Стан для сварки продольных швов труб большого диаметра конечной длины. Сварка продольных швов труб
16.3. Сварка продольных швов
16.3.1. Продольные швы (по плавникам) выполняют ручной дуговой сваркой, механизированной сваркой в углекислом газе или механизированной сваркой порошковой проволокой.
Сварка производится углеродистым присадочным материалом независимо от способа сварки и марки свариваемой стали:
при ручной дуговой сварке - электродами Э50А (УОНИ-13/55, ЦУ-5, ТМУ-21У) диаметром не более 4 мм;
при механизированной сварке в углекислом газе - сварочной проволокой Св-08Г2С или Св-08ГС диаметром 1,2-1,6 мм;
при механизированной сварке порошковой проволокой - проволокой марок, указанных в табл.П9.2 приложения 9(при использовании проволоки ПП-АН8 требуется дополнительная защита углекислым газом).
16.3.2. Наложение продольных швов по плавникам в районе стыковых соединений труб (на участках, остающихся недоваренными на заводе), а также при соединении (укрупнении) панелей на сборочной площадке следует производить с двух сторон. Допускается односторонняя сварка при условии снятия фаски на плавниках под углом 30° с обеспечением провара корня шва на всю глубину плавника.
16.3.3. Зазор между свариваемыми плавниками независимо от способа сварки должен быть не менее 1,5 и не более 3 мм. В местах отсутствия зазора необходимо пропилить плавники механическим путем (наждачным кругом, фрезой и т.д.) и обеспечить требуемый зазор.
Если зазор превышает норму и составляет 3-5 мм или плавники состыкованы со смещением (ступенькой), сварку продольных швов необходимо выполнять с двух сторон обратноступенчатым способом.
16.3.4. После сварки и ультразвукового контроля стыков труб соединения выравнивают по плавникам на участках, оставшихся недоваренными на заводе, и накладывают по две прихватки длиной 60-70 мм на каждом участке.
16.3.5. Сварку недоваренных на заводе участков продольных швов должны производить два сварщика, начиная от середины блока к краям через одну трубу.
16.3.6. Сварку швов необходимо осуществлять обратноступенчатым способом. Заварив швы с одной стороны панели, сварщики в той же последовательности должны сваривать швы с противоположной стороны блока (панели).
16.3.7. Если недоваренные на заводе участки находятся с обеих сторон кольцевого шва, то накладывают все швы вначале с одной стороны стыка труб, затем - с другой. После этого сварщики переходят на противоположную сторону блока и выполняют швы в той же последовательности.
16.3.8. При сварке продольных швов допускается, чтобы сварщики работали одновременно на противоположных сторонах панели (один сверху, другой снизу). В этом случае порядок сварки тот же, что указан в пп.16.3.5-16.3.7.
16.3.9. Стенки топочной части котла собирают на плазе из блоков панелей с зазором между плавниками 1,5-3 мм. Панели, собранные в блоки, прихватывают по краям, отступая от края на 50-70 мм, и далее через каждые 400-500 мм по всей длине блока. Длина прихваточных швов должна быть 150-200 мм, высота - равной толщине плавника. Прихватки не перевариваются, а являются частью основного шва.
16.3.10. Продольные швы панелей должны выполнять одновременно два или четыре сварщика. Швы длиной более 16 м должны выполнять одновременно четыре сварщика. Сварку могут вести одновременно все сварщики с одной стороны панели (сверху или снизу) или с противоположных ее сторон (один снизу, другой сверху или двое снизу и двое сверху). Сварку следует производить от середины блока к краям независимо от числа сварщиков по схеме рис.16.2. Каждую часть шва выполняют обратноступенчатым способом.
16.3.11. При стыковке блоков А и Б панелей с большой серповидностью, когда зазор а между плавниками превышает 5 мм (рис.16.3), необходимо распределить его равномерно по соседним стыкам. Для этого следует разрезать несколько (два-пять) соседних продольных швов на участках длиной l и развести трубы до образования зазора не более 5 мм, затем эти участки прихватить и заварить с двух сторон обратноступенчатым способом. Если панели нельзя состыковать с зазором менее 5 мм, сваривать их необходимо по технологии завода - изготовителя котла.
"Рис.16.2. Схема сварки панелей по плавникам на сборочной площадке"
16.3.12. Продольные стыковые швы на вертикальной плоскости (при стыковке блоков панелей в проектном положении) выполняют, как правило, ручной дуговой сваркой. Сварку ведут одновременно два или четыре сварщика с разбивкой шва по длине на четыре равные части. Каждую часть заваривают обратноступенчатым способом, однако в этом случае на всей длине шва участки по 400-500 мм сваривают в одном направлении - снизу вверх. Сварку следует выполнять электродами диаметром 2,5-3 мм. Разрешается сварку вертикальных швов с одной стороны панели выполнять электродами диаметром 4 мм.
"Рис.16.3. Стыковка панелей с большой серповидностью"
16.3.13. Стенки в углах топки соединяют с помощью прутка диаметром d = 8-10 мм из стали 20 или 12X1МФ (рис.16.4), при этом зазор b между стенками должен быть не более 12 мм. Если зазор превышает указанный размер, то конструкция узла соединения стенок и технология сварки должны быть определены заводом - изготовителем котла.
После установки стенок в проектное положение приваривают пруток к обеим стенкам в вертикальном положении с соблюдением требований, изложенных в п.16.3.12. Пруток к трубе необходимо приваривать электродами диаметром 2,5-3 мм на минимальном токе, чтобы глубина проплавления стенки трубы была не более 2 мм. Для приварки прутка к плавнику могут быть применены электроды диаметром 4 мм.
16.3.14. Оборудование и режим механизированной сварки в углекислом газе приведены в разделе 11.
"Рис.16.4. Соединение стенок газоплотных панелей"
16.3.15. Для механизированной сварки порошковой проволокой используются полуавтоматы ПМП-6, А-765УЗ, А-1197П, А-1197С, А-1035. При сварке самозащитной порошковой проволокой полуавтоматы комплектуются горелками А-1231-5-02 или А-1231-5-03, при сварке порошковой проволокой с дополнительной защитой углекислым газом - горелками А-1231-5Г2 или А-1231-5Г3.
Сварку порошковой проволокой следует выполнять на постоянном токе обратной полярности.
В качестве источников питания постоянного тока используются преобразователи или выпрямители с жесткой или пологопадающей вольт-амперной характеристикой.
Ориентировочные режимы механизированной сварки порошковой проволокой приведены в табл.16.1; они должны уточняться при пробной сварке.
Толщина наплавляемого слоя должна быть не более 6 мм.
16.3.16. Все продольные швы по плавникам подвергаются визуальному контролю и проверке керосиновой пробой. Нормы оценки качества по результатам визуального контроля приведены в подразделе 18.3. Керосиновая проба на плотность производится по документу ПНАЭ Г7-019-89.
studfiles.net
Способы сварки трубопроводов и виды сварных соединений
Способы сварки трубопроводов и виды сварных соединений
При изготовлении и монтаже технологических трубопроводов наиболее распространенным способом получения неразъемных соединений является сварка. Сваривать трубопроводы можно промышленным способом, обеспечивающим выполнение требований СНиП III-Г.9—62. При этом должны быть максимально использованы автоматические или полуавтоматические способы сварки.
Сварке подвергают металлы, неметаллические материалы — пластмассы, стекло.
Все существующие способы сварки можно разделить на две основные группы: сварка давлением (пластическая) и сварка плавлением.
Основные способы сварки, получившие или получающие в настоящее время широкое применение в народном хозяйстве, приведены в классификации.
При изготовлении и монтаже технологических трубопроводов применяют в основном следующие виды сварки: ручную газовую, ручную электродуговую с помощью металлических электродов, полуавтоматическую и автоматическую электродуговую под слоем флюса, полуавтоматическую и автоматическую электродуговую в среде защитных газов, электроконтактную стыковую. В последнее время внедряется сварка порошковой и голой электродной проволоками, а также стыковая при высокочастотном нагреве (рис. 76).
Наибольшее применение при изготовлении трубопроводов получили способы электродуговой сварки, которые производят на постоянном и переменном токе. При сварке на постоянном токе к изделию присоединяют провод, соединенный с плюсовым полюсом машины, а к электроду — провод от минусового полюса машины. Такое соединение сварочной цепи называется соединением с прямой полярностью. Обратное соединение сварочных проводов — плюс на электроде и минус на изделии называется соединением с обратной полярностью.
Рис. 76. Принципиальная схема стыковой сварки труб при индукционном нагреве: 1 — труба, 2 — зажим, 3 — трансформатор ТВЧ, 4 — индуктор
Экономически более выгодна сварка на переменном токе вследствие меньшего расхода электроэнергии, меньшей стоимости оборудования и более простого ухода за ними по сравнению с машинами постоянного тока.
При сварке технологических трубопроводов используют различные виды сварных соединений — стыковые, нахлесточные, а в ряде случаев — угловые (приварка штуцеров, плоских фланцев). На рис. 77 приведены часто применяемые виды сварных соединений труб и деталей трубопроводов.
Рис. 77. Виды сварных соединений труб и деталей трубопроводов:
а — стыковое продольное с односторонним швом, б — стыковое продольное с двухсторонним швом, в — стыковое поперечное с односторонним швом без скоса кромок, г — то же со скосом кромок, д — стыковое поперечное с подкладным кольцом без расточки, е — то же с внутренней расточкой, ж — стыковое контактное, з — угловое одностороннее без скоса кромок, и — угловое двухстороннее без скоса кромок, к — угловое одностороннее со скосом кромок, л — раструбное нахлесточное.
Благодаря повышенной прочности наибольшее распространение имеет сварное соединение встык. Стыковые соединения могут иметь продольное (рис. 77, а,б)и поперечное (рис. 76,в— ж) расположение шва. Продольные стыки часто выполняют при изготовлении труб и деталей трубопроводов из листа, поперечные стыки — при соединении труб и деталей трубопроводов между собой.
По характеру выполнения сварного соединения швы разделяются на односторонние (рис. 77,а, в, г), двухсторонние (рис. 77,6), односторонние с подкладным кольцом (рис. 77, д, е). Трубопроводы с условным проходом до 500 мм сваривают только односторонним швом. Двухсторонний шов, т. е. с подваркой корня шва с внутренней стороны для повышения прочности соединения применяют для трубопроводов с условным проходом 600 мм и выше. Ограниченное применение подкладных колец объясняется тем, что они уменьшают проходное сечение трубопровода и вызывают дополнительное гидравлическое сопротивление.
Угловое сварное соединение без скоса кромок (рис. 77, з, и)и со скосом одной кромки (рис. 77, к) выполняют при изготовлении сварных деталей трубопроводов, а также при сварке деталей с трубами.
Рис. 78. Положение сварного шва в пространстве: I — нижнее, II — вертикальное, I I I — потолочное, IV — горизонтальное на вертикальной плоскости
Сварное соединение в раструб — нахлесточное (рис. 77, л) является менее прочным, чем стыковое, и требует дополнительного расхода труб, а также необходимости производить предварительную раздачу конца трубы по диаметру. Такое соединение нашло применение в основном при сварке труб из цветных металлов и неметаллических материалов.
В соответствии с положением швов в пространстве различают сварку в нижнем I и вертикальном II положениях, а также в верхнем потолочном Положении III (рис. 78). В зависимости от условий выполнения сварочных работ их подразделяют на поворотные и неповоротные.
Большинство поворотных стыков труб и деталей, выполняемых на трубозаготовительных заводах и в мастерских, сваривают наиболее простым и удобным швом в нижнем положении. Сварка неповоротных стыков значительно сложнее и требует высокой квалификации сварщика.
Вне зависимости от способа сварки основными требованиями, предъявляемыми к сварному шву технологических трубопроводов, являются прочность, пластичность и плотность. Прочность и пластичность металла швов должна быть не ниже, чем у основного металла.
К сварке и прихватке стыков трубопроводов I, II, III и IV категории допускаются сварщики, имеющие удостоверение о сдаче испытаний в соответствии с «Правилами испытания электросварщиков и газосварщиков для допуска их к ответственным сварочным работам», утвержденными Госгортехнадзором.
Номера сварных стыков трубопроводов I и II категории необходимо записывать в журнале сварочных работ. К сварке и прихватке стыков трубопроводов V категории допускаются сварщики без сдачи испытаний по правилам Госгортехнадзора, неуспешно выполнившие пробные стыки.
Каждому сварщику выдается клеймо, номер которого он обязан выбивать на расстоянии 30—50 мм от стыка.
1. Какие основные виды сварки применяют при трубопроводных работах?
2. Какие основные виды сварных соединений используют при сварке трубопроводов, в чем их особенности?
3. Какие основные требования предъявляют к сварным швам?
4. Какие положения могут иметь сварные швы в пространстве, в чем особенности?
Все материалы раздела «Сварка труб» :
● Способы сварки трубопроводов и виды сварных соединений
● Подготовка труб под сварку
● Технология газовой сварки и резки
● Кислородно-флюсовая и дуговая резка
● Технология ручной электродуговой сварки, электроды
● Источники питания сварочной дуги
● Автоматическая и полуавтоматическая сварка под флюсом
● Автоматическая и полуавтоматическая сварка в защитных газах
● Сварка трубопроводов из легированной стали
● Сварка трубопроводов высокого давления, термообработка сварных соединений
● Сварка трубопроводов из алюминия и его сплавов, из меди и ее сплавов
● Пайка трубопроводов, дефекты сварных швов
● Контроль качества сварных швов
● Виды сварки и применяемое оборудование
● Сварка и склеивание винипластовых труб
● Сварка полиэтиленовых трубопроводов
● Правила техники безопасности при резке и сварке трубопроводов
shkval-antikor.ru
16.3. Сварка продольных швов
16.3.1. Продольные швы (по плавникам) выполняют ручной дуговой сваркой, механизированной сваркой в углекислом газе или механизированной сваркой порошковой проволокой.
Сварка производится углеродистым присадочным материалом независимо от способа сварки и марки свариваемой стали:
при ручной дуговой сварке - электродами Э50А (УОНИ-13/55, ЦУ-5, ТМУ-21У) диаметром не более 4 мм;
при механизированной сварке в углекислом газе - сварочной проволокой Св-08Г2С или Св-08ГС диаметром 1,2-1,6 мм;
при механизированной сварке порошковой проволокой - проволокой марок, указанных в табл.П9.2 приложения 9(при использовании проволоки ПП-АН8 требуется дополнительная защита углекислым газом).
16.3.2. Наложение продольных швов по плавникам в районе стыковых соединений труб (на участках, остающихся недоваренными на заводе), а также при соединении (укрупнении) панелей на сборочной площадке следует производить с двух сторон. Допускается односторонняя сварка при условии снятия фаски на плавниках под углом 30° с обеспечением провара корня шва на всю глубину плавника.
16.3.3. Зазор между свариваемыми плавниками независимо от способа сварки должен быть не менее 1,5 и не более 3 мм. В местах отсутствия зазора необходимо пропилить плавники механическим путем (наждачным кругом, фрезой и т.д.) и обеспечить требуемый зазор.
Если зазор превышает норму и составляет 3-5 мм или плавники состыкованы со смещением (ступенькой), сварку продольных швов необходимо выполнять с двух сторон обратноступенчатым способом.
16.3.4. После сварки и ультразвукового контроля стыков труб соединения выравнивают по плавникам на участках, оставшихся недоваренными на заводе, и накладывают по две прихватки длиной 60-70 мм на каждом участке.
16.3.5. Сварку недоваренных на заводе участков продольных швов должны производить два сварщика, начиная от середины блока к краям через одну трубу.
16.3.6. Сварку швов необходимо осуществлять обратноступенчатым способом. Заварив швы с одной стороны панели, сварщики в той же последовательности должны сваривать швы с противоположной стороны блока (панели).
16.3.7. Если недоваренные на заводе участки находятся с обеих сторон кольцевого шва, то накладывают все швы вначале с одной стороны стыка труб, затем - с другой. После этого сварщики переходят на противоположную сторону блока и выполняют швы в той же последовательности.
16.3.8. При сварке продольных швов допускается, чтобы сварщики работали одновременно на противоположных сторонах панели (один сверху, другой снизу). В этом случае порядок сварки тот же, что указан в пп.16.3.5-16.3.7.
16.3.9. Стенки топочной части котла собирают на плазе из блоков панелей с зазором между плавниками 1,5-3 мм. Панели, собранные в блоки, прихватывают по краям, отступая от края на 50-70 мм, и далее через каждые 400-500 мм по всей длине блока. Длина прихваточных швов должна быть 150-200 мм, высота - равной толщине плавника. Прихватки не перевариваются, а являются частью основного шва.
16.3.10. Продольные швы панелей должны выполнять одновременно два или четыре сварщика. Швы длиной более 16 м должны выполнять одновременно четыре сварщика. Сварку могут вести одновременно все сварщики с одной стороны панели (сверху или снизу) или с противоположных ее сторон (один снизу, другой сверху или двое снизу и двое сверху). Сварку следует производить от середины блока к краям независимо от числа сварщиков по схеме рис.16.2. Каждую часть шва выполняют обратноступенчатым способом.
16.3.11. При стыковке блоков А и Б панелей с большой серповидностью, когда зазор а между плавниками превышает 5 мм (рис.16.3), необходимо распределить его равномерно по соседним стыкам. Для этого следует разрезать несколько (два-пять) соседних продольных швов на участках длиной l и развести трубы до образования зазора не более 5 мм, затем эти участки прихватить и заварить с двух сторон обратноступенчатым способом. Если панели нельзя состыковать с зазором менее 5 мм, сваривать их необходимо по технологии завода - изготовителя котла.
"Рис.16.2. Схема сварки панелей по плавникам на сборочной площадке"
16.3.12. Продольные стыковые швы на вертикальной плоскости (при стыковке блоков панелей в проектном положении) выполняют, как правило, ручной дуговой сваркой. Сварку ведут одновременно два или четыре сварщика с разбивкой шва по длине на четыре равные части. Каждую часть заваривают обратноступенчатым способом, однако в этом случае на всей длине шва участки по 400-500 мм сваривают в одном направлении - снизу вверх. Сварку следует выполнять электродами диаметром 2,5-3 мм. Разрешается сварку вертикальных швов с одной стороны панели выполнять электродами диаметром 4 мм.
"Рис.16.3. Стыковка панелей с большой серповидностью"
16.3.13. Стенки в углах топки соединяют с помощью прутка диаметром d = 8-10 мм из стали 20 или 12X1МФ (рис.16.4), при этом зазор b между стенками должен быть не более 12 мм. Если зазор превышает указанный размер, то конструкция узла соединения стенок и технология сварки должны быть определены заводом - изготовителем котла.
После установки стенок в проектное положение приваривают пруток к обеим стенкам в вертикальном положении с соблюдением требований, изложенных в п.16.3.12. Пруток к трубе необходимо приваривать электродами диаметром 2,5-3 мм на минимальном токе, чтобы глубина проплавления стенки трубы была не более 2 мм. Для приварки прутка к плавнику могут быть применены электроды диаметром 4 мм.
16.3.14. Оборудование и режим механизированной сварки в углекислом газе приведены в разделе 11.
"Рис.16.4. Соединение стенок газоплотных панелей"
16.3.15. Для механизированной сварки порошковой проволокой используются полуавтоматы ПМП-6, А-765УЗ, А-1197П, А-1197С, А-1035. При сварке самозащитной порошковой проволокой полуавтоматы комплектуются горелками А-1231-5-02 или А-1231-5-03, при сварке порошковой проволокой с дополнительной защитой углекислым газом - горелками А-1231-5Г2 или А-1231-5Г3.
Сварку порошковой проволокой следует выполнять на постоянном токе обратной полярности.
В качестве источников питания постоянного тока используются преобразователи или выпрямители с жесткой или пологопадающей вольт-амперной характеристикой.
Ориентировочные режимы механизированной сварки порошковой проволокой приведены в табл.16.1; они должны уточняться при пробной сварке.
Толщина наплавляемого слоя должна быть не более 6 мм.
16.3.16. Все продольные швы по плавникам подвергаются визуальному контролю и проверке керосиновой пробой. Нормы оценки качества по результатам визуального контроля приведены в подразделе 18.3. Керосиновая проба на плотность производится по документу ПНАЭ Г7-019-89.
studfiles.net
Способ лазерной сварки продольного шва трубы (варианты)
Изобретение относится к производству труб, в частности к сборке-сварке сформованных заготовок для труб большого диаметра с применением технологий лазерной и гибридной лазерно-дуговой сварки.
В сварных соединениях большой толщины (более 15 мм), выполненных по технологиям лазерной и гибридной лазерно-дуговой сварки, часто встречаются характерные для этих технологий дефекты, представляющие собой плоские полости различной глубины залегания и протяженности, расположенные точно по оси шва, в поперечном сечении похожие на трещину (фиг. 1). Причиной образования дефекта является то, что большой объем расплавленного металла стекает по стенкам относительно небольшого по сечению парогазового канала и перекрывает его. Высокая плотность, вязкость и короткий срок пребывания металла в жидком состоянии практически не дают времени всему газу выйти из парогазового канала, вследствие чего металл кристаллизуется, образуя полости по центру шва. Кроме того, при больших толщинах свариваемых изделий присадочный металл от дугового процесса не доставляется в центральную и корневую часть шва из-за малого размера сварочной ванны и больших скоростей расплавления и кристаллизации.
Из уровня техники известен способ сварки металлических материалов лазерным лучом высокой мощности (патент US 20100243621), в котором между свариваемыми поверхностями прижимаются металлическая прокладка, причем торец прокладки располагается выше поверхности стыка деталей.
Недостатками данного способа являются:
1. Высокая вероятность образования характерных дефектов (газовой полость) при сварке изделий большой толщины, поскольку парогазовый канал имеет очень небольшой размер и легко может быть перекрыт расплавленным металлом, текущим по стенкам парогазового канала.
2. При сборке-сварке заготовок для труб большого диаметра зажимать прокладку между кромок по всей длине с одинаковой высотой выступа торца крайне трудоемко.
3. Фактическая толщина, которую должен будет проплавить лазер, больше толщины свариваемых деталей на величину выступа торца металлической прокладки над поверхностью деталей.
Наиболее близким техническим решением к каждому изобретению из группы является способ лазерной сварки с использованием вентилируемой прокладки (патент ЕР 2248624), в котором между свариваемыми кромками изделий прижимаются металлические прокладки. Причем металлические прокладки расположены друг относительно друга на расстоянии, чтобы во время сварки образовывать канал между деталями для выхода газов из сварочного канала. Торец прокладок располагается выше поверхности стыка деталей. После установки прокладок в способе выполняют наложение сварного шва с использованием лазерного излучения.
К причинам, препятствующим достижению указанного ниже технического результата при использовании известного способа, относится необходимость прижимать прокладки к кромкам трубной заготовки, а тем более при расположении их на одинаковом расстоянии друг от друга. Это приводит к необходимости контроля положения указанных элементов при операции сборки трубной заготовки, предваряющей наложение корневого шва с использованием технологий лазерной сварки.
Заявляемые варианты способа сварки продольного шва трубы решают одну и ту же проблему повышения качества продольного сварного шва трубы, выполняемого с использованием лазерного излучения.
Техническим результатом, обеспечиваемым настоящим изобретением (вариантами способа), является повышение технологичности процесса сварки.
Технический результат заявляемого изобретения по первому варианту обеспечивается тем, что в способе лазерной сварки продольного шва трубы, включающем наложение сверху корневого шва с использованием лазерного луча на стык кромок трубной заготовки, имеющей в стыке расположенные с шагом элементы из сплава металлов с образованием между ними наклонных каналов для выхода газов при наложении корневого шва, перед наложением корневого шва выполняют подготовку кромок трубной заготовки и ее пошаговую формовку, при этом элементы представляют собой валики из сплава металлов, имеющего легирующий состав, которые наплавляют на одну из кромок трубной заготовки так, что каналы имеют восходящее направление относительно направление движения лазерного луча.
Технический результат заявляемого изобретения по второму варианту обеспечивается тем, что в способе лазерной сварки продольного шва трубы, включающем наложение сверху корневого шва с использованием лазерного луча на стык кромок трубной заготовки, имеющей в стыке расположенные с шагом элементы из сплава металлов с образованием между ними наклонных каналов для выхода газов при наложении корневого шва, перед наложением корневого шва выполняют подготовку кромок трубной заготовки, ее пошаговую формовку и наложение технологического шва, при этом элементы представляют собой валики из сплава металлов, имеющего легирующий состав, которые наплавляют на одну из кромок трубной заготовки так, что каналы имеют нисходящее направление относительно направления движения лазерного луча.
По двум вариантам способа высота валиков не превышает 0,5 мм.
Выполнение наплавки на одну из кромок трубной заготовки элемента перед выполнением корневого шва исключает необходимость придерживать прокладки и контролировать их положение в процессе сварки. По мере наложения корневого шва с использованием лазерного излучения образование наклонных каналов происходит в процессе смыкания кромок, следовательно, на протяжении процесса сварки нет препятствий для выхода газов.
Выполнение наплавки повышает технологичность процесса, не осложненного операциями зажима вставляемых между кромками элементов и контроля, обеспечивающего соблюдение интервала (шага) между ними.
По первому варианту наплавку производят для образования каналов, имеющих восходящее направление. Это обусловлено направлением движения лазерного луча при наложении корневого шва сверху.
По второму варианту способа наличие технологического (прихваточного) шва, выполняемого с наружной стороны трубной заготовки, обусловливает нисходящее направление каналов для выхода газов.
По двум вариантам способа наличие валиков из сплава металлов, имеющего легирующий состав, обеспечивает легирование по всей толщине сварного соединения, т.к. в процессе сварки расплавленный металл валиков соединяется с основным металлом сварочной ванны.
Высота валика выбрана исходя из необходимости сжатия кромок трубной заготовки с зазором, величина которого равна величине высоты валика наплавки. Таким образом, превышение размера 0,5 мм приводит к излишнему зазору между кромками и увеличивает вероятность появления дефекта в виде неоплавления одной из кромок. Химический состав легирующего сплава наплавляемых валиков выбирается близким основному металлу.
Совокупность существенных признаков заявляемого изобретения позволяет обеспечить высокую технологичность сварного соединения, т.е. достичь заявленного технического результата.
Сущность заявляемого способа поясняется чертежами.
Фиг. 1 - возможные дефекты сварного шва;
Фиг. 2 - схематично показан пример сварки согласно изобретению в месте контакта продольных краев открытой трубы по первому варианту.
Фиг. 3 - схематично показан пример сварки согласно изобретению по второму варианту.
Осуществление изобретения.
В первом варианте предлагаемого способа перед сборкой-сваркой, на этапе подготовки поверхности кромок к сварке, а именно после фрезеровки на притупление одной из кромок трубной заготовки 1 любым известным способом наплавляются элементы, которые представляют собой валики из сплава металлов, имеющего легирующий состав. Наплавку производят так, чтоб при сжатии сформованной трубной заготовки каналы имели восходящее направление относительно направления движения лазерного луча для создания условия беспрепятственного выхода газа из парогазового канала.
Между валиками выдерживается интервал 3 (фиг. 2). Далее сформованная трубная заготовка поступает в сборочно-сварочный стан, где происходит ее обжатие и сборка кромок встык и в собранном виде проваривается лазером 4 или гибридным лазерно-дуговым процессом.
Во втором варианте предлагаемого способа перед сборкой-сваркой, на этапе подготовки поверхности кромок к сварке, а именно после фрезеровки на притупление одной из кромок трубной заготовки 1 любым известным способом наплавляются элементы, которые представляют собой валики из сплава металлов, имеющего легирующий состав. Наплавку производят так, чтоб при сжатии сформованной трубной заготовки каналы имели нисходящее направление относительно направления движения лазерного луча для создания условия беспрепятственного выхода газа из парогазового канала.
Между валиками выдерживается интервал (шаг) 3 (фиг. 2). Далее сформованная трубная заготовка поступает в сборочно-сварочный стан, где происходит ее обжатие и сборка кромок встык и в собранном виде проваривается технологическим швом, после этого проваривается корневой шов.
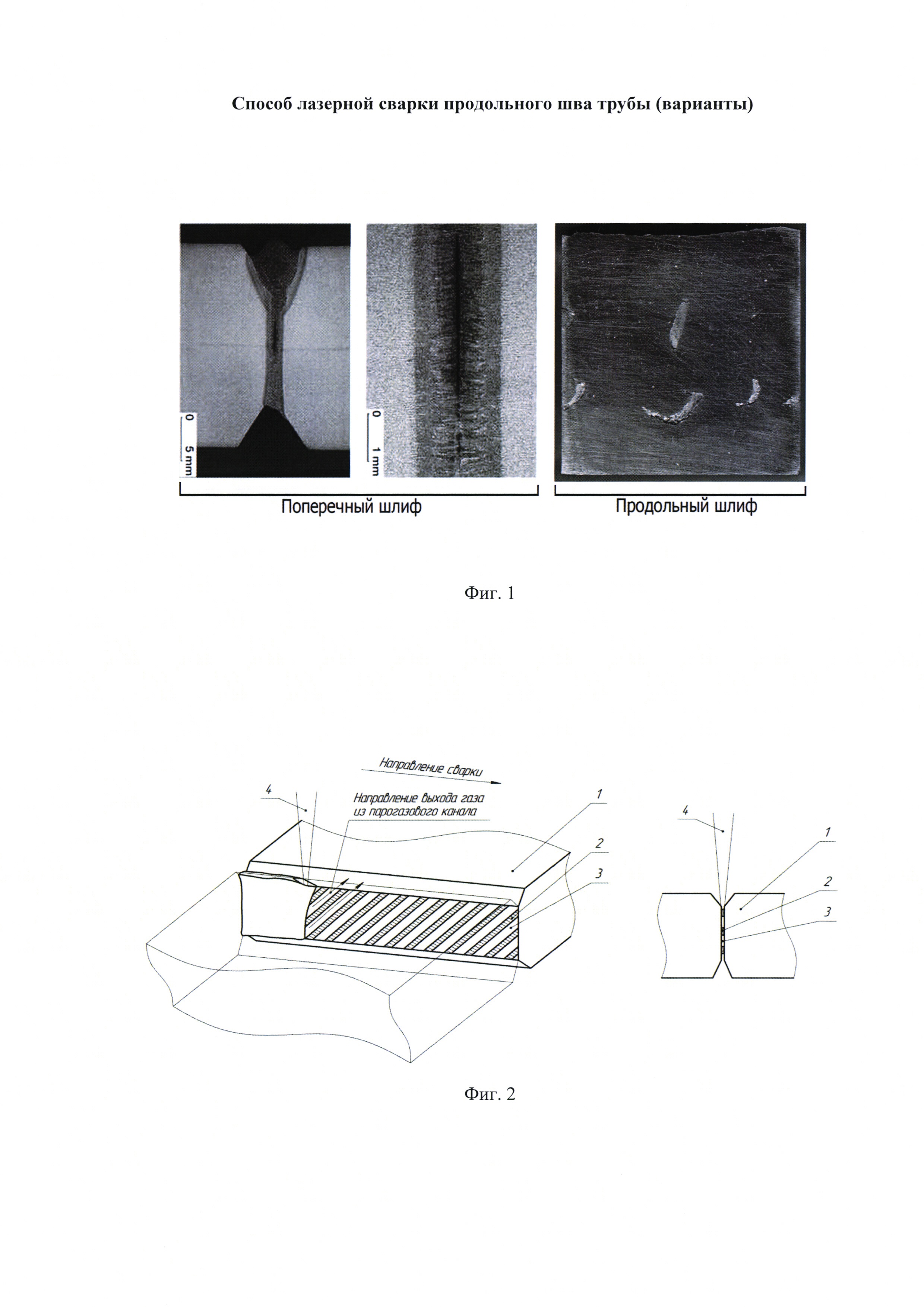
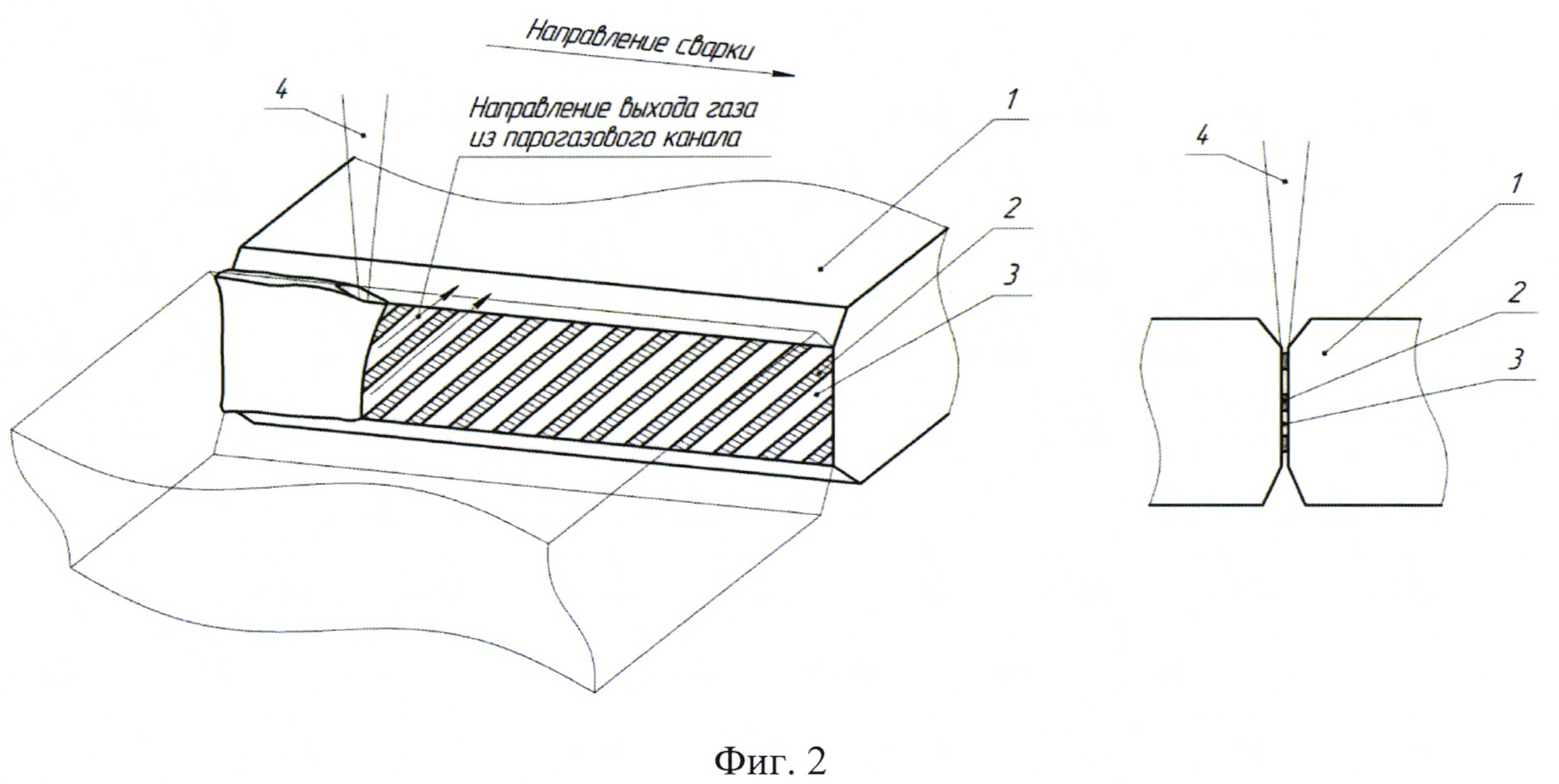
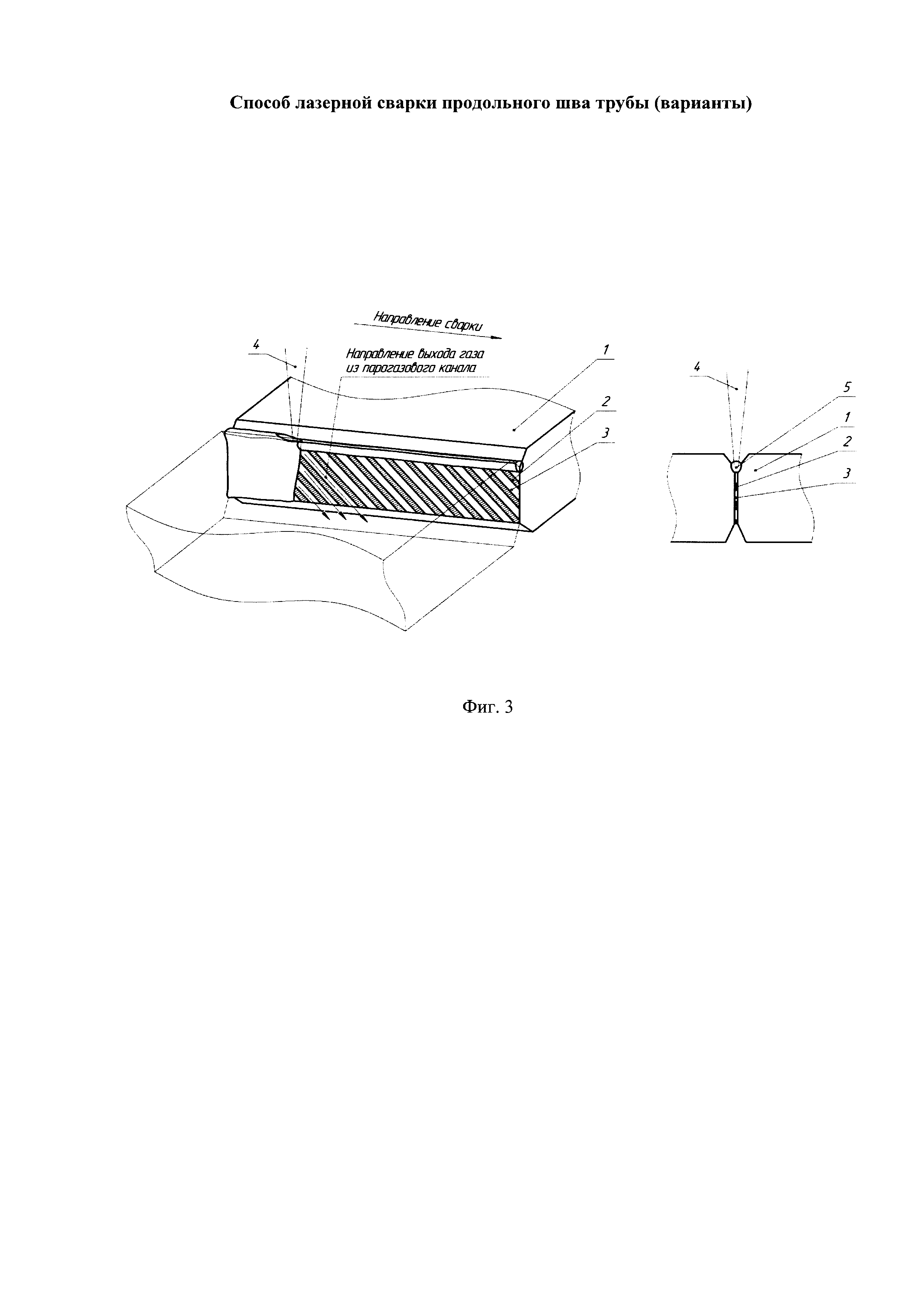
edrid.ru
Искать все виды документовДокументы неопределённого видаISOАвиационные правилаАльбомАпелляционное определениеАТКАТК-РЭАТПЭАТРВИВМРВМУВНВНиРВНКРВНМДВНПВНПБВНТМ/МЧМ СССРВНТПВНТП/МПСВНЭВОМВПНРМВППБВРДВРДСВременное положениеВременное руководствоВременные методические рекомендацииВременные нормативыВременные рекомендацииВременные указанияВременный порядокВрТЕРВрТЕРрВрТЭСНВрТЭСНрВСНВСН АСВСН ВКВСН-АПКВСПВСТПВТУВТУ МММПВТУ НКММПВУП СНЭВУППВУТПВыпускГКИНПГКИНП (ОНТА)ГНГОСТГОСТ CEN/TRГОСТ CISPRГОСТ ENГОСТ EN ISOГОСТ EN/TSГОСТ IECГОСТ IEC/PASГОСТ IEC/TRГОСТ IEC/TSГОСТ ISOГОСТ ISO GuideГОСТ ISO/DISГОСТ ISO/HL7ГОСТ ISO/IECГОСТ ISO/IEC GuideГОСТ ISO/TRГОСТ ISO/TSГОСТ OIML RГОСТ ЕНГОСТ ИСОГОСТ ИСО/МЭКГОСТ ИСО/ТОГОСТ ИСО/ТСГОСТ МЭКГОСТ РГОСТ Р ЕНГОСТ Р ЕН ИСОГОСТ Р ИСОГОСТ Р ИСО/HL7ГОСТ Р ИСО/АСТМГОСТ Р ИСО/МЭКГОСТ Р ИСО/МЭК МФСГОСТ Р ИСО/МЭК ТОГОСТ Р ИСО/ТОГОСТ Р ИСО/ТСГОСТ Р ИСО/ТУГОСТ Р МЭКГОСТ Р МЭК/ТОГОСТ Р МЭК/ТСГОСТ ЭД1ГСНГСНрГСССДГЭСНГЭСНмГЭСНмрГЭСНмтГЭСНпГЭСНПиТЕРГЭСНПиТЕРрГЭСНрГЭСНсДИДиОРДирективное письмоДоговорДополнение к ВСНДополнение к РНиПДСЕКЕНВиРЕНВиР-ПЕНиРЕСДЗемЕТКСЖНМЗаключениеЗаконЗаконопроектЗональный типовой проектИИБТВИДИКИМИНИнструктивное письмоИнструкцияИнструкция НСАМИнформационно-методическое письмоИнформационно-технический сборникИнформационное письмоИнформацияИОТИРИСОИСО/TRИТНИТОсИТПИТСИЭСНИЭСНиЕР Республика КарелияККарта трудового процессаКарта-нарядКаталогКаталог-справочникККТКОКодексКОТКПОКСИКТКТПММ-МВИМВИМВНМВРМГСНМДМДКМДСМеждународные стандартыМетодикаМетодика НСАММетодические рекомендацииМетодические рекомендации к СПМетодические указанияМетодический документМетодическое пособиеМетодическое руководствоМИМИ БГЕИМИ УЯВИМИГКМММНМОДНМонтажные чертежиМос МУМосМРМосСанПинМППБМРМРДСМРОМРРМРТУМСанПиНМСНМСПМТМУМУ ОТ РММУКМЭКННАС ГАНБ ЖТНВННГЭАНДНДПНиТУНКНормыНормы времениНПНПБНПРМНРНРБНСПНТПНТП АПКНТП ЭППНТПДНТПСНТСНЦКРНЦСОДМОДНОЕРЖОЕРЖкрОЕРЖмОЕРЖмрОЕРЖпОЕРЖрОКОМТРМОНОНДОНКОНТПОПВОПКП АЭСОПНРМСОРДОСГиСППиНОСНОСН-АПКОСПОССПЖОССЦЖОСТОСТ 1ОСТ 2ОСТ 34ОСТ 4ОСТ 5ОСТ ВКСОСТ КЗ СНКОСТ НКЗагОСТ НКЛесОСТ НКМОСТ НКММПОСТ НКППОСТ НКПП и НКВТОСТ НКСМОСТ НКТПОСТ5ОСТНОСЭМЖОТРОТТПП ССФЖТПБПБПРВПБЭ НППБЯПВ НППВКМПВСРПГВУПереченьПиН АЭПисьмоПМГПНАЭПНД ФПНД Ф СБПНД Ф ТПНСТПОПоложениеПорядокПособиеПособие в развитие СНиППособие к ВНТППособие к ВСНПособие к МГСНПособие к МРПособие к РДПособие к РТМПособие к СНПособие к СНиППособие к СППособие к СТОПособие по применению СППостановлениеПОТ РПОЭСНрППБППБ-АСППБ-СППБВППБОППРПРПР РСКПР СМНПравилаПрактическое пособие к СППРБ АСПрейскурантПриказПротоколПСРр Калининградской областиПТБПТЭ |
files.stroyinf.ru
Стан для сварки продольных швов труб большого диаметра конечной длины
Изобретение относится к области трубосварочного производства, а именно к стану для сварки продольных швов труб большого диаметра конечной длины. Стан содержит закрепленные на фундаменте входной и выходной рольганги, тележку с подъемно-поворотными и транспортными роликами, сварочный аппарат, размещенный на балконе, устройство для удаления флюсовой корки и ленточный транспортер с коробом для флюса. Тележка установлена с возможностью перемещения по рельсовому пути. Подъемно-поворотные и транспортные ролики установлены в корпусах. Устройство для удаления флюсовой корки выполнено в виде двух параллельно расположенных вдоль оси движения трубы желобов с отверстиями и двурогого поворотного рычага. Желоба установлены на тележке с возможностью горизонтального перемещения посредством параллелограммных механизмов, кинематически соединенных через тяги и оси с корпусами подъемно-поворотных роликов. На двурогом рычаге закреплены несущий ролик и упругие скребки. Ленточный транспортер с коробом для флюса установлен ниже рельсового пути. Это позволит уменьшить габариты и металлоемкость стана, а также повысить надежность работы оборудования. 2 з.п. ф-лы, 4 ил.
Изобретение относится к области трубосварочного производства, а точнее к стану для сварки продольных швов труб большого диаметра конечной длины.
Известен стан для сварки труб большого диаметра, см. а.с. СССР №457507, кл. В 21 С 37/08, заявл. 24.07.72 г., опубл. 25.01.75 г. Известный стан содержит транспортный рольганг, цепной толкатель, роликовую обойму и сварочную головку, которые смонтированы на единой жесткой раме, установленной с возможностью ее наклона к горизонтальной плоскости.
Недостаток известной конструкции стана заключается в значительной его металлоемкости и стоимости изготовления из-за наличия общей рамы, снабженной механизмами ее регулирования по высоте.
Другим недостатком этого стана является то, что флюсовая корка, образующаяся сверху сварного шва при сварке продольного шва под слоем флюса, не убирается и засоряет механизмы стана, вызывая их поломку, что снижает надежность его работы.
Из известных станов для сварки продольных швов труб наиболее близким по технической сущности является стан для сварки продольных швов труб конечной длины, описанный в а.с. СССР №1013013, кл. В 21 С 37/08, заявл. 23.04.81 г., опубл. 23.04.83 г.
Этот стан содержит закрепленные на фундаменте входной и выходной рольганги, тележку с подъемно-поворотными и транспортными роликами в корпусах, установленную на рельсовом пути и снабженную механизмом наклона ее вместе с расположенным на раме рельсовым путем в горизонтальной плоскости, размещенный на балконе сварочный аппарат и средство дозированной подачи флюса. Механизм наклона рамы выполнен в виде толкателя, шарнирно связанного с рамой, радиусных направляющих, центр кривизны которых находится в точке сварки, и катков, установленных на раме с возможностью взаимодействия с направляющими.
Недостаток известного стана для сварки продольных швов труб заключается в конструктивной сложности, значительных габаритах, металлоемкости и стоимости изготовления.
Другим недостатком является недостаточная надежность из-за выхода из строя отдельных механизмов в связи с попаданием в них флюсовой корки, образующейся при сварке продольного шва под слоем флюса.
Задача настоящего изобретения состоит в создании стана для сварки продольных швов труб большого диаметра конечной длины, имеющего меньшие габариты, металлоемкость и стоимость изготовления и позволяющего повысить надежность работы его оборудования.
Поставленная задача достигается тем, что стан для сварки продольных швов труб большого диаметра конечной длины, содержащий закрепленные на фундаменте входной и выходной рольганги, установленную с возможностью перемещения по рельсовому пути тележку с подъемно-поворотными и транспортными роликами, установленными в корпусах, размещенный на балконе сварочный аппарат со средством дозированной подачи флюса, согласно изобретению снабжен устройством для удаления флюсовой корки, выполненным в виде двух параллельно расположенных вдоль оси движения трубы желобов с отверстиями, установленных на тележке с возможностью горизонтального перемещения посредством параллелограммных механизмов, кинематически соединенных через тяги и оси с корпусами подъемно-поворотных роликов, и расположенного на балконе двурогого поворотного рычага для охватывания трубы по периметру, несущего ролик и упругие скребки, а также ленточным транспортером с коробом для флюса, размещенным ниже рельсового пути. Кроме того, над выходным рольгангом в зоне ленточного транспортера расположена закрытая камера с висящим в ней на опорах рычагом с роликом, форсункой для подачи воздуха и упругими элементами для контактирования с наружной поверхностью трубы. При этом рельсовый путь закреплен на фундаменте с углом наклона к горизонту 20'-40' в направлении движения трубы.
Такое конструктивное выполнение стана для сварки продольных швов труб большого диаметра конечной длины позволит уменьшить его габариты, металлоемкость и стоимость изготовления и повысить надежность работы оборудования.
Это достигается за счет упрощения конструкции и механизированной уборки флюсовой корки и мелких фракций.
Расположение рельсового пути на фундаменте под углом 20'-40' (20' - для труб диаметром 530-820 мм, 40' - для труб диаметром 1020-1420 мм) позволяет производить процесс сварки труб "на спуск", что повышает качество сварного соединения.
При углах больше или меньше 20'-40' процесс сварки труб "на спуск" затруднен, что отрицательно сказывается на качестве сварного соединения.
Для пояснения изобретения ниже приводится конкретный пример выполнения изобретения со ссылкой на прилагаемые чертежи, на которых:
на фиг.1 - изображен стан для сварки продольных швов труб конечной длины;
на фиг.2 - разрез А-А на фиг.1;
на фиг.3 - разрез Б-Б на фиг.1;
на фиг.4 - вид по стрелке В на фиг.1.
Стан для сварки продольных швов труб конечной длины содержит входной 1 и выходной 2 рольганги, закрепленные на фундаменте 3, тележку 4, установленную с возможностью перемещения по рельсовому пути 5, который жестко закреплен на фундаменте с углом наклона к горизонту 20'-40' в направлении движения трубы. Тележка 4 снабжена подъемно-поворотными 6 и транспортными 7 роликами, установленными в корпусах 8, 9 и имеющими приводы подъема, вращения и транспортировки (не показаны). В средней части стана установлен балкон 10, на котором размещены сварочный аппарат 11, контейнер 12 и средство 13 дозированной подачи флюса. Стан снабжен устройством для удаления флюсовой корки, выполненным в виде двух параллельно расположенных вдоль оси движения трубы желобов 14, установленных на тележке с возможностью горизонтального перемещения посредством параллелограммных механизмов 15, и расположенного на балконе 10 двурогого поворотного от цилиндра 16 рычага 17 для схватывания труб по периметру наружной поверхности и несущего ролик 18 и упругие скребки 19.
Желобы 14 выполнены с отверстиями (не показаны) для уборки флюсовой корки.
Параллелограммные механизмы 15 кинематически соединены через тяги 20 и оси 21 с корпусами 8 подъемно-поворотных роликов 6. Ниже рельсового пути 5 размещены ленточный транспортер 22 с коробом 23 для флюса. Над выходным рольгангом 2 в зоне ленточного транспортера 22 расположена закрытая камера 24 с висящим в ней на опорах 25 рычагом 26 с роликом 27, форсункой 28 для подачи воздуха и упругими элементами 29, охватывающими наружную поверхность сваренной трубы по всему периметру.
Стан работает следующим образом.
Трубная заготовка 30 по входному рольгангу 1 поступает на транспортные ролики 7 тележки 4 в положение, при котором передний торец ее останавливается перед электродом сварочного аппарата 11. Затем с подъемно-поворотными роликами 6 трубная заготовка поворачивается до совмещения свариваемых кромок с электродом. До подъема трубной заготовки 30 желоба 14 находились в крайних отведенных положениях относительно оси стана. При подъеме трубной заготовки подъемно-поворотными роликами 6 желоба 14 посредством параллелограммных механизмов 15 приближаются к наружной цилиндрической поверхности заготовки по всей длине. Далее включается сварочный аппарат 11 и средство дозированной подачи флюса, а также привод перемещения тележки 4 по рельсовому пути 5. Производится сварка кромок трубной заготовки в трубу. Угол наклона рельсового пути 5 под углом 20'-40' (20' - для труб диаметром 530-820 мм, 40' - для труб диаметром 1020-1420 мм) к горизонту позволяет производить процесс сварки "на спуск", что повышает качество сварного соединения. Одновременно с началом процесса сварки цилиндром 16 поворачивается в вертикальное положение двурогий рычаг 17, ролик 18 которого при прохождении сварного шва дробит флюсовую корку, которая падает в желоба 14. При дальнейшем движении тележки 4 с трубой упругие скребки 19 сдвигают упавшие флюсовые корки в отверстия желобов 14 и затем на ленточный транспортер 22 и в короб 23.
Далее работа стана происходит по двум вариантам в зависимости от сварки одношовной или двухшовной трубы.
После окончания сварки одношовной трубы последняя транспортными роликами 7 передается на выходной рольганг 2, с помощью которого задается в закрытую камеру 24. Ролик 27, закрепленный на висящем в закрытой камере 24 рычаге 26, окончательно дробит оставшуюся флюсовую корку (шлак), форсунка 28 сдувает более мелкие фракции со шва, а охватывающие наружную поверхность трубы по периметру упругие элементы 29 сдвигают оставшиеся мелкие фракции флюсовой корки.
После окончания сварки первого продольного шва двухшовной трубы последняя подъемно-поворотными роликами 7 поворачивается на 180°, цилиндр 16 поднимает рычаг 17, на приводе тележки 4 меняется направление вращения.
При движении тележки 4 с трубой с помощью сварочного аппарата производится сварка второго продольного шва трубы.
После сварки шва двурогий рычаг 17 опускается цилиндром 16 и при обратном движении тележки 4 с трубой осуществляется удаление флюсовой корки посредством ролика 18 и упругих скребков 19, закрепленных на этом рычаге.
Далее труба поступает в закрытую камеру 24, в которой удаляются остатки флюсовой корки.
Предложенный стан для сварки продольных швов труб большого диаметра конечной длины по сравнению с известными позволит уменьшить металлоемкость, стоимость изготовления и повысить надежность работы оборудования.
1. Стан для сварки продольных швов труб большого диаметра конечной длины, содержащий закрепленные на фундаменте входной и выходной рольганги, установленную с возможностью перемещения по рельсовому пути тележку с подъемно-поворотными и транспортными роликами, установленными в корпусах, размещенный на балконе сварочный аппарат со средством дозированной подачи флюса, отличающийся тем, что он снабжен устройством для удаления флюсовой корки, выполненным в виде двух параллельно расположенных вдоль оси движения трубы желобов с отверстиями, установленных на тележке с возможностью горизонтального перемещения посредством параллелограммных механизмов, кинематически соединенных через тяги и оси с корпусами подъемно-поворотных роликов, и расположенного на балконе двурогого поворотного рычага для охватывания трубы по периметру, несущего ролик и упругие скребки, а также ленточным транспортером с коробом для флюса, размещенными ниже рельсового пути.
2. Стан по п.1, отличающийся тем, что он снабжен расположенной над выходным рольгангом в зоне ленточного транспортера закрытой камерой с висящим в ней на опорах рычагом с роликом, форсункой для подачи воздуха и упругими элементами для контактирования с наружной поверхностью трубы.
3. Стан по п.1, отличающийся тем, что рельсовый путь закреплен на фундаменте с углом наклона к горизонту 20′-40′ в направлении движения трубы.
www.findpatent.ru
Сварка трубы - стык неповоротный при горизонтальном расположении трубы
Рекомендуем приобрести:
Установки для автоматической сварки продольных швов обечаек - в наличии на складе! Высокая производительность, удобство, простота в управлении и надежность в эксплуатации.
Сварочные экраны и защитные шторки - в наличии на складе! Защита от излучения при сварке и резке. Большой выбор. Доставка по всей России!
Сварка этих сварных швов является самым сложным по выполнению и требует особых навыков и высокого мастерства сварщика. Только при твердых навыках в сварке в нижнем положении, вертикальных швов (раздел 3.3) и потолочных швов (раздел 3.4) можно добиться качественной сварки трубы неповоротной в горизонтальном положении. При постоянном поступательном движении электрода необходимо постоянно изменять угол наклона электрода по отношению к поверхности периметра трубы (рис. 68а и 68б, поз. 1-11). Труба делится вертикальной осевой на два участка. По положению сварного шва в пространстве каждый участок можно разбить на три положения:
I-ое - потолочное (поз. электрода с 1 по 3).
II-ое - вертикальное (поз. электрода с 3 по 8).
III-e - нижнее (поз. электрода с 8 по 11).
При сварке труб диаметром более 150 мм и толщиной стенки более 6 мм рекомендуется величину сварочного тока подбирать для каждого положения. Сварочный ток на потолочном положении должен быть на 10% выше, чем на вертикальном положении.
Сварка начинается с потолочного положения и заканчивается на нижнем положении.
При оптимальном подборе сварочного тока для каждого положения реко.мендуется сварку производить непрерывно. Сварка ведется только ко роткой дугой. Сварка любого участка начинается с другого участка на 10 20 мм от вертикальной осевой. Длина «замка» (20-40 мм) зависит от диаметра трубы. Чем больше диаметр, тем больше перехлест в «замке», наоборот. При начале сварки с потолочного положения сварку производить «углом назад» (рис. 68а, поз. 1-2), После перехода за осевую сварку производить «углом вперед» (поз. 3-7). При переходе за горизонтальную осевую электрод выравнивать до перпендикулярного положения (поз. 8), Сварку нижнего положения (верхняя часть трубы) выполнять «углом назад» (поз. 9-11).
Заканчивать первую половинку шва на 10-15 мм за вертикальной осевой на другом участке.
Валик должен быть «нормальным» по всей длине шва, который достигается определенной скоростью поступательного движения электрода, манипулированием и задержкой на кромках, используя все методы и технику сварки потолочных, вертикальных и нижних швов.
Перед сваркой второй половины (второго участка рис. 68б) - при необходимости зачистить (подрубить) начало сварки в потолочном положении и окончание в нижнем положении до плавного перехода к зазору или предыдущему валику. Сварку второго участка выполнить с той же техникой, что и первый участок.
Сварка корневого валика (рис. 70)
Сварка корневого валика выполняется электродом диаметром 3 мм. Величина сварочного тока в потолочном положении в зависимости от толщины стенки 80-95 А. В зависимости от технических условий рекомендуется выполнить корневой валик по двум вариантам.
1-й вариант - при сварке труб малого диаметра, когда невозможна подварка обратной стороны корня шва, а по техническим требованиям необходимо обратное формирование валика, то при сварке корневого валика следует добиться качественного формирования обратного валика. Достичь проплавления, особенно в потолочном положении, можно путем постоянной подачи электрода в зазор. Добиваясь проплава внутрь трубы, формирование валика с наружной стороны может получиться «горбатым», что потребует после заварки 1-го участка зачистки «горбатости» шва в потолочном положении.
При сварке вертикальной зоны сварочный ток рекомендуется уменьшить до 75-90 А. Валик выполнять малого сечения, избегая чрезмерного проплавления внутрь трубы. При сварке верхней части трубы (нижнее положение) увеличение сварочного тока до 85-100 А произвести в каждом конкретном случае, не допуская прожога или непровара.
После заварки второй половины трубы второй валик также выполняется электродом диаметром 3 мм, но на повышенном сварочном токе.
2-й вариант - при сварке труб большого диаметра, где доступна и заложена подварка обратного корня шва, в целях производительности не следует обращать такого тщательного внимания на формирование обратного валика. Рекомендуется корневой валик сформировать «нормальным» во всех положениях и с более полным сечением. Это позволит избежать зачистки по наружному шву и применить при сварке второго валика электрод диаметром 4 мм.
Заполнение разделки (рис. 70)
Здесь необходимо применить все методы и технику сварки заполнения разделки, описанную в предыдущих разделах. Сварку труб диаметром менее 150 мм рекомендуется выполнять электродом диаметром 3 мм.
Заполнение разделки труб толщиной стенки более 8 мм происходит неравномерно. Как обычно, отстает нижнее положение. Для выравнивания заполнения разделки необходимо проложить в каждом конкретном случае дополнительные слои в верхней части трубы. Предпоследний слой выполнить так, чтобы глубина незаполненной разделки была не более 2-х мм.
Сварка лицевого слоя (рис. 71)
В зависимости от ширины разделки лицевой слой выполняется за один или несколько проходов. Техника сварки описана в начале раздела и в предыдущих разделах. Особое внимание обратить на поступательное движение электрода, задержку на кромках и шаг манипулирования.
Сварка труб диаметром менее 150 мм и толщиной стенок менее 6 мм, а также в сложных монтажных условиях при отдаленности источника питания от места сварки, в основном, выполняется при одной величине сварочного тока. Рекомендуется сварочный ток подбирать по потолочному положению, величина которого достаточна и для нижнего положения. Во избежание чрезмерного проплавления на подъеме с потолочного положения и в вертикальном положении сварку необходимо вести прерывистым способом. Дугу прерывать на одной из кромок. В зависимости от толщины стенки, зазора и притупления кромок, рекомендуется выполнять прерывистую сварку «мазками» следующим способом:
Рис. 72а - перегрев кромок не допускает длительной задержки электрода. Зажигание рекомендуется производить постоянно на одной из кромок, обрыв дуги (после соединения кромок металлом шва) на другой кромке. Время между обрывом и новым зажиганием дуги должно быть таким, чтобы в месте начала зажигания дуги металл шва не успел полностью закристаллизоваться, а шлак - остыть. После обрыва дуги, описав как бы полукруг в обратном направлении, снова произвести зажигание чуть выше места предыдущего зажигания. Если проследить за торцом электрода, то получается манипулирование по спирали. Слева направо дуга горит, обрыв вправо и на себя, переход справа налево, дуга не горит, затем слева направо, одновременно приближая электрод к месту зажигания, и, пока шлак еще красный, происходит легкое возбуждение дуги и т.д;
Рис. 72б - когда толщина металла позволяет сделать два и более колебательных движений, затем прервать дугу и возобновить снова.
Нe рекомендуется:
1) зажигание производить на месте, где только что был обрыв дуги;
2) не обрывая до конца дугу, уходить электродом вперед по разделке и затем возвращаться на валик.
Такие методы приводят к большому перегреву и прожогу, к неровности валика по бокам, частому залипанию электрода во время нового зажигания.
Тудвасев В.А. "Рекомендации сварщикам".
См. также:
www.autowelding.ru