Газы, применяемые при сварке и резке. Газ используемый для сварки и резки металлов
Газы применяемые при сварке и резке металлов
Газы, применяемые для сварки и резки металлов
Газовая сварка, при которой происходит плавление кромок свариваемых деталей в высокотемпературном пламени газовой горелки (рис. 1) с дальнейшим формированием шва, имеет по сравнению со сваркой электродуговой как преимущества, так и недостатки. К первым относится тот факт, что при помощи данного метода можно сваривать практически любые материалы, более того, чугун, медь, латунь и свинец даже легче поддаются газовой сварке, чем дуговой. При этом отсутствует потребность в применении дорогого и сложного оборудования, а также в подключении к источнику электропитания. В то же время газовую сварку обычно применяют для обработки относительно тонких изделий, так как с увеличением толщины свариваемого металла в результате сравнительно медленного его прогрева пламенем и невысокой концентрации тепла резко падает ее производительность. Кроме того, стоимость газов, применяемых для создания высокотемпературного пламени, достаточно высока, поэтому эксплуатационные расходы в процессе газовой сварки часто оказываются выше, нежели для сварки электродуговой. Отметим, что при газовой сварке часто применяют присадочную проволоку, близкую по составу к свариваемому металлу, участвующую в образовании сварного соединения.
Рис. 1. Схема инжекторной горелки для газовой сварки: 1 — мундштук; 2 — сменный наконечник; 3 — смесительная камера; 4 — инжектор; 5 — кислородный вентиль; 6 — ацетиленовый вентиль
Температура пламени при газовой сварке должна быть не меньше чем в два раза выше температуры плавления свариваемого материала. Лучше всего удовлетворяет этому условию ацетилен — при сжигании его в кислороде образуется пламя с температурой порядка 3150 ˚С, что позволяет сваривать практически любую сталь.
При этом в зависимости от соотношения ацетилен-кислород горючая смесь может образовывать различные типы пламени, по-разному влияющие на процесс сварки.
Нормальное пламя, образуется при подаче 1,1-1,3 объема кислорода на один объем ацетилена. Этого недостаточно для полного окисления горючего газа - как следствие в пламени преобладает монооксид углерода(СО) и водород, выделившийся при разложении ацетилена. Последний защищает расплавленный металл шва от окисления. Окончательное сгорание смеси до углекислого газа и воды происходит за счет кислорода воздуха.
При подаче меньшего объема кислорода получается коптящее науглероживающее пламя — недоокисленный углерод переходит в расплавленный металл, ухудшая качество шва.
Впрочем, избыток кислорода пользы также не приносит. Образующееся при этом окислительное пламя, хотя и характеризуется повышенной температурой, однако сообразно со своим названием окисляет металл шва, снижая его прочностные свойства. Оказывается, что при большом избытке кислорода и должном давлении он вообще может полностью окислить металл, выдувая из рабочей зоны продукты его сгорания. На этом принципе основана технология газовой резки. При ней ацетиленовое пламя исполняет скорее вспомогательную роль, подогревая место разреза до температуры, при которой металл начинает сгорать в струе чистого кислорода, подающегося в зону резки параллельно с горючей смесью. Основная теплота при этом выделяется именно за счет окисления металла. Логическим продолжением данного метода является копьевая резка, которая применяется для разрезания низкоуглеродистой и легированной стали большой толщины. Более того, копьевая резка позволяет справиться и с железобетоном. Сущность метода заключается в прожигании отверстий стальной трубкой(копьем), по которой под большим давлением подается кислород, при этом необходимую для процесса теплоту получают окислением металла конца трубки(предварительно подогретого) и железа обрабатываемого изделия. Совершая копьем горизонтальные и вертикальные движения можно вырезать куски материала нужной формы.
Важнейшее значение для сварки и резки металлов имеет надлежащий выбор применяемых в этих процессах газов и способов их получения.
Кислород
Технический кислород различают по степени чистоты, так 1-ый сорт содержит не менее 99,7% (объемных) кислорода, 2-й — не менее 99,5%, 3-й — не менее 99,2%. Особенно большое значение чистота кислорода имеет для кислородной резки. С понижением содержания в нем газовых примесей увеличивается скорость реза, и уменьшается расход самого кислорода. Доставлять кислород к месту сварки можно как в баллонах, так и в жидком состоянии. В первом случае, полученный путем криогенной ректификации из воздуха кислород закачивается в баллоны под давлением в 150-165 атм. Второй метод, позволяющий уменьшить расходы на содержание и транспортировку баллонов, заключается в доставке жидкого кислорода прямо к месту сварки в специальных сосудах с хорошей теплоизоляцией с последующим его испарением. При этом из 1 дм3 жидкости получают 860 дм3 газообразного кислорода (при нормальных условиях).
Ацетилен
Ацетилен также можно либо получать в готовом виде на месте, либо везти его издалека в баллонах. В первом случае используются так называемые ацетиленовые генераторы, где его получают реакцией карбида кальция с водой. Теоретически одного килограмма чистого карбида достаточно для образования 350 дм3 ацетилена, на практике же выход горючего газа составляет не более 300 дм3/кг. Данный метод имеет определенные недостатки, связанные с хлопотностью хранения карбида кальция — он жадно поглощает воду из воздуха, образуя взрывоопасные ацетилен-воздушные смеси. Соответственно, загруженный в генератор кусок карбида должен быть полностью превращен в ацетилен, а полученный ацетилен — сожжен в горелке, во избежание проблем с безопасностью труда. Отбор данного газа из баллона не создает подобных трудностей. В то же время, сама технология баллонного хранения и перевозки ацетилена достаточно необычна, именно за счет его чрезвычайной взрывоопасности. Которая понижается при растворении ацетилена в ацетоне. В результате ацетиленовый баллон представляет собой наполненную пористой массой емкость. Пористая масса (например, активированный уголь) пропитана ацетоном, в ацетоне же растворяется ацетилен, закачиваемый в баллон под давлением 10-20 атм. При 10 атм. в стандартном 40-литровом баллоне помещается порядка 5 кг ацетилена, что эквивалентно 4,5 м3 газа при нормальных условиях. Отбор ацетилена из баллона нежелательно производить со скоростью выше 1,5 м3/ч, так как при более интенсивной откачке газа из емкости уносится и часть ацетона. Таким образом, при больших объемах потребляемого ацетилена имеет смысл использовать ацетиленовые генераторы, для не столь масштабных работ более подходящим решением является отбор газа из баллонов.
Ацетилен для закачки в баллоны получают как из карбида кальция, так и при пиролизе природного газа. Отметим, что контакт с оксидом меди резко снижает температуру воспламенения ацетилена, поэтому при изготовлении оборудования для работы с этим газом стараются избегать использования медьсодержащих деталей.
Заменители ацетилена
Дороговизна ацетилена зачастую вынуждает искать ему газы-заменители, ведущее место среди которых занимает пропан, или же пропан-бутановая смесь, обладающие высокой теплотворной способностью. Впрочем, для удовлетворительного сгорания пропана требуется примерно в три раза больше кислорода, чем для ацетилена, что делает выгодность его применения не столь однозначной. Самым же большим недостатком пропана является более низкая, нежели у ацетилена температура пламени, что существенно осложняет его применение для сварки сталей. Поэтому пропан чаще используют либо при сварке легко плавящихся цветных металлов, либо для создания подогревающего пламени при кислородной резке сталей.
Если все же пропановое пламя используют для сварки углеродистых сталей, то приходится применять сварочную проволоку, содержащую повышенную концентрацию кремния и марганца, использующихся в качестве раскислителей, что улучшает качество сварного соединения. Отметим, что большой коэффициент объемного расширения пропана (и бутана) накладывают ограничения на объем газа, который может быть безопасно закачан в баллон.
Аналогичные проблемы возникают и при использовании других заменителей ацетилена — водорода, коксового газа, бензина, керосина. Низкая температура пламени, поучаемая при сжигании данных веществ, затрудняет их применение при сварке сталей, однако позволяет использовать их в процессах резки, а также сварки и наплавки более легкоплавких металлов.
В общем, возможности выбора того или иного варианта состава горючей смеси, а также способов ее получения, для газовой сварки или резки достаточно широки, и всецело зависят от конкретной ситуации.
www.kriopass.com.ua
Какой газ применяется при сварке и резке металлов и сплавов?
Существует несколько видов сварки, отличающихся друг от друга методом получения сварочной ванны высокой температуры, предназначенной для резки или соединения различных металлов и сплавов: электрическая дуга, ультразвук, газовое пламя. Принцип действия заключается в том, что края конструкций подлежащих воссоединению, плавятся, и в месте их стыка образуется совершенно новая структурная единица – сварочный шов.
Сварочные газы
Показатель температуры зависит в первую очередь от того, какой газ используется при сварке. Например, в результате реакции воды с карбидом кальция, выделяется ацетилен, который взаимодействуя с кислородом, дает возможность получить температуру пламени более 3000 градусов. К сварочным газам относятся все разновидности пропанов, бутанов, МАФ (альтернатива ацетилену), бензолов, керосинов и прочих.
Присутствие кислорода, являющегося катализатором горения, обязательно в процессе применения любых сварочных газов. Подаваемый в горелку кислород, должен иметь высокое качество и чистоту. От этих показателей зависит максимальная температура, получаемая во время работы.
Элементы газовой смеси
Независимо от того, какой газ применяется при сварке, важно помнить, что получить высокую температуру горения и определенные свойства пламени, можно только при использовании в смеси технически чистого кислорода. От качества составляющей зависит полнота сгорания или испарения горючих элементов, а от количества – свойства, получаемые пламенем: восстановительные или окислительные.
Особые требования предъявляются к условиям хранения и подачи. Использование специальных отдельных баллонов необходимо в данном случае:
- технический кислород является мощным катализатором;
- многие газы, применяемые для сварки, очень токсичны.
Если применяется атмосферный кислород, то вряд ли удастся получить идеально ровные швы. При этом изменятся свойства металла, обретенные в процессе расплавления и соединения, что значительно снизит качество сделанного шва.
Считается не эффективным использование в сварочной газовой смеси обычного кислорода, содержащегося в атмосфере. Наличие примесей, существующих в воздухе, значительно уменьшает скорость сгорания элементов, что отражается на температуре пламени.
Сварочные газы
Независимо от того, какой газ используют при сварке, инертный или углекислый, следует помнить о соблюдении пропорций в смеси. Конкретный выбор зависит от металла. Например, в сварке стальных конструкций преобладает углекислый газ (около 18%), а при работе с нержавеющей сталью – аргон (почти 98%).
При сварке применяются инертные и активные газы. Инертные элементы, как правило, не ядовиты, не взаимодействуют с металлом и не растворяются в них.
- Аргон (Ar) – не имеет цвета и запаха, не горит, тяжелее воздуха в полтора раза. Различают два сорта. Высший сорт используется для сварки нагружаемых металлоконструкций из активных и редких металлов и сплавов. Первый сорт необходим для алюминиевых и стальных изделий.
- Гелий (He) – без цвета, запаха, легче воздуха. Различают два вида: высокой чистоты и технический элемент. Редкое использование гелия обусловлено его высокой стоимостью. Рекомендуется для чистых и активных металлов, алюминия и стали.
- Азот (N2) – не имеет цвета, запаха. Применяется для меди и медных сплавов. Бывает 4 сорта азота с разным содержанием вещества.
Газы активные служат защитой сварочной зоны от воздуха, вступают в химическое взаимодействие с металлами и растворяются в них.
- Кислород (О2) – не имеет цвета, запаха, вкуса. Кислород не горит, но является мощным катализатором, поддерживающим горение. Применяется в смесях с инертными или активными компонентами.
- Углекислый газ (СО2) обладает запахом и ярко выраженными окислительными свойствами. Отлично растворяется в воде и весит в 1,5 раза тяжелее воздуха. Различают 3 сорта вещества, которые используют для соединения чугунных, низко и среднеуглеродистых металлов и сплавов, низколегированных конструкций и коррозийных сталей. Следует помнить, что двуокись углерода в сварке не применяется.
Улучшают процесс и качество шва с помощью сварочных смесей. Наиболее востребованы смеси:
- гелий и аргон;
- аргон и кислород;
- углекислый газ и аргон;
- кислород и углекислый газ;
- аргон, углекислый газ, кислород.
Выбирая, какой газ для сварки подойдет в конкретном случае, необходимо учитывать несколько факторов: характеристики соединяемого металла, тип оборудования, желаемую форму шва, условия выполнения работы, свойства химического состава.
Газовая сварка стоит дороже электрической, потому что цена ацетилена и кислорода значительно выше стоимости электрической энергии, требуемой при контактной или дуговой сварке.
stroitel5.ru
Газы, применяемые для сварки и резки металлов - online presentation
ема: «Газы, применяемые для сварки и резки металлов. ель: изучение газов, применяемых для сварки и резки еталлов, что является неотъемлемой задачей моей рофессии. адачи: составить презентацию в которой максимально росто и удобно перечислены газы, применяемые ри сварке и резке металлов и их значение.главление: Газы, понятие-----------------------------------------------------3 Резка металлов------------------------------------------------4-5 Сварка металлов-------------------------------------------------6 Газы, применяемые в сварке и резке металлов—7-9 1. Кислород----------------------------------------------------------10 2. Ацетилен-------------------------------------------------------11-12 3. Заменители ацетилена---------------------------------------133. Газ (газообразное состояние) (от нидерл. gas, восходит к др.-греч. χάος) — одно из трёх агрегатных состояний вещества, характеризующееся очень слабыми связями между составляющими его частицами (молекулами, атомами или ионами), а также их большой подвижностью. Частицы газа почти свободно и хаотически движутся в промежутках между столкновениями, во время которых происходит резкое изменение характера их движения. Также термин «газ» можно определить как вещество, температура которого равна или превышает критическую точку, при такой температуре сжатие газа не приводит к образованию жидкости. В этом и заключается отличие газа от пара. При повышении давления насыщенный пар частично превращается в жидкость, газ - нет. Газообразное состояние вещества в условиях, когда возможно существование устойчивой жидкой или твёрдой фазы этого же вещества, обычно называется паром. Подобно жидкостям, газы обладают текучестью и сопротивляются деформации. В отличие от жидкостей, газы не имеют фиксированного объёма[1] и не образуют4. Что же такое сварка и резка металлов? Резкой металлов называют отделение частей (заготовок) от сортового, листового или литого металла. Различают механическую (ножницами, пилами, резцами), ударную (рубка) и термическую резку. Термической резкой называют обработку металла (вырезку заготовок, строжку, создание отверстий) посредством нагрева. Паз, образующийся между частями металла в результате резки, называют резом. По форме и характеру реза может быть разделительная и поверхностная резка, по шероховатости поверхности реза - заготовительная и чистовая. Термическая резка отличается от других видов высокой производительностью при относительно малых затратах энергии и возможностью получения заготовок любого, сколь угодно сложного, контура при большой толщине металла. Можно выделить три группы процессов термической резки: окислением, плавлением и плавлением-окислением. При резке окисление м металл в зоне резки нагревают до температуры его воспламенения в кислороде, затем сжигают его в струе кислорода, используя образующуюся теплоту для подогрева следующих участков металла. Продукты сгорания выдувают из реза струей кислорода и газов, образующихся при горении5. К резке окислением относятся газопламенная (кислородная) и кислородно-флюсовая резка. При резке плавлением металл в месте резки нагревают мощным концентрированным источником тепла выше температуры его плавления и выдувают расплавленный металл из реза с помощью силы давления дуговой плазмы,, реакции паров металла, электродинамических и других сил, возникающих при действии источника тепла, либо специальной струей газа. К способам этой группы относятся дуговая, воздушно-дуговая, сжатой дугой (плазменная), лазерная и термогазоструйная резка. При резке плавлением-окислением применяют одновременно оба процесса, на которых основаны две предыдущие группы способов резки. К способам этой группы относятся кислородно-дуговая, кислородноплазменная, кислородно-лазерная резка.6. Теперь перейдем к процессу сварки металлов. Сва́рка — процесс получения неразъёмных соединений посредством установления межатомных связей между свариваемыми частями при их местном или общем нагреве, пластическом деформировании или совместном действии того и другого[1]. Неразъёмное соединение, выполненное с помощью сварки, называют сварным соединением[1]. Чаще всего с помощью сварки соединяют детали из металлов. Однако сварку применяют и для неметаллов — пластмасс, керамики или их сочетания. При сварке используются различные источники энергии: электрическая дуга, электрический ток, газовое пламя, лазерное излучение, электронный луч, трение, ультразвук. Развитие технологий позволяет в настоящее время проводить сварку не только в условиях промышленных предприятий, но в полевых и монтажных условиях (в степи, в поле, в открытом море и т. п.), под водой и даже в космосе. Процесс сварки сопряжён с опасностью возгораний; поражений электрическим током; отравлений вредными газами; поражением глаз и других частей тела тепловым, ультрафиолетовым, инфракрасным излучением7. Ну что же, мы подошли к кульминации нашего вопроса. А именно, к самим газам, которые применяются для сварки и резки металлов. Газовая сварка, при которой происходит плавление кромок свариваемых деталей в высокотемпературном пламени газовой горелки (рис. 1) с дальнейшим формированием шва, имеет по сравнению со сваркой электродуговой как преимущества, так и недостатки. К первым относится тот факт, что при помощи данного метода можно сваривать практически любые материалы, более того, чугун, медь, латунь и свинец даже легче поддаются газовой сварке, чем дуговой. При этом отсутствует потребность в применении дорогого и сложного оборудования, а также в подключении к источнику электропитания. В то же время газовую сварку обычно применяют для обработки относительно тонких изделий, так как с увеличением толщины свариваемого металла в результате сравнительно медленного его прогрева пламенем и невысокой концентрации тепла резко падает ее производительность. Кроме того, стоимость газов, применяемых для создания высокотемпературного пламени, достаточно высока, поэтому эксплуатационные расходы в процессе газовой сварки часто оказываются выше, нежели для8. Температура пламени при газовой сварке должна быть не меньше чем в два раза выше температуры плавления свариваемого материала. Лучше всего удовлетворяет этому условию ацетилен — при сжигании его в кислороде образуется пламя с температурой порядка 3150 ˚С, что позволяет сваривать практически любую сталь. При этом в зависимости от соотношения ацетилен-кислород горючая смесь может образовывать различные типы пламени, по-разному влияющие на процесс сварки. Нормальное пламя, образуется при подаче 1,1-1,3 объема кислорода на один объем ацетилена. Этого недостаточно для полного окисления горючего газа - как следствие в пламени преобладает монооксид углерода(СО) и водород, выделившийся при разложении ацетилена. Последний защищает расплавленный металл шва от окисления. Окончательное сгорание смеси до углекислого газа и воды происходит за счет кислорода воздуха. При подаче меньшего объема кислорода получается коптящее науглероживающее пламя — недоокисленный углерод9. Впрочем, избыток кислорода пользы также не приносит. Образующееся при этом окислительное пламя, хотя и характеризуется повышенной температурой, однако сообразно со своим названием окисляет металл шва, снижая его прочностные свойства. Оказывается, что при большом избытке кислорода и должном давлении он вообще может полностью окислить металл, выдувая из рабочей зоны продукты его сгорания. На этом принципе основана технология газовой резки. При ней ацетиленовое пламя исполняет скорее вспомогательную роль, подогревая место разреза до температуры, при которой металл начинает сгорать в струе чистого кислорода, подающегося в зону резки параллельно с горючей смесью. Основная теплота при этом выделяется именно за счет окисления металла. Логическим продолжением данного метода является копьевая резка, которая применяется для разрезания низкоуглеродистой и легированной стали большой толщины. Более того, копьевая резка позволяет справиться и с железобетоном. Сущность метода заключается в прожигании отверстий стальной трубкой(копьем), по которой под большим давлением подается кислород, при этом необходимую для процесса теплоту получают окислением10. Теперь перейдем непосредственно к газам, которые Участвуют при сварке и резке металлов, первый газ — кислород Технический кислород различают по степени чистоты, так 1-ый сорт содержит не менее 99,7% (объемных) кислорода, 2-й — не менее 99,5%, 3-й — не менее 99,2%. Особенно большое значение чистота кислорода имеет для кислородной резки. С понижением содержания в нем газовых примесей увеличивается скорость реза, и уменьшается расход самого кислорода. Доставлять кислород к месту сварки можно как в баллонах, так и в жидком состоянии. В первом случае, полученный путем криогенной ректификации из воздуха кислород закачивается в баллоны под давлением в 150-165 атм. Второй метод, позволяющий уменьшить расходы на содержание и транспортировку баллонов, заключается в доставке жидкого кислорода прямо к месту сварки в специальных сосудах с хорошей теплоизоляцией с последующим его испарением. При этом из 1 дм3 жидкости получают 860 дм3 газообразного кислорода (при нормальных условиях).11. Ацетилен Ацетилен также можно либо получать в готовом виде на месте, либо везти его издалека в баллонах. В первом случае используются так называемые ацетиленовые генераторы, где его получают реакцией карбида кальция с водой. Теоретически одного килограмма чистого карбида достаточно для образования 350 дм3 ацетилена, на практике же выход горючего газа составляет не более 300 дм3/кг. Данный метод имеет определенные недостатки, связанные с хлопотностью хранения карбида кальция — он жадно поглощает воду из воздуха, образуя взрывоопасные ацетилен-воздушные смеси. Соответственно, загруженный в генератор кусок карбида должен быть полностью превращен в ацетилен, а полученный ацетилен — сожжен в горелке, во избежание проблем с безопасностью труда. Отбор данного газа из баллона не создает подобных трудностей. В то же время, сама технология баллонного хранения и перевозки ацетилена достаточно необычна, именно за счет его чрезвычайной взрывоопасности. Которая понижается при растворении ацетилена в ацетоне. В результате ацетиленовый12. Ацетилен При 10 атм. в стандартном 40-литровом баллоне помещается порядка 5 кг ацетилена, что эквивалентно 4,5 м3 газа при нормальных условиях. Отбор ацетилена из баллона нежелательно производить со скоростью выше 1,5 м3/ч, так как при более интенсивной откачке газа из емкости уносится и часть ацетона. Таким образом, при больших объемах потребляемого ацетилена имеет смысл использовать ацетиленовые генераторы, для не столь масштабных работ более подходящим решением является отбор газа из баллонов. Ацетилен для закачки в баллоны получают как из карбида кальция, так и при пиролизе природного газа. Отметим, что контакт с оксидом меди резко снижает температуру воспламенения ацетилена, поэтому при изготовлении оборудования для работы с этим газом стараются избегать использования медьсодержащих деталей.13. Заменители ацетилена Дороговизна ацетилена зачастую вынуждает искать ему газызаменители, ведущее место среди которых занимает пропан, или же пропан-бутановая смесь, обладающие высокой теплотворной способностью. Впрочем, для удовлетворительного сгорания пропана требуется примерно в три раза больше кислорода, чем для ацетилена, что делает выгодность его применения не столь однозначной. Самым же большим недостатком пропана является более низкая, нежели у ацетилена температура пламени, что существенно осложняет его применение для сварки сталей. Поэтому пропан чаще используют либо при сварке легко плавящихся цветных металлов, либо для создания подогревающего пламени при кислородной резке сталей. Если все же пропановое пламя используют для сварки углеродистых сталей, то приходится применять сварочную проволоку, содержащую повышенную концентрацию кремния и марганца, использующихся в качестве раскислителей, что улучшает качество сварного соединения. Отметим, что большой коэффициент объемного расширения пропана (и бутана) накладывают ограничения на объем газа, который может быть
Газовая сварка и резка Газы, применяемые при сварке
Различают два вида газовой сварки: сварку плавлением и газопрессовую сварку.
В первом случае кромки свариваемых частей (основной металл) и присадочный металл расплавляют и образуют общую ванну, которая застывает швом.
Источником тепла для расплавления металла является сгорание горючего газа в струе кислорода.
Газы. В качестве горючих газов используют ацетилен, водород и другие газы. Чаще других применяют ацетилен, дающий наибольшую температуру пламени.
Кислород необходим для сжигания горючего газа. При промышленном использовании его получают из воздуха, который в жидком состоянии разлагают на кислород и азот.
Ацетилен (С2Н2) получают из карбида кальция (СаС2) в ацетиленовых генераторах. Из одного килограмма чистого карбида получают 250-300лацетилена.
Сварочное пламяслужит для расплавления металла, а также для восстановления, науглероживания или окисления ванны. В средней части пламени температура достигает 32000С. Получение пламени того или иного характера достигается изменением соотношения горючего газа и кислорода в смеси. Нормальное ацетиленовое пламя (С2Н2 : О2 = 1 :1) восстановительное. Оно применяется для сварки стали и цветных металлов.
Пламя с избытком ацетилена является науглероживающим. Оно применяется при сварке чугуна, так как за счет пламени пополняется углерод, выгорающий при сварке, и понижается температура плавления металла в шве.
Окислительное пламя применяется при сварке латуни для получения окисной пленки, уменьшающей испарение цинка.
Приемы газовой сварки и резки
При сварке горелку продвигают вдоль шва, причем соблюдают необходимый угол наклона горелки к свариваемой поверхности. Этот угол a(рис.80) колеблется от 200С (для сварки листов толщиной 1мм) до 800С (при толщине 15мм и выше).
Рис.80. Схема левой (а) и правой (б) газовой сварки: 1-шов;
2-разделка шва
Различают левую и правую сварку. При левой сварке горелку передвигают справа налево (рис.80,а) и пламя направляется на еще не сваренный участок шва. При правой сварке (рис.80,б) горелку передвигают слева направо и пламя направляется на сваренную часть шва. Конец проволоки погружен в расплавленный металл.
Правая сварка применяется для деталей толщиной - более 5 мм, левая - до 5мм. При правой сварке качество шва лучше вследствие более продолжительной защиты расплавленного и остывающего металла; однако на листах толщиной до 5ммлевая сварка оказывается производительнее, так как пламя подогревает впереди лежащие кромки.
Присадочный материалв виде прутков или проволоки продвигают в пламя горелки, он расплавляется и стекает в ванну, где смешивается с расплавленным основным металлом. Затвердевая металл образует сварной шов. Для сварки стали в качестве присадочного материала применяют стальную проволоку с содержанием до 0.18%С, а для легированных сплавов - проволоку, содержащую хром, марганец и другие легирующие элементы.
При сварке цветных металлов и сплавов применяют проволоку, близкую по своему химическому составу к основному металлу. Диаметр присадочной проволоки должен быть на 1-2 ммбольше половины толщины свариваемых листов.
Сварка чугунаприменяется для исправления дефектов литья. Она производится с подогревом свариваемых частей до 400-6000С. Подогрев нужен для предупреждения отбела и трещин вблизи сварочного шва, которые появляются вследствие больших местных напряжений, возникающих во время охлаждения. Для сварки чугуна с подогревом в качестве присадочного металла используют чугунные литые прутки диаметром 6-12ммс повышенным содержанием углерода (3-3.6%) и кремния (3-4.8%), а при сварке без подогрева - латунную проволоку с содержанием 37-40%Zn.
Газовую сварку применяют для соединения тонкостенных стальных деталей, а также деталей из цветных металлов и сплавов. В этих случаях газовая сварка превосходит по качеству электродуговую. Газовую сварку используют также при наплавке твердых сплавов.
Газопрессовая сварка. Свариваемые части нагревают сварочным пламенем до пластического состояния и прикладывают усилие , сдавливающее эти части. Она применяется для соединения встык преимущественно труб больших диаметров (до 1000мм). Стыки нагревают кольцевой многопламенной горелкой. Кроме сварки труб, этим способом пользуются для сварки рельсов, бурильного оборудования и инструментов.
Контроль сварки. Качество сварных швов проверяют внешним осмотром, рентгеноанализом, магнитным дефектоскопом, а также по выборочным образцам с определением макро- и микроструктуры и механических свойств.
Газовая резкав струе кислорода применима лишь для тех металлов, у которых температура воспламенения ниже температуры плавления: железа, стали с содержанием углерода до 0.7% и некоторых сортов легированной стали. Чугун, алюминий, а также медь и ее сплавы непосредственно струей кислорода не режутся, так как струя кислорода при плавлении быстро окисляет их, а при резке алюминия образуется тугоплавкая окись его. Для газовой резки этих металлов применяют порошковые флюсы, состоящие в основном из железа. Флюс сгорает в струе кислорода и повышает температуру в месте резки настолько, что образующиеся тугоплавкие окислы шлакуются с окислами железа и жидкий шлак выдувается струей.
Газовой резке поддаются детали большой толщины до 300 мм. Наряду с ацетиленом, резка которым производительнее, применяют водород или пары бензина.
studfiles.net
www.samsvar.ru
Газовая сварка и резка металла.
При газопламенной обработке металлов в качестве источника теплоты используется газовое пламя – пламя горючего газа, сжигаемого для этой цели в специальных горелках.
В качестве горючих газов используют ацетилен, водород, природные газы, нефтяной газ, пары бензина, керосина и др. Наиболее высокую температуру по сравнению с пламенем других газов имеет ацетиленокислородное пламя, поэтому оно нашло наибольшее применение.
Газовая сварка- это сварка плавлением, при которой металл в зоне соединения нагревается до расплавления газовым пламенем. При нагреве газовым пламенем кромки свариваемых заготовок расплавляются вместе с присадочным металлом,который может дополнительно вводиться в пламя горелки. После затвердевания жидкого металла образуется сварной шов.
К преимуществам газовой сварки относятся: простота способа, несложность оборудования, отсутствие источника электрической энергии.
К недостаткам газовой сварки относятся: меньшая производительность, сложность механизации, большая зона нагрева и более низкие механические свойства сварных соединений, чем при дуговой сварке.
Газовую сварку используют при изготовлении и ремонте изделий из тонколистовой стали толщиной 1-3 мм, сварке чугуна, алюминия, меди, латуни, наплавке твёрдых сплавов, исправлении дефектов литья и др.
В практике применяют два способа сварки - правый и левый. При правом способе сварку ведут слева на право, сварочное пламя направляют на сваренный участок шва, а присадочную проволоку перемещают вслед за горелкой. Так как при правом способе пламя направлено на сваренный шов, то обеспечивается лучшая защита сварочной ванны от кислорода и азота воздуха, большая глубина плавления, замедленное охлаждение металла шва в процессе кристаллизации. Теплота пламени рассеивается меньше, чем при левом способе, поэтому угол разделки кромок делается не 90 °, а 60-70°, что уменьшает количество наплавленного металла и коробление. При правом способе производительность на 20-25 %выше, а расход газов на 15-20 % меньше, чем при левом. Правый способ целесообразно применять при сварке металла толщиной боле 5 мм и металлов с большой теплопроводностью.
При левом способе сварку ведут справа налево, сварочное пламя направляют на ещё не сваренные кромки металла, а присадочную проволоку перемещают впереди пламени. При левом способе сварщик хорошо видит свариваемый металл, поэтому внешний вид шва лучше, чем при правом способе; предварительный подогрев кромок свариваемого металла обеспечивает хорошее перемешивание сварочной ванны. Благодаря этим свойствам левый способ наиболее распространён и применяется для сварки тонколистовых материалов и легкоплавких металлов.
Мощность сварочной горелки при правом способе выбирают из расчёта 120-150 дм^3/ч ацетилена, а при левом -100-130 дм^3/ч на 1 мм толщина свариваемого металла.
Диаметр присадочной проволоки выбирают в зависимости от толщины свариваемого металла и способа сварки. При правом способе сварки диаметр присадочной проволоки d=S/2 мм., но не более 6 мм, при левом d=S/2+1 мм, где S- толщина свариваемого металла, мм
Скорость нагрева регулируют изменением угла наклона aмундштука к поверхности свариваемого металла. Чем толще металл и больше его теплопроводность, тем больше угол наклона мундштука к поверхности свариваемого металла.
В процессе сварки газосварщик концом мундштука горелки совершает одновременно два движения: поперечное (перпендикулярно оси шва) и продольное (вдоль оси шва). Основным является продольное движение. Поперечное движение служит для равномерного прогрева кромок основного металла и получения шва необходимой ширины.
Газовой сваркой можно выполнять нижние, горизонтальные (на вертикальной плоскости), вертикальные и потолочные швы. Горизонтальные и потолочные швы обычно выполняют правым способом сварки, вертикальные снизу вверх - левым способом.
Кислородная резка — процесс сгорания металлов и их сплавов в струе технически чистого кислорода. Для этого металл вдоль линии предполагаемого разреза предварительно нагревают до температуры его воспламенения в кислороде. Таким образом, весь процесс можно подразделить на стадию подогрева ацетиленовым пламенем (или пламенем других газов) и стадию резки металла струей кислорода, во время которой происходит сгорание металла, а образовавшиеся оксиды выдуваются из участка разреза. Такая резка носит еще одно название — разделительная. Она предназначена для раскроя листов металла, разделки кромок под сварку, вырезки заготовок различной формы и других работ, связанных с разрезанием металла на части. Однако вышеописанную резку можно применять и для разделки канавок, удаления поверхностного слоя металла и устранения поверхностных дефектов. В этом случае резка будет называться поверхностной.
Такой инструмент, как кислородный резак, удобно совмещает все стадии резки и предназначен для правильного смешивания горючих газов или паров жидкости с кислородом, образования подогревающего пламени и подачи струи чистого кислорода в зону резки. Резаки классифицируют по принципу смешения газов (инжекторные и безынжекторные), по назначению (универсальные, вставные и специальные), по применению (для ручной и машинной резки) и по виду резки (для разделительной и поверхностной резки). Принцип действия горелки заключается в следующем. Ацетилен подается по шлангу к ниппелю 1, а кислород — к ниппелю 2. От ниппеля 2 кислород идет по двум направлениям. Одна часть кислорода, как и в обычных сварочных горелках, попадает в инжектор, а потом в смесительную камеру. В последней образуется горючая смесь кислорода с ацетиленом, который поступает через ниппель. Далее смесь идет по трубке, проходит через кольцевой зазор между наружным и внутренним мундштуками и образует подогревательное пламя. Остальная часть кислорода через трубки и продвигается к центральному отверстию внутреннего мундштука и создает струю режущего кислорода.
Кислородной резке поддаются только те металлы, которые удовлетворяют следующим главным требованиям. Температура плавления металла должна быть больше температуры воспламенения его в кислороде. В противном случае металл будет только плавиться, но не будет сгорать. Например, низкоуглеродистая сталь имеет температуру воспламенения в кислороде 1300-1350 °С, а температуру плавления — около 1500 °С. Однако повышение количества углерода в стали будет сопровождаться увеличением температуры воспламенения в кислороде и уменьшением температуры плавления. В связи с этим резка стали с повышенным содержанием углерода и примесей становится проблематичной.
Температура плавления металла должна быть выше температуры плавления оксидов. Данное требование необходимо для того, чтобы образующиеся при резке оксиды легко выдувались кислородом и не мешали дальнейшему окислению и резке. Например, при резке алюминия образуются оксиды с температурой плавления приблизительно 2050 °С, а при резке хромистых сталей — оксиды с температурой плавления около 2000 °С. Совершенно очевидно, что эти оксиды покрывают поверхность металла и прекращают тем самым дальнейший процесс резки.
Теплопроводность металла должна быть как можно меньшей, ибо при большой теплопроводности сообщаемая металлу теплота быстро уходит из зоны резки и подогреть такой металл до температуры воспламенения будет трудно.
Количество выделяющейся при сгорании металла теплоты должно быть достаточно большим, так как эта теплота нагревает пограничные с зоной резки участки металла и тем самым обеспечивает непрерывность процесса резки. Так, например, при резке низкоуглеродистой стали 65—70% суммарного количества теплоты выделяется от сгорания металла в струе кислорода, остальные 30-35% составляет теплота от подогревающего пламени резака.
Возникшие при резке шлаки должны быть достаточно текучими и без труда выдуваться из разреза. Вязкие и тугоплавкие шлаки будут серьезно затруднять процесс резки. Перед началом резки нужно тщательно очистить поверхность разрезаемого металла от ржавчины, окалины, грязи и краски. Для их удаления необходимо медленно провести пламенем резака по поверхности металла вдоль предполагаемой линии разреза. При этом окалина отстает от металла, а краска и масло выгорают. После этого следует зачистить металлическую поверхность щеткой.
Разные металлы в разной степени подвергаются кислородной резке. Низкоуглеродистые стали с содержанием углерода не более 0,3% режутся очень хорошо, тогда как среднеуглеродистые стали (с количеством углерода не выше 0,7%) режутся несколько хуже. Высокоуглеродистые стали режутся с большим трудом, а при содержании углерода свыше 1% резка неосуществима без добавки специальных флюсов. Высоколегированные стали газокислородной сварке не поддаются, для их резки нужно использовать плазменно-дуговую или кислородно-флюсовую резку, которой можно разрезать еще медь, латунь, бронзу. Для разделки алюминия и его сплавов применима плазменно-дуговая резка. Таким образом, после характеристики разрезаемости следует изучить особенности технологии резки разных металлов в зависимости от их толщины, вида разрезаемого профиля, химического состава и деформируемости в результате высокотемпературного воздействия.
Если толщина металла не достигает 300 мм, то достаточно нормального пламени. При толщине металла свыше 400 мм длину факела подогревающего пламени нужно увеличить за счет избытка притока ацетилена. Это позволит глубоко прогреть металл. Скорость резки играет большую роль в эффективности выполняемой работы. Скорость перемещения резака должна соответствовать скорости горения металла. Самым простым способом определения скорости будет являться характер выброса искр и шлака
Не нашли то, что искали? Воспользуйтесь поиском гугл на сайте:
zdamsam.ru
Газовая сварка и резка металлов. Технология газовой сварки. Оборудование для газовой сварки.
Газовая сварка – это вид сварочных работ, когда детали требуется нагреть до расплавленного состояния посредством высокотемпературного пламени. Такой способ широко применяется при создании конструкций на основе тонкой углеродистой стали, при ремонте изделий из чугуна, а также при необходимости заварки дефектов в разных изделиях, полученных литьем из цветных или черных металлов.
Cодержание статьи
Какие газы используются?
При газовой сварке используются горючие газы – природный, ацетилен, пары бензина, водород. Эти газы отличаются хорошим горением на воздухе, не развивая при этом высокой температуры, для сжигания достаточно и кислородной струи. Газовая сварка чаще всего ведется на основе ацетилена, который создается на основе воды и карбида кальция. Он горит при температуре в 3200-3400 градусов.
В чем особенности?
К преимуществам газовой сварки можно отнести следующее:
- Простую технологию.
- Отсутствие необходимости в источнике сварочного тока.
- Простоту оборудования, на основе которого выполняется газовая сварка.
С другой стороны, этот процесс не отличается высокой производительностью. Сварка выполняется только вручную, а механические и эксплуатационные свойства готовых изделий не всегда высокого качества.
Кислородный редуктор
При сварке кислород поступает из специального баллона – он окрашивается в голубой или синий цвет. Чтобы обеспечивалась нормальная работа, кислород должен поступать в горелку равномерно и при небольшом давлении. Именно для этих целей на баллонах есть редуктор – он регулирует подачу газа.
В таком случае к горелке подводятся рукава для газовой сварки – ацетиленовый и кислородный. Кислород подается в центральный канал, где струя больше разряжается, засасывает ацетилен, который попадает в горелку под небольшим давлением. Газы смешиваются в камере, после чего выходят наружу из наконечника.
Особенности технологии
При выполнении газовой сварки важно получить качественное соединение, поэтому большое внимание уделяется тщательной подготовке свариваемых кромок, выбору способа соединения металла, установке горелки в нужное положение и определению необходимых параметров мощности горелки.
Технология газовой сварки предполагает, что кромки должны тщательно очищаться от различных загрязнений. Скос выполняется с применением ручного или пневматического зубила, а иногда привлекаются специальные станки. Окалина и шлаки могут удаляться металлической щеткой. Прихватка кромок позволяет предотвратить изменение их положения во время сварки.
Способы сварки
Газовая сварка может вестись несколькими способами. Первый – это левая сварка, которая наиболее распространена. Она применяется при работе с тонкими и легкоплавкими металлами. Горелка перемещается справа налево, а присадочная проволока ведется впереди пламени, направленного на несваренный участок шва.
При правой сварке горелка ведется слева направо, а присадочная проволока перемещается за горелкой. При данном способе тепло пламени рассеивается в меньшей степени, поэтому и угол раскрытия шва – не 90 градусов, а меньше – 60-70.
Правую сварку целесообразно использовать для соединения металла, толщина которого – от 3 мм и выше, а также металлов с высоким уровнем теплопроводности. Рекомендуется использовать присадочную проволоку, диаметр которой равен половине толщины свариваемого металла.
Технология газовой сварки предполагает и процесс, который ведется сквозным валиком. В этом случае листы устанавливаются вертикально зазору – он по размеру равен половине толщины листа. С помощью горелки расплавляются кромки, чтобы образовалось круглое отверстие. Затем оно со всех сторон оплавляется, пока шов не будет сварен. Такой способ хорош тем, что свариваемые листы имеют плотный шов без пор и шлаковых включений.
Сварка ванночками хороша для сваривания стыков и углов соединения металлов, которые имеют толщину максимум 3 мм. Как только на шве образуется ванночка, в нее вводится конец присадочной проволоки, которая слегка расплавляется, затем конец проволоки перемещается на другой участок шва. Особенность такого подхода – в шве отличного качества, особенно если сваривались тонкие листы и трубы из стали (малоуглеродистой и низколегированной).
Газовая сварка и резка могут вестись на основе многослойной сварки. Этот способ имеет ряд особенностей:
- зона нагрева небольшая;
- нижележащие слои при наплавке последующих просто отжигаются;
- каждый шов можно проковать, прежде чем наложить на него следующий.
Это сказывается на улучшении качества шва. С другой стороны, такой способ отличается небольшой производительностью, требует высокого расхода газов по сравнению с однослойной сваркой, поэтому применяется он при необходимости создания ответственных и качественных изделий.
Особенности сварки различных швов
Для работы с горизонтальными швами используется правый способ, что дает возможность легко формировать шов, а сам металл ванны не стекает. Сварка вертикальных и наклонных швов ведется левым способом, а если толщина металла выше 5 мм, используется двойной валик. Сварка потолочных швов предполагает нагревание кромок, пока они не оплавятся, затем в ванну вводится присадочная проволока – ее конец быстро оплавляется. Сам процесс ведется правым способом.
Газосварочное оборудование
Газосварочное оборудование для газовой сварки – это широкий выбор приборов, позволяющих проводить ряд работ. Подобный тип сварки считается простым, и само оборудование довольно лаконичное и легкое в эксплуатации. В зависимости от типа горючего газосварочные устройства бывают пропано-кислородными или ацетилено-кислородными, бензино- или керосино-кислородными.
Чаще всего сварка выполняется на основе пропано-кислородной и ацетилено-кислородной сварки, поскольку пламя этих газов имеет самую высокую температуру.
Газосварочное оборудование для газовой сварки – это еще и генератор, который дополняется разными видами газа. Также при работе потребуется баллон с кислородом и редукторы. Самыми распространенными считаются ацетиленовые генераторы для газовой сварки, которые позволяют получить непосредственно ацетилен путем смешивания карбида кальция и воды.
Данный тип генератора представлен в пяти типах, что позволяет подобрать оптимальный вариант для конкретного материала.
Важную роль при работе со сваркой играют предохранительные затворы, их задача – обеспечить безопасность при проведении сварки. С их помощью предотвращается прохождение обратного удара пламени, которое возникает во время сварки. Кроме того, благодаря обратным клапанам предотвращается обратный поток газа в резиновые рукава при газопламенной обработке металлов и работе со сжатыми газами.
Газовые баллоны
Оборудование для газовой сварки включает в себя баллоны и вентили для них. Баллон – это сосуд цилиндрической формы, который имеет отверстие с резьбой в горловине, куда ввинчивается запорный вентиль. Он создается из легированной или углеродистой стали, причем каждое такое изделие имеет свою окраску в зависимости от содержащегося в нем газа. Вентили для баллонов создаются из латуни, поскольку сталь отличается неустойчивостью к коррозии.
Редукторы: виды и особенности
Газовый редуктор представляет собой устройство, которое постоянно понижает или держит на определенном уровне давление газа. Газовая сварка и резка металлов ведутся на основе разных типов редукторов:
- Кислородные используются при газовой сварке и сварке металлов. Такой редуктор выполняется с голубой маркировкой. Может использоваться в агрессивной среде, поскольку создан из стойких к коррозии металлов.
- Ацетиленовые редукторы нашли широкое применение в газовой сварке. Они маркируются белым цветом, крепление к баллону выполняется накидным хомутом. Данный вид редуктора имеет два манометра, один из которых держит под контролем давление газа в баллоне, второй – давление газа в рабочей камере.
- Углекислотные редукторы широко применяются в промышленности – пищевой, химической. Они имеют один или два манометра и могут подключаться только к вертикальному манометру.
При аргонодуговой сварке нашли широкое применение аргоновые редукторы, которые могут работать и с негорючими газами.
Особенности газовых горелок
Газовая сварка сталей – процесс, требующий применения самых разных приборов. Газовые горелки – неотъемлемый элемент оборудования, которое используется в различных отраслях промышленности. По конструкции изделия примерно одинаковые: каждая горелка состоит из корпуса. К нему крепится сразу несколько элементов: наконечник, вентиль, регулирующий подачу топлива, и рычаг, который регулирует высоту пламени.
Соединение с баллоном выполняется редуктором, при этом сама горелка часто может дополняться пьезподжигом, ветрозащитой пламени и другими компонентами.
Газовая горелка для сварки на основе пропана отличается безопасностью работы, обеспечивая высокую температуру пламени: ее достаточно для выполнения целого ряда работ. Многие виды сварки ведутся на основе ацетиленовых горелок, которые работают на смеси ацетилена и кислорода.
Виды газовых резаков
Газовые резаки бывают разного типа: ацетиленовыми, пропановыми и работающими на заменителях газа или жидком горючем. Конструкция изделий включает в себя рукоятку, ниппели, к которым крепятся газовые рукава, корпус, инжектор, смесительную камеру, трубку, головку газового резака и трубку с вентилем. Газовая сварка металлов и ее качество зависят от того, насколько хорошо подобран именно резак.
Суть его работы в следующем: из баллона кислород поступает в редуктор, рукав, после чего попадает в корпус – здесь резак разветвляется на два канала. Часть кислорода проходит через вентиль и направляется в инжектор. Отсюда газ выходит с большой скоростью, причем во время этого процесса подсасывается горючий газ. При соединении с кислородом он образует горючую смесь, которая направляется в пространство между мундштуками и сгорает.
Как следствие, появляется подогревающее пламя. Кислород, который направлялся по второму каналу, выходит в трубку, за счет чего образуется режущая струя. Именно он обрабатывает участок металла.
Особенности сварки труб
Сварка газовых труб производится в несколько этапов. Сначала подготавливается металл, то есть проводится разметка, режутся и собираются трубы. Из-за круглого сечения труб резка выполняется термическим резаком. Большая часть работ по сварке – это сборка деталей под нее, когда требуется учесть множество деталей – от серии изделий до их диаметра и других факторов.
Сборка выполняется сварочными прихватками, которые предотвращают возможное смещение отрезков труб, сказывающееся на появлении трещин при охлаждении.
Зажигается дуга. Это делается разными способами. Затем начинается плавление металлов – основного и электродного. Для качественного шва важно уделять внимание углу наклона электрода.
Технология газовой резки
Газокислородная резка ведется с использованием металлов и их сплавов, которые горят в струе технически чистого кислорода. Такой тип резки выполняется двумя способами – разделительно или поверхностно.
Первый способ позволяет вырезать заготовки, раскроить металл, разделать кромки шва под сварки. С помощью поверхностной резки снимается поверхностный металл, разделываются канавки, удаляются поверхностные дефекты. Такая процедура выполняется на основе специальных резаков.
Техника безопасности
Газовая сварка – процесс, требующий внимательного отношения. Опасные ситуации могут возникнуть в нескольких случаях:
- Сварку нельзя проводить рядом с огнеопасными и легковоспламеняющимися материалами (бензином, керосином, паклей, стружкой).
- Если сварка выполняется в замкнутом пространстве, рабочим следует периодически выходить на свежий воздух.
- Работы должны проводиться в хорошо проветриваемых помещениях.
- Если проводится газопламенная обработка металла, помещение должно вентилироваться, чтобы удалялись вредные газы.
- Резка и сварка проводятся на расстоянии до 10 м от перепускных рамп, ацетиленовых генераторов.
- Секции загрузочных коробок не должны переполняться карбидом.
- Корпус генератора постоянно должен быть наполнен нужным количеством воды.
- Запрещено работать с баллоном кислорода, давление которого ниже нормы.
- Пламя горелки направляется в сторону, противоположную источнику газопитания.
Сварочные работы должны производиться с максимальным соблюдением правил безопасности и с применением только качественного оборудования. Это позволит сделать процесс безопасным, а соединение металлов – надежным.
promsnabservisnk.ru
ГАЗОВАЯ СВАРКА И РЕЗКА МЕТАЛЛОВ — МегаЛекции
1. ЦЕЛЬ РАБОТЫ: изучить сущность газовой сварки и резки металлов, применяемое оборудование и материалы. Освоить технику газовой сварки и резки металлов.
2. КРАТКИЕ СВЕДЕНИЯ ИЗ ТЕОРИИ
Газовая сваркаявляетсяодной из разновидностей термической сварки, сущность которой заключается в расплавлении кромок свариваемых изделий и добавочно вводимого присадочного материала теплом горящей газовой смеси.
При газовой сварке заготовки 1 и присадочный материал 2 в виде прутка или проволоки расплавляют высокотемпературным пламенем 4 газовой горелки 3 (рисунок 1). Газовое пламя получают при сгорании горючих газов (чаще ацетилена) в атмосфере кислорода.
Рисунок 1 – Схема газовой сварки Рисунок 2 – Схема ацетиленового генератора комбинированного типа: 1 – отбор газа; 2 – бак с водой; 3 – газосборник; 4 – зарядник
Кислород, используемый для сварочных работ, поставляют к месту потребления в стальных баллонах под давлением 15 МПа.
Кислородные баллоны окрашивают в голубой цвет с черной надписью «Кислород».
Для снижения давления газа на выходе из баллона и поддержания постоянного рабочего давления применяют газовые редукторы. Кислородные редукторы понижают давление от 15 до 0,1 МПа, ацетиленовые – от 1,6 до 0,02 МПа. Редукторы, применяемые в сварочной технике, обычно имеют два манометра, один из которых измеряет давление газа до входа в редуктор, другой – на выходе из него.
В качестве горючих газов чаще всего используют ацетилен, т.к. он имеет бóльшую теплоту сгорания по сравнению с другими горючими газами и высокую температуру пламени (3200°С). Кроме ацетилена можно также применять природные газы, водород, пары бензина и керосина, нефтяные газы и др. Перечисленные горючие газы могут быть использованы главным образом для кислородной резки, не требующей высокой температуры пламени.
Ацетилен получают в специальных аппаратах – газогенераторах при взаимодействии воды с карбидом кальция:
СаС2 + 2Н2О ↔ Са(ОН)2 +С2Н2 + Q.
Существуют следующие типы и системы генераторов. По давлению вырабатываемого ацетилена - два типа генераторов: низкого давления (до 0,02 МПа) и среднего давления (0,02 ... 0,15 МПа). По способу применения - передвижные и стационарные. По способу взаимодействия карбида кальция с водой - три типа генераторов: система генераторов KB - карбид в воду; ВК - вода на карбид, с вариантами процессов: М - "мокрого" и С - "сухого"; К - контактный с вариантами процессов: ВВ - вытеснения воды и ПК - погружения карбида.
Количественное регулирование ацетилена осуществляют периодической дозировкой либо карбида кальция при постоянном объеме воды в зоне реакции (система «карбид на воду»), либо воды при загрузке всего карбида кальция (система «вода на карбид»). Широко применяют и комбинированную систему генераторов с дозировкой обоих реагирующих веществ.
Ацетиленовые генераторы (рисунок 2) независимо от системы имеют следующие основные элементы: зарядник, газосборник, предохранительные устройства против повышения давления в газосборнике и защиты генератора от обратных ударов пламени.
Наиболее распространенным ацетиленовым генератором является передвижной ацетиленовый генератор АСП-1,25-6 (выпускаемый в настоящее время) производительностью 1,25 м3/ч, рабочим давлением 0,01—0,07 МПа - контактного типа среднего давления прерывного действия - работает по системе ПК в сочетании с системой ВВ (рисунок 3).
Корпус 2 генератора состоит из газообразователя и промывателя, соединенных между собой переливной трубкой. В газообразователе происходит разложение карбида кальция с выделением ацетилена, в промывателе - охлаждение и отделение ацетилена от частиц извести. Вода в газообразователь заливается через горловину. При достижении переливной трубки 15 вода переливается по ней в промыватель, который заполняется до уровня контрольной пробки 13. Карбид кальция загружают в корзину 4, закрепляют поддон 10, устанавливают крышку с мембраной на горловину. Уплотнение крышки 8 с горловиной обеспечивается винтом 6 с помощью мембраны 5. Образующийся в газообразователе ацетилен по переливной трубке 15 поступает в промыватель, где, проходя через слой воды, охлаждается и промывается.
Рисунок 3 – Генератор ацетилена: а - общий вид; I - горловина;
II- газообразователь; III- вытеснитель; IV— промыватель;
б - генератор в разрезе
Из промывателя через вентиль 12 по шлангу ацетилен поступает в предохранительный затвор 1 и далее на потребление.
По мере повышения давления в газообразователе давление ацетилена на мембрану преодолевает сопротивление пружины 7, перемещая ее вверх, при этом корзина с карбидом кальция, связанная с мембраной, также перемещается вверх, уровень смоченного карбида уменьшается, выработка ацетилена ограничивается и возрастание давления прекращается. При снижении давления в газообразователе усилием пружины 7, корзина с карбидом кальция возвращается вниз и происходит замочка карбида кальция. Таким образом, процесс выработки ацетилена регулируется с помощью мембраны.
Одновременно по мере увеличения давления в газообразователе избыточное давление ацетилена перемещает воду в вытеснитель и корзина с карбидом кальция оказывается выше уровня воды, в результате чего реакция прекращается. По мере уменьшения давления вода вновь занимает прежний объем и вновь происходит замочка карбида кальция.
Давление ацетилена контролируется манометром 9. Слив ила из газообразователя и иловой воды из промывателя осуществляется соответственно через штуцеры 13 и 14. Предохранительный клапан 3 служит для сброса ацетилена при увеличении давления в генераторе выше допустимого. В месте присоединения клапана к корпусу установлена сетка для задержания частиц карбидного ила, окалины и др.
На пути следования газа от генератора к сварочной горелке устанавливают предохранительные водяные затворы, предотвращающие проникновение кислородно-ацетиленового пламени в ацетиленовый генератор при его обратном ударе. Обратный удар происходит при перегреве горелки и засорении сопла или центрального отверстия инжектора.
Ацетиленовые генераторы взрывоопасны и нуждаются в специальном обслуживании. При работе одного-двух сварочных постов и в полевых условиях целесообразно использовать баллонный ацетилен.
Ацетиленовые баллоны окрашивают в белый цвет и делают на них красной краской надпись «Ацетилен». Давление ацетилена в баллоне 1,5 МПа. В баллоне находятся пористая масса (активированный уголь) и ацетон. Растворение ацетилена в ацетоне позволяет поместить в малом объеме большое количество ацетилена. Растворенный в ацетоне ацетилен пропитывает пористую массу и становится безопасным.
Сварочные горелки используют для образования сварочного пламени. В промышленности наиболее распространена инжекторная горелка, так как она наиболее безопасна и работает на низком и среднем давлениях (рисунок 4). В инжекторной горелке кислород под давлением 0,1…0,4 МПа через регулировочный вентиль 6 подается к инжектору 5. Выходя с большой скоростью из узкого канала инжекторного конуса, кислород создает значительное разряжение в камере 4 и засасывает горючий газ, поступающий через вентиль 7 в ацетиленовые каналы 8 горелки и камеру смешения 3, где образуется горючая смесь. Затем горючая смесь поступает по наконечнику 2 к мундштуку 1, на выходе из которого при сгорании образуется газосварочное пламя.
Рисунок 4 – Схема газовой горелки Рисунок 5 – Газосварочное пламя
Сварочное пламя образуется в результате сгорания ацетилена, смешивающегося в определенных пропорциях с кислородом в сварочных горелках. Ацетилено-кислородное пламя состоит из трех зон (рисунок 5): ядра пламени 1, средней зоны 2 (сварочной), факела пламени 3 (l – длина). В зоне 1 происходит постепенный нагрев до температуры воспламенения газовой смеси, поступающей из мундштука; в зоне 2 – первая стадия горения ацетилена за счет кислорода, поступающего из баллона. Эта зона имеет самую высокую температуру и обладающая восстановительными свойствами, называется сварочной, или рабочей, зоной. В зоне 3 (факеле) протекает вторая стадия горения ацетилена за счет атмосферного кислорода. Зона 3 обладает окислительными свойствами.
В зависимости от соотношения ацетилена и кислорода различают следующие виды пламени: нормальное, окислительное и науглероживающее.
Сварочное пламя называется нормальным, когда соотношение O2/C2h3 ≈ 1,1. Ядро нормального пламени имеет четкое очертание и яркое свечение. Такое пламя способствует получению качественного сварного шва. Нормальным пламенем сваривают большинство сталей.
При увеличении содержания кислорода (O2/C2h3 > 1,1) пламя приобретает голубоватый оттенок и имеет заостренную форму ядра. Такое пламя называется окислительным и может быть использовано только при сварке латуни.
При увеличении содержания ацетилена (O2/C2h3 < 1,1) пламя становится коптящим, удлиняется и имеет красноватый оттенок. Такое пламя называют науглероживающим и применяется для сварки чугуна и цветных металлов.
Применение. Газовой сваркой можно сваривать почти все металлы, используемые в технике, причем такие металлы и сплавы, как чугун, медь, свинец, латунь, легче поддаются газовой сварке, чем дуговой.
К преимуществам газовой сварки относится и то, что она не требует сложного оборудования и источника электрической энергии. В настоящее время газовая сварка широко применяется при монтаже металлоконструкций и трубопроводов из тонкостенных труб, сантехнических работах, сварке сплавов на основе меди, ремонтной сварке изделий из чугуна.
Резка металлов заключается в разделении металлических заготовок и конструкций.
Наиболее распространена кислородная резка металлов, сущность которой заключается в сжигании металла в струе кислорода и удалении этой струей образующихся оксидов. При горении железа в кислороде образуется оксид железа и значительное количество теплоты:
3Fe + 2O2 = Fe3O4 + Q.
Для начала горения металл подогревают до температуры его воспламенения в кислороде (например, сталь до 1000…1200°С). На рисунке 6 показан процесс кислородной резки. Металл 3 (заготовка) нагревается в начальной точке реза подогревающим пламенем 2, затем направляется струя режущего кислорода 1, и нагретый металл начинает гореть. Горение металла сопровождается выделением теплоты, которая вместе с подогревающим пламенем разогревает лежащие ниже слои на всю толщину металла. Образующиеся оксиды 5 расплавляются и выдуваются струей режущего кислорода из зоны реза 4. Конфигурация перемещения струи соответствует заданной форме вырезаемого изделия.
Рисунок 6 – Схема кислородной резки Рисунок 7 – Схема газокислородного
резака
По характеру и направленности кислородной струи различают несколько способов резки.
При разделительной резке режущая струя направлена нормально к поверхности металла и прорезает его на всю толщину. Разделительной резкой раскраивают листовую сталь, разрезают профильный материал, вырезают косынки, круги, фланцы и т. п.
При поверхностной резке режущая струя направлена под очень малым углом к поверхности металла (почти параллельно ей) и обеспечивает грубую его строжку или обдирку. Ею удаляют поверхностные дефекты отливок.
При резке кислородным копьем копье образуется тонкостенной стальной трубкой, присоединенной к рукоятке и свободным концом прижатой к прожигаемому металлу. Резка начинается с подогрева конца трубки сварочной дугой или горелкой. При пропускании кислорода через трубку (копье) ее конец быстро загорается и дальнейший подогрев не нужен. Копье прижимают к металлу и углубляют в него. Таким образом, выжигают отверстия круглого сечения. Кислородным копьем отрезают прибыли крупных отливок, прожигают летки в металлургических печах, отверстия в бетоне и т. п.
Газокислородная резка может быть ручной и машинной. Для ручной резки применяют универсальный резак типа УР со сменными мундштуками (рисунок 7). В резаке конструктивно объединены подогревающая и режущая части. Подогревающая часть аналогична таковой у сварочных горелок. Режущая часть состоит из дополнительной трубки 4 для подачи режущего кислорода. В мундштуке находятся два концентрически расположенных отверстия для выхода подогревающего пламени 1 и режущей струи 2. Мундштук резака 3 образует прямой угол со стволом. При замене ацетилена другими горючими газами в резаке увеличивают сечения каналов инжектора и смесительной камеры.
Обычной кислородной резкой разрезают металлы, толщина которых 5...300 мм. При резке металла толщиной более 300 мм применяют специальные резаки.
Кроме рассмотренной выше кислородной резки существуют и другие способы резки металлов: кислородно-флюсовая, воздушно-дуговая, плазменно-дуговая и др.
3. ТЕХНИКА ГАЗОВОЙ СВАРКИ И РЕЗКИ МЕТАЛЛОВ
Техника газовой сварки.
Пост для газовой сварки (рисунок 8) состоит из переносного ацетиленового генератора с предохранительным затвором или баллона с горючим газом, баллона с кислородом, газовых редукторов, руковов и сварочной горелки со сменными наконечниками. Также применяются стационарные ацетиленовые генераторы, от которых ацетилен подается по ацетиленопроводу к сварочному посту.
![]() |
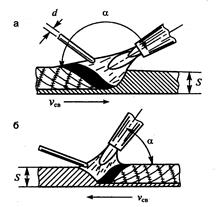
Рисунок 8 – Оборудование поста для Рисунок 9 – Способы газовой сварки: 1 – сварочная горелка; сварки: а – правый; б - левый
2 – кислородный редуктор; 3 – баллон
с кислородом; 4 – предохранительный
затвор; 5 - рукова
В практике применяют два способа сварки - правый и левый (рисунок 9) При правом способе (рисунок 9, а) сварку ведут слева на право, сварочное пламя направляют на сваренный участок шва, а присадочную проволоку перемещают вслед за горелкой. Т.к. при правом способе пламя направлено на сваренный шов, то обеспечивается лучшая защита сварочной ванны от кислорода и азота воздуха, большая глубина плавления, замедленное охлаждение металла шва в процессе кристаллизации. Теплота пламени рассеивается меньше, чем при левом способе, поэтому угол разделки кромок делается не 90 °, а 60-70°, что уменьшает количество наплавленного металла и коробление. Правый способ целесообразно применять при сварке металла толщиной более 5 мм и металлов с большой теплопроводностью.
При левом способе (рисунок 9, б) сварку ведут справа налево, сварочное пламя направляют на ещё не сваренные кромки металла, а присадочную проволоку перемещают впереди пламени. При левом способе сварщик хорошо видит свариваемый металл, поэтому внешний вид шва лучше, чем при правом способе; предварительный подогрев кромок свариваемого металла обеспечивает хорошее перемешивание сварочной ванны. Благодаря этим свойствам левый способ наиболее распространён и применяется для сварки тонколистовых материалов и легкоплавких металлов.
Мощность сварочной горелки при правом способе выбирают из расчёта 120-150 дм3/ч ацетилена, а при левом - 100-130 дм3/ч на 1 мм толщины свариваемого металла.
Диаметр присадочной проволоки выбирают в зависимости от толщины свариваемого металла и способа сварки. При правом способе сварки диаметр присадочной проволоки d = S/2 мм., но не более 6 мм, при левом d = S/2+1 мм, где S- толщина свариваемого металла, мм.
Скорость нагрева регулируют изменением угла наклона мундштука к поверхности свариваемого металла. Чем толще металл и больше его теплопроводность, тем больше угол наклона мундштука к поверхности свариваемого металла.
В процессе сварки газосварщик концом мундштука горелки совершает одновременно два движения: поперечное (перпендикулярно оси шва) и продольное (вдоль оси шва). Основным является продольное движение. Поперечное движение служит для равномерного прогрева кромок основного металла и получения шва необходимой ширины.
Газовой сваркой можно выполнять нижние, горизонтальные (на вертикальной плоскости), вертикальные и потолочные швы. Горизонтальные и потолочные швы обычно выполняют правым способом сварки, вертикальные снизу вверх – левым способом.
megalektsii.ru
Газы, применяемые при сварке и резке
Полуавтоматы для дуговой сварки и их основные узлы
Кислород при атмосферном давлении и обычной температуре - это газ без цвета и запаха, несколько тяжелее воздуха. При атмосферном давлении и температуре 20 ° С масса 1 м3 кислорода равна 1,33 кг. Сгорание горючих газов или паров горючих жидкостей в чистом кислороде происходит очень интенсивно, в зоне горения развивается высокая температура. Для получения сварочного пламени с высокой температурой, необходимой для расплавления металла в месте сварки, горючий газ или пары горючей жидкости сжигают в смеси с технически чистым кислородом. Если горение газов происходит на воздухе, в котором кислорода содержится только 1/5 по объему (остальные 4/5 составляют азот и другие атмосферные газы), то температура сварочного пламени будет значительно ниже и процесс горения происходит значительно медленнее, чем в технически чистом кислороде. Сам кислород не токсичен, не горюч и не взрывоопасен, однако, являясь сильнейшим окислителем, резко увеличивает способность других материалов к горению, а при очень высокой скорости горения - к взрыву. Технический кислород добывают из атмосферного воздуха, который подвергают обработке в воздухоразделительных установках, где он очищается от пыли, углекислоты и осушается от влаги. Перерабатываемый в установке воздух сжимается компрессором до высокого давления и охлаждается в теплообменниках до сжижения. Жидкий воздух разделяют на кислород и азот. Процесс разделения происходит вследствие того, что температура кипения жидкого азота жиже температуры жидкого кислорода на 13 °С. Азот оказывается более легкокипящим газом и испаряется первым, поэтому его отводят из воздухоразделительной установки в атмосферу. Жидкий чистый кислород накапливается в воздухоразделительном аппарате. При испарении кислорода им заполняют баллоны под давлением, создаваемым с помощью компрессора. Технический кислород транспортируют в стальных баллонах согласно требованиям существующих нормативных документов или в автореципиентах под давлением 15±0,5 МПа (150±5 кгс/см2) или 20±1,0 МПа (200 ±10 кгс/см2) при 20 °С. При наполнении баллонов, их хранении и транспортировании в интервале температур от —50 до +30 °С давление газа в баллоне должно соответствовать приведенному в табл. 49.
Таблица 49
Давление кислорода в баллоне в зависимости от температуры окружающего воздуха
Температура газа. СС | Давление газа в баллоне, МПа (кгсУсм2) | Допустимое отклонение. МПа (кгс см:) | Давление гава в баллоне. МПа (кгс см3) | Допустимое отклонение. МПа (кгс'см3) |
15 МПа (150 кгс/см5) арн 20 °С | 20 МПа (200 кгс см3) прн 20 "С | |||
-50 | 9.3 (93) | 12 3 (123) | ||
-Ц0 | 10.2 (102) | 13.5(135) | ||
-30 | 11,1 (111) | 14.6 (146) | ||
-20 | 11.9 (119) | 15.& (158) | ||
-10 | 12.7 (127) | = 0.5(5) | 16.9 (169) | =1,0(10) |
0 | 13.5(135) | 179 (179) | ||
- 10 | 14.3 (143) | 19.0(190) | ||
-20 | 15.0 (150) | 20.0 (200) | ||
-30 | 15.7(157) | 21.0 (210) |
Для сварки и резки выпускают технический кислород 1-го сорта чистотой не менее 99,7 % и 2-го сорта чистотой не менее 99,5 %. При хранении или транспортировке наполненных баллонов давление в них должно соответствовать температуре окружающего воздуха. Хранение и транспортировка наполненных баллонов при температуре выше 60 °С не допускается. Баллоны с кислородом должны возвращаться на
заполнение с остаточным давлением не ниже 0,05 МПа (0,5 кгс/ см2).
Ацетилен (С2Н2) является химическим соединением углерода с
«—V jr jr jr
водородом. Это бесцветный горючий газ, имеющий резкий характерный
запах. Длительное вдыхание ацетилена вызывает головокружение, тошноту, а иногда и сильное общее отравление. Aцетилен легче воздуха:
1 м3 ацетилена при 20 °С и атмосферном давлении имеет массу 1,09 кг Ацетилен является взрывоопасным газом. Температура
самовоспламенения ацетилена лежит в пределах 240—630 °С и зависит от давления и присутствия в ацетилене различных примесей. При
атмосферном давлении смесь ацетилена с воздухом взрывается при содержании в ней ацетилена 2,2 % и более, а в смеси с кислородом при содержании - 2,8 % и более. Взрыв ацетилено-воздушной или
ацетилено-кислородной смеси может произойти от искры, пламени или сильного местного нагрева, поэтому обращение с карбидом кальция и с ацетиленом требует осторожности и строгого соблюдения правил безопасного труда. В промышленности ацетилен получают при
разложении жидких горючих, таких как нефть, керосин, воздействием электродугового разряда. Применяется также способ производства ацетилена из природного газа (метана). Смесь метана с кислородом сжигают в специальных реакторах при температуре 1300—1500 °С. Из полученной смеси с помощью растворителя извлекается концентрированный ацетилен. Получение ацетилена промышленными способами на 30—40 % дешевле, чем из карбида кальция.
Промышленный ацетилен закачивается в баллоны, где находится в порах специальной массы растворенным в ацетоне. В таком виде потребители получают баллонный промышленный ацетилен. Свойства ацетилена не зависят от способа его получения. Остаточное давление в ацетиленовом баллоне при температуре 20 °С должно быть 0,05—0,1 МПа (0,5—1,0 кгс/см2). Рабочее давление в наполненном баллоне не должно превышать 1,9 МПа (19 кгс/см2) при 20 °С. Для сохранности наполнительной массы нельзя отбирать ацетилен из баллона со скоростью 1700 дм3/ч. Рассмотрим подробнее способ получения ацетилена в генераторе из карбида кальция. Карбид кальция получают путем сплавления кокса и негашеной извести в электрических дуговых печах при температуре 1900—2300 °С, при которой протекает реакция: СаО + 3С = СаС2 + СО. Расплавленный карбид кальция сливают из печи в формы-изложницы, где он остывает. Далее его дробят и сортируют на куски размером от 2 до 80 мм. Готовый карбид кальция упаковывают в герметически закрываемые барабаны или банки из кровельной жести по 40; 100; 130 кг. В карбиде кальция не должно быть более 3 % частиц размером менее 2 мм (пыль). По соответствующему стандарту устанавливаются размеры (грануляция) кусков карбида кальция: 2x8; 8x15;15x25;25x80 мм. При взаимодействии с водой карбид кальция выделяет газообразный ацетилен и образует в остатке гашеную известь, являющуюся отходом. Реакция разложения карбида кальция водой происходит по схеме:
Из 1 кг химически чистого карбида кальция теоретически можно получить 372 дм3 (литра) ацетилена. Практически из-за наличия примесей в карбиде кальция выход ацетилена составляет до 280 дм3 (литров). В среднем для получения 1000 дм3 (литров) ацетилена расходуется 4,3—4,5 кг карбида кальция. Карбидная пыль при смачивании водой разлагается почти мгновенно. Карбидную пыль нельзя применять в обычных ацетиленовых генераторах, рассчитанных для работы на кусковом карбиде кальция. Для разложения карбидной пыли применяются генераторы специальной конструкции. Для охлаждения ацетилена при разложении карбида кальция берут от 5 до 20 дм3 (литров) воды на 1 кг карбида кальция. Применяют также «сухой» способ разложения карбида кальция. На 1 кг мелко раздробленного карбида кальция в генератор подают 0,2—1 дм3 (литр) воды. В этом процессе гашения известь получается, не в виде жидкого известкового ила, а в виде сухой «пушонки», удаление, транспортировка и утилизация которой значительно упрощаются. При сварке и резке металлов можно применять также и другие горючие газы и пары горючих жидкостей. Для нагрева и расплавления металла при сварке необходимо, чтобы температура пламени примерно в 2 раза превышала температуру свариваемого металла. Поэтому использовать газы - заменители ацетилена целесообразно только при сварке металлов с более низкой температурой плавления, чем у стали, таких как алюминий, его сплавы, латунь, свинец. При резке металлолома используют пропан. Пропан - это горючий газ, который получают при добыче природных газов или при переработке нефти. Обычно получают не чистый пропан, а с примесью бутана до 5—30 %. Такая смесь именуется пропан-бутановой. Для сварочных работ пропан-бутановая смесь доставляется потребителю в сжиженном состоянии в специальных баллонах. Переход смеси из жидкого состояния в газообразное происходит самопроизвольно в верхней части баллона из-за меньшей удельной массы газа по сравнению со сжиженной смесью. Технический пропан тяжелее воздуха и имеет неприятный специфический запах. Природный газ состоит в основном из метана (степень чистоты 98 %), остальное - примеси в небольших количествах бутана и пропана. Газ имеет слабый запах, поэтому, чтобы обнаружить утечку, добавляют специальные пахнущие вещества. Чаще всего метан применяют при резке металлов. Для образования газового пламени в качестве горючего можно использовать и другие газы (водород, коксовый и нефтяной газы), горючие жидкости (бензин, керосин, ацетон и т. д.). Жидкие горючие менее дефицитны, но требуют специальной тары для хранения. Для сварки, резки и пайки горючая жидкость преобразуется в пары пламенем наконечника горелки или резака. Характеристика различных горючих газов и жидкостей, применяющихся в различных отраслях машиностроения и в ювелирной промышленности, приведена в табл. 50.
Таблица 50
Характеристика горючих газов и жидкостей, выраженная через коэффициент ацетилена
Наименование горючего | Температура пламен;! при сгорании е кислороде, °С | Масса І и’ горючего при 20 °С и даьлен;ш 7£0 мм рт_ ст.. кг | Коэффициент замены ап етиле на | Количество кислорода, подаваемого б горелку на 1 ьг1 горючего, м1 |
Г азы: ацетилен | 3050-3150 | 1.09 | 1.0 | 1.0-1.3 |
водород | 3000-2100 | O. OS4 | 5.2 | 0.3 -0.4 |
пиролизный | 2300 | Q.65-Q. S5 | 1.6 | 1.2-1.5 |
нефіяной | 2300 | 0.65-1.45 | 1.2 | 1.5-1.6 |
пропан технический | 2400-2500 | 1,90 | 0.6 | 3.4-3.S |
природный | 2100-2200 | 0.7-0.9 | 1,6-1,8 | 1.5-2 |
коксовый | 2000 | 0.4—0.5 | 3,2—4,0 | 0,6-0,8 |
сланцевый | 2000 | 0.7-0.9 | 4.0 | Г" О |
Пары керосина | 2400-2450 | S00-S4G* | 1,0-1,3 | 1.7-2.4 на 1кг |
Пары бензина | 2500-2600 | 700-760 | 1.4 | 1.1-1.4 на 1кг |
* Для керосина и бензина приведена масса 1 м3 жидкости.
Методы контроля качества сварных соединений могут быть разделены на две основные группы: методы контроля без разрушения образцов или изделий - неразрушающий контроль; методы контроля с разрушением образцов или производственных стыков …
Надежность эксплуатации сварных соединений зависит от их соответствия нормативно-технической документации, которая регламентирует конструктивные размеры и форму готовых сварных швов, прочность, пластичность, коррозионную стойкость и свойства сварных соединений. Сварные соединения, выполненные …
Для предупреждения пожаров необходимо соблюдать следующие противопожарные мероприятия. Постоянно следить за наличием и исправным состоянием противопожарных средств (огнетушителей, ящиков с сухим песком, лопат, пожарных рукавов, асбестовых покрывал и т. д.). …
msd.com.ua