Особенности сварки легированных сталей и сплавов. Сварка легированных сталей
Сварка легированных сталей — технология и особенности
Июнь 22, 2017
При соединении заготовок с определёнными параметрами главной задачей является сохранение структуры и свойств материала в зоне сварного шва. При нарушении температурного режима могут возникнуть кристаллизационные трещины и поры, что приводит к потере качества соединения. Чтобы избежать негативных последствий, сварку легированных сталей производят определёнными электродами с соблюдением температурного цикла, который позволяет избежать потери качества. Мы расскажем о технологических приёмах и особенностях при работе с этими материалами.
Типы сталей с добавками и их свойства
С помощью легирующих добавок сплаву придают определённые качества такие, как жаростойкость, низкая степень коррозии, стойкость к ударным нагрузкам и к воздействию агрессивных сред. В этих сплавах имеются различные химические элементы и их процентное содержание и определяет качество металла. В них присутствуют хром, никель, вольфрам, ванадий, марганец, ниобий и титан, а также их сочетания, определяющие степень характерных физических качеств. В итоге содержание примесей в определённых процентных долях и определяет свариваемость легированной стали определённой марки.
- низколегированные марки, в которых присутствие примесей не превышает 2,5%, при этом содержание углерода в металле не учитывается;
- металл среднелегированного состава, где добавочные элементы занимают от 2,5% до 10% состава металла;
- высоколегированная сталь, с содержанием более, чем 10% специальных элементов.
При сварке этого вида металлов крайне важно максимально точно знать марку стали, чтобы получить высококачественный, прочный и долговечный шов без нарушения структуры материала заготовок.
Зависимость свариваемости деталей, которые легированы низким и средним количеством химических добавок, от содержания углерода, кремния и марганца подразумевает использование электродов определённого вида. Также необходима зачистка стыков от загрязнений и следов коррозии, обязательным является цикл прокаливания электродов до 400о С, и нагрев заготовок до 200о С. Сплав с высоким легированием должен соединяться с низкой величиной сварочных токов, во избежание перегрева исходных материалов.
Технологические особенности сварки специфических сталей
Соединение специальных металлов требует особого подхода, который позволит избежать перегрева заготовок в зоне шва и потери качеств соединения путём вывода из него необходимых компонентов. Здесь необходимо использование электродов или сварочной проволоки с особыми свойствами и химическим составом. Кроме того, существуют такие технические решения, как плазменная сварка, которая обеспечивает прочность только в зоне шва, без перегрева близлежащей толщи металла. Таким образом, качественная сварка легированных сталей может осуществляться разнообразными способами.
- применение новых технических подходов таких, как использование плазменного метода работ;
- использование низкой плотности сварочного тока с применением инверторных методов в среде защитных или активных газов;
- соединение металлов под флюсом, который подбирается с учётом свойств заготовок;
- подбор специальных покрытых электродов близких по составу к свариваемому составу и выбор режима работ и локального прокаливания деталей, исключающих перегрев сплава с потерей его качеств.
Важно отметить, что каждый из этих подходов требует изучения справочной литературы и научного подхода к проблеме соединения сплавов с различными физико-химическими параметрами.
Способы сварки легированных составов зависят от марки и подразумевают использование дозированных сварочных токов, температурных режимов подготовки заготовок, а также химического состава покрытых электродов или сварочной проволоки. Эти решения подробно описаны в руководстве по соединению подобных деталей в соответствии с их свойствами.
Итог
Технология сварки легированных сталей не является особенно сложной, если соблюдать соответствие состава заготовок и сварочного режима. Эти методики описаны в ГОСТах и руководствах достаточно подробно, поэтому следуя им можно получить качественное и долговечное соединение этого вида материалов.
electrod.biz
Сварка легированных сталей - Cварочные работы
Сварка легированных сталей
К низколегированной относится сталь, легированная одним или несколькими элементами, если содержание каждого из них не превышает 2%, а суммарное содержание легирующих добавок не более 5%. Низколегированные стали делятся на низкоуглеродистые конструкционные, теплоустойчивые и среднеуглеродистые стали.
Низколегированная низкоуглеродистая конструкционная сталь по реакции на термический цикл сварки мало отличается от обычной низкоуглеродистой стали. Различие в основном состоит в несколько большей склонности к образованию закалочных структур в металле шва и околошовной зоны при повышенных скоростях охлаждения. Дополнительное легирование стали марганцем, кремнием и другими элементами способствует образованию в сварных соединениях закалочных структур. Поэтому режим сварки большинства этих сталей ограничивается более узкими пределами погонной энергии, чем при сварке пизкоуглеродистой стали. Обеспечение равнопрочности металла шва с основным металлом достигается главным образом за счет легирования его элементами, переходящими из основного металла. Иногда для повышения стойкости против хрупкого разрушения металл шва дополнительно легируют через сварочную проволоку. Стойкость металла против кристаллизационных трещин несколько ниже, чем у низкоуглеродистых сталей. Повышения стойкости достигают путем снижения содержания в металле шва углерода, серы и некоторых других элементов за счет применения сварочной проволоки с пониженным содержанием указанных элементов, а также выбора соответствующей технологии и рациональной конструкции. Технология сварки низколегированных низкоуглеродистых конструкционных сталей покрытыми электродами мало отличается от технологии сварки низкоуглеродистых сталей. Сварку ведут в основном электродами с фтористо-кальциевым покрытием типа Э42А и Э50А, которые обеспечивают более высокую стойкость против образования кристаллизационных трещин и повышенные пластические свойства по сравнению с электродами других типов. При газовой сварке низколегированной стали используют нормальное пламя, мощность которого выбирают из расчета 75—100 дм3/ч ацетилена при левом способе и 100—130 дм3/ч при правом способе на 1 мм толщины металла. Для повышения механических свойств металла шва его проковывают при 800—850 °С с последующей нормализацией.
При изготовлении изделий из низколегированных теплоустойчивых сталей наибольшее распространение находит ручная сварка покрытыми электродами и полуавтоматическая сварка в защитных газах. Работа конструкций при высоких температурах способствует протеканию диффузионных процессов. Поэтому для снижения интенсивности протекания этих процессов в сварном соединении стремятся максимально приблизить составы металла шва и основного. Для сварки хромомолиб-деновых сталей применяют электроды типа ЭМХ. Стали с малым содержанием углерода рекомендуется сваривать с предварительным подогревом до 200 °С, при большем содержании подогрев производят при 250 —300 °С. Хромомолибденованадиевые стали сваривают электродами типа ЭХМФ с предварительным и сопутствующим подогревом до 300—350 °С и последующим высоким отпуском при 700—740 °С в течение 2 —3 ч. При сварке листовой молибденовой стали малых толщин предварительный подогрев не выполняют, а при толщинах более 6 мм требуется предварительный подогрев, температуру которого увеличивают с увеличением толщины металла. Многослойную сварку ведут способом «каскад». При сварке трубопроводов с толщиной стенки более 6 мм и содержанием углерода в металле более 0,18 % следует применять предварительный подогрев, обеспечивающий во время сварки температуру металла шва в околошовной зоне не ниже 200 °С. Стык должен завариваться без перегрева. В случае возникновения перегрева необходимо обеспечить медленное остывание и нагрев перед возобновлением сварки до 200 °С. Газовую сварку низколегированных теплоустойчивых сталей выполняют нормальным ацетилено-кислородным пламенем (расход ацетилена 100 дм3/ч на 1 мм толщины металла левым и правым способами). Металл сварочной ванны необходимо поддерживать в густом состоянии, чтобы предотвратить выгорание хрома и молибдена. Рекомендуется предварительный подогрев до 250—300 °С. Применяется одно- и многослойная сварка с наименьшим числом перерывов. После окончания сварки пламя горелки медленно отводят вверх, что способствует более полному выделению газов из расплавленного металла. Хромомо-либденовые и молибденовые стали подвергают термической обработке.
К среднелегированным относятся стали, легированные одним или несколькими элементами при суммарном их содержании 2,5—10 %. Главной и общей характеристикой этих сталей являются механические свойства. Так, временное сопротивление их составляет 588—1960 МПа, что значительно превышает аналогичный показатель обычных углеродистых конструкционных сталей. При высоких прочностных свойствах среднелегирован-ные стали после соответствующей термообработки по пластичности и вязкости не только не уступают, но в ряде случаев и превосходят малоуглеродистую сталь. При этом среднелегированные стали обладают высокой стойкостью против перехода в хрупкое состояние. Поэтому их применяют для работы в условиях ударных и знакопеременных нагрузок, низких и высоких температур, в агрессивных средах. Получение сварных соединений необходимого качества, учитывая особые физико-химические свойства среднелегированных сталей, встречает ряд специфических трудностей. Прежде всего, главным образом при сварке сталей с повышенным содержанием углерода и легирующих элементов, является предупреждение появления холодных трещин в металле сварного соединения. Второй трудностью является предупреждение возникновения кристаллизационных трещин в металле шва. Борются с этим теми же методами, что и при сварке углеродистых сталей. Возникает также трудность в получении металла сварного соединения с равноценными или близкими механическими свойствами к основному металлу. В ряде случаев возникают серьезные затруднения в обеспечении необходимых прочностных и пластических свойств металла околошовной зоны и зоны сплавления. Для предупреждения образования холодных трещин в сварных соединениях из среднелегированных сталей следует применять стали, обладающие требуемыми механическими свойствами при возможно низком содержании углерода и легирующих элементов; регулировать сварочный термический цикл путем изменения режима сварки. Если стойкость сварного соединения против появления холодных трещин очень низкая и избежать их образования путем подбора режима сварки не удается, в отдельных случаях прибегают к регулированию термического цикла путем предварительного и сопутствующего подогрева свариваемых кромок. Стойкость сварных соединений из среднелегированных сталей против возникновения холодных трещин можно также изменять, регулируя нарастание временных сварочных напряжений при охлаждении применением сварочных проволок с возможно более низкой температурой плавления, уменьшением содержания водорода в основном металле и металле шва, термообработкой сварных соединений сразу же после окончания сварки, предварительной наплавкой кромок, а также проковкой сварных соединений и обработкой ультразвуком сразу после окончания сварки, понижением температуры сварных соединений ниже 0 °С сразу после их остывания до комнатной температуры, предупреждением увлажнения сварных соединений после окончания сварки.
Большинство конструкций из среднелегированных сталей сваривают вручную низководородистыми электродами с фтористо-кальциевым покрытием на постоянном токе обратной полярности. Швы большого сечения выполняют каскадным и блочным способами. При этом обеспечивается разогрев области шва, особенно при сварке сталей большой толщины, свыше 150 °С. Для создания такого разогрева используют каскадный способ сварки при небольшой (менее 200 мм) длине его ступени. Режимы сварки выбирают в зависимости от типа стержня — при ферритном стержне они не отличаются от режимов сварки низкоуглеродистых сталей, при аустенитном — от режимов сварки аустенитных сталей.
Высоколегированные стали и сплавы составляют значительную группу конструкционных материалов. К числу основных трудностей, которые возникают при сварке указанных материалов, относится обеспечение стойкости металла шва и околошовной зоны против образования трещин, коррозионной стойкости сварных соединений, получение и сохранение в процессе эксплуатации требуемых свойств сварного соединения, получение плотных швов. При сварке высоколегированных сталей могут возникать горячие и холодные трещины в шве и околошовной зоне. С кристаллизационными трещинами борются путем создания в металле шва двухфазной структуры, ограничения в нем содержания вредных примесей и легирования вольфрамом, молибденом и марганцем, применения фтористо-кальциевых электродных покрытий и фторидных сварочных флюсов, использования различных технологических приемов. Присутствие бора может привести к образованию холодных трещин в швах и околошовной зоне. Предотвращение их появления достигается предварительным и сопутствующим подогревом сварного соединения свыше 250 — 300 °С. С помощью технологических приемов можно также предотвратить кристаллизационные трещины. В ряде случаев это достигается увеличением коэффициента формы шва, увеличением зазора до 1,5 — 2 мм при сварке тавровых соединений. Предварительный и сопутствующий подогрев не оказывает заметного влияния на стойкость против образования кристаллизационных трещин. Большое влияние оказывает режим сварки. Применение электродной проволоки диаметром 1,2 — 2 мм на умеренных режимах при минимально возможных значениях погонной энергии создает условия для предотвращения появления трещин. Предпочтение следует отдавать сварочным материалам повышенной чистоты. При сварке аустенитных сталей проплавление основного металла должно быть минимальным. Горячие трещины образуются при сварке стали с повышенным содержанием серы, фосфора, кремния, марганца в сочетании с медью, ниобием и легкоплавкими примесями. С околошовными горячими трещинами борются созданием в околошовной зоне двухфазной структуры, уменьшением содержания в стали серы и фосфора, применением чистых сварочных материалов и мелкозернистых сталей и сплавов.
Технология сварки высоколегированных сталей за некоторыми исключениями не отличается от технологии сварки углеродистых конструктивных сталей. Из-за пониженной теплопроводности и высокого коэффициента линейного расширения во избежание коробления необходимо выбирать режимы сварки, обеспечивающие минимальную концентрацию нагрева. Сварку аустенитных сталей выполняют укороченными электродами для снижения коэффициента наплавки. Для получения заданной глубины провара силу тока снижают на 10—15 % по сравнению со сваркой углеродистой стали. Для уменьшения угара легирующих элементов сварку ведут короткой дугой без колебаний конца электрода. При сварке коррозионностойких сталей не допускается возбуждение дуги на основном металле, попадание брызг металла на основной металл. Складки на поверхности шва, углубления между чешуйками, щели или непрова-ры в корне шва при воздействии агрессивной среды могут явиться очагами коррозии. Лучшей коррозионной стойкостью обладают гладкие швы с плавным переходом к основному металлу. Поэтому очистка швов пневматическим зубилом или другими способами, при которых образуются вмятины и забоины, не рекомендуется.
При изготовлении конструкций из высоколегированных сталей применяют все виды сварки плавлением. Ручную сварку покрытыми электродами выполняют за некоторым исключением, как сварку обычных конструкционных сталей. Сварку производят на постоянном токе обратной полярности в основном электродами с фтористо-кальциевым покрытием короткой дугой без поперечных колебаний конца электрода. Сварку выполняют электродами меньшей длины по сравнению с обычными и на небольших токах. Перед сваркой электроды прокаливают при 250—400 °С в течение 1 —1,5 ч. Силу тока для аустенитных электродов берут из расчета 25—30 А на 1 мм диаметра электрода. При сварке в вертикальном или потолочном положении силу тока уменьшают на 10—30 % по сравнению со сваркой в нижнем положении. Сварка в аргоне или гелии характеризуется стабильностью дуги, высоким качеством сварных швов, которое обеспечивается хорошей защитой зоны сварки от воздуха. Сварку вольфрамовым электродом ведут на постоянном токе прямой полярности. При сварке сталей с высоким содержанием алюминия рекомендуется переменный ток, способствующий разрушению оксидной пленки. Конец присадочной проволоки должен все время находиться в струе защитного газа. Как правило, аустенитные стали сваривают плазменной сваркой.
При газовой сварке хромистых сталей применяют нормальное пламя. Сварку ведут пламенем пониженной мощности из расчета 70 дм3/ч ацетилена на 1 мм толщины свариваемого металла. Для предохранения выгорания хрома и для удаления из сварочной вапны его окислов применяют специальные флюсы. Стали толщиной до 3 мм сваривают левым способом, толщиной более 3 мм — правым способом. С целью уменьшения коробления выполняют предварительный подогрев до [50 — 250 °С. Сварку ведут в один слой с максимально допустимой скоростью, без перерывов и повторного нагрева одного и того же места. Хромоникелевые аусте-нитные стали толщиной до 3 мм сваривают газовой сваркой. Сварку осуществляют строго нормальным пламенем с максимальной скоростью. Сварку ведут левым и правым способами, длинные швы — обратноступенчатым способом. Для удаления окислов применяют флюс НЖ-8, а для улучшения механических свойств, предупреждения межкристаллитной коррозии и деформаций — термическую обработку с нагревом до 1050— 1100 °С с последующим охлаждением в воде.
Одним из путей экономии дорогостоящих высоколегированных сталей является применение комбинированных конструкций, изготовленных из нескольких сталей. Сварка высоколегированных сталей со средне- или низколегированными и обычными углеродистыми сталями явилась настолько трудной задачей, что составила целую проблему, известную как проблема сварки разнородных сталей. При сварке разнородных сталей в шве часто появляются трещины, в зоне сплавления может происходить изменение структуры с образованием прослоек, существенно отличающихся от структуры свариваемых металлов. Сварка разнородных сталей затруднена еще тем, что в подавляющем большинстве случаев они отличаются друг от друга коэффициентом линейного расширения. Основным путем решения вопроса сварки разнородных сталей является использование сварочных материалов, способствующих получению аусте-нитного металла шва с высоким содержанием никеля, который обеспечивает стабильную зону сплавления. Содержание никеля в металле шва зависит от температуры его эксплуатации. Для экономии никеля сварные соединения разнородных сталей делят на четыре группы: I — работающие при температурах до 350°С, II — 350 —450 °С, III —450 — 550 °С и IV — выше 550 °С. Ручную сварку разнородных сталей первой группы можно производить существующими электродами. Не следует пользоваться электродами типа ЭА-1. Для соединений II—IV групп рекомендуются электроды АНЖР-1, АНЖР-2 и АНЖР-3. В остальном технология сварки разнородных сталей такая же, как и сварки других сталей.
—
В зависимости от химического состава конструкционных легированных сталей процесс сварки происходит по-разному. Сварка этих сталей имеет ряд особенностей, так как происходит частичное выгорание легирующих компонентов, поэтому металл шва по своим свойствам отличается от основного металла. Легированные стали по сравнению с низкоуглеродистыми хуже проводят тепло, склонны к перегреву свариваемого металла и появлению больших деформаций.
Для предупреждения перегрева металла и появления больших деформаций легированные стали сваривают горелками меньшей мощности. Для уменьшения выгорания легирующих компонентов пламя горелки должно быть нормальным или с небольшим избытком ацетилена. Отдельные конструкционные легированные стали способны к закалке на воздухе. Для предотвращения этого необходимо перед сваркой подогреть подготовленное изделие. Некоторые легированные стали после сварки подвергают термической обработке.
Низколегированные хромокремненикелемедистые стали для строительных конструкций марок 15ХСНД и ЮХСНД хорошо свариваются газовой сваркой в связи с небольшим содержанием углерода и легирующих примесей. Мощность наконечника выбирают из расчета 90—120 л/ч ацетилена при левой и 120—150 л/ч ацетилена при правой сварке на 1 мм толщины свариваемого металла. Пламя должно быть нормальным. При сварке применяют сварочную проволоку Св08, СвОЗА или Св10Г2. Для получения более плотного сварного шва Делают проковку шва при светло-красном калении (800—850 °С). Для снятия напряжений, полученных в результате проковки сварного шва, его подвергают нормализации с нагревом в печи или горелками с последующим медленным охлаждением на воздухе.
Низколегированные молибденовые и хромомолибде-новые теплоустойчивые стали применяют для изготовления труб в котлах высокого давления. Пламя горелки должно быть нормальным, мощностью 100—130 л/ч ацетилена на 1 мм толщины свариваемого металла.
Для сварки применяют проволоку марок Св08ХНМ, СвЮНМ, Св18ХМА, СвЮХМ, СвЮМХ. Сварку производят небольшими участками длиной 15—20 мм. При сварке металла толщиной 16 мм изделие подогревают до температуры 250—360 °С, поддерживая ее до окончания сварки. Заданную температуру в процессе сварки поддерживают вспомогательными, многоплеменными горелками или специальными электроподогревателями. Стали 15М и 20М толщиной 10 мм при температуре минус 103 С можно сваривать без предварительного подогрева, стали большей толщины подогревают до 250— 300 °С. Хромомолибденовые стали 12ХМ, 15ХМ, 12Х1МФ при температуре минус 10 °С сваривают с подогревом до 250—300 °С независимо от толщины металла.
Перед сваркой кромки зачищают до металлического блеска. Детали с толщиной стенки 5 мм сваривают за один проход, детали или узлы с толщиной стенки более 5 мм сваривают в несколько проходов.
Для получения качественного сварного соединения этих сталей первый шов образуется за счет взаимного оплавления кромок, т.е. без присадочного металла участками не более 15—25 мм во избежание появления микротрещин. Чтобы предотвратить выгорание хрома и молибдена, металл сварочной ванны поддерживают в более густом состоянии, не перегревая его.
Перед возобновлением сварки после перерыва подогревают место сварки, а при сварке кольцевых швов — весь шов, до температуры 250—300 °С. При завершении сварки следят за тем, чтобы переход от усиления шва к основному металлу был плавным по всей длине шва.
Детали и узел котлов с толщиной стенки свыше 10 мм подвергают термообработке при температуре 900—930 °С для молибденовой и 930—950 °С для хромо-молибденовой стали с выдержкой при этой температуре I —1,5 мин на 1 мм толщины свариваемого металла с последующим охлаждением на спокойном воздухе. После монтажа и сварки паропроводных труб их необходимо подвергнуть термической обработке газовыми го* релками или специальными электронагревателями.
Местную термообработку труб на монтаже из молибденовых и хромомолибденовых труб производят при температуре 680—700° С; хромомолибденованадиевые стали подвергают термообработке при температуре 720—740° С с выдержкой 4—5 мин на 1 мм толщины свариваемого металла. Сварной стык подвергают термической обработке на ширину 100 мм в обе стороны от шва. Хорошее качество сварного соединения из хро-момолибденовой стали получается при сварке присадочной проволокой СвГ8ХМА.
К низколегированным хромокремнемарганцовистым сталям (хромансиль) относятся следующие наиболее часто используемые марки: 20ХГС, 25ХГС, ЗОХГС, 30ХГСА, 35ХГС, с содержанием 0,17—0,4% углерода, 0,9—1,2% кремния, 0,8—1,1% марганца, 0,8—1,1% хрома. Эти стали сваривают нормальным пламенем. Мощность наконечника выбирают из расчета 75—100 л ацетилена в час на 1 мм толщины свариваемого металла. При сварке окислительным пламенем более интенсивно выгорают такие легирующие компоненты, как хром, кремний, марганец, с образованием в сварном шве окислов, шлаков и частично непровара.
В качестве присадочного материала используют сварочную низкоуглеродистую проволоку Св08 и Св08А, а в том случае, когда к сварному соединению предъявляют повышенные требования, применяют сварочную проволоку Св18ХГСА или Св18ХМА. Кромки свариваемых деталей должны быть хорошо подогнаны под сварку и очищены до металлического блеска от всевозможных загрязнений; зазор по всей длине (периметру) шва должен быть одинаковым.
Прихватку листов под сварку производят через 20— 30 мм при толщине металла до 1,5 мм, а при большей толщине — через 40—60 мм. Прихватки от края листа располагают на расстоянии 10—15 мм. Сварку производят в один слой от середины шва к его краям. С целью уменьшения выгорания легирующих компонентов сварку производят быстро без задержки пламени на одном месте и без перерывов. Хромокремнемарганцови-стые стали при резком охлаждении легко закаливаются с образованием трещин в шве и околошовной зоне.
Поэтому горелку отводят медленно вверх, одновременно прогревая факелом пламени металл конечного участка радиусом 20—40 мм.
В зависимости от назначения сварной детали или узла его подвергают термической обработке (закалке с последующим отпуском). Закалку производят при температуре 500—650 °С с выдержкой при этой температуре 5 мин, затем изделие нагревают до 880 °С с той же выдержкой с последующим охлаждением в массе. Отпуск производят путем нагрева до температуры 400— 600 °С с охлаждением в горячей воде.
Хромистые стали. При монтаже специального оборудования применяют кислотостойкие и стойкие (при высоких температурах) хромистые стали с содержанием хрома до 30% и углерода — от 0,13 до 0,9%. Хромистые стали склонны к закалке на воздухе, в результате чего после сварки могут образовываться трещины. Чем больше в стали углерода, тем хуже она сваривается и тем чаще образуются трещины. Чтобы уменьшить опасность трещинообразования, сталь перед сваркой подогревают до температуры 150—200 °С. Обязателен подогрев хромистых сталей с содержанием хрома более 14%. Данные стали склонны к большому короблению в результате малой теплопроводности и большого коэффициента линейного расширения.
Сварку хромистых сталей ведут нормальным пламенем, наконечником мощностью 70 л ацетилена в час на 1 мм толщины свариваемого металла. Избыток кислорода приводит к окислению хрома, а избыток ацетилена— к образованию так называемых карбидов хрома.
При таком положении металл шва и околошовной зоны перестает быть стойким против кислот. При сварке применяют присадочную проволоку из хромоникеле-вой стали Св02Х19Н9 или Св06Х19Н9Т (с титаном), позволяющую получать лучшее качество сварного соединения. Титан и ниобий препятствуют образованию в сварном шве и околошовной зоне карбидов хрома (твердых химических соединений хрома с углеродом). Сварку производят быстро, избегая перерывов и повторных нагревов. Сварка должна быть с одной стороны и в один слой. Предупредить выгорание хрома можно путем нанесения флюса на проволоку и свариваемые кромки, при этом флюс должен покрывать как лицевую, так и обратную сторону шва.
После сварки детали подвергают термической обработке по режиму, соответствующему данной марке стали.
Кислотостойкие стали с высоким содержанием хрома при длительном нагреве склонны к росту зерна в зоне нагрева со снижением прочности сварного соединения. Поэтому эти стали газовой сваркой не сваривают.
Хромоникелевые аустенитные стали — стали, сохраняющие структуру аустенита при медленном понижении температуры от 1000° С и более до комнатной.
Основу аустенитной стали составляет железо (более 45%). Содержание легирующих элементов, важнейшими из которых являются хром и никель, не превышает 55%. Если сумма легирующих компонентов превышает 55%, вместо термина аустенитная сталь применяют термин аустенитный сплав.
Металлургическая промышленность выпускает десятки марок высоколегированных хромоникелевых сталей и никелехромовых сплавов. Наибольшее распространение при изготовлении сварных конструкций получили нержавеющие стали — стали с высоким содержанием хрома, устойчивые против коррозии в атмосфере и различных средах.
Стали и сплавы с высоким содержанием хрома (более 6—8%) делят на три основные группы:1) коррозионностойкие (нержавеющие) стали;2) жаростойкие стали и сплавы;3) жаропрочные стали и сплавы.
К группе коррозионностойких относятся стали, обладающие стойкостью против электрохимической коррозии — атмосферной, почвенной, щелочной, кислотной, солевой, морской и др.
Наиболее распространенными аустенитными корро-зиониостойкими сталями являются 0Х10Н20Т2, Х14Г14НЗТ (ЭИ711), 1Х16Н15МЗБ (ЭИ847) и др. (ГОСТ 5632—61), к аустенитным жаростойким сталям и сплавам относятся: Х20Н14С2 (ЭИ211), 0Х23Н18 и др.
К группе жаростойких относятся стали и сплавы, обладающие стойкостью против химического разрушения поверхности в газовых средах при температуре выше 550 °С и работающие в ненагруженном или слабонагру-жениом состоянии. Эти стали обладают высокой прочностью н вязкостью, хорошо сопротивляются действию высоких температур, щелочей, кислот, хорошо поддаются штамповке и вытяжке.
Применительно к нержавеющим сталям ацетилено-кислородная сварка имеет следующие серьезные недостатки. При избытке ацетилена возможно науглероживание металла шва, а в ряде случаев и околошовной зоны. В результате этого снижается коррозионная стойкость сварного соединения и появляется опасность образования горячих трещин.
Если в пламени газовой горелки содержится избыток кислорода, то появляется возможность окисления таких элементов, как титан, алюминий, хром и др. Окисление ферритообразующих элементов может, кроме того, вызвать аустенизацию сварного шва и появление горячих трещин. Поэтому ни восстановительное, ни окислительное пламя нельзя использовать при газовой сварке нержавеющих сталей. Сварку следует производить строго нейтральным пламенем. Мощность пламени горелки берут из расчета 75 л ацетилена в час на 1 мм толщины свариваемого металла.
Для сварки нержавеющих сталей применяют проволоку СвОХ18Н9, СвОХ!8Н9С2, Св1Х18Н9Т, Св1Х18НЭБ, Св1Х18Н11М и др. При сварке жаропрочной стали применяют проволоку, содержащую 21% никеля и 25% хрома. При сварке металла толщиной до 2 мм делают отбортовку, величина которой равна толщине листа. При толщине листа 3—4 мм сварку ведут без разделки, при большей толщине свариваемого металла делают разделку кромок под углом 70—80°.
Для удаления окислов хрома и улучшения внешнего вида сварного шва применяют флюс, состоящий из 80% плавикового шпата и 20% ферротитана.
Можно использовать флюс, состоящий из смеси 50% буры и 50% борной кислоты или 80% буры и 20% окиси кремния.
Флюс разводят в воде до смеганообразного состояния. Приготовленный флюс наносят на кромки за 15— 20 мин до сварки. Наносят его с лицевой и обратной стороны свариваемых кромок детали. Чтобы уменьшить коробление свариваемого изделия, применяют обратно-ступенчатый способ сварки с началом сварки на расстоянии 75—100 мм от кромки.
Сварку необходимо вести быстро, за один проход и без колебаний присадочной проволокой. Ванну расплавленного металла покрывают тонким слоем шлака, а конец присадочной проволоки погружают в ванну.
Сваривать можно и левым и правым способами. Наклон мундштука горелки и присадочной проволоки такой же, как и при сварке углеродистой стали.
Для получения заданных механических свойств и повышения коррозионной стойкости сварное соединение после сварки подвергают термической обработке (закалке) нагревом до температуры 1050—1100 °С с последующим быстрым охлаждением в воде. Закалку можно заменить отжигом при температуре 850° С с последующим охлаждением на воздухе. Сварное соединение из металла толщиной 1—2 мм можно охлаждать на воздухе. Сталь с добавлением титана подвергать термической обработке после сварки не обязательно.
После сварки шлак и остатки флюса удаляют путем промывки сварного шва и околошовной зоны в горячей воде волосяной щеткой.
Схемы сборки и сварки пластин из нержавеющей стали марки Х18Н9Т толщиной 1,5 мм (без разделки кромок) и толщиной 5 мм с V-образной разделкой кромок представлены на рис. 37 и 38.
Присадочная проволока: Св06Х19Н9Т диаметром 1 и 4 мм с флюсом состоит из смеси прокаленной буры (50%) и борной кислоты (50%) в виде пасты, разведенной водой.
Перед сваркой за 15—20 мин флюс наносят при помощи кисточки на свариваемые кромки и на присадочную проволоку.
Рис. 38. Схема сварки и сборки пластин из нержавеющей стали толщиной 5 мм
Читать далее:Сварочные флюсыСварочные электродыОбщие сведения о сварке арматурыПротивопожарные мероприятия при сваркеБезопасность труда при сварке технологических трубопроводовБезопасность труда при сварке строительных металлических и железобетонных конструкцийЗащита от поражения электрическим током при сваркеТехника безопасности и производственная санитария при сваркеУправление качеством сваркиСтатистический метод контроля
stroy-server.ru
Сварка высоколегированных сталей: особенности и технология, видео
Оглавление:
- Низколегированные стали
- Среднелегированные стали
- Высоколегированные стали
- Технология сварки высоколегированных металлов
- Особенности сварки легированных сталей
- Интересное видео
Легированными считают стали, которые содержат элементы, которые придают сплавам особенные свойства. Элементы называются легирующими. Чаще всего это никель, хром, молибден, вольфрам и т.д. процесс легирования необходим для повышения стойкости, гибкости, прочности, устойчивости к коррозии металла.
Выделяется три вида легированных сталей:
- низколегированные - содержат легирующих элементов до 2,5%;
- среднелегированные - содержат легирующих элементов до 10%;
- высоколегированные - содержат легирующих элементов более 10%.
Каждый из видов подразумевает свои особенности сварки легированных сталей. Для краткого обозначения присутствующего элемента стали называются по его названию. Например, хромистыми, вольфрамовыми, никелевыми. Компоненты отмечаются буквами - Ю - алюминий, Ф - ванадий, Р - бор, Н - никель; Г - марганец.

Для определения назначения отдельного вида стали выделяются такие группы:
- нержавеющие;
- жаростойкие;
- кислотостойкие;
- окалиностойкие.
Низколегированные стали
От низколегированных сплавов требуется пластичность, хорошая свариваемость, высокая устойчивость к деформации. Наилучшие свойства такие стали приобретают после закаливания. В некоторых видах такие свойства достигаются низким содержанием углерода. Также для улучшения свойств добавляются дополнительные присадки, например, хром, кремний.
Такие виды металла отлично свариваются, имеют низкую степень ломкости при холоде ниже сорока градусов. Основным минусом низколегированного сплава считается слабая вибрационная устойчивость.
Сварные соединения сталей хорошо сопротивляются холодным трещинам и деформационному разрушения. Для сварки низколегированных сплавов используются специальные электроды, имеющие слабоводородное фтористо-кальциевое напыление. Технология сварки легированных сталей подразумевает быструю сварку определенных участков, чтобы не допустить охлаждение шва ниже температуры предварительного нагрева.
Сварка низколегированных сталей под флюсом проводится при помощи постоянного тока, который имеет обратную полярность. При сварке металлов в углекислом газе в качестве электродов используется порошковая проволока. Таким образом достигается большая прочность и холодоустойчивость, особенно швам изделия.
Низколегированные металлы не стоит варить газом, так как это серьезно ухудшает качество изделия - при выгорании легирующих элементов соединения склоны к коррозии и механическим разрушениям.
Среднелегированные стали
Для таких сплавов характерно более чем в два раза увеличенное содержание углерода. В качестве присадок чаще всего используются Ni, Mo, Cr, V, W. Идеальные характеристики металла достигаются закалкой и низким отпуском. Такие виды сталей тщательно очищают ор различных видов неметаллических примесей. Для достижения оптимальных свойств используются переплавки, термомеханическая обработка.
Для надежности и износостойкости сварных швов необходимо получить идеальные химические показатели соединений. Сварочные материалы должны содержать меньший объем легирующих элементов, чем основной металл. С помощью правильно подобранного материала можно получить отличную прочность и другие качества шва при сварке легированных сталей.
Среднелегированные сплавы с высокой прочностью и уровнем прокаливания необходимо сваривать с помощью материалов, которые придадут соединениям максимальную возможность деформации. Для таких целей используются низколегированные электроды, не содержащие органических веществ, которые прокалили при высоких температурах. При сварке следует обеспечить оптимальные условия работы - не допускать наличия влажности, появления ржавчины в сварочной ванне, чтобы не повысить уровень водорода.
Оптимальным методом для легированных и углеродистых сталей является аргоновая сварка с неплавящимися электродами. Такой вид оптимален для механизированного проплавления, обеспечивая оптимальную глубину и равномерность процесса.
Газовая сварка легированных сталей осуществляется ацетиленокислородом, который обеспечивает высококачественный шов. Газы-заменители в данном случае применять не следует. Однако даже ацетиленокислород дает полной гарантии качественного шва. Этого можно добиться только путем использования дуговой сварки.
Высоколегированные стали
В состав высоколегированных сплавов входят Cr и Ni в повышенном содержании. Эти элементы придают металлам особенную структуру и свойства. Высоколегированные сплавы обладают большей устойчивостью к коррозии, низким и высоким температурам, более жаропрочные. В зависимости от сферы применения стали различаются на жаростойкие, жаропрочные, коррозионностойкие.
После пройденной специфической термической обработки высоколегированные сплавы становятся очень прочными и эластичными. При закалке пластичность данных металлов только повышается. На структуру сталей существенно влияет их химический состав и разновидности легирующих компонентов.
Технология сварки высоколегированных металлов

Высоколегированные сплавы имеют множество положительных характеристик, что позволяет использовать их для самых разнообразных изделий. Поэтому технология сварки высоколегированных сталей для каждого изделия могут быть отдельной. Эта особенность определяет разность в выполнении сварки для получения шва определенного типа и состава.
Особенности сварки легированных сталей
Особенности сварки легированных сталей регламентируются тепловыми особенностями сплава. Понижение тепловой проводимости может серьезно изменить температурное распределение температуры в области шва. При неправильной сварке такие показатели могут привести к деформации изделия. Для того чтобы избежать подобной проблемы сварка должна проходить с наибольшими температурами.
Ручная дуговая сварка допускает применение электродов с фтористокальциевым покрытием, таким образом возможно получение шва с оптимальным содержанием химических веществ. Для предотвращения перфорации при сварке высоколегированных сталей и сплавов в швах следует прокаливать электроды с особой тщательностью.
Газовая сварка не особенно подходит для такого типа металлов по причине нередких внутренних коррозий. Такой вид работ допустим для температуроустойчивых сплавов толщиной не более 2 мм. В швах может возникать заметная деформация.
Для более толстых пластин оптимальным вариантом является флюсовая сварка. Таким образом по всей поверхности соединения состав и характеристики металла остаются стабильными. Причиной явления является отсутствие сварных промежутков, связанных с заменой электродов, равномерностью плавки металла по поверхности шва.
Кроме того, место на котором проводятся работы надежно защищается от окисления легирующих компонентов. Что имеет особенно важное значение при сварке высоколегированных сталей.
Интересное видео
osvarka.com
Технология сварки легированных сталей | Строительный справочник | материалы - конструкции
Сварка низколегированных и среднелегированных конструкционных сталей
Свариваемость таких сталей зависит от содержания углерода и легирующих компонентов и ухудшается с ростом содержания углерда и легирующих компонентов. Стали кремнемарганцевой группы 15ГС, 18Г2С и 25Г2С сваривают электродами типа Э60А марки УОНИ-13/65. Перед сваркой кромки тщательно зачищают от грязи, ржавчины и окалины.
Сварку выполняют предельно короткой дугой. Изделие перед сваркой подогревают до температуры 200 С, электроды перед сваркой прокаливают при 400°С в течение одного часа.
Кремнемарганцемедистые стали 10Г2СД, 10ХГСНД, 15ХСНД и 12ХГ сваривают электродами типа Э50А марки УОНИ-13/55. Изделие перед сваркой не подогревают.Сварка низколегированных и среднелегированных конструкционных сталей
Особенности сварки высоколегированных сталей
К высоколегированным относят стали, суммарный состав легирующих элементов в которых составляет не менее 10%, при содержании одного из них не менее 8%. При этом содержание железа должно составлять не менее 45%. В основном это стали, обладающие повышенной коррозионной стойкостью или жаростойкостью. Легирование сталей выполняют углеродом, марганцем, кремнием, молибденом, алюминием, ванадием, вольфрамом, титаном и ниобием, бором, медью, серой и фосфором. Введение легирующих элементов меняет физические и химические особенности стали.
Так, углерод способствует повышению прочности стали и снижению ее пластичности. Окисление углерода в процессе сварки способствует появлению пор. Кремний является раскислителем и содержание его в стали более 1% приводит к снижению свариваемости. Хром также снижает свариваемость, способствуя созданию тугоплавких окислов. Никель повышает прочность и пластичность сварочного шва, не снижая свариваемость стали. Молибден увеличивает прочность и ударную вязкость стали, ухудшая свариваемость. Ванадий в процессе сварочных работ сильно окисляется, поэтому его содержание в стали предусматривает введение раскислителей. Вольфрам тоже сильно окисляется при повышенных температурах, ухудшает свариваемость стали.
Титан и ниобий предотвращают межкристаллитную коррозию. Бор повышает прочность, но затрудняет свариваемость. Медь повышает прочность, ударную вязкость и коррозийную стойкость стали, но снижает ее свариваемость. Повышенное содержание в стали серы приводит к образованию горячих трещин, а фосфор способствует образованию холодных трещин.
Содержание тех или иных легирующих элементов определяют по маркировке стали. Первые две цифры в маркировке означают содержание углерода в сотых долях процента; легирующие элементы обозначают буквенными символами, а стоящие за ними цифры указывают на примерное содержание этих элементов, при этом единицу и меньше не ставят. Символ «А», установленный в конце маркировки, указывает, что сталь высококачественная, с пониженным содержанием серы и фосфора. Наиболее широкое применение получили коррозионно-стойкие хромоникелевые стали (12Х18Н10Т, 10Х23Н18 и некоторые другие).
Из вышесказанного видно, что, как правило, легирование стали приводит к снижению ее свариваемости, а первостепенную роль при этом играет углерод. Поэтому доля влияния каждого легирующего элемента может быть отнесена к доле влияния углерода. Повышенное содержание углерода и легирующих элементов способствует увеличению склонности стали к резкой закалке в пределах термического цикла, происходящего во время сварки. В результате этого околошовная зона оказывается резко закаленной и теряет свою пластичность.
Поэтому при сварочных процессах высоколегированных сталей, происходящих в зоне плавления металла и околошовной области, возникают горячие трещины и межкристаллитная коррозия, проявляющаяся в процессе эксплуатации. Основной причиной появления трещин является образование крупнозернистой структуры в процессе кристаллизации и значительные остаточные напряжения, полученные при затвердевании металла. Легирование влияет на вязкость металла и коэффициент поверхностного натяжения, поэтому у большинства высоколегированных сталей сварочный шов формируется хуже, чем у низколегированных и даже углеродистых сталей.
Межкристаллитная коррозия характерна для всех видов высоколегированных сталей, имеющих высокое содержание хрома. Под действием нагрева образовавшиеся карбиды хрома выпадают по границам зерен, снижая их антикоррозийные свойства.
Препятствует образованию карбидов хрома легирование стали титаном, ниобием, танталом, цирконием и ванадием. Положительное влияние на качество сварочного шва оказывает дополнительное легирование сварочной проволоки хромом, кремнием, алюминием, ванадием, молибденом и бором.
Для сварки высоколегированных сталей используют как ручную дуговую, так механизированную сварку под флюсом и в среде защитных газов. Сварка выполняется при минимальном тепловложении с использованием термообработки и применением дополнительного охлаждения. Введение легирующих элементов меняет и технологические особенности стали. Так, система легирования снижает теплопроводность стали и повышает ее электрическое сопротивление. Это оказывает влияние на скорость и глубину плавления металла, что требует меньшего вложения энергии, и увеличения скорости подачи сварочной проволоки.
Ручную дуговую сварку высоколегированных сталей выполняют при пониженных тока обратной полярности. Сварку ведут короткой дугой ниточными валиками без поперечных колебаний.
Проволока, применяемая для изготовления электродов, должна соответствовать марке стали с учетом ее свариваемости. Защитное покрытие электродов должно иметь состав, снижающий отрицательное действие повышенной температуры. К примеру, для сварки кислотостойкой стали 12X18HI0T электроды типа Э-04Х20Н9 (марки ЦЛ-11) препятствуют образования горячих трещин и межкристаллитной коррозии. Предварительный и сопутствующий подогрев снижает опасность возникновения трещин. Для защиты сварочной ванны используют инертный газ или аргон и его смеси с гелием, кислородом и углекислым газом.
Сварку в среде углекислого газа можно выполнять только в случаях, когда отсутствует опасность возникновения межкристаллитной коррозии. Сварка плавящимся электродом выполняется при значениях тока, обеспечивающих струйный перенос электродного металла.
При сварке возникает опасность коробления и остаточных сварочных напряжений. Поэтому после сварки часто возникает необходимость в термообработке.
build.novosibdom.ru
Читать книгу Cварка легированных сталей Ильи Мельникова : онлайн чтение
Илья МельниковCварка легированных сталей
ЛЕГИРУЮЩИЕ ЭЛЕМЕНТЫ
Легированные стали подразделяют на низколегированные (с содержанием легирующих компонентов, кроме углерода, не более 2,5%), среднелегированные (с содержанием легирующих компонентов, кроме углерода, 2,5-10%) и высоколегированные (с содержанием легирующих компонентов, кроме углерода, свыше 10%).
Свариваемость легированных сталей оценивается не только возможностью получения сварного соединения с физико-механическими свойствами, близкими к свойствам основного металла, но и возможностью сохранения специальных свойств: коррозионной стойкости, жаропрочности, химической стойкости, стойкости против образования закалочных структур и др. Большое влияние на свариваемость стали оказывает наличие в ней различных легирующих примесей: марганца, кремния, хрома, никеля, молибдена и др.
Влияние кремния и марганца на свариваемость стали уже рассматривалось, остановимся на других элементах.
Хром содержится в низколегированных сталях до 0,9 %. При таком содержании он не оказывает существенного влияния на свариваемость стали. В конструкционных сталях хрома содержится 0,7-3,5 %, в хромистых – 12-18 %, в хромоникелевых – 9-35 %. С повышением содержания хрома свариваемость стали ухудшается, так как, окисляясь, хром образует тугоплавкие оксиды Сr2О3, резко повышает твердость стали в зоне термического влияния, образуя карбиды хрома, а также способствует возникновению закалочных структур.
Никель содержится в низколегированных сталях до 0,6 %, в конструкционных сталях – 1,0-5 %, в легированных сталях – 8-35 %. Никель способствует измельчению кристаллических зерен, повышению пластичности и прочностных качеств стали и не снижает свариваемости.
Молибдена в теплоустойчивых сталях содержится от 0,15 до 0,8 %, в сталях, работающих при высоких температурах, и ударных нагрузках, – 3,5 %. Молибден способствует измельчению кристаллических зерен, повышению прочности и ударной вязкости стали, но ухудшает свариваемость стали, так как способствует образованию трещин в металле шва и в зоне термического влияния. В процессе сварки легко окисляется и выгорает. Поэтому требует специальных мер для надежной защиты от выгорания при сварке.
Ванадий содержится в сталях до 1,5 %. Он придает стали высокую прочность, повышает ее вязкость и упругость. Ухудшает свариваемость, так как способствует образованию закалочных структур в металле шва и околошовной зоны. При сварке легко окисляется и выгорает.
Вольфрам содержится в сталях от 0,8 до 18 %. Значительно повышает твердость стали и теплостойкость. Снижает свариваемость стали, в процессе сварки легко окисляется и выгорает.
Титан и ниобий содержатся в нержавеющих и жаропрочных сталях в пределах 0,5-1,0%. Они являются хорошими карбидообразователями и препятствуют образованию карбидов хрома. При сварке нержавеющих сталей ниобий способствует образованию горячих трещин.
СВАРКА НИЗКОЛЕГИРОВАННЫХ СТАЛЕЙ
Низколегированные стали содержат углерода до 0,25 % и легирующих примесей до 3 %. Они относятся к категории удовлетворительно свариваемых сталей. Следует учитывать, что при содержании в стали углерода более 0,25 % возможно образование закалочных структур и даже трещин в зоне сварного шва. Кроме того, выгорание углерода вызывает образование пор в металле шва.
Сталь марки 15ХСНД сваривают вручную электродами типа Э50А или Э55А. Наилучшие результаты дают электрод типа УОНИИ-13/55 и электрод ДСК-50. Сварку электродами типа ДСК-50 можно выполнять переменным током, но лучшие результаты дает сварка постоянным током обратной полярности. Многослойную сварку следует производить каскадным методом. Чтобы предупредить перегрев стали, следует выполнять сварку при токах 40-50 А на 1 мм диаметра электрода. Рекомендуется применять электроды диаметром 4-5 мм. Автоматическую сварку сталей 15ХСНД, 15ГС и 14Г2 производят проволокой типа Св-08ГА или Св-10ГА под флюсом АН-348-А или ОСЦ-45 при высоких скоростях, но при малой погонной энергии. В зимних условиях сварку конструкций из стали марки 15ХСНД можно производить при температурах не ниже -10°С. При более низких температурах применяют предварительный подогрев зоны сварки на ширине до 120 мм по обе стороны шва до температуры 100-150°С. При температуре – 25 °С сварка не допускается.
Стали марок 09Г2С и 10Г2С1 относятся к группе незакаливающихся, не склонных к перегреву и стойких против образования трещин. Ручная сварка электродами типов Э50А и Э55А выполняется на режимах, предусмотренных для сварки низкоуглеродистой стали. Механические свойства сварного шва не уступают показателям основного металла. Автоматическая и полуавтоматическая сварки выполняются электродной проволокой типа Св-08ГА, Св-10ГА или Св-10Г2 под флюсом АН-348-А или ОСЦ-45.
Сварку листов толщиной до 40 мм производят без разделки кромок. При этом равнонрочность сваренного шва обеспечивается за счет перехода легирующих элементов из электродной проволоки в металл шва.
Стали хромокремниемарганцовистые типа хромансиль, относятся к низколегированным (марки 20ХГСА, 25ХГСА, ЗОХГСА и 35ХГСА). Они дают закалочные структуры и склонны к образованию трещин. При этом чем меньше толщина кромок, тем больше опасность закалки металла и образования трещин, особенно в околошовной зоне. Для сварки могут применяться электроды НИАТ-ЗМ типов Э70, Э85. Для ответственных сварных швов рекомендуются электроды со стальными стержнями из проволоки типа Св-18ХГС или Св-18ХМА с покрытием следующих типов: ЦЛ-18-63, ЦК-18Мо, УОНИИ-13/65, УОНИИ-13/85, УОНИИ-13/НЖ.
При сварке рекомендуются следующие режимы:
При сварке более толстых металлов применяется многослойная сварка с малыми интервалами времени между наложением последующих слоев. При сварке кромок разной толщины сварочный ток выбирается по кромке большей толщины и на нее направляется большая часть зоны дуги. Для устранения закалки и повышенной твердости металла шва и околошовной зоны рекомендуется после сварки нагреть изделие до температуры 650-680 °С, выдержать при этой температуре определенное время в зависимости от толщины металла (1 ч на каждые 25 мм) и охладить на воздухе или в горячей воде.
Сварку низколегированных сталей в защитном газе производят при плотностях тока более 80 А/мм2. Сварка в углекислом газе выполняется при постоянном токе обратной полярности. Рекомендуется электродная проволока диаметром 1,2-2,0 мм марки Св-08Г2С или Св-10Г2, а для сталей, содержащих хром и никель, Св-08ХГ2С, Св-08ГСМТ.
Электрошлаковая сварка сталей любой толщины успешно производится электродной проволокой марки Св-10Г2 или Св-18ХМА под флюсом АН-8 при любой температуре окружающего воздуха. Эффективной является сварка в углекислом газе с применением порошковой проволоки.
Газовая сварка отличается значительным разогревом свариваемых кромок, снижением коррозионной стойкости и более интенсивным выгоранием легирующих примесей. Поэтому качество сварных соединений ниже, чем при других способах сварки. При газовой сварке пользуются только нормальным пламенем при удельной мощности 75-100 л/(ч•мм) при левом способе, а при правом – 100-130 л/(ч•мм). Присадочным материалом служит проволока марок Св-08, Св-08А, Св-10Г2, а для ответственных швов – Св-18ХГС и Св-18ХМА. Проковка шва при температуре 800-850 °С с последующей нормализацией повышает механические качества шва.
СВАРКА СРЕДНЕ– И ВЫСОКОЛЕГИРОВАННЫХ СТАЛЕЙ
Сварка этих видов сталей затруднена по ряду причин. В процессе сварки происходит частичное выгорание легирующих примесей и углерода. Вследствие малой теплопроводности возможен перегрев свариваемого металла. Эти стали отличает повышенная склонность к образованию закалочных структур, а больший, чем у низкоуглеродистых сталей, коэффициент линейного расширения может вызвать значительные деформации и напряжения, связанные с тепловым влиянием дуги. Причем, чем больше в стали углерода и легирующих примесей, тем сильнее проявляются эти свойства. Для устранения влияния перечисленных причин на качество сварного соединения рекомендуется:
–тщательно подготавливать изделие под сварку;
–сварку вести при больших скоростях с малой погонной энергией, чтобы не допускать перегрева металла;
–применять термическую обработку для предупреждения образования закалочных структур и снижения внутренних напряжений;
–применять легирование металла шва через электродную проволоку и покрытие с целью восполнения выгорающих в процессе сварки примесей.
Электроды для сварки высоколегированных сталей изготовляют из высоколегированной сварочной проволоки. Применяют покрытие типа Б. Обозначения типов электродов состоят из индекса Э и следующих за ним цифр и букв. Две или три цифры, следующие за индексом, указывают на количество углерода в металле шва в сотых долях процента. Следующие затем буквы и цифры указывают примерный химический состав металла. Сварку производят постоянным током обратной полярности. При этом сварочный ток выбирают из расчета 25-40 А на 1 мм диаметра электрода. Длина дуги должна быть возможно короткой. Рекомендуется многослойная сварка малого сечения при малой погонной энергии.
Хромистые стали относятся к группе нержавеющих коррозионно– стойких и кислотостойких сталей. По содержанию хрома они делятся на среднелегированные (до 14 % хрома) и высоколегированные (14-30% хрома). При сварке хромистых сталей возникают следующие затруднения. Хром при температуре 600-900 °С легко вступает во взаимодействие с углеродом, образуя карбиды, которые, располагаясь в толще металла, вызывают межкристаллитную коррозию, снижающую механические свойства стали. Чем выше содержание углерода в стали, тем активнее образуются карбидные соединения. Кроме того, хромистые стали обладают способностью к самозакаливанию (при охлаждении на воздухе), вследствие чего при сварке металл шва и околошовной зоны получает повышенную твердость и хрупкость. Возникающие при этом внутренние напряжения повышают опасность возникновения трещин в металле шва. Усиленное окисление хрома и образование густых и тугоплавких оксидов являются также серьезными препятствиями при сварке хромистых сталей.
Среднелегированные хромистые стали, содержащие углерода до 2 %, относятся к мартенситному классу. Они свариваются удовлетворительно, но требуют подогрева до 200-300 °С и последующей термической обработки.
Высоколегированные хромистые стали ферритного класса сваривают с предварительным подогревом до 300-400°С. После сварки для снятия внутренних напряжений и восстановления первоначальных физико-механических свойств изделие подвергают высокому отпуску – нагреву до 650-750 °С и медленному охлаждению. Электроды изготовляют из сварочной проволоки марок CB-01X19Н9, СВ-04Х19Н9 и Св-07Х25Н13 с покрытием, содержащим плавиковый шпат и оксид марганца. Это обеспечивает получение жидкого шлака, хорошо растворяющего окислы хрома. Рекомендуются покрытия типов ПЛ-2, ЦТ-2 и УОНИИ13/НЖ.
Хромистые стали, как и большинство легированных сталей, обладают малой теплопроводностью и легко подвергаются перегреву. Поэтому сварку их производят постоянным током обратной полярности при малых сварочных токах из расчета 25-30 А на 1 мм диаметра электрода.
Высоколегированные хромоникелевые аустенитные стали обладают рядом важных физико-химических и механических свойств: коррозионной стойкостью, кислотоупорностью, теплостойкостью, вязкостью, стойкостью против образования окалин. Важным качеством этих сталей является хорошая свариваемость.
Хромоникелевые стали марок 08Х18Н10 и 12Х18Н9 при нагреве до температуры 600-800 °С теряют антикоррозионную стойкость. Выделение карбидов хрома по границам зерен приводит к межкристаллитной коррозии стали. Поэтому сварку выполняют при постоянном токе обратной полярности при малых сварочных токах, сокращая продолжительность нагрева металла. Применяют также меры по отводу теплоты, например, при помощи медных подкладок или охлаждения. После сварки рекомендуется изделие подвергнуть нагреву до температуры 850-1100°С и закалке в воде или воздухе (для малых толщин металла).
Хромоникелевые стали марок 12Х18Н9Т и 08Х18Н12Б содержат титан и ниобий, которые, являясь более сильными карбидообразователями, связывают углерод стали, предупреждая образование карбидов хрома. Поэтому эти стали после сварки не подвергают термообработке. Для сварки хромоникелевых сталей применяют электроды типов ОЗЛ-7, ОЗЛ-8, ЦТ-1 и ЦТ-7. Рекомендуются электроды из сварочной проволоки типа Св-01Х19Н9, Св-06Х19Н9Т или Св-04Х19Н9С2 с покрытием ЦЛ-2, ЦЛ-4 (содержат 35,5 % мрамора, 41 % плавикового шпата, 8,5% ферромарганца и 15% молибдена), УОНИИ-13/НЖ и др.
Тонколистовую сталь марки 12Х18Н9Т следует сваривать аргонодуговой сваркой, так как при сварке качественными электродами или под флюсом происходит науглероживание металла шва. Это снижает стойкость стали против межкристаллитной коррозии.
Хромоникелевые аустенитные стали сваривают газовой сваркой при толщине металла не более 3 мм нормальным пламенем удельной мощности 75 л/(ч•мм). Присадочным материалом служат проволоки марок Св-01Х19Н9, CB-04X19Н9C2, Св-06Х19Н9Т и Св-07Х19Н10Б. Сварку следует вести быстро. Флюсом служат смесь буры (50%) и борной кислоты (50%) или плавиковый шпат (80%) и двуоксид кремния (20%).
Высоколегированная марганцовистая сталь, обладающая большой твердостью и износостойкостью, содержит 13-18% марганца и 1,0-1,3 % углерода. Она применяется для изготовления зубьев экскаваторов, шеек камнедробилок и других рабочих органов дорожных и строительных машин, работающих при ударных нагрузках и на истирание. Для сварки применяют электроды со стержнями из углеродистой проволоки марок Св-08А, Св-08ГА, Св-10Г2 с покрытием, которое применяется для наплавочных электродов марки ОМГ, содержащим 23 % мрамора, 15 % плавикового шпата, 60 % феррохрома, 2 % графита, замешанных на жидком стекле (30 % к общей массе сухих компонентов). Рекомендуются покрытия, применяемые для наплавочных электродов типа ОЗН (45-49 % мрамора, 15-18 % плавикового шпата, 26-33 % ферромарганца, 3 % алюминия, 4 % поташа, замешанных на жидком стекле). Применяют также стержни электродов из проволоки марок Св-04Х19Н9 и Св-07Х25Н13 с покрытием ЦЛ-2, состоящим из 44 % мрамора, 51 % плавикового шпата, 5 % ферромарганца, замешанных на жидком стекле (20-22 % к массе сухих компонентов). Хорошие результаты дает также покрытие УОНИИ-13/НЖ.
Сварка выполняется постоянным током обратной полярности короткими участками. Сварочный ток определяется из расчета 30-35 А на 1 мм диаметра электрода. Для получения шва повышенной прочности и износостойкости следует сварной шов проковать в горячем состоянии. При этом металл шва следует интенсивно охлаждать холодной водой.
Стали молибденовые, хромомолибденовые и хромомолибденованадиевые относятся к теплоустойчивым сталям перлитного класса. Эти стали применяют при изготовлении сварных паровых котлов, турбин, различной аппаратуры в химической и нефтяной промышленности, для работы при высоких температурах и давлениях. Эти стали свариваются удовлетворительно при выполнении установленных технологических приемов: предварительного подогрева до 200-300 °С и последующего отжига при температуре 680-780 °С или отпуска при температуре 650 °С. Температура окружающего воздуха должна быть не ниже 4-5 °С. Сварка выполняется постоянным током обратной полярности. Рекомендуются электроды типов ОЗС-11, ТМЛ-1, ТМЛ-2, ТМЛ-3, ЦЛ-38, ЦЛ-39 и др.
Для автоматической и полуавтоматической сварки применяют сварочную проволоку марок Св-08ХМ, Св-10Х5М и Св-18ХМА. При сварке в углекислом газе применяют предварительный и сопутствующий нагрев до температуры 250-300 °С, присадочную проволоку применяют типа Св-10ХГ2СМА. После сварки рекомендуется термообработка.
Газовая сварка выполняется нормальным пламенем при удельной мощности 100 л/(ч•мм). Присадочный материал – сварочная проволока типов Св-08ХНМ, Св-18ХМА и Св-08ХМ. Рекомендуется предварительный подогрев до 250-300 °С, а после сварки – термообработка (нормализация с температуры 900-950 °С).
Высоколегированные стали с особыми свойствами успешно сваривают в защитных газах. Режимы сварки подобны тем, которые используются при ручной сварке и под флюсом (ток обратной полярности, малые токи, термообработка). Электродную проволоку и флюсы применяют с учетом повышенного выгорания марганца, титана, ниобия, молибдена, никеля, т. е. элементов, обеспечивающих сохранение свойств свариваемых сталей.
КОНТРОЛЬНЫЕ ВОПРОСЫ. 1. Какое влияние оказывают легирующие примеси на свариваемость сталей? 2. Назовите особенности сварки деталей из низколегированных сталей. 3. В чем заключатся трудности сварки средне– и высоколегированных сталей? 4. Какие электроды применяют для сварки легированных сталей? 5. Как сваривают высоколегированные хромистые стали?
СВАРКА ЦВЕТНЫХ МЕТАЛЛОВ И ИХ СПЛАВОВ
ОСОБЕННОСТИ СВАРКИ ЦВЕТНЫХ МЕТАЛЛОВ
Температуры плавления и кипения цветных металлов относительно невысокие, поэтому при сварке легко получить перегрев и даже испарение металла. Если сваривают сплав металлов, то перегрев и испарение его составляющих может привести к образованию пор и изменению состава сплава. Способность цветных металлов и их сплавов легко окисляться с образованием тугоплавких оксидов значительно затрудняет процесс сварки, загрязняет сварочную ванну оксидами, снижает физико-механические свойства сварного шва.
Ухудшению качества сварного соединения способствует также повышенная способность расплавленного металла (сплава) поглощать газы (кислород, азот, водород), что приводит к пористости металла шва. Большая теплоемкость и высокая теплопроводность цветных металлов и их сплавов вызывают необходимость повышения теплового режима сварки и предварительного нагрева изделия перед сваркой. Сравнительно большие коэффициенты линейного расширения и большая литейная усадка приводят к возникновению значительных внутренних напряжений, деформаций и к образованию трещин в металле шва и околошовной зоны. Резкое уменьшение механической прочности и возрастание хрупкости металлов при нагреве могут привести даже к непредвиденному разрушению изделия.
Для выполнения качественного сварного соединения применяют различные технологические меры, учитывающие особенности каждого металла (сплава).
СВАРКА МЕДИ И ЕЕ СПЛАВОВ
При дуговой сварке меди следует учитывать, что теплопроводность меди примерно и шесть раз больше теплопроводности железа. При температуре 500-600 °С медь приобретает хрупкость, а при 700-800 °С прочность меди настолько снижается, что уже при легких ударах образуются трещины. Плавится медь при температуре 1083 °С.
Свариваемость меди в значительной степени зависит от наличия в металле примесей – висмута, свинца, сурьмы и мышьяка. Чистая электролитическая медь обладает наилучшей свариваемостью.
Расплавленная медь легко окисляется, образуя оксид меди Си20, поглощает водород и оксид углерода. При охлаждении в объеме металла выделяются пузырьки паров воды и углекислого газа, которые не растворяются в меди. Эти газы, расширяясь, создают большое внутреннее давление и приводят к образованию мелких межкристаллитных трещин. Это явление получило название водородной болезни меди.
Сварку меди и ее сплавов производят только в нижнем положении или при очень малых углах наклона.
Ручная дуговая сварка меди выполняется угольным или металлическим электродом. При сварке угольным или графитовым электродом в качестве присадочного материала применяют прутки из меди M1, из бронзы БрОФ6,5-0,15 или латуни ЛК62-0,5, а также медные прутки MCp1, содержащие до 1 % серебра.
Для предохранения меди от окисления и улучшения процесса сварки применяют флюсы, которые наносят на разделку шва и на присадочные прутки. Флюсы применяют следующих составов: 1) буры прокаленной – 68%, кислого фосфорнокислого натрия – 15 %, кремневой кислоты – 15 %, древесного угля – 2%; 2) буры прокаленной – 50%, кислого фосфорнокислого натрия – 15 %, кремневой кислоты – 15 %, древесного угля – 20%. Можно также применять одну буру, но лучше с присадкой 4-6 % металлического магния.
Листы толщиной до 4 мм можно сваривать с отбортовкой без присадочного металла, а более 4 мм – со скосом кромок под углом 35-45°. Сборка под сварку должна обеспечить минимальные зазоры (до 0,5 мм), чтобы предупредить протекание расплавленного металла шва. Рекомендуется также использовать подкладки из графита, асбеста или керамики. По концам шва следует сделать формовку. Сварку производят постоянным током прямой полярности. Длина дуги должна составлять 10-13 мм, напряжение тока 45-60 В. Сварку ведут со скоростью не менее 0,2-0,3 м/мин и при возможности за один проход.
Режимы сварки угольным электродом зависят от толщины свариваемых кромок. При толщине листов до 4 мм используют угольные электроды диаметром 4-6 мм, а сварочный ток выбирают в пределах 140-320 А. Если толщина листов более 4 мм, применяют электроды диаметром 8-10 мм при сварочном токе 350-550 А. После сварки металл шва проковывают – тонкие листы в холодном, а толстые в нагретом до температуры 200-350 °С состоянии. Для повышения вязкости металла шов подвергают отжигу с нагревом до температуры 500-550 °С с быстрым охлаждением в воде.
При сварке металлическим электродом подготовка кромок и обработка шва производится так же, как и при угольном электроде. Металлические электроды изготовляют из меди M1. Покрытие имеет следующий состав: ферромарганца – 50 %, ферросилиция 75 %-ного – 8%, полевого шпата – 12%, плавикового шпата – 10 %, жидкого стекла – 20 %. Толщина покрытия составляет 0,4 мм.
Применяют также электроды марки ЗТ со стержнем из бронзы БрКМц-3-1 и покрытием следующею содержания: марганцевой руды – 17,5 %, ферросилиция 75 %-ного – 32 %, плавикового шпата – 32, графита серебристого – 16 %, алюминия – 2,5 %. Связующим является жидкое стекло. Покрытие наносят на стержень диаметром 4-6 мм слоем толщиной 0,2-0,3 мм. Сварку выполняют возможно короткой дугой на постоянном токе обратной полярности. Сварочный ток определяют из расчета 50-60 А на 1 мм диаметра электрода.
Сварку меди в защитных газах (аргон, гелий или азот) применяют для изделий толщиной 1,5-20 мм и выполняют постоянным током прямой полярности. При диаметре вольфрамового электрода 2,5-5 мм и присадочной проволоки марки M1 или БрКМц-3-1 диаметром 2-6 мм сварочный ток составляет 200-500 А.
Автоматическую сварку меди производят под флюсами ОСЦ-45, АН-348-А или АН-20 проволокой диаметром 1,6-4 мм марки M1 или БрКМц-3-1. Напряжение составляет 38-40 В, сварочный ток принимают из расчета 100 А на 1 мм диаметра проволоки. Ток постоянный обратной полярности, скорость сварки 15-25 м/ч. Листы толщиной более 8 мм требуют предварительного подогрева.
При газовой сварке меди следует учитывать высокую теплопроводность меди и поэтому для сварки требуется пламя повышенной мощности. Для листов толщиной до 10 мм удельная мощность пламени должна быть равна 150 л/(ч•мм), для листов толщиной свыше 10 мм – 200 л/(ч•мм). Рекомендуется производить сварку одновременно двумя горелками: одна служит для подогрева свариваемых кромок с удельной мощностью 150-200 л/(ч•мм) и вторая – для сварки с удельной мощностью 100 л/(ч•мм).
Для уменьшения отвода теплоты изделия закрывают листовым асбестом. Пламя должно быть строго нормальным. Избыток ацетилена вызывает появление пор и трещин, а окислительное пламя приводит к окислению металла шва. Мундштук горелки устанавливают под углом 80-90°. Нагрев и плавку меди производят восстановительной зоной в месте максимальной температуры. Сварку производят без перерывов, в один проход. В процессе сварки подогретый конец присадочного прутка периодически обмакивают во флюс и таким образом переносят налипший флюс в сварочную ванну. Для получения мелкозернистой структуры и уплотнения металла производят проковку шва. Металл толщиной до 5 мм проковывают в холодном состоянии, а при большей толщине – в горячем состоянии при температуре 200-300 °С. После проковки производят отжиг с нагревом до температуры 500-550 °С и охлаждением в воде.
Латунь (сплав меди с цинком) сваривают всеми способами, указанными для меди. Основное затруднение при сварке латуни связано с кипением и интенсивным испарением цинка, пары которого в воздухе образуют ядовитые оксиды.
При сварке латуни угольным электродом применяют присадочные прутки из латуни ЛМц-58-2 и флюс из молотого борного шлака или буры. Применяют также прутки из латуни типа ЛК, содержащей, кроме меди и цинка, кремний.
При сварке плавящимся электродом применяют проволоку из латуни, содержащий цинка – 38,5-42,5 %, марганца – 4-5%, алюминия – 9,5%, железа – 0,5-1,5 %, остальное – медь. Покрытие наносят в два слоя. Первый слой толщиной 0,2-0,3 мм состоит из марганцевой руды – 30%, титанового концентрата – 30 %, ферромарганца – 15 %, мела – 20 % и сернокислого калия – 5 %. Связующим является жидкое стекло. Второй слой толщиной 0,8-1,1 мм состоит из борного шлака, замешанного на жидком стекле.
Автоматическая сварка латунных изделий производится электродной проволокой марки M1 под флюсом АН-348-А или ОСЦ-45 с добавкой 10 мас. ч. борной кислоты и 20 мас. ч. кальцинированной соды на 100 мас. ч. флюса. Сварка ведется постоянным током прямой полярности. Напряжение тока 38-42 В, сварочный ток при диаметре проволоки 2 мм составляет 300-480 А.
Латунь при газовой сварке нормальным пламенем выделяет пары, в результате чего шов получается пористым. Поэтому применяют пламя с избытком кислорода (до 30-40 %). Кислород окисляет часть цинка. Образующаяся на поверхности сварочной ванны оксидная пленка защищает расплавленный металл от дальнейшего окисления. Свариваемые кромки зачищают до металлического блеска. Оксиды удаляют травлением с помощью 10 %-ного водного раствора азотной кислоты, с последующей промывкой горячей водой и протиркой насухо. Удельная мощность пламени 100-150 л/(ч•мм). Мундштук горелки устанавливают под углом 80-90°, а присадочный пруток – под углом 80° к мундштуку горелки. Чтобы не допустить интенсивного окисления, сварку производят быстро, без перерывов и в один проход. Расстояние ядра пламени от ванны 7-10 мм. Латунь толщиной более 15 мм рекомендуется предварительно подогревать до 500-550 °С. После сварки шов проковывают. Если латунь содержит меди более 60 %, то проковку шва производят в холодном состоянии. Если меди менее 60%, то швы проковывают при температуре 700 °С. После проковки швы подвергают отжигу при температуре 600-650 °С с последующим медленным охлаждением.
Бронза – сплав меди с оловом, алюминием, кремнием, марганцем, цинком и свинцом. При сварке угольным электродом оловянистых бронз в качестве присадочного материала применяют прутки из сплава, содержащего меди – 95-96 %, кремния – 3-4%, фосфора – 0,25 %. Флюс – прокаленная бура или борный шлак.
При сварке специальных бронз применяют прутки, изготовленные из бронз свариваемых марок или близких им по химическому составу. Ток постоянный, прямой полярности. Сварку металлическим электродом фосфористой бронзы выполняют прутками следующего состава: олова – 10-12 %, фосфора – 0,15-0,45 %, остальное – медь. Для свинцовых бронз применяют прутки из сплава, содержащего (%): свинец – 21, олово – 8, цинк – 1,5, остальное – медь. Прутки покрывают различными защитными покрытиями. Ток постоянный, обратной полярности. При диаметре прутка 6-8 мм сварочный ток составляет 200-300 А.
Рекомендуется предварительный подогрев свариваемых деталей до температуры 250-300 °С. Допускается легкая проковка сварного шва для улучшения качества наплавленного металла.
Газовую сварку бронзы производят нормальным пламенем. Удельная мощность горелки 100-150 л/(ч•мм). Свариваемые кромки подготавливают так же, как и при сварке меди. Сварку ведут возможно быстро и в один проход. Конец ядра пламени должен быть на расстоянии 7-10 мм от поверхности сварочной ванны. Как и при сварке меди, допускается применение второй подогревающей горелки удельной мощности 100 л/(ч•мм). После сварки изделие нагревают до температуры 400-450 °С и затем охлаждают в воде.
iknigi.net
Сварка специальных (легированных) сталей
В зависимости от химического состава специальных сталей процесс сварки протекает по-разному. При сварке этих сталей происходит частичное выгорание легирующих примесей, вследствие чего металл шва по своим свойствам отличается от основного металла. Легированные стали хуже проводят тепло, чем малоуглеродистые стали. Малая теплопроводность легированных сталей способствует, во-первых, перегреву свариваемого металла, а во-вторых, появлению больших деформаций. Появление деформаций объясняется также большим, чем у малоуглеродистой стали коэффициентом линейного расширения.
С целью предупреждения перегрева металла и появления больших деформаций легированные стали сваривают горелкой меньшей мощности, чем это требуется для малоуглеродистой стали. Для уменьшения выгорания специальных примесей пламя горелки должно быть нормальным или с небольшим избытком ацетилена. Некоторые сорта специальных сталей могут закаливаться на воздухе, особенно в зоне термического влияния. Во избежание этого применяется перед сваркой подогрев изделия. Ряд сталей после сварки проходит термическую обработку.
Низколегированные хромокремненикелемедистые стали для строительных конструкций марок 15ХСНД (СХЛ-1, HJ1-2) и 10ХСНД (CXJ1-4). Эти стали хорошо свариваются ввиду небольшого количества углерода (соответственно до 0,18 и 0,12%) и малого содержания легирующих примесей (марганца 0,4—0,8%, никеля — 0,3— 0,6%, хрома 0,6—0,9%, меди —0,2—0,4%, кремния — 0,7—1,1 %).
Наконечник выбирается из расчета 100—130 л ацетилена в час при левой и 120—150 л/ч при правой сварке на 1 мм толщины металла. Пламя — нормальное. Присадочная проволока берется малоуглеродистая или того же сорта стали, что и свариваемый металл. Для получения большей плотности шва применяется проковка при светло-красном калении (800—850° С). Для улучшения пластических свойств соединения после проковки его подвергают нормализации с нагревом в лечи или горелкой и последующим охлаждением на воздухе.
Низколегированные молибденовые и хромомолибденовые стали. Стали этого типа применяются для изготовления труб в котлах высокого давления. Молибденовые стали — 15М, 20М и ЗОМ содержат 0,4—0,55% молибдена и до 0,3% хрома. Хромомолибденовые стали 20ХМ и ЗОХМ содержат 0,15—0,25% молибдена и 0,8—1,1% хрома. При сварке этих сталей мощность наконечника составляет 100— 130 л ацетилена в час на 1 мм толщины металла. Пламя горелки должно (быть нормальным. Иногда, чтобы предотвратить образование окислительного пламени в процессе сварки, начальную регулировку его производят с небольшим избытком ацетилена. В качестве присадочного металла применяют проволоку ,марок Св-18ХМА, Св-ЮХМ, Св-ЮМХ и Св-10Х5М по ГОСТ 2246-60, химический состав которых приведен в табл. 1. Хромомолибденовую сталь лучше сваривать проволокой марки Св-18ХМА. Диаметр проволоки в зависимости от толщины металла берется равным:
Толщина металла в мм. до 3 4—6 7—10 Диаметр присадочной
проволоки в мм . . . 3—4 4—5 4—6
Кромки металла перед сваркой должны быть зачищены до металлического блеска. При температуре окружающей среды ниже нуля должен проводиться предварительный подогрев изделия до 250—300° С. Если толщина свариваемого металла больше 16 мм, то вне зависимости от температуры окружающей среды изделие предварительно подогревают до той «же температуры, причем она должна сохраняться во время сварки примерно постоянной.
При толщине металла до 5 мм сварка ведется в один слой, а при большей толщине — в два и больше слоев. При двухслойной сварке первый слой накладывается на всю толщину металла, а вторым слоем усиливают шов. Сварка должна проводиться без перерыва. После окончания сварки пламя горелки должно медленно отводиться вверх, что способствует более .полному выделению газов из расплавленного металла; шов при этом получается плотным. При возобновлении сварки следует равномерно прогреть весь шов до 250— 300° С.
Сварные изделия из хромомолибденовой и молибденовой стали после сварки подвергаются термообработке. Стали 15М и 20М подвергаются нормализации путем нагрева горелкой до 900—930° и охлаждения на воздухе. Такая термообработка уменьшает внутренние напряжения и улучшает механические свойства сварного соединения.
Низколегированные хромокремнемарганцовистые стали (хромансиль). К этим сталям относятся следующие наиболее распространенные марки: 20ХГС, 25ХГС, ЗОХГС и 35ХГС. Они содержат от 0,17 до 0,40% углерода; 0,9—1,2% кремния; 0,8—1,1% марганца; 0,8—1,1% хрома. Эти стали после термической обработки обладают высокой прочностью. Мощность пламени наконечника выбирают из расчета 75 л ацетилена в час на 1 мм свариваемой толщины металла. Пламя должно быть нормальным. Окислительное пламя способствует усиленному выгоранию хрома, кремния и марганца, что приводит к появлению в сварочной ванне окислов и шлаков.
В качестве присадочного металла используется малоуглеродистая проволока марки Св-08 и Св08А, а когда от шва требуется повышенная прочность, то применяется проволока Св-18ХГСА или Св-18ХМА.
Кромки деталей должны быть очищены и хорошо подогнаны; зазор по всей длине шва должен быть строго одинаковым.
Прихватка листов производится через каждые 20—30 мм при толщине металла до 1,5 мм, а при большей толщине — через 40— 60 мм. От края листа прихватка должна отстоять на 10—15 мм.
Сварка должна проводиться в один слой от середины длины шва к его краям. Для уменьшения выгорания легирующих добавок сварку надо производить быстро, без перерывов и задержки пламени горелки на одном месте. Так как хромокремнемарганцовистые стали при резком охлаждении легко закаливаются, то при быстром отводе горелки от сварочной ванны возможно появление трещин в шве и в зоне термического влияния. Поэтому горелку нужно отводить медленно вверх, одновременно прогревая факелом пламени металл вокруг места окончания сварки.
Сваренные узлы иногда подвергаются термической обработке (закалке с отпуском). Закалку производят нагреванием до 500— 650° С, выдерживают при этой температуре 5 мин и дольше (из расчета 1,5 мин на 1 мм толщины), затем изделие нагревают до 880° С при той же продолжительности выдержки. После этого деталь охлаждают в масле. Отпуск заключается в нагреве стали до 400—600° С с последующим охлаждением в горячей воде.
Хромистые стали. Стали с содержанием хрома больше 12— 14% хорошо сопротивляются действию кислот и высоких температур. В промышленности применяются хромистые стали с содержанием хрома до 30% и углерода — от 0,13 до 0,9%.
Хромистые стали легко закаливаются на воздухе и поэтому в швах после сварки могут образоваться трещины, причем чем больше в стали углерода, тем чаще образуются трещины. Предварительный подогрев до 150—200° уменьшает опасность появления трещин. Такой подогрев обязателен для сталей с содержанием хрома более 14%. Большой коэффициент линейного расширения и малая теплопроводность этих сталей способствуют значительному короблению. Для уменьшения коробления и предупреждения перегрева хромистые стали варят пламенем пониженной мощности из расчета 70 л ацетилена в час на 1 мм толщины свариваемого металла.
Пламя горелки должно быть строго нормальным; избыток кислорода приводит к окислению хрома, а избыток ацетилена — к образованию так называемых карбидов хрома, что нежелательно, так как металл перестает быть стойким против кислот.
Присадочная проволока может быть из стали той же марки, что и основной материал, или же марки Св-04Х19Н9.
Для предупреждения выгорания хрома и выпадения карбидов хрома сварку необходимо производить быстро, избегая перерывов и повторных нагревов. Сварка должна быть односторонней и в один слой. Выгорание хрома предупреждается также нанесением на проволоку и свариваемые кромки флюса, причем флюс должен покрывать как лицевую, так и обратную стороны шва. Флюс не только предохраняет хром от выгорания, но и удаляет из ванны в шлак образовавшиеся окислы хрома. Состав флюса следующий (в %):
Борная кислота ..............55
Окись кремния..................10
Ферромарганец........ 10
Феррохром .................10
Ферротитан .................5
Титановая руда (концентрат) . 5
Плавиковый шпат...... 5
После сварки детали проходят термическую обработку, соответствующую данной марке стали.
Из-за длительного нагрева, имеющего место при газовой сварке в зоне нагрева у сталей марок XI7, Х28, получается крупнозернистая структура. Поэтому для таких сталей применение газовой сварки нежелательно.
Хромоникелевые нержавеющие стали. Наиболее распространенными марками этих сталей являются 1Х18Н9Т, Х18Н12М2Т и др. Они обладают высокой прочностью и вязкостью и хорошо сопротивляются действию высоких температур, щелочей, кислот и прочих, хорошо выдерживают холодную штамповку. Указанные свойства получаются благодаря определенному содержанию легирующих элементов: хрома 17—19%, никеля 8—11%.
Эти стали свариваются хорошо, но при сварке встречаются следующие затруднения.
1. При нагреве стали происходит выделение карбидов хрома, благодаря чему уменьшается устойчивость стали против действия кислот и щелочей. Титан и ниобий, введенные в сталь, уменьшают в ней склонность к выпаданию карбидов.
2. Хром при сварке легко окисляется и дает тугоплавкие окислы хрома, которые остаются в шве в виде шлаковых включений.
3. Так как хромоникелевые стали плохо проводят тепло и имеют большой коэффициент линейного расширения, то при сварке получаются значительные напряжения и коробления.
Мощность пламени горелки берут из "расчета 75 л/ч ацетилена на 1 мм толщины металла. Пламя должно быть строго нормальным: избыток кислорода приводит к образованию окислов !хрома и шов становится пористым; при избытке ацетилена образуются карбиды хрома и снижается пластичность металла.
Присадочная проволока может быть того же состава, что и основной металл; лучше брать проволоку с присадкой титана или ниобия, а углерода не должно быть более 0,12%.
Для металла толщиной до 1,5—2 мм делается отбортовка. Высота отбортовки равна толщине листа. При толщине листа 3—4 мм сварка производится без скоса кромок, а при большей толщине делается скос под углом 70—90°.
Для удаления окислов хрома и предупреждения появления их применяется флюс следующего состава: плавиковый шпат 80%; ферротитан 20%. Можно также взять флюс, состоящий из смеси 50% буры и 50% борной кислоты или 80% буры и 20% окиси кремния. Флюс замешивается на воде до консистенции сметаны. На кромки изделия он наносится за 15—20 мин до сварки. Наносить флюс необходимо с лицевой и с обратной сторон кромок. Для уменьшения коробления применяется обратноступенчатый способ сварки, причем начинают сварку на расстоянии 75—100 мм от края изделия. Желательно также сварку вести на медной или стальной подкладке, что усиливает отвод тепла от шва. Сварку следует вести быстро и в один проход, колебаний проволокой не производить. Сварочная ванна должна быть покрыта тонким слоем шлака, а конец проволоки— погружен в ванну. Сварка производится как левым, так и правым способами. Наклон мундштука горелки и проволоки такой же, как и при сварке углеродистой стали.
Для улучшения механических свойств и повышения стойкости против коррозии после сварки рекомендуется термообработка (нагрев до 1100° и быстрое охлаждение при толщине металла 1—2 мм на воздухе, при большей — в воде).
После сварки шлак и оставшийся флюс должны быть удалены промывкой швов в горячей воде.
Читайте также
Добавить комментарий
electrowelder.ru
Сварка легированных сталей
В состав легированных сталей входят специальные легирующие элементы: хром, никель, вольфрам, молибден, ванадий, титан и другие. К легированным сталям относятся также и те стали, которые имеют повышенное содержание марганца и кремния. Легированные стали обладают по сравнению с углеродистыми более высокими механическими свойствами, а также и специальными свойствами, которые необходимы для работы изделий в условиях глубокого холода, агрессивных сред, высоких температур и давлений.
Для легированных сталей принято буквенно-цифровое обозначение. По этим обозначениям можно приблизительно определить химический состав сталей.
В государственных стандартах приняты следующие обозначения для легирующих элементов (см. табл. 67).
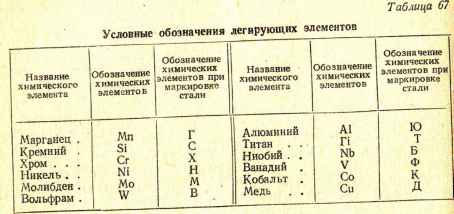
Табл.67.Условное обозначение легирующих элементов
Цифры, стоящие впереди марки стали, указывают среднее содержание углерода в десятых долях процента для высоколегированных сталей, и в сотых долях процента для низколегированных сталей.
Цифра, стоящая после той или иной буквы, указывает на среднее содержание этого элемента в процентах. Если после буквы цифра не стоит, то содержание этого элемента составляет около одного процента. Буква «А», стоящая в конце марки, указывает на повышенное качество стали. Такая сталь имеет ограничейное содержание вредных примесей.
Пример расшифровки состава стали по ее маркировке.
Маркировка 1Х18Н9Т относится к нержавеющей стали, содержащей в среднем 0,1% углерода, 18% хрома, 9% никеля и до 1 % титана.
Маркировка ЗОХГСА относится к низколегированной стали, в состав которой входит около 0,30% углерода, а содержание хрома, марганца и кремния не превышает 1% для каждого элемента в отдельности. Содержание вредных примесей ограничено: сера 0,03%, фосфор 0,035%.
Легирующие добавки оказывают следующее действие.
Хром вводится в конструкционные стали в пределах 0,7— 1,75%. В специальных сталях содержание хрома доходит до 30%. Хром способствует закаливаемости стали, несколько понижает пластические свойства стали; часто его добавляют в сплавы вместе с другими легирующими примесями, например, никелем, молибденом и др.
Никель сильно улучшает прочность и пластичность стали. Содержание никеля в легированных конструкционных сталях доходит до 5%. В специальных сталях никеля может быть до 50%. Чаще всего никель применяется в сочетании с другими элементами (хромом, кремнием и др.).
Молибден в конструкционных сталях содержится обычно в небольших количествах — до 0,60%- Молибден уменьшает склонность стали к перегреву, повышает ее стойкость при повышенных температурах, устраняет явление хрупкости при отпуске, повышает ударную вязкость, а также улучшает обрабатываемость стали в холодном и горячем состояниях.
Ванадий вводится в легированную конструкционную сталь в количествах 0,2—0,3%. Весьма ценным свойством малых количеств ванадия явдяется его способность измельчать зерно в стали. Ванадий повышает сопротивление стали перегреву, а также значительно улучшает механические свойства стали.
Титан вводится в сталь в небольших количествах — около 0,5%. Оказывает такое же действие, как ванадий. Кроме того, титан повышает вязкость стали и улучшает ее сварочные свойства.
Марганец содержится в любой стали в количествах 0,3— 0,7%. Как легирующая примесь марганец вводится в количестве до 14—17%. Марганец повышает закаливаемость стали и улучшает ее механические свойства.
Кремний входит в любую сталь в пределах до 0,6%. В легированные стали кремний вводится в количестве 0,8—1,2% для повышения упругих свойств. Большее содержание кремния (до 1,9%) вызывает некоторое понижение пластических свойств стали и ухудшает свариваемость.
Сварка легированной стали находится в большой зависимости от ее химического состава, при этом основное значение имеет количественное содержание углерода. Легирующие добавки влияют на свариваемость слабее углерода. Влияние легирующих примесей неодинаково, например, хром и марганец способствуют образованию трещин больше, чем никель. Благоприятно действует на свариваемость присадка титана.
Значительно ухудшают свариваемость стали вредные примеси: сера, фосфор и растворенные газы. Для получения нормальных результатов сварки содержание серы и фосфора не должно превышать 0,020—0,055%.
www.prosvarky.ru