Строительный справочник | материалы - конструкции - технологии. Технология кислородной резки металла
технология, необходимое оборудование, техника безопасности
Кислородную резку металлов (в литературе можно встретить термин «автогенная резка») активно применяют в промышленности для нарезки листового материала из стали и иных сплавов на заготовки необходимой длины. Также данная технология применяется при проведении ряда ремонтных работ и работ по демонтажу конструкций. Популярность ее обусловлена сравнительной простотой и низкой стоимостью оборудования, а также высокой степенью безопасности. Статья содержит сведения о самой технологии, о необходимом оборудовании и основах техники безопасности при проведении кислородной резки металлов и других материалов.
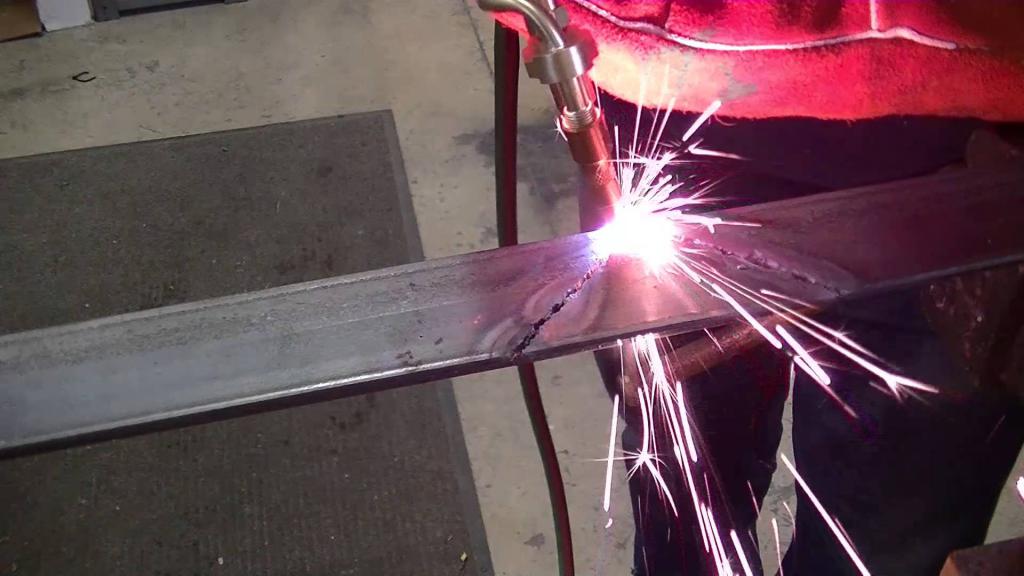
Основы технологии
Перед началом резания металл рекомендуется нагреть пламенем горелки. Это касается лишь материалов с большим сечением. Упомянутое пламя появляется вследствие реакции кислорода с газом. Если пренебречь этой рекомендацией, то металл неизбежно поведет, произойдет коробление. Впрочем, если геометрическая форма нарезаемых кусков не важна, например, при осуществлении работ по демонтажу сооружений из строительных сталей, а также при нарезании тонкостенных листов, допускается газовая сварка и кислородная резка металла без предварительного подогрева изделий.
Высокие температуры в зоне резания достигаются путем сжигания кислорода высокой степени очистки из баллона. В металлических резервуарах под очень высоким давлением содержится от 99 до 99,8 % кислорода. Если для подогрева используется кислород обычной чистоты (грубо говоря, атмосферный воздух), то для эффективной кислородной резки металла нужен именно кислород высокой чистоты.
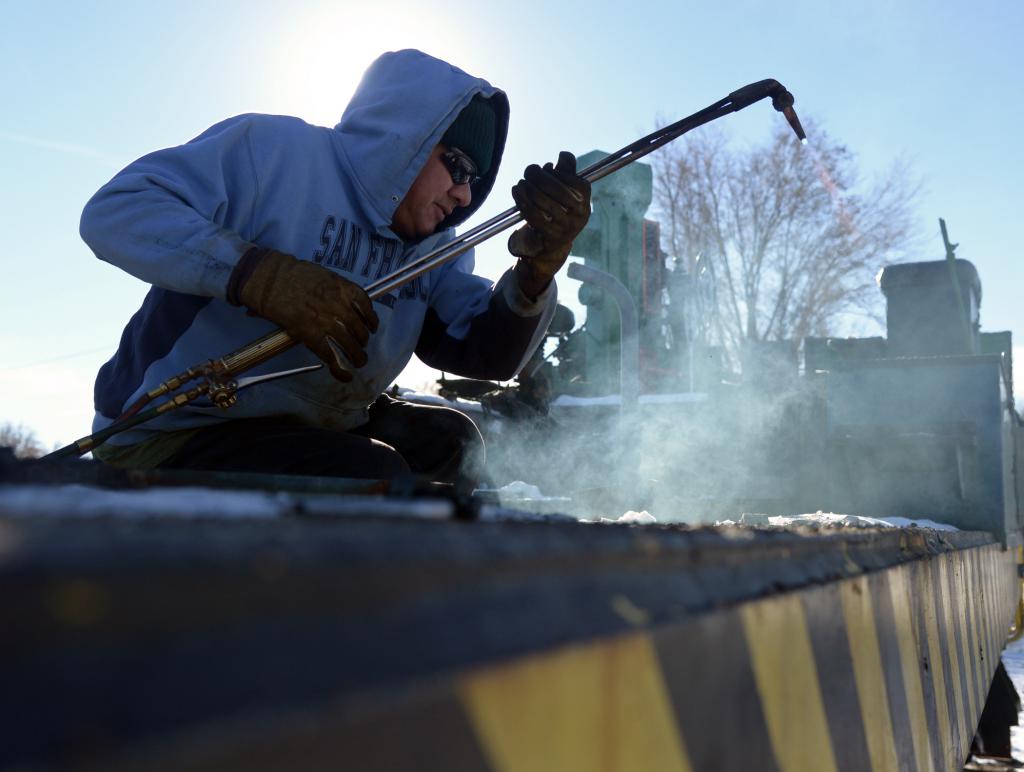
Подготовка поверхности
Если стоит задача распилить на транспортируемые куски крупный объект, который подлежит утилизации, то подготовкой поверхности можно и не заниматься. Резак справится с этой задачей в кратчайшие сроки. Другое дело – производство новых изделий. В этом случае важно получить качественную линию разреза, чистую от окалины и других нежелательных включений. Кислородной резке металла предшествует тщательная очистка материала.
Существует большое количество методов устранения загрязнений. Наиболее популярные из них – прогрев поверхности газовым пламенем и механическая очистка. Первый способ наиболее прост. Он позволяет эффективно устранять окалину – злейшего врага газосварщика. Сущность его заключается в прогреве поверхности металла до критических температур. Второй метод является более затратным и требует наличия специального оборудования (пескоструйные машины, скребки, щетки и так далее) и квалифицированного рабочего персонала.
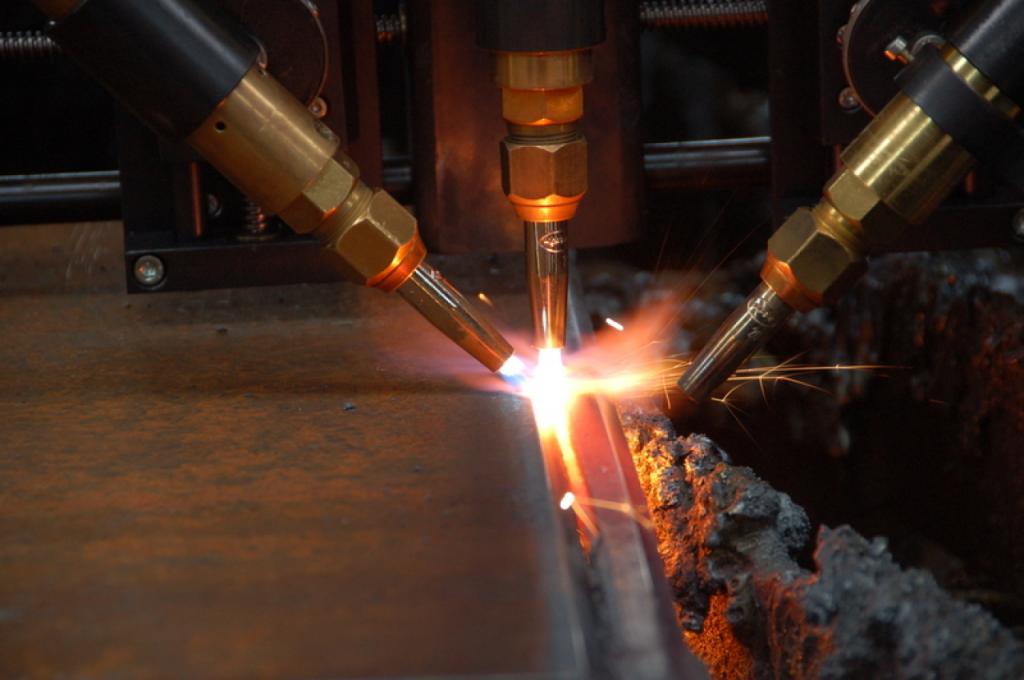
Требования к материалам
Кислородно-флюсовой резке металлов могут подвергаться далеко не все марки стали и сплавы. Одними из главных условий являются температура плавления и температура воспламенения. Для нормального протекания процесса первый показатель должен быть значительно выше второго. Понятно почему: в противном случае материал будет оплавляться, а не сгорать, что приведет к образованию потеков. Линия реза будет иметь неаккуратный вид, зачастую это делает невозможной дальнейшую обработку детали на механообрабатывающих станках в результате смещения баз. Кроме того, такой слой металла может иметь плохие механические и физические свойства.
Определенные элементы, добавляемые в состав сталей в качестве примесей, могут оказывать отрицательное воздействие на процесс кислородно-пропановой резки металла. Так наиболее обрабатываемыми считаются стали, содержание углерода в которых не превышает 0,3 %. Скорость резки при увеличении содержания углерода не уменьшается, однако сталь становится склонной к перегреву, закалке поверхностного слоя и образованию закалочных трещин, которые могут послужить концентраторами напряжений и привести к хрупкому разрушению всей заготовки.
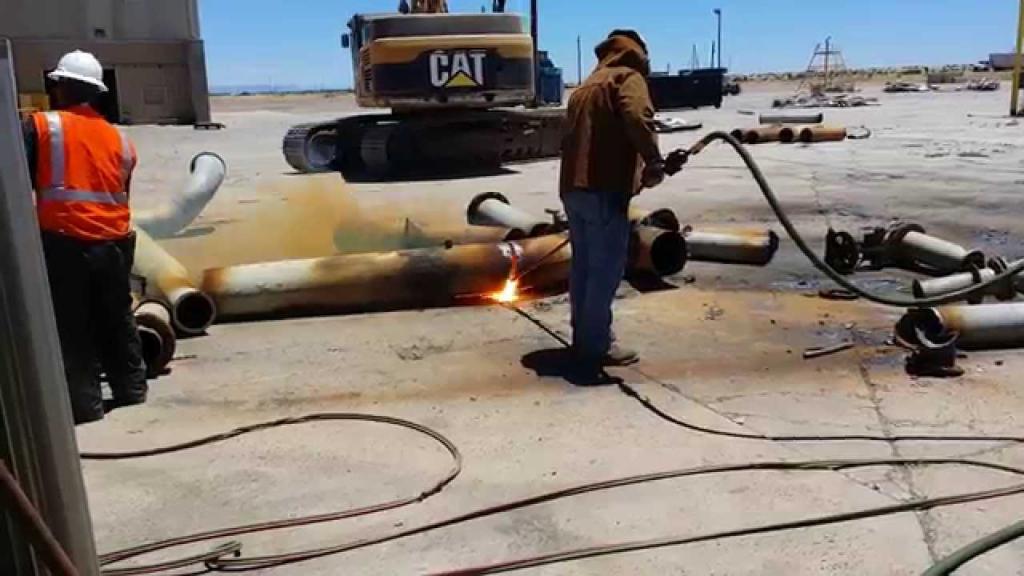
Ручная резка
Газовая кислородная резка металла, в зависимости от степени автоматизации и механизации, подразделяется на механизированную и ручную.
Ручную сварку целесообразно использовать в условиях мелкосерийного и единичного производства, а также при проведении работ по демонтажу конструкций и сооружений. Идеально подходит для вырезания заготовок из труб, устранения литников с литых изделий и так далее.
Оборудование кислородной резки металлов и сплавов отличается высокой мобильностью, простотой в эксплуатации и надежностью. Благодаря этим качествам эта технология является наиболее распространенной как на промышленных предприятиях, так и в ремонтных организациях.
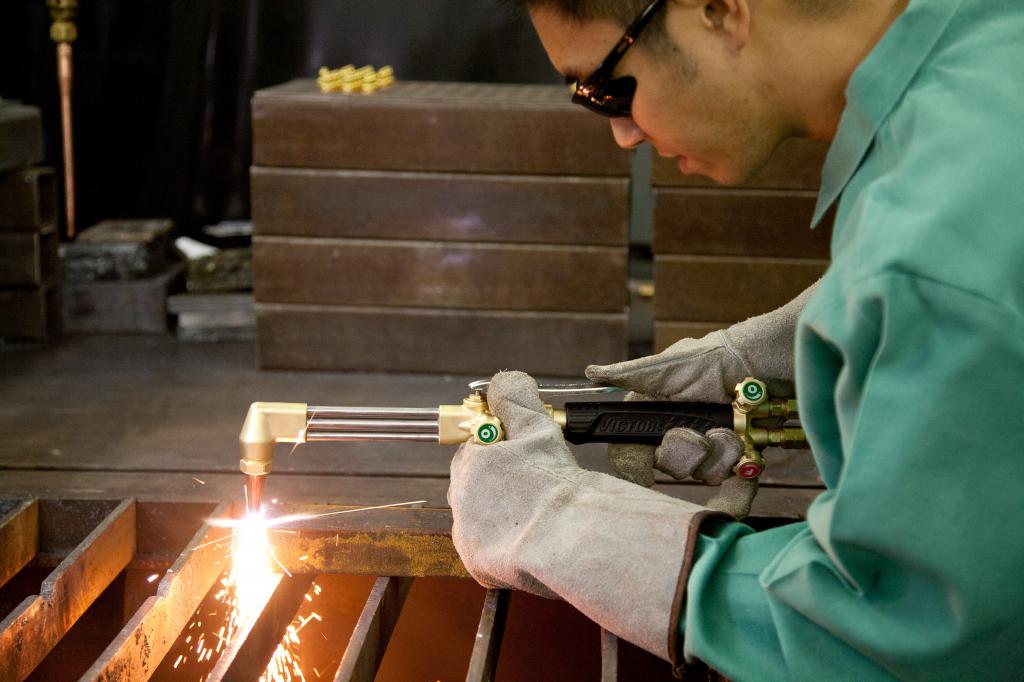
Механизация процесса
За последние десятилетия робототехника развивалась очень стремительно. Сегодня роботы применяются практически повсеместно. И кислородно-дуговая резка металлов – не исключение. В настоящее время оборудованием для резки с числовым программным управлением уже никого не удивишь. Эти аппараты могут оснащаться несколькими кислородными резаками для резки металла, что значительно повышает их и без того высокую производительность. Все ведущие зарубежные машиностроительные холдинги и компании уже давно активно внедряют подобную технику в свои производственные цепочки, стараются не отставать и отечественные компании. Уровень механизации сварочных работ в среднем составляет порядка 80 %.
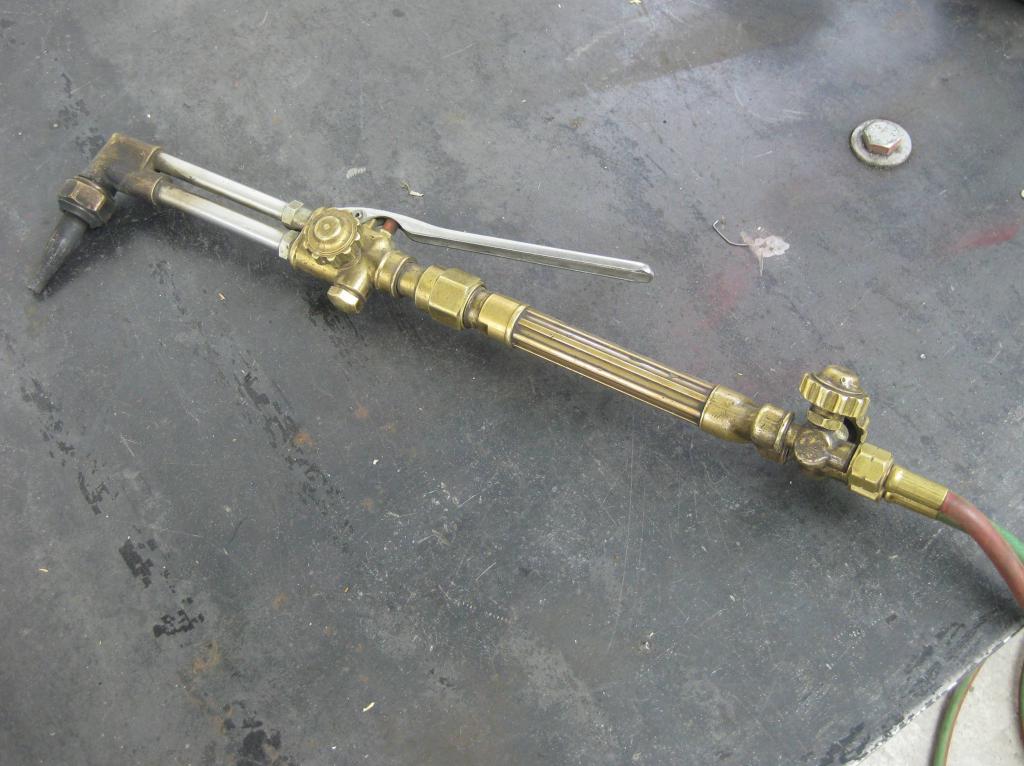
Сущность кислородно-флюсовой резки металла
Традиционная резка подходит далеко не для всех материалов. Например, сталь, легированная хромом с никелем, плохо поддается резке. Аналогичная проблема возникает и при нарезании цветных металлов и чугунов.
Тогда на выручку приходит кислородно-флюсовая технология. Сущность ее заключается в следующем. В зону резания подается порошок флюса. Это вещество в процессе резания воспламеняется и сгорает, выделяя при этом большое количество тепла, что делает возможным оплавление тугоплавких карбидов, боридов и оксидов металлов.
Оборудование для кислородно-флюсовой резки
Можно сказать, что для этого вида резки металла используется обычное стандартное оборудование, дополнительно оснащенное устройством для подачи флюса (так называемый флюсопитатель и кислородный резак для резки металла с подачей флюса). Самыми распространенными установками такого типа являются приборы конструкции научно-исследовательского института Автогенмаш «УРХС». Это оборудование предназначается для резки сталей с высоким содержанием хрома и других легирующих элементов.
Такое оборудование использовать и для механизированной резки, оснастив станок устройством подачи флюса.
Приемы кислородно-флюсовой резки
Техника не отличается от уже ставших традиционными приемов классической кислородной резки. Сам процесс может осуществляться как руками, так и механизированным путем с использованием вспомогательных средств, роботов и приспособлений. Она также может быть как разделительной, так и поверхностной. Рекомендуется применять для раскроя и нарезания сталей с высоким содержанием хрома и никеля (то есть для тугоплавких сталей).
Особенности кислородно-флюсовой резки чугуна
При сгорании флюс выделяет много тепла. Настолько много, что происходит так называемый отбел чугуна. Сущность этого явления заключается в том, что углерод переходит из свободного состояние в связанное. Иными словами, атомы углерода на определенном участке образуют с атомами металла химическое соединение. Это сопровождается ухудшением механическим свойств чугуна (увеличивается твердость, он становится более хрупким). В результате ускоренного прогрева и охлаждения, на поверхности появляются трещины, которые могут вызвать разрушение изделия.
Решить проблему позволяет предварительный прогрев металла и регулирование скорости его охлаждения. Справиться с такими задачами под силу лишь рабочему с высокой квалификацией и большим опытом в проведении подобных работ.
Особенности кислородно-флюсовой резки цветных металлов и сплавов
Как и чугун, медь необходимо подогревать перед тем, как начать ее резать. Нагрев осуществляется до температуры 800–900 градусов по Цельсию. Медь обладает высокой теплопроводностью, поэтому резка без предварительного подогрева приведет к значительным короблениям, пространственным искажениям и браку.
Сплавы на основе меди с другими элементами (латунь, бронза и так далее) также необходимо подогревать. Однако температура предварительного нагрева не должна превышать 500 градусов Цельсия.
Преимущества и минусы технологии кислородной резки
По сравнению с другими, альтернативными методами раскроя листового материала разных марок сталей, данная технология отлично подходит для разрезания по кривым линиям, для вырезания отверстий большого диаметра. Также этот метод позволяет получать глухие отверстия.
Вторым, и весьма значительным, преимуществом является простота в использовании оборудования. Газовый резак имеет небольшую массу, благодаря чему сварщик может длительное время работать с ним, при этом не уставая. Это положительно сказывается на производительности.
Газ является сравнительно доступным и дешевым видом топлива. И это третье преимущество.
Весьма существенны недостатком технологии является взрывоопасность используемых веществ. Поэтому не допускается нарушения технологической дисциплины. Игнорирование правил техники безопасности может привести к тяжелым последствиям.
Правила эксплуатации кислородного редуктора для резки металла
Перед подключением редуктора рабочий обязан убедиться в отсутствии загрязнений на резьбовых поверхностях. При наличии таковых необходимо обработать загрязненные поверхности керосином или растворителем. Лишь после продувки системы и удаления всех посторонних частиц и элементов, которые могут попасть в редуктор и нарушить его работу, можно накидывать и закреплять гайку на редуктор.
Таким же образом происходит установка и других редукторов.
Пуск газов осуществляется плавным открытием вентиля баллона. Если никаких отклонений от работы не наблюдается, вентиль можно открывать полностью. Если редуктор начнет греться, аномально шуметь, необходимо немедленно перекрыть маховик кислородного баллона для резки металла.
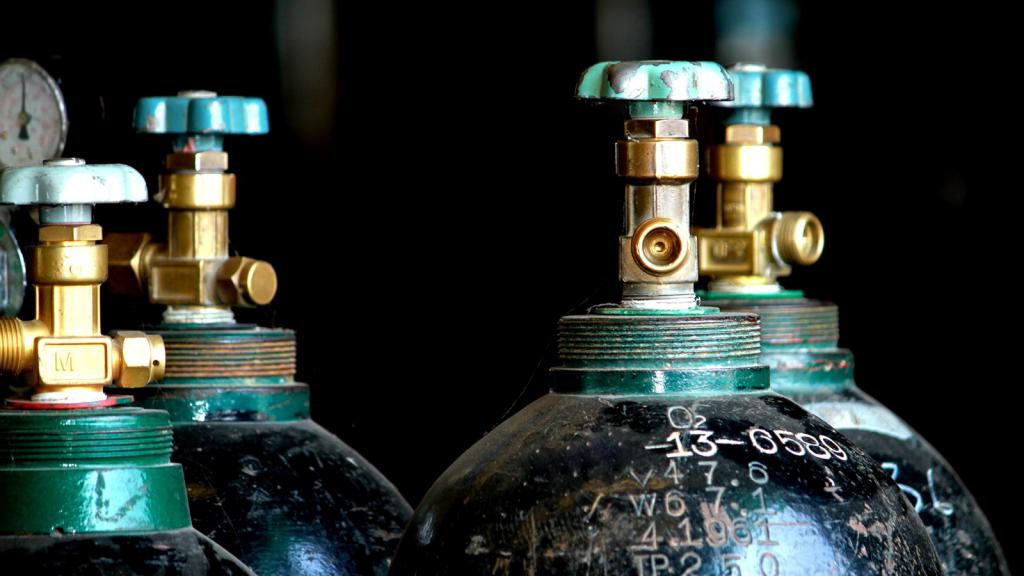
Техника безопасности при проведении работ
После подготовительных работ необходимо убедиться в отсутствии утечек газов. Это может быть очень опасно. Лишь после этого можно зажечь резак и отрегулировать пламя.
Если необходимо сделать небольшую паузу в работе (не более двух-трех минут), то достаточно лишь перекрыть вентиль резака. В том случае, если работы прекращаются на длительное время, необходимо перекрыть редуктор и вентиль газового баллона.
Ко всем работам по кислородной резке металла допускаются лишь рабочие, прошедшие все необходимые инструктажи.
Запрещено проводить любые работы вблизи от взрывоопасных резервуаров и легковоспламеняющихся материалов. Если работы выполняются в небольших закрытых пространствах, то рабочие должны регулярно отдыхать и дышать свежим воздухом.
Сварочные работы на производстве, которые выполняются систематически (не временного характера) должны проводиться в специально оборудованных помещениях. При этом площадь одного рабочего места – не менее четырех метров квадратных. Проходы между рабочими местами должны быть не менее 0,8 метра.
Помещения должны быть оборудованы мощной вытяжкой вредных веществ. Ее производительность должна составлять 2500–3000 м3 на 1 м3 сжигаемого газа.
В том случае, если в одном помещении (цехе) оборудовано более десяти рабочих мест сварщиков, газ должен поступать на них не из баллонов, а централизованно из газораспределительной станции. Допускается подача газов из действующих газопроводов.
Баллоны с рабочим газом допускается транспортировать лишь с защитными колпаками. Они предотвратят вентиль от повреждений и загрязнений. Запрещено транспортировать баллоны на большие расстояния руками. Для этих целей нужно применять специальные приспособления и тележки. Удары баллонов о землю или друг о друга недопустимы.
В кислородном баллоне для резки металла при нарушении технологии и порядка работы может образоваться взрывоопасная смесь газа с кислородом. Поэтому необходимо с ответственностью подходить к регулировке редукторов.
fb.ru
1.Введение
Содержание.
Страница
1.Введение...........................................................................................................4
2. Технология ручной кислородной резки деталей из листовой стали до
60 мм по разметке.....................................................................................4
2.1. Общие сведения о кислородной резке.....................................................4
2.2.Подготовка металла под резку..................................................................5
2.3 Техника и приемы ручной резки..............................................................5
2.4.Резаки для кислородной резки...................................................................6
3. Технический контроль резки........................................................................8
4.Техника безопасности при резке...................................................................9
4.1 Техника безопасности при газопламенной обработке..........................9
4.2 Пожарная безопасность при сварке........................................................10
Список литературы.....................................................................................11
Временем возникновения профессии «сварщик» считается 1802 год, когда русским академиком Василием Петровым было сделано открытие эффекта электрической дуги, возникающей между двумя угольными стержнями при прохождении через них тока. С момента этого открытия и до его применения прошёл немалый период времени .
Сегодня вряд ли найдется хоть одна отрасль, где не приняли бы своего участия сварщики. Эта профессия требует высокого уровня ответственности, так как срок эксплуатации всевозможной техники напрямую связаны с качественно выполненной работой сварщика. Именно благодаря сварке металлические элементы будут надежно соединены как при изготовлении новых конструкций или изделий, так и при ремонте старых элементов.
Для того, чтобы любые сварочные работы проходили с наименьшим риском, необходимо строго соблюдать технику безопасности и хорошо знать санитарные нормы. Любые ошибки или небрежность сварщика ставят под угрозу не только его здоровье, но и безопасность окружающих.
из листовой стали до 60 мм по разметке.
2.1.Общие сведения о кислородной резке.
Кислородная резка является одним из наиболее распространённых процессов газопламенной обработки металлов. Она широко используется в металлообработке и металлургии при резке листов, заготовок профильного проката, труб и т.д. Различают два вида кислородной резки: разделительную и поверхностную.
При разделительной резке образуются сквозные разрезы, а при поверхностной – канавки круглого очертания.
Разделительная резка производится без и со скосом кромок под сварку, а поверхностная бывает либо сплошной, когда обрабатывается вся поверхность заготовки за один проход, либо выборочной с удалением поверхностного слоя металла.
В отличие от сварки кислородная резка на вертикальной плоскости или в потолочном положении не представляет трудностей и может производиться в любом пространственном положении.
В процессе резки металл расплавляется и вытекает из полости реза. Однако железо легко окисляется, а в чистом кислороде горит и превращается в оксиды и шлаки.
К термическому и химическому действию может присоединяться механическое действие струи газа, выталкивающее жидкие и размягчённые продукты из полости реза.
При кислородной резке происходит химическая реакция сгорания железа в кислороде.
Железо и сталь не загораются, как известно в кислороде при низких температурах, поэтому кислород хранят в стальных баллонах. Температура начала горения металла зависти от его химического состава и равна 1000-1200. Температура начала горения повышается с увеличением содержания углерода в металле при одновременном понижении температуры его плавлении. Высококачественная кислородная резка металла возможна лишь в том случае, если он горит в твёрдом состоянии. Если же металл загорается лишь при расплавлении, то в процессе резки он вытекает из полости реза и рез получается широким и неравномерным. 2.2. Подготовка металла под резку.
При выполнении кислородной резки необходимо учитывать требования, предъявляемые к точности резки и качеству поверхности газа. Большое влияние на качество реза и производительность резки оказывает подготовка металла под резку. Перед началом резки листы подаются на рабочее место и укладываются на подкладки так, чтобы обеспечить беспрепятственное удаление шлаков из зоны реза. Зазор между полом и нижним листом должен быть не менее 100–150 мм.
Поверхность металла перед резкой должна быть очищена. На практике окалину, ржавчину, краску и другие загрязнения удаляют с поверхности металла нагревом зоны резки газовым пламенем с последующей зачисткой стальной щеткой.
Разметку вырезаемых деталей производят металлической линейкой, чертилкой и мелом. Часто разрезаемый лист подают к рабочему месту резчика уже размеченным. Перед началом резки газорезчик должен установить необходимое давление газов на ацетиленовом и кислородном редукторах, подобрать нужные номера наружного и внутреннего мундштуков в зависимости от вида и толщины разрезаемого металла.
studfiles.net
3.2. Техника резки
Техника ручной кислородной резки листов
Подготовка поверхности разрезаемого металла
Перед резкой поверхность разрезаемого металла по линии реза должна быть очищена от окалины, ржавчины, краски и грязи. Очистку можно производить щетками, пламенем резака, пескоструйной обработкой. При резке должен быть обеспечен свободный выход струи искр и шлака. С этой целью свободное пространство под разрезаемой деталью должно составлять не менее половины толщины металла плюс 100 мм. Отсутствие свободного пространства может привести к прерыванию процесса резки и обратному удару.
Начало резки
Резку металла обычно начинают с края детали. Подогревающее пламя направляют на край детали и нагревают его до температуры горения, после чего подается режущий кислород. При резке листовой стали резак в начальной точке резки устанавливают практически вертикально к поверхности листа. Для ускорения прогрева металла большой толщины рекомендуется делать зарубку зубилом в начальной точке реза. В ряде случаев при резке листов необходимо начинать резку не с края листа, а внутри контура листа. В этом случае необходимо производить операцию пробивки отверстия. С помощью ручной кислородной резки можно выполнять пробивку отверстий в листах толщиной до 100 мм. При большей толщине для пробивки отверстий применяются другие методы. При небольшой толщине (менее 20 мм) пробивку отверстия можно производить неподвижным резаком. С этой целью после подогрева металла до температуры горения плавно производят пуск режущего кислорода и немного поднимают резак для предотвращения попадания брызг на резак до момента окончания пробивки. При большей толщине после нагрева места пробивки плавно включают режущий кислород и одновременно начинают перемещение резака. В этом случае кислородная струя постепенно углубляется в металл.
Расстояние от режущего наконечника до металла
Для обеспечения качества реза и стабильности процесса резки расстояние от наконечника до металла необходимо поддерживать постоянным. При ручной резке этого можно добиться использованием специальных тележек, прикрепляемых к головке резака и другими способами. При резке листов менее 100 мм расстояние от наконечника до поверхности металла должно быть на расстоянии 2 – 3 мм от конца ядра. При большей толщине металла для избежания перегрева резака расстояние необходимо увеличить на 30 – 40%.
Рис. 31. Схема перемещения резака в процессе резки:
1. В начале реза; 2. В процессе резки; 3. В конце резки (3)
При резки со скосом кромки поверхности реза получаются не одинаковые по качеству. Поверхность б всегда лучше, чем поверхность а. Острый угол на поверхности а оплавляется сильнее, так как на нем концентрируется большая часть подогревающего пламени. Тупой угол поверхности а (нижняя кромка) омывается жидким шлаком кислородной струей, вследствие чего также оплавляется. Поэтому лучше, если позволяет характер реза, располагать резак таким образом, чтобы была использована отрезанная часть с поверхностью б.
Рис. 32. Вид поверхностей при резке под углом (3)
www.e-ope.ee
Сущность процесса кислородной резки. Сварка
Сущность процесса кислородной резки
Кислородная резка (рис. 78) основана на свойстве металлов и их сплавов сгорать в струе технически чистого кислорода.

Рис. 78. Газокислородная резка:
1 – разрезаемый металл; 2 – струя режущего кислорода; 3 – горючая смесь; 4 – режущий мундштук; 5 – мундштук подогревающего пламени; 6 – подогревающее пламя; 7 – рез; 8 – шлаки
Резке поддаются металлы, удовлетворяющие следующим требованиям:
1. Температура плавления металла должна быть выше температуры воспламенения его в кислороде. Металл, не отвечающий этому требованию, плавится, а не сгорает. Например, низкоуглеродистая сталь имеет температуру плавления около 1500 °C, а воспламеняется в кислороде при температуре 1300–1350 °C. Увеличение содержания углерода в стали сопровождается понижением температуры плавления и повышением температуры воспламенения в кислороде. Поэтому резка стали с увеличением содержания углерода и примесей усложняется.
2. Температура плавления оксидов должна быть ниже температуры плавления самого металла, чтобы образующиеся оксиды легко выдувались и не препятствовали дальнейшему окислению и процессу резки. Например, при резке хромистых сталей образуются оксиды хрома с температурой плавления 2000 °C, а при резке алюминия – оксиды с температурой плавления около 2050 °C. Эти оксиды покрывают поверхность металла и препятствуют дальнейшему процессу резки.
3. Образующиеся при резке шлаки должны быть достаточно текучи и легко выдуваться из разреза. Тугоплавкие и вязкие шлаки будут препятствовать процессу резки.
4. Теплопроводность металла должна быть наименьшей, так как при высокой теплопроводности теплота, сообщаемая металлу, будет интенсивно отводиться от участка резки и подогреть металл до температуры воспламенения будет трудно.
5. Количество теплоты, выделяющейся при сгорании металла, должно быть возможно большим – она способствует нагреванию прилегающих участков металла и тем самым обеспечивает непрерывность процесса резки. Например, при резке низкоуглеродистой стали около 70 % общего количества теплоты выделяется от сгорания металла в струе кислорода и только 30 % составляет теплота от подогревающего пламени резака.
Различают два вида кислородной резки: разделительную и поверхностную.
Разделительная резка применяется для вырезки различного вида заготовок, раскроя листового металла, разделки кромок под сварку и других работ, связанных с разрезкой металла на части. Сущность процесса заключается в том, что металл вдоль линии разреза нагревают до температуры воспламенения его в кислороде, он сгорает в струе кислорода, а образующиеся оксиды выдуваются этой струей из места разреза.
Поверхностная резка (рис. 79) применяется для снятия поверхностного слоя металла, разделки каналов, удаления поверхностных дефектов и других работ. Резаки имеют большую длину и увеличенные сечения каналов для газов подогревающего пламени и режущего кислорода.

Рис. 79. Схема поверхностной резки:
1 – мундштук; 2 – шлак; 3 – канавка
Применяют два вида поверхностной резки – строжку и обточку. При строжке резак совершает возвратно-поступательное движение как строгальный резец. При обточке резак работает как токарный резец. Наклон мундштука резака к поверхности металла в начале реза составляет 70–80°. После начала горения угол наклона плавно уменьшают до 15–20°. Уменьшение угла наклона увеличивает ширину и уменьшает глубину строжки.
Поделитесь на страничкеСледующая глава >
info.wikireading.ru
Технология разделительной кислородной резки
При выполнении разделительной кислородной резки необходимо учитывать, какие требования предъявляются к точности резки и качеству поверхности вырезаемой детали. Чем ниже эти требования, тем меньше расходуется кислорода и горючего и тем большей может быть скорость резки.
Например, при разделочной резке (резка в лом) качество поверхности и точность резки не имеют значения. Поэтому резка ведется вручную при наибольшей возможной скорости.
При заготовительной резке (вырезается заготовка, из которой механической обработкой изготавливается деталь) качество реза также не имеет значения, но должен быть выдержан определенный размер заготовки при наименьших припусках на механическую обработку. Резка производится вручную. При этом часто применяются простейшие приспособления (опорные ролики, циркуль, направляющие тележки и т. п.), с помощью которых легче выдержать задаваемые припуски.
Резка под сварку должна осуществляться так, чтобы была чистая поверхность реза и были соблюдены заданные размеры детали. Требования повышаются, когда детали подготавливаются под автоматическую сварку. В этом случае применяется обычно механизированная резка.
Чистовая вырезка круглых и фасонных деталей, которые будут использованы без последующей механической обработки, производится только автоматами.
Таким образом, в зависимости от вида кислородной разделительной резки необходимо добиваться определенного качества реза.
Качество реза определяется следующими показателями.
Отклонением линии реза от намеченной (не получается прямолинейный рез, вместо окружности получился эллипс и т. д.). Это отклонение вызывается смещением резака или разрезаемого листа, деформацией листа в процессе резки.
Отклонением от заданного угла реза, которое наблюдается при изменении угла наклона резака, при изменении формы струи режущего кислорода или при неправильно выбранной скорости резки.
Степенью оплавления верхней кромки, которое происходит при излишней мощности подогревающего пламени или заниженной скорости резки.
Глубиной и искривлением бороздок на поверхности реза. Эти бороздки обычно имеют криволинейное очертание, что объясняется отставанием режущей струи кислорода. Отставание становится особенно заметным при слишком высокой скорости резки или при слишком низком давлении кислорода.
Глубина бороздок также зависит от скорости перемещения резака и давления кислорода. Образованию бороздок способствует неравномерная скорость передвижения резака и колебания его, а также засорение отверстия режущего мундштука.
Техника резки. Перед началом резки лист нужно уложить на подкладки, чтобы беспрепятственно удалялись шлаки из места реза. Зазор между полом и, нижней плоскостью листа должен быть не менее 100— 150 мм. Затем лист по предполагаемой линии реза необходимо очистить от окалины, ржавчины, краски и других загрязнений. При кислородной резке металла с загрязненной поверхностью резко ухудшается качество резки и уменьшается производительность.
Зачистка поверхности производится стальной щеткой. Для удаления окалины, краски и масла следует медленно провести по линии реза пламенем резака или горелки. Под действием тепла окалина отделится от поверхности металла, краска и масло сгорят. После этого поверхность зачищают стальной щеткой.
Разметка листа производится с помощью чертилки или мела. Перед началом резки газорезчик подбирает и устанавливает на резаке нужные для заданной толщины разрезаемого металла номера мундштуков, проверяет редукторы, водяной затвор, шланги, резак, вентили баллонов, присоединяет шланги и надежно их закрепляет на резаке и источнике газов.
Установив необходимое давление газов, производят зажигание резака и регулировку пламени. Состав, свойства и строение подогревательного пламени такие же, как и у сварочного.
Роль подогревательного пламени при разделительной кислородной резке различна в зависимости от толщины разрезаемой стали, условий резки и требований, предъявляемых к поверхности реза.
При резке стали толщиной до 80 мм на скорость резки главным образом влияет мощность подогревательного пламени: чем мощнее пламя, тем больше скорость. Количество тепла, выделяемое подогревательным пламенем, больше или равно количеству тепла, получаемого при сжигании металла во время резки. Однако увеличивать в значительной степени подогревательное пламя нельзя, так как начинают заметно оплавляться верхние кромки реза. Поэтому в данном случае выгоднее брать подогревающее пламя с избытком кислорода, при котором получается высокая концентрация тепла на поверхности нагреваемого листа.
При резке стали толщиной 80—300 мм наилучшее состояние поверхности обеспечивается при нормальном подогревательном пламени.
При резке стали толщиной свыше 300 мм количество тепла, выделяемое подогревательным пламенем, значительно меньше количества тепла, получаемого при сгорании металла в месте реза. В этом случае следует брать подогревательное пламя с избытком ацетилена.
При резке литья, покрытого окисленной коркой и песком, а также при резке проката с окалиной и ржавчиной на поверхности необходимо более мощное пламя с избытком кислорода для быстрого удаления (оплавления) поверхностного слоя и доведения чистого металла до температуры воспламенения, чем при резке проката с чистой поверхностью.
Окончательную регулировку пламени необходимо вести при открытом вентиле режущего кислорода. В противном случае вследствие того, что режущий и подогревательный кислород поступает в резак по одному шлангу, при пуске режущего кислорода во время резки пламя будет обедняться кислородом.
При пуске режущей струи кислорода подогревательное пламя не должно гаснуть или изменяться по форме и размерам.
Мощность подогревательного пламени выбирают в зависимости от толщины разрезаемого металла, скорости резки и состава стали. Требуемая для подогрева мощность увеличивается при увеличении содержания в стали углерода и специальных примесей.
Практически при резке листовой стали ядро пламени отстоит от поверхности металла на 1,5—2,5 мм. Расстояние от мундштука до металла в процессе резки следует поддерживать постоянным.
Давление режущего кислорода также имеет большое значение при резке. При слишком большом давлении увеличивается расход, кислорода и разрез получается менее чистым. При недостаточном давлении шлаки не будут выдуваться и резка будет происходить не на всю толщину металла.
Процесс резки начинается с нагревания участка металла, расположенного в начале намечаемой линии разреза, до температуры, близкой к температуре плавления металла. Затем на нагретое место пускают струю режущего кислорода и начинают перемещать резак вдоль линии реза.
В некоторых случаях резку приходится начинать не с края поверхности. В этом случае необходимо в точке начала реза проделать отверстие диаметром, равным примерно ширине предполагаемого реза. При толщине металла до 50 мм это отверстие может быть вырезано ручным резаком. В этом случае поверхность листа подогревают при вертикальном положении горелки резака. После подогрева головку резака наклоняют и одновременно подают режущий кислород. В наклонном положении головка удерживается в течение времени, какое нужно для получения сквозного отверстия. Этот наклон головки резака необходим для того, чтобы предупредить засорение отверстия сопла подогревающего пламени шлаком. Признаком засорения являются, хлопки. С получением сквозного отверстия головке резака придают нормальное положение, и отверстие разделывается до нужных размеров.
При толщине металла 50—100 мм отверстие просверливается сверлом. При больших толщинах первоначальное отверстие в металле может прожигаться кислородным копьем.
При резке металла круглого сечения на поверхности в месте начала реза надо сделать насечку зубилом. В месте насечки края металла быстро нагреваются до температуры воспламенения и тем самым облегчается начало процесса резки.
В начале резки подогревательное пламя резака, направляемое на край разрезаемого металла, может составлять различные углы наклона к поверхности. При резке металла толщиной до 50 мм подогревательное пламя направляется вертикально. При резке более толстого металла подогревательное пламя резака устанавливается с наклоном к поверхности разрезаемого металла на угол 10—15° по ходу резака, что позволяет лучше прогреть кромки по всей толщине металла и облегчить начало процесса резки. Резку толстого металла часто начинают с нижней кромки, постепенно поднимая резак по торцу до верхней кромки, после чего производят резку на всю толщину.
Положение резака в процессе резки деталей малой толщины (до 5—6 мм) должно быть таким, чтобы режущая струя имела наклон в направлении, противоположном направлению резки, что искусственно увеличивает разрезаемую толщину, замедляет прогрев места реза и тем самым предупреждает оплавление кромок.
При резке деталей средней толщины (10—50 мм) резак обычно устанавливается перпендикулярно к поверхности разрезаемого металла. Однако при резке по прямой линии листовой стали толщиной до 30 мм резак следует располагать с наклоном на угол 20—30° в сторону, обратную движению. В этом случае скорость резки существенно повышается.
При резке металла большой толщины перпендикулярное направление режущей струи приводит к отставанию резки нижней кромки, и резка может прекратиться. Поэтому при резке деталей толщиной свыше 50 мм режущую струю следует направлять по ходу резки под углом 15—25° от вертикали для достижения полного срезания нижнего края листа. Наклоны резака возможны только при выполнении резки вручную или при прямолинейной резке резательными приборами. При резке по криволинейным контурам положение резака должно быть перпендикулярным к поверхности разрезаемого металла.
Движение резака должно быть равномерным. Скорость передвижения резака должна соответствовать скорости окисления металла. При движении резака с правильно установленной скоростью поток искр вылетает под прямым углом к разрезаемой поверхности, т. е. прямо вниз. При слишком большой скорости движения резака поток искр будет отставать, а при слишком медленном — опережать резак.
По окончании резки резак следует задержать на выходе и произвести разрез нижнего участка (если имеется значительное отставание).
При резке с предварительным подогревом, обычно применяющимся для сталей с повышенным содержанием углерода и специальных примесей, скорость резки увеличивается. Температура подогрева берется около 300°.
При резке профильной стали - уголка, швеллера, двутавра и других — нужно направлять струю режущего кислорода так, чтобы не повредить соседнюю полку или стенку.
При реже углового профиля лучше всего положить его на прокладку краями полок вниз, утлом вверх. Резку производить снизу без перерывов. По мере передвижения резака к вершине угла струю режущего кислорода необходимо наклонить в сторону начала реза, т. е. от второй полки, с тем чтобы ее не повредить. Такой же наклон придается головке резака , при резке швеллера,
При резке тавра или двутавра при приближении резака к средине полки его также следует наклонить струей наружу (от стенки) и в таком положении перерезать металл за средину полки. Далее, не прерывая резки, резак нужно установить перпендикулярно к полке.
При резке стальных заготовок круглого сечения положение резака в момент подогрева должно соответствовать позиции 7, а при резке — позиции 2.
Для повышения производительности и качества резки следует использовать простейшие приспособления: циркульное устройство и тележку, поставляемые заводом-изготовителем к каждому резаку, а также направляющие. Такие приспособления дают возможность избежать случайных колебаний резака относительно линии реза.
На рисунке приведены примеры вырезки кругов и отверстий при помощи циркуля и резки трубы с помощью специальной каретки.
При резке по окружности газорезчику приходится перемешаться вместе с резаком, что представляет большие неудобства.
В этих случаях лучше пользоваться циркулем с вращающейся головкой.
Циркуль имеет головку 3, внутри которой свободно вращается втулка 1. В последней крепится резак 6 винтом 2.При резке по окружности резчик остается на месте, шланги при этом не скручиваются, так как положение резака во время работы сохраняется в одном направлении, а вращается только головка циркуля вокруг центра 7.
В головке циркуля имеется гнездо с резьбой для крепления планки с опорным роликом.
Вращающаяся головка для резки по окружности позволяет укреплять резак на необходимой высоте. При резке ровных листов могут быть применены простейшие приспособления.
Однотипные фигурные детали могут вырезаться с помощью шаблона, устанавливаемого на разрезаемый лист. Постоянство расстояния между концом мундштука резака и поверхностью листа обеспечивается кольцом 2, укрепляемым на головке резака. Головка резака в процессе резки прижимается к краю шаблона.
При резке тавра или двутавра при приближении резака к средине полки его также следует наклонить струей наружу (от стенки) и в таком положении перерезать металл за средину полки. Далее, не прерывая резки, резак нужно установить перпендикулярно к полке.
Читайте также
Добавить комментарий
electrowelder.ru
Инструкционная карта 33 - Технология кислородной резки металлов

Категория:
Руководство газосварщика газорезчика

Учебно-производственные задания. I — разделительная ручная кислородная резка, II — поверхностная кислородная резка, III — машинная кислородная резка
Цель заданий: научиться выполнять ручную и машинную резку низкоуглеродистых сталей с применением в качестве горючего газа ацетилена и газов-заменителей ацетилена, уметь выбирать оптимальные параметры режима резки.
Организационные указания. Подготовить рабочие места для производства работ по кислородной резке, оснастив их оборудованием, приспособлениями и инструментом. Подготовить пластины из низкоуглеродистой стали толщиной 20—30 мм, обрезки уголков, швеллеров, двутавров, сваренные пластины с дефектами шва и корня шва.
I. Разделительная ручная кислородная резка
Резка пластин
1. Уложить пластину из низкоуглеродистой стали размером 200 X 200 X 20 мм на подставки так, чтобы расстояние от пола до разрезаемой пластины было не менее 100—150 мм.2. Нагреть подогревающим пламенем резака поверхность металла вдоль предполагаемой линии реза.3. Зачистить металлической щеткой прогретую поверхность от окалины, отделившейся от металла в результате нагрева пламенем.4. Разметить предполагаемую линию реза мелом.5. Установить необходимые номера наружного и внутреннего мундштуков в зависимости от толщины разрезаемого металла (20 мм).6. Установить давление газов на ацетиленовом и кислородном редукторах в зависимости от выбранных мундштуков и толщины разрезаемого металла.7. Выполнить разделительную резку.7.1. Зажечь и отрегулировать до нормального подогревающее пламя.7.2. Установить мундштук резака на расстоянии 3— мм от разрезаемого металла под углом 90° или с небольшим наклоном (5—10°) в сторону, обратную направлению резки 7.3. Подогреть поверхность торца пластины до температуры, близкой к температуре плавления, при резке низкоуглеродистой стали — до температуры 1350— 1360 °С.7.4. По истечении 5—10 с открыть вентиль режущего кислорода и начать процесс резки перемещением резака вдоль линии реза.7.5. После прорезания пластины на 15—20 мм установить угол наклона 20—30 °С.7.6. В процессе резки резак перемещать равномерно с постоянной скоростью; резку выполнять на оптимальной скорости, на что указывает поток искр, вылетающих под углом 85—90° к разрезаемой поверхности; при слишком малой скорости резки поток искр вылетает в сторону, обратную перемещению резака, а при большой — под углом меньше 85°.7.7. По окончании резки закрыть вентиль режущего кислорода, затем вентиль горючего газа и подогревающего кислорода.
Подготовка кромок под сварку
1. Повторить п. 1—6.2. Подготовить кромки на металле толщиной 20 мм под V-образную разделку.2.1. Нагреть подогревающим пламенем резака поверхность торца размеченной пластины до температуры воспламенения металла в кислороде (для низкоуглеродистой стали — 1350—1360 °С). Угол наклона головки резака к изделию а поддерживать в пределах 45°.2.2. Подать на нагретый металл струю режущего кислорода и, как только металл прорежется на всю глубину, перемещать головку резака вдоль линии реза. Угол (3 между осью головки резака и поверхностью разрезаемого металла в начале процесса резки должен быть порядка 90°, в процессе резки — порядка 60—70°.2.3. Следует иметь в виду, что поверхности реза будут получаться неодинаковыми. Поверхность b всегда лучше, чем поверхность а. Оплавление металла сверху объясняется тем, что в этом месте концентрируется большее количество тепловой энергии подогревающего пламени, а скругление нижней кромки обусловлено действием жидкого шлака и кислородной струи, выходящей в сторону поверхности а. В связи с изложенным нужно стремиться к тому, чтобы в отходы шла обрезь с поверхностью а.
Вырезка отверстий на пластинах
1. Подобрать пластину из низкоуглеродистой стали размером 300 X 200 X 20 мм.2. Очистить поверхность от окалины и других загрязнений.3. Разметить мелом фигуры типа треугольника, квадрата, кольца.4. Наметить центры будущих отверстий, для обеспечения начала резки, а в фигуре типа кольца наметить еще и центр для установки ножки тележки.5. Просверлить отверстия сверлом диаметром 10— 12 мм.6. Расположить пластину на подставках для резки. Обеспечить свободное удаление продуктов резки.7. Подготовить пост газокислородной резки к работе.8. Зажечь подогревающее пламя резака и вырезать фигуры по разметочным линиям.8.1. Расположить пламя резака над кромкой отверстия перпендикулярно и на расстоянии 2—3 мм от ядра. Нагреть металл до температуры воспламенения его в кислороде.8.2. Открыть вентиль режущего кислорода и выполнить резку.8.3. Нагреть кромку отверстия, расположенную ближе к направлению резки, до требуемой температуры. Направить струю режущего кислорода на нагретую поверхность и вырезать прямоугольную фигуру.8.4. Установить на головку резака опорную тележку с циркулем, зажечь пламя, установить резак в исходное положение для вырезки кольца по внешнему контуру.8.5. Выполнить резку по внешнему контуру кольца. Оставить непрорезанным участок длиной 40—50 мм.8.6. Перевести резак в исходное положение над отверстием. Вырезать внутренний контур кольца по всему периметру. По окончании резки принять меры, исключающие перекос или падение головки резака, вследствие потери точки опоры циркулем и роликом, двигавшимся по металлу.8.7. Снять тележку с головки мундштука и вырезать кольцо.
Резка профильного металла
1. Выполнить резку уголка.1.1. Установить уголок 40 X 40 мм (60X60 мм) так, чтобы обеспечить расстояние под уголком 100— 150 мм для свободного выброса продуктов резки.1.2. Установить требуемую мощность подогревающего пламени.1.3. Осуществить резку так, как показано на рис. 4, а. Сначала прорезать одну полку снизу вверх, затем резак плавно развернуть, установить перпендикулярно второй полке и закончить резку. Последовательность резки можно изменить.2. Разрезать двутавровую балку.2.1. Начать резку следует с верхней точки одной из полок. Прорезать полку на всю длину и толщину. Для этого при подходе резака к стойке балки скорость резки уменьшить с целью прорезания стойки на некоторую величину I до точки А.2.2. Переместить резак в точку А и установить его перпендикулярно стойке двутавровой балки. Нагреть металл и прорезать стойку до точки Б.2.3. Установить резак в верхнюю точку второй полки и закончить резку.
Резка швеллера
1. Установить мундштук резака под углом к поверхности швеллера. Нагреть кромку и начать резку. 2. Выполнить резку в таком же порядке, но резак разместить снаружи контура швеллера.
Резка прутков квадратного профиля
1. Начать резку с угла. Головку резака установить под углом примерно 45° Нагреть металл до температуры воспламенения. Перевести головку резака в вертикальное положение. Начать резку.2. В конце резки наклонить головку резака на 5— 10° в сторону, противоположную направлению резки, с тем чтобы в первую очередь прорезать нижний угол.
Резка проката круглого профиля
1. Нагреть металл в верхней точке (зените) круга до температуры воспламенения. Перевести головку резака в положение, пустить струю режущего кислорода на нагретый участок металла.2. Осуществить разделительную резку, перемещая головку резака в положения 3—6. Расстояние мундштука от поверхности металла поддерживать постоянным.3. Выполнить резку по схеме.4. Производительность процесса кислородной резки повысится, если осуществлять резку нескольких прутков, расположенных друг за другом. Особенность процесса резки состоит в том, что в местах перехода на каждый последующий пруток нужно наклонять мундштук резака в сторону, обратную направлению резки.
Резка труб
1. Разметить трубу, используя металлическую гибкую линейку и мел. Опоясать трубу линейкой, провести разметочную линию мелом 2. Трубу расположить на роликовом стенде.3. На головке мундштука прикрепить каретку8. Вырезать канавки по линиям разметки. Заметить время нагрева металла до температуры воспламенения и время резки в каждом упражнении (привлечь товарища по группе с секундомером). После выполнения упражнений сравнить результаты и сделать соответствующие выводы.8.1. Вырезку канавки начать с нагрева выступающего металла, образованного зарубкой зубилом. Скорость выдержать нормальной, как и при резке канавки 2.8.2. Процесс резки по линии начать с нагрева плоской поверхности пластины. Резку вести на повышенной скорости.8.3. Процесс резки по линии начать с нагрева и расплавления конца присадочной низкоуглеродистой проволоки диаметром мм на поверхности металла, т. е. нанести в начале реза расплавленный металл проволоки и пустить струю режущего кислорода. Скорость резки уменьшить по сравнению со скоростью вырезки канавки 3.9. Снять поверхность металла на глубину 8—10 мм грубой и чистой поверхностной резкой.10. Вырезать дефектное место в корне шва на ранее сваренных образцах (толщина металла 10 мм).10.1. Отступить от дефекта на расстояние 10— 15 мм вправо . Вырезать канавку на глубину залегания дефекта. Резку закончить примерно на середине дефектного места.10.2. Начать резку в точке, отстоящей от дефектного места слева на 10—15 мм,и закончить вырезку дефекта, перемещая пламя резака слева направо.
Ill. Машинная кислородная резка
Резка листов под прямым углом
1. Расположить чистый лист из углеродистой стали толщиной 20 мм на подставках в горизонтальном положении.2. Подготовить к работе машину АСШ-70, состоящую из колонны, шарнирной рамы, копира, магнитной катушки, резаков или переносную машину «Микрон-2», «МГП-2».2.1. Проверить исправность машины внешним осмотром и пуском ее на холостом ходу.2.2. Установить копир на консоли машины.2.3. Установить параметры режима резки: давление кислорода и ацетилена, скорость резки, расстояние между торцом мундштука и поверхностью металла, расход ацетилена и кислорода.2.4. Зажечь подогревающее пламя и отрегулировать до нормального. Пустить струю режущего кислорода и убедиться в отсутствии нарушения формы подогревающего пламени.3. Вырезать деталь.3.1. Подвести резак к начальной точке реза и расположить его так, чтобы ось режущего канала мундштука находилась над точкой начала реза.3.2. Нагреть металл до появления ванночки расплавленного металла.3.3. Включить перемещение резака на пониженной скорости и режущий кислород пониженного давления, затем постепенно наращивать давление режущего кислорода до требуемого. Пламя при этом будет постепенно врезаться в металл, брызги будут выбрасываться струей кислорода вверх мимо торца мундштука (рис. 10) К моменту установления нормального давления режущего кислорода отверстие будет пробито (длительность прожигания отверстия составляет порядка 0,5 мин для данной толщины металла). После пробивки отверстия включить заданную скорость перемещения резака (300—340 мм/мин).3.4. По окончании вырезки детали перекрыть вентиль режущего кислорода и перевести резак в исходную точку для вырезки следующей детали. По окончании урока или при перерыве в работе более мин погасить пламя, закрыть все газовые вентили, отключить машину от электросети.
IV. Качество кислородной резки
1. Качество резки определяется точностью резки. Точность резки зависит от квалификации резчика при ручной резке и возрастает при резке на машинах с ручным электромагнитным, фотоэлектронным и программным управлением. Величина отклонений от заданного контура зависит также от длины, толщины, состояния поверхности листа, формы вырезаемой заготовки, установления правильной последовательности резки и др.2. Качество разделительной резки характеризуется отклонением поверхности реза от перпендикулярности и шириной реза. Неперпендикулярность можно снизить точным ведением резки без отклонений резака от вертикального положения.3. Качество поверхности реза оценивается следующими параметрами.3.1. Шероховатостью поверхности, т. е. количеством бороздок на единицу длины и глубиной бороздок, оставляемых режущей струей кислорода.3.2. Отклонением бороздок от прямолинейности в результате отставания Д от оси мундштука режущей струи кислорода.3.3. Оплавлением кромок.3.4. Наличием или отсутствием грата.
ГОСТ устанавливает три класса качества поверхности при машинной резке: 1-й класс — высший, 2-й класс — повышенный, 3-й класс — обычный. Для каждого класса установлены предельные допуски.
Читать далее:
Инструкционная карта 34 - Правила эксплуатации аппаратуры для кислородно-флюсовой резки
Статьи по теме:
pereosnastka.ru
Газовая резка металлов | Строительный справочник | материалы - конструкции
Под газопламенной резкой (чаще ее называют кислородной) понимают способ разделения металла по прямому или криволинейному контуру. Метод основан на использовании для нагрева смесь горючих газов с кислородом и экзотермической (с выделением тепла) реакции окисления металла. Суть кислородной резки заключается в сгорании железа в струе чистого кислорода, нагретом до температуры, близкой к плавлению. Для удаления оксидов железа из зоны реза используется кинетическая энергия режущего кислорода. Сам процесс резки включает в себя стадию подогрева металла ацетиленовым (или другим заменителем) пламенем и непосредственную резку струей режущего кислорода.
По характеру и направленности кислородной струи различают три основных вида резки: разделительная, при которой образуются сквозные резы, поверхностная, при которой снимают поверхностный слой металла, кислородное копье, заключающееся в прожигании в металле глубоких отверстий. Процесс кислородной резки представлен на рис.1. Металл 3 нагревается в начальной точке реза до температуры воспламенения (в кислороде для стали до 1000 - 1200°С) подогревающим ацетилено-кислородным пламенем 2, после «его направляется струя режущего кислорода 1 и металл начинает гореть с выделением значительного количества тепла.
Выделяемое тепло Q вместе с пламенем резака разогревают нижние слои металла на всю его толщину. Роль подогревающего пламени в процессе резки меняется в зависимости от толщины разрезаемого металла. Так, при толщине металла до 5 мм подогревающее пламя занимает до 80% в общем количестве тепла, участвующего в процессе резки.
С увеличением толщины металла роль подогревающего пламени в балансе температур падает, и при толщине 50 мм и более доля подогревающего пламени падает до 10%. В результате взаимодействия расплавленного металла с кислородом образуются оксиды железа 5, которые вместе с расплавленным металлом удаляются из зоны реза кинетической энергией струи кислорода 1.
Для обеспечения стабильности процесса и нормальной резки металла необходимо, чтобы в зоне реза выполнялись следующие условия:
- мощность источника тепла должна быть достаточной для нагрева металла до температуры, при которой происходит реакция сгорания металла;
- количество тепла, выделяемое при сгорании металла в струе кислорода, должно обеспечивать непрерывность процесса;
- реакция окисления металла должна происходить при температуре меньшей, чем требуется для плавления;
- температура плавления металла должна быть выше температуры образовавшихся оксидов. В противном случае пленка тугоплавких оксидов изолирует металл от кислорода;
- текучесть образовавшихся оксидов должна быть такой, чтобы они легко выдувались струей режущего кислорода;
- теплопроводность металла не должна быть высокой, иначе процесс резки может прерваться из-за интенсивного теплообмена.
Далеко не все металлы обладают свойствами, удовлетворяющими все эти условия, поэтому кислородная резка для некоторых из них становится невозможной. К примеру, большая теплопроводность меди не обеспечивает условий для нагрева до температуры реакции сгорания металла, что затрудняет начальный этап резки. Поэтому мощности газовых резаков недостаточно для разрезания меди, которую режут дуговой сваркой. Стали с большим содержанием хрома, магния и никеля, а также алюминий образуют тугоплавкую пленку оксидов, которая препятствует контакту металла с кислородом, что затрудняет кислородную резку.
Чугун, содержащий более 1,7% углерода, кислородной резкой не обрабатывается. Это. объясняется тем, что температура плавления чугуна ниже температуры плавления образующихся оксидов, поэтому металл удаляется из зоны реза без характерного окисления. Кроме того, образующиеся при нагреве оксиды имеют низкую текучесть и с трудом удаляются струей кислорода.
Лучше всего подходит для кислородной резки углеродистая сталь, которая удовлетворяет всем условиям, необходимым для поддержания непрерывности процесса. Влияние примесей в стали на процесс кислородной резки отражено таблице.
Влияние примесей стали на процесс кислородной резки
Элемент | Влияние на процесс резки |
Углерод | При содержании до 0, 4% процесс резки не гсудаается, при более высоком содержании ухудшается, а при содержании 1-1,25%- становится невозможным |
Марганец | Содержание до 0,4% на процесс резки заметно не ыгаяет. При более высоком содержании процесс резки затрудняется, а при 14% становится |
Кремний | Содержание в количестве, обычном для сталей отрицательного влияния на процесс резки не оказывает. При повышенном содержании процесс усложняется, а при содержании более 4% -становиться невозможным |
Фосфор и сера | В обычных количествах отрицательного влияния не оказывает |
Хром | Содержание до 4-5% отрицательного влияния на процесс резки не оказывает. При большем Содержании процесс резки становится невозможным и требует применения флюса. |
Никель | Содержание до 7-8% отрицательного влияния на процесс резки не оказывает. С увеличением содержания процесс резки услажняется. |
Молибден | Содержание до 0,25% отрицательного влияния на процесс резки не оказьвает. |
Вольфрам | Содержание до 10% отрицательного влияния на Процесс резки не оказывает. При более вьсоком содержании процесс резки затрудняется, а при 20% |
Ванадий | В обычных количествах отрицательного влияния не оказывает |
Медь | Содержание до 0,7% влияния на процесс резки не оказывает |
Алюминий | Содержание до 0,5 % влияния на процесс резки не оказавает |
![]() | ![]() |
Рис. 1. Кислородная резка: 1 — струя кислорода; 2 — подогревающее пламя; 3 — металл; 4 — зона реза; 5 — оксиды железа | Рис. 2. Резка по прямой линии |
Технология газокислородной резки
Технологию газокислородной резки рассмотрим на примере использования вставного резака. Установку для газокислородной резки готовят так же, как и для газовой сварки. Вставной резак присоединяют к стволам горелки и устанавливают рабочее давление кислорода и ацетилена, равное значениям, рекомендуемым для данного размера мундштука. Для зажигания факела полностью открывают вентили подачи кислорода и примерно наполовину — вентиль подачи ацетилена. Пламя устанавливают, вращая вентиль подачи кислорода на вставном резаке. Пламя проверяют, нажимая на секунду рычаг подачи кислорода, и при необходимости выполняют регулировку.
На разрезаемой детали мелом наносят линию реза и устанавливают ее на верстак, закрепив при необходимости струбцинами или другим доступным способом. Для удобства можно укрепить вдоль линии реза (на расстоянии примерно 6 мм) направляющий уголок (рис. 2). Прижав боковую сторону горелки к направляющему уголку, делают два — три медленных прохода вдоль линии реза. Для обеспечения устойчивости можно опереться предплечьем рабочий верстак. Металл в начале реза разогрева до ярко-красного цвета, затем, полностью открыв рычагом (или вентилем в другой конструкции) подачу кислорода и начинают медленно перемещать пламя резака вдоль нанесенной линии.
Криволинейные контуры или отверстия режут методике, показанной на рис. 3. Для удобства перемещения резака его устанавливают на лев руку. Для резки отверстий сначала намечают её контуры, а затем прожигают внутри отверстие, из которого проводят рез до контуров, обведенных линией. После этого продолжают резку окружности.
![]() | ![]() |
Рис. 3. Резка криволинейного контура | Рис. 4. УГПР — Установка кислородно-флюсовой резки. 1 — тележка; 2 — циклон; 3 — флюсопитатель; 4 — редуктор кислорода; 5 — резак; 6 — шланги |
Высококачественная скоростная резка достигается наклоном резака под острым углом и применением специальных мундштуков, у которых имеется три отверстия для режущего кислорода. Центры этих отверстий образуют равнобедренный треугольник, вершиной которого служит отверстие, предназначенное для основной режущей струи. Режущая струя осуществляет резку и проходит первой. Две вторые струи, перемещаясь вслед за основной, осуществляют зачистку образовавшихся кромок. К недостаткам этого вида резки относят большую ширину реза и невозможность прохода по криволинейным контурам.
Кислородно-флюсовую резку выполняют при резке легированных сталей. Для этого вместе с кислородом вводят порошкообразный флюс, при сгорании которого выделяется дополнительное тепло, что увеличивает температуру в зоне резки. В качестве флюса чаще всего используют железный порошок, которым заполняют специальный флюсопитатель, обеспечивающий подачу и регулировку расхода. Продукты сгорания флюса взаимодействуют с оксидами, образуя жидкотекучие шлаки, которые легко удаляются из зоны реза. Лучше всего подаются кислородно-флюсовой резке хромистые и хромоникелевые стали. Этим же методом можно резать и чугун. Резка сплавов на медной и алюминиевой основе затруднительна и требует последующей механической обработки. Для механизации работ по кислородно-флюсовой резке существует установка УГПР (рис. 4). Сама установка состоит из бачка флюсопитателя с редуктором ДКС-66, смонтированных на тележке, универсального резака Р2А-01 в блоке с узлом подачи флюса. Флюс подается кислородом. Применяемая марка флюса - ПЖ (железный порошок). При резке подобных сплавов выделяется большое количество вредных паров и газов, что может оказать отрицательное влияние на здоровье резчика. Поэтому рабочее место должно хорошо вентилироваться, а при больших объемах работ может применяться дополнительная защита органов дыхания респиратором. Поверхностная резка (рис. 5) позволяет снять с основного металла слой нужной толщины.
![]() | ![]() |
Рис. 5. Поверхностная резка: 1 — мундштук; 2 — шлак; 3 — канавка | Рис. 6. Прожигание бетона кислородным копьем: 1 — бетон; 2 — копье; 3 — защитный экран; 4 — ручка подачи и вращения копья; 5 — подача кислорода; 6 — подача воздуха с флюсом. |
Для этого мундштук резака направляют к поверхности под углом 15 — 40°. Металл, расположенный вперед кислородной струи, нагревается перемещающимся нагретым шлаком и выдувается из зоны реза. Струю режущего кислорода подают с меньшей скорость чем при разделительной резке, что обеспечивает сгорание лишь поверхностных слоев металл Подобной резкой можно снимать полностью слой ил вырезать канавки, нужные для технологических целей.
Резку кислородным копьем (рис.6) можно выполнять по металлу, бетону или железобетон. Для этого к рукоятке с вентилем для кислород подсоединяют тонкостенную стальную трубку наружным диаметром 20 — 35 мм и подают к месту реза. До начала реза трубку нагревают газовой горелкой или электрической дугой до температуры, при которой происходит воспламенение кислорода.
Затем по трубке к месту реза направляют кислород, который, воспламеняясь, образует копье. Кислородное копье с большим усилием прижимают к нужному месту, прожигая отверстие. В процессе прожигания копью придают возвратно-поступательное и вращательное движение. Образовавшиеся при этом шлаки выдуваются через зазоры, образованные между стенками отверстия и копьем.
build.novosibdom.ru