Автоматическая и полуавтоматическая сварка в защитных газах. Аргонодуговая сварка алюминия и его сплавов
Технология аргонодуговой сварки алюминия и его сплавов
Аргонодуговым способом сваривают различные типы соединений алюминия и сплавов на его основе. В зависимости от толщины свариваемых элементов применяют аргонодуговую сварку неплавящимся вольфрамовым (с присадкой и без нее), а также плавящимся электродами.
Аргонодуговая сварка неплавящимся вольфрамовым электродом — лучший способ соединения тонколистового алюминия, не уступает по производительности сварке по флюсу и аргонодуговой сварке плавящимся электродом толстолистового алюминия.
Качество швов при аргонодуговой сварке алюминия и сплавов на его основе зависит от чистоты аргона, поэтому он должен не иметь следов влаги и содержать не более 0,03% кислорода и не более 0,3% азота. Хорошие (плотные) швы получаются также при сварке в защитной смеси из 65% гелия и 35% аргона.
При сварке вольфрамовым электродом стыковых соединений металла толщиной до 3 мм кромки не скашиваются. В соединениях металла толщиной до 6 мм делают односторонний скос кромок с общим углом раскрытия 60—90° и притуплением в стыке до 1,5 мм, а при толщине металла до 9 мм — такой же скос кромок, но с притуплением до 2,5 мм.
Металл толщиной до 20 мм сваривают с двусторонним скосом кромок и углом раскрытия 60—90°, с притуплением 3 мм или односторонней рюмкообразной подготовкой кромок с углом раскрытия 40—60°, радиусом закругления у основания разделки 5 мм и притуплением в стыке 3 мм.
Металл толщиной до 6 мм сваривают односторонним швом на подкладке. При толщине металла более 6 мм после выполнения шва с одной стороны вырубают корень этого шва и стык затем сваривают с обратной стороны. В том случае, когда за один проход не удается заполнить разделку, сварку выполняют в два прохода, причем первый проход делают без присадки с полным проплавлением стыка, а второй — с присадкой для заполнения разделки и получения необходимого усиления шва.
При сварке алюминия и его сплавов в инертных газах раскисляющий флюс не применяется. Вместе с тем аргон даже самого высокого качества содержит некоторое количество кислорода, достаточное для образования пленок окислов жидкого металла.
Если в процессе сварки пленки окислов не разрушаются, то металл шва засоряется ими и в отдельных местах сварного соединения может образоваться несплавление кромок, а также несплавление присадочного металла с основным. Разрушить же эти пленки можно лишь в том случае, если сварочная ванна (изделие) будет катодом.
Тогда с поверхности жидкой ванны и соседних с ней зон менее нагретого металла происходит вырывание металлических частиц (катодное распыление металла). Вследствие катодного распыления пленки окислов, образующиеся в сварочной ванне, разрушаются, что обеспечивает хорошее сплавление кромок и формирование шва без применения флюса.
Изделие может быть катодом как при сварке постоянным током обратной полярности, так и при сварке переменным током. В последнем случае катодное распыление и, следовательно, очищение сварочной ванны от окислов происходит в полупериоды обратной полярности тока.
Поскольку ток обратной полярности (плюс на электроде) нельзя использовать из-за перегрева электрода, а прямой из-за необходимости очищения сварочной ванны от пленок окислов, аргонодуговую сварку алюминия вольфрамовым электродом выполняют переменным током.
Аргонодуговая сварка алюминия плавящимся электродом выполняется постоянным током обратной полярности. Переменный ток при такой сварке не применяется. Для питания дуги переменным током используют стандартные сварочные трансформаторы с осцилляторами и стабилизаторами, а для питания постоянным током — преобразователи с падающей, жесткой или возрастающей внешней характеристикой.
Для сварки разноименных алюминиевых сплавов, обеспечивающих сварным соединениям повышенную стойкость против горячих трещин, рекомендуется применять следующие марки проволок:
Марки свариваемых сплавов | Марки сварочной проволоки |
АДО+АМц | СвА5 |
АДО+АМгЗ | СвАМг6 |
АДО+АМг5 | СвАМг6 |
АДО+АМг6 | СвАМг6 |
АДЦ+АМгЗ | СвАМг6 |
АДЦ+АМг5 | СвАМг6 |
АДЦ+АМг6 | СвАМг6 |
Марки свариваемых сплавов | Марки сварочной проволоки |
АМг3+АМг5 | СвАМг6 |
АМг3+АМг6 | СвАМг6 |
АМг5+1915 | СвАМг6, Св1557 |
АМг6+1915 | Св1557 |
АД31+АМцС | СвАК5 |
АД31+АМгЗ | СвАМг6 |
АД31+АМг6 | СвАМг6 |
АД51+АМг6 | СвАМг6 |
Состав газообразного аргона должен быть следующим:
Марка аргона | Содержание, % | |||
Аг | О2 | Н1 | Влага при давлении 760 мм рт.ст., г/м3 | |
А | Не менее 99,99 | Не более 0,003 | 0,01 | 0,03 |
Б | Не менее 99,96 | Не более 0,005 | 0,04 | 0,03 |
Состав газообразного гелия, применяемого для сварки (%):
Содержание | Гелий высокой чистоты |
Гелия (не менее) | 99,985 |
Водорода (не более) | 0,0025 |
Азота (не более) | 0,005 |
Кислорода (не более) | 0,002 |
Углеводородов (не более) | 0,003 |
Неона (не более) | 0,002 |
Точка росы (не выше) | -55°С |
При автоматической аргонодуговой сварке вольфрамовым электтродом горелка (мундштук) обычно располагается вертикально, а присадка подается механизмом автомата со стороны, противоположной направлению сварки.
Сварка плавящимся электродом может выполняться автоматом и шланговым полуавтоматом. При полуавтоматической сварке горелку наклоняют под углом 60—80° к плоскости изделия и перемещают углом вперед или углом назад с небольшими плавными поперечными колебаниями или без колебаний. При автоматической сварке горелку располагают вертикально.
www.prosvarky.ru
Технология сварки алюминия и его сплавов
Температура плавления алюминия 660°С, окисной пленки 2060°С
Марка | Свариваемость | Технологические особенности сварки | |
Технически чистый алюминий | Очистка кромок и присадка от окисной пленки | ||
АД00, АД0, АД1 , АД | Хорошая | Присадок Св-А1, СвА000, Св-85Т | |
Деформируемые, термически не упрочняемые сплавы | |||
АМц, АМцС, Д12 | Хорошая | Присадок Св-AMц | |
АМг1, АМг2, АМг3 | Присадок Св-AMг3 | ||
АМг4, АМг5 | Присадок Св-AMг5 | ||
АМг6 | Прксадок Св-АМг6, Св-АМг7 | ||
Деформируемые, термически упрочняемые сплавы | |||
АД31, АДЗЗ, АД35 АВ, АК6, АК8 | Удовлетворительная | Присадок Св-АК5, Св-1557 | |
АК4, АК4-1 | Ограниченная | ||
В95 | Плохая | Предварительный подогревТермообработка после сварки при t°= 200-250°С Присадок Св-1557, Св-АМг5,. Св-АМг6 | |
1915,1925 | Удовлетворительная | ||
Литейные сплавы | |||
АЛ1, АЛ2, АЛ9, АЛ25, АЛ26 | Хорошая | Присадок той же марки, что и основной металл | |
АЛЗ, АЛ4, АЛ5, АЛ7, АЛ8, АЛ10В | Удовлетворительная |
Марки присадочной проволоки, используемой для сварки алюминия и его сплавов
Св-А1 | Св-1557 | Св-А97 | Св-А5с | Св-АМц |
Св-АМг3 | Св-АМг5 | Св-АМг6 | Св-АМг7 | Св-АК3 |
Св-АК5 | Св-АКЮ | Св-А85Т | Св-А000 | Св-1201П4 |
Толщина металла, мм | до 1,5 | 1,6-3 | 3,1-5 | 5,1-10 | 10-15 |
Рекомендуемый диаметр присадка, мм | 1-2,5 | 2,5-3 | 3-4 | 4-6 | 6-8 |
Ориентировочные расходы сварочных материалов
Толщина свариваемого металла, мм | Диаметр электрода, мм | Расход W-электродов на 100 пог. м шва, г | Расход аргона на 1 пог. м шва, л |
1 | 1,5 | 8,3 | 60-80 |
2 | 2 | 23 | 65-90 |
3 | 3 | 51 | 85-120 |
4 | 3,5-4 | 88 | 95-130 |
6 | 4 | 132 | 105-145 |
Трудности при сварке
- Температура плавления окисной пленки значительно выше, чем алюминия, и она расплавляется позже. Это затрудняет формирование шва
- Высокая теплопроводность алюминия требует увеличения сварочного тока в 1,2-1,5 раза по сравнению, например, со сваркой стали
- Образуются значительные остаточные деформации, что требует специальных мер и приспособлений
- Окисная пленка не растворяется в жидком алюминии. Это мешает формированию шва и служит причиной появления в нем металлических включений
- При нагреве алюминия и его сплавов нет явных признаков их перехода в жидкое состояние. Это требует высокой квалификации сварщика
Несплавление кромок алюминиевых конструкций
Подготовка к сварке. Резка и подготовка кромок ведутся механическим способом. На ширину 100-150 мм их обезжиривают ацетоном, авиационным бензином, уайт-спиритом или другим растворителем. Окисленную пленку удаляют механически или химическим травлением. При механической обработке свариваемые кромки на ширину 25-30 мм зачищают наждачной бумагой, шабером и металлической щеткой из нержавеющей проволоки. Зачистку проводят непосредственно перед сваркой.
Химическое травление проводят в течение 0,5-1 мин в реактиве, состоящем из 50 г едкого натра и 45 г фтористого натрия на 1 л воды. После травления следует промывка в проточной воде, а затем осветление в 30-35%-ном растворе азотной кислоты (для алюминия и сплавов типа АМц) или в 25%-ном растворе ортофосфорной кислоты (для сплавов типа АМг и В-95). После повторной промывки необходима сушка до полного испарения влаги.
Алюминиевую сварочную проволоку перед сваркой также обрабатывают. Сначала ее обезжиривают, а затем подвергают травлению в 15%-ном растворе едкого натра в течение 5-10 мин при температуре 60-70°С. После этого промывают в холодной воде и сушат 10-30 мин при температуре 300°С.
Подготовленные к сварке материалы сохраняют свои свойства в течение 3-4 дней. Затем на поверхности вновь образуется окисная пленка
ПОДКЛАДКИ ДЛЯ ЗАЩИТЫ ОТ ВЫТЕКАНИЯ МЕТАЛЛА ИЗ СВАРОЧНОЙ ВАННЫ
Выбор параметров режима
Метод сварки неплавящимся электродом применяют для изделий из алюминиевых сплавов толщиной до 12 мм. При сварке металла толщиной от 1 до 6 мм применяют вольфрамовые электроды диаметром от 1 до 5 мм. Сварочный ток (А) определяют по формуле:
Iсв=(60÷65)dэ,
где dэ - диаметр электрода, мм
Питание дуги осуществляется от источника переменного тока с осциллятором, что помогает разрушить окисную пленку. Напряжение холостого хода источника должно быть повышенным. Надежность газовой защиты дуги и сварочной ванны зависит от диаметра и формы сопла горелки, расстояния сопла от поверхности свариваемого изделия.
Рекомендуется выдерживать такие соотношения:
Диаметр электрода, мм | 2-3 | 4 | 5 | 6 |
Диаметр сопла, мм | 10-12 | 12-16 | 14-18 | 16-22 |
Длина выступающего из сопла W-электрода (выпуск) должна составлять при сварке стыковых соединений 1-1,5 мм, а тавровых и угловых 4-8 мм. Длину дуги поддерживают в пределах 1,5-3 мм. Скорость сварки выбирают от 8 до 12 м/ч.
Соединения с отбортовкой кромок целесообразно применять при сварке металла толщиной 0,8-2 мм.
Техника сварки
Ручной аргонодуговой сваркой W-электродом выполняют стыковые, угловые и тавровые соединения. Конструкции толщиной до 10 мм сваривают «углом вперед», а более 10 мм - «углом назад». Угол между присадочной проволокой и горелкой должен составлять 90°. Проволоку подают короткими возвратно-поступательными движениями. Поперечные колебания W-электрода недопустимы.
Изделия толщиной до 4 мм включительно сваривают за один проход на стальной подкладке. При толщине от 4 до 6 мм сварку выполняют с двух сторон, а при толщине 6-12 мм подготавливают кромки с V-образной или Х-образной разделкой.
Подачу аргона начинают за 3-5 с до возбуждения дуги, а прекращают через 5-7 с после окончания сварки.
Чтобы снизить вероятность окисления металла шва, размеры сварочной ванны нужно выдерживать минимальными.
ОРИЕНТИРОВОЧНЫЕ РЕЖИМЫ РУЧНОЙ СВАРКИ АЛЮМИНИЕВЫХ СПЛАВОВ
Подготовка кромок и форма шва | Размеры, мм | Сварочный ток, А | Диаметр электрода, мм | Диаметр присадка, мм | Расход аргона, л/мин | Число проходов | ||
S | b | с | ||||||
![]() | 2 3 4 | 0+1,0 0+1,5 0+2,0 | - | 70-80 100-140 160-190 | 2 3 4 | 2-2,5 3 3-4 | 5-6 7-8 7-8 | 2 |
![]() | 2 3 | 0+1,0 | 80-100 120-140 | 3 | 2,5-3,5 3 | 5-6 7-8 | 1 | |
![]() | 2 3 4 | 80-100 120-140 160-210 | 2 3 4 | 2,5-3,5 3 4 | 5-6 7-8 7-8 | 1 1 2 | ||
![]() | 4 6 8 10 | 1+0,5 1+1,0 1+1,0 1+1,0 | 150-200 250-300 300-350 350-400 | 6 5 5-6 6-7 | 3-4 4 4-5 4-5 | 7-8 8-9 9-10 10-12 | 1 2 2 2 | |
![]() | 4 6 8 10 15 | 1+1,0 1,5+1,0 2,0+1,0 2,0+1,0 2,5+1,0 | 1+0,5 1+1,0 1+1,0 1+1,0 | 220-260 260-300 320-360 380-420 440-480 | 4 4-5 5-6 6-7 8 | 3-4 4 4 4-5 4-5 | 8-10 10-12 12-14 16-18 16-18 | 1 2 2 2 2 |
![]() | 10 15 25 | 0+1,0 0+1,5 0+1,5 | 1+0,5 | 350-400 380-420 480-550 | 6-7 7 8 | 4-5 | 10-12 16-18 18-20 | 4 6 6 |
![]() | 2 4 6 | 0+0,5 0+1,0 0+1,5 | - | 100-120 170-220 240-280 | 2-3 4 5 | 2 3-4 4 | 5-6 7-8 8-10 | 2 |
![]() | 4 10 15 | 0+1,0 0+1,5 0+2,0 | 0,5 0+0,5 1,5 | 170-220 350-400 380-420 | 4 6-7 7 | 4 4-5 4-5 | 8-10 10-12 16-18 | 2 |
![]() | 8 10 15 20 | 0+1,0 0+2,0 0+2,0 0+2,0 | 0,5 1,0 1,5 1,5 | 280-320 350-400 380-420 480-550 | 5-6 6-7 7 8 | 4 4-5 4-5 4-5 | 8-10 10-12 16-18 18-20 | 2 2 2 5 |
![]() | 2 4 6 | 0+0,5 0+1,0 0+1,5 | 0+1,0 | 100-120 150-200 220-260 | 2-3 4 5 | 2-3 3 4 | 5-6 8-10 8-10 | 2 |
![]() | 4 10 15 | 0+1,0 0+1,5 0+2,0 | 0,5 1+0,9 1,5 | 150-200 320-380 360-400 | 4 6-7 7 | 3-4 4-5 4-5 | 8-10 10-12 16-18 | 2 2 3 |
weldering.com
Сварка алюминия и его сплавов - Сварочные работы. Практическое пособие - Юрий Федорович Подольский - Ogrik2.ru
Сварка алюминия и его сплавов
Сварка алюминия и его сплавов затруднена тем, что на поверхности расплавленного металла постоянно образуется тугоплавкая пленка оксида алюминия Al2O3, препятствующая сплавлению частиц металла между собой. Высокая температура плавления оксида алюминия (2050 °C) и низкая температура плавления алюминия (658 °C) крайне затрудняют управление процессом сварки. Попадая в шов, окисная пленка образует неметаллические включения, резко снижая показатели прочности и пластичности.
Алюминий при расплавлении не меняет свой цвет, поэтому визуальное наблюдение при сварке за состоянием ванны затруднено, особенно при подогреве, так как в один момент металл стыка может просто провалиться, распасться. Алюминий очень хрупок в нагретом состоянии. При сварке окисную пленку удаляют флюсами, покрытиями электродов и специальными циклическими импульсами на дуге от источников питания.
Следующая трудность – образование пор по причине наличия в шве водорода. Он, вяло выделяясь из ванны, оставляет дефекты в виде пор. Алюминий при сварке склонен к кристаллизационным трещинам. Присутствие в нем железа и кремния сильно влияет на появление трещин в металле шва. Увеличение содержания кремния до 0,6 % снижает стойкость против образования трещин. Железо в шве до 0,7 % положительно влияет на стойкость к образованию трещин. При содержании железа более 0,8 % стойкость к образованию трещин снижается.
К проблемным параметрам алюминия при сварке относятся также высокая теплопроводность – в 3 раза выше, чем у железа, и высокий коэффициент теплового расширения – в 2 раза больше, чем у железа, что способствует увеличению деформаций.
Абсолютное большинство сварных конструкций изготавливается из деформируемых, термически не упрочняемых сплавов алюминия с марганцем (АМц) и с магнием (АМг), а также литейных недеформируемых сплавов алюминия с кремнием (силумин). К таким сплавам относятся: АД, АД-1, АМц, АМг, АМг3, АМг5В, АМг6, АВ, АД33, АД35, Д20, ВАД-1, В92У.
Для прочих сплавов сварка плавлением почти не применяется, так как околошовная зона сильно разупрочняется и невозможно получить прочное соединение. Распространенный сплав алюминия с медью (4–5 % Cu) Д16, Д1, называемый дюралюминием, имеет очень плохую свариваемость и для сварных конструкций не применяется, а соединяется клепкой.
Высокая теплопроводность алюминия и его сплавов требует применения специальных технологических приемов, а при массивных деталях – предварительного подогрева. Алюминий сваривают плавлением и давлением; в первом случае применяется ручная и механизированная сварка в аргоне плавящимся и неплавящимся электродом, покрытыми электродами, газовая.
Независимо от способа сварки алюминиевые изделия перед сваркой должны проходить специальную подготовку, заключающуюся в обезжиривании металла и удалении с его поверхности пленки оксида алюминия. Поверхность металла обезжиривают растворителями (авиационным бензином, техническим ацетоном), затем механической зачисткой или химическим травлением удаляют оксидную пленку.
Химический способ удаления пленки оксида алюминия состоит из следующих операций: травление в течение 0,5–1 мин раствором 45–55 г едкого натра и 40–50 г фтористого натрия на 1 л воды; промывка в проточной воде; нейтрализация в 25–30 %-ном растворе азотной кислоты в течение 1–2 мин; промывка в проточной, а затем в горячей воде; сушка до полного удаления влаги. Обезжиривание и травление рекомендуется делать не более чем за 2–4 ч до сварки.
Ручную электросваркуалюминия используют во многих случаях.
Ручную сварку угольным электродом на постоянном токе прямой полярности используют только для неответственных изделий. Этот способ сварки ранее успешно был внедрен электротехниками для сварки контактов электропроводов. Недостаток: чистый алюминий загрязняется углеродом. Оксидную пленку удаляют с помощью флюса АФ-4А (табл. 39). Сварку ведут на графитовых или угольных подкладках. Электроды графитовые или угольные, ∅ 8–15 мм; сварочный ток – 150–450 А. Флюс наносят на основной и присадочный материал.
Сварку металла толщиной до 2 мм ведут без присадки и без разделки кромок, металл толщиной свыше 2 мм сваривают с зазором 0,5–0,7 толщины свариваемых листов или с разделкой кромок.
Ручную сварку покрытыми электродами применяют в основном при изготовлении малонагруженных конструкций из технического алюминия, сплавов типа АМц и АМг, силумина при толщине материала более 5 мм. Тонкий листовой алюминий (до 3 мм) нужно варить с отбортовкой.
Использование постоянного тока обратной полярности с предварительным подогревом (для средних толщин – 250–300 °C, для больших толщин – до 400 °C) обеспечивает требуемое проплавление при умеренных сварочных токах. В связи с тем, что алюминиевый электрод плавится в 2–3 раза быстрее стального, скорость сварки алюминия должна быть соответственно выше.
Сварку рекомендуется выполнять непрерывно в пределах одного электрода, так как пленка шлака на кратере и конце электрода препятствует повторному зажиганию дуги. Для обеспечения устойчивого процесса при минимальных потерях на разбрызгивание рекомендуется применять сварочный ток из расчета 25–32 А на 1 мм диаметра электрода, но не более 60 А.
Электроды ОЗА-1 предназначены для сварки алюминия АД0, А6, АД1, АД и подобного. Электродный стержень Св-А97 (ГОСТ 7871–75). Предел прочности металла шва 6,5–8,5 кгс/мм2. После сварки шов следует немедленно промыть горячей водой и очистить стальной щеткой от остатков шлака. Покрытие электродов гигроскопично (поглощает влагу из окружающей среды), поэтому электроды перед сваркой просушивают при температуре 200 °C в течение 2 ч.
Для заварки литейных дефектов применяются электроды марки ОЗА-2 с электродным стержнем из кремнистого алюминия АК5 (ГОСТ 7871–75). Электроды ОЗА-2 применяются для наплавки деталей из литейных сплавов марки AЛ-2, АЛ-4, AЛ-5, AЛ-9, АЛ-11, а также для их сварки. При сварке нужно учитывать необходимость любых подкладок (даже формовка размягченным водой асбестом) для удержания расплава алюминия от провала.
Рекомендованные флюсы приведены в табл. 39. Флюс наносится либо в виде порошка, либо в виде пасты, приготовленной на воде или спирте. Разводят флюс в необходимом количестве с учетом его хранения до 6 ч в закрытой таре, чтобы не уменьшить его химическую активность. При применении указанных флюсов для электродных покрытий к ним добавляют до 30 % криолита Na3AlF6.
Основной вид соединения – стыковой, но при механизированной сварке в защитных газах применяют и тавровые, угловые соединения.
Аргонодуговая сварка алюминия. Аргонодуговая сварка алюминия и его сплавов с середины 60-х годов прошлого века является несложной и хорошо разработанной в части технологии сварки задачей. Она обеспечивает наилучшее качество по прочности, внешнему виду, имеет наименьшие технологические сложности. При ручной дуговой сварке применяется неплавящийся вольфрамовый электрод, а при полуавтоматической и автоматической – плавящийся, хотя при автоматической сварке нередко применяют и неплавящийся электрод.
При сварке в аргоне не требуется тщательной подготовки (очистки от окислов) кромок алюминия, сварка выполняется на специальном оборудовании, импульсом тока дуги, от которого разрушается и удаляется окисная пленка. В процессе сварки хорошо видно, как пленка окислов оттесняется в стороны от ванны и вскрывается чистый (как ртуть) серебристый металл, который медленно расплавляется при правильном режиме.
Сварщику необходимо помнить, что алюминий и его сплавы при нагреве сразу переходят из твердой фазы в жидкую, минуя пластическую. Поскольку при нагреве до 400–500 °C алюминий почти полностью теряет прочность, надо следить за тем, чтобы деталь не разрушилась под действием собственной силы тяжести.
Для автоматической сварки алюминиевых сплавов вольфрамовым (неплавящимся) электродом оптимальные режимы указаны в табл. 40. На сварочных полуавтоматах применяется сварочная алюминиевая проволока ∅ 1–2 мм, сварочный ток до 300 А, скорость подачи проволоки – 150–650 м/ч, расход защитного газа (аргона) 300–600 л в час; чем больше скорость сварки, тем больше расход аргона. Сварка вольфрамовым (неплавящимся) электродом выполняется на переменном токе с использованием в сварочной цепи специального осциллятора. Сварка плавящимся электродом проводится на постоянном токе при обратной полярности, сварочный ток – 300–400 А, напряжение на дуге 38–44 В, скорость сварки – 12–20 м/ч. При сварке вольфрамовым электродом на прямой полярности («—» на электроде) стойкость электрода и допустимый предельный ток выше примерно в 7 раз.
Присадочную проволоку ∅ 2,0 мм подают в зону сварки механически, по мере надобности. Подающий механизм по принципу действия – не толкающего, как для стальной проволоки, а тянущего типа.
Ручную аргонодуговую сварку выполняют неплавящимся вольфрамовым электродом в осушенном от влаги аргоне высшего или первого сорта на переменном токе. Для металла толщиной до 5–6 мм используют электроды ∅ 1,5–5,0 миллиметров.
Проволоку и свариваемые кромки обезжиривают ацетоном или бензином, затем счищают окисную пленку стальной щеткой. Зачистка позволяет сохранить алюминий чистым в течение 2 часа.
Сварка выполняется без поперечных колебаний электродом или прутком. Сварку желательно вести на больших скоростях в один слой, чтобы не перегревать металл.
Если толщина свариваемого металла более 8 мм, то алюминий нужно предварительно подогревать до температуры 150–300 °C горелкой – по 80–100 мм с каждой стороны стыка.
Особые требования предъявляются к технике сварки. Угол между присадочной проволокой и электродом должен составлять ~90°. Присадку следует подавать короткими возвратно-поступательными движениями. Недопустимы поперечные колебания вольфрамового электрода. Обеспечение эффективной защиты для каждого режима сварки достигается оптимальным расходом газа (табл. 41). Для уменьшения опасности окисления размеры сварочной ванны должны быть минимальными. Сварку алюминия толщиной до 10 мм обычно ведут левым способом (справа налево), который позволяет снизить перегрев свариваемого металла.
Автоматическая сварка алюминия по флюсу. Особенность сварки алюминия – по флюсу, а не под флюсом – заключается в том, что флюс имеет высокую электропроводность, шунтируется электродугой и дуга горит с видимым ярким свечением.
Применяемый флюс марки АН-А1 имеет следующий состав: хлористый калий (50 %), хлористый натрий (20 %), криолит Na3AlF6 (30 %). Есть и другие марки флюсов, например АН-А4, АН-А6, но их составы отличаются незначительно. Высота слоя флюса – 15–30 мм; сварочная проволока – Св-А97 и Св-АМц ∅ 2–3 мм. Сварку ведут постоянным током при обратной полярности. Сварочный ток – 300–400 А, напряжение на дуге – 38–44 В (т. е. повышенное), скорость сварки – 12–20 м/ч. Алюминий толщиной 4–10 мм варят таким способом без разделки на стальной подкладке.
Газовая сварка алюминия. Одним из наиболее доступных и недорогих способов сварки алюминия и его сплавов является газовая сварка с использованием как ацетилена, так и пропан-бутана. Способ является надежным и незаменимым при отсутствии технических возможностей применить более совершенный способ, например аргонодуговую сварку. По качеству соединения деталей газовая сварка дает удовлетворительные результаты. Однако основным видом соединений при газовой сварке алюминия и его сплавов является стыковое. Выполнять тавровые, угловые и нахлесточные соединения не рекомендуется.
Кромки разделывают механическим способом и за 2 ч до сварки тщательно зачищают. Перед сваркой кромки деталей и присадочную проволоку промывают в течение 10 мин в щелочном растворе, содержащем 20–25 г едкого натра и 20–30 г карбоната натрия на 1 дм3 воды при температуре 65 °C, с последующей промывкой в воде. После этого кромки и присадку протравливают в течение 2 мин в 15 %-ном растворе азотной кислоты, промывают в горячей и холодной воде, а затем сушат.
Сварку проводят с применением флюсов (см. табл. 39), до создания которых газовая сварка алюминия была невыполнимой задачей. Для ответственных сварочных работ, в особенности для тонких металлов, при сварке алюминия и сплавов нужно применять флюсы, содержащие соли лития. Лучшим из них считается флюс АФ-4А. В качестве горючего газа, кроме ацетилена, можно использовать природный газ, пропан-бутановые смеси и водород. Качество соединения в таких случаях получается вполне удовлетворительное.
Флюс наносят в зону сварки различными удобными способами в виде пасты или порошка, прилипающего к разогретому металлу. Находящиеся во флюсе фтористые соединения растворяют окисную пленку Аl2О3 в расплавленной ванне, а хлористые соли лития отнимают кислород у окиси алюминия, и металл становится чистым. Флюсы очень гигроскопичны, поэтому их хранят в герметичной таре. Флюс, разведенный в виде пасты на воде, может храниться не более 10 часов.
Соли лития очень дефицитны и дороги, поэтому делается много попыток создать флюсы, не содержащие лития. Но все безлитиевые флюсы на сегодняшний день не являются полноценными; это всего лишь заменители, дающие более или менее удовлетворительные результаты.
Настоящий флюс содержит от 15 до 30 % солей лития. Проверка его пригодности проводится так: нагревается небольшая зона (точка) горелкой до появления серой шероховатой поверхности (окисления), затем разогрев посыпается флюсом. Если поверхность металла очищается до ртутного блеска, то флюс хороший.
Сварку осуществляют в нижнем положении за один проход с максимально возможной скоростью. Левым способом сваривают детали толщиной до 5 мм, правым – толщиной свыше 5 мм. Сварку плоских конструкций целесообразно выполнять обратноступенчатым методом.
Детали толщиной свыше 10 мм перед сваркой рекомендуется подогреть до температуры 300–350 °C. В качестве присадочного материала используют сварочную проволоку одиннадцати марок (СвАК5, СвАМц, СвАМг3 и др.).
Пламя газовой горелки нормальное, его тепловую мощность выбирают исходя из расхода ацетилена 75 дм3/ч на 1 мм толщины металла. Сварку ведут с расположением мундштука горелки под углом 20–40°, а прутка – под углом 40–60° к плоскости детали. При сварке нужно постоянно помешивать (или щупать – при подогреве) концом прутка ванну. Прочность сварного шва составляет 70–90 % от прочности основного металла. Чтобы флюс не разъедал алюминий, после сварки его удаляют промывкой горячей водой или пятиминутным травлением в 2 %-ном растворе хромовой кислоты при температуре 80 °C. При обнаружении на поверхности белого налета промывку повторяют.
Показать оглавление Скрыть оглавлениеogrik2.ru
Сварка алюминия аргоном своими руками (фото и видео)
Сварка алюминия аргоном — сложный технологический процесс, требующий специального оборудования, определенных знаний и опыта. Успех производства зависит от многих факторов: марки алюминия, качества оборудования, соблюдения рекомендованных режимов, мастерства сварщика.

Схема аргонной сварки.
Алюминиевые сплавы
Достоинствами алюминия являются легкость, податливость механической обработке, высокие показатели электро- и теплопроводности. Эти качества делают его популярным материалом, используемым в различных сварных изделиях. Однако технология сварки достаточна сложна. Во многом сложность процесса определяется маркой алюминия.
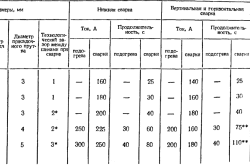
Режимы сварки алюминия в среде аргона.
В зависимости от состава алюминиевые сплавы классифицируются как нетермоупрочняемые и термоупрочняемые. К первой группе относятся:
- технический алюминий;
- сплавы алюминиево-магниевые;
- сплавы алюминиево-марганцевые.
Эти марки алюминия относительно легко поддаются сварке и широко используются в сварных конструкциях.
Ко второй группе относятся сплавы:
- алюминиево-магниево-медные;
- алюминиево-магниево-цинковые;
- алюминиево-марганцево-медные;
- алюминиево-магниево-кремневые и алюминиево-магниево-кремниево-медные;
- алюминиево-магниево-медно-железно-никелевые;
- алюминиево-марганцево-медно-литиево-кадмиевые;
- алюминиево-магниево-медно-цинковые.
Эти марки являются трудносвариваемыми. Их использование в сварных конструкциях имеет смысл лишь тогда, когда предусматривается термическая обработка изделия.
Вернуться к оглавлению
Сложности процесса и способы их преодоления

Рисунок 1. Схема устройства сварочной горелки.
- Покрытие поверхности оксидом Al2O3. Этот налет обладает большей плотностью, чем сам металл и тугоплавкостью. Это затрудняет сплавление кромок, а сварной шов загрязняется оксидом. Перед выполнением сварочных работ кромки должны быть очищены. Оксидная пленка образуется и непосредственно при проведении сварки. Для разрушения Al2O3 на аппаратах постоянного тока устанавливают обратную полярность. Оксид удаляется методом катодного напыления. При переменном токе, разрушение оксида приходится на витки обратной полярности.
- Под воздействием высоких температур прочность алюминия резко падает. Разрушение металла может произойти под весом сварочной ванны. Ее размеры тяжело контролировать визуально, ввиду того, что изменение цвета при нагреве алюминия практически невидимо. Прожог приведет к вытеканию металла через корень шва. Во избежание этого аргонная сварка алюминия производится на керамических или графитовых формирующих подкладках.
- Алюминий склонен к деформации. Избежать коробления можно, используя предварительный подогрев.
- Образование пор на шве под воздействием водорода. Пористость снижает технические характеристики конструкции. Наиболее подвержены образованию пор сплавы АМг. Перед проведением сварочных работ стыкуемые кромки обезжиривают. При сварке толстостенных изделий проводят предварительный подогрев до 200°C.
- Высокая теплопроводность алюминия обуславливает использование мощных источников нагрева. В отдельных случаях необходим предварительный подогрев.
- Образование на шве горячих трещин. Для улучшения структуры шва используются специальные модификаторы.
Вернуться к оглавлению
Оборудование для сварки и рекомендуемые режимы

Схема устройства электрода.
Аргоннодуговая сварка производится на специальном оборудовании. Схема устройства горелки и принцип действия показаны на рис.1.
Аргонодуговая сварка алюминия выполняется неплавящимися или плавящимися электродами. Газ препятствует попаданию в зону сварки кислорода из воздушного пространства, выполняя защитную функцию. Применяют высокосортный аргон. Также возможно использование гелиево-аргоновой смеси или чистого гелия.
Неплавящиеся электроды изготовлены из вольфрама. Они могут быть легированы окислами редкоземельных металлов. Для поверхностей толщиной до 15 мм применяют электроды 2-6 мм и присадки 1-4 мм. Состав присадки определяется маркой алюминиевого сплава. Так, для сварки технического алюминия используют присадки АД, АК, АО. Для сварки сплава АМг подойдет проволока тех же типов, но с повышенным соотношением магния (примерно на 1,5%). Это позволит компенсировать его угар.
Работы производятся аппаратами переменного тока. К таким относятся модификации установки УДГ. Разность потенциалов дуги составляет 15-20 В, а если вместо аргона используется гелий — 25-30 В. Расход аргона в минуту — 6-15 л. Для гелия этот показатель примерно в 2 раза выше.
Сварка листов до 3 мм выполняется одним проходом без разделки. Детали толщиной 4-6 мм сваривается двумя проходами с разных сторон. Для более толстых кромок необходима разделка. При сваривании листов от 8 мм количество проходов увеличивается до 4.
При ручной сварке необходимо уделять внимание технике проведения работ. Угол между присадкой и электродом должен быть близок к прямому. Подача проволоки осуществляется короткими толчками. Колебания электрода в поперечной плоскости недопустимы. Выступ электрода из горелки — 1-1,5 мм, длина дуги 1,5-2 мм. При расположении горелки в правой руке, а проволоки — в левой, шов накладывается справа налево во избежание перегрева металла.
Использование трехфазной дуги увеличивает производительность примерно в 5 раз. Это позволяет сваривать листы толщиной до 30 мм одним проходом.
При использовании плавящихся электродов аргоннодуговая сварка выполняется на аппаратах постоянного тока. Устанавливается обратная полярность. Для защиты применяется либо чистый аргон, либо гелиево-аргоновая смесь. Оптимальной для создания качественного глубокого шва является смесь аргона и гелия в соотношении 30:70.
Для обеспечения устойчивого переноса капель расплавленного металла на основной ток накладываются электрические импульсы.
expertsvarki.ru
Аргонодуговая сварка алюминиевых и магниевых сплавов в среде защитных газов
Настоящая инструкция распространяется на ручную дуговую сварку в среде аргона алюминиевых и магниевых сплавов.
Инструкцией надлежит руководствоваться при проектировании, разработке технологических процессов, изготовлении, контроле и приемке сварных узлов.
Отступления (ужесточение или снижение требований) от настоящей инструкции могут быть внесены в технологическую документацию на изделие по согласованию с главным технологом и представителем заказчика.
Материалы, оборудование, приспособления, инструмент даны в приложениях №1 и №2.
Выполнение аргонодуговой сварки алюминиевых и магниевых сплавов должно производиться при соблюдение правил техники безопасности, изложенных в инструкции по ТБ.
Подготовка деталей к сварке
Удалить со свариваемых поверхностей деталей масло и другие жировые загрязнения протиркой хлопчатобумажной тканью, смоченной в бензине.
Произвести после обезжиривания дальнейшую подготовку деталей к сварке путем химического травления или механической зачистки свариваемых кромок.
Произвести подготовку сварочной проволоки только химическим травлением.
Произвести химическое травление сварочной проволоки и деталей из алюминиевых и магниевых сплавов согласно соответствующей инструкции. После химической обработки сварочная проволока и детали должны иметь серебристо-матовый цвет. На поверхности не допускается загрязнений и налетов.
Производить механическую зачистку свариваемых деталей с двух сторон до металлического блеска на ширину 15-20 мм с помощью стальной щетки или шабера. На подготовленных к сварке кромках деталей не допускаются заусенцы, трещины, расслоения.
Протереть после механической зачистки кромки деталей хлопчатобумажной тканью, смоченной в бензине.
Использовать подготовленные согласно данной инструкции детали и сварочную проволоку под сварку не позднее: 24 часов – из магниевых сплавов; 72 часов – из алюминиевых сплавов. Для герметичных швов из алюминиевых сплавов использовать проволоку после обработки под сварку только в течение 8-16 ч.
Не допускать не использованные за указанный срок материалы и сварочную проволоку под сварку. Подвергнуть их повторной обработке.
Разрешить химическое травление и зачистку одних и тех же деталей производить не более трех раз.
Хранить очищенные детали в чистом сухом помещении, а очищенную сварочную проволоку, кроме того, в закрытых картонных или деревянных ящиках.
Сборка, прихватка
Произвести сборку и подгонку кромок, деталей из алюминиевых сплавов в соответствии с требованиями ГОСТ 14806-80.
Произвести сборку и подгонку кромок деталей из магниевых сплавов.
Допускать в собранных под сварку стыковых соединениях смещение кромок относительно друг друга не более 0,5 мм для листов толщиной до 5 мм.
Производить сборку под сварку, по возможности, с помощью приспособлений, которые должны обеспечить:
- точность сборки деталей, их надежное закрепление;
- возможность ведения сварки без прихватки свариваемых кромок;
- сопутствующий подогрев, контроль и регулировку температуры в пределах от 200 до 250 °С для магниевых сплавов.
Подогреть перед сборкой деталей рабочие части приспособления хлопчатобумажной тканью, смоченной в бензине.
Собрать и закрепить в приспособлении свариваемые детали.
Рекомендовать перед сваркой швов значительной протяженности для нежестких конструкций предварительный подогрев приспособления до 250-300 °С.
Нагреть детали из магниевых сплавов перед сваркой до 250-300 °С.
Произвести в случае необходимости, прихватку кромок свариваемых деталей, согласно таблицы 1.
Толщина свариваемого материала, мм | до 1,5 | 2,0-6,0 |
Длина прихваток | 10-15 | 20-25 |
Расстояние между прихватками, мм | 80-100 | 100-150 |
Произвести тщательную зачистку прихваток перед началом сварки с помощью стальной щетки.
Сборка, прихватка
Допускать к выполнению сварочных работ дипломированных сварщиков, имеющих право на производство работ по сварке алюминиевых и магниевых сплавов.
Производить сварку необходимо путем непрерывного перемещения вольфрамового электрода, вдоль оси шва без остановок на отдельных участках.
В случае вынужденного обрыва дуги необходимо зачистить конец шва металлической щеткой.
Закрепить вольфрамовый электрод в сварочной горелке таким образом, чтобы вылет его из сопла горелки не превышал при сварке стыковых соединений 4 мм, а при сварке угловых и тавровых соединений – 6 мм.
Наклонить горелку при сварке в сторону противоположную направлению сварки таким образом, чтобы ось вольфрамового электрода составляла с осью сварного шва 70-80°.
Вносить в зону сварки сварочную проволоку таким образом, чтобы угол между вольфрамовым электродом и проволокой составлял примерно 90°.
Производить сварку при длине дуги 10-15 мм.
Задержать при обрыве дуги в процессе сварки горелку над швом на 4-5 сек для предупреждения возможного окисления шва.
«Пролудить» обратную сторону шва после сварки основного шва в угловых и стыковых односторонних соединениях, сваренных из алюминиевых сплавов.
Производить пролудку на режиме, пониженном по сравнению с режимом для основного шва примерно на 20 % без применения сварочной проволоки.
Производить пролудку обратной стороны шва для магниевых сплавов рекомендуется при сварке деталей толщиной более 2-х мм.
Выполнять сварку многопроходных швов руководствуясь следующими указаниями:
- производить сварку первого прохода на пониженных режимах;
- зачищать металлической щеткой сварной шов после каждого выполненного прохода и производить контроль внешним осмотром согласно разделам «Контроль качества сварных соединений»;
- устранить обнаруженные дефекты, приступить к выполнению следующего прохода.
Вынуть сварной узел из приспособления после его сварки и остывания и зачистить сварной шов стальной щеткой.
Произвести контроль ОТК сварных конструкций после окончания работ согласно разделам «Контроль качества сварных соединений».
Направить узлы из магниевых сплавов на отжиг согласно разделу «Термическая обработка».
Ориентировочные режимы сварки приведены в таблицах 2 и 3.
У1С1С2 | 0,8 | 1,5-2 | 1,0 | 4-5 | 50-75 | 40-45 | 1 |
1,0 | 1,5-2 | 1,0 | 4-5 | 50-75 | 45-55 | 1 | |
1,5 | 2 | 1-2 | 5-6 | 60-90 | 70-85 | 1 | |
2,0 | 2 | 1-2 | 5-6 | 60-90 | 85-100 | 1 | |
С3 | 0,8-1 | 1,5-2 | 1,0 | 5-6 | 60-90 | 55-60 | 1 |
2 | 2 | 1-2 | 5-6 | 60-90 | 70-75 | 1 | |
3 | 3 | 2-5 | 7-8 | 85-120 | 100-120 | 1 | |
4 | 4 | 3-4 | 7-8 | 85-120 | 120-150 | 1-2 | |
С7 | 3 | 3 | 2-3 | 7-8 | 120-140 | 100-120 | 1 |
4 | 4 | 3-4 | 7-8 | 170-240 | 120-150 | 1-2 | |
5 | 5 | 4-5 | 7-8 | 170-240 | 170-200 | 1-2 | |
6 | 5 | 4-5 | 8-9 | 170-240 | 220-250 | 1-2 | |
С8С18 | 5 | 4 | 4 | 5-6 | 70-100 | 180-200 | 1-2 |
6 | 5 | 4-5 | 5-6 | 80-120 | 220-240 | 1-2 | |
8 | 5 | 4-5 | 7-8 | 150-300 | 250-270 | 3-4 | |
10 | 5 | 4-5 | 7-8 | 240-450 | 280-300 | 4-5 | |
20 | 5 | 4-5 | 10-12 | 400-600 | 300-320 | 5-6 | |
С11С31 | 5 | 4 | 3-4 | 7-8 | 170-240 | 180-200 | 1-2 |
6 | 5 | 3-4 | 7-8 | 170-360 | 220-240 | 1-2 | |
8 | 5 | 4-5 | 9-10 | 325-600 | 250-270 | 3-4 | |
10 | 5 | 4-5 | 10-12 | 480-700 | 280-300 | 4-5 | |
20 | 5 | 4-5 | 10-12 | 600-900 | 300-320 | 5-6 | |
Н1Н2Н3 | 1,5-2 | 2 | 1,5-2 | 5-6 | 60-90 | 80-100 | 1 |
4 | 3 | 3-4 | 7-8 | 85-120 | 120-150 | 1-2 | |
5-6 | 4 | 3-4 | 8-9 | 95-135 | 170-200 | 1-2 | |
7-8 | 4-5 | 4-5 | 9-10 | 110-150 | 240-270 | 2-3 | |
10 | 4-5 | 4-5 | 9-10 | 110-150 | 280-300 | 4-5 | |
20 | 4-5 | 4-5 | 10-12 | 120-170 | 300-320 | 5-6 | |
Т1Т5 | 1,5-2 | 2 | 1,5-2 | 5-6 | 100-120 | 80-100 | 1 |
3-4 | 3 | 1,5-2 | 7-8 | 170-190 | 120-150 | 1 | |
5-6 | 4 | 3-4 | 7-8 | 200-260 | 170-200 | 1-2 | |
7-8 | 4-5 | 3-4 | 7-8 | 290-300 | 240-270 | 2-3 | |
10 | 4-5 | 4-5 | 9-10 | 300-320 | 270-300 | 4-5 | |
Т2Т3Т4 | 1,5-2 | 2 | 1,5-2 | 5-6 | 100-120 | 80-100 | 1 |
3-4 | 3 | 1,5-2 | 7-8 | 170-190 | 120-150 | 1 | |
5-6 | 4 | 3-4 | 7-8 | 200-260 | 170-200 | 1-2 | |
7-8 | 4-5 | 3-4 | 7-8 | 290-300 | 240-270 | 2-3 | |
10 | 4-5 | 4-5 | 9-10 | 300-320 | 270-300 | 3-4 | |
У3У4У5 | 1 | 1,5-2 | 1-2 | 5-6 | 70-80 | 70-80 | 1 |
1,5 | 2 | 2 | 5-6 | 80-100 | 80-95 | 1 | |
2 | 2-3 | 2-3 | 5-6 | 85-120 | 100-120 | 1 | |
3 | 3 | 2-3 | 7-8 | 100-120 | 200-220 | 1-2 | |
4 | 4 | 3-4 | 7-8 | 100-120 | 200-220 | 1-2 | |
6 | 5 | 4-5 | 9-10 | 110-150 | 260-270 | 2-3 | |
10 | 5 | 4-5 | 9-10 | 110-150 | 270-290 | 3 | |
12 | 5 | 4-5 | 9-10 | 120-160 | 300-320 | 3-4 | |
У6У7 | 5 | 4 | 3-4 | 7-8 | 100-120 | 200-220 | 1-2 |
6 | 4 | 4-5 | 7-8 | 110-150 | 240-260 | 1-2 | |
8 | 4-5 | 4-5 | 8-9 | 120-170 | 270-290 | 3-4 | |
10 | 5 | 4-5 | 9-10 | 130-180 | 290-300 | 3-4 | |
20 | 5 | 5 | 10-12 | 160-200 | 300-320 | 4-5 |
Примечание — Сварка всех сварных швов алюминиевых сплавов независимо от типа соединения выполняется сварочной проволокой.
1,0 | 70-90 | 1 | 1,6 | 7-8 | 1,6 | 8 |
1,5 | 80-115 | 1 | 1,6 | 8-9 | 2,0 | 8-10 |
2,0 | 90-120 | 1 | 1,6-2,0 | 9-10 | 3,0 | 8-10 |
2,5 | 110-140 | 1 | 1,6-2,0 | 11-12 | 3,0 | 8-10 |
3,0 | 120-180 | 1 | 1,5-3,0 | 11-12 | 4,0 | 10-12 |
5,0 | 180-240 | 1 | 3-4 | 12-13 | 4,0 | 10-12 |
10 | 220-260 | 2-3 | 3-4 | 12-13 | 5,0 | 12-14 |
15-20 | 260-400 | 2-5 | 4-5 | 13-18 | 5,0-6,0 | 12-18 |
Контроль качества сварных соединений из алюминиевых сплавов
Выполнить сплошной контроль сварных швов и околошовной зоны внешним осмотром непосредственно после сварки, а также после пескоструйной обработки, если таковая впоследствии имеет место.
Произвести осмотр сварных швов по всей их длине с обеих сторон.
Произвести разбраковку дефектов сварных швов согласно таблице 4.
Непровары | Не допускаются, устраняются повторной сваркой |
Прожоги суммарной длиной не более 10 мм на 100 мм шва и шириной или диаметром не более ширины шва | Не допускаются, после механической зачистки устраняются повторной сваркой |
Проплавы в стыковых тавровых и нахлесточных соединениях, не мешающие элементам дальнейшей сборки и не представляющие собой пористого провисания материала | Допускаются |
Натеки наплавленного металла на основной металл | Не допускаются, удаляются зачисткой или другой механической обработкой по всей длине шва |
Подрезы швов | Допускаются, если их суммарная длина не превышает 5 % длины шва. Допустимая глубина подреза не должна превышать 10 % наименьшей свариваемой толщины |
Трещины в сварных швах и околошовной зоне | Не допускаются, устраняются повторной заваркой с предварительной разделкой механическим путем после полной выборки дефектного материала |
Произвести разбраковку сварных швов по количеству и размерам пор согласно таблице 5.
1,0 | 0,5 | Не менее 10 | Не более 3 | 0,6 |
1,5 | 0,8 | Не менее 10 | Не более 3 | 1,4 |
2,0 | 1,0 | Не менее 10 | Не более 3 | 2,4 |
3,0 | 1,5 | Не менее 10 | Не более 3 | 3,4 |
4-6 | 2-6 | Не менее 10 | Не более 3 | 6 |
8-10 | 4-5 | Не менее 10 | Не более 3 | 10 |
Примечание — Допускается подварка одного и того же участка шва не более двух раз. Считать браком узлы и детали, имеющие дефекты, размеры которых превышают размеры дефектов, указанных в таблице 5.
Контроль качества сварных соединений из магниевых сплавов
Выполнить сплошной контроль качества сварных швов внешним осмотром после окончания сварки.
Произвести осмотр сварных швов по всей длине с обеих сторон.
Произвести разбраковку дефектов сварных швов согласно требованиям таблицы 6.
Подваривать дефектные участки сварных швов допускается не более двух раз.
Забраковать окончательно сварные узлы, имеющие в сварных швах дефекты, размеры которых не более допустимых к исправлению.
Непровары любой протяженности | Устранить подваркой |
Продольные или поперечные трещины, обнаруженные до и после механической обработки сварных швов | Устранить подваркой |
Прожоги, если их суммарная протяженность не превышает 10 мм на 100 мм шва | Устранить подваркой |
Поры, выходящие на поверхность шва, обнаруженные до и после механической обработки, диаметром до 0,2δ (но не более 2 мм) не более 2-х шт на 100 мм шва(δ – наименьшая толщина свариваемых деталей) | ДопускаютсяВ остальных случаях устранить подваркой |
Занижение размеров шва относительно требований чертежа | Устранить подваркой |
Завышение размеров шва относительно требований чертежа не мешающие элементам сборки изделия | ДопускаютсяВ остальных случаях устранить механической обработкой |
Вольфрамовые включения, выходящие на поверхность шва, обнаруженные до или после механической обработки | Вырубить включения и подварить |
Свищи, незаваренные кратеры, раковины | Устранить подваркой |
Проплав в стыковых и угловых швах, не мешающий элементам дальнейшей сборки и не представляющий пористого провиса металла | Допускаются |
Термическая обработка
Допустить к отжигу сварные конструкции, прошедшие контроль согласно разделу «Контроль качества сварных соединений».
Протереть перед отжигом поверхность изделий хлопчатобумажной тканью, смоченной в бензине.
Производить отжиг следует не позднее, чем через 72 ч после начала сварки.
Производить отжиг конструкций технологических оправках или в приспособлениях рекомендуется с целью сохранения заданных чертежей размеров и форм.
Производить все операции по загрузке и выгрузке отжигаемых узлов в печь в чистых трикотажных перчатках.
Производить отжиг изделий в электропечах с автоматической регулировкой температуры.
Режим отжига:
- Температура 250-300 °С;
- Время выдержки 0,5-2,0 ч.
Конкретное время отжига зависит от толщины отжигаемых изделий, определяется технологом, сварщиком и указывается в технологическом процессе.
Производить загрузку и выгрузку изделий из электропечи при температуре печей 150-200 °С.
Произвести, в случае необходимости, правку изделий после отжига.
Производить правку при температуре изделий не ниже 120 °С.
После правки изделия могут быть подвергнуты механической доработке в соответствие с требованиями чертежа.
Произвести повторной сплошной контроль готовых изделий в соответствии с требованиями чертежа.
Производить отжиг на весь технологический цикл изготовления изделий допускается не более трех раз.
Вспомогательные материалы
- Вольфрам лантанированный в виде продуктов ТУ-48-19-27-72.
- Аргон газообразный высший сорт или первый сорт. ГОСТ 10157-73.
- Проволока сварочная см. таблицу 7.
- Бензин авиационный Б 70 ГОСТ 1012-72.
- Ткань хлопчатобумажная ГОСТ 11680-76.
- Перчатки трикотажные ГОСТ 1108-74.
- Бензин А-76 ГОСТ 2084-77 и «Галоша» ТУ 38-401-67-108-92.
Сплав АМГ | СВАМ-5 | ГОСТ 7871-75 |
Сплав АМц | СвАМц | ГОСТ 7871-75 |
Сплав МА1 | МА8 | ОСТ 190116-74 |
Сплав МА1 и МА8 | МА2-1 | ОСТ 190116-74 |
Сплав МА8 | МА2-1 | ОСТ 190116-74 |
Оборудование, приспособления и инструмент
- Установка переменного тока для аргоно-дуговой сварки типа УДГ-301, УДГ-501 или УДАР-300, УДАР-500 с комплектом сварочных горелок, цанг и сопел.
- Печь электрическая с автоматической регулировкой температуры.
- Ротаметр типа РМ-I или РМ-IУ ГОСТ 13045-67.
- Редуктор кислородный типа РК-30 или РК-50 или КР-14 ГОСТ 6268-78.
- Манометр низкого давления (0,2 МПа) ГОСТ 6521-72.
- Шлем-маска защитная сварочная с набором защитных сварочных стекол ЭС-100, ЭС-300, ЭС-500 ГОСТ 1361-69.
- Очки герметичные защитные ГОСТ 9496-60.
- Щетки стальные из нержавеющей проволоки ∅0,2-0,3 мм для зачистки деталей и металла шва.
- Лупа 5-х ГОСТ 8309-75 или ГОСТ 7594-75.
- Сборочно-сварочные приспособления, обеспечивающие:
- точность сборки деталей под сварку и их надежное закрепление;
- возможность формирования обратного валика, приспособление для отжига деталей и узлов после сварки.
- Шаблоны специальные и шаблоны радиусные ГОСТ 4126-66.
- Штангенциркуль тип I-Ш ГОСТ 166-73.
- Линейка металлическая измерительная ГОСТ 427-75.
weldworld.ru
Сварка алюминия: ручная аргонодуговая и полуавтоматическая
Алюминий имеет множество достоинств и один серьезный недостаток – его трудно варить.Самый оптимальный метод – сварка алюминия аргоном.
Термическая обработка алюминиевых поверхностей в инертной среде

Сварка алюминия это высший пилотаж
Сложность для термообработки алюминия объясняется его особенностями:
- Сам металл правится при температуре 660°C, а пленка его окислов – при 2044°C;
- Пленка окислов есть всегда, поскольку алюминий – один из самых химически активных металлов;
- У алюминия высокий коэффициент линейного расширения. Из-за этого металл сильно усаживается, шов деформируется.
Термическая обработка металла в инертном газе, принцип
Термин «дуговая» («электродуговая») сварка означает, что термическая обработка осуществляется посредством электрической дуги. Дуга возникает между двумя электродами. Первый электрод – рабочий элемент сварочного аппарата (собственно стержень, которым варят), второй – поверхность металла, которую вы обрабатываете. Металл плавится, образуется «сварочная ванна». Как это выглядит, можно посмотреть на видео – красивое зрелище. Чтобы металл не горел и не окислялся, вступая во взаимодействие с кислородом воздуха, в зону обработки из аппарата подается инертный газ – аргон, гелий или их смесь. Получается аргонная прослойка, сварочная ванна оказывается закрыта от атмосферного кислорода химически инертным защитным слоем – аргоном. Отсюда еще одно название – аргонодуговая.
При этом можно использовать электрод либо только как источник тепла (неплавящийся стержень, неметаллический либо из тугоплавкого металла), либо еще и в качестве присадочного материала (плавящийся стержень, металлическая проволока). Первая технология называется TIG (tungsten inert gas, ручная дуговая сварка, используется вольфрамовый электрод), вторая – MIG/MAG (Metal Inert Gas / Metal Active Gas), полуавтоматическая сварка. Полуавтоматическая – потому что электрод (он же присадочная проволока) подается из аппарата автоматически, то есть, не все процессы осуществляются вручную (имеет смысл посмотреть работу полуавтомата на видео).
Дуговая сварка алюминия может осуществляться как вольфрамовым электродом, так и плавящимся (алюминиевой проволокой). В первом случае присадочная проволока из алюминия подбирается отдельно.
Технология MIG/MAG существенно проще в исполнении, ей после некоторой тренировки может овладеть новичок. И скорость работы получается гораздо выше. Но лучшее качество шва обеспечивает аргонодуговая сварка алюминия методом TIG.
Оборудование
- Аппараты для аргонно-дуговой сварки.
- Сварочные аппараты полуавтоматические инверторные.
При выборе аппарата нужно обращать внимание на характер подачи тока. Аппарат TIG для аргонно-дуговой сварки должен иметь пометку AC (это значит, что он работает на переменном токе) или AC+DC (переменный и постоянный). Во втором случае оборудование можно будет использовать для любого металла, но стоит оно дорого.
Варить по методу TIG постоянным током нельзя.

Прочный и красивый шов это визитка сварщика
Для присадки берется проволока из алюминия АК, АО, АД если нужно варить чистый алюминий. Для сплавов подбираются проволоки в зависимости от состава сплава.
Полуавтомат MIG для аргонно-дуговой сварки имеет пометку DC. Сварка происходит постоянным током с обратной полярностью.
Сила тока зависит от диаметра электрода:
- 4 мм – 130 А
- 5 мм – 160 А
- 6 мм – 220 А.
Чистый алюминий варят электродом из алюминия АД1 и АВ2Т, сплавы – проволокой Св.АКЗ и Св.АК10.
Еще одна особенность алюминия – высокая тепло- и электропроводность. Поэтому сварочный ток должен быть большим, гораздо выше, чем для стали.
Толщина электрода тем меньше, чем меньше толщина свариваемого металла. Работать с аппаратурой TIG в принципе сложнее, чем с полуавтоматами, поэтому если речь идет о листах тоньше 4 мм и совсем тонком электроде, лучше воспользоваться полуавтоматом. Чтобы освоиться с ним, нужно посмотреть видео.
Рабочий процесс
- Перед обработкой поверхность нужно очистить стальной щеткой от грязи и обезжирить ацетоном, бензином или еще каким-нибудь растворителем.
- Если толщина листа больше 4 мм, нужно провести разделку кромок (сделать отбортовку). Дуговая сварка тонких листов может производиться без разделки кромок. Очистить на кромках оксидную пленку (подойдет напильник, металлическая щетка с тонким ворсом, напильник).
- Во избежание прожогов (в первую очередь это касается тонких листов) под алюминий нужно помещать медную или стальную подложку.
- Аргонно-дуговая сварка TIG проводится короткой дугой (до 2,5 мм). Угол между электродом и листом – 70-80 градусов, между электродом и проволокой – 90. Проволока движется впереди электрода (этот процесс показан в обучающих видео).
- Аргонно-дуговая сварка MIG проводится с предварительным нагревом при толщине листа до 9 мм – до 250°С, свыше 9 – до 350.
- Варить следует в вертикальном или нижнем положении, дуга должна быть как можно короче, без поперечных штрихов (смотрите видео).
Сразу по окончании шлак нужно смыть горячей водой с помощью стальных щеток.
zavarimne.ru
Режимы автоматической аргонодуговой сварки стыковых соединений алюминия и его сплавов
Ориентировочные режимы механизированной аргонодуговой сварки алюминия и сплавов на его основе приведены в табл. 84—86.
Для аргонодуговой сварки алюминия и его сплавов используют те же проволоки, что и для сварки по флюсу.
Таблица 84. Ориентировочные режимы автоматической аргонодуговой сварки стыковых соединений алюминия и его сплавов вольфрамовым электродом с присадкой проволоки диаметром 2 мм.
Толщина металла, мм | Диаметр электрода, мм | Iсв А | Vэл м/час | Vсв м/час | Расход аргона, л/мин |
2 | 3-4 | 170—180 | 54 | 19 | 16—18 |
3 | 4—5 | 200—220 | 20—24 | 15 | 16—18 |
4 | 4-5 | 210—235 | 20—24 | 11 | 18—20 |
6 | 4—5 | 230—260 | 20-26 | 8 | 18—20 |
Примечание. Сварка соединений из металла толщиной 6 мм о односторонней разделкой кромок выполняется двусторонним швом.
Таблица 85. Ориентировочные режимы полуавтоматической аргонодуговой сварки стыковых соединений алюминия и его сплавов плавящимся электродом.
Толщина металла, мм | Подготовка кромок | Диаметр проволоки, мм | Iсв А | Vсв м/час | Vэл м/час | Расход аргона, л/мин | Число слоев шва |
1,6 | Без разделки, без зазора | 0,5—0,75 | 70—75* | 30 | 1200—1800 | 15—17 | 1 |
2,0 | 0,5-0,75 | 75—105* | 30 | 1200—1800 | 15—17 | 1 | |
3,0 | 0,5—0,75 | 120—145* | 30 | 1200—1800 | 15—17 |
| |
3,0 | 1,5 | 150—160 | 36 | 290—300 | 15—17 |
| |
4,0 | 1,5 | 160—190 | 28 | 300—320 | 15—17 | 1 | |
5,0 | Без разделки, с зазором 1,5 мм | 1,5 | 180—200 | 22 | 320—350 | 15—18 | 1 |
8,0 | V-образная разделка с углом раскрытия 60° | 1,5—2,0 | 270—280 | 36 | 340—360 | 15—18 | 2 |
20,0 | 2,0 | 240—300 | 18 | 240—270 | 15—18 | 2—4 |
* Дуга питается от источника тока о возрастающей характеристикой, в остальных случаях — от источника тока с падающей характеристикой.
Медь сваривают под флюсом, состоящим из смеси древесного угля, феррофосфора, алюминиевого порошка, ферросилиция и ферромарганца.
Для сварки мышьяковистой меди угольным электродом в качестве присадки рекомендуется применять медную проволоку, содержащую 3% кремния и 1% марганца.
При сварке меди вольфрамовым электродом в качестве присадки используется медная проволока, содержащая примерно 0,1 % титана, или проволока, содержащая 0,2% титана и 0,1% алюминия. Тонкую медь в большинстве случаев сваривают на графитовой или асбестовой подкладке.
Таблица 86. Ориентировочные режимы автоматической аргонодуговой сварки алюминия и его сплавов плавящимся электродом.
Толщина металла, мм | Подготовка кромок | Диаметр проволоки,мм | Iсв А | Vсв м/час | Vэл м/час | Расход аргона, л/мин | Число слоев шва |
31 | Без разделки, без зазора | 2,0 | 150—160 | 30 | 210 | 15 | 1 |
4 | 1,6—2,0 | 150—200 | 20—36 | 210—240 | 15 | 1 | |
5 | Без разделки, с зазором до 1,5 мм | 2,0 | 170—185 | 32 | 210 | 18 | 1 |
6 | 1,6-2,0 | 140—220 | 20—36 | 210—250 | 18 | 1 | |
8 | V-образная с углом раскрытия 60 | 2,0—2,5 | 260—290 | 18—20 | 160—210 | 18 | 2 |
10 | 2,0—2,5 | 260—300 | 20—25 | 160—240 | 18—20 | 2 | |
15 | 2,0—2,5 | 290—300 | 14—18 | 160—245 | 18—20 | 2—4 | |
20 | 2,0—2,5 | 290—300 | 15—20 | 160—270 | 18—20 | 3—5 | |
Свыше 20 | Х-образная с углом раскрытия 60° | 2,0—2,5 | 290—300 | 9—18 | 160—270 | 18—20 | 4 и более |
Примечание. Листы толщиной 8—10 мм можно сваривать двухдуговой сваркой за один проход без разделки кромок. При двухдуговой сварке сварочный ток удваивается.
www.prosvarky.ru