Какие методы контроля сварных швов существуют и как их используют? Методы контроля сварных соединений
Методы неразрушающего контроля сварных соединений |

Практически с момента изобретения сварки, как метода неразъёмного соединения нескольких деталей, возникла и проблема качества таких соединений. Поскольку расплав в зоне сваривания металлов во многих случаях является материалом с иным химическим составом, к тому же подвергающимся активному воздействию сварочной плазмы, кислорода воздуха и прочих факторов, то прочность такого соединения не может превышать прочность исходного металла.
До тех пор, пока сваренные металлоконструкции не подвергались существенным эксплуатационным нагрузкам, визуального контроля мест сварки было вполне достаточно. Но с возрастанием технических требований к качеству сварных швов возникла потребность в разработке эффективных средств и технологий неразрушающего контроля.
Основные дефекты сварных швов
Их классификация и влияние на качество соединения.В наиболее общем случае дефекты сварного шва подразделяют на две группы:1. Внутренние дефекты, вызванные термохимическими процессами, происходящими в расплаве при сварке.2. Внешние дефекты, преимущественно механического характера, связанные с возникающими термическими напряжениями в соединяемых металлах.
Внутренние дефекты
В свою очередь, внутренние дефекты могут представлять собой:
- Газовые включения и поры, образующиеся в результате колебаний внутреннего давления в расплаве и интенсивного окисления металла струёй высокотемпературного плазмы сварочной дуги. Такие поры могут образовывать пустоты, а могут и наполняться газами – продуктами термохимических реакций;
- Высокотемпературные включения шлаков и интерметаллидных соединений различной формы и направленности.
Разнородность материала, пониженные механические характеристики: прочность, сопротивление изгибу, ударная вязкость – основные причины разрушения сварных соединений, имеющих в своём составе газовые включения и несплошности.
Шлаковые и металлические включения ослабляют сварной шов вследствие пониженной прочности отвердевших при охлаждении шлаков, а также неблагоприятной микроструктуры в зоне сварки.
Внешние дефекты
Внешние дефекты сварного шва определяются:
- Качеством проведения процесса, следствием чего является либо односторонность сварки, либо надрез готового шва, в основном по его корню;
- Нарушением технологии охлаждения металла после сварки, в результате чего образуются поверхностные или глубинные трещины, прожоги, поверхность с грубой шероховатостью и неравномерными сварочными швами.
Наличие трещин является следствием существенной неравномерности условий охлаждения металла в зоне расплава, в результате чего его отдельные объёмы охлаждаются с заметно различной скоростью. Возникающие при этом напряжения растяжения определяют место возникновения трещины, путь её распространения, и габаритные размеры дефекта.
Общая классификация методов контроля качества сварки
Исторически первым методом определения качества сварного шва был метод сопоставления параметров фактического шва с так называемым идеальным. Однако сам критерий идеальности подразумевал испытание работоспособности готовой сварной металлоконструкции, а потому фактически являлся методом разрушающего контроля. По его результатам делался вывод о возможном применении неразъёмного соединения с ограничениями по внешним нагрузкам.
В настоящее время выбор методов неразрушаюшего контроля сварных соединений диктуется техническими требованиями к эксплуатационной стойкости конструкции, ограничениями на возможность практического применения, а также соображениями трудоёмкости обработки полученных результатов.
Практически используются следующие технологии контроля и диагностики сварных швов:
- 1. Метод просвечивания зоны соединения рентгеновскими лучами.
- 2. Метод ультразвукового контроля.
- 3. Метод пенетрации.
Сущность метода просвечивания
Метод просвечивания (иначе – радиографический) основан на оценке результатов взаимодействия потока γ-излучения с веществом, через которое проходят γ-лучи. Конечный эффект такого взаимодействия приводит к ослаблению интенсивности γ-излучения. Интенсивность такого потока Ф определяется:
- 1. Толщиной изменённой зоны.
- 2. Плотностью вещества в изменённой зоне.
- 3. Геометрическими размерами изменённой зоны.
Под изменённой зоной в данном случае понимается зона сварного шва.
При реализации радиографического метода главной задачей является обеспечение когерентности потока рентгеновских лучей, направляемых на объект контроля, поскольку при рассеивании лучей точность конечного результата заметно снижается. Поэтому излучатель рентгеновских частиц должен быть достаточно мощным, расстояние до объекта диагностики – по возможности минимальным, а глубина сварного шва – наименьшей. Указанные ограничения существенно снижают ценность практического применения данного метода
Конструктивно применяемые для контроля γ-дефектоскопы представляют собой защищённый свинцовым экраном стальной корпус, внутри которого устанавливается шар из тяжёлого металла с отверстием, где монтируется рабочая головка с излучателем. С противоположной стороны шара находятся клеммы соединения рабочей головки с источником γ-излучения.
С целью снижения вредного воздействия на окружающую среду в качестве источника рентгеновского излучения применяется изотоп кобальта Со60, обладающий наиболее короткой длиной волны γ-излучения, и, следовательно, наибольшей проникающей способностью.
Результат просвечивания сварного шва отображается на рентгенограмме, которая фиксирует численное изменение параметра Ф в зависимости от характера имеющихся неоднородностей. Сравнивая отмеченные неравномерности распределения, делают вывод о качестве сварки.
Радиографический метод обладает рядом ограничений и недостатков, среди которых:
- Ограниченная зона расстояния между дефектоскопом и объектом проверки – при слишком малом расстоянии искажается фактическая конфигурация и размеры дефекта, при слишком большом требуется заметно увеличивать мощность источника генерации излучения;
- Невозможность применения метода при глубинных дефектах, образующихся в результате сварки особо толстолистового металла;
- Невозможность оперативного получения результатов дефектоскопии сварного шва до обработки рентгеновской плёнки с его изображением;
- Высокие требования к безопасности источника γ-излучения, и необходимость в отдельном защищенном помещении для него.
Ряд указанных недостатков снимается применением метода электроградиографии, который использует не рентгеновские плёнки, а металлические пластины, предварительно покрываемые тонким слоем фоточувствительного полупроводника (в частности, селена). Слой обрабатывается коронным разрядом, и результате получает способность фиксировать дефекты сварного шва. Однако и этот метод несвободен от недостатков, основными их которых являются нестабильность получаемых результатов и зависимость от внешних условий диагностики.
Электрорадиография используется главным образом при контроле сварных швов из алюминия.
Иногда диагностику сварных швов ведут с применением нейтронного излучения, а также, используя импульсное рентгеновское просвечивание. Однако практического применения эти методы не получили ввиду сложности оборудования и его большой энергозатратности.Сущность методов ультразвукового контроля
Метод основан на акустических изменениях, которые происходят при прохождении звуковых колебаний сверхвысокой частоты сквозь исследуемый объём металла. Для неразрушающего контроля качества сварных швов используются такие свойства ультразвука, как скорость его распространения и степень ослабления обратного сигнала.Принцип ультразвуковой дефектоскопии заключается в следующем:
- Звуковые волны, генерируемые источником ультразвука – магнитострикционным или пьезоэлектрическим преобразователем, проходят через диагностируемую зону металла, отражаясь при этом от возможных источников искажений микроструктуры – углов, граней, пустот и т.д.
- Для фиксирования возможных внутренних дефектов звуковую волну необходимо отразить, «вернув» её в дефектоскоп, для чего в конструкции последнего предусмотрена угловая искательная головка.
- При наличии внутреннего дефекта происходит отражение звуковой волны, либо изменение угла её преломления. По интенсивности этих изменений можно судить о величине внутренних дефектов, о месте их расположения, а также о их конфигурации.
Основными узлами промышленных конструкций ультразвуковых дефектоскопов являются:
- Излучатель – узел, распространяющий высокочастотные колебания от источника в определённом направлении. Наибольшей равномерностью отличаются излучатели дискового типа;
- Собственно вибратор, размещаемый в корпусе, который не должен испытывать искажающее воздействие сдвиговых сред, а потому размещается в вязких материалах – гипсе, пастообразных веществах или графите;
- Приёмник ультразвукового сигнала, включающий в себя угловую искательную головку, который располагается с противоположной стороны от диагностируемого элемента сварного шва;
- Широкополосный усилитель ультразвукового сигнала, в качестве которого применяются радиочастотные приборы, снабжённые кварцевой головкой;
- Аналогово-цифровой преобразователь с цветным дисплеем, на экран которого выводится как качественная картинка с изображением дефекта, так и числовые его характеристики. Возможно представление результата в виде графика изменения интенсивности дефекта по его длине.
Современные ультразвуковые дефектоскопы используют следующие методы диагностики:
- 1. Резонансный метод, при котором происходит непрерывное излучение высокочастотных колебаний, с отражением волны в преобразователь. В результате в проверяемом изделии создаются так называемые стоячие волны, которые вводят испытуемую деталь в резонансные колебания. Их амплитуда фиксируется измерительным узлом дефектоскопа.
- 2. Метод звукового импульса, при котором оценивается время отражения высокочастотного сигнала от дефекта или пустоты в сварной конструкции. Генерируемый импульс определённой частоты предварительно синхронизируется и через усилитель направляется на изделие, проходящее акустический контроль качества. Искательная головка фиксирует объёмы с внутренними неоднородностями, и преобразует акустический сигнал в электрический, который затем воспроизводится на экране дисплея. Результат такого измерения называют рефлектограммой.
Сущность метода пенетрации (капиллярный метод)
Во многих случаях нет надобности в сложной измерительной технике, которая бы производила оценку качества сварного шва. Например, в сварных ограждающих конструкциях имеет значение на суммарный предел их механической прочности, а цельность шва, определяющая долговечность соединения в условиях внешних атмосферных воздействий. В таких случаях применяют визуальную оценку качества сварного шва по диффузии в него специальных жидкостей с высокой проникающей способностью. Таким образом, при пенетрации (проникновении) используются капиллярная проводимость поверхностных трещин и их взаимодействие с веществом (проявителем).
Методом пенетрации можно выявлять только поверхностные трещины, в частности, их ширину и протяжённость. В сложных и ответственных случаях результат проявления исследуется при помощи электронного растрового микроскопа.
Методика практической реализации метода следующая. Испытуемую сварную конструкцию очищают от поверхностных загрязнений, после чего покрывают индикаторной жидкостью. Если изделие – больших габаритов, то жидкость наносится кистью или пульверизатором, малые по размерам детали погружают в специальный резервуар. После нанесения жидкости требуется некоторое время (0,5…30 мин) для того, чтобы она полностью проникла в возможные поры на диагностируемом изделии, после чего излишки жидкости удаляют, а изделие обрабатывают в высококонтрастном проявителе, распыляемом по поверхности. Высыхая, проявитель извлекает индикаторную жидкость из трещин, воспроизводя размеры и конфигурацию дефекта.
Состав проявляющих веществ подбирается таким образом, чтобы увеличить фактические размеры дефекта по сравнению с реальными.
Это повышает точность метода. На практике в качестве индикаторной жидкости применяют горячее масло, а в качестве проявителя используют известковое молоко. При вторичном нагреве сварной конструкции известковая смесь высыхает, а на поверхности в местах поверхностных трещин остаются тёмные следы. Иногда используют индикацию краской, а в роли проявителя применяют бензол. Повышения контрастности дефектной зоны можно добиться, используя различные флуоресцирующие покрытия.
www.m-deer.ru
Способы контроля качества сварочных швов
Качество сварочных работ и сварных соединений сильно влияет на прочность конструкций или герметичность резервуаров. Несоответствие сварных швов заданным характеристикам приводит к разрушениям конструкций с катастрофическими последствиями, то же относится и к системам, работающим с сосудами и трубопроводами под давлением.
Поэтому после сварочных работ в обязательном порядке готовое изделие подвергают испытаниям и контролю на предмет обнаружения дефектов в сварных соединениях.
Все процедуры по контролю над качеством сварки определены ГОСТом или руководящими документами. В них также указаны допустимые нормы погрешностей. После испытаний составляется акт и протоколы с результатами измерений.
Методы проверки
Контроль качества сварочных работ, выполняемых на производстве, может быть разрушающим и неразрушающим. Первые методы используются выборочно. Проверяется одно или несколько изделий из большой партии, или часть металлоизделия в строительной конструкции.
Оно проверяется по различным параметрам определенным протоколом испытаний. Но главным образом используют специальные приборы или материалы позволяющие проверить качество сварных соединений без разрушения конструкции.
Основными способами неразрушающего контроля качества сварки являются:
- визуальный;
- капиллярный;
- проверка на проницаемость;
- радиационный;
- магнитный;
- ультразвуковой.
Имеются и другие способы и виды контроля качества сварки, но в силу своей специфики они не получили распространения.
Проверка состояния сварных швов не является одноразовым актом, это результирующий этап, который показывает, как работает система контроля качества на предприятии.
Для минимизации дефектов сварочных соединений проводят операционный контроль работ. Регулярно проводится аттестация, на которой комиссия сначала дает разрешение на сварку контрольного соединения. При прохождении сварщиками этого испытания проверяются теоретические знания.
Перед началом работ проверяется квалификация сварщика, у него должно быть удостоверение на право сваривания определенных марок стали и наряд-допуск.
Инженер по сварке и контролер из службы техконтроля проверяют качество сборки, состояние кромок, работоспособность сварочного аппарата, контролирует температуру прогрева, если это предусмотрено нормативно-технической документацией.
Контроль качества сварочных материалов осуществляется с момента поступления их на предприятие и до использования на сварочном посту. Проверку электродов проводят на каждом этапе хранения и использования, при необходимости их прокаливают.
При непосредственном проведении работ проверяют, какой режим сварки используется, дуговая сварка, аргонодуговая или иной вид сварки. Проверяют порядок наложения швов, размеры слоев и всего соединения.
Если предусмотрены специальные требования в проектно-технической документации, то и их реализацию. По завершении сваривания проверяет наличие клейма сварщика.
Внешний осмотр
Любая проверка качества сварных швов начинается с визуального контроля. Осматривают все 100% сварных соединений. Сначала проверяют геометрию и форму шва.
Визуальный контроль помогает выявить, наряду с наружными, часть внутренних изъянов. Так, переменные по габаритам валики швов и неравномерные складки говорят о непроварах, возникающих из-за частых обрывов электрической дуги.
Перед началом работ со сварных соединений удаляют шлак, окалины прочие загрязнения. Чтобы лучше можно было разглядеть дефекты, швы обрабатывают азотной кислотой (10%). Это придает матовость шву, что облегчает поиск изъянов.
После обработки кислотой необходимо провести тщательную протирку спиртом, чтобы предупредить ее вредное влияние на сплав.
Для повышения качества проверки можно использовать фонарь и оптическую лупу. Для контроля геометрических размеров применяют штангенциркуль и шаблоны.
Капиллярный метод
Данный способ контроля использует свойство жидкости затягиваться в очень мелкие капилляры. Быстрота и степень проникновения внутрь материала связана с его смачиваемостью и диаметром капилляров. Больше смачивается сплав и тоньше капилляры – глубже проникает жидкость.
Капиллярный способ контроля качества шва позволяет иметь дело не только с любыми металлами, но и с керамикой, пластмассой, стеклом. Главное его применение связано с проявлением внешних изъянов, которые невозможно или трудно определить невооруженным глазом. Иногда, используя, к примеру, керосин, можно обнаружить сквозные дефекты.
Способ очень простой, работает со времен возникновения потребности проверки сварочных швов. Для него даже разработан специальный ГОСТ 18442-80.
В капиллярном методе контроля качества сварки используют пенетранты – вещества, имеющие малое поверхностное натяжение и сильный цветовой контраст.
Проникая в дефектные зоны, и подсвечивая их, пенетранты визуализируют изъяны сварки. Их делают на основе воды, керосина, масла для трансформаторов и прочих жидкостей.
Наиболее чувствительные пенетранты могут проявить дефекты диаметром от 0,1 микрона. Капиллярный метод контроля качества сварки эффективен для дефектов до 0,5 мм шириной. При больших диаметрах пор или трещин он не работает.
Способ с применением пенетрантов заключается в очистке поверхности, нанесении контрольной жидкости и проявлении изъянов. Очень эффективен способ контроля сварных соединений с помощью керосина.
Несмотря на разнообразные приборы контроля качества сварки, проверку этим способом используют до сих пор. С одной стороны наносят раствор мела, дают время для сушки, затем с другой стороны шов смазывается керосином. Бракованные места проявляются через несколько часов в виде темных пятен.
Проверка сварных соединений на проницаемость
В случае применения сварки при изготовлении резервуаров требуется контроль герметичности. Для этого проводят испытания на непроницаемость соединений. Контроль качества проходит с применением газов или жидкостей.
Суть метода основана на создании большой разности давлений между наружной и внутренней областью емкости. При сквозных изъянах в сварном шве жидкость или газ будут переходить из области с высоким давлением в область с низким давлением.
В зависимости от используемого вещества и способа получения избыточного давления контроль проницаемости осуществляют пневматикой, гидравликой или вакуумом.
Пневматический способ
Применение пневматического метода контроля качества сварки требует накачивания резервуара каким-либо газом до давления величиной 150% от номинального.
Затем все сварные швы смачивают мыльным раствором. В местах протечек образуются пузыри, что очень легко фиксируется. Для лучшей визуализации используют добавку аммиака, а шов покрывают бинтом пропитанным фенолфталеином. В местах протечек появляются красные пятна.
Если нет возможности накачать емкость, то применяют способ обдува. С одной стороны шов обдувается под давлением не менее 2,5 атмосферы, а с другой обмазывается мыльным раствором. Если имеется брак, то он выявится в виде пузырьков.
Гидравлический способ
При гидравлическом способе контроля качества сварки проверяемая емкость заполняется водой или маслом. В сосуде создается избыточное давление, которое больше номинального в полтора раза.
Затем в течение определенного времени, обычно 10 минут, область вокруг шва обстукивают молотком со скругленным бойком. При наличии сквозного дефекта сварки появится течь. Если избыточное давление невелико, то время выдержки резервуара увеличивают до нескольких часов.
Магнитная дефектоскопия
Явление электромагнетизма используется в магнитных дефектоскопах. Каждый металл имеет свою степень магнитной проницаемости. При прохождении через неоднородные материалы магнитное поле искажается, что говорит о присутствии инородных элементов внутри структуры.
Это используется в приборе для контроля качества сварки. Он вырабатывает магнитное поле, которое проникает в исследуемый металл. Неоднородности фиксируются магнитопорошковым или магнитографическим способом.
В первом случае на сварной шов наносят ферромагнитный порошок. Там где происходит скопление порошка вероятнее всего непровар, нет сплошного соединения. Порошок может быть сухим или влажным, с примесью масла или керосина.
Во втором случае на шов накладывают ферромагнитную ленту. Затем ее пропускают через прибор, где анализируют все аномалии, зафиксированные на ленте, и определяют дефекты сварки.
Магнитный способ контроля качества имеет ограничения, связанные с самим принципом действия прибора. Он может проверять качество сварных соединений только ферромагнетиков, к которым некоторые стали и цветные металлы не относятся. Соответственно, такой способ контроля имеет ограниченное применение.
Ультразвуковая дефектоскопия
Для контроля качества сварки применяют ультразвук. Принцип действия аппарата основан на отражении ультразвуковых волн от границы соединения двух сред с различными акустическими свойствами.
Датчик и излучатель плотно прикладывают к исследуемому материалу, после чего устройством вырабатывается ультразвук. Он проходит через весь металл и отражается от задней стенки, возвращаясь, попадает на приемный сенсор, который в свою очередь преобразует ультразвук в электрические колебания. Прибор представляет полученный сигнал в виде изображения отраженных волн.
Если внутри металла присутствуют какие-нибудь изъяны, датчик зафиксирует искажение отраженной волны. Опытным путем установлено, что различные дефекты сварки по-разному себя проявляют на ультразвуковом дефектоскопе. Это позволило провести их классификацию. При соответствующем обучении специалист может точно определить вид брака в шве.
Способ контроля качества сварных соединений ультразвуком широко распространился благодаря простоте и удобству применения, относительно недорогому оборудованию, безопасности использования по сравнению с радиационным методом.
Минусом способа является трудность расшифровки графического изображения. Контроль качества соединения может сделать только сертифицированный специалист. Его проблематично использовать для контроля крупнозернистых металлов типа чугуна.
Радиационный метод
Для контроля качества сварки используют радиационные методы и устройства. По сути это тот же рентгеновский аппарат, используемый в больницах, или прибор с источником гамма-излучения, приспособленный для облучения сварных соединений.
Он основан на способности этих лучей, проникать через любые материалы. Интенсивность проникновения зависит от вида исследуемых веществ. Благодаря этому на фотопленке, стоящей за исследуемым изделием, остается изображение, характеризующее состояние данного материала.
Все дефекты сварки в виде неоднородностей выявляются на пленке. Метод контроля очень точный, но дорогой и вредный для людей, требует подготовительных работ по установке защитных экранов и проведения организационных мероприятий.
Оформление документации
Для проведения сварки предусматривается специальный журнал. Он является первичным документом, оформляющийся по требованиям СНиП. Проектная организация составляет перечень узлов в металлоконструкции, которые необходимо сдать заказчику с оформлением сварочных документов.
Помимо журнала, сварочные работы сопровождает схема стыков, прилагаются сертификаты на расходные материалы (электроды, флюс или присадочную проволоку) и акты по контролю качества снаружи изделия.
Если проводились ультразвуковые или иные специфические исследования, то результаты и заключения по ним также прилагаются.
Все это позволяет говорить о качестве сварке и надежности конструкции. Только после сдачи в полном объеме сварочной документации производятся дальнейшие процедуры по принятию металлоконструкций объекта.
svaring.com
Методы контроля качества сварных соединений
Вне зависимости от выбранного способа проведения сварочных работ, контроль качества сварных соединений является определяющим показателем дальнейшего поведения данного соединения конструкции. Наличие различных дефектов в сварных соединениях, скрытых при простом визуальном осмотре, может приводить не только к потере его прочности или герметичности, но и к возможности аварийного разрушения во время эксплуатации.
Зачем необходим контроль
После проведения сварочных работ на ответственных конструкциях и изделиях необходимо проводить контроль качества выполненных работ на предмет обнаружения различных дефектов. Если наличие крупных наружных трещин и воздушных пор можно выявить при простом визуальном осмотре, то непровары, внутренние поры и вкрапления шлака уже невозможно обнаружить невооруженным глазом, так как большая их часть скрыта под поверхность металла, имея при этом довольно малые размеры.
Поэтому контроль качества сварных швов подразумевает применение различных методик, специальных приборов и реагентов для того, чтобы:
- своевременно выявлять и устранять все виды дефектов;
- получать сварные высококачественные соединения;
- определять точность выполнения технологического процесса сварочных работ;
- готовое изделие могло соответствовать предъявляемым заказчиком требованиям.
Контролирующие органы
Контроль качества сварных швов осуществляется специально подготовленными контролерами, имеющими аттестационные удостоверения, которые дают им право на проведение визуально-измерительного контроля сварных соединений, но только определенным способом или методикой.
Для этого из числа ИТР назначаются наиболее ответственные работники, которые проходят по специальной программе теоретическое и практическое обучение. После прохождения курса обучения и сдав аттестационные экзамены, контролеры допускаются отделениями Госгортехнадзора России к контролю качества сварных соединений.
Обучения контролеров осуществляется только специальными учебными заведениями, имеющими соответствующие лицензии на право подготовки таких специалистов.
Обучение контролеров проводится по программам теоретической и практической подготовки, строго по специализациям в зависимости от методики проведения контроля качества или вида сварных соединений. Специализация контролеров должна быть указана в их аттестационных удостоверениях, к примеру: вид радиографирования или ультразвуковая дефектоскопия.
Существующие методы контроля
На практике существуют два способа проведения проверки качества для сварных соединений:
- разрушающий метод контроля,
- неразрушающий метод контроля.
К разрушающим методикам проверки качества можно отнести:
- все механические испытания готовых образцов;
- различные химические и физические исследования;
- металлографическое обследование;
- мероприятия по контролю исходного материала.
Неразрушающий контроль сварных соединений включает:
- квалификационную проверку производственного персонала;
- проверку сварочного оборудования и режима сварки;
- визуальный осмотр внешнего вида сварного шва;
- различные методики проведения непосредственного выявления дефектов.
К неразрушающим методикам выявления дефектов относятся:
- метод тепловой томографии;
- капиллярный метод контроля;
- методом истечения или испытания избыточным давлением;
- акустический или ультразвуковой метод контроля;
- электромагнитная дефектоскопия;
- различные радиографические методы;
- рентгенографический метод.
При этом, вне зависимости от конечного способа контроля качества полученного соединения сварного шва, проверка обязательно должна включать и учитывать всю совокупность подготовительных, технологических и организационных мероприятий, начиная от качества подготовки поверхности заготовки, вида используемого оборудования и материалов, а также квалификации сварщика, заканчивая непосредственной технологией выполнения сварочных работ.
Технология применения
К наиболее технологически простым и наименее затратным можно отнести или выделить визуально-измерительные методы неразрушающего контроля сварных соединений, а именно:
- тепловой томографии;
- капиллярную методику;
- методом истечения или испытания давлением;
Метод тепловой томографии сварных соединений, в свою очередь, делиться на:
- пассивный, когда не требуется внешнее тепловое поле;
- активный, когда исследуемый образец нагревают за счет внешнего источника тепла.
Данная тепловая методика основывается на том, что все обнаруженные дефекты нарушений однородности в виде раковин, воздушных пор, трещин и тому подобных отклонений представляют собой локальные цветовые отклонения при отражении температурного поля на поверхности экрана тепловизора.
Отсутствие необходимости в дополнительных материалах и мероприятиях является главным достоинством такой методики. А вот обязательное наличие дорогостоящего тепловизора, а также невозможность выявить глубину обнаруженных дефектов можно отнести к недостаткам этого метода.
Капиллярная методика контроля основывается на физических свойствах различных активных жидкостей, которые заключаются в способности заполнять мельчайшие воздушные поры и каналы, которые могут образоваться в структуре сварного шва металла. Главным условиями работы такой методики являются наличие высокой текучести применяемой жидкости, а также и величина радиуса воздушного канала, причем чем выше текучесть и больше размер капиллярного отверстия, тем больше вероятность визуального выявления дефекта.
Методика, основанная на капиллярном эффекте, позволяет проверять сварные швы любых металлов как черных, обладающих ферромагнитными свойствами, так и цветных. Данную методику в основном применяют для обнаружения не только поверхностных неоднородностей, но и для выявления сквозных дефектов на открытых поверхностях, например таких, как сварные швы трубопроводов и различных наливных емкостей.
Для получения нужного эффекта жидкостью смачивают сварной шов, после чего, спустя некоторое время, ее вытирают с поверхности. Путем подсвечивания ультрафиолетом все дефекты в виде капилляров начинают светиться.
Для данного метода используют смесь керосина с мелом или пенетранты. Это специальные жидкости, которые обладают высокой текучестью и большой световой и цветовой контрастность, что позволяет с легкостью обнаруживать дефекты, за счет их особой окраски из-за заполнения пенетрантами.
Основным достоинством капиллярной методики контроля является быстрота и небольшая стоимость проведения работ. А вот невозможность выявить глубину и характер обнаруженных дефектов можно отнести к довольно существенным недостаткам данной методики.
Метод истечения или испытания давлением является одним из наиболее широко применяемых способов обнаружения дефектов в целостности сварных швов. Как правило, метод истечения применяется для закрытых трубопроводных систем или различных емкостей и сосудов.
Сущность метода заключается в нагнетании давления пневматическим или гидравлическим способом в закрытой системе. После достижения давления, превышающего рабочее для данного трубопровода или сосуда, производится визуальный осмотр сварных швов с использованием пенообразующих растворов, что позволяет выявлять все возможные утечки.
Минусом этой методике является то, что она позволяет лишь обнаруживать исключительно сквозные дефекты сварных соединений.
Для более точного и ответственного обнаружения дефектов используют более наукоемкие и технологически дорогие методики контроля сварных соединений:
- ультразвуковая дефектоскопия;
- электромагнитная дефектоскопия;
- радиография;
- рентгенография.
Ультразвуковая и электромагнитная дефектоскопия является относительно несложными методиками и позволяют по ряду визуальных признаков, отображенных на экране приборов, определять количество, вид и глубину дефектов, но при этом никак не получиться установить точный характер имеющегося отклонения в структуре металла.
Стопроцентную визуализацию структуры выполненного сварного соединения позволяют получить только рентгеновский и радиографический контроль сварных соединений. Данные методики технологически очень сложны, поэтому их применяют для проверки сварочных соединений для особо ответственных конструкций и изделий в следующих отраслях:
- в нефтегазовой промышленности при строительстве магистральных трубопроводов;
- в точном и среднем машиностроении;
- в авиационной и космической промышленности.
Самым достоверным способом проверки целостности основного металла и состояния сварных соединений является просвечивание с помощью рентгеновского излучения. Этот способ широко применяют для проверки качества сварных швов магистральных трубопроводов, технологических конструкций кранового оборудования, композитных соединений материалов в авиационной и космической промышленности.
Рентгенографическая дефектоскопия основывается на физическом явлении, которое заключается в прохождении рентгеновского излучения практически через любой существующий материал. А точнее, используется интенсивность его прохождения, которая во многом зависит от физико-химических свойств испытуемого материала и его плотности. Отсюда, рентгеновские лучи, проходя через среду, позволяют показать на экране прибора или на фотопластине любые дефекты в масштабе, которые их ослабляют в зависимости от своей плотности.
Главным достоинством рентгенографии является возможность по отражению контрастности на детекторе не только визуально определять количество и расположение, но и размеры дефектов, а также их структуру в испытуемом материале.
Недостатками рентгенографии дефектоскопии можно считать:
- громоздкость оборудования;
- жесткое электромагнитное излучение, опасное для жизни человека;
- существенные энергозатраты;
- высокая стоимость исследований.
К более специфичным методикам контроля сварных соединений можно отнести различные радиографические способы. К ним можно отнести:
- ксерорадиографию, использующую рентгеновское или Y-излучение, как ионизационное облучение для ионизации красящегося порошка в местах обнаружения дефектов;
- флюорографию, позволяющего отразить структуру исследуемого материала со всеми дефектами на фотобумаге или фотопленке, за счет просвечивания его рентгеновским или Y-излучением;
- цветовую радиографию, при которой можно получать дополнительно цветное изображение на обычном черно-белом рентгеновском снимке;
- нейтронную радиографию, использующую облучение материала пучком нейтронов для показа его структуры на детекторе излучения;
- протонную радиографию, где для просвечивания материала используются особенности прохождения различных веществ потоком протонов или α-чaстиц.
Все эти методики дефекторадиографии позволяют получать самую достоверную и высокоточную информацию при контроле качества сварных соединений, но они имеют один существенный недостаток, который заключается в необходимости использования жесткого электромагнитного излучения, которое, в свою очередь, сильно усложняет применение данной методике на практике.
wikimetall.ru
Аттестационный центр - безопасность труда
Методы контроля качества сварных швов
Внешний осмотр (ГОСТ 3242-79).
Служит для определения наружных дефектов в сварных швах. Производится невооруженным глазом или с помощью лупы 10-кратного увеличения. Перед осмотром сварной шов н прилегающую к нему поверхность металла шириной 20 + 20 мм очищают от шлака, брызг и загрязнений, стыки паропроводов из аустенитных сталей проходят механическую и химическую обработку. Размеры сварного шва и дефектных участков определяют измерительным инструментом и специальными шаблонами. Границы трещин выявляют путем засверливания, подрубки металла зубилом, шлифовки дефектного участка и последующего травления. При нагреве металла до вишнево-красного цвета трещины обнаруживаются в виде темных зигзагообразных лниний. В случаях, когда необходима термическая обработка сварных стыков, внешний осмотр и измерения следует производить до и после термообработки.
Просвечивание сварных соединений (ГОСТ 3242-79, ГОСТ 7512-75 и ГОСТ 23055-78).
Основано на способности рентгеновских или гамма-лучей; проникать через толщу металла, действуя на чувствительную фотопленку, фотобумагу, или селеновую пластину, приложенную к шву с обратной стороны. В местах, где имеются поры, шлаковые включения или непровар, на пленке (пластине) образуются более темные пятна. Рентгенопросвечнваиием выявляют дефекты в металле толщиной до 60 мм размером 0,5-3% толщины металла, гамма-просвечнваиием - в металле толщиной до 100 мм размером 2-5%. Просвечивание не позволяет выявлять трещины, если оин расположены под углом не более 5° к направлению центрального луча, а также непровары в виде слипания свариваемых металлов без газовой или шлаковой прослойки. При обнаружении в шве недопустимых дефектов просвечивают удвоенное количество швов (стыков). Если вновь обнаруживают дефекты, то просвечивают все швы, заваренные данным сварщиком. Выявленные дефекты удаляют, швы переваривают и вновь просвечивают. При оценке качества швов рекомендуется иметь эталонные снимки для толщин 8-12, 14-20, 30-50 н 60-100 мм с характерными дефектами. Альбомы эталонных снимков утверждаются инспекцией Госгортех- надзора и администрацией и являются неотъемлемой частью технических условий на приемку изделий.
Магнитографический контроль (ГОСТ 3242-79).
Основан на обнаружении полей рассеивания, образующихся в местах дефектов при намагничивании контролируемых изделий. Поля рассеивания фиксируются на эластичной магнитной ленте, плотно прижатой к поверхности шва. Запись производят на дефектоскопе или считывают. Выявляют поверхностные и подповерхностные макротрещины, непровары, поры и шлаковые включения глубиной 2-7% на металле толщиной 4-12 мм. Менее четко обнаруживаются поры округлой формы, широкие непровары (2,5-3 мм), поперечные трещины, направление которых совпадает с направлением магнитного потока. В ряде случаев результаты магнитного контроля проверяют просвечиванием. Производительность метода 5-6 м/мии.
Ультразвуковой метод (ГОСТ 3242-79, ГОСТ 22368-77).
Основан на различном отражении направленного пучка высокочастотных звуковых колебаний (0,8-2,5 Мгц) от металла (сварного шел) и имеющихся в нем дефектов в виде несплошностей. Применяют для контроля сварных швов сталей и цветных металлов. Для получения ультразвуковых волн используют пьезоэлектрические пластинки из кварца или титаната бария, которые вставляют в держатели-щупы. Отраженные колебания улавливают искателем, преобразуют в электрические импульсы, подают на усилитель и воспроизводят индикатором. Для обеспечения акустического контакта поверхность изделия в месте контроля обильно покрывают маслом (автол марок 6, 8, 18; компрессорное масло и т. д.). Предельная чувствительность при толщине металла до 10 мм 0,2-2,5 мм2, свыше 10 до 50 мм 2-7 мм2, свыше 50 до 150 мм 3,5-15 мм2.
Вскрытие шва (ГОСТ 3242-79).
Применяют для определения дефектов в сомнительных местах, после проведения контроля другими методами, а также для контроля угловых швов. Вскрытие производят вырубкой, сверлением, термической строжкой, а также вырезкой участка сварного соединения. При засверливании в сварном шве высверливают воронкообразное углубление диаметром на 2-3 мм больше ширины шва. Поверхность воронки шлифуют и протравливают 15%-пым раствором азотной кислоты. При этом отчетливо выделяются границы шва.
Контроль плотности методом химических реакций (ГОСТ 3242-79).
На наружный шов металла толщиной до 16 мм наносят 4%-ный раствор фенолфталеина или накладывают марлю, пропитанную 5%-ным раствором азотнокислого серебра. В изделие нагнетают воздух в смеси с аммиаком (его получают из баллона со сжиженным газом). В местах локальных течей фенолфталеин окрашивается в ярко-красный цвет, а азотнокислое серебро - в серебристо-черный. Перед испытанием требуется тщательная очистка шва от загрязнений и шлака.
Люминесцентная и цветная дефектоскопия (ГОСТ 3242-79).
В полость дефекта вводят флюоресцирующий раствор или ярко-красную проникающую жидкость, которую затем удаляют с поверхности. Под действием ультрафиолетовых лучей происходит видимое свечение раствора, адсорбированного из полости дефекта. При цветной дефектоскопии дефекты выявляют белой проявляющейся краской (на белом фоне появляется красный рисунок, соответствующий форме дефекта). С помощью этих методов выявляют поверхностные дефекты, главным образом трещины в различных сварных соединениях, в том числе из немагнитных сталей, цветных металлов и сплавов. Для цветной дефектоскопии используют готовые комплекты (ДАК-2Ц).
Керосиновая проба (ГОСТ 3242-79).
Служит для определения плотности сварных швов на металле толщиной до 10 мм. Керосиновой пробой обнаруживают дефекты размером 0,1 мм и выше. Доступную для осмотра сторону шва покрывают водной суспензией мела или каолина и подсушивают. Противоположную сторону смачивают 2-3 раза керосином. Проницаемость обнаруживают по жирным желтым пятнам на поверхности, покрытой мелом или каолином. Продолжительность испытания составляет не менее 4 ч при положительной температуре и не менее 8 - при температуре ниже О3 С. Если швы нагреть до 50-60° С, то процесс ускорится до 1,5-2 ч. Его также можно ускорить, добавлял в керосин краску "Судан-Ш" (2,5 г/л) и обдувая швы со стороны керосина сжатым воздухом или создавая вакуум.
Гидравлическое испытание (ГОСТ 3242-79, ГОСТ 3285-77).
Налив воды применяют для испытания на прочность и плотность вертикальных резервуаром, газгольдеров и других сосудов с толщиной стенки не более 10 мм. Воду наливают на полную высоту сосуда и выдерживают не менее 2 ч. Поливу из шланга с брандспойтом (диаметр выходного отверстия 15-30 мм) под давлением не ниже 1 атм (0,1 МПа) подвергают сварные швы открытых сосудов. При испытании с дополнительным гидростатическим давлением последнее создают в наполненном водой и закрытом сосуде с помощью напорной трубки диаметром не менее 30 мм, а также гидравлическим насосом. Величину давления определяют по техническим условиям и правилам Котлонадзора. При проведении испытаний сварные швы обстукивают молотком массой 0,5-1,5 кг. Дефектные места определяют по наличию капель, струек воды и отпотеваний.
Пневматическое испытание (ГОСТ 3242-79, ГОСТ 3285-77).
Метод основан на создании с одной стороны шва избыточного давления воздуха и промазывании другой стороны мыльной пеной, образующей пузыри под действием проникающего через неплотности сжатого воздуха. При создании в сосудах избыточного давления воздуха утечку определяют также по понижению давления на манометре. Небольшие сосуды под давлением опускают в воду и следят за появлением пузырьков выходящего воздуха. Обдувают швы сжатым воздухом под давлением 4-5 атм (0,4-0,5 МПа) при расстоянии между наконечником шланга н швом не более 50 мм. Мыльный раствор: 100 г хозяйственного мыла на 1 л воды (зимой до 60% воды заменяют спиртом или применяют незамерзающие жидкости).
Вакуум-метод (ГОСТ 3242-79, ГОСТ 3285-77).
Сущность метода заключается в создании вакуума и регистрации проникновения воздуха через дефекты на одной, доступной для испытания стороне шва. Применяют для испытания на плотность днищ вертикальных резервуаров и других конструкций. Выявляют сквозные неплотности размером 0,1 мм и более металла толщиной до 16 мм. В качестве пенного индикатора используют мыльный раствор (250 г хозяйственного мыла на 10 л воды), а в зимнее время -водный раствор хлористой соли (кальция или натрия) с концентрированным раствором экстракта лакричного корня (1 кг экстракта на 0,5 л воды).Для создания вакуума используют плоские, кольцевые и сегментные камеры. Величина вакуума 500-600 мм вод. ст. (5000-6000 Па). Длительность испытания 20 с.
Технологическая проба (ГОСТ 3242-79).
Служит для определения сплавления металла, характера излома соединений (по шву или по основному металлу), наличия непровара и других внутренних дефектов на образцах. Место разрушения осматривают невооруженным глазом или с помощью лупы 10-кратного увеличения. Применяют при аттестации сварщиков, испытании сварочных материалов и выбранной технологии.
Определение склонности швов к межкристаллитной коррозии (ГОСТ 6032-75).
Служит для проверки склонности соединений, изготовленных из легированных ферритных, аустенитно-мартенситных, аустенитно-ферритных и аустенитных сталей (например, сталей типа 18-8), к межкристаллитиой коррозии в зависимости от свойств применяемой стали и условий работы сосуда. Образцы, изготовленные из сварного соединения, в течение определенного времени находятся под воздействием специального раствора, после чего их промывают, просушивают и загибают под углом 90°. Наличие трещин указывает па то, что образец испытаний не выдержал.
Металлографическое исследование (ГОСТ 3242-79).
Макроструктуру контролируют для установления глубины проплавления металла, ширины зоны термического влияния, наличия внутренних дефектов путем осмотра поверхности образца, вырезанного поперек сварного шва с помощью режущего или абразивного инструмента (огневая резка должна быть на расстоянии, при котором в исследуемом сечении не происходит структурных изменений). Контролируемую поверхность шлифуют и подвергают травлению специальными реактивами до четкого выявления структуры. Микроисследованием устанавливают точность соблюдения предписанной технологии сварки и термической обработки. Шлифы - темплеты перед испытанием полируют и протравливают 4%-ным раствором азотной кислоты в этиловом спирте.
Механические испытания (ГОСТ 6996-66*).
Данное испытание позволяет определить прочность и пластичность сварных соединений. Образцы сваривают в тех же условиях, что и изделие, или вырезают из него. Испытания на разрыв и загиб (сплющивание для труб диаметром до 100 мм) являются обязательными, на ударную вязкость - только для назначенных изделий. Испытания проводят при проверке квалификации сварщиков, а также для определения пригодности сварочных материалов и выбранной технологии сварки.
Испытание на твердость (ГОСТ 22761-77).
Его применяют для проверки качества термической обработки сварных соединений толстостенных трубопроводов из углеродистых (С) и хромомарганцовистых (ХГ) сталей, а также трубопроводов из легированных сталей перлитного и мартенситно-ферритного классов (ХМ и ХФ).Твердость измеряют на двух участках по окружности стыка на трубах с наружным диаметром более 100 мм и на одном участке при наружном диаметре труби до 100 мм. При автоматической сварке и общей термической обработке допускается производить измерение на одном участке независимо от наружного диаметра. Измеряют в пяти точках: по центру шва, на расстоянии 1-2 мм от границы сплавления в сторону основного металла и на расстоянии 10-20 мм от границы сплавления - на основном металле.Испытанию подвергают 15% общего количества сваренных каждым сварщиком в течение месяца однотипных стыков на сталях групп С и ХГ, но не менее двух, и 100% стыков на сталях групп ХМ и ХФ.По результатам измерения твердости качество сварки считается неудовлетворительным, если:снижение твердости наплавленного металла превышает 25 НВ по сравнению с нижним значением твердости основного металла;твердость наплавленного металла превышает 20 НВ по сравнению с верхним значением твердости основного металла;разность в твердости основного металла и зоны термического влияния превышает 50 НВ на сталях групп С н ХГ и 75 НВ на сталях групп ХМ и ХФ.При разности в твердости, превышающей допустимую, стыки повторно термически обрабатывают. При разности в твердости, превышающей допустимую на сталях групп С и ХГ, твердость замеряют на 100% стыков; в случае необходимости производят термическую обработку независимо от толщины стенки. При разности в твердости, превышающей допустимую после повторной термической обработки, делают стилоскопирование наплавленного металла всех однотипных производственных стыков, сваренных данным сварщиком во время последней контрольной проверки. При несоответствии химического состава наплавленного металла заданному стыки бракуют окончательно.В полевых условиях применяют переносные твердомеры типа ТПП-10, ТПК-1, ТШП-3, ТШП-4 и ТШП-0,75. Для приближенного определения твердости по Бринеллю (НВ) служат приборы с произвольной энергией удара, называемые твердомерами Польди-Хютте.Динамическое нагружение стального шарового индентора осуществляют посредством удара по бойку (штоку) ручным молотком. При ударе индентор одновременно внедряется в эталон и изделие. Твердость находят путем сравнения отпечатков.
Контроль содержания ферритной фазы в швах (ГОСТ 11878-66*).
Наплавленный металл на содержание ферритной фазы контролируют на изделиях из стали группы ХН переносными ферритометрами ФА-1 ФМ-10Н и альфа-фазометрами в объеме 100% на трубах, предназначенных для работы при температуре свыше 350° С и в коррозионных средах (при наличии требования в проекте). Измерения производят не менее чем в пяти точках на каждой из трех равнорасположенных по окружности стыка площадок размером не более 10 X 10 мм. На трубах с наружным диаметром не менее 50 мм замеры проводят на двух диаметрально-противоположных площадках. Шероховатость поверхности, подготовленной под замеры, должна быть не менее Rz =20 по ГОСТ 2789-73 (СТ СЭВ 638-77).Результаты измерений на содержание ферритной фазы считаются неудовлетворительными, если количество ее превышает 7% в деталях, предназначенных для работы при температуре свыше 350° С; 3%-в трубопроводах из хромони кельмолибденовых сталей, работающих в коррозионной среде, с толщиной стенки трубы до 5 мм и в корне на высоте не менее 5 мм - при большей толщине, а также 5% - на наружной поверхности швов деталей из тех же сталей с толщиной стенки трубы более 5 мм.Стилоскопирование наплавленного металла. Стилоскопирование, или экспресс - анализ химического состава наплавленного металла, проводят с целью установления соответствия марок использованных сварочных материалов требованиям технических условий и производственных инструкций на сварку. Стилоскопированию на выявление основных легирующих элементов подвергают наплавленный металл шва в случае, рассмотренном выше, и если соответствие использованных сварочных материалов назначенным вызывает сомнение. Для этой цели служат переносные стилоскопы СЛП-2 п СЛП-4, стационарные СЛ-12 "Спектр".При получении неудовлетворительных результатов выполняют стилоскопирование 100% однотипных стыков, сваренных данным сварщиком. При несоответствии (по результатам стилоскопировання) химического состава наплавленного металла требуемому проводят химический анализ лабораторными методами, результаты которого считаются окончательными.
Методы контроля качества сварных швов
ac-bt.ru
Методы контроля сварных швов: как их применять?
Каждый сварщик знает, что сварные конструкции имеют эксплуатационные свойства, которые определяются качеством сварных швов.

Для получения надежной и прочной конструкции необходимо сделать качественный шов.
Недостаточное качество выполнения сварного шва вызывает быстрое разрушение сварных швов, а при недостаточной плотности будет нарушена их герметичность. Процесс разрушения ускоряется при использовании конструкции в условиях высокого уровня давления.
Цель проведения контроля сварного шва
Перед отправкой сварного готового изделия на последующую проверку обязательно контролируют уровень качества его сварных швов, а это помогает выявлять не только наружные недостатки, но и скрытые, с целью их устранения. Применяется сварная конструкция только после тщательного контроля.

После сварки необходимо тщательно осмотреть шов на наличие трещин и непроваров.
На первом этапе изделие подвергают внешнему осмотру и выявляют различные недостатки сварных швов, включая наличие трещин и непроваров. Обнаружение данных дефектов доступно и при невооруженном взгляде, а остальные типы недостатков определяются за счет применения специального оборудования.
Различают контроль сварных швов, который относят к разрушающим типам и неразрушающим. К последним видам относится не только один способ внешнего осмотра, но и следующие виды контроля швов:
- Капиллярный.
- Ультразвуковой.
- Радиационный.
- Магнитный.
- На проницаемость.
Применение неразрушающих способов контроля не связано с изменением внешнего вида самого изделия. Разрушающие методы применяют, когда проверяют выпуск сварных деталей в достаточном количестве с использованием постоянного типа сварки и одинаковых условий.
Вернуться к оглавлению
Проверка и испытания сварных швов: методы контроля

Факторы, влияющие на качество сварных швов.
Сварные швы можно контролировать различными способами, для чего предусмотрена их классификация, которая включает следующие методы, используемые при проведении контроля:
- Химические.
- Механические.
- Физические.
- Внешний осмотр.
Если подробно рассматривать каждый из них, то одним из распространенных и доступных является внешний осмотр, который не связан с какими-либо материальными затратами. Применение любых сварных соединений подвергается данному методу контроля независимо от процесса проведения дальнейших операций, сопровождаемых другими способами контроля швов.
Проводить внешний осмотр можно с выявлением практически всех типов дефектов сварных швов. Данный метод контроля связан с выявлением непроваров, подрезов, наплывов либо других дефектов, которые являются доступными для обозрения. Для осуществления внешнего осмотра можно применять лупу, которая увеличивает в 10 раз.
В условиях внешнего осмотра наблюдение может быть не только визуальным, но и связанным с обмером сварного шва, проведением замеров кромок, которые заранее подготовлены. Процесс массового выпуска сварных изделий связан с использованием специальных шаблонов, которые позволяют максимально точно делать замеры каждого параметра сварного шва.
Вернуться к оглавлению
Физические методы контроля
Вернуться к оглавлению
Применение магнитного метода сварочных швов

Схема магнитного метода контроля качества сварного шва.
Обнаружение дефектов в процессе осуществления магнитного контроля основано на такой способности магнитного поля, как его рассеивание. С этой целью необходимо подключение электромагнитного сердечника с последующим помещением его в соленоид. Намагниченное соединение должно иметь поверхность, предварительно покрытую железными опилками, окалиной и др. Должны быть использованы такие элементы, которые реагируют на появление магнитных полей.
Если сварной шов имеет дефекты, то происходит образование скоплений порошка, который при взаимодействии с магнитным полем начинает перемещаться с образованием магнитного направленного спектра. Для более легкого перемещения порошка под влиянием магнитных полей сварные изделия простукивают, что придает наибольшую подвижность мелким крупинкам и зернам.
Фиксацию магнитного поля рассеивания осуществляют с использованием специального прибора, то есть магнитографического дефектоскопа. Определить качество соединения можно с помощью метода сравнения с эталоном. Данный метод является простым и надежным, а также дешевым. Магнитный метод контроля сварочных швов незаменим в процессе прокладки трубопроводов, которые играют ответственную роль. Его часто используют во время строительства.
Вернуться к оглавлению
Радиационный способ контроля и ультразвуковой метод

Схема радиографического контроля: 1—источник излучения; 2—прямой пучок; 3—сварной шов; 4—кассета с детектором и экранами; 5—эпюра интенсивности излучения.
Радиационный способ контроля связан с определением недочетов в любой полости сварных швов, которые являются невидимыми. Просвечивают швы с применением рентгеновских лучей или с помощью гамма-излучения, которое способно проникать через металлическую структуру изделия.
Излучение создается за счет специальных источников, рентгеновской либо гамма-установки. Шов и источник излучения должны находиться друг перед другом. Расположение рентгеновской пленки связано с ее установкой в специальную кассету, которая является светонепроницаемой. При облучении пленки рентгеновским излучением, проходящим через структуру металла, остаются пятна, которые являются более темными. Это связано с наименьшим поглощением лучей дефектными местами.
Использование метода рентгеновского излучения является безопасным для здоровья человека, но источник излучения, то есть рентгеновский аппарат, является слишком громоздким. Используют его исключительно в условиях стационара. Интенсивность работы источника гамма-излучения бывает значительной, что позволяет контролировать сварные швы, которым свойственна наибольшая толщина. Портативная аппаратура и доступность дешевого метода делает данный тип контроля наиболее распространенным в строительстве.
Гамма-излучение более опасно, чем рентгеновское, что обусловлено прохождением специального обучения. Применение радиографического метода контроля имеет недостаток, связанный с отсутствием возможности выявлять наличие трещин, которые располагаются не в соответствии с направлением потока лучей.

Схема ультразвукового контроля сварных швов.
Использование ультразвукового метода связано с применением акустического способа контроля. Это позволяет выявлять различные недочеты, то есть газовые поры и трещины, включая такие дефекты, ради определения которых не применяется способ радиационной дефектоскопии.
Ультразвуковым методом проводят испытания, связанные с отражением звуковой волны от границы разделения сред. Использование пьезоэлектрического способа при создании звуковой волны получило широкое распространение в качестве способа контроля сварного шва. В основе данного метода лежит принцип создания механического колебания в результате наложения переменного электрического поля.
Вернуться к оглавлению
Проверка при разрушающем контроле
Вернуться к оглавлению
Условия проведения механического способа контроля

Схема дефектов сварных швов.
Механическое разрушение изделий в процессе испытаний металлографическим методом необходимо для выявления характеристик сварных швов.
Объектом проводимых испытаний являются образцы со сварными швами, которые вырезают из сварных швов специально сваренных контрольных образцов соединений. Они представляют собой пробы, выполненные на основе соответствующих требований к технологическому уровню сварки изделий в специальных условиях. Требуется взять образцы, имеющие соответствующую форму и определенный размер.
Основная цель проведения контрольных проверок — это анализ и оценка:
- прочности сварного шва;
- качественного состояния металла;
- верного выбора технологии;
- квалификационного уровня рабочего-сварщика.
Сопоставить характеристики сварных швов можно со свойствами металла. При неудовлетворительных результатах соответствие итогов для заданного уровня не отмечается. Проведение механического испытания осуществляется на основе ГОСТа 6996-66, где указаны соответствующие виды проведения контрольных испытаний сварных металлических швов на:

Параметры для контроля качества сварного шва.
- Различных отдельных участках и в целом.
- Предмет статического растяжения и изгиба.
- Характер ударного изгиба.
- Уровень стойкости в условиях старения.
- Результат измерения характеристик твердости.
Проведение контрольных испытаний для выявления статистического растяжения связано с определением уровня прочности сварного шва. Определение статистического изгиба предполагает изучение свойств пластичности сварного шва. Испытания, связанные с обнаружением дефектов, проводятся до начала образования первых недочетов в области растянутой зоны с учетом угла изгиба.
Испытания на выявление статистического изгиба производят с использованием технологических образцов, взятых из узлов, имеющих поперечный или продольный шов. При проведении контроля на предмет ударного изгиба и разрыва определяется ударная вязкость сварного шва. По его выявленной твердости исследуется каждое из структурных изменений металла, значения степени его подкалки после сварочных работ и при последующем охлаждении.
Вернуться к оглавлению
Применение макро- и микроструктурных методов контроля

Схема микроструктуры сварного шва.
Исследование металлов, которое проводят на основе макро- и микроструктурного метода, включает не только процесс выявления присутствия дефектов определенного характера, но и определение качества сварного соединения.
Макроструктурный метод предполагает изучение макрошлифов, присутствующих в металле изломов, которые определяются с использованием лупы либо визуальным осмотром. Проведение макроисследований определяет характер каждого дефекта, его расположение, если они являются видимыми в различных зонах сварных швов.
Микроструктурный анализ связан с анализом структуры металлов. В процессе исследования возможно визуальное увеличение в 50-2000 раз, если используется оптический микроскоп. Проведение микроисследования связано с определением количества металла, обнаружением его пережогов, наличия оксидов в его структуре, засоренности сварных швов, наличия неметаллических включений. Это дает возможность изучать зерна металла, определяя их размер, исследовать изменения в составе металла. Возможно обнаружение микроскопических пор, трещин, иных дефектов, которые заполняют сварные швы.
Использование соответствующей методики, позволяющей изготавливать шлифы при металлографических исследованиях, связано с подготовкой образцов для контроля путем их вырезки из основного изделия. Проведение металлографического анализа связано с дополнительным использованием химических методов.

Металлографические исследования сварного шва.
Проведение испытаний позволяет получить соответствующие характеристики сварных швов, которые учитывают соответствующие условия применения сварных металлических конструкций. Процесс контроля связан с выявлением коррозионной стойкости изделий, функционирующих в агрессивных средах.
Все соответствующие методы контроля применяются в процессе разрушения конструкций. Протекание этих испытаний основано на способности конструкции к выдерживанию заданной расчетной нагрузки и определении разрушающих нагрузок, имеющих определенный запас прочности.
Проводя испытания разрушаемых конструкций, следят за состоянием схемы разрушения, которая должна быть сопоставлена с условиями работы конструкции. Количество изделий, подвергаемое испытаниям, должно соответствовать установленным техническим условиям, что определяется существующей организацией производственного процесса.
Вернуться к оглавлению
Метод неразрушающего контроля сварных швов
Контроль, являющийся неразрушающими, связан не только с проведением внешнего осмотра, включая исследование непроницаемости швов. Он позволяет обнаружить дефекты на поверхности, которые могут быть внутренними и скрытыми.
Обмер, связанный с проведением внешнего осмотра сварного шва, можно считать распространенным по причине его простоты. Приемка любых сварных готовых узлов осуществляется после проведения первых операций по контролю.
Контроль непроницаемости сварного шва предполагает соответствие стандартам изделий в плане герметичности, то есть непроницаемости, с учетом используемых газов и жидкостей.

Схема контроля герметичности с помощью вакуумной камеры.
Контроль изделий и узлов производится, когда они уже являются полностью готовыми.
Если внешний осмотр показал наличие каких-либо дефектов, то их требуется устранить перед началом осуществления испытаний. Контроль герметичности сварных швов осуществляется с использованием таких методов, как:
- Капиллярный (керосин).
- Химический (аммиак).
- Пузырьковый (гидравлическое или воздушное давление).
- Вакуумирование.
Остановимся подробнее на данных способах контроля.
Вернуться к оглавлению
Капиллярное исследование
Применение капиллярного метода основано на определенном свойстве жидкостей, связанном с возможностью проникновения через капилляры, представляющие собой микроскопические трещины, в структуру металлов. Капиллярный метод связан с активностью жидкости в капиллярах. Жидкость способна втягиваться, проникая в капилляры. Применение определенных из них (керосина) позволяет обнаружить наличие сквозных дефектов сварных швов.

Таблица для капиллярного контроля сварных швов.
Использование капиллярного контроля связано с осуществлением проверки любых сварных изделий без учета их форм, размеров и материалов, из которого они сделаны. Данный метод является более подходящим при обнаружении различных недостатков на поверхности швов. Недостатки являются невидимыми, поэтому их нельзя обнаружить простым невооруженным глазом, а также с лупой.
Испытать сварные швы на плотность на основе капиллярного способа позволяют специальные вещества, которые носят название пенетранты. Проникая в структуру исследуемых материалов с дефектами на поверхности сварного соединения, они окрашивают их в яркий цвет, позволяющий быстрее увидеть трещину.
При высоком уровне смачиваемости жидкости и наименьшем радиусе капилляра происходит увеличение глубины и скорости проникновения жидкости. В результате применения капиллярного метода можно обнаружить не только невидимые или слабовидимые дефекты с открытой полостью. Вместе с тем данный способ позволяет выявлять и сквозные виды дефектов, если в процессе их обнаружения использовать керосин.
Вернуться к оглавлению
Химический контроль и его применение

Для контроля качества сварных швов химическим методом используют раствор мела в воде.
Для покрытия сварных швов используется раствор мела в воде, которым обрабатывается доступная сторона шва, что позволяет провести тщательный осмотр и выявить все дефекты. После высушивания окрашенной поверхности шов следует обильно смочить керосином. Если швы неплотные, то это выявляется при наличии покрытия мелом и следов керосина на нем.
Контроль за счет аммиака проводится при наличии индикаторов, способных менять свою окраску при наличии щелочной среды, оказывающей воздействие на него. Реагентом в данном процессе выступает газ аммиак, который используют для контроля.
Проводя испытания, с одной стороны шва укладывают ленту из бумаги, которая смочена в 5%-тном растворе специального индикатора. На противоположной стороне шва проводится обработка соединения за счет смеси газообразного аммиака и воздуха. При проникновении аммиака через неплотные сварные швы происходит его окрашивание в местах наличия дефектов.
Вернуться к оглавлению
Методы контроля гидравлического и воздушного давления
Контроль воздушным давлением проводится при проверке на основе анализа герметичности сварных швов. Для этого их погружают полностью в ванну, наполненную водой. Далее в нее осуществляется подача сжатого воздуха с учетом уровня давления, которое превышает рабочее на 10-20%.
Если конструкции являются крупногабаритными, то их покрывают пенными индикаторами после того, как осуществлена подача внутреннего давления по сварному шву. В качестве пенного индикатора может выступать мыльный раствор. Если в сварных швах есть различные неплотности, то начинают появляться пузырьки воздуха. Испытание за счет сжатого воздуха либо газа должно сопровождаться соблюдением правил требуемой безопасности.
Прочность и плотность изделий проверяют путем контроля при наличии гидравлического давления. Предварительно швы полностью герметизируют с использованием водонепроницаемых заглушек. Просушку воздушных швов осуществляют за счет воздушного обдува. После этого следует заполнить изделие в условиях избыточного давления водой, что в 1,5-2 раза превышает уровень рабочего давления. Далее следует выдержать требуемый период. Там, где проявляется течь, можно обнаружить дефекты.
Вакуумный контроль связан с проведением испытания сварного шва, который не поддается испытанию с использованием керосина, воды или воздуха. В процессе проведения испытаний шов регистрируется на предмет проникновения воздуха через недочеты сварного шва. Регистрацию производят на одном и том же участке шва с одной и той же стороны изделия, где создается вакуум.
moiinstrumenty.ru
Дефектоскопия сварных швов - виды контроля качества
Окончание сварных работ – это начало контроля качества сварных соединений. Ведь понятно, что от качества проведенных работ зависит долгосрочная эксплуатация сборной конструкции. Дефектоскопия сварных швов – это методы контроля сварных соединений. Их несколько, поэтому стоит разобраться в теме досконально.
Виды контроля сварных соединений
Существует видимые дефекты сварочного шва и невидимые (скрытые). Первые легко можно увидеть глазами, некоторые из них не очень большие, но при помощи лупы обнаружить их не проблема. Вторая группа более обширная, и располагаются такие дефекты внутри тела сварного шва.
Обнаружить скрытые дефекты можно двумя способами. Способ первый – неразрушающий. Второй – разрушающий. Первый вариант, по понятным причинам, используется чаще всего.
Неразрушающий способ контроля качества сварных швов В этой категории несколько способов, использующихся для проверки качества сварных швов.
- Визуальный осмотр (внешний).
- Магнитный контроль.
- Дефектоскопия радиационная.
- Ультразвуковая.
- Капиллярная.
- Контроль сварных соединений на проницаемость.
Есть и другие способы, но используются они нечасто.
Визуальный осмотр
С помощью внешнего осмотра можно выявить не только видимые дефекты швов, но и невидимые. К примеру, неравномерность шва по высоте и ширине говорит о том, что в процессе сварки были прерывания дуги. А это гарантия, что шов внутри имеет непровары.
Как правильно проводится осмотр.
- Шов очищается от окалин, шлака и капель металла.
- Затем его обрабатывают техническим спиртом.
- После еще одна обработка десятипроцентным раствором азотной кислоты. Она называется травление.
- Поверхность шва получается чистой и матовой. На ней хорошо видны самые мелкие трещинки и поры.
Внимание! Азотная кислота – материал, разъедающий металл. Поэтому после осмотра металлический сварной шов надо обработать спиртом.
О лупе уже упоминалось. С помощью этого инструмента можно обнаружить мизерные изъяны в виде тонких трещин толщиною меньше волоса, пережоги, мелкие подрезы и прочие. К тому же при помощи лупы можно проконтролировать – растет ли трещина или нет.
При осмотре можно также пользоваться штангенциркулем, шаблонами, линейкой. Ими замеряют высоту и ширину шва, его ровное продольное месторасположение.
Магнитный контроль сварных швов
Магнитные методы дефектоскопии основаны на создании магнитного поля, которое пронизывает тело сварного шва. Для этого используется специальный аппарат, в принцип работы которого вложено явления электромагнетизма.
Есть два способа, как определить дефект внутри соединения.
- С использованием ферромагнитного порошка, обычно это железо. Его можно использовать как в сухом виде, так и во влажном. Во втором случае железный порошок смешивают с маслом или керосином. Его посыпают на шов, а с другой стороны устанавливают магнит. В местах, где есть дефекты, порошок будет собираться.
- С помощью ферромагнитной ленты. Ее укладывают на шов, а с другой стороны устанавливают прибор. Все дефекты, которые оказываются в стыке двух металлических заготовок, будут отображаться на этой пленке.
Этот вариант дефектоскопии сварных соединений можно использовать для контроля только ферромагнитных стыков. Цветные металлы, стали с хромникелевым покрытием и другие таким способом не контролируются.
Радиационный контроль
Это, по сути, рентгеноскопия. Здесь используются дорогие приборы, да и гамма-излучение вредно для человека. Хотя это самый верный вариант обнаружения дефектов в сварочном шве. Они четко видны на пленке.
Ультразвуковая дефектоскопия
Это еще один точный вариант обнаружения изъянов в сварочном шве. В его основе лежит свойство ультразвуковых волн отражаться от поверхности материалов или сред с разными плотностями. Если сварной шов не имеет внутри себя дефектов, то есть, его плотность однородна, то звуковые волны пройдут сквозь него без помех. Если внутри дефекты есть, а это полости, наполненные газом, то внутри получаются две разные среды: металл и газ.
Поэтому ультразвук будет отражаться от металлической плоскости поры или трещины, и вернется обратно, отображаясь на датчике. Необходимо отметить, что разные изъяны отражают волны по-разному. Поэтому можно итог дефектоскопии классифицировать.
Это самый удобный и быстрый способ контроля сварных соединений трубопроводов, сосудов и других конструкций. Единственный у него минус – сложность расшифровки полученных сигналов, поэтому с такими приборами работают только высококвалифицированные специалисты.
Капиллярный контроль
Методы контроля сварных швов капиллярным способом основаны на свойствах некоторых жидкостей проникать в тело материалов по самым мельчайшим трещинкам и порам, структурным каналам (капиллярам). Самое главное, что этим способом можно контролировать любые материалы, разной плотности, размеров и формы. Неважно, это металл (черный или цветной), пластик, стекло, керамика и так далее.
Проникающие жидкости просачиваются в любые изъяны поверхности, а некоторые из них, к примеру, керосин, могут проходить сквозь достаточно толстые изделия насквозь. И самое главное, чем меньше размер дефекта и выше впитываемость жидкости, тем быстрее протекает процесс обнаружения изъяна, тем глубже жидкость проникает.
Сегодня специалисты пользуются несколькими видами проникающих жидкостей.
Пенетранты
С английского это слово переводится, как впитывающий. В настоящее время существует более десятка составов пенетрантов (водные или на основе органических жидкостей: керосин, масла и так далее). Все они обладают малым поверхностным натяжением и сильной цветовой контрастностью, что позволяет их легко увидеть. То есть, суть метода такова: наносится пенетрант на поверхность сварочного шва, он проникает внутрь, если есть дефект, окрашивается с этой же стороны после очистки нанесенного слоя.
Сегодня производители предлагают разные проникающие жидкости с разным эффектом обнаружения изъяном.
- Люминесцентные. Из названия понятно, что в их состав входят люминесцентные добавки. После нанесения такой жидкости на шов нужно посветить на стык ультрафиолетовой лампой. Если дефект есть, то люминесцентные вещества будут отсвечивать, и это будет видно.
- Цветные. В состав жидкостей входят специальные светящиеся красители. Чаще всего это красители ярко-красные. Они хорошо видны даже при дневном свете. Наносите такую жидкость на шов, и если с другой стороны появились красные пятнышки, то дефект обнаружен.
Есть разделение пенетрантов по чувствительности. Первый класс – это жидкости, с помощью которых можно определить дефекты с поперечным размером от 0,1 до 1,0 микрона. Второй класс – до 0,5 микрон. При этом учитывается, что глубина изъяна должна превосходить его ширину в десять раз.
Наносить пенетранты можно любым способом, сегодня предлагаются баллончики с этой жидкостью. В комплект к ним прилагаются очистители для зачистки дефектуемой поверхности и проявитель, с помощью которого выявляется проникновение пенетранта и показывается рисунок.
Как это надо делать правильно.
- Шов и околошовные участки необходимо хорошо очистить. Нельзя использовать механические методы, они могут стать причиной занесения грязи в сами трещины и поры. Используют теплую воду или мыльный раствор, последний этап – очистка очистителем.
- Иногда появляется необходимость протравить поверхность шва. Главное после этого кислоту убрать.
- Вся поверхность высушивается.
- Если контроль качества сварных соединений металлоконструкций или трубопроводов проводится при минусовой температуре, то сам шов перед нанесением пенетрантов надо обработать этиловым спиртом.
- Наносится впитывающая жидкость, которую через 5-20 минут надо удалить.
- После чего наносится проявитель (индикатор), который из дефектов сварного шва вытягивает пенетрант. Если дефект небольшой, то придется вооружиться лупой. Если никаких изменений на поверхности шва нет, то и дефектов нет.
Керосин
Этот способ можно обозначить, как самый простой и дешевый, но от этого эффективность его не снижается. Его проводят по этой технологии.
- Очищают стык двух металлических заготовок от грязи и ржавчины с двух сторон шва.
- С одной стороны на шов наносится меловой раствор (400 г на 1 л воды). Необходимо дождаться, чтобы нанесенный слой просох.
- С обратной стороны наносится керосин. Смачивать надо обильно в несколько подходов в течение 15 минут.
- Теперь нужно наблюдать за стороной, где был нанесен меловой раствор. Если появились темные рисунки (пятна, линии), то значит, в сварочном шве присутствует дефект. Эти рисунки со временем будут только расширяться. Здесь важно точно определить места выхода керосина, поэтому после первого нанесения его на шов, нужно сразу проводить наблюдение. Кстати, точки и мелкие пятнышки будут говорить о наличие свищей, линии – о наличии трещин. Очень эффективен этот метод при стыковочных вариантах соединение, к примеру, труба к трубе. При сварке металлов, уложенных внахлест, он менее эффективен.
Методы контроля качества сварных соединений на проницаемость
В основном этот способ контроля используется для емкостей и резервуаров, которые изготовлены методом сварки. Для этого можно использовать газы или жидкости, которыми заполняется сосуд. После чего внутри создается избыточное давление, выталкивающее материалы наружу.
И если в местах сварки емкостей есть дефекты, то жидкость или газ тут же начнут через них проходить. В зависимости от того, какой контрольный компонент используется в проверочном процессе, различаются четыре варианта: гидравлический, пневматический, пневмогидравлический и вакуумный. В первом случае используется жидкость, во втором газ (даже воздух), третий – комбинированный. И четвертый – это создание внутри емкости вакуума, который через дефектные швы будет втягивать внутрь резервуара окрашивающие вещества, наносимые на внешнюю сторону шва.
При пневматическом способе внутрь сосуда закачивается газ, давление которого превышает номинальный в 1,5 раза. С внешней стороны на шов наносится мыльный раствор. Пузырьки покажут наличие дефектов. При гидравлической дефектоскопии в сосуд заливается жидкость под давлением в 1,5 раза превышающее рабочее, производится обстукивание околошовного участка. Появление жидкости говорит о наличии изъяна.
Вот такие варианты дефектоскопии трубопроводов, резервуаров и металлоконструкций сегодня используют для определения качества сварного шва. Некоторые из них достаточно сложные и дорогие. Но основные просты, поэтому и часто используемые.
Поделись с друзьями
0
0
0
0
svarkalegko.com
Неразрушающие методы контроля сварных соединений, дефекты швов
После сборки ответственных узлов различного назначения, например, строительных конструкций, сосудов под давлением или деталей и секций кораблей, в обязательном порядке проверяется качество выполнения сварочных работ. Дефекты, выявленные во время проверки, подлежат устранению, если их количество и размеры превышают установленные для определенного вида изделий нормативы.

Виды сварных соединений.
Способы проверки качества
Качество сварочных работ подвергается контролю, начиная с проверки квалификации сварщиков до начала работ и заканчивая проверкой сварных соединений неразрушающими методами после их окончания. Методы контроля производят несколькими способами:
- осмотр стыков;
- контроль проницаемости;
- магнитные способы проверки;
- проверка с помощью ультразвука;
- просвечивание с помощью рентгеновских лучей;
- просвечивание гамма-излучением;
- метод люминесцентной дефектоскопии.

Методы контроля сварных конструкций.
Каждый из вышеперечисленных способов применяется с целью выявления дефектов определенного вида. Внешний осмотр позволяет обнаружить дефекты снаружи сварного стыка, производится с помощью измерительных приспособлений, шаблонов и лупы. Перед тем как приступить в проверке, место соединения очищают от загрязнений, шлака, брызг металла и окалины. Визуальный осмотр делается на всех сварных соединениях, при этом обнаруживаются непроваренные участки, трещины, кратеры, несоответствие размеров шва нормативным требованиям и прочие внешние дефекты.
Проверка проницаемости
Контроль проницаемости выполняется при монтаже трубопроводов и производстве различных металлических сосудов, работающих под давлением. Суть способа в том, чтобы создать внутри закрытого сосуда или трубопровода избыточное давление гидравлическим или пневматическим способом, а снаружи выявить места, в которых теряется герметичность. Гидравлическим способом проверяют изделия с толщиной стенки не выше 10 мм. Емкость или трубопровод наполняются водой и герметизируются, после чего насос создает в них давление, которое требуется по нормативам для данного вида изделия. Дефекты сварных соединений обнаруживают по каплям воды, струйкам или запотеванию на поверхности. В последнем случае потребуется выполнить контроль дополнительно другим методом.
Пневматический способ проверки герметичности заключается в повышении давления воздуха внутри изделия до определенного значения (0,1-0,2 бар). При этом наблюдают за падением давления в емкости по манометру, а сварные швы промазывают мыльной пеной, в местах дефектов появятся пузыри.
Магнитный способ обследования

Рисунок 1. Схема магнитного способа проверки.
Магнитные методы проверки качества сварных соединений основаны на изменениях формы магнитного поля при огибании им скрытых дефектов или пор внутри металла. Изменение поведения магнитного поля можно увидеть на рис. 1: а) соединение без дефекта, б) с дефектом.
Чаще всего применяется для обследования швов магнитопорошковая дефектоскопия. Она выполняется сухим или мокрым способом. Первый осуществляют нанесением на исследуемые поверхности сухого магнитного порошка, обычно это окись железа. В некоторых случаях используют окалину мелкого помола. После этого материал намагничивают, порошок принимает форму магнитных полей, огибающих скрытые дефекты, которые можно изучить визуально. Мокрый способ отличается тем, что на поверхность набрызгивают или поливают магнитную суспензию. Эта жидкость представляет собой керосин либо трансформаторное масло, в котором частицы магнитного порошка находятся во взвешенном состоянии. После нанесения порошок опять же принимает форму магнитных полей.
Магнитный метод эффективен при небольшой толщине металла и обнаруживает трещины, непроваренные участки, разрывы и поры. Его недостатки следующие:
- Дефекты, расположенные параллельно плоскости поверхности (трещина, расслоение), данный метод обнаружить не сможет.
- Метод неприменим для проверки стыков нержавеющих и цветных металлов и сплавов, не поддающихся намагничиванию.
- Магнитопорошковая дефектоскопия не выявляет дефекты глубокого залегания, поэтому не может использоваться для обследования металла большой толщины.
Проверка ультразвуком
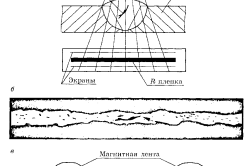
Схема контроля сварного соединения: а — просвечиванием рентгеновскими лучами, б — рентгенограмма шва, в — намагничиванием.
Сварные соединения проверяют способом ультразвуковой дефектоскопии при толщине шва свыше 4 мм. Данный метод — акустический, основан на способности к отражению звуковых волн определенной частоты (25-50 кГц) ультразвукового диапазона. Для справки: ухо человека способно воспринимать звук частотой до 20 кГц. Методы контроля сварных соединений с помощью УЗД позволяют обнаружить такие внутренние дефекты, как поры, расслоения материала, трещины, включения шлака, непроваренные области. При прохождении звуковой волны сквозь толщу металла она отражается от тех мест, где материал перестает быть однородным и переходит в дефект, это отражение фиксирует дефектоскоп.
Перед тем как приступить к диагностике, сварные швы и поверхность на расстоянии 60-120 мм от них следует зачистить угловой шлифовальной машиной или иным механическим способом. Наружные дефекты, ранее обнаруженные при визуальном осмотре, перед акустической диагностикой нужно устранить, чтобы они не повлияли на результаты обследования.
Контроль с помощью УЗД бывает нескольких разновидностей, больше всего применяется проверка эхо-методом. Щуп, посылающий звуковые волны в толщу металла в определенном направлении, располагают на поверхности сварного шва. Для того чтобы ультразвук полностью проходил в материал, пространство между щупом и поверхностью металла заполняют контактной средой, в качестве которой может выступать вода либо минеральное масло. Звуковые волны подают под различными углами к поверхности (40⁰, 50⁰, 60⁰, 65⁰, 70⁰). Встретив на своем пути дефект, ультразвук отражается и улавливается дефектоскопом, расположенным в том же щупе либо в отдельном исполнении (при двухщуповой комплектации прибора).

Рисунок 2. Схема радиологического способа проверки.
Происходит преобразование звукового сигнала в электрический, который поступает на осциллограф, в результате чего на его экране можно увидеть скачок графика.
Современные модели ультразвуковых дефектоскопов укомплектованы микропроцессором и позволяют посылать импульсы в металл с разных позиций и сразу под несколькими углами, отражая состояние проверяемого материала наиболее точно. Неразрушающие методы с применением УЗД выявляют местонахождение, количество и геометрические размеры дефектов, но не дают расшифровку его видов, что является единственным недостатком этого способа контроля.
Радиологические способы обследования
При толщине свариваемых элементов до 60 мм контроль сварных соединений осуществляется просвечиванием рентгеновским излучением. Место соединения очищают от шлака, окалины, брызг металла и грязи. Дефекты, обнаруженные ранее с помощью визуальной проверки, должны быть устранены, так как результатом обследования является выявление внутренних дефектов.
Рентгеновскую трубку, которая является источником излучения, располагают перед проваренным швом таким образом, чтобы пучок лучей проходил перпендикулярно его оси. Сзади изделия устанавливают кассету со специальной пленкой, чувствительной к рентгеновскому излучению. Схему расположения приборов можно увидеть на рис. 2: 1 — рентгеновская трубка; 2 — кассета; 3 — фотопленка; 4 — экраны.
Изделие просвечивают в течение определенного времени, которое зависит от параметров пленки, расстояния от рентгеновской трубки до шва, толщины изделия и мощности излучения. После проверки пленку проявляют, в тех местах, где находятся дефекты, она будет засвечена сильнее. Появятся более темные области, по которым можно судить о характере дефектов и их размерах. Для того чтобы узнать глубину залегания этих областей, со стороны рентгеновской трубки параллельно сварному шву устанавливают дефектометр, который служит эталоном. Он представляет собой пластину, которая имеет такую же толщину, как и глубина шва, и такой же материал по своему составу.

Этапы контроля сварных соединений.
Данный метод распространен в промышленности, так как дает очень полную картину того, в каком состоянии находится место сварки двух или более деталей. Еще одно преимущество — возможность автоматизации и механизации процесса. Современные технологии позволяют устанавливать сзади изделия вместо пленки специальный экран, регистрирующий интенсивность излучения на выходе из металла. Свои показания экран передает в виде электрического сигнала на видеомонитор, при этом исследуемый образец перемещают, в результате чего на мониторе можно видеть состояние сварного шва в реальном времени. Такой способ называется радиоскопическим.
По способу проведения обследования радиологический контроль с помощью гамма-излучения мало отличается от просвечивания рентгеном.
Разница есть в толщине исследуемого изделия, она может достигать 300 мм. Кроме того, источник гамма-излучения действует во все стороны, а не в одну, что дает возможность произвести проверку сразу нескольких изделий за один раз. В капсулах, используемых для этого метода, применяются следующие радиоактивные материалы: иридий — 192, цезий — 137, тулий — 170, кобальт — 60. Еще одно преимущество перед рентгеновской трубкой — длительный срок службы радиоактивных источников, от 5 до 30 лет.
Радиологические неразрушающие методы контроля, к которым относится как рентгеновское просвечивание, так и обработка гамма-излучением, имеет свои недостатки:
- Капсулы с изотопами радиоактивных элементов представляют опасность, их требуется хранить в особых контейнерах в специально оборудованных помещениях, что не всегда возможно осуществить. При работе оператору необходимо следить за временем работы и дозиметром, чтобы уберечь свое здоровье от передозировки радиацией.
- Чувствительность просвечивания гамма-излучением понижается при толщине свариваемых элементов менее 50 мм, время выдержки при съемке увеличивается по сравнению с рентгенографией.
- Оба метода могут не заметить некоторые виды дефектов. Это непроваренные области и трещины с очень малым раскрытием в металле толщиной до 40 мм. Поэтому для проверки сосудов или трубопроводов из менее тонкого металла лучше применять другие способы контроля, например, УЗД.
Люминесцентная дефектоскопия — относительно простой капиллярный метод контроля качества сварных соединений. На шов наносят ярко-красную проникающую жидкость либо флуоресцирующий раствор. Через некоторое время жидкость убирают, а поверхность освещают источником ультрафиолета, в результате чего хорошо становятся видны все наружные дефекты соединения.
Каждую из методик неразрушающего контроля сварных стыков следует применять по назначению и в условиях, при которых она наиболее эффективна, это позволит исключить брак свариваемых элементов ответственных конструкций и изделий.
moyasvarka.ru