Большая Энциклопедия Нефти и Газа. Прессовая сварка
Прессовая сварка - Большая Энциклопедия Нефти и Газа, статья, страница 1
Прессовая сварка
Cтраница 1
Прессовая сварка более универсальна и применяется для соединения изделий различной формы, изготовленных из термопластичных или из отвержденных пластмасс. Соединение производят внахлестку, встык, встык с одной или двумя накладками, втавр, на ус - во всех случаях преимущественно без присадочного материала. Единственным назначением присадочного материала в перечисленных случаях является достижение более полного контакта между соединяемыми поверхностями. [1]
Прессовая сварка позволяет приваривать тонкие листы к толстым по всей площади соприкосновения и при меняется при изготовлении специального режущего инструмента и многослойного металла. [2]
Прессовая сварка позволяет приваривать тонкие листы к толстым по всей площади соприкосновения и применяется при изготовлении специального режущего инструмента и многослойного металла. [3]
Прессовая сварка по методу Игнатьева ( см. фиг. Для провара по всей плоскости касания заготовка из инструментальной стали делается более узкой, чем заготовка из углеродистой стали, или врезается в нее. Каждая сварная заготовка разрезается после термической обработки на несколько частей ( фиг. [4]
Прессовая сварка ( рис. 61) применяется при соединении листовых материалов одновременно по всему периметру или значительной его части. При этом используются сменные электроды ( штампы), предназначенные для образования сварных швов заданной конфигурации и размеров. [5]
Прессовая сварка применяется во многих отраслях промышленности. Все шире ее используют при производстве металлорежущего инструмента. Изготовление биметаллических - ( двухслойных) пластин без расплавления ( рис. 49) для резцов является одним из эффективных способов экономии дорогостоящей быстрорежущей стали. [7]
Прессовая сварка применяется во многих отраслях промышленности. Все шире ее используют при производстве металлорежущего инструмента. Изготовление биметаллических ( двухслойных) пластин без расплавления ( рис. 49) для резцов является одним из эффективных способов экономии дорогостоящей быстрорежущей стали. [9]
Прессовая сварка с помощью контактных нагревателей является единственно возможным методом сваривания фторопла-ста-4. [11]
Прессовая сварка термопластов и прессовая сварка отвержденных пластмасс ничем не отличаются друг от друга, и их можно осуществлять по одним и тем же схемам. [13]
Лучевая прессовая сварка - вид сварки термомеханического класса, объединяющий способы сварки, при которых для передачи энергии в форме теплоты к соединяемым поверхностям используют электромагнитное излучение видимой или инфракрасной области спектра ( диапазон длин волн 0 4 - 15 мкм), а образование сварного соединения осуществляют с приложением давления. В литературе этот вид сварки чаще называется сваркой излучением. [14]
Страницы: 1 2 3 4 5
www.ngpedia.ru
ПРЕССОВАЯ СВАРКА - это... Что такое ПРЕССОВАЯ СВАРКА?
сварка давлением, при к-рой для нагрева соединяемых частей и рабочих инструментов - штампов используется теплота, выделяющаяся при прохождении электрич. тока через проволочные сопротивления. Применяется преимущественно для алюм. сплавов, реже для конструкц. и легир. сталей.
Большой энциклопедический политехнический словарь. 2004.
- ПРЕССОВАННЫЕ ПРОФИЛИ
- ПРЕССОВАЯ СЕЯЛКА
Смотреть что такое "ПРЕССОВАЯ СВАРКА" в других словарях:
Сварка — Сварщик за работой Сварка это технологический процесс получения неразъёмного соединения посредством установления межатомных и межмолекулярных связей между свариваемыми частями изделия при их нагреве (местном или общем), и/или … Википедия
СВАРКА В ТВЕРДОМ СОСТОЯНИИ — [solid phase welding] получение неразъемного соединения за счет образования химических (металлических) связей при совместной пластической деформации в контактной зоне соединяемых материалов. Способы сварки в твердом состоянии (термокомпрессионная … Металлургический словарь
прессовый — ая, ое. 1. Отн. к прессу, связанный с работой пресса. Прессовый цех. Прессовый поршень. Прессовое оборудование. БАС 1. Прессовые железные доски, прессовые железы, клещи, которыми кладут горячие прессовые железы между половинок.. пяльцы деревянные … Исторический словарь галлицизмов русского языка
Технология авиастроения — область технологии машиностроения, включающая процессы, методы, способы и технические средства изготовления изделий авиационной техники. В начальный период развития авиационной техники Т. а. располагала ограниченными средствами, которые… … Энциклопедия техники
Казанское авиационное производственное объединение имени С. П. Горбунова — Казанское авиационное производственное объединение имени С. П. Горбунова … Википедия
Пресс-ножницы комбинированные — – кузнечно прессовая машина, сочетающая в себе комбинированные ножницы и пресс для пробивки отверстий. [Толковый словарь Ефремовой. Т. Ф. Ефремова. 2000.] Рубрика термина: Арматурное оборудование Рубрики энциклопедии: Абразивное… … Энциклопедия терминов, определений и пояснений строительных материалов
технология авиастроения — технология авиастроения область технологии машиностроения, включающая процессы, методы, способы и технические средства изготовления изделий авиационной техники.В начальный период развития авиационной техники Т. а. располагала ограниченными … Энциклопедия «Авиация»
технология авиастроения — технология авиастроения область технологии машиностроения, включающая процессы, методы, способы и технические средства изготовления изделий авиационной техники.В начальный период развития авиационной техники Т. а. располагала ограниченными … Энциклопедия «Авиация»
dic.academic.ru
Холодная и прессовая сварка - Сварка металлов

Категория:
Сварка металлов

Холодная сварка выполняется без применения нагрева, одним приложением давления, создающим значительную пластическую деформацию; металл на всем протяжении процесса сварки остается холодным. Принципиальная возможность холодной сварки металлов известна давно, но разработка методов, отвечающих требованиям современной промышленности, является делом новым.
Сущность холодной сварки состоит в том, что атомы металла у поверхности соприкосновения соединяемых частей приводятся в соприкосновение или сближаются примерно на те же расстояния, на которых они находятся внутри металла.
Задача сближения большого количества атомов, что необходимо для получения прочного соединения, является технически достаточно трудной. Прежде всего действительному полному соприкосновению соединяемых поверхностей мешает твердость холодного металла, его сопротивление воздействию внешних сил, деформирующих металл. Наиболее тщательно отшлифованные поверхности металла имеют все же многочисленные неровности, выступы и впадины, величина которых во много раз превышает размеры атома. Приложение даже очень больших удельных давлении не может вызвать действительное соприкосновение по всей площади соединяемых поверхностей; после снятия давления возникшие соединения металла в немногих точках действительного соприкосновения разрываются действием упругих сил. Очень важным препятствием для прочного соединения твердых металлов являются также загрязнения поверхности и наличие пленки адсор-нтрованных газов. Пленка адсорбированных газов после зачистки мгновенно восстанавливается, если металл соприкасается с атмосферой. Действительно чистую поверхность металла можно получить и сохранять только в высоком вакууме.
Пластическая деформация металла является необходимым условием для выполнения холодной сварки. Деформация должна быть не ниже определенного значения, характерного для данного металла. Усилие для создания этой деформации зависит от многих обстоятельств и может меняться в широких пределах. Поэтому не всегда легко заранее определить усилие, необходимое для холодной сварки, и обычно задается не усилие осадки, а величина деформации.
Течение металла должно происходить вдоль поверхности раздела, приблизительно параллельно ей. При этом разрушаются и раздробляются поверхностные слои металла с загрязнениями, на поверхность выдвигаются свежие слои с чистыми, ювенильными поверхностями; происходит перемешивание и тесное соприкосновение атомов металла соединяемых частей и возникает прочное сварное соединение.
Существенное значение для холодной сварки имеет зачистка соединяемых поверхностей, осуществляемая вращающимися проволочными не слишком жесткими щетками или путем шабрения со снятием пленки окислов и тонкого поверхностного слоя металла. Зачистка напильником и абразивными материалами дает худшие результаты и, как правило, не рекомендуется. Недостаточно устойчивы результаты химической очистки различными растворами
Зачищенные поверхности алюминия сохраняют пригодность к сварке несколько дней при условии, что на зачищенную поверхность не попадут никакие загрязнения. Особенно опасны жировые пленки, поэтому недопустимо прикосновение руками к зачищенным поверхностям. Холодная сварка является методом универсальным, пригодным для многих металлов. Этим способом могут быть соединены и неметаллические твердые тела, обладающие достаточной пластичностью: смолы, пластмассы, стекла и т. д.
Имеется несколько разновидностей этого способа. Первым по времени разработан способ точечной холодной сварки, по форме соединения напоминающий контактную точечную сварку, особенно удобный для соединения листового металла (рис. 211). Листы металла с тщательно зачищенной поверхностью места сварки помещают между пуансонами с рабочей частью — выступом или зубком.
Рис. 1. Холодная точечная сварка
Рис. 2. Деформация металла при точечной сварке
Рис. 3. Разрез сварной точки
Указанные значения остаточной толщины являются максимальными, при которых еще возможна прочная качественная сварка; на практике нередко применяют и более глубокое вдавливание пуансонов, уменьшая остаточную толщину и иногда сводя ее к нулю.
Прочность сварной точки пропорциональна скорее ее периметру, чем площади; сварка захватывает полосу, окружающую точку по периметру; высверливание точки не очень сильно уменьшает ее прочность. На рис. 3 схематически показано направление течения металла при вдавливании точечных пуансонов и зона сварки, значительно выходящая за пределы вмятины. Форма и размеры сварных точек могут быть весьма разнообразныи определяются конфигурацией рабочей части пуансона. Часто применяются узкие прямоугольные 10Чки Длиной, в несколько раз превышающей ширину.
Точечной сваркой можно соединять и разнородные металлы, например алюминий с медью. При наличии соединения с несколькими точками целесообразно применять штампы с несколькими пуансонами, сваривающими сразу все точки за один ход пресса. При сварке нескольких близко расположенных точек по одной поочередно часто наблюдается значительное коробление деталей и некоторое ослабление точки сваркой последующей точки. Для устранения этих явлений применяют обжимные приспособления; детали плотно сжимаются значительным усилием и затем свариваются точками в сжатом состоянии.
Точечной сваркой успешно соединяются листы толщиной от 0,1—0,2 до 12—15 мм. Усилие на одну точку при сварке алюминия в среднем 1,5—12 т. Давление на рабочую поверхность пуансона 60—80 кГ/мм2, в зависимости от разных условий.
Рис. 5. Схема стыковой холодной сварки
Рис. 6. Облицовка алюми-ниевых шин медью
Недостатком точечной сварки является глубокая вмятина в металле, часто на 80—90% его толщины. В настоящее время изыскиваются способы уменьшения глубины вмятины. Заменив точечные пуансоны стальными роликами соответствующей конфигурации, катящимися по металлу, можно осуществить шовную холодную сварку.
Возможна и стыковая холодная сварка (рис. 5). Подлежащие сварке стержни 1 зажимают в зажимах. При осадке правый и левый зажимы сближают до соприкосновения и острый край зажима, как нож, отрубает излишний выдавленный металл — грат. В процесс осадки сближающиеся зажимы затрудняют течение металла и позволяют увеличить давление осадки. Деформируемый и текущий подобно жидкости металл стержней заполняет насечку 3, играющую роль уплотнителя и мешающую вытеканию металла и смещению его в зажимах. Величина удельного давления для технически чистого алюминия 50—70 кГ/мм2.
Таким образом свариваются стержни и проволоки круглого, квадратного и прямоугольного сечения, полосы и т. п. Место сварки получается чистым и не требует последующей обработки-Металл в зоне сварки упрочняется вследствие наклепа, и разрыв при испытаниях происходит всегда вне зоны сварки. Стыковое соединение, выполненное холодным способом, безупречно по
(Ьорме, что же касается соединений нахлесточного, точечного или шовного, то они имеют глубокие вмятины.
Из наиболее важных для промышленности металлов лучше всего свариваются холодным способом технически чистые алюминий и медь. Оба металла вследствие высокой электропроводности широко применяются в электропромышленности, где холодная сварка уже используется в значительных размерах. На очереди стоит вопрос освоения холодной сварки прочных конструкционных сплавов алюминия: дюралюминия, АМц, АМг и др., что позволит использовать холодную сварку в самолетостроении и других отраслях промышленности. Точечная холодная сварка уже нашла некоторое применение в производстве алюминиевой посуды, электрических чайников и т. п. Освоена точечная сварка алюминиевых шин в электрических распределительных устройствах.
Начинает применяться облицовка алюминиевых шин листовой медью (рис. 216). Алюминиевую шину с зачищенными под сварку поверхностями обертывают мягкой листовой медью толщиной 0,8—1 мм с зачищенной поверхностью; медную облицовку с обеих сторон приваривают к алюминию несколькими точками за один ход пресса. Размер точки примерно 12X2 мм. После сварки сверлят или пробивают отверстия для сборочных болтов; поверхность медной облицовки может быть облужена. Алюминиевые шины, облицованные медью в местах присоединений, дают хороший электрический контакт и вполне работоспособны. Применение алюминиевых шин полностью себя оправдало и дает значительную экономию дефицитной меди.
Точечную сварку можно выполнять на любых прессах: гидравлических, эксцентриковых и т. п. Если сразу сваривается несколько точек за один ход пресса, что является наиболее совершенным приемом, то требуются прессы усилием 50—100 т. Для сварки одной точки достаточны прессы усилием 5—10 т. Такие гидравлические прессы могут быть выполнены легкими переносными с ручным или педальным приводом; они довольно широко применяются на электромонтажных работах и легко могут быть приспособлены для точечной сварки.
Находит производственное применение и стыковая холодная сварка. Например разработаны ручные клещи типа КС-6 (рис. 217) Для стыковой сварки алюминиевых проводов сечением 2,5—10 мм2; вес клещей около 1,4 кг. Клещамп можно сваривать медные Г|ровода сечением 2,5 и 4 мм2, а также алюминиевые с медными.
Рис. 7. Клещи КС-6 для холодной сварки проводов
Клещи КС-6 применяются на электромонтажных работах. Свежеобрезанные концы проводов закладывают в клещи, зажимают и сваривают при нажатии на ручки клещей. Место стыка имеет чистую поверхность и не требует дальнейшей обработки, излишний выдавленный металл — грат — отрубается в клещах одновременно с процессом сварки. Металл в зоне сварки нагарто-ван и имеет высокую прочность, разрушение при всех видах нагрузок происходит вне зоны сварки. Металлографическое исследование сварного соединения показывает высокую плотность металла, его электропроводность выше, чем металла остального провода. По-видимому, обработка давлением порядка 60 кГ/мм2 заметно улучшает качество металла в зоне сварки, делает его более плотным и однородным.
Начинает находить промышленное применение стыковая сварка и более крупных сечений, для чего конструируются стыковые машины с гидравлическим или электрическим приводом. Стыковая сварка алюминия с медью широко применяется в электротехнической промышленности при изготовлении токоведущих деталей.
Стыковое соединение считается более надежным по сравнению с нахлесточным. Применяется стыковая сварка троллейных проводов на электротранспорте, проволок на проволочных и кабельных заводах. Здесь холодная сварка ценна высокой прочностью стыка, «горячие» способы сварки вызывают уменьшение прочности вследствие отжига металла. Холодная сварка успешно применяется для изготовления теплообменников для бытовых холодильников. При изготовлении теплообменника два алюминиевых листа свариваются по всей поверхности соприкосновения посредством совместной прокатки. Общий расход электроэнергии при холодной сварке в 20—SO раз меньше, чем при контактной электросварке.
Шовная сварка используется для изготовления тонкостенных алюминиевых труб и оболочек.
Применение холодной сварки ограничивается физическими свойствами металлов. Недостаточно пластичные металлы, например высокопрочные алюминиевые сплавы, часто дают трещины при таких больших деформациях, которые необходимы для холодной сварки. Высокопрочные металлы даже и при достаточной пластичности практически не свариваются холодным способом; требующиеся удельные давления настолько велики, что практически невозможно изготовить достаточно прочные приспособления и рабочий инструмент.
Твердость металлов может быть снижена, а пластичность повышена подогревом до соответствующей температуры. Опыт показал, например, что высокопрочные алюминиевые сплавы при температуре 300—350° С, а низкоуглеродистая сталь при температуре 900—-1000° С свариваются за счет соответственно направленной пластической деформации, подобно технически чистому аиюминию при комнатной температуре. От давно известной кузнечной или горновой сварки такой способ отличается характером птастической деформации, аналогичным характеру деформации при холодной сварке: деформация значительна, распространяется в строго определенном направлении; развитие ее стеснено; удельные давления высоки и во много раз превосходят предел текучести нагретого металла. Нагрев может создавать значительную диффу-зию и рекристаллизацию, способствующих получению прочного сварного соединения.
Применение нагрева делает неподходящим название «холодная» сварка. Может быть предложено название «прессовая сварка», которое шире, чем «холодная сварка», и охватывает все разновидности способа, как с применением нагрева, так и без него. Несомненно, что прессовая сварка в указанном расширенном понимании — с применением нагрева в необходимых случаях, найдет широкое промышленное применение.
Рис. 8. Сварка биметаллической заготовки
Читать далее:
Сварка взрывом
Статьи по теме:
Реклама:
Главная → Справочник → Статьи → Блог → Форум
pereosnastka.ru
Дуго-прессовая сварка
пер.Каштановый 8/14 51100 пгт.Магдалиновка
Nikolaenko Dmitrij
Дуго-прессовая сварка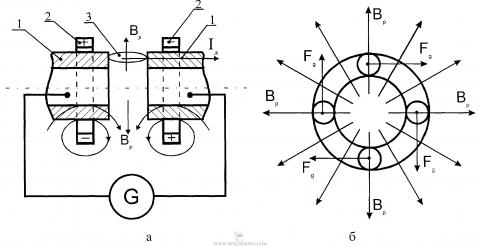
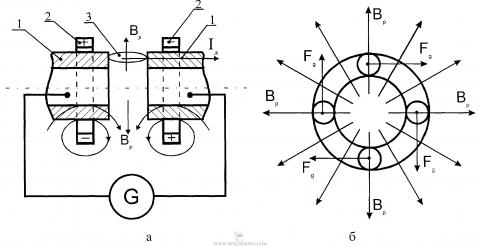
Дуго-прессовая сварка относительно новый вид сварки, используемый для сваривания деталей узкой направленности. В основном ее используют для присоединения деталей (типа шпильки) к металлической пластине. Характерной особенностью этой сварки является то, что сама заготовка является электродом. Если заготовка из нелегированной или низколегированной стали, то для соединения применяют подкладное флюсовое кольцо, защищающее шов от окисления. Когда заготовка из легких или тяжелых металлов, применяются специальные защитные газы. Такими газами могут быть азот или углекислый газ. Допустимые параметры присоединяемой детали:
- труба может быть диаметром от 6мм. до 219 мм., толщина стенки 10 мм;
- заготовка сплошного сечения максимальный диаметр 32 мм.
Процесс работы такой сварки:
- заготовку подготавливают к сварке;
- в специальное сварочное приспособление (сварочный пистолет) вставляют заготовку;
- подводят к пластине или металлической плите, на которую она будет привариваться;
- подается ток, возбуждается сварочная дуга, оплавляющая соединяемые металлы;
- электрическую цепь отключают и производят соединение деталей ударом шпильки.
Окислы металлов и загрязнения устраняются вместе с жидким металлом. Качество такого соединения достаточно высокое, чтобы выдерживать значительные нагрузки.
В настоящее время разработана система автоматического поддержания зазора сварочной дуги, что значительно повысило эффективность процесса соединения деталей. Такая технология основана на законах физики, а именно, электрическая дуга перемещается в поперечном магнитом поле. Это поле создается постоянными магнитами между торцами свариваемых деталей. Относительно высокая скорость перемещения дуги побуждает ее мощность перераспределяться по всей поверхности детали. Благодаря этому происходит равномерный нагрев свариваемых торцов. Чтобы придать максимальный нагрев поверхности, дуговой зазор между торцами деталей поддерживается в заданных пределах. Дуго-прессовая сварка в современном мире шагнула далеко вперед. Сварочное оборудование способно работать двумя способами:
- Ускоренным;
- Дуговым.
Ускоренный метод производится очень быстро, позволяет использовать шпильки с любым наконечником. Деталь можно приварить на грязную или жирную поверхность металла, толщина которого не должна превышать 0,6 мм. Защитой сварочной ванны служит защитный газ. Применение газа особенно важно при сварке алюминия. Свариваемые шпильки могут быть из разного материала и величины.
Дуговой метод не особо отличается от ускоренного. Его применяют для приваривания накладных шпилек разных геометрических форм на металлическую поверхность, толщина которой должна быть не меньше 1/4 от диаметра шпильки. Для защиты сварочной ванны от внешнего влияния, используют керамические шайбы. Дуго-прессовая сварка прочно сваривает металлы, применяя высокоточное сварочное оборудование «Alpha 850», в котором применяется метод вытягивающейся дуги с коротким циклом. Таким же способом работает сварочное оборудование «Nelweld». Области применения такой сварки находят:
- в транспортном машиностроении, вагоностроении и судостроительстве;
- в химическом приборостроении;
- для жесткого крепления при производстве светильников.
Опубликовано/отредактировано: 2018-01-17
metallsmaster.ru
Глава 4. ПРЕССОВЫЕ И МЕХАНИЧЕСКИЕ СВАРОЧНЫЕ ПРОЦЕССЫ
При контактной сварке принципиально возможно вести процесс в двух вариантах: 1) с нагревом металла до высокопластичного состояния без плавления; 2) с плавлением металла в зоне сварки и образованием литой структуры (литого ядра).
Оба эти процесса находят промышленное применение, однако сварка с плавлением энергетически выгоднее, так как сопротивление переходного контакта в этом случае обычно больше и требуются меньшие сварочные токи. Кроме того, образование литого ядра — известная гарантия получения качественного сварного соединения, так как ядро может быть значительно более просто проконтролировано, чем зона деформации при сварке без плавления.
Сварка токами высокой частоты. Этот способ сварки давлением, при котором кромки деталей нагреваются током высокой частоты (2,5…450 кГц) до температуры оплавления. В основе эффекта нагрева при высокочастотной сварке металлов лежит закон электромагнитной индукции. В массе материала, имеющего электронную проводимость (металл, графит), в переменном магнитном поле наводится ЭДС, изменяющаяся с той же частотой, что и внешнее магнитное поле. В результате появляются индукционные токи (вихревые токи, или токи Фуко), которые и вызывают его нагрев.
Идея высокочастотного нагрева металла в технологических целях, в частности при сварке, по существу сводится к задаче концентрации магнитного поля в малом объеме материала и, как следствие, к повышению плотности индуцируемых токов в месте желаемого нагрева.
Нагрев свариваемых поверхностей при высокочастотной сварке обеспечивается за счет использования основных эффектов, связанных с прохождением тока высокой частоты по металлическим проводникам - поверхностного эффекта и эффекта близости. Кроме того, при использовании тока высокой частоты возможна бесконтактная передача энергии в зону сварки даже сравнительно тонкостенных деталей в результате наведения в свариваемых кромках вихревых токов при помощи индукторов.
Достоинства высокочастотного нагрева легли в основу нескольких разновидностей процессов сварки и пайки, применяемых в промышленности.
При высокочастотной сварке металлов процесс может вестись как плавлением соединяемых кромок с образованием сварочной ванны, так и давлением, в результате применения которого возникают пластические деформации.
Относительная сложность и энергоемкость оборудования для высокочастотной сварки делают ее наиболее приемлемой для сварки в условиях непрерывного производства (сварка продольных швов труб, замкнутых профилей и изделий аналогичной формы, биметаллических лент), где необходимо обеспечить большую скорость сварки (10…120 м/мин). Сварочное оборудование обычно представляет собой лимитирующее звено в общей достаточно сложной и дорогой цепи технологического оборудования.
Нагрев токами высокой частоты применяют и для сварки пластмасс. Частота используемого в этом случае тока значительно выше — до 40 МГц, причем сваривать можно лишь пластмассы с относительно большим тангенсом угла диэлектрических потерь (tg δ ) —полиметил-метакрилат,поливинилхлорид и т. д.
studfiles.net
прессовая сварка - это... Что такое прессовая сварка?
Большой англо-русский и русско-английский словарь. 2001.
- прессовая посадка
- прессовая ткань
Смотреть что такое "прессовая сварка" в других словарях:
ПРЕССОВАЯ СВАРКА — сварка давлением, при к рой для нагрева соединяемых частей и рабочих инструментов штампов используется теплота, выделяющаяся при прохождении электрич. тока через проволочные сопротивления. Применяется преимущественно для алюм. сплавов, реже для… … Большой энциклопедический политехнический словарь
Сварка — Сварщик за работой Сварка это технологический процесс получения неразъёмного соединения посредством установления межатомных и межмолекулярных связей между свариваемыми частями изделия при их нагреве (местном или общем), и/или … Википедия
СВАРКА В ТВЕРДОМ СОСТОЯНИИ — [solid phase welding] получение неразъемного соединения за счет образования химических (металлических) связей при совместной пластической деформации в контактной зоне соединяемых материалов. Способы сварки в твердом состоянии (термокомпрессионная … Металлургический словарь
прессовый — ая, ое. 1. Отн. к прессу, связанный с работой пресса. Прессовый цех. Прессовый поршень. Прессовое оборудование. БАС 1. Прессовые железные доски, прессовые железы, клещи, которыми кладут горячие прессовые железы между половинок.. пяльцы деревянные … Исторический словарь галлицизмов русского языка
Технология авиастроения — область технологии машиностроения, включающая процессы, методы, способы и технические средства изготовления изделий авиационной техники. В начальный период развития авиационной техники Т. а. располагала ограниченными средствами, которые… … Энциклопедия техники
Казанское авиационное производственное объединение имени С. П. Горбунова — Казанское авиационное производственное объединение имени С. П. Горбунова … Википедия
Пресс-ножницы комбинированные — – кузнечно прессовая машина, сочетающая в себе комбинированные ножницы и пресс для пробивки отверстий. [Толковый словарь Ефремовой. Т. Ф. Ефремова. 2000.] Рубрика термина: Арматурное оборудование Рубрики энциклопедии: Абразивное… … Энциклопедия терминов, определений и пояснений строительных материалов
технология авиастроения — технология авиастроения область технологии машиностроения, включающая процессы, методы, способы и технические средства изготовления изделий авиационной техники.В начальный период развития авиационной техники Т. а. располагала ограниченными … Энциклопедия «Авиация»
технология авиастроения — технология авиастроения область технологии машиностроения, включающая процессы, методы, способы и технические средства изготовления изделий авиационной техники.В начальный период развития авиационной техники Т. а. располагала ограниченными … Энциклопедия «Авиация»
dic.academic.ru
Способ прессовой сварки
Изобретение может быть использовано при сооружении трубопроводов с применением труб малого и среднего диаметра, для сварки деталей со сплошным и развитым сечением, а также для соединения деталей в тавр. Нагрев торцов свариваемых деталей осуществляют дугой, управляемой магнитным полем. В процессе формирования сварного соединения осадку выполняют путем проведения многократных встречных движений одной детали относительно другой детали. Закрытие дугового промежутка и формирования сварного соединения на толщину слоя расплавленного металла достигается заданным количеством встречных движений со скоростью не ниже 20 мм/с. Способ обеспечивает повышение качества сварных соединений, полученных прессовой сваркой за счет высокой стабильности процесса на начальной стадии сварки и равномерного нагрева кромок свариваемых деталей по всей площади сечения.
Предлагаемый способ является одним из способов прессовой сварки, при котором источником нагрева свариваемых деталей является сварочная дуга, управляемая магнитным полем, и может быть использован в таких отраслях народного хозяйства, как автомобилестроение, строительство водонагревательных котлов, промышленное и гражданское строительство, при сооружении трубопроводов с применением труб малого и среднего диаметра, для сварки деталей со сплошным и развитым сечением, а также для соединения деталей в тавр.
Известен способ сварки дугой, управляемой магнитным полем, при котором для повышения качества полученных сварных соединений, используют сигналы звуковой частоты, генерируемые при перемещенных сварочной дуги по торцам свариваемых деталей. В процессе движения дуги характер, частота и сила звука изменяются, сигнал расходимости полученных характеристик звука с заранее известными и заданными используется как критерий регулирования силой сварочного тока, напряжением дуги и величиной промежутка между свариваемыми деталями (ГДР, "Schweistechnik," №6, 1980 г.).
Недостатком этого способа является сложность реализации системы управления, низкая вероятность повтора системы с учетом акустических свойств помещения, где функционирует система управления и свойств измерительной аппаратуры, которая используется.
Также известен способ управления процессом сварки дугой, управляемой магнитным полем с подсчетом энергии, которая использована на нагрев деталей (ZIS - Mitteilungen №10, 1982 г. Стр. 1051-1055). Способ управления качеством осуществляют в следующем алгоритме.
Обработанные и преобразованные сигналы сварочного тока и напряжения в процессе нагрева деталей поступают в вычислительное устройство, где они накапливаются, и рассчитывается электрическая мощность, выделяемая на кромках свариваемых деталей. Дискретность поступления преобразованных сигналов составляет 0,1 сек.
В процессе нагрева выполняют приведение электрической мощности, которая выделяется на кромках деталей, к тепловой энергии нагревания. Накопленный эквивалент энергии анализируется в ЭВМ и по мере достижения предварительно рассчитанного значения, служит параметром управления процессом нагрева. Система управления анализирует соответствие накопленной энергии эталонному значению. При отклонении накопленного значения от эталонного более чем на 10%, выполняется отбраковка полученного с нарушениями технологии соединения.
Недостатком этого способа является то, что в процессе нагрева сварочный ток и напряжение дуги не являются постоянными, их значение в значительной степени зависят от положения дуги относительно сечения свариваемых деталей. Опытным путем установлено, что напряжение дуги изменяется в течение всего цикла сварки. Это изменение напряжения в течение цикла сварки имеет характерную зависимость.
В ходе лабораторных исследований установлено, что на начальном этапе перемещения дуги по кромкам деталей (это касается деталей с трубчатым сечением) дуга перемещается с внешней на внутреннюю кромку. При этом отклонение напряжения дуги может достигать 20% от значения, устанавливаемого в момент начала стабильного движения дуги по торцам изделий. Также установлено, что качество полученных соединений в значительной степени зависит от положения дуги в процессе нагрева относительно кромки сечения свариваемых деталей. Таким образом, при одном и том же значении затраченной энергии на достижение пластического состояния деталей качество полученных соединений может иметь значительные разногласия с прогнозируемыми значениями.
Прототипом заявленного изобретения принят способ прессовой сварки, при котором нагревают свариваемые детали, при этом определяют момент достижения деталями необходимой температуры нагрева на торцах деталей и выполняют осадку путем проведения многократных встречных движений соединяемых деталей, встречные движения повторяют через промежутки времени, в течение каждого из которых получается заданная скорость сближения деталей, после чего она снижается до нуля и выполняется повторное сближение, а частота поступательных движений за весь период осадки поддерживается на уровне не ниже 10 Гц (Патент на изобретение №100278 «Способ прессовой сварки», Кучук-Яценко С.И., Качинский B.C., Коваль М.П., 10.12.2012).
Способ сварки, который выбран в качестве прототипа, осуществлялся следующим образом. Опытным путем определяют необходимую продолжительность нагрева деталей, после его прохождения, увеличивают сварочный ток (форсирование) и включают устройство, выполняющее осадку (деформация деталей).
Недостатком данного способа сварки является невозможность получения устойчивого формирования сварного соединения, которая становится причиной значительных отклонений качественных параметров полученных соединений, которые определяются путем проведения механических испытаний.
Кроме того, на характер формирования сварного соединения, а соответственно и на механические свойства, значительно влияет продолжительность фазы формирования соединения после нагрева.
В основу изобретения положена задача повышения качества сварных соединений.
Суть изобретения в том, что после выполнения нагрева деталей выполняют осадку путем проведения многоразовых встречных движений деталей, которые свариваются, встречные движения повторяют через промежутки времени, в течении которого достигается заданная скорость сближения деталей, а частота поступательных движений за весь период осадки поддерживается на уровне не ниже 10 Гц, согласно изобретению осадку выполняют путем проведения многоразовых встречных движений одной детали относительно другой детали, которые свариваются, при этом закрытие дугового зазора и формирование сварного соединения на толщину слоя расплавленного металла достигается заданным количеством встречных движений со скоростью не ниже 20 мм/с. Данная скорость перемещения обусловлена необходимостью предотвращения образования термических дефектов материала шва.
Способ осуществлялся следующим образом. Вначале детали устанавливают в устройствах удержания деталей сварочной машины вплотную (без зазора). С началом сварочного цикла детали автоматически разводятся на промежуток, при котором падение напряжения на сварочной дуге будет равно заранее установленному.
После возбуждения сварочная дуга начинает перемещаться по кромкам свариваемых деталей под воздействием магнитодвижущей силы, созданной магнитной системой сварочной машины.
В момент, который определяется программно, выполняется форсирование сварочного тока. После конца форсирования включается устройство осадки, которое выполняет программно заданное количество встречных движений свариваемых деталей со скоростью не ниже 20 мм/с.
Испытания сваренных деталей происходило в соответствии с существующими нормами и правилами.
Анализ сварных соединений, выполненных с применением прототипа и предлагаемого способа показал, что качество соединений, выполненных предложенным способом, выше в сравнении с прототипом.
Предложенный способ обладает следующими по сравнению с прототипом преимуществами:
1. Высокая стабильность процесса нагрева на начальной стадии.
2. Стабильно равномерный нагрев кромок изделий по всей площади сечения.
3. Стабильное перемещение дуги.
4. Низкие требования к подготовке торцов свариваемых деталей (на перетекание процесса мало влияют наличие ржавчины, масел, грязи и неровности сечения).
Способ прессовой сварки, включающий нагрев свариваемых деталей дугой, управляемой магнитным полем, при этом определяют момент достижения деталями необходимой температуры нагрева на их торцах и выполняют осадку путем проведения многоразовых встречных движений свариваемых деталей, причем встречные движения повторяют через промежутки времени, в течении которого достигается заданная скорость сближения деталей, а частоту поступательных движений за весь период осадки поддерживают на уровне не ниже 10 Гц, отличающийся тем, что осадку выполняют путем проведения многоразовых встречных движений деталей с амплитудой, соответствующей дуговому зазору, при этом закрытие дугового зазора и формирование сварного соединения на толщину слоя расплавленного металла достигают заданным количеством встречных движений со скоростью не ниже 20 мм/с.
www.findpatent.ru