сухая и мокрая система. Калибровочное устройство, открывающееся с помощью шарниров (петлей). Изготовлено из нержавеющей стали.
D.1.3. Под вакуумными охлаждающими емкостями. Изготовлено из 3 секций длиной 2 м. 2 секции с вакуумным кольцом. 1 секция только для охлаждения. Изготовлено из алюминия и органического стекла (плексиглас). Система охлаждения «полная вода (полностью водяная)».
Поз. D.2. Пресс-формы профилей насыпного материала в виде полу-пирамиды, профиль 70х60х45
D.2.1. Экструзионные пресс-формы для профилей Соединение с редукторным насосом. Встроенный нержавеющая сталь. Обогрев при помощи электрических нагревателей. #5 терморегулируемых зон, вкл. главный кабинет.
D.2.2. Калибровочная группа профилей Сухая и мокрая система. Калибровочное устройство, открывающееся с помощью шарниров (петлей). Изготовлено из нержавеющей стали.
D.2.3. Под вакуумными охлаждающими емкостями. Будет поставляться та же емкость охлаждения, как и для формы профилей 60х60
СЕКЦИЯ E Главный шкаф управления
Поз.Е.1 Главный шкаф управления Система на основе ПЛК для контроля всей последовательности передвижения. Интерфейс оператора с сенсорным экраном с цветным монитором. # 18 зон температурного контроля (2 отдельные зоны для пресс-форм). Зоны терморегуляции, встроенные в ПЛК. Все системы кондиционирования. Построен по стандартам ЕС. Степень защиты: IP54.
Е.1.1. Удаленный пакет обновлений Через промышленный LAN с доступом в Интернет. ПО и техника на основе системы eWon. Соединение с Интернетом, необходимое на поле со статичным IP адресом и открытым межсетевым экраном компании.
Е.1.2. Соединительные кабели Соединительные кабели и коробы для прокладки кабеля от кабинета к экструдеру. Панель управления, расположенный макс на расстоянии 3 м от экструдера.
СЕКЦИЯ F оборудование, расположенное ниже по технологической цепочке
Поз. F.1 Держатель калибровочного устройств Для профилей с макс шириной: 150 мм Длина опорного стола: 7 м Продольное и высокое (наверное, осевое) смещение двигателями переменного тока. Ручное поперечное смещение. Сеть распределения охлаждающей воды с термометрами и регуляторами потока. Центробежный насос 4 кВт для циркуляции воды. 200 л коллекторы для воды из нержавеющей стали. Теплообменник вода/вода. Вакуумная распределяющая сеть с вакуумметрами и регуляторами. # 3 вакуумный насос 5,5 кВт.
Поз. F.2 Устройство отвода изделия из экструдера конвейерного. Для макс ширины профиля 150 мм. Стальная рама и алюминиевая конструкция держателя конвейера. Плоский конвейер из специальной синтетической резины, стойкой к износу. Приводной двигатель 1,5 кВт для каждого конвейера. Пневматические цилиндры для верхнего открытия/закрытия конвейера, макс шаг 160 мм.
F.3. Устройство поперечной резки Для макс ширины профиля 150 мм Для макс высоты профиля 60 мм. Стальная конструкция. Лопасть из видиа, диаметр 400 мм. Пневматический цилиндр для хода цилиндра вниз. Приводной двигатель 1,5 кВт. Устройства безопасности.
F.3.1. Устройство всасывания стружки Металлическая конструкция для опоры тканевого воздушного фильтра и приемные полиэтиленовые мешки. Всасывающий вентилятор из стали. Макс мощность 2500 м3/ч.
F.4. Стенд / стан сборки для профиля разреза Стальная структура с подвижными пластинами из алюминия. Габариты пластины: 500х6000 мм. Система бокового выталкивания с пневматическим приводом для передвижения профилей в /к приемной наклонной плоскости.
Опция 1. Оборудование для соэкструдированного отделочного слоя
Поз.Е.1. – Экструдер с одним винтом. Винт, диаметр: 45 мм Номинальное отношение длины к диаметру: 1:30 Макс скорость винта: 100 об в мин
Е.1.1 Опора стальной сварной рамы
Е.1.2. Бачок (емкость) Изготовлено из азотированной стали LK3. Обогрев керамическим обогревателем. Система охлаждения электро-вентилятора.
Е.1.3. Винты Изготовлено из азотированной стали LK3.
Е.1.4. Редуктор Двигатель / коробка передач с помощью ремня и шкива. Принудительная смазка.
Е.1.5. Главный двигатель переменного тока
Е.1.6. Температура плавления и датчик давления
Поз. Е.2. Дополнительные инструменты для соэктсрудирования Для пресс-форм для профилей из материала 60х60.
Экструзионная линия по производству профиля
Одношнековый экструдер 75 мм
Производительность: 60-90 кг/ч профиля (в зависимости от размеров и состава смеси)
Редуктор
Система подачи материала
- приводной двигатель: 1/2 л.с., с понижающим редуктором
- питатель: загрузка 50кг., нержавеющая сталь
Шнек
Цилиндр
Управление
- независимая панель управления
- семизонный температурный контроллер *4 зоны для цилиндра с четырьмя воздуходувками *1 зона для фланца *2 зоны для экструзионной головки
- инверторный контроль скорости
Калибровочный стол
Тянущее гусеничное устройство
- максимальный размер отреза ШхВ 200х60мм либо 120х100мм
- микрорегуляция скорости отреза
- контроль давления микрозажима
- пневмоконтроль пилы на соответствие скорости линии
- точный и регулируемый контроль длины
- двигатель 1 л.с., диаметр пилы 14"
Пылесборник
- двигатель 3л.с.
- звукоуловитель
- мобильное исполнение
Полуавтоматический укладчик
- длина укладчика 3000мм со свайной структурой для сбора в стопки
- максимальная высота 1100мм
- выравнивание укладчика гидравлическое
- гидропривод ЛА л.с.
- настраиваемое пошаговое понижение уровня
Пресс-форма
Пресс-форма 25*25
- выход в 2 ручья
- экструзионная головка
- размерная форма 300Lх1компл., 50Lх1компл.
Пресс-форма 20*20
- выход в 2 ручья
- экструзионная головка
- размерная форма 300Lх1компл., 50Lх1компл.
Перфоратор
- двустороннее ударное (одновременно)исполнение
- линейная скорость 10м/мин
- контроль перфорации - инверторный
- 2 сменные головки
Станок для оклейки сеткой с автоматическим питателем
- система управления
- датчик контроля положения сетки
- резервуар термоплавкого клея с изоляцией, защищающей оператора от термических ожогов
Экструдер производительностью 1-12 кг/час
Характеристики экструдера:
- Производительность экструдера: 1 – 12 кг/час
- Входной материал необходимо определить
- Высота оси 1070 мм ± 100 мм
- Диаметр шнека и цилиндра 30 мм
- Экструдер оснащен загрузочным бункером
- Сторона управления будет указана после заказа
- Рама, цвет RAL 5012
- Щит управления, цвет RAL 7035
- Цилиндр горизонтальный и его невозможно перемещать по вертикали
Цилиндр:
- Внутренний диаметр 30 мм с допуском H7
- Обработка цилиндра – азотирование
- Три зоны нагрева. Каждая зона охлаждается отдельно при помощи вентилятора с производительностью 150 м3/час
- Цилиндр охлаждается в нижней части бункера (заказчик заботится об охлаждающем средстве)
- Температура в нижней части бункера только измеряется и отображается. Эта температура не регулируется.
Шнек:
- Диаметр 30 мм
- Обработка шнека – азотирование
- Рабочая длина шнека 24 L/D
Двигатель экструдера:
- Конический редуктор с двигателем
- Мощность 5,5 кВт
- Напряжение 400/690 В
- Двигатель оснащен независимым охлаждением с мощностью 0,25 кВт
На панели управления экструдера возможно настроить следующие параметры:
- Ручное управления располагается на передней стороне щита управления
- На стороне щита управления будет сделан один служебный разъем 230В/16A/1Ф
- На панели управления экструдера можно настроить следующие характеристики:
- Число оборотов шнека 5 – 90 об / мин
- Старт/стоп экструдера
- Настройка температуры
Значения, отображаемые на дисплее экструдера:
- Температура и давление
- Число оборотов шнека
- Мощность двигателя при эксплуатации
- Температура в нижней части бункера
- Сигнализация
Безопасность:
- Центральная остановка
- Защита от давления (механическая) макс. давление 6500 Psi (448 бар)
Полимерное оборудование
Валковые машины и каландрыОборудование для переработки полимерных материаловОборудование и линии по переработке пластиковых бутылокПрессовое оборудование для полимеров. Машины таблетированияПроцесс переработки полимерной пленки. Линии (оборудование) мойки (очистки) и сушки полимерной пленкиТермопластавтоматы (литьевые машины)
Редукторы
Винтовые насосы. Шнековые насосы для мазутаВинтовые компрессоры. Винтовые компрессорные установки
Винтовые насосы
Инженеры всегда готовы проконсультировать или предоставить дополнительную техническую информацию по предлагаемым экструдерам и экструзионным линиям.
Ваши запросы на оборудование просим присылать в технический департамент нашей компании на e-mail: [email protected], тел. +7 (495) 225 57 86.
Центральный сайт компании ENCE GmbHНаша сервисная компания Интех ГмбХ
Головные Представительства в странах СНГ:РоссииКазахстанеУкраинеТуркменистанеУзбекистанеЛатвииЛитве
ence-gmbh.ru
Экструдеры: назначение, устройство, комплектация
Примечание. В статье описан общий принцип работы и устройство экструдеров. Чтобы ознакомиться с конкретными моделями экструдеров и их характеристиками, посетите страницу «Экструдеры для переработки полиэтилена, полипропилена, ПВХ-пластиката и других полимерных материалов».
Что такое экструдер?
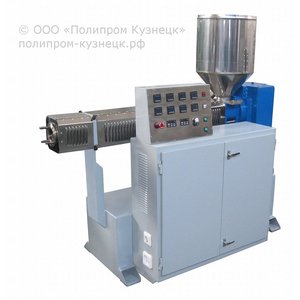
Экструдер ЭПК 50x27(для увеличения кликните по миниатюре)
Экструдер — это машина для непрерывной переработки полимерного сырья (гранул, дробленки, агломерата) в однородный расплав и придания ему формы путём продавливания через экструзионную головку и специальное калибрующее устройство, сечение которого соответствует конфигурации готового изделия.
Исходное сырьё засыпается (вручную или с помощью специального загрузчика) в бункер экструдера. Из бункера, минуя горловину загрузочной воронки, сырьё попадает в загрузочную зону шнека, а затем транспортируется по цилиндру пластикации. От сдавливания, перемешивания и контакта с нагретым цилиндром и шнеком полимерное сырьё расплавляется и превращается в однородную массу — расплав.
Чтобы получить готовое изделие, кроме экструдера необходимо ещё несколько устройств, которые вместе составляют экструзионную линию.
Чтобы ознакомиться с нашими предложениями по производству экструзионных линий, позволяющих выпускать готовые изделия, такие как напорные трубы или профили из ПВХ-пластиката, откройте интересующий вас раздел меню в левой части страницы.
Как устроен экструдер?
Экструдеры одношнековые, производимые ООО «Полипром Кузнецк», имеют оптимальную компоновку: на единой раме смонтированы специальный вертикальный редуктор со встроенным упорным подшипником и асинхронный электродвигатель, расположенный под узлом пластикации и соединенный с редуктором упругой муфтой. Шнек вставляется непосредственно в выходной вал редуктора. Такая схема расположения элементов позволяет сократить размеры экструдера, что упрощает его транспортировку и обслуживание.
Электрошкаф с системой тепловой автоматики, приборами управления всей технологической линией и пультом оператора прикреплен так же к единой раме. Сосредоточение важнейших приборов в одном месте позволяет минимизировать количество обслуживающего персонала — для управления необходим всего один оператор (для обслуживания полноценной экструзионной линии кроме оператора необходимо наличие одного или двух подсобных рабочих, общее количество персонала зависит от назначения и мощности экструзионной линии).
Система тепловой автоматики включает в себя температурные зоны экструдера, а так же дополнительные зоны для управления нагревом головок или фильер. Для контроля и управления каждой зоной используется отдельный прибор тепловой автоматики. Это позволяет тонко регулировать температуру на каждом участке, что (при правильном использовании) благоприятно сказывается на качестве получаемого расплава.
Поверхности шнека и цилиндра пластикации насыщаются азотом, что придаёт им долговечность и коррозионную стойкость.
Экструдеры, предназначеные для работы в составе трубных и плёночных линий, оснащаются барьерными шнеками, обеспечивающими наивысшее качество расплава и отличную производительность.
Принцип действия барьерного шнека состоит в разделении твердого материала и расплава в зоне плавления. На данном участке шнек имеет дополнительный виток, который не касается стенки цилиндра. Таким образом, образуются два канала шнека: вначале — небольшого объема для расплава и значительного — для гранул, а в конце наоборот: большой объем — для расплава и небольшой — для нерасплавленного полимера. Через барьерный виток расплав из канала с гранулами перетекает в канал с расплавом.
Экструдеры, предназначенные для работы в составе линий для производства профиля из пластифицированного ПВХ, имеют увеличенный диаметр шнековой пары и уменьшенную частоту вращения шнека.
Оба типа экструдеров комплектуются частотными преобразователями «Дельта Электроникс», позволяющими бесступенчато регулировать частоту вращения шнека и, соответственно, производительность по расплаву.
poly-prom.ru
Зерновой экструдер: описание, принцип работы, использование
Экструдер зерновой — это один из наиболее значимых аппаратов для улучшения качества зерновых. Необходимость его приобретения обоснована многими факторами. Экструдер позволяет в несколько раз повысить качественные характеристики зерновых. Корма, прошедшие обработку экструдером, более экономичны, легче усваиваются и полностью безопасны.
\
Данная технология применяется как в сельском хозяйстве, помогая значительно сократить расход кормов, так и в пищевой промышленности для улучшения качеств конечного продукта.
Экструдирование на сегодняшний день является наиболее действенным способом повышения питательной ценности зерновых!
Описание
Зерновые экструдеры предназначаются для быстрого изготовления кормов, усваиваемость которых составляет 90-95%, при том, что усваиваемость необработанных зерновых не превышает 65%.
В результате кратковременного повышения температуры, а также механическому воздействию и искусственным перепадам давления, в зерне происходят структурные и химические изменения.
Крахмал, который составляет 50% зерновых и довольно тяжело усваивается животными, и белок зерна приобретают структуру, легче воспринимаемую организмом.
Крахмал распадается на простые сахара, сложные белки и углеводы расщепляются на простые, а клетчатка преобразуется во вторичные сахара. Так как температурное воздействие длится всего несколько секунд, полезные витамины и минералы полностью сохраняются, а грибки, вредители и бактерии погибают.
В процессе обработки зерно как бы взрывается изнутри, становясь более воздушным и приобретая необходимую пластичность и пористость. Объем переработанного зерна увеличивается примерно на 15-20% по сравнению с изначальным.
Для изготовления кормов для животных при помощи экструдирования подходят даже пораженные насекомыми, грибками или плесенью зерна.
Корма после обработки намного легче воспринимаются организмом, так как большую часть работы желудка уже провел аппарат. Благодаря этому животное тратит в 2 раза меньше энергии на переработку пищи. В результате при том же объеме скармливаемого корма прирост веса увеличивается до 40%, надои до 35%, а яйценоскость птицы до 30%.
Принцип работы экструдера
После подачи зерна в бункер процессы внутри аппарата проходят без постороннего вмешательства. При помощи вибрации материал подается в рабочую зону агрегата, где подвергается трехфазной обработке.
Перерабатываемый материал не нужно запаривать или подвергать каким-либо дополнительным обработкам!
После попадания в экструдер зерно проходит термическую обработку при температуре от 110 до 160 градусов под давлением до 40 атмосфер. При выбросе зерна из данного отсека давление резко падает, вода, содержащаяся в клетках, превращается в пар и увеличивается в объеме в 1000 раз. В результате происходит взрыв внутри зерна, благодаря чему оно вспучивается, приобретает пористую структуру, увеличивается в объеме и лучше поддается формовке.
После продавливания через профилирующий инструмент из экструдера выходит вспученный стренг, имеющий форму жгута. При наличии отсекателя величина фракции составляет примерно 10-50 мм.
Процесс экструдации происходит примерно за 30 секунд, что обеспечивает высокую производительность при минимальных затратах энергии. Нагрев и сжатие зерна проходит без ТЭНов и гидравлики, только за счет электродвигателя.
Применяются три метода экструзии:
- Холодная формовка;
- Теплая обработка;
- Горячая экструзия.
Фундамент для установки экструдера не нужен. Он устанавливается на любую ровную поверхность, даже на земляной пол!
Использование
Экструдеры применяются для изготовления кормов для животных. Применение данной технологии позволяет значительно снизить затраты на откорм животных. Кроме того, при переводе животных на питание экструдированными кормами снижается падеж молодняка.
Корма, изготовленные при помощи экструдеров, обладают способностью предотвращать желудочно-кишечные заболевания у животных и значительно улучшать пищеварительный процесс!
Применяются экструдеры и в пищевой промышленности. С их помощью изготавливаются сухие завтраки, кукурузные палочки, чипсы, сухарики, детское питание, диетические хлебцы.
Двухшнековые экструдеры применяются и при изготовлении полимеров: пленки для пакетов, полистирола и полипропилена.
Однако наиболее распространено использование экструдера для улучшения кормовых качеств зерновых культур. В качестве материала для изготовления кормов можно использовать любые злаковые культуры, сою, бобовые.
После переработки вкусовые качества зерновых значительно улучшаются, благодаря выделению масел. Корм приобретает приятный аромат и хлебный вкус. При этом животные быстрее наедаются.
Отдельные модели экструдеров позволяют перерабатывать отходы мясного и рыбного производства. Также применяют экструдеры для обработки маслосодержащих продуктов перед отжимом. Этот процесс облегчает отжим и увеличивает конечный объем получаемых масел.
Экструдер Е-500
Аппарат предназначен для изготовления кормов для животных, очистки зерновых от вредных микроорганизмов. Также применяется для подготовки сои, рапса, подсолнечника к отжиму масла.
С помощью аппарата можно обрабатывать пшеницу, рожь, кукурузу, ячмень, горох, амарант, люпин, сою и подсолнечник. В воронке экструдера установлен магнитный улавливатель металлических частиц, что позволяет избежать попадания ненужных примесей в аппарат и, в последствии, в корм.
Производительность при переработке сои достигает 500 кг. в час, при переработке зерновых до 300 кг. в час. При этом потребляемая мощность составляет 55 кВт/час.
Размеры экструдера:
- Длина — 230 см;
- Ширина — 210 см;
- Высота — 170 см;
- Вес — 1400 кг.
Отличительной особенностью данной модели является наличие узла увлажнения в рабочей зоне. Это гарантирует мягкий и равномерный процесс обработки зерновых, а также обеспечивает снижение износа рабочих деталей.
Экструдер ES-1250
Мощный агрегат для использования в крупных и средних хозяйствах. Производительность данной модели доходит до 1250 кг/час. При этом экструдер способен работать круглосуточно. Оснащен боковой подачей сырья из бункера непосредственно в рабочую зону. Это позволяет исключить проблемы в работе, которые присутствуют при переработке влажного зерна или сложных смесей в экструдерах с верхней подачей.
Кроме стандартных материалов для экструдирования (пшеница, овес, просо, ячмень), данная модель подходит для переработки биоотходов, мясокостного фарша, муки и других отходов. Аппарат снабжен двумя гидроцилиндрами при помощи которых происходит автоматический съем корпусов при разборке рабочей части экструдера или замене шнеков. Это значительно упрощает длительный и трудоемкий процесс обслуживания и ремонта, особенно в аварийных ситуациях.Вес экструдера составляет 2130 кг, а потребляемая мощность 110 кВт.
Данная модель позволяет регулировать зазоры внутри рабочей части экструдера, благодаря чему становится возможным проводить точные настройки аппарата под каждое сырье.
Экструдер ПЭ-900 УШК
Снабжен системой кондиционирования и парообработки зерна. Данная технология позволяет придавать обрабатываемому материалу мягкость и эластичность, что значительно сокращает энергозатраты на переработку. Кроме того, это помогает увеличить срок службы основных узлов экструдера.
Применяется для обработки пшеницы, сои, ячменя, кукурузы, и гороха. Производительность от 1300 до 1800 кг/час. Потребляемая мощность от 97 кВт/час. Расход пара приблизительно 100 кг/час при давлении 0,4-0,6 Мпа. Размеры 280*256*255 см. При этом вес агрегата 2500 кг.
Экструдер данной модели отличается высокой производительностью и может применяться для подготовки сои и подсолнечника к отжиму масла.
Итог
Приобретение экструдера, несомненно, является выгодным вложением средств. Помимо того, что количество скармливаемого животным корма уменьшается, а его пищевая ценность возрастает, экструдация позволяет изготовить высококачественные корма без химических примесей. Корма, изготовленные при помощи экструдеров, позволяют увеличить производительность хозяйств без добавления в пищу животных химических и гормональных препаратов.
Экструдация позволяет добавлять в изначальное сырье до 30% примесей (сено, силос, солома, отходы мясопереработки), не понижая качество и энергетическую ценность производимого корма.
Кроме того, приобретение экструдера положительно скажется на экономическом состоянии производителей зерновых. Готовый высококачественный корм намного превосходит по цене необработанное зерно, а спрос на него практически не снижается.
То есть, экструдация позволяет увеличить стоимость конечного продукта без больших энергетических и трудозатрат. Процесс полностью автоматизирован и проходит буквально за несколько секунд!
При производстве кормов по данной технологии можно использовать пораженные плесенью или насекомыми зерна для получения годного конечного продукта. Это позволяет избежать потерь урожая, которые даже при правильном хранении зерна составляют не менее 20%. Это одна из немногих технологий, позволяющая получить высокую прибыль при минимальных затратах.
zernokorm.biz
что это такое? Описание специализированного оборудования для производства ПВХ-изделий.
Экструдер представляет собой оборудование, которое применяется для создания различных изделий из пластика. Суть заключается в том, что пластиковое сырье:
- гранулы;
- дроблённый пластик;
- агломерат и т.д.
разогревается до такой температуры, которая обеспечивает высокие пластичные качества. С применением давления происходит создание продукции. Сырьё проходит через головку экструдера. В зависимости от её конфигурации выбираются технические характеристики будущих изделий.
Тут можно приобрести специализированное оборудование по выгодным ценам. В условиях кризисного положения экономики очень сложно будет найти предложение выгоднее.
Принцип работы экструдера
Означенное оборудование состоит из следующих узлов: шнек, вертикальный редуктор, асинхронный двигатель, и шкаф управления. Всё это размещается в большинстве случаев на одной раме.
Это даёт возможность снизить количество обслуживающего профессионала до одного человека. Стоит отметить, что выпуск продукции и регулировка настроек осуществляется при помощи микроконтроллера.
В нём уже записаны несколько программ. Достаточно будет лишь заменить головку на другую и появится возможности вместо ПВХ-труб, к примеру, начать производить ПВХ-плёнку.
Правда в этом случае потребуется ещё и дополнительное оборудование, которое будет вытягивать плёнку и наматывать её в рулоны. Между тем, для хранения изделий из ПВХ-сырья рекомендуется оборудовать специальный склад, в котором будут сохраняться сухость и отсутствие прямых солнечных лучей.
Можно ли сделать экструдер самостоятельно?
Многие профессионалы думают, что им достаточно лишь приобрести головку, а сам экструдер можно сделать самостоятельно, тем более если асинхронный двигатель уже есть в наличии.
Наверняка есть какие-то кустарнее модели. Но стоит ли говорить о том, что их эффективность, а также ремонтопригодность оставляет желать лучшего. В фирменном оборудовании в шнек по стенкам закачивается азот.
Он даёт возможность защитить стенки не только от высокой температуры, но и от преждевременной коррозии и выхода оборудования из строя.
Смотрите также:
- Знаете ли Вы, какой инструмент необходимо использовать для создания дверного или оконного проёма в кирпичной стене?
На видео будет продемонстрирована классическая работа экструдера труб:
Источник №1: http://www.plastikmash.ru/
Твитнутьglavspec.ru