Металлургические процессы при дуговой сварке плавлением. Температура плавления при сварке металла
Температура плавления металла при сварке
пер.Каштановый 8/14 51100 пгт.Магдалиновка
Nikolaenko Dmitrij
Температура плавления металла при сварке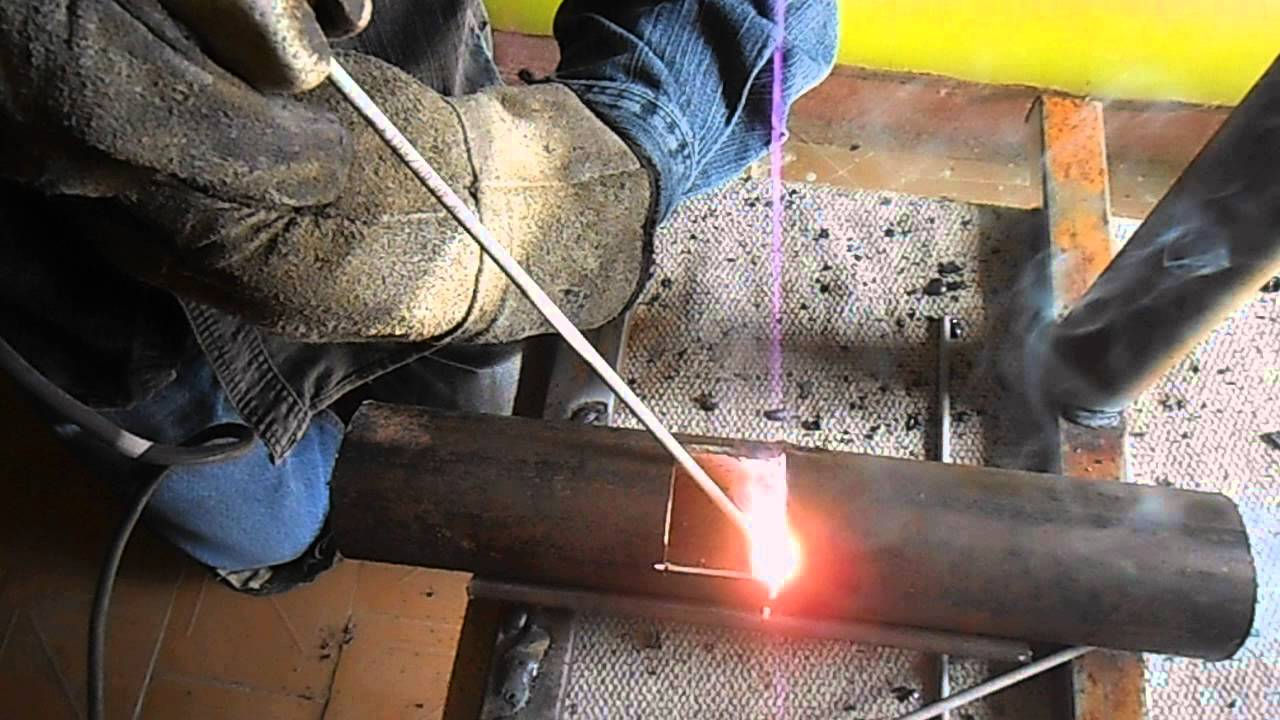
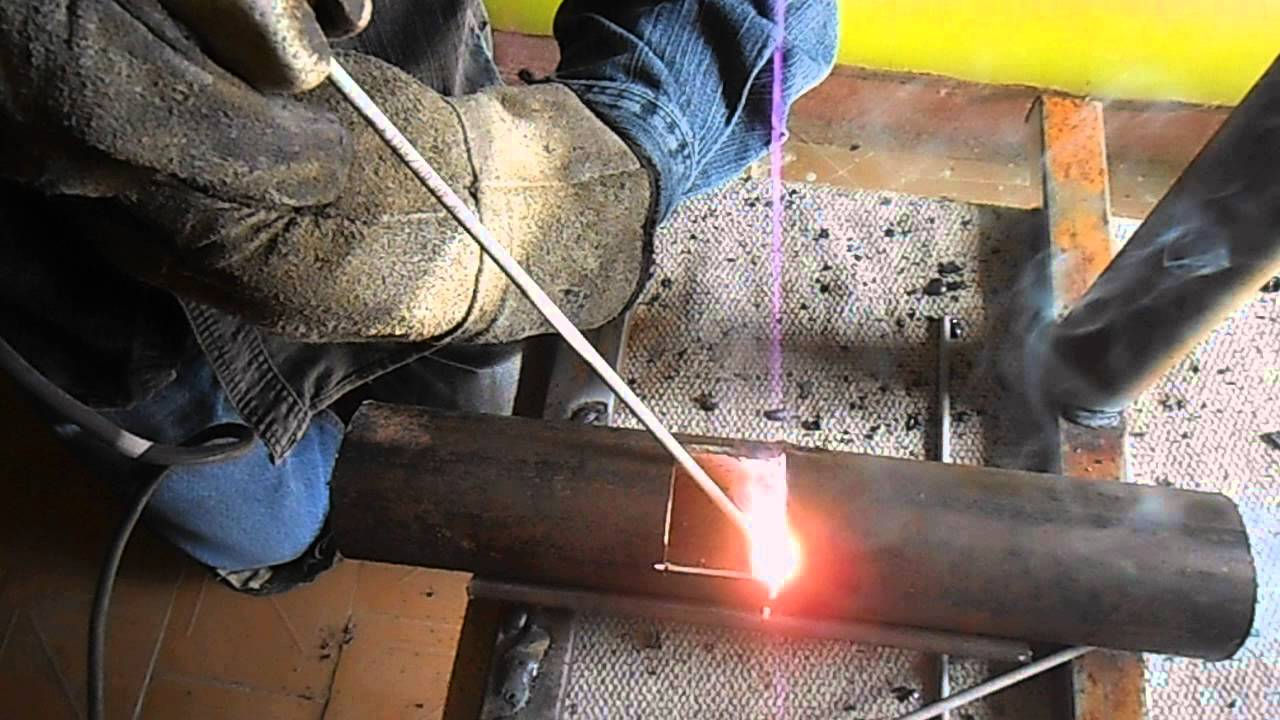
- Газовая сварка. Используемый горючий газ — ацетилен, кислород. Каждый из газов способен нагреть и расплавить любой металл. Температура плавления металла при сварке достигает 30000С. Для такой сварки необходим кислород, горючий газ ацетилен, рукава подачи газов из баллона, газовая горелка, в которой образуется горючая смесь. Место сваривания нагревают, доводя до расплавленного состояния, потом подводят присадочный материал, сливающийся с основным металлом и образующий шов.
- Дуговая сварка. Источником энергии при этой сварке служит электрический дуговой разряд, который появляется при соприкосновении свариваемых деталей к одному полюсу источника тока, а электрода к другому полюсу. При этом, движение совершает электрод с дуговым разрядом, необходимо использовать присадочный материал для образования прочного соединения.
- Аргонодуговая сварка. Прогрессивная сварка для цветных металлов. Применяют плавящийся электрод-проволоку, который подходит по составу со свариваемым металлом или используют неплавящийся вольфрамовый электрод, его в основном применяют для ответственных конструкций, а сбоку подают присадочный металл. Особенно хорошо использовать этот вид сварки для титана и его сплавов.
Температура плавления при сварке титана 16680 С, а аргонодуговой сварки 20000 С. Дело в том, что титан при температуре 5000С начинает активно реагировать с окружающей средой, и он начинает окисляться, а при такой сварке аргон исполняет роль защиты от атмосферы и титан не реагирует на нее. Плавление сплава происходит равномерно, и шов получается ровный и чистый. Это только некоторые виды сварки плавлением. Существуют средства, которые содействуют плавлению, метала — это флюсы, роль которых растворять окислы при повышенных температурах и способствовать равному шву. Также имеются еще такие средства как шлаки, защитные газы, которые вдуваются в зону сварки.
Опубликовано/отредактировано: 2018-02-18
metallsmaster.ru
Нагрев и плавление металла при сварке — КиберПедия
Эффективность использования теплоты, выделяемой источником нагрева, характеризуется э ф ф е к т и в н о й т е п л о в о й м о щ н о с т ь ю – количеством теплоты, введенным в изделие в процессе его нагрева за единицу времени qи. Отношение qи к скорости сварки vсв характеризует количество теплоты, вводимое на единицу длины шва, и называется п о г о н н о й э н е р г и е й сварки. Для обозначения погонной энергии сварки часто используют символ .
Рассмотрим ряд сварочных T- процессов.
В ходе дуговой сварки подводимая к сварочной дуге энергия источника питания расходуется на нагрев электрода и основного металла, а также отдается окружающей среде путем конвективной и радиационной теплоотдачи, светового излучения, звуковых колебаний, вместе с брызгами электродного металла и т.д. (рис.2.17).
Рис. 2.17. Тепловой баланс ручной дуговой сварки покрытыми электродами |
При дуговой сварке qи связана со сварочным током Iсв, напряжением дуги Uд и эффективным коэффициентом полезного действия (КПД) нагрева металла сварочной дугой hи соотношением .
Коэффициент hи уменьшается с увеличением длины дуги и повышается с увеличением скорости сварки и углублением дуги в сварочную ванну и имеет различные значения в зависимости от способа сварки (табл.2.4).
Таблица 2.4
Значения hи для различных сварочных дуг
Способ сварки | hи |
Покрытыми электродами | 0,70 – 0.85 |
Под флюсом | 0,80 – 0,95 |
В углекислом газе | 0,58 – 0,72 |
В аргоне неплавящимся электродом | 0,60 – 0,80 |
В аргоне плавящимся электродом | |
Плазменная с аргоном в качестве плазмообразующего газа | 0,3 – 0,75 |
Для дуг, мало погруженных в металл, , а для сильно погруженных – , где DUст – часть падения напряжения в столбе дуги. Однако при сварке на постоянном токе эффективность нагрева изделия зависит также от полярности. В дугах при плавящемся электроде большее количество тепла выделяется на катоде, а в дугах при неплавящемся электроде, как правило, – на аноде. Поэтому сварку неплавящимся (вольфрамовым) электродом наиболее часто ведут на прямой полярности.
Наплавочные работы, выполняемые плавящимся электродом, с целью повышения производительности ведут на прямой полярности, а сварочные работы, требующие глубокого проплавления изделия, – на обратной полярности.
В дуге переменного тока расположение анодных и катодных областей на электроде и изделии чередуется с частотой питающей сети. По этой причине интенсивность тепловыделения на электроде и изделии в дуге переменного тока занимает промежуточное положение по отношению к дугам постоянного тока прямой и обратной полярности.
При электронно-лучевой сварке энергия электронного луча затрачивается на нагрев изделия, а также на испарение металла и отражение излучения в окружающую среду, на вторичную термоэлектронную эмиссию электронов и электромагнитное излучение.
Эффективный КПД нагрева зависит от атомного номера свариваемого металла и составляет 70 – 90 %.
Для лазерной сварки применяют импульсные и непрерывно действующие лазеры.
В лазерах до 94 % энергии теряется в системе накачки. Около 3 % энергетических потерь приходится на оптическую систему и ~1 % – на испарение металла и отражение лазерного излучения от изделия.
Эффективный КПД нагрева во многом зависит от степени заглубления лазерного луча в металл и может лежать в пределах от ~6 % (сварка алюминия) или ~10 % (сварка стали) до ~90 % (сварка стальных или алюминиевых конструкций).
Распространение теплоты в изделии осуществляется теплопроводностью, а в сварочной ванне – конвективным теплообменом и теплопроводностью.
Распределение температуры в изделии в конкретный момент времени представляет собой т е м п е р а т у р н о е п о л е.
Температурное поле в изделии при сварке обычно анализируют в системе пространственных координат, перемещающихся с источником нагрева.
Процесс распространения теплоты в изделии при сварке разделяют на три стадии:
– теплонасыщение, когда в температурном поле, перемещаемом вместе с источником тепла, температура нарастает;
– предельное квазистационарное состояние, когда подвижное температурное поле практически устанавливается;
– выравнивание температуры после окончания сварки.
Если тепловые процессы анализировать путем наблюдения за температурой в некоторой точке изделия, то изменение температуры в данной точке при сварке называют т е р м и ч е с к и м ц и к л о м.
При однопроходной сварке (наплавке) термический цикл простой (рис.2.18, а). Такой цикл характеризуется максимальной температурой Tmax, скоростью нагрева и скоростью охлаждения, а также длительностью tп пребывания материала при температуре выше заданной температуры Tз.
При многопроходной сварке термический цикл сложный. Например, при трехпроходной сварке без расхолаживания изделия после каждого прохода максимум температуры в рассматриваемой точке достигается несколько раз (рис.2.18, б).
а | б |
Рис. 2.18. Простой (а) и сложный (б) сварочные термические циклы
Температурное поле в каждый момент времени часто представляют в виде совокупности и з о т е р м – линий на поверхности или в сечении тела, соединяющих точки с одинаковой температурой (рис.2.19).
Рис. 2.19. Изотермы температурного поля на поверхности изделия
из стали 12Х18Н10Т толщиной 3 мм, свариваемого аргонодуговой сваркой
неплавящимся (вольфрамовым) электродом диаметром 5 мм;
Iсв = 470 А, lд = 2,5 мм (Uд = 11 В), Vсв = 90 м/ч
Изотерма температуры солидуса определяет собой профиль сварочной ванны, например, на рис.2.19 это 1403 оС.
Сварочная ванна при дуговой сваркехарактеризуется длиной L и шириной e, практически равной ш и р и н е ш в а (рис.2.20). Глубина сварочной ванны, отсчитываемая от поверхности основного металла, определяет г л у б и н у п р о п л а в л е н и я H. Выступающая над поверхностью основного металла часть сварного шва высотой g называется у с и л е н и е м ш в а.
Рассмотрим характеристики сварного соединения в поперечном сечении (рис. 2.20).
Площадь основного металла Fпр, переплавленного при сварке, называется п л о щ а д ь ю п р о п л а в л е н и я. Форму зоны проплавления оценивают коэффициентом формы провара , а также коэффициентом полноты проплавления . Для Т-процессов в зависимости от способа сварки (наплавки) mпр изменяется от 0,05 до 20.
Площадь сварного шва Fн, образованная путем расплавления электродного металла, называется п л о щ а д ь ю н а п л а в к и. Очертания зоны наплавки характеризуются коэфициентом формы валика и коэфициентом полноты валика . Для плоского шва (не имеющего усиления) . Для швов стандартных соединений, выполненных луговой сваркой, .
Объем сварочной ванны в зависимости от способа и режима сварки плавлением составляет от 0,1 до 10 мл.
Максимальное время пребывания металла в сварочной ванне для разных случаев составляет до 30 – 40 с.
Сварочная ванна нагревается неоднородно. Г о л о в н а я ч а с т ь сварочной ванны (abc – на рис.2.20) перегрета, в ней идет плавление основного и электродного металла. Х в о с т о в а я ч а с т ь сварочной ванны (cda) более холодная. В хвостовой части ванны идет охлаждение расплава и его кристаллизация.
Средняя температура металла Tср в сварочной ванне определяется источником нагрева, теплофизическими свойствами свариваемого материала и параметрами теплоотвода с наружной и внутренней поверхностей ванны. Например, при дуговой сварке низкоуглеродистых и низколегированных сталей оС.
Сварочная ванна образуется смешением расплавленных основного и электродного металла.
Доля основного металла в шве . Доля электродного металла составляет 1–q.
Давление столба сварочной дуги,возникающее вследствие давления газов, электродинамических усилий и упругих ударов заряженных частиц о поверхность металла, оттесняет жидкий металл от основания дуги (см. рис.2.20).
Величина прослойки жидкого металла под сварочной дугой во многом определяет глубину проплавления H (см. рис.2.20, сечение А – А). Это обусловлено тем, что жидкий металл, обладая меньшей теплопроводностью, чем твердый, затрудняет процесс распространения теплоты источника нагрева в глубину изделия.
Чем больше давление дуги, оказываемое на поверхность расплавленного металла, тем больше глубина погружения дуги в его толщу, меньше прослойка жидкого металла под сварочной дугой и больше H. Давление дуги растет с увеличением силы и плотности сварочного тока.
Плавление электрода происходит в основном за счет тепловой энергии дуги. Скорость плавления зависит от состава сварочной проволоки, покрытия, флюса, защитного газа, плотности и полярности тока и других параметров режима сварки.
Технологические характеристики плавления электрода определяются экспериментально и используются для оценки производительности процесса сварки. К таким характеристикам в первую очередь относят производительность расплавления и производительность наплавки.
Производительность наплавки оценивается количеством металла с плотностью r, наплавленного на изделие в единицу времени: . Количество наплавленного электродного металла всегда меньше, чем расплавленного, на величину коэффициента потерь на угар и разбрызгивание kп (под угаром понимаются потери металла на испарение и окисление). По этой причине производительность расплавления .
Вклад разбрызгивания в величину kп зависит от типа переноса электродного металла через дуговой промежуток.
Удельные производительности расплавления и наплавки оцениваются коэффициентами расплавления и наплавки , причем . Для ряда способов дуговой сварки коэффициенты aр и kп приведены в табл.2.5.
Перенос электродного металла через дуговой промежуток осуществляется, как правило, каплями. Различают крупнокапельный с замыканиями дугового промежутка, мелкокапельный и струйный перенос металла.
Таблица 2.5
Характеристики процесса плавления электрода
Способ дуговой сварки | aр, г/(А×ч) | kп |
Покрытыми электродами | 8 – 14 | 0,05 – 0,3(с учетом огарков) |
В углекислом газе | 15 – 25 | 0,05 – 0,14 |
Под флюсом | 14 – 23 | 0,01 – 0,02 |
Мелкокапельный перенос может осуществляться с замыканиями дугового промежутка и без замыканий (рис.2.21, а).
С т р у й н ы й п е р е н о с представляет собой поток быстро следующих друг за другом капель электродного металла, производящий внешнее впечатление струи расплавленного металла (рис.2.21, б).
а | б |
Характер переноса электродного металла зависит от соотношения сил, действующих на каплю при ее образовании и перемещении через дуговой промежуток. Основные из них: сила тяжести, сила поверхностного натяжения, электромагнитная сила, электростатическая сила, электродинамическая сила, сила реактивного давления паров и нейтрализовавшихся на катоде ионов и аэродинамическая сила. Направление и величина равнодействующей данных сил зависит от параметров режима сварки, состава электродного металла и газовой среды, наличия поверхностно-активных веществ на торце сварочной проволоки и ее диаметра.
Лучшее формирование и качество шва обеспечиваются при струйном переносе, а также при принудительном направленном переносе металла. Последний случай достигается при импульсно-дуговой сварке. Электродинамические силы пропорциональны квадрату тока, поэтому с помощью периодических кратковременных импульсов сварочного тока достигается направленный мелкокапельный перенос металла порциями с частотой воздействия импульсов. В наиболее оптимальном случае реализуется режим "одна капля за один импульс сварочного тока" (рис.2.22). Вертикальными линиями на осциллограммах сварочного тока (см. рис.2.22) указаны моменты времени, для которых представлены кадры скоростной киносъемки переноса.
Время пролета капель через дуговой промежуток для различных типов переноса составляет 10-3 – 10-1 с. За это время металл капель сильно перегревается.
Рис. 2.22. Плавление электрода (а), формирование капли (б) и ее перенос
через дуговой промежуток (в) при импульсно-дуговой сварке
в режиме "одна капля за один импульс сварочного тока"
Например, средняя температура стальных капель при различных способах дуговой сварки составляет 2100 – 3200 оС. Такая высокая температура обусловливает интенсивное протекание химических реакций металла капли с окружающей средой.
Вопросы для самоконтроля
1. Дайте определение погонной энергии сварки.
2. Какие составляющие определяют тепловой баланс при дуговой сварке и как различаются эффективные коэффициенты полезного действия нагрева металла при различных дуговых и лучевых способах сварки плавлением?
3. Охарактеризуйте стадии процесса распространения теплоты в изделии при сварке.
4. Представьте примеры различных термических циклов сварки.
5. Приведите показатели, характеризующие сварочную ванну, и укажите основные параметры сварного шва (в поперечном сечении).
6. Какими показателями определяются технологические характеристики плавления электрода?
7. Сравните между собой различные типы переноса электродного металла через дуговой промежуток.
cyberpedia.su
ОСНОВЫ СВАРКИ СТАЛИ. Особенности металлургических процессов при сварке стали плавлением
Дуговая сварка плавлением является своеобразным маталлургическим процессом, протекающим в’ совершенно необычных для металлургии условиях, в небольшом объеме сварочной ванны и в течение короткого времени. Объем сварочной ванны естественного формирования (рис. 9.1) определяется ее размерами.
Длину ванны А можно определить по формуле А = Р/д(/д> где Р — коэффициент, определяемый опытным путем; для ручной сварки плавящимся электродом Р=( 1,7—2,3) 10—а мм/Вт; /д — сварочный ток, A; UA — напряжение дуги, В. |
Задавшись величиной сварочного тока /д=300 А, напряжением дуги Нд=30 В, молено определить длину ванны; она будет равна 15,3—20,7 мм. Практически длина ванны колеблется от 15 до 25 мм, что примерно соответствует расчету. Ширина ванны Б обычно равна 2—4 диаметрам электрода. Для наиболее ходовых электродов диаметром-4 мм длина ванны равна 8— 12 мм, а диаметром 5 мм — 10—20 мм. Глубина проплавления h не превышает 2—4 мм. Таким образом, ориентировочный объем сварочной ванны 0,2—0,5 см*, а масса 1,5—4 г. Среднее время существования ванны составляет всего 15 с, после чего металл затвердевает и кристаллизуется. Маленький объем ванны и интенсивный отвод тепла в основной металл предопределяет большую скорость затвердевания расплавленного металла. Как видно из рис. 9.1, наибольшая температура в переднем участке ванны, а на периферии задней части она равна температуре плавления стали Т,1Л. В передней части ванны происходит плавление металла и совершаются интенсивные реакции элементов металла, газовой и шлаковой среды. В задней части, начиная с периферийных участков, прилегающих к основному металлу, происходят затвердевание и кристаллизация металла ванны. Металл сварочного шва и прилегающего к нему изделия в процессе сварки претерпевает нагрев и охлаждение, т. е. термическую обработку. Эти изменения температуры в каждой точке сварного соединения называют термическим циклом.
Таким образом, сварной шов образуется в результате сложного металлургического процесса, характеризующегося высокой температурой; небольшим объемом расплавленного металла электрода и металла изделия, перемешанных между собой в результате расплавления; коротким временем процесса; быстрым отводом тепла в прилегающий металл изделия и атмосферу; интенсивным воздействием металла, шлака и газа при высокой температуре.
Температура расплавленного железа в районе анодного (или катодного) пятна достигает температуры кипения 2200—2300 °С. При высокой температуре происходит диссоциация (разъединение, распад) некоторой части молекулярных газов на атомарные, которая сопровождается поглощением тепла:
02;Д 20 —Qi, N2^2N-Q2; h3^2H-Q3.
Атомарный кислород и азот активно вступают в реакции с металлом (железом, марганцем и др.) и частично остаются в шве. Атомарный водород легко растворяется в жидкой стали и при ее затвердевании часто не успевает выделиться.
При высокой температуре происходят выгорание и испарение некоторых элементов из стали и шлака.
Большая скорость подачи тепла сварочной дугой и его отвода в основной металл и в атмосферу влияет на характер кристаллизации ванны. В отличие от основного металла шов имеет структуру литой стали. По химическому составу он может отличаться от основного металла, так как образуется в результате перемешивания основного и электродного металла и под влиянием реакций, происходящих между металлом, газом и шлаком в процессе сварки. Термический цикл, который претерпевает сварное соединение, оказывает существенное влияние на структуру шва и прилегающие к нему зоны основного металла.
hssco.ru
Металлургические процессы при дуговой сварке плавлением
сварщик
Особенности металлургии сварки. Применение при сварке мощных высококонцентрированных и высокотемпературных источников теплоты приводит к местному расплавлению основного и присадочного металлов и образованию сварочной ванны. Нагрев основного и присадочного металлов до расплавления, их последующее охлаждение и затвердевание сопровождаются Фазо Выми переходами в веществе. При сварке плавлением имеет место взаимодействие между жидким и твердым металлами, газом и жидким шлаком.
Высокая температура нагрева расплавленного металла, малый объем сварочной ванны и ее перемешивание, значительная скорость процесса, интенсивный отвод теплоты в околошовную зону и окружающую атмосферу, быстрая кристаллизация сварочной ванны усложняют получение сварного шва с заданными физико-механическими свойствами, которые предопределяются химическим составом металла шва и его структурой.
Химический состав металла шва и его свойства зависят от состава и доли участия в формировании шва основного и присадочного металлов, покрытия и флюсов, степени защиты от воздуха, приемов ведения и режимов сварки. Металл шва образуется в результате перемешивания в сварочной ванне основного и присадочного металлов и реакций взаимодействия нагретого металла с газами атмосферы и защитной средой.
Одной из серьезных задач при сварке плавлением является зашита сварочной ванны ст вредного воздействия воздуха І Предотвращение попадания в металл шва вредных веществ (влаги, ржавчины, минеральных масел и других загрязнений) Высокая температура источника нагрева и объекта теплового воздействия значительно ускоряет физико-химические процессы в зоне сварки. Кислород, азот и водород переходят в атомарное состояНиє и более интенсивно взаимодействуют с расплавленным металлом Кислород является наиболее вредной примесью, и его повышенное содержание в сварном шве приводит к понижению прочности, пластичности, вязкости и антикоррозионных свойств
Последнего.
С железом кислород образует три вида оксидов: FeO, ЇїегОз И РезС>4. Наиболее отрицательное воздействие оказывает FeO, Который хорошо растворяется в расплавленном металле шва, повышая его порог хладноломкости — температуру, при которой металл теряет пластичность. Для швов с повышенным содержанием FeO Этот порог составляет —(10...15) °С.
Азот, попадающий в зону сварки главным образом из воздуха, растворяется в большинстве конструкционных материалов и со многими элементами образует называемые нитридами соединения, снижающие пластичность и повышающие твердость металла шва.
На степень насыщения металла шва азотом оказывают влияние режимы сварки и охлаждения. С увеличением силы тока и дугового промежутка содержание азота уменьшается. Медленное охлаждение шва способствует удалению из него газообразного азота.
Водород поступает в зону сварки из атмосферной влаги, а также из влаги, содержащейся в покрытиях электродов, флюсах, ржавчине на кромках заготовок; он растворяется в большинстве металлов. Железо, никель, кобальт, медь и некоторые другие металлы не вступают в соединение с водородом, а титан, ванадий, тантал, ниобий и другие образуют с ним химические соединения — гидриды.
Атомарный водород, растворяясь в жидком металле, может оставаться в этом состоянии до тех пор, пока температура достигает —200 °С. В интервале температур 200...20 °С водород переходит из атомарного состояния в молекулярное, вызывая при этом значительные внутренние напряжения и, как следствие, образование флокенов — трещин, представляющих собой в изломе светлые скруглые пятна, напоминающие хлопья снега. Гидриды и флокены снижают прочность, вязкость и пластичность шва.
Для защиты сварочной ванны от вредного воздействия воздуха используют флюсы, покрытые электроды, порошковую проволоку При их расплавлении образуется шлак, который, растекаясь по поверхности металла, играет роль защитного слоя.
Сера попадает в сварочную ванну из флюсов либо из основного или электродного металла; соединяясь с железом, она образует сульфид железа FeS. Соединение последнего с железом при кристаллизации сварочной ванны приводит к возникновению эвтектики (FeS—Fe) С температурой плавления 988 °С Обладая малой растворимостью в жидкой стали, эвтектика группируется в колонии, располагающиеся между зернами и проходящие цикл кристаллизации значительно позже основного металла шва. П( д воздействием внутренних напряжений происходит образование горячих трещин.
Попадающий в сварочную ванну из флюсов или диффундирующий из основного металла фосфор, растворяясь в зернах феррита, подобно оксиду железа FeO, Резко повышает температуру перехода в хрупкое состояние — вызывает хладноломкость стали.
Для уменьшения содержания в шве водорода пользуются рядом практических приемов: электроды и флюсы перед сваркой тщательно прокаливают; кромки свариваемых заготовок и сварочную проволоку очищают от влаги, грязи и ржавчины; швы выполняют за минимальное число проходов, так как при наложении последующего шва предыдущий шов в момент вторичного расплавления насыщается водородом; при выполнении сварочны операций на открытой площадке обеспечивают защиту зоны сварки от атмосферных осадков; сварку ответственных конструкций выполняют только при положительных температурах.
Раскисление, рафинирование и легирование сварочной ванны
Зашита сварочной ванны шлаками не обеспечивает полного пре дохранения металла от насыщения кислородом и образования оксидов. Раскисление металла сварочной ванны производят с целью удаления из нее химическим путем главным образом оксида железа FeO Осуществляют операцию с помощью марганца, кремния, титана либо алюминия, которые специально вводят в состав флюсов или покрытий электродов. Раскислителями яв ляются и чистые металлы, и ферросплавы. В результате раскис ления образуются соединения (MnO, Si02, ТЮ2, А1203), нерас творимые в расплавленном металле шва и переходящие в шлак
FeO + Мп ->■ Fe -F- MnO 2FeO-F Si 2Fe -F- Si02 2FeO + Ті -* 2Fe + Ti02 3FeO + 2A1 3Fe -F A1203 Операцию по удалению сульфитов, фосфидов, нитридов и водорода, осуществляемую также химическим путем, называю-' рафинированием. Для уменьшения в шве количества серь в покрытия и флюсы вводят марганец и известь СаО, образую шие прочные практически нерастворимые в жидком металле сульфиты, полностью переходящие в шлак:
FeS — Мп — Fe — MnS FeS -f СаО -> FeO — CaS, FeO - r Mn -> Fe + MnO
Фосфор присутствует в стали в виде фосфидов железа Fe3P И Fe2P, Удаляемых при раскислении:
2Fe3P + 5FeO 1 IFe + Р205 2Fe2P + 5FeO 9Fe + P205 Неметаллические включения удаляют из металла шва флюсами-растворителями, специально вводимыми в состав флюсов, покрытий электродов и сердечников порошковой проволоки. Продукты их взаимодействия с включениями образуют легкоплавкую механическую смесь, имеющую невысокую плотность. Наиболее часто в качестве флюса-растворителя используют плавиковый шпат CaF2, Который одновременно позволяет уменьшить содержание атомарных азота и водорода, растворенных в металле сварочной ванны.
Атомарный фтор, выделяющийся из фтористого кальция CaF2, При высокой температуре вступает в химическую реакцию с атомарным азотом или водородом, образуя фтористый азот (фтористый водород), переходящий из металла в шлак или атмосферу.
Рис. 3.3. Схема кристаллизации металла в сварочной ванне: |
Легированием Называется введение специальных, так называемых легирующих элементов в основной металл с целью получения заданных служебных свойств последнего. При легировании металла сварочной ванны в электродный или присадочный металл вводят хром, никель, ванадий, молибден, вольфрам, титан, бор и др.
/ — неметаллические шлаковые частицы, 2 — зона сплавления, 3 — зона термического влияния, 4 — столбчатые кристаллы шва |
Кристаллизация металла при сварке. Различают первичную и вторичную кристаллизации. Переход металла сварочной ванны из жидкого состояния в твердое называется первичной кристаллизацией. Первичная кристаллизация металла сварочной ванны начинается от частично оплавленных зерен основного или ранее наплавленного металла и продолжается по нормали от линии расплавления (рис. 3.3)
Вторичная кристаллизация происходит после завершения первичной и характеризуется сменой кристаллических решеток (полиморфные превращения) и изменением структуры.
Вторичная кристаллизация характерна только для металлов, испытывающих полиморфные превращения (железо, кобальт, титан, марганец и др.). Решающее влияние на характер протекания п >. диморфных превращений оказывает скорость охлаждения. Чем тоньше слой шлакового покрытия и ниже температура окружающей среды, тем выше скорость охлаждения и вероятность обр. зования внутренних напряжений и трещин.
Строение сварного соединения.
Соединение, выполняем'Є Сваркой плавлением, состоит из четырех зон: наплавленного талла; сплавления; термического влияния; основного метал а (рис. 3.4).
Рис. 3.4. Схема строения сварного соединения при дуговой сваг Ке стали: А — зона наплавленного металла Б — зона сплавления. В — зона терм 1 ческого влияния, Г — зона основного металла |
Зона наплавленного металла представляет Собої Перемешанный в жидком состоянии с основным металлом мате риал электрод г. или присадочной проволоки.
Зона сплавления — это слой основного металла тог шиной О, К..0,4 мм с частично оплавленными зернами. Перегре металла в этой зоне приводит к образованию игольчатой структуры отличающейся хрупкостью и пониженной прочностью, и оказывает значительное влияние на свойства соединения в целом.
Зона термического влияния состоит из четырех участков (1...4), различающихся структурой. Участок перегрева /—область основного металла, нагретого до 1100. ..1450 °С и имеющего крупнозернистую структуру с площадью поверхности зерна, до 12 раз превышающую площадь исходных зерен. Перегрев снижает механические свойства металла, главным образом пластичность и вязкость. Разрушение сварного соединения обыч но происходит по этому участку, ширина которого достигает 3...4 мм.
Участок нормализации 2—область основного металла, нагретого до 900... 1100 °С. Благодаря мелкозернистой структуре механические свойства металла на этом участке выше по сравнению с основным металлом. Ширина участка составляет 1...4 мм
Участок неполной перекристаллизации 3 — область основного металла, нагретого до 725...900 ЭС; состоит из мелких и крупных зерен. Неравномерное кристаллическое строение приводит к снижению механических свойств
Участок рекристаллизации 4 — область основного металла, нагретого до 450...725 °С. При этих температурах происходит восстановление формы зерен, деформированных в результате предыдущего механического воздействия (при прокатке, штамповке и др.). Ширина зоны термического влияния зависит от удельной энергии е3, введенной в заготовку, и вида сварки (например, при ручной дуговой сварке качественными электродами она составляет 5...7 мм).
Зона основного металла условно начинается от границы с температурой 450 °С. Структура при температурах ниже 450 °С не отличается от структуры исходного металла, однако сталь, нагретая до температур 200...400 °С, обладает худшими механическими свойствами, что объясняется выпадением по границам зерен оксидов и нитридов, ослабляющим связь между зернами. Это явление, вызывающее понижение пластичности и ударной вязкости при одновременном повышении прочности металла, называется синеломкостью (характерны синие цвета побежалости) .
Свариваемость металлов и сплавов.
Под свариваемостью понимают способность материалов образовывать соединения, механические и другие эксплуатационные свойства которых находятся на уровне основного материала. Свариваемость может быть оценена конкретными количественными характеристиками. В зависимости от назначения и условий эксплуатации конструкции определяют: склонность к образованию горячих и холодных трещин в металле шва и зоне термического влияния; склонность к образованию пор; механические свойства; коррозионную стой - кость; структуру; химический состав и другие свойства. Свариваемость определяется не только свойствами материала — она зависит от способа и режима сварки, состава сварочных материалов, конструктивного оформления сварного узла, условий эксплуатации изделия. Различают физическую, технологическ ю и эксплуатационную свариваемость.
Физическая свариваемость определяется процессами, происходящими на границе соприкосновения свариваемых заготовок при различных физико-химических методах соединения металлов (физический контакт, химическое взаимодействие, рекристаллизация и др.).
Под технологической свариваемостью понимают возможность получения сварного соединения определенным способом сварки. Технологическая свариваемость влияет на выбор параметров режима сварки и технологическую последовательность выполнения работ.
Под эксплуатационной свариваемостью понимают условия допустимого применения материалов в сварных конструкциях сварных изделиях.
Трещины в сварных соединениях.
В зависимости от темпера туры, при которой они образуются, трещины условно подразде ляют на горячие и холодные. Горячие трещины в сталях возникают при температуре, превышающей 1000 °С, а холодные — при более низкой. Трещины являются самым серьезным дефектом сварного соединения, как правило, не подлежащим устранению
Горячие трещины — это хрупкие межкристаллические разрушения металла шва и околошовной зоны, возникающие в твердо-жидком состоянии в процессе кристаллизации, а такж^ при высоких температурах в твердом состоянии. По современным представлениям горячие трещины вызываются действием дву факторов: наличием жидких прослоек между зернами в процессе кристаллизации и деформациями укорочения. При кристаллиз; ции жидкий металл шва последовательно переходит в жидк-. твердое, твердо-жидкое и твердое состояния.
В интервале температур плавления и полного затвердевани происходит миграция примесей и загрязнений в межзеренны пространства. Наличие между зернами жидкой фазы, примесе и загрязнений снижает деформационную способность шва и ок лошовной зоны. Неравномерность линейной и объемной усадо шва и основного металла при охлаждении приводит к возникновению внутренних напряжений, являющихся причиной появление микро- и макроскопических трещин как вдоль, так и поперек шва (рис. 3.5).
Причинами образования горячих трещин при сварке являются следующие: большое количество вредных примесей (особенно серы и фосфора) в металле свариваемых заготовок; наличие в
Рис. 3.5. Топография горячих трещин в сварных соединениях: Л 2 — продольные в зоне термического влияния и шве, 3 — поперечные в зоне термического влияния |
Металле шва элементов, образующих химические соединения с низкой температурой затвердевания (хром, молибден, ванадий, вольфрам, титан), нарушающие связь между зернами; жесткое закрепление свариваемых заготовок или повышенная жесткость самого сварного узла, затрудняющие перемещение заготовок при остывании.
Холодные трещины — это локальные меж - или транскристаллические разрушения сварных соединений, образующиеся в металле при остывании до относительно невысоких температур (как правило, ниже 200 ЭС) или при вылеживании готового изделия. Наиболее часто они поражают околошовную зону и реже — металл шва.
Для предупреждения образования холодных трещин применяют следующие технологические приемы: прокаливание флюсов и электродов перед сваркой; предварительный подогрев свариваемых заготовок до 250...450 °С; ведение процесса сварки в режиме с оптимальными параметрами; наложение швов в правильной последовательности; медленное охлаждение изделия после сварки; проведение непосредственно после сварки смягчающего отжига для снятия остаточных сварочных напряжений
Термическим способом широко пользуются для снятия остаточных сварочных напряжений в изделиях из углеродистых и ле - 3.3. Температура снятия напряжений в стальных сосудах, работающих под давлением, после сварки плавлением
Температуря | ||
Сталь | Снятия напря - жения, °С | |
Низкоуглеродистая | 580. | .650 |
Углеродистая с марганцем | Т. | .65 ) |
Углеродистая с 0,5 % молибдена | 620. | .660 |
Легированная: | ||
С 1 % хрома и 0,5 % молибдена | 620. | .660 |
С 2,25 % хрома и 1 % молибдена | 660. | .700 |
С 5 % хрома и 0,5 % молибдена | 700. | .740 |
С 3,5 % никеля | 500. | .620 |
Тированных сталей. Он основан на уменьшении предела текуче сти металла с ростом температуры. При общем нагреве изделия до заданных температур (табл. 3.3) остаточные ра
msd.com.ua
Плавление основного металла
ТЕОРИЯ сварочных процессов
ФОРМЫ СВАРОЧНОЙ ВАННЫ ПРИ РАЗЛИЧНЫХ СПОСОБАХ СВАРКИ
Плавление основного металла при сварке осуществляется с целью соединения между собой свариваемых деталей. Идеальным в отношении затрат теплоты представляется такое тепловыделение в источнике, при котором обеспечивалась бы минимальная глубина проплавления сопрягаемых поверхностей, а присадочный металл не требовался бы вовсе или входил в соединение в минимальном объеме. Если не рассматривать диффузионную сварку и пайку, при которых детали нагреваются полностью, и сварку трением, при которой полного плавления металла не достигается, наиболее близко этому требованию отвечает высокочастотная сварка и некоторые виды контактной сварки (точечная, шовная, рельефная). В перечисленных способах сварки существенная роль в образовании соединения принадлежит давлению, что позволяет плавить основной металл незначительно. Ограничимся рассмотрением случаев плавления основного металла в способах сварки без применения давления.
При электронно-лучевой сварке удается получить минимальное проплавление основного металла при сварке встык вплоть до толщин, измеряемых сотнями миллиметров. Сварочная ванна в поперечном сечении имеет форму, близкую к конусу (см. рис. 5.14, д), а в плоскостях, перпендикулярных лучу, — близкую к эллипсу.
При электрошлаковой сварке также можно получить минимальное проплавление основного металла (см. рис. 5.14, в), но для ведения шлакового процесса с целью получения достаточного выделения теплоты необходим зазор, который затем должен заполняться присадочным металлом. Сварочная ванна может быть мелкой или глубокой в зависимости от скорости сваркии мощности источника. Форма ванны при электрошлаковой сварке зависит от соотношения между количествами теплоты, поступающими в основной металл непосредственно от шлака и от опускающегося в металлическую ванну перегретого электродного металла.
При использовании дуговых, плазменных и газопламенных источников теплоты при сварке встык металла небольшой толщины форма ванны близка к форме изотермической линии температуры плавления, рассчитанной для движущегося линейного источника теплоты в пластине. С ростом толщины металла разница в размерах ванны на верхней и нижней поверхностях листа становится все более значительной, а при некоторой толщине полное проплавление уже не достигается, как показано на рис. 7.19. Для увеличения проплавляющей возможности указанных источников используют разделку кромок. Особенности различных источников нагрева в части их проплавляющей способ-
Рис. 7.19 Формы сварочной ванны при дуговой сварке: а — поверхностная дуга; 6 — погруженная дуга; в — дуга под флюсом |
В
ности обычно оценивают экспериментальным путем, расплавляя поверхность массивного тела или толстой пластины (рис. 7.19).
Ванну характеризуют следующими параметрами: L — длина ванны, В — ее ширина, Н — глубина проплавлення, Нк — глубина кратера. Очертание зоны проплавления характеризуют относительной глубиной проплавления Н/В или обратной ей величиной — коэффициентом формы проплавления Ф =В/Н, а также коэффициентом полноты проплавления ц„р= гп?/{НВ), где Fa? — площадь проплавления. Значения р обычно находятся в пределах 0,6...0,8. Для дуговой сварки под флюсом характерно большое Н/В, но при дуговых способах сварки оно все же не превышает 3. Очертание зоны наплавки характеризуют коэффициент формы валика А>в = В/А, а также коэффициент полноты валика iB = FJ(AB), где А — высота шва, FH—площадь наплавки.
Расчеты позволяют лишь приближенно оценить размеры ванны при дуговых способах сварки. При наплавке на поверхность массивного тела длину ванны L можно получить из уравнения (6.42), приняв г = 0, а АТ=ТП, — ТН и использовав при этом соотношение tu=L:
2лк(Тш-Т„) ' (7-44)
Формула (7.44) показывает, что длина ванны на поверхности массивного тела от скорости сварки не зависит. Опытные данные в целом указывают на справедливость этой формулы, хотя и обнаруживают некоторую зависимость длины ванны от скорости. Аналогично можно оценить и ширину ванны.
При заполнении разделки в случае многослойной сварки форма ванны имеет меньшее значение. Более существенно полное сплавление наплавляемого металла с ранее уложенными слоями и отсутствие шлаковых включений.
Форма и размеры ванны при прочих равных условиях (мощности источника и скорости сварки) существенно зависят от характера подачи и температуры присадочного металла. При подаче в ванну холодной непрерывной или рубленной на мелкие части проволоки ванна становится короче. Поэтому оценка L по формуле (7.44) справедлива лишь для идеализированных условий.
ТЕМПЕРАТУРА СВАРОЧНОЙ ВАННЫ
Температуры жидкого металла в различных точках сварочной ванны могут сильно различаться между собой. У границы с твердым металлом температура жидкого металла близка к температуре его плавления (табл. 7.2). Она может быть как несколько ниже Тпл вследствие кристаллизационного переохлаждения, так и выше при больших скоростях движения жидкого металла вдоль твердой границы. Как следует из рис. 7.19, расплавляю-
Таблица 7.2. Температуры плавления и кипения различных металлов, К, при атмосферном давлении
|
щийся на передней кромке ванны жидкий металл поступает в ее заднюю часть, проходя вдоль боковых поверхностей и дна ванны. При этом скорости движения металла могут превышать скорость сварки в 1,5...10 раз. Максимальные температуры жидкого металла существенно зависят от источника теплоты. При лучевых способах сварки, особенно при значительной концентрации энергии в пятне нагрева, металл может достигать температуры кипения (см. табл. 7.2).
Дуговые и плазменные источники энергии также способны создавать на поверхности металла довольно высокие температуры, например у сталей до 2300 К. При электрошлаковом процессе температура жидкого присадочного металла, проходящего через активную зону шлаковой ванны, где выделяется теплота, достигает температуры шлака, которая в средней по высоте части шлаковой ванны составляет 2100...2200 К, а на поверхности шлака около 2000 К-
При способах сварки плавлением, особенно с использованием дуги, происходит интенсивное перемешивание жидкого металла как вследствие его движения из передней части ванны в заднюю, так и под влиянием других воздействий источника теплоты на жидкий металл. Происходит интенсивный теплообмен между отдельными порциями различно нагретого жидкого металла, а также вследствие теплоотвода в твердый металл. По этой причине энергетическое состояние ванны целесообразно характеризовать не только возможными максимальными и минимальными температурами, но и средней температурой жидкого металла. Она зависит от режима сварки (тока, напряжения, скорости сварки), характера подачи присадочного металла, устойчивости дуги и положения ее активного пятна. Например, средняя температура ванны при аргонно-дуговой сварке алюминиевого сплава АМгб может изменяться от 920 до 1050 К при возрастании тока от 300 до 450 А при (/д= 14 В и от 1070 до 1200 К при 1/д= 8 В, в то время как температура плавления сплава АМгб составляет около 890 К.
Во многих случаях, в особенности при сварке легированных сталей и различных сплавов, требуется прежде всего получение определенных механических свойств и структуры металла околошовной зоны и шва, которые зависят от длительности пребывания металла выше определенной температуры, скорости охлаждения в необходимом интервале температур, повторного нагрева и многих других особенностей термического цикла сварки (см. разд. IV). Поэтому оценка эффективности процесса сварки по энергетическим критериям часто оказывается второстепенной. Однако для сталей, мало чувствительных к воздействию термического цикла сварки, оценка эффективности различных режимов сварки по энергетическим затратам необходима. Следует различать сварные соединения двух основных крайних типов: соединения, в которых преобладает наплавленный металл (заштрихованные участки на рис. 7.20, вверху), и соединения, образуемые преимущественно в результате расплавления основного металла (рис. 7.20, внизу). Для последнего типа соединений, например
стыкового, тепловую эффективность процесса целесообразно ха
рактеризовать удельной затратой количества теплоты на единицу площади свариваемой поверхности:
г— UI/F СВ), (7.45)
где Ссв1 — площадь соединения, свариваемая за 1 с; для однопроходной сварки встык, например Ссв| = иб; UI—полная тепловая мощность сварочного источника.
Эффективность использования тепловой энергии движущихся источников теплоты характеризуют также так называемым термическим к. п. д. процесса проплавления основного металла:
4t=vFupphaJq. (7.46)
Коэффициент т)/ выражает отношение условного теплосодержания vFn;phn„ проплавленного за единицу времени основного металла к эффективной тепловой мощности источника теплоты. Величина теплосодержания в единице массы металла /гпл включает в себя также скрытую теплоту плавления, затрачиваемую на
ут
-4А
без присадки
Рис. 7.20. Поперечные сечения сварных соединений (штриховыми линиями показаны границы расплавления)
переход металла из твердого в жидкое состояние. Здесь принято, что лишь теплота, истраченная на плавление металла, израсходована полезно, а остальная часть, ушедшая на подогрев металла, окружающего ванну, истрачена бесполезно. Расчетное определение тр для точечного и линейного источников теплоты соответственно в полубесконечном массивном теле и в пластине проводят по формулам (6.22) и (6.26). По ним определяют площадь F„р в выражении (7.46), ограниченную изотермой ДТ =Т„А — Тп. Для точечного источника т]( возрастает с ростом безразмерного критерия ез —qv/(a2phm), т. е. термический к. п. д. выше у мощных дуг, движущихся с высокой скоростью. Однако при вз —оо не может быть выше 1/0 = 0,368.
Соответственно для линейного источника теплоты в пластине т], возрастает с ростом безразмерного критерия е2= q/(8aphnJ, но не может быть более У2/(ле) = 0,484 в случае предельно мощных линейных источников теплоты, т. е. при q/8-voo.
Полный тепловой к. п. д. проплавления т)пр выражает отношение vFBpph„„ ко всей (полной) тепловой мощности сварочного источника теплоты VI. Источники теплоты, когда они используются для соединений, формирование которых происходит в основном в результате наплавки металла (см. рис. 7.20, вверху), целесообразно оценивать по полному тепловому к. п. д. наплавки
4H=vFuph„J{UI), (7.47)
где F„ — площадь наплавки.
Чтобы решить дифференциальное уравнение теплопроводности, необходимо задать распределение температур в начальный момент времени (начальное условие) и условия взаимодействия тела с окружающей средой на его границах (граничные условия). Начальное условие определяется …
На современном уровне развития математики аналитическое решение уравнения теплопроводности в общем виде (5.21) еще не найдено, однако при введении некоторых допущений и упрощений можно получить пригодные для практического использования частные …
Сложный процесс изменения температуры точек тела с координатами jc, у, z во времени t описывается дифференциальным уравнением теплопроводности. Для вывода этого уравнения необходимо рассмотреть баланс теплоты в некотором элементарном объеме …
msd.com.ua
Плавление электродного и основного металла

Категория:
Сварка металлов

Сварной шов образуется в результате кристаллизации металла сварочной ванны. При сварке без дополнительного металла расплавляется только основной металл. Металл, предназначенный для введения в сварочную ванну в дополнение к расплавленному основному металлу, называется присадочным металлом.
Расплавленные основной и присадочный металлы, сливаясь, образуют общую сварочную ванну. Границами сварочной ванны служат оплавленные участки основного металла и ранее образовавшегося шва.
Плавление и перенос электродного металла. Электродный металл при дуговой сварке плавится за счет тепла, выделяемого на конце электрода в приэлектродной области дуги, тепла, попадающего из столба дуги, нагрева вылета электрода при прохождении сварочного тока от токопровода и до дуги. Чем больше вылет электрода, тем больше его сопротивление, и тем больше выделяется тепла.
Конец электрода нагревается до температур 2300—2500 °С, что и обеспечивает его плавление. На конце электрода образуются капли расплавленного металла, которые переносятся через дуговое пространство в сварочную ванну.
Капли формируются на конце электрода и переносятся под воздействием сил поверхностного натяжения, тяжести, давления газов, образующихся внутри расплавленного металла, давления газового потока, электростатических и электродинамических сил, реактивного давления паров металла.
Рис. 1. Схема сварного соединения: а — при сварке плавлением, б — при сварке давлением; 1 — сварной шов, 2 — зона сплавления (сцепления), 3 — зона влияния, 4 — основной металл:
В зависимости от соотношения сил, действующих на каплю, характер переноса электродного металла может быть различным: – крупнокапельным (характерен для ручной дуговой сварки покрытым электродом) или мелкокапельным (наблюдается при сварке под флюсом и в защитных газах — аргоне, углекислом газе и др.; – струйным; – за счет коротких замыканий.
Главными силами, формирующими и удерживающими каплю на конце электрода, являются силы поверхностного натяжения, возникающие на поверхности капли и направленные внутрь ее.
Отрыв капли и ее перенос обеспечивается электродинамическими силами и давлением газовых потоков. Эти силы увеличиваются с ростом сварочного тока, увеличение тока приводит к измельчению капель. Сила тяжести капли имеет существенное значение при малых плотностях тока и способствует отрыву и переносу капель металла только при сварке в нижнем положении.
Перенос электродного металла в дуге сопровождается выбросом части металла за пределы сварочной ванны — разбрызгиванием. Разбрызгивание связано главным образом с электрическим взрывом перемычки между отделяющейся каплей и торцом электрода под действием электромагнитных сил.
Плавление основного металла. Основной металл плавится в результате выделения тепла в активном пятне (в приэлектродной области) на поверхности изделия и тепла столба дуги.
Форма проплавления (глубина и ширина) определяется концентрацией теплового и силового воздействия дуги.
Основные компоненты силового воздействия дуги; поверхностные силы — давление, вызываемое торможением струи плазмы дуги о поверхность металла, реактивное давление струи пара с поверхности сварочной ванны; объемная электродинамическая сила в жидком металле. Давление осевого плазменного потока вызывается электромагнитными силами, его величина пропорциональна квадрату тока. Дуга с плавящимся электродом оказывает большее силовое воздействие на сварочную ванну, чем дуга с неплавящимся электродом. Сила давления от газового потока невелика и составляет около 1 % силы давления потока, вызываемого электромагнитными силами.
Рис. 2. Схемы расплавления и переноса электродного металла: а — короткими замыканиями, б — капельный, в — струйный
Процесс проплав лен и я металла определяется тепловым и силовым воздействием дуги.
Производительность процессов плавления. В наибольшей степени тепловую мощность дуги, производительность процесса плавления и глубину проплавления определяет величина сварочного тока.
Читать далее:
Формирование и кристаллизация сварочной ванны
Статьи по теме:
pereosnastka.ru
ПЛАВЛЕНИЕ МЕТАЛЛА В СВАРОЧНОЙ ВАННЕ — КиберПедия
Наибольшую актуальность проблема влияния кислорода на свойства металлических швов имеет при сварке плавлением. Это объясняется тем, что при плавлении металл высоко активен, вступает во взаимодействие не только с окружающей атмосферой, но и с защитной средой (защитным газом, компонентами расплавленного флюса и электродного покрытия).
Поэтому кратко рассмотрим природу плавления металла в сварочной ванне.
При сварке плавлением кромки свариваемого металла и присадочный металл расплавляются под действием источника энергии. В результате образуется общая для соединяемых деталей сварочная ванна (рис.1). При этом под сварочной ванной понимают как ванну жидкого металла, так и капли расплавленного металла, образующиеся на конце электрода (электродной проволоки).
В процессе сварки дуга перемещается вдоль свариваемых кромок и образует подвижную сварочную ванну, в передней части которой (abc) происходит плавление металла (основного и присадочного, а в хвостовой части (dkn)) – кристаллизация (рис.2). По мере движения дуги и ванны происходит формирование сварного шва
Рис.1. Схема процесса сварки плавлением |
Конвективные потоки badn и bckn в ванне способствуют перемешиванию металла, а также его интенсивному взаимодействию с защитной средой. Несмотря на относительно небольшую продолжительность контакта металла с расплавленным шлаком, степень взаимодействия их весьма значительная из-за высоких температур в зоне плавлении я и больших поверхностей контакта. Кроме того при сварке под флюсом масса шлака в 1,1-1,2 больше массы расплавленного металла, что на порядок превышает соотношения при металлургических процессах плавки.
Кроме этого особенность металлургических процессов в сварочной ванне определяет и температурное поле в ней (рис.3).
Наибольшая температура наблюдается под дугой в передней части ванны (~3000 К). Периферийные участки сварочной ванны имеют температуру, близкую к температуре кристаллизации. Средняя температура электродного металла обычно выше, чем в сварочной ванне. Например, при сварке в проволокой св-08Г2С средняя температура в сварочной ванне 2170 К, а электродных капель (2860-2970) К, при сварке электродами с кислым покрытием (1870-2270) К и (2380-2470) К соответственно.
Повышенная температура и большая удельная поверхность капель электродного металла создают более благоприятные по сравнению с ванной условия взаимодействия металла с газами и шлаком именно на стадии капель.
Повышение температуры до максимума с последующим спадом приводит к тому, что на разных участках зоны плавления идут процессы разных направлений. Например, одновременно с восстановлением и из шлака при сварке под флюсом возможно их окисление в хвостовой части ванны или абсорбция жидким металлом газов в более нагретой части зоны плавления может сопровождаться их десорбцией в менее нагретых участках.
Наиболее интенсивно большинство процессов взаимодействия металл - защитная среда протекают на высокотемпературных участках. Поэтому особо благоприятные условия реакционного взаимодействия создаются на стадии капли и ее переноса. (Здесь происходит и значительное перемешивание металла и шлака).
По мере уменьшения температуры большинство процессов начинает протекать в обратном направлении. Однако, скорость обратных процессов ниже скорости прямых в наиболее горячей части зоны плавления. Т.е. количество прореагировавшего вещества в процессе нагрева оказывается больше, чем при снижении температуры. Поэтому в закристаллизовавшемся металле часто наблюдается изменение концентрации того или иного элемента по сравнению с исходной. Схематически процесс представлен на рисунке 4.
В связи с обратимостью большинства процессов на границе металл - защитная среда они стремятся к равновесию. Однако равновесное состояние зависит от температуры. В зоне сварки температуры металла и шлака постоянно изменяются, поэтому принципиально возможно не достижение равновесия реакций взаимодействия, а достаточно высокая степень приближения к нему.
Рис.4. Схема изменения концентрации элемента в наплавляемом металле в результате его взаимодействия со шлаком в сварочной ванне.
Будем считать, что между жидким металлом и шлаком при сварке под флюсом идет реакция по схеме:
(10)
В результате такой реакции в наплавленном металле с увеличением температуры возрастает концентрация . Исходное равновесное содержание этого элемента в металле было [C1] (рис. 4).
Реакция стремится к новому равновесию, причем скорость ее возрастает с повышением температуры. После достижения Тmax температура снижается и следовательно в обратном направлении должна меняться концентрация в наплавленном металле, стремясь к [C1]. Однако при достижении Тmax концентрация соответствует равновесному [Cp] для более низкой температуры, поэтому при начальном снижении температуры [C1] продолжает расти, стремясь к равновесному состоянию [Cp]max. Т.е. температура начинает снижаться, а концентрация в наплавленном металле продолжает расти.
При дальнейшем снижении температуры увеличение содержания сначала замедляется, а затем, пройдя через максимальную концентрацию [Cp], соответствующую температуре Тp, начинает понижаться, но по-прежнему отставая от изменения температуры. Это отставание по мере снижения температуры должно увеличиваться, т.к. скорость реакции уменьшается. При остывании металла до температуры Ткр концентрация не будет иметь значение [C1], а останется на некоем уровне [C2], что и создает прирост элемента в наплавленном металле.
Аналогичные рассуждения справедливы и применяются к взаимодействию между газами и металлом в зоне плавления.
cyberpedia.su