Как получить карбид кальция. Получение карбида кальция из кальция
Карбид кальция « Попаданцев.нет
Что такое «карбид», знает любой мальчишка. Если бросить кусочек карбида в лужу, то кроме дикого шипения получается еще дичайшая вонь. А как получается сам карбид?
Вообще карбидов существует множество, как и применений ему. Но нас пока интересует карбид кальция CaC2 — то есть тот, который используют для получения ацетилена при соединении карбида с водой.
Слишком сложного в получении карбида кальция нет. Сейчас для этого в электропечах пережигают негашеную известь с коксом. При всей этой простоте — впервые карбид кальция был получен в лаборатории в 1836-м году, а промышленно его начали получать в 1892 году. Для попаданца — широчайшее поле для внедрения!
Все реакция — CaO + 3C = CaC2 + COНегашеная известь соединяется с углеродом. Негашеную известь получали с древних времен, пережигая известняк, ну и древесный уголь тоже дефицитом не был никогда. Полученный попутно угарный газ (СО) окисляется до углекислого газа прямо при выходе из печи, хотя сейчас часто печи делают закрытыми для сбора угарного газа.На 100 весовых частей негашеной извести нужно 70-80 весовых частей углерода.При производстве лучше иметь избыток угля, чем извести — такой карбид отдает больше ацетилена.Готовый карбид кальция технического качества почти на 80% состоит из самого карбида кальция, 17% — известь, остальное примеси.Карбид выходит в виде расплава, который после затвердевания измельчают.
Но, несмотря на простоту реакции получения, есть некоторые неприятные нюансы.Главное — процесс этот эндотермический, он поглощает дикое количество тепла в процессе производства — 3000 кВт на тонну продукта. Именно из-за этого его делают электродуговым способом. При этом сам процесс идет в жидкой фазе — то есть расплавленная известь постепенно реагирует с кусками углерода. При этом нужна температура примерно 2000°С, что совсем немало. И что совсем неприятно — при перегреве до 2200-2400°С карбид кальция распадается на составляющие.
Поэтому, если нам не доступно электричество в больших объемах, у нас есть два выхода.
Первый — это плавить в тигле. Проблема в том, что тигель должен выдержать эти самые 2000°С, а в древние времена ни графитовый, ни вольфрамовый тигель нам будут недоступны.
Второй — построить небольшую доменную печь. Требуемое тепло даст избыточное количество угля. Уголь и известь насыпаются туда слоями и печь поддувается большим количеством воздуха. Такие печи пытались строить и главная проблема — поддержка точных условий реакции, что регулируется силой поддува.С одной стороны — такую печь можно построить только когда уже работают доменные печи для железа. А с другой стороны — а нам точно нужен карбид, если нет даже железа?
Трудность вызовет хранение карбида. Он должен быть абсолютно изолирован от воды — много лучше, чем порох. Потому что если порох намокнет, то он не взорвется, а если намокнет карбид — то взрыв обеспечено. И что хуже всего — при хранении не должна использоваться медь, серебро или золото.
Проблем с производством карбида будет немало. Но при каком производстве их будет мало?Зато все проблемы — решаемые чуть ли не с технологиями Древнего Египта.А пользы от карбида будет много…
И последнее — ацетилен, который получается после контакта карбида с водой — ничем не пахнет, человек просто не имеет обонятельных рецепторов для него. Та вонь, по которой мы безошибочно определяем карбид — это примеси, которых в техническом карбиде несколько процентов.
www.popadancev.net
Производство карбида кальция - Справочник химика 21
из "Производства ацетилена "
Первые попытки получения карбида кальция сплавлением обожженной извести и угля в электрической дуге были сделаны еще в 1839 г., однако лишь в 1892 г. Муассан (Франция) и Вильсон (Канада) предложили конструкцию электродуговой печи, пригодной для промышленного использования. Сначала во Франции и Канаде в 1896 г., а вскоре и в других странах этот способ получил широкое распространение. [c.43] В России производство карбида кальция было организовано в 1908 г. До революции объем его производства в нашей стране был очень небольшой, и только с развитием промышленности в годы первых пятилеток началось ускоренное строительство новых заводов и отдельных крупных цехов. В настоящее время СССР имеет развитое производство карбида кальция. [c.43] Вначале карбид кальция использовался для получения ацетилена в небольших переносных или стационарных генераторах — только для целей сварки или резки металла. В машиностроении и в ремонтных службах заводов и в настоящее время применяется карбид кальция, причем во все возрастающих количествах. Но, как отмечалось ранее, теперь большая часть карбида кальция используется химической промышленностью для производства продуктов органического синтеза. Некоторая доля карбида кальция все еще потребляется в производстве цианамида. Однако расход карбида на эти цели не превышает 3—5% от его общего производства, и это — единственная область применения собственно карбида кальция. [c.43] Метод производства ацетилена из карбида кальция имеет ряд технологических достоинств. Ацетилен получается более чистым и очень высокой концентрации, что исключает необходимость выделения его из реакционных газов и специальной очистки. Карбид кальция можно легко транспортировать, поэтому районы его производства можно отдалить от мест потребления ацетилена. [c.43] Производство ацетилена из карбида кальция делится на две стадии 1) получение карбида кальция в электродуговых печах и 2) разложение карбида кальция водой с образованием ацетилена. [c.43] При этом получается окись углерода, и таким образом осуществляется восстановление обожженной извести. [c.44] Обожженная известь сплавляется с углеродом лишь на 70—80%, поэтому в товарном продукте всегда присутствует 12—25% СаО. Последнее обстоятельство очень важно, так как для облегчения выпуска расплава из печи необходимо максимально снижать температуру плавления карбида кальция, а наличие извести в сплаве как раз и понижает температуру его плавления. Чистый карбид кальция плавится при 2300 С, а обожженная известь — при 2585 С. При сплавлении карбида кальция с обожженной известью температура плавления смеси снижается в зависимости от содержания компонентов (рис. П-1). Наиболее низкая температура плавления (1750° С) у эвтектичной смеси состава 69,4% СаС, и 30,6% СаО. [c.44] Таким же путем образуются соединения кальция с мышьяком и некоторые другие вещества. [c.45] В соответствии с теоретическими подсчетами для образования 1 т СаСз в электродуговы.х печах требуется затратить 1965 квт-ч электроэнергии, однако практически расходуется от 2800 до 3500 квт-ч. Электроэнергия затрачивается на разогрев и расплавление шихты, на проведение основной эндотермической реакции, а также на побочные химические реакции и потери в окружающую среду. Кроме того, некоторое количество электроэнергии расходуется на подогрев и расплавление избыточной (20%) обожженной извести, загружаемой в печь вместе с шихтой для снижения температуры плавления карбида кальция. [c.45] Создание высокопроизводительных карбидных печей позволяет более эффективно использовать электроэнергию, так как тепловые потери в окружающую среду в таких печах значительно ниже, чем в маломощных иечах. Если в малопроизводительных печах расход электроэнергии составляет 3500 квт-ч на 1 т СаСд, то в крупном производстве эта величина снижается до 2800 квт-ч. Высокопроизводительные печи с большими ваннами для накопления плава имеют еще одно достоинство — высокую тепловую инертность, что позволяет снижать потребляемую мощность на 40—50% в часы перегрузки обслуживающей энергосистемы и тем самым способствует стабильности печи. По этой же причине для крупных печей часто предоставляется льготный тариф на электроэнергию, вследствие чего себестоимость продукции снижается. [c.45] Однако окситермический способ производства карбида кальция промышленного развития не получил, так как наряду с кислородом приходится расходовать в несколько раз больше металлургического кокса, чем при электротермическом методе. Это связано с тем, что около 70% кокса при окситермическом способе расходуется на получение необходимого тепла. Электротермический метод использует электроэнергию, полученную из различных топлив (природный газ), или гидроэлектроэнергию и является экономически более выгодным. [c.46]Вернуться к основной статье
chem21.info
Карбид кальция
В итоге взаимодействия углерода с металлами при больших температурахполучаются карбиды. К примеру, карбид кальция: Ca + 2C → CaC2. Из всех карбидов он имеет наибольшее практическое значение. Незапятнанный CaC2 — отлично кристаллизующееся жесткое вещество, тусклые кристаллы образованы ионами Ca2+ и C2-. Другие его наименования — ацетиленид кальция либо углеродистый кальций. Молярная масса приравнивается 64,1 г/моль. Он не летуч и не растворим ни в каком из узнаваемых растворителей, а под действием воды разлагается. Плотность его составляет 2,22 г/см³. Температура плавления приравнивается 2160°С, а кипения — 2300°С. По степени воздействия на организм относится к субстанциям очень небезопасным (1-й класс угрозы).
В первый раз ацетиленид кальция был получен в 1862 году германским химиком Фридрихом Велером при нагревании с углем сплава из цинка и кальция. Им была описана реакция углеродистого кальция с h3O. Даже с ее следами (к примеру, с атмосферной влагой) карбид кальция реагирует энергично, с выделением огромного количества тепла. Но в случае недочета воды может произойти самовоспламенение образующегося ацетилена. Карбид кальция бурно ведет взаимодействие с разбавленными неорганическими кислотами и аква смесями щелочей. При всем этом также происходит выделение ацетилена. Являясь сильным восстановителем, CaC2 способен восстанавливать все оксиды металлов до карбидов либо незапятнанных металлов.
Получение карбида кальция удобнее не из самого кальция, а его окисла. При высочайшей температуре (от 2000 до 2300°С) происходит его восстановление. При всем этом металл и углерод соединяются: CaO + 3C → CO↑ + CaC2. Процесс протекает в электродуговой печи, где накаливают смесь негашеной извести и кокса либо антрацита. Технический продукт окрашен, имеет серый цвет, потому что содержит примеси в виде свободного углерода, окиси, также сульфида, фосфида кальция и других хим соединений. Массовая толика CaC2 в нем составляет 80—85%.
При содействии карбидов с водой выделяется либо металл, либо ацетилен. По второму варианту с водой реагирует карбид кальция. Ацетилен, приобретенный в итоге реакции, которая имеет промышленное значение: 2h3O + CaC2 → C2h3 + Ca(OH)2, является техническим и имеет противный запах, потому что содержит ряд примесей (Nh4, h3S, Ph4 и другие). Хотя в чистом виде он является тусклым газом с соответствующим слабоватым запахом, и он достаточно отлично растворяется в воде. Имеет огромное значение для получения цианамида кальция (является сырьем в производстве цианистых соединений либо применяется в качестве удобрения) из карбида взаимодействием его с азотом по уравнению реакции: N2 + CaC2 → CaCN2 + C.
В прошедшем CaC2 обширно употреблялся в карбидных лампах, где служил источником ацетиленового пламени. В текущее время применение такового источника света ограничивается в главном спелеологией, его употребляют также в бакенах и маяках. Другие принципиальные направления внедрения CaC2 — это хим технологии, где он является сырьем. К примеру, в производстве товаров органического синтеза, основным из их является каучук синтетический. Также из углеродистого кальция получают ацетиленовую сажу, винилхлорид, уксусную кислоту, акрилонитрил, этилен, ацетон, искусственные смолы, стирол. В металлургии служит для раскисления металлов и десульфурации (понижение содержания кислорода и серы соответственно). Карбид кальция употребляют для производства регулятора роста растений, порошкового карбидного реагента (ацетиленовая сварка).
Получение каждой тонны CaC2 просит приблизительно 3 тыщи квт/час электроэнергии. Потому оно оправдано при наличии низких цен на нее. Но в целом мировое создание углеродистого кальция вырастает. Если в 70-х годах предыдущего столетия раз в год вырабатывалось до 5 миллионов тонн, то в нашем веке это количество подросло приблизительно в два раза. Так, в Китае создание ацетилена на базе карбида кальция является главным источником сырья для хим индустрии, а именно, для производства поливинилхлорида. Получение ацетилена из собственного сырья экономичнее, чем при использовании ввезенной нефти. Потому создание его в Китае вырастает. В 2005 году оно достигало 8,94 миллионов тонн, и была настоящая возможность выпускать 17 миллион тонн.
В отличие от Китая, в США, Европе и Стране восходящего солнца потребление углеродистого кальция, обычно, понижается. Уровень его производства в США в 90-х годах составлял всего 236 тыщ тонн в год. В нашей стране карбид кальция выпускают по техническим условиям, изложенным в ГОСТ 1460-81. Главные его потребители — это Украина, Узбекистан, Румыния и Словакия. Из-за высочайшей энергоемкости продукта и в связи с ростом цен на электроэнергию потребление ацетиленида кальция в Рф и странах-экспортерах снизилось в два раза.
tipsboard.ru
способ получения карбида кальция - патент РФ 2015104
ФОРМУЛА ИЗОБРЕТЕНИЯ
СПОСОБ ПОЛУЧЕНИЯ КАРБИДА КАЛЬЦИЯ, включающий подачу шихты из извести и углеродсодержащего материала в электропечь, ее плавление и кристаллизацию полученного расплава, отличающийся тем, что перед подачей в печь шихту измельчают до размеров частиц менее 3 мм и подают ее непрерывно так, чтобы толщина слоя шихты над расплавом составляла 5 - 60 мм, плавление ведут в индукционной печи с охлаждаемым тиглем, а кристаллизацию расплава осуществляют также непрерывно путем перемещения полученного слитка из зоны нагрева. www.freepatent.ru
СПОСОБ ПОЛУЧЕНИЯ КАРБИДА КАЛЬЦИЯ
Изобретение относится к способам переработки углекарбонатного минерального сырья и может быть использовано при его глубокой переработке с получением карбида кальция.
Известен способ переработки углекарбонатного минерального сырья, включающий обжиг известняка в реакторе с подачей в него и сжиганием высокотемпературного энергоносителя (см. SU №1449553, кл. С04В 2/02, 1989).
Однако в этом техническом решении невелик спектр получаемых товарных продуктов (только известь), низка экологичность производственного процесса, кроме того, осложнен процесс обеспечения производства высокотемпературным энергоносителем.
Известен также способ получения карбида кальция, включающий термическую обработку дробленых известняка и угля с отводом газообразных продуктов и их использованием для производства углекислоты (RU №2256611, С01В 31/32, С04В 2/02, C01F 11/06, C07C 11/24, 2005).
Однако в этом техническом решении процесс обеспечения производства высокотемпературным энергоносителем осуществляется за счет использования части получаемого карбида кальция для производства ацетилена, который и сжигают для подвода тепла в процессы обжига извести и синтеза карбида кальция, что снижает выход целевого продукта. Кроме того, процессы обжига извести и синтеза карбида кальция осуществляют в двух последовательно размещенных реакторах, что приводит к непроизводительным потерям тепла в процессе передачи материалов из одного реактора в другой.
Задачей, на решение которой направлено предлагаемое техническое решение, является повышение выхода целевого продукта и снижение энергоемкости производства карбида кальция.
Технический результат, получаемый при решении поставленной задачи, выражается в исключение расхода карбида кальция на технологические нужды и исключении непроизводительных потерь тепла (из-за охлаждения сырьевых компонентов) за счет реализации способа в объеме одного реактора.
Поставленная задача решается тем, что способ получения карбида кальция, включающий термическую обработку дробленых известняка и угля с отводом газообразных продуктов, которые используют для производства углекислоты, отличается тем, что используют тонкодисперсную смесь сырьевых материалов, при этом ее термическую обработку ведут в одном реакторе, при этом на первом этапе в процессе ввода сырья в реактор его подвергают нагреву, предпочтительно до 1000°-1200°С для чего нагрев сырьевой массы осуществляют теплопередачей от конструктивных элементов загрузочного канала, по которому тонкодисперсное сырье перемещают самотеком, и воздействием на него плазменного луча, формируемого плазмотроном в зоне свободного перемещения частиц сырьевой массы, при этом термическую обработку сырья осуществляют в атмосфере диоксида углерода, который подают в загрузочный канал, причем, последующий синтез карбида кальция осуществляют при температуре, как минимум 1700-1800°, для чего осуществляют индукционный нагрев реакционной массы, кроме того, расплав карбида кальция отводят через выпускное отверстие, расположенное на дне реактора, при этом из верхней части полости реактора отводят газообразные продукты из которых выделяют окись углерода и диоксид углерода, причем как минимум часть отводимого диоксида углерода используют для заполнения загрузочного канала, кроме того, для производства углекислоты используют объем диоксида углерода оставшийся после заполнения загрузочного канала и весь объем окиси углерода.
Сопоставительный анализ признаков заявленного решения с признаками прототипа и аналогов свидетельствует о соответствии заявленного решения критерию"новизна".
Признаки отличительной части формулы изобретения обеспечивают решение следующих функциональных задач:
Признак "используют тонкодисперсную смесь сырьевых материалов" обеспечивает возможность прогрева сырьевой массы до температуры диссоциации карбонатов, при сравнительно небольшой длине загрузочного канала.
Признак указывающий, что "термическую обработку (тонкодисперсной смеси сырьевых материалов) ведут в одном реакторе" исключает потерю тепла прогретой сырьевой массой при переходе из зоны контактного и плазменного нагрева в зону индукционного нагрева реактора.
Признаки "на первом этапе в процессе ввода сырья в реактор его подвергают нагреву, предпочтительно до 1000-1200°С для чего нагрев сырья осуществляют теплопередачей от конструктивных элементов загрузочного канала, по которому тонкодисперсное сырье перемещают самотеком, и воздействием на него плазменного луча, формируемого плазмотроном в зоне свободного перемещения частиц сырьевой массы" обеспечивают прогрев сырьевой массы до температуры диссоциации карбонатов, что снижает затраты энергии на индукционный прогрев реакционной массы.
Признак "термическую обработку сырья осуществляют в атмосфере диоксида углерода, который подают в загрузочный канал" обеспечивает наличие плазмообразующего газа в загрузочном канале, кроме того, тем самым исключается взрывное горение горючих газов, выделяющихся при газифицировании угольной массы.
Признак "последующий синтез карбида кальция осуществляют при температуре, как минимум 1700-1800°, для чего осуществляют индукционный нагрев реакционной массы" обеспечивает возможность получения карбида кальция при прогреве до заявленного температурного диапазона, предварительно подогретой реакционной массы.
Признак "расплав карбида кальция отводят через выпускное отверстие, расположенное на дне реактора» обеспечивает оптимальную схему перемещения материала реакционной массы, сверху-вниз, под действием силы тяжести, не требующее использования специальных средств.
Признак "из верхней части полости реактора отводят газообразные продукты из которых выделяют окись углерода и диоксид углерода» упрощают организацию отвода газовой массы из реактора, при котором не оказывается влияние на расплав реакционной массы, при этом обеспечивается возможность утилизации окислов углерода.
Признак "как минимум часть отводимого диоксида углерода используют для заполнения загрузочного канала» обеспечивают возможность получения диоксида углерода для обеспечения процесса синтеза карбида углерода, без использования внешнего источника этого газа.
Признак "кроме того, для производства углекислоты используют объем диоксида углерода оставшийся после заполнения загрузочного канала и весь объем окиси углерода» обеспечивает возможность полной утилизации газов-окислов углерода, образующихся при синтезе карбида углерода.
Изобретение поясняется чертежом, на котором показана схема реализации способа.
На чертеже показаны верхняя 1 и нижняя 2 части корпуса плазменного реактора, загрузочный канал 3, источник сырьевой смеси 4, верхняя крышка 5 загрузочного канала 3, источник плазмообразующего газа 6, наклонные пересыпные полки 7, каналы 8 и 9, соответственно для ввода сырьевой смеси и диоксида углерода, верхняя 10 и нижняя 11 электромагнитные катушки, выпускной патрубок 12, поворотная платформа 13, привод 14 поворота платформы, источники угля 15, известняка 16, воды 17, плазмотрон 18 с соплом 19, продольная ось 20 загрузочного канала 3, плазменный шнур 21, кромки 22 пересыпных полок 7, первый 23 и второй 24 газоотводящие каналы, газоразделительный блок 25, второй реактор 26, основание 27 поворотной платформы 13, ролики 28, дополнительный канал подачи угля 29.
Верхняя 1 и средняя часть корпуса плазменного реактора выполнена в виде цилиндрической камеры. Ее нижняя часть 2 выполнена конической и завершена выпускным патрубком 12. Корпус плазменного реактора и выступающая из него часть загрузочного канала 3 выполнены водоохлаждаемыми (снабжены рубашкой, выполненной известным образом с возможностью прокачки теплоотводящего агента (воды). Загрузочный канал 3 пропущен через верхнюю крышку корпуса плазме иного реактора, выполнен из тепло-стойкой стали. Он снабжен герметичной крышкой и сообщен каналом 8 с источником сырьевой смеси 4 (бункером-накопителем дисперсного сухого материала), размещенным выше корпуса 1, что обеспечивает самотечное перемещение смеси в реактор при открытых затворах (на чертежах не показаны), при этом источник сырьевой смеси 4 сообщен с источниками угля 15 и известняка 16. Кроме того, источник угля 15, посредством дополнительного канала подачи угля 29 (снабженного запорным клапаном известной конструкции - на чертеже не обозначен) сообщен напрямую с каналом 8.
Полость загрузочного канала 3 выполнена с возможностью сообщения известным образом с источником плазмообразующего газа 6 (в качестве которого используют диоксид углерода), кроме того, источник плазмообразующего газа 6 сообщен каналом 9, для ввода диоксида углерода с плазмотроном 18. Кроме того, в полости загрузочного канала 3 установлены наклонные пересыпные полки 7 выполненные из металла, наклоненные под углом близким к углу естественного откоса шихты, используемой для синтеза карбида кальция. На верхнем торце загрузочного канала 3(на его верхней крышке 5) зафиксирован по меньшей мере один плазмотрон известной конструкции, мощностью до 25-50 квт, обеспечивающий формирование плазменного шнура 21 ориентированного вниз, в зазор между кромками 22 пересыпных полок 7. Целесообразно, чтобы плазмотронов было бы хотя бы два, при этом формируемые ими плазменные шнуры 21 должны быть ориентированы под острым углом к продольной оси 20 загрузочного канала 3 в зазоре между кромками 22 пересыпных полок 7.
В качестве средств нагрева сырьевой смеси в реакторе используют верхнюю 10 и нижнюю 11 электромагнитные катушки, выполненные известным образом с возможностью индукционного нагрева сырьевого материала до температуры его плавления, размещенные на разной высоте относительно корпуса плазменного реактора.
При этом нижняя 11 электромагнитная катушка установлена стационарно или с возможностью возвратно-поступательного перемещения по высоте реактора (например, на платформе установленной на раздвижных силовых цилиндрах - на чертежах названные элементы не показаны и не обозначены) с возможностью ее опускания максимально близко к выпускному патрубку 12 - до начала нижнего (конического) участка корпуса реактора.
Верхняя катушка 10 установлена на поверхности поворотной платформы 13, выполненной с возможностью поворота вокруг корпуса реактора, которой придана переменная высота и которая снабжена приводом 14 обеспечивающим ее поворот, для этого, нижняя поверхность поворотной платформы 13 оперта на ряд роликов 28 опирающихся на кольцевой желоб (на чертеже не обозначен) основания 27, один из которых и выполнен приводным (например, закреплен на валу реверсивного электродвигателя).
Второй реактор 26 выполнен с возможностью синтеза углекислоты, в виде емкости связанной с газоразделительным блоком 25 газопроводами подачи CO2 и СО, кроме того, он сообщен с источником воды 17 выполненному в виде емкости с водой. Второй реактор 26 снабжен насосным, дозирующим и контрольно-измерительным оборудованием известной конструкции (на чертежах не показаны), обеспечивающим реализацию процесса синтеза Н2СО3. Выход второго реактора 26 связан с хранилищем углекислоты (на чертеже не показано), конструкция которого определяется формой поставки углекислоты потребителю, т.е. сжиженная или "сухой лед", и не отличается от известных конструкций, сходного назначения.
Заявленный способ реализуется следующим образом.
На этапе запуска плазменного реактора в плазмотрон 18 подают плазмо-образующий газ (диоксид углерода) и включают его в работу, что обеспечивает формирование плазменного шнура 21 в зазоре между кромками 22 пересыпных полок 7 загрузочного канала 3.
На этапе запуска плазменного реактора в него подают только дисперсный уголь, для чего уголь из источника угля 15 направляют по дополнительному каналу подачи угля 29 напрямую в канал 8 и далее в загрузочный канал 3.
Таким образом, на самую верхнюю из пересыпных полок 7 поступает дисперсный уголь, который пересыпаясь с одной полки на другую перемещается вниз по загрузочному каналу 3 и пересекая зазор между кромками 22 пересыпных полок 7 попадает под действие плазменного шнура 21 (или шнуров) действующих в названном зазоре. Это приводит к воспламенению объема дисперсного угля и прогрева загрузочного канала и полости реактора.
Генерируемые при этом газы-продукты сжигания дисперсного угля отбираются через первый 23 и второй 24 газоотводящие каналы, после чего попадают в газоразделительный блок 25, где из них выделяются оксид и диоксид углерода (остальные газы выбрасываются в атмосферу. При этом, оксид углерода подают во второй реактор 26, а диоксид углерода накапливают в источнике плазмообразующего газа 6.
После прогрева загрузочного канала до температуры 1000°-1200°С дополнительный канал подачи угля 29 перекрывают, полость реактора и загрузочного канала 3 заполняют диоксидом углерода, который известным образом подают от источника плазмообразующего газа 6, добиваясь вытеснения всех иных газов.
Далее, от источника сырьевой смеси 4, в загрузочный канал 3 по каналу 8 подают сухую сырьевую шихту, содержащую в расчетном количестве химические соединения (дисперсные уголь и известняк), обеспечивающие при их плавлении получение карбида кальция (коммуникации связывающие источник сырьевой смеси 4 и загрузочный канал 3 выполнены известным образом).
Таким образом, на самую верхнюю из пересыпных полок 7 (прогретую, как и остальные узлы загрузочного канала 3, до температуры 1000°-1200°С) поступает смесь дисперсных известняка и угля, которая пересыпаясь с одной полки на другую перемещается вниз по загрузочному каналу 3. При относительно медленном (по сравнению с вертикальным падением) перемещении частиц шихты происходит их контактный нагрев от деталей загрузочного канала 3. Это приводит к разогреву шихты до температуры диссоциации карбонатов и обеспечивает конверсию частиц известняка СаСО3 в частицы извести (СаО), в соответствии с формулой:
CaCO3=CaO+СО2.
Таким образом далее в процессе участвует шихта содержащая частицы извести и частицы угля.
При этом, воздействие на частицы этой шихты плазменных шнуров 21 (формируемых работой плазматронов 18), фактически полностью пересекающих поток частиц шихты обеспечивает расплавление материала и синтез карбида кальция (температура расплава достигает 1700-1900°С и выше). Синтез карбида кальция идет в соответствии с формулой:
Расплав попадает на дно реактора постепенно накапливаясь при этом процесс расплавления идет с большой скоростью, т.к. в этом случае происходят уже экзотермические реакции.
При подъеме уровня расплава выше уровня нижней катушки 11 подается напряжение на ее обмотку. Стенки камеры плазменного реактора выполняются из немагнитного материала, например стали, содержащей большое количество никеля, хрома и титана. Образующееся в результате прохождения тока через катушку электромагнитное поле воздействует на расплав, который в жидком состоянии становится токопроводным. Индуктивный ток поддерживает температуру на достигнутом (благодаря воздействию плазмы) уровне.
При подъеме расплава выше верхней электромагнитной катушки 10, подается напряжение на последнюю. Это обеспечивает индукционный прогрев остального объема расплава в камере плазменного реактора.
При этом включают привод 14 вращения приводного ролика 28, который, плотно контактируя с нижней поверхностью поворотной платформы 13, в свою очередь приводит последнюю во вращательное движение на остальных (неприводных) роликах 28 относительно ее основания 27 жестко закрепленного на корпусе реактора. Благодаря тому, что катушка 10 закреплена на поверхности поворотной платформы 13, при вращении последней происходит колебательное движение катушки 10 в плоскостях, пересекающих продольную (вертикальную) ось реактора.
При колебательных движениях катушки 10 меняет свое положение и магнитное поле, образующееся внутри токопроводящего расплава, который активно перемешивается и дополнительно нагревается. В результате перемешивания расплава за счет вращающегося магнитного поля, создаваемого трехфазной катушкой и колебательного движения самой катушки происходит гомогенизация расплава, что активно способствует увеличению производительности установки и повышению качества основной продукции, расплава карбида кальция. Скорость перемешивания задается скоростью изменения магнитного поля и зависит от частоты и мощности переменного тока и скорости механических колебаний катушки, которая в свою очередь зависит от скорости вращения поворотной платформы 13. Скорость перемешивания регулируется в зависимости от вязкости расплава, а последняя - от его температуры. Имея данные по температуре расплава, задают и скорость колебаний катушки 10 (скорость вращения поворотной платформы 13).
Диоксид и оксид углерода, выделяемые в результате декарбонизации карбонатных компонентов сырьевой смеси, выходят под действием разрежения, создаваемого в газоотводных каналах, расположенных в верхней части плазменного реактора (выше максимального уровня расплава), где может использоваться для получения сухого льда или снова вводится в реактор через электроды. Расплав карбида кальция периодически или непрерывно (при согласованном вводе в реактор) выливают через выпускной патрубок 12 в холодильник или гранулятор, в которых утилизируют тепло расплава (на чертежах не показаны).
Для снижения вязкости расплава карбида кальция во время периодического слива, нижняя катушка должна быть подвижной по высоте корпуса реактора, чтобы ее можно было перемещать в зону разгрузочного отверстия.
Остывший карбид кальция известным образом измельчают для получения кондиционного материала.
При выходе реактора на рабочий режим возникает избыток диоксида углерода по сравнению с его количеством необходимым для использования в технологическом процессе синтеза карбида кальция. При этом избыток диоксида и оксида углерода подают во второй реактор 26, где используют для синтеза углекислоты.
Способ получения карбида кальция, включающий термическую обработку дробленых известняка и угля с отводом газообразных продуктов, которые используют для производства углекислоты, отличающийся тем, что используют тонкодисперсную смесь сырьевых материалов, при этом термическую обработку смеси ведут в одном реакторе, причем на первом этапе в процессе ввода сырья в реактор его подвергают нагреву предпочтительно до 1000-1200°С путем нагрева сырьевой массы теплопередачей от конструктивных элементов загрузочного канала реактора, по которому тонкодисперсное сырье перемещают самотеком, и воздействием на него плазменного луча, формируемого плазмотроном в зоне свободного перемещения частиц сырьевой массы, при этом термическую обработку сырья осуществляют в атмосфере диоксида углерода, который подают в загрузочный канал с последующим синтезом карбида кальция, осуществляемого при температуре как минимум 1700-1800°С путем индукционного нагрева реакционной массы, и полученный расплав карбида кальция отводят через выпускное отверстие, расположенное на дне реактора, при этом из верхней части полости реактора отводят газообразные продукты, из которых выделяют окись углерода и диоксид углерода, причем как минимум часть отводимого диоксида углерода используют для заполнения загрузочного канала, а для производства углекислоты используют объем диоксида углерода, оставшийся после заполнения загрузочного канала, и весь объем выделенной окиси углерода.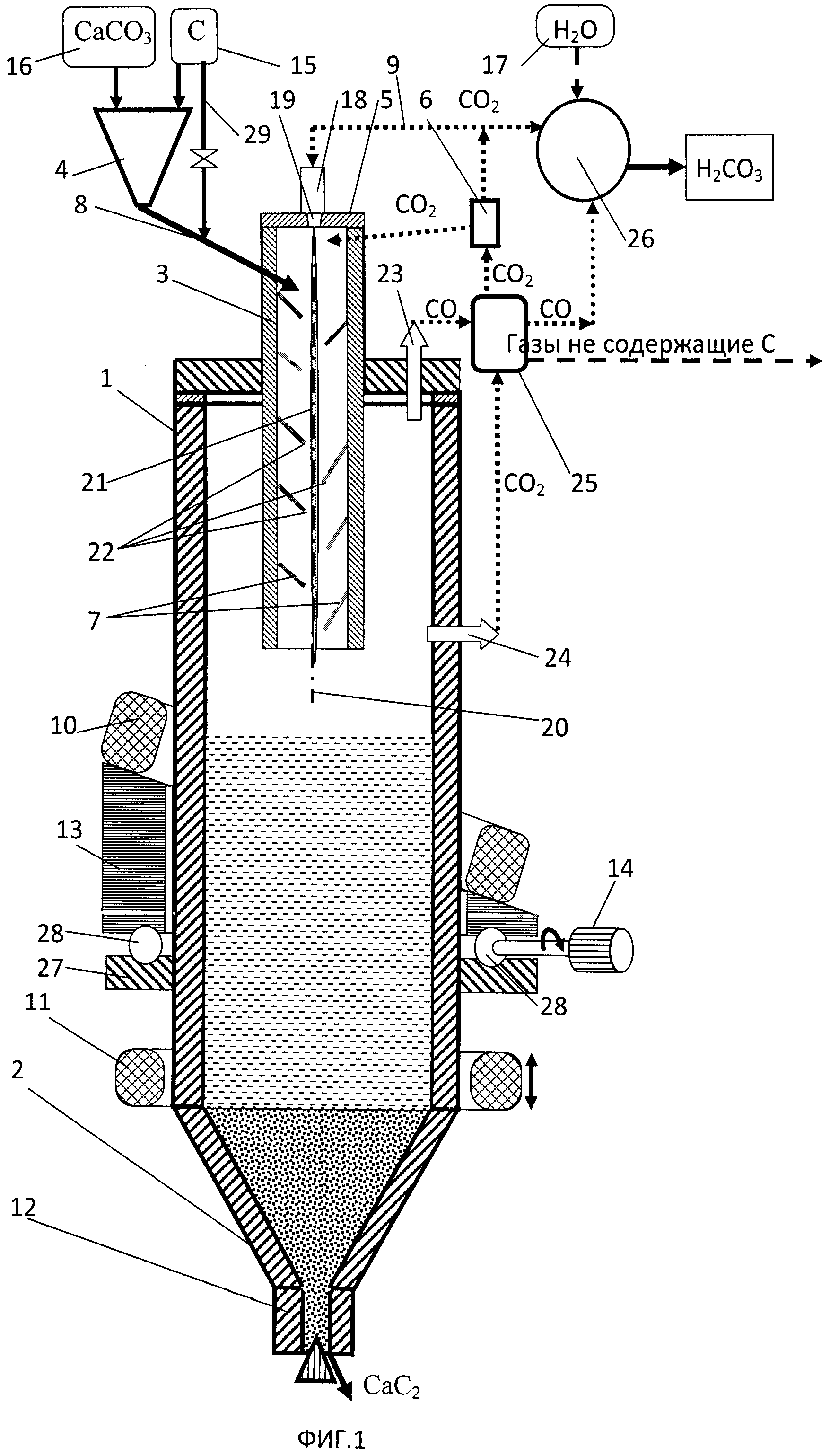
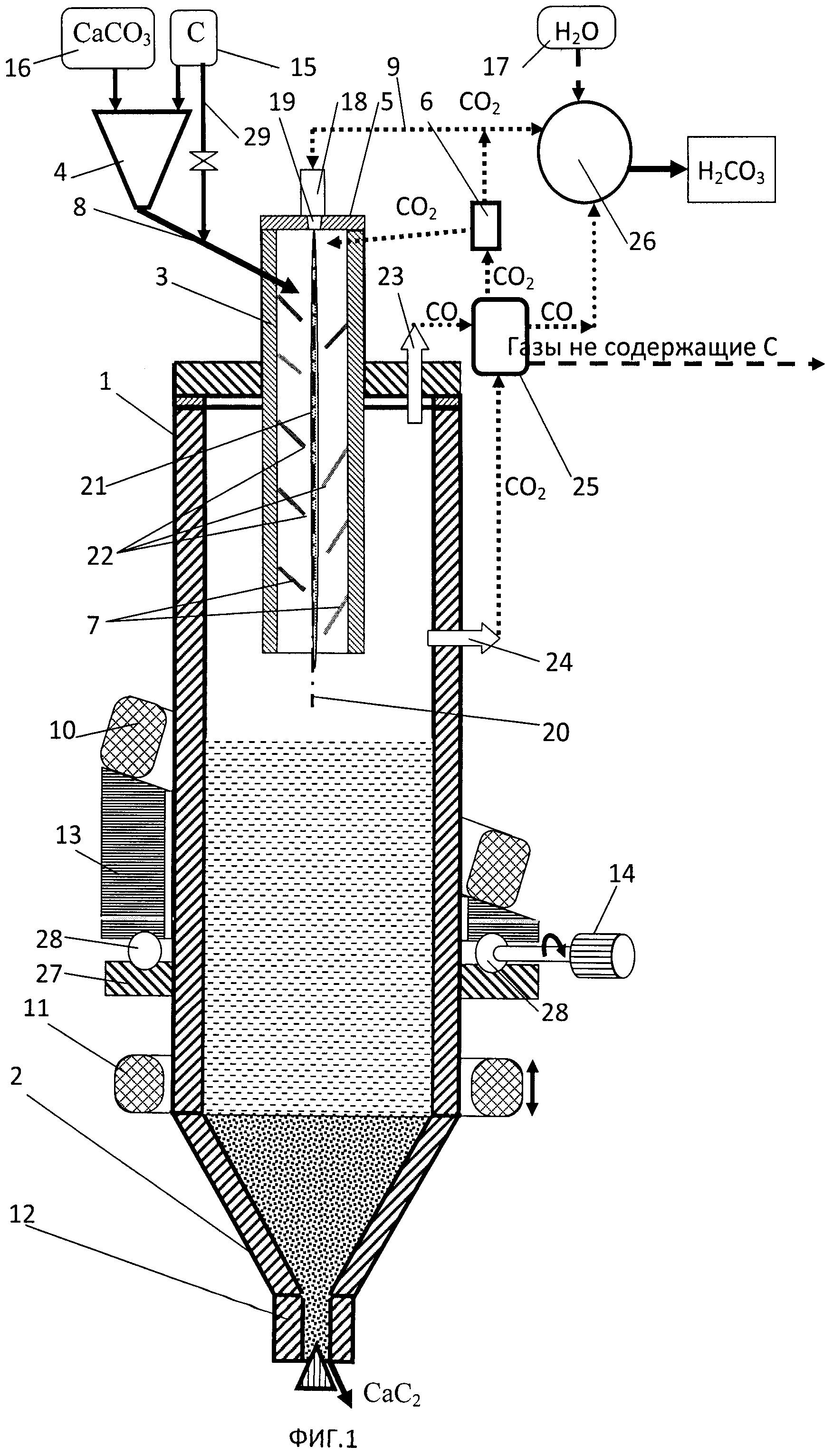
edrid.ru
Как получить карбид кальция
Как получить карбид кальция
Наверное, каждый человек помнит свои веселые школьные дни. А особенное веселье приходилось на момент проведения ремонтных работ в здании школы, когда рабочие, помимо всего прочего оборудования, приносили с собой генератор ацетилена и бочку карбида кальция. Такие дни были страшным сном для работников всех школ, начиная с директора и заканчивая уборщицей потому, что карбид кальция - это любимое развлечение школяров. Нет счету испорченным унитазам в школьных туалетах. Вот такой он карбид кальция.
- Тигель (желательно графитовый), графитовый электрод, оксид кальция (негашеная известь), кокс, источник тока.
- Карбонат кальция в виде известняка или мела. Керамический тигель для отжига. Пропановая или ацетиленовая горелка.
- Запишите уравнения реакций, с помощью которых можно
- Азотная кислота. Карбонат кальция. Стеклянная реторта. Посуда для выпаривания соляного раствора. Газовая горелка или спиртовка.
www.kakprosto.ru
Карбид кальция
Что такое «карбид», знает любой мальчишка. Если бросить кусочек карбида в лужу, то кроме дикого шипения получается еще дичайшая вонь. А как получается сам карбид?
Вообще карбидов существует множество, как и применений ему. Но нас пока интересует карбид кальция CaC2 — то есть тот, который используют для получения ацетилена при соединении карбида с водой.
Слишком сложного в получении карбида кальция нет. Сейчас для этого в электропечах пережигают негашеную известь с коксом. При всей этой простоте — впервые карбид кальция был получен в лаборатории в 1836-м году, а промышленно его начали получать в 1892 году. Для попаданца — широчайшее поле для внедрения!
Все реакция — CaO + 3C = CaC2 + CO Негашеная известь соединяется с углеродом. Негашеную известь получали с древних времен, пережигая известняк, ну и древесный уголь тоже дефицитом не был никогда. Полученный попутно угарный газ (СО) окисляется до углекислого газа прямо при выходе из печи, хотя сейчас часто печи делают закрытыми для сбора угарного газа. На 100 весовых частей негашеной извести нужно 70-80 весовых частей углерода. При производстве лучше иметь избыток угля, чем извести — такой карбид отдает больше ацетилена. Готовый карбид кальция технического качества почти на 80% состоит из самого карбида кальция, 17% — известь, остальное примеси.
Карбид выходит в виде расплава, который после затвердевания измельчают.
Но, несмотря на простоту реакции получения, есть некоторые неприятные нюансы. Главное — процесс этот эндотермический, он поглощает дикое количество тепла в процессе производства — 3000 кВт на тонну продукта. Именно из-за этого его делают электродуговым способом. При этом сам процесс идет в жидкой фазе — то есть расплавленная известь постепенно реагирует с кусками углерода. При этом нужна температура примерно 2000°С, что совсем немало. И что совсем неприятно — при перегреве до 2200-2400°С карбид кальция распадается на составляющие.
Поэтому, если нам не доступно электричество в больших объемах, у нас есть два выхода.
Первый — это плавить в тигле. Проблема в том, что тигель должен выдержать эти самые 2000°С, а в древние времена ни графитовый, ни вольфрамовый тигель нам будут недоступны.
Второй — построить небольшую доменную печь. Требуемое тепло даст избыточное количество угля. Уголь и известь насыпаются туда слоями и печь поддувается большим количеством воздуха. Такие печи пытались строить и главная проблема — поддержка точных условий реакции, что регулируется силой поддува. С одной стороны — такую печь можно построить только когда уже работают доменные печи для железа. А с другой стороны — а нам точно нужен карбид, если нет даже железа?
Трудность вызовет хранение карбида. Он должен быть абсолютно изолирован от воды — много лучше, чем порох. Потому что если порох намокнет, то он не взорвется, а если намокнет карбид — то взрыв обеспечено. И что хуже всего — при хранении не должна использоваться медь, серебро или золото.
Проблем с производством карбида будет немало. Но при каком производстве их будет мало? Зато все проблемы — решаемые чуть ли не с технологиями Древнего Египта.
А пользы от карбида будет много…
И последнее — ацетилен, который получается после контакта карбида с водой — ничем не пахнет, человек просто не имеет обонятельных рецепторов для него. Та вонь, по которой мы безошибочно определяем карбид — это примеси, которых в техническом карбиде несколько процентов.
www.popadancev.net
Карбид кальция - это... Что такое Карбид кальция?
Карби́д ка́льция (углеро́дистый ка́льций, ацетилени́д кальция) — CaC2 — в чистом виде белое кристаллическое вещество. Соединение кальция с углеродом.
История получения
Впервые получен в 1862 г. Ф. Вёлером нагреванием сплава цинка и кальция с углём.
Получение
В настоящее время получают прокаливанием в электрических печах (температура 1900—1950 °C) смеси оксида кальция с коксом.
Полученный таким образом технический продукт имеет грязную окраску вследствие загрязнения углём и другими красящими примесями. Он содержит также примеси фосфида и сульфида кальция, вследствие чего такой карбид кальция и полученный из него ацетилен имеют неприятный запах.
Свойства
При соединении с водой разлагается, образуя ацетилен и гидроксид кальция (гашеную известь).
CaC2 + 2h4O → C2h4 + Ca(OH)2Применение
Карбид кальция широко применяют в технике для производства ацетилена, цианамида кальция (при нагревании с азотом), а также для восстановления щелочных металлов.
См. также
В этой статье не хватает ссылок на источники информации. Информация должна быть проверяема, иначе она может быть поставлена под сомнение и удалена. Вы можете отредактировать эту статью, добавив ссылки на авторитетные источники. Эта отметка установлена 31 мая 2011. |
dic.academic.ru
Как получить ацетилен из карбида кальция
Ацетилен – самый простой представитель класса алкинов, имеет химическую формулу С2Н2. Бесцветный газ, горюч, в смеси с воздухом взрывоопасен. Благодаря наличию тройной связи в своей молекуле, весьма активен с химической точки зрения, легко вступает в реакции присоединения. При сгорании выделяет большое количество тепла, что может быть использовано, например, многим известная «ацетиленовая горелка». Как же его синтезировать? При хранении ацетилена следует учитывать его особенности. Например, его нельзя держать в баллонах, имеющих бронзовый вентиль, поскольку газ реагирует с медью, входящей в состав бронзы, образуя чрезвычайно взрывоопасное вещество – ацетиленид меди. Самый старый, проверенный временем метод получения ацетилена – реакция карбида кальция с водой. Наверное, многие мальчишки в детстве развлекались, бросая кусочки карбида в лужу, тут же начиналось яростное шипение, карбид буквально «бурлил», исчезая на глазах, и в воздухе отчетливо пахло чем-то резким, «острым». Эта реакция протекает таким образом: СаС2 + 2Н2О = С2Н2 + Са(ОН)2 Для того чтобы она протекала не слишком бурно, можно использовать не простую воду, а насыщенный раствор хлорида натрия, например. Если этот опыт планируется показать на уроке химии, следует подобрать реакционную колбу подходящего размера. Если она будет слишком маленькой, то образующая при растворении карбида пена может быть «выброшена» давлением ацетилена в отводную трубку, и дальше – в приемный сосуд. В случае же с чересчур большой колбой, придется долго ждать, пока образующийся ацетилен не вытеснит весь воздух из прибора. Воду, а лучше насыщенный раствор хлорида натрия, следует добавлять в колбу с кусочками карбида медленно, по каплям, регулируя скорость реакции, не допуская, чтобы она протекала чересчур бурно. Используется ацетилен в самых разных областях. Например, как сырье для получения целого ряда химических веществ (уксусной кислоты, пластмасс, некоторых ароматических углеводородов, некоторых видов синтетического каучука, этилового спирта и т.д.). На его основе синтезируют некоторые очень сильные взрывчатые вещества, используемые в качестве инициаторов, т.е. для детонации. Повсеместно применяется при резке и сварке металлов, при получении яркого света в автономных светильниках. Как получить ацетилен из карбида кальция
www.kakprosto.ru
www.moscow-vitaminp.ru
Карбид кальция | khimie.ru
Карбид кальция — собственно ацетилид кальция (ибо его можно производить от ацетилена), обычно называемый просто карбидом, образует в чистом виде бесцветную кристаллическую массу удельного веса 2,22, Он нерастворим ни в одном из обычных растворителей. Водой разлагается с образованием ацетилена. Из оксидов металлов он выделяет при высокой температуре свободные металлы или взаимодействует с ними с образованием карбидов соответствующих металлов и оксида кальция. С азотом карбид кальция при нагревании переходит в цианамид кальция СаСN2.
Технически карбид получают нагреванием жженой извести с коксом; или древесным углем в электрических почах. Электроды состоят из больших угольных брусков, через которые пропускают ток до 50000 А.
При получении в технических масштабах на каждый килограмм 85% -ного карбида расходуется около 1 кг едкой извести, 0,7 кг кокса и 2,8-3,5 квт-ч электроэнергии.
Для получения карбида в небольших количествах лучше всего поступать следующим образом в плавильном тигле средней величины стачивают наждачным кругом дно, так что образуется отверстие, через которое вставляется уголь дуговой лампы толщипой 13-15 мм.
Верхнюю часть угля вдвигают приблизительно на 2 мм в тигль, укрепляют его в этом положении при помощи глины и соединяют через сопротивление и амперметр с отрицательным полюсом электрической сети. Анодом служит твердый заостренный уголь длиной 10-15 см, толщиной 7 мм, укрепленный зажимом на стеклянном штативе, который для удобства передвижения угля вверх и вниз целесообразно снабдить зубчатым механизмом. Реакционную смесь приготовляют, тщательно перемешивая 15 г тонко измельченного порошка оксида кальция с 20 г порошка древесного угля. Сначала насыпают очень немного этой смеси и включают ток силой примерно 12-14 А. Вместо постоянного тока можно пользоваться и переменным. Во время опыта, продолжающегося около 10-15 мин, понемногу подсыпают смесь. Кроме того, тигель следует закрыть асбестовым листом с проделанным в нем отверстием. Расстояние между углями, равное вначале 1 см, во время опыта доводят до 5-6 см. Количество карбида, получаемого при помощи такого простого устройства, достаточно для приготовления нескольких литров ацетилена.
Помимо получения ацетилена, карбид кальция. расходуется прежде всего для получения цианамида кальция. Кроме того, его используют в качестве восстановителя в металлургии.
Чистый СаС2 обладает, как показал Франк, решеткой иной структуры, чем загрязненный примесями и технический карбид. Последний кристаллизуется, образуя тетрагональную гранецентрированную решетку, так же как чистый SrС2 и ВаС2. Карбид кальция, содержащий СаСN2, образует иную решетку. Чистый СаС2 легко, а технический с большим трудом превращается в СаСN2.
Ваш отзыв
Вы должны войти, чтобы оставлять комментарии.
khimie.ru