Как отжечь медь в домашних условиях. Как сварить медь с медью в домашних условиях
Как отжечь медь в домашних условиях, пайка аргоном
Отжиг стальных деталей
Чтобы облегчить механическую или пластическую обработку стальной детали, уменьшают ее твердость путем отжига. Так называемый полный отжиг заключается в том, что деталь или заготовку нагревают до температуры 900°С, выдерживают при этой температуре некоторое время, необходимое для прогрева ее по всему объему, а затем медленно (обычно вместе с печью) охлаждают до комнатной температуры.
Внутренние напряжения, возникшие в детали при механической обработке, снимают низкотемпературным отжигом, при котором деталь нагревают до температуры 500—600°С, а затем охлаждают вместе с печью. Для снятия внутренних напряжений и некоторого уменьшения твердости стали применяют неполный отжиг — нагрев до 750—760°С и последующее медленное (также вместе с печью) охлаждение.
Отжиг используется также при неудачной закалке или при необходимости перекаливания инструмента для обработки другого металла (например, если сверло для меди нужно перекалить для сверления чугуна). При отжиге деталь нагревают до температуры несколько ниже температуры, необходимой для закалки, и затем постепенно охлаждают на воздухе. В результате закаленная деталь вновь становится мягкой, поддающейся механической обработке.
Отжиг меди
Термической обработке подвергают и медь. При этом медь можно сделать либо более мягкой, либо более твердой. Однако в отличие от стали закалка меди происходит при медленном остывании на воздухе, а мягкость медь приобретает при быстром охлаждении в воде. Если медную проволоку или трубку нагреть докрасна (600° С) на огне и затем быстро погрузить в воду, то медь станет очень мягкой. После придания нужной формы изделие вновь можно нагреть на огне до 400° С и дать ему остыть на воздухе. Проволока или трубка после этого станет твердой. Если необходимо выгнуть трубку, ее плотно заполняют песком, чтобы избежать сплющивания и образования трещин.
Отжиг латуни позволяет повысить ее пластичность. После отжига латунь становится мягкой, легко гнется, выколачивается и хорошо вытягивается. Для отжига ее нагревают до 600° С и дают, остыть на воздухе при комнатной температуре.
Отжиг и закаливание дюралюминия
Отжиг дюралюминия производят для снижения его твердости. Деталь или заготовку нагревают примерно до 360°С, как и при закалке, выдерживают некоторое время, после чего охлаждают на воздухе. Твердость отожженного дюралюминия почти вдвое ниже, чем закаленного.
Приближенно температуру нагрева дюралюминиевой детали можно определить так: При температуре 350—360°С деревянная лучина, которой проводят по раскаленной поверхности детали, обугливается и оставляет темный след. Достаточно точно температуру детали можно определить с помощью небольшого (со спичечную головку) кусочка медной фольги, который кладут на ее поверхность. При температуре 400°С над фольгой появляется небольшое зеленоватое пламя.
Отожженный дюралюминий обладает небольшой твердостью, его можно штамповать и изгибать вдвое, не опасаясь появления трещин.
Закаливание. Дюралюминий можно подвергать закаливанию. При закаливании детали из этого металла нагревают до 360—400°С, выдерживают некоторое время, затем погружают в воду комнатной температуры и оставляют там до полного охлаждения. Сразу после этого дюралюминий становится мягким и пластичным, легко гнется и куется. Повышенную же твердость он приобретает спустя три-четыре дня. Его твердость (и одновременно хрупкость) увеличивается настолько, что он не выдерживает изгиба на небольшой угол.
Наивысшую прочность дюралюминий приобретает после старения. Старение при комнатных температурах называют естественным, а при повышенных температурах — искусственным. Прочность и твердость свежезакаленного дюралюминия, оставленного при комнатной температуре, с течением времени повышается, достигая наивысшего уровня через пять — семь суток. Этот процесс называется старением дюралюминия.
<<<Назад
Пайка или сварка алюминия? В чем разница и что лучше?
Во-первых, давайте рассмотрим определения. Сварка — это процесс получения соединений «все-в-одном» путем установления межатомных связей. Пайка представляет собой процесс объединения металлов в нагретом состоянии путем плавления сплава, плавильного припоя, такого как соединяемые металлы.
Другими словами, при сварке края сварных деталей расплавляются и затем замораживаются. При пайке обычный металл нагревается только до определенной температуры, и соединение получают путем поверхностной диффузии и химической реакции припоя и сплавленных металлов.
Итак, что лучше, пайка или алюминиевая сварка?
Чтобы ответить на этот вопрос, рассмотрите основные методы пайки и сварки алюминиевых сплавов, их преимущества и недостатки.
Алюминиевая сварка.
Четыре типа сварки наиболее часто используются при сварке алюминия:
1. Сварка электродом или сваркой ВИГ. В качестве электрода, который не потребляет, вольфрам используется со специальными легирующими добавками (лантан, церий и т. Д.).
Через этот электрод возникает электрическая дуга, которая расплавляет металл. Сварочная проволока вручную подается сварным бассейном. Весь процесс очень похож на обычную газовую сварку, только нагрев металла не осуществляется путем сжигания горелки, а электрической дугой в защитной среде. Такая сварка осуществляется исключительно в аргоновой или гелиевой среде или их смесях.
Есть ли разница между сварочным аргоном и гелием? Есть. Суть в том, что гелий обеспечивает более компактную дугу сгорания и, следовательно, более глубокое и более эффективное проникновение основных металлов. Гелий более дорогой, а его потребление намного выше, чем потребление аргона. Кроме того, гелий очень жидкий, что создает дополнительные проблемы при производстве, транспортировке и хранении.
Поэтому рекомендуется использовать его в качестве защитного газа только при сварке больших деталей, где требуется глубокое и эффективное плавление сварных кромок. На практике гелий редко используется в качестве инертного газа, так как почти такой же эффект проникновения может быть достигнут в аргоне, что увеличивает только сварочный ток. Сварка ВИГ алюминия, как правило, приводит к переменному току.
Почему при переменном токе? Все дело в оксиде алюминия, небольшое количество которого при сварке неизбежно присутствует во всех типах сварки. Дело в том, что температура плавления алюминия составляет около 660 градусов. Температура плавления оксида алюминия составляет 2060. Поэтому в сварном шве алюминиевый оксид не может плавиться — недостаточно температуры.
И не будет никакого руководства для высококачественного сварочного оксида. Что делать? Доход приходит к полярности обратной связи, которая имеет очень интересную особенность для очистки шва от ненужных примесей. Это свойство называется «катодная дисперсия». Однако сварочный ток с обратной полярностью имеет очень низкую мощность плавления. Поэтому дуга также содержит компоненты тока прямой полярности, которые предназначены для нечувствительности, но плавления металлов.
И обмен прямых и обратных полярных токов представляет собой переменный ток, который сочетает в себе как чистящие, так и плавильные свойства.
2. Сварка с помощью расходуемого электрода или полуавтоматическая сварка (сварка МИГ). Все это относится к этому типу сварки с той лишь разницей, что, как правило, единственной постоянной «очисткой» является замена полюсов дуговых потоков и не проходит через вольфрамовый электрод и непосредственно через сварочную проволоку, расплавленную при сварке.
Обычная полуавтоматическая машина используется для сварки, но с более высокими требованиями к подаче проволоки. Этот тип сварки характеризуется высокой производительностью.
третий
Ручная дуговая сварка электродами с покрытием (MMA-сварка). Он используется для сварки твердых деталей толщиной 4 мм и более. Он применяется к потоку обратной полярности и имеет шов низкого качества.
4. Газовая сварка алюминия. Его можно использовать только для ограниченного количества алюминиевых сплавов, который характеризуется отвратительным качеством шва. Это очень сложно и доступно далеко не каждому смертному.
На практике это почти не применяется.
Оставляя в одиночку экзотическую сварку (фрикционная сварка, сварка взрывом и плазма), качество сварного соединения и распространенность намного опережают формы, аргонодуговая сварка переменным током.
Он позволяет сваривать чистый алюминий, дюралюминий, силамин и т. Д., Сплавы от нескольких миллиметров до нескольких сантиметров. Кроме того, он является наиболее экономичным и единственно возможным для ядерной сварки и некоторых других алюминиевых сплавов.
Пайка алюминия
Обычно отделяется низкая температура (пайка мягкими соединениями) и высокая температура (пайка пайкой), тип пайки.
первый
Пайка алюминиевого мягкого припоя обычно выполняется с помощью обычного паяльника и может использоваться в качестве специального припоя для алюминия с высоким содержанием цинка и обычного свинцово-оловянного припоя. Основной проблемой такого типа пайки является борьба с легким алюминиевым оксидом. Чтобы нейтрализовать его, необходимо использовать различные типы флюсов, паяльных жиров и специальные типы пайки. В некоторых случаях поверхность алюминия покрыта гальваническим покрытием тонким слоем меди, который уже припаян традиционным пайкой припоя.
Однако использование гальванических покрытий далеко не технологически выполнимо и экономически целесообразно. В любом случае пайка алюминиевых сплавов при низких температурах довольно сложна, а качество паяных соединений, как правило, более чем среднее. Кроме того, из-за неоднородности металлов связанное соединение подвержено коррозии и всегда должно быть покрыто лаком или краской. Пайка мягкими муфтами не может использоваться для загруженных систем.
В частности, он не должен использоваться для ремонта радиаторов кондиционера, но может использоваться для ремонта двигателей радиатора.
второй
Высокотемпературная пайка алюминия. При пайке алюминиевых радиаторов на заводах используется пайка. Его характеристика заключается в том, что температура плавления припоя составляет всего 20-40 градусов ниже точки плавления самого металла. Для этой пайки, как правило, используется специальная высокотемпературная паста (например, нейлон), используемая для пайки, а затем спеченная в специальных печах в среде защитного газа.
Этот процесс пайки характеризуется высокой прочностью и низкой коррозионной стойкостью полученных соединений, поскольку припой используется в качестве композиции, близкой к основному металлу. Такой припой идеально подходит для тонкостенных изделий, но его технология довольно сложна и совершенно бесполезна при ремонте.
Второй тип высокотемпературной пайки алюминия — пайка газовым пламенем. В качестве припоя используются специальные самонарезающие стержни (например, HTS 2000, Castolin 21 F и т. Д.).
Для нагревания используют ацетилен, пропан и, предпочтительно, водородное пламя (гидролиз). Технология здесь следующая. Во-первых, пламя горелки нагревает металл, а затем паяльник осторожно заполняется в области пайки. Когда стержень расплавляется, пламя удаляется. Точка плавления стержня не намного ниже температуры базовой плиты, поэтому ее следует тщательно нагревать, чтобы она не удалялась.
Следует отметить, что этот тип припоя очень, очень дорогой, и его цена может достигать 300 долларов. за 1 килограмм. Как правило, он используется для местного ремонта.
Так что лучше?
Бейкер тает дома: шаг за шагом, видео
Пайка или сварка алюминия?Теперь мы можем ответить на этот вопрос. Если толщина металлов больше 0,2-0,3 мм, то используйте аргонодуговую сварку. В частности, аргоновая сварка простых сотовых излучателей бальзама, лотков, крыльев, кронштейнов, легкосплавных колес, рулевого механизма, головки двигателя и т. Д. Полученный сварной шов. Это монолитная, химически стойкая и прочная связь.
Если толщина металлов меньше 0,2-0,3 мм, лучше использовать высокотемпературную пайку алюминия. Во-первых, он используется для пайки радиаторов тонкой сотовой стенки из двигателя, которую очень трудно пить аргоном. Более низкая температура пайки мягким припоем лучше, если вообще не использовать, поскольку эти швы намного менее прочны и химически менее устойчивы.
Кроме того, кислотные флюсы, используемые в низкотемпературной пайке, могут за сравнительно короткое время уничтожить как обычные металлы, так и пайки
Большинство обычных металлов нельзя упрочнить термической обработкой. Однако почти все металлы упрочняются – до той или иной степени – в результате ковки, прокатки или гибки. Это называют наклепом или нагартовкой металла.
Отжиг является видом термической обработки для умягчения металла, который стал нагартованным — наклепанным, чтобы можно было продолжать его холодную обработку.
Холодная обработка: медь, свинец и алюминий
Обычные металлы весьма сильно различаются по своей степени и скорости деформационного упрочнения — наклепа или нагартовки.
Медь довольно быстро наклепывается в результате холодной ковки, а, значит, быстро снижает свою ковкость и пластичность. Поэтому медь требует частого отжига, чтобы ее можно было дальше обрабатывать без риска разрушения.
С другой стороны, свинец можно обрабатывать ударами молотка почти в любую форму без отжига и без риска его разрушения.
Свинец обладает таким запасом пластичности, который позволяет ему получать большую пластическую деформацию с очень малой степенью деформационного наклепа. Однако, медь хотя и тверже свинца, обладает в целом большей ковкостью.
Алюминий может выдерживать весьма большое количество пластической деформации в результате формовки молотком или холодной прокатки, прежде чем ему понадобится отжиг для восстановления его пластических свойств.
Чистый алюминий наклепывается намного медленнее, чем медь, а некоторые листовые алюминиевые сплавы являются слишком твердыми или хрупкими, чтобы позволять большой наклеп.
Холодная обработка железа и стали
Промышленное чистое железо можно подвергать холодной обработке до больших степеней деформации, прежде чем оно станет слишком твердым для дальнейшей обработки.
Примеси в железе или стали ухудшают способность металла к холодной обработке до такой степени, что большинство сталей нельзя подвергать холодной пластической обработке, кроме конечно, специальных низкоуглеродистых сталей для автомобильной промышленности. Вместе с тем, почти все стали можно успешно пластически обрабатывать в раскаленном докрасна состоянии.
Зачем нужен отжиг металлов
Точная природа процесса отжига, которому подвергают металл, в значительной степени зависит от назначения отожженного металла.
Существует значительное различие отжига по методам его выполнения между отжигом на заводах, где производят огромное количество листовой стали, и отжигом в небольшой автомастерской, когда всего лишь одна деталь требует такой обработки.
Если кратко, то холодная обработка – это пластическая деформация путем разрушения или искажения зеренной структуры металла.
При отжиге металл или сплав нагревают до температуры, при которой происходит рекристаллизация — образование вместо старых — деформированных и удлиненных — зерен новых зерен — не деформируемых и круглых. Затем металл охлаждают с заданною скоростью. Другими словами, кристаллам или зернам внутри металла, которые были смещены или деформированы в ходе холодной пластической обработки, дают возможность перестроиться и восстановиться в свое естественное состояние, но уже при повышенной температуре отжига.
Отжиг железа и стали
Железо и низкоуглеродистые стали необходимо нагревать до температуры около 900 градусов Цельсия, а затем давать возможность медленно охлаждаться для обеспечения максимально возможной «мягкости».
При этом принимают меры, чтобы предотвратить контакт металла с воздухом во избежание окисления его поверхности. Когда это делают в небольшой автомастерской, то для этого применяют теплый песок.
Высокоуглеродистые стали требуют аналогичной обработки за исключением того, что температура отжига для них ниже и составляет около 800 градусов Цельсия.
Отжиг меди
Медь отжигают при температуре около 550 градусов по Цельсию, когда меди разогрета до темно-красного цвета.
После нагрева медь охлаждают в воде или позволяют медленно охлаждаться на воздухе. Скорость охлаждения меди после нагрева при температуре отжига не влияет на степень получаемой «мягкости» этого металла. Преимущество быстрого охлаждения заключается в том, что при этом металл очищается от окалины и грязи.
Отжиг алюминия
Алюминий отжигают при температуре при температуре 350 градусов Цельсия.
Термическая обработка цветных сплавов
На заводах это делают в подходящих печах или соляных ваннах. В мастерской алюминий отжигают газовой горелкой. Рассказывают, что при этом деревянной лучиной трут по поверхности нагретого металла.
Когда дерево начинает оставлять черные следы, то это значит, что алюминий получил свой отжиг. Иногда вместо дерева применяют кусок мыла: когда мыло начинает оставлять коричневые следы, нагрев нужно прекращать. Затем алюминий охлаждают в воде или оставляют охлаждаться на воздухе.
Отжиг цинка
Цинк становиться снова ковким при температуре между 100 и 150 градусами Цельсия.
Это значит, что его можно отжигать в кипятке. Цинк нужно обрабатывать, пока он горячий: когда он охлаждается, то сильно теряет свою ковкость.
Медь находит широкое применение при изготовлении изделий различного назначения: сосудов, трубопроводов, электрораспределительных устройств, химической аппара- туры и т. д. Многообразие использования меди связано с ее особыми физическими свойствами.
Медь обладает высокой электропроводностью и теплопроводностью, устойчива в отношении коррозии. Плотность меди 8,93 Н/см3, температура плавления 1083°С, температура кипения 2360°С.
Трудности сварки меди обусловлены ее физико-химическими свойствами4. Медь склонна к окислению с образованием тугоплавких оксидов, поглощению газов расплавленным металлом, обладает высокой теплопроводностью, значительной величиной коэффициента линейного расширения при нагревании.
Склонность к окислению вызывает необходимость применения при сварке специальных флюсов, защищающих расплавленный металл от окисления ,и растворяющих образующиеся оксиды, переводя их в шлаки.
Высокая теплопроводность требует применения более мощного пламени, чем при сварке стали. Свариваемость Си зависит от ее чистоты, особенно ухудшают свариваемость Си наличие в ней В1, РЪ, 3 и Оз. Содержание рг в зависимости от марки Си колеблется от 0,02 до 0,15%, Ш и РЬ придают меди хрупкость и красноломкость.. Наличие в Си кислорода в виде оксида меди Си20 вызывает образование хрупких прослоек металла и трещин, которые появляются в зоне термического влияния.
Оксид меди образует с медью легкоплавкую эвтектику, которая обладает более низкой температурой плавления. Эвтектики располагается вокруг зерен меди и таким образом ослабляет связь между зернами.
На процесс сварки Си оказывает влияние не только кислород, растворенный в меди, но и кислород, поглощаемый из атмосферы. При этом наряду с оксидом меди СиаО образуется оксид меди СиО. При сварке оба эти оксида затрудняют процесс газовой сварки, поэтому их необходимо удалять с помощью флюса.
Водород и оксид углерода также отрицательно влияют на процесс сварки Си.
В результате их взаимодействия с оксидом меди СиаО образуются пары воды и углекислый газ, которые образуют поры в металле шва. Чтобы избежать этого явления, сварку меди необходимо выполнять строго нормальным пламенем. Чем "чище Си и чем меньше она содержит 0-2, тем лучше она сваривается.
По ГОСТ 859—78 промышленностью для изготовления сварных конструкций выпускается медь марок М1р, М2р МЗр, имеющая пониженное содержание Оа- (до 0,01%).
При газовой сварке Си нашли применение стыковые и угловые соединения, тавровые и нахлесточные соединения не дают хороших результатов.
Перед сваркой свариваемые кромки необходимо очистить от грязи, масла, оксидов и других загрязнений на участке не менее 30 мм от места сварки. Места сварки очищают вручную или механическим способом стальными щетками. Сварку меди толщиной до 8 мм выполняют без разделки кромок, а при толщине свыше 3 мм требуется Х-образна.я разделка кромок под углом 45° в каждой стороне стыка. Притупление делаетоя равным 0,2 от толщины свариваемого металла. В связи с повышенной жидкотеку честью меди в расплавленном состоянии тонкие листы сваривают встык без зазора, а листы свыше 6 мм сваривают на графитовых и угольных подкладках.
Мощность сварочного пламени при сварке меди толщиной до 4 мм выбирают из расчета расхода ацетилена 150—175 дм3/ч на 1 мм толщины свариваемого металла, при толщине до 8—10 мм мощность увеличивают до 175—225 дм8/ч.
При больших толщинах рекомендуется сварка двумя горелками — одной ведется подогрев, а другой — сварка. Для уменьшения теплоотвода сварку выполняют на асбестовой подкладке. Для компенсации больших потерь теплоты за счет отвода в околошовную зону применяют предварительный и сопутствующий подогрев свариваемых кромок.
Подогревают кромки одной или несколькими горелками.
Пламя для сварки Си выбирают строго нормальным, так как окислительное пламя вызывает сильное окисление, а при науглероживающем пламени появляются поры и трещины. Пламя должно быть мягким и направлять его следует под большим, чем при сварке стали, углом. Сварка проводится восстановительной зоной, расстояние от конца ядра до свариваемого металла 3—6 мм.
В процессе сварки нагретый металл должен быть все время защищен пламенем. Сварку выполняют как левым, так и правым способом, однако наиболее предпочтителен при сварке меди правый способ. Сварка ведется с максимальной скоростью без перерывов.
При сварке Си рекомендуется свариваемые изделия устанавливать под углом 10° к горизонтальной плоскости.
Сварка ведется на подъем. Угол наклона мундштука горелки к свариваемому изделию составляет 40—50°, а присадочной проволоки — 30—40°. При выполнении вертикальных швов угол наклона мундштука горелки составляет 30° и сварку ведут снизу вверх. При сварке меди не рекомендуется скреплять детали прихватками. Длинные швы сваривают в свободном состоянии обратноступенчатым способом.
Газовую сварку меди выполняют только за один проход.
На процесс газовой сварки Си оказывает большое влияние состав присадочной проволоки. Для сварки в качестве присадка применяют прутки и проволоку согласно ГОСТ 16130—72 следующих марок: М1, МСр1, МНЖ5-1, МНЖКТ5-1-0,2-0,2.
Error 503 Service Unavailable
Сварочная проволока МСр1 содержит 0,8—1,2% серебра. Диаметр присадочной проволоки выбирают в зависимости от толщины свариваемого металла и берут равным 0,5—0,75 8, где 5 — толщина металла, мм, но не более 8 мм.
Сварочная проволока должна плавиться спокойно, без разбрызгивания. Желательно, чтобы температура плавления присадочной проволоки была ниже температуры плавления основного металла. Для предохранения Си от окисления, а также для раскисления и удаления в шлак образующихся оксидов сварку осуществляют с флюсом. Флюсы изготовляют из оксидов и солей бора и натрия. Флюсы для сварки Си применяют в виде порошка, пасты и в газообразной форме Флюсы № 5 и 6, содержащие соли фосфорной кислоты, необходимо применять при сварке проволокой, не содержащей раскислителей фосфора и кремния.
Сварку Си можно выполнять и с применением газообразного флюса БМ-1, в этом случае наконечник горелки надо увеличить на один номер, чтобы снизить скорость нагрева и увеличить мощность сварочного пламени. При использовании газообразного флюса применяют установку КГФ-2-66. Порошкообразный флюс посыпают на место сварки на 40—50 мм по обе стороны от оси шва. Флюс в виде пасты наносят на кромки свариваемого металла и на присадочный пруток. Остатки флюса удаляют промывкой шва 2%-ным раствором азотной или серной кислоты.
Для улучшения механических свойств наплавленного металла и повышения плотности и.
пластичности шва после сварки металл шва рекомендуется проковывать. Детали толщиной до 4 мм проковьшают в холодном состоянии, а при большей толщине — при нагреве до температуры 550— 600°С.
Дополнительное улучшение шва после проковки дает термическая обработка — нагрев до 550—600°С и охлаждение в воде. Свариваемые изделия нагревают сварочной горелкой или в печи. После отжига металл шва становится вязким.
⇐ Предыдущая27282930313233343536Следующая ⇒
Дата публикования: 2015-01-26; Прочитано: 455 | Нарушение авторского права страницы
studopedia.org — Студопедия.Орг — 2014-2018 год.(0.001 с)…
Главная>>Сварка цветных металлов>>Сварки меди со сталью
Сварка меди и её сплавов со сталью. Как сваривать медь и сталь?
На практике сварка меди и стали, чаще всего, осуществляется в стыковых соединениях. В зависимости от характера конструкции, швы в таком соединении могут быть наружными и внутренними.
Для сварки латуни со сталью лучше всего подходит газовая сварка, а для сварки красной меди со сталью — электродуговая сварка металлическими электродами.
Хорошие результаты также получаются при сварке угольными электродами под слоем флюса и газовая сварка под флюсом БМ-1. Часто на практике выполняют газовую сварку латуни со сталью, используя медь в качестве присадочного материала.
Подготовку сварных кромок при одинаковой толщине цветного металла и стали выполняют так же, как и при сварке чёрных металлов.
Сварку листов, толщиной менее 3мм выполняют без разделки, а листов, начиная с 3мм — со скосом кромок.
При недостаточном скосе кромок, или при наличии загрязнений на торцах свариваемых деталей, хорошего провара добиться невозможно. Исходя из этого, при сварке деталей больших толщин, в которых выполнена Х-образная разделка, притупление делать не следует.
Сварка меди со сталью — задача сложная, но вполне выполнимая для наплавочных работ и сварки, например, деталей химической аппаратуры, медного провода со стальной колодкой.
Качество сварки таких соединений удовлетворяет требованиям, предъявляемым к ним. Прочность меди можно повысить путём введения в её состав до 2% железа. При большем количестве железа прочность начинает падать.
При сварке угольным электродом необходимо применять постоянный ток прямой полярности.
Напряжение электрической дуги равно 40-55В, а её длина, примерно, 14-20мм. Сварочный ток выбирается в соответствии с диаметром и качеством электрода (угольный или графитовый) и составляет в пределах 300-550А. Флюс используют такой же, как и для сварки меди, состав этих флюсов дан на этой странице.
Вводят флюс в зону сварки, засыпая его в разделку.
Способ сварки применяют "левый".
Наилучшие результаты при сварке медных шин со стальными получаются при сварке "в лодочку". Схема такой сварки показана на рисунке. Вначале выполняется подогрев медных кромок угольным электродом, а затем сварка с определённым положением электрода и присадочного прутка (см. рисунок). Скорость сварки составляет 0,25м/ч. Сварка меди с чугуном производится с помощью таких же технологических приёмов.
Приварку низколегированной бронзы малой толщины (до 1,5мм) к стали толщиной до 2,5мм можно осуществить внахлёст неплавящимся вольфрамовым электродом в среде аргона на автомате с подачей присадочной проволоки диаметром 1,8мм со стороны.
При этом очень важно направить дугу на нахлёстку со стороны меди. Режимы такой сварки: сила тока 190А, напряжение дуги 11,5В, скорость сварки 28,5м/ч, скорость подачи проволоки 70м/ч.
Медь и латунь хорошо свариваются со сталью стыковой сваркой с оплавлением.
При таком способе сварки стальные кромки оплавляются достаточно сильно, а кромки цветного металла незначительно. Учитывая это обстоятельство, и принимая в расчёт разность удельных сопротивлений этих металлов, принимают вылет для стали, равный 3,5d, для латуни 1,5d, для меди 1,0d, где d — диаметры свариваемых стержней.
Для стыковой сварки таких стержней методом сопротивления рекомендуют вылет, равный 2,5d для стали, 1,0d для латуни и 1,5d для меди. Удельное сопротивление осадки принимается в пределах 1,0-1,5 кг/мм2.
На практике часто возникает необходимость приварки шпилек диаметром 8-12мм из меди и её сплавов к стали, или стальных шпилек к медным изделиям.
Такую сварку осуществляют на постоянном токе обратной полярности под мелким флюсом марки ОСЦ-45 без предварительного подогрева.
Хорошо привариваются к стали или чугуну медные шпильки диаметром до 12мм или шпильки из латуни марки Л62, диаметром до 10мм при силе тока 400А.
А шпильки из латуни марки ЛС 59-1 для приварки не используют.
Стальные шпильки к медным и латунным изделиям привариваются плохо.
Как производится сварка меди в домашних условиях?
Если надеть на конец шпильки, диаметром до 8мм, медное кольцо высотой 4мм, то процесс сварки металлов протекает удовлетворительно. Такие же шпильки диаметром 12мм к брозе марки Бр. ОФ 10-1 привариваются хорошо. Для дуговой сварки меди и стали, наилучшие результаты обеспечивают электроды К-100.
Дополнительные материалы по теме:
Холодная обработка и отжиг металлов
Сварка медных труб
Сварка медных труб является сложным процессом, так как медь сваривается, довольно беспокойная. Выбор технологии для сварки медных труб в зависимости от цели сварных работ и необходимой герметизации сварного шва.
Сварка медных труб Вероятно, это два самых популярных способа: газовая и дуговая сварка.
Дуговая сварка делится на два метода, таких как сварка обычными и неуправляемыми электродами.
Газовая сварка меди Он используется для сварки медных и медных труб, а качество сварки очень велико.
Этот тип сварки означает широкое использование различных токов, которые удаляют оксидную пленку с металлической поверхности. Это дефект при сварке газом, поскольку полученный сварной шов имеет пористую структуру из-за образования пара потока во время нагрева, и сварка не будет герметизирована.
Лучшая сварка медных труб, когда при работе используются специальные электроды, которые позволяют получать высокую температуру сварки и горение.
Температура сварки при сварке должна быть высокой, потому что это более высокий, более чистый сварочный материал и более высокая теплопроводность. Эта технология также не позволяет получить полностью герметичный и высококачественный сварочный шов, так как крышка сварочного электрода останавливается, и прочность шва сильно капает.
Наиболее качественный метод сварки заключается в сварке в среде защитного газа с использованием летучего электрода из вольфрама.
В этом случае газ аргона действует как защитный газ, потому что он инертен. Использование азота позволяет производить сварной бассейн, но для уменьшения его глубины. Аргон позволяет получить узкий и глубокий сварной шов, который улучшит качество сварных деталей.
Из-за поступления кислорода в сварочный бассейн для достижения высокого качества работы, использовать медный провод, в качестве наполнителя.
Он должен содержать много кислородсвязывающих добавок. Одной из этих добавок является марганец.
Некоторые наполнители не дают желаемого результата, потому что некоторые из их включений изменяют свойства металла шва, делая его более хрупким или менее долговечным. Поэтому, чтобы избежать таких эффектов сварки, как снижение свойств сварочных металлов, необходимо использовать наполнители с добавлением редкоземельных металлов, использование которых позволяет достичь высокой чистоты сварного шва и улучшить его качество.
Единственными неудобствами использования редкоземельных металлов являются их высокие затраты, поэтому их необходимо приобрести в специализированных магазинах от производителей.
stroitel12.ru
как паять газовой горелкой, твердым, мягким припоем

В домашних условиях предпочтительнее использовать спаивание медных изделий, этот вариант, наиболее простой и быстрый, в сравнении с варкой. К тому же не понадобится специальное оборудование, которым будет осуществляться скрепление. При соблюдении всех правил и условий технологического процесса, можно получить прочное и надежное соединение элементов, увеличивая стойкость к различным нагрузкам.
Для того чтобы спаивание в домашних условиях не вызвало затруднений, в первую очередь нужно позаботиться об основных инструментах, которые будут задействованы в этом процессе:
- труборез;
- фаскосниматель;
- труборасширитель;
- ершик стальной;
- щетка стальная;
- припой;
- горелка или фен.
Для трубчатого устройства применяют метод, когда элемент погружается в состав соли и припоя. Соль выполняет функции источника тепла, и заменяет функции флюса. Поэтому дополнительный флюс не понадобится.
Кроме этого способа, есть еще несколько вариантов пайки, которые заслуживают внимания.
Пайка меди
Пайка твердым припоем
Самым распространенным способом пайки в домашних условиях является пайка меди твердым припоем. Это объясняется свойствами меди, которая легко плавится при невысоких температурах. В качестве инструмента вполне подойдет паяльник или газовая горелка.Пайка меди немного похожа на процесс сварки, но все же имеет небольшие отличия:
- При пайке деталей используется дополнительное вещество-припой, который и соединяет эти элементы. Это возможно, благодаря свойствам припоя, который имеет низкую температуру плавления.
- Самый распространенный материал для спаивания деталей используют никель и олово. Это доступные и простые компоненты, которые используются в большинстве случаев. Что касается промышленного использования, то для этих целей применяют другие виды припоя, но для домашнего использования они достаточно дорогие, а, следовательно, нерентабельные.
- Чтобы паять медные изделия, необходимо сначала расплавить припой, до того состояния, пока он не достигнет нужной консистенции, чтобы нанести его на место спаивания элементов. После этого, следует подождать до полного остывания соединения.
Если все нюансы процесса выполнены в точности, то такое соединение получится прочным и долговечным.
Пайка в печах
Пайка меди в печах осуществляется в производственных условиях. Этот процесс обеспечивает равномерное прогревание деталей, полностью, исключая ее деформацию. В качестве сплава применяется олово или сплав из олова и свинца, в качестве флюса выступает состав из канифоли и спирта, или состав их хлористого аммония или цинка.
При применении припоя с основой из серебра, используют флюсы, в основу которых входят соединения из фтора, калия и бора. Эти флюсы наилучшим образом очищают скрепляемые поверхности от оксидной пленки, это позволит сплаву отлично распределиться по всей поверхности.
Флюсовая пайка
Эта процедура имеет один большой минус, это выполнение герметичного скрепления. Излишки флюса создают дополнительные очаги, которые подвергаются коррозии, вследствие этого пайку выполняют в нейтральных условиях или в условиях восстановительной среды газа. Чтобы паять в азоте, необходимая температура должна достигать 750–800 градусов.
Вакуумная пайка

Вакуумная печь для пайки меди
Вакуумную пайку используют для многих металлов, медь не считается исключением. Пайка меди проводится в специализированных печах, или контейнерах, которые потом помещают в печь. Несмотря на сложное оборудование, этот вариант считается наиболее эффективным по всем критериям. Скрепление медных изделий производится мягким припоем, или чистым оловом. Можно использовать другие виды, к примеру, серебряные сплавы, с применением флюса канифольно-спиртового раствора.
Для того чтобы использовать кадмиевый припой, необходимо подготовить специальный инструмент, и запастись необходимыми знаниями в этой области, потому как технологичность у данного материала намного ниже, чем у оловянно-свинцовых тинолей.
Низкотемпературная пайка
Если во время пайки припой не плавится, не стоит спешить, необходимо подождать нагрева паяльника. После того как сплав начинает течь, источник нагрева убирают, позволяя составу самостоятельно заполнить зазоры между элементами. Для избежания излишков, не рекомендуют добавлять сплав, кроме излишков, может быть попадание материала внутрь детали.
Если паять медь, применяя обычные прутья припоя, то его объем должен равняться диаметру соединяемой поверхности. Чтобы примерно рассчитать нужное количество материала, можно прут согнуть буквой Г, и приложить к трубе.
При данной технологии, прочность меди не изменяется, а вот механические критерии уменьшаются.
Высокотемпературная пайка

Высокотемпературная пайка
Данная технология подходит для тех поверхностей, которые будут использоваться с высокими температурами. Так как для осуществления этого процесса необходимая температура должна составлять 700 градусов, используют газопламенный вариант нагрева.
Готовность к спаиванию определяют при помощи прута сплава, который при окончании процесса расплавляется.
Чтобы увеличить качественные характеристики соединения, необходимо предварительно подогреть прут припоя. Преимуществом этого метода соединения является высокие показатели прочности швов, а также их стойкость в процессе эксплуатации, под воздействием высоких температур. Но есть и недостаток, который заключается в неизбежном отжиге меди. Стоит учесть, что при работе этим методом, необходимо иметь достаточную квалификацию и опыт, так как новичок может случайно перегреть медь, тем самым вызвав ее разрыв.
Технология пайки труб
Чтобы паять трубы из меди, необходимо подготовить труборез. После того как нужный кусок трубы отрезан, наружный срез обрабатывается щеткой, для удаления заусениц и шероховатости. Используя труборасширитель, второй отрез трубы расширяют до нужного размера, чтобы одна часть трубы входила в другую.
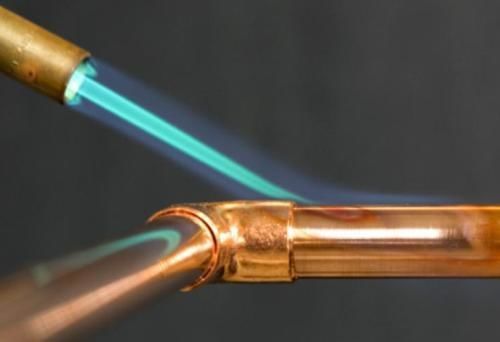
Пайка медных труб
На трубу с меньшим диаметром наносят флюс, и скрепляются два элемента тр. Место соединения равномерно прогревается, для этого можно использовать или горелку или фен. В это место наносят припой, после его расплавления, поверхность полностью закроется им. В качестве сплава можно воспользоваться мягким припоем, он отлично справится с этой работой.
Видео: Пайка медных труб
ecology-of.ru
Меднение в домашних условиях | Строительный портал
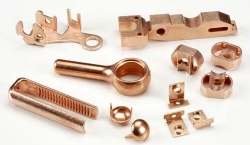
Медь – это один из древних металлов: люди начали применять ее для создания орудий труда еще в 4 тысячелетии до нашей эры. Такое широкое распространение меди объяснимо тем, что вещество встречается в природе в металлическом самородном состоянии. И сегодня медь используется повсеместно – в металлургии, автомобильной промышленности, электротехнике и строительстве.
Содержание:
- Состав меди
- Физические свойства меди
- Процедура меднения
- Использование меднения
- Виды меднения
- Ванны меднения
Состав меди
Металлическая медь представляет собой тяжелый металл розово-красного цвета, ковкий и мягкий, который плавится при температуре больше 1080 градусов по Цельсию, очень хорошо проводит теплоту и электрический ток: электропроводимость меди выше в 1,7 раза, чем алюминия и больше в 6 раз выше, чем железа, и только немного уступает электропроводимости серебра.
Специфические особенности меди определяются содержанием в металле конкретных примесей, количество которых может различаться приблизительно в 10 – 50 раз. По содержанию кислорода принято использовать следующую классификацию меди:
- бескислородная медь с содержанием кислорода меньше 0,001%;
- медь рафинированная с содержанием кислорода от 0,001до 0,01%, но с увеличенным присутствием фосфора;
- медь большой чистоты с содержанием кислорода примерно 0,03-0,05%;
- металл общего назначения с содержанием кислорода 0,05 – 0,08%.
В меди кроме кислорода может присутствовать водород, который в металл попадает в процессе электролиза или при совершении отжига в атмосфере, которая содержит водяной пар. При высокой температуре водяной пар разлагается с формированием водорода, который в медь легко диффундирует. Атомы водорода в бескислородной меди размещаются в междоузлиях кристаллической решетки и на свойствах металла особо не сказываются. В кислородсодержащей меди водород способен взаимодействовать при высоких температурах с закисью меди, при этом образуется в толще меди водяной пар, которому присуще высокое давление, что приводит к вздутиям, трещинам и разрывам. Это явление носит название «водородная болезнь».
Железо, висмут, сурьма и свинец ухудшают пластичность меди. Примеси, что являются малорастворимыми в меди (свинец, кислород, сера, висмут), провоцируют хрупкость при высокой температуре, что затрудняет процесс горячей обработки давлением.
Физические свойства меди
Основное свойство меди, определяемое её использование, - высокая электропроводность или малое удельное электрическое сопротивление. Подобные примеси как железо, фосфор, мышьяк, олово и сурьма, значительно ухудшают её электрическую проводность. На величину электропроводности оказывает большое влияние механическое состояние меди.
Второе важное свойство меди – значительная теплопроводность. Легирующие добавки и свойства уменьшают теплопроводность меди, поэтому созданные на медной основе сплавы самой меди значительно уступают по этому показателю.
Медь при нормальных температурах является коррозиционно устойчивой в таких средах, как пресная вода, сухой воздух, морская вода при небольшой скорости движения воды, неокислительные кислоты и растворы соли при отсутствии кислорода, сухие галогенные газы, щелочные растворы за исключением солей аммония и аммиака, органические кислоты, фенольные смолы и спирты.
В аммиаке, хлористом аммонию, окислительных минеральных кислотах и растворах кислых солей медь не устойчива. Её коррозионные свойства также заметно ухудшаются в некоторых средах с возрастанием количества примесей. Допускается контакт меди с её сплавами, с оловом, свинцом во влажной атмосфере, морской и пресной воде. В то же время контакт меди с цинком и алюминием не допускается вследствие их быстрого разрушения.
Медь, ее сплавы и соединения нашли широкое применение в разных отраслях промышленности. Медь в электротехнике используют в чистом виде в производстве шин контактного и голого проводов, кабельных изделий, электрогенераторов, телефонного оборудования и радиоаппаратуры. Из меди изготавливают вакуум-аппараты, теплообменники и трубопроводы.
Сплавы меди с различными металлами используют в автомобильной промышленности и для изготовления химических аппаратов. Проволока из красной меди изготовления всевозможных шнуров и выгибания самых сложных элементов. Высокие свойства меди делают ее незаменимой при производстве филигранных деталей.
Процедура меднения
Меднением называют процедуру гальванического нанесения меди, толщина слоя которой составляет 1 - 300 мкм и больше. Меднение стали является одним из важнейших процессов в гальванике, что применяется в качестве предварительного процесса при подготовке металлической поверхности для покрытия другими металлами – при хромировании, никелировании и покрытии серебром, а также как законченный самостоятельный процесс.
Использование меднения как подготовительной манипуляции связано с тем, что этот металл способен очень прочно держатся на стали, выравнивать дефекты поверхности. Другие материалы на медь хорошо осаждаются, а вот на чистую сталь – не очень.
Медные покрытия характеризуются высоким сцеплением с разными металлами, высокой электропроводностью и пластичностью. Их принято наносить на стальные, цинковые и алюминиевые детали.
Только что нанесённое покрытие меди имеет ярко-розовый матовый или блестящий цвет, зависимо от технологии нанесения. Медные покрытия в атмосферных условиях способны легко окисляться и покрываться налетом окислов, приобретая пятна различных оттенков и радужные разводы.
Использование меднения
В большинстве своем гальваническое меднение металлов используют в таких случаях:
- В декоративных целях. Огромной популярностью в настоящее время пользуются старинные изделия из меди. Процедура меднения позволяет наносить на металл медные покрытия, которые как бы «состариваются» после специальной обработки и выглядят так, будто изготовлены давным-давно.
- В гальванопластике. Используется гальваническое меднение железа для создания металлических копий изделий разной формы и различных размеров. Создаётся пластиковая или восковая основа, которую покрывают электропроводящим лаком и слоем меди. Подобную технологию меднения часто используют при изготовлении ювелирных изделий, сувениров, барельефов, матриц и волноводов.
- В технических целях. Меднение металла большое значение имеет в электротехнической области. Благодаря низкой стоимости меднения по сравнению с покрытиями золотом или серебром, медные покрытия нашли применение при изготовлении электротехнических шин, электродов, контактов и прочих элементов, которые работают под напряжением. Меднение зачастую используется как покрытие под пайку.
Меднение применяется в сочетании с прочими гальваническими покрытиями:
- При нанесении многослойного защитно-декоративного покрытия. Как правило, медь используется в сочетании с хромом и никелем (3-слойное защитно-декоративное покрытие) и прочими металлами как промежуточный слой для увеличения сцепления с основным металлом и получения более прочного и блестящего покрытия.
- Для предохранения участка при цементации. Меднение свинца способно предохранять участки стальных изделий от цементации - науглероживания. Покрывают медью исключительно те участки, которые подлежат в будущем обработке резанием. Твёрдый науглероженный поверхностный слой не поддается подобным обработкам, а медь может защитить покрытые участки от процесса диффузии углерода в них.
- При восстановлении и ремонте деталей. Меднение металла является важной процедурой при работах реставрационного характера и восстановлении хромированных частей мотто- и автомобильной техники. Наносить принято значительный слой меди – порядка 100-250 мкм и больше, который закрывает дефекты металла и поры и выполняет функции новой основы для последующих покрытий.
Виды меднения
Процедура меднения своими руками доступна для выполнения даже новичками. Для этого достаточно только знать её основные тонкости. Существует два способа меднения в домашних условиях: с погружением в электролит и без погружения.
С погружением в электролит
Металлическое изделие обрабатывают наждачной бумагой для удаления оксидной пленки, протирают щеткой, промывают как следует водой, обезжиривают в горячем содовом растворе и промывают еще один раз. После этого принято опускать в стакан или банку на медных проволочках две медные пластинки, которые являются анодами.
Между пластинками подвешивают на проволочке деталь. Проволочки, идущие от медных пластинок, соединяют вместе и подключают к плюсу источника тока, а деталь – к минусу. После этого в цепь включается реостат для регулировки тока и миллиамперметр. Необходим источник постоянного тока, который имеет напряжение не больше 6 В.
Для меднения дома нужно приготовить следующий раствор электролита. Возьмите 20 грамм медного купороса и 2-3 миллилитра серной кислоты на 100 миллилитров воды и налейте в посуду. Следите, чтобы данный раствор полностью покрыл электроды.
При использовании реостата нужно установить ток в пределах 10 - 15 мА на каждый сантиметр квадратный поверхности детали. Где-то через 20 минут следует выключить ток и вынуть изделие, оно уже покрылось тонким медным слоем. Чем дольше будет идти процесс, тем слой меди получится толще.
Без погружения в электролит
Данную процедуру проводят для стали, алюминия и цинка. С одного конца многожильного провода снимают изоляцию, затем необходимо растеребить тонкие медные проволочки для получения медной кисти. Для удобства работы необходимо привязать ее к медной кисти или деревянной палочке, а другой конец кабеля нужно подсоединить к плюсу источника тока.
Дальше следует приготовить электролит - раствор медного купороса, лучше слегка подкисленный, и налить в широкую склянку, в которую кисть будет удобно макать. Подготовьте металлическую пластинку или какой-то другой маленький предмет с плоской поверхностью. Его нужно протереть с помощью мелкой наждачной шкурки и обезжирить посредством кипячения в растворе стиральной соды.
Затем необходимо положить пластинку в кювету или ванночку и подсоединить ее с помощью провода к минусу источника тока. После того, как схема собрана, вам следует только ввести электролит. Обмакните в раствор медного купороса «кисть», которой следует провести вдоль пластинки, не дотрагиваться до поверхности.
Рекомендуется работать так, чтобы между кистью и пластинкой всегда располагался слой электролита. Все время работы проводки должны быть смоченными раствором. Пластинка на глазах будет покрываться слоем металлической меди красного цвета. Для обработки маленькой детали понадобятся считанные минуты.
Когда вы нанесли покрытие, нужно высушить на воздухе деталь и натереть матовый слой меди до блеска с помощью суконной или шерстяной тряпки. Процесс меднения алюминия, когда изделие в электролитическую ванну не опускают, а обрабатывают небольшими участками снаружи, добавляя электролит, применяют в таких случаях, когда изделие настолько велико, что для него нельзя подобрать подходящую ванны.
Ванны меднения
Установки для меднения от обыкновенных гальванических ванн ничем не отличаются. Электролиты для меднения довольно просто получить, если иметь под рукой необходимые ингредиенты. Бывают два вида медных растворов: щелочные и кислые.
В кислых растворах вы не сможете получить хорошо сцепленные покрытия из меди на цинковых и стальных изделиях, потому что цинк и железо в этом случае растворяются с медью, и нарушается сцепление с защитным покрытием.
Для устранения данной особенности рекомендуется первый тонкий медный слой (2—3 мкм) создать в щелочном растворе для меднения, а в будущем наращивать покрытие до заданной толщины в кислом электролите, который является более экономичным. Цинковые изделия, что имеют сложную форму, лучше всего меднить в щелочных электролитах.
Самыми распространенными кислыми электролитами являются борфтористоводородные и сернокислые. Наибольшее использование нашли сернокислые электролиты, которые отличаются простотой состава, высоким выходом по току и значительной устойчивостью.
Перед меднением деталей из стали в кислых электролитах их рекомендуется предварительно меднить в цианистом электролите или осаждать тонкий подслой никеля. Данные электролиты имеют несколько недостатков.
Один из них состоит в невозможности непосредственного покрытия цинковых и стальных деталей из-за контактного выделения меди, которая имеет плохое сцепление с металлом основы. Также электролиты незначительную рассеивающую способность и более грубую структуру осадков по сравнению с прочими электролитами.
Среди щелочных электролитов меднения известны пирофосфатные и цианистые электролиты.Цианистые электролиты из меди характеризуются высокими рассеивающими способностями, возможностью проведения меднения столярных изделий и мелкокристаллической структурой осадков.
К недостаткам щелочных электролитов относят низкую плотность тока и неустойчивость раствора вследствие карбонизации под действием двуокиси углерода свободного цианида. Помимо этого, цианистые электролиты отличаются уменьшенным выходом по току - не больше 60-70%.
Таким образом, медь является металлом, который используется повсеместно: в автомобильной промышленности, электротехнике и строительстве. А в гальванопластике известна технология меднения для подготовки металлической поверхности под покрытие другими металлами или как самостоятельный процесс.
strport.ru
Температура плавления меди
На заре человечества люди пытались освоить создание различных элементов из металлов. Такие вещи были более изящные, тонкие и долговечные. Одним из первых была «покорена» медь. Наличие руды требовало расплавления материала и отделения от шлака. Это выполнялось в раскаленных углях на земле. Температуру нагнетали мехами, создающими жар. Процесс был горячим и трудоемким, но позволял получать необычные украшения, посуду и орудия труда. Отдельным направлением стало изготовление оружия для охоты, которое могло служить долгое время. Температура плавления меди относительно невысока, что позволяет и сегодня плавить ее в бытовой обстановке и производить предметы, необходимые для ремонта механизмов или электрического оборудования. Какая температура плавки у меди и ее сплавов? Чем можно выполнить эту процедуру в домашних условиях?
Главное о меди
В таблице Менделеева этот материал получил название Cuprum. Ему присвоен атомный номер 29. Это пластичный материал, отлично обрабатывающийся в твердом виде шлифовальным и резным оборудованием. Хорошая проводимость напряжения позволяет активно использовать медь в электрике и промышленном оборудовании.
В земной коре материал находится в виде сульфидной руды. Часто встречаемые залежи обнаруживаются в Южной Америке, Казахстане, России. Это медный колчедан и медный блеск. Они образовываются при средней температуре, как геотермальные тоненькие пласты. Находят и чистые самородки, которые не нуждаются в отделении шлака, но требуют плавления для добавки других металлов, т. к. в чистом виде медь обычно не используется.
Красновато-желтый оттенок металл имеет благодаря оксидной пленке, покрывающей поверхность сразу, при взаимодействии с кислородом. Оксид не только придает красивый цвет, но и содействует более высоким антикоррозийным свойствам. Материал без оксидной пленки имеет светло-желтый цвет.
Плавится чистая медь при достижении 1080 градусов. Это относительно невысокая цифра позволяет работать с металлом как в производственных условиях, так и дома. Другие физические свойства материала следующие:
- Плотность меди в чистом виде составляет 8,94 х 103 кг/м квадратный.
- Отличается металл и хорошей электропроводностью, которая при средней температуре в 20 градусов является 55,5 S.
- Медь хорошо передает тепло, и этот показатель составляет 390 Дж/кг.
- Выделение углерода при кипении жидкого материала начинается от 2595 градусов.
- Электрическое сопротивление (удельное) в температурном диапазоне от 20 до 100 градусов — 1,78 х 10 Ом/м.
Плавление металла и его сплавов
График плавления меди имеет пять ступеней процесса:
- При температуре 20-100 градусов металл находится в твердом состоянии. Последующий нагрев содействует изменению цвета, что происходит при удалении верхнего оксида.
- При достижении отметки температуры в 1083 градуса, материал переходит в жидкое состояние, а его цвет становится абсолютно белым. В этот момент разрушается кристаллическая решетка металла. На небольшой период рост температуры прекращается, а после достижения полностью жидкой стадии, возобновляется.
- Закипает материал при 2595 градусах. Это схоже с кипением густой жидкости, где также происходит выделение углерода.
- Когда источник тепла выключается, то пиковая температура начинает понижаться. При кристаллизации происходит замедление снижения температуры.
- После обретения твердой стадии, металл остывает окончательно.
Температура плавления бронзы немного ниже из-за наличия в составе олова. Разрушение кристаллической решетки этого сплава происходит при достижении 950-1100 градусов. Медный сплав с цинком, известный как латунь, способен плавиться от 900°C. Это позволяет работать с материалами при несложном оборудовании.
Плавление в бытовых условиях
Плавка меди в домашних условиях возможна несколькими способами. Для этого понадобиться ряд приспособлений. Сложность процесса зависит от использования конкретного вида оборудования.
Самым простым способом для плавления меди дома является муфельная печь. У мастеров по металлу найдется такое устройство, которым можно будет воспользоваться. Кусочки металла ложатся в специальную емкость — тигель. Он устанавливается в печь, на которой выставляется требуемая температура. Через смотровое окно можно заметить процесс перехода в жидкое состояние, и открыв дверцу удалить оксидную пленку. Делать это необходимо стальным крюком и в защитной перчатке. Жар от печи довольно сильный, поэтому действовать необходимо аккуратно.
Еще одним способом плавки меди в домашних условиях является пропан-кислородное пламя. Оно хорошо подходит и для сплавов металла с цинком или оловом. В качестве рабочего инструмента в руках мастера может быть горелка или резак. Ацетилен-кислородное пламя тоже подойдет, но погреть материал придется немного подольше. Кусочки сплава помещают в тигель, устанавливаемый на жаропрочное основание. Горелкой выполняют произвольные движения по всему корпусу емкости. Быстрый эффект можно получить, если следить чтобы факел пламени касался поверхности тигеля кончиком синего цвета. Там наибольшая температура.
Еще одним способом является мощная микроволновка. Но чтобы повысить теплосберегающие свойства и защитить внутренние детали техники от перегрева, необходимо поместить тигель в жаропрочный материал и накрыть его сверху. Это могут быть специальные виды кирпича.
Самым простым в экономическом плане способом служит слой древесного угля, на который устанавливается горн с медью. Усилить жар можно при помощи пылесоса, работающего на выдув. Кончик шланга направленный на угли должен быть металлическим, а сопло иметь плоскую форму для усиления потока воздуха.
Изготовление деталей и других элементов из меди, путем ее плавки в домашних условиях, возможно благодаря относительно низкой температуре разрушения кристаллической решетки в материале. Используя описанные выше приспособления и ознакомившись с видео, у большинства получится реализовать эту цель.
Поделись с друзьями
0
0
0
0
svarkalegko.com