МЕТОДЫ КОНТРОЛЯ КАЧЕСТВА СВАРНЫХ ШВОВ. Виды контроля сварки
Виды контроля сварных соединений
Основы сварочного дела
Для получения сварного соединения хорошего качества необходимо осуществлять контроль, начиная с проверки качества подготовки шва и кончая проверкой полученного сварного соединения. Качество основного металла, электродной проволоки, присадочного металла, флюса и других материалов проверяют по сертификатам и заводским документам. Маркировка и качество должны соответствовать установленным техническим условиям и технологическому процессу сварки. Сборку под сварку и разделку шва проверяют по стандартам и техническим условиям.
Сварное соединение проверяется внешним осмотром, металлографическими исследованиями, химическим анализом, механическими испытаниями, просвечиванием рентгеновскими и гамма-лучами, магнитными методами и с помощью ультразвука. Предварительно сварное соединение очищают от шлака, окалины и металлических брызг.
Внешним осмотром выявляют наружные дефекты шва. Осмотр производят невооруженным глазом или с помощью лупы с десятикратным увеличением. Размеры сварных швов проверяют шаблонами и мерительным инструментом.
Металлографические исследования Заключаются в следующем: сверлят отверстие, проходящее через шов и основной металл. Поверхность отверстия протравливают 10%-иым водным раствором двойной соли хлорной меди и аммония в течение 1...3 мин. Осадок меди удаляют водой. Протравленную поверхность осматривают невооруженным глазом или с помощью лупы. При этом выявляют качество провара и наличие внутренних дефектов. Для ответственных сварных конструкций производят более полные металлографические исследования макро - и микрошлифов из специально сваренных контрольных пластин или из пластин, вырезанных из сварных соединений.
Химическим анализом определяют сослав основного и наплавленного металлов и электродов, а также их соответствие установленным техническим условиям на изготовление сварного изделия. Методы отбора проб для химического и спектрального анализов предусмотрены ГОСТ 7122—81.
Механические испытания проводят либо специально сваренных контрольных образцов, либо образцов, вырезанных из сварного соединения. Определяют предел прочности на растяжение, ударную вязкость, твердость и угол загиба.
Рентгенодефектоскопия основана на различном поглощении рентгеновских лучей различными веществами. Этим методом обнаруживают поры,
Микротрещины, непровары, неметаллические включения. Рентгеновские лучи направляют на сварной шов, а с обратной стороны, прикладывают фотопленку. Дефектные места пропускают лучи с меньшим поглощением, чем сплошной металл. После проявления на пленке хорошо видны очертания дефектов шва.
Рентгеновские лучи—коротковолновое электромагнитное излучение— получают в рентгеновских трубках бомбардировкой быстрыми электронами положительного электрода. К рентгеновской трубке подводится ток высокого постоянного напряжения (104—10® эВ). Следует иметь в виду, что рентгеновские лучи вредны для человеческого организма, поэтому рентгеновская трубка изолируется защитным свинцовым кожухом, в котором имеется узкая щель для выхода лучей, направляемых на контролируемое изделие. Для контроля в монтажных условиях очень удобны малогабаритные отечественные рентгеновские аппараты РУП-120-5-1, ИРА-1Д, ИРА-2Д, РИНА-ЗД и др. Толщина металла, которая может контролироваться этими аппаратами,— 25... 100 мм. Схема просвечивания рентгеновскими лучами показана на рис. 117: 1—рентгеновская трубка, 2—контролируемый шов, 3—кассета с фотопленкой.
Гамма-дефектоскопия также основана на различном поглощении веществами гамма-лучей. Как и прирентгенодефектоскопии, получают теневой снимок сварного шва. Гамма - лучи получаются при ядерном распаде естественных и искусственных радиоактивных веществ (радия, мезатория, кобальта, цезия, иридия и др.). Наибольшее распространение как более дешевые получили радиоактивные изотопы кобальта 60Со, цезия 137Cs и иридия 192 1г. Гамма-лучи обладают большой проникающей способностью и позволяют контролировать металл толщиной до 350 мм. Гамма - лучи также вредны для человека, поэтому ампула с радиоактивным веществом помещается в переносной свинцовый контейнер или в стационарный аппарат с дистанционным управлением. Контейнер устанавливают против контролируемого участка, а с обратной стороны сварного шва помещают кассету с пленкой. Затем с помощью дистанционного управления выдвигают ампулу из аппарата или открывают щель в контейнере для выхода гамма-лучей. На рис.118,а показана* схема просвечивания сварного шва: 1—контейнер, '2—ампула, 3— контролируемый шов, 4—кассета с пленкой; на рис.118,б—схема устройства ампулы с радиоактивным веществом: 1—радиоактивное вещество, 2— стеклянная ампула, 3—вата, 4—латунная или алюминиевая оболочка, 5—крышка, 6—свинцовый футляр. Для гамма - просвечивания применяют аппараты ГУП-1г-5-2, ГУП-Сэ-2-1 и др.
Магнитные методы контроля основаны на исследовании магнитных полей рассеяния на намагниченном контролируемом изделии. Применяется несколько методов магнитного контроля сварного шва: магнитно-порошковый, магнитографический, индукционный и др.
Метод порошковой дефектоскопии является наиболее простым, но и менее четким. После намагничивания изделия сварной шов опыливают магнитным порошком (изготовляют из железной окалины)или покрывают суспензией (смесь магнитного порошка с керосином, маслом или другими веществами). В зоне дефекта порошок распределяется неравномерно—скапливается у краев пор, трещин; по этим скоплениям определяют расположение дефектов в сварном шве. Для большей наглядности магнитный порошок или суспензию окрашивают в яркие цвета.
Рис. 118 |
Магнитографический контроль сварных швов разработан ВНИИСТ. Он широко применяется при контроле сварных швов магистральных трубопроводов. На сварной шов трубы накладывают ферромагнитную пленку, а затем намагничивают шов соленоидом или дисковым магнитом. В зависимости от вида и величины дефектов шва в соответствующих местах пленки будет та или иная степень .намагниченности. Магнитные сигналы преобразуют в звуковые с помощью магнитофона или наблюдают на экране осциллографа. Аппараты для магнитографического контроля с осциллографом позволяют проверять сварные швы со скоростью 0,5... 1 м/мин. Кроме высокой производительности они отличаются большой точностью (не уступающей рентгено - и гамма-дефектоскопии), простотой контроля, дешевизной применяемых материалов, возможностью проверки швов в различных пространственных положениях и безопасностью работы.
Индукционный метод контроля основан на рассеянии магнитного потока датчиком дефектоскопа и последующем наведении электродвижущей силы в индикаторе. Наведенный индукционный ток усиливается и подается на телефон, сигнальную лампу или на магнитоэлектрический прибор. По звуку, отклонению стрелки прибора или зажиганию лампы определяют расположение дефекта. Индукционный контроль производят дефектоскопом, МД-138.
Ультразвуковой метод контроля Основан на способности ультразвуковых колебаний проникать в-толщу металла на значительную глубину и отражаться от неметаллических включений и других дефектных участков шва. Ультразвуковые дефектоскопы работают по следующему принципу. Пластинка из кварца или сегнетовой соли под действием переменного электрического поля высокой частоты дает ультразвуковые колебания, которые с помощью щупа направляются на проверяемое сварное соединение. На границе между однородным металлом и дефектом эти волны частично отражаются и воспринимаются второй пластинкой. Под действием переменного давления ультразвуковой волны на гранях этой пластинки появляется переменная разность потенциалов, зависящая от интенсивности отраженной волны. Электрические колебания от граней пластинки усиливаются и направляются в осциллограф. На экране осциллографа одновременно изображаются импульсы излучаемой и отражаемой волн. По относительному расположению этих импульсов и по интенсивности отраженного импульса можно судить о местонахождении и характере дефекта в сварном шве. В настоящее время выпускают ультразвуковые дефектоскопы, работающие на одной пластинке, которая подает короткими импульсами ультразвуковые волны на контролируемый шов. Отраженные волны воспринимаются этой же пластинкой в промежутки времени между импульсами излучения. При этом получается высокая четкость излучаемых и отраженных ультразвуковых волн. Ультразвуковой метод контроля позволяет обнаружить все основные дефекты сварных швов. Кроме того, ультразвуковые дефектоскопы УЗД-7н имеют приспособления для настройки на заданную толщину шва и для определения глубины расположения обнаруженного дефекта. Недостатками ультразвукового контроля являются трудность определения характера дефекта и проверки швов толщиной менее 10 мм.
Испытание сварных швов емкостей на герметичность проводят различными методами.
Испытание керосином: емкости, работающие без избыточного давления, с внутренней стороны обильно смачивают керосином; сварные швы с внешней стороны покрывают меловым водным раствором. При наличии даже мельчайших пор, трещин или неплотностей керосин просачивается через них и на покрытой мелом поверхности появляются керосиновые пятна.
Испытание. сжатым воздухом проводят нагнетанием в испытываемый резервуар сжатого воздуха до давления, указанного в технических условиях на изготовление резервуара. Швы покрывают мыльной эмульсией; при наличии дефектов появляются мыльные пузырьки. Если габариты позволяют погрузить испытываемый резервуар в ванну с водой, тогда дефекты определяют по пузырькам воздуха. Трубопроводы и большие резервуары испытывают сжатым воздухом на величину потери давления за время, установленное техническими условиями.
Вакуум-аппаратом контролируют сварные швы, имеющие односторонний доступ, когда невозможно использовать керосин, воздух или воду. Аппарат состоит из камеры с вакуумметром и насоса. Контролируемый сварной шов покрывают мыльной эмульсией, на нее устанавливают камеру и включают насос, который создает в камере вакуум, в результате камера присасывается к испытуемой поверхности. Для герметичности камера имеет в торце мягкую резиновую прокладку. Если шов имеет дефекты (поры, трещины, неплотности), то появляются мыльные пузырьки, которые наблюдаются через стекло камеры.
Испытание аммиаком проводят нагнетанием в испытываемый резервуар воздуха до рабочего давления или давления, указанного в технических условиях на изготовление изделия. Затем добавляют 1% аммиака от объема воздуха в резервуаре при нормальном давлении. Контролируемые сварные швы обертывают бумагой, пропитанной 5%-ным водным раствором азотнокислой ртути. При наличии неплотностей (поры, трещины и др.) аммиак проходит через них и, взаимодействуя с азотнокислой ртутью, дает на бумаге черные пятна.
Гидравлическое испытание проводят с целью проверки не только плотности швов, но и их прочности. Такому испытанию подвергают сварные трубопроводы, сосуды и резервуары для газа или жидкости, работающие под давлением. Для этой цели все отверстия изделия плотно закрывают заглушками и заполняют его водой. С помощью гидравлического пресса создают давление, в 1,5 раза превышающее рабочее давление, и выдерживают в течение времени, указанного в технических условиях на изготовление изделия. Затем снижают давление до рабочего значения и проверяют наличие потения и пропусков воды в швах. При этом изделие обстукивают молотком на расстоянии 20 мм от сварного шва. Вертикальные цилиндрические резервуары обстукивать при испытании водой не разрешается.
Для контроля сварных соединений магистральных трубопроводов используют передвижную лабораторию PMJ12B, смонтированную на автомашине. Оборудование состоит из рентгеновской установки, позволяющей просвечивать стыки трубопроводов диаметром 720... 1420 мм, гамма-дефектоскопа и установки для магнитографического контроля. За смену лаборатория проверяет гамма - просвечиванием 6 стыков, рентгеновским просвечиванием 12 и магнитографическим контролем 20 стыков. Масса лаборатории— 5 т.
В последнее время с появлением китайской техники на мировом рынке, сварочный аппарат стал наиболее популярным инструментом у владельцев частных домов, коттеджей, дач и гаражей. Учитывая соотношение цен на приобретение сварки …
Выполнение сварочных работ на строительно-монтажной площадке требует особо четкого выполнения всех правил безопасности производства работ. Сварочные работы на высоте с лесов, подмостей и люлек разрешается производить только после проверки этих …
Из применяемых средств контроля особую опасность представляют рентгеновские и гамма-лучи. Рентгеновские и гамма-лучи опасны для человека при продолжительном облучении и большой дозе. Предельно ДОпустимая доза, которая не вызывает необратимых изменений …
msd.com.ua
Виды контроля при сварке
СВАРКА И РЕЗКА МЕТАЛЛОВ
Контроль необходим для определения качества швов и предупреждения брака. При сварке осуществляются три основных вида контроля:
1. Предварительный контроль для предупреждения брака. Этот вид контроля заключается в проверке марки и состава основного металла, качества электродной и присадочной проволоки, флюсов, кислорода, карбида, ацетилена. При предварительном контроле проверяют качество заготовки и сборки деталей под сварку, правильность сборочных приспособлений, состояние и работу контрольно-измерительных приборов, инструментов, квалификацию сварщиков. Предварительный контроль имеет важное значение как средство своевременного предупреждения брака и осуществляется в случае необходимости с помощью заводской лаборатории.
2. Контроль в процессе сварки состоит в систематической проверке исправности используемой сварочной аппаратуры и приспособлений. Кроме того, производится проверка правильности принятого режима сварки и соблюдения сварщиком установленной технологии процесса; контроль осуществляется мастером или контролером ОТК.
3. Контроль готового узла, детали или изделия выполняется контролерами ОТК или мастером. Этот вид контроля включает наружный осмотр и обмер швов, испытание на плотность (для швов сосудов), механические испытания сварных образцов, просвечивание швов, если таковое предусмотрено техническими условиями на сварку. Наиболее сложные операции данного вида контроля выполняются с привлечением заводской лаборатории.
Сварка металлов – классификация и виды
Сварка – технологический процесс, используемый на многих производствах, для соединения деталей путем их нагрева и установления межатомных связей. Существует более ста видов сварки, которые классифицируются по различным признакам. Классификация по …
Лазерная гравировка и резка
Такая технология гравировки, резки и раскроя материала использует лазер высокого уровня мощности. Лазерный луч, который сфокусирован, двигается в графической программе по траектории отрисованного эскиза. Используются разные материалы: двухслойный пластик, органическое …
Как правильно выбрать сварочный кабель для своего апарата?
Как правильно выбрать сварочный кабель? На обеспечение бесперебойной работы сварочного оборудования, а также длительность его эксплуатационного срока зависит то, как правильно выбрать сварочный кабель. Необходимо, чтобы это было приспособление высокого …
msd.com.ua
Пороки сварных соединений и методы контроля сварки » Привет Студент!
Пороками сварных соединений называют такие недостатки их, которые снижают прочность соединения и, следовательно, надежность всей конструкции. Главными видами пороков сварных соединений являются непровар, неполномерный шов, пережог, проплавление и прожог, подрезы, наплывы, пористость, трещины.
Непровар. Непроварами называют отсутствие соединения между основным и наплавленным металлом или недостаточное проникновение наплавленного металла в основной.
Пример непровара показан на фиг. 395, а, б.
Причиной непровара при всех видах сварки может быть загрязнение поверхности свариваемых деталей, при дуговой и контактной сварке—недостаточная сила сварочного тока, при газовой — применение несоответствующего наконечника горелки, при газовой и дуговой — преждевременное введение в сварочную ванну присадочного материала или слишком большая скорость сварки. Непровар является наиболее серьезным дефектом сварных швов.
Неполномерный шов. Сварочный шов может оказаться ниже поверхности свариваемых листов. Недостаточное заполнение шва металлом называют иногда недоваром (фиг. 395, в). Причиной недовара при дуговой и газовой сварке является неравномерность скорости сварки или нарушение равномерности подачи присадочного материала. Неполномерный шов может быть легко исправлен дополнительной наплавкой.
Пережогом в сварочном деле называют сильное окисление наплавленного и прилегающего к нему основного металла; в результате пережога прочность шва понижается. Причиной пережога при газовой сварке является избыток кислорода, при дуговой — излишне длинная дуга. Пережог является результатом совершенно неправильного режима сварки и представляет собой такой же серьезный дефект, как и непровар.
Проплавление и прожог. Проплавлением называют сквозное расплавление основного металла при хорошем соединении свариваемых деталей. Причиной проплавления при всех видах сварки является избыток тепла, подводимого к месту сварки.
Местное расплавление дугой основного металла, сопровождающееся образованием пустой полости или без образования таковой, называется прожогом. Прожоги наблюдаются при сварке деталей небольшой толщины.
Подрезы. Выплавление или выгорание металла по границам сварочного шва называют подрезом (фиг. 395, г). Подрез ослабляет прочность сварного соединения, особенно при динамической нагрузке. Причиной подрезов являются задержки дуги или пламени горелки на одном месте или неравномерность в подаче присадочного материала.
Наплывами называют отсутствие соединения между краем шва и основным металлом при наличии хорошего соединения во всей остальной части шва. Причиной наплывов может быть густоплавкость присадочного материала.
Пористостью сварного шва называют наличие в нем газовых пузырей, свищей, включения шлаков. Причиной пористости является загрязнение основного и присадочного материала.
Трещины вызываются большими внутренними напряжениями, возникающими в основном и наплавленном металле. Причиной больших внутренних напряжений может быть неправильное ведение сварки: отсутствие зазора между свариваемыми деталями, большое количество сварочных швов на небольшом участке металла, отсутствие подогрева и термической обработки для смягчения внутренних напряжений. В ряде случаев трещины можно исправить заваркой или перекрытием накладками, привариваемыми к изделию.
Кратерами называются углубления в сварочном шве при дуговой сварке. Причиной кратеров являются обрывы дуги. Незаваренные кратеры в середине швов, выполненных ручной или автоматической сваркой (вследствие обрыва дуги), являются так же серьезными дефектами, так как они могут служить очагами образования трещин в процессе работы сварной конструкции.
Методы контроля сварки
Технический контроль производства сварочных работ нельзя ограничивать оценкой степени доброкачественности уже выполненных работ, а следует распространять на самый процесс работы и даже на подготовку к ней. Поэтому при правильной постановке дела технический контроль должен быть предварительным, пооперационным — во время самого процесса сварки и приемочным— после окончания сварочных работ.
Предварительный контроль заключается в проверке качества основного и присадочного металла, обмазок и флюсов, проверке правильности разделки швов, точности совпадения кромок и соблюдения необходимых зазоров. К предварительному контролю относят также проверку квалификации сварщика.
Контроль во время процесса сварки (пооперационный). В процессе сварки необходимо следить за силой сварочного тока или применением соответствующих горелок, толщиной наплавленного слоя, за очисткой поверхности шва от окалины и шлака в случае наложения следующего слоя, за правильностью ведения процесса в целом.
Контроль по окончании работ. Для выявления дефектов сварки пользуются внешним осмотром, просвечиванием рентгеновскими лучами, магнитным методом, механическими испытаниями, металлографическими исследованиями.
Внешний осмотр. После прихватки и сварки изделия подвергают осмотру. Осмотром проверяют правильность размеров шва, а также его качество. В случае обнаружения мест, подозрительных в отношении трещин, такие места промывают спиртом и подвергают травлению 10%-ным водным раствором азотной кислоты, после чего поверхность шва принимает матовый вид. Подготовленная таким образом поверхность шва просматривается в лупу.
Просвечивание рентгеновскими лучами. Этот метод контроля основан на свойстве рентгеновских лучей неодинаково проникать через различную среду. В сварном шве рентгеновские лучи поглощаются металлом в большей мере, чем шлаковыми включениями, газовыми пузырями, трещинами; также чем толще слой металла, тем большее количество лучей поглощается им.
Различают два способа рентгеновского контроля — визуальный и фотографический. Первый заключается в наблюдении картины просвечивания на экране, второй — в фотографировании этой картины. Фотографический метод дает более надежный результат.
Доброкачественный шов дает ровное потемнение пленки, а различные дефекты создают отклонения от такого характера рентгенограммы; так, непровар обнаруживается резкостью границы между наплавленным и основным металлом; шлаковые включения и базовые пузыри выходят на негативе темнее основного металла и т. д.
На фиг. 396 показан рисунок рентгенограммы V-образного шва с непроваром в нижней части.
Рентгеновский контроль применяют в целях установления правильных режимов сварки деталей, дающих большой процент брака, а также в тех случаях, когда о качестве сварки трудно судить по наружному осмотру; целесообразно также применение этого метода контроля при опытной сварке сложных и особо ответственных деталей.
Длина просвечиваемого участка шва обычно не превышает 300 мм. В некоторых случаях требуется просвечивание рентгеном 10, 20% и более сварных швов данного изделия.
Магнитный контроль. При магнитном испытании сварочный шов покрывают бумагой, на которую насыпают порошок магнитного железа. При пропускании через исследуемое сварное соединение магнитного потока частицы порошка расположатся по направлению магнитных линий. В случае наличия в сварочном шве шлаковых включений, непровара, трещин сопротивление шва магнитному потоку в местах таких дефектов сварки будет больше, чем в сплошном металле, и распределение магнитных линий окажется неравномерным. Неравномерность распределения силовых линий в исследуемом материале отражается на распределении частиц порошка, находящегося на бумаге, и позволяет установить наличие в исследуемом шве дефектов.
Магнитный контроль производят также приборами, действие которых заключается в намагничивании исследуемого соединения электромагнитом. Наличие дефектов (непровар, шлаковые включения, газовые пузыри, трещины) отражается на степени намагничивания и улавливается по силе звука в телефонной трубке или по показанию стрелки прибора.
Магнитный контроль дает хороший результат в случае стыковых соединений листов толщиной до 25 мм; для швов внахлестку и тавровых его не применяют.
Механические испытания. Наплавленный металл и сварные швы подвергают испытаниям на растяжение, удар и изгиб, для чего готовят образцы, форма и размер которых должны соответствовать действующим ГОСТ. Механические испытания готовых изделий должны производиться под нагрузками, обеспечивающими необходимый запас прочности сварной детали при ее работе, но без излишних перегрузок. В результате нагрузок, значительно превышающих нагрузку детали в работе, могут возникать мелкие трещины, не различимые при испытании, но могущие повести к разрушению изделия в процессе его службы.
Сварные сосуды, котлы, трубопроводы испытывают на прочность гидравлическим давлением. Обнаруженные такими испытаниями неплотности не следует устранять подчеканкой, так как подчеканенные участки впоследствии быстро корродируют; участки шва с обнаруженными неплотностями необходимо вырубать, заваривать и подвергать новому испытанию.
Металлографический контроль. Рассмотрение макро- и микрошлифов металла сварного соединения позволяет судить о качестве сварного металла и выявить структуру переходных зон. Этим методом обнаруживают и все виды пороков сварки.
Систематически проводимый металлографический контроль является надежным средством для установления рационального режима сварки в определенных условиях производства сварочных работ.
Техника безопасности при сварочных работах
Техника безопасности при сварочных работах подробно регламентируется соответствующими инструкциями и правилами; мы остановимся лишь на главнейших и общих требованиях.
При газовой сварке необходимо правильное обращение с кислородными баллонами. Нельзя допускать баллоны к эксплуатации, если срок периодического испытания их уже наступил; этот срок должен быть указан клеймом, накладываемым технической инспекцией. Наполненные газом баллоны не должны подвергаться ударам и нагреву, так как возникающие при ударе искры могут вызвать взрыв баллона. Редуктор, навинчиваемый на кислородный баллон не должен иметь следов масла и жира. Нельзя допускать переноску баллонов на руках во избежание удара, если баллон уронят. Редуктор должен содержаться в чистоте, так как от трения частиц пыли, ржавчины также может возникнуть искра, которая приводит в атмосфере кислорода к возгоранию металла редуктора. Отогрев вентиля и редуктора можно производить только горячей водой или паром, не допуская применения пламени горелок.
Ацетиленовые генераторы необходимо содержать в чистоте и держать их на расстоянии не ближе 10 м от горелок. Подводящие газ шланги не должны пропускать газа. Водяной затвор должен быть всегда наполнен водой и находиться под постоянным наблюдением сварщика. Сварщик обязан следить за плотностью закрывания кранов горелки и не должен выпускать из рук или ставить куда-либо горящую горелку.
Все части электросварочных установок, находящиеся под напряжением, должны быть надежно заземлены медным проводом сечением не менее 6 мм2. Прикосновение голыми руками к токоведущим частям сварочной машины допускается только при выключении рубильника. При всех работах по электросварке внутри сосудов, цистерн и резервуаров рекомендуется пользоваться резиновыми ковриками или резиновыми галошами.
Для предохранения глаз от поражения действием световых лучей при газовой сварке необходимо пользоваться очками с защитными стеклами темного цвета; при дуговой сварке защитные стекла должны быть укреплены в щитке или шлеме, защищающем не только глаза, но и лицо сварщика от ожогов.
Для защиты от капель и брызг расплавленного металла сварщик должен пользоваться рукавицами и быть одетым в спецодежду, плотно прилегающую к телу.
В помещениях, предназначенных для сварочных работ, необходимо устраивать вентиляцию, гарантирующую отвод вредных газов, и нельзя допускать хранения легковоспламеняющихся материалов.
Рабочие, занятые очисткой швов от окалины и шлака, должны быть снабжены очками, предохраняющими глаза от засорения.
Нельзя допускать производства сварочных работ на изделиях, находящихся под давлением жидкости или газов.
Токоведущие сварочные провода и газовые шланги нельзя укладывать совместно.
Место производства сварочных работ необходимо ограждать перегородками или переносными щитками.
Скачать реферат: У вас нет доступа к скачиванию файлов с нашего сервера. КАК ТУТ СКАЧИВАТЬ
Пароль на архив: privetstudent.com
privetstudent.com
МЕТОДЫ КОНТРОЛЯ КАЧЕСТВА СВАРНЫХ ШВОВ
Полуавтоматы для дуговой сварки и их основные узлы
Методы контроля качества сварных соединений могут быть разделены на две основные группы: методы контроля без разрушения образцов или изделий - неразрушающий контроль; методы контроля с разрушением образцов или производственных стыков - разрушающий контроль. Обе группы методов контроля регламентируются соответствующими стандартами. Группа методов контроля, объединенная общими физическими характеристиками, составляет вид контроля. Все виды неразрушающего контроля классифицируются по следующим основным признакам: по характеру физических полей или излучений, взаимодействующих с контролируемым объектом; по характеру аналогичных взаимодействий веществ с контролируемым объектом; по различным видам информации о качестве контролируемого объекта. Существуют десять видов неразрушающего контроля: акустический, капиллярный, магнитный, оптический, радиационный, радиоволновой, тепловой, течеисканием, электрический, электромагнитный. Для контроля качества сварных соединений могут быть применены все перечисленные виды, однако наиболее широкое применение на практике нашли методы: акустический, капиллярный, магнитный,
радиационный и течеисканием. Каждый вид контроля имеет свою оптимальную область применения, отличается определенными достоинствами и недостатками. Поэтому наиболее полную информацию о качестве изделия или сварного шва можно получить только при сочетании различных видов контроля. Наиболее распространенным видом неразрушающего контроля является внешний осмотр и обмер сварных швов, который имеет существенное значение для получения качественных сварных конструкций. Широкое применение получил радиационный вид контроля, осуществляемый с помощью рентгеновского и гамма-излучений, которые проникают через контролируемый объект и изменяют интенсивность излучения в местах наличия дефектов. Это изменение регистрируется на рентгеновской пленке или на пластине (радиографический метод). Радиационные методы позволяют выявить скрытые внутренние дефекты в стыковых швах практически любых материалов. Невозможно обнаружить дефекты только в угловых швах. Из акустических методов контроля наибольшее распространение, получила ультразвуковая дефектоскопия. Хорошо обнаруживаются дефекты с малым раскрытием, типа трещин, газовых пор и шлаковых включений, в том числе и те, которые невозможно определить радиационной дефектоскопией. Среди магнитных методов контроля следует отметить магнитографический и магнитопорошковый. Наибольшее распространение имеет магнитопорошковый метод, так как он позволяет визуально наблюдать расположение ферромагнитного порошка вокруг дефекта. Однако этот метод применим только для контроля ферромагнитных материалов (углеродистые стали). В капиллярном виде контроля используют движение индикаторного вещества, т. е. проникновение индикатора по микропорам и микротрещинам вглубь дефектов как бы по капиллярам. После нанесения индикаторов на поверхность шва и выдержки излишний индикатор удаляют. Оставшийся в дефектах индикатор под воздействием облучения начинает высвечиваться, и тем самым обнаруживаются дефекты сварного шва. При контроле течеисканием также используют движение контрольного вещества для обнаружения течей - сквозных несплошностей в сварных соединениях. С помощью этого вида контроля проверяют герметичность свариваемого изделия. Как правило, это сосуды и трубопроводы, работающие под давлением. Он основан на регистрации специальными приборами или счетчиками утечки индикаторных жидкостей или газов через сквозные дефекты в сварных швах. Контроль герметичности течеисканием может быть применен для любых материалов любой толщины. К основным методам контроля относятся: пневматический, гидравлический, керосиновый, галоидный, химический и люминесцентно-гидравлический. Выбор метода контроля связан с определением возможностей различных методов выявить опасные для работы данного сварного соединения дефекты, их производительностью и стоимостью. Из всего многообразия методов и видов контроля представляется необходимым подробно рассмотреть только основные, широко применяемые в производственных условиях. Осмотр и обмер готового сварного изделия является первым и наиважнейшим этапом приемочного контроля. Прежде всего осматривают все сварные швы и поверхность изделий в зонах термического влияния. Внешний осмотр позволяет обнаружить такие наружные дефекты, как подрезы, незаваренные кратеры, выходящие на поверхность трещины, непровары, наплывы и т. д. При осмотре предварительно очищенной от шлака и брызг поверхности швов и околошовных зон применяют лупы и при необходимости - дополнительное местное освещение. Размеры швов - ширину, выпуклость, плавность перехода шва к основному металлу, катет шва - проверяют с помощью специальных приборов или шаблонов. Из наиболее известных и широко применяемых методов неразрушающего контроля следует кратко описать гидравлические и пневматические испытания, рентген-контроль, испытание керосином. Гидравлическим испытаниям подвергают трубопроводы, резервуары, технологические аппараты и другие объекты с целью проверки плотности и прочности сварных швов. Гидравлические испытания регламентируются стандартом, который предусматривает осуществление их тремя способами: гидравлическим давлением, наливом воды и поливом водой. При испытании гидравлическим давлением изделие заполняют водой, герметизируют и с помощью насоса создают в замкнутой системе необходимое заданное давление (по манометру), выдерживают установленное время, остукивают молотком с круглым бойком вдоль швов и осматривают сварные швы с целью выявления мест утечек. Испытания наливом воды проводятся для контроля соединений (швов) открытых сосудов, резервуаров и т. д. Сварные швы протирают и сушат, обдувая воздухом. Заполняют изделие водой и по истечении времени все швы подвергают внешнему осмотру. Этот контроль проводят, как правило, при положительных температурах. Испытания поливом водой проводят в тех случаях, когда есть возможность доступа к сварным швам с двух сторон, но изделия очень громоздкие. С одной стороны поливают водой из брандспойта (давление до 1 МПа), а с другой стороны
производят внешний осмотр с целью выявления течей. Вертикальные соединения поливают снизу вверх. Это метод применяется при сварке и проверке корпусов судов, резервуаров и т. д. Пневматические методы испытаний применяют для контроля сварных швов замкнутых систем - трубопроводов, сосудов и аппаратов. Испытания сжатым воздухом проводятся путем создания испытательного давления, приблизительно на 10—20 % выше рабочего. Швы покрывают пенообразующими составами. В местах, где имеются сквозные дефекты, под действием выходящего воздуха образуются пузырьки, по которым и определяют место нахождения дефекта. Пенообразующие вещества наносят на поверхность швов кистью или пульверизатором. Составы пенообразующих веществ различают и применяют для летнего пользования и для соответствующей работы при отрицательных температурах до —30 °С. Контроль рентгеновским излучением в технике известен как контроль радиационным методом и основан на способности рентгеновских лучей проникать через сварное соединение и воздействовать на регистрирующее устройство (фотопленку). В зависимости от способа регистрации результатов различают три метода радиационного контроля: радиографический, радиоскопический и
радиометрический. Наибольшее распространение получил радиографический метод контроля сварных соединений, поскольку снимок является документом, подтверждающим качество сварного шва. Рентгеновский снимок на фотопленке хранится столько времени, сколько по техническим условиям должно работать изделие. Например, рессивер вагона метро должен работать 10 лет - столько же лет хранится в архиве рентгеновская пленка продольного шва рессивера. Образцы рентгеновских снимков на рис. 118.
Рис. 118. Дефекты сварных швов, выявленные рентген-контролем: а - продольная трещина; б - непровар; в - поры; г - шлаковое включение
Среди известных смесей жидких углеводородов, применяемых для контроля непроницаемости, наиболее широко используется керосин. Это объясняется его свойствами (высокой жидкотекучестью, высокой смачивающей способностью и т. д.), которые обеспечивают четкое обнаружение дефектов. Контроль керосином отличается простотой и общедоступностью, не требует сложного и дорогого оборудования, дефицитных материалов. Различают четыре способа испытания керосином: керосиновый, керосинопневматический, керосиновакуумный и керосиновибрационный. При керосиновом способе сварное соединение простукивают молотком на расстоянии 30—40 мм от шва и тщательно очищают швы от шлака, масла и других загрязнений. Для лучшего удаления шлака и развития несквозных дефектов в сквозные целесообразно в течение 10—15 мин подвергнуть вибрации сварное соединение. После очистки на поверхность шва наносят тонкий равномерный слой меловой суспензии. Меловую суспензию готовят из расчета 350—450 г молотого просеянного мела на 1 дм3 воды. После высыхания суспензии противоположную сторону сварного шва смачивают керосином 5—10 раз. В местах течей на меловой суспензии появляются темные пятна, обозначающие наличие дефектов. Описывать другие методы контроля (как неразрушающего, так и разрушающего) не представляется возможным, так как их на сегодняшний день более сотни, разрабатываются и внедряются все более современные (быстродействующие и более точные). Необходимо отметить некоторые виды испытаний при контроле качества сварных соединений разрушающими методами. Механическим испытаниям подвергаются как отдельные образцы, вырезанные из сварных швов, так и детали и узлы. Эти испытания подразделяются на статические и динамические. Статические испытания подразделяются на следующие виды: растяжение, изгиб, смятие, ползучесть. Динамические испытания - на ударный изгиб, усталость. Проводятся и металлографические исследования для выявления изменений, происходящих в металле при различных режимах сварки и термообработки; различают макроанализ и микроанализ. Кроме указанных методов разрушающего контроля проводят измерение твердости, коррозионные испытания, химический и спектральный анализ сварных соединений. Более подробное ознакомление с различными видами и методами контроля сварных соединений представляется самим читателям при самостоятельном углубленном изучении сварочных процессов.
В этих полуавтоматах с помощью специального блока управления обеспечивается запрограммированная зависимость сварочного тока от
марки электродной проволоки, ее диаметра, режима сварки. Это упрощает настройку полуавтомата. Режим сварки можно задавать
изменением положения ручки регулятора напряжения источника
[4] Для электродов типов Э38, Э42, Э46, Э50, Э42А, Э46А, Э50А, Э55 и Э60 приведенные значения механических свойств установлены в
[5] ОП - обратная полярность, ток постоянный (=) или переменный
(-)■
Покрытые электроды для ручной дуговой сварки и наплавки подразделяются по назначению на группы: 1) для сварки углеродистых и низкоуглеродистых конструкционных сталей обозначаются буквой У; 2) для сварки легированных сталей - Л; 3) для сварки теплоустойчивых
[6] Цифрой 0 обозначают электроды для сварки или наплавки только на постоянном токе обратной полярности.
[7] - ОП (обратная полярность).
Контрольные вопросы:
[8] Горелка ГЗУ-3 - универсальная; ГЗУ-4 - для сварки чугуна и цвет металлов (кроме меди), а также наплавки, пайки, нагрева.
[9] Горелка типа Г1 - безынжекторная, остальных типов -
инжекторные. ** Горелка ГС-4 предназначена для подогрева, горелка Г2-04 по конструкции подобна ранее выпускавшимся горелкам Г2-02, «Звездочка», «Малютка»; горелка ГЗ-03 заменила выпускавшиеся
горелки «Звезда», «Москва», ГС-3, ГС-3А.
Таблица 62
Техническая характеристика безинжекторных горелок типа Г1
[11] ПМЦ - припой медно-цинковый. ** ПСр - припой серебряный.
Надежность эксплуатации сварных соединений зависит от их соответствия нормативно-технической документации, которая регламентирует конструктивные размеры и форму готовых сварных швов, прочность, пластичность, коррозионную стойкость и свойства сварных соединений. Сварные соединения, выполненные …
Для предупреждения пожаров необходимо соблюдать следующие противопожарные мероприятия. Постоянно следить за наличием и исправным состоянием противопожарных средств (огнетушителей, ящиков с сухим песком, лопат, пожарных рукавов, асбестовых покрывал и т. д.). …
msd.com.ua
Виды и методы неразрушающего контроля сварных соединений
Под поверхностью внешне красивого и аккуратного сварного шва могут скрываться. Недопустимо, чтобы из-за подобных дефектов ответственная деталь развалилась в самый неподходящий момент. Эта проблема остро стоит перед разработчиками самой разной продукции.
-
В машиностроении, для которого особенно важна способность конструкций противостоять динамическим нагрузкам. Не вышедшие на орбиту спутники, разбившиеся самолеты, попавшие в аварию автомобили или затонувшие корабли – вполне возможно, что все это результат некачественно выполненной сварки.
-
В строительстве, где преобладают статические нагрузки. Многоэтажные небоскребы, пролеты мостов или большие по площади перекрытия простоят много лет лишь в том случае, если надежно соединить их металлические конструкции и арматуру. Причиной обрушения может стать даже незначительная трещина.
-
В массовом производстве, когда идет речь о десятках и сотнях тысяч сварных соединений. Падение спроса на продукцию из-за ее низкого качества приводит к большим финансовым потерям. Ради того, чтобы подобного не произошло, стоит пойти на дополнительные траты и организовать пост контроля качества сварных швов.
-
При изготовлении штучной продукции и опытных образцов. Результаты научного эксперимента могут оказаться не точны, а время, потраченное на проведение замеров, будет потрачено впустую, если не соблюсти точных параметров сварного соединения при изготовлении ответственного оборудования. Уникальное изделие, созданное для того, чтобы прослужить десятки лет, не проработает и малой части расчетного срока. А все из-за того, что вовремя не была проведена дефектоскопия.
Повсюду соединительные швы должны быть надежны. Важно, чтобы они были равномерны, герметичны, прочны и по всей площади полностью соответствовали предъявляемым требованиям.
Применяемые методы проверки
Чтобы повысить качество продукции и своевременно выявить опасный брак, ученые разработали методы неразрушающего контроля сварных соединений. Для этого они использовали процессы, в основе которых лежат различные физические явления. На сегодняшний день наибольшее распространение получили следующие способы обнаружения дефектов:
-
Визуально-оптический. Используя оптические приборы, можно во всех подробностях разглядеть поверхность детали и обнаружить пропуски и трещины, невидимые невооруженным глазом. В большинстве случаев для этого используют устройства с увеличением до десяти крат. Но если у контролера возникнут сомнения, допускается двадцатикратное увеличение. Заглянуть при этом под поверхность шва все равно не получится, а потому этот метод контроля – первичный. Он не дает полной и объективной картины
-
Радиографический, при котором используют гамма-лучи, проходящие сквозь контролируемую деталь. Полученное таким способом изображение фиксируется на пленке. Эта методика довольно эффективна, но позволяет получить представление лишь об ограниченном участке шва. Скорость подобного обследования невелика и технология плохо подходит для массового производства.
-
Радиоскопический. В этом случае также применяется источник гамма-излучение, но изображение не фиксируется на пленке, а выводится на экран специального устройства. Появляется возможность контроля в реальном времени, что важно при постоянном обследовании больших партий продукции. С учетом этого можно закрыть глаза даже на относительно высокую стоимость оборудования.
-
Радиометрический. Изображения на экране или пленке невозможно перевести в цифры, а визуальная оценка не всегда бывает объективна. Измеряя интенсивность гамма-излучения при его прохождении через сварное соединение, и сравнивая полученные результаты с результатами, полученными при обследовании эталонных образцов, удается значительно повысить стандарты контроля качества.
-
Ультразвуковой. Это самый эффективный из методов акустической дефектоскопии. Его целесообразно использовать в тех случаях, когда толщина сварного шва превышает 4 мм. Известно, что ультразвуковые волны отражаются от границы между разными средами. Анализируя характер прохождения этих волн через структуру материала, можно составить точное представление о ее однородности.
-
Магнитографический. Намагничивая контролируемые детали и регистрируя изменение магнитных полей, полученные результаты фиксируют на прижимаемом к шву специальном носителе. Полученные данные точны, и по ним можно судить не только о внешних, но и о внутренних дефектах. Основной недостаток очевиден – как и радиография, такой способ контроля требует определенного времени.
-
Магнитопорошковый. С помощью суспензии на основе смешанного с керосином флюоресцирующего порошка, частицы которого намагничены, удается обнаружить малые, шириной в один и более микрон, трещины. Под воздействием созданного переменного магнитного поля частицы скапливаются в местах дефектов и повторяют их форму. Это можно хорошо рассмотреть, подсветив их кварцевой лампой. При всей своей относительной простоте магнитопорошковый метод показывает достаточную эффективность в основном при контроле уже зачищенных швов.
-
Индукционный. С помощью искателя, конструкция которого может быть различна, можно проверить однородность магнитного поля, создаваемого на ограниченном, до 300 мм длиной, участке шва. Таким образом, регистрируются потоки рассеивания, возникающие в местах дефектов. Обследование не занимает много времени. Но это лишь предварительный метод диагностики, требующий обследования места обнаруженного повреждения более точными способами.
-
Вихретоковый. Основанный на взаимодействии специального преобразователя с создаваемыми внутри контролируемого участка вихревыми токами, этот метод неразрушающего контроля сварных соединений не получил широкого распространения. Дело в том, что на результаты измерений оказывает сильное влияние однородность материала, создавая трудности для точного выявления места дефекта. Его просто не видно на фоне возникающих помех.
-
Капиллярный. Этот метод дефектоскопии был известен еще в Средние века. Однако, и сегодня он не потерял своей актуальности. Его суть в том, что на обследуемую деталь наносят проникающую жидкость – ее называют пенетрант – и по следам ее проникновения выявляют трещины и другие повреждения. Чтобы облегчить процесс, пенетрант часто окрашивают во флюоресцирующие цвета. Понятно, что таким образом удается выявить лишь внешние повреждения. Зато он подходит для обследования ферромагнитных материалов.
-
Пузырьковый, с использованием вакуумных камер. Нанеся на поверхность детали мыльный раствор, и создав разряжение с помощью вакуумной камеры, удается с достаточно высокой точностью обнаружить место, где сварной шов негерметичен. Этот специфический способ можно использовать при проверке таких конструкций, как цистерны, гидроизоляционные ящики или газгольдеры. Однако установка вакуумной камеры – непростая задача. Высокая стоимость оборудования и трудности при его использовании ограничивают применение эффективной методики.
-
Контроль сварных швов с помощью газоэлектрических течеискателей. Наибольшее распространение получили устройства, в которых в качестве рабочего тела используется гелий. С одной стороны проверяемой поверхности устанавливают вакуумную камеру, оборудованную масс-спектрометром. С другой – обдувают сварное соединение гелем, находящимся под небольшим давлением. Если шов негерметичен, то вещество проникает внутрь камеры. По регистрируемым показаниям можно судить о размерах повреждения. Из-за сложности оборудования этот метод оправдывает себя лишь при проверке особо ответственных деталей.
Существуют и другие технологии, по разным причинам применяемые лишь ограниченно, или считающиеся неэффективными.
Выбор технологии
Желая наладить контроль сварных швов, нужно осознавать, что выбор конкретной методики зависит от множества факторов.
-
Объемов выпуска продукции. Сколь бы ни были точны полученные данные, использовать при крупносерийном производстве способы проверки, отнимающие много времени, попросту нерентабельно. С его помощью возможен лишь выборочный контроль, а он не всегда дает объективную картину. В то же время, при опытном, штучном или мелкосерийном производстве, скорость контроля не имеет решающего значения. Когда стоимость конечного продукта высока, а его качество имеет решающее значение, имеет смысл потратить время на самое тщательное обследование.
-
Необходимой точности замеров. Для изделий, где герметичность сварного соединения не имеет значения, и не испытывающих высоких нагрузок, достаточно получить информацию общего характера. Это касается бытовой техники, простых строительных конструкций или изделий легкой промышленности. В случае, когда важна герметичность шва, следует отдать предпочтение способам, выявляющим даже малейшие неплотности в соединениях. Для обследования деталей, испытывающих высокие нагрузки, придется использовать технологии, способные дать максимально полное представление о внутренней структуре сварного шва. Ведь скрытые дефекты, проявившиеся спустя какое-то время, часто становятся причиной серьезных техногенных катастроф. В связи с этим отдельную проблему представляет неразрушающий контроль сварных соединений трубопроводов. Тысячи километров магистралей, по которым течет вода, движется жидкое или газообразное топливо могут быть выведены из эксплуатации из-за невидимой глазу трещины. Разрыв труб, по которым в производственных цехах перекачиваются химически агрессивные вещества, недопустим, так как вполне способен привести к человеческим жертвам.
-
Особенностей производства. При анализе сварных соединений электронных компонентов, нагрев которых недопустим, а размер деталей которых мал, приходится отказываться от многих эффективных методов дефектоскопии в пользу пусть и не столь надежных, но лучше подходящих для решения задачи. Иные проблемы приходится решать там, где длина швов составляет многие сотни метров. При прокладке газопроводов или строительстве судов не получится использовать оборудование, с успехом работающее в научной лаборатории.
-
Применяемые материалы. В современном производстве используются различные детали и сплавы. Все они имеют свои особенности, отличаясь по внутренней структуре, магнитным свойствам, реакции на температурный нагрев или воздействие давлением. Все это следует учитывать при выборе способа контроля. Ведь методика, хорошо зарекомендовавшая себя при проверке качества сварных швов изделий, выполнены из стали, может оказаться неэффективна для дефектоскопии деталей, изготовленных из алюминия.
Вникая в суть процесса
Важно не только правильно определиться с технологией проведения замеров. Многое зависит от того, насколько хорошо используемое оборудование будет освоено персоналом. Применяемые в современном производстве способы автоматизации не отменяют человеческого фактора. Ведь обслуживают автоматику все равно люди. А потому необходимо, чтобы персонал не просто бездумно нажимал кнопки и реагировал на сигналы, подаваемые чувствительной аппаратурой. Подобный подход ошибочен, хотя и выглядит для многих организаторов производств привлекательно. Лишь понимая суть происходящих процессов, можно дать объективную оценку данным, полученным при неразрушающем контроле сварных соединений.
Поделись с друзьями
0
0
0
0
svarkalegko.com
Контроль сварных швов и его разновидности
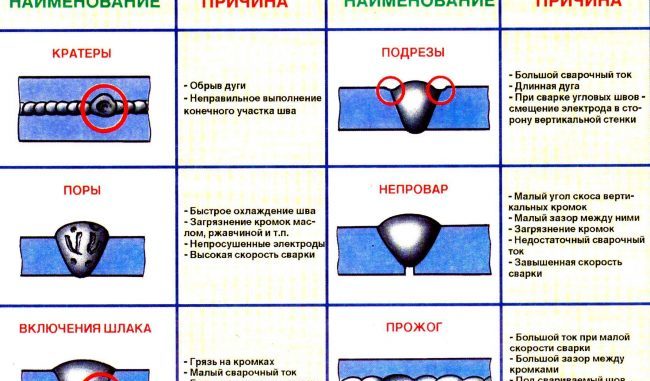
Сварное соединение — неразъемная конструкция, содержащая сварные швы, один или несколько. Сварка металлических изделий выполняется в соответствии с определенным ГОСТом, в зависимости от ее вида (электродуговая сварка, ручная, автоматическая и др).по окончанию сварочных работ обязательно выполняется контроль качества сварных швов полученной конструкции.
Применяют несколько методов контроля качества для обнаружения дефектов и выявления брака сварных элементов. Выполняются они поэтапно. Методы контроля и его технология указываются в нормативной и технической документации в соответствии с ГОСТом 3242-69.
Технический осмотр
Технический осмотр – начальный этап контроля сварного соединения. С помощью технического осмотра можно выявить поверхностные дефекты, поверхностное окисление сварного шва, а также заданные по чертежу отклонение формы и размера. Внешним осмотром определяют брак такого рода как прожоги, наплывы, частичные непровары, трещины. Осмотр может производиться как с увеличительной лупой, так и без нее.
Капиллярный контроль (метод капиллярной дефектоскопии)
Этот вид контроля предназначается для выявления как поверхностных, так и сквозных дефектов сварной конструкции. Метод капиллярной дефектоскопии использую при сварке черных и цветных металлов. Суть этого метода заключается в том, насколько специальные индикаторные жидкости (окрашенные или светящиеся) могут внедряться и проникать в места дефектов сварного шва, а также возможности ультрафиолетовых лучей заставлять светиться эти вещества, которые называются люминофорами. Для применения окрашенных жидкостей облучение не требуется. Капиллярный контроль выявляет дефекты слабо заметные человеческому глазу, это мелкие трещины, расслоения и раковины.
Магнитный метод контроля
Метод магнитного контроля основывается на возможности магнитных силовых линий менять свое направление в местах, где выявлен дефект или брак. Этот способ помогает выявить наличие дефектов как снаружи, так и внутри металла.Существует три разновидности магнитного контроля:
1. Порошковый. Данный способ предполагает использование порошка, состоящего из мелкой окалины. Этот порошок необходимо тонким слоем распределить на поверхности контролируемого сварного шва, затем с помощью электромагнита произвести намагничивание металла. Струей воздушного потока производят сдув мелкоизмельченной окалины, далее можно оценить результат по оставшемуся порошку на поверхности сварного шва
2. Индукционный. Основное отличие этого метода заключается в том, что намагничивание производится с помощью индукционной катушки, А для самого контроля брака сварного шва применяют магнитные дефектоскопы.
3. Графический. Этот метод заключается в использовании магнитной ленты, которую необходимо плотно прижать к поверхности шва сварного соединения, а отклонения магнитного поля отобразятся на экране электронно-лучевого прибора.
Способ ультразвуковой дефектоскопии
Этот способ заключается в использовании ультразвуковых волн для контроля и выявления брака сварных швов. Эти волны представлены в виде колебаний, частота которых 20 кГц. Это на порядок выше, чем та частота, которую воспринимает человеческий слух. Дефекты сварных швов (трещины, поры, раковины), которые встречаются на пути звуковых колебаний, отражаются от линии разграничения металл — дефект и фиксируются с помощью специализированных ультразвуковых дефектоскопов.
svarkagid.com
Виды контроля сварных соединений | Инструмент, проверенный временем
Для получения сварного соединения хорошего качества необходимо осуществлять контроль, начиная с проверки качества подготовки шва и кончая проверкой полученного сварного соединения. Качество основного металла, электродной проволоки, присадочного металла, флюса и других материалов проверяют по сертификатам и заводским документам. Маркировка и качество должны соответствовать установленным техническим условиям и технологическому процессу сварки. Сборку под сварку и разделку шва проверяют по стандартам и техническим условиям.
Сварное соединение проверяется внешним осмотром, металлографическими исследованиями, химическим анализом, механическими испытаниями, просвечиванием рентгеновскими и гамма-лучами, магнитными методами и с помощью ультразвука. Предварительно сварное соединение очищают от шлака, окалины и металлических брызг.
Внешним осмотром выявляют наружные дефекты шва. Осмотр производят невооруженным глазом или с помощью лупы с десятикратным увеличением. Размеры сварных швов проверяют шаблонами и мерительным инструментом.
Металлографические исследования заключаются в следующем: сверлят отверстие, проходящее через шов и основной металл. Поверхность отверстия протравливают 10%-иым водным раствором двойной соли хлорной меди и аммония в течение 1…3 мин. Осадок меди удаляют водой. Протравленную поверхность осматривают невооруженным глазом или с помощью лупы. При этом выявляют качество провара и наличие внутренних дефектов. Для ответственных сварных конструкций производят более полные металлографические исследования мак — ро — и микрошлифов из специально сваренных контрольных пластин или из пластин, вырезанных из сварных соединений.
Химическим анализом определяют сослав основного и наплавленного металлов и электродов, а также их соответствие установленным техническим условиям на изготовление сварного изделия. Методы отбора проб для химического и спектрального анализов предусмотрены ГОСТ 7122—81.
Механические испытания проводят либо специально сваренных контрольных образцов, либо образцов, вырезанных из сварного соединения. Определяют предел прочности на растяжение, ударную вязкость, твердость и угол загиба.
Рентгенодефектоскопия основана на различном поглощении рентгеновских лучей различными веществами. Этим методом обнаруживают поры,
Рис. 117 |
микротрещины, непровары, неметаллические включения. Рентгеновские лучи направляют на сварной шов, а с обратной стороны, прикладывают фотопленку. Дефектные места пропускают лучи с меньшим поглощением, чем сплошной металл. После проявления на пленке хорошо видны очертания дефектов шва.
Рентгеновские лучи—коротковолновое электромагнитное излучение— получают в рентгеновских трубках бомбардировкой быстрыми электронами положительного электрода. К рентгеновской трубке подводится ток высокого постоянного напряжения (104—10® эВ). Следует иметь в виду, что рентгеновские лучи вредны для человеческого организма, поэтому рентгеновская трубка изолируется защитным свинцовым кожухом, в котором имеется узкая щель для выхода лучей, направляемых на контролируемое изделие. Для контроля в монтажных условиях очень удобны малогабаритные отечественные рентгеновские аппараты РУП-120-5-1, ИРА-1Д, ИРА-2Д, РИНА-ЗД и др. Толщина металла, которая может контролироваться этими аппаратами,—
25.. . 100 мм. Схема просвечивания рентгеновскими лучами показана на рис. 117: 1—рентгеновская трубка,
2— контролируемый шов, 3—кассета с фотопленкой.
Гамма-дефектоскопия также основана на различном поглощении веществами гамма-лучей. Как и при
рентгенодефектоскопии, получают теневой снимок сварного шва. Гамма- лучи получаются при ядерном распаде естественных и искусственных радиоактивных веществ (радия, мезатория, кобальта, цезия, иридия и др.). Наибольшее распространение как более дешевые получили радиоактивные изотопы кобальта 60Со, цезия 137Cs и иридия 192 1г. Гамма-лучи обладают большой проникающей способностью и позволяют контролировать металл толщиной до 350 мм. Гамма — лучи также вредны для человека, поэтому ампула с радиоактивным веществом помещается в переносной свинцовый контейнер или в стационарный аппарат с дистанционным управлением. Контейнер устанавливают против контролируемого участка, а с обратной стороны сварного шва помещают кассету с пленкой. Затем с помощью дистанционного управления выдвигают ампулу из аппарата или открывают щель в контейнере для выхода гамма-лучей. На рис.118,а показана* схема просвечивания сварного шва: 1—контейнер, ‘2—ампула, 3— контролируемый шов, 4—кассета с пленкой; на рис.118,6—схема устройства ампулы с радиоактивным веществом: /—радиоактивное вещество, 2— стеклянная ампула, 3—вата, 4—латунная или алюминиевая оболочка, 5—крышка, 6—свинцовый футляр. Для гамма — просвечивания применяют аппараты ГУП-Іг-5-2, ГУП-Сэ-2-1 и др.
Магнитные методы контроля основаны на исследовании магнитных полей рассеяния на намагниченном контролируемом изделии. Применяется несколько методов магнитного контроля сварного шва: магнитно-порошковый, магнитографический, индукционный и др.
Метод порошковой дефектоскопий является наиболее простым, но и менее четким. После намагничивания изделия сварной шов опыливают магнитным порошком (изготовляют из железной окалины)или покрывают суспензией (смесь магнитного порошка с керосином, маслом или другими веществами). В зоне дефекта порошок распределяется неравномерно—скапливается у краев пор, трещин; по этим скоплениям определяют расположение дефектов в сварном шве. Для большей наглядности магнитный порошок или суспензию окрашивают в яркие цвета.
Магнитографический контроль сварных швов разработан ВНИИСТ. Он широко применяется при контроле сварных швов магистральных трубопроводов. На сварной шов трубы накладывают ферромагнитную пленку, а затем намагничивают шов соленоидом или дисковым магнитом. В зависимости от вида и величины дефектов шва в соответствующих местах пленки будет та или иная степень. намагниченности. Магнитные сигналы преобразуют в звуковые с помощью магнитофона или наблюдают на экране осциллографа. Аппараты для магнитографического контроля с осциллографом позволяют проверять сварные швы со скоростью 0,5… 1 м/мин. Кроме высокой производительности они отличаются большой точ-
ностью (не уступающей рентгено — и гамма-дефектоскопии), простотой контроля, дешевизной применяемых материалов, возможностью проверки швов в различных пространственных положениях и безопасностью работы.
Индукционный метод контроля основан на рассеянии магнитного потока датчиком дефектоскопа и последующем наведении электродвижущей силы в индикаторе. Наведенный индукционный ток усиливается и подается на телефон, сигнальную лампу или на магнитоэлектрический прибор. По звуку, отклонению стрелки прибора или зажиганию лампы определяют расположение дефекта. Индукционный контроль производят дефектоскопом, МД-138.
Ультразвуковой метод контроля основан на способности ультразвуковых колебаний проникать в-толщу металла на значительную глубину и отражаться от неметаллических включений и других дефектных участков шва. Ультразвуковые дефектоскопы работают по следующему принципу. Пластинка из кварца или сегнетовой соли под действием переменного электрического поля высокой частоты дает ультразвуковые колебания, которые с помощью щупа направляются на проверяемое сварное соединение. На границе между однородным металлом и дефектом эти волны частично отражаются и воспринимаются второй пластинкой. Под действием переменного давления ультразвуковой волны на гранях этой пластинки появляется переменная разность потенциалов, зависящая от интенсивности отраженной волны. Электрические колебания от граней пластинки усиливаются и направляются в осциллограф. На экране осциллографа одновременно изображаются импульсы излучаемой и отражаемой волн. По относительному расположению этих импульсов и по Интенсивности отраженного импульса можно судить о местонахождении и характере дефекта в сварном шве. В настоящее время выпускают ультразвуковые дефектоскопы, работающие на одной пластинке, которая подает короткими импульсами ультразвуковые волны на контролируемый шов. Отраженные волны воспринимаются этой же пластинкой в промежутки времени между импульсами излучения. При этом получается высокая четкость излучаемых и отраженных ультразвуковых волн. Ультразвуковой метод контроля позволяет обнаружить все основные дефекты сварных швов. Кроме того, ультразвуковые дефектоскопы УЗД-7н имеют приспособления для настройки на заданную толщину шва и для определения глубины расположения обнаруженного дефекта. Недостатками ультразвукового контроля являются трудность определения характера дефекта и проверки швов толщиной менее 10 мм.
Испытание сварных швов емкостей на герметичность проводят различными методами.
Испытание керосином: емкости, работающие без избыточного давления, с внутренней стороны обильно смачивают керосином; сварные швы с внешней стороны покрывают меловым водным раствором. При наличии даже мельчайших пор, трещин или неплотностей керосин просачивается через них и на покрытой мелом поверхности появляются керосиновые пятна.
Испытание, сжатым воздухом проводят нагнетанием в испытываемый резервуар сжатого воздуха до давления, указанного в технических условиях на изготовление резервуара. Швы покрывают мыльной эмульсией; при наличии дефектов появляются мыльные пузырьки. Если габариты позволяют погрузить испытываемый резервуар в ванну с водой, тогда дефекты определяют по пузырькам воздуха. Трубопроводы и большие резервуары испытывают сжатым воздухом на величину потери давления за время, установленное техническими условиями.
Вакуум-аппаратом контролируют сварные швы, имеющие односторонний доступ, когда невозможно использовать керосин, воздух или воду. Аппарат состоит из камеры с вакуумметром и насоса. Контролируемый сварной шов покрывают мыльной эмульсией, на нее устанавливают камеру и включают насос, который создает в камере вакуум, в результате камера присасывается к испытуемой поверхности. Для герметичности камера имеет в торце мягкую резиновую прокладку. Если шов имеет дефекты (поры, трещины, неплотности), то появляются мыльные пузырьки, которые наблюдаются через стекло камеры.
Испытание аммиаком проводят нагнетанием в испытываемый резервуар воздуха до рабочего давления или давления, указанного в технических условиях на изготовление изделия. Затем добавляют 1% аммиака от объема воздуха в резервуаре при нормальном давлении. Контролируемые сварные швы обертывают бумагой, пропитанной 5%-ным водным раствором азотнокислой ртути. При наличии неплотностей (поры, трещины и др.) аммиак проходит через них и, взаимодействуя с азотнокислой ртутью, дает на бумаге черные пятна.
Гидравлическое испытание проводят с целью проверки не только плотности швов, но и их прочности. Такому испытанию подвергают сварные трубопроводы, сосуды и резервуары для газа или жидкости, работающие под давлением. Для этой цели все отверстия изделия плотно закрывают заглушками и заполняют его водой. С помощью гидравлического пресса создают давление, в 1,5 раза превышающее рабочее давление, и выдерживают в течение времени, указанного в технических условиях на изготовление изделия. Затем снижают давление до рабочего значения и проверяют наличие потения и пропусков воды в швах. При этом изделие обстукивают молотком на расстоянии 20 мм от сварного шва. Вертикальные цилиндрические резервуары обстукивать при испытании водой не разрешается.
Для контроля сварных соединений магистральных трубопроводов используют передвижную лабораторию PMJ12B, смонтированную на автомашине. Оборудование состоит из рентгеновской установки, позволяющей просвечивать стыки трубопроводов диаметром 720… 1420 мм, гамма-дефектоскопа и установки для магнитографического контроля. За смену лаборатория проверяет гамма — просвечиванием 6 стыков, рентгеновским просвечиванием 12 и магнитографическим контролем 20 стыков. Масса лаборатории— 5 т.
hssco.ru