способ изготовления сварных тонкостенных конструкций. Сварка тонкостенного металла
Сварка тонкостенных трубчатых деталей
При сварке тонкостенных трубчатых деталей обычно возникает ряд затруднений. Для их сварки можно рекомендовать следующие приемы:
1. Короткие трубчатые детали со сквозными гладкими отверстиями сваривать, предварительно вставив внутрь пробки из твердого материала (рис. 52). Минимального эксцентриситета (при очень тонкостенных трубах) достигают с помощью взаимной центровки этих пробок, например, так, как показано на рис. 53. Для уменьшения износа круглого пальца одной пробки и соответствующего отверстия в другой пробке, последняя может быть снабжена шарикоподшипником.
2. Если по условиям производства внутрь деталей вставлять пробки нельзя, то их заменяют охватывающими кольцами.
3. Машины, предназначенные для сварки труб, снабжают многокулачковыми зажимами, позволяющими охватить трубы почти по всей ее окружности (рис. 54).
В Т-образных соединениях стержень или трубу приваривают впритык к плоской поверхности другой детали.
Основная особенность сварки таких соединений — асимметрия температурного поля. От плоского источника на поверхности трения теплота распространяется фронтально вдоль оси стержня и в направлениях, нормальных к некоторой сферической поверхности в теле другой детали (рис. 55). Это различие в интенсивности теплоотвода по обе стороны от поверхности трения вызывает асимметрию температурного поля. В стержне наблюдаются более высокие температуры, чем в пластине, поэтому в стержне происходит процесс глубинного вырывания частиц металла, тогда как в массивной и менее прогретой пластине имеет место лишь эффект поверхностного полирования.
Для обеспечения высокого качества Т-образных соединений при их сварке трением необходимо торцевать поверхность плоской детали в машине для сварки трением, после чего (не переставляя ее в зажиме) проводить сварку; искусственно сводить сварку асимметричного Т-образного соединения к сварке симметричного соединения. Для этого либо на детали с плоской поверхностью заранее протачивают выступ (рис. 56) диаметром, равным диаметру привариваемого стержня, и высотой 3—6 мм для сталей и несколько более для пластичных металлов, либо на торцовой поверхности массивной детали заранее протачивают кольцевую канавку (рис. 56, б) для сварки этой детали со стержнем. Для соединения с трубой плоскую деталь подготовляют, как показано на рис. 56, в. Надежное соединение трубы с фланцем рекомендуется выполнять также по схеме, представленной на рис. 56, в.
Для сварки трением необходимо специальное оборудование, которое должно быть рассчитано на работу при достаточно больших скоростях вращения и осевых усилиях, свойственных сварке трением, должно позволять быстрый запуск и мгновенную остановку шпинделя машины, обладать достаточной прочностью для восприятия и гашения значительных радиальных вибраций, возникающих в процессе сварки, и удовлетворять ряду других требований.
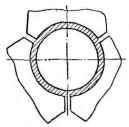
Рис.54. Зажимы, охватывающие трубу снаружи
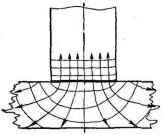
Рис.55. Температурное поле в Т-образном соединении
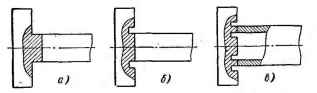
Рис. 56. Подготовка плоской детали перед сваркой Т-образного соединения пластины со стержнем (а и б) и с трубой (в)
Этим требованиям не отвечают обычные металлорежущие (токарные, фрезерные, сверлильные) станки, применение которых для сварки трением даже после соответствующей реконструкции может быть допущено лишь в виде исключения и только при выполнении неответственных работ.
Современные машины для сварки трением достаточно сложны, состоят из большого числа следующих элементов и узлов (рис. 57): два зажима 5 и 7 для подлежащих сварке деталей 6; передняя бабка 4 со шпинделем, несущим на себе вращающийся зажим 5; узел 8, в котором размещен невращающийся зажим 7; привод вращения шпинделя с электродвигателем 1, ременной передачей 2 и устройством для натяжения ремней; фрикционная муфта 3 для сцепления шпинделя с приводным устройством, а также для торможения шпинделя, пневматические или гидравлические цилиндры 9, обеспечивающие создание необходимого рабочего (осевого) усилия машины; пневматическая, пневмогидравлическая или гидравлическая схема управления силовым приводом машины; электрическая схема управления машиной; станина машины, шкаф управления.
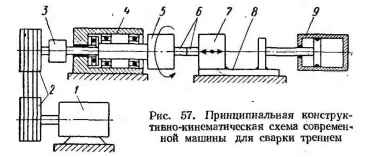
Рис.57.Принципиальная конструктивно-кинетическая схема современной машины для сварки трением
www.prosvarky.ru
Ручная сварка тонколистовой стали
Наименьшая толщина листовой стали, при которой можно с известным успехом применять дуговую электросварку металлическим электродом, равна 1,5 мм. Сварка листов толщиной 3 мм не представляет затруднений и выполняется распространенными электродами с покрытием типа ОММ-5, ЦМ-7, УОНИ-13/45 и другими.
Для сварки тонких листов лучше применять постоянный ток при обратной полярности (минус на детали).
Сварка тонких листов производится электродами диаметром 2—3 мм. Слой покрытия должен быть тонким и содержать элементы, способствующие устойчивому горению дуги, так как сварка ведется на малых токах (20—60 а).
Сварка на переменном токе возможна с применением осцилляторов или специальных трансформаторов с повышенным до 80 в напряжением холостого хода.
Таблица 52.Режимы сварки тонколистовой малоуглеродистой стали
| Сварка в стык | Сварка внахлестку и в тавр | ||
Толщина в мм | d электрода в мм | сила тока в а | d электрода в мм | сила тока в а |
1,5 | 2 | 30— 50 | 2,5 | 40—75 |
2,0 | 2,5 | 45— 70 | 2,8—3,0 | 50—85 |
3,0 | 3,0 | 70—100 | 3,0—4,0 | 80—135 |
4,0 | 3,0—4,0 | 90—130 | 4,0 | 100—150 |
5 | 4,0 | 115—160 | 4—5 | 150—190 |
В табл. 52 даны режимы сварки тонких листов из малоуглеродистой стали.
Сварка тонких листов производится с периодическими замыканиями дуги через расплавленные капли, переходящие с электрода. Основной металл при этом расплавляется на всю толщину и с нижней стороны шва получается небольшой протек. Рекомендуется при сварке стыковых швов применять различного рода теплоотводящие и удерживающие подкладки. Они значительно улучшают качество сварки.
Сварочные посты, предназначенные для сварки тонкостенных изделий, оборудуются электрододержателем с гибким проводом небольшого сечения, облегчающим свободу манипулирования электродом, что очень важно при сварке тонкого материала.
www.prosvarky.ru
Стыковая сварка оплавлением тонкостенных деталей на постоянном токе
Характерной особенностью сварки оплавлением тонкостенных деталей является то, что зона пластического деформирования ограничена устойчивостью стенки детали при осадке. При этом чтобы обеспечить деформацию небольшой приторцовой зоны, используются узкие температурные поля с высоким градиентом. Ввиду малой величины осадки при сварке тонкостенных деталей очень большое значение имеет состояние оплавленных торцов перед ее началом. Они должны быть покрыты сплошной пленкой расплавленного металла и иметь по возможности лучший макрорельеф. Чтобы сохранить жидкую пленку на торце при высоком градиенте температуры, при сварке тонкостенных деталей требуются большие скорости оплавления и осадки [1]. Чтобы получить соединение с высокими свойствами, необходимо при осадке выдавить из зоны соединения расплавленный металл и окислы. Чем ровнее оплавленные поверхности, тем для этого требуется меньшая величина осадки.
Размер лунок - кратеров определяется размером перемычек жидкого металла между торцами. Чем больше перемычки, тем хуже макрорельеф оплавленного торца. Величина перемычек зависит от многих факторов, в частности, от природы свариваемого металла, параметров процесса, характеристик сварочной машины и геометрии сечения детали [1, 2]. Процесс образования и разрушения перемычек сопровождается характерным импульсным изменением сварочного тока. При этом увеличению размера перемычек соответствует увеличение амплитуды и длительности импульсов тока. Поэтому осциллографирование тока позволяет косвенно изучить влияние различных параметров на размер перемычек. В настоящей работе при осциллографировании использовали шинный трансформатор тока, включенный во вторичную цепь сварочного трансформатора. Оплавляли пластинки из стали ВНС-2 сечением 0,8×30,0 мм. Запись осуществляли на светолучевом осциллографе Н-105 с масштабом тока 500 А/см, напряжения 3,3 в/см, перемещения 0,04 мм/имп.
Изучение осциллограмм (рис. 1, а) выявило характерную особенность процесса оплавления на переменном токе. Периодически на кривой тока наблюдаются импульсы с повышенной амплитудой и длительностью. Это свидетельствует об увеличенном размере перемычки. Ускоренная киносъемка, синхронная с осциллографированием, показала, что увеличенному импульсу тока соответствует взрыв преимущественно одной перемычки. На рис. 2, а показана схема киносъемки. Оплавляли пластины из стали ВНС-2 сечением 0,8×20,0 мм. Изображение стыка размещено во всю ширину кадра. Частота съемки равна 4000 кадр/сек. На рис. 2, б показан участок осциллограммы процесса, а на рис. 2, в, г кадры, снятые при разрушении перемычек, в момент импульсов тока 1 и 2. Таким образом, увеличенные импульсы тока связаны с образованием крупных перемычек. Такие перемычки образуются, если элементарный контакт возникает при небольшом уменьшающемся мгновенном значении напряжения. Он продолжает существовать и при нулевом значении тока.
Рис. 1. Осциллограммы сварочного напряжения и тока:
а — при оплавлении на переменном токе; б — то же, на постоянном токе
Рис. 2. Ускоренная киносъемка процесса оплавления:
а — схема съемки; б — синхронная осциллограмма процесса; в — взрыв перемычки, соответствующий импульсу 1 тока; г — то же, соответствующий импульсу 2 тока
Ввиду сближения деталей размер контакта непрерывно увеличивается. После перехода сварочного напряжения через нуль ток в контакте резко возрастает и интенсивное тепловыделение приводит к разрушению перемычки, обычно при мгновенном значении напряжения, близком к амплитудному. Таким образом, процесс оплавления как бы синхронизируется частотой питающего напряжения. Это наиболее явно выражено, когда время существования перемычки меньше полупериода переменного напряжения.
Явление синхронизации усиливается при увеличении скорости оплавления и уменьшении вторичного напряжения. Ввиду большого значения, которое имеет макрорельеф при сварке тонкостенных деталей, необходимо в этом случае исключить образование крупных перемычек. С этой целью изучили возможность использования для сварки источника постоянного тока.
В качестве такого источника использовали трехфазный сварочный трансформатор с выпрямлением тока во вторичной цепи по схеме Ларионова (рис. 3). При осциллографировании тока использованы три шинных трансформатора тока ТТ1, ТТ2, ТТ3 и трехфазный выпрямитель В2. Осциллограмма процесса оплавления пластин из стали ВНС-2 (сечением 0,8×30,0 мм) на постоянном токе показана на рис. 1, б. Масштабы записи тока и напряжения при оплавлении на постоянном и переменном токе одинаковы. Амплитуда напряжения в первом случае выбрана такая же, как и во втором. При оплавлении на постоянном токе амплитуда и длительность импульсов тока меньше, чем при оплавлении на переменном токе, а их частота больше. На переменном токе его амплитуда превышает 2500 А, а на постоянном токе она меньше 1500 А. Длительность существования элементарного контакта в первом случае достигает 6 мсек, а во втором не превышает 2 мсек.
Рис. 3. Схема источника постоянного тока и измерения тока оплавления
Об уменьшении перемычек и улучшении макрорельефа при постоянном токе свидетельствует и непосредственное измерение рельефа оплавленных торцов. При оплавлении на переменном токе пластин из никеля толщиной 1,0 мм глубина отдельных кратеров достигала 0,3 мм относительно средней линии профиля (рис. 4, а), а на постоянном токе она не превосходила 0,15 мм (рис. 4, б). Пластины оплавляли на 6 мм при линейном увеличении скорости их сближения до 5 мм/сек. При этом следует учитывать, что эффект от использования постоянного тока был несколько снижен вследствие того, что активное сопротивление источника постоянного тока было выше сопротивления источника переменного тока.
Рис. 4. Макрорельеф торцовой поверхности пластин, оплавленных на переменном (а) и постоянном (б) токе
При оплавлении на постоянном токе значительно уменьшается вероятность коротких замыканий. Так, максимальная начальная скорость оплавления пластинок из стали ВНС-2 сечением 0,8×300 мм, при которой еще может возбудиться процесс на переменном токе, меньше 2 мм/сек, а на постоянном токе она достигает 6 мм/сек. Повышение устойчивости процесса оплавления на постоянном токе позволит снизить вторичное напряжение, что, как известно [1, 2, 3], способствует поддержанию слоя расплавленного металла на торцах.
Использование постоянного тока при оплавлении тонкостенных деталей приводит к некоторому повышению механических свойств соединений, в первую очередь угла загиба (см. таблицу). Сваривали образцы из стали ВНС-2 толщиной 1 мм с защитой аргоном при одинаковых параметрах режима мм, мм/сек, мм.
Место вырезки образца | Угол изгиба , град (ч=1 мм) |
Основной материал ВНС-2 (отжиг+нормализация) | 140…155 |
Сварное соединение (переменный ток) | 95…125 |
Сварное соединение (постоянный ток) | 120…142 |
Выводы
1. При оплавлении тонкостенных деталей на переменном токе промышленной частоты наблюдается периодическое образование перемычек увеличенного размера, что ухудшает макрорельеф оплавленной поверхности и повышает вероятность короткого замыкания сварочной цепи при увеличении скорости сближения деталей и снижении вторичного напряжения.
2. Использование постоянного тока при оплавлении таких деталей снижает вероятность коротких замыканий и улучшает макрорельеф оплавленных поверхностей. Повышение устойчивости процесса оплавления на постоянном токе позволит снизить вторичное напряжение, что благоприятствует образованию жидкой пленки на торцах деталей.
Литература
1. Гельман А.С. Технология и оборудование контактной электросварки. Машгиз, 1960.
2. Кучук-Яценко С.И. и Лебедев В.К. Контактная стыковая сварка непрерывным оплавлением. «Наукова думка», 1965.
3. Яворский Ю.Д. Влияние режима сварки на макрорельеф оплавленных поверхностей. «Автоматическая сварка», 1964, № 11.
Источник: журнал «Сварочное производство» № 9, 1969г.
k-svarka.com
способ изготовления сварных тонкостенных конструкций - патент РФ 2016726


ФОРМУЛА ИЗОБРЕТЕНИЯ
СПОСОБ ИЗГОТОВЛЕНИЯ СВАРНЫХ ТОНКОСТЕННЫХ КОНСТРУКЦИЙ, преимущественно сильфонов, включающий сварку плавлением конструкции из заготовок и последующее деформирование до получения требуемой конфигурации, отличающийся тем, что, с целью повышения деформационной способности сварного соединения, перед операцией деформирования осуществляют местное покрытие сварного соединения слоем металла толщиной 10 - 15% от толщины материала свариваемой конструкции.www.freepatent.ru
Сварка - тонкостенная труба - Большая Энциклопедия Нефти и Газа, статья, страница 2
Сварка - тонкостенная труба
Cтраница 2
Еще меньшее влияние оказывает величина вторичного напряжения холостого хода, если скорость оплавления сохраняется неизменной. При сварке тонкостенных труб изменение вторичного напряжения на 50 % по сравнению с некоторым средним значением совсем не отражается на показателях ударной вязкости. Скорость оплавления весьма заметно сказывается на показателях ударной вязкости. Для каждого свариваемого изделия существует некоторая наилучшая скорость оплавления. Она определяется в зависимости от вторичного напряжения и наклона внешней характеристики. [16]
При дуге постоянного тока большее количество тепла выделяется на положительном полюсе, поэтому к нему подключается свариваемый газопровод, а электрод подключается к отрицательному полюсу. При сварке тонкостенных труб газопровод подключают к отрицательному, а электрод - к положительному полюсу источника тока. [18]
При дуге постоянного тока большее количество теплоты выделяется па положительном полюсе, поэтому к нему подключается свариваемый газопровод, а электрод подключается к отрицательному полюсу. При сварке тонкостенных труб газопровод подключают к отрицательному, а электрод - к положительному полюсу источника тока. [19]
Электродуговая сварка с поддувом защитных газов при давлении, не превышающем давление газа в горелке ( порядка 100 - 150 мм вод. ст.), применяется для получения с внутренней стороны плотного, хорошо сформированного валика, что обеспечивает полное проплавле-ние по всей толщине стенки трубы. Это особенно важно при сварке тонкостенных труб. [20]
Электроды, зажимы и система привода должны гарантировать строгую соосность свариваемых деталей. В связи с этим, например, при сварке тонкостенных труб допустимая величина смещения не должна превышать 5 - 8 % от толщины стенки. [21]
При ручной газовой сварке происходит частичное выгорание ряда входящих в сталь компонентов, что несколько снижает качество металла в месте сварного шва. Поэтому данный вид сварки применяют в настоящее время только для сварки тонкостенных труб мелких диаметров, электродуговая сварка которых затруднительна. [22]
Наибольшее распространение получили способы сварки электрической дуговой ( ручной, полуавтоматической и автоматической под флюсом и в защитных газах), а также контактной сварки. Меньше применяется ручная газовая сварка, используемая преимущественно при ремонтных работах, сварке тонкостенных труб, цветных металлов и чугуна. [23]
Возникают из-за неправильной сборки деталей под сварку ( недостаточного притупления кромок, большого зазора), большой силы сварочного тока при невысоких скоростях сварки. Наиболее часто прожоги образуются при сварке тонкостенных труб и при выполнении первого прохода многослойного шва. [24]
Возникают из-за неправильной сборки деталей под сварку ( недостаточного притупления кромок, большого зазора), большой силы сварочного тока при невысоких скоростях сварки. Наиболее часто прологи образуются при сварке тонкостенных труб и при выполнении первого прохода многослойного шва. [25]
Круглые детали ( прутки и трубы) могут свариваться в призматических ( фиг. Первый тип у побей при сварке мелких партий деталей изменяющегося диаметра, так как допускает сварку в одних и тех же электродах деталей разного диаметра. Сварка тонкостенных труб без упоров может проводиться только в цилиндрических электродах, так как в призматических электродах трубы деформируются под действием значительных усилий зажатия. Для уменьшения износа электродов сварку уголков и штампованных профилей желательно проводить в фасонных электродах ( фиг. [26]
Технологический процесс [4] производства сварных прямошов-ных труб обычно состоит из следующих основных операций. Отформованные заготовки труб поступают к сварочным станам. Для сварки продольных швов электросварных труб применяют автоматическую сварку под флюсом, электроконтактную сварку оплавлением и сопротивлением. Для сварки тонкостенных труб, кроме того, используют прессовую сварку с индукционным нагревом токами радиочастоты. [27]
Сварка непрерывным оплавлением выполняется в такой последовательности. Детали, закрепленные в зажимах машины, плавным перемещением подвижного зажима приводят в соприкосновение при включенном сварочном токе. При этом происходит оплавление свариваемых торцов. Затем производят осадку на установленную величину и выключение тока. Такой способ применяют при сварке тонкостенных труб, листов, рельсов и др. Допускается сварка разнородных металлов. Достоинством сварки непрерывным оплавлением является высокая производительность, недостатком - значительные потери металла на угар и разбрызгивание. [28]
Дуговая сварка может осуществляться на постоянном и переменном токе. При дуге постоянного тока большее количество тепла выделяется на положительном полюсе. Поэтому к нему подключается свариваемый газопровод, требующий большего количества тепла на оплавление кромок, а электрод подключается к отрицательному полюсу. Таким подключением обеспечивается так называемая прямая полярность. Однако в отдельных случаях, например при сварке тонкостенных труб во избежание их перегрева, применяют обратную полярность, при которой газопровод подключают к отрицательному, а электрод - к положительному полюсу источника тока. [29]
При газовой резке труб и металла часто может оказаться целесообразным использовать керосин вместо ацетилена и карбида. Для этой цели применяется керосинорез К-51. Электросварочные трансформаторы и генераторы применяются для электродуговой сварки при монтаже внутренних трубопроводов, особенно если они прокладываются из труб больших диаметров. Ручная электродуговая сварка производится постоянным или переменным током. Она создает устойчивую дугу, обеспечивая высокое качество сварки и более применима для сварки тонкостенных труб. Для сварки переменным током применяют сварочный аппарат, в состав которого входят трансформатор и регулятор. Сварочный трансформатор питается от сети переменного тока напряжением 220, 380 или 500 в. После трансформатора указанное напряжение снижается до 55 - 65 в. Из трансформатора электрический ток проходит через сварочный регулятор, который регулирует силу сварочного тока и улучшает устойчивость электрической дуги. [30]
Страницы: 1 2
www.ngpedia.ru
Сварочным полуавтоматом можно варить только тонкостенный металл или не только?
Любой толщины. Толстые изделия просто нужно прогревать докрасна паяльной лампой. Бери инвертор и не парься! А аргон - это совсем другое дело! Полуавтомат ведь стальную проволоку плавит и заполняет ее расплавом швы, а чтоб не окислялось - все это под углекислотой происходит.. . А аргон используется потому что алюминий при окислении и у углекислого газа кислород отбирает! Для варки активных металлов нужна атмосфера из инертных газов, которые не дадут кислороду атмосферы или других вещесть (воды, например) реагировать с этим металлом.. . Иначе получится лужа оксида, которая нифига не держит...
только тонкостенный, потомучто толстый не прогреет и полностью непроварит.
Для дома обычный с электродами постоянного тока, для авто полуавтомат)) . Под аргон вообще другой аппарат)).
Тут смотря что вы будете им варить, полуавтомат предназначен для сварки тонкого метала, хорошо используется при сварки автомобилей. Обычным автоматом автомобиль не поваришь, но и качество сварки больше у полуавтомата. Алюминий и медь на сколько я помню ни полуавтоматом ни обычным сварочным не поваришь. А аргон используется при сварки алюминия так как в другой среде его не поваришь.
Любой (в пределах разумного) -зависит от характеристик аппарата Сварка алюминия более напоминает пайку-электрод вольфрамовый (неплавкий) медь варится медью, а контактный наконечник полуавтомата-медный. Т. е проволока просто не пойдет, а приварится.. В остальном варится простым аппаратом с медным электродом.. соединение ненадежно- металл "кипит"...
Ответ на твой комментарий; В какой то степени академиком, по твоему взял держак в руки, тыкнул электродом и все нормально? Если ты не имеешь даже никакого понятия что и с чем сваривается и какой сваркой, то ты в этом деле профан, ты далек от этого я не говорю что я классный сварщик, я варю и электро и газо сваркой не первый год, у меня есть и то и другое, но я слобак в этом деле по сравнению с профи. Если тебе нужно только электродом тыкать, то купи самую дешевую китайскую и тыкай на здоровье. А через годик другой при постоянной тренировке купишь агрегат посерьезней. А словами" Наверное электродом тыкать ума дохуя надо, академиком быть нужно"ты обижаешь многих профи в этом деле!
dlea avto mojna poluavtomat on varit do 4 mm esli u nego transformator i travers serioznii ih ishio mojna peredelati oni variat ishio na argone tak 4to horoshaia veshi recomenduiu
touch.otvet.mail.ru