Типовые режимы термической обработки сталей (Таблица). Как закалить 45 сталь
Термообработка стали 45
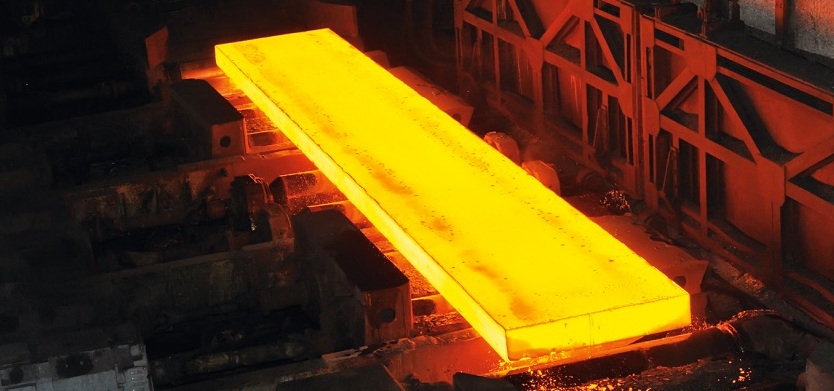
Термообработка стали 45, так же как и термическая обработка любой другой марки стали выполняется для улучшения технических характеристик данного материала. Такая обработка подразумевает первоначальный нагрев металла и последующее его охлаждение. Собственно, в зависимости от времени нагрева материала и скорости охлаждения, термообработка стали 45 и других марок подразделяется на 3 последовательно выполняемых операции:
- Отжиг стали 45
- Закалка стали 45
- Отпуск стали 45
Отжиг стали 45 — это нагрев материала в специальной печи до очень высокой температуры и последующее его охлаждение, которое выполняется естественным образом, то есть вместе с печью. Существует отжиг первого рода, при котором нагрев идет до критических значений, но не превышает их. Также существует и отжиг второго рода, при котором температура уже превышает критическую отметку и приводит к некоторым изменениям в структуре.
Так или иначе, любой из данных способов позволяет избавиться от неоднородности состава, а также снять внутреннее напряжение материала и достичь зернистой структуры. Кроме того, проведение отжига стали 45 поможет снизить твердость сплава, что значительно облегчит в дальнейшем процесс переработки. Примечательно, что отжиг второго рода подразделяется на несколько следующих категорий, различающихся по их назначению и исполнению:
- диффузионный отжиг
- полный отжиг
- неполный отжиг
- изотермический отжиг
- рекристализационный
Как правило, для углеродистых сталей применяется полный отжиг. Суть данной технологии состоит в том, что заготовки нагреваются до температуры, которая превышает критическую отметку (верхняя точка Ас3) примерно на значение от +30°С до +50°С. После этого сталь 45 охлаждают с медленной скоростью от +150°С до +200°С до тех пор, пока ее температура не сравняется со значением температуры в рабочем интервале от +500°С до +550°С.
Кстати говоря, при отжиге первого и второго рода охлаждение материала происходит в печи, в которой был произведен нагрев. Если же процесс охлаждения производят уже на открытом воздухе, то такая технология будет называться не отжиг стали 45, а нормализация. Поскольку при нормализации стали охлаждение происходит быстрее, перлит получает тонкое строение и наибольшую твердость. Поэтому нормализованная сталь тверже отожженной.
Закалка стали 45
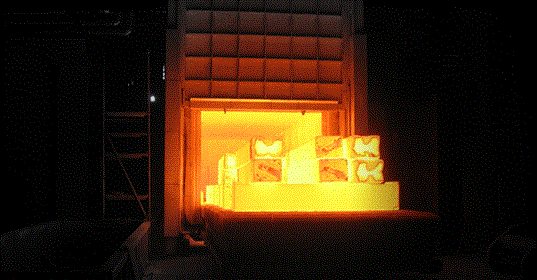
В целом, отжиг стали или же ее нормализация являются подготовкой сплава к последующим процессам термообработки. Вторым по счету процессом обработки идет закалка стали 45. С виду может показаться, что этот этап полностью дублирует отжиг и нормализацию: Закалка стали 45 также состоит из двух основных технологических операций: нагрева и охлаждения. Однако у него имеются свои довольно важные отличительные характеристики.
Если быть точнее, то этой важной отличительной чертой будет скорость охлаждения стали. В случае с закалкой стали 45 заготовка сперва нагревается до температуры, которая превышает критическую. После этого сталь будет сразу же охлаждена в специальной жидкости. В роли такой жидкости может выступать чистая вода, вода с растворами солей, вода с содержанием в составе 5%-й каустической соды, либо же различные минеральные масла (рис. 1)
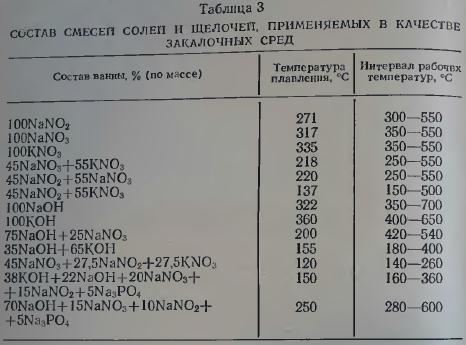
Закалка стали 45 в воде производится при температуре жидкости от +20°С до +30°С. Если в качестве закалочной среды используют раствор каустической соды, то его температура будет составлять от +50°С до +60°С. Температура закалки стали 45, при которой этот материал помещают в охлаждающую жидкость, составляет от +820°С до +860°С. Визуально подобные температуры соответствует диапазону от светло-красного до темно-оранжевого цвета.
Устройство для нагрева стали |
Температура нагрева стали |
Печь |
От +820°С до +860°С |
ТВЧ |
От +880°С до +920°С |
Несмотря на то, что при использовании ТВЧ нагрев стали 45 нужно выполнять до чуть более высоких температур, как такового перегрева материала не происходит. Размер и структура у зерна остается прежним, так как для нагрева через ТВЧ требуется намного меньше времени. Кстати говоря, с помощью проведения закалки токами высокой частоты, твердость стали 45 возрастает по шкале Роквелла (HRC) возрастает приблизительно на 2-3 единицы.
При нагреве стали 45 до температуры, превышающей критическое значение на отметку в +30°С — +50°С, материал достигнет своего аустенитного состояния. Иначе говоря, атомная решетка железа (Fe) изменит объемно-центрированной вид на решетку гранецентрированной формы. Углерод (С), содержащийся в перлите как кристаллы соединения Fe3C (цементита) примет вид твердого раствора — атомы внедрятся в гранецентрированную решетку.
После помещения раскаленного материала в охлаждающую ванну для закалки, температура стали 45 очень быстро понижается до значения комнатной от +20°С до +25°С. Само собой, в связи с этим в структуре сразу происходит процесс обратной перестройки атомной решетки металла — из гранецентрированной она возвращается в исходную объемно-центрированную. Именно это и придает итоговому материалу высокую твердость и прочность.
Дело в том, что при комнатной температуре рабочей среды атомы будут иметь крайне малую степень подвижности. Поэтому при резком охлаждении они попросту не успевают выйти из состояния раствора и образовать цементит. Получается, что сам углерод силой удерживается в решетке железа, тем самым образовывая перенасыщенный твердый раствор. В решетке при этом создается избыточное внутреннее напряжение от атомов углерода.
Они попросту распирают решетку, за счет чего она вытягивается вдоль одного направления. Таким образом, все ячейки из кубической формы переходят в тетрагональную. Иначе говоря, ячейки решетки образуют форму прямоугольной призмы (рис. 2). Естественно, это влияет на структуру материала, которая становится игольчатой. Подобную игольчатую конфигурацию у материала принято называть специальным термином — мартенсит.
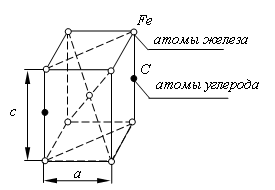
Сами кристаллы мартенсита имеют вид пластин с небольшой толщиной. Если рассматривать данные пластины в поперечном сечении микрошлифа, то они будут иметь форму игл. Кстати, раствор мартенсит отличается достаточно высокими показателями по твердости и прочности. В первую очередь, это объясняется тем, что удельный объем мартенсита будет чуть больше в сравнении с удельным объемом аустенита, из которого он образован.
Это объясняется тем, что образование самого мартенсита обуславливается возникновением в кристаллах мартенсита множества дислокаций, которые образуются за счет большого числа внутренних напряжений. Напряжения вызваны тем, что возникающая пластина мартенсита воздействует на аустенит, который, в свою очередь, отвечает уже обратным сопротивлением к мартенситу, создавая тем самым ответное давление к данной пластине.
Таким образом, при попытке деформировать закаленную сталь с мартенситной структурой, можно встретить серьезное препятствие. Этим препятствием будут движущиеся в различных направлениях дислокации, которые взаимно блокируют друг друга, не давая перемещаться. Именно эти препятствия передвижения дислокаций увеличивают сопротивление деформации материала, соответственно, увеличивая степень твердости и прочности.
Кроме того, с учетом воздействия внутренних напряжений, кристаллы мартенсита образуют раздельные блоки (рис. 3). При этом те плоскости, которые должны быть параллельными в пределах одного кристалла, на самом деле имеют искажение под небольшим углом. Но такие искажения у атомной решетки как раз и оказывают препятствие к перемещению дислокаций. За счет этих особенностей мартенсита сталь и имеет высокую прочность.
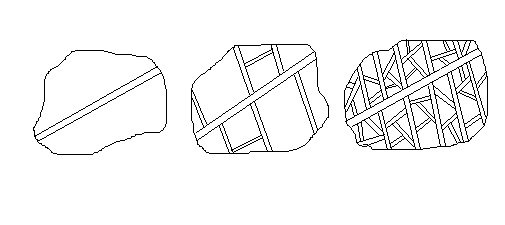
Отпуск стали 45
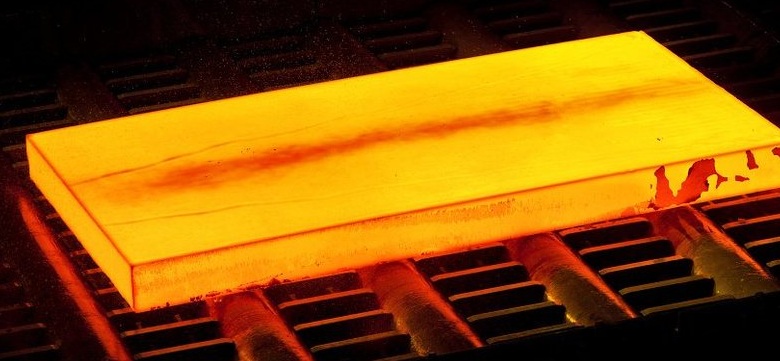
Отпуск стали 45 производят сразу после этапа закалки. Эта разновидность термообработки нужна для того, чтобы существенно уменьшить или полностью снять остаточное напряжение в материале, которое появилось после изменения структуры посредством его закаливания. В целом, отпуск стали 45 позволяет также повысить вязкость заготовок и уменьшить степень их хрупкости. Однако этот процесс немного уменьшает твердость стали.
Технология процесса отпуска стали 45, в зависимости от температуры, выполняется через:
- печи с принудительной циркуляцией воздуха;
- специальные ванны с селитровым раствором;
- специальные ванны с минеральным маслом;
- ванны, заполненные расплавленной щелочью.
Принцип отпуска стали 45 состоит в том, что материал первоначально нагревают до отметки ниже, чем критический уровень, а после этого охлаждают. Однако такой режим термической обработки имеет несколько различных способов проведения, которые будут отличаться друг от друга в зависимости от скорости охлаждения заготовки и температуры её нагрева. Отпуск углеродистых сталей принято классифицировать на 3 следующие категории:
- Высокий. Температура нагрева стали составит от +350°С до +600°С до критической отметки. Как правило, такой метод используют для металлических конструкций.
- Средний. Температура обработки составляет от +350°С до +500°С. Этот способ по большей части используется для пружинных изделий и рессор.
- Низкий. Температура нагрева заготовки не превышает +250°С. Подобный способ принято задействовать для достижения высокой прочности и износостойкости.
Таблица значений термической обработки стали 45
Марка стали |
Твёрдость (HRC) |
Температура закалки, °С |
Температура отпуска, °С |
Температура закалки ТВЧ, °С |
Температура отжига, °С |
Среда закалки |
Сталь 45 |
20…25 |
820…860 |
550…600 |
|
|
Вода |
20…28 |
550…580 |
|
|
|||
24…28 |
500…550 |
|
|
|||
30…34 |
490…520 |
|
|
|||
42…51 |
180…220 |
|
|
|||
49…57 |
200…220 |
880…920 |
|
|||
До 22 |
|
|
780…860 |
Термообработка стали 45, 40х, 20, 30хгса, 65г, 40, 40хн, 35, и стали 20х13
В машиностроении чаще всего подвергают термообработки сталь 45 (в качестве заменителя 40Х, 50, 50Г2), сталь 40х (в качестве заменителя стали 38ха, 40хр, 45х, 40хс, 40хф, 40хн), сталь 20 (в качестве заменителя 15, 25), сталь 30хгса (заменители 40хфа, 35хм, 40хн, 25хгса, 35хгса), сталь 65г, сталь 40хн, сталь 35, и сталь 20х13, также
Термообработка стали 45
Термообработка стали 45 - конструкционная углеродистая. После предварительной термообработки стали 45 - нормализации, довольно легко проходит механическую обработку. Точение, фрезеровку и т. д. Получают детали, например,типа вал-шестерни, коленчатые и распределительные валы, шестерни, шпиндели, бандажи, цилиндры, кулачки.После окончательной термообработки стали 45 (закалка), детали приобретают высокую прочность и износостойкость. Часто шлифуются. Высокое содержание углерода (0,45%) обеспечивает хорошую закаливаемость и соответственно высокую твёрдость поверхности и прочность изделия. Сталь 45 калят «на воду». То есть после калки деталь охлаждают в воде. После олаждения деталь подвегается низкотепмературному отпуску при температуре 200-300 градусов Цельсия. При такой термообработки стали 45 получают твердость порядка 50 HRC.
Термообрабтка стали 45 и применение изделий: Кулачки станочных патронов, согласно указаниям ГОСТ, изготовляют из сталей 45 и 40Х. Твёрдость Rc = 45 -50. В кулачках четырёхкулачных патронов твёрдость резьбы должна быть в пределах Rс = 35-42. Отпуск кулачков из стали 45 производится при температуре 220-280°, из стали 40Х при 380-450° в течение 30-40 мин.
Расшифровка марки стали 45: марка 45 означает, что в стали содержится 0,45% углерода,C 0,42 - 0,5; Si 0,17 - 0,37;Mn 0,5 - 0,8; Ni до 0,25; S до 0,04; P до 0,035; Cr до 0,25; Cu до 0,25; As до 0,08.
Термообработка стали 40Х
Термообработка стали 40Х - легированная конструкционная сталь предназначена для деталей повышенной прочности такие как оси, валы, вал-шестерни, плунжеры, штоки, коленчатые и кулачковые валы, кольца, шпиндели, оправки, рейки, губчатые венцы, болты, полуоси, втулки и прочих деталей повышенной прочности. Сталь 40Х также часто используется для производства поковок, штампованных заготовок и деталей трубопроводной арматуры. Однако последние перечисленные детали нуждаются в дополнительной термической обработке, заключающейся в закалке через воду в масле или просто в масле с последующим отпуском в масле или на воздухе.
Расшифровка марки стали 40Х. Цифра 40 указывает на то, что углерод в стали содержится в объеме 0,4 %. Хрома содержится менее 1,5 %. Помимо обычных примесей в своем составе имеет в определенных количествах специально вводимые элементы, которые призваны обеспечить специально заданные свойства. В качестве легирующего элемента в данном случае используется хром, о чем говорит соответствующая маркировка.
Термообработка стали 20
Термообработка стали 20 - сталь конструкционная углеродистая качественная. Широкое применение в котлостроении, для труб и нагревательных трубопроводов различного назначения, кроме того промышленность выпускает пруток, лист. Температура начала ковки стали 20 составляет 1280° С, окончания - 750° С, охлаждение поковки - воздушное. Сталь 20 нефлокеночувствительна и не склонна к отпускной способности.После цементации и цианирования из стали 20 можно изготавливать детали, от которых требуется высокая твёрдость поверхности и допускается невысокая прочность сердцевины: кулачковые валики, крепёжные детали, шпиндели, звёздочки, шпильки, вилки тяг и валики переключения передач, толкатели клапанов, валики масляных насосов. Сталь 20 применяют для производства малонагруженных деталей ( пальцы, оси, копиры, упоры, шестерни ), цементуемых деталей для длительной и весьма длительной службы (эксплуатация при температуре не выше 350° С), тонких деталей, работающих на истирание и другие детали автотракторного и сельскохозяйственного машиностроения.
Термообработка стали 30хгса
Термообработка стали 30хгса - относится к среднелегированной конструкционной стали. Сталь 30хгса проходит улучшение – закалку с последующим высоким отпуском при 550-600 °С, поэтому применяется при создании улучшаемых деталей (кроме авиационных деталей это могут быть различные корпуса обшивки, оси и валы, лопатки компрессорных машин, которые эксплуатируются при 400°С, и многое другое), рычаги, толкатели, ответственные сварные конструкции, работающие при знакопеременных нагрузках, крепежные детали, работающие при низких температурах.Сталь 30хгса обладает хорошей выносливостью, отличными показателями ударной вязкости, высокой прочностью. Она также отличается замечательной свариваемостью.
Сварка стали 30хгса тоже имеет свои особенности. Она осуществляется с предварительным подогревом материала до 250-300 °С с последующим медленным охлаждением. Данная процедура очень важна, поскольку могут появиться трещины из-за чувствительности стали к резким перепадам температуры после сварки. Поэтому по завершении сварных работ горелка должна отводиться медленно, при этом осуществляя подогрев материала на расстоянии 20-40 мм от места сварки. Также, не более, чем спустя 8 часов по завершении сварки сварные узлы стали 30ХГСА нуждаются в закалке с нагревом до 880 °С с последующим высоким отпуском. Далее изделие охлаждается в масле при 20-50 °С. Отпуск осуществляется нагревом до 400 - 600 °С и охлаждением в горячей воде. Сварку же необходимо выполнять максимально быстро, дабы избежать выгорания легирующих элементов.После прохождения термомеханической низкотемпературной обработки сталь 30хгса приобретает предел прочности до 2800 МПа, ударная вязкость повышается в два раза (в отличии от обычной термообработки стали 30хгса), пластичность увеличивается.
Термообработка стали 65г
Термообработка стали 65г - Сталь конструкционная рессорно-пружинная. Используют в промышленности пружины, рессоры, упорные шайбы, тормозные ленты, фрикционные диски, шестерни, фланцы, корпусы подшипников, зажимные и подающие цанги и другие детали, к которым предъявляются требования повышенной износостойкости, и детали, работающие без ударных нагрузок. (заменители: 70, У8А, 70Г, 60С2А, 9ХС, 50ХФА, 60С2, 55С2).
Термообработка стали 40 - Сталь конструкционная углеродистая качественная. Использование в промышленности: трубы, поковки, крепежные детали, валы, диски, роторы, фланцы, зубчатые колеса, втулки для длительной и весьма длительной службы при температурах до 425 град.
Термообработка стали 40хн - Сталь конструкционная легированная Использование в промышленности: оси, валы, шатуны, зубчатые колеса, валы экскаваторов, муфты, валы-шестерни, шпиндели, болты, рычаги, штоки, цилиндры и другие ответственные нагруженные детали, подвергающиеся вибрационным и динами ческим нагрузкам, к которым предъявляются требования повышенной прочности и вязкости. Валки рельсобалочных и крупносортных станов для горячей прокатки металла.
Термообработка сталь 35 - Сталь конструкционная углеродистая качественная. Использование в промышленности: детали невысокой прочности, испытывающие небольшие напряжения: оси, цилиндры, коленчатые валы, шатуны, шпиндели, звездочки, тяги, ободы, траверсы, валы, бандажи, диски и другие детали.
Термообработка стали 20Х13 - Сталь коррозионно-стойкая жаропрочная. Использование в промышленности: энергетическое машиностроение и печестроение; турбинные лопатки, болты, гайки, арматура крекинг-установок с длительным сроком службы при температурах до 500 град; сталь мартенситного класса Сталь марки 20Х13 и другие стали мартенситного класса: жаропрочные хромистые стали мартенситного класса применяют в различных энергетических установках, они работают при температуре до 600° С. Из них изготовляют роторы, диски и лопатки турбин, в последнее время их используют для кольцевых деталей больших толщин. Существует большое количество марок сталей данного класса. Общим для всех является пониженное содержание хрома, наличие молибдена, ванадия и вольфрама. Они эффективно упрочняются обычными методами термообработки, которая основана на у - a-превращении и предусматривает получение в структуре мартенсита с последующим улучшением в зависимости от требований технических условий. (заменители: 12Х13, 14Х17Н2)
xn--80aafddgcctbhpvrdabo8b4bh1e8f.xn--p1ai
№ п/п | Марка стали | Твёрдость (HRCэ) | Температ. закалки, град.С | Температ. отпуска, град.С | Температ. зак. ТВЧ, град.С | Температ. цемент., град.С | Температ. отжига, град.С | Закал. среда | Прим. |
1 | 2 | 3 | 4 | 5 | 6 | 7 | 8 | 9 | 10 |
1 | Сталь 20 | 57…63 | 790…820 | 160…200 |
| 920…950 |
| Вода |
|
2 | Сталь 35 | 30…34 | 830…840 | 490…510 |
|
|
| Вода |
|
33…35 | 450…500 |
|
|
|
| ||||
42…48 | 180…200 | 860…880 |
|
|
| ||||
3 | Сталь 45 | 20…25 | 820…840 | 550…600 |
|
|
| Вода |
|
20…28 | 550…580 |
|
|
|
| ||||
24…28 | 500…550 |
|
|
|
| ||||
30…34 | 490…520 |
|
|
|
| ||||
42…51 | 180…220 |
|
|
| Сеч. до 40 мм | ||||
49…57 | 200…220 | 840…880 |
|
|
| ||||
<= 22 |
|
|
|
| 780…820 |
| С печью | ||
4 | Сталь 65Г | 28…33 | 790…810 | 550…580 |
|
|
| Масло | Сеч. до 60 мм |
43…49 | 340…380 |
|
|
| Сеч. до 10 мм (пружины) | ||||
55…61 | 160…220 |
|
|
| Сеч. до 30 мм | ||||
5 | Сталь 20Х | 57…63 | 800…820 | 160…200 |
| 900…950 |
| Масло |
|
59…63 |
| 180…220 | 850…870 | 900…950 |
| Водный раствор | 0,2…0,7% поли-акриланида | ||
"-- |
|
|
|
| 840…860 |
|
| ||
6 | Сталь 40Х | 24…28 | 840…860 | 500…550 |
|
|
| Масло |
|
30…34 | 490…520 |
|
|
|
| ||||
47…51 | 180…200 |
|
|
| Сеч. до 30 мм | ||||
47…57 |
| 860…900 |
|
| Водный раствор | 0,2…0,7% поли-акриланида | |||
48…54 |
|
|
|
|
| Азотирование | |||
<= 22 |
|
|
|
| 840…860 |
|
| ||
7 | Сталь 50Х | 25…32 | 830…850 | 550…620 |
|
|
| Масло | Сеч. до 100 мм |
49…55 | 180…200 |
|
|
| Сеч. до 45 мм | ||||
53…59 | 180…200 | 880…900 |
|
| Водный раствор | 0,2…0,7% поли-акриланида | |||
< 20 |
|
|
|
| 860…880 |
|
| ||
8 | Сталь 12ХН3А | 57…63 | 780…800 | 180…200 |
| 900…920 |
| Масло |
|
50…63 |
| 180…200 | 850…870 |
| Водный раствор | 0,2…0,7% поли-акриланида | |||
<= 22 |
|
|
|
| 840…870 |
| С печью до 550…650 | ||
9 | Сталь 38Х2МЮА | 23…29 | 930…950 | 650…670 |
|
|
| Масло | Сеч. до 100 мм |
<= 22 |
| 650…670 |
|
|
|
| Нормализация 930…970 | ||
HV > 670 |
|
|
|
|
|
| Азотирование | ||
10 | Сталь 7ХГ2ВМ | <= 25 |
|
|
|
| 770…790 |
| С печью до 550 |
28…30 | 860…875 | 560…580 |
|
|
| Воздух | Сеч. до 200 мм | ||
58…61 | 210…230 |
|
|
| Сеч. до 120 мм | ||||
11 | Сталь 60С2А | <= 22 |
|
|
|
| 840…860 |
| С печью |
44…51 | 850…870 | 420…480 |
|
|
| Масло | Сеч. до 20 мм | ||
12 | Сталь 35ХГС | <= 22 |
|
|
|
| 880…900 |
| С печью до 500…650 |
50…53 | 870…890 | 180…200 |
|
|
| Масло |
| ||
13 | Сталь 50ХФА | 25…33 | 850…880 | 580…600 |
|
|
| Масло |
|
51…56 | 850…870 | 180…200 |
|
|
| Сеч. до 30 мм | |||
53…59 |
| 180…220 | 880…940 |
|
| Водный раствор | 0,2…0,7% поли-акриланида | ||
14 | Сталь ШХ15 | <= 18 |
|
|
|
| 790…810 |
| С печью до 600 |
59…63 | 840…850 | 160…180 |
|
|
| Масло | Сеч. до 20 мм | ||
51…57 | 300…400 |
|
|
| |||||
42…51 | 400…500 |
|
|
| |||||
15 | Сталь У7, У7А | НВ <= 187 |
|
|
|
| 740…760 |
| С печью до 600 |
44…51 | 800…830 | 300…400 |
|
|
| Вода до 250, масло | Сеч. до 18 мм | ||
55…61 | 200…300 |
|
|
| |||||
61…64 | 160…200 |
|
|
| |||||
61…64 | 160…200 |
|
|
| Масло | Сеч. до 5 мм | |||
16 | Сталь У8, У8А | НВ <= 187 |
|
|
|
| 740…760 |
| С печью до 600 |
37…46 | 790…820 | 400…500 |
|
|
| Вода до 250, масло | Сеч. до 60 мм | ||
61…65 | 160…200 |
|
|
| |||||
61…65 | 160…200 |
|
|
| Масло | Сеч. до 8 мм | |||
61…65 |
| 160…180 | 880…900 |
|
| Водный раствор | 0,2…0,7% поли-акриланида | ||
17 | Сталь У10, У10А | НВ <= 197 |
|
|
|
| 750…770 |
|
|
40…48 | 770…800 | 400…500 |
|
|
| Вода до 250, масло | Сеч. до 60 мм | ||
50…63 | 160…200 |
|
|
| |||||
61…65 | 160…200 |
|
|
| Масло | Сеч. до 8 мм | |||
59…65 |
| 160…180 | 880…900 |
|
| Водный раствор | 0,2…0,7% поли-акриланида | ||
18 | Сталь 9ХС | <= 24 |
|
|
|
| 790…810 |
| С печью до 600 |
45…55 | 860…880 | 450…500 |
|
|
| Масло | Сеч. до 30 мм | ||
40…48 | 500…600 |
|
|
| |||||
59…63 | 180…240 |
|
|
| Сеч. до 40 мм | ||||
19 | Сталь ХВГ | <= 25 |
|
|
|
| 780…800 |
| С печью до 650 |
59…63 | 820…850 | 180…220 |
|
|
| Масло | Сеч. до 60 мм | ||
36…47 | 500…600 |
|
|
| |||||
55…57 | 280…340 |
|
|
| Сеч. до 70 мм | ||||
20 | Сталь Х12М | 61…63 | 1000…1030 | 190…210 |
|
|
| Масло | Сеч. до 140 мм |
57…58 | 320…350 |
|
|
| |||||
21 | Сталь Р6М5 | 18…23 |
|
|
|
| 800…830 |
| С печью до 600 |
64…66 | 1210…1230 | 560…570 3-х кратн. |
|
|
| Масло, воздух | В масле до 300…450 град., воздух до 20 | ||
26…29 | 780…800 |
|
|
|
| Выдержка 2…3 часа, воздух | |||
22 | Сталь Р18 | 18…26 |
|
|
|
| 860…880 |
| С печью до 600 |
62…65 | 1260…1280 | 560…570 3-х кратн. |
|
|
| Масло, воздух | В масле до 150…200 град., воздух до 20 | ||
23 | Пружин. сталь Кл. II |
|
| 250…320 |
|
|
|
| После холодной навивки пружин 30-ть минут |
24 | Сталь 5ХНМ, 5ХНВ | >= 57 | 840…860 | 460…520 |
|
|
| Масло | Сеч. до 100 мм |
42…46 |
|
|
| Сеч. 100..200 мм | |||||
39…43 |
|
|
| Сеч. 200..300 мм | |||||
37…42 |
|
|
| Сеч. 300..500 мм | |||||
НV >= 450 |
|
|
| Азотирование. Сеч. св. 70 мм | |||||
25 | Сталь 30ХГСА | 19…27 | 890…910 | 660…680 |
|
|
| Масло |
|
27…34 | 580…600 |
|
|
|
| ||||
34…39 | 500…540 |
|
|
|
| ||||
"-- |
|
|
|
| 770…790 |
| С печью до 650 | ||
26 | Сталь 12Х18Н9Т | <= 18 | 1100…1150 |
|
|
|
| Вода |
|
27 | Сталь 40ХН2МА, 40ХН2ВА | 30…36 | 840…860 | 600…650 |
|
|
| Масло |
|
34…39 | 550…600 |
|
|
|
| ||||
28 | Сталь ЭИ961Ш | 27…33 | 1000…1010 | 660…690 |
|
|
| Масло | 13Х11Н2В2НФ |
34…39 | 560…590 |
|
|
| При t>6 мм вода | ||||
29 | Сталь 20Х13 | 27…35 | 1050 | 550…600 |
|
|
| Воздух |
|
43,5…50,5 | 200 |
|
|
|
| ||||
30 | Сталь 40Х13 | 49,5…56 | 1000…1050 | 200…300 |
|
|
| Масло |
|
infotables.ru